BMW M3 1998 E36 Owners Manual
Manufacturer: BMW, Model Year: 1998, Model line: M3, Model: BMW M3 1998 E36Pages: 759
Page 91 of 759
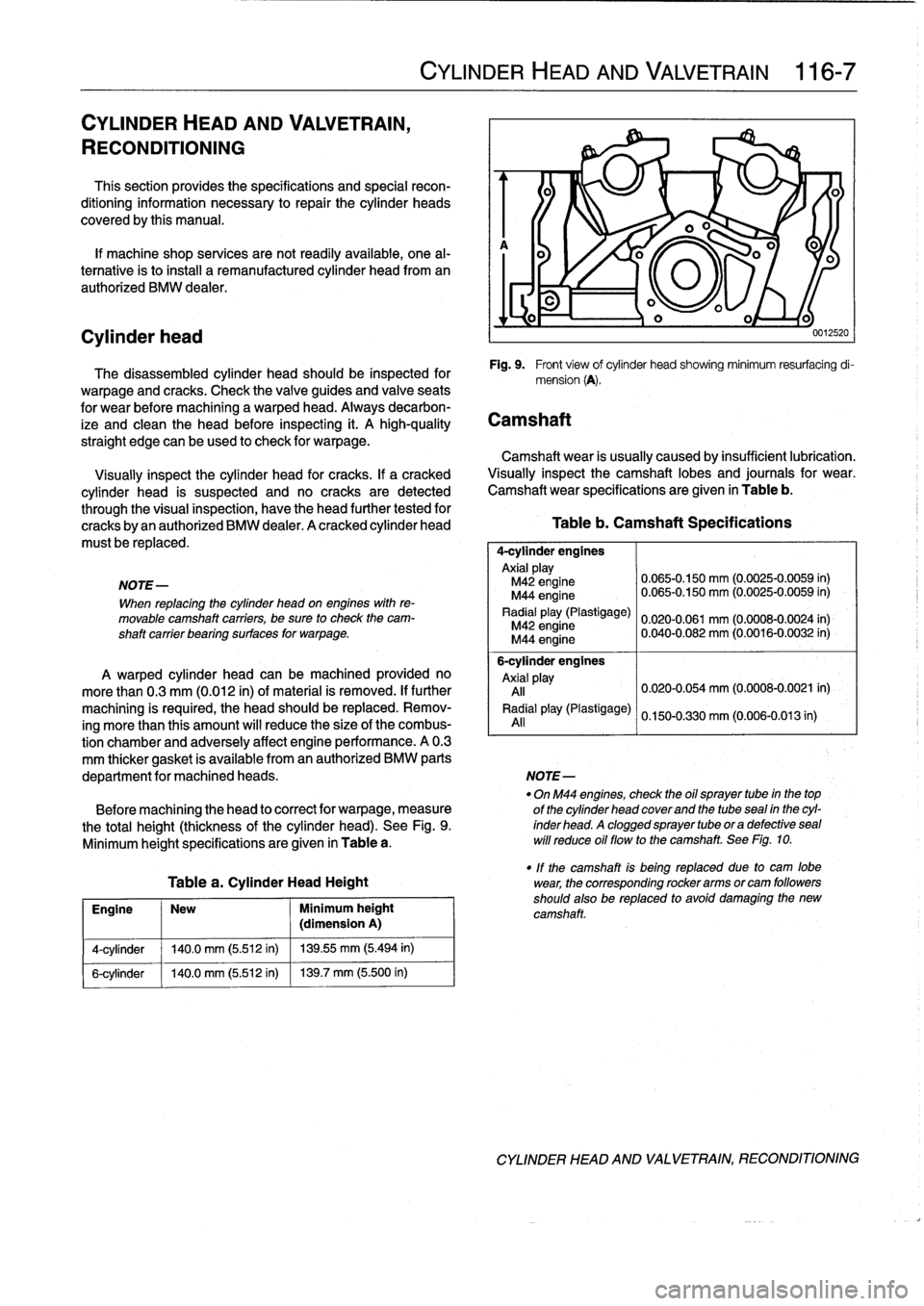
CYLINDER
HEAD
AND
VALVETRAIN,
RECONDITIONING
Thís
section
provides
the
specifications
and
special
recon-
ditioning
information
necessary
to
repair
the
cylinder
heads
covered
by
this
manual
.
If
machine
shop
services
are
not
readily
available,
one
al-
ternative
is
to
install
a
remanufactured
cylinder
head
froman
authorized
BMW
dealer
.
Cylinder
head
NOTE-
When
replacing
the
cylinder
headon
engines
with
re-
movablecamshaft
carriers,
be
sure
to
check
the
cam-
shaft
carrier
bearing
surfaces
for
warpage
.
4-cylinder
1
140
.0
mm
(5
.512
in)
1
139
.55
mm
(5
.494
in)
6-cylinder
1
140
.0
mm
(5
.512
in)
1
139
.7
mm
(5
.500
in)
CYLINDER
HEAD
AND
VALVETRAIN
116-
7
A
The
disassembled
cylinder
head
should
be
inspected
for
Fig
.
9
.
Front
víew
of
cylinder
head
showing
minimum
resurfacing
di-
warpage
and
cracks
.
Check
the
valve
guides
and
valveseats
mension
(A)
.
for
wear
before
machining
a
warped
head
.
Always
decarbon-
ize
and
clean
the
head
before
inspectiog
it
.
A
high-quality
Camshaft
straíght
edge
can
be
used
to
check
for
warpage
.
Camshaft
wear
is
usually
caused
by
insufficient
lubrication
.
Visually
inspect
the
cylinder
head
for
cracks
.
If
acracked
Visually
inspect
the
camshaft
lobes
and
journals
for
wear
.
cylinder
head
is
suspected
and
no
cracks
are
detected
Camshaftwear
specifications
are
given
in
Table
b
.
through
the
visual
inspection,
have
the
head
further
tested
for
cracks
byan
authorized
BMW
dealer
.
A
cracked
cylinder
head
Table
b
.
Camshaft
Specifications
must
be
replaced
.
4-cylinder
engines
Axialplay
M42
engine
0
.065-0
.150
mm
(0
.0025-0
.0059
in)
M44
engine
0
.065-0
.150
mm
(0
.0025-0
.0059
in)
Radial
play(Plastigage)
0
.020-0.061
mm
(0
.0008-0
.0024
in)
M42
engine
M44
engine
0
.040-0
.082
mm
(0
.0016-0
.0032
in)
6-cylinder
engines
A
warped
cylinder
head
can
be
machined
provided
no
Axial
pla
y
more
than
0
.3
mm
(0
.012
in)
of
material
is
removed
.
If
further
All
0
.020-0.054
mm
(0
.0008-0
.0021
in)
machining
is
required,
the
head
should
be
replaced
.
Remov-
Radial
play(Plastigage)
0
.150-0.330
mm
(0
.006-0.013
in)
ing
more
than
this
amount
will
reduce
the
size
of
the
combus-
All
tion
chamber
and
adversely
affect
engine
performance
.
A
0
.3
mm
thicker
gasket
is
available
from
an
authorized
BMW
parts
department
for
machined
heads
.
NOTE-
-
On
M44
engines,
check
the
oil
sprayer
tube
in
the
top
Before
machining
the
head
to
correct
for
warpage,
measure
of
the
cylinder
head
coverand
the
tubesea¡
in
the
cyl-
the
total
height(thicknessof
the
cylinder
head)
.
See
Fig
.
9
.
inderhead
.Acloggedsprayertubeoradefectiveseal
Minimum
height
specifications
are
given
in
Table
a
.
will
reduce
oil
flowto
the
camshaft
.
See
Fig
.
10
.
-
If
the
camshaft
is
being
replaced
due
to
cam
lobe
Table
a
.
Cylinder
Head
Height
wear,
the
corresponding
rockerarms
orcam
followers
Engine
New
Minimum
height
shouId
also
be
replaced
to
avofd
damaglng
the
new
(dimension
A)
camshaft
.
