oil change ASTON MARTIN V8 VANTAGE 2010 Workshop Manual
[x] Cancel search | Manufacturer: ASTON MARTIN, Model Year: 2010, Model line: V8 VANTAGE, Model: ASTON MARTIN V8 VANTAGE 2010Pages: 947, PDF Size: 43.21 MB
Page 311 of 947
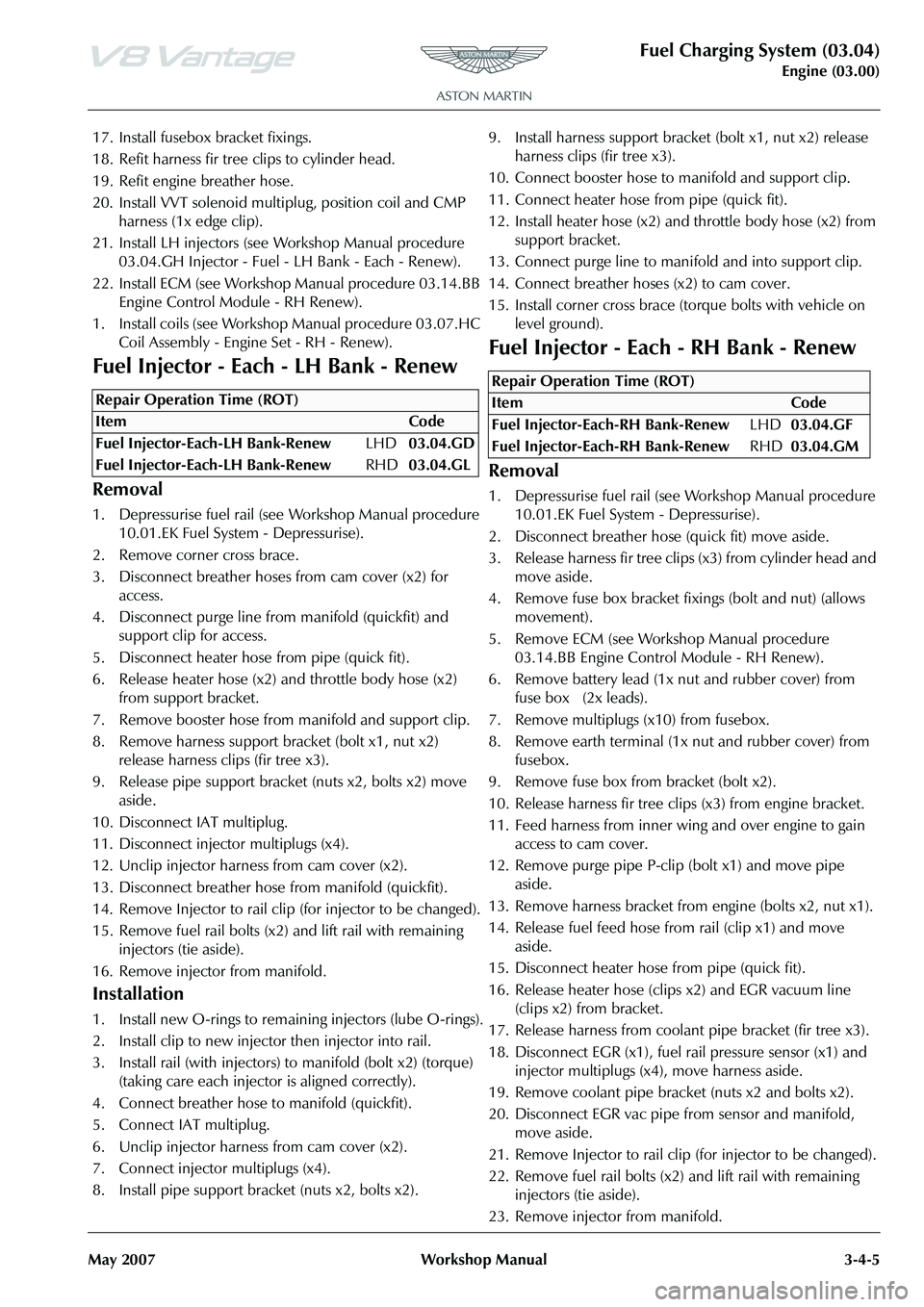
Fuel Charging System (03.04)
Engine (03.00)
May 2007 Workshop Manual 3-4-5
17. Install fusebox bracket fixings.
18. Refit harness fir tree clips to cylinder head.
19. Refit engine breather hose.
20. Install VVT solenoid multiplug, position coil and CMP
harness (1x edge clip).
