oil temperature ASTON MARTIN DB7 1997 Workshop Manual
[x] Cancel search | Manufacturer: ASTON MARTIN, Model Year: 1997, Model line: DB7, Model: ASTON MARTIN DB7 1997Pages: 421, PDF Size: 9.31 MB
Page 27 of 421
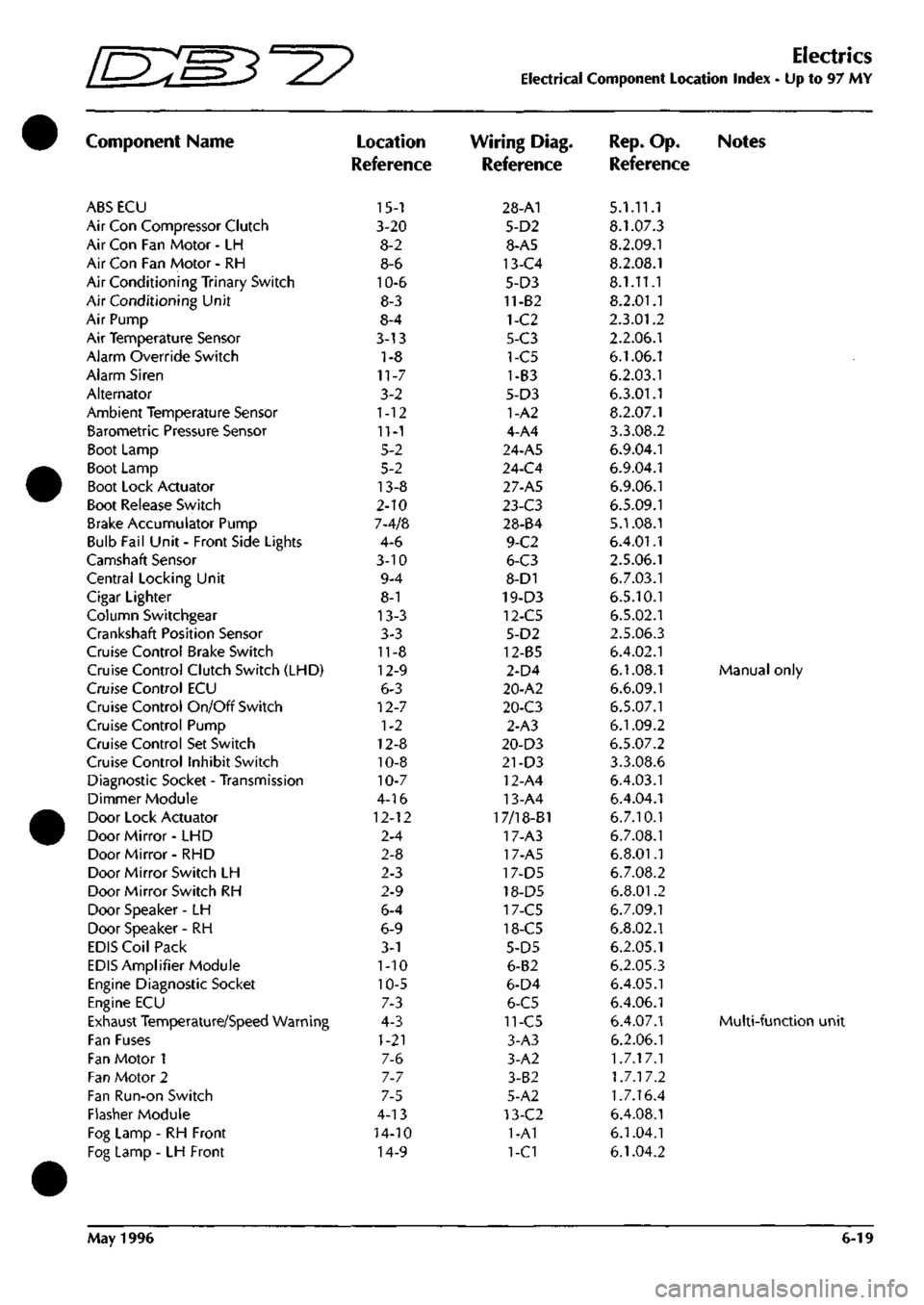
Electrics
Electrical Component Location Index - Up to 97 MY
Component Name
ABS ECU
Air Con Compressor Clutch
Air Con Fan Motor - LH
Air Con Fan Motor - RH
Air Conditioning Trinary Switch
Air Conditioning Unit
Air Pump
Air Temperature Sensor
Alarm Override Switch
Alarm Siren
Alternator
Ambient Temperature Sensor
Barometric Pressure Sensor
Boot Lamp
Boot Lamp
Boot Lock Actuator
Boot Release Switch
Brake Accumulator Pump
Bulb Fail Unit - Front Side Lights
Camshaft Sensor
Central Locking Unit
Cigar Lighter
Column Switchgear
Crankshaft Position Sensor
Cruise Control Brake Switch
Cruise Control Clutch Switch (LHD)
Cruise Control ECU
Cruise Control On/Off Switch
Cruise Control Pump
Cruise Control Set Switch
Cruise Control Inhibit Switch
Diagnostic Socket - Transmission
Dimmer Module
Door Lock Actuator
Door Mirror- LHD
Door Mirror- RHD
Door Mirror Switch LH
Door Mirror Switch RH
Door Speaker -LH
Door Speaker - RH
EDIS Coil Pack
EDIS Amplifier Module
Engine Diagnostic Socket
Engine ECU
Exhaust Temperature/Speed Warning
Fan Fuses
Fan Motor 1
Fan Motor 2
Fan Run-on Switch
Flasher Module
Fog Lamp - RH Front
Fog Lamp - LH Front
Location
Reference
15-1
3-20
8-2
8-6
10-6
8-3
8-4
3-13
1-8
11-7
3-2
1-12
11-1
5-2
5-2
13-8
2-10
7-4/8
4-6
3-10
9-4
8-1
13-3
3-3
11-8
12-9
6-3
12-7
1-2
12-8
10-8
10-7
4-16
12-12
2-4
2-8
2-3
2-9
6-4
6-9
3-1
1-10
10-5
7-3
4-3
1-21
7-6
7-7
7-5
4-13
14-10
14-9
Wiring Diag.
Reference
28-A1
5-D2
8-A5
13-C4
5-D3
11-82
1-C2
5-C3
1-C5
1-B3
5-D3
1-A2
4-A4
24-A5
24-C4
27-A5
l-i-C3
28-84
9-C2
6-C3
8-D1
19-D3
12-C5
5-D2
12-85
2-D4
20-A2
20-C3
2-A3
20-D3
21-D3
12-A4
13-A4
17/18-B1
17-A3
17-A5
17-D5
18-D5
17-C5
18-C5
5-D5
6-B2
6-D4
6-C5
11-C5
3-A3
3-A2
3-B2
5-A2
13-C2
1-A1
1-C1
Rep.