CYLINDER
HEAD
AND
VALVETRAIN,
RECONDITIONING
Page 92 of 759
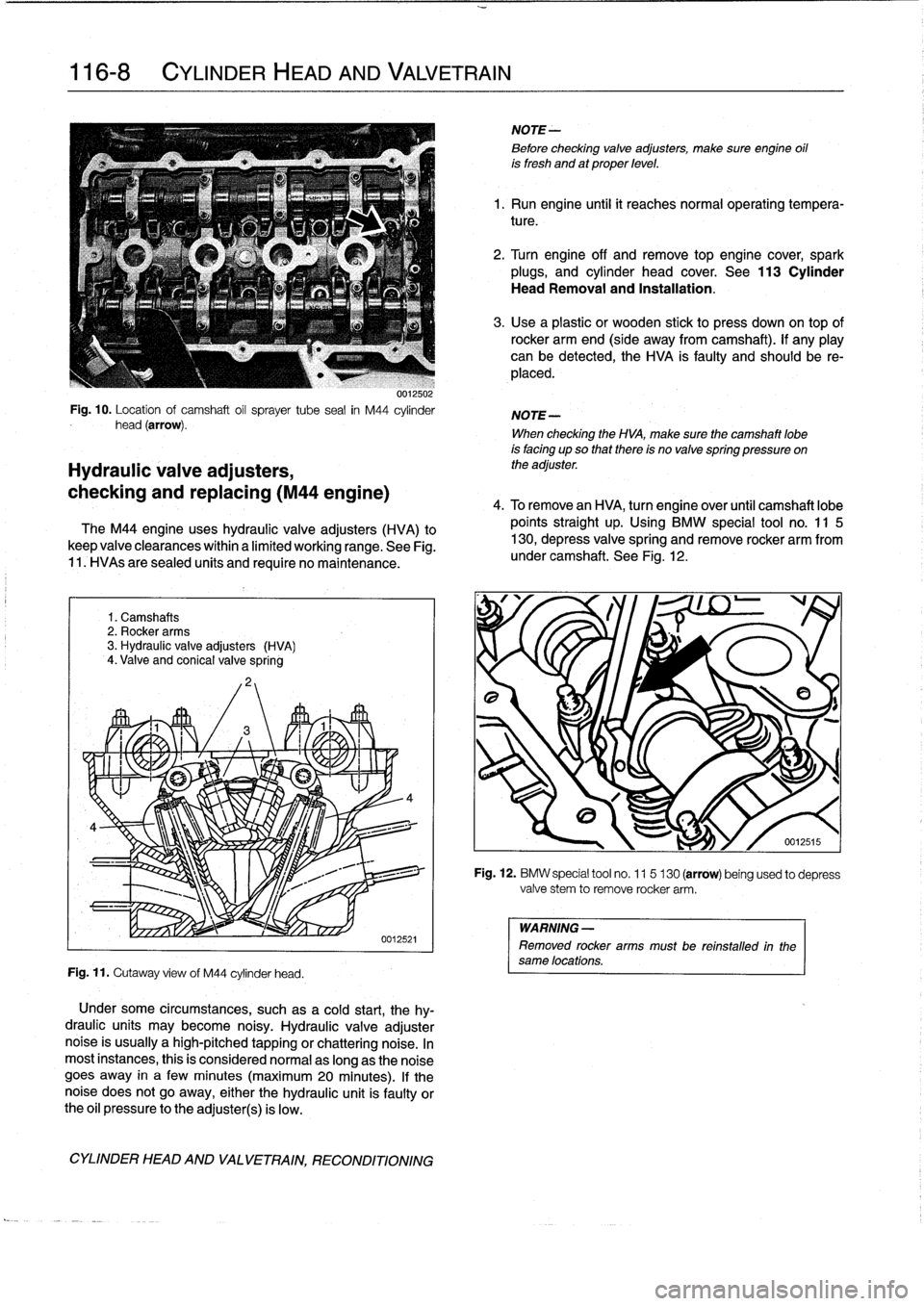
116-
8
CYLINDER
HEAD
AND
VALVETRAIN
0012502
Fig
.
10
.
Location
of
camshaft
oil
sprayer
tube
sea¡
in
M44
cylinder
head
(arrow)
.
Hydraulic
valve
adjusters,
checking
and
replacing
(M44
engine)
The
M44
engine
uses
hydraulic
valveadjusters
(HVA)
to
keep
valve
clearances
within
a
limited
working
range
.
See
Fig
.
11
.
HVAs
are
sealed
units
and
require
no
maintenance
.
1
.
Camshafts
2
.
Rocker
arms
3
.
Hydraulic
valve
adjusters
(HVA)
4
.
Valve
and
conical
valve
spring
Fig
.
11
.
Cutaway
view
of
M44
cylinder
head
.
Under
some
circumstances,
such
as
a
cold
start,
thehy-
draulic
units
may
become
noisy
.
Hydraulic
valve
adjusternoise
is
usually
ahigh-pitched
tapping
or
chattering
noise
.
In
most
instances,
this
is
consídered
normal
aslong
as
the
noise
goes
away
in
a
few
minutes
(maximum20
minutes)
.
If
thenoise
does
not
go
away,
either
the
hydraulic
unit
is
faulty
orthe
oil
pressure
tothe
adjuster(s)
is
low
.
CYLINDER
HEAD
AND
VALVETRAIN,
RECONDITIONING
NOTE-
8efore
checking
valveadjusters,
make
sure
engine
oil
is
fresh
and
at
proper
level
.
1
.
Run
engine
until
it
reaches
normal
operating
tempera-
ture
.
2
.
Turn
engine
off
and
remove
top
engine
cover,
spark
plugs,
and
cylinder
head
cover
.
See
113
Cylinder
Head
Removal
and
Installation
.
3
.
Use
a
plastic
or
wooden
stick
to
press
down
on
top
of
rocker
armend
(side
away
from
camshaft)
.
If
any
play
can
be
detected,the
HVA
is
faulty
and
should
be
re-
placed
.
NOTE-
When
checking
the
HVA,
make
sure
the
camshaft
lobe
is
facing
upso
that
there
is
no
valve
spring
pressure
on
the
adjuster
.
4
.
To
remove
an
HVA,
turn
engine
over
until
camshaft
lobe
points
straight
up
.
Using
BMW
special
tool
no
.
11
5
130,
depress
valvespring
and
remove
rocker
arm
from
under
camshaft
.
See
Fig
.
12
.
Fig
.
12
.
BMW
special
tool
no
.
115
130
(arrow)
being
used
to
depress
valve
stem
to
remove
rocker
arm
.
WARNING
-
Removed
rocker
armsmustbe
reinstalled
in
the
same
locations
.
Page 93 of 759
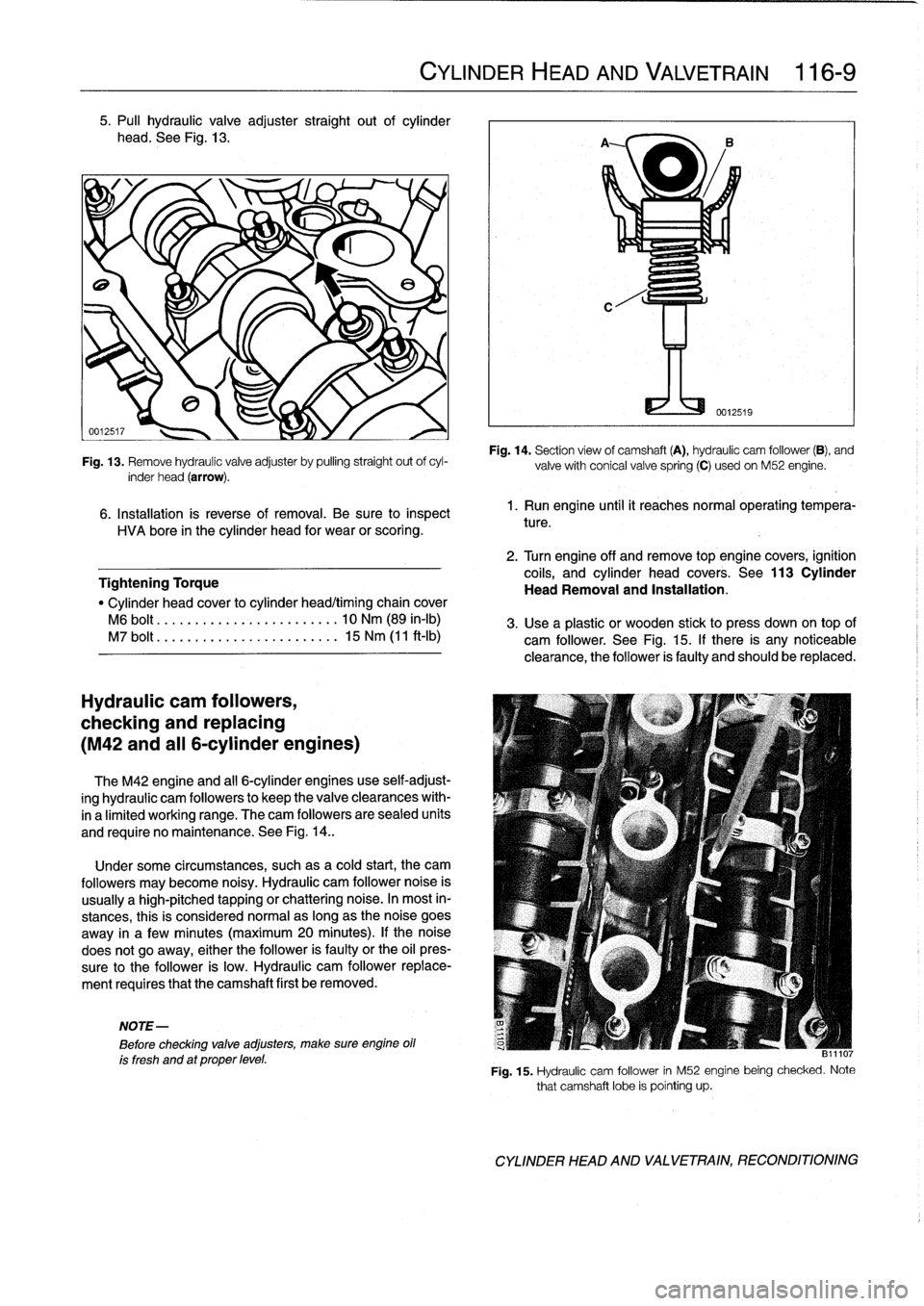
5
.