21. Install LH injectors (see Workshop Manual procedure
03.04.GH Injector - Fuel - LH Bank - Each - Renew).
22. Install ECM (see Workshop Manual procedure 03.14.BB Engine Control Module - RH Renew).
1. Install coils (see Workshop Manual procedure 03.07.HC
Coil Assembly - Engine Set - RH - Renew).
Fuel Injector - Each - LH Bank - Renew
Removal
1. Depressurise fuel rail (see Workshop Manual procedure 10.01.EK Fuel System - Depressurise).
2. Remove corner cross brace.
3. Disconnect breather hoses from cam cover (x2) for access.
4. Disconnect purge line from manifold (quickfit) and support clip for access.
5. Disconnect heater hose from pipe (quick fit).
6. Release heater hose (x2) and throttle body hose (x2) from support bracket.
7. Remove booster hose from manifold and support clip.
8. Remove harness support bracket (bolt x1, nut x2) release harness clips (fir tree x3).
9. Release pipe support bracket (nuts x2, bolts x2) move aside.
10. Disconnect IAT multiplug.
11. Disconnect injector multiplugs (x4).
12. Unclip injector harness from cam cover (x2).
13. Disconnect breather hose from manifold (quickfit).
14. Remove Injector to rail clip (for injector to be changed).
15. Remove fuel rail bolts (x2) and lift rail with remaining injectors (tie aside).
16. Remove injector from manifold.
Installation
1. Install new O-rings to remaining injectors (lube O-rings).
2. Install clip to new injector then injector into rail.
3. Install rail (with injectors) to manifold (bolt x2) (torque) (taking care each injector is aligned correctly).
4. Connect breather hose to manifold (quickfit).
5. Connect IAT multiplug.
6. Unclip injector harness from cam cover (x2).
7. Connect injector multiplugs (x4).
8. Install pipe support br acket (nuts x2, bolts x2). 9. Install harness support bracket (bolt x1, nut x2) release
harness clips (fir tree x3).
10. Connect booster hose to manifold and support clip.
11. Connect heater hose from pipe (quick fit).
12. Install heater hose (x2) and throttle body hose (x2) from support bracket.
13. Connect purge line to manifold and into support clip.
14. Connect breather hoses (x2) to cam cover.
15. Install corner cross brace (t orque bolts with vehicle on
level ground).
Fuel Injector - Each - RH Bank - Renew
Removal
1. Depressurise fuel rail (see Workshop Manual procedure 10.01.EK Fuel System - Depressurise).
2. Disconnect breather hose (quick fit) move aside.
3. Release harness fir tree clips (x3) from cylinder head and move aside.
4. Remove fuse box bracket fi xings (bolt and nut) (allows
movement).
5. Remove ECM (see Workshop Manual procedure 03.14.BB Engine Control Module - RH Renew).
6. Remove battery lead (1x nut and rubber cover) from fuse box (2x leads).
7. Remove multiplugs (x10) from fusebox.
8. Remove earth terminal (1x nut and rubber cover) from fusebox.
9. Remove fuse box from bracket (bolt x2).
10. Release harness fir tree clips (x3) from engine bracket.
11. Feed harness from inner wing and over engine to gain access to cam cover.
12. Remove purge pipe P-clip (bolt x1) and move pipe aside.
13. Remove harness bracket from engine (bolts x2, nut x1).
14. Release fuel feed hose from rail (clip x1) and move aside.
15. Disconnect heater hose from pipe (quick fit).
16. Release heater hose (clips x2) and EGR vacuum line
(clips x2) from bracket.