Op. Notes
Reference
5.1.11.1
8.1.07.3
8.2.09.1
8.2.08.1
8.1.11.1
8.2.01.1
2.3.01.2
2.2.06.1
6.1.06.1
6.2.03.1
6.3.01.1
8.2.07.1
3.3.08.2
6.9.04.1
6.9.04.1
6.9.06.1
6.5.09.1
5.1.08.1
6.4.01.1
2.5.06.1
6.7.03.1
6.5.10.1
6.5.02.1
2.5.06.3
6.4.02.1
6.1.08.1 Manual only
6.6.09.1
6.5.07.1
6.1.09.2
6.5.07.2
3.3.08.6
6.4.03.1
6.4.04.1
6.7.10.1
6.7.08.1
6.8.01.1
6.7.08.2
6.8.01.2
6.7.09.1
6.8.02.1
6.2.05.1
6.2.05.3
6.4.05.1
6.4.06.1
6.4.07.1 Multi-functio
6.2.06.1
1.7.17.1
1.7.17.2
1.7.16.4
6.4.08.1
6.1.04.1
6.1.04.2
May 1996 6-19
Page 109 of 421
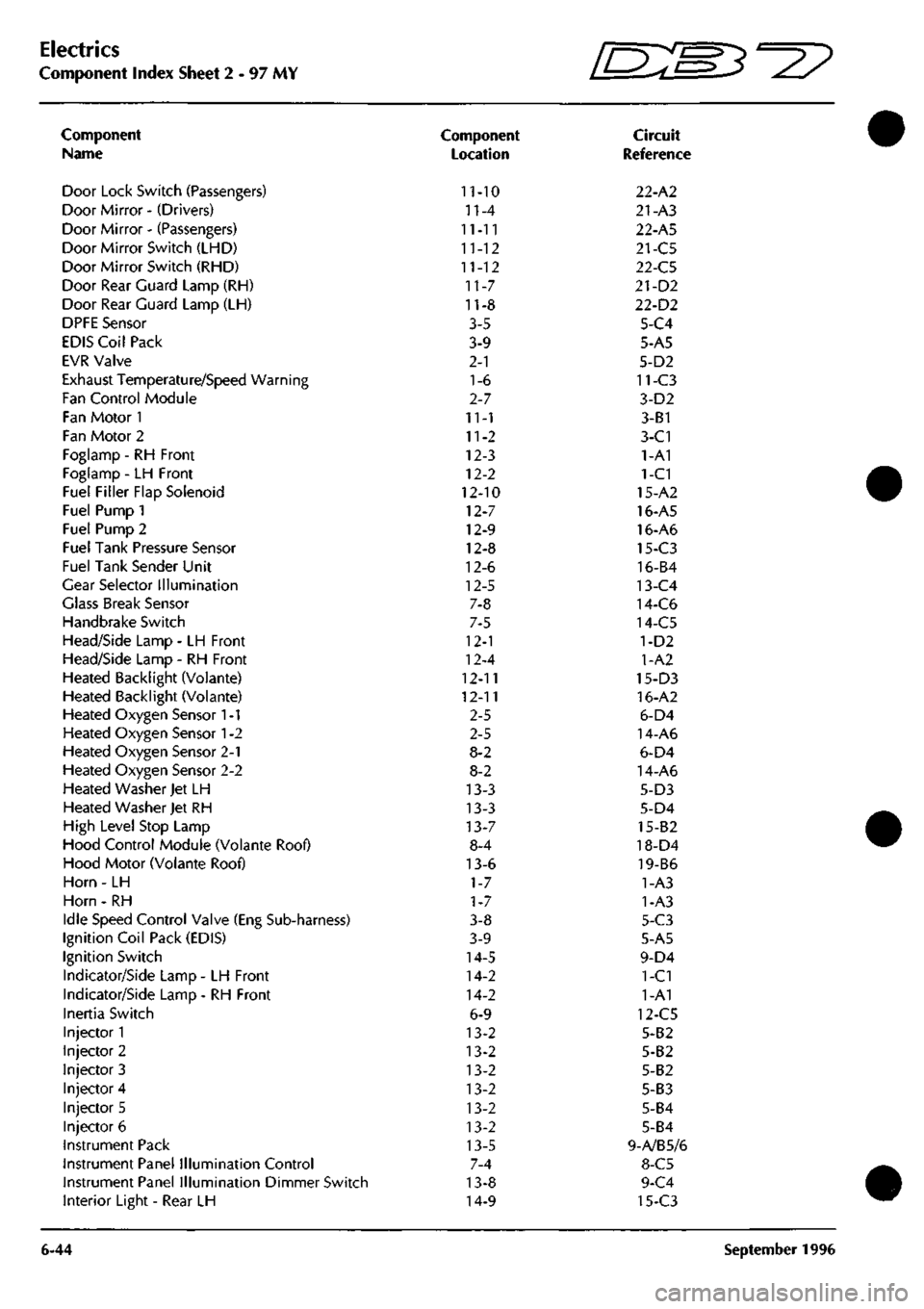
Electrics
Component Index Sheet 2 - 97 MY
Component
Name
Door Lock Switch (Passengers)
Door Mirror - (Drivers)
Door Mirror - (Passengers)
Door Mirror Switch (LHD)
Door Mirror Switch (RHD)
Door Rear Guard Lamp (RH)
Door Rear Guard Lamp (LH)
DPFE Sensor
EDIS Coil Pack
EVR Valve
Exhaust Temperature/Speed Warning
Fan Control Module
Fan Motor 1
Fan Motor 2
Foglamp - RH Front
Foglamp - LH Front
Fuel Filler Flap Solenoid
Fuel Pump 1
Fuel Pump 2
Fuel Tank Pressure Sensor
Fuel Tank Sender Unit
Gear Selector Illumination
Glass Break Sensor
Handbrake Switch
Head/Side Lamp - LH Front
Head/Side Lamp - RH Front
Heated Backlight (Volante)
Heated Backlight (Voiante)
Heated Oxygen Sensor
1
-1
Heated Oxygen Sensor
1
-2
Heated Oxygen Sensor 2-1
Heated Oxygen Sensor 2-2
Heated Washer Jet LH
Heated Washer Jet RH
High Level Stop Lamp
Hood Control Module (Volante Roof)
Hood Motor (Volante Roof)
Horn - LH
Horn - RH
Idle Speed Control Valve (Eng Sub-harness)
Ignition Coil Pack (EDIS)
Ignition Switch
Indicator/Side Lamp - LH Front
Indicator/Side Lamp - RH Front
Inertia Switch
Injector 1
Injector 2
Injector 3
Injector 4
Injector 5
Injector 6
Instrument Pack
Instrument Panel Illumination Control
Instrument Panel Illumination Dimmer Switch
Interior Light - Rear LH
6-44
Component
Location
11-10
n-4
11-11
11-12
11-12
11-7
11-8
3-5
3-9
2-1
1-6
2-7
11-1
11-2
12-3
12-2
12-10
12-7
12-9
12-8
12-6
12-5
7-8
7-5
12-1
12-4
12-11
12-11
2-5
2-5
8-2
8-2
13-3
13-3
13-7
8-4
13-6
1-7
1-7
3-8
3-9
14-5
14-2
14-2
6-9
13-2
13-2
13-2
13-2
13-2
13-2
13-5
7-4
13-8
14-9
fEB^-^?
Circuit
Reference
22-A2
21-A3
22-A5
21-C5
22-C5
21-D2
22-D2
5-C4
5-A5
5-D2
11-C3
3-D2
3-B1
3-C1
1-A1
1-C1
15-A2
16-A5
16-A6
15-C3
16-B4
13-C4
14-C6
14-C5
1-D2
1-A2
15-D3
16-A2
6-D4
14-A6
6-D4
14-A6
5-D3
5-D4
15-82
18-D4
19-B6
1-A3
1-A3
5-C3
5-A5
9-D4
1-C1
1-A1
12-C5
5-B2
5-B2
5-B2
5-B3
5-B4
5-B4
9-A/B5/6
8-C5
9-C4
15-C3
September 1996
Page 278 of 421
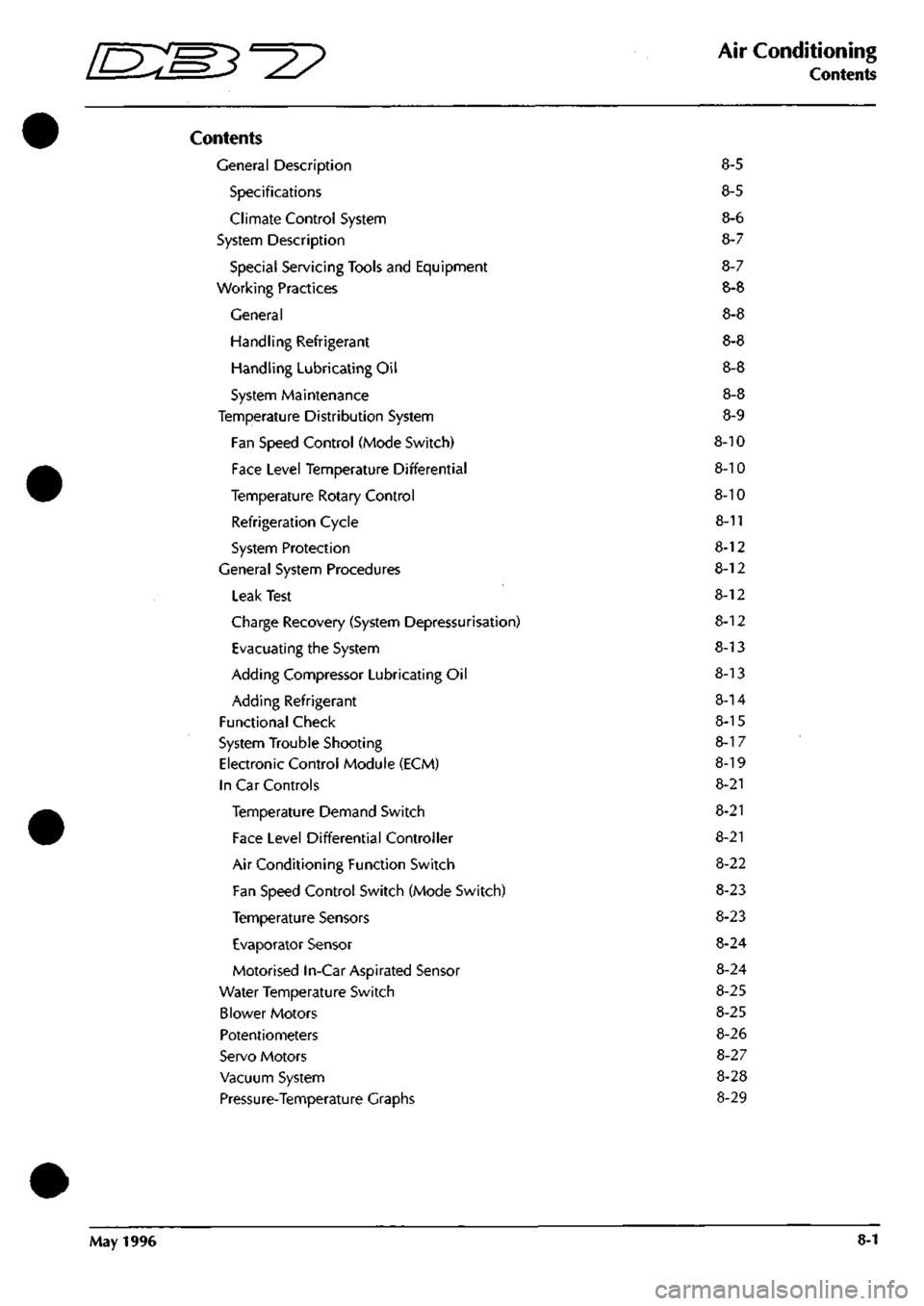
in:!M3^^?
Air Conditioning
Contents
Contents
General Description 8-5
Specifications 8-5
Climate Control System 8-6
System Description 8-7
Special Servicing Tools and Equipment 8-7
Working Practices 8-8
General 8-8
Handling Refrigerant 8-8
Handling Lubricating Oil 8-8
System Maintenance 8-8
Temperature Distribution System 8-9
Fan Speed Control (Mode Switch) 8-10
Face Level Temperature Differential 8-10
Temperature Rotary Control 8-10
Refrigeration Cycle 8-11
System Protection 8-12
General System Procedures 8-12
Leak Test 8-12
Charge Recovery (System Depressurisation) 8-12
Evacuating the System 8-13
Adding Compressor Lubricating Oil 8-13
Adding Refrigerant 8-14
Functional Check 8-15
System Trouble Shooting 8-1 7
Electronic Control Module (ECM) 8-19
In Car Controls 8-21
Temperature Demand Switch 8-21
Face Level Differential Controller 8-21
Air Conditioning Function Switch 8-22
Fan Speed Control Switch (Mode Switch) 8-23
Temperature Sensors 8-23
Evaporator Sensor 8-24
Motorised In-Car Aspirated Sensor 8-24
Water Temperature Switch 8-25
Blower Motors 8-25
Potentiometers 8-26
Servo Motors 8-27
Vacuum System 8-28
Pressure-Temperature Graphs 8-29
May 1996 8-1
Page 279 of 421
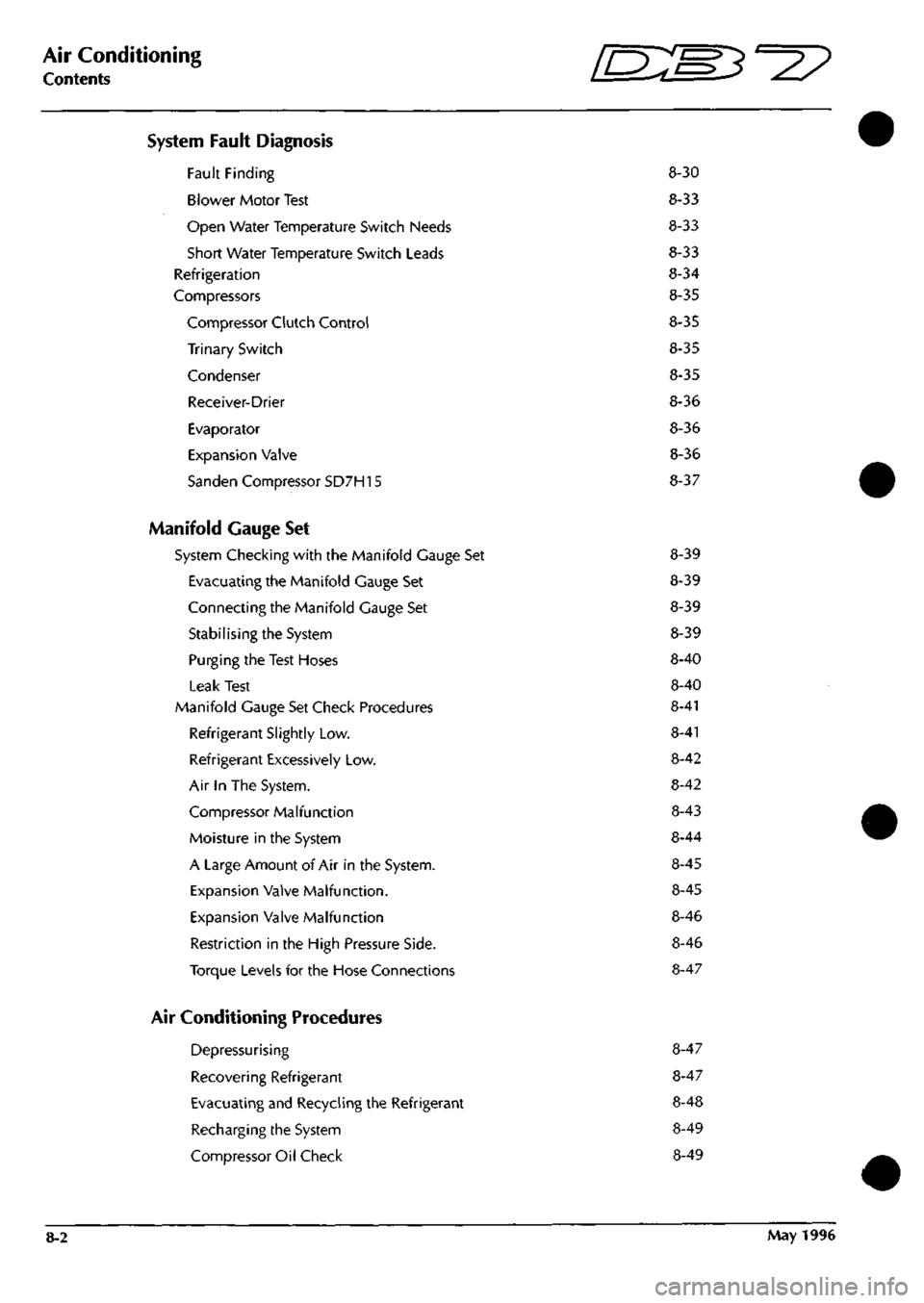
Air Conditioning
Contents '=2?
System Fault Diagnosis
Fault Finding
Blower Motor Test
Open Water Temperature Switch Needs
Short Water Temperature Switch Leads
Refrigeration
Compressors
Compressor Clutch Control
Trinary Switch
Condenser
Receiver-Drier
Evaporator
Expansion Valve
Sanden Compressor SD7H15
Manifold Gauge Set
System Checking with the Manifold Gauge Set
Evacuating the Manifold Gauge Set
Connecting the Manifold Gauge Set
Stabilising the System
Purging the Test Hoses
Leak Test
Manifold Gauge Set Check Procedures
Refrigerant Slightly Low.
Refrigerant Excessively Low.
Air In The System.
Compressor Malfunction
Moisture in the System
A Large Amount of Air in the System.
Expansion Valve Malfunction.
Expansion Valve Malfunction
Restriction in the High Pressure Side.
Torque Levels for the Hose Connections
8-30
8-33
8-33
8-33
8-34
8-35
8-35
8-35
8-35
8-36
8-36
8-36
8-37
8-39
8-39
8-39
8-39
8-40
8-40
8-41
8-41
8-42
8-42
8-43
8-44
8-45
8-45
8-46
8-46
8-47
Air Conditioning Procedures
Depressurising
Recovering Refrigerant
Evacuating and Recycling the Refrigerant
Recharging the System
Compressor Oil Check
8-47
8-47
8-48
8-49
8-49
8-2 May 1996
Page 280 of 421
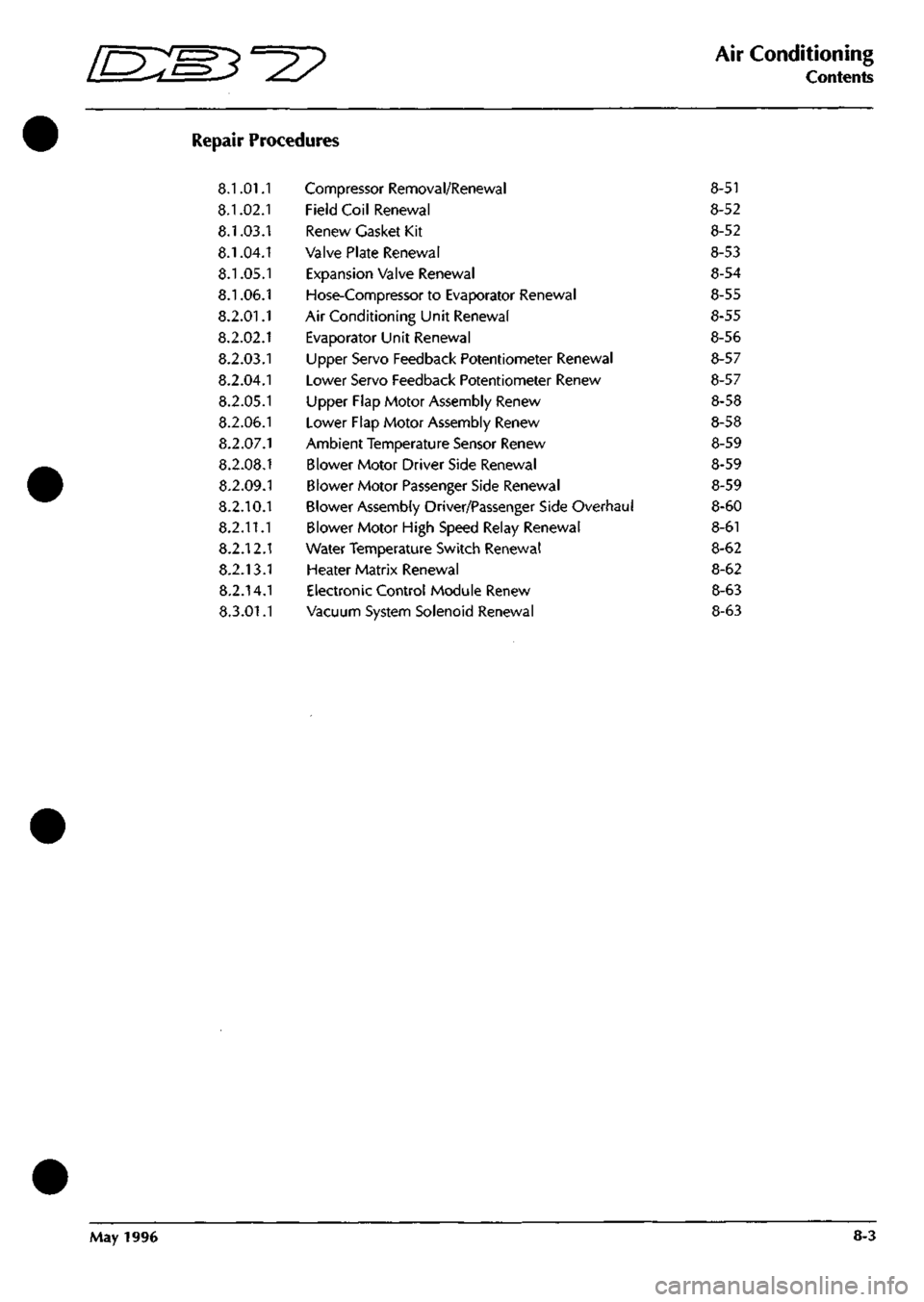
^7
Air Conditioning
Contents
Repair Procedures
8.1.01.1 Compressor Removal/Renewal 8-51
8.1.02.1 Field Coil Renewal 8-52
8.1.03.1 Renew Gasket Kit 8-52
8.1.04.1 Valve Plate Renewal 8-53
8.1.05.1 Expansion Valve Renewal 8-54
8.1.06.1 Hose-Compressor to Evaporator Renewal 8-55
8.2.01.1 Air Conditioning Unit Renewal 8-55
8.2.02.1 Evaporator Unit Renewal 8-56
8.2.03.1 Upper Servo Feedback Potentiometer Renewal 8-57
8.2.04.1 Lower Servo Feedback Potentiometer Renew 8-57
8.2.05.1 Upper Flap Motor Assembly Renew 8-58
8.2.06.1 Lower Flap Motor Assembly Renew 8-58
8.2.07.1 Ambient Temperature Sensor Renew 8-59
8.2.08.1 Blower Motor Driver Side Renewal 8-59
8.2.09.1 Blower Motor Passenger Side Renewal 8-59
8.2.10.1 Blower Assembly Driver/Passenger Side Overhaul 8-60
8.2.11.1 Blower Motor High Speed Relay Renewal 8-61
8.2.12.1 Water Temperature Switch Renewal 8-62
8.2.13.1 Heater Matrix Renewal 8-62
8.2.14.1 Electronic Control Module Renew 8-63
8.3.01.1 Vacuum System Solenoid Renewal 8-63
May 1996 8-3
Page 289 of 421
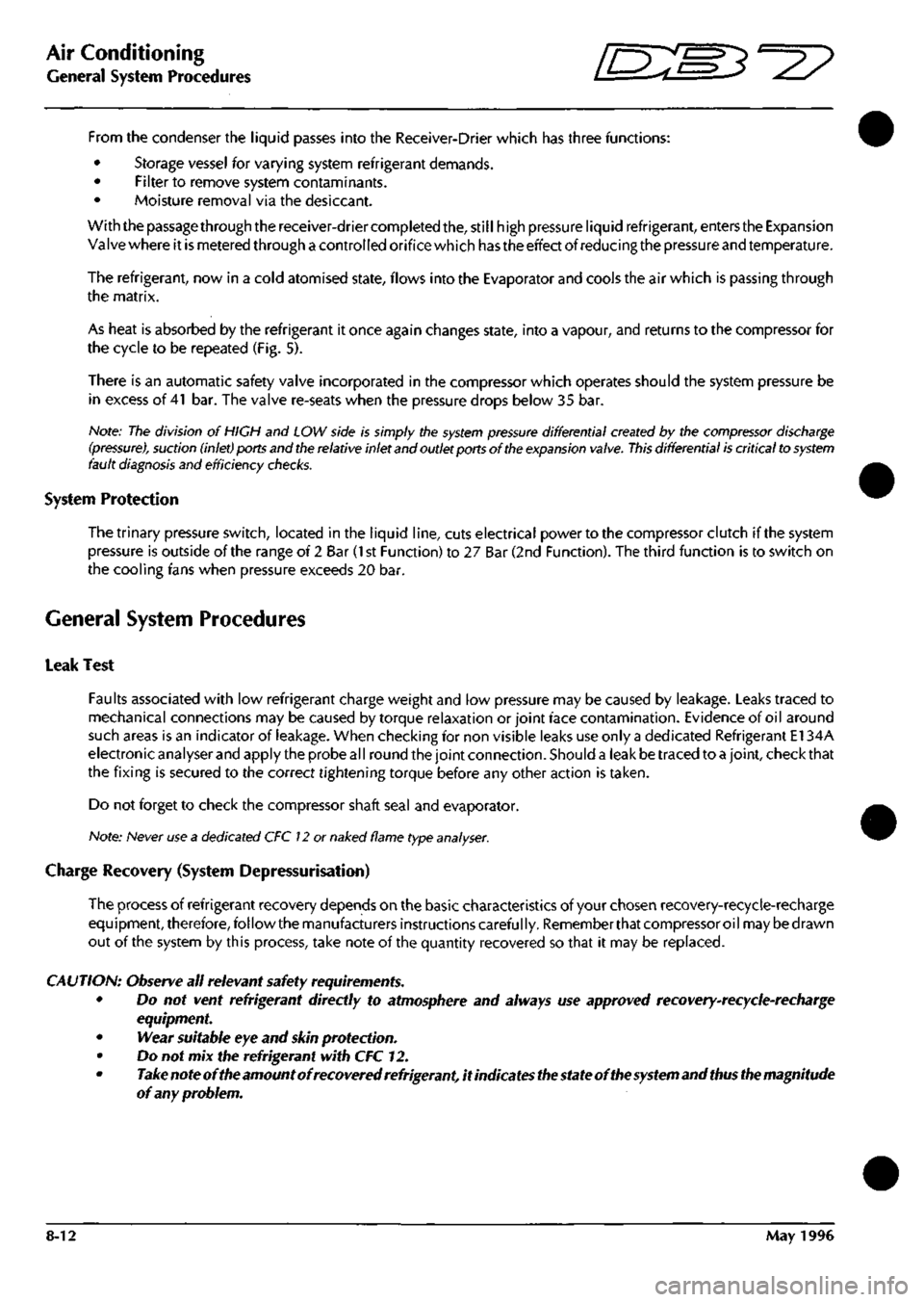
Air Conditioning //~-->> ^/zz:^^ • ^ ^
General Svstem Procedures ' —"^ ^ '^ General System Procedures
From the condenser the liquid passes into the Receiver-Drier which has three functions:
• Storage vessel for varying system refrigerant demands.
• Filter to remove system contaminants.
• Moisture removal via the desiccant.
With the passage through the receiver-drier completed the, still high pressure liquid refrigerant, enters the Expansion