Pull
hydraulic
valve
adjuster
straight
out
of
cylinder
head
.
See
Fig
.
13
.
Fig
.
13
.
Remove
hydraulic
valve
adjuster
by
pulling
straight
out
ofcyl-
inder
head
(arrow)
.
6
.
Installation
is
reverse
of
removal
.
Be
sure
to
inspect
HVA
bore
in
the
cylinder
head
for
wear
or
scoring
.
Tightening
Torque
"
Cylinder
head
cover
to
cylinder
head/timing
chain
cover
M6
bolt
.........
..
..
...
........
10
Nm
(89
in-lb)
M7
bolt
.......
.
.
..
...
.
...
.
.....
15
Nm
(11
ft-Ib)
Hydraulic
cam
followers,
checking
and
replacing
(M42
and
al¡
6-cylinder
engines)
The
M42
engine
and
al¡
6-cylinder
engines
use
self-adjust-
ing
hydraulic
cam
followers
to
keep
the
valveclearances
with-
ina
limited
working
range
.
The
cam
followers
are
sealed
units
and
require
no
maintenance
.
See
Fig
.
14
.
.
Under
some
circumstances,
suchasa
cold
start,
the
cam
followers
may
become
noisy
.
Hydraulic
cam
follower
noise
is
usually
a
high-pitched
tapping
or
chattering
noise
.
In
most
in-
stances,
this
is
considered
normalas
long
as
the
noise
goes
away
in
a
fewminutes
(maximum
20
minutes)
.
lf
the
noise
does
not
go
away,
either
the
follower
is
faulty
or
the
oil
pres-
sure
to
the
follower
is
low
.
Hydraulic
cam
follower
replace-
ment
requires
that
the
camshaft
first
be
removed
.
NOTE-
Before
checking
valve
adjusters,
make
sure
engine
oil
ís
fresh
and
at
proper
level
.
CYLINDER
HEAD
AND
VALVETRAIN
116-
9
Fig
.
14
.
Section
view
of
camshaft
(A),
hydraulic
cam
follower
(B),
and
valvewith
conical
valvespring
(C)
usedon
M52
engine
.
1.
Run
engine
until
it
reachesnormal
operating
tempera-
ture
.
2
.
Turn
engine
off
and
remove
top
engine
covers,
ignition
coils,
and
cylinder
head
covers
.
See
113
Cylinder
Head
Removal
and
Installation
.
3
.
Use
a
plastic
or
wooden
stickto
press
down
on
top
of
cam
follower
.
See
Fig
.
15
.
If
there
is
any
noticeable
clearance,
the
follower
is
faulty
and
should
be
replaced
.
811107
Fig
.
15
.
Hydraulic
cam
follower
in
M52
enginebeing
checked
.
Note
that
camshaft
lobe
is
pointing
up
.
CYLINDER
HEAD
AND
VALVETRAIN,
RECONDITIONING
Page 94 of 759
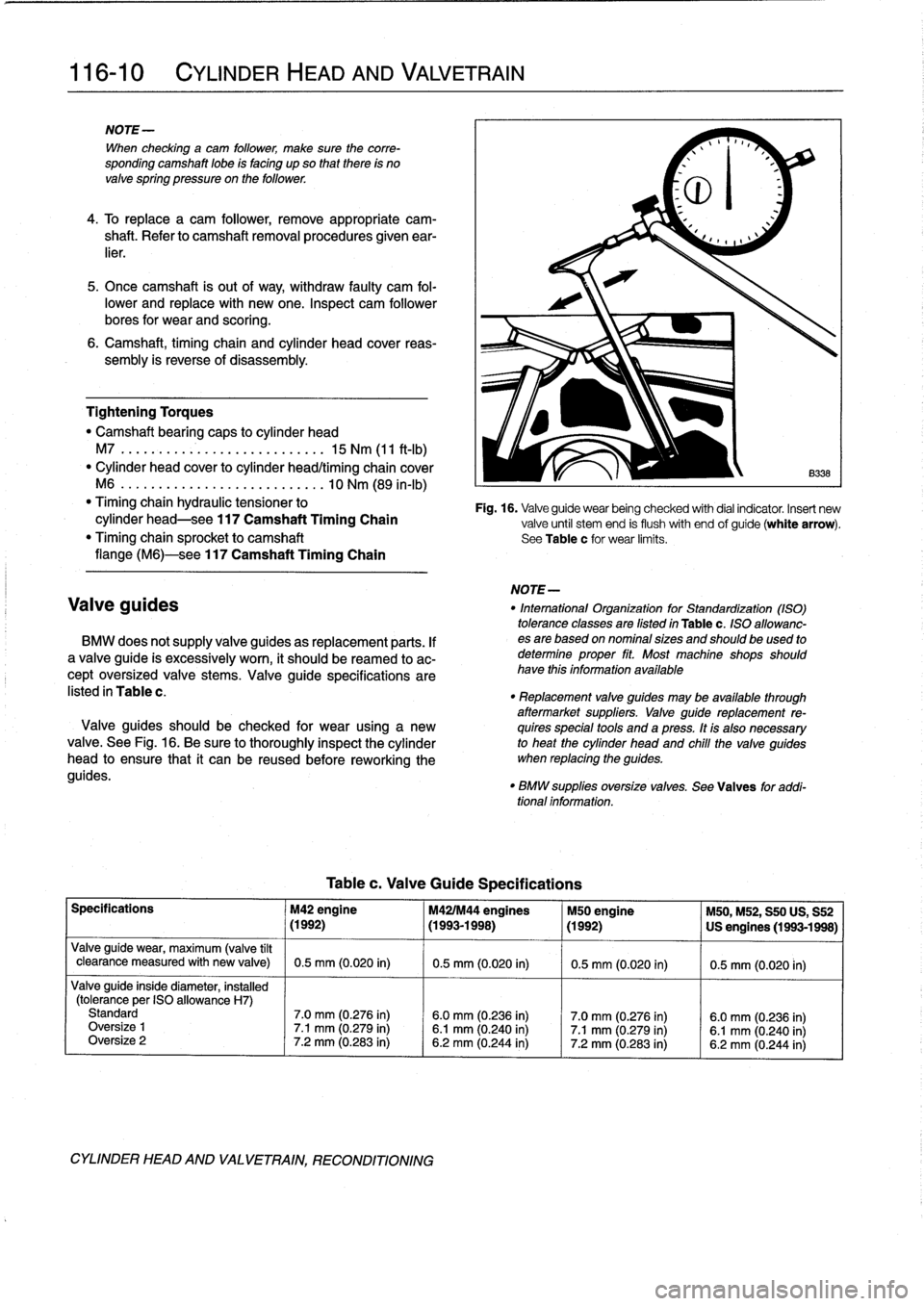
116-
1
0
CYLINDER
HEADAND
VALVETRAIN
NOTE-
When
checking
a
cam
follower,
make
sure
the
corre-
sponding
camshaft
lobe
ís
facing
up
so
that
there
is
no
valve
spring
pressure
on
the
follower
.
4
.
To
replace
a
cam
follower,
remove
appropriate
cam-
shaft
.
Refer
to
camshaft
removal
procedures
given
ear-
lier
.
5
.
Once
camshaft
is
out
of
way,
withdraw
faulty
cam
fol-
lower
and
replace
with
new
one
.
Inspect
cam
follower
bores
for
wear
and
scoring
.
6
.
Camshaft,
timing
chain
and
cylinder
head
cover
reas-
sembly
is
reverse
of
disassembly
.
Tightening
Torques
"
Camshaft
bearing
caps
to
cylinder
head
M7
....
.
..
.
......
.
.....
...
.
..
.
15
Nm
(11
ft-Ib)
"
Cylinder
head
cover
to
cylinder
headltiming
chain
cover
M6
....
.
..
.
.
.
..........
...
.
.
..
10
Nm
(89
in-lb)
"
Timing
chain
hydraulic
tensioner
to
cylinder
head-see
117
Camshaft
Timing
Chain
"
Timing
chain
sprocket
to
camshaft
flange
(M6)-see
117
Camshaft
Timing
Chain
CYLINDER
HEAD
AND
VALVETRAIN,
RECONDITIONING
Table
c
.
Valve
Guide
Specifications
Fig
.
16
.
Valveguide
wear
being
checked
with
dial
indicator
.
Insert
new
valve
until
stem
end
is
flush
with
end
of
guide(white
arrow)
.
See
Table
c
for
wear
limits
.
NOTE-
Valve
guides
"
Intemational
Organization
for
Standardization
(ASO)
tolerance
classes
are
Gsted
in
Table
c
.
ISO
allowanc
BMW
does
notsupply
valve
guides
as
replacement
parts
.
If
esare
based
on
nominal
sizes
and
should
beused
to
a
valve
guide
is
excessively
worn,
it
should
be
reamed
to
ac-
determine
proper
fit
.
Most
machine
shops
should
cept
oversized
valve
stems
.
Valve
guide
specifications
are
have
thís
informationavailable
listed
in
Table
c
.
"
Replacement
valve
guides
may
be
available
through
aftermarket
suppliers
.
Valve
guide
replacement
re-
Valve
guides
should
be
checked
for
wear
using
a
new
quires
specíal
tools
and
a
press
.
It
is
also
necessary
valve
.
See
Fig
.
16
.
Be
sure
to
thoroughly
inspect
the
cylinder
to
heat
the
cylinder
head
and
chile
the
valve
guides
head
to
ensure
that
it
can
be
reused
before
reworking
the
when
replacing
the
guides
.
guides
.
"
BMW
suppllesoversize
valves
.
Sea
Valves
for
addi-
tional
information
.
Specifications
M42
engine
M421M44
engines
M50
engine
M50,M52,
S50
US,
S52
~
(1992)
~
(1993-1998)
~
(1992)
~
US
engines
(1993-1998)
Valve
guide
wear,
maximum
(valve
tílt
clearance
measured
with
new
valve)
0
.5
mm
(0
.020
in)
0
.5
mm
(0
.020
in)
0
.5
mm
(0
.020
in)
0
.5
mm
(0
.020
in)
Valveguide
inside
diameter,
installed
(tolerance
per
ISO
allowance
H7)
Standard
7
.0
mm
(0
.276
in)
6
.0
mm
(0
.236
in)
7
.0
mm
(0.276
in)
6
.0
mm
(0
.236
in)
Oversize
1
7
.1
mm
(0
.279
in)
6
.1
mm
(0
.240
in)
7
.1
mm
(0.279
in)
6
.1
mm
(0
.240
in)
Oversize
2
7
.2
mm
(0
.283
in)
6
.2
mm
(0
.244
in)
7
.2
mm
(0
.283
in)
6
.2
mm
(0
.244
in)
Page 95 of 759
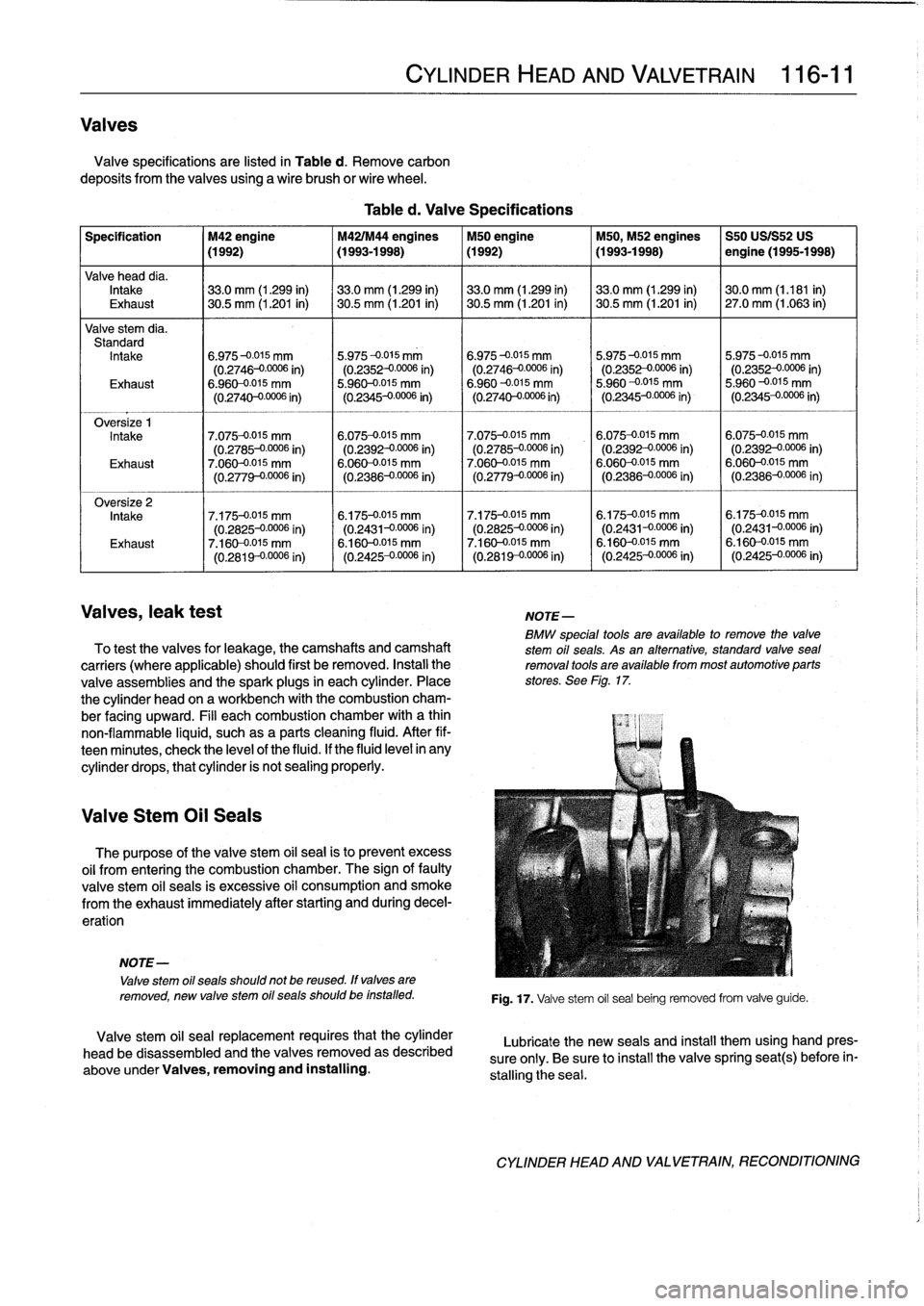
Valves
Valve
specifications
are
listed
in
Table
d
.
Remove
carbon
deposits
from
thevalves
using
a
wire
brush
or
wire
wheel
.
Specification
M42
engine
M42IM44
engines
M50
engine
M50,
M52
engines
S50
USIS52
US
(1992)
(1993-1998)
(1992)
(1993-1998)
I
engine
(1995-1998)
Valve
head
dia
.
Intake
133
.0
mm
(1
.299
in)
133
.0
mm
(1
.299
in)
33
.0
mm
(1
.299
in)
33
.0
mm
(1
.299
in)
130
.0
mm
(1
.181
in)
Exhaust
30
.5
mm
(1
.201
in)
30
.5
mm
(1
.201
in)
30
.5
mm
(1
.201
in)
~
30
.5
mm
(1
.201
in)
27
.0
mm
(1
.063
in)
Valve
stem
dia
.
Standard
Intake
6
.975-0
.015
mm
5
.975-0
.015
mm
6
.975-0
.015
mm
5
.975-0
.015
mm
5
.975-0015
mm
(0
.2746-00006
in)
(0
.2352-00006
in)
(0
.2746-00006
in)
(0
.2352-00006
in)
(0
.2352
-
00006
in)
Exhaust
6
.960-0015
mm
5
.960-0
.015
mm
6
.960
--0
.015
mm
5
.960
-0
.015
mm
5
.960-0
.015
mm
(0
.2740-00006
in)
(0
.2345-0
.0006
in)
(0
.2740--0
.0006
in)
(0
.2345-0
.0006
in)
(0
.2345-0
.0006
in)
Intake
7
.075-0
.015
mm
6
.075-0
.015
mm
7
.075-0
.015
mm
6
.075-0
.015
mm
6
.075-0
.015
mm
(0
.2785-00006
in)
(0
.2392-0
.0006
in)
(0
.2785-00006
in)
(0
.2392
-
00006
in)
(0
.2392-00006
in)
Exhaust
7
.060-0015
mm
6
.060-0015
mm
7
.060-0
.015
mm
6
.060-0015
mm
6
.060-0015
mm
(0
.
2779-0
.0006
in)
(0
.2386-00006
in)
(0
.2779-00006
in)
(0
.2386-00006
in)
(0
.2386-00006
in)
Oversize
2
Intake
7
.175-0
.015
mm
6
.175-0
.015
mm
7
.175-0
.015
mm
6
.175-0
.015
mm
6
.175-0
.015
mm
(0
.2825-00006
in)
(0
.2431-00006
in)
(0
.2825-00006
in)
(0
.2431--0
.0006
in)
(0
.2431-00006
in)
Exhaust
7
.160-0015
mm
6
.160-0015
mm
7
.160-0
.015
mm
6
.160-0015
mm
6
.160-0-015
mm
(0
.2819
-
00006
i
n
)
(0
.2425-00006
in)
(0
.2819-00006
in)
(0
.2425-00006
in)
(0
.2425-00006
in)
Valves,
leak
test
NOTE-
BMW
speclal
tools
are
available
to
remove
the
valve
To
test
thevalves
for
leakage,
the
camshafts
and
camshaft
stem
oil
seals
.
As
an
alternative,
standard
valvesea¡
carriers
(where
applicable)
should
first
be
removed
.
Instali
the
removal
tools
are
available
from
most
automotive
parts
valve
assemblies
and
the
spark
plugs
in
each
cylinder
.
Place
stores
.
See
Flg
.
17
.
the
cylinder
head
on
a
workbench
with
the
combustion
cham-
ber
facing
upward
.
Fill
each
combustion
chamber
with
a
thin
non-flammable
liquid,
suchas
a
parts
cleaning
fluid
.
After
fif-
teenminutes,
check
the
leve¡
of
the
fluid
.
If
the
fluid
level
in
any
cylinder
drops,
thatcylinder
is
not
sealing
properly
.
Valve
Stem
Oil
Seals
The
purpose
of
the
valve
stem
oil
sea¡
is
to
prevent
excess
oil
from
entering
the
combustion
chamber
.
The
sign
offautty
valve
stem
oil
seals
is
excessive
oil
consumption
and
smoke
from
the
exhaust
immediately
after
starting
and
during
decel-
erat¡on
NOTE-
Valve
stem
oil
seals
should
not
be
reused
.
ff
valves
are
removed,
new
valve
stem
oil
seals
should
be
installed
.
Valve
stem
oil
sea¡
replacement
requires
that
the
cylinder
head
be
disassembled
and
thevalves
removed
as
described
above
under
Valves,
removing
and
installing
.
CYLINDER
HEAD
AND
VALVETRAIN
116-
11
Table
d
.
Valve
Specifications
Fig
.
17
.
Valve
stem
oil
sea¡
being
removed
from
valve
guide
.
Lubricate
the
new
seals
and
insta¡]
them
using
hand
pres-
sure
only
.
Be
sure
to
install
the
valve
spring
seat(s)
before
in-
stalling
the
sea¡
.
CYLINDER
HEAD
AND
VALVETRAIN,
RECONDITIONING
Page 96 of 759
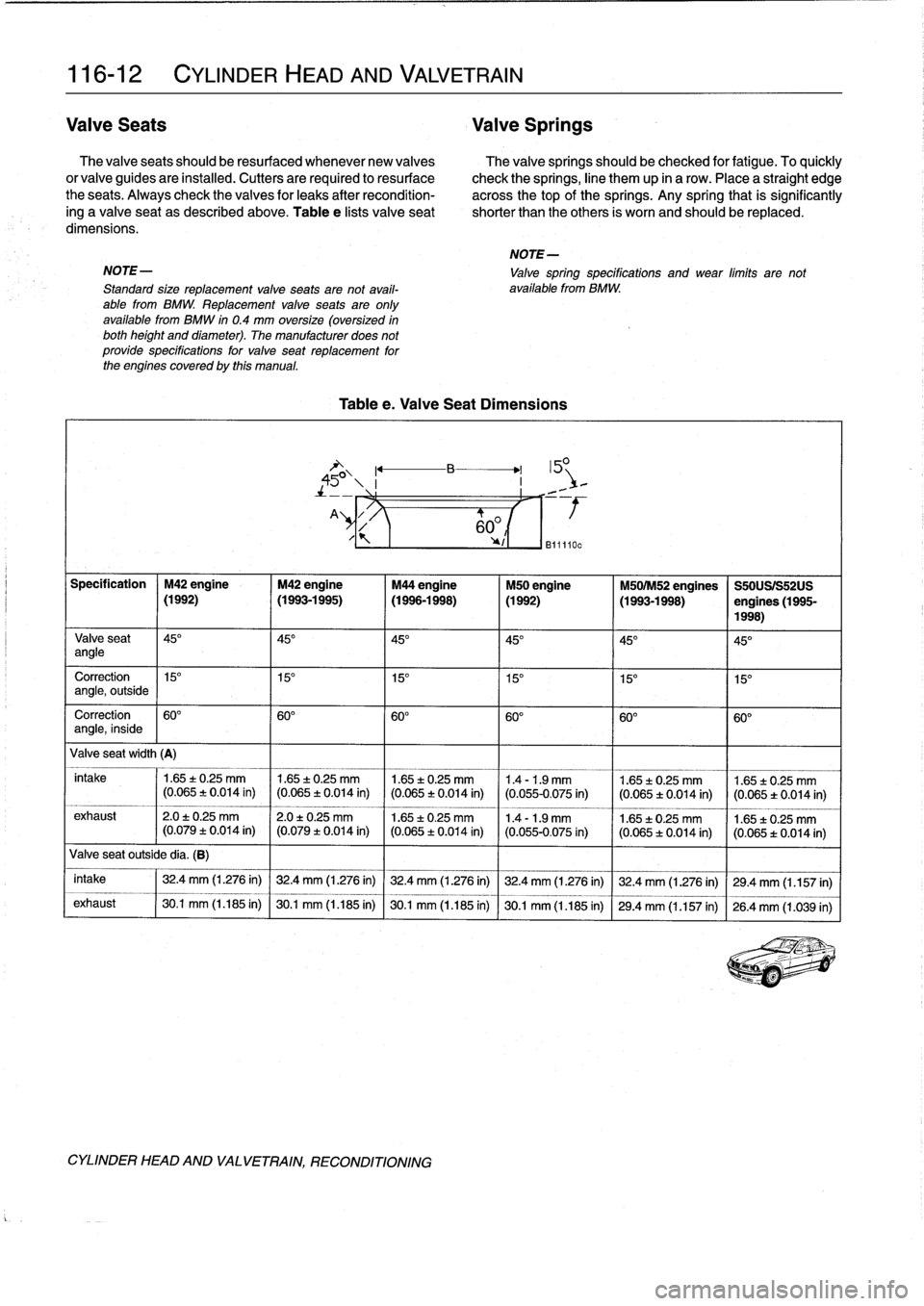
116-12
CYLINDER
HEADAND
VALVETRAIN
Valve
Seats
Valve
Springs
The
valve
seats
should
be
resurfaced
whenever
new
valves
The
valvesprings
should
be
checked
for
fatigue
.
To
quickly
or
valve
guides
are
installed
.
Cutters
are
required
to
resurface
check
the
springs,
line
them
up
in
a
row
.
Place
a
straight
edge
the
seats
.
Always
check
thevalves
for
leaks
after
recondition-
across
thetop
of
the
springs
.
Any
spring
that
is
significantly
ing
a
valve
seat
as
described
above
.
Table
e
lists
valve
seat
shorter
than
theothers
is
worn
and
should
be
replaced
.
dimensions
.
NOTE-
NOTE-
Valve
spring
specifications
and
wear
límits
arenot
Standard
size
replacement
valve
seats
are
not
avail-
available
from
BMW
.
ablefrom
BMW
.
Replacement
valve
seats
are
only
available
from
BMW
in
0
.4
mm
oversize
(oversized
in
both
height
and
diameter)
.
The
manufacturer
does
not
provide
specífications
for
valve
seat
replacement
for
the
enginescovered
by
this
manual
.
Table
e
.
Valve
Seat
Dimensions
"Y
Valve
seat
outside
dia
.
