charging ASTON MARTIN V8 VANTAGE 2010 Owner's Manual
[x] Cancel search | Manufacturer: ASTON MARTIN, Model Year: 2010, Model line: V8 VANTAGE, Model: ASTON MARTIN V8 VANTAGE 2010Pages: 947, PDF Size: 43.21 MB
Page 644 of 947
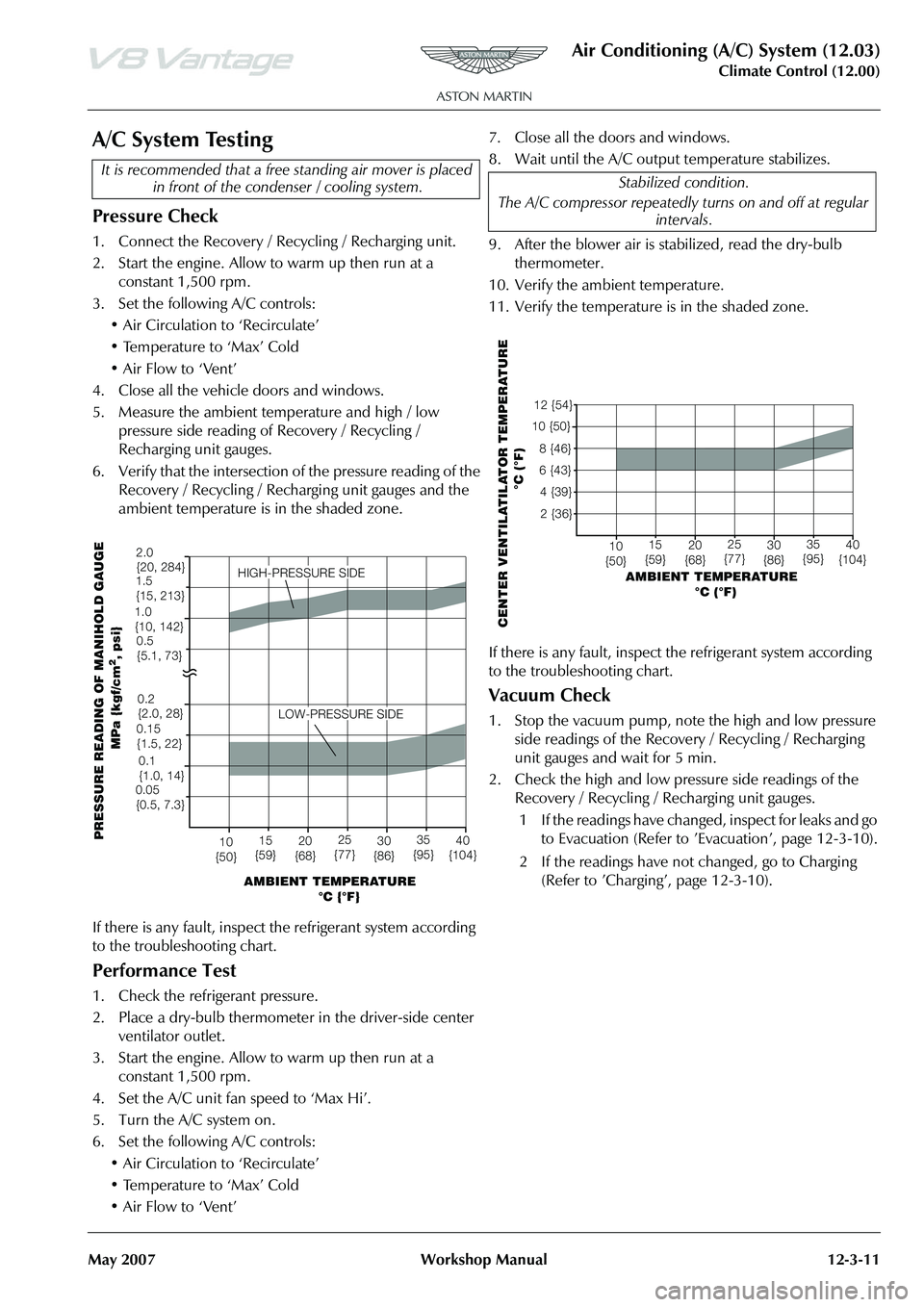
Air Conditioning (A/C) System (12.03)
Climate Control (12.00)
May 2007 Workshop Manual 12-3-11
A/C System Testing
Pressure Check
1. Connect the Recovery / Recycling / Recharging unit.
2. Start the engine. Allow to warm up then run at a constant 1,500 rpm.
3. Set the following A/C controls:
• Air Circulation to ‘Recirculate’
• Temperature to ‘Max’ Cold
• Air Flow to ‘Vent’
4. Close all the vehicle doors and windows.
5. Measure the ambient temperature and high / low pressure side reading of Recovery / Recycling /
Recharging unit gauges.