Valve where it is metered through a controlled orifice which has the effect of reducing the pressure and temperature.
The refrigerant, now in a cold atomised state, flows into the Evaporator and cools the air which is passing through
the matrix.
As heat is absorbed by the refrigerant it once again changes state, into a vapour, and returns to the compressor for
the cycle to be repeated (Fig. 5).
There is an automatic safety valve incorporated in the compressor which operates should the system pressure be
in excess of
41
bar. The valve re-seats when the pressure drops below 35 bar.
Note: The division of HIGH and LOW side is simply the
system pressure
differential created by the
compressor
discharge
(pressure),
suction
(inlet)
ports and
the
relative inlet and outlet
ports
of the
expansion
valve.
This
differential is critical to
system
fault
diagnosis
and efficiency checks.
System Protection
The trinary pressure switch, located in the liquid line, cuts electrical power to the compressor clutch if the system
pressure is outside of the range of 2 Bar
(1
st Function) to 27 Bar (2nd Function). The third function is to switch on
the cooling fans when pressure exceeds 20 bar.
General System Procedures
Leak Test
Faults associated with low refrigerant charge weight and low pressure may be caused by leakage. Leaks traced to
mechanical connections may be caused by torque relaxation or joint face contamination. Evidence of oil around
such areas is an indicator of leakage. When checking for non visible leaks use only a dedicated Refrigerant El 34A
electronic analyser and apply the probe all round the joint connection. Should a leak be traced to a joint, check that
the fixing is secured to the correct tightening torque before any other action is taken.
Do not forget to check the compressor shaft seal and evaporator.
Note: Never
use
a dedicated
CFC 12
or
naiced
flame type
analyser.
Charge Recovery (System Depressurisation)
The process of refrigerant recovery depends on the basic characteristics of your chosen recovery-recycle-recharge
equipment, therefore, follow the manufacturers instructions carefully. Remember that compressor oil may be drawn
out of the system by this process, take note of the quantity recovered so that it may be replaced.
CAUTION: Observe all relevant safety requirements.
• Do not vent refrigerant directly to atmosphere and always use approved recovery-recycle-recharge
equipment.
• Wear suitable eye and skin protection.
• Do not mix the refrigerant with CFC 12.
• Take note of the amount of recovered refrigerant, it indica
tes the
state of the
system
and
thus the
magnitude
of any problem.
8-12 May 1996
Page 294 of 421
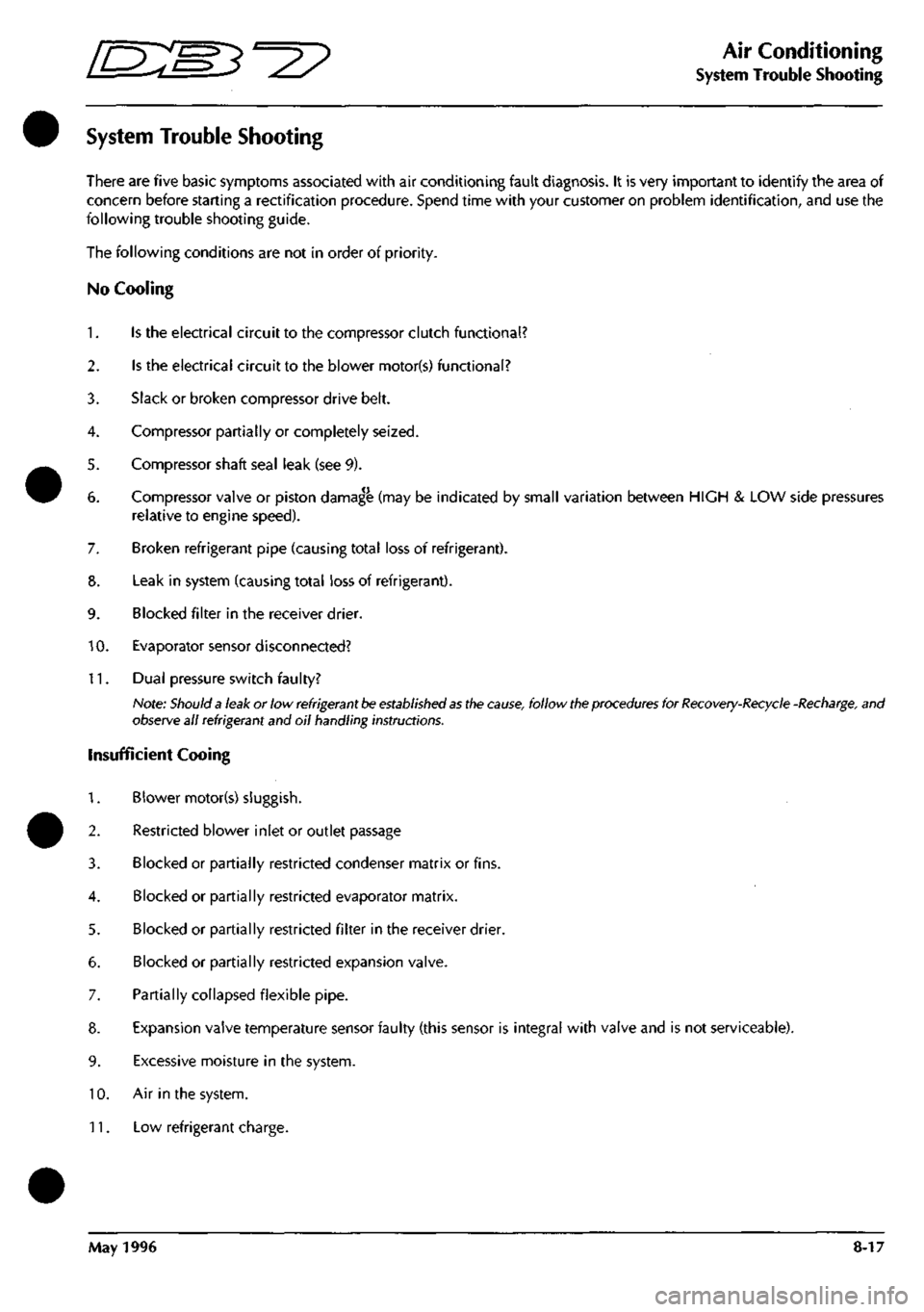
^=2?
Air Conditioning
System Trouble Shooting
System Trouble Shooting
There are five basic symptoms associated with air conditioning fault diagnosis. It is very important to identify the area of
concern before starting a rectification procedure. Spend time with your customer on problem identification, and use the
following trouble shooting guide.
The following conditions are not in order of priority.
No Cooling
1.
Is the electrical circuit to the compressor clutch functional?
2.
Is the electrical circuit to the blower motor(s) functional?
3. Slack or broken compressor drive belt.
4.
Compressor partially or completely seized.
5. Compressor shaft seal leak (see 9).
6. Compressor valve or piston damag^ (may be indicated by small variation between HIGH & LOW side pressures
relative to engine speed).
7. Broken refrigerant pipe (causing total loss of refrigerant).
8. Leak in system (causing total loss of refrigerant).
9. Blocked filter in the receiver drier.
10.
Evaporator sensor disconnected?
11.
Dual pressure switch faulty?
Note:
Should a
leak or low
refrigerant be established as
the
cause,
follow
the procedures
for
Recovery-Recycle
-Recharge,
and
observe all refrigerant and oil handling instructions.
insufficient Cooing
1.
Blower motor(s) sluggish.
2.
Restricted blower inlet or outlet passage
3. Blocked or partially restricted condenser matrix or fins.
4.
Blocked or partially restricted evaporator matrix.
5. Blocked or partially restricted filter in the receiver drier.
6. Blocked or partially restricted expansion valve.
7. Partially collapsed flexible pipe.
8. Expansion valve temperature sensor faulty (this sensor is integral with valve and is not serviceable).
9. Excessive moisture in the system.
10.
Air in the system.
11.
Low refrigerant charge.
May 1996 8-17
Page 295 of 421
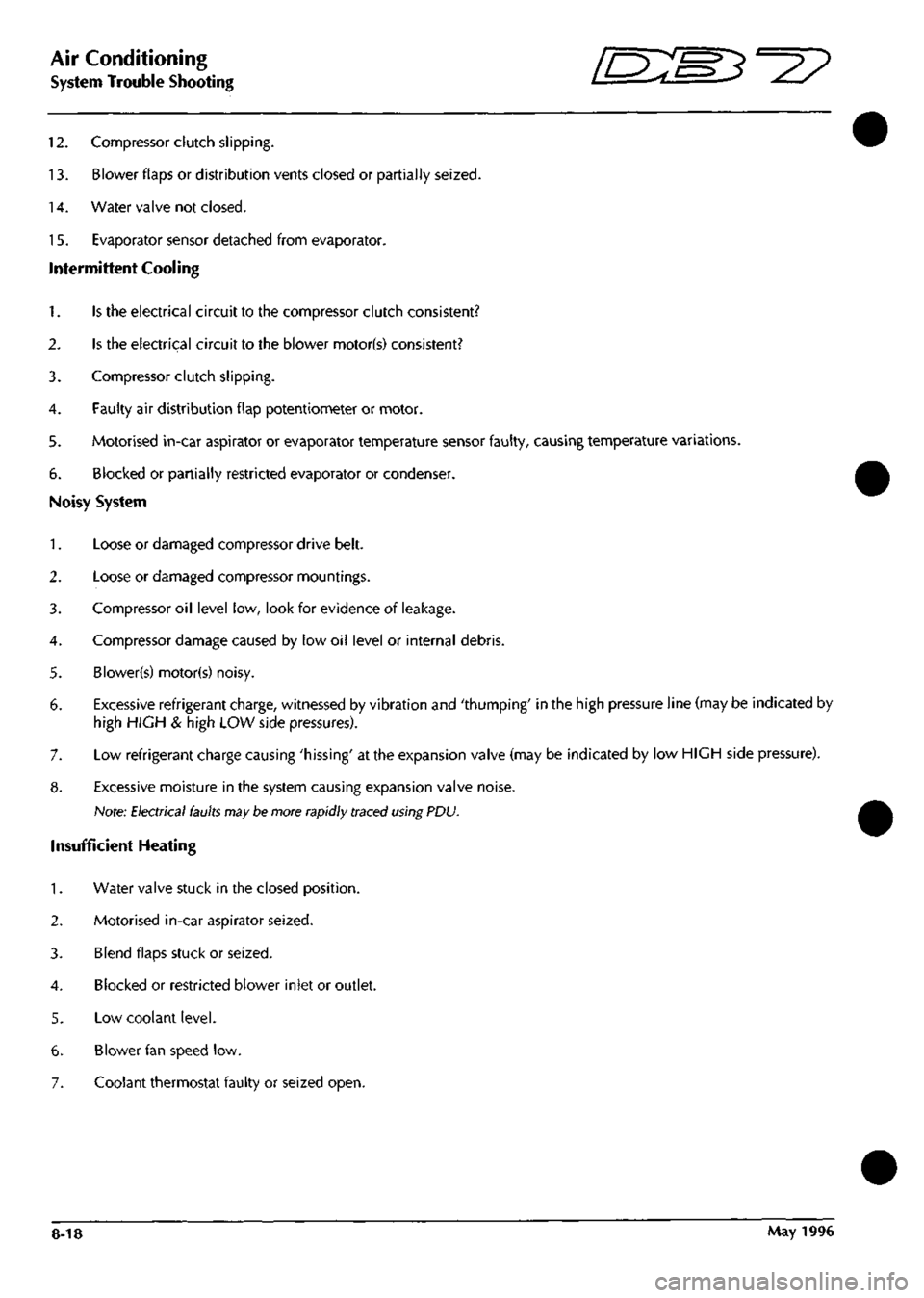
Air Conditioning
/J=y>f^^^
—p )
System Trouble Shooting
12.
