power steering BMW 3 SERIES 1987 E30 User Guide
[x] Cancel search | Manufacturer: BMW, Model Year: 1987, Model line: 3 SERIES, Model: BMW 3 SERIES 1987 E30Pages: 228, PDF Size: 7.04 MB
Page 51 of 228
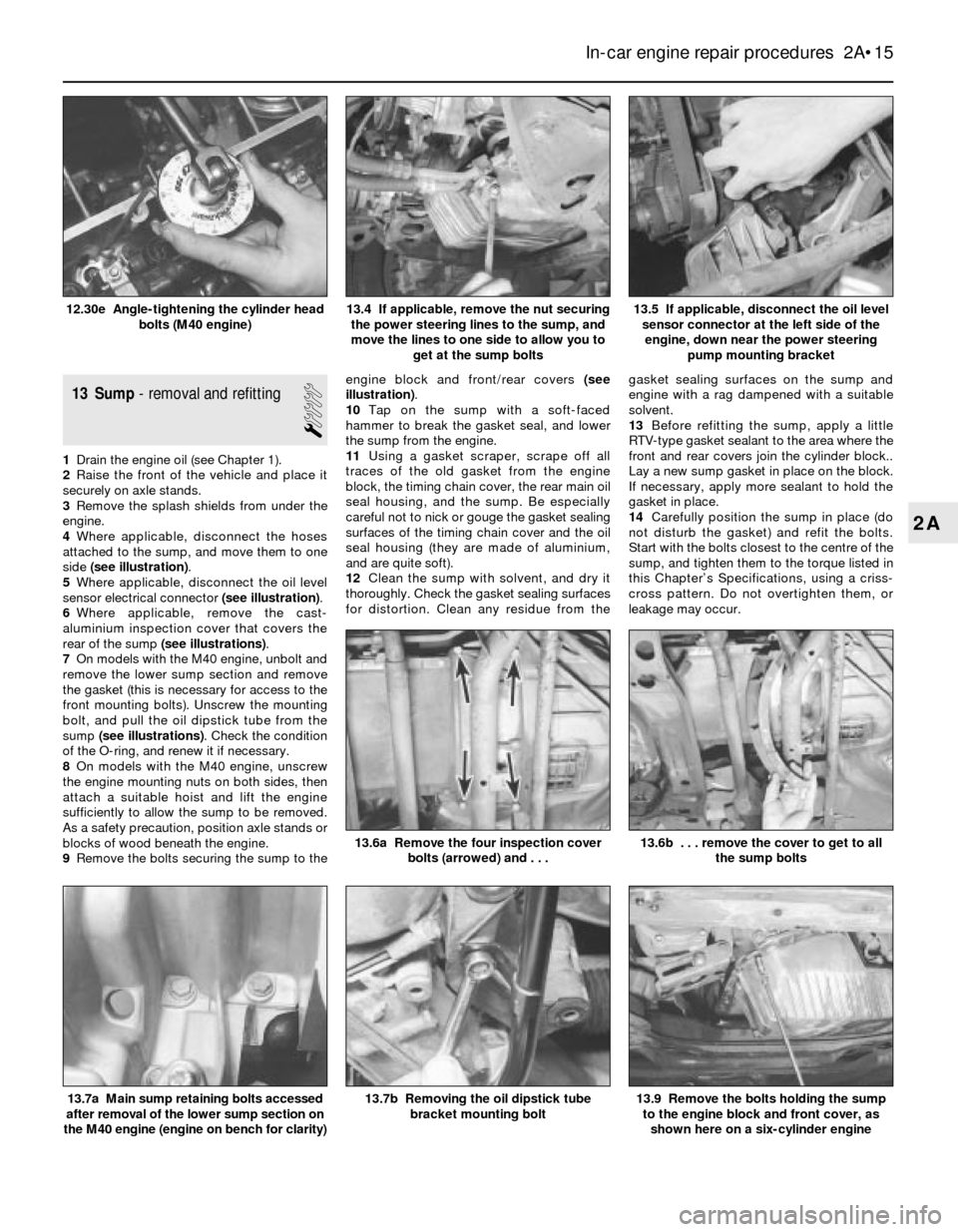
13 Sump- removal and refitting
1
1Drain the engine oil (see Chapter 1).
2Raise the front of the vehicle and place it
securely on axle stands.
3Remove the splash shields from under the
engine.
4Where applicable, disconnect the hoses
attached to the sump, and move them to one
side (see illustration).
5Where applicable, disconnect the oil level
sensor electrical connector (see illustration).
6Where applicable, remove the cast-
aluminium inspection cover that covers the
rear of the sump (see illustrations).
7On models with the M40 engine, unbolt and
remove the lower sump section and remove
the gasket (this is necessary for access to the
front mounting bolts). Unscrew the mounting
bolt, and pull the oil dipstick tube from the
sump (see illustrations). Check the condition
of the O-ring, and renew it if necessary.
8On models with the M40 engine, unscrew
the engine mounting nuts on both sides, then
attach a suitable hoist and lift the engine
sufficiently to allow the sump to be removed.
As a safety precaution, position axle stands or
blocks of wood beneath the engine.
9Remove the bolts securing the sump to theengine block and front/rear covers (see
illustration).
10Tap on the sump with a soft-faced
hammer to break the gasket seal, and lower
the sump from the engine.
11Using a gasket scraper, scrape off all
traces of the old gasket from the engine
block, the timing chain cover, the rear main oil
seal housing, and the sump. Be especially
careful not to nick or gouge the gasket sealing
surfaces of the timing chain cover and the oil
seal housing (they are made of aluminium,
and are quite soft).
12Clean the sump with solvent, and dry it
thoroughly. Check the gasket sealing surfaces
for distortion. Clean any residue from thegasket sealing surfaces on the sump and
engine with a rag dampened with a suitable
solvent.
13Before refitting the sump, apply a little
RTV-type gasket sealant to the area where the
front and rear covers join the cylinder block..
Lay a new sump gasket in place on the block.
If necessary, apply more sealant to hold the
gasket in place.
14Carefully position the sump in place (do
not disturb the gasket) and refit the bolts.
Start with the bolts closest to the centre of the
sump, and tighten them to the torque listed in
this Chapter’s Specifications, using a criss-
cross pattern. Do not overtighten them, or
leakage may occur.
In-car engine repair procedures 2A•15
13.5 If applicable, disconnect the oil level
sensor connector at the left side of the
engine, down near the power steering
pump mounting bracket13.4 If applicable, remove the nut securing
the power steering lines to the sump, and
move the lines to one side to allow you to
get at the sump bolts12.30e Angle-tightening the cylinder head
bolts (M40 engine)
13.9 Remove the bolts holding the sump
to the engine block and front cover, as
shown here on a six-cylinder engine13.7b Removing the oil dipstick tube
bracket mounting bolt
13.6b . . . remove the cover to get to all
the sump bolts13.6a Remove the four inspection cover
bolts (arrowed) and . . .
13.7a Main sump retaining bolts accessed
after removal of the lower sump section on
the M40 engine (engine on bench for clarity)
2A
Page 62 of 228
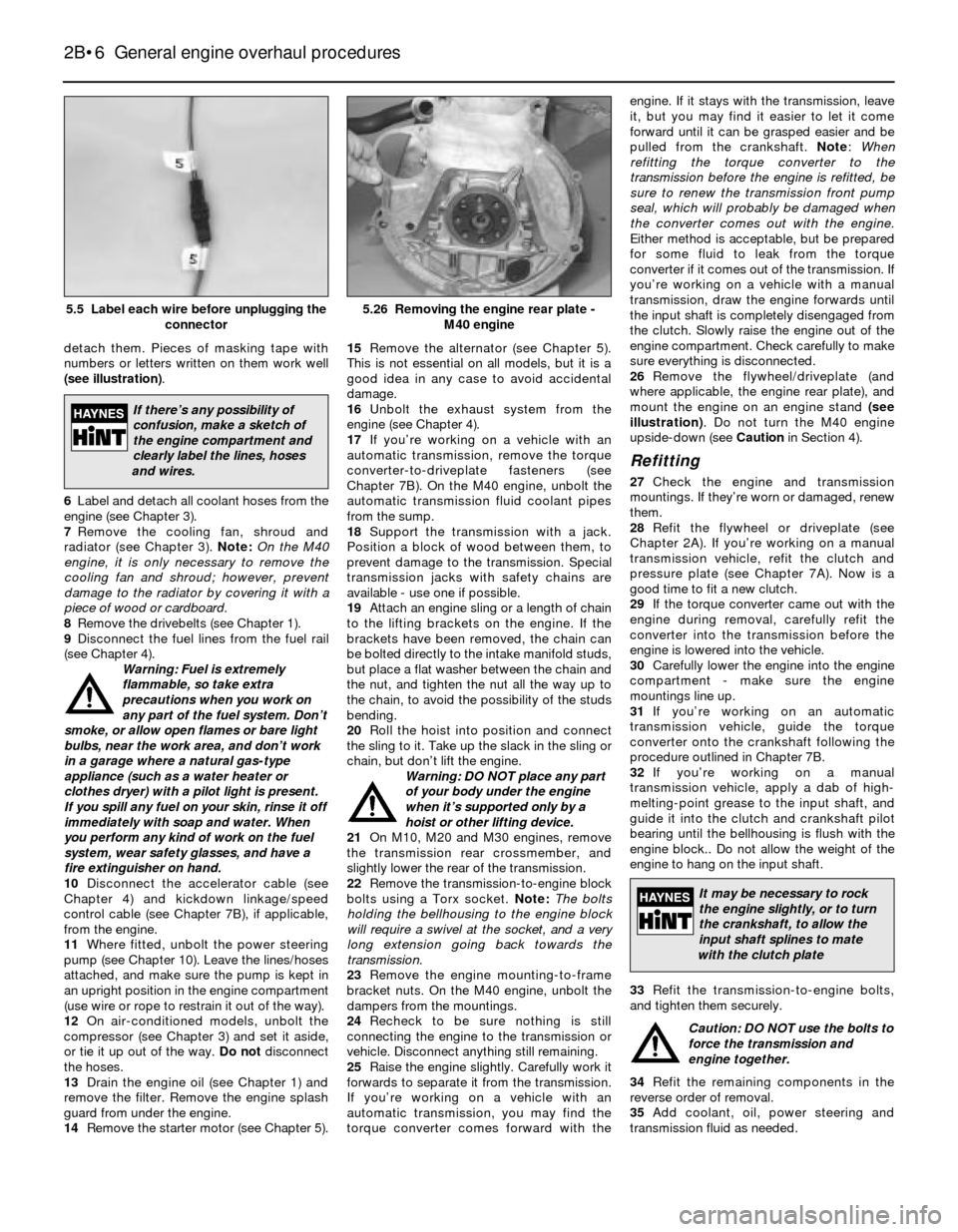
detach them. Pieces of masking tape with
numbers or letters written on them work well
(see illustration).
