key BMW 318i 1992 E36 Owner's Manual
[x] Cancel search | Manufacturer: BMW, Model Year: 1992, Model line: 318i, Model: BMW 318i 1992 E36Pages: 759
Page 161 of 759

u0
I
.[
Ia
Fig
.
21
.
Air
flow
sensor
harness
connector
terminal
identification
.
4
.
Replacing
air
flow
sensor
:
"
Remove
large
band
clamp
attaching
air
boot
to
sensor
.
"
Remove
airfiltertop
cover,
then
remove
airflow
sensor
mounting
nuts
inside
cover
.
"
Reconnect
air
boot
and
harness
connector
.
Engine
coolant
temperature
(ECT)
sensor,
testing
and
replacing
The
engine
coolant
temperature
(ECT)
sensor
sends
con-
tinuous
engine
coolant
temperature
information
to
the
ECM
.
As
temperature
increases,
sensor
resistance
decreases
.
"
With
harness
connector
disconnected,
check
resis-
tance
across
sensor
terminals
.
"
Compare
tests
results
to
values
in
Table
d
.
FUEL
INJECTION
130-
1
5
0011984
Fig
.
22
.
M42
engine
coolant
temperature
(ECG
sensor
(arrow)
.
Table
d
.
Engine
Coolant
Temperature
Sensoror
Intake
Air
TemperatureSensor
Test
Values
(DME
1
.7)
Test
temperatures
Resistance
(k
ohms)
',
14±2°F(-10t1°C)
7-11
.6
68±2°F
(20
t
1
°C)
2
.1
-2
.9
176
±
2°F
(80
t
V
C)
0
.27-0
.40
The
ECT
sensor
is
located
under
number
one
intake
run-
'
ner
.
See
Fig
.
22
.
NOTE-
1
.
Check
ECM
referente
voltage
to
sensor
:
The
test
values
listed
represent
only
three
test
points
from
a
continuous
resistance
NTC
sensor
.
Check
the
"
Disconnect
harness
connectorfrom
ECT
sensor
.
full
linear
response
to
increasing
temperature
as
the
"
Turn
ignition
key
on
.
engine
warms
up
.
"
Check
for
5
volts
between
supply
voltage
(brown/red)
wire
of
harness
connector
and
ground
.
3
.
If
ECT
sensor
fails
these
tests,
it
is
faulty
and
should
be
"
Turn
ignition
key
off
.
replaced
.
If
no
faults
are
found,
reconnect
electrical
"
If
voltage
is
not
present
or
incorrect,
check
wring
from
harness
.
ECM
and
check
ECT
sensor
reference
voltage
output
at
ECM
.
See
Table
h
.
NOTE-
2
.
Check
ECT
sensor
resistance
:
Use
a
new
copper
sealing
washer
when
installing
sen-
sor
.
Reptace
any
lost
coolant
.
WARNING
-
Do
not
replace
the
ECT
sensor
unlessthe
engine
is
cold
.
Hot
coolant
can
scald
.
Tightening
Torque
"
ECT
sensor
to
cylinder
head
.....
..
13
Nm
(10
ft-Ib)
BOSCH
DME
M1
.7
COMPONENT
TESTS
AND
REPAIRS
Page 162 of 759
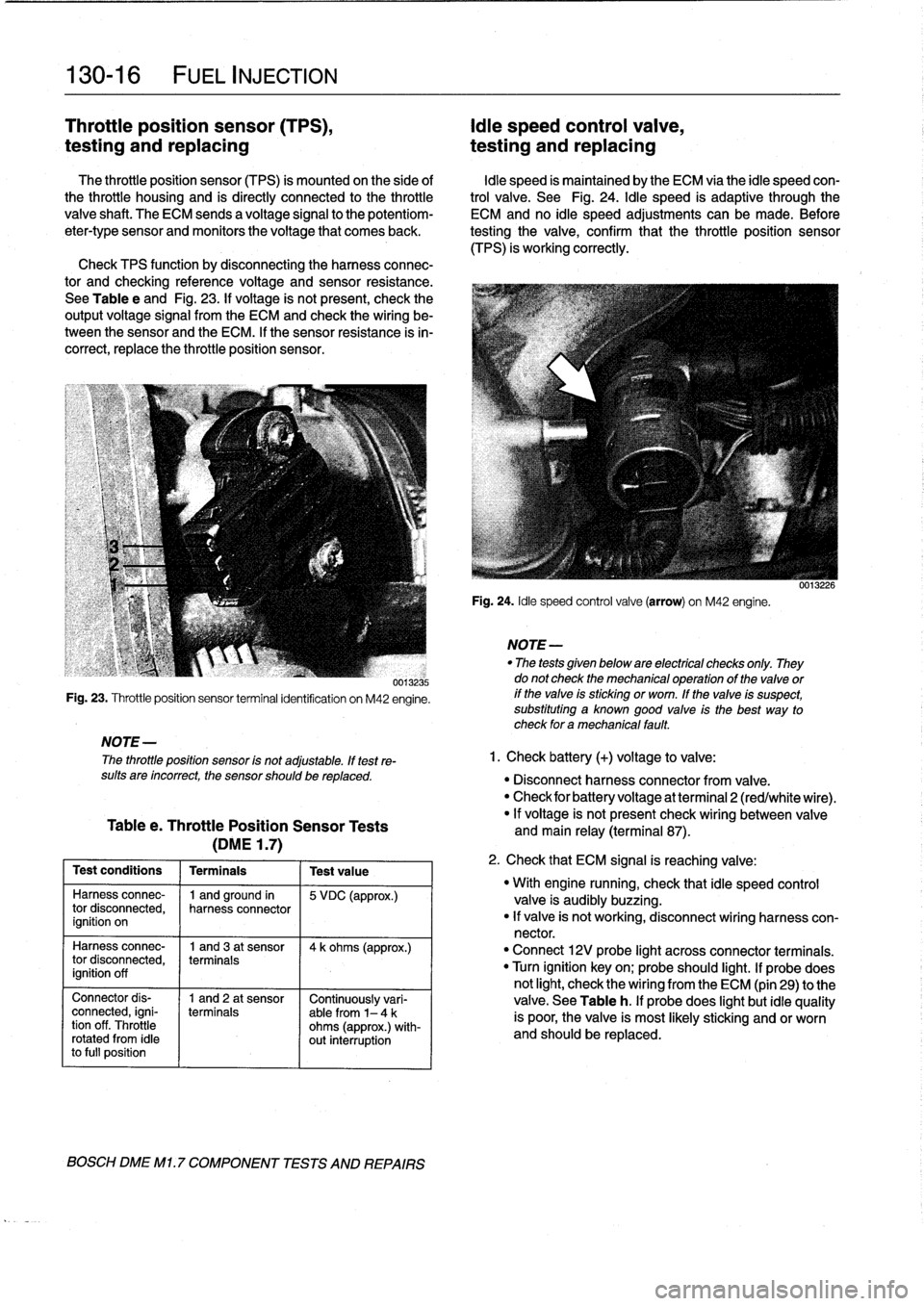
130-
1
6
FUEL
INJECTION
Throttie
position
sensor
(TPS),
Idie
speed
control
valve,
testing
and
replacing
testing
and
replacing
The
throttie
position
sensor
(TPS)
is
mounted
on
the
side
of
¡die
speed
is
maintained
by
the
ECM
via
the
¡die
speed
con-
the
throttie
housing
and
is
directly
connected
to
the
throttie
trol
valve
.
See
Fig
.
24
.
¡die
speed
is
adaptive
through
the
valve
shaft
.
The
ECM
sends
a
voltage
signal
to
the
potentiom-
ECM
and
no
¡die
speed
adjustments
can
be
made
.
Before
eter-type
sensor
and
monitors
the
voltage
that
comes
back
.
testing
the
valve,
confirm
that
the
throttie
position
sensor(TPS)
is
working
correctly
.
Check
TPS
function
by
disconnecting
the
harnessconnec-
tor
and
checking
reference
voltage
and
sensor
resistance
.
See
Table
e
and
Fig
.
23
.
If
voltage
is
not
present,
check
the
output
voltage
signal
from
the
ECM
and
check
the
wiring
be-
tween
the
sensor
and
the
ECM
.
If
the
sensor
resistance
is
in-
correct,
replace
the
throttie
position
sensor
.
NOTE
-
The
throttie
position
sensor
is
not
adjustable
.
If
test
re-
sults
are
íncorrect,
the
sensor
should
be
replaced
.
Table
e
.
Throttle
Position
Sensor
Tests
(DME
1
.7)
Testconditions
1
Terminais
1
Test
value
Harness
connec-
(
1
and
ground
in
15
VDC
(approx
.)
tor
disconnected,
harness
connector
ignition
on
0013235
Fig
.
23
.
Throttieposition
sensor
terminal
identification
on
M42
engine
.
