ECU AUDI S4 1998 B5 / 1.G Engine Manual
[x] Cancel search | Manufacturer: AUDI, Model Year: 1998, Model line: S4, Model: AUDI S4 1998 B5 / 1.GPages: 72, PDF Size: 3.25 MB
Page 11 of 72
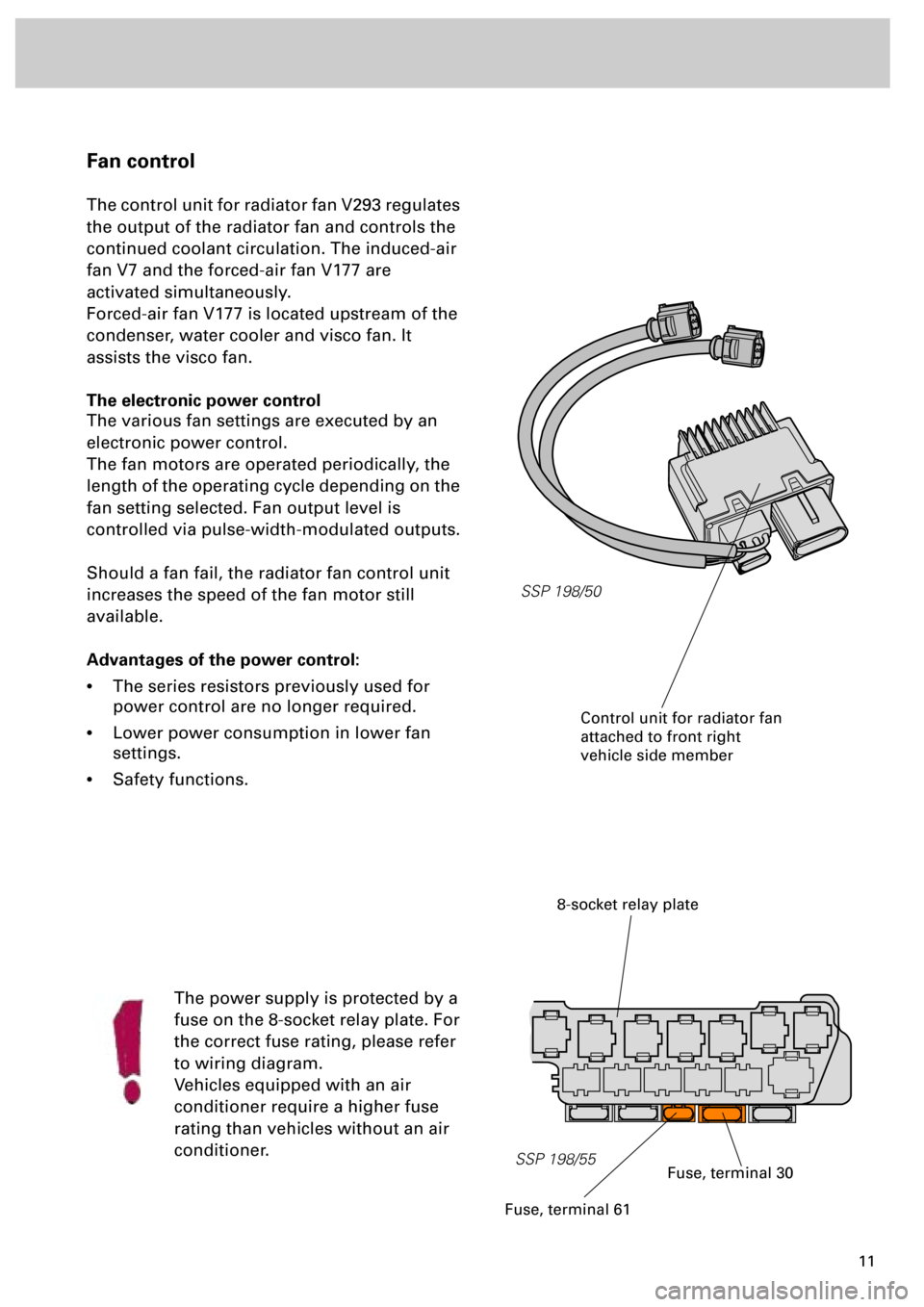
11
Fan control
The control unit for radiator fan V293 regulates
the output of the radiator fan and controls the
continued coolant circulation. The induced-air
fan V7 and the forced-air fan V177 are
activated simultaneously.
Forced-air fan V177 is located upstream of the
condenser, water cooler and visco fan. It
assists the visco fan.
The electronic power control
The various fan settings are executed by an
electronic power control.
The fan motors are operated periodically, the
length of the operating cycle depending on the
fan setting selected. Fan output level is
controlled via pulse-width-modulated outputs.
Should a fan fail, the radiator fan control unit
increases the speed of the fan motor still
available.
Advantages of the power control:
•
The series resistors previously used for
power control are no longer required.
•
Lower power consumption in lower fan
settings.
•
Safety functions.
The power supply is protected by a
fuse on the 8-socket relay plate. For
the correct fuse rating, please refer
to wiring diagram.
Vehicles equipped with an air
conditioner require a higher fuse
rating than vehicles without an air
conditioner.
SSP 198/50
8-socket relay plate
SSP 198/55
Control unit for radiator fan
attached to front right
vehicle side member
Fuse, terminal 30
Fuse, terminal 61
Page 35 of 72
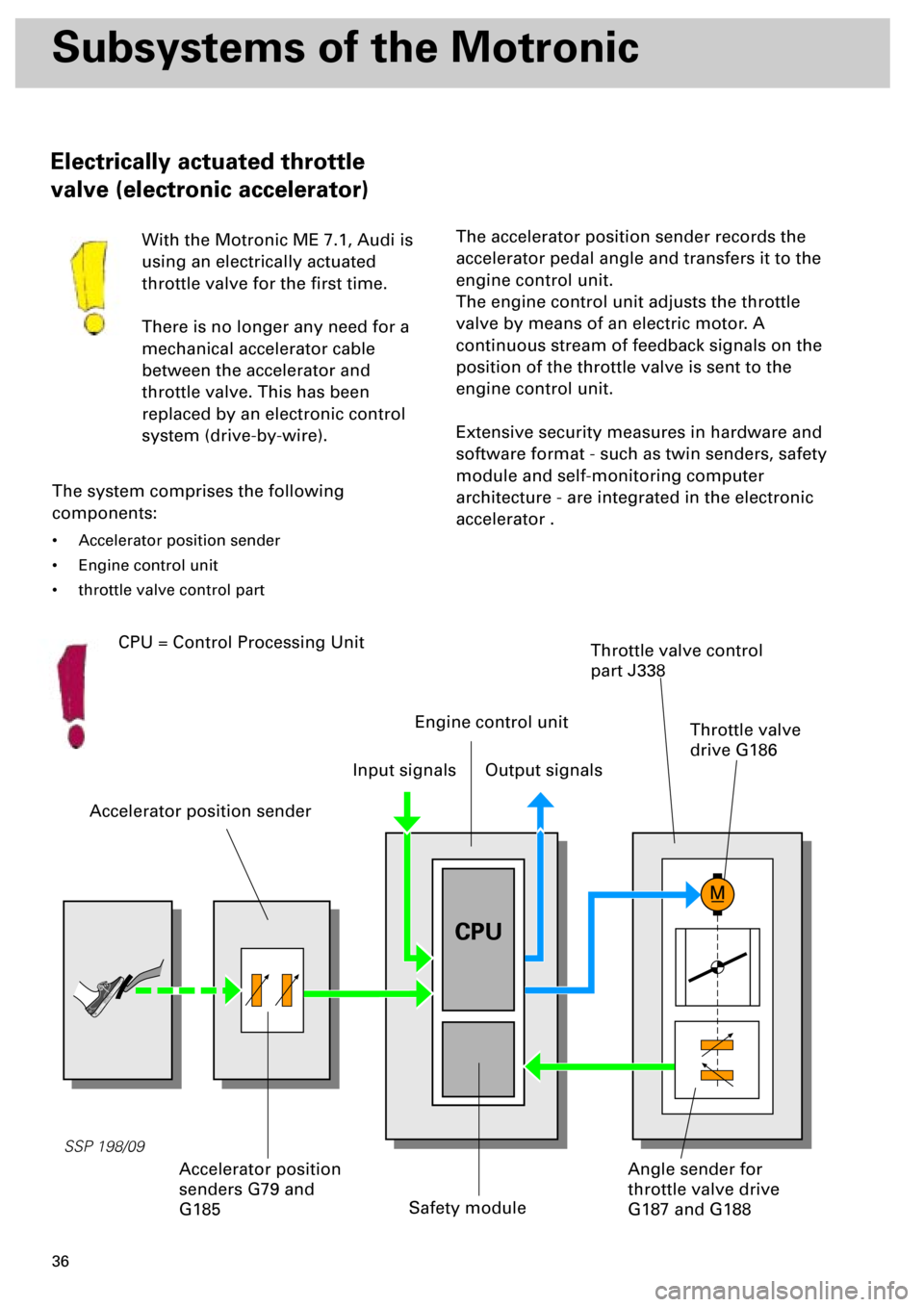
36
SSP 198/09
Subsystems of the Motronic
Electrically actuated throttle
valve (electronic accelerator)
With the Motronic ME 7.1, Audi is
using an electrically actuated
throttle valve for the first time.
There is no longer any need for a
mechanical accelerator cable
between the accelerator and
throttle valve. This has been
replaced by an electronic control
system (drive-by-wire).
The system comprises the following
components:
• Accelerator position sender
• Engine control unit
• throttle valve control part
Accelerator position sender
Safety module
Throttle valve control
part J338
The accelerator position sender records the
accelerator pedal angle and transfers it to the
engine control unit.
The engine control unit adjusts the throttle
valve by means of an electric motor. A
continuous stream of feedback signals on the
position of the throttle valve is sent to the
engine control unit.
Extensive security measures in hardware and
software format - such as twin senders, safety
module and self-monitoring computer
architecture - are integrated in the electronic
accelerator .
Input signalsOutput signals
Angle sender for
throttle valve drive
G187 and G188Accelerator position
senders G79 and
G185
Engine control unit
CPU
CPU = Control Processing Unit
Throttle valve
drive G186
Page 36 of 72
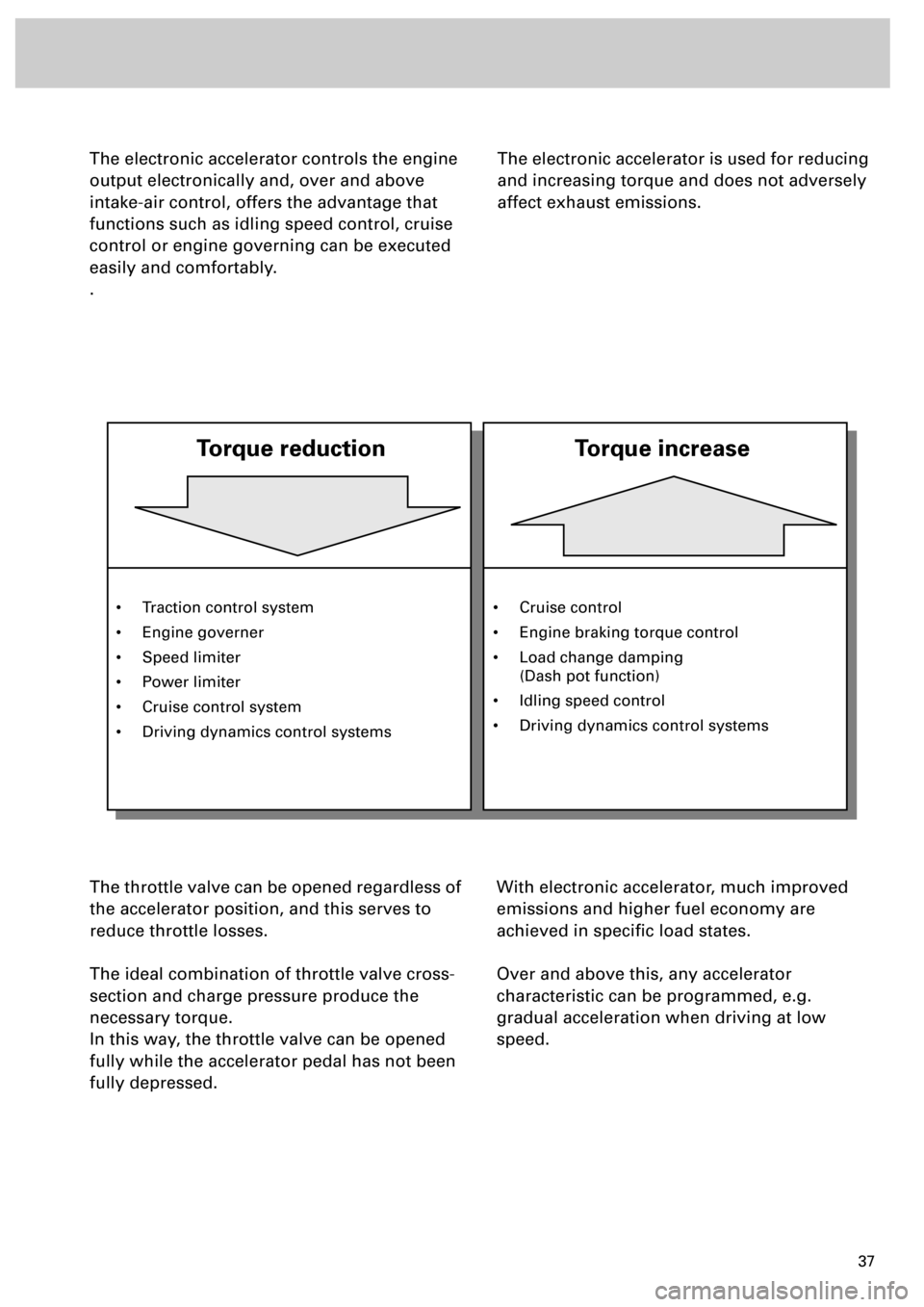
37
The electronic accelerator controls the engine
output electronically and, over and above
intake-air control, offers the advantage that
functions such as idling speed control, cruise
control or engine governing can be executed
easily and comfortably.
.
The throttle valve can be opened regardless of
the accelerator position, and this serves to
reduce throttle losses.
The ideal combination of throttle valve cross-
section and charge pressure produce the
necessary torque.
In this way, the throttle valve can be opened
fully while the accelerator pedal has not been
fully depressed.With electronic accelerator, much improved
emissions and higher fuel economy are
achieved in specific load states.
Over and above this, any accelerator
characteristic can be programmed, e.g.
gradual acceleration when driving at low
speed.
The electronic accelerator is used for reducing
and increasing torque and does not adversely
affect exhaust emissions.
