key BMW M3 1992 E36 Workshop Manual
[x] Cancel search | Manufacturer: BMW, Model Year: 1992, Model line: M3, Model: BMW M3 1992 E36Pages: 759
Page 4 of 759
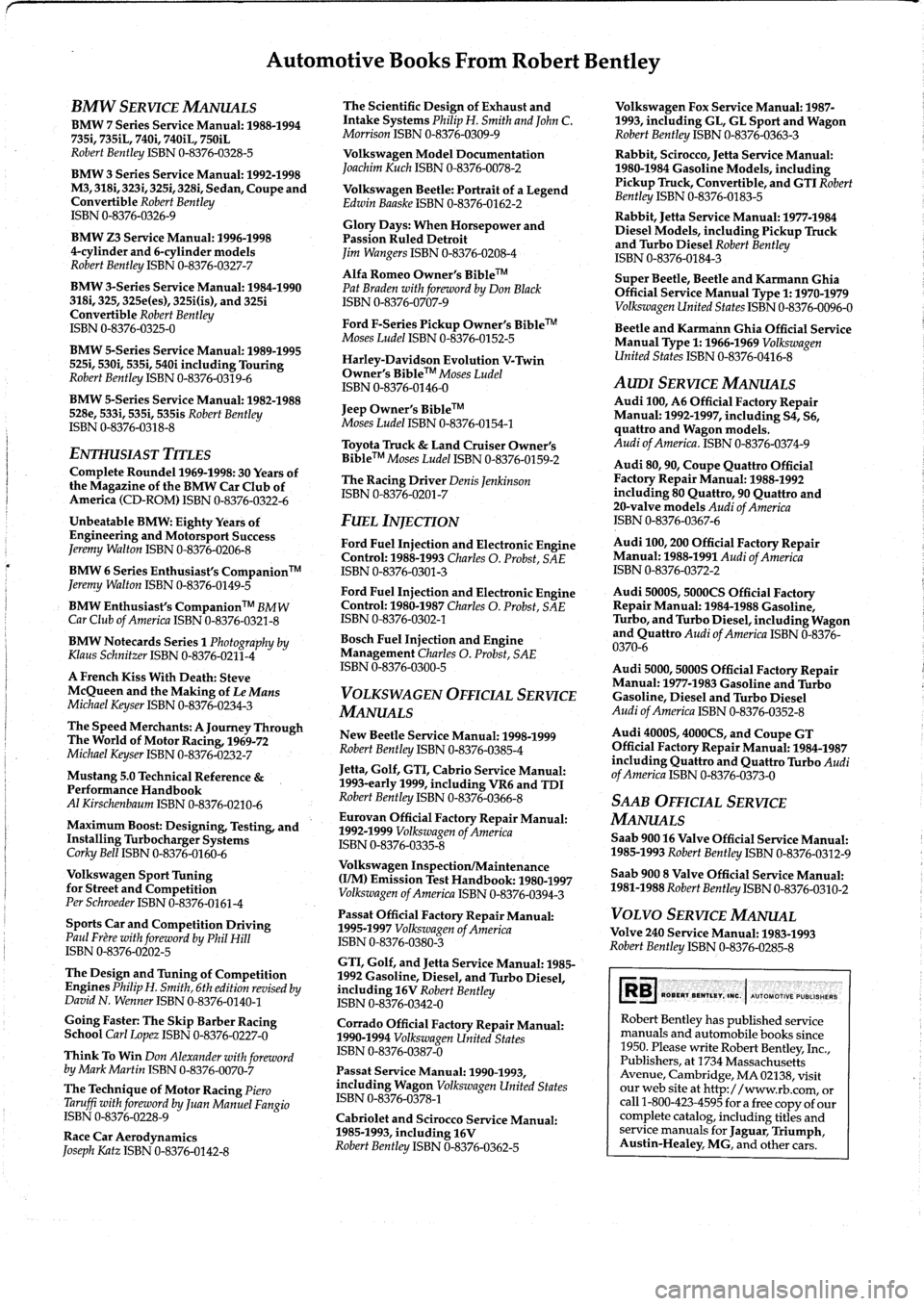
BMW
SERVICE
MANUUAS
BMW
7
Series
Service
Manual
:
1988-1994
7351,735iL,
740i,
740iL,
750iL
Robert
Bentley
ISBN
0-8376-0328-5
BMW
3
Series
Service
Manual
:
1992-1998
M3,
3181,323i,325i,
328i,
Sedan,
Coupe
and
Convertible
Robert
Bentley
ISBN
0-8376-0326-9
Glory
Days
:
When
Horsepowerand
BMW
Z3
Service
Manual
:
1996-1998
Passion
Ruled
Detroit
4-cylinder
and
6-cylinder
models
Jim
Wangers
ISBN
0-8376-0208-4
RobertBentley
ISBN
0-8376-0327-7
Alfa
Romeo
Owner's
BibleTM
BMW
3-Series
Service
Manual
:
1984-1990
Pat
Braden
with
foreword
by
Don
Black
3181,
325,325e(es),
325i(is),
and
325i
ISBN
0-8376-0707-9
Convertible
RobertBentley
ISBN
0-8376-0325-0
Ford
F-Series
Pickup
Owner's
BibleTM
Moses
Ludel
ISBN
0-8376-0152-5
BMW
5-Series
Service
Manual
:
1989-1995
5251,
530i,535i,
540i
including
Touring
Robert
Bentley
ISBN
0-8376-0319-6
BMW
5-Series
Service
Manual
:
1982-1988
528e,
5331,
535i,
535is
RobertBentley
ISBN
0-8376-0318-8
ENTHUSIAST
TITLES
Complete
Roundel
1969-1998
:30
Years
of
the
Magazine
of
the
BMW
Car
Club
of
America
(CD-ROM)
ISBN
0-8376-0322-6
A
French
Kiss
WithDeath
:
Steve
McQueen
and
the
Making
ofLe
Mans
Michael
Keyser
ISBN
0-8376-0234-3
The
Speed
Merchants
:
A
Journey
Through
The
World
of
Motor
Racing,1969-72Michael
Keyser
ISBN
0-8376-0232-7
Mustang
5
.0
Technical
Reference
&
Performance
Handbook
Al
Kirschenbaum
ISBN
0-8376-0210-6
Maximum
Boost
:
Designing,
Testing,
and
Installing
Turbocharger
Systems
Corky
Bell
ISBN
0-8376-0160-6
Volkswagen
Sport
Tuning
for
Street
and
Competition
Per
SchroederISBN
0-8376-0161-4
Sports
Carand
CompetitionDriving
Paul
Frérewithforewordby
PhilHill
ISBN
0-8376-0202-5
Automotive
Books
From
Robert
Bentley
GTI,
Golf,
and
Jetta
Service
Manual
:
1985-
The
Design
and
Tuning
of
Competition
1992
Gasoline,
Diesel,
and
Turbo
Diesel,
EnginesPhilipH
.
Smith,
6th
editionrevised
by
including
16V
Robert
Bentley
David
N
.
Wenner
ISBN
0-8376-0140-1
ISBN
0-8376-0342-0
Going
Faster
:
The
Skip
BarberRacing
Corrado
Official
Factory
Repair
Manual
:
School
Carl
Lopez
ISBN
0-8376-0227-0
1990-1994
Volkswagen
United
States
9M-f,
Ir-
Win
n
on
Alexander
with
foreword
ISBN
0-8376-0387-0
by
Mark
Martín
ISBN
0-8376-0070-7
Passat
Service
Manual
:
1990-1993,
The
Technique
of
Motor
Racing
Piero
including
Wagon
Volkswagen
United
States
Taruf
fi
with
foreword
by
Juan
Manuel
Fangio
ISBN
0-8376-0378-1
ISBN
0-8376-0228-9
Cabriolet
and
SciroccoService
Manual
:
Race
Car
Aerodynamics
1985-1993,
including
16V
Joseph
Katz
ISBN
0-8376-0142-8
RobertBentley
ISBN
0-8376-0362-5
The
Scientific
Design
of
Exhaust
and
VolkswagenFox
Service
Manual
:
1987-
Intake
Systems
Philip
H
.
Smith
and
John
C
.
1993,
including
GL,
GL
Sport
and
Wagon
Morrison
ISBN
0-8376-0309-9
RobertBentley
ISBN
0-8376-0363-3
Volkswagen
Model
Documentation
Rabbit,
Scirocco,
Jetta
Service
Manual
:
Joachim
Kuch
ISBN
0-8376-0078-2
1980-1984
Gasoline
Models,
including
Volkswagen
Beetle
:
Portrait
of
a
Legend
Pickup
Truck,
Convertible,
and
GTI
Robert
Edwin
Baaske
ISBN
0-8376-0162-2
Bentley
ISBN
0-8376-0183-5
Jeep
Owner's
BibleTM
Moses
Ludel
ISBN
0-8376-0154-1
Eurovan
Official
Factory
Repair
Manual
:
MANUUAS
Volkswagen
Inspection/Maintenance
(I/M)
Emission
Test
Handbook
:1980-1997
Volkswagen
of
America
ISBN
0-8376-0394-3
Rabbit,
Jetta
Service
Manual
:
1977-1984Diesel
Models,
including
Pickup
Truck
and
Turbo
Diesel
RobertBentley
ISBN
0-8376-0184-3
Super
Beetle,
Beetle
and
Karmann
Ghia
Official
Service
Manual
Type1
:1970-1979Volkswagen
United
States
ISBN
0-8376-0096-0
Beetle
and
Karmann
Ghia
Official
Service
Manual
Type1
:1966-1969
Volkswagen
United
States
ISBN
0-8376-0416-8
Harley-Davidson
Evolution
V
Twin
Owner's
BibleTM
Moses
Ludel
ISBN
0-8376-0146-0
Audi
100,
A6
Official
Factory
Repair
Manual
:
1992-1997,
including
S4,
S6,
quattro
and
Wagon
models
.
Toyota
Truck
&
Land
Cruiser
Owner's
Audi
of
America
.
ISBN
0-8376-0374-9
BibleTM
Moses
Ludel
ISBN
0-8376-0159-2
Audi
80,
90,
Coupe
Quattro
Official
AUDI
SERVICE
MANUUAS
The
Racing
Driver
Denis
Jenkinson
Factory
Repair
Manual
:
1988-1992
ISBN
0-8376-0201-7
including
80
Quattro,
90
Quattro
and
20-valve
models
Audi
of
America
Unbeatable
BMW
:
Eighty
Years
of
FUEL
INJECTION
ISBN
0-8376-0367-6
Engineering
and
Motorsport
Success
Ford
Fuel
Injection
and
Electronic
Engine
Audi
100,
200
Official
Factory
Repair
JeremyWalton
ISBN
0-8376-0206-8
Charles
O
Probst,
SAE
Manua1
:1988-1991
Audi
of
America
Control
:
1788-1993
.
BMW
6
Series
Enthusiast's
CompanionTM
ISBN
0-8376-0301-3
ISBN
0-8376-0372-2
Jeremy
W
.11
ISBN
0-8376-0149-5
Ford
Fuel
Injection
and
Electronic
Engine
Audi
50005
5000CS
Official
Fa
,ctory
BMW
Enthusiast's
CompanionTM
BMW
Control
:
1980-1987
Charles
O
.
Probst,
SAE
Repair
Manual
:
1984-1988
Gasoline,
Car
Club
of
America
ISBN
0-8376-0321-8
ISBN
0-8376-0302-1
Turbo,
and
Turbo
Diesel,
including
Wagon
BMW
Notecards
Series
1
Photography
by
Bosch
Fuel
In1ection
and
Engne
and
Quattro
Audi
of
America
ISBN
0-8376-
i
Klaus
Schnitzer
ISBN
0-8376-0211-4
Management
Charles
O
.
Probst,
SAE
0370-6
ISBN
0-8376-0300-5
Audi
5000,
50005
Official
Factory
Repair
Manual
:
1977-1983
Gasoline
and
Turbo
VOLKSWAGEN
OFFICIAL
SERVICE
Gasoline,
Diesel
and
Turbo
Diesel
MANUUAS
Audi
of
America
ISBN
0-8376-0352-8
New
Beetle
Service
Manual
:
1998-1999
Audi
40005,
4000CS,
and
Coupe
GT
RobertBentley
ISBN
0-8376-0385-4
Official
Factory
Repair
Manual
:
1984-1987including
Quattro
and
Quattro
Turbo
Audi
Jetta,
Golf,
GTI,
Cabrio
Service
Manual
:
of
America
ISBN
0-8376-0373-01993-early
1999,
including
VR6
and
TDI
Robert
Bentley
ISBN
0-8376-0366-8
SAAB
OFFICIALSERVICE
1992-1999
Volkswagen
of
America
Saab
90016
Valve
Official
Service
Manual
:
ISBN
0-8376-0335-8
19851993
RobertBentl
ISBN
0837603129
-ey---
Saab
900
8
Valve
Official
Service
Manual
:
1981-1988
Robert
Bentley
ISBN
0-8376-0310-2
Passat
Official
Factory
Repair
Manual
:
VOLVO
SERVICE
MANUAL
1995-1997
Volkswagen
of
America
Volve
240
Service
Manual
:
1983-1993
ISBN
0-8376-0380-3
Robert
Bentley
ISBN
0-8376-0285-8
Robert
Bentley
has
published
service
manualsand
automobile
books
since
1950
.
Please
write
Robert
Bentley,
Inc
.,
Publishers,
at
1734
Massachusetts
Avenue,Cambridge,
MA
02138,
visit
our
web
síte
athttp
://www
.rb
.com,
or
call
1-800-423-4595
for
a
free
copy
of
our
complete
catalog,
including
titles
and
service
manuals
for
Jaguar,
Triumph,
Austin-Healey,
MG,
and
other
cars
.
Page 14 of 759
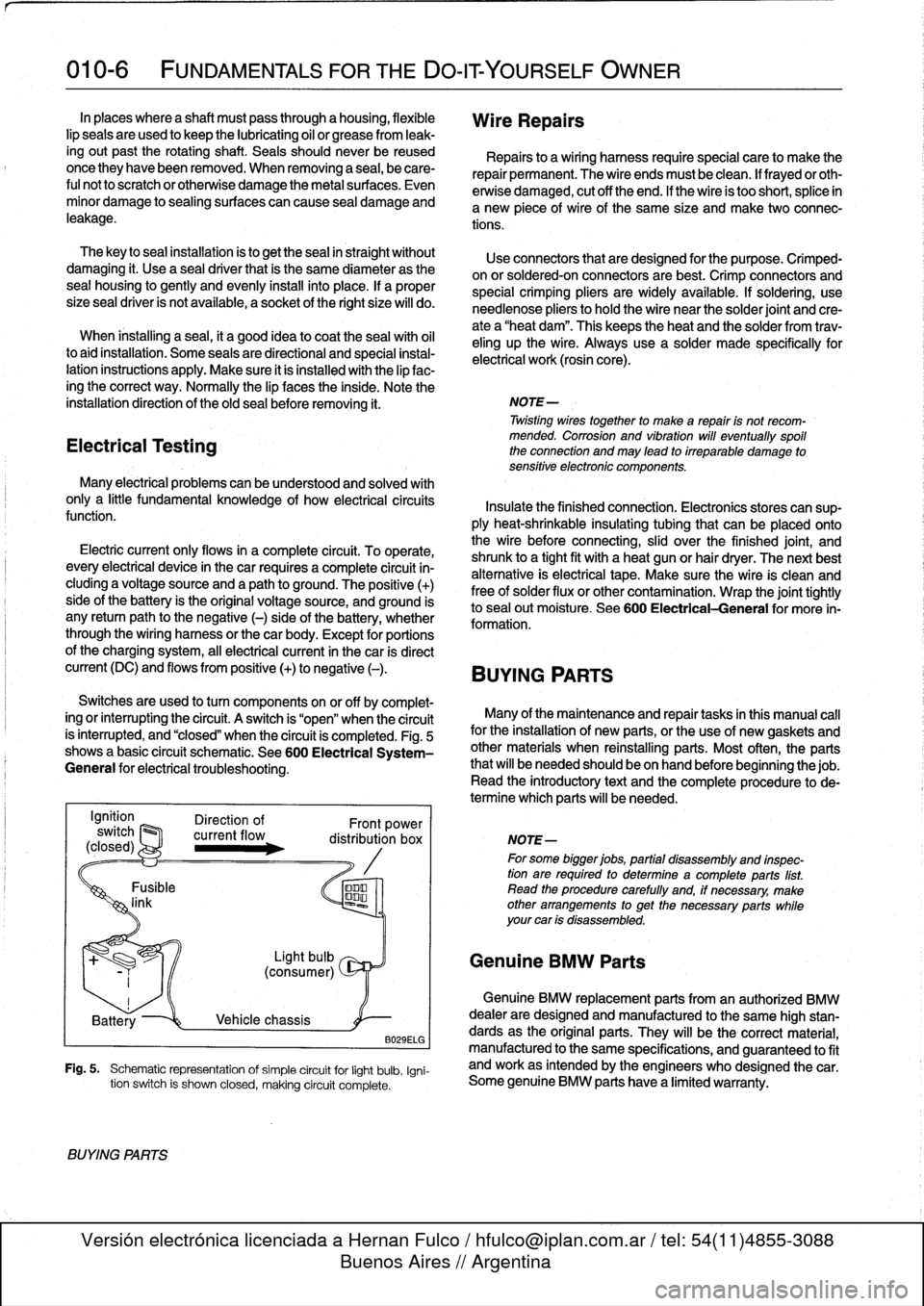
010-
6
FUNDAMENTALS
FOR
THE
DO-ITYOURSELF
OWNER
In
places
where
a
shaft
mustpass
through
a
housing,
flexible
lip
seals
areused
to
keep
the
lubricating
oil
or
grease
from
leak-
ingout
past
the
rotating
shaft
.
Seals
should
never
be
reused
once
they
have
been
removed
.
When
removing
a
seal,
be
care-
ful
not
lo
scratch
or
otherwise
damage
the
metal
surfaces
.
Even
minor
damage
to
sealing
surfaces
can
cause
sea¡
damage
and
leakage
.
The
key
to
sea¡
installation
is
to
get
the
sea¡
in
straight
without
damaging
¡t
.
Use
a
sea¡
driver
that
is
the
same
diameter
as
the
seal
housing
to
gently
and
evenly
insta¡I
into
place
.
If
a
proper
size
seal
driver
is
not
available,
a
socket
of
the
right
size
will
do
.
When
installing
a
seal,
¡t
a
good
idea
to
coat
the
sea¡
with
o¡I
to
aid
installation
.
Some
seals
are
directional
and
special
instal-
lation
instructions
apply
.
Make
sure
¡t
is
installed
with
the
lip
fac-
ing
the
correct
way
.
Normally
the
lip
faces
the
inside
.
Note
the
installation
direction
of
the
old
sea¡before
removing
¡t
.
Electrical
Testing
Many
electrical
problems
canbe
understood
and
solved
with
only
a
little
fundamental
knowledge
of
how
electrical
circuits
Insulate
the
finished
connection
.
Electronics
stores
can
sup-
function
.
ply
heat-shrinkable
insulating
tubing
that
can
be
placed
onto
the
wire
before
connectiog,
slid
over
the
finished
joint,
and
Electric
current
only
flows
in
a
complete
circuit
.
To
operate,
shrunk
to
a
tight
fit
with
a
heat
gun
orhair
dryer
.
The
nextbest
every
electrical
device
in
thecar
requires
a
complete
circuit
in-
alternative
is
electrical
tape
.
Make
sure
the
wire
is
clean
and
cluding
a
voltage
source
and
a
pathto
ground
.
The
positive
(+)
free
ofsolder
flux
or
other
contamination
.
Wrap
the
joint
tightly
side
of
the
battery
is
the
original
voltagesource,
and
ground
is
to
sea¡
out
moisture
.
See
600
Electrical-General
for
more
in-
any
retum
path
to
the
negative
()
-
side
ofth
e
battery°
whether
li
formation
.
through
the
wiring
harness
or
thecar
body
.
Except
for
portions
of
the
charging
system,
al¡
electrical
current
in
the
car
is
direct
current
(DC)
and
flows
from
positive
(+)
to
negative
(-)
.
BVYING
PART$
Switches
are
used
to
turn
components
on
or
off
by
complet-
ing
or
interrupting
#he
circuit
.
A
switch
is
"open"
when
the
circuit
Many
of
the
maíntenance
and
repair
tasks
in
this
manual
cal¡
is
ínterrupted,
and
"closed"
when
the
circuit
is
completed
.
Fig
.
5
for
the
installation
of
new
parte,
or
the
use
of
new
gaskets
and
shows
a
basic
circuit
schematic
.
See600
Electrical
System-
other
materials
when
reinstalling
parts
.
Most
often,
the
parts
General
for
electrical
troubleshooting
.
that
will
be
needed
should
be
on
hand
beforebeginningthe
job
.
Read
the
introductory
text
and
the
complete
procedure
to
de-
termine
which
parts
will
be
needed
.
B029ELG
Fig
.
5
.
Schematic
representation
of
simple
circuit
for
light
bulb
.
Igni-
tion
switch
is
shown
closed,
making
circuit
complete
.
BVYING
PARTS
Wire
Repairs
Repairs
to
a
wiring
harness
requirespecial
care
to
make
the
repair
permanent
.
The
wire
endsmust
be
clean
.
lf
frayedor
oth-
erwise
damaged,
cut
off
the
end
.
If
the
wire
is
too
short,
splice
in
a
new
piece
of
wire
of
the
same
size
and
make
two
connec-
tions
.
Use
connectors
that
are
designed
for
the
purpose
.
Crimped-
on
or
soldered-onconnectors
are
best
.
Crimp
connectors
and
special
crimping
pliers
are
widely
available
.
If
soldering,
use
needlenose
pliers
tohold
the
wire
near
the
solder
joint
and
cre-
ate
a
"heat
dam"
.
This
keeps
the
heat
and
the
solder
from
trav-
eling
up
the
wire
.
Always
use
a
solder
made
specifically
for
electrical
work
(rosin
core)
.
NOTE-
Twisting
wirestogether
to
make
a
repair
is
not
recom-
mended
.
Corrosion
and
vibration
will
eventually
spoil
the
connection
and
may
lead
to
irreparable
damage
to
sensitive
electronic
componente
.
NOTE-
For
some
bigger
jobs,
partial
disassembly
and
inspec-
tion
are
required
to
determine
acomplete
parts
list
.
Read
the
procedure
carefully
and,
if
necessary,
make
other
arrangements
to
get
the
necessary
parts
while
your
car
is
disassembled
.
Genuine
BMW
Parts
Genuine
BMW
replacement
parts
from
an
authorized
BMW
dealer
are
designed
and
manufactured
lo
the
same
high
stan-
dards
as
the
original
parts
.
They
will
be
the
correct
material,
manufactured
to
the
same
specifications,
and
guaranteed
lo
fit
and
work
as
intended
by
the
engineers
who
designed
thecar
.
Some
genuine
BMW
parts
have
a
limited
warranty
.
Page 16 of 759
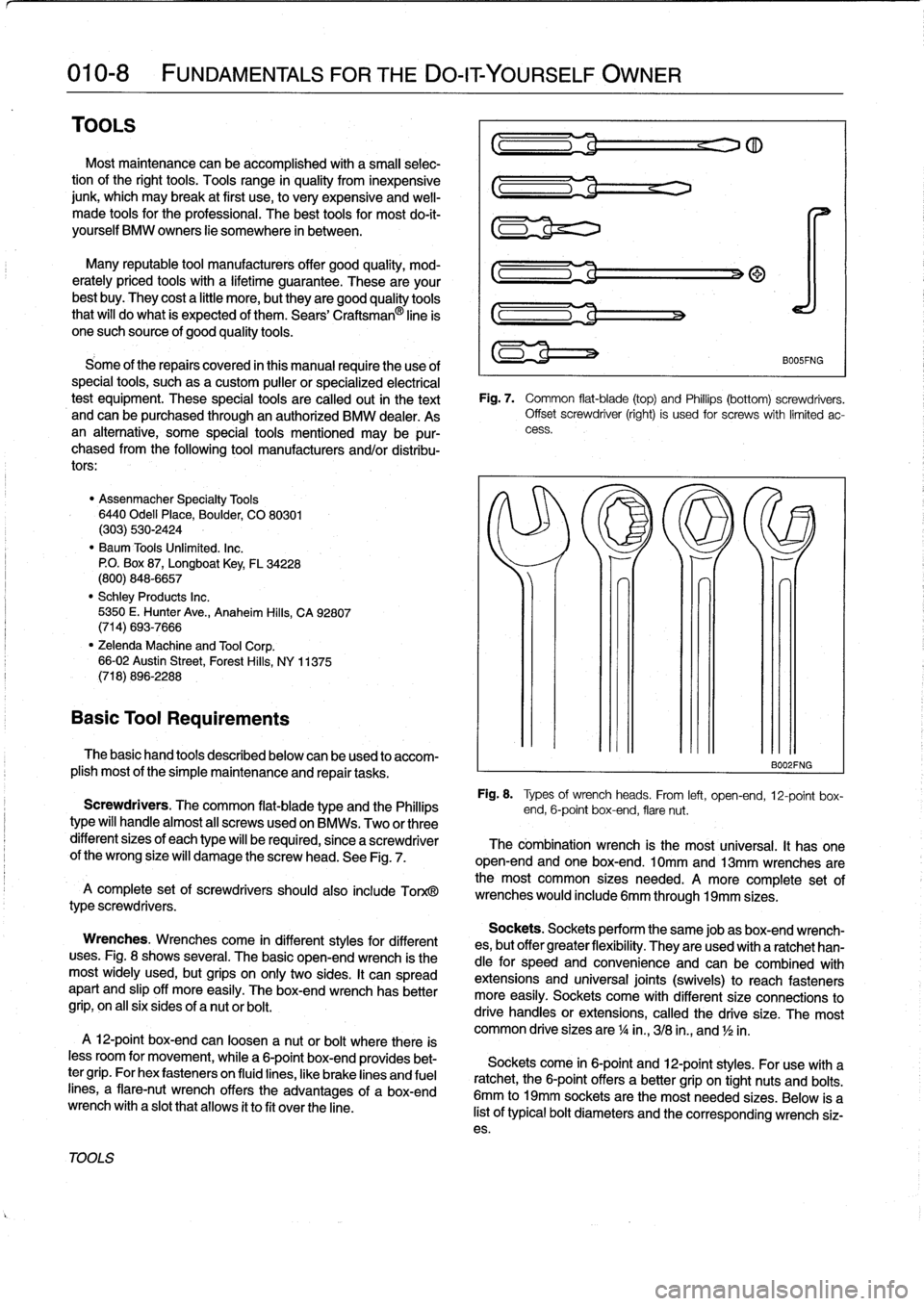
010-
8
FUNDAMENTALSFORTHE
DO-ITYOURSELF
OWNER
TOOLS
Mostmaintenance
can
be
accomplished
with
a
small
selec-
tion
of
the
right
tools
.
Toolsrange
in
quality
from
inexpensive
junk,
which
may
brakk
at
first
use,
tovery
expensive
and
well-
made
tools
for
the
professional
.
The
best
tools
for
most
do-it
yourself
BMW
owners
He
somewhere
in
between
.
O
Many
reputable
tool
manufacturers
offer
good
quality,
mod-
erately
priced
tools
with
a
lifetime
guarantee
.
These
are
your
best
buy
.
They
cost
a
little
more,
but
they
are
good
quality
tools
that
will
dowhat
is
expected
of
them
.
Sears'
Craftsman®
line
is
one
such
source
of
good
quality
tools
.
Some
of
the
repairs
covered
in
this
manual
require
the
use
of
special
tools,
suchas
a
custom
puller
or
specialized
electrical
test
equipment
.
These
special
tools
are
called
out
in
the
text
andcan
be
purchased
through
an
authorized
BMW
dealer
.
As
an
alternative,
some
special
tools
mentioned
may
be
pur-
chased
from
the
following
tool
manufacturers
andlor
distribu-
tors
:
"
Assenmacher
Specialty
Tools
6440
Odell
Place,Boulder,
CO
80301
(303)
530-2424
"
Baum
Tools
Unlimited
.
Inc
.
PO
.
Box
87,
Longboat
Key,
FL
34228
(800)
848-6657
"
Schley
Products
Inc
.
5350
E
.
Hunter
Ave
.,
Anaheim
Hills,
CA
92807
(714)
693-7666
"
Zelenda
Machine
and
Tool
Corp
.
66-02
Austin
Street,
Forest
Hills,
NY
11375
(718)
896-2288
Basic
Tool
Requirements
The
basic
hand
tools
described
below
canbe
used
to
accom-
plish
most
of
thesimple
maintenance
and
repair
tasks
.
Fig
.
8
.
Types
of
wrench
heads
.
From
left,
open-end,
12-point
box-
Screwdrivers
.
The
common
fíat-blade
type
and
the
Phillips
end,6-point
box-end,
fiare
nut
.
type
will
handlealmost
all
screws
used
on
BMWs
.
Two
orthree
different
sizes
of
each
type
will
be
required,
since
a
screwdriver
The
cómbination
wrench
is
the
most
universal
.
It
hasone
of
the
wrong
size
will
damage
the
screw
head
.
See
Fig
.
7
.
open-end
andone
box-end
.
10mm
and
13mm
wrenches
arethe
most
common
sizes
needed
.
A
more
complete
set
of
A
complete
set
of
screwdrivers
should
also
include
Torx@
wrenches
would
inciude
6mm
through
19mm
sizes
.
typescrewdrivers
.
Wrenches
.
Wrenches
come
in
different
styles
for
different
uses
.
Fig
.
8
shows
several
.
The
basic
open-end
wrench
is
the
most
widely
used,
but
grips
on
only
two
sides
.
It
can
spread
apart
and
slip
off
more
easily
.
The
box-end
wrench
has
better
grip,
on
al¡
six
sides
of
a
nut
or
bolt
.
A
12-point
box-end
can
loosen
a
nut
or
bolt
where
there
is
less
room
for
movement,
while
a
6-point
box-end
provides
bet-
ter
grip
.
Forhex
fasteners
on
fluid
lines,
like
brake
lines
and
fuel
lines,
a
fiare-nut
wrench
offers
the
acivantages
of
a
box-end
wrench
with
a
slot
that
ailows
it
to
fit
over
the
line
.
TOOLS
B005FNG
Fig
.
7
.
Common
flat-blade
(top)
and
Phillips
(bottom)
screwdrivers
.
Offset
screwdríver
(right)
is
used
for
screws
with
limited
ac-
cess
.
B002FNG
Sockets
.
Socketsperform
the
same
job
asbox-end
wrench-
es,
but
offer
greater
flexibility
.
They
are
used
with
a
ratchet
han-
dle
for
speed
and
conveniente
and
can
be
combined
with
extensions
and
universal
joints
(swivels)
to
reach
fasteners
more
easily
.
Sockets
come
with
different
size
connections
to
drive
handies
or
extensions,
called
the
drive
size
.
The
most
common
drive
sizes
are
1
/4
in
.,
318
in
.,
and
1
/2
in
.
Sockets
come
in
6-point
and
12-point
styles
.
For
use
with
a
ratchet,
the
6-point
offers
a
better
grip
on
tight
nuts
and
bolts
.
6mm
to
19mm
sockets
arethe
most
needed
sizes
.
Below
is
a
list
oftypical
bolt
diameters
and
the
corresponding
wrench
siz-
es
.
Page 24 of 759
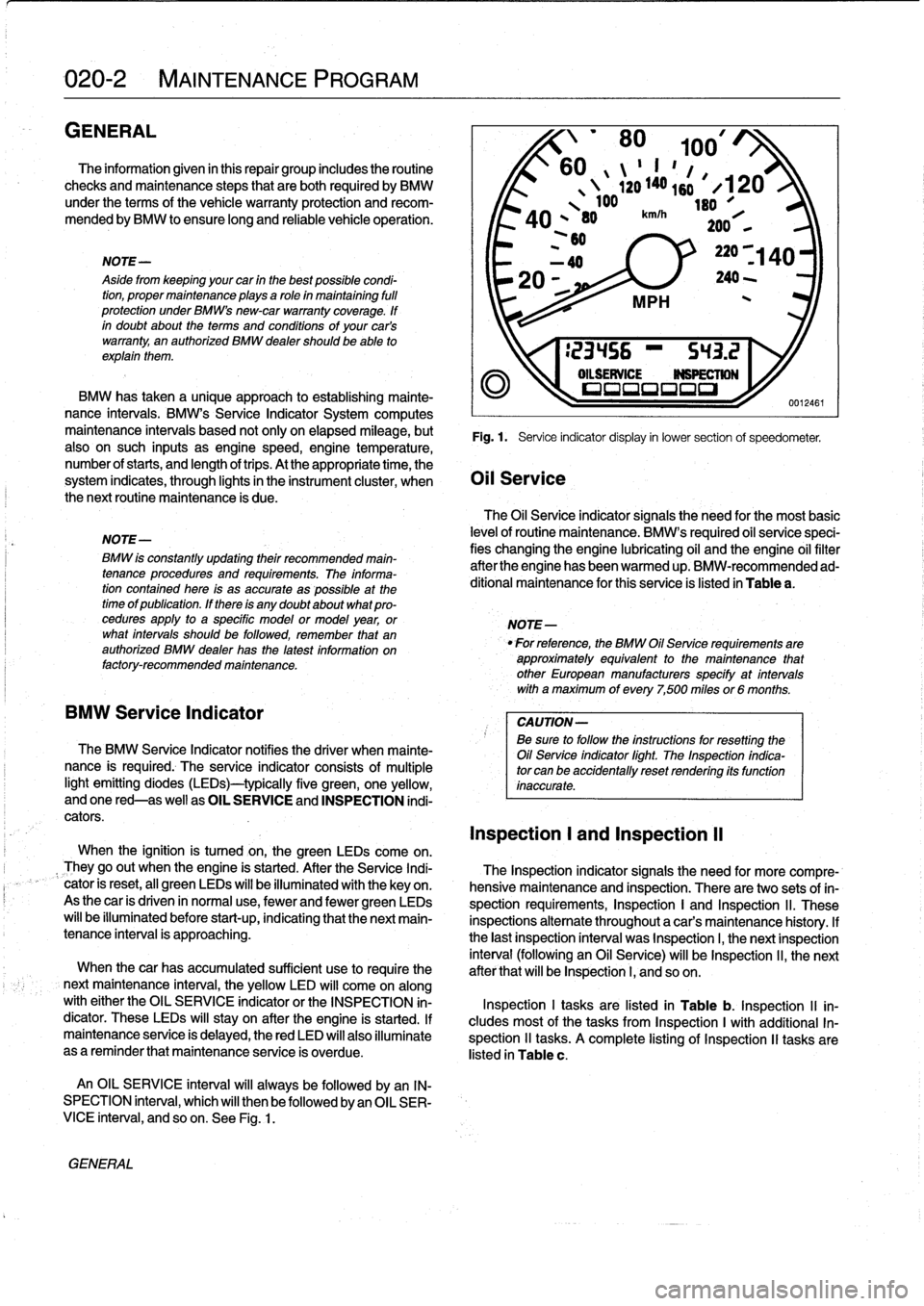
020-2
MAINTENANCE
PROGRAM
GENERAL
The
information
given
in
this
repair
group
includes
the
routine
checks
and
maintenance
steps
that
are
both
required
by
BMW
under
the
terms
of
the
vehicle
warranty
protection
and
recom-
mended
by
BMW
to
ensure
long
and
reliable
vehicle
operation
.
GENERAL
NOTE-
Aside
from
keeping
yourcar
in
the
bestpossible
condi-
tion,
proper
maintenance
plays
a
role
in
maintaining
full
protection
under
BMWs
new-car
warranty
coverage
.
If
in
doubtabout
the
terms
and
conditions
of
yourcark
warranty,
an
authorized
BMW
dealer
should
be
able
to
explain
them
.
NOTE-
BMW
is
constantly
updating
their
recommended
main-
tenance
procedures
and
requirements
.
The
informa-
tion
contained
here
is
as
accurate
as
possible
at
the
time
of
publication
.
If
hhere
is
any
doubt
aboutwhat
pro-
cedures
apply
to
a
specific
model
or
model
year,
or
what
intervals
should
be
followed,
remember
that
an
authorized
BMW
dealer
has
the
latest
information
on
factory-recommended
maintenance
.
BMW
Service
Indicator
The
BMW
Service
Indicator
notifies
the
driver
when
mainte-
nance
is
required
.
The
service
indicator
consístsof
multiple
light
emitting
diodes
(lEDs)-typically
five
green,
one
yellow,
andone
red-as
well
as
OIL
SERVICE
and
INSPECTION
indi-
cators
.
When
the
ignition
is
tumed
on,the
green
LEDs
come
on
.
They
go
out
when
the
engine
is
started
.
After
the
Service
Indi-
cator
is
reset,
al¡
green
LEDs
will
be
illuminatedwith
the
keyon
.
As
thecar
is
driven
in
normal
use,
fewer
and
fewer
green
LEDs
will
be
illuminated
before
start-up,indicating
that
the
next
main-
tenance
interval
is
approaching
.
When
thecar
has
accumulated
sufficient
use
to
require
the
next
maintenance
interval,
the
yellow
LED
will
come
on
along
with
either
the
OIL
SERVICE
indicator
or
the
INSPECTION
in-
dicator
.
These
LEDs
will
stay
on
after
the
engine
is
started
.
If
maintenance
service
is
delayed,
thered
LED
will
also
illuminate
as
a
reminder
that
maintenance
service
is
overdue
.
An
OIL
SERVICE
interval
will
alwaysbe
followed
by
an
IN-
SPECTION
interval,
which
will
then
be
followed
byan
OIL
SER-VICE
interval,
andsoon
.
See
Fig
.
1
.
'
80
100/
60
II
"
1
,
ló
1
,
4
`20
140s
#
X120
100
leo
A
O
,
80
km/h`F
*101
200
,
,
~60
BMW
has
taken
a
unique
approach
to
establishing
mainte-
nance
intervals
.
BMW's
Service
Indicator
System
computes
maintenance
intervais
based
not
only
on
elapsed
mileage,
but
Fig
.
1
.
Service
indicator
display
in
lower
section
of
speedometer
.
also
on
such
inputs
as
enginespeed,engine
temperature,
number
of
starts,
and
length
oftrips
.
At
the
appropriate
time,
the
system
indicates,
through
lights
in
the
instrument
cluster,
when
Oil
Service
the
next
routine
maintenance
is
due
.
The
Oil
Service
indicator
signals
the
need
for
the
most
basic
levelof
routine
maintenance
.
BMW's
required
oil
service
speci-
fies
changing
the
engine
lubricating
oil
and
the
engine
oil
filter
after
the
engine
has
been
warmed
up
.
BMW-recommended
ad-
ditional
maintenance
for
this
service
is
listed
in
Table
a
.
NOTE-
For
reference,
the
BMW
Oil
Service
requirements
are
approximately
equivalent
to
the
maintenance
that
other
European
manufacturers
specify
at
intervals
with
a
maximum
of
every
7,500
miles
or6
months
.
CAUTION-
Be
sure
to
follow
the
ínstructions
forresetting
the
Oil
Service
indicator
fight
.
The
Inspection
indica-
tor
can
be
accidentally
reset
rendering
its
function
inaccurate
.
Inspection
l
and
Inspection
II
The
Inspection
indicator
signals
the
need
for
more
compre-
hensive
maintenance
and
Inspection
.
There
are
two
sets
of
in-
spection
requirements,
Inspection
I
and
Inspection
ll
.
These
inspections
alternate
throughout
a
car's
maintenance
history
.
If
the
last
Inspection
interval
was
Inspection
I,
the
next
Inspection
interval
(following
an
Oil
Service)
will
be
Inspection
ll,
the
next
after
that
will
be
Inspection
I,
and
so
on
.
Inspection
I
tasks
are
listed
in
Table
b
.
Inspection
II
in-
cludes
most
of
the
tasks
from
Inspection
I
with
additional
In-
spection
11
tasks
.
A
complete
listing
of
Inspection
II
tasks
are
listed
in
Table
c
.
Page 27 of 759
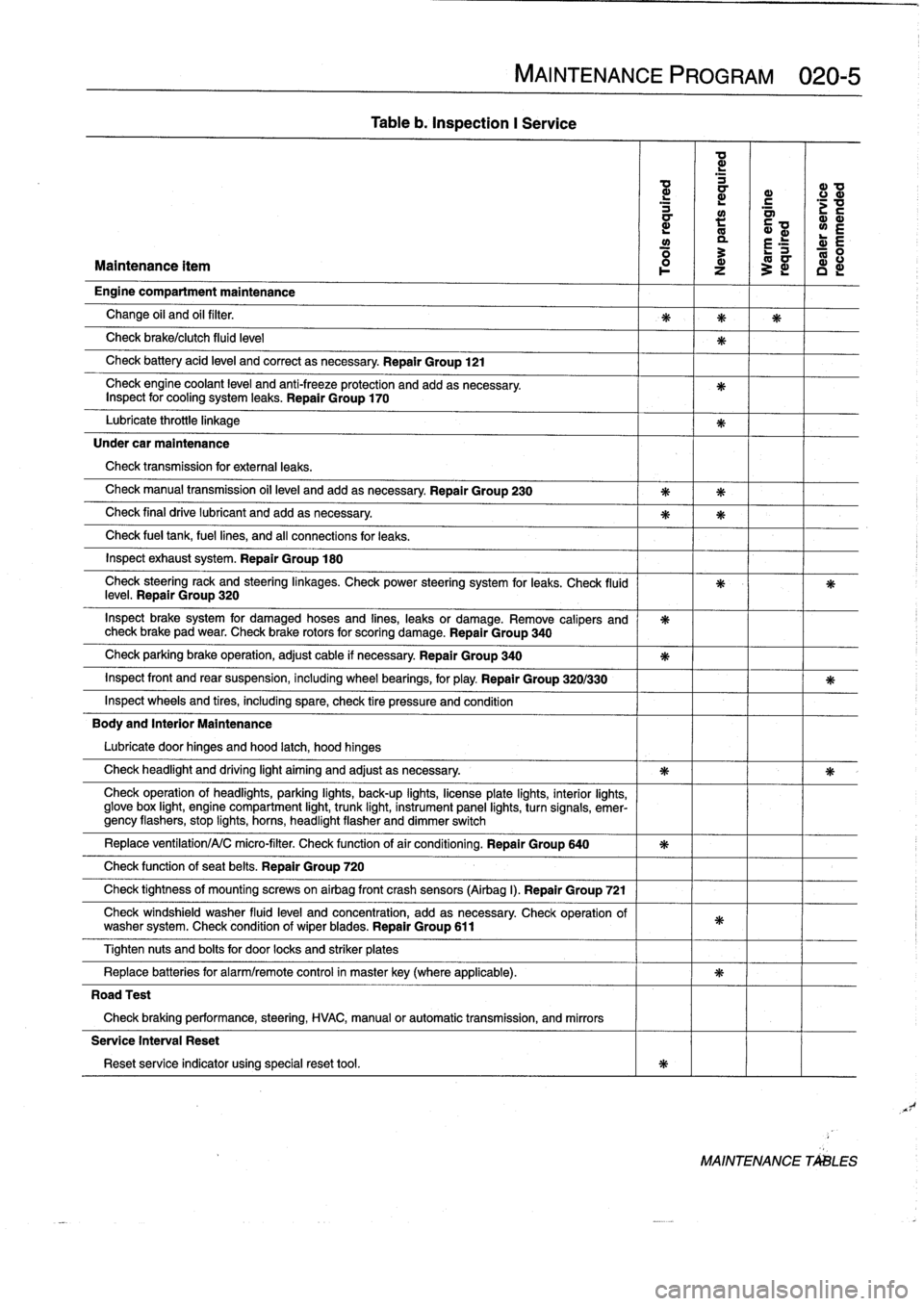
Table
b
.
Inspection
I
Service
MAINTENANCE
PROGRAM
020-5
ad
d
d
ID
a
r
c
d
a~
;v
a
:
Q~
wE
y
a
r
E
R
:
L-
0
Maintenance
ítem
1
z
3
~
c
d
Engine
compartment
maintenance
Change
oil
and
oil
filter
.
Check
brake/clutch
fluid
leve¡
Check
battery
acid
leve¡
and
correct
asnecessary
.
Repair
Group
121
Check
engine
coolant
level
and
anti-freeze
protection
and
addasnecessary
.
Inspect
for
cooling
system
leaks
.
Repair
Group
170
Lubricate
throttie
linkage
Under
car
maintenance
Check
transmission
for
externa¡
leaks
.
Check
manual
transmission
oil
leve¡
andadd
asnecessary
.
Repair
Group
230
Check
final
drive
lubricant
and
addasnecessary
.
Check
fue¡
tank,
fuel
lines,
and
all
connections
for
leaks
.
Inspect
exhaust
system
.
Repair
Group
180
Check
steeringrack
and
steeringlinkages
.
Check
power
steering
system
for
leaks
.
Check
(luid
leve¡
.
Repair
Group
320
Inspect
brake
system
for
damaged
hoses
and
fines,
leaks
or
damage
.
Remove
calipers
and
check
brake
pad
wear
.
Check
brake
rotors
for
scoring
damage
.
Repair
Group
340
Check
parking
brake
operation,
adjust
cable
if
necessary
Repair
Group
340
Inspect
front
and
rear
suspension,
including
wheel
bearings,
for
play
.
Repair
Group
320/330
Inspect
wheelsand
tires,
including
spare,
check
tire
pressure
and
condition
Body
and
Interior
Maintenance
Lubricate
door
hinges
and
hood
latch,
hood
hinges
Check
headlight
and
driving
light
aiming
and
adjust
as
necessary
.
Check
operation
of
headlights,
parking
lights,
back-up
fights,
licenseplate
lights,
interior
lights,
glove
box
light,
engine
compartment
light,
trunk
light,
instrument
panel
lights,
turnsignals,
emer-gency
flashers,
stop
fights,
horas,
headlight
flasher
and
dimmer
switch
Replace
ventilation/A/C
micro-filter
.
Check
functionof
air
conditioning
.
Repair
Group
640
Check
function
of
seat
belts
.
Repair
Group
720
Check
tightness
of
mountfng
screws
on
airbag
front
crash
sensors
(Airbag
I)
.
Repair
Group
721
Check
windshield
washer
fluid
leve¡
and
concentration,
add
as
necessary
Check
operation
of
washer
system
.
Check
condition
of
wiperblades
.
Repair
Group
611
Tighten
nuts
and
bolts
for
door
locks
and
striker
plates
Replace
batteries
for
alarm/remote
control
in
masterkey(where
applicable)
.
Road
Test
Check
braking
performance,
steering,
HVAC,
manual
or
automatic
transmission,
and
mirrors
Service
Interval
Reset
Reset
service
indicator
using
specialreset
tool
.
MAINTENANCE
TALES
Page 29 of 759
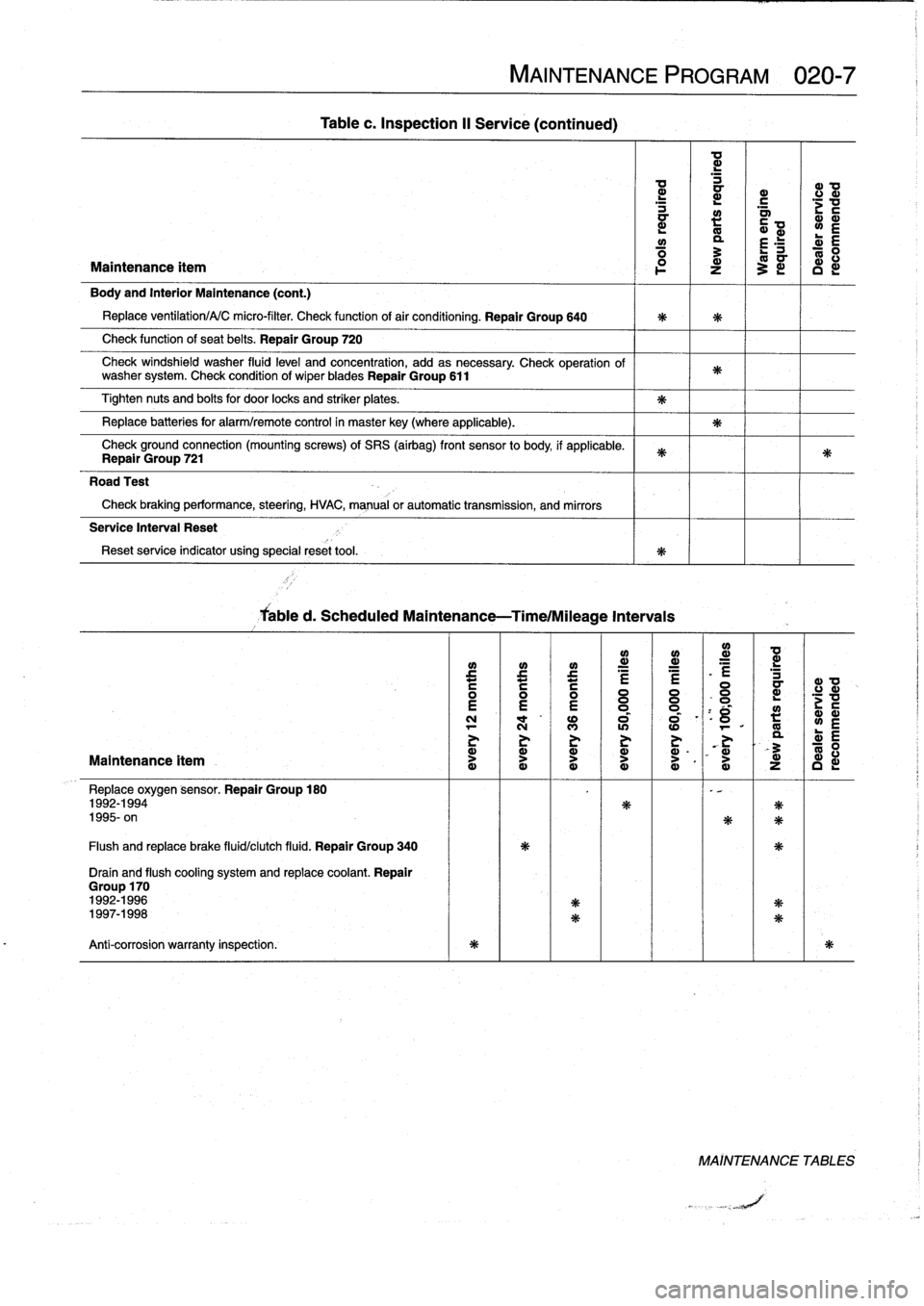
d
a
d
_
L
G>
G1
a
N
.
G1
Ñ
N
N
O
.
r
d
Maintenance
ítem
°
~
Z
~
i
I
D
i
Body
and
Interior
Maintenance
(cont
.)
Replace
ventilation/A/C
micro-filter
.
Check
function
of
air
conditioning
.
Repair
Group
640
Check
function
of
seat
belts
.
Repair
Group
720
Check
windshield
washer
fluid
level
and
concentration,
add
asnecessary
.
Check
operation
of
washer
system
.
Check
condition
of
wiperblades
Repair
Group
611
Tighten
nuts
and
belts
for
door
locks
and
striker
plates
.
Replace
batteries
for
alarm/remote
control
in
masterkey
(where
applicable)
.
Check
ground
connection
(mounting
screws)
of
SRS
(airbag)
front
sensor
to
body,
if
applicable
.
Repair
Group
721
Road
Test
Check
braking
performance,
steering,
HVAC,
manual
or
automatic
transmission,
and
mirrors
Service
Interval
Reset
Reset
service
indicator
using
specialreset
tool
.
Maintenance
ítem
Replace
oxygen
sensor
.
Repair
Group
180
1992-1994
1995-
on
Flush
and
replace
brake
fluid/clutch
fluid
.
Repair
Group
340
Drain
and
flush
cooling
system
and
replace
coolant
.
Repair
Group
170
1992-19961997-1998
Anti-corrosion
warranty
inