tail light BMW 325i 1993 E36 Workshop Manual
[x] Cancel search | Manufacturer: BMW, Model Year: 1993, Model line: 325i, Model: BMW 325i 1993 E36Pages: 759
Page 22 of 759
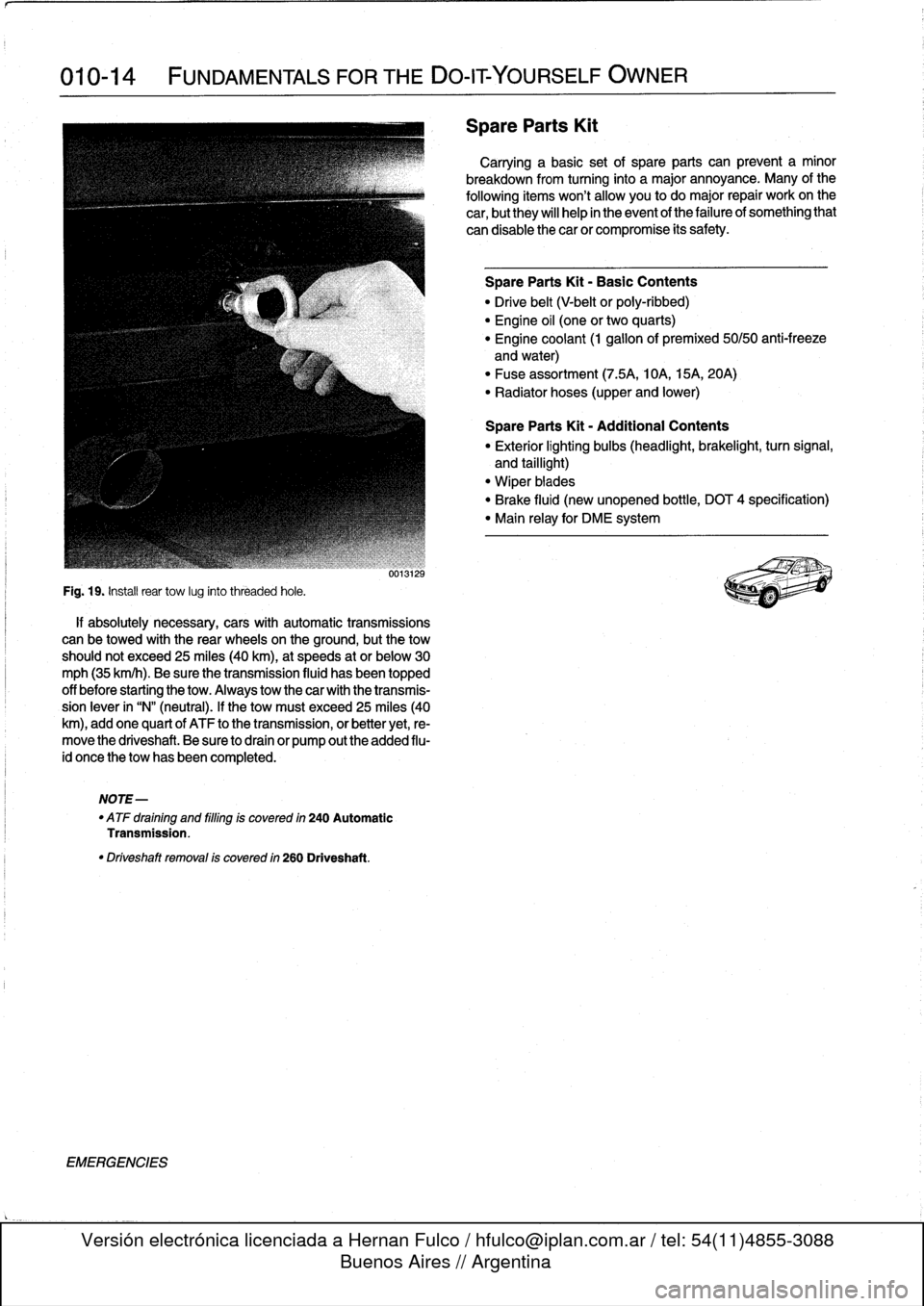
010-14
FUNDAMENTALS
FOR
THE
DO-ITYOURSELF
OWNER
Fig
.
19
.
Instaf
rear
tow
lug
into
threaded
hole
.
if
absolutely
necessary,
cars
with
automatic
transmissions
can
be
towed
with
the
rear
wheels
on
the
ground,
butthe
tow
should
not
exceed
25
miles
(40
km),at
speeds
at
or
below30
mph
(35
km/h)
.
Be
sure
the
transmission
fluid
hasbeen
topped
off
before
starting
the
tow
.
Always
tow
thecar
with
the
transmis-
sion
lever
in
"N"
(neutral)
.
If
the
tow
must
exceed25
miles
(40
km),
add
one
quart
of
ATF
to
the
transmission,
or
better
yet,
re-
move
the
driveshaft
.
Be
sure
to
drain
or
pump
outthe
added
flu-
id
once
the
tow
has
been
completed
.
NOTE-
"
ATF
draining
and
filling
is
covered
in
240
Automatic
Transmission
.
"
Driveshaft
removal
is
covered
in
260
Driveshaft
.
EMERGENCIES
úo1W¿b
Spare
Parts
Kit
Carrying
a
basic
set
of
spare
parts
can
prevent
a
minor
breakdown
from
turning
into
a
major
annoyance
.
Many
of
the
following
itemswon't
allow
you
todo
major
repair
workon
the
car,
but
they
will
help
in
the
event
of
the
failure
of
something
that
can
disable
thecar
or
compromise
its
safety
.
Spare
Parts
Kit
-
Basic
Contents
"
Drive
belt
(V-belt
or
poly-ribbed)
"
Engine
oil
(one
or
two
quarts)
"
Engine
coolant
(1
gallonof
premixed
50/50
anti-freeze
and
water)
"
Fuse
assortment
(7
.5A,
10A,
15A,
20A)
"
Radiator
hoses
(upper
and
lower)
Spare
Parts
Kit
-
Additional
Contents
"
Exterior
lighting
bulbs
(headlight,
brakelight,
turn
signal,
and
taillight)
"
Wiper
biades
"
Brake
fluid
(new
unopened
bottle,
DOT
4
specification)
"
Main
relay
for
DME
system
Page 34 of 759
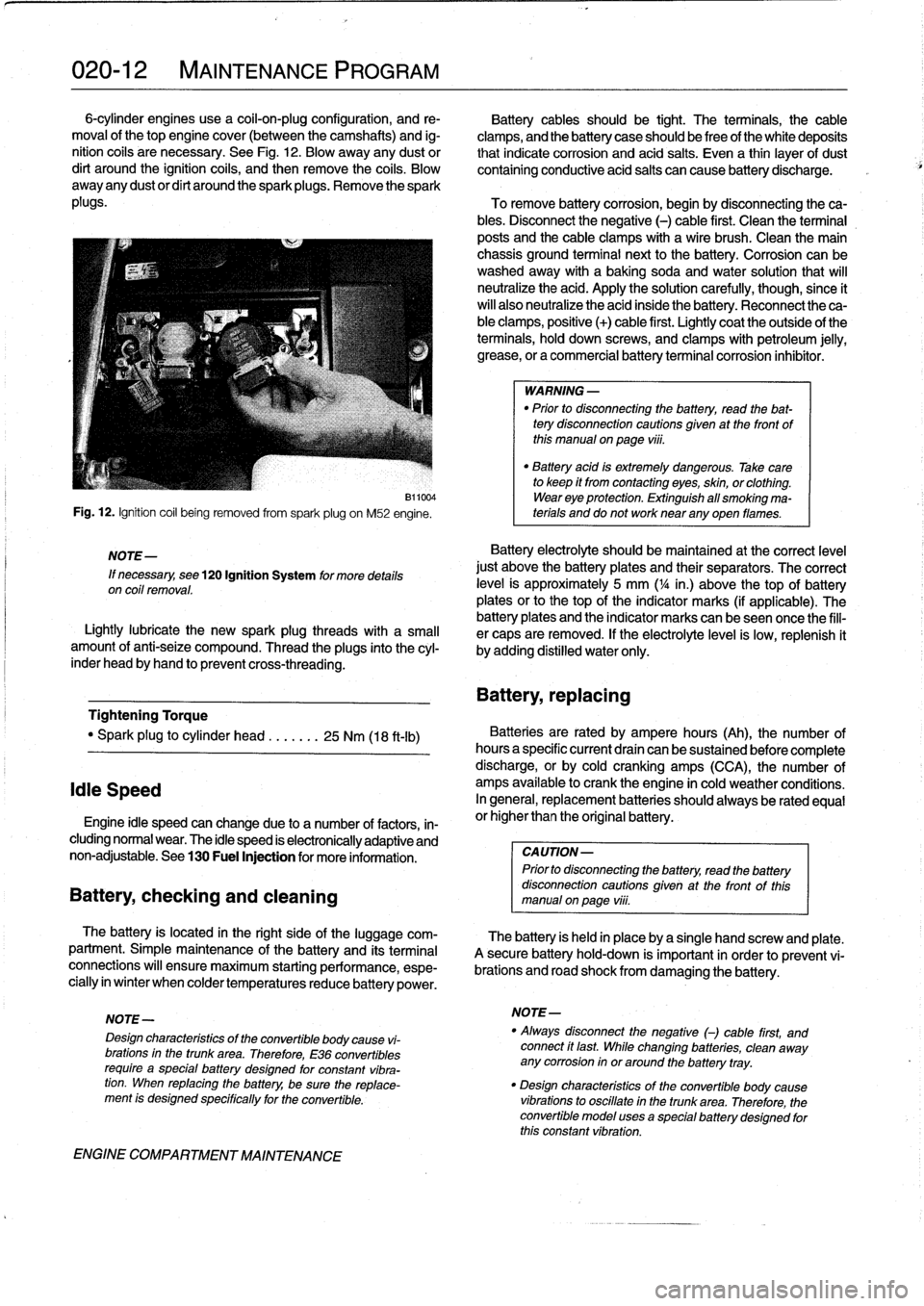
020-
1
2
MAINTENANCE
PROGRAM
6-cylinder
engines
use
a
coil-on-plug
configuration,
and
re-
Battery
cablesshould
be
tight
.
The
terminals,
the
cable
moval
of
thetop
engine
cover
(between
the
camshafts)
and
ig-
clamps,
and
the
battery
case
should
be
freeof
the
white
deposits
nition
cofs
are
necessary
.
See
Fig
.
12
.
Blow
away
any
dust
or
that
indicate
corrosion
and
acid
salts
.
Even
a
thin
¡ayer
of
dust
dirt
around
the
ignition
coils,
and
then
remove
the
coils
.
Blow
containing
conductive
acid
salts
can
cause
battery
discharge
.
away
any
dustor
dirt
around
the
sparkplugs
.
Remove
the
spark
plugs
.
To
remove
battery
corrosion,
begin
by
disconnecting
theca-
bles
.
Disconnect
the
negative
(-)
cable
first
.
Clean
the
terminal
posts
and
the
cable
clamps
with
a
wire
brush
.
Clean
the
main
chassis
ground
terminal
next
to
the
battery
.
Corrosion
can
be
washedaway
with
a
baking
soda
and
water
solution
that
will
neutralize
the
acid
.
Apply
the
solution
carefully,
though,since
ít
will
also
neutralize
the
acid
inside
the
battery
.
Reconnect
the
ca-
ble
clamps,
positive
(+)
cable
first
.
Lightly
coat
the
outside
of
the
terminals,
hold
down
screws,
and
clamps
with
petroleum
jelly,
grease,
or
a
commercial
battery
terminal
corrosion
inhibitor
.
Fig
.
12
.
Ignition
coil
being
removed
from
spark
plug
on
M52
engine
.
NOTE-
If
necessary,
see
120
Ignition
System
for
more
details
on
coil
removal
.
B11004
Lightlylubricate
the
new
spark
plug
threads
with
a
small
amount
of
anti-seize
compound
.
Thread
the
plugs
into
the
cyl-
inder
head
byhand
to
prevent
cross-threading
.
Tightening
Torque
"
Spark
plug
to
cylinder
head
.......
25
Nm
(18
ft-ib)
Idie
Speed
Engine
¡dle
speed
canchange
due
to
a
number
of
factors,
in-
cluding
normal
wear
.
The
idle
speed
is
electronically
adaptive
and
non-adjustable
.
See
130
Fuel
Injection
for
more
information
.
Battery,
checking
and
cleaning
The
battery
is
located
in
the
right
side
of
the
luggage
com-
partment
.
Simple
maintenance
of
the
battery
and
its
terminal
connections
will
ensure
maximum
starting
performance,
espe-
cially
in
winter
when
colder
temperaturesreduce
battery
power
.
ENGINE
COMPARTMENT
MAINTENANCE
WARNING
-
"
Prior
to
disconnecting
the
battery,
read
the
bat-
tery
disconnection
cautions
given
at
the
front
of
this
manualonpage
viii
.
"
Battery
acid
is
extremely
dangerous
.
Take
care
to
keep
it
from
contacting
eyes,
skin,
or
clothing
.
Wear
eye
protection
.
Extinguish
all
smoking
ma-
terials
and
do
not
worknear
any
oyen
flames
.
Battery
electrolyte
should
be
maintained
at
the
correct
level
just
above
the
battery
plates
and
their
separators
.
The
correct
leve¡
is
approximately
5
mm
(
1
/4
in
.)
above
thetop
of
battery
plates
orto
thetop
of
the
indicator
marks
(if
applicable)
.
The
battery
plates
and
the
indicator
marks
can
beseen
once
the
fill-
er
caps
are
removed
.
If
the
electrolyte
level
is
low,
replenish
it
by
adding
distilled
water
only
.
Battery,
repiacing
Batteries
are
rated
by
ampere
hours
(Ah),
the
number
of
hoursa
specific
current
draín
can
be
sustained
before
complete
discharge,
or
by
cold
cranking
amps
(CCA),
the
number
of
amps
available
to
crank
the
engine
in
cold
weather
conditions
.
In
general,
replacement
batteries
should
alwaysbe
rated
equal
or
higherthan
the
original
battery
.
CAUTION-
Prior
to
disconnecting
the
battery,
read
the
battery
disconnection
cautions
given
at
the
front
of
thls
manual
on
page
viii
.
The
battery
is
held
in
place
bya
single
hand
screw
and
píate
.
A
secure
battery
hold-down
is
important
in
order
to
prevent
vi-
brations
and
road
shock
from
damaging
the
battery
.
NOTE-
NOTE-
"
Always
disconnect
the
negative
()
cable
first,
and
Design
characteristics
of
the
convertible
body
cause
vi-
connect
ft
last
While
changing
batteries,
clean
away
brations
in
the
trunk
area
.
Therefore,
E36
convertibles
any
corrosion
in
or
around
the
battery
tray
.
require
a
specialbattery
designed
for
constant
vibra-
tion
.
When
repiacing
the
battery,
be
sure
the
replace-
"
Design
characteristics
of
the
convertible
body
cause
ment
is
designed
specffically
for
the
convertible
.
vibrations
to
oscillate
in
the
trunk
area
.
Therefore,
the
convertible
model
uses
a
specialbattery
designed
for
this
constant
vibration
.
Page 37 of 759
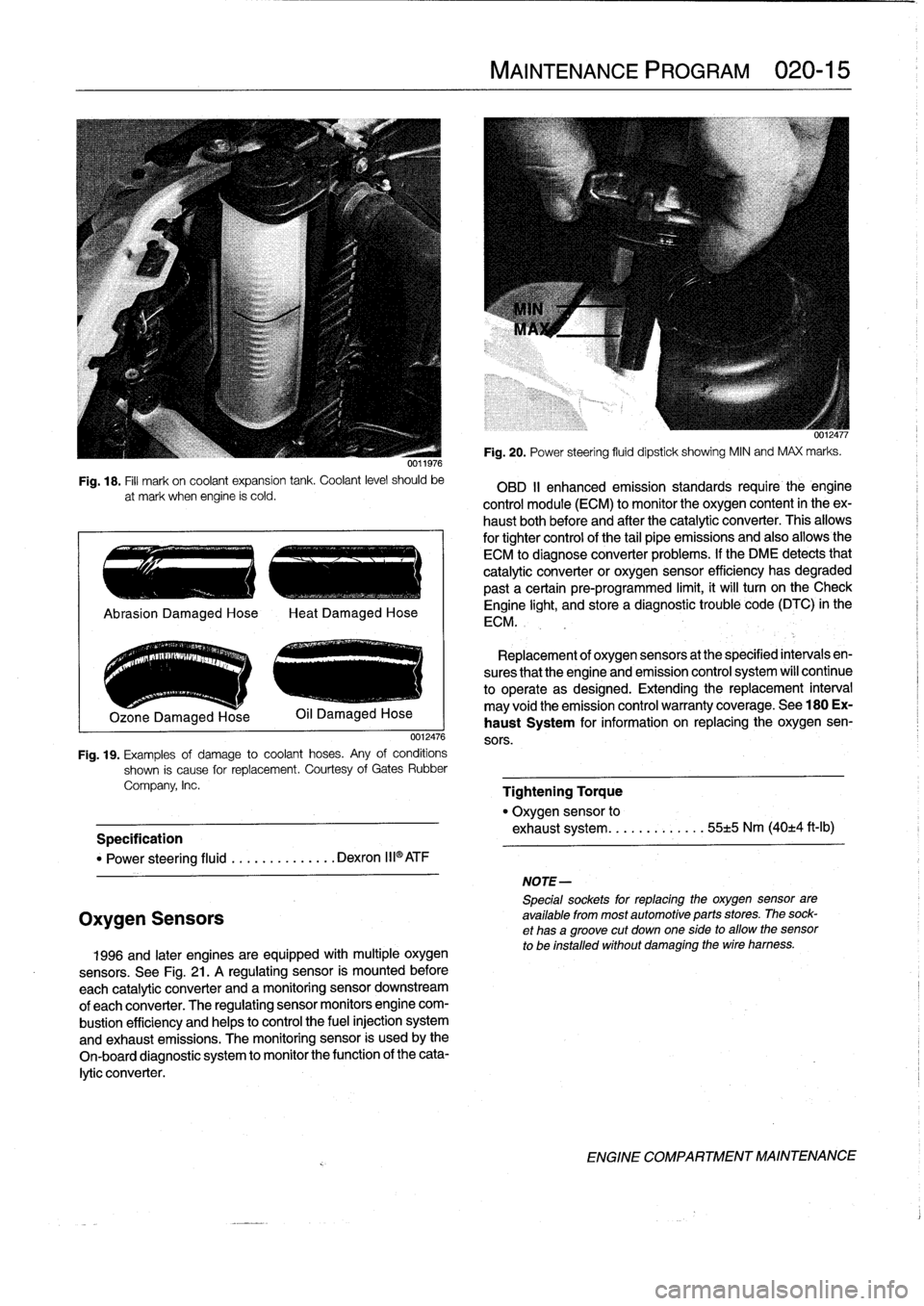
Fig
.
18
.
Fill
mark
on
coolant
expansion
tank
.
Coolant
level
should
be
at
mark
when
engine
ís
cold
.
.
..
e
..
.-
..
~
..
.-
.
Ozone
Damaged
Hose
0012476
Fig
.
19
.
Examples
of
damage
to
coolant
hoses
.
Any
of
conditions
shown
is
cause
for
replacement
.
Courtesy
of
Gates
Rubber
Company,
Inc
.
Specification
"
Power
steering
fluid
..........
.
...
Dexron
III®ATF
Oxygen
Sensors
1996
and
later
engines
are
equipped
withmultiple
oxygen
sensors
.
See
Fig
.
21
.
A
regulating
sensor
is
mounted
before
each
catalytic
converter
and
amonitoring
sensor
downstream
of
each
converter
.
The
regulating
sensor
monitors
engine
com-
bustion
efficiency
and
helps
to
control
the
fuel
injection
system
and
exhaust
emissions
.
The
monitoring
sensor
is
usedby
the
On-board
diagnostic
system
to
monitor
the
function
of
the
cata-
lytic
converter
.
MAINTENANCE
PROGRAM
020-
1
5
NOTE-
5pecialsockets
for
replacingthe
oxygen
sensor
are
available
from
most
automotive
parts
stores
.
The
sock-
et
has
agroove
cut
down
one
side
to
allow
the
sensor
to
be
installed
without
damaging
the
wire
hamess
.
Fig
.
20
.
Power
steering
fluid
dipstick
showing
MIN
and
MAX
marks
.
OBD
II
enhanced
emission
standards
require
the
engine
control
module
(ECM)
to
monitor
the
oxygen
content
in
theex-
haust
bothbefore
and
after
the
catalytic
converter
.
This
allows
for
tightercontrol
of
the
tail
pipe
emissions
and
also
allowsthe
ECM
to
diagnose
converter
problems
.
lf
the
DME
detects
that
catalytic
converter
or
oxygen
sensor
efficiency
has
degraded
past
a
certain
pre-programmed
limit,
it
will
turn
on
the
Check
Engine
light,
and
store
a
diagnostic
trouble
code
(DTC)
in
the
ECM
.
Replacement
of
oxygen
sensors
at
the
specified
intervals
en-
sures
that
the
engine
and
emission
control
system
wíll
continue
to
operate
as
designed
.
Extending
the
replacement
interval
may
void
the
emission
control
warranty
coverage
.
See
180
Ex-
haust
System
for
information
on
replacing
the
oxygen
sen-
sors
.
Tightening
Torque
"
Oxygen
sensor
to
exhaust
system
........
.
.
.
..
55±5
Nm
(40±4
ft-Ib)
ENGINE
COMPARTMENT
MAINTENANCE
Page 39 of 759
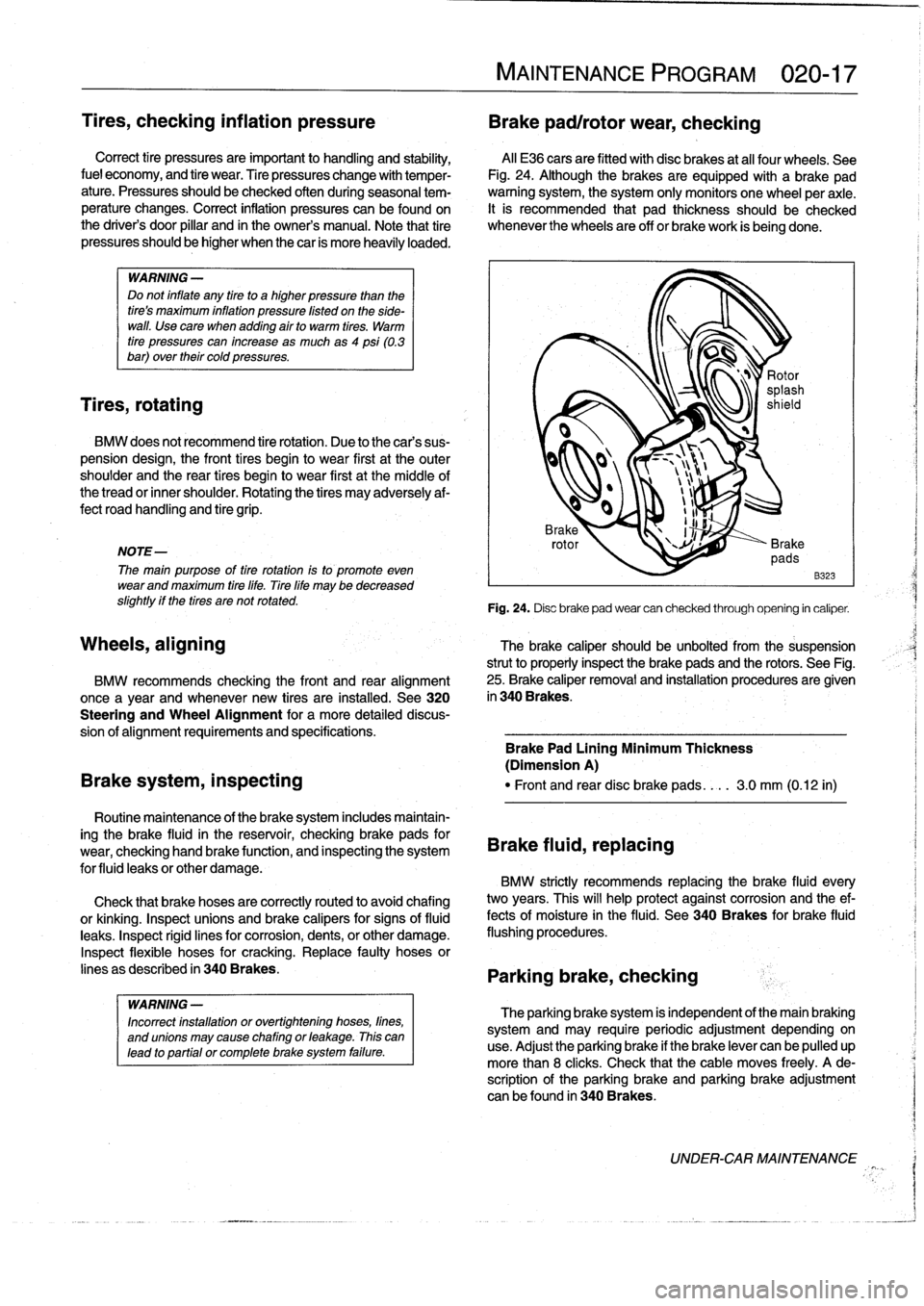
Tires,
checking
inflation
pressure
Brake
pad/rotor
wear,
checking
Correct
tire
pressuresare
important
to
handling
and
stability,
Al¡
E36
cars
are
fitted
withdisc
brakes
at
al¡
four
wheels
.
See
fuel
economy,
and
tire
wear
.
Tire
pressures
change
with
temper-
Fig
.
24
.
Although
thebrakesare
equipped
with
a
brake
pad
ature
.
Pressures
should
be
checked
often
during
seasonal
tem-
warning
system,
the
system
only
monitors
one
wheel
per
axle
.
perature
changes
.
Correct
inflation
pressures
canbe
found
on
It
is
recommended
that
pad
thickness
should
be
checked
the
driver's
door
pillar
and
in
the
owner's
manual
.
Note
that
tire
whenever
the
wheels
are
off
or
brakework
is
beggg
done
.
pressuresshould
be
higher
when
thecar
is
more
heavily
loaded
.
WARNING
-
Do
not
inflate
any
tire
to
a
higher
pressure
than
the
tiress
maximum
ínflation
pressure
listed
on
the
side-
wall
.
Use
cara
when
addlng
air
to
warm
tires
.
Warm
tire
pressures
can
increase
as
much
as4
psi
(0.3
bar)
over
their
cold
pressures
.
Tires,
rotating
BMW
does
not
recommend
tire
rotation
.
Due
to
the
cars
sus-
pension
design,
the
fronttires
begin
to
wear
first
at
the
outer
shoulder
and
the
rear
tires
begin
to
wear
first
at
themiddle
of
the
tread
or
inner
shoulder
.
Rotating
the
tires
may
adversely
af-
fect
roadhandling
and
tire
grip
.
NOTE-
The
main
purpose
of
tire
rotation
isto
promote
even
wear
and
maximum
tire
life
.
Tire
life
may
be
decreased
slightly
if
the
tires
are
not
rotated
.
Wheels,
aligning
Routine
maintenance
of
the
brake
system
includes
maintain-
ing
the
brake
fluid
in
the
reservoir,
checking
brakepads
for
wear,
checking
hand
brake
functíon,
and
inspecting
the
system
for
fluid
leaks
or
other
damage
.
Check
that
brake
hoses
are
correctly
routed
to
avoidchafing
or
kinkíng
.
Inspect
unions
and
brake
calipers
for
signs
of
fluid
leaks
.
Inspect
rigid
fines
for
corrosion,
dents,
or
other
damage
.
Inspect
flexible
hoses
for
cracking
.
Replace
faulty
hoses
or
lines
as
described
in
340Brakes
.
WARNING
-
Incorrect
installation
or
overtightening
hoses,
fines,
and
unions
may
cause
chafing
or
leakage
.
This
can
lead
to
partíal
or
completebrake
system
failure
.
MAINTENANCE
PROGRAM
020-
1
7
B323
Fig
.
24
.
Disc
brake
pad
wear
can
checked
through
opening
in
caliper
.
The
brake
caliper
should
be
unbolted
from
the
suspension
strut
to
properly
inspect
the
brake
pads
and
the
rotors
.
See
Fig
.
25
.
Brake
caliper
removal
and
installation
procedures
are
given
in
340
Brakes
.
BMW
recommends
checking
the
front
and
rear
alignment
once
a
year
and
whenever
new
tires
are
installed
.
See320
Steering
and
Wheel
Alignment
for
a
more
detailed
discus-
sion
of
alignment
requirements
and
specifications
.
Brake
Pad
Lining
Minimum
Thickness
(Dimension
A)
Brake
system,
inspecting
"
Front
and
reardisc
brake
pads
....
3
.0
mm
(0
.12
in)
Brake
fluid,
replacing
BMW
strictly
recommends
replacing
the
brake
fluid
every
two
years
.
This
will
help
protect
against
corrosion
and
the
ef-
fects
of
moisture
in
the
(luid
.
See340
Brakes
for
brake
fluid
flushing
procedures
.
Parking
brake,
checking
The
parking
brakesystem
is
independent
of
the
main
braking
system
and
may
requireperiodic
adjustment
dependingon
use
.
Adjust
the
parking
brake
if
the
brake
lever
can
be
pulled
up
more
than
8
clicks
.
Check
that
the
cable
moves
freely
.
A
de-
scription
of
the
parking
brake
and
parking
brake
adjustment
can
be
found
in
340Brakes
.
UNDER-CARMAINTENANCE
Page 54 of 759
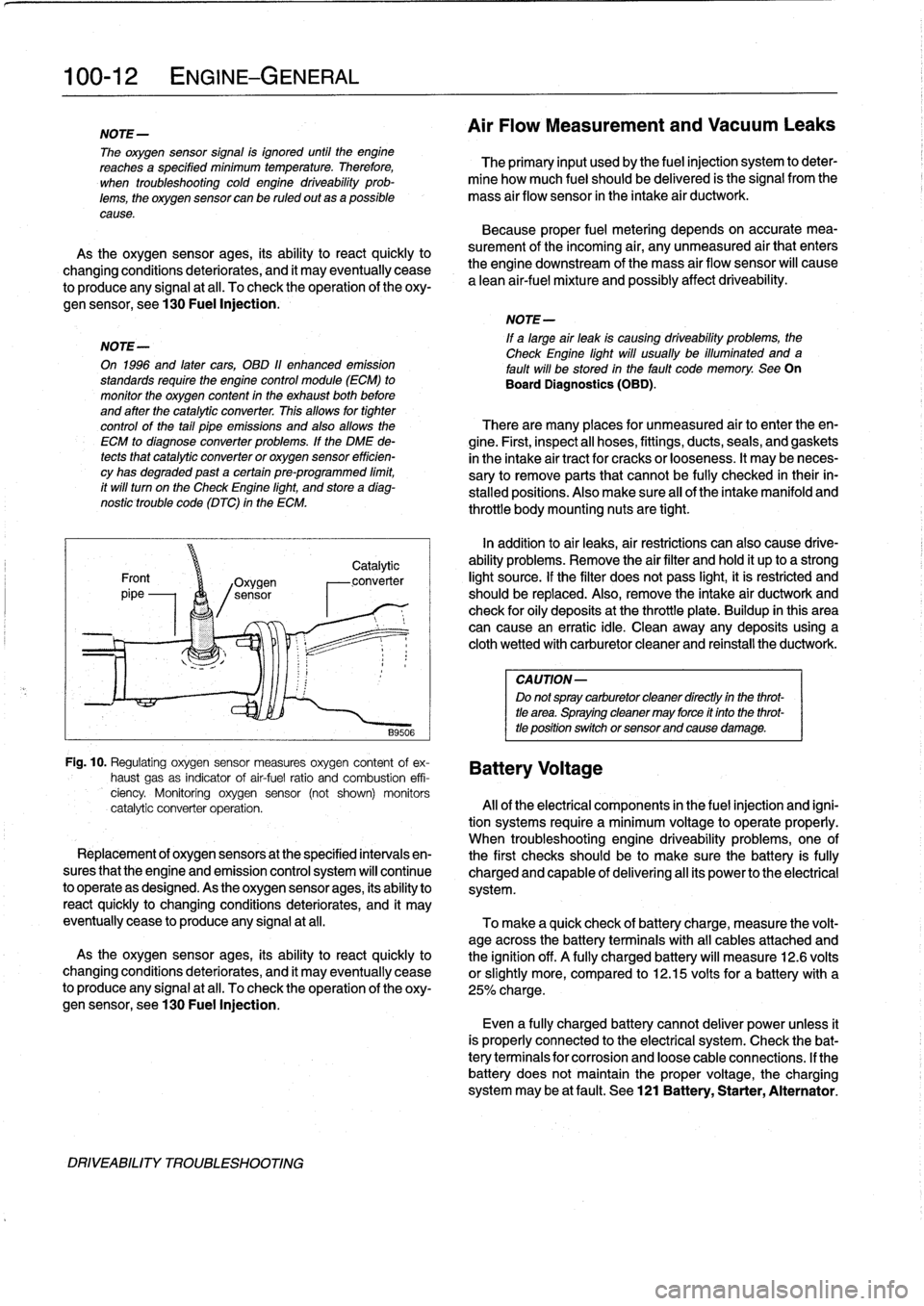
100-
1
2
ENGINE-GENERAL
NOTE-
The
oxygen
sensor
signal
is
ignored
until
the
engine
reachesa
specified
minimum
temperature
.
Therefore,
The
primary
input
usedby
the
fuel
injection
system
to
deter-
when
troubleshooting
cold
engine
driveability
prob-
mine
how
much
fuel
should
be
delivered
is
the
signal
from
the
lems,
the
oxygensensor
canbe
ruled
out
asa
possible
mass
air
flow
sensor
in
the
intake
air
ductwork
.
cause
.
As
the
oxygen
sensor
ages,
its
ability
to
react
quickly
to
changing
conditions
deteriorates,
and
it
may
eventually
cease
to
produce
any
signal
at
all
.
To
check
the
operation
of
the
oxy-
gen
sensor,
see
130
Fuel
Injection
:
NOTE-
On
1996
and
latercars,
OBD
11
enhanced
emission
standards
require
the
engine
control
module
(ECM)
to
monitor
the
oxygen
content
in
the
exhaust
both
before
and
after
the
catalytic
converter
.
Thisallows
for
tighter
control
of
the
tail
pipe
emissions
and
also
allowsthe
ECM
to
diagnose
converter
problems
.
If
the
DME
de-
tects
that
catalytic
converter
or
oxygensensor
efficien-
cyhas
degraded
pasta
certain
pre-programmed
limit,
it
will
turn
on
the
Check
Engine
light,
and
store
a
diag-
nostic
trouble
code
(DTC)
in
the
ECM
.
DRIVEABILITY
TROUBLESHOOTING
Catalytic
B9506
Air
Flow
Measurement
and
Vacuum
Leaks
Because
proper
fuel
metering
depends
on
accurate
mea-
surement
of
the
incoming
air,
any
unmeasured
air
that
enters
the
engine
downstream
of
the
mass
air
flow
sensor
will
cause
a
lean
air-fuel
mixture
and
possibly
affectdriveability
.
NOTE-
Fig
.
10
.
Regulating
oxygen
sensor
measures
oxygen
content
of
ex-
gattery
Voltage
hausY
gas
as
indicator
of
.¡_fi
.1
ratio
and
"-k,
.
E-
effi-
ciency
.
Monitoríng
oxygen
sensor
(not
shown)
monitors
If
a
large
air
leak
is
causing
driveability
problems,
the
Check
Engine
light
will
usually
be
illuminated
and
a
fault
will
be
stored
in
the
fault
code
memory
.
See
On
Board
Diagnostics
(OBD)
.
There
are
many
places
for
unmeasured
air
to
enter
theen-
gine
.
First,
inspect
all
hoses,
fittings,
ducts,
seals,
and
gaskets
in
the
intake
air
tract
for
cracks
or
looseness
.
It
may
be
neces-
sary
to
remove
parts
that
cannot
be
fully
checked
in
their
in-
stalled
positions
.
Also
make
sure
all
of
the
intake
manifold
and
throttle
body
mounting
nuts
are
tight
.
In
addition
to
air
leaks,
air
restrictions
can
also
cause
drive-
ability
problems
.
Remove
the
air
filter
and
hold
it
up
to
a
strong
light
source
.
If
the
filter
does
not
pass
light,
it
is
restricted
and
should
be
replaced
.
Also,
remove
the
intake
air
ductwork
and
check
for
oily
deposits
at
the
throttle
plate
.
Buildup
in
this
area
can
cause
an
erratic
idle
.
Clean
away
any
deposits
using
a
cloth
wetted
withcarburetor
cleaner
and
reinstall
the
ductwork
.
CAUTION-
Do
not
spray
carburetor
cleaner
directly
in
the
throt-
tle
anea
.
Spraying
cleaner
may
force
it
into
the
throt-
tle
position
switch
or
sensor
and
cause
damage
.
catalytic
converter
operation
.
All
of
the
electrical
components
in
the
fuelinjection
and
igni-
tion
systems
require
a
minimum
voltage
to
operate
properly
.
When
troubleshooting
engine
driveability
problems,
one
of
Replacement
of
oxygensensors
at
the
specified
intenrals
en-
the
first
checks
should
be
to
make
sure
the
battery
is
fully
sures
that
the
engine
and
emission
control
system
wili
continue
charged
and
capable
of
delivering
allits
power
to
the
electricalto
operate
as
designed
.
As
the
oxygen
sensor
ages,
its
ability
to
system
.
react
quickly
to
changing
conditions
deteriorates,
and
it
may
eventually
cease
to
produceany
signal
at
all
.
To
make
a
quick
check
of
battery
charge,
measure
the
volt-
age
across
the
battery
terminals
with
all
cables
attached
and
As
the
oxygen
sensor
ages,
its
ability
to
react
quickly
to
the
ignition
off
.
A
fully
charged
battery
will
measure
12
.6
volts
changing
conditions
deteriorates,
and
it
may
eventually
cease
or
slightly
more,
compared
to
12
.15
volts
for
a
battery
with
a
to
produce
any
signal
at
all
.
To
check
theoperation
of
the
oxy-
25%
charge
.
gen
sensor,
see130
Fuel
Injection
.
Even
a
fully
charged
battery
cannot
deliver
power
unless
it
is
properly
connected
to
the
electrical
system
.
Check
the
bat-
tery
terminals
for
corrosion
and
loosecableconnections
.
If
the
battery
does
not
maintain
the
proper
voltage,
the
charging
system
may
be
atfault
.
See
121
Battery,
Starter,
Alternator
.
Page 149 of 759
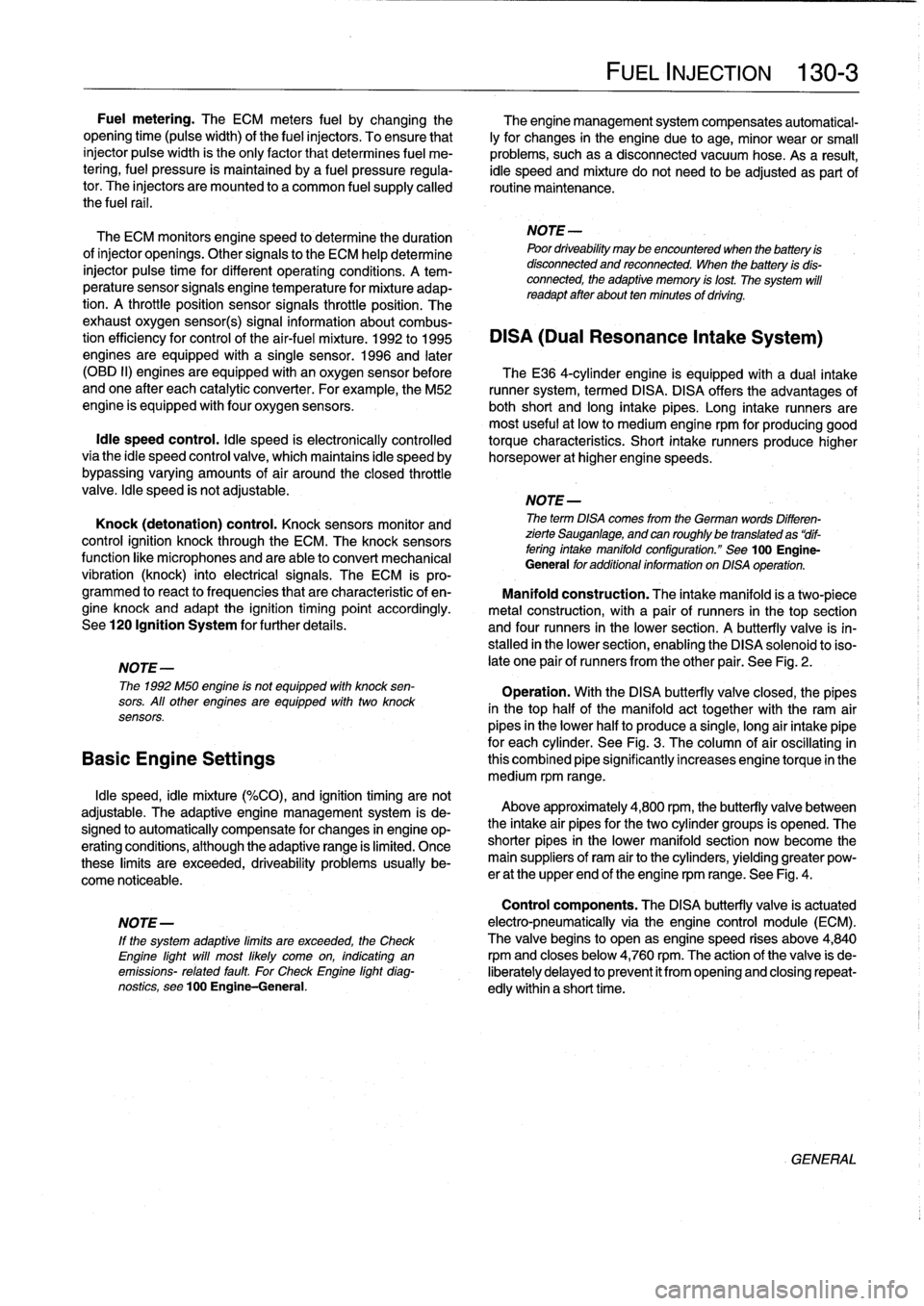
FUEL
INJECTION
130-
3
Fuel
metering
.
The
ECM
meters
fuel
bychanging
the
The
engine
management
system
compensates
automatical-
opening
time
(pulsewidth)
of
the
fuel
injectors
.
To
ensure
that
ly
for
changes
in
the
engine
due
to
age,
minor
wear
or
small
injector
pulsewídth
is
the
only
factor
that
determines
fuel
me-
problems,
such
as
a
disconnected
vacuum
hose
.
Asa
result,
tering,fuel
pressure
is
maintained
bya
fuel
pressure
regula-
idle
speed
and
mixture
do
not
need
lo
be
adjustedas
partof
tor
.
The
injectors
are
mounted
lo
a
common
fuel
supply
called
routine
maintenance
.
the
fuel
rail
.
The
ECM
monitors
engine
speed
to
determine
the
duration
NOTE-
ofinjector
openings
.
Other
signals
to
the
ECM
help
determine
Poordriveabilitymaybe
encountered
when
the
batteryis
injector
pulse
time
for
different
operating
conditions
.
A
tem-
disconnected
and
reconnected
.
when
the
battery
is
dis-
connected,
the
adaptive
memory
is
lost
The
system
will
perature
sensor
signals
engine
temperature
for
mixture
adap-
readaptafterabout
ten
minutes
of
drfving
.
tion
.
A
throttle
position
sensor
signals
throttle
position
.
The
exhaust
oxygen
sensor(s)
signal
information
about
combus-
tion
efficiency
for
control
of
the
air-fuel
mixture
.
1992
to
1995
DISA
(Dual
Resonance
Intake
System)
engines
are
equipped
with
a
single
sensor
.
1996
and
later
(OBD
II)
engines
are
equipped
with
an
oxygen
sensor
before
TheE36
4-cylinder
engine
is
equipped
with
a
dual
intake
andone
after
each
catalytic
converter
.
Forexample,the
M52
runner
system,
termed
DISA
.
DISA
offers
the
advantages
of
engine
is
equipped
withfour
oxygen
sensors
.
both
short
and
long
intake
pipes
.
Long
intake
runners
are
most
useful
at
low
to
medium
engine
rpm
for
producing
good
Idle
speed
control
.
ldle
speed
is
electronically
controlled
torque
characteristics
.
Short
intake
runners
produce
hígherviathe
idle
speed
control
valve,
which
maintains
idle
speed
by
horsepower
at
hígher
engine
speeds
.
bypassing
varying
amounts
of
air
around
theclosed
throttle
valve
.
Idle
speed
is
not
adjustable
.
NOTE-
Knock
(detonation)
control
.
Knock
sensors
monitor
and
The
term
DISA
comes
from
the
German
words
Differen-
control
ignition
knock
through
the
ECM
.
The
knock
sensors
zierte
Sauganlage,
and
can
roughlybe
translated
as
"dif-
fering
intake
manifold
configuration
."
See
100
Engine-
function
like
microphones
and
are
able
to
convert
mechanical
General
foradditional
information
on
DISA
operation
.
vibration
(knock)
into
electrical
signals
.
The
ECM
is
pro-
grammed
to
react
to
frequencies
that
are
characteristic
of
en-
Manifold
construction
:
The
intake
manifold
is
a
two-piece
gine
knock
and
adapt
the
ignition
timing
point
accordingly
.
metal
construction,
with
a
pair
of
runners
in
thetop
section
See120
Ignition
System
for
further
details
.
and
four
runners
in
the
lower
section
.
A
butterfly
valve
is
in-
stalled
in
the
lower
section,
enabling
the
DISA
solenoid
toiso-
NOTE-
late
one
pair
of
runners
from
the
other
pair
.
See
Fig
.
2
.
The
1992
M50
engine
is
not
equipped
with
knock
sen-
Operation
.
With
the
DISA
butterfly
valve
closed,
the
pipes
sors
.
All
other
engines
are
equipped
with
two
knock
in
thetop
half
of
the
manifold
act
together
with
the
ram
air
sensors
.
pipes
in
the
lower
halfto
producea
single,
long
air
intake
pipe
for
each
cylinder
.
See
Fig
.
3
.
The
column
of
aír
oscíllating
in
Basic
Engine
Settings
this
combined
pipe
significantly
increases
engine
torque
in
the
medium
rpm
range
.
Idle
speed,
idle
mixture
(%CO),
and
ignition
timing
arenot
adjustable
.
The
adaptive
engine
management
system
is
de-
signed
to
automatically
compensate
for
changes
in
engine
op-
eratingconditions,
although
the
adaptive
range
is
limited
.
Once
these
limits
are
exceeded,
driveability
problems
usually
be-
come
noticeable
.
Above
approximately
4,800
rpm,
the
butterfly
valve
between
the
intake
air
pipes
for
the
two
cylinder
groups
is
opened
.
The
shorter
pipes
in
the
lower
manifold
section
now
become
the
main
suppliers
of
ram
air
to
the
cylinders,yielding
greater
pow-
er
at
the
upper
end
of
the
engine
rpm
range
.
See
Fig
.
4
.
Control
components
.
The
DISA
butterfly
valve
is
actuated
NOTE-
electro-pneumatically
via
the
engine
control
module
(ECM)
.
lf
the
system
adaptive
limits
are
exceeded,
the
Check
The
valve
begins
to
open
as
engine
speed
rises
aboye
4,840
Engine
light
will
most
likely
come
on,
indicating
an
rpmand
closes
below
4,760
rpm
.
The
action
of
the
valve
is
de-
emissions-
related
fault
For
Check
Engine
light
diag-
liberately
delayed
to
prevent
it
from
opening
and
closing
repeat-
nostics,
see100
Engine-General
.
edly
within
a
short
time
.
GENERAL
Page 306 of 759
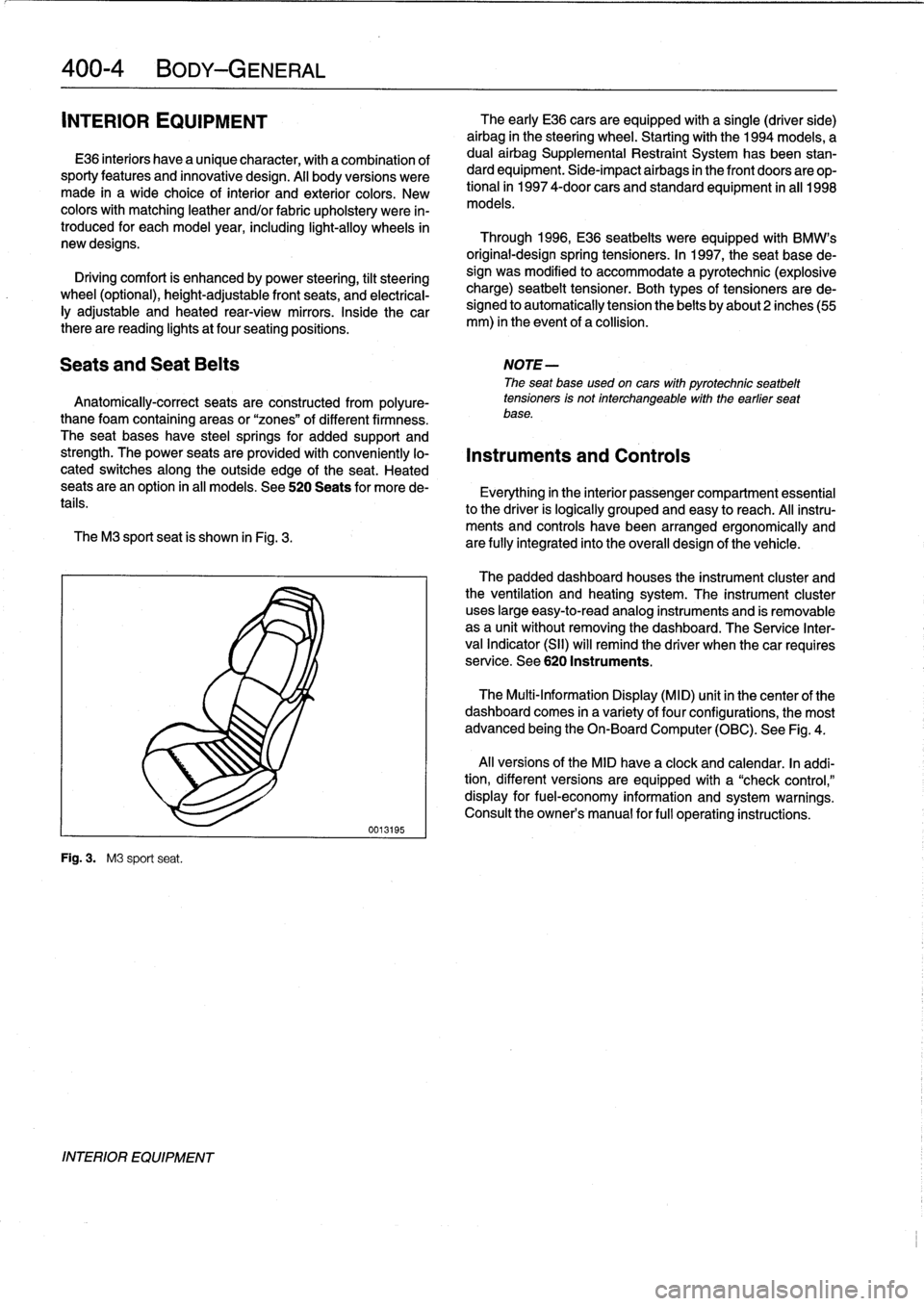
400-
4
BODY-GENERAL
INTERIOR
EQUIPMENT
E36
interiors
have
a
unique
character,
with
a
combínation
of
sporty
features
and
innovative
design
.
Al¡
body
versions
were
made
in
a
wide
choice
of
interior
and
exterior
colors
.
New
colors
with
matching
leather
and/or
fabric
upholstery
were
in-
troduced
for
each
model
year,
including
light-alloy
wheels
in
new
designs
.
Driving
comfort
is
enhanced
by
power
steering,
tilt
steering
wheel
(optional),
height-adjustable
front
seats,
and
electrical-
ly
adjustable
and
heated
rear-view
mirrors
.
Inside
thecar
there
are
reading
lights
at
four
seating
positions
.
Seats
and
Seat
Belts
NOTE-
Theseat
base
usedon
cars
with
pyrotechnic
seatbelt
Anatom¡cal
ly-correct
seats
are
constructed
from
polyure-
tensioners
is
not
interchangeable
with
the
earlier
seat
thane
foam
containing
areas
or
"zones"
of
different
firmness
.
base
.
The
seat
bases
have
steel
springs
for
added
support
and
strength
.
The
power
seats
are
provided
with
conveniently
lo-
Instruments
and
Controls
cated
switches
along
the
outside
edge
of
the
seat
.
Heated
seats
are
an
option
in
all
models
.
See
520
Seats
for
more
de-
Everything
in
the
interior
passenger
compartment
essential
tails
.
to
the
driver
is
logically
grouped
and
easy
to
reach
.
Al¡
instru-
ments
and
controls
havebeen
arranged
ergonomically
and
The
M3
sport
seat
is
shown
in
Fig
.
3
.
are
fully
integrated
into
the
overall
design
of
the
vehicle
.
Fig
.
3
.
M3
sport
seat
.
INTERIOR
EQUIPMENT
0013195
The
early
E36
cars
areequipped
with
a
single
(driver
side)
airbag
in
the
steering
wheel
.
Startingwith
the
1994
models,
a
dual
airbag
Supplemental
Restraint
System
has
been
stan-
dard
equipment
.
Side-impact
airbags
in
the
front
doors
are
op-
tional
in
1997
4-door
cars
and
standard
equipment
in
all
1998
models
.
Through
1996,
E36
seatbelts
were
equipped
with
BMW's
original-designspring
tensioners
.
In
1997,
the
seat
base
de-
sign
was
modified
to
accommodate
a
pyrotechnic
(explosive
charge)
seatbelt
tensioner
.
Both
types
of
tensioners
arede-
signed
to
automatically
tension
the
belts
by
about2
inches(55
mm)
in
the
event
of
a
collision
.
The
padded
dashboard
houses
the
instrument
cluster
and
the
ventilation
and
heating
system
.
The
instrument
cluster
uses
large
easy-to-read
analog
instruments
and
is
removable
as
a
unit
without
removing
the
dashboard
.
The
Service
Inter-
val
Indicator
(SII)
will
remind
the
driver
when
thecar
requires
service
.
See
620
Instruments
.
The
Multi-Information
Display
(MID)
unit
in
thecenter
of
the
dashboard
comes
in
a
variety
of
four
configurations,
the
most
advanced
being
the
On-Board
Computer
(OBC)
.
See
Fig
.
4
.
Al¡
versions
of
the
MID
have
a
clock
and
calendar
.
In
addi-
tion,
different
versions
areequipped
with
a
"check
control,"
display
for
fuel-economy
information
and
system
warnings
.
Consult
the
owner's
manual
for
fui¡
operating
instructions
.
Page 388 of 759
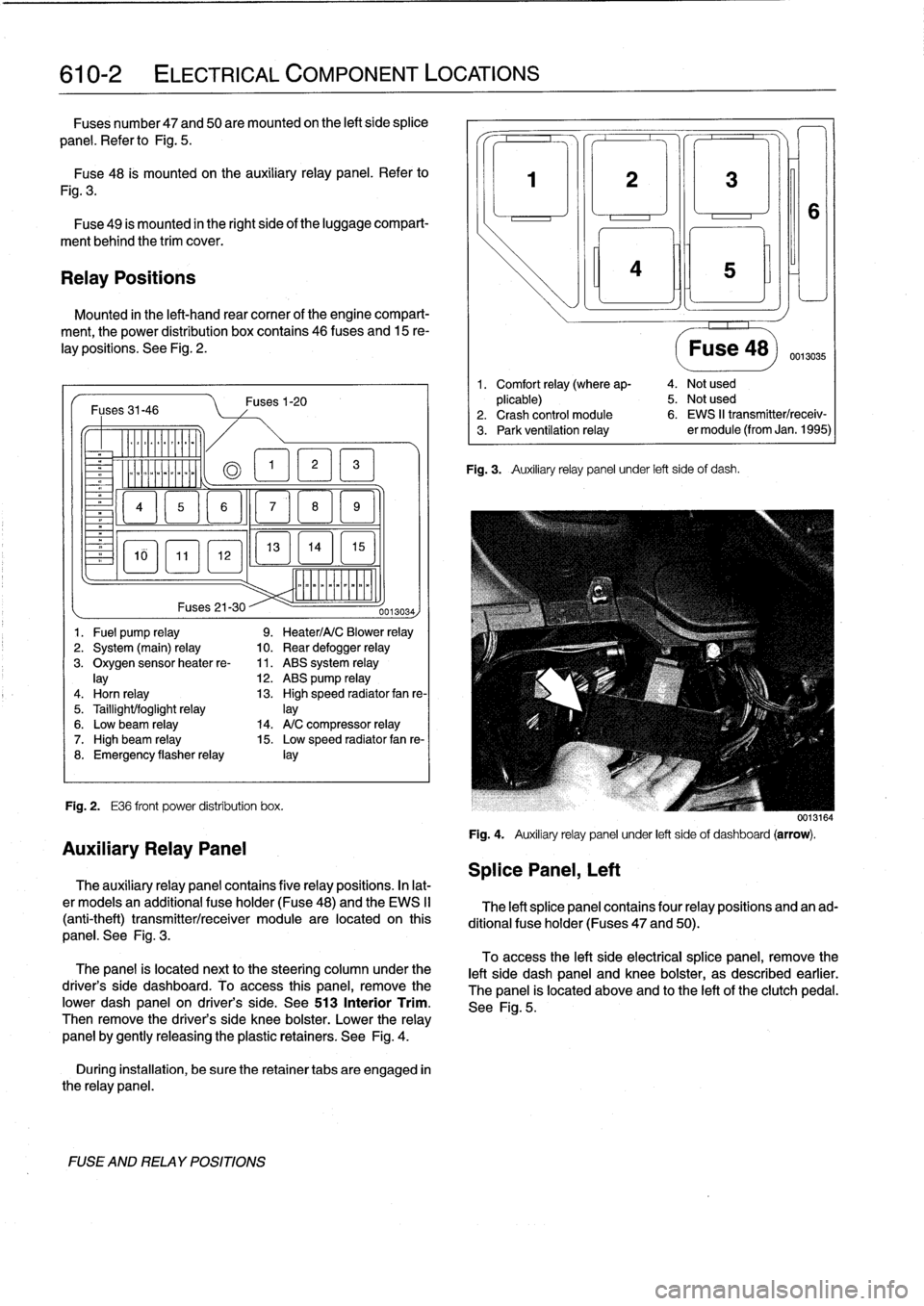
610-2
ELECTRICAL
COMPONENT
LOCATIONS
Fuses
number47
and
50are
mounted
on
the
left
side
splice
panel
.
Refer
lo
Fig
.
5
.
Fuse48
is
mounted
on
the
auxiliary
relay
panel
.
Refer
to
Fig
.
3
.
Fuse
49
is
mounted
in
the
right
side
of
the
luggage
compart-
ment
behind
the
trim
cover
.
Relay
Positions
Mounted
in
the
left-hand
rear
comer
of
the
engine
compart-
ment,
the
power
distribution
box
contains
46
(uses
and
15
re-
lay
positions
.
See
Fig
.
2
.
Fuses31-46
-
Er
a
&QT
MM
~
Fig
.
2
.
E36
front
power
distribution
box
.
FUSE
AND
RELAY
POSITIONS
Fuses1-20
13
EL1
5
]
mmmmmmmmmm
Fuses
21-30
--
0013034)
1
.
Fuel
pump
relay
9
.
Heater/A/C
Blower
relay
2
.
System
(main)
relay
10
.
Rear
defogger
relay
3
.
Oxygen
sensorheater
re-
11
.
ABS
system
relay
lay
12
.
ABS
pump
relay
4
.
Horn
relay
13
.
High
speed
radiator
fan
re-
5
.
Taillight/foglight
relay
]ay
6
.
Low
beam
relay
14
.
A/C
compressor
relay
7
.
High
beam
relay
15
.
Low
speed
radiator
fan
re-
8
.
Emergency
flasherrelay
¡ay
Auxiliary
Relay
Panel
The
auxiliary
relay
panel
contains
five
relay
positions
.
In
lat-
er
modeis
an
additional
fuse
holder
(Fuse48)
and
the
EWS
II
(anti-theft)
transmitter/receiver
module
are
located
on
this
panel
.
See
Fig
.
3
.
The
panel
is
located
nextto
the
steering
column
under
the
driver's
side
dashboard
.
To
access
this
panel,
remove
the
pwer
dash
panel
on
driver's
side
.
See513
Interior
Trim
.
Then
remove
the
driver's
side
knee
bolster
.
Lower
the
relay
panel
by
gently
releasing
the
plastic
retainers
.
See
Fig
.
4
.
During
installation,
be
sure
the
retainer
tabs
are
engaged
in
the
relay
panel
.
Splice
Panel,
Left
3
¡ni
Fig
.
3
.
Auxiliary
relay
panel
under
left
side
of
dash
.
Fuse
48)
0013035
1
.
Comfort
relay
(where
ap-
4
.
Not
used
plicable)
5
.
Not
used
2
.
Crash
control
module
6
.
EWS
II
transmitter/receiv-
3
.
Park
ventilation
relay
er
module
(from
Jan
.
1995)
0013164
Fig
.
4
.
Auxiliary
relay
panel
under
left
sideof
dashboard
(arrow)
.
The
left
splice
panel
contains
four
relay
positions
and
an
ad-
ditional
fuse
holder
(Fuses
47
and
50)
.
To
access
the
left
side
electrical
splice
panel,
remove
the
left
side
dash
panel
and
knee
bolster,
as
described
earlier
.
The
panel
is
located
above
and
lo
the
left
of
the
clutch
pedal
.
See
Fig
.
5
.
Page 406 of 759
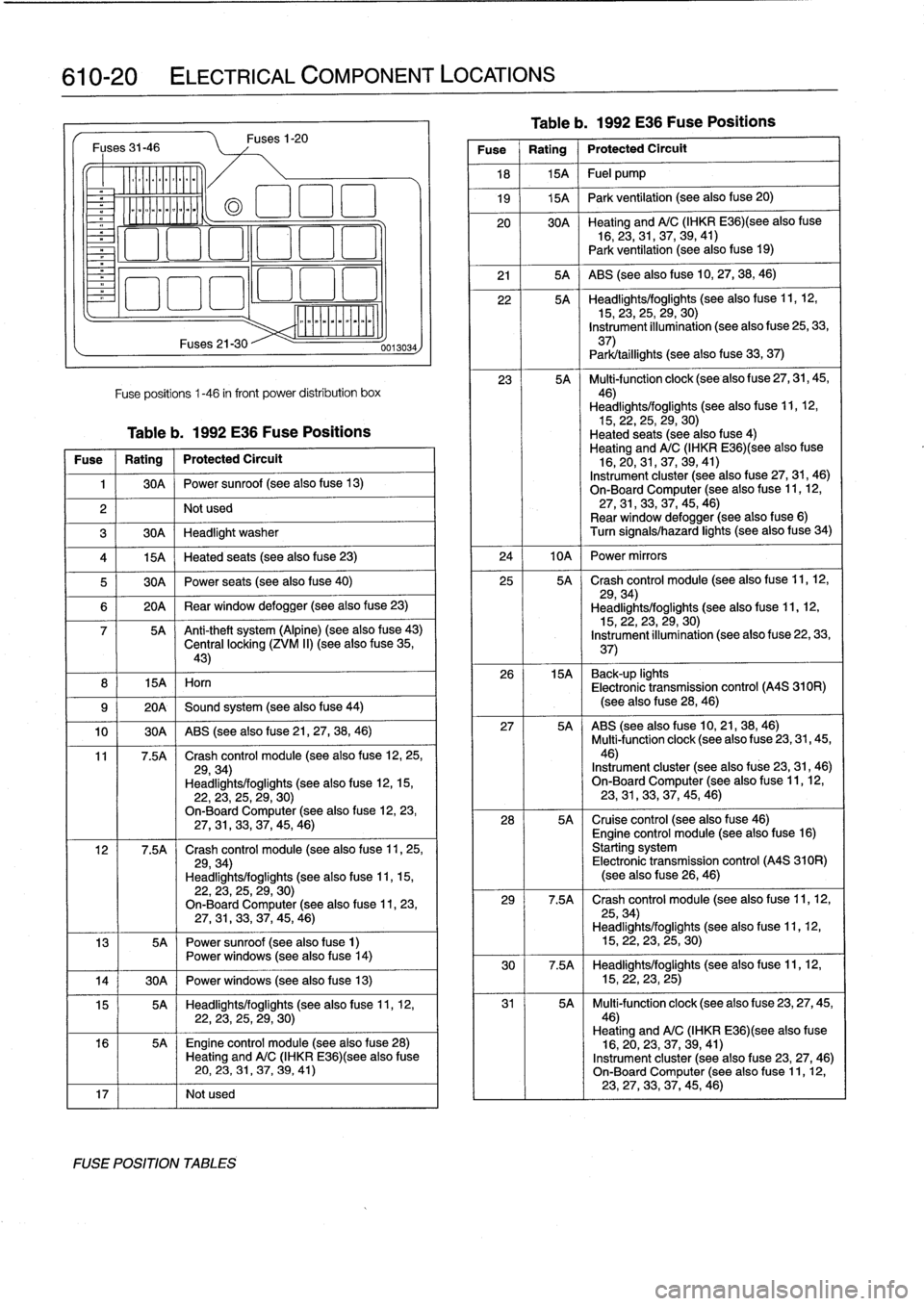
610-20
ELECTRICAL
COMPONENT
LOCATIONS
Fuses
31-46
o_
~oomoo
ommmo~
8
I
15A
I
Horn
Fuses21-30
Fuses
1-20
Fuse
positions
1-46
in
front
power
distribution
box
Table
b
.
1992
E36
Fuse
Positions
Fuse
1
Rating
1
Protected
Circuit
1
1
30A
1
Power
sunroof
(see
also
fuse
13)
2
I
I
Not
used
3
1
30A
1
Headlight
washer
(a
El
1
:1
El
4
1
15A
1
Heated
seats
(see
also
fuse
23)
5
1
30A
1
Power
seats
(see
also
fuse
40)
6
1
20A
1
Rear
window
defogger
(see
also
fuse
23)
7
5A
~
Anti-theft
system
(Alpine)
(see
also
fuse
43)
Central
locking
(ZVM
II)
(see
also
f
use
35,43)
9
(
20A
1
Sound
system
(see
also
fuse
44)
10
1
30A
1
ABS
(see
also
f
use
21,
27,
38,
46)
11
7
.5A
Crash
control
module
(seealso
fuse
12,25,
29,34)
Headlights/foglights
(see
also
fuse
12,15,22,23,
25,29,
30)
On-BoardComputer
(seealsofuse
12,
23,27,31,
33,37,
45,
46)
12
7
.5A
Crash
control
module
(see
also
f
use
11,
25,
29,34)
Headlights/foglights
(seealsofuse
11,15,
22,
23,25,
29,
30)
On-BoardComputer
(see
also
fuse
11,
23,27,
31,33,
37,45,
46)
13
5A
Power
sunroof
(see
also
fuse
1)
Power
windows
(see
also
f
use
14)
14
j
30A
1
Power
windows
(see
also
fuse
13)
15
5A
Headlights/foglights
(see
also
fuse
11,
12,22,
23,
25,29,
30)
16
5A
~
Engine
control
module
(seealsofuse
28)
Heating
andA/C
(IHKR
E36)(see
alsofuse
20,
23,
31,37,
39,
41)
17
I
I
Notused
FUSE
POSITION
TABLES
0013034
Table
b
.
1992
E36
Fuse
Positions
Fuse
Rating
Protected
Circult
18
1
15A
1
Fuel
pump
19
j
15A
1
Park
ventilation
(see
also
fuse
20)
20
30A
~
Heating
andA/C
(IHKR
E36)(see
alsofuse
16,23,31,37,39,
41)
Park
ventilation
(see
also
f
use
19)
21
1
5A
{
ABS
(see
also
fuse
10,27,
38,46)
22
5A
Headlights/foglights
(see
also
f
use
11,12,15,
23,
25,29,
30)
Instrument
illumination
(see
also
fuse
25,33,
37)
Park/taillights
(seealsofuse
33,
37)
23
5A
Multi-function
clock
(see
also
fuse
27,
31,
45,
46)
Headlights/foglights
(see
also
fuse
11,12,15,22,25,
29,30)
Heated
seats
(seealsofuse
4)
Heating
andA/C
(IHKR
E36)(see
alsofuse
16,20,31,37,39,
41)
Instrument
cluster
(see
also
fuse
27,31,
46)
On-Board
Computer
(seealso
fuse
11,
12,
27,31,
33,
37,45,
46)
Rear
window
defogger
(see
alsofuse
6)
Turn
signals/hazard
lights
(seealsofuse
34)
24
I
10A
I
Power
mirrors
25
5A
Crash
control
module
(see
also
f
use
11,12,
29,34)
Headlights/foglights
(see
also
fuse
11,12,15,22,23,29,
30)
Instrument
illumination
(see
also
fuse
22,
33,
37)
26
15A
~
Back-up
lights
Electronic
transmission
control
(A4S
310R)
(seealsofuse
28,46)
27
5A
ABS
(see
also
fuse
10,21,38,
46)
Multi-function
clock
(see
also
fuse
23,
31,
45,46)
Instrument
cluster
(see
also
fuse
23,
31,46)
On-BoardComputer
(see
also
fuse
11,12,23,
31,
33,37,45,
46)
28
5A
Cruise
control
(see
alsofuse
46)
Engine
control
module
(see
alsofuse
16)
Starting
system
Electronic
transmission
control
(A4S
310R)
(see
also
f
use
26,
46)
29
7
.5A
Crash
control
module
(see
also
fuse
11,12,
25,34)
Headlights/foglights
(see
also
fuse
11,12,15,22,23,
25,
30)
30
7
.5A
Headlights/foglights
(see
also
fuse
11,
12,
15,22,23,
25)
31
5A
Multi-function
clock
(see
alsofuse
23,27,
45,46)
Heating
andA/C
(IHKR
E36)(see
also
fuse
16,20,
23,
37,39,
41)
Instrument
cluster
(seealso
fuse
23,
27,46)
On-Board
Computer
(see
also
f
use
11,12,23,27,
33,
37,45,
46)
Page 407 of 759
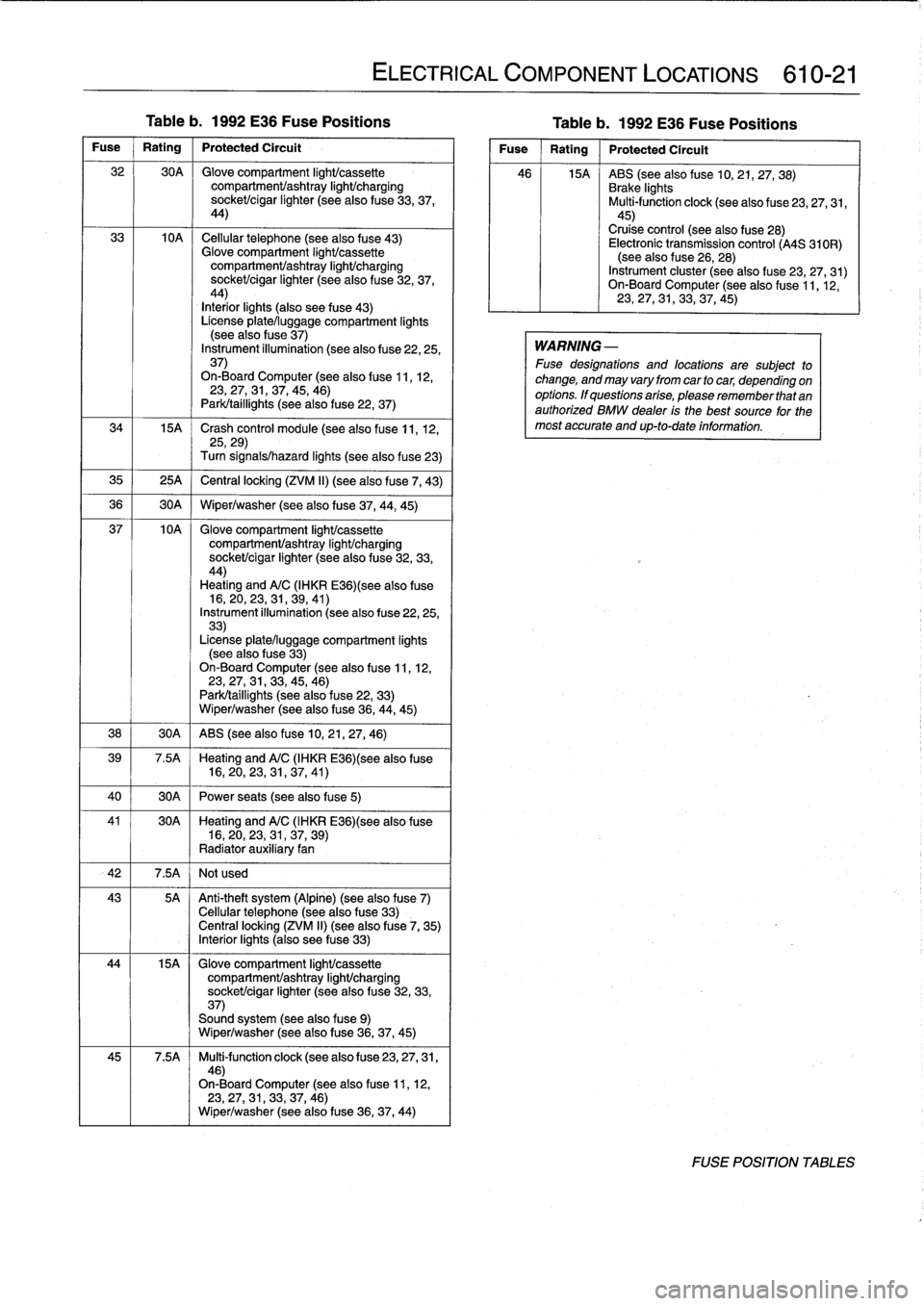
Table
b
.
1992
E36
Fuse
Positions
Table
b
.
1992
E36
Fuse
Positions
Fuse
Rating
Protected
Circuit
32
30A
Glove
compartment
light/cassette
compartmenVashtray
light/charging
socket/cigar
lighter
(see
also
fuse
33,37,
44)
33
10A
Cellular
telephone
(seealsofuse
43)
Glove
compartment
light/cassette
compartment/ashtray
IighUcharging
sockeUcigar
lighter
(seealsofuse
32,
37,
44)
Interiorlights
(also
see
fuse
43)
License
plate/luggage
compartment
lights
(see
also
f
use
37)
Instrument
íllumination
(see
also
fuse
22,25,
37)
On-Board
Computer
(see
also
fuse
11,12,23,27,31,37,45,
46)
Park/taillights
(seealso
fuse
22,
37)
34
15A
~
Crash
control
module
(see
also
fuse
11,
12,
25,29)
Turn
signals/hazard
lights
(seealsofuse
23)
35
1
25A
j
Central
locking
(ZVM
II)
(see
alsofuse
7,
43)
36
1
30A
1
Wiper/washer
(seealsofuse
37,44,
45)
37
10A
Glove
compartment
IighUcassette
compartmenVashtray
light/charging
socket/cigar
lighter
(see
also
fuse
32,33,
44)
Heating
andA/C
(IHKR
E36)(see
alsofuse
16,
20,23,31,
39,41)
Instrument
illumination
(see
also
fuse
22,25,
33)
License
plate/luggage
compartment
lights
(see
also
fuse
33)
On-Board
Computer
(see
also
fuse
11,12,23,27,31,33,45,
46)
Park/taillights
(see
alsofuse
22,
33)
Wiper/washer
(see
also
fuse
36,
44,
45)
38
1
30A
1
ABS
(see
also
fuse
10,21,27,
46)
39
7
.5A
Heating
andA/C
(IHKR
E36)(see
also
fuse
16,20,
23,
31,37,
41)
40
1
30A
1
Power
seats
(see
also
fuse
5)
41
30A
~
Heating
andA/C
(IHKR
E36)(see
alsofuse
16,20,23,
31,
37,
39)
Radiator
auxiliary
fan
42
I
7
.5A
I
Not
used
43
5A
Anti-theft
system
(Alpine)
(see
also
fuse
7)
Cellular
telephone
(seealsofuse
33)
Centrallocking
(ZVM
II)
(see
also
f
use
7,
35)
Interiorlights
(also
see
fuse
33)
44
15A
Glove
compartment
light/cassette
compartmenVashtray
light/charging
sockeUcigar
lighter
(see
also
fuse
32,
33,
37)
Sound
system
(see
also
fuse
9)
Wiper/washer
(see
also
fuse
36,37,
45)
45
7
.5A
Multi-function
clock
(see
also
fuse
23,
27,
31,
46)
On-Board
Computer
(see
also
fuse
11,12,
23,
27,31,33,
37,46)
Wiper/washer
(see
also
fuse
36,37,
44)
ELECTRICAL
COMPONENT
LOCATIONS
610-21
Fuse
Rating
Protected
Circuít
46
15A
ABS
(see
also
fuse
10,21,27,
38)
Brake
lights
Multi-function
clock
(seealso
fuse
23,27,31,
45)
Cruise
control
(see
also
fuse
28)
Electronic
transmission
control
(A4S
310R)
(see
also
f
use
26,
28)
Instrument
cluster
(seealsofuse
23,
27,31)
On-Board
Computer
(see
also
f
use
11,12,
23,
27,31,33,
37,45)
WARNING
-
Fuse
designations
and
locations
are
subject
to
change,
and
may
vary
from
car
tocar,
depending
on
options
.
If
questions
arise,
please
remember
that
an
authorized
BMW
dealer
is
the
best
source
for
the
most
accurate
and
up-to-date
information
.
FOSE
POSITION
TABLES