6. Verify that the intersection of the pressure reading of the Recovery / Recycling / Recharging unit gauges and the
ambient temperature is in the shaded zone.
If there is any fault, inspect the refrigerant system according
to the troubleshooting chart.
Performance Test
1. Check the refrigerant pressure.
2. Place a dry-bulb thermometer in the driver-side center ventilator outlet.
3. Start the engine. Allow to warm up then run at a constant 1,500 rpm.
4. Set the A/C unit fan speed to ‘Max Hi’.
5. Turn the A/C system on.
6. Set the following A/C controls: • Air Circulation to ‘Recirculate’
• Temperature to ‘Max’ Cold
• Air Flow to ‘Vent’ 7. Close all the doors and windows.
8. Wait until the A/C output temperature stabilizes.
9. After the blower air is stabilized, read the dry-bulb
thermometer.
10. Verify the ambient temperature.
11. Verify the temperature is in the shaded zone.
If there is any fault, inspect the refrigerant system according
to the troubleshooting chart.
Vacuum Check
1. Stop the vacuum pump, note the high and low pressure side readings of the Recovery / Recycling / Recharging
unit gauges and wait for 5 min.
2. Check the high and low pressure side readings of the Recovery / Recycling / Recharging unit gauges.
1 If the readings have changed, inspect for leaks and go to Evacuation (Refer to ’E vacuation’, page 12-3-10).
2 If the readings have not changed, go to Charging (Refer to ’Charging’, page 12-3-10).
It is recommended th
at a free standing air mover is placed
in front of the conden ser / cooling system.
AMBIENT TEMPERATURE
°C {°F}
10
{50} 15
{59} 20
{68} 25
{77} 30
{86} 35
{95} 40
{104}
LOW-PRESSURE SIDE
HIGH-PRESSURE SIDE
PRESSURE READING OF MANIHOLD GAUGE
MPa {kgf/cm
2, psi}
2.0
{20, 284}
1.5
{15, 213}
1.0
{10, 142}
0.2
{2.0, 28}0.1
{1.0, 14}
0.15
{1.5, 22}
0.05
{0.5, 7.3} 0.5
{5.1, 73}
Stabilized condition.
The A/C compressor repeatedly turns on and off at regular intervals.
AMBIENT TEMPERATURE
°C (°F)
CENTER VENTILATILATOR TEMPERATURE
°C (°F)
12 {54}
10 {50}
8 {46}
6 {43}4 {39} 2 {36}
10
{50} 15
{59} 20
{68} 25
{77} 30
{86} 35
{95} 40
{104}
Page 645 of 947
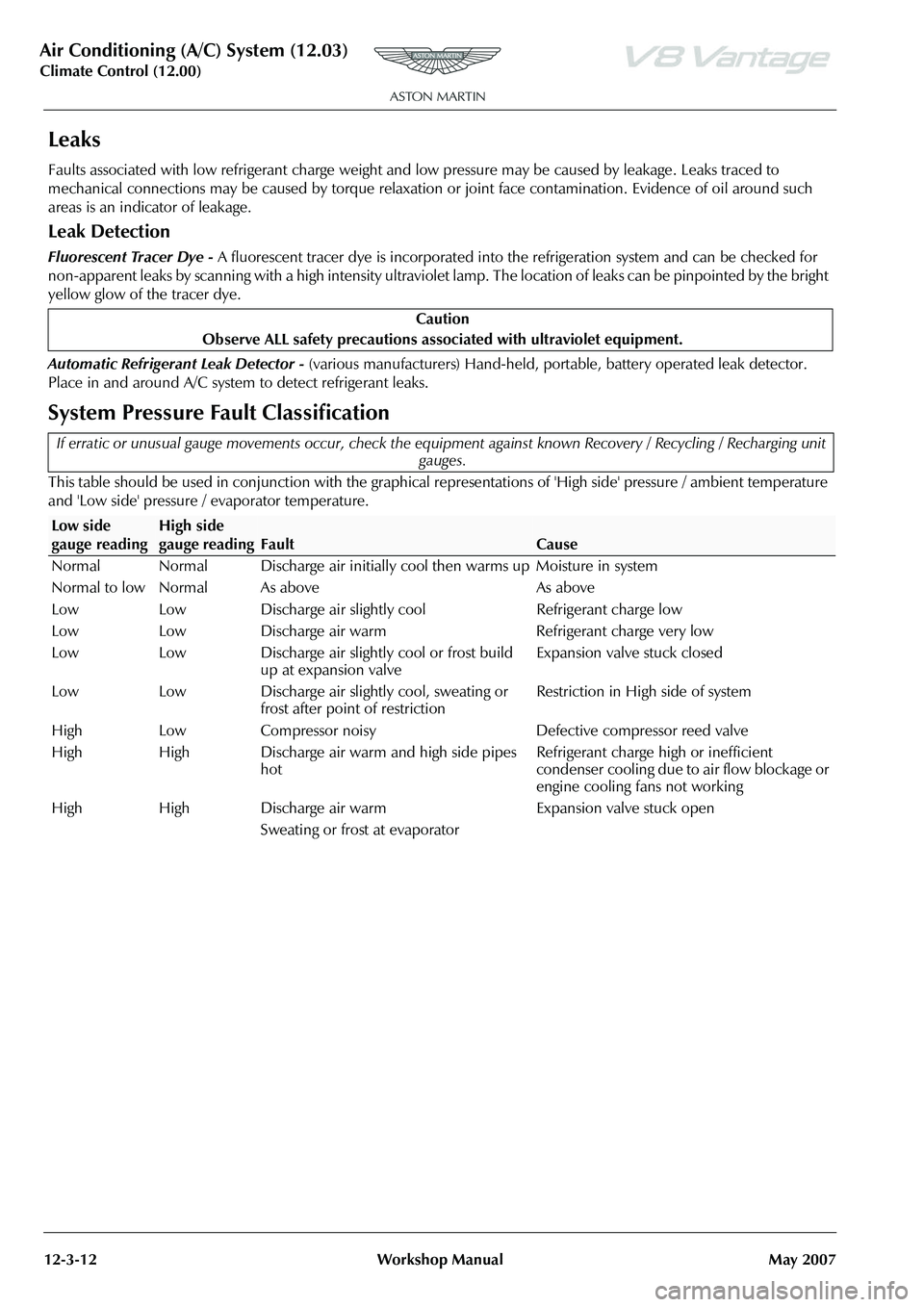
Air Conditioning (A/C) System (12.03)
Climate Control (12.00)
12-3-12 Workshop Manual May 2007
Leaks
Faults associated with low refrigerant charge weight and low pressure may be caused by leakage. Leaks traced to
mechanical connections may be caused by torque relaxation or joint face contamination. Evidence of oil around such
areas is an indicator of leakage.
Leak Detection
Fluorescent Tracer Dye - A fluorescent tracer dye is incorporated into th e refrigeration system and can be checked for
non-apparent leaks by scanning with a high intensity ultraviolet lamp. The location of leaks can be pinpointed by the bright
yellow glow of the tracer dye.
Automatic Refrigerant Leak Detector - (various manufacturers) Hand-held, portable, battery operated leak detector.
Place in and around A/C system to detect refrigerant leaks.
System Pressure Fault Classification
This table should be used in conjunction with the graphical representations of 'High side' pressure / ambient temperature
and 'Low side' pressure / evaporator temperature. Caution
Observe ALL safety precautions associ ated with ultraviolet equipment.
If erratic or unusual gauge movements occur, check the equipment against known Recovery / Recycling / Recharging unit
gauges.
Low side
gauge readingHigh side
gauge reading
Fault
Cause
Normal Normal Discharge air initially c ool then warms up Moisture in system
Normal to low Normal As above As above
Low Low Discharge air slightly cool Refrigerant charge low
Low Low Discharge air warm Refrigerant charge very low
Low Low Discharge air slightly cool or frost build up at expansion valve Expansion valve stuck closed
Low Low Discharge air slightly cool, sweating or frost after point of restriction Restriction in High side of system
High Low Compressor noisy Defective compressor reed valve
High High Discharge air warm and high side pipes hot Refrigerant charge high or inefficient