Harnessconnec-
I
1
and
3
at
sensor
(
4k
ohms
(approx
.)
tor
disconnected,
terminais
ignition
off
Connector
dis-
1
and
2
at
sensor
Continuously
vari-
connected,
igni-
terminais
able
from
1-4
k
tion
off
.
Throttle
ohms
(approx
.)
with
rotated
from
¡die
out
interruption
to
fui]
position
BOSCH
DME
Ml
.
7
COMPONENT
TESTS
AND
REPAIRS
Fig
.
24
.
¡die
speed
control
valve
(arrow)
on
M42
engine
.
NOTE
-
"
The
tests
given
below
are
electrical
checks
only
.
They
do
not
check
the
mechanical
operation
of
the
valve
or
if
the
valve
is
sticking
or
worn
.
If
the
valve
is
suspect,
substituting
a
known
good
valve
is
the
best
way
to
check
for
amechanical
fault
.
1
.
Check
battery
(+)
voltage
to
valve
:
0013226
"
Disconnect
harness
connector
from
valve
.
"
Check
for
battery
voltage
at
terminal
2
(red/white
wire)
.
"
If
voltage
is
not
present
check
wiring
between
valve
and
main
relay
(terminal
87)
.
2
.
Check
that
ECM
signal
is
reaching
valve
:
"
With
engine
running,
check
that
¡die
speed
control
valve
is
audibly
buzzing
.
"
If
valve
is
not
working,
disconnect
wiring
harness
con-
nector
.
"
Connect
12V
probe
light
across
connector
terminais
.
"
Turn
ignition
key
on
;
probe
should
light
.
lf
probe
does
nof
light,
check
the
wiring
from
the
ECM
(pin
29)
to
the
valve
.
See
Table
h
.
lf
probe
does
light
but
¡die
quality
is
poor,
the
valve
is
most
likely
sticking
and
or
worn
and
should
be
replaced
.
Page 163 of 759
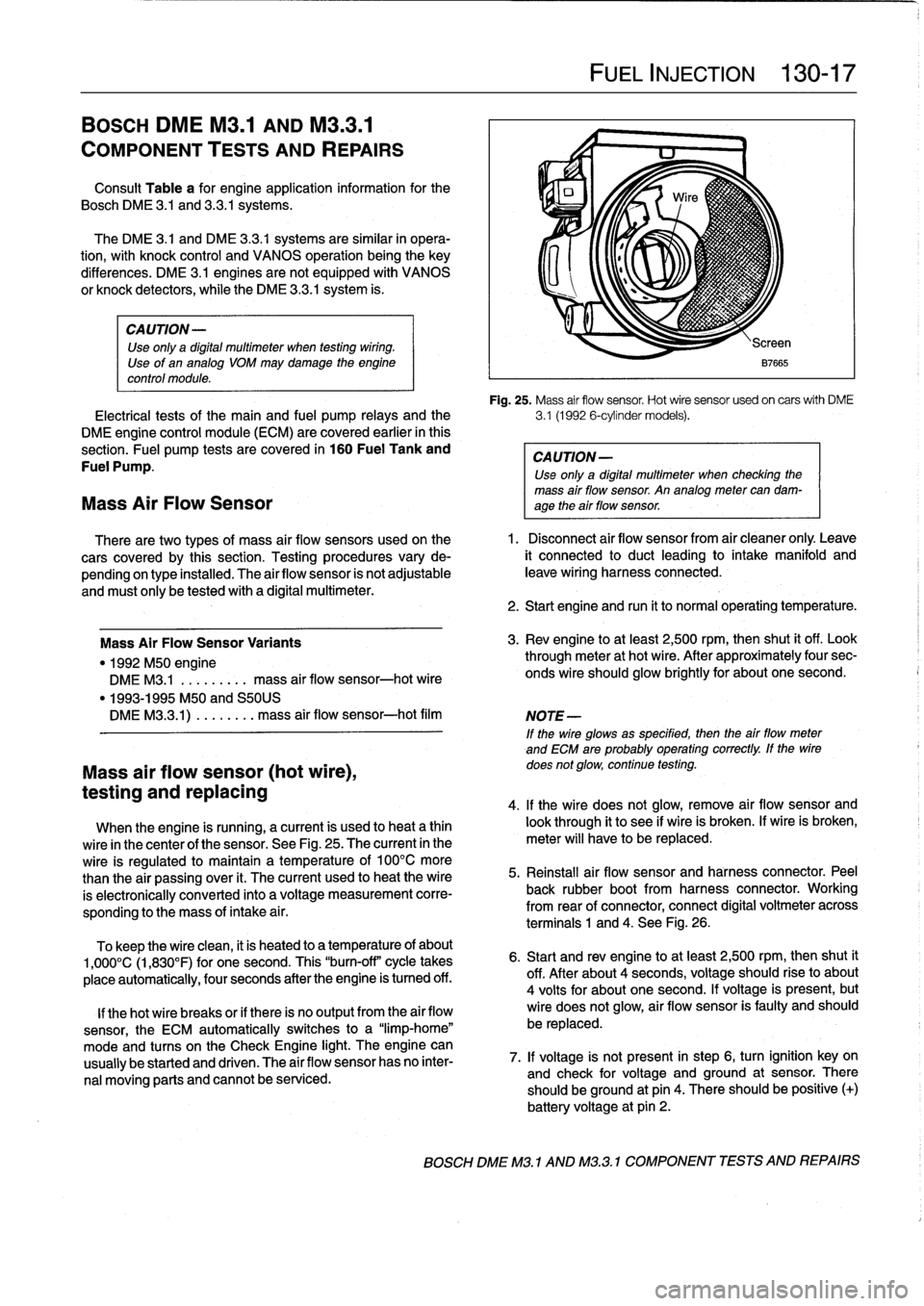
BOSCH
DME
MM
AND
M33
.1
COMPONENT
TESTS
AND
REPAIRS
Consult
Table
a
for
engine
application
information
for
the
Bosch
DME
3
.1
and
3
.3.1
systems
.
The
DME
3
.1
and
DME
3
.3
.1
systems
are
similar
in
opera-
tion,
with
knock
control
and
VANOS
operation
being
the
key
differences
.
DME
3
.1
engines
arenot
equipped
with
VANOS
or
knock
detectors,
while
the
DM
E3
.3
.1
system
is
.
CA
UTION-
Use
onty
a
digital
multimeter
when
testing
wiring
.
Use
of
an
analog
VOM
may
damage
the
engine
control
module
.
Fig
.
25
.
Mass
air
flow
sensor
.
Hot
wire
sensor
usedon
carswith
DME
Electrical
tests
of
the
main
and
fuel
pump
relays
and
the
3
.1
(1992
6-cylinder
models)
.
DME
engine
control
module
(ECM)
are
covered
earlier
in
this
section
.
Fuel
pump
tests
are
covered
in
160
Fuel
Tank
and
CAUTION-
Fuel
Pump
.
Use
only
a
digital
multimeter
when
checking
the
mass
air
flow
sensor
.
An
analog
meter
can
dam-
Mass
Air
Flow
Sensor
age
theair
flow
sensor
.
There
are
two
types
of
mass
air
flow
sensors
used
onthe
1
.
Disconnect
air
flow
sensor
from
air
cleaner
only
.
Leave
cars
covered
by
this
section
.
Testing
procedures
vary
de-
it
connected
to
duct
leading
to
intake
manifold
and
pending
on
type
installed
.
The
airflow
sensor
is
not
adjustable
leave
wiring
harness
connected
.
and
must
only
be
tested
with
a
digital
multimeter
.
Mass
Air
FlowSensor
Variants
"
1992
M50
engine
DME
M3
.1
.
.
.
.
...
..
mass
air
flow
sensor-hot
wire
"
1993-1995
M50
and
S50US
DMEM33
.1)
.
...
...
.
mass
air
flow
sensor-hot
film
Mass
air
flow
sensor
(hot
wire),
testing
and
replacing
When
the
engine
is
running,
a
current
is
used
to
heat
a
thin
wire
in
the
center
of
the
sensor
.
See
Fig
.
25
.
The
current
in
the
wire
is
regulated
to
maintain
a
temperature
of
100°C
more
than
the
air
passing
over
it
.
The
current
used
to
heat
the
wire
is
electronically
conneced
into
a
voltage
measurement
corre-
sponding
to
the
mass
of
intake
a¡
r
.
To
keep
the
wire
clean,
it
is
heated
to
a
temperature
of
about
1,000°C
(1,830°F)
for
one
second
.
This
"burn-off"
cycle
takes
place
automatically,
four
seconds
after
the
engine
is
tumed
off
.
lf
thehot
wire
breaks
or
if
there
is
no
output
from
the
air
flow
sensor,
the
ECM
automatically
switches
to
a
"limp-home"
mode
and
tucos
on
the
Check
Engine
light
.
