differential BMW 3 SERIES 1987 E30 Workshop Manual
[x] Cancel search | Manufacturer: BMW, Model Year: 1987, Model line: 3 SERIES, Model: BMW 3 SERIES 1987 E30Pages: 228, PDF Size: 7.04 MB
Page 11 of 228
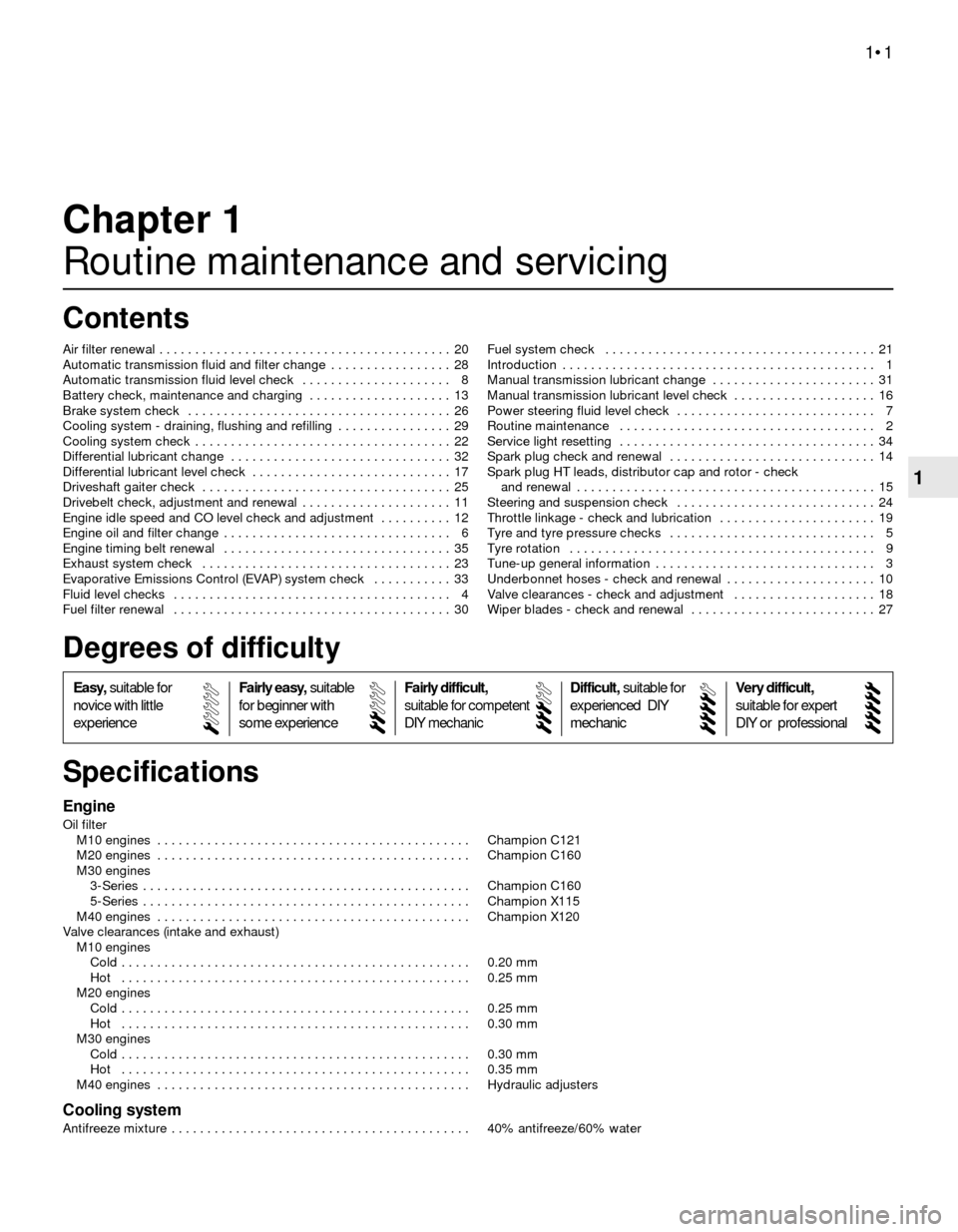
1
Engine
Oil filter
M10 engines . . . . . . . . . . . . . . . . . . . . . . . . . . . . . . . . . . . . . . . . . . . . Champion C121
M20 engines . . . . . . . . . . . . . . . . . . . . . . . . . . . . . . . . . . . . . . . . . . . . Champion C160
M30 engines
3-Series . . . . . . . . . . . . . . . . . . . . . . . . . . . . . . . . . . . . . . . . . . . . . . Champion C160
5-Series . . . . . . . . . . . . . . . . . . . . . . . . . . . . . . . . . . . . . . . . . . . . . . Champion X115
M40 engines . . . . . . . . . . . . . . . . . . . . . . . . . . . . . . . . . . . . . . . . . . . . Champion X120
Valve clearances (intake and exhaust)
M10 engines
Cold . . . . . . . . . . . . . . . . . . . . . . . . . . . . . . . . . . . . . . . . . . . . . . . . . 0.20 mm
Hot . . . . . . . . . . . . . . . . . . . . . . . . . . . . . . . . . . . . . . . . . . . . . . . . . 0.25 mm
M20 engines
Cold . . . . . . . . . . . . . . . . . . . . . . . . . . . . . . . . . . . . . . . . . . . . . . . . . 0.25 mm
Hot . . . . . . . . . . . . . . . . . . . . . . . . . . . . . . . . . . . . . . . . . . . . . . . . . 0.30 mm
M30 engines
Cold . . . . . . . . . . . . . . . . . . . . . . . . . . . . . . . . . . . . . . . . . . . . . . . . . 0.30 mm
Hot . . . . . . . . . . . . . . . . . . . . . . . . . . . . . . . . . . . . . . . . . . . . . . . . . 0.35 mm
M40 engines . . . . . . . . . . . . . . . . . . . . . . . . . . . . . . . . . . . . . . . . . . . . Hydraulic adjusters
Cooling system
Antifreeze mixture . . . . . . . . . . . . . . . . . . . . . . . . . . . . . . . . . . . . . . . . . . 40% antifreeze/60% water
Chapter 1
Routine maintenance and servicing
Air filter renewal . . . . . . . . . . . . . . . . . . . . . . . . . . . . . . . . . . . . . . . . . 20
Automatic transmission fluid and filter change . . . . . . . . . . . . . . . . . 28
Automatic transmission fluid level check . . . . . . . . . . . . . . . . . . . . . 8
Battery check, maintenance and charging . . . . . . . . . . . . . . . . . . . . 13
Brake system check . . . . . . . . . . . . . . . . . . . . . . . . . . . . . . . . . . . . . 26
Cooling system - draining, flushing and refilling . . . . . . . . . . . . . . . . 29
Cooling system check . . . . . . . . . . . . . . . . . . . . . . . . . . . . . . . . . . . . 22
Differential lubricant change . . . . . . . . . . . . . . . . . . . . . . . . . . . . . . . 32
Differential lubricant level check . . . . . . . . . . . . . . . . . . . . . . . . . . . . 17
Driveshaft gaiter check . . . . . . . . . . . . . . . . . . . . . . . . . . . . . . . . . . . 25
Drivebelt check, adjustment and renewal . . . . . . . . . . . . . . . . . . . . . 11
Engine idle speed and CO level check and adjustment . . . . . . . . . . 12
Engine oil and filter change . . . . . . . . . . . . . . . . . . . . . . . . . . . . . . . . 6
Engine timing belt renewal . . . . . . . . . . . . . . . . . . . . . . . . . . . . . . . . 35
Exhaust system check . . . . . . . . . . . . . . . . . . . . . . . . . . . . . . . . . . . 23
Evaporative Emissions Control (EVAP) system check . . . . . . . . . . . 33
Fluid level checks . . . . . . . . . . . . . . . . . . . . . . . . . . . . . . . . . . . . . . . 4
Fuel filter renewal . . . . . . . . . . . . . . . . . . . . . . . . . . . . . . . . . . . . . . . 30 Fuel system check . . . . . . . . . . . . . . . . . . . . . . . . . . . . . . . . . . . . . . 21
Introduction . . . . . . . . . . . . . . . . . . . . . . . . . . . . . . . . . . . . . . . . . . . . 1
Manual transmission lubricant change . . . . . . . . . . . . . . . . . . . . . . . 31
Manual transmission lubricant level check . . . . . . . . . . . . . . . . . . . . 16
Power steering fluid level check . . . . . . . . . . . . . . . . . . . . . . . . . . . . 7
Routine maintenance . . . . . . . . . . . . . . . . . . . . . . . . . . . . . . . . . . . . 2
Service light resetting . . . . . . . . . . . . . . . . . . . . . . . . . . . . . . . . . . . . 34
Spark plug check and renewal . . . . . . . . . . . . . . . . . . . . . . . . . . . . . 14
Spark plug HT leads, distributor cap and rotor - check
and renewal . . . . . . . . . . . . . . . . . . . . . . . . . . . . . . . . . . . . . . . . . . 15
Steering and suspension check . . . . . . . . . . . . . . . . . . . . . . . . . . . . 24
Throttle linkage - check and lubrication . . . . . . . . . . . . . . . . . . . . . . 19
Tyre and tyre pressure checks . . . . . . . . . . . . . . . . . . . . . . . . . . . . . 5
Tyre rotation . . . . . . . . . . . . . . . . . . . . . . . . . . . . . . . . . . . . . . . . . . . 9
Tune-up general information . . . . . . . . . . . . . . . . . . . . . . . . . . . . . . . 3
Underbonnet hoses - check and renewal . . . . . . . . . . . . . . . . . . . . . 10
Valve clearances - check and adjustment . . . . . . . . . . . . . . . . . . . . 18
Wiper blades - check and renewal . . . . . . . . . . . . . . . . . . . . . . . . . . 27
1•1
Easy,suitable for
novice with little
experienceFairly easy,suitable
for beginner with
some experienceFairly difficult,
suitable for competent
DIY mechanic
Difficult,suitable for
experienced DIY
mechanicVery difficult,
suitable for expert
DIY or professional
Degrees of difficulty
Specifications Contents
Page 14 of 228
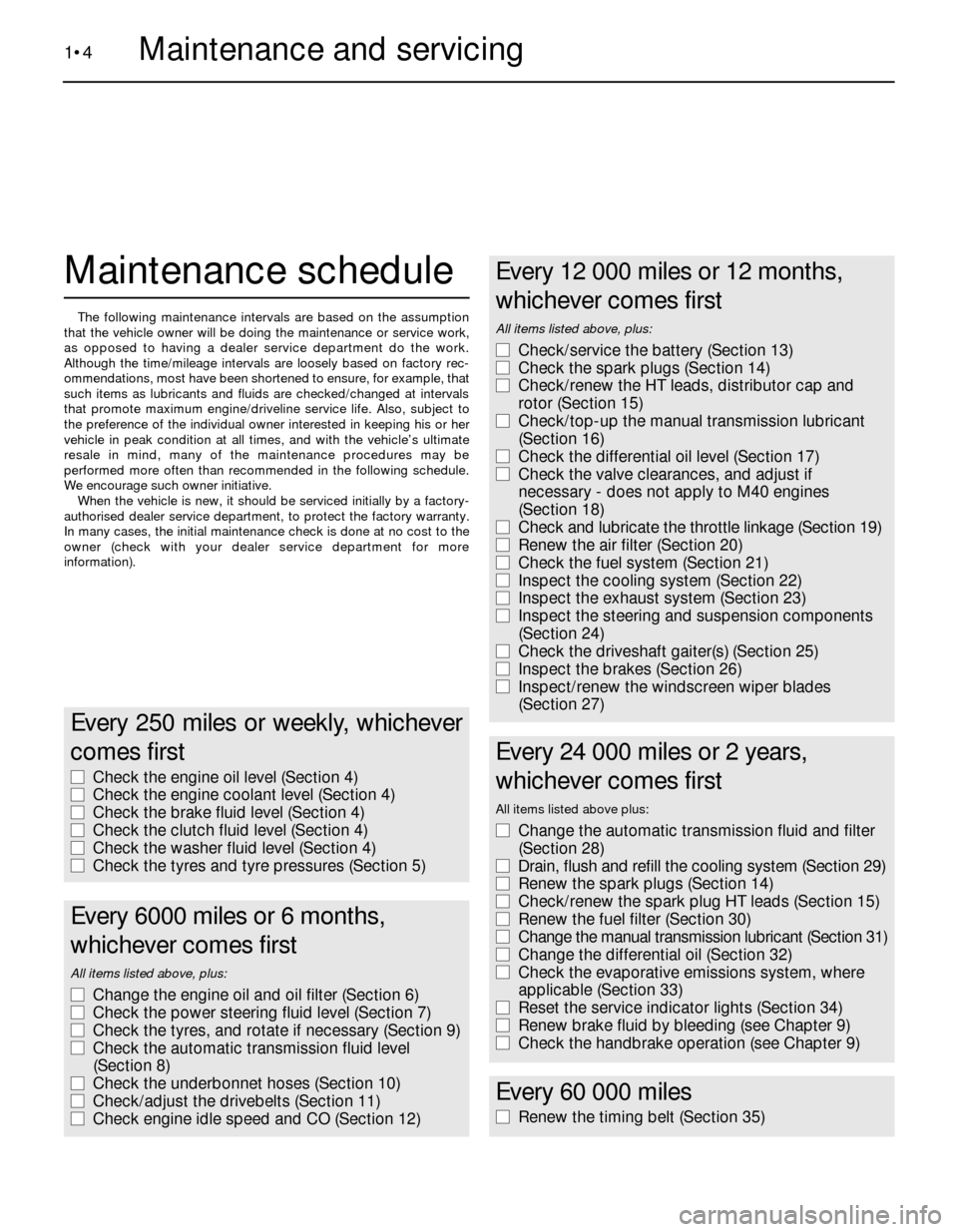
Maintenance schedule
The following maintenance intervals are based on the assumption
that the vehicle owner will be doing the maintenance or service work,
as opposed to having a dealer service department do the work.
Although the time/mileage intervals are loosely based on factory rec-
ommendations, most have been shortened to ensure, for example, that
such items as lubricants and fluids are checked/changed at intervals
that promote maximum engine/driveline service life. Also, subject to
the preference of the individual owner interested in keeping his or her
vehicle in peak condition at all times, and with the vehicle’s ultimate
resale in mind, many of the maintenance procedures may be
performed more often than recommended in the following schedule.
We encourage such owner initiative.
When the vehicle is new, it should be serviced initially by a factory-
authorised dealer service department, to protect the factory warranty.
In many cases, the initial maintenance check is done at no cost to the
owner (check with your dealer service department for more
information).
1•4Maintenance and servicing
Every 250 miles or weekly, whichever
comes first
m mCheck the engine oil level (Section 4)
m mCheck the engine coolant level (Section 4)
m mCheck the brake fluid level (Section 4)
m mCheck the clutch fluid level (Section 4)
m mCheck the washer fluid level (Section 4)
m mCheck the tyres and tyre pressures (Section 5)
Every 6000 miles or 6 months,
whichever comes first
All items listed above, plus:
m mChange the engine oil and oil filter (Section 6)
m mCheck the power steering fluid level (Section 7)
m mCheck the tyres, and rotate if necessary (Section 9)
m mCheck the automatic transmission fluid level
(Section 8)
m mCheck the underbonnet hoses (Section 10)
m mCheck/adjust the drivebelts (Section 11)
m mCheck engine idle speed and CO (Section 12)
Every 12 000 miles or 12 months,
whichever comes first
All items listed above, plus:
m mCheck/service the battery (Section 13)
m mCheck the spark plugs (Section 14)
m mCheck/renew the HT leads, distributor cap and
rotor (Section 15)
m mCheck/top-up the manual transmission lubricant
(Section 16)
m mCheck the differential oil level (Section 17)
m mCheck the valve clearances, and adjust if
necessary - does not apply to M40 engines
(Section 18)
m mCheck and lubricate the throttle linkage (Section 19)
m mRenew the air filter (Section 20)
m mCheck the fuel system (Section 21)
m mInspect the cooling system (Section 22)
m mInspect the exhaust system (Section 23)
m mInspect the steering and suspension components
(Section 24)
m mCheck the driveshaft gaiter(s) (Section 25)
m mInspect the brakes (Section 26)
m mInspect/renew the windscreen wiper blades
(Section 27)
Every 24 000 miles or 2 years,
whichever comes first
All items listed above plus:
m mChange the automatic transmission fluid and filter
(Section 28)
m mDrain, flush and refill the cooling system (Section 29)
m mRenew the spark plugs (Section 14)
m mCheck/renew the spark plug HT leads (Section 15)
m mRenew the fuel filter (Section 30)
m mChange the manual transmission lubricant (Section 31)
m mChange the differential oil (Section 32)
m mCheck the evaporative emissions system, where
applicable (Section 33)
m mReset the service indicator lights (Section 34)
m mRenew brake fluid by bleeding (see Chapter 9)
m mCheck the handbrake operation (see Chapter 9)
Every 60 000 miles
m
mRenew the timing belt (Section 35)
Page 16 of 228
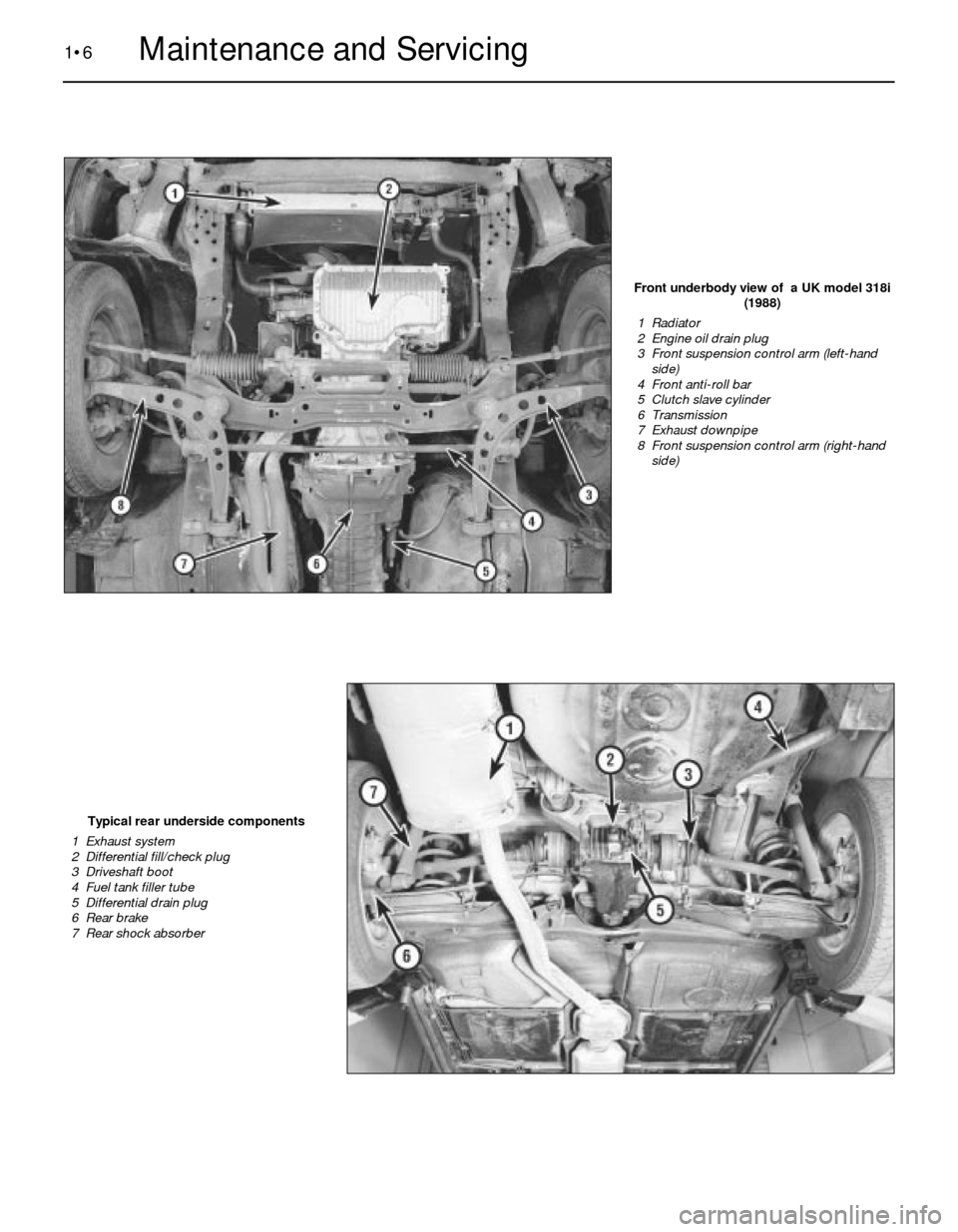
1•6Maintenance and Servicing
Front underbody view of a UK model 318i
(1988)
1 Radiator
2 Engine oil drain plug
3 Front suspension control arm (left-hand
side)
4 Front anti-roll bar
5 Clutch slave cylinder
6 Transmission
7 Exhaust downpipe
8 Front suspension control arm (right-hand
side)
Typical rear underside components
1 Exhaust system
2 Differential fill/check plug
3 Driveshaft boot
4 Fuel tank filler tube
5 Differential drain plug
6 Rear brake
7 Rear shock absorber
Page 29 of 228
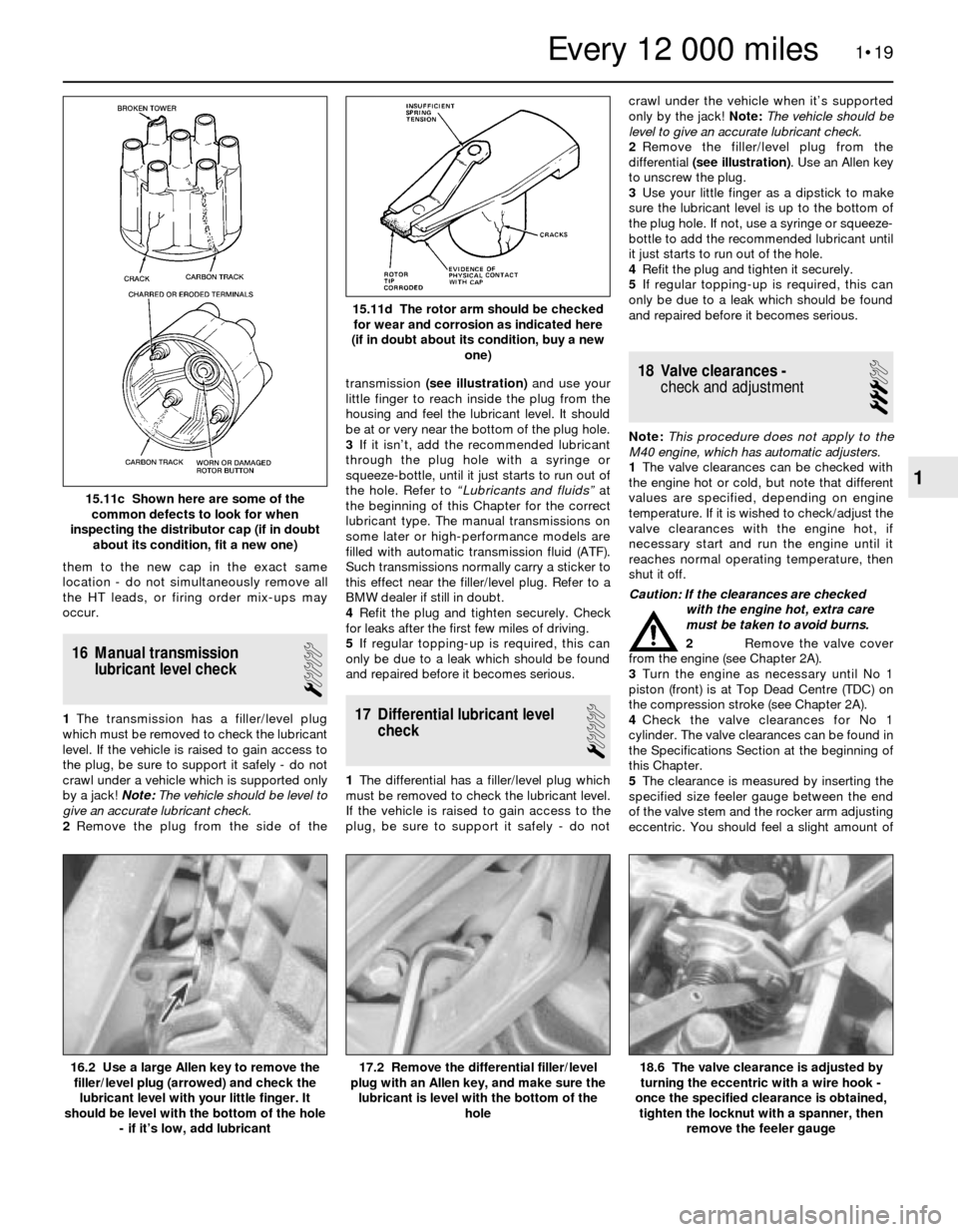
them to the new cap in the exact same
location - do not simultaneously remove all
the HT leads, or firing order mix-ups may
occur.
16 Manual transmission
lubricant level check
1
1The transmission has a filler/level plug
which must be removed to check the lubricant
level. If the vehicle is raised to gain access to
the plug, be sure to support it safely - do not
crawl under a vehicle which is supported only
by a jack!Note:The vehicle should be level to
give an accurate lubricant check.
2Remove the plug from the side of thetransmission (see illustration)and use your
little finger to reach inside the plug from the
housing and feel the lubricant level. It should
be at or very near the bottom of the plug hole.
3If it isn’t, add the recommended lubricant
through the plug hole with a syringe or
squeeze-bottle, until it just starts to run out of
the hole. Refer to “Lubricants and fluids” at
the beginning of this Chapter for the correct
lubricant type. The manual transmissions on
some later or high-performance models are
filled with automatic transmission fluid (ATF).
Such transmissions normally carry a sticker to
this effect near the filler/level plug. Refer to a
BMW dealer if still in doubt.
4Refit the plug and tighten securely. Check
for leaks after the first few miles of driving.
5If regular topping-up is required, this can
only be due to a leak which should be found
and repaired before it becomes serious.17 Differential lubricant level
check
1
1The differential has a filler/level plug which
must be removed to check the lubricant level.
If the vehicle is raised to gain access to the
plug, be sure to support it safely - do notcrawl under the vehicle when it’s supported
only by the jack! Note:The vehicle should be
level to give an accurate lubricant check.
2Remove the filler/level plug from the
differential (see illustration). Use an Allen key
to unscrew the plug.
3Use your little finger as a dipstick to make
sure the lubricant level is up to the bottom of
the plug hole. If not, use a syringe or squeeze-
bottle to add the recommended lubricant until
it just starts to run out of the hole.
4Refit the plug and tighten it securely.
5If regular topping-up is required, this can
only be due to a leak which should be found
and repaired before it becomes serious.
18 Valve clearances -
check and adjustment
3
Note:This procedure does not apply to the
M40 engine, which has automatic adjusters.
1The valve clearances can be checked with
the engine hot or cold, but note that different
values are specified, depending on engine
temperature. If it is wished to check/adjust the
valve clearances with the engine hot, if
necessary start and run the engine until it
reaches normal operating temperature, then
shut it off.
Caution: If the clearances are checked
with the engine hot, extra care
must be taken to avoid burns.
2Remove the valve cover
from the engine (see Chapter 2A).
3Turn the engine as necessary until No 1
piston (front) is at Top Dead Centre (TDC) on
the compression stroke (see Chapter 2A).
4Check the valve clearances for No 1
cylinder. The valve clearances can be found in
the Specifications Section at the beginning of
this Chapter.