condenser cooling due to air flow blockage or
engine cooling fans not working
High High Discharge air warm
Sweating or frost at evaporator Expansion valve stuck open
Page 654 of 947
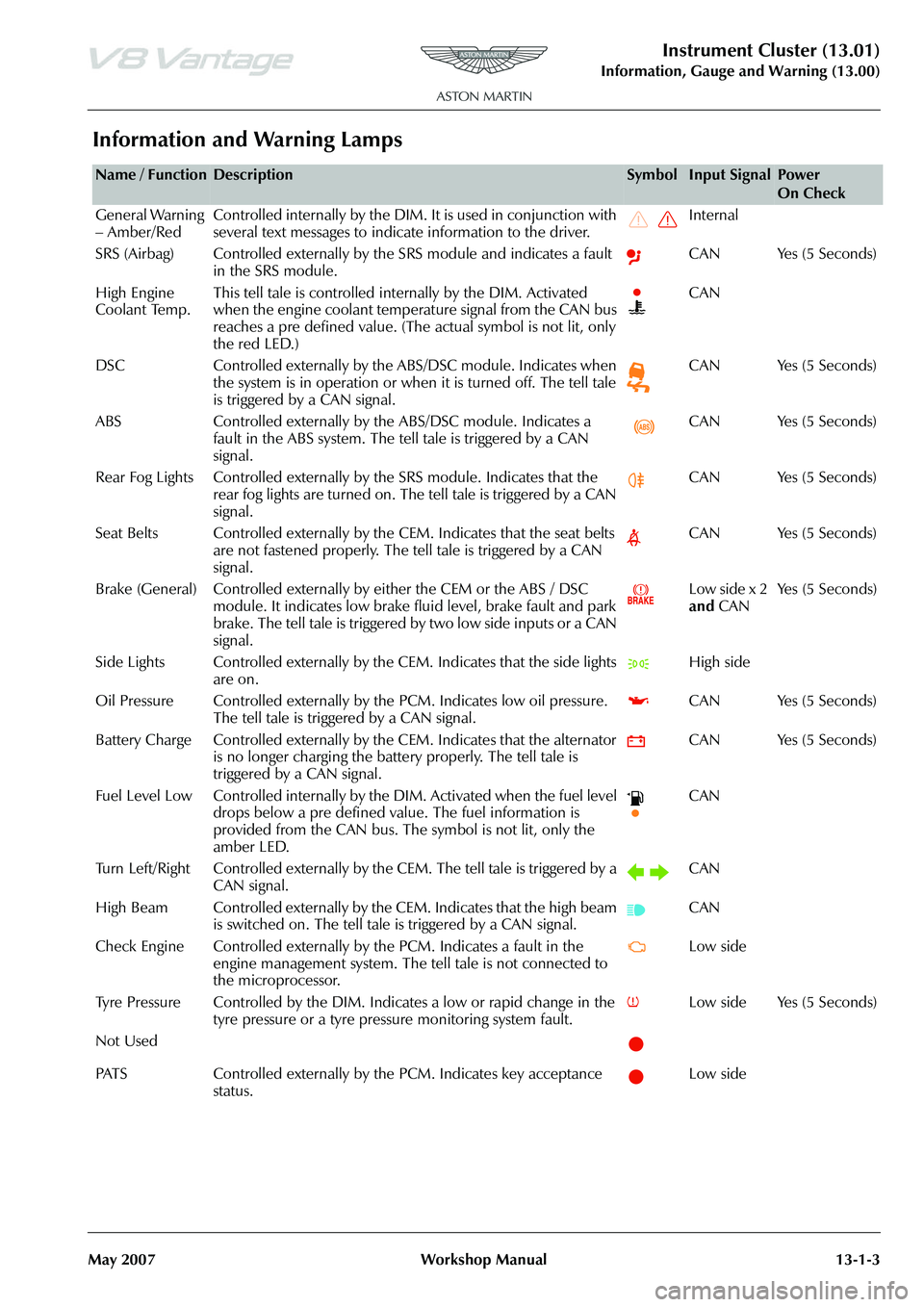
Instrument Cluster (13.01)
Information, Gauge and Warning (13.00)
May 2007 Workshop Manual 13-1-3
Information and Warning Lamps
Name / FunctionDescriptionSymbolInput SignalPower
On Check
General Warning
– Amber/Red Controlled internally by the DIM. It is used in conjunction with
several text messages to indicate information to the driver. Internal
SRS (Airbag) Controlled externally by the SRS module and indicates a fault in the SRS module. CAN Yes (5 Seconds)
High Engine
Coolant Temp. This tell tale is controlled internally by the DIM. Activated
when the engine coolant temperature signal from the CAN bus
reaches a pre defined value. (The
actual symbol is not lit, only
the red LED.) CAN
DSC Controlled externally by the ABS/DSC module. Indicates when the system is in operation or when it is turned off. The tell tale
is triggered by a CAN signal. CAN Yes (5 Seconds)
ABS Controlled externally by th e ABS/DSC module. Indicates a
fault in the ABS system. The tell tale is triggered by a CAN
signal. CAN Yes (5 Seconds)
Rear Fog Lights Controlled externally by the SRS module. Indicates that the
rear fog lights are turned on. The tell tale is triggered by a CAN
signal. CAN Yes (5 Seconds)
Seat Belts Controlled externally by the CEM. Indicates that the seat belts are not fastened properly. The tell tale is triggered by a CAN
signal. CAN Yes (5 Seconds)
Brake (General) Controlled externally by either the CEM or the ABS / DSC module. It indicates low brake fluid level, brake fault and park
brake. The tell tale is triggered by two low side inputs or a CAN
signal. Low side x 2
and
CAN Ye s ( 5 S e c o n d s )
Side Lights Controlled externally by th e CEM. Indicates that the side lights
are on. High side
Oil Pressure Controlled exte rnally by the PCM. Indicates low oil pressure.
The tell tale is triggered by a CAN signal. CAN Yes (5 Seconds)
Battery Charge Controlled externally by th e CEM. Indicates that the alternator
is no longer charging the battery properly. The tell tale is
triggered by a CAN signal. CAN Yes (5 Seconds)
Fuel Level Low Controlled internally by the DIM. Activated when the fuel level drops below a pre defined value. The fuel information is
provided from the CAN bus. The symbol is not lit, only the
amber LED. CAN
Turn Left/Right Controlled externally by th e CEM. The tell tale is triggered by a
CAN signal. CAN
High Beam Controlled externally by the CEM. Indicates that the high beam is switched on. The tell tale is triggered by a CAN signal. CAN
Check Engine Controlled externally by the PCM. Indicates a fault in the engine management system. The te ll tale is not connected to
the microprocessor. Low side
Tyre Pressure Controlled by the DIM. In dicates a low or rapid change in the
tyre pressure or a tyre pressure monitoring system fault. Low side Yes (5 Seconds)
Not Used
PATS Controlled externally by the PCM. Indicates key acceptance status. Low side
Page 656 of 947
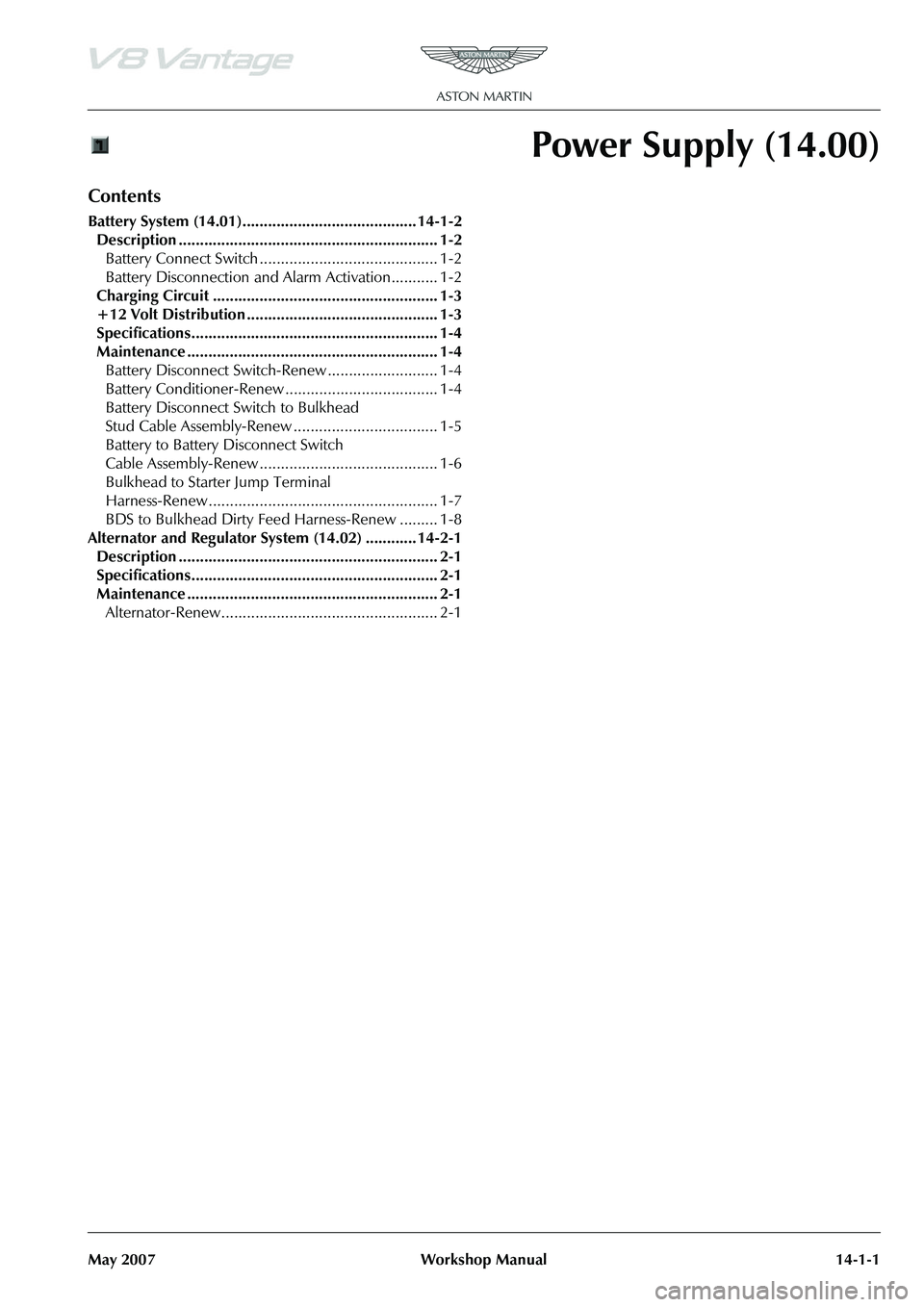
May 2007 Workshop Manual 14-1-1
Power Supply (14.00)
Contents
Battery System (14.01)......................................... 14-1-2Description ............................................................. 1-2 Battery Connect Switch .......................................... 1-2
Battery Disconnection and Alarm Activation........... 1-2
Charging Circuit ..................................................... 1-3
+12 Volt Distribution ............................................. 1-3
Specifications.......................................................... 1-4