(B)
CYLINDER
HEAD
AND
VALVETRAIN,
RECONDITIONING
60
°
yl
1
B11110c
Specification
M42
engine
M42
engine
M44
engine
M50
engine
M501M52
engines
S50USIS52US
(1992)
(
(1993-1995)
I
(1996-1998)
(1992)
I
(1993-1998)
I
engines
(1995-
1998)
Valve
seat
45°
451
145°
145°
(
45°
145°
angle
Correction
1
15°
15°
115°
(
15°
15°
15
angle,
outside
Correction
60°
60°
I60°
60°
I60°
I60°
angle,
inside
Va
lve
seat
width
(A)
intake
1
1
.65
±0
.25
mm
1
1.65
±0
.25
mm
1
1
.65
t
0
.25
mm
1
1
.4
-1
.9
mm
1
1
.65
±0
.25
mm
1
1
.65
±
0
.25
mm
(0
.065
+0
.014
in)
I
(0.065
t
0
.014
in)
(0
.065
:E
0
.014
in)
(0
.055-0.075
in)
(0
.065
t
0
.014
in)
l(0
.065t0
.014
in)
____
___
exhaust
12
.0
±0
.25
mm
12
.0
t
0
.25
mm
1
1
.65
t
0
.25
mm
1
1
.4
-
1
.9
mm
11
.65
±
0
.25
mm
1
1
.65
:t
0
.25
mm
(0.079
±
0
.014
in)
1
(0
.079
t0
.014
in)
1
(0
.065
±
0
.014
in)
1
(0
.055-0.075
in)
1
(0
.065
t
0
.014
in)
1
(0.065
t0
.014
in)
intake
32
.4
mm
(1
.276
in)
32
.4
mm
(1
.276m)
32
.4
mm
(1
.276
in)
32
.4
mm
(1
.276
in)
32
.4
mm
(1
.276
in)
29
.4
mm
(1
.157
in)
exhaust
30
.1
mm
(1
.185
in)
30
.1
mm
(1
.185
in)
30
.1
mm
(1
.185
in)
30
.1
mm
(1
.185
in)
29
.4
mm
(1
.157
in)
26
.4
mm
(1
.039
in)
Page 97 of 759
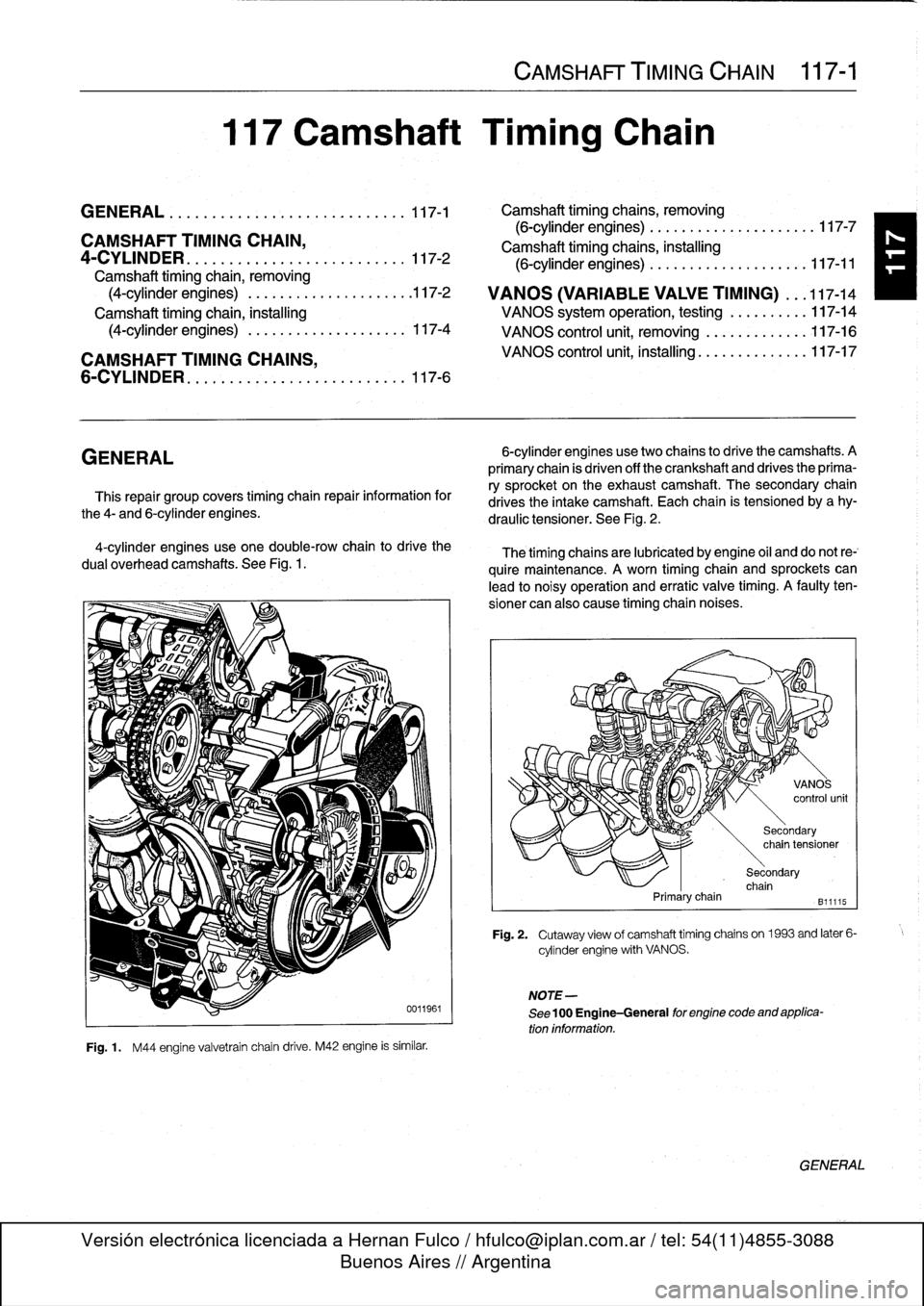
GENERAL
......
.
.
.
.
.
.
.
.
.
...
.
.
.
.
.
.
.
.
.
.
117-1
Camshaft
timing
chains,
removing
(6-cylinder
engines)
....
.
....
..
....
..
...
.117-7
CAMSHAFT
TIMING
CHAIN,
Camshaft
timing
chains,
installing
4-CYLINDER
....
.
.
.
.
.
.
.
.
.
.
.
.......
.
...
117-2
6-clinderen
nes
117-11
Camshaft
timingchain,
removing
(
y
gi
(4-cylinder
engines)
...
..
....
..
...
...
....
117-2
VANOS
(VARIABLE
VALVE
TIMING)
.
..
117-14
Camshaft
timingchain,
installing
VANOS
system
operation,
testing
.....
.
....
117-14
(4-cylinder
engines)
...
..
...
....
..
.
.....
117-4
VANOS
control
unit,
removing
.
..
..........
117-16
CAMSHAFT
TIMINGCHAINS,
VANOS
control
unit,
installing
..
..
..........
117-17
6-CYLINDER
.
.........................
117-6
GENERAL
117
Camshaft
Timing
Chain
This
repair
group
covers
timing
chain
repair
information
for
the
4-
and
6-cylinder
engines
.
4-cylinder
enginesuse
one
double-row
chain
to
drive
the
dual
overhead
camshafts
.
See
Fig
.
1
.
Fig
.
1
.
M44
engine
valvetrain
chain
drive
.
M42
engine
is
similar
.
CAMSHAFT
TIMING
CHAIN
117-1
6-cylinder
enginesusetwo
chains
to
drive
the
camshafts
.
A
primary
chain
is
driven
off
the
crankshaft
and
drives
the
prima-
ry
sprocket
on
the
exhaustcamshaft
.
The
secondary
chain
drives
the
intake
camshaft
.
Each
chain
is
tensioned
by
a
hy-
draulic
tensioner
.
See
Fig
.
2
.
The
timing
chainsare
lubricated
by
engine
oil
and
do
not
re-`
quire
maintenance
.
A
worn
timing
chain
and
sprockets
can
lead
to
noisy
operation
and
erratic
valve
timing
.
A
faulty
ten-
sioner
can
also
cause
timing
chaín
noises
.
Primarychain
NOTE-
See
100
Engine-General
for
engine
code
and
applica-
tion
information
.
Secondary
chain
tensioner
Secondary
chain
B11115
Fig
.
2
.
Cutaway
view
of
camshaft
timing
chains
on1963
and
later
6-
cylinder
engine
with
VANOS
.
GENERAL
Page 98 of 759
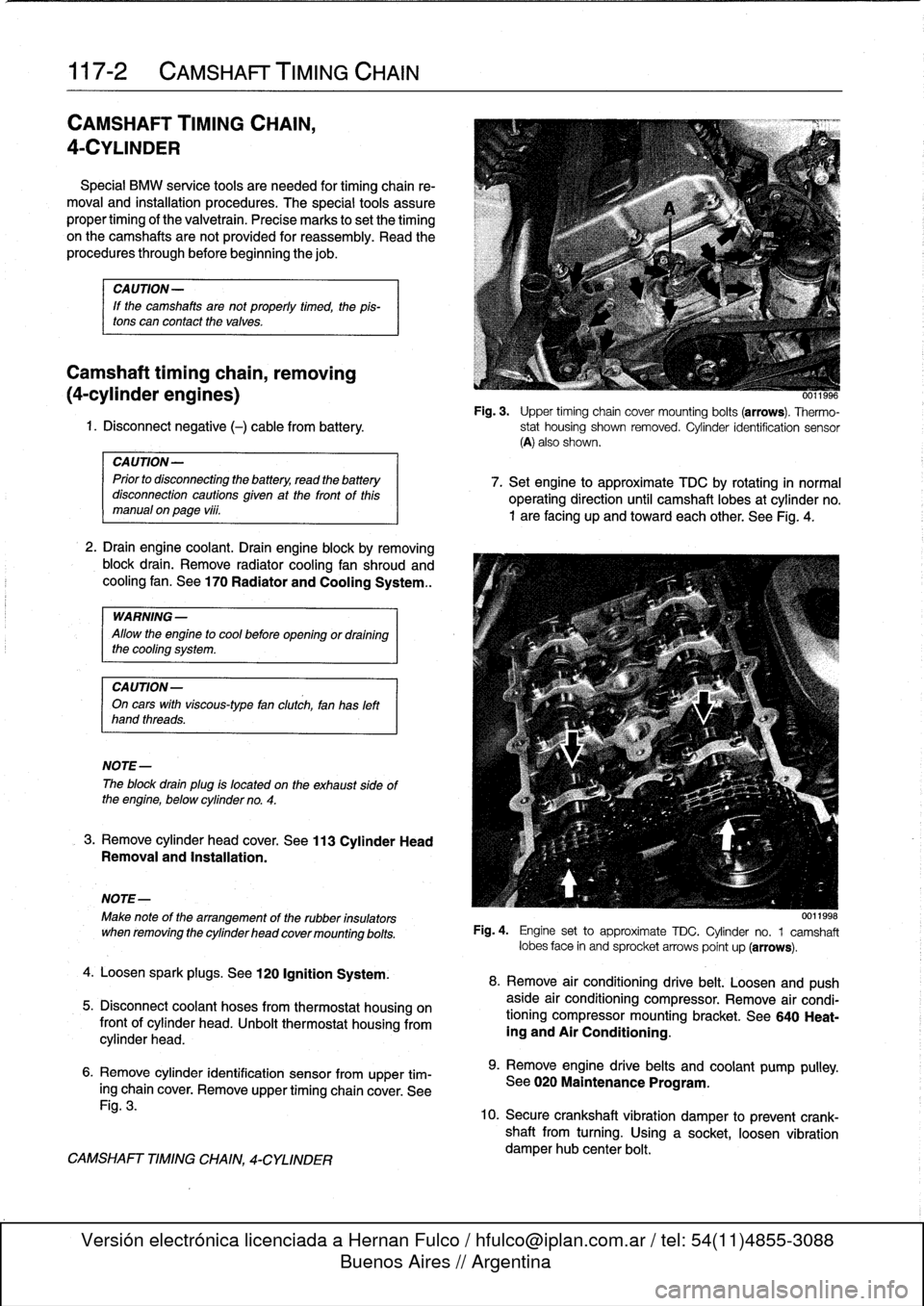
117-2
CAMSHAFT
TIMING
CHAIN
CAMSHAFT
TIMING
CHAIN,
4-CYLINDER
Special
BMW
service
tools
are
needed
for
timing
chain
re-
moval
and
installation
procedures
.