6Label and detach all coolant hoses from the
engine (see Chapter 3).
7Remove the cooling fan, shroud and
radiator (see Chapter 3). Note:On the M40
engine, it is only necessary to remove the
cooling fan and shroud; however, prevent
damage to the radiator by covering it with a
piece of wood or cardboard.
8Remove the drivebelts (see Chapter 1).
9Disconnect the fuel lines from the fuel rail
(see Chapter 4).
Warning: Fuel is extremely
flammable, so take extra
precautions when you work on
any part of the fuel system. Don’t
smoke, or allow open flames or bare light
bulbs, near the work area, and don’t work
in a garage where a natural gas-type
appliance (such as a water heater or
clothes dryer) with a pilot light is present.
If you spill any fuel on your skin, rinse it off
immediately with soap and water. When
you perform any kind of work on the fuel
system, wear safety glasses, and have a
fire extinguisher on hand.
10Disconnect the accelerator cable (see
Chapter 4) and kickdown linkage/speed
control cable (see Chapter 7B), if applicable,
from the engine.
11Where fitted, unbolt the power steering
pump (see Chapter 10). Leave the lines/hoses
attached, and make sure the pump is kept in
an upright position in the engine compartment
(use wire or rope to restrain it out of the way).
12On air-conditioned models, unbolt the
compressor (see Chapter 3) and set it aside,
or tie it up out of the way. Do not disconnect
the hoses.
13Drain the engine oil (see Chapter 1) and
remove the filter. Remove the engine splash
guard from under the engine.
14Remove the starter motor (see Chapter 5).15Remove the alternator (see Chapter 5).
This is not essential on all models, but it is a
good idea in any case to avoid accidental
damage.
16Unbolt the exhaust system from the
engine (see Chapter 4).
17If you’re working on a vehicle with an
automatic transmission, remove the torque
converter-to-driveplate fasteners (see
Chapter 7B). On the M40 engine, unbolt the
automatic transmission fluid coolant pipes
from the sump.
18Support the transmission with a jack.
Position a block of wood between them, to
prevent damage to the transmission. Special
transmission jacks with safety chains are
available - use one if possible.
19Attach an engine sling or a length of chain
to the lifting brackets on the engine. If the
brackets have been removed, the chain can
be bolted directly to the intake manifold studs,
but place a flat washer between the chain and
the nut, and tighten the nut all the way up to
the chain, to avoid the possibility of the studs
bending.
20Roll the hoist into position and connect
the sling to it. Take up the slack in the sling or
chain, but don’t lift the engine.
Warning: DO NOT place any part
of your body under the engine
when it’s supported only by a
hoist or other lifting device.
21On M10, M20 and M30 engines, remove
the transmission rear crossmember, and
slightly lower the rear of the transmission.
22Remove the transmission-to-engine block
bolts using a Torx socket. Note:The bolts
holding the bellhousing to the engine block
will require a swivel at the socket, and a very
long extension going back towards the
transmission.
23Remove the engine mounting-to-frame
bracket nuts. On the M40 engine, unbolt the
dampers from the mountings.
24Recheck to be sure nothing is still
connecting the engine to the transmission or
vehicle. Disconnect anything still remaining.
25Raise the engine slightly. Carefully work it
forwards to separate it from the transmission.
If you’re working on a vehicle with an
automatic transmission, you may find the
torque converter comes forward with theengine. If it stays with the transmission, leave
it, but you may find it easier to let it come
forward until it can be grasped easier and be
pulled from the crankshaft. Note:When
refitting the torque converter to the
transmission before the engine is refitted, be
sure to renew the transmission front pump
seal, which will probably be damaged when
the converter comes out with the engine.
Either method is acceptable, but be prepared
for some fluid to leak from the torque
converter if it comes out of the transmission. If
you’re working on a vehicle with a manual
transmission, draw the engine forwards until
the input shaft is completely disengaged from
the clutch. Slowly raise the engine out of the
engine compartment. Check carefully to make
sure everything is disconnected.
26Remove the flywheel/driveplate (and
where applicable, the engine rear plate), and
mount the engine on an engine stand (see
illustration). Do not turn the M40 engine
upside-down (see Cautionin Section 4).
Refitting
27Check the engine and transmission
mountings. If they’re worn or damaged, renew
them.
28Refit the flywheel or driveplate (see
Chapter 2A). If you’re working on a manual
transmission vehicle, refit the clutch and
pressure plate (see Chapter 7A). Now is a
good time to fit a new clutch.
29If the torque converter came out with the
engine during removal, carefully refit the
converter into the transmission before the
engine is lowered into the vehicle.
30Carefully lower the engine into the engine
compartment - make sure the engine
mountings line up.
31If you’re working on an automatic
transmission vehicle, guide the torque
converter onto the crankshaft following the
procedure outlined in Chapter 7B.
32If you’re working on a manual
transmission vehicle, apply a dab of high-
melting-point grease to the input shaft, and
guide it into the clutch and crankshaft pilot
bearing until the bellhousing is flush with the
engine block.. Do not allow the weight of the
engine to hang on the input shaft.
33Refit the transmission-to-engine bolts,
and tighten them securely.
Caution: DO NOT use the bolts to
force the transmission and
engine together.
34Refit the remaining components in the
reverse order of removal.
35Add coolant, oil, power steering and
transmission fluid as needed.
2B•6 General engine overhaul procedures
5.26 Removing the engine rear plate -
M40 engine5.5 Label each wire before unplugging the
connector
If there’s any possibility of
confusion, make a sketch of
the engine compartment and
clearly label the lines, hoses
and wires.
It may be necessary to rock
the engine slightly, or to turn
the crankshaft, to allow the
input shaft splines to mate
with the clutch plate
Page 130 of 228
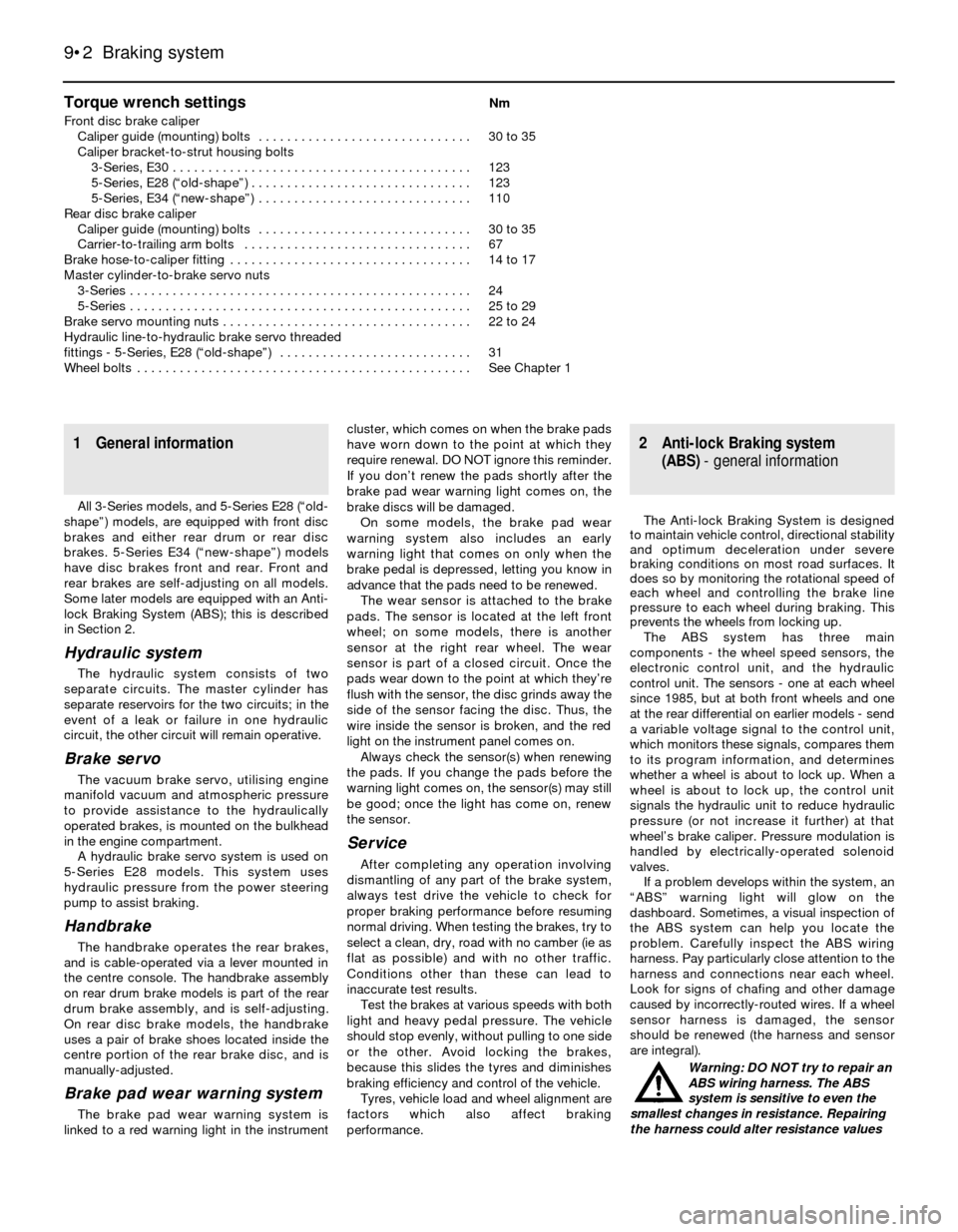
Torque wrench settingsNm
Front disc brake caliper
Caliper guide (mounting) bolts . . . . . . . . . . . . . . . . . . . . . . . . . . . . . . 30 to 35
Caliper bracket-to-strut housing bolts
3-Series, E30 . . . . . . . . . . . . . . . . . . . . . . . . . . . . . . . . . . . . . . . . . . 123
5-Series, E28 (“old-shape”) . . . . . . . . . . . . . . . . . . . . . . . . . . . . . . . 123
5-Series, E34 (“new-shape”) . . . . . . . . . . . . . . . . . . . . . . . . . . . . . . 110
Rear disc brake caliper
Caliper guide (mounting) bolts . . . . . . . . . . . . . . . . . . . . . . . . . . . . . . 30 to 35
Carrier-to-trailing arm bolts . . . . . . . . . . . . . . . . . . . . . . . . . . . . . . . . 67
Brake hose-to-caliper fitting . . . . . . . . . . . . . . . . . . . . . . . . . . . . . . . . . . 14 to 17
Master cylinder-to-brake servo nuts
3-Series . . . . . . . . . . . . . . . . . . . . . . . . . . . . . . . . . . . . . . . . . . . . . . . . 24
5-Series . . . . . . . . . . . . . . . . . . . . . . . . . . . . . . . . . . . . . . . . . . . . . . . . 25 to 29
Brake servo mounting nuts . . . . . . . . . . . . . . . . . . . . . . . . . . . . . . . . . . . 22 to 24
Hydraulic line-to-hydraulic brake servo threaded
fittings - 5-Series, E28 (“old-shape”) . . . . . . . . . . . . . . . . . . . . . . . . . . . 31
Wheel bolts . . . . . . . . . . . . . . . . . . . . . . . . . . . . . . . . . . . . . . . . . . . . . . . See Chapter 1
9•2 Braking system
1 General information
All 3-Series models, and 5-Series E28 (“old-
shape”) models, are equipped with front disc
brakes and either rear drum or rear disc
brakes. 5-Series E34 (“new-shape”) models
have disc brakes front and rear. Front and
rear brakes are self-adjusting on all models.