5The clearance is measured by inserting the
specified size feeler gauge between the end
of the valve stem and the rocker arm adjusting
eccentric. You should feel a slight amount of
1•19
15.11d The rotor arm should be checked
for wear and corrosion as indicated here
(if in doubt about its condition, buy a new
one)
15.11c Shown here are some of the
common defects to look for when
inspecting the distributor cap (if in doubt
about its condition, fit a new one)
18.6 The valve clearance is adjusted by
turning the eccentric with a wire hook -
once the specified clearance is obtained,
tighten the locknut with a spanner, then
remove the feeler gauge17.2 Remove the differential filler/level
plug with an Allen key, and make sure the
lubricant is level with the bottom of the
hole16.2 Use a large Allen key to remove the
filler/level plug (arrowed) and check the
lubricant level with your little finger. It
should be level with the bottom of the hole
- if it’s low, add lubricant
1
Every 12 000 miles
Page 36 of 228
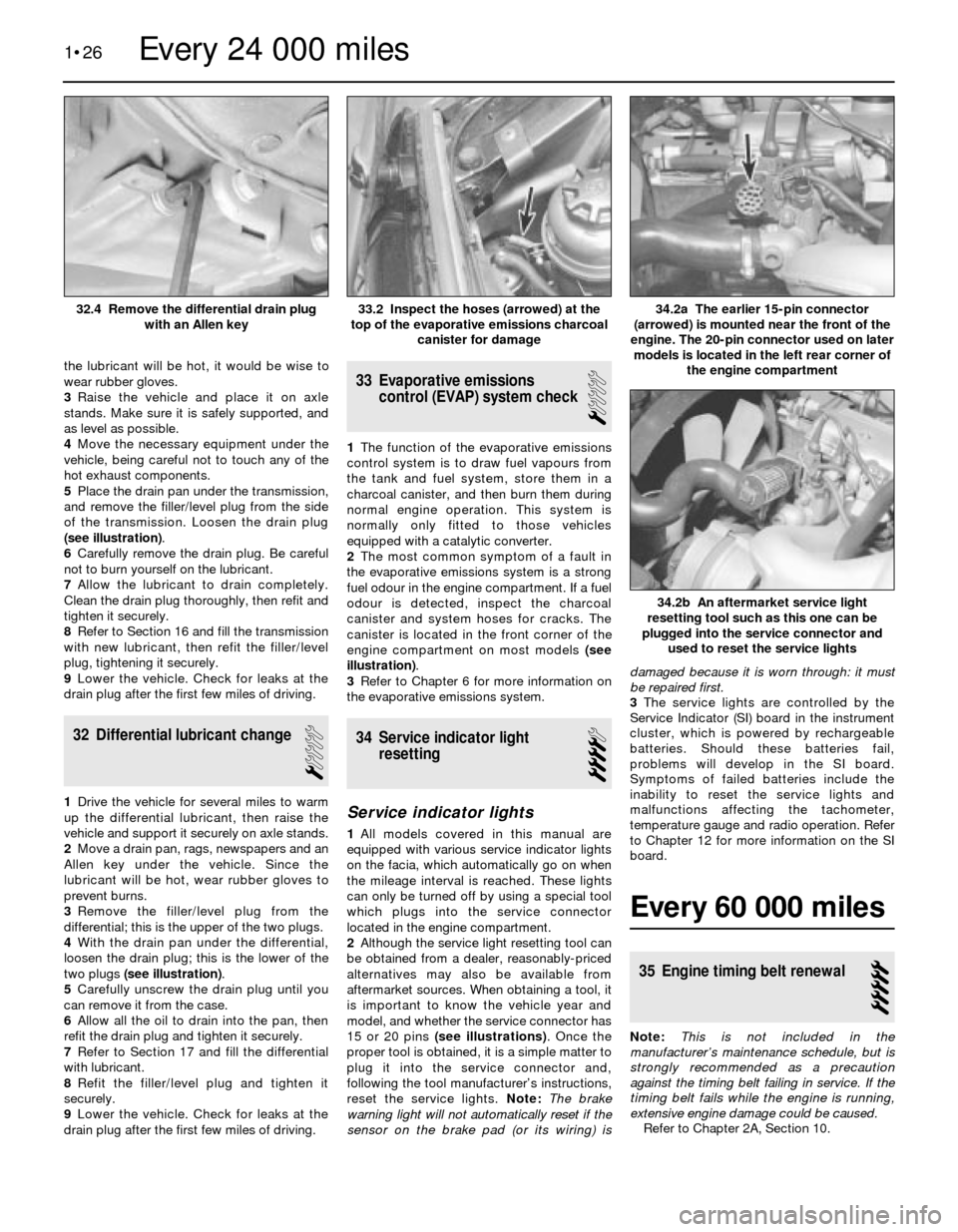
the lubricant will be hot, it would be wise to
wear rubber gloves.
3Raise the vehicle and place it on axle
stands. Make sure it is safely supported, and
as level as possible.
4Move the necessary equipment under the
vehicle, being careful not to touch any of the
hot exhaust components.
5Place the drain pan under the transmission,
and remove the filler/level plug from the side
of the transmission. Loosen the drain plug
(see illustration).
6Carefully remove the drain plug. Be careful
not to burn yourself on the lubricant.
7Allow the lubricant to drain completely.
Clean the drain plug thoroughly, then refit and
tighten it securely.
8Refer to Section 16 and fill the transmission
with new lubricant, then refit the filler/level
plug, tightening it securely.
9Lower the vehicle. Check for leaks at the
drain plug after the first few miles of driving.
32 Differential lubricant change
1
1Drive the vehicle for several miles to warm
up the differential lubricant, then raise the
vehicle and support it securely on axle stands.
2Move a drain pan, rags, newspapers and an
Allen key under the vehicle. Since the
lubricant will be hot, wear rubber gloves to
prevent burns.
3Remove the filler/level plug from the
differential; this is the upper of the two plugs.
4With the drain pan under the differential,
loosen the drain plug; this is the lower of the
two plugs (see illustration).
5Carefully unscrew the drain plug until you
can remove it from the case.
6Allow all the oil to drain into the pan, then
refit the drain plug and tighten it securely.
7Refer to Section 17 and fill the differential
with lubricant.
8Refit the filler/level plug and tighten it
securely.
9Lower the vehicle. Check for leaks at the
drain plug after the first few miles of driving.
33 Evaporative emissions
control (EVAP) system check
1
1The function of the evaporative emissions
control system is to draw fuel vapours from
the tank and fuel system, store them in a
charcoal canister, and then burn them during
normal engine operation. This system is
normally only fitted to those vehicles
equipped with a catalytic converter.
2The most common symptom of a fault in
the evaporative emissions system is a strong
fuel odour in the engine compartment. If a fuel
odour is detected, inspect the charcoal
canister and system hoses for cracks. The
canister is located in the front corner of the
engine compartment on most models (see
illustration).
3Refer to Chapter 6 for more information on
the evaporative emissions system.
34 Service indicator light
resetting
4
Service indicator lights
1All models covered in this manual are
equipped with various service indicator lights
on the facia, which automatically go on when
the mileage interval is reached. These lights
can only be turned off by using a special tool
which plugs into the service connector
located in the engine compartment.
2Although the service light resetting tool can
be obtained from a dealer, reasonably-priced
alternatives may also be available from
aftermarket sources. When obtaining a tool, it
is important to know the vehicle year and
model, and whether the service connector has
15 or 20 pins (see illustrations). Once the
proper tool is obtained, it is a simple matter to
plug it into the service connector and,
following the tool manufacturer’s instructions,
reset the service lights. Note: The brake
warning light will not automatically reset if the
sensor on the brake pad (or its wiring) isdamaged because it is worn through: it must
be repaired first.
3The service lights are controlled by the
Service Indicator (SI) board in the instrument
cluster, which is powered by rechargeable
batteries. Should these batteries fail,
problems will develop in the SI board.
Symptoms of failed batteries include the
inability to reset the service lights and
malfunctions affecting the tachometer,
temperature gauge and radio operation. Refer
to Chapter 12 for more information on the SI
board.
Every 60 000 miles
35 Engine timing belt renewal
5
Note:This is not included in the
manufacturer’s maintenance schedule, but is
strongly recommended as a precaution
against the timing belt failing in service. If the
timing belt fails while the engine is running,
extensive engine damage could be caused.
Refer to Chapter 2A, Section 10.
1•26
34.2b An aftermarket service light
resetting tool such as this one can be
plugged into the service connector and
used to reset the service lights
34.2a The earlier 15-pin connector
(arrowed) is mounted near the front of the
engine. The 20-pin connector used on later
models is located in the left rear corner of
the engine compartment33.2 Inspect the hoses (arrowed) at the
top of the evaporative emissions charcoal
canister for damage32.4 Remove the differential drain plug
with an Allen key
Every 24 000 miles
Page 130 of 228
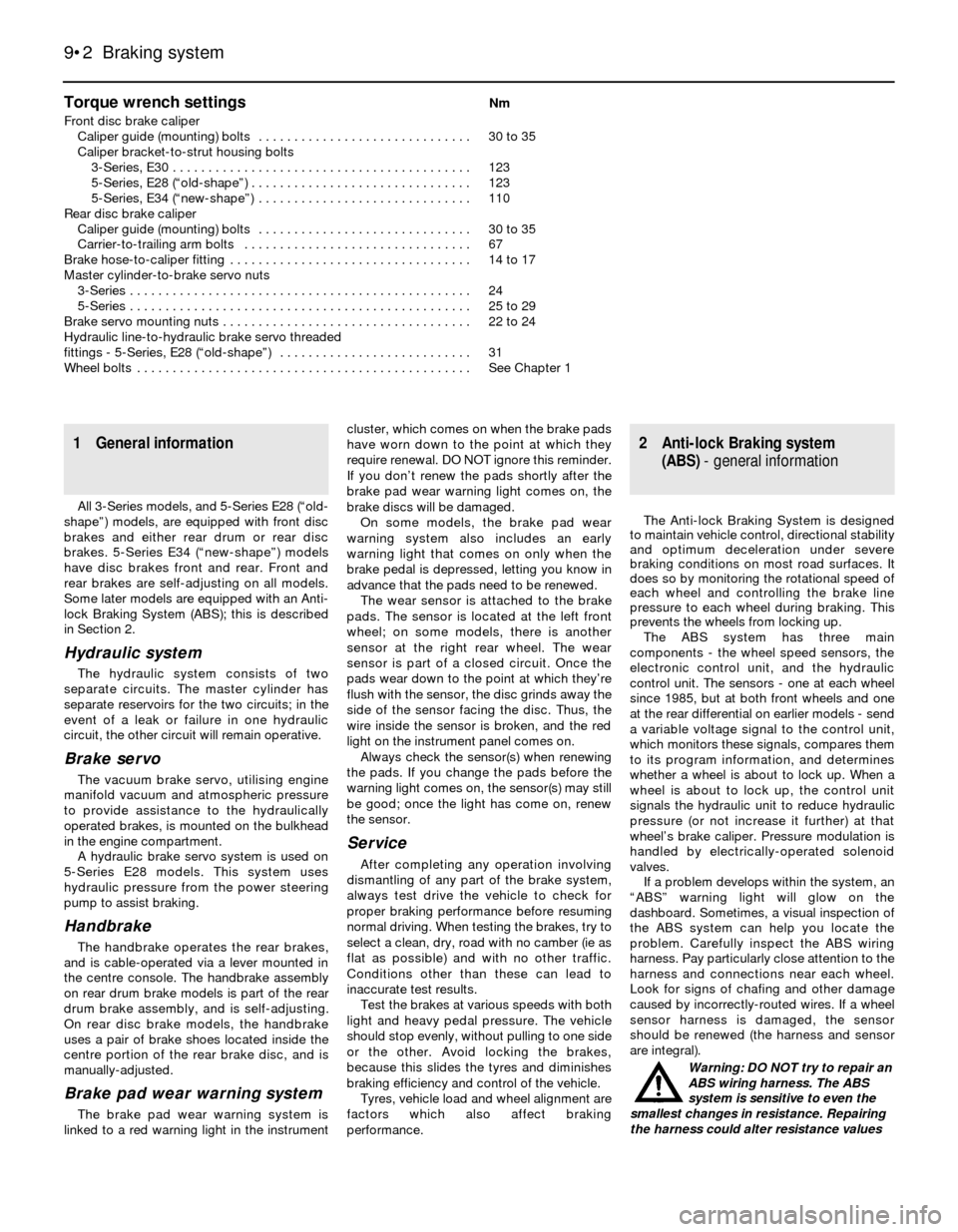
Torque wrench settingsNm
Front disc brake caliper
Caliper guide (mounting) bolts . . . . . . . . . . . . . . . . . . . . . . . . . . . . . . 30 to 35
Caliper bracket-to-strut housing bolts
3-Series, E30 . . . . . . . . . . . . . . . . . . . . . . . . . . . . . . . . . . . . . . . . . . 123
5-Series, E28 (“old-shape”) . . . . . . . . . . . . . . . . . . . . . . . . . . . . . . . 123
5-Series, E34 (“new-shape”) . . . . . . . . . . . . . . . . . . . . . . . . . . . . . . 110
Rear disc brake caliper
Caliper guide (mounting) bolts . . . . . . . . . . . . . . . . . . . . . . . . . . . . . . 30 to 35