Maintenance ........................................................... 1-4 Battery Disconnect Switch-Renew .......................... 1-4
Battery Conditioner-Renew .................................... 1-4
Battery Disconnect Switch to Bulkhead
Stud Cable Assembly-Renew .................................. 1-5
Battery to Battery Disconnect Switch
Cable Assembly-Renew .......................................... 1-6
Bulkhead to Starter Jump Terminal
Harness-Renew ...................................................... 1-7
BDS to Bulkhead Dirty Feed Harness-Renew ......... 1-8
Alternator and Regulator System (14.02) ............ 14-2-1 Description ............................................................. 2-1
Specifications.......................................................... 2-1
Maintenance ........................................................... 2-1 Alternator-Renew................................................... 2-1
Page 658 of 947
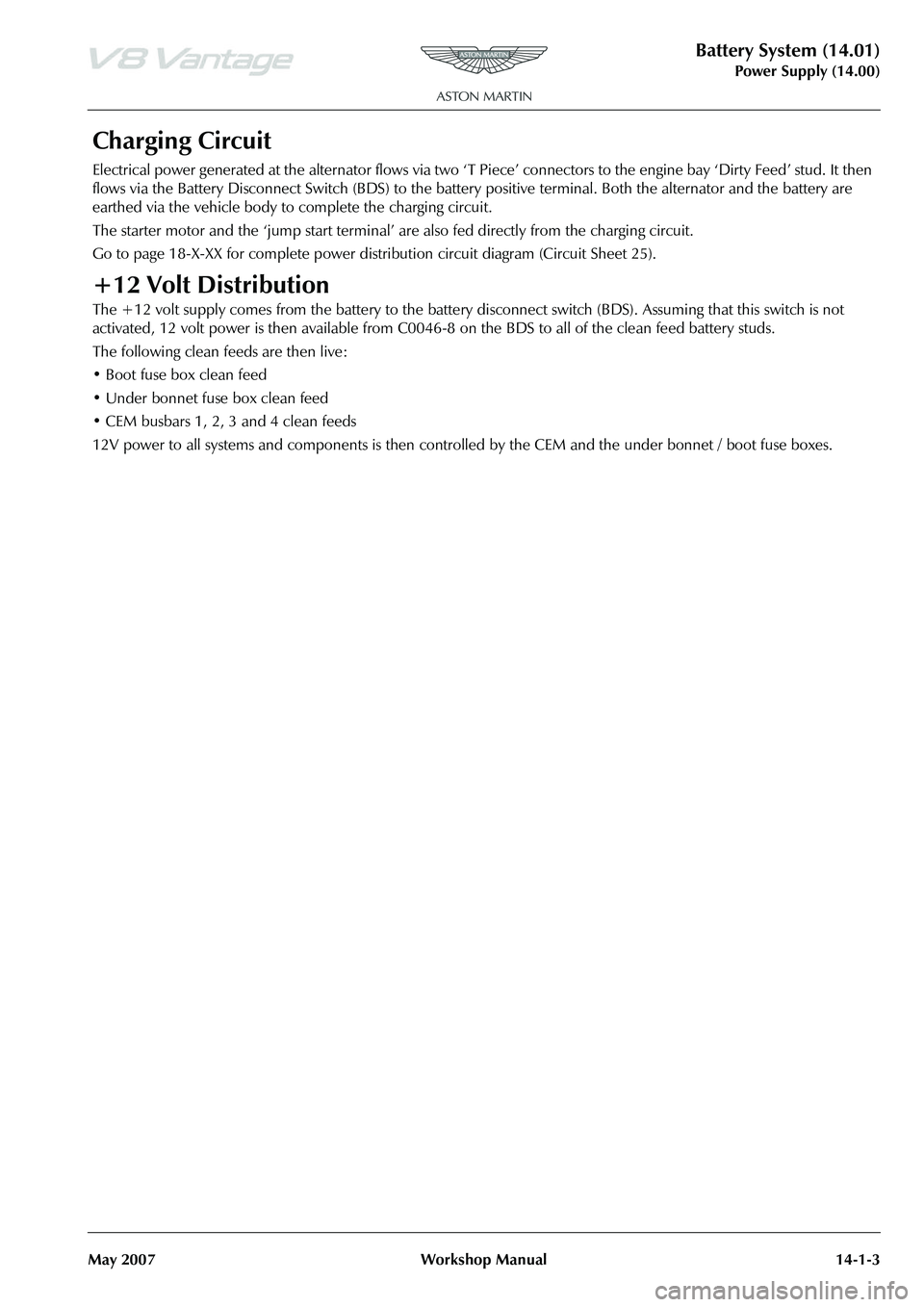
Battery System (14.01)
Power Supply (14.00)
May 2007 Workshop Manual 14-1-3
Charging Circuit
Electrical power generated at the alternator flows via two ‘T Pi ece’ connectors to the engine bay ‘Dirty Feed’ stud. It then
flows via the Battery Disconnect Switch (BDS) to the battery positive terminal. Both the alternator and the battery are
earthed via the vehicle body to complete the charging circuit.
The starter motor and the ‘jump start terminal’ ar e also fed directly from the charging circuit.
Go to page 18-X-XX for complete power dist ribution circuit diagram (Circuit Sheet 25).
+12 Volt Distribution
The +12 volt supply comes from the battery to the battery disc onnect switch (BDS). Assuming that this switch is not