17. Release harness from coolan t pipe bracket (fir tree x3).
18. Disconnect EGR (x1), fuel rail pressure sensor (x1) and injector multiplugs (x4), move harness aside.
19. Remove coolant pipe bracket (nuts x2 and bolts x2).
20. Disconnect EGR vac pipe from sensor and manifold, move aside.
21. Remove Injector to rail clip (for injector to be changed).
22. Remove fuel rail bolts (x2) and lift rail with remaining injectors (tie aside).
23. Remove injector from manifold.
Repair Operation Time (ROT)
Repair Operation Time (ROT)
Page 602 of 947
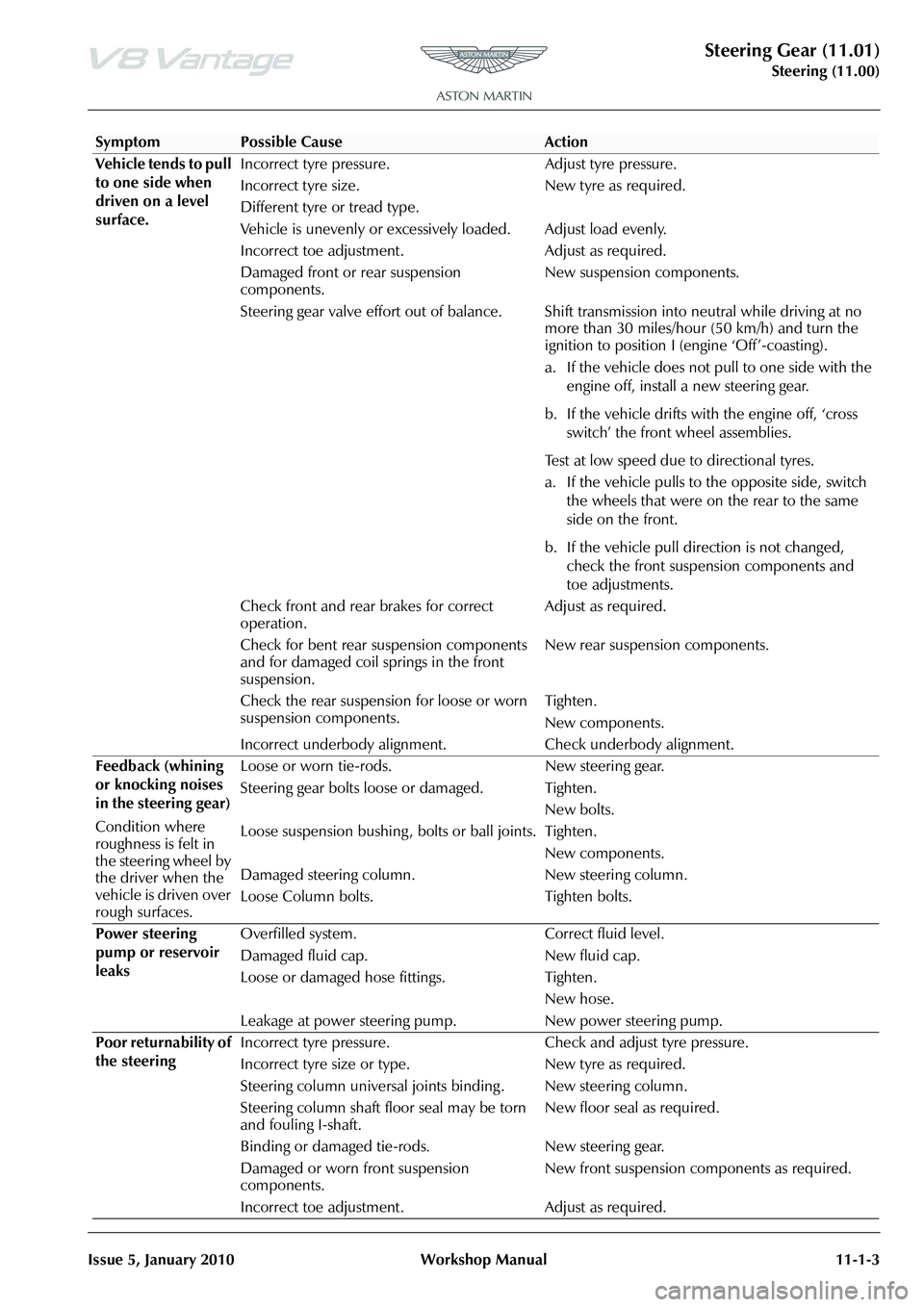
Steering Gear (11.01)
Steering (11.00)
Issue 5, January 2010 Workshop Manual 11-1-3
Vehicle tends to pull
to one side when
driven on a level
surface. Incorrect tyre pressure. Adjust tyre pressure.
Incorrect tyre size.
Different tyre or tread type.
New tyre as required.
Vehicle is unevenly or excessively loaded. Adjust load evenly.
Incorrect toe adjustment. Adjust as required.
Damaged front or rear suspension
components. New suspension components.