Some later models are equipped with an Anti-
lock Braking System (ABS); this is described
in Section 2.
Hydraulic system
The hydraulic system consists of two
separate circuits. The master cylinder has
separate reservoirs for the two circuits; in the
event of a leak or failure in one hydraulic
circuit, the other circuit will remain operative.
Brake servo
The vacuum brake servo, utilising engine
manifold vacuum and atmospheric pressure
to provide assistance to the hydraulically
operated brakes, is mounted on the bulkhead
in the engine compartment.
A hydraulic brake servo system is used on
5-Series E28 models. This system uses
hydraulic pressure from the power steering
pump to assist braking.
Handbrake
The handbrake operates the rear brakes,
and is cable-operated via a lever mounted in
the centre console. The handbrake assembly
on rear drum brake models is part of the rear
drum brake assembly, and is self-adjusting.
On rear disc brake models, the handbrake
uses a pair of brake shoes located inside the
centre portion of the rear brake disc, and is
manually-adjusted.
Brake pad wear warning system
The brake pad wear warning system is
linked to a red warning light in the instrumentcluster, which comes on when the brake pads
have worn down to the point at which they
require renewal. DO NOT ignore this reminder.
If you don’t renew the pads shortly after the
brake pad wear warning light comes on, the
brake discs will be damaged.
On some models, the brake pad wear
warning system also includes an early
warning light that comes on only when the
brake pedal is depressed, letting you know in
advance that the pads need to be renewed.
The wear sensor is attached to the brake
pads. The sensor is located at the left front
wheel; on some models, there is another
sensor at the right rear wheel. The wear
sensor is part of a closed circuit. Once the
pads wear down to the point at which they’re
flush with the sensor, the disc grinds away the
side of the sensor facing the disc. Thus, the
wire inside the sensor is broken, and the red
light on the instrument panel comes on.
Always check the sensor(s) when renewing
the pads. If you change the pads before the
warning light comes on, the sensor(s) may still
be good; once the light has come on, renew
the sensor.
Service
After completing any operation involving
dismantling of any part of the brake system,
always test drive the vehicle to check for
proper braking performance before resuming
normal driving. When testing the brakes, try to
select a clean, dry, road with no camber (ie as
flat as possible) and with no other traffic.
Conditions other than these can lead to
inaccurate test results.
Test the brakes at various speeds with both
light and heavy pedal pressure. The vehicle
should stop evenly, without pulling to one side
or the other. Avoid locking the brakes,
because this slides the tyres and diminishes
braking efficiency and control of the vehicle.
Tyres, vehicle load and wheel alignment are
factors which also affect braking
performance.
2 Anti-lock Braking system
(ABS)- general information
The Anti-lock Braking System is designed
to maintain vehicle control, directional stability
and optimum deceleration under severe
braking conditions on most road surfaces. It
does so by monitoring the rotational speed of
each wheel and controlling the brake line
pressure to each wheel during braking. This
prevents the wheels from locking up.
The ABS system has three main
components - the wheel speed sensors, the
electronic control unit, and the hydraulic
control unit. The sensors - one at each wheel
since 1985, but at both front wheels and one
at the rear differential on earlier models - send
a variable voltage signal to the control unit,
which monitors these signals, compares them
to its program information, and determines
whether a wheel is about to lock up. When a
wheel is about to lock up, the control unit
signals the hydraulic unit to reduce hydraulic
pressure (or not increase it further) at that
wheel’s brake caliper. Pressure modulation is
handled by electrically-operated solenoid
valves.
If a problem develops within the system, an
“ABS” warning light will glow on the
dashboard. Sometimes, a visual inspection of
the ABS system can help you locate the
problem. Carefully inspect the ABS wiring
harness. Pay particularly close attention to the
harness and connections near each wheel.
Look for signs of chafing and other damage
caused by incorrectly-routed wires. If a wheel
sensor harness is damaged, the sensor
should be renewed (the harness and sensor
are integral).
Warning: DO NOT try to repair an
ABS wiring harness. The ABS
system is sensitive to even the
smallest changes in resistance. Repairing
the harness could alter resistance values
Page 139 of 228
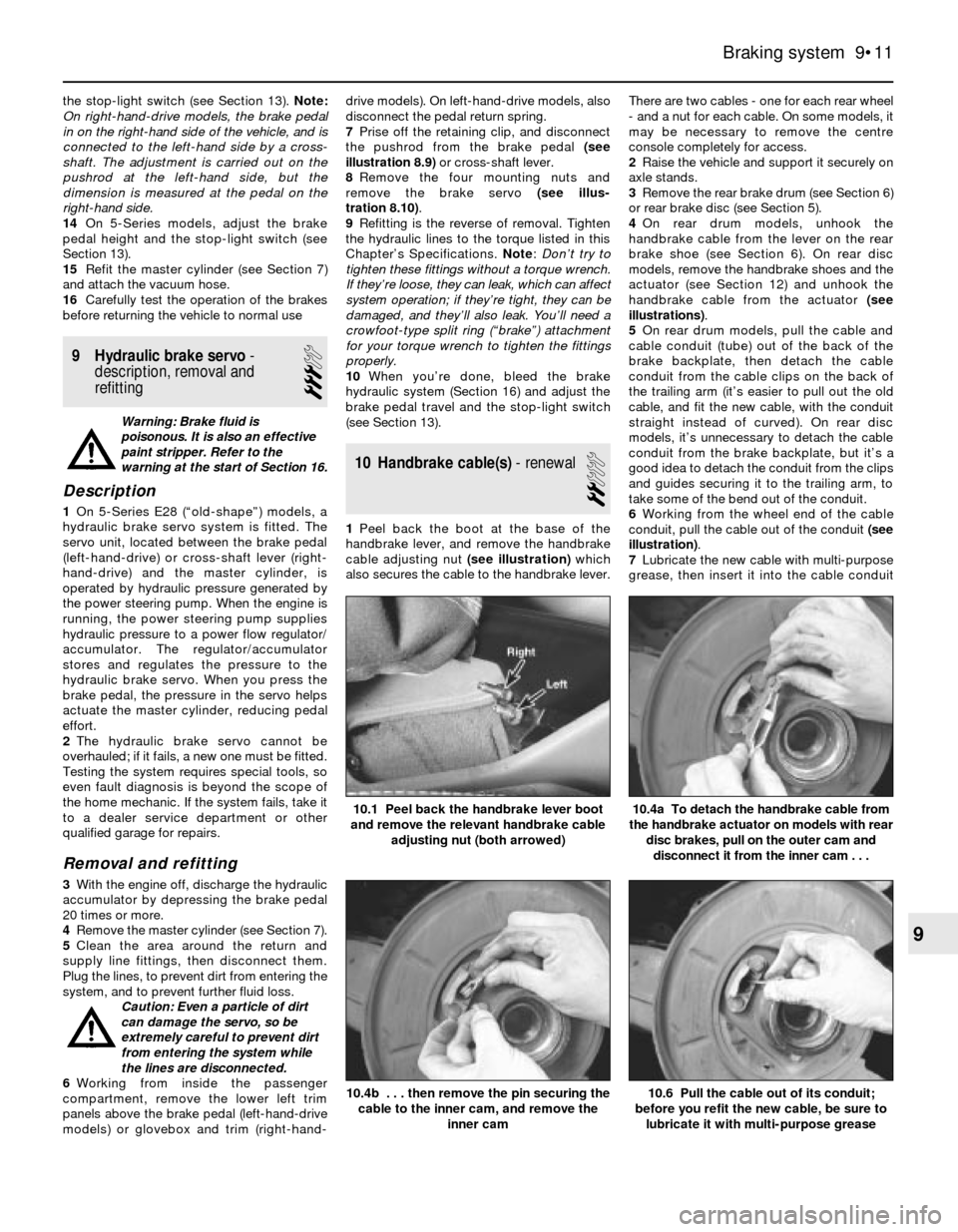
the stop-light switch (see Section 13). Note:
On right-hand-drive models, the brake pedal
in on the right-hand side of the vehicle, and is
connected to the left-hand side by a cross-
shaft. The adjustment is carried out on the
pushrod at the left-hand side, but the
dimension is measured at the pedal on the
right-hand side.
14On 5-Series models, adjust the brake
pedal height and the stop-light switch (see
Section 13).
15Refit the master cylinder (see Section 7)
and attach the vacuum hose.
16Carefully test the operation of the brakes
before returning the vehicle to normal use
9 Hydraulic brake servo-
description, removal and
refitting
3
Warning: Brake fluid is
poisonous. It is also an effective
paint stripper. Refer to the
warning at the start of Section 16.
Description
1On 5-Series E28 (“old-shape”) models, a
hydraulic brake servo system is fitted. The
servo unit, located between the brake pedal
(left-hand-drive) or cross-shaft lever (right-
hand-drive) and the master cylinder, is
operated by hydraulic pressure generated by
the power steering pump. When the engine is
running, the power steering pump supplies
hydraulic pressure to a power flow regulator/
accumulator. The regulator/accumulator
stores and regulates the pressure to the
hydraulic brake servo. When you press the
brake pedal, the pressure in the servo helps
actuate the master cylinder, reducing pedal
effort.
2The hydraulic brake servo cannot be
overhauled; if it fails, a new one must be fitted.
Testing the system requires special tools, so
even fault diagnosis is beyond the scope of
the home mechanic. If the system fails, take it
to a dealer service department or other
qualified garage for repairs.
Removal and refitting
3With the engine off, discharge the hydraulic
accumulator by depressing the brake pedal
20 times or more.
4Remove the master cylinder (see Section 7).
5Clean the area around the return and
supply line fittings, then disconnect them.
Plug the lines, to prevent dirt from entering the
system, and to prevent further fluid loss.
Caution: Even a particle of dirt
can damage the servo, so be
extremely careful to prevent dirt
from entering the system while
the lines are disconnected.
6Working from inside the passenger
compartment, remove the lower left trim
panels above the brake pedal (left-hand-drive
models) or glovebox and trim (right-hand-drive models). On left-hand-drive models, also
disconnect the pedal return spring.
7Prise off the retaining clip, and disconnect
the pushrod from the brake pedal (see
illustration 8.9) or cross-shaft lever.
8Remove the four mounting nuts and
remove the brake servo (see illus-
tration 8.10).
9Refitting is the reverse of removal. Tighten
the hydraulic lines to the torque listed in this
Chapter’s Specifications. Note:Don’t try to
tighten these fittings without a torque wrench.
If they’re loose, they can leak, which can affect
system operation; if they’re tight, they can be
damaged, and they’ll also leak. You’ll need a
crowfoot-type split ring (“brake”) attachment
for your torque wrench to tighten the fittings
properly.
10When you’re done, bleed the brake
hydraulic system (Section 16) and adjust the
brake pedal travel and the stop-light switch
(see Section 13).
10 Handbrake cable(s)- renewal
2
1Peel back the boot at the base of the
handbrake lever, and remove the handbrake
cable adjusting nut (see illustration)which
also secures the cable to the handbrake lever.There are two cables - one for each rear wheel
- and a nut for each cable. On some models, it
may be necessary to remove the centre
console completely for access.
2Raise the vehicle and support it securely on
axle stands.
3Remove the rear brake drum (see Section 6)
or rear brake disc (see Section 5).
4On rear drum models, unhook the
handbrake cable from the lever on the rear
brake shoe (see Section 6). On rear disc
models, remove the handbrake shoes and the
actuator (see Section 12) and unhook the
handbrake cable from the actuator (see
illustrations).
5On rear drum models, pull the cable and
cable conduit (tube) out of the back of the
brake backplate, then detach the cable
conduit from the cable clips on the back of
the trailing arm (it’s easier to pull out the old
cable, and fit the new cable, with the conduit
straight instead of curved). On rear disc
models, it’s unnecessary to detach the cable
conduit from the brake backplate, but it’s a
good idea to detach the conduit from the clips
and guides securing it to the trailing arm, to
take some of the bend out of the conduit.
6Working from the wheel end of the cable
conduit, pull the cable out of the conduit (see
illustration).
7Lubricate the new cable with multi-purpose
grease, then insert it into the cable conduit
Braking system 9•11
10.1 Peel back the handbrake lever boot
and remove the relevant handbrake cable
adjusting nut (both arrowed)
10.6 Pull the cable out of its conduit;
before you refit the new cable, be sure to
lubricate it with multi-purpose grease10.4b . . . then remove the pin securing the
cable to the inner cam, and remove the
inner cam
10.4a To detach the handbrake cable from
the handbrake actuator on models with rear
disc brakes, pull on the outer cam and
disconnect it from the inner cam . . .
9
Page 143 of 228
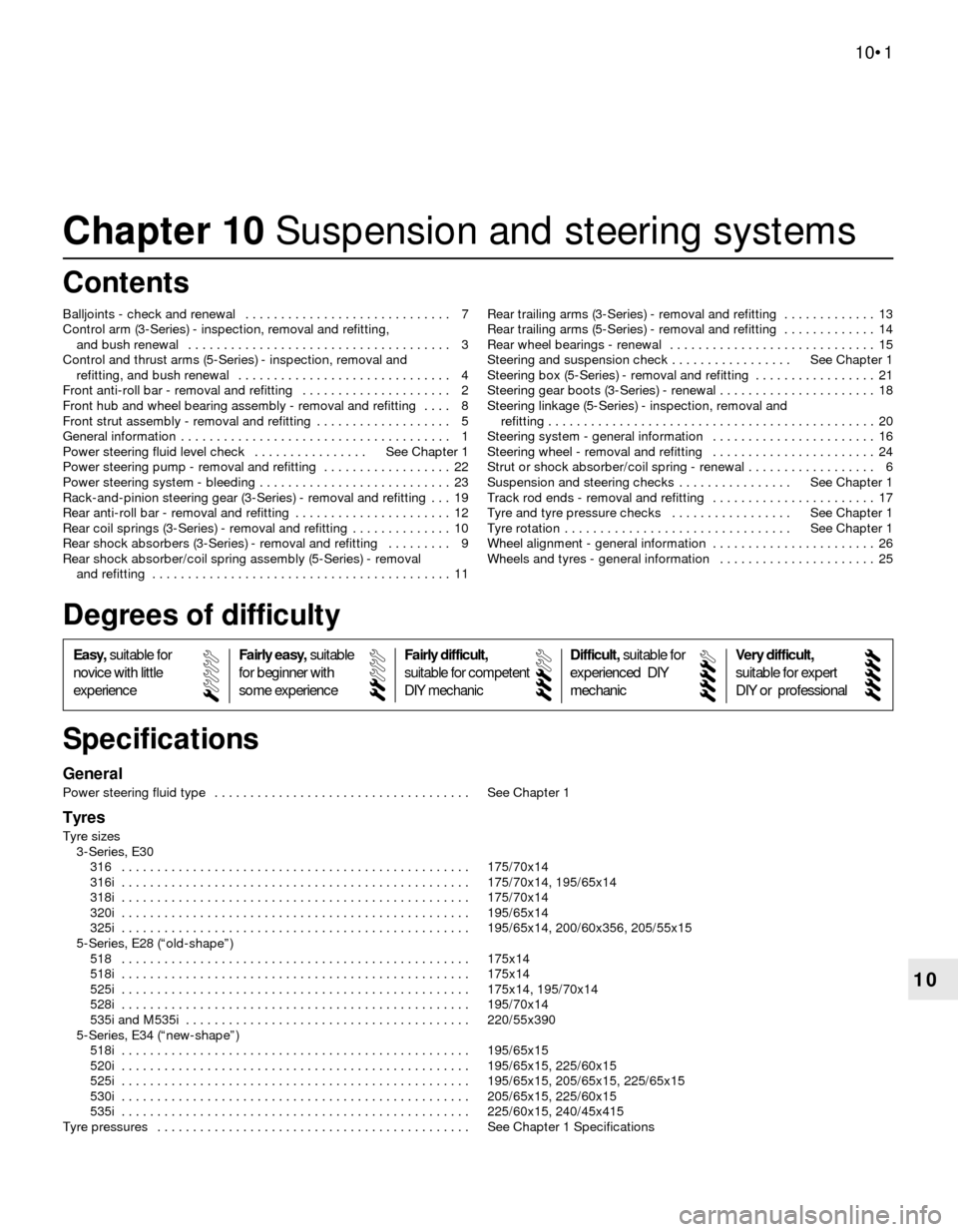
10
General
Power steering fluid type . . . . . . . . . . . . . . . . . . . . . . . . . . . . . . . . . . . . See Chapter 1
Tyres
Tyre sizes
3-Series, E30
316 . . . . . . . . . . . . . . . . . . . . . . . . . . . . . . . . . . . . . . . . . . . . . . . . . 175/70x14
316i . . . . . . . . . . . . . . . . . . . . . . . . . . . . . . . . . . . . . . . . . . . . . . . . . 175/70x14, 195/65x14
318i . . . . . . . . . . . . . . . . . . . . . . . . . . . . . . . . . . . . . . . . . . . . . . . . . 175/70x14
320i . . . . . . . . . . . . . . . . . . . . . . . . . . . . . . . . . . . . . . . . . . . . . . . . . 195/65x14
325i . . . . . . . . . . . . . . . . . . . . . . . . . . . . . . . . . . . . . . . . . . . . . . . . . 195/65x14, 200/60x356, 205/55x15
5-Series, E28 (“old-shape”)
518 . . . . . . . . . . . . . . . . . . . . . . . . . . . . . . . . . . . . . . . . . . . . . . . . . 175x14
518i . . . . . . . . . . . . . . . . . . . . . . . . . . . . . . . . . . . . . . . . . . . . . . . . . 175x14
525i . . . . . . . . . . . . . . . . . . . . . . . . . . . . . . . . . . . . . . . . . . . . . . . . . 175x14, 195/70x14
528i . . . . . . . . . . . . . . . . . . . . . . . . . . . . . . . . . . . . . . . . . . . . . . . . . 195/70x14
535i and M535i . . . . . . . . . . . . . . . . . . . . . . . . . . . . . . . . . . . . . . . . 220/55x390
5-Series, E34 (“new-shape”)
518i . . . . . . . . . . . . . . . . . . . . . . . . . . . . . . . . . . . . . . . . . . . . . . . . . 195/65x15
520i . . . . . . . . . . . . . . . . . . . . . . . . . . . . . . . . . . . . . . . . . . . . . . . . . 195/65x15, 225/60x15
525i . . . . . . . . . . . . . . . . . . . . . . . . . . . . . . . . . . . . . . . . . . . . . . . . . 195/65x15, 205/65x15, 225/65x15
530i . . . . . . . . . . . . . . . . . . . . . . . . . . . . . . . . . . . . . . . . . . . . . . . . . 205/65x15, 225/60x15
535i . . . . . . . . . . . . . . . . . . . . . . . . . . . . . . . . . . . . . . . . . . . . . . . . . 225/60x15, 240/45x415
Tyre pressures . . . . . . . . . . . . . . . . . . . . . . . . . . . . . . . . . . . . . . . . . . . . See Chapter 1 Specifications
Chapter 10 Suspension and steering systems
Balljoints - check and renewal . . . . . . . . . . . . . . . . . . . . . . . . . . . . . 7
Control arm (3-Series) - inspection, removal and refitting,
and bush renewal . . . . . . . . . . . . . . . . . . . . . . . . . . . . . . . . . . . . . 3
Control and thrust arms (5-Series) - inspection, removal and
refitting, and bush renewal . . . . . . . . . . . . . . . . . . . . . . . . . . . . . . 4
Front anti-roll bar - removal and refitting . . . . . . . . . . . . . . . . . . . . . 2
Front hub and wheel bearing assembly - removal and refitting . . . . 8
Front strut assembly - removal and refitting . . . . . . . . . . . . . . . . . . . 5