activated, 12 volt power is then available from C0046-8 on the BDS to all of the clean feed battery studs.
The following clean feeds are then live:
• Boot fuse box clean feed
• Under bonnet fuse box clean feed
• CEM busbars 1, 2, 3 and 4 clean feeds
12V power to all systems and components is then controlled by the CEM and the under bonnet / boot fuse boxes.
Page 666 of 947
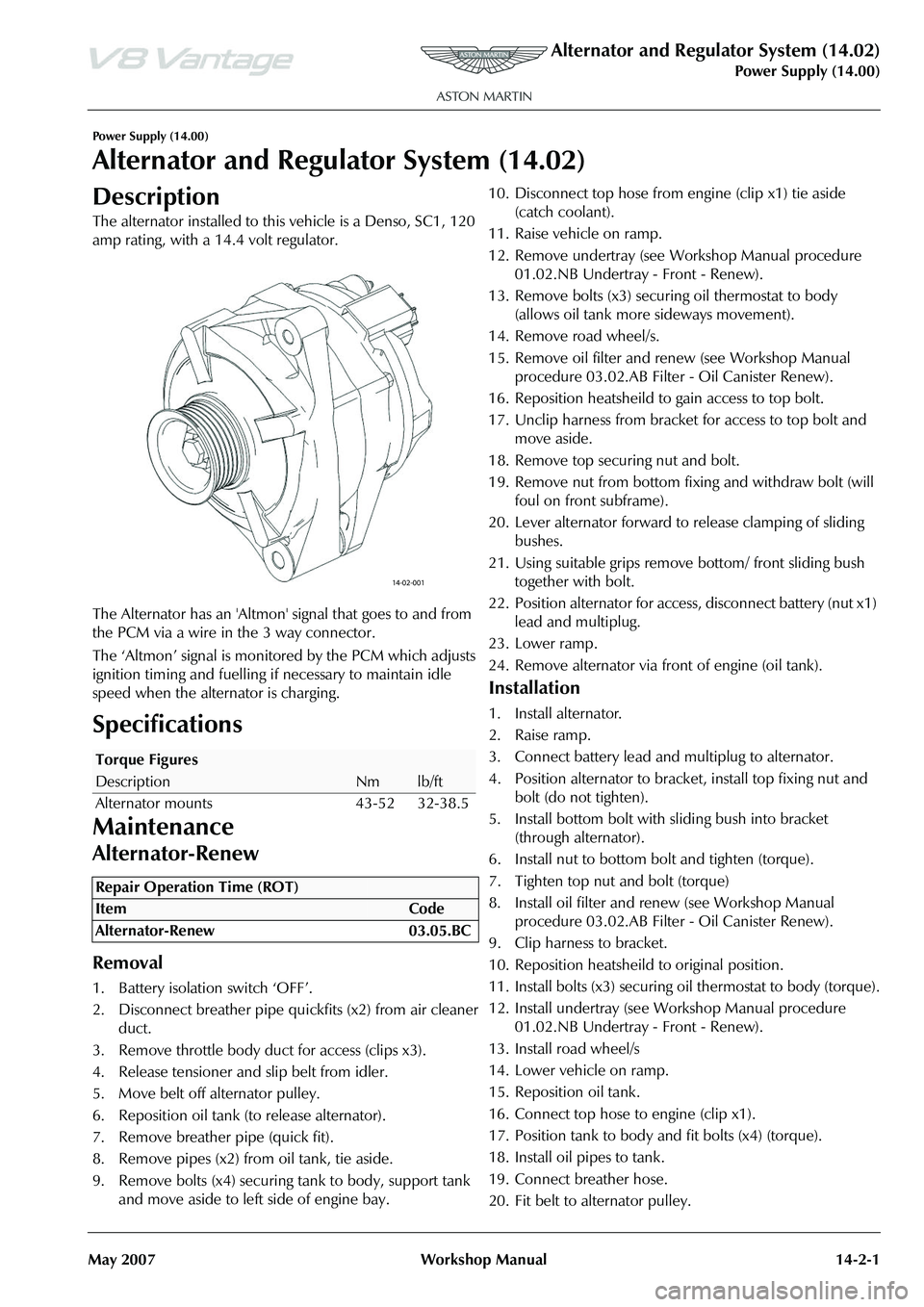
Alternator and Regulator System (14.02)
Power Supply (14.00)
May 2007 Workshop Manual 14-2-1
Power Supply (14.00)
Alternator and Regulator System (14.02)
Description
The alternator installed to this vehicle is a Denso, SC1, 120
amp rating, with a 14.4 volt regulator.
The Alternator has an 'Altmon' signal that goes to and from
the PCM via a wire in the 3 way connector.
The ‘Altmon’ signal is monitored by the PCM which adjusts
ignition timing and fuelling if necessary to maintain idle
speed when the alternator is charging.
Specifications
Maintenance
Alternator-Renew
Removal
1. Battery isolation switch ‘OFF’.
2. Disconnect breather pipe qu ickfits (x2) from air cleaner
duct.
3. Remove throttle body du ct for access (clips x3).
4. Release tensioner and slip belt from idler.
5. Move belt off alternator pulley.
6. Reposition oil tank (to release alternator).
7. Remove breather pipe (quick fit).
8. Remove pipes (x2) fr om oil tank, tie aside.
9. Remove bolts (x4) securing tank to body, support tank and move aside to left side of engine bay. 10. Disconnect top hose from engine (clip x1) tie aside
(catch coolant).
11. Raise vehicle on ramp.
12. Remove undertray (see Workshop Manual procedure 01.02.NB Undertray - Front - Renew).
13. Remove bolts (x3) securing oil thermostat to body (allows oil tank more sideways movement).
14. Remove road wheel/s.
15. Remove oil filter and renew (see Workshop Manual procedure 03.02.AB Filter - Oil Canister Renew).
16. Reposition heatsheild to gain access to top bolt.
17. Unclip harness from bracket for access to top bolt and move aside.
18. Remove top securing nut and bolt.
19. Remove nut from bottom fixing and withdraw bolt (will foul on front subframe).
20. Lever alternator forward to release clamping of sliding bushes.
21. Using suitable grips remove bottom/ front sliding bush together with bolt.
22. Position alternator for access, disconnect battery (nut x1) lead and multiplug.
23. Lower ramp.
24. Remove alternator via front of engine (oil tank).
Installation
1. Install alternator.
2. Raise ramp.
3. Connect battery lead and multiplug to alternator.
4. Position alternator to bracket, install top fixing nut and bolt (do not tighten).
5. Install bottom bolt with sliding bush into bracket (through alternator).
6. Install nut to bottom bolt and tighten (torque).
7. Tighten top nut and bolt (torque)
8. Install oil filter and re new (see Workshop Manual
procedure 03.02.AB Filter - Oil Canister Renew).
9. Clip harness to bracket.
10. Reposition heatsheild to original position.
11. Install bolts (x3) securing oil thermostat to body (torque).
12. Install undertray (see Workshop Manual procedure 01.02.NB Undertray - Front - Renew).
13. Install road wheel/s
14. Lower vehicle on ramp.
15. Reposition oil tank.
16. Connect top hose to engine (clip x1).
17. Position tank to body and fit bolts (x4) (torque).
18. Install oil pipes to tank.
19. Connect breather hose.
20. Fit belt to alternator pulley.
Torque Figures
DescriptionNmlb/ft
Alternator mounts 43-52 32-38.5
Repair Operation Time (ROT)