Steering gear valve effort out of balance. Shift transmission into neutral while driving at no more than 30 miles/hour (50 km/h) and turn the
ignition to position I (engine ‘Off’-coasting).
a. If the vehicle does not pull to one side with the
engine off, install a new steering gear.
b. If the vehicle drifts with the engine off, ‘cross switch’ the front wheel assemblies.
Test at low speed due to directional tyres.
a. If the vehicle pulls to the opposite side, switch the wheels that were on the rear to the same
side on the front.
b. If the vehicle pull direction is not changed, check the front suspension components and
toe adjustments.
Check front and rear brakes for correct
operation. Adjust as required.
Check for bent rear suspension components
and for damaged coil springs in the front
suspension. New rear suspension components.
Check the rear suspension for loose or worn
suspension components. Tighten.
New components.
Incorrect underbody alignment. Check underbody alignment.
Feedback (whining
or knocking noises
in the steering gear)
Condition where
roughness is felt in
the steering wheel by
the driver when the
vehicle is driven over
rough surfaces. Loose or worn tie-rods. New steering gear.
Steering gear bolts loose or damaged. Tighten.
New bolts.
Loose suspension bushing , bolts or ball joints. Tighten.
New components.
Damaged steering column.
Loose Column bolts. New steering column.
Tighten bolts.
Power steering
pump or reservoir
leaks Overfilled system. Correct fluid level.
Damaged fluid cap. New fluid cap.
Loose or damaged hose fittings. Tighten.
New hose.
Leakage at power steering pump. New power steering pump.
Poor returnability of
the steering Incorrect tyre pressure. Check
and adjust tyre pressure.
Incorrect tyre size or ty pe. New tyre as required.
Steering column universal joints binding . New steering column.
Steering column shaft floor seal may be torn
and fouling I-shaft. New floor seal as required.
Binding or damaged tie-rods. New steering gear.
Damaged or worn front suspension
components. New front suspension components as required.
Incorrect toe adjustment. Adjust as required.
SymptomPossible CauseAction
Page 637 of 947
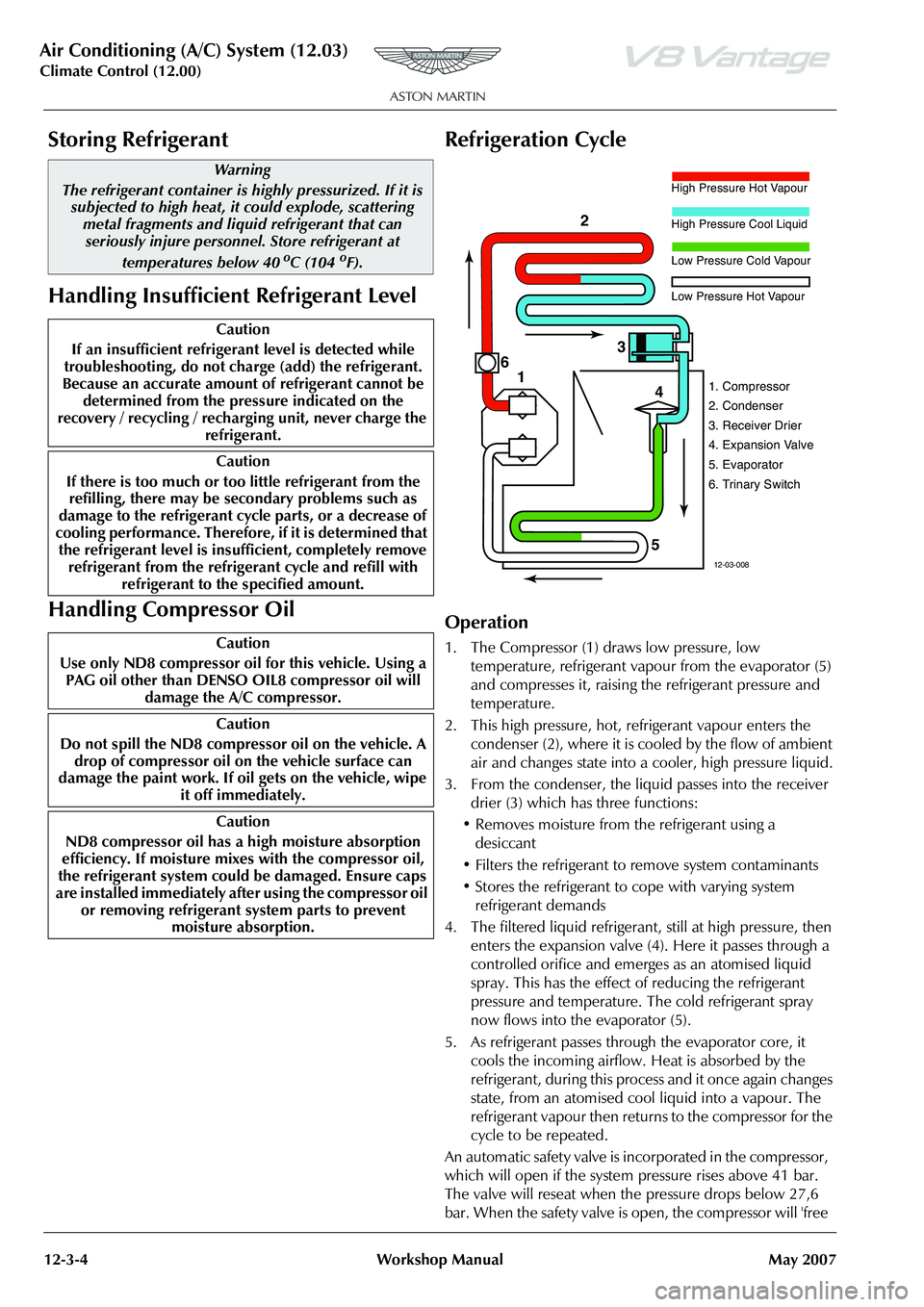
Air Conditioning (A/C) System (12.03)
Climate Control (12.00)
12-3-4 Workshop Manual May 2007
Storing Refrigerant
Handling Insufficient Refrigerant Level
Handling Compressor Oil
Refrigeration Cycle
Operation
1. The Compressor (1) dr aws low pressure, low
temperature, refrigerant vapour from the evaporator (5)
and compresses it, raising th e refrigerant pressure and
temperature.
2. This high pressure, hot, refrigerant vapour enters the condenser (2), where it is cooled by the flow of ambient
air and changes state into a cooler, high pressure liquid.