General information . . . . . . . . . . . . . . . . . . . . . . . . . . . . . . . . . . . . . . 1
Power steering fluid level check . . . . . . . . . . . . . . . . See Chapter 1
Power steering pump - removal and refitting . . . . . . . . . . . . . . . . . . 22
Power steering system - bleeding . . . . . . . . . . . . . . . . . . . . . . . . . . . 23
Rack-and-pinion steering gear (3-Series) - removal and refitting . . . 19
Rear anti-roll bar - removal and refitting . . . . . . . . . . . . . . . . . . . . . . 12
Rear coil springs (3-Series) - removal and refitting . . . . . . . . . . . . . . 10
Rear shock absorbers (3-Series) - removal and refitting . . . . . . . . . 9
Rear shock absorber/coil spring assembly (5-Series) - removal
and refitting . . . . . . . . . . . . . . . . . . . . . . . . . . . . . . . . . . . . . . . . . . 11Rear trailing arms (3-Series) - removal and refitting . . . . . . . . . . . . . 13
Rear trailing arms (5-Series) - removal and refitting . . . . . . . . . . . . . 14
Rear wheel bearings - renewal . . . . . . . . . . . . . . . . . . . . . . . . . . . . . 15
Steering and suspension check . . . . . . . . . . . . . . . . . See Chapter 1
Steering box (5-Series) - removal and refitting . . . . . . . . . . . . . . . . . 21
Steering gear boots (3-Series) - renewal . . . . . . . . . . . . . . . . . . . . . . 18
Steering linkage (5-Series) - inspection, removal and
refitting . . . . . . . . . . . . . . . . . . . . . . . . . . . . . . . . . . . . . . . . . . . . . . 20
Steering system - general information . . . . . . . . . . . . . . . . . . . . . . . 16
Steering wheel - removal and refitting . . . . . . . . . . . . . . . . . . . . . . . 24
Strut or shock absorber/coil spring - renewal . . . . . . . . . . . . . . . . . . 6
Suspension and steering checks . . . . . . . . . . . . . . . . See Chapter 1
Track rod ends - removal and refitting . . . . . . . . . . . . . . . . . . . . . . . 17
Tyre and tyre pressure checks . . . . . . . . . . . . . . . . . See Chapter 1
Tyre rotation . . . . . . . . . . . . . . . . . . . . . . . . . . . . . . . . See Chapter 1
Wheel alignment - general information . . . . . . . . . . . . . . . . . . . . . . . 26
Wheels and tyres - general information . . . . . . . . . . . . . . . . . . . . . . 25
10•1
Easy,suitable for
novice with little
experienceFairly easy,suitable
for beginner with
some experienceFairly difficult,
suitable for competent
DIY mechanic
Difficult,suitable for
experienced DIY
mechanicVery difficult,
suitable for expert
DIY or professional
Degrees of difficulty
Specifications Contents
Page 144 of 228
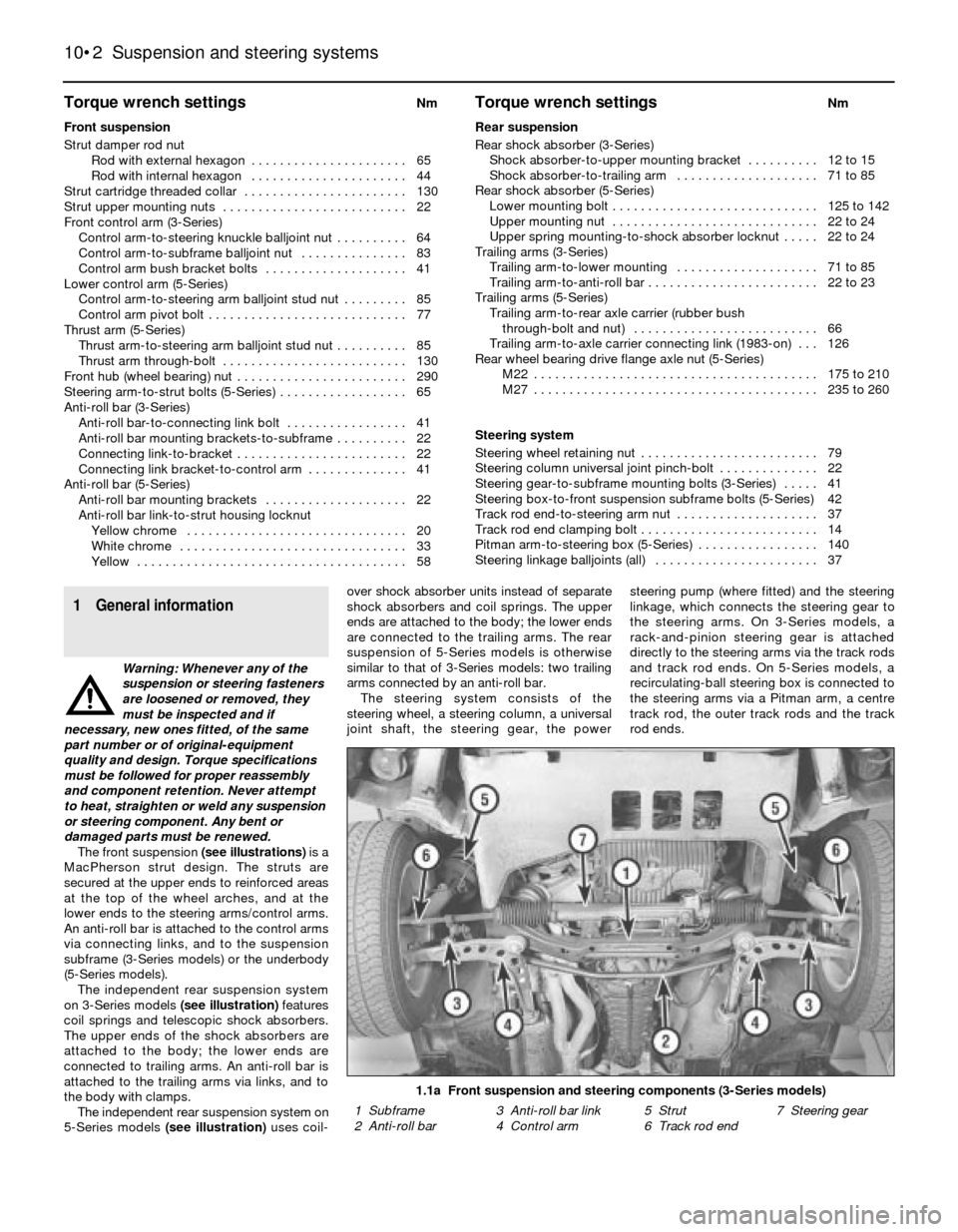
Torque wrench settingsNm
Front suspension
Strut damper rod nut
Rod with external hexagon . . . . . . . . . . . . . . . . . . . . . . 65
Rod with internal hexagon . . . . . . . . . . . . . . . . . . . . . . 44
Strut cartridge threaded collar . . . . . . . . . . . . . . . . . . . . . . . 130
Strut upper mounting nuts . . . . . . . . . . . . . . . . . . . . . . . . . . 22
Front control arm (3-Series)
Control arm-to-steering knuckle balljoint nut . . . . . . . . . . 64
Control arm-to-subframe balljoint nut . . . . . . . . . . . . . . . 83
Control arm bush bracket bolts . . . . . . . . . . . . . . . . . . . . 41
Lower control arm (5-Series)
Control arm-to-steering arm balljoint stud nut . . . . . . . . . 85
Control arm pivot bolt . . . . . . . . . . . . . . . . . . . . . . . . . . . . 77
Thrust arm (5-Series)
Thrust arm-to-steering arm balljoint stud nut . . . . . . . . . . 85
Thrust arm through-bolt . . . . . . . . . . . . . . . . . . . . . . . . . . 130
Front hub (wheel bearing) nut . . . . . . . . . . . . . . . . . . . . . . . . 290
Steering arm-to-strut bolts (5-Series) . . . . . . . . . . . . . . . . . . 65
Anti-roll bar (3-Series)
Anti-roll bar-to-connecting link bolt . . . . . . . . . . . . . . . . . 41
Anti-roll bar mounting brackets-to-subframe . . . . . . . . . . 22
Connecting link-to-bracket . . . . . . . . . . . . . . . . . . . . . . . . 22
Connecting link bracket-to-control arm . . . . . . . . . . . . . . 41
Anti-roll bar (5-Series)
Anti-roll bar mounting brackets . . . . . . . . . . . . . . . . . . . . 22
Anti-roll bar link-to-strut housing locknut
Yellow chrome . . . . . . . . . . . . . . . . . . . . . . . . . . . . . . . 20
White chrome . . . . . . . . . . . . . . . . . . . . . . . . . . . . . . . . 33
Yellow . . . . . . . . . . . . . . . . . . . . . . . . . . . . . . . . . . . . . . 58
10•2 Suspension and steering systems
Torque wrench settingsNm
Rear suspension
Rear shock absorber (3-Series)
Shock absorber-to-upper mounting bracket . . . . . . . . . . 12 to 15
Shock absorber-to-trailing arm . . . . . . . . . . . . . . . . . . . . 71 to 85
Rear shock absorber (5-Series)
Lower mounting bolt . . . . . . . . . . . . . . . . . . . . . . . . . . . . . 125 to 142
Upper mounting nut . . . . . . . . . . . . . . . . . . . . . . . . . . . . . 22 to 24
Upper spring mounting-to-shock absorber locknut . . . . . 22 to 24
Trailing arms (3-Series)
Trailing arm-to-lower mounting . . . . . . . . . . . . . . . . . . . . 71 to 85
Trailing arm-to-anti-roll bar . . . . . . . . . . . . . . . . . . . . . . . . 22 to 23
Trailing arms (5-Series)
Trailing arm-to-rear axle carrier (rubber bush
through-bolt and nut) . . . . . . . . . . . . . . . . . . . . . . . . . . 66
Trailing arm-to-axle carrier connecting link (1983-on) . . . 126
Rear wheel bearing drive flange axle nut (5-Series)
M22 . . . . . . . . . . . . . . . . . . . . . . . . . . . . . . . . . . . . . . . . 175 to 210
M27 . . . . . . . . . . . . . . . . . . . . . . . . . . . . . . . . . . . . . . . . 235 to 260
Steering system
Steering wheel retaining nut . . . . . . . . . . . . . . . . . . . . . . . . . 79
Steering column universal joint pinch-bolt . . . . . . . . . . . . . . 22
Steering gear-to-subframe mounting bolts (3-Series) . . . . . 41
Steering box-to-front suspension subframe bolts (5-Series) 42
Track rod end-to-steering arm nut . . . . . . . . . . . . . . . . . . . . 37
Track rod end clamping bolt . . . . . . . . . . . . . . . . . . . . . . . . . 14
Pitman arm-to-steering box (5-Series) . . . . . . . . . . . . . . . . . 140
Steering linkage balljoints (all) . . . . . . . . . . . . . . . . . . . . . . . 37
1 General information
Warning: Whenever any of the
suspension or steering fasteners
are loosened or removed, they
must be inspected and if
necessary, new ones fitted, of the same
part number or of original-equipment
quality and design. Torque specifications
must be followed for proper reassembly
and component retention. Never attempt
to heat, straighten or weld any suspension
or steering component. Any bent or
damaged parts must be renewed.