The
special
tools
assure
proper
timing
of
the
valvetrain
.
Precíse
marks
to
setthe
timing
on
the
camshafts
are
not
provided
for
reassembly
.
Read
the
procedures
through
before
beginning
the
job
.
CAUTION-
lf
the
camshaftsare
not
properly
timed,
the
pis-
tons
can
contact
thevalves
.
Camshaft
timing
chain,
removing
(4-cylinder
engines)
U0119-
Fig
.
3
.
Upper
timing
chain
covermounting
bolts(arrows)
.
Thermo-
1
.
Disconnect
negative
(-)cablefrom
battery
.
stat
housing
shown
removed
.
Cylinder
ídentification
sensor
(A)
also
shown
.
CAUTION-
Prior
to
disconnecting
the
battery,
read
the
battery
disconnection
cautions
given
at
the
front
of
this
manual
on
page
viii
.
2
.
Drain
engine
coolant
.
Drain
engine
block
byremoving
block
drain
.
Remove
radiator
cooling
fan
shroud
and
cooling
fan
.
See
170
Radiator
and
Cooling
System
..
WARNING
-
Allow
the
engine
to
cool
before
openingor
draining
the
cooling
system
.
CA
UTION-
On
cars
with
viscous-type
fan
clutch,
fan
has
left
hand
threads
.
NOTE-
The
block
drain
plug
is
located
on
the
exhaust
sideof
the
engine,
below
cylinder
no
.
4
.
3
.
Remove
cylinder
head
cover
.
See
113
Cylinder
HeadRemoval
and
Installation
.
NOTE-
Make
note
of
the
arrangement
of
the
rubber
insulators
when
removing
the
cylinder
head
cover
mounting
belts
.
4
.
Loosen
sparkplugs
.
See
120
Ignition
System
.
5
.
Disconnect
coolant
hoses
from
thermostat
housingon
front
of
cylinder
head
.
Unbolt
thermostat
housing
from
cylinder
head
.
6
.
Remove
cylinder
identification
sensor
from
upper
tim-
ing
chain
cover
.
Remove
upper
timing
chain
cover
.
See
Fig
.
3
.
CAMSHAFT
TIMING
CHAIN,
4-CYLINDER
7
.
Set
engine
to
approximate
TDC
by
rotating
in
normal
operating
direction
until
camshaft
lobes
at
cylinder
no
.
1
are
facing
up
and
toward
each
other
.
See
Fig
.
4
.
0011998
Fig
.
4
.
Engine
set
to
approximate
TDC
.
Cylinder
no
.
1
camshaft
lobes
face
in
and
sprocket
arrows
point
up
(arrows)
.
8
.
Remove
air
conditioning
drive
belt
.
Loosenand
push
aside
air
conditioning
compressor
.
Remove
air
condi-
tioning
compressor
mounting
bracket
.
See
640
Heat-
ing
and
Air
Conditioning
.
9
.
Remove
engine
drive
belts
and
coolant
pump
pulley
.
See
020
Maintenance
Program
.
10
.
Secure
crankshaft
vibration
damper
to
prevent
crank-
shaft
from
turning
.
Using
a
socket,
loosen
vibration
damper
hub
center
bolt
.
Page 99 of 759
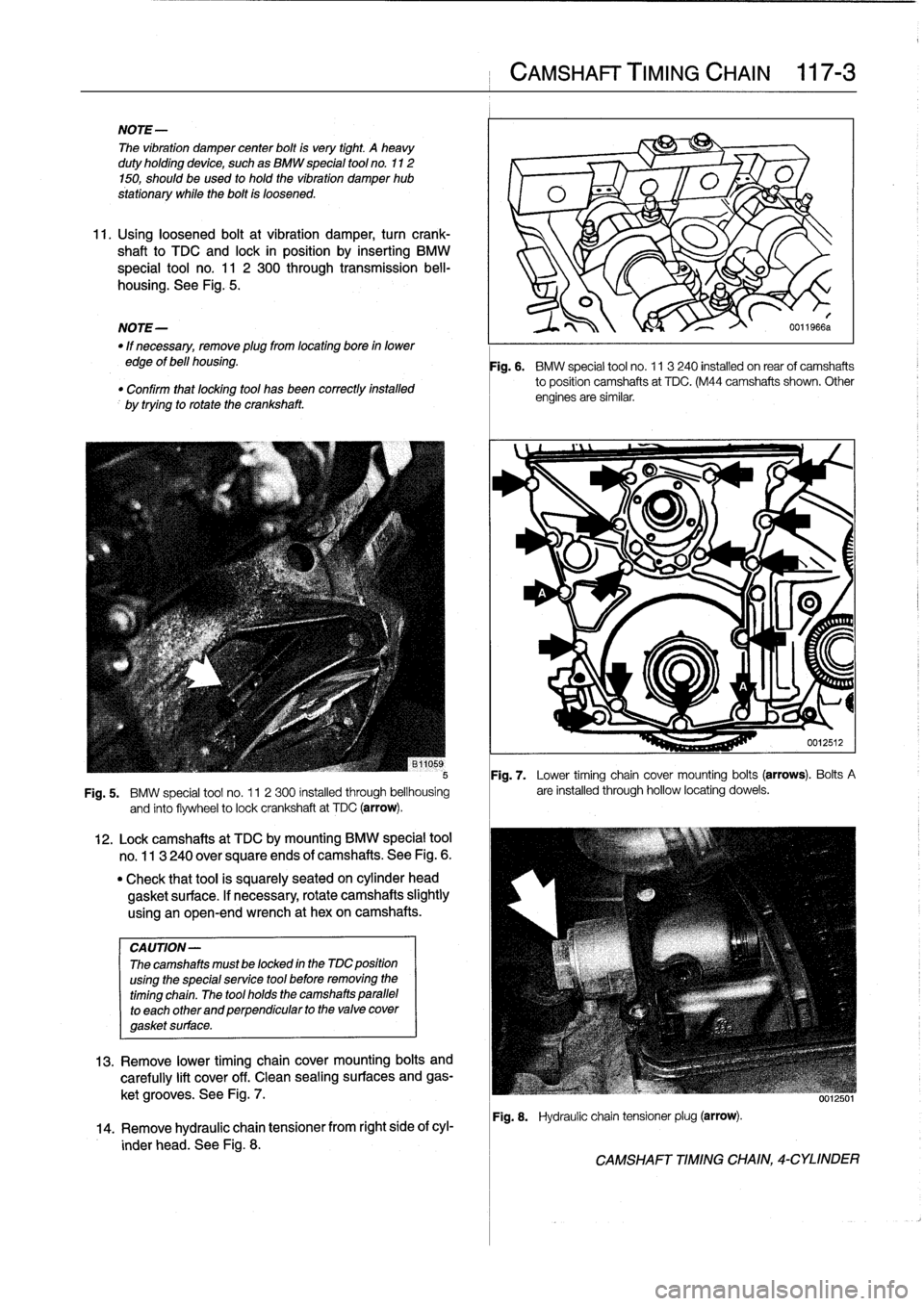
NOTE-
The
vibration
damper
center
bolt
is
very
tight
.
A
heavy
duty
holding
device,
such
as
BMW
special
tool
no
.
112
150,
should
be
used
to
hold
the
vibration
damper
hub
V
stationary
while
the
bolt
is
loosened
.
v
11
.
Usingloosened
bolt
at
vibration
damper,
turn
crank-
shaft
to
TDC
and
lock
in
position
by
inserting
BMW
special
tool
no
.
11
2
300
through
transmission
bell-
-
p
housing
.
See
Fig
.
5
.
v
O
NOTE-
I\
0011966a
"
If
necessary,
remove
plugfrom
locating
boye
in
lower
edge
of
bell
housing
.
"
Confirm
that
locatng
tool
has
been
correctlyinstalled
by
trying
to
rotate
the
crankshaft
.
Fig
.
7
.
Lower
timing
chain
cover
mounting
bolts
(arrows)
.
Bolts
A
Fig
.
5
.
BMW
special
tool
no
.
11
2300
installed
through
bellhousing
are
installed
through
hollow
locating
dowels
.
and
finto
flywheel
to
lock
crankshaft
at
TDC
(arrow)
.
CA
UTION-
Thecamshafts
mustbe
locked
in
the
MC
position
using
the
specialservice
tool
before
removing
the
timing
chain
.