The
engine
can
usually
be
started
and
driven
.
The
air
flow
sensor
has
no
inter-
nal
moving
parts
and
cannot
be
serviced
.
FUEL
INJECTION
130-
1
7
2
.
Start
engine
and
run
it
to
normal
operating
temperature
.
3
.
Rev
engine
toat
least
2,500
rpm,then
shut
it
off
.
Look
through
meter
at
hot
wire
.
After
approximately
four
sec-
onds
wire
should
glow
brightly
for
about
one
second
.
NOTE
-
If
the
wire
glowsas
specified,
then
the
airflow
meter
and
ECM
are
probably
operating
correctly
.
lf
the
wire
does
not
glow,
continue
testing
.
4
.
lf
the
wire
does
not
glow,
remove
air
flow
sensor
and
look
through
it
to
see
if
wire
is
broken
.
lf
wire
is
broken,
meter
will
have
to
be
replaced
.
5
.
Reinstall
air
flow
sensor
and
harness
connector
.
Peel
back
rubber
bootfrom
harness
connector
.
Working
from
rear
of
connector,
connect
digital
voltmeter
across
terminals
1
and
4
.
See
Fig
.
26
.
6
.
Start
and
rev
engine
toat
least
2,500
rpm,thenshut
it
off
.
After
about
4
seconds,
voltage
should
riseto
about
4
volts
for
about
one
second
.
lf
voltage
is
present,
but
wire
does
not
glow,
air
flow
sensor
is
faulty
and
should
be
replaced
.
7
.
lf
voltage
is
not
present
in
step
6,
turn
ignition
key
on
and
check
for
voltage
and
ground
at
sensor
.
There
should
beground
at
pin
4
.
There
should
be
positive
(+)
battery
voltage
at
pin
2
.
BOSCH
DME
M3
.1
AND
M32
.1
COMPONENT
TESTS
AND
REPAIRS
Page 164 of 759
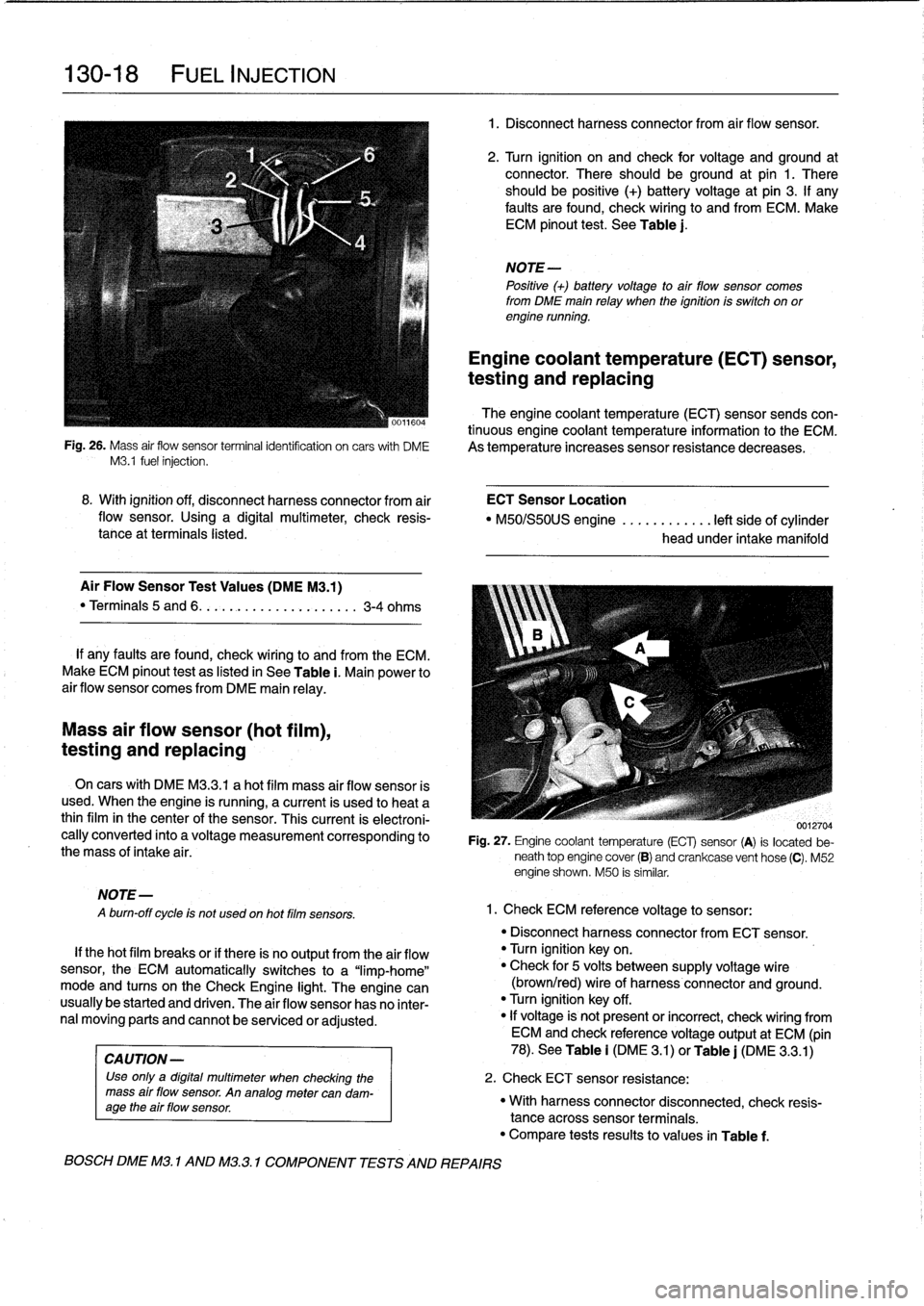
130-18
FUEL
INJECTION
The
engine
coolant
temperature
(ECT)
sensor
sends
con-
tinuous
engine
coolant
temperature
information
to
the
ECM
.
Fig
.
26
.
Mass
air
flow
sensor
terminalidentifcation
on
carswith
DME
As
temperature
increases
sensor
resistance
decreases
.
M3
.1
fuel
injection
.
Mass
air
flow
sensor
(hot
film),
testing
and
replacing
MOTE-
A
burn-off
cycle
is
not
used
on
hot
film
sensors
.
8
.
With
ignition
off,
disconnect
harness
connector
from
air
ECT
Sensor
Location
flow
sensor
.
Using
a
digital
multimeter,
check
resis-
"
M50/S50US
engine
............
left
side
of
cylinder
tance
at
terminals
listed
.
head
under
intake
manifold
Air
Flow
Sensor
Test
Values
(DMEM3
.1)
"
Terminals
5
and
6
.
.
.
.........
..
.
..
....
3-4
ohms
If
any
faults
are
found,
check
wiring
lo
and
from
the
ECM
.
Make
ECM
pinout
test
as
listed
in
See
Table
i
.
Main
power
to
air
flow
sensor
comes
from
DME
main
relay
.
On
cars
with
DME
M3
.3
.1
a
hot
film
mass
air
flow
sensor
is
used
.
When
the
engine
is
running,
a
current
is
used
lo
heat
a
thinfilm
in
the
center
of
the
sensor
.
This
current
is
electroni-
cally
converted
into
a
voltage
measurement
corresponding
to
the
mass
of
intake
air
.
If
thehot
film
breaks
or
if
there
is
no
output
from
the
air
flow
sensor,
the
ECM
automatically
switches
to
a
"limp-home"
mode
and
tucos
on
the
Check
Engine
light
.
The
engine
can
usually
be
started
and
driven
.
The
air
flow
sensor
has
no
inter-
nal
moving
parts
and
cannot
be
senricedor
adjusted
.
CA
UTION-
Use
only
a
digital
multimeter
when
checking
the
mass
air
flow
sensor
.
An
analogmetercan
dam-
age
the
air
flow
sensor
.
BOSCH
DME
M3
.
1
AND
M32
.1
COMPONENT
TESTS
AND
REPAIRS
1
.
Disconnect
harnessconnector
from
air
flow
sensor
.
2
.
Turn
ignition
on
and
check
for
voltage
and
ground
at
connector
.
There
should
beground
at
pin
1
.
There
should
be
positive
(+)
battery
voltage
at
pin
3
.
If
any
faults
are
found,
check
wiring
to
and
from
ECM
.
Make
ECM
pinout
test
.
See
Table
j
.
NOTE-
Positive
(+)
battery
voltage
to
air
flow
sensor
comes
from
DME
main
relay
when
the
ignition
is
switch
on
orengine
running
.
Engine
coolant
temperature
(ECT)
sensor,
testing
and
replacing
0012704
Fig
.
27
.
Engine
coolant
temperature
(ECT)
sensor
(A)
is
located
be-
neath
top
engine
cover
(B)
and
crankcase
vent
hose
(C)
.
M52
engine
shown
.
M50
is
similar
.
1
.
Check
ECM
reference
voltage
to
sensor
:
"
Disconnect
harnessconnector
from
ECT
sensor
.
"
Turn
ignition
keyon
.
"
Check
for
5
volts
between
supply
voltage
wire
(brown/red)
wire
of
harness
connector
and
ground
.
"
Turn
ignition
key
off
.
"
If
voltage
is'
not
present
or
incorrect,
check
wiring
from
ECM
and
check
referencevoltage
output
at
ECM
(pin
78)
.
See
Table
i
(DM
E
3
.1)
or
Table
j
(DME
3
.3
.1)
2
.
Check
ECT
sensor
resistance
:
"
With
harnessconnector
disconnected,
check
resis-
tance
acrosssensor
terminals
.
"
Compare
tests
results
to
values
in
Table
f
.
Page 165 of 759
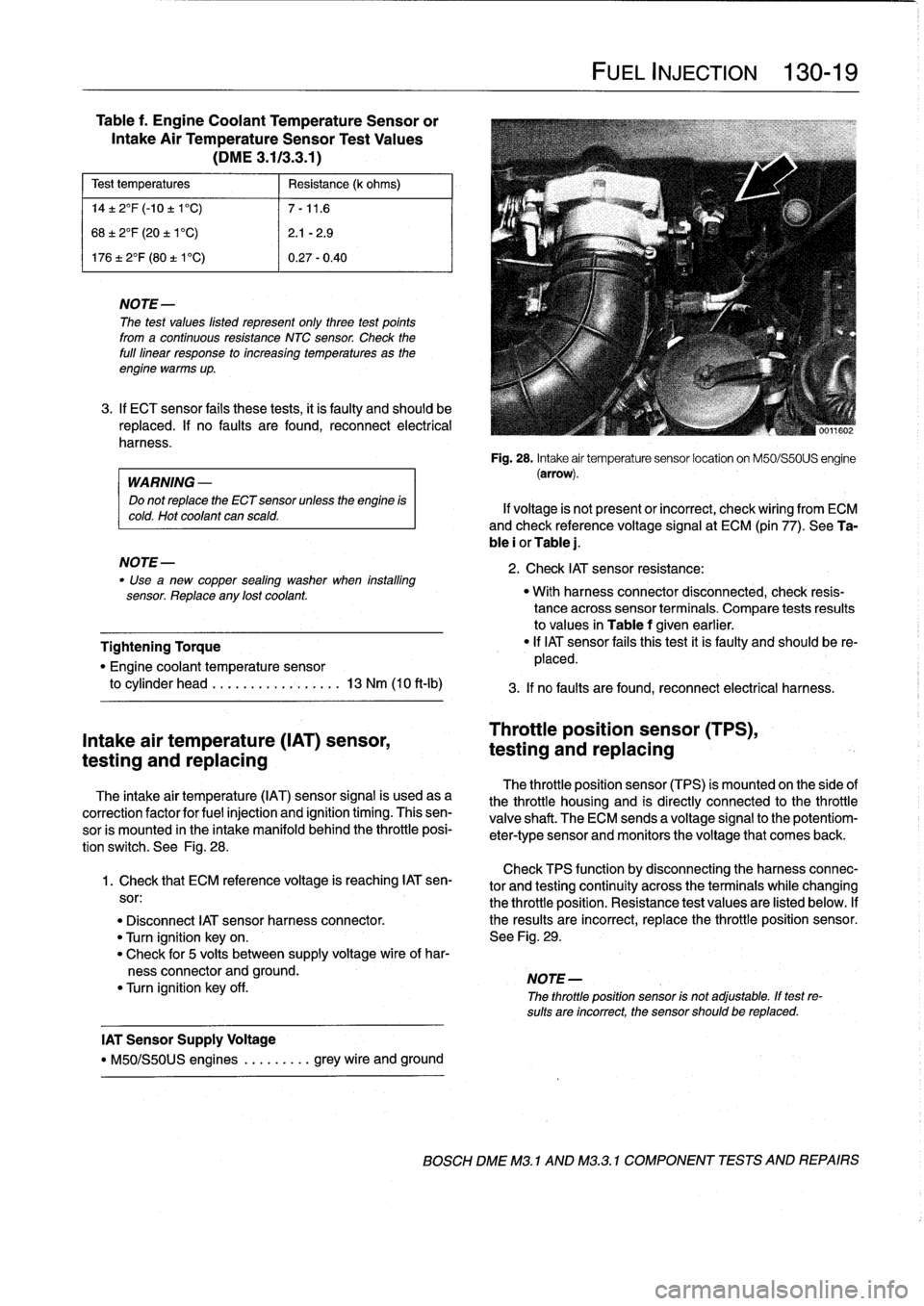
Table
f
.
Engine
Coolant
TemperatureSensor
or
Intake
Air
TemperatureSensor
Test
Values
(DME
3
.113
.3
.1)
Test
temperatures
Resistance
(k
ohms)
14±
2°F
(-10
±
1'C)
7-11
.6
68±
2°F
(20
±
1'C)
2
.1
-2
.9
17612°F
(80
t
V
C)
0
.27-0
.40
NOTE
The
test
values
listed
represent
only
three
test
points
from
a
continuous
resistance
NTC
sensor
.
Check
the
full
linear
response
to
increasing
temperatures
as
the
engine
warms
up
.
3
.
If
ECT
sensor
fails
these
tests,
it
is
faulty
and
should
be
replaced
.
If
no
faults
are
found,
reconnect
electrical
harness
.
WARNING
-
Do
not
replace
the
ECT
sensor
unless
the
engine
is
cold
.
Hot
coolant
can
scald
.
NOTE-
Use
"
a
new
copper
sealing
washer
when
installing
sensor
.
Replace
any
lost
coolant
.
Tightening
Torque
"
Engine
coolant
temperature
sensor
to
cylinder
head
.........
..
.
..
...
13
Nm
(10
ft-lb)
Intake
air
temperature
(IAT)
sensor,
testing
and
replacing
The
intake
air
temperature
(IAT)
sensor
signal
is
usedasa
correction
factor
for
fuel
injection
and
ignition
timing
.
Thissen-
sor
is
mounted
in
the
intake
manifold
behind
the
throttle
posi-
tion
switch
.
See
Fig
.
28
.
Check
TPS
function
by
disconnecting
theharnessconnec-
1
.
Check
that
ECM
reference
voltage
is
reaching
IAT
sen-
tor
and
testing
continuity
across
the
terminalswhile
changing
sor
:
the
throttle
position
.
Resistance
test
values
are
listed
below
.
If
"
Disconnect
IAT
sensor
harness
connector
.
the
resuits
are
incorrect,
replace
the
throttle
position
sensor
.
"
Turn
ignition
keyon
.
See
Fig
.
29
.
"
Check
for
5
volts
between
supply
voltage
wire
of
har-
ness
connector
and
ground
.
NOTE-
"
Turn
ignition
key
off
.
The
throttle
position
sensor
is
not
adjustable
.
If
test
re-
sults
are
incorrect,
the
sensor
should
be
replaced
.
IAT
Sensor
Supply
Voltage
"
M50/S50US
engines
.
........
grey
wire
and
ground
FUEL
INJECTION
130-19
Fig
.
28
.
Intake
air
temperature
sensor
location
on
M50/S50US
engine
(arrow)
.
If
voltage
is
not
present
or
incorrect,
check
wiring
from
ECM
and
check
reference
voltage
signal
at
ECM
(pin
77)
.
See
Ta-
ble
i
or
Table
j
.
2
.
Check
IAT
sensor
resistance
:
"
With
harness
connector
disconnected,
check
resis-
tance
acrosssensor
terminals
.
Compare
tests
resuits
to
values
in
Table
f
given
earlier
.
"
If
IAT
sensor
fafs
thistest
it
is
faulty
and
should
be
re-
placed
.
3
.
If
no
faults
are
found,
reconnect
electrical
harness
.
Throttle
position
sensor
(TPS),
testing
and
replacing
The
throttle
position
sensor
(TPS)
is
mounted
on
the
side
of
the
throttle
housing
and
is
directly
connected
to
the
throttle
valve
shaft
.
The
ECM
sends
a
voltage
signal
to
the
potentiom-
eter-type
sensor
and
monitors
the
voltage
that
comes
back
.
BOSCH
DME
M3
.
1
AND
M32
.1
COMPONENT
TESTS
AND
REPAIRS
Page 177 of 759
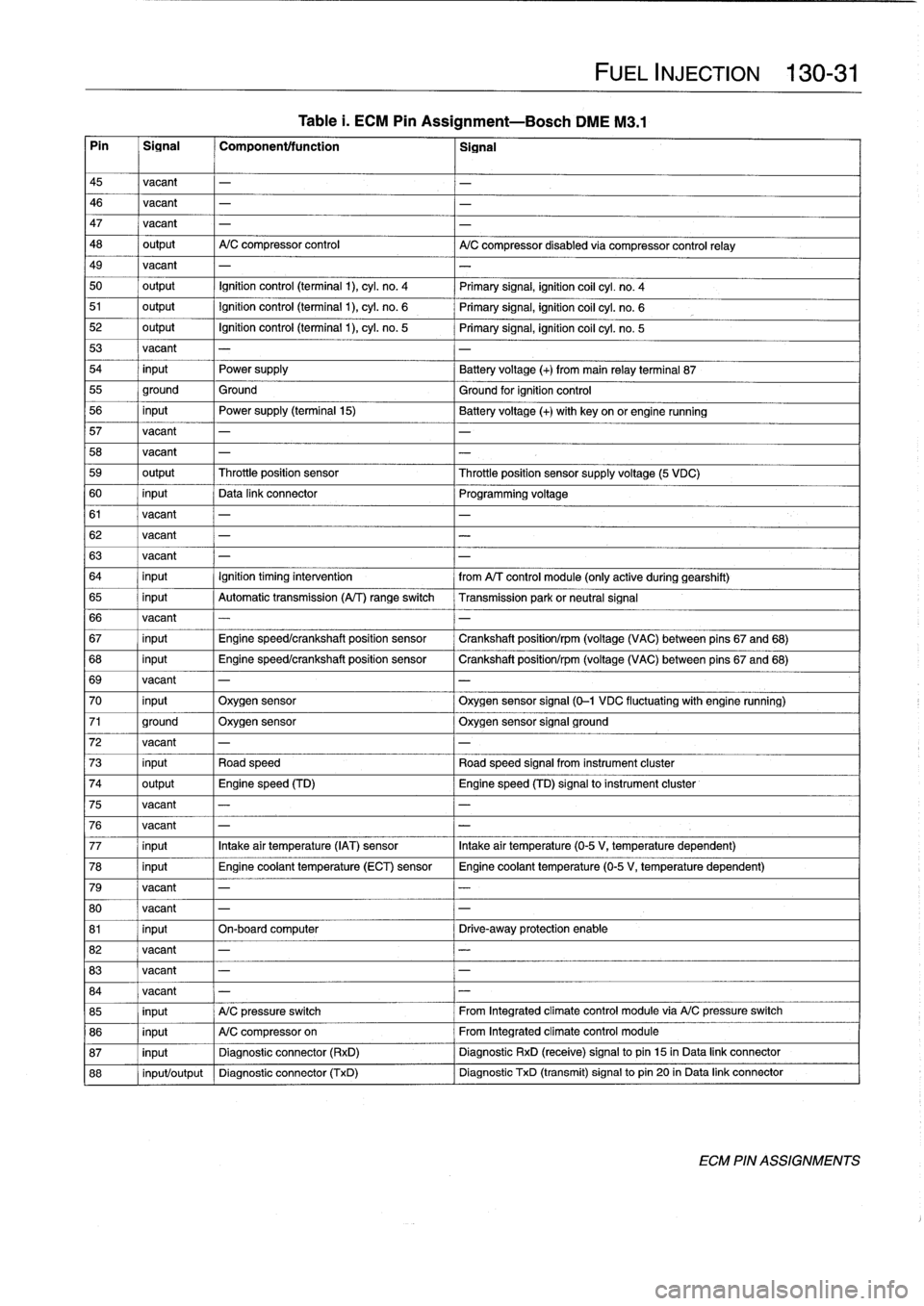
Table
i
.
ECM
Pin
Assignment-Bosch
DME
M3
.1
Pin
Signal
Component/function
2
ignal
FUEL
INJECTION
130-
3
1
45
vacant
-
46
vacant
-
-
47
vacant
-
-
48
output
A/C
compressor
control
A/C
compressor
disabled
via
compressor
control
relay
49
vacant
-
-
50
output
Ignition
control
(terminal
1),cyl
.
n
o
.
4
Primary
signal,
ignition
coil
cyl
.
n
o
.
4
51
output
Ignition
control
(terminal
1),cyl
.
n
o
.
6
Primary
signal,
ignition
coil
cyl
.
no
.
6
52
output
Ignition
control
(terminal
1),cyl
.
n
o
.
5
Primary
signal,
ignitioncoil
cyl
.
no
.
5
53
vacant
-
54
input
Power
supply
Battery
voltage
(+)
from
main
relay
terminal
87
55
ground
Ground
Ground
for
ignition
control
56
input
Power
supply
(terminal
15)
Batteryvoltage
(+)
with
key
on
or
engine
running
57
vacant
-
-
58
vacant
-
-
59
output
Throttleposition
sensor
Throttleposition
sensorsupply
voltage
(5
VDC)
60
input
Data
link
connector
Programming
voltage
61
vacant
-
-
62
vacant
-
-
63
vacant
-
-
64
input
Ignition
timing
intervention
from
A/T
control
module
(only
active
during
gearshift)
65
input
Automatic
transmission
(A/T)
range
switch
Transmission
park
or
neutral
signal
66
vacant
-
-
67
input
Engine
speed/crankshaft
position
sensor
Crankshaft
position/rpm
(voltage
(VAC)
between
pins
67
and
68)
68
input
Engine
speed/crankshaft
position
sensor
Crankshaft
position/rpm
(voltage
(VAC)
between
pins
67
and
68)
69
vacant
-
-
70
input
Oxygen
sensor
Oxygen
sensor
signal
(0-1
VDC
fluctuating
with
engine
running)
71
ground
Oxygen
sensor
Oxygen
sensor
signal
ground
72
vacant
-
-
73
input
Road
speed
Road
speed
signal
from
instrument
cluster
74
output
Engine
speed
(TD)
Engine
speed
(TD)
signalto
instrument
cluster
75
vacant
-
-
76
vacant
-
-
77
input
Intakeair
temperature
(IAT)
sensor
Intake
air
temperature
(0-5
V,
temperaturedependent)
78
input
Engine
coolant
temperature
(ECT)
sensor
Engine
coolant
temperature
(0-5V,
temperature
dependent)
79
vacant
-
-
80
vacant
-
-
81
input
On-boardcomputer
Drive-away
protection
enable
82
vacant
-
-
83
vacant
-
-
84
vacant
-
-
85
input
A/C
pressure
switch
From
Integrated
climate
control
module
via
A/C
pressure
switch
86
input
A/C
compressor
on
From
Integrated
climate
control
module
87
input
Diagnostic
connector
(RxD)
Diagnostic
RxD
(receive)signal
to
pin
15
in
Data
link
connector
88
input/output
Diagnostic
connector
(TxD)
Diagnostic
TxD
(transmit)
signal
to
pin
20
in
Data
link
connector
ECM
PIN
ASSIGNMENTS
Page 179 of 759
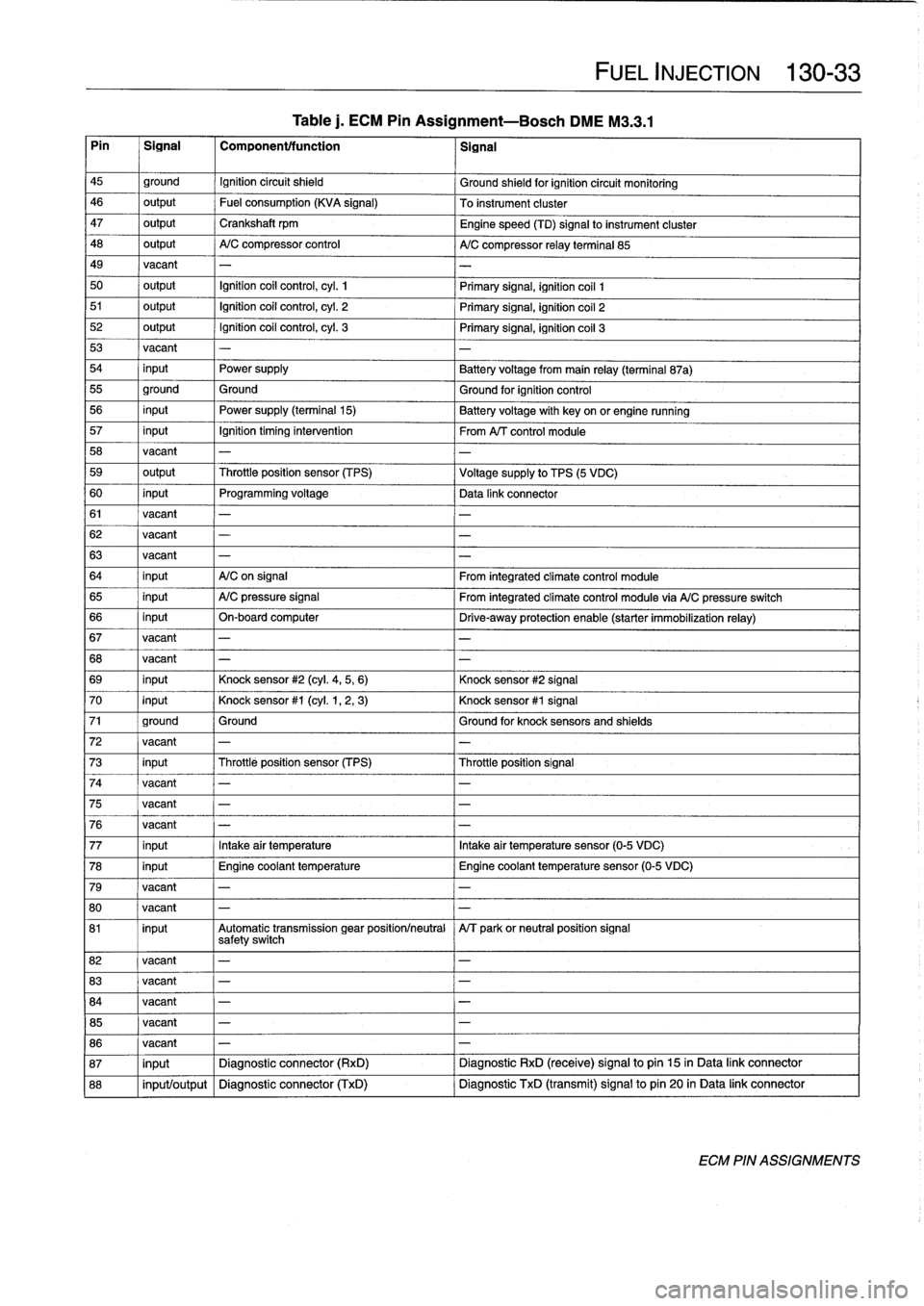
Table
j.
ECM
Pin
Assignment-Bosch
DME
M3
.3
.1
Pin
~
Signal
1
Componentffunction
1
signal
FUEL
INJECTION
130-
33
45
ground
Ignition
circuit
shield
Ground
shieldfor
ignition
circuit
monitoring
46
output
Fuel
consumption
(KVA
signal)
To
instrument
cluster
47
output
Crankshaft
rpm
Engine
speed
(TD)
signal
to
instrument
cluster
48
output
A/C
compressor
control
A/C
compressor
relay
terminal
85
49
vacant
-
-
50
output
Ignition
coil
control,
cyl
.
1
Primary
signal,
ignition
coil
1
51
output
Ignition
coil
control,
cyl
.
2
Primary
signal,
ignition
coil
2
52
output
Ignition
coil
control,
cyl
.
3
Primary
signal,
ignition
coil
3
53
vacant
-
-
54
input
Power
supply
Battery
voltagefrom
main
relay
(terminal
87a)
55
ground
Ground
Ground
for
ignition
control
56
input
Power
supply
(terminal15)
Batteryvoltage
with
key
on
or
engine
running
57
input
Ignition
timing
intervention
From
A/T
control
module
58
vacant
-
-
59
output
Throttleposition
sensor
(TPS)
Voltage
supply
to
TPS
(5
VDC)
60
input
Programming
voltage
Data
link
connector
61
vacant
-
-
62
vacant
-
-
63
vacant
-
-
64
input
A/C
on
signal
From
integrated
climate
control
module
65
input
A/C
pressure
signal
From
integrated
climate
control
module
via
A/C
pressure
switch
66
input
On-board
computer
Drive-away
protection
enable
(starter
immobilization
relay)
67
vacant
-
-
68
vacant
-
-
69
input
Knock
sensor
#2
(cyl
.
4,5,
6)
Knock
sensor
#2
signal
70
input
Knock
sensor
#1
(cyl
.
1,2,
3)
Knock
sensor
#1
signal
71
ground
Ground
Ground
for
knock
sensors
and
shields
72
vacant
-
-
73
input
Throttleposition
sensor
(TPS)
Throttleposition
signal
74
vacant
-
75
vacant
-
-
76
vacant
-
77
input
Intakeair
temperatura
Intakeair
temperatura
sensor
(0-5
VDC)
78
input
Engine
coolant
temperature
Engine
coolant
temperature
sensor
(0-5
VDC)
79
vacant
-
80
vacant
-
-
81
input
Automatic
transmission
gear
positionlneutral
A/T
parkor
neutral
position
signal
safetyswitch
82
vacant
-
-
83
vacant
-
-
84
vacant
-
-
85
vacant
-
-
86
vacant
-
-
87
input
Diagnostic
connector
(RxD)
Diagnostic
RxD
(receive)
signal
to
pin
15
in
Data
link
connector
88
input/output
Diagnostic
connector
(TxD)
Diagnostic
TxD
(transmit)
signal
to
pin
20
in
Data
link
connector
ECM
PIN
ASSIGNMENTS
Page 181 of 759
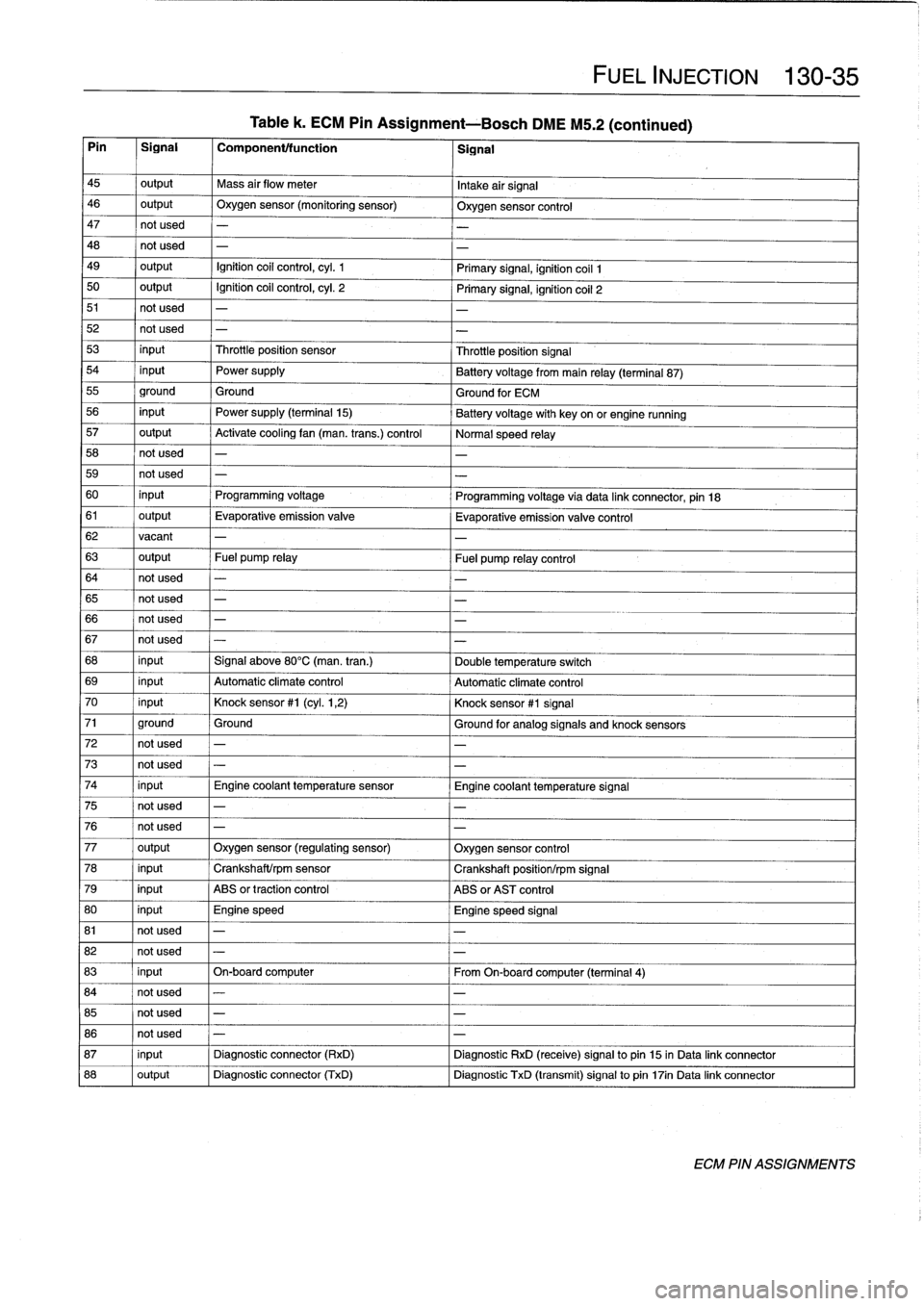
Table
k
.
ECM
Pin
Assignment-Bosch
DME
M5
.2
(continued)
Pin
I
Signal
1
Componentltunction
1
Signal
45
I
output
I
Mass
air
flow
meter
I
Intake
airSignal
46
output
Oxygen
sensor
(monitoring
sensor)
Oxygen
sensor
control
47
not
used
-
48
not
used
-
49
output
Ignition
coil
control,
cyl
.
1
Primary
signal,
ignition
coil
1
50
output
Ignition
coil
control,
cyl
.
2
Primary
signal,
ignition
coil
2
51
not
used
-
52
not
used
-
53
input
Throttleposition
sensor
Throttleposition
Signal
54
input
Power
supply
Batteryvoltage
from
main
relay
(terminal
87)
55
ground
Ground
Ground
for
ECM
56
input
Power
supply
(terminal
15)
Battery
voltage
with
key
on
or
engine
running
57
output
Activate
cooling
fan
(man
.
trans
.)
control
Normal
speed
relay
58
not
used
-
-
59
not
used
-
-
60
input
Programming
voltage
Programming
voltage
via
data
link
connector,
pin
18
61
output
Evaporative
emissionvalve
Evaporative
emission
valve
control
62
vacant
-
-
63
output
Fuel
pump
relay
Fuel
pump
relay
control
64
not
used
-
65
not
used
-
-
66
not
used
-
-
67
not
used
-
-
68
input
Signal
above
80°C(man
.
tran
.)
Double
temperature
switch
69
input
Automatic
climate
control
Automatíc
climate
control
70
input
Knock
sensor
#1
(cyl
.
1,2)
Knock
sensor
#1
Signal
71
ground
Ground
Ground
for
analog
signals
and
knock
sensors
72
not
used
-
-
73
not
used
-
-
74
input
Engine
coolant
temperature
sensor
Engine
coolant
temperatura
Signal
75
not
used
-
-
76
not
used
-
-
77
output
Oxygen
sensor
(regulating
sensor)
Oxygen
sensor
control
78
input
Crankshaft/rpm
sensor
Crankshaft
position/rpmSignal
79
input
ABS
or
traction
control
ABS
or
AST
control
80
input
Engine
speed
Engine
speed
Signal
81
not
used
-
-
82
not
used
-
-
FUEL
INJECTION
130-
3
5
83
input
On-board
computar
From
On-boardcomputer
(terminal
4)
84
not
used
-
-
85
not
used
-
-
86
not
used
-
-
87
input
Diagnostic
connector
(RxD)
Diagnostic
RxD
(receive)signal
to
pin
15
in
Data
link
connector
88
output
I
Diagnostic
connector
(TxD)
Diagnostic
TxD
(transmit)
signal
to
pin
17in
Data
link
connector
ECM
PIN
ASSIGNMENTS
Page 183 of 759
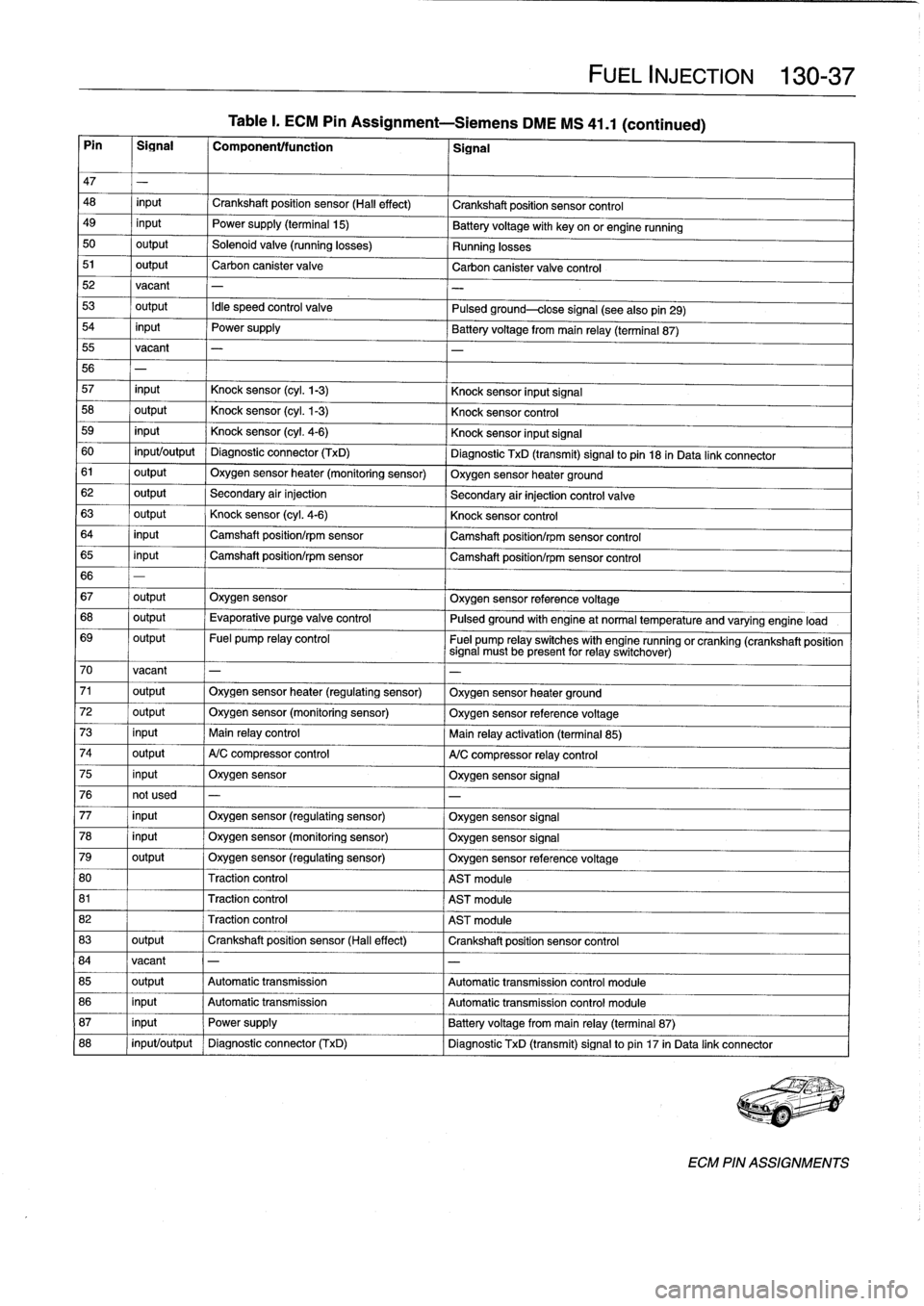
Table
I
.
ECM
Pin
Assignment-Siemens
DME
MS
41
.1
(continued)
Pin
I
Signal
I
Component/function
1
Signal
FUEL
INJECTION
130-
37
47
-
48
input
Crankshaft
position
sensor
(Hall
effect)
Crankshaft
position
sensor
control
49
input
Power
supply
(terminal
15)
Batteryvoltage
with
key
onor
engine
running
50
output
Solenoid
valve
(running
losses)
Running
losses
51
output
Carbon
canister
valve
Carbon
canister
valve
control
52vacant
-
53
output
Idle
speed
control
valve
Pulsed
ground-close
signal
(seealsopin29)
54
input
Power
supply
Battery
voltagefrom
main
relay
(terminal
87)
55
vacant
-
56
-
57
input
Knock
sensor
(cyl
.
1-3)
Knock
sensor
input
Signal
58
output
Knock
sensor
(cyl
.
1-3)
Knock
sensor
control
59
input
Knock
sensor
(cyl
.
4-6)
Knock
sensor
input
Signal
60
input/output
Diagnostic
connector
(TxD)
Diagnostic
TxD
(transmit)
signal
to
pin
18
in
Data
link
connector
61
output
Oxygen
sensor
heater
(monitoring
sensor)
Oxygen
sensor
heater
ground
62
output
Secondary
air
injection
Secondary
air
injection
control
valve
63
output
Knock
sensor
(cyl
.
4-6)
Knock
sensor
control
64
input
Camshaft
position/rpm
sensor
Camshaft
position/rpm
sensor
control
65
input
Camshaft
position/rpm
sensor
Camshaft
position/rpm
sensor
control
66
-
67
output
Oxygen
sensor
Oxygen
sensor
reference
voltage
68
output
Evaporative
purge
valve
control
Pulsed
ground
with
engine
at
normal
temperature
and
varyingengine
load
69
output
Fuel
pump
relay
control
Fuel
pump
relay
switches
with
engine
runningorcranking
(crankshaft
position
signal
must
be
present
for
relay
switchover)
70
vacant
-
-
71
output
Oxygen
sensor
heater
(regulating
sensor)
Oxygen
sensor
heater
ground
72
output
Oxygen
sensor
(monitoring
sensor)
Oxygen
sensor
referencevoltage
73
input
Main
relay
control
Main
relay
activation
(terminal
85)
74
output
A/C
compressor
control
A/C
compressor
relay
control
75
input
Oxygen
sensor
Oxygen
sensor
signal
76
not
used
-
-
77
input
Oxygen
sensor
(regulating
sensor)
Oxygen
sensor
signal
78
input
Oxygen
sensor
(monitoring
sensor)
Oxygen
sensor
signal
79
output
Oxygen
sensor
(regulating
sensor)
Oxygen
sensor
referencevoltage
80
Traction
control
AST
module
81
Traction
control
AST
module
82
Traction
control
AST
module
83
output
Crankshaft
position
sensor
(Hall
effect)
Crankshaft
position
sensor
control
84
vacant
-
-
85
output
Automatic
transmission
Automatic
transmission
control
module
86
input
Automatic
transmission
Automatic
transmissíon
control
module
87
input
Power
supply
Battery
voltage
from
main
relay
(terminal
87)
88
input/output
Diagnostic
connector
(TxD)
Diagnostic
TxD
(transmit)
signal
to
pin
17
in
Data
link
connector
ECM
PIN
ASSIGNMENTS
Page 191 of 759
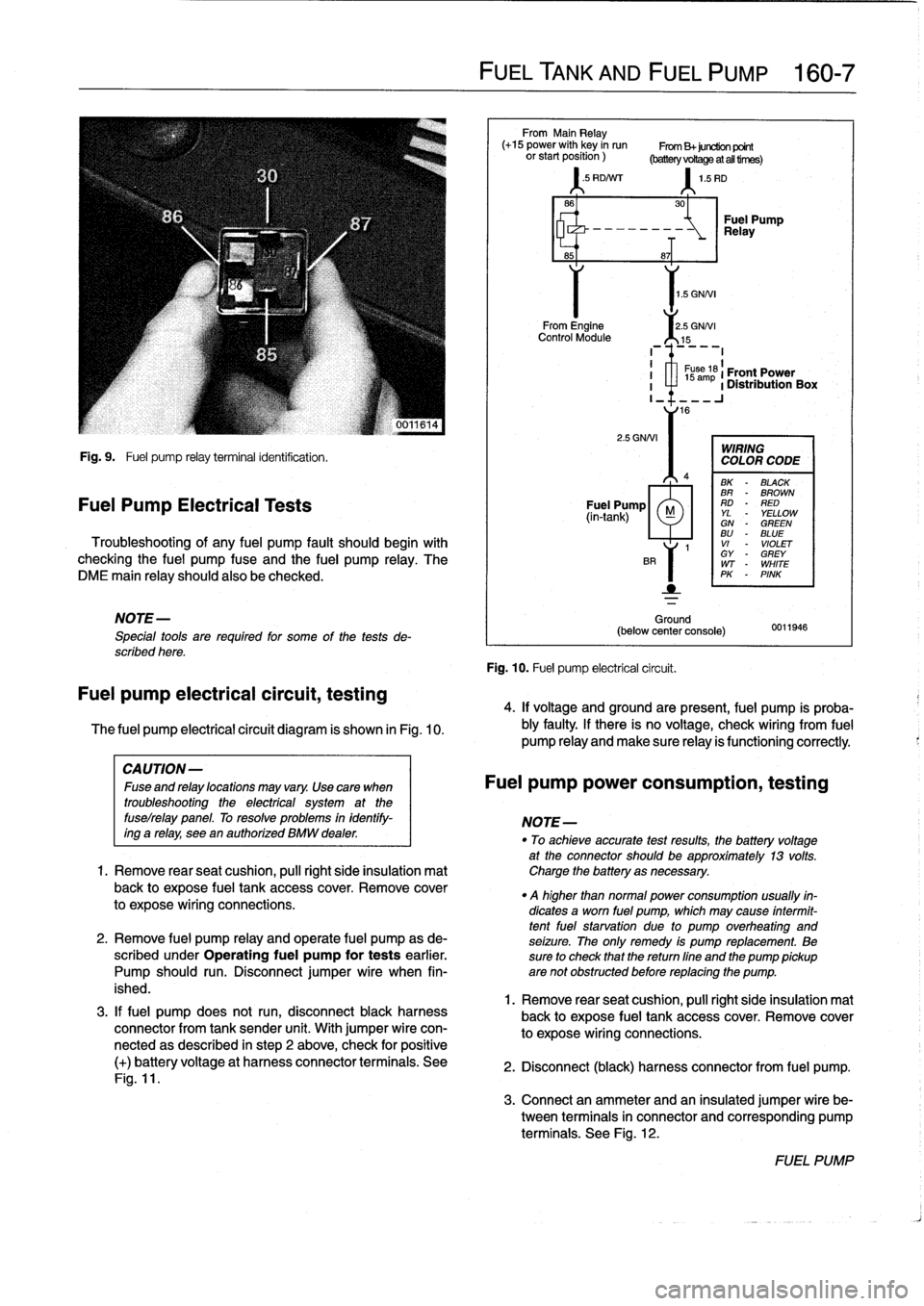
Fig
.
9
.
Fuel
pump
relay
terminal
identification
.
Fuel
Pump
Electrical
Tests
Troubleshooting
of
any
fuel
pump
fault
should
begin
with
checking
the
fuel
pump
fuse
and
the
fuel
pump
relay
.
The
DME
main
relay
should
also
be
checked
.
NOTE-
Special
tools
are
requíred
for
some
of
the
tests
de-
scribed
here
.
Fuel
pump
electrical
circuit,
testing
The
fuel
pump
electrical
circuit
diagram
is
shown
in
Fig
.
10
.
3
.
If
fuel
pump
does
not
run,
disconnect
black
harness
connector
from
tank
sender
unit
.
With
jumper
wire
con-
nectedas
described
in
step
2
above,
check
for
positive
(+)
batteryvoltage
at
harness
connector
terminals
.
See
Fig
.
11
.
FUEL
TANK
AND
FUEL
PUMP
160-
7
From
Main
Relay
(+15
power
with
key
in
run
From
B+juretion
point
orstartposition)
(batteryvoRageatalltirnes)
'
.5
RD/Nrr
1
.5
RD
1
.5
GNNI
From
Engine
2
.5
GNNI
Control
Module
15
2
.5
GNNI
Ground
(below
center
console)
Fig
.
10
.
Fuel
pump
electrical
circuit
.
30
-~
Relay
Fuel
Pump
8~T
I
1
s
ám
61
Front
Power
I
a
1
Distribution
Box
I_
16
WIRING
COLOR
CODE
BK
-
BLACK
BR
-
BROWN
Fuel
Pump
RD
-
RED
(in-tank)
M
YL
YELLOWGN
-
GREENBU
-
BLUE
1
VI
-
VIOLET
GY
-
GREY
WT
-
WHITE
PK
-
PINK
0011946
4
.
If
voltage
and
groundare
present,
fuel
pump
is
proba-
bly
faulty
.
If
there
is
no
voltage,
check
wiring
From
fuel
pump
Reay
and
make
sure
Reay
is
functioning
correctly
.
CAUTION-
Fuseandrelaylocationsmayvary
.
Usecara
when
Fuel
pump
power
consumption,
testing
troubleshooting
the
electrical
system
at
the
fuselrelay
panel
.
To
resolve
problems
in
identify-
NOTE-
ing
a
relay,
see
en
authorízed
BMW
dealer
.
"
To
achieveaccurate
testresults,
fhe
battery
voltage
at
the
connector
should
be
approximately
13
volts
.
1.
Remove
rearseat
cushion,
pull
right
side
insulation
mat
Charge
the
battery
asnecessary
.
back
to
expose
fuel
tank
accesscover
.
Remove
cover
.
q
higher
than
normal
power
consumption
usually
fin-
to
expose
wiring
connections
.
dicates
a
worn
fuel
pump,
which
may
cause
intermit-
tentfuel
starvation
due
lo
pump
overheating
and
2
.
Remove
fuel
pump
relay
and
opérate
fuel
pump
as
de-
seizure
.
The
only
remedy
is
pump
replacement
.
Be
scribed
under
Operating
fuel
pump
for
tests
earlier
.
sure
to
check
that
thereturn
fine
and
the
pump
pickup
Pump
should
run
.
Disconnect
jumper
wire
when
fin-
are
not
obstructed
before
replacing
the
pump
.
ished
.
1
.
Remove
rear
seat
cushion,
pull
right
side
insulation
mal
back
to
expose
fuel
tank
accesscover
.
Remove
cover
to
expose
wiring
connections
.
2
.
Disconnect
(black)
harness
connector
from
fuel
pump
.
3
.
Connect
an
ammeter
and
an
insulated
jumper
wire
be-
tween
terminals
in
connector
and
corresponding
pump
terminals
.
See
Fig
.
12
.
FUEL
PUMP