The front suspension (see illustrations)is a
MacPherson strut design. The struts are
secured at the upper ends to reinforced areas
at the top of the wheel arches, and at the
lower ends to the steering arms/control arms.
An anti-roll bar is attached to the control arms
via connecting links, and to the suspension
subframe (3-Series models) or the underbody
(5-Series models).
The independent rear suspension system
on 3-Series models (see illustration)features
coil springs and telescopic shock absorbers.
The upper ends of the shock absorbers are
attached to the body; the lower ends are
connected to trailing arms. An anti-roll bar is
attached to the trailing arms via links, and to
the body with clamps.
The independent rear suspension system on
5-Series models (see illustration)uses coil-over shock absorber units instead of separate
shock absorbers and coil springs. The upper
ends are attached to the body; the lower ends
are connected to the trailing arms. The rear
suspension of 5-Series models is otherwise
similar to that of 3-Series models: two trailing
arms connected by an anti-roll bar.
The steering system consists of the
steering wheel, a steering column, a universal
joint shaft, the steering gear, the powersteering pump (where fitted) and the steering
linkage, which connects the steering gear to
the steering arms. On 3-Series models, a
rack-and-pinion steering gear is attached
directly to the steering arms via the track rods
and track rod ends. On 5-Series models, a
recirculating-ball steering box is connected to
the steering arms via a Pitman arm, a centre
track rod, the outer track rods and the track
rod ends.
1.1a Front suspension and steering components (3-Series models)
1 Subframe 3 Anti-roll bar link 5 Strut 7 Steering gear
2 Anti-roll bar 4 Control arm 6 Track rod end
Page 154 of 228
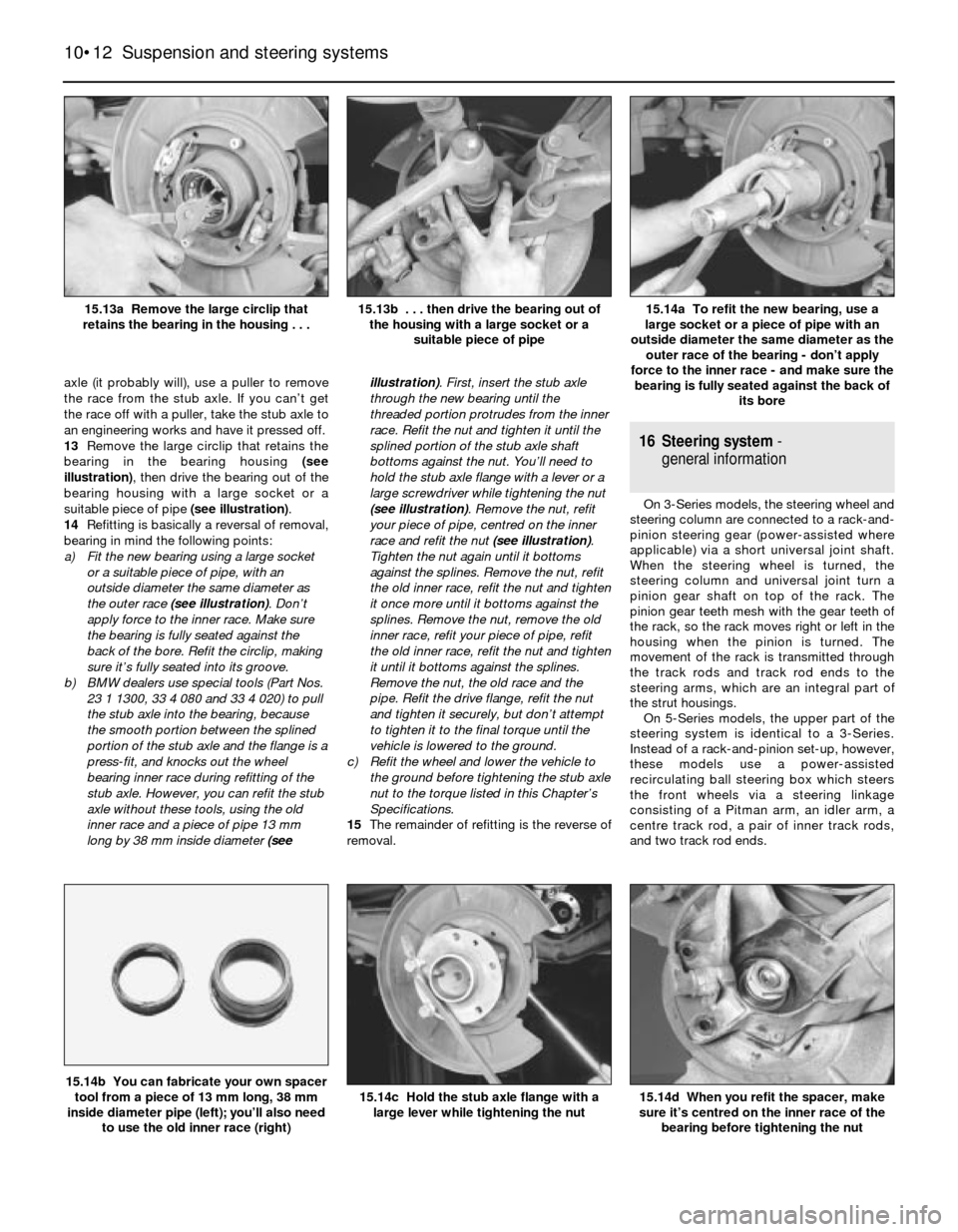
axle (it probably will), use a puller to remove
the race from the stub axle. If you can’t get
the race off with a puller, take the stub axle to
an engineering works and have it pressed off.
13Remove the large circlip that retains the
bearing in the bearing housing (see
illustration), then drive the bearing out of the
bearing housing with a large socket or a
suitable piece of pipe (see illustration).
14Refitting is basically a reversal of removal,
bearing in mind the following points:
a) Fit the new bearing using a large socket
or a suitable piece of pipe, with an
outside diameter the same diameter as
the outer race (see illustration). Don’t
apply force to the inner race. Make sure
the bearing is fully seated against the
back of the bore. Refit the circlip, making
sure it’s fully seated into its groove.
b) BMW dealers use special tools (Part Nos.
23 1 1300, 33 4 080 and 33 4 020) to pull
the stub axle into the bearing, because
the smooth portion between the splined
portion of the stub axle and the flange is a
press-fit, and knocks out the wheel
bearing inner race during refitting of the
stub axle. However, you can refit the stub
axle without these tools, using the old
inner race and a piece of pipe 13 mm
long by 38 mm inside diameter (seeillustration). First, insert the stub axle
through the new bearing until the
threaded portion protrudes from the inner
race. Refit the nut and tighten it until the
splined portion of the stub axle shaft
bottoms against the nut. You’ll need to
hold the stub axle flange with a lever or a
large screwdriver while tightening the nut
(see illustration). Remove the nut, refit
your piece of pipe, centred on the inner
race and refit the nut (see illustration).
Tighten the nut again until it bottoms
against the splines. Remove the nut, refit
the old inner race, refit the nut and tighten
it once more until it bottoms against the
splines. Remove the nut, remove the old
inner race, refit your piece of pipe, refit
the old inner race, refit the nut and tighten
it until it bottoms against the splines.
Remove the nut, the old race and the
pipe. Refit the drive flange, refit the nut
and tighten it securely, but don’t attempt
to tighten it to the final torque until the
vehicle is lowered to the ground.
c) Refit the wheel and lower the vehicle to
the ground before tightening the stub axle
nut to the torque listed in this Chapter’s
Specifications.
15The remainder of refitting is the reverse of
removal.
16 Steering system-
general information
On 3-Series models, the steering wheel and
steering column are connected to a rack-and-
pinion steering gear (power-assisted where
applicable) via a short universal joint shaft.
When the steering wheel is turned, the
steering column and universal joint turn a
pinion gear shaft on top of the rack. The
pinion gear teeth mesh with the gear teeth of
the rack, so the rack moves right or left in the
housing when the pinion is turned. The
movement of the rack is transmitted through
the track rods and track rod ends to the
steering arms, which are an integral part of
the strut housings.
On 5-Series models, the upper part of the
steering system is identical to a 3-Series.
Instead of a rack-and-pinion set-up, however,
these models use a power-assisted
recirculating ball steering box which steers
the front wheels via a steering linkage
consisting of a Pitman arm, an idler arm, a
centre track rod, a pair of inner track rods,
and two track rod ends.
10•12 Suspension and steering systems
15.14d When you refit the spacer, make
sure it’s centred on the inner race of the
bearing before tightening the nut15.14c Hold the stub axle flange with a
large lever while tightening the nut15.14b You can fabricate your own spacer
tool from a piece of 13 mm long, 38 mm
inside diameter pipe (left); you’ll also need
to use the old inner race (right)
15.14a To refit the new bearing, use a
large socket or a piece of pipe with an
outside diameter the same diameter as the
outer race of the bearing - don’t apply
force to the inner race - and make sure the
bearing is fully seated against the back of
its bore15.13b . . . then drive the bearing out of
the housing with a large socket or a
suitable piece of pipe15.13a Remove the large circlip that
retains the bearing in the housing . . .
Page 155 of 228
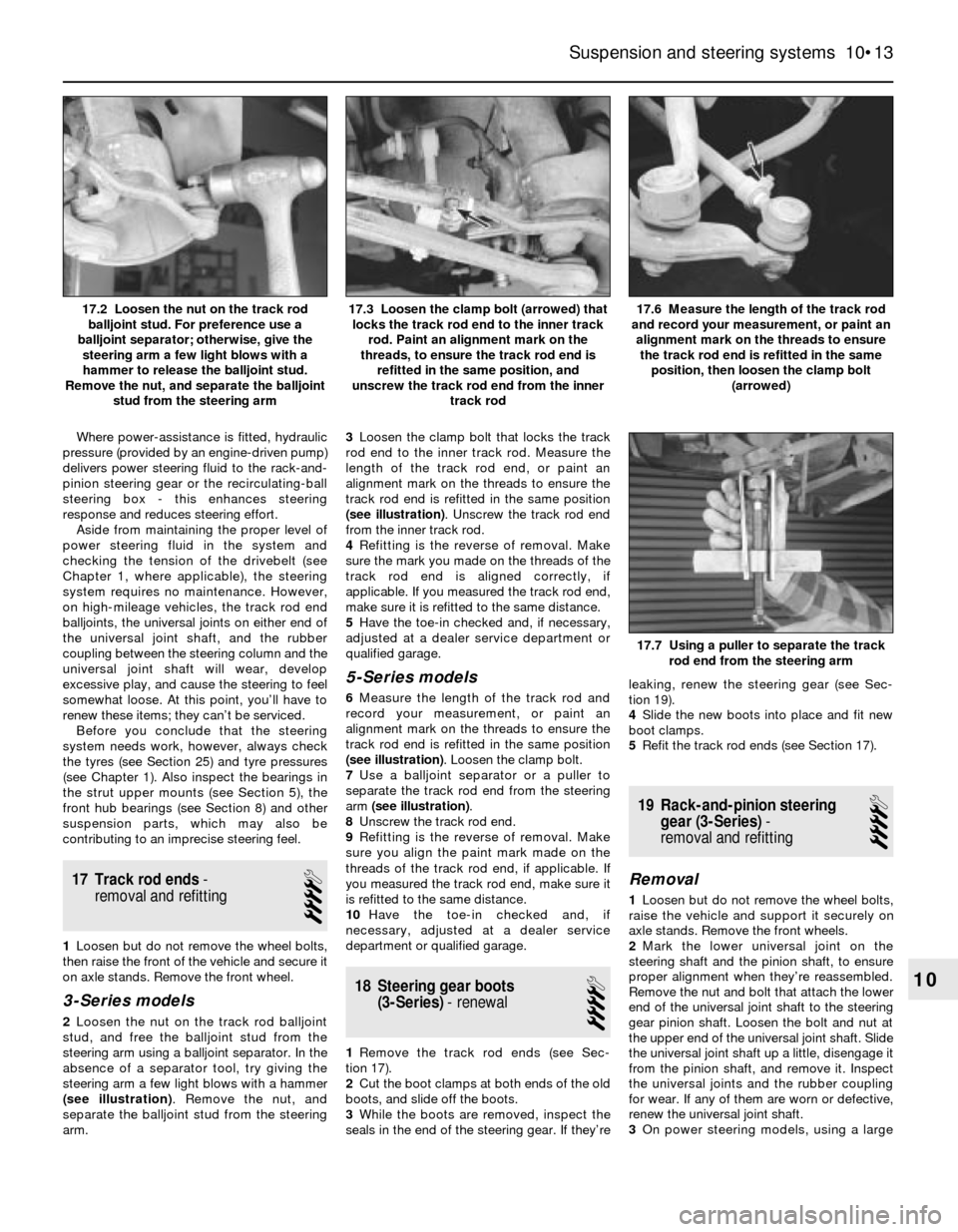
Where power-assistance is fitted, hydraulic
pressure (provided by an engine-driven pump)
delivers power steering fluid to the rack-and-
pinion steering gear or the recirculating-ball
steering box - this enhances steering
response and reduces steering effort.
Aside from maintaining the proper level of
power steering fluid in the system and
checking the tension of the drivebelt (see
Chapter 1, where applicable), the steering
system requires no maintenance. However,
on high-mileage vehicles, the track rod end
balljoints, the universal joints on either end of
the universal joint shaft, and the rubber
coupling between the steering column and the
universal joint shaft will wear, develop
excessive play, and cause the steering to feel
somewhat loose. At this point, you’ll have to
renew these items; they can’t be serviced.
Before you conclude that the steering
system needs work, however, always check
the tyres (see Section 25) and tyre pressures
(see Chapter 1). Also inspect the bearings in
the strut upper mounts (see Section 5), the
front hub bearings (see Section 8) and other
suspension parts, which may also be
contributing to an imprecise steering feel.
17 Track rod ends-
removal and refitting
4
1Loosen but do not remove the wheel bolts,
then raise the front of the vehicle and secure it
on axle stands. Remove the front wheel.
3-Series models
2Loosen the nut on the track rod balljoint
stud, and free the balljoint stud from the
steering arm using a balljoint separator. In the
absence of a separator tool, try giving the
steering arm a few light blows with a hammer
(see illustration). Remove the nut, and
separate the balljoint stud from the steering
arm.3Loosen the clamp bolt that locks the track
rod end to the inner track rod. Measure the
length of the track rod end, or paint an
alignment mark on the threads to ensure the
track rod end is refitted in the same position
(see illustration). Unscrew the track rod end
from the inner track rod.
4Refitting is the reverse of removal. Make
sure the mark you made on the threads of the
track rod end is aligned correctly, if
applicable. If you measured the track rod end,
make sure it is refitted to the same distance.
5Have the toe-in checked and, if necessary,
adjusted at a dealer service department or
qualified garage.
5-Series models
6Measure the length of the track rod and
record your measurement, or paint an
alignment mark on the threads to ensure the
track rod end is refitted in the same position
(see illustration). Loosen the clamp bolt.
7Use a balljoint separator or a puller to
separate the track rod end from the steering
arm (see illustration).
8Unscrew the track rod end.
9Refitting is the reverse of removal. Make
sure you align the paint mark made on the
threads of the track rod end, if applicable. If
you measured the track rod end, make sure it
is refitted to the same distance.
10Have the toe-in checked and, if
necessary, adjusted at a dealer service
department or qualified garage.
18 Steering gear boots
(3-Series)- renewal
4
1Remove the track rod ends (see Sec-
tion 17).
2Cut the boot clamps at both ends of the old
boots, and slide off the boots.
3While the boots are removed, inspect the
seals in the end of the steering gear. If they’releaking, renew the steering gear (see Sec-
tion 19).
4Slide the new boots into place and fit new
boot clamps.
5Refit the track rod ends (see Section 17).
19 Rack-and-pinion steering
gear (3-Series)-
removal and refitting
4
Removal
1Loosen but do not remove the wheel bolts,
raise the vehicle and support it securely on
axle stands. Remove the front wheels.
2Mark the lower universal joint on the
steering shaft and the pinion shaft, to ensure
proper alignment when they’re reassembled.
Remove the nut and bolt that attach the lower
end of the universal joint shaft to the steering
gear pinion shaft. Loosen the bolt and nut at
the upper end of the universal joint shaft. Slide
the universal joint shaft up a little, disengage it
from the pinion shaft, and remove it. Inspect
the universal joints and the rubber coupling
for wear. If any of them are worn or defective,
renew the universal joint shaft.
3On power steering models, using a large
Suspension and steering systems 10•13
17.6 Measure the length of the track rod
and record your measurement, or paint an
alignment mark on the threads to ensure
the track rod end is refitted in the same
position, then loosen the clamp bolt
(arrowed)17.3 Loosen the clamp bolt (arrowed) that
locks the track rod end to the inner track
rod. Paint an alignment mark on the
threads, to ensure the track rod end is
refitted in the same position, and
unscrew the track rod end from the inner
track rod17.2 Loosen the nut on the track rod
balljoint stud. For preference use a
balljoint separator; otherwise, give the
steering arm a few light blows with a
hammer to release the balljoint stud.
Remove the nut, and separate the balljoint
stud from the steering arm
17.7 Using a puller to separate the track
rod end from the steering arm
10
Page 156 of 228

syringe or hand pump, empty the power
steering fluid reservoir.
4On power steering models, remove the
banjo bolts and disconnect the power
steering pressure and return lines from the
steering gear. Place a container under the
lines to catch spilled fluid. Plug the lines to
prevent excessive fluid loss and
contamination. Discard the sealing washers
(new ones should be used when
reassembling).
5Disconnect the track rod ends from the
steering arms (see Section 17).
6Remove the nuts and bolts from the
steering gear mounting brackets (see
illustration). Discard the old nuts.
7Withdraw the assembly from beneath the
vehicle. Take care not to damage the steering
gear boots.
Refitting
8Refitting is the reverse of removal. Make
sure the marks you made on the lower
universal joint and the pinion shaft are aligned
before you tighten the clamping bolts for the
upper and lower universal joints. Use new
self-locking nuts on the steering rackmounting bolts, and new sealing washers on
the hydraulic line fittings. Tighten the
mounting bolts, the track rod end nuts and the
universal joint shaft clamping bolts to the
torque values listed in this Chapter’s Specifi-
cations.
9Lower the vehicle to the ground.
10On power steering models, fill the
reservoir with the recommended fluid (see
Chapter 1) and bleed the power steering
system (see Section 23).
11It’s a good idea to have the front wheel
alignment checked by a dealer service
department or qualified garage.
20 Steering linkage (5-Series)-
inspection, removal and
refitting
4
Inspection
1Raise the vehicle and place it securely on
axle stands.
2Firmly grasp each front tyre at the top and
bottom, then at the front and rear, and check
for play in the steering linkage by rocking the
tyre back and forth. There should be little or
no play in any of the linkage balljoints. Inspect
the Pitman arm, the idler arm, the centre track
rod, the inner track rods, the track rod ends
and the steering arms for any obvious
damage. Try forcing the linkage parts in
opposite directions from one another. There
should be no play between any of them. If any
of the parts are bent or damaged in any way,
or if any of the balljoints are worn, renew the
parts concerned.
Removal
3Before dismantling the steering linkage,
obtain a suitable balljoint separator. A two-jaw
puller or a wedge-type tool will work (although
the wedge-type tends to tear the balljoint
boots). Sometimes, you can also jar a balljoint
taper pin free from its eye by striking opposite
sides of the eye simultaneously with two large
hammers, but the space available to do this is
limited, and the balljoint stud sometimessticks to the eye because of rust and dirt.
There is also a risk of damaging the
component being struck.
4To remove the outer track rods, disconnect
the track rod ends from the steering arms (see
Section 17). Remove the nut that attaches the
balljoint on the inner end of each outer track
rod to the centre track rod (see illustration).
Using a balljoint separator, disconnect the
outer track rods from the centre track rod. If
you’re renewing the balljoint at either end of
the outer track rods, paint or scribe alignment
marks on the threads to mark their respective
positions as a guide to adjustment during
reassembly (see illustration 17.3).
5To remove the centre track rod, remove the
nuts that attach the centre track rod balljoints
to the Pitman arm and the idler arm, and use a
balljoint separator to disconnect the balljoints
from the two arms.
6To remove the Pitman arm, you’ll have to
remove the steering box first (see Section 21).
Look for match marks between the sector
shaft and arm. If there aren’t any, scribe a
mark across the bottom face of both parts.
Remove the Pitman arm pinch-bolt and nut,
then remove the arm with a puller.
7To unbolt the idler arm, first remove the
small cover bolted to the top of the subframe
crossmember. Put a spanner on the bolt, and
remove the nut recessed into the underside of
the subframe crossmember (see illustration).
Check the idler arm rubber bush for wear. If
it’s damaged or worn, renew it.
8Check each balljoint for excessive play or
stiffness, and for split or deteriorated rubber
dust boots. Renew all worn or damaged
balljoints. The inner and outer track rod ends
on the outer track rods can be renewed
individually; if either balljoint on the centre
track rod is damaged or worn, you must
renew the centre track rod.
Refitting
9Refitting is the reverse of the removal
procedure, but observe the following points:
a) Realign the match marks on the Pitman
arm and the steering box sector shaft
when reassembling them.
b) If you’re fitting new inner or outer track
rod ends on the outer track rods, position
them so that the match marks made
during dismantling are aligned, and make
sure they are equally spaced on each
side.
c) Position the track rod end balljoint studs
on the outer track rods at an angle of 90°
to each other.
d) Make sure the left and right outer track
rods are equal in length when they are
fitted.
e) Tighten all retaining bolts to the torque
values listed in this Chapter’s Specifi-
cations.
f) When reassembly of the linkage is
complete, have the front wheel alignment
checked, and if necessary, adjusted.
10•14 Suspension and steering systems
20.7 To unbolt the idler arm from the
subframe crossmember, remove this nut
(arrowed)
20.4 To remove an outer track rod,
remove this nut (arrowed) from the end of
the centre track rod, and use a balljoint
separator to separate the balljoint stud
from the centre track rod (if you’re
renewing the inner track rod end, mark the
threads with paint before loosening the
clamp bolt and nut)
19.6 Rack-and-pinion steering gear
mounting bolts (arrowed) - 3-Series
models - (self-locking nuts not visible in
this photo)
Page 157 of 228
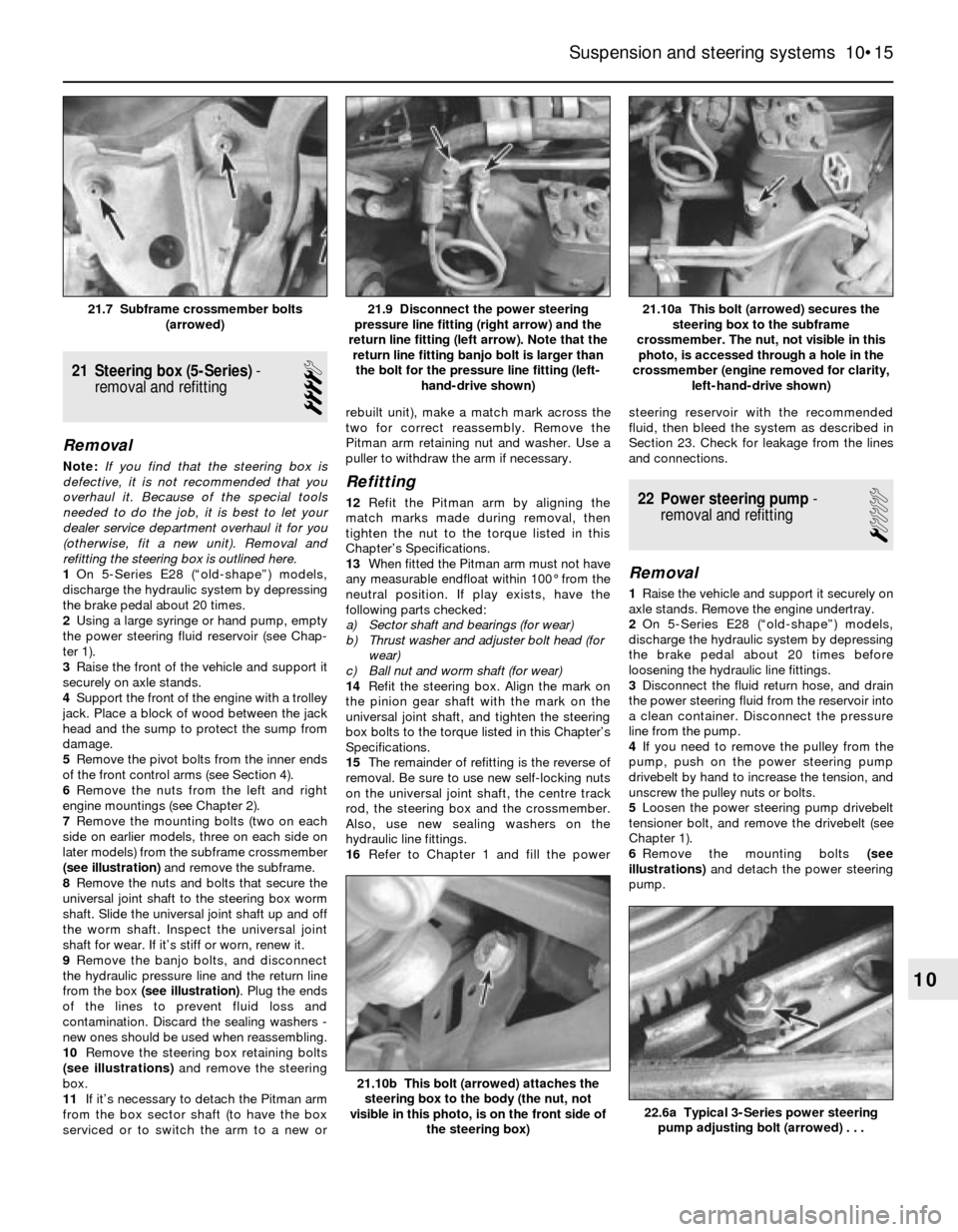
21 Steering box (5-Series)-
removal and refitting
4
Removal
Note:If you find that the steering box is
defective, it is not recommended that you
overhaul it. Because of the special tools
needed to do the job, it is best to let your
dealer service department overhaul it for you
(otherwise, fit a new unit). Removal and
refitting the steering box is outlined here.
1On 5-Series E28 (“old-shape”) models,
discharge the hydraulic system by depressing
the brake pedal about 20 times.
2Using a large syringe or hand pump, empty
the power steering fluid reservoir (see Chap-
ter 1).
3Raise the front of the vehicle and support it
securely on axle stands.
4Support the front of the engine with a trolley
jack. Place a block of wood between the jack
head and the sump to protect the sump from
damage.
5Remove the pivot bolts from the inner ends
of the front control arms (see Section 4).
6Remove the nuts from the left and right
engine mountings (see Chapter 2).
7Remove the mounting bolts (two on each
side on earlier models, three on each side on
later models) from the subframe crossmember
(see illustration)and remove the subframe.
8Remove the nuts and bolts that secure the
universal joint shaft to the steering box worm
shaft. Slide the universal joint shaft up and off
the worm shaft. Inspect the universal joint
shaft for wear. If it’s stiff or worn, renew it.
9Remove the banjo bolts, and disconnect
the hydraulic pressure line and the return line
from the box (see illustration). Plug the ends
of the lines to prevent fluid loss and
contamination. Discard the sealing washers -
new ones should be used when reassembling.
10Remove the steering box retaining bolts
(see illustrations)and remove the steering
box.
11If it’s necessary to detach the Pitman arm
from the box sector shaft (to have the box
serviced or to switch the arm to a new orrebuilt unit), make a match mark across the
two for correct reassembly. Remove the
Pitman arm retaining nut and washer. Use a
puller to withdraw the arm if necessary.
Refitting
12Refit the Pitman arm by aligning the
match marks made during removal, then
tighten the nut to the torque listed in this
Chapter’s Specifications.
13When fitted the Pitman arm must not have
any measurable endfloat within 100° from the
neutral position. If play exists, have the
following parts checked:
a) Sector shaft and bearings (for wear)
b) Thrust washer and adjuster bolt head (for
wear)
c) Ball nut and worm shaft (for wear)
14Refit the steering box. Align the mark on
the pinion gear shaft with the mark on the
universal joint shaft, and tighten the steering
box bolts to the torque listed in this Chapter’s
Specifications.
15The remainder of refitting is the reverse of
removal. Be sure to use new self-locking nuts
on the universal joint shaft, the centre track
rod, the steering box and the crossmember.
Also, use new sealing washers on the
hydraulic line fittings.
16Refer to Chapter 1 and fill the powersteering reservoir with the recommended
fluid, then bleed the system as described in
Section 23. Check for leakage from the lines
and connections.22 Power steering pump-
removal and refitting
1
Removal
1Raise the vehicle and support it securely on
axle stands. Remove the engine undertray.
2On 5-Series E28 (“old-shape”) models,
discharge the hydraulic system by depressing
the brake pedal about 20 times before
loosening the hydraulic line fittings.
3Disconnect the fluid return hose, and drain
the power steering fluid from the reservoir into
a clean container. Disconnect the pressure
line from the pump.
4If you need to remove the pulley from the
pump, push on the power steering pump
drivebelt by hand to increase the tension, and
unscrew the pulley nuts or bolts.
5Loosen the power steering pump drivebelt
tensioner bolt, and remove the drivebelt (see
Chapter 1).
6Remove the mounting bolts (see
illustrations)and detach the power steering
pump.
Suspension and steering systems 10•15
21.10a This bolt (arrowed) secures the
steering box to the subframe
crossmember. The nut, not visible in this
photo, is accessed through a hole in the
crossmember (engine removed for clarity,
left-hand-drive shown)21.9 Disconnect the power steering
pressure line fitting (right arrow) and the
return line fitting (left arrow). Note that the
return line fitting banjo bolt is larger than
the bolt for the pressure line fitting (left-
hand-drive shown)21.7 Subframe crossmember bolts
(arrowed)
22.6a Typical 3-Series power steering
pump adjusting bolt (arrowed) . . .
21.10b This bolt (arrowed) attaches the
steering box to the body (the nut, not
visible in this photo, is on the front side of
the steering box)
10