The
tool
holds
the
camshafts
parallel
to
each
other
and
perpendicular
to
the
valve
cover
gasket
surface
.
12
.
Lockcamshafts
at
TDC
bymounting
BMW
special
tool
no
.
113
240
over
square
ends
of
camshafts
.
See
Fig
.
6
.
"
Check
that
tool
is
squarely
seated
on
cylinder
head
gasket
surface
.
If
necessary,
rotate
camshafts
slightly
using
an
open-end
wrench
at
hexon
camshafts
.
13
.
Remove
lower
timing
chaincover
mounting
bolts
and
carefully
lift
cover
off
.
Clean
sealing
surfaces
and
gas-
ket
grooves
.
See
Fig
.
7
.
14
.
Remove
hydraulic
chaintensioner
from
right
side
of
cyl-
inder
head
.
See
Fig
.
8
.
CAMSHAFT
TIMING
CHAIN
117-
3
Fig
.
6
.
BMW
special
tool
no
.
11
3240
installed
on
rearof
camshafts
to
position
camshafts
at
TDC
.
(M44
camshafts
shown
.
Other
engines
are
similar
.
Fig
.
8
.
Hydraulic
chain
tensionerplug
(arrow)
.
CAMSHAFT
TIMING
CHAIN,
4-CYLINDER
Page 100 of 759
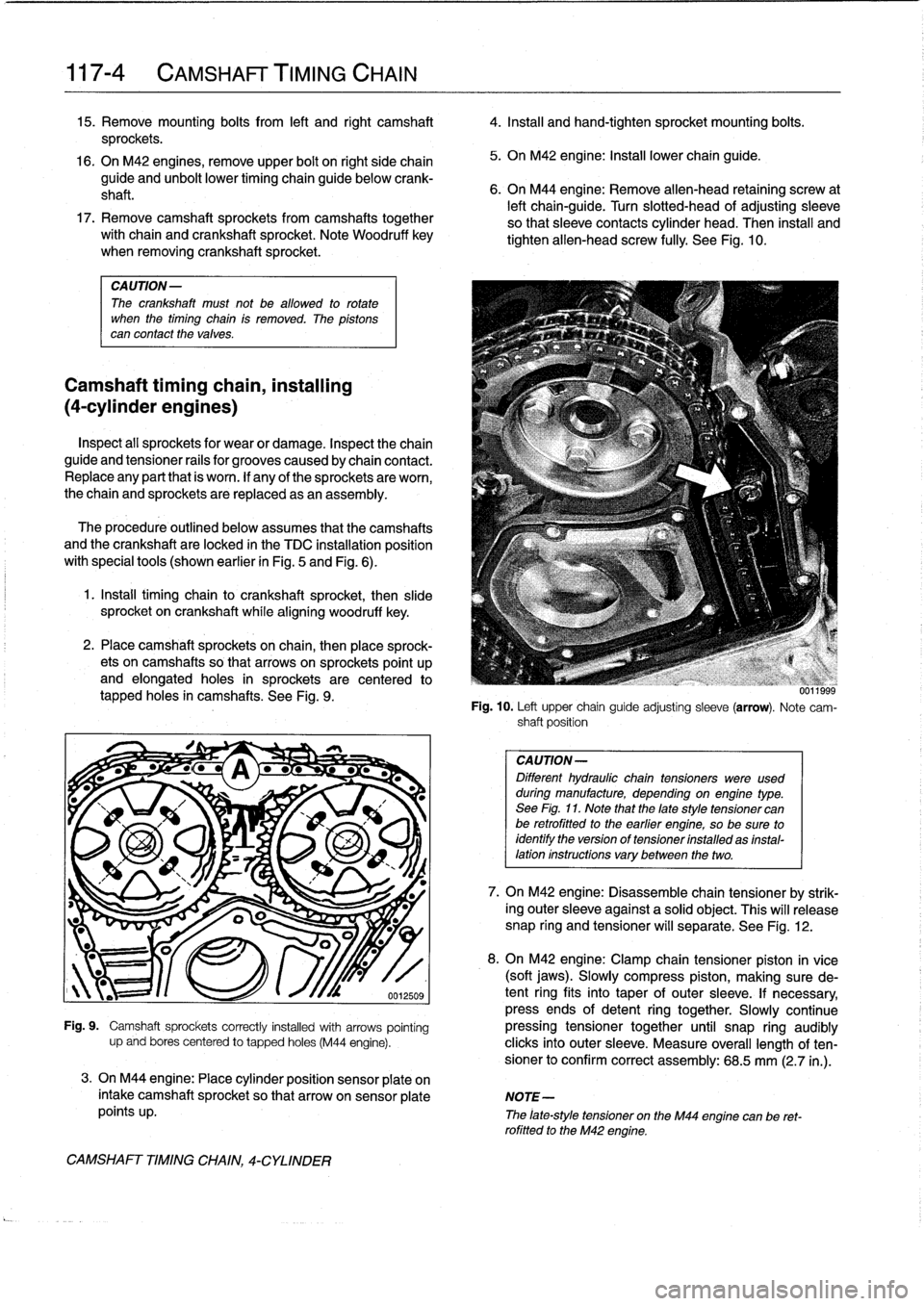
117-
4
CAMSHAFT
TIMING
CHAIN
15
.
Remove
mounting
bolts
from
left
and
right
camshaft
4
.
Insta¡¡
and
hand-tighten
sprocket
mounting
bolts
.
sprockets
.
16
.
On
M42
engines,
remove
upper
bolt
on
right
side
chainguide
and
unbolt
lower
timing
chainguide
below
crank-
shaft
.
17
.
Remove
camshaft
sprockets
from
camshafts
together
with
chain
and
crankshaft
sprocket
.
NoteWoodruffkey
when
removing
crankshaftsprocket
.
CA
UTION-
The
crankshaft
must
not
be
allowed
to
rotate
when
the
timing
chaín
is
removed
.
The
pistons
can
contact
the
valves
.
Camshaft
timing
chain,
installing
(4-cylinder
engines)
Inspectal¡
sprockets
for
wear
or
damage
.
Inspect
the
chain
guide
and
tensioner
rails
for
grooves
caused
by
chain
contact
.
Replace
any
partthat
is
worn
.
If
any
of
the
sprockets
are
worn,
the
chain
and
sprocketsare
replaced
asan
assembly
.
The
procedure
outlined
below
assumes
that
the
camshafts
and
the
crankshaft
arelocked
in
the
TDC
installation
positionwithspecial
tools
(shown
earlier
in
Fig
.
5
and
Fig
.
6)
.
1
.
Install
timing
chain
to
crankshaft
sprocket,
then
slide
sprocket
on
crankshaft
whílealigníng
woodruff
key
.
2
.
Place
camshaft
sprockets
on
chain,
then
place
sprock-
ets
oncamshafts
so
that
arrows
on
sprockets
point
up
and
elongatedholes
in
sprockets
are
centered
lo
tapped
holes
in
camshafts
.
See
Fig
.
9
.
.
I
Pa
-
s
~_
a
Ge
..
.
0012509
5
.
On
M42
engine
:
Install
lowerchainguide
.
6
.
On
M44
engine
:
Remove
allen-head
retaining
screw
at
left
chain-guide
.
Turn
slotted-head
of
adjusting
sleeve
so
that
sleeve
contacts
cylinder
head
.
Then
install
and
tighten'allen-head
screw
fully
.
See
Fig
.
10
.
Fig
.
10
.
Left
upper
chain
guide
adjusting
sleeve
(arrow)
.
Note
cam-
shaft
position
CAUTION-
Different
hydraulic
chaintensioners
were
used
duringmanufacture,
depending
onengíne
type
.
See
Fig
.
11
.
Note
that
the
late
style
tensioner
canbe
retrofitted
to
the
earlier
engíne,
so
be
sure
to
identify
the
versíon
of
tensioner
ínstalled
as
ínstal-
lation
instructions
vary
between
the
two
.
7
.
On
M42
engine
:
Disassemble
chain
tensioner
by
strik-
ing
outer
sleeve
against
a
solid
object
.
This
will
release
snap
ring
and
tensioner
will
separate
.
See
Fig
.
12
.
8
.
On
M42
engine
:
Clamp
chain
tensioner
piston
in
vice
(soft
jaws)
.
Slowly
compress
piston,
making
sure
de-
tent
ring
fits
into
taper
of
outer
sleeve
.
If
necessary,
press
ends
of
detent
ring
together
.
Slowly
continueFig
.
9
.
Camshaft
sprockets
correctly
installed
with
arrows
pointing
pressing
tensioner
together
until
snap
ring
audibly
upand
bores
centered
to
tapped
holes
(M44
engine)
.
clicks
into
outer
sleeve
.
Measure
overall
length
of
ten-
sionerto
confirm
correct
assembly
:
68
.5
mm
(2
.7
in
.)
.
3
.
On
M44
engine
:
Place
cylinder
position
sensor
plate
on
intake
camshaft
sprocket
so
that
arrowonsensor
plate
NOTE-
points
up
.
The
¡ate-style
tensioner
on
the
M44
engine
can
be
ret-rofittedto
the
M42
engíne
.
CAMSHAFT
TIMING
CHAIN,
4-CYLINDER