3. From the condenser, the liqu id passes into the receiver
drier (3) which has three functions:
• Removes moisture from the refrigerant using a desiccant
• Filters the refrigerant to remove system contaminants
• Stores the refrigerant to cope with varying system refrigerant demands
4. The filtered liquid refrigerant, still at high pressure, then enters the expansion valve (4). Here it passes through a
controlled orifice and emerges as an atomised liquid
spray. This has the effect of reducing the refrigerant
pressure and temperature. The cold refrigerant spray
now flows into the evaporator (5).
5. As refrigerant passes through the evaporator core, it cools the incoming airflow. Heat is absorbed by the
refrigerant, during this process and it once again changes
state, from an atomised cool liquid into a vapour. The
refrigerant vapour then returns to the compressor for the
cycle to be repeated.
An automatic safety valve is incorporated in the compressor,
which will open if the system pressure rises above 41 bar.
The valve will reseat when the pressure drops below 27,6
bar. When the safety valve is open, the compressor will 'free
Warning
The refrigerant container is highly pressurized. If it is subjected to high heat, it could explode, scattering metal fragments and liquid refrigerant that can
seriously injure personnel. Store refrigerant at
temperatures below 40
oC (104 oF).
Caution
If an insufficient refrigerant level is detected while
troubleshooting, do not char ge (add) the refrigerant.
Because an accurate amount of refrigerant cannot be
determined from the pressure indicated on the
recovery / recycling / rechar ging unit, never charge the
refrigerant.
Caution
If there is too much or to o little refrigerant from the
refilling, there may be secondary problems such as
damage to the refrigerant cycl e parts, or a decrease of
cooling performance. Therefore, if it is determined that the refrigerant level is insufficient, completely remove refrigerant from the refriger ant cycle and refill with
refrigerant to the specified amount.
Caution
Use only ND8 compressor oil for this vehicle. Using a PAG oil other than DENSO OIL8 compressor oil will damage the A/C compressor.
Caution
Do not spill the ND8 compressor oil on the vehicle. A drop of compressor oil on the vehicle surface can
damage the paint work. If oil gets on the vehicle, wipe it off immediately.
Caution
ND8 compressor oil has a high moisture absorption
efficiency. If moisture mixe s with the compressor oil,
the refrigerant system could be damaged. Ensure caps
are installed immediately afte r using the compressor oil
or removing refrigerant system parts to prevent moisture absorption.
+ L J K 3 U H V V X U H + R W 9 D S R X U
+ L J K 3 U H V V X U H &