Carrier-to-trailing arm bolts . . . . . . . . . . . . . . . . . . . . . . . . . . . . . . . . 67
Brake hose-to-caliper fitting . . . . . . . . . . . . . . . . . . . . . . . . . . . . . . . . . . 14 to 17
Master cylinder-to-brake servo nuts
3-Series . . . . . . . . . . . . . . . . . . . . . . . . . . . . . . . . . . . . . . . . . . . . . . . . 24
5-Series . . . . . . . . . . . . . . . . . . . . . . . . . . . . . . . . . . . . . . . . . . . . . . . . 25 to 29
Brake servo mounting nuts . . . . . . . . . . . . . . . . . . . . . . . . . . . . . . . . . . . 22 to 24
Hydraulic line-to-hydraulic brake servo threaded
fittings - 5-Series, E28 (“old-shape”) . . . . . . . . . . . . . . . . . . . . . . . . . . . 31
Wheel bolts . . . . . . . . . . . . . . . . . . . . . . . . . . . . . . . . . . . . . . . . . . . . . . . See Chapter 1
9•2 Braking system
1 General information
All 3-Series models, and 5-Series E28 (“old-
shape”) models, are equipped with front disc
brakes and either rear drum or rear disc
brakes. 5-Series E34 (“new-shape”) models
have disc brakes front and rear. Front and
rear brakes are self-adjusting on all models.
Some later models are equipped with an Anti-
lock Braking System (ABS); this is described
in Section 2.
Hydraulic system
The hydraulic system consists of two
separate circuits. The master cylinder has
separate reservoirs for the two circuits; in the
event of a leak or failure in one hydraulic
circuit, the other circuit will remain operative.
Brake servo
The vacuum brake servo, utilising engine
manifold vacuum and atmospheric pressure
to provide assistance to the hydraulically
operated brakes, is mounted on the bulkhead
in the engine compartment.
A hydraulic brake servo system is used on
5-Series E28 models. This system uses
hydraulic pressure from the power steering
pump to assist braking.
Handbrake
The handbrake operates the rear brakes,
and is cable-operated via a lever mounted in
the centre console. The handbrake assembly
on rear drum brake models is part of the rear
drum brake assembly, and is self-adjusting.
On rear disc brake models, the handbrake
uses a pair of brake shoes located inside the
centre portion of the rear brake disc, and is
manually-adjusted.
Brake pad wear warning system
The brake pad wear warning system is
linked to a red warning light in the instrumentcluster, which comes on when the brake pads
have worn down to the point at which they
require renewal. DO NOT ignore this reminder.
If you don’t renew the pads shortly after the
brake pad wear warning light comes on, the
brake discs will be damaged.
On some models, the brake pad wear
warning system also includes an early
warning light that comes on only when the
brake pedal is depressed, letting you know in
advance that the pads need to be renewed.
The wear sensor is attached to the brake
pads. The sensor is located at the left front
wheel; on some models, there is another
sensor at the right rear wheel. The wear
sensor is part of a closed circuit. Once the
pads wear down to the point at which they’re
flush with the sensor, the disc grinds away the
side of the sensor facing the disc. Thus, the
wire inside the sensor is broken, and the red
light on the instrument panel comes on.
Always check the sensor(s) when renewing
the pads. If you change the pads before the
warning light comes on, the sensor(s) may still
be good; once the light has come on, renew
the sensor.
Service
After completing any operation involving
dismantling of any part of the brake system,
always test drive the vehicle to check for
proper braking performance before resuming
normal driving. When testing the brakes, try to
select a clean, dry, road with no camber (ie as
flat as possible) and with no other traffic.
Conditions other than these can lead to
inaccurate test results.
Test the brakes at various speeds with both
light and heavy pedal pressure. The vehicle
should stop evenly, without pulling to one side
or the other. Avoid locking the brakes,
because this slides the tyres and diminishes
braking efficiency and control of the vehicle.
Tyres, vehicle load and wheel alignment are
factors which also affect braking
performance.
2 Anti-lock Braking system
(ABS)- general information
The Anti-lock Braking System is designed
to maintain vehicle control, directional stability
and optimum deceleration under severe
braking conditions on most road surfaces. It
does so by monitoring the rotational speed of
each wheel and controlling the brake line
pressure to each wheel during braking. This
prevents the wheels from locking up.
The ABS system has three main
components - the wheel speed sensors, the
electronic control unit, and the hydraulic
control unit. The sensors - one at each wheel
since 1985, but at both front wheels and one
at the rear differential on earlier models - send
a variable voltage signal to the control unit,
which monitors these signals, compares them
to its program information, and determines
whether a wheel is about to lock up. When a
wheel is about to lock up, the control unit
signals the hydraulic unit to reduce hydraulic
pressure (or not increase it further) at that
wheel’s brake caliper. Pressure modulation is
handled by electrically-operated solenoid
valves.
If a problem develops within the system, an
“ABS” warning light will glow on the
dashboard. Sometimes, a visual inspection of
the ABS system can help you locate the
problem. Carefully inspect the ABS wiring
harness. Pay particularly close attention to the
harness and connections near each wheel.
Look for signs of chafing and other damage
caused by incorrectly-routed wires. If a wheel
sensor harness is damaged, the sensor
should be renewed (the harness and sensor
are integral).
Warning: DO NOT try to repair an
ABS wiring harness. The ABS
system is sensitive to even the
smallest changes in resistance. Repairing
the harness could alter resistance values
Page 151 of 228
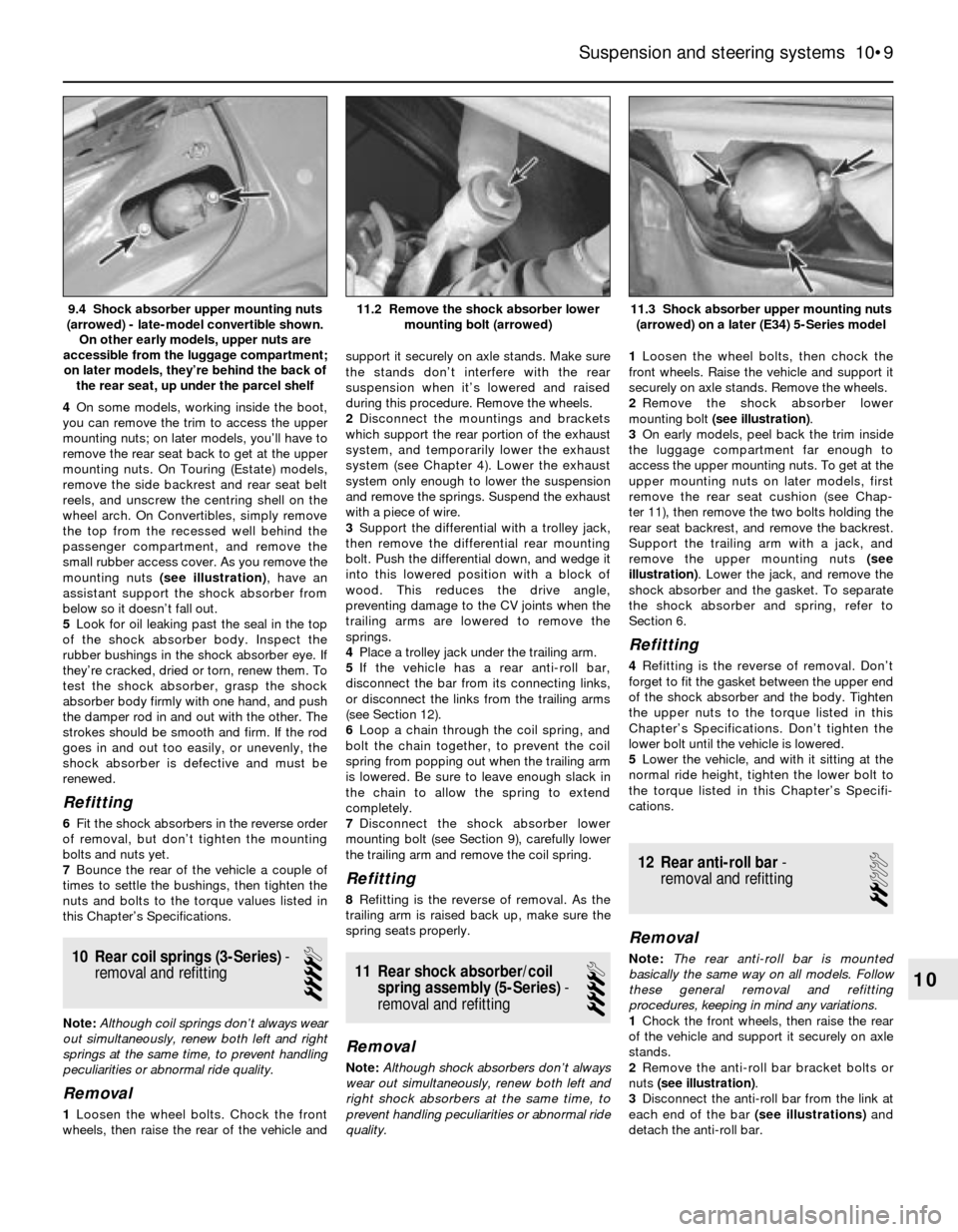
4On some models, working inside the boot,
you can remove the trim to access the upper
mounting nuts; on later models, you’ll have to
remove the rear seat back to get at the upper
mounting nuts. On Touring (Estate) models,
remove the side backrest and rear seat belt
reels, and unscrew the centring shell on the
wheel arch. On Convertibles, simply remove
the top from the recessed well behind the
passenger compartment, and remove the
small rubber access cover. As you remove the
mounting nuts (see illustration), have an
assistant support the shock absorber from
below so it doesn’t fall out.
5Look for oil leaking past the seal in the top
of the shock absorber body. Inspect the
rubber bushings in the shock absorber eye. If
they’re cracked, dried or torn, renew them. To
test the shock absorber, grasp the shock
absorber body firmly with one hand, and push
the damper rod in and out with the other. The
strokes should be smooth and firm. If the rod
goes in and out too easily, or unevenly, the
shock absorber is defective and must be
renewed.
Refitting
6Fit the shock absorbers in the reverse order
of removal, but don’t tighten the mounting
bolts and nuts yet.
7Bounce the rear of the vehicle a couple of
times to settle the bushings, then tighten the
nuts and bolts to the torque values listed in
this Chapter’s Specifications.
10 Rear coil springs (3-Series)-
removal and refitting
4
Note: Although coil springs don’t always wear
out simultaneously, renew both left and right
springs at the same time, to prevent handling
peculiarities or abnormal ride quality.
Removal
1Loosen the wheel bolts. Chock the front
wheels, then raise the rear of the vehicle andsupport it securely on axle stands. Make sure
the stands don’t interfere with the rear
suspension when it’s lowered and raised
during this procedure. Remove the wheels.
2Disconnect the mountings and brackets
which support the rear portion of the exhaust
system, and temporarily lower the exhaust
system (see Chapter 4). Lower the exhaust
system only enough to lower the suspension
and remove the springs. Suspend the exhaust
with a piece of wire.
3Support the differential with a trolley jack,
then remove the differential rear mounting
bolt. Push the differential down, and wedge it
into this lowered position with a block of
wood. This reduces the drive angle,
preventing damage to the CV joints when the
trailing arms are lowered to remove the
springs.
4Place a trolley jack under the trailing arm.
5If the vehicle has a rear anti-roll bar,
disconnect the bar from its connecting links,
or disconnect the links from the trailing arms
(see Section 12).
6Loop a chain through the coil spring, and
bolt the chain together, to prevent the coil
spring from popping out when the trailing arm
is lowered. Be sure to leave enough slack in
the chain to allow the spring to extend
completely.
7Disconnect the shock absorber lower
mounting bolt (see Section 9), carefully lower
the trailing arm and remove the coil spring.
Refitting
8Refitting is the reverse of removal. As the
trailing arm is raised back up, make sure the
spring seats properly.
11 Rear shock absorber/coil
spring assembly (5-Series)-
removal and refitting
4
Removal
Note:Although shock absorbers don’t always
wear out simultaneously, renew both left and
right shock absorbers at the same time, to
prevent handling peculiarities or abnormal ride
quality.1Loosen the wheel bolts, then chock the
front wheels. Raise the vehicle and support it
securely on axle stands. Remove the wheels.
2Remove the shock absorber lower
mounting bolt (see illustration).
3On early models, peel back the trim inside
the luggage compartment far enough to
access the upper mounting nuts. To get at the
upper mounting nuts on later models, first
remove the rear seat cushion (see Chap-
ter 11), then remove the two bolts holding the
rear seat backrest, and remove the backrest.
Support the trailing arm with a jack, and
remove the upper mounting nuts (see
illustration). Lower the jack, and remove the
shock absorber and the gasket. To separate
the shock absorber and spring, refer to
Section 6.
Refitting
4Refitting is the reverse of removal. Don’t
forget to fit the gasket between the upper end
of the shock absorber and the body. Tighten
the upper nuts to the torque listed in this
Chapter’s Specifications. Don’t tighten the
lower bolt until the vehicle is lowered.
5Lower the vehicle, and with it sitting at the
normal ride height, tighten the lower bolt to
the torque listed in this Chapter’s Specifi-
cations.
12 Rear anti-roll bar-
removal and refitting
2
Removal
Note:The rear anti-roll bar is mounted
basically the same way on all models. Follow
these general removal and refitting
procedures, keeping in mind any variations.
1Chock the front wheels, then raise the rear
of the vehicle and support it securely on axle
stands.
2Remove the anti-roll bar bracket bolts or
nuts (see illustration).
3Disconnect the anti-roll bar from the link at
each end of the bar (see illustrations)and
detach the anti-roll bar.
Suspension and steering systems 10•9
11.3 Shock absorber upper mounting nuts
(arrowed) on a later (E34) 5-Series model11.2 Remove the shock absorber lower
mounting bolt (arrowed)9.4 Shock absorber upper mounting nuts
(arrowed) - late-model convertible shown.
On other early models, upper nuts are
accessible from the luggage compartment;
on later models, they’re behind the back of
the rear seat, up under the parcel shelf
10
Page 218 of 228
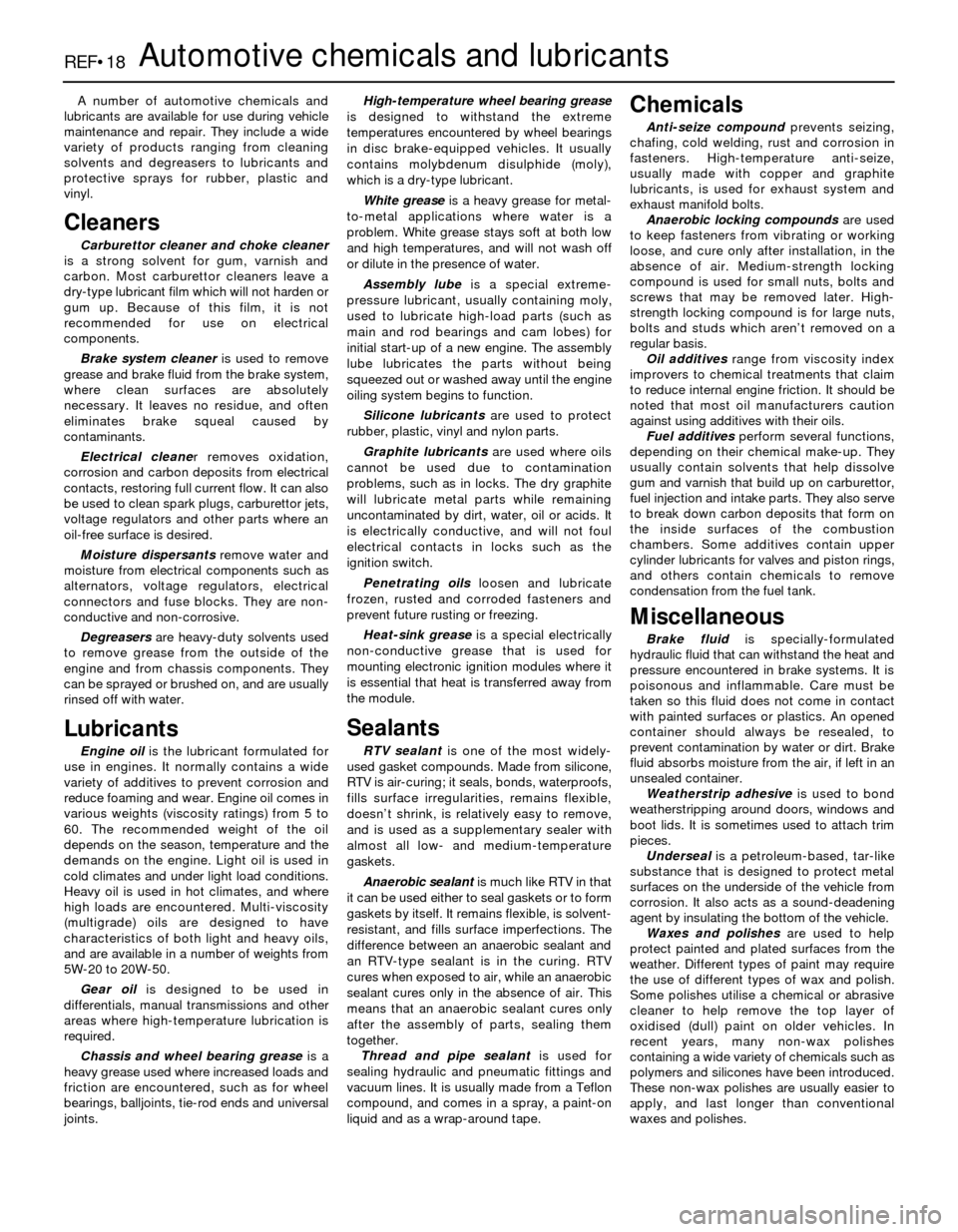
REF•18Automotive chemicals and lubricants
A number of automotive chemicals and
lubricants are available for use during vehicle
maintenance and repair. They include a wide
variety of products ranging from cleaning
solvents and degreasers to lubricants and
protective sprays for rubber, plastic and
vinyl.
Cleaners
Carburettor cleaner and choke cleaner
is a strong solvent for gum, varnish and
carbon. Most carburettor cleaners leave a
dry-type lubricant film which will not harden or
gum up. Because of this film, it is not
recommended for use on electrical
components.
Brake system cleaneris used to remove
grease and brake fluid from the brake system,
where clean surfaces are absolutely
necessary. It leaves no residue, and often
eliminates brake squeal caused by
contaminants.
Electrical cleaner removes oxidation,
corrosion and carbon deposits from electrical
contacts, restoring full current flow. It can also
be used to clean spark plugs, carburettor jets,
voltage regulators and other parts where an
oil-free surface is desired.
Moisture dispersantsremove water and
moisture from electrical components such as
alternators, voltage regulators, electrical
connectors and fuse blocks. They are non-
conductive and non-corrosive.
Degreasersare heavy-duty solvents used
to remove grease from the outside of the
engine and from chassis components. They
can be sprayed or brushed on, and are usually
rinsed off with water.
Lubricants
Engine oilis the lubricant formulated for
use in engines. It normally contains a wide
variety of additives to prevent corrosion and
reduce foaming and wear. Engine oil comes in
various weights (viscosity ratings) from 5 to
60. The recommended weight of the oil
depends on the season, temperature and the
demands on the engine. Light oil is used in
cold climates and under light load conditions.
Heavy oil is used in hot climates, and where
high loads are encountered. Multi-viscosity
(multigrade) oils are designed to have
characteristics of both light and heavy oils,
and are available in a number of weights from
5W-20 to 20W-50.
Gear oilis designed to be used in
differentials, manual transmissions and other
areas where high-temperature lubrication is
required.
Chassis and wheel bearing greaseis a
heavy grease used where increased loads and
friction are encountered, such as for wheel
bearings, balljoints, tie-rod ends and universal
joints.High-temperature wheel bearing grease
is designed to withstand the extreme
temperatures encountered by wheel bearings
in disc brake-equipped vehicles. It usually
contains molybdenum disulphide (moly),
which is a dry-type lubricant.
White greaseis a heavy grease for metal-
to-metal applications where water is a
problem. White grease stays soft at both low
and high temperatures, and will not wash off
or dilute in the presence of water.
Assembly lubeis a special extreme-
pressure lubricant, usually containing moly,
used to lubricate high-load parts (such as
main and rod bearings and cam lobes) for
initial start-up of a new engine. The assembly
lube lubricates the parts without being
squeezed out or washed away until the engine
oiling system begins to function.
Silicone lubricants are used to protect
rubber, plastic, vinyl and nylon parts.
Graphite lubricantsare used where oils
cannot be used due to contamination
problems, such as in locks. The dry graphite
will lubricate metal parts while remaining
uncontaminated by dirt, water, oil or acids. It
is electrically conductive, and will not foul
electrical contacts in locks such as the
ignition switch.
Penetrating oilsloosen and lubricate
frozen, rusted and corroded fasteners and
prevent future rusting or freezing.
Heat-sink greaseis a special electrically
non-conductive grease that is used for
mounting electronic ignition modules where it
is essential that heat is transferred away from
the module.
Sealants
RTV sealantis one of the most widely-
used gasket compounds. Made from silicone,
RTV is air-curing; it seals, bonds, waterproofs,
fills surface irregularities, remains flexible,
doesn’t shrink, is relatively easy to remove,
and is used as a supplementary sealer with
almost all low- and medium-temperature
gaskets.
Anaerobic sealantis much like RTV in that
it can be used either to seal gaskets or to form
gaskets by itself. It remains flexible, is solvent-
resistant, and fills surface imperfections. The
difference between an anaerobic sealant and
an RTV-type sealant is in the curing. RTV
cures when exposed to air, while an anaerobic
sealant cures only in the absence of air. This
means that an anaerobic sealant cures only
after the assembly of parts, sealing them
together.
Thread and pipe sealant is used for
sealing hydraulic and pneumatic fittings and
vacuum lines. It is usually made from a Teflon
compound, and comes in a spray, a paint-on
liquid and as a wrap-around tape.
Chemicals
Anti-seize compoundprevents seizing,
chafing, cold welding, rust and corrosion in
fasteners. High-temperature anti-seize,
usually made with copper and graphite
lubricants, is used for exhaust system and
exhaust manifold bolts.
Anaerobic locking compoundsare used
to keep fasteners from vibrating or working
loose, and cure only after installation, in the
absence of air. Medium-strength locking
compound is used for small nuts, bolts and
screws that may be removed later. High-
strength locking compound is for large nuts,
bolts and studs which aren’t removed on a
regular basis.
Oil additivesrange from viscosity index
improvers to chemical treatments that claim
to reduce internal engine friction. It should be
noted that most oil manufacturers caution
against using additives with their oils.
Fuel additivesperform several functions,
depending on their chemical make-up. They
usually contain solvents that help dissolve
gum and varnish that build up on carburettor,
fuel injection and intake parts. They also serve
to break down carbon deposits that form on
the inside surfaces of the combustion
chambers. Some additives contain upper
cylinder lubricants for valves and piston rings,
and others contain chemicals to remove
condensation from the fuel tank.
Miscellaneous
Brake fluidis specially-formulated
hydraulic fluid that can withstand the heat and
pressure encountered in brake systems. It is
poisonous and inflammable. Care must be
taken so this fluid does not come in contact
with painted surfaces or plastics. An opened
container should always be resealed, to
prevent contamination by water or dirt. Brake
fluid absorbs moisture from the air, if left in an
unsealed container.
Weatherstrip adhesiveis used to bond
weatherstripping around doors, windows and
boot lids. It is sometimes used to attach trim
pieces.
Undersealis a petroleum-based, tar-like
substance that is designed to protect metal
surfaces on the underside of the vehicle from
corrosion. It also acts as a sound-deadening
agent by insulating the bottom of the vehicle.
Waxes and polishesare used to help
protect painted and plated surfaces from the
weather. Different types of paint may require
the use of different types of wax and polish.
Some polishes utilise a chemical or abrasive
cleaner to help remove the top layer of
oxidised (dull) paint on older vehicles. In
recent years, many non-wax polishes
containing a wide variety of chemicals such as
polymers and silicones have been introduced.
These non-wax polishes are usually easier to
apply, and last longer than conventional
waxes and polishes.
Page 220 of 228
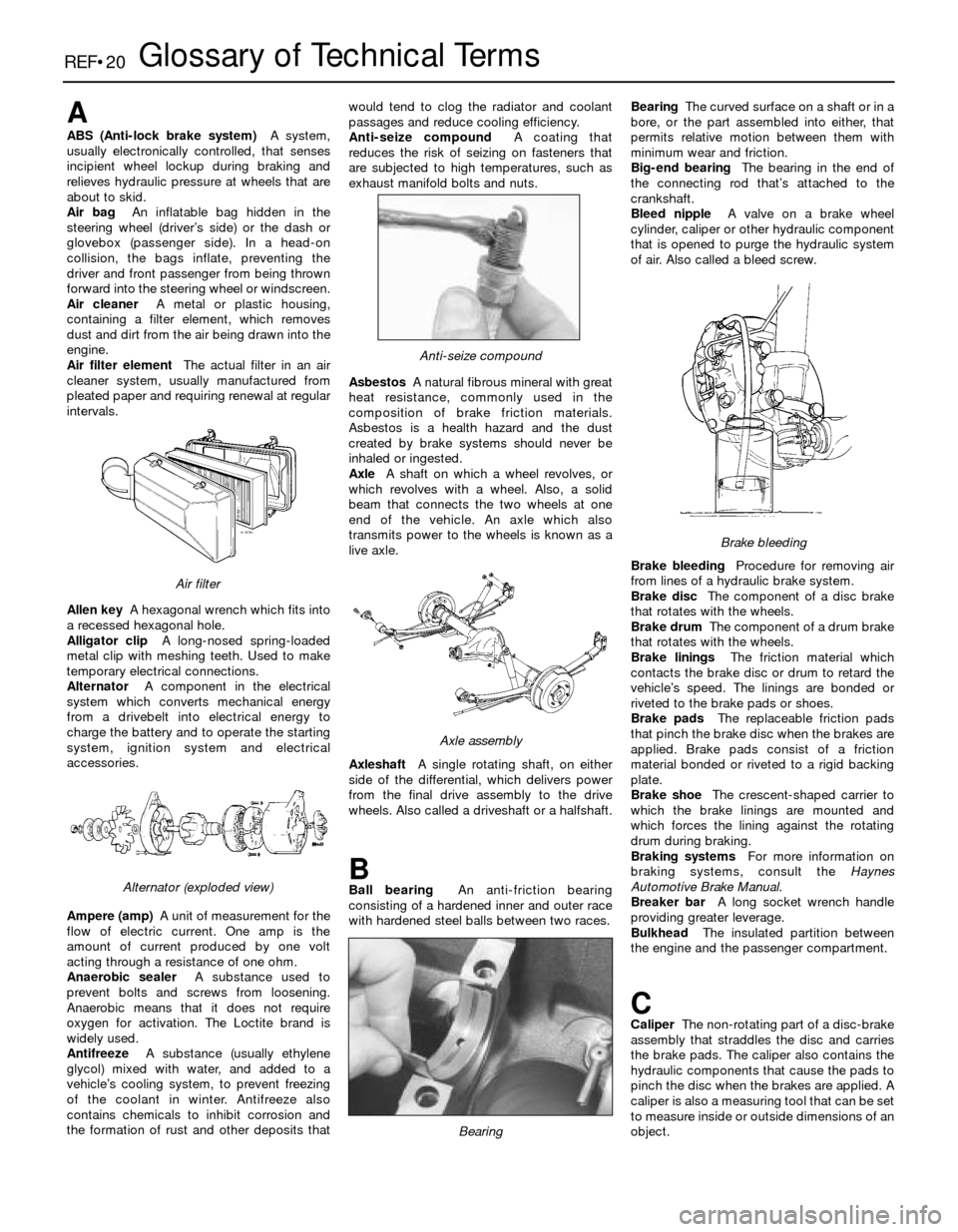
REF•20Glossary of Technical Terms
A
ABS (Anti-lock brake system)A system,
usually electronically controlled, that senses
incipient wheel lockup during braking and
relieves hydraulic pressure at wheels that are
about to skid.
Air bag An inflatable bag hidden in the
steering wheel (driver’s side) or the dash or
glovebox (passenger side). In a head-on
collision, the bags inflate, preventing the
driver and front passenger from being thrown
forward into the steering wheel or windscreen.
Air cleanerA metal or plastic housing,
containing a filter element, which removes
dust and dirt from the air being drawn into the
engine.
Air filter elementThe actual filter in an air
cleaner system, usually manufactured from
pleated paper and requiring renewal at regular
intervals.
Allen keyA hexagonal wrench which fits into
a recessed hexagonal hole.
Alligator clipA long-nosed spring-loaded
metal clip with meshing teeth. Used to make
temporary electrical connections.
AlternatorA component in the electrical
system which converts mechanical energy
from a drivebelt into electrical energy to
charge the battery and to operate the starting
system, ignition system and electrical
accessories.
Ampere (amp)A unit of measurement for the
flow of electric current. One amp is the
amount of current produced by one volt
acting through a resistance of one ohm.
Anaerobic sealerA substance used to
prevent bolts and screws from loosening.
Anaerobic means that it does not require
oxygen for activation. The Loctite brand is
widely used.
AntifreezeA substance (usually ethylene
glycol) mixed with water, and added to a
vehicle’s cooling system, to prevent freezing
of the coolant in winter. Antifreeze also
contains chemicals to inhibit corrosion and
the formation of rust and other deposits thatwould tend to clog the radiator and coolant
passages and reduce cooling efficiency.
Anti-seize compoundA coating that
reduces the risk of seizing on fasteners that
are subjected to high temperatures, such as
exhaust manifold bolts and nuts.
AsbestosA natural fibrous mineral with great
heat resistance, commonly used in the
composition of brake friction materials.
Asbestos is a health hazard and the dust
created by brake systems should never be
inhaled or ingested.
AxleA shaft on which a wheel revolves, or
which revolves with a wheel. Also, a solid
beam that connects the two wheels at one
end of the vehicle. An axle which also
transmits power to the wheels is known as a
live axle.
AxleshaftA single rotating shaft, on either
side of the differential, which delivers power
from the final drive assembly to the drive
wheels. Also called a driveshaft or a halfshaft.
BBall bearingAn anti-friction bearing
consisting of a hardened inner and outer race
with hardened steel balls between two races.BearingThe curved surface on a shaft or in a
bore, or the part assembled into either, that
permits relative motion between them with
minimum wear and friction.
Big-end bearingThe bearing in the end of
the connecting rod that’s attached to the
crankshaft.
Bleed nippleA valve on a brake wheel
cylinder, caliper or other hydraulic component
that is opened to purge the hydraulic system
of air. Also called a bleed screw.
Brake bleedingProcedure for removing air
from lines of a hydraulic brake system.
Brake discThe component of a disc brake
that rotates with the wheels.
Brake drumThe component of a drum brake
that rotates with the wheels.
Brake liningsThe friction material which
contacts the brake disc or drum to retard the
vehicle’s speed. The linings are bonded or
riveted to the brake pads or shoes.
Brake padsThe replaceable friction pads
that pinch the brake disc when the brakes are
applied. Brake pads consist of a friction
material bonded or riveted to a rigid backing
plate.
Brake shoeThe crescent-shaped carrier to
which the brake linings are mounted and
which forces the lining against the rotating
drum during braking.
Braking systemsFor more information on
braking systems, consult the Haynes
Automotive Brake Manual.
Breaker barA long socket wrench handle
providing greater leverage.
BulkheadThe insulated partition between
the engine and the passenger compartment.
CCaliperThe non-rotating part of a disc-brake
assembly that straddles the disc and carries
the brake pads. The caliper also contains the
hydraulic components that cause the pads to
pinch the disc when the brakes are applied. A
caliper is also a measuring tool that can be set
to measure inside or outside dimensions of an
object.
Brake bleeding
Bearing
Axle assembly
Anti-seize compound
Alternator (exploded view)
Air filter
Page 223 of 228

REF•23
REF
Glossary of Technical Terms
JJump startStarting the engine of a vehicle
with a discharged or weak battery by
attaching jump leads from the weak battery to
a charged or helper battery.
LLoad Sensing Proportioning Valve (LSPV)A
brake hydraulic system control valve that
works like a proportioning valve, but also
takes into consideration the amount of weight
carried by the rear axle.
LocknutA nut used to lock an adjustment
nut, or other threaded component, in place.
For example, a locknut is employed to keep
the adjusting nut on the rocker arm in
position.
LockwasherA form of washer designed to
prevent an attaching nut from working loose.
MMacPherson strutA type of front
suspension system devised by Earle
MacPherson at Ford of England. In its original
form, a simple lateral link with the anti-roll bar
creates the lower control arm. A long strut - an
integral coil spring and shock absorber - is
mounted between the body and the steering
knuckle. Many modern so-called MacPherson
strut systems use a conventional lower A-arm
and don’t rely on the anti-roll bar for location.
MultimeterAn electrical test instrument with
the capability to measure voltage, current and
resistance.
NNOxOxides of Nitrogen. A common toxic
pollutant emitted by petrol and diesel engines
at higher temperatures.
OOhmThe unit of electrical resistance. One
volt applied to a resistance of one ohm will
produce a current of one amp.
OhmmeterAn instrument for measuring
electrical resistance.
O-ringA type of sealing ring made of a
special rubber-like material; in use, the O-ring
is compressed into a groove to provide the
sealing action.Overhead cam (ohc) engineAn engine with
the camshaft(s) located on top of the cylinder
head(s).
Overhead valve (ohv) engineAn engine with
the valves located in the cylinder head, but
with the camshaft located in the engine block.
Oxygen sensorA device installed in the
engine exhaust manifold, which senses the
oxygen content in the exhaust and converts
this information into an electric current. Also
called a Lambda sensor.
PPhillips screwA type of screw head having a
cross instead of a slot for a corresponding
type of screwdriver.
PlastigageA thin strip of plastic thread,
available in different sizes, used for measuring
clearances. For example, a strip of Plastigage
is laid across a bearing journal. The parts are
assembled and dismantled; the width of the
crushed strip indicates the clearance between
journal and bearing.
Propeller shaftThe long hollow tube with
universal joints at both ends that carries
power from the transmission to the differential
on front-engined rear wheel drive vehicles.
Proportioning valveA hydraulic control
valve which limits the amount of pressure to
the rear brakes during panic stops to prevent
wheel lock-up.
RRack-and-pinion steeringA steering system
with a pinion gear on the end of the steering
shaft that mates with a rack (think of a geared
wheel opened up and laid flat). When the
steering wheel is turned, the pinion turns,
moving the rack to the left or right. This
movement is transmitted through the track
rods to the steering arms at the wheels.
RadiatorA liquid-to-air heat transfer device
designed to reduce the temperature of the
coolant in an internal combustion engine
cooling system.
RefrigerantAny substance used as a heat
transfer agent in an air-conditioning system.
R-12 has been the principle refrigerant for
many years; recently, however, manufacturers
have begun using R-134a, a non-CFC
substance that is considered less harmful tothe ozone in the upper atmosphere.
Rocker armA lever arm that rocks on a shaft
or pivots on a stud. In an overhead valve
engine, the rocker arm converts the upward
movement of the pushrod into a downward
movement to open a valve.
RotorIn a distributor, the rotating device
inside the cap that connects the centre
electrode and the outer terminals as it turns,
distributing the high voltage from the coil
secondary winding to the proper spark plug.
Also, that part of an alternator which rotates
inside the stator. Also, the rotating assembly
of a turbocharger, including the compressor
wheel, shaft and turbine wheel.
RunoutThe amount of wobble (in-and-out
movement) of a gear or wheel as it’s rotated.
The amount a shaft rotates “out-of-true.” The
out-of-round condition of a rotating part.
SSealantA liquid or paste used to prevent
leakage at a joint. Sometimes used in
conjunction with a gasket.
Sealed beam lampAn older headlight design
which integrates the reflector, lens and
filaments into a hermetically-sealed one-piece
unit. When a filament burns out or the lens
cracks, the entire unit is simply replaced.
Serpentine drivebeltA single, long, wide
accessory drivebelt that’s used on some
newer vehicles to drive all the accessories,
instead of a series of smaller, shorter belts.
Serpentine drivebelts are usually tensioned by
an automatic tensioner.
ShimThin spacer, commonly used to adjust
the clearance or relative positions between
two parts. For example, shims inserted into or
under bucket tappets control valve
clearances. Clearance is adjusted by
changing the thickness of the shim.
Slide hammerA special puller that screws
into or hooks onto a component such as a
shaft or bearing; a heavy sliding handle on the
shaft bottoms against the end of the shaft to
knock the component free.
SprocketA tooth or projection on the
periphery of a wheel, shaped to engage with a
chain or drivebelt. Commonly used to refer to
the sprocket wheel itself.
Starter inhibitor switchOn vehicles with an
O-ring
Serpentine drivebelt
Plastigage