• Traction control system
• Engine governer
• Speed limiter
• Power limiter
• Cruise control system
• Driving dynamics control systems
Torque reduction
Torque increase
• Cruise control
• Engine braking torque control
• Load change damping
(Dash pot function)
• Idling speed control
• Driving dynamics control systems
Page 38 of 72
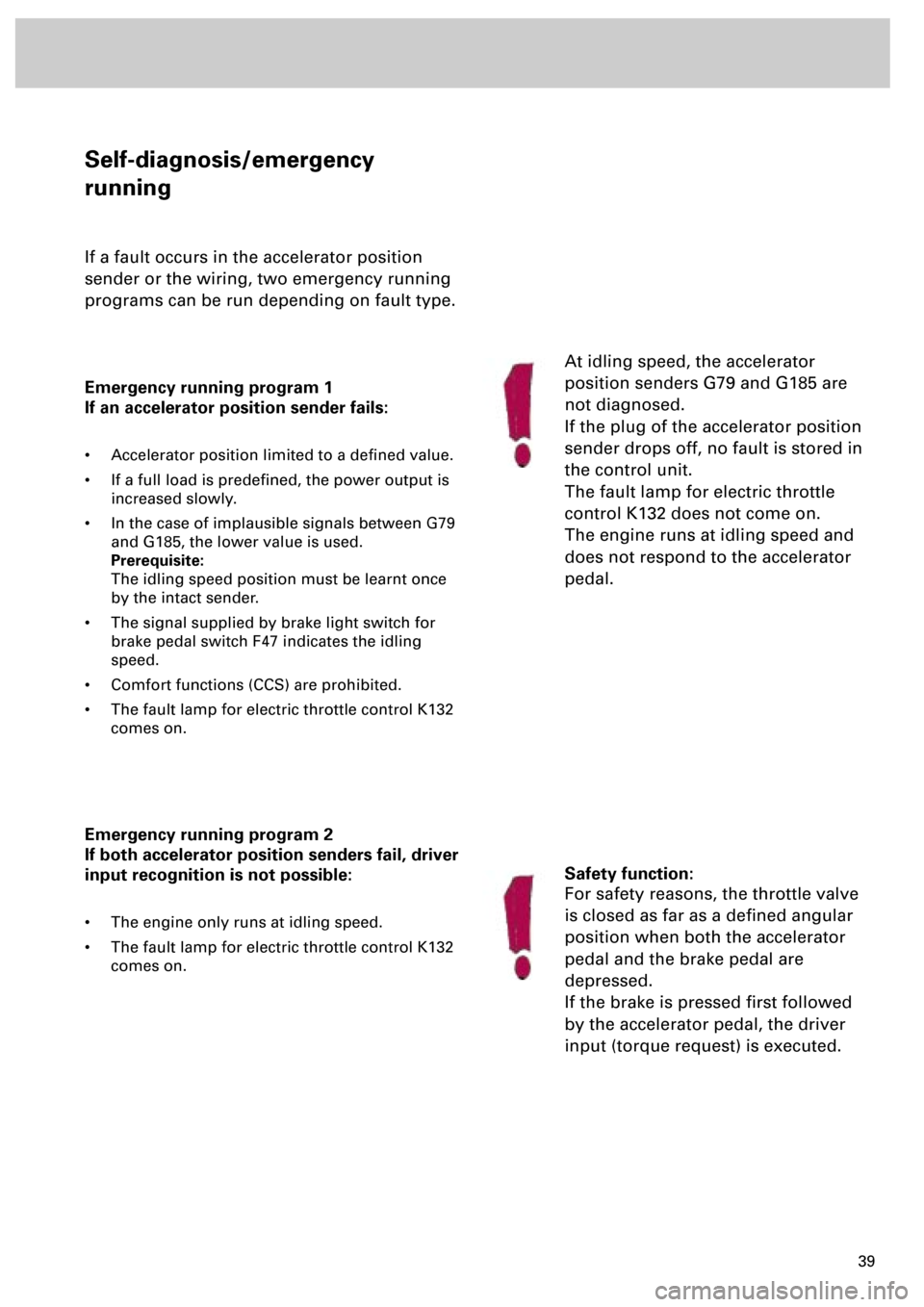
39
Self-diagnosis/emergency
running
If a fault occurs in the accelerator position
sender or the wiring, two emergency running
programs can be run depending on fault type.
Emergency running program 1
If an accelerator position sender fails:
• Accelerator position limited to a defined value.
• If a full load is predefined, the power output is
increased slowly.
• In the case of implausible signals between G79
and G185, the lower value is used.
Prerequisite:
The idling speed position must be learnt once
by the intact sender.
• The signal supplied by brake light switch for
brake pedal switch F47 indicates the idling
speed.
• Comfort functions (CCS) are prohibited.
• The fault lamp for electric throttle control K132
comes on.
Emergency running program 2
If both accelerator position senders fail, driver
input recognition is not possible:
• The engine only runs at idling speed.
• The fault lamp for electric throttle control K132
comes on.
At idling speed, the accelerator
position senders G79 and G185 are
not diagnosed.
If the plug of the accelerator position
sender drops off, no fault is stored in
the control unit.
The fault lamp for electric throttle
control K132 does not come on.
The engine runs at idling speed and
does not respond to the accelerator
pedal.
Safety function:
For safety reasons, the throttle valve
is closed as far as a defined angular
position when both the accelerator
pedal and the brake pedal are
depressed.
If the brake is pressed first followed
by the accelerator pedal, the driver
input (torque request) is executed.
Page 42 of 72
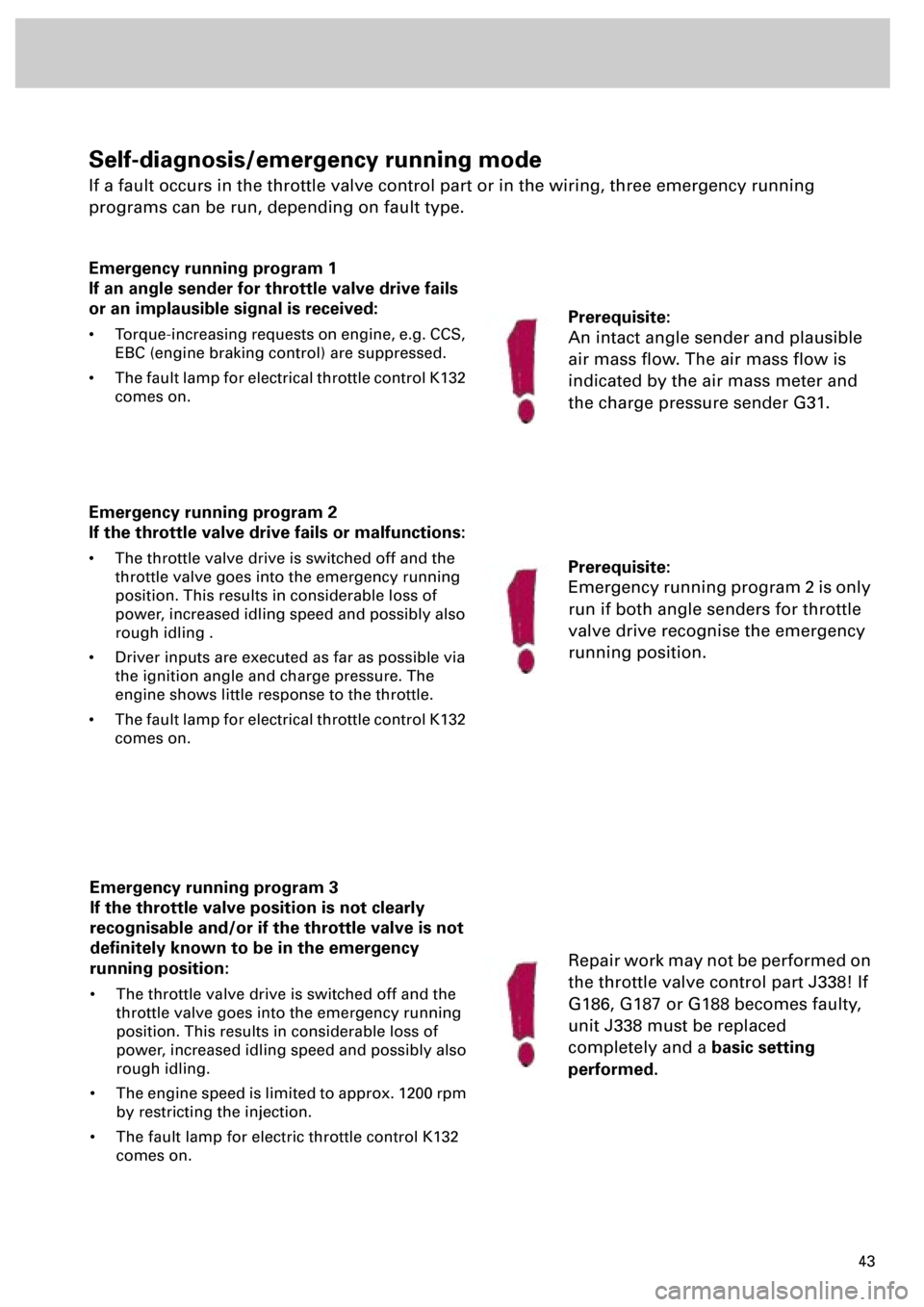
43
Emergency running program 1
If an angle sender for throttle valve drive fails
or an implausible signal is received:
• Torque-increasing requests on engine, e.g. CCS,
EBC (engine braking control) are suppressed.
• The fault lamp for electrical throttle control K132
comes on.
Prerequisite:
An intact angle sender and plausible
air mass flow. The air mass flow is
indicated by the air mass meter and
the charge pressure sender G31.
Self-diagnosis/emergency running mode
If a fault occurs in the throttle valve control part or in the wiring, three emergency running
programs can be run, depending on fault type.
Emergency running program 2
If the throttle valve drive fails or malfunctions:
• The throttle valve drive is switched off and the
throttle valve goes into the emergency running
position. This results in considerable loss of
power, increased idling speed and possibly also
rough idling .
• Driver inputs are executed as far as possible via
the ignition angle and charge pressure. The
engine shows little response to the throttle.
• The fault lamp for electrical throttle control K132
comes on.
Prerequisite:
Emergency running program 2 is only
run if both angle senders for throttle
valve drive recognise the emergency
running position.
Emergency running program 3
If the throttle valve position is not clearly
recognisable and/or if the throttle valve is not
definitely known to be in the emergency
running position:
• The throttle valve drive is switched off and the
throttle valve goes into the emergency running
position. This results in considerable loss of
power, increased idling speed and possibly also
rough idling.
• The engine speed is limited to approx. 1200 rpm
by restricting the injection.
• The fault lamp for electric throttle control K132
comes on.
Repair work may not be performed on
the throttle valve control part J338! If
G186, G187 or G188 becomes faulty,
unit J338 must be replaced
completely and a
basic setting
performed.
Page 60 of 72
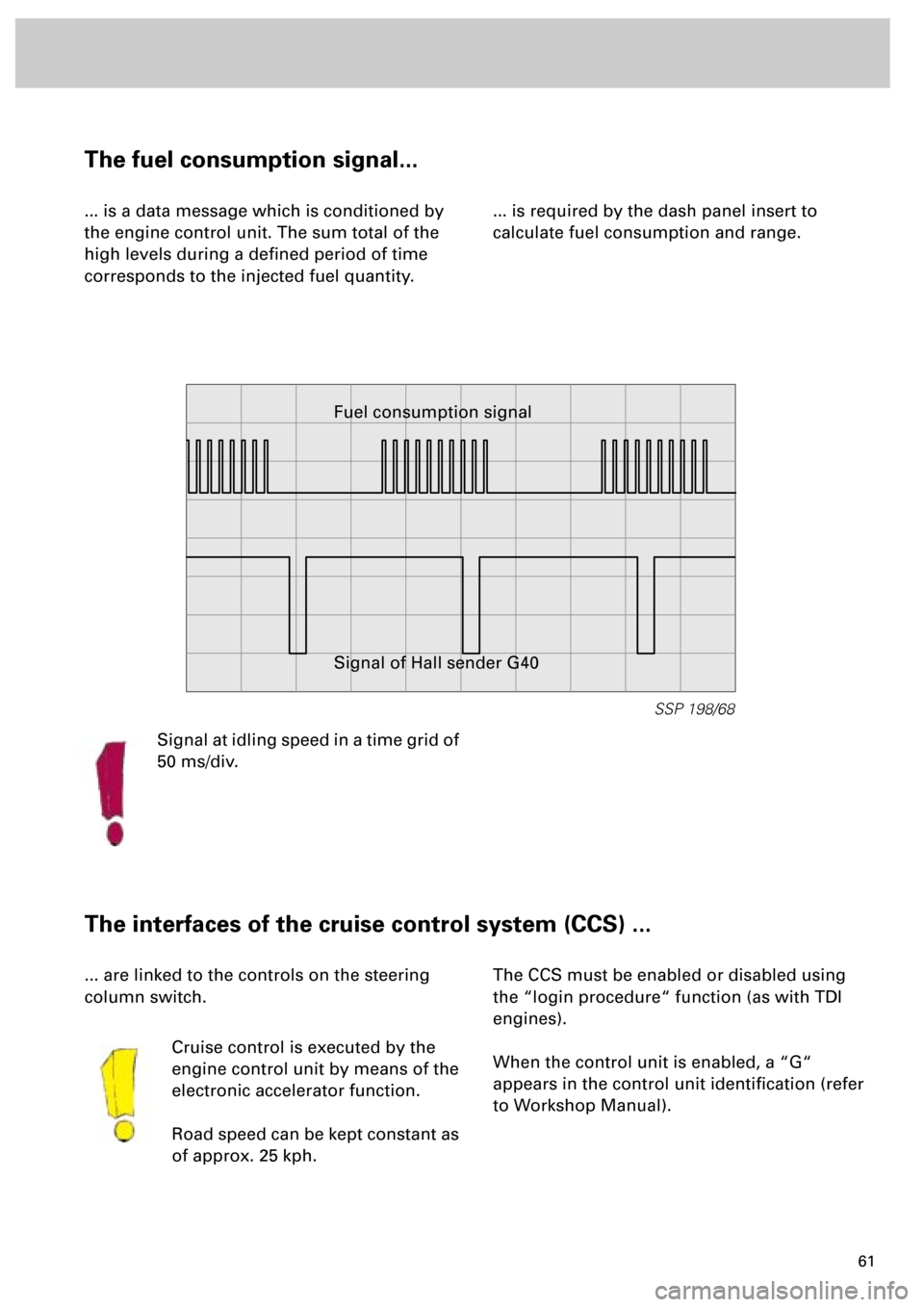
61
The fuel consumption signal...
... is a data message which is conditioned by
the engine control unit. The sum total of the
high levels during a defined period of time
corresponds to the injected fuel quantity.... is required by the dash panel insert to
calculate fuel consumption and range.
The interfaces of the cruise control system (CCS) ...
... are linked to the controls on the steering
column switch.
Cruise control is executed by the
engine control unit by means of the
electronic accelerator function.
Road speed can be kept constant as
of approx. 25 kph.The CCS must be enabled or disabled using
the “login procedure“ function (as with TDI
engines).
When the control unit is enabled, a “G“
appears in the control unit identification (refer
to Workshop Manual).
SSP 198/68
Fuel consumption signal
Signal of Hall sender G40
Signal at idling speed in a time grid of
50 ms/div.