Compressor clutch slipping.
13.
Blower flaps or distribution vents closed or partially seized.
14.
Water valve not closed.
15.
Evaporator sensor detached from evaporator.
Intermittent Cooling
Is the electrical circuit to the compressor clutch consistent?
2.
Is the electrical circuit to the blower motor(s) consistent?
3. Compressor clutch slipping.
4.
Faulty air distribution flap potentiometer or motor.
5. Motorised in-car aspirator or evaporator temperature sensor faulty, causing temperature variations.
6. Blocked or partially restricted evaporator or condenser.
Noisy System
1.
Loose or damaged compressor drive belt.
2.
Loose or damaged compressor mountings.
3. Compressor oil level low, look for evidence of leakage.
4.
Compressor damage caused by low oil level or internal debris.
5. Blower(s) motor(s) noisy.
6. Excessive refrigerant charge, witnessed by vibration and 'thumping' in the high pressure line (may be indicated by
high HIGH & high LOW side pressures).
7. Low refrigerant charge causing 'hissing' at the expansion valve (may be indicated by low HIGH side pressure).
8. Excessive moisture in the system causing expansion valve noise.
Note;
Electrical faults
may
be more rapidly traced using PDU.
Insufficient Heating
1.
Water valve stuck in the closed position.
2.
Motorised in-car aspirator seized.
3. Blend flaps stuck or seized.
4.
Blocked or restricted blower inlet or outlet.
5. Low coolant level.
6. Blower fan speed low.
7. Coolant thermostat faulty or seized open.
8-18 May 1996
Page 311 of 421
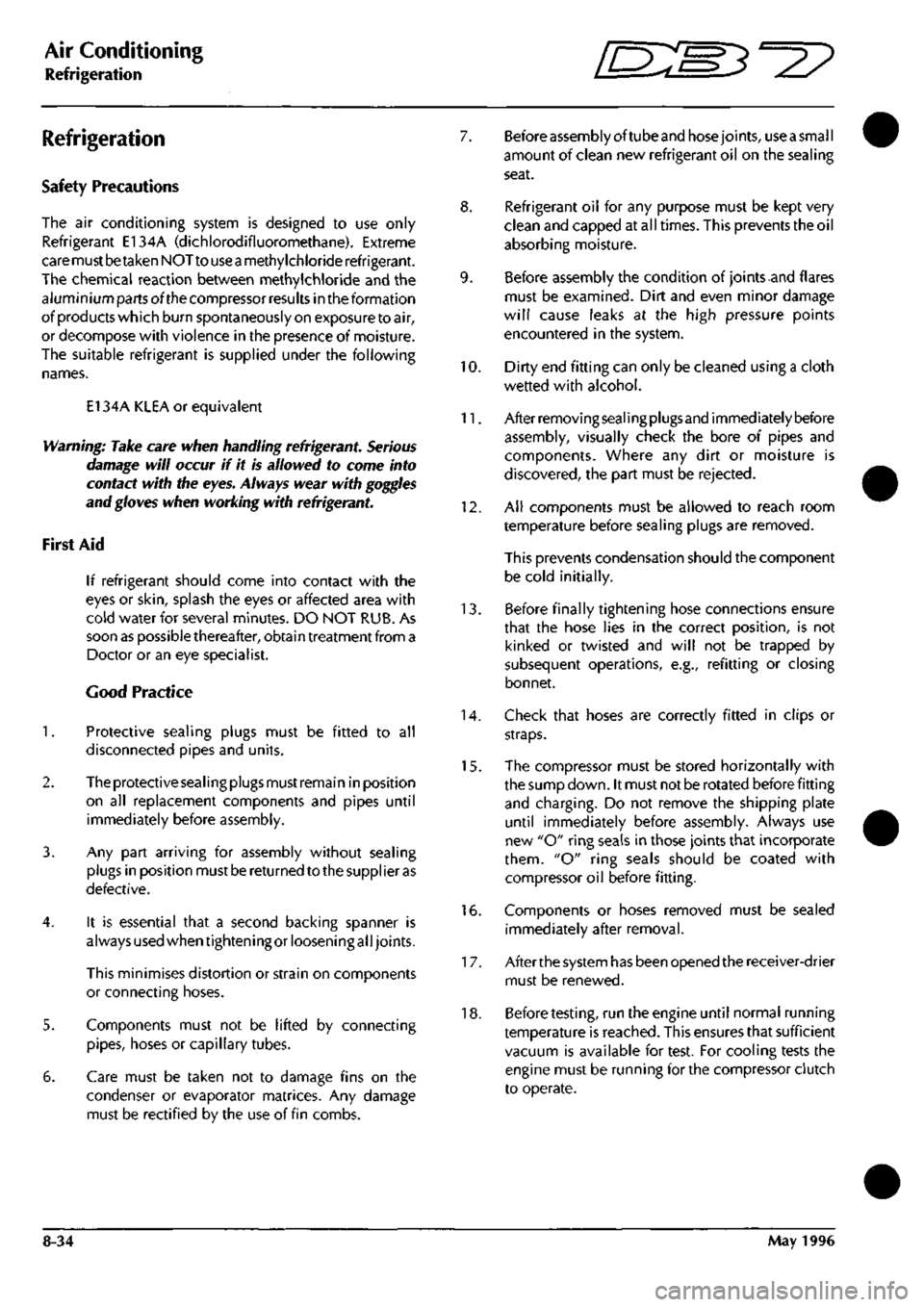
Air Conditioning
Refrigeration /s:s^°27
Refrigeration
Safety Precautions
The air conditioning system is designed to use only
Refrigerant E134A (dichlorodifluoromethane). Extreme
care must betaken NOT to use
a
methylchloride refrigerant.
The chemical reaction between methylchloride and the
aluminium parts ofthe compressor results in the formation
ofproductswhich burn spontaneously on exposure toair,
or decompose with violence in the presence of moisture.
The suitable refrigerant is supplied under the following
names.
El 34A KLEA or equivalent
Warning: Take care when handling refrigerant. Serious
damage will occur if it is allowed to come into
contact with the eyes. Always wear with goggles
and gloves when working with refrigerant
First Aid
If refrigerant should come into contact with the
eyes or
skin,
splash the eyes or affected area with
cold water for several minutes. DO NOT RUB. As
soon as possible thereafter, obtain treatment from a
Doctor or an eye specialist.
Good Practice
1.
Protective sealing plugs must be fitted to all
disconnected pipes and units.
2.
Theprotectivesealingpiugsmustremain inposition
on ail replacement components and pipes until
immediately before assembly.
3. Any part arriving for assembly without sealing
plugs in position must be returned to the supplier as
defective.
4.
It is essential that a second backing spanner is
always used when tightening or loosening all joints.
This minimises distortion or strain on components
or connecting hoses.
5. Components must not be lifted by connecting
pipes,
hoses or capillary tubes.
6. Care must be taken not to damage fins on the
condenser or evaporator matrices. Any damage
must be rectified by the use of fin combs.
7. Before assembly oftube and hosejoints, use
a
small
amount of clean new refrigerant oil on the sealing
seat.
8. Refrigerant oil for any purpose must be kept very
clean and capped at all times. This prevents the oil
absorbing moisture.
9. Before assembly the condition of joints and flares
must be examined. Dirt and even minor damage
will cause leaks at the high pressure points
encountered in the system.
10.
Dirty end fitting can only be cleaned using a cloth
wetted with alcohol.
11.
Afterremovingsealingplugsand immediatelybefore
assembly, visually check the bore of pipes and
components. Where any dirt or moisture is
discovered,
the part must be rejected.
12. Ail components must be allowed to reach room
temperature before sealing plugs are removed.
This prevents condensation should the component
be cold initially.
13.
Before finally tightening hose connections ensure
that the hose lies in the correct position, is not
kinked or twisted and will not be trapped by
subsequent operations, e.g., refitting or closing
bonnet.
14.
Check that hoses are correctly fitted in clips or
straps.
15.
The compressor must be stored horizontally with
the sump down. It must not be rotated before fitting
and charging. Do not remove the shipping plate
until immediately before assembly. Always use
new "O" ring seals in those joints that incorporate
them.
"O" ring seals should be coated with
compressor oil before fitting.
16.
Components or hoses removed must be sealed
immediately after removal.
1 7. Afterthe system has been opened the receiver-drier
must be renewed.
18.
Before
testing,
run the engine until normal running
temperature is reached. This ensures that sufficient
vacuum is available for test. For cooling tests the
engine must be running for the compressor clutch
to operate.
8-34 May 1996
Page 313 of 421
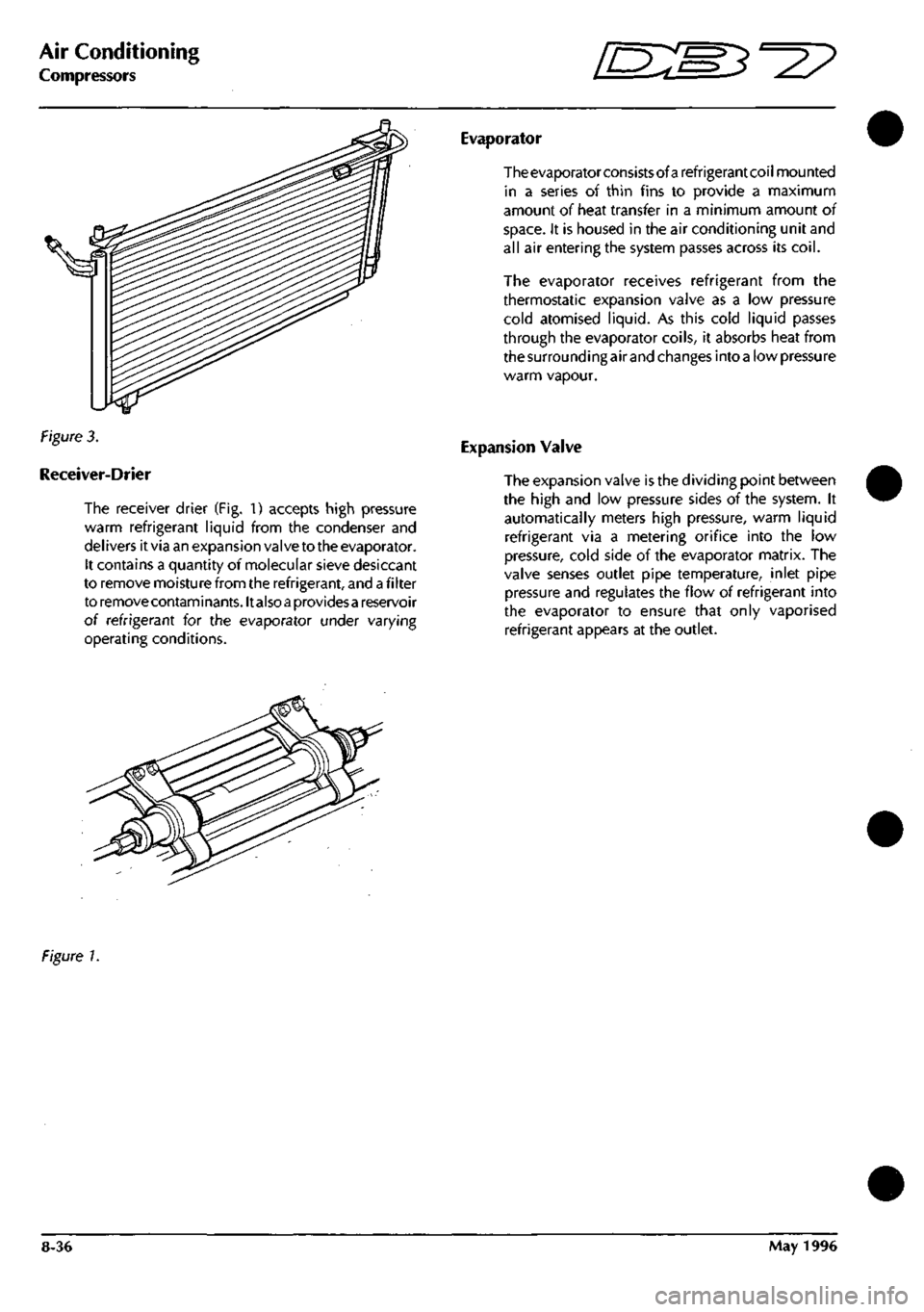
Air Conditioning
Compressors ^?
Evaporator
Figure 3.
Receiver-Drier
The receiver drier (Fig. 1) accepts high pressure
warm refrigerant liquid from the condenser and
del ivers it via an expansion valve to the evaporator.
It contains a quantity of molecular sieve desiccant
to remove moisture from the refrigerant, and
a
fi Iter
to removecontaminants.lt also
a
providesa reservoir
of refrigerant for the evaporator under varying
operating conditions.
The evaporator consists of a refrigerant coil mounted
in a series of thin fins to provide a maximum
amount of heat transfer in a minimum amount of
space.
It is housed in the air conditioning unit and
all air entering the system passes across its
coil.
The evaporator receives refrigerant from the
thermostatic expansion valve as a low pressure
cold atomised liquid. As this cold liquid passes
through the evaporator coils, it absorbs heat from
the surrounding air and changes into
a
low pressure
warm vapour.
Expansion Valve
The expansion valve is the dividing point between
the high and low pressure sides of the system. It
automatically meters high pressure, warm liquid
refrigerant via a metering orifice into the low
pressure, cold side of the evaporator matrix. The
valve senses outlet pipe temperature, inlet pipe
pressure and regulates the flow of refrigerant into
the evaporator to ensure that only vaporised
refrigerant appears at the outlet.
Figure 1.
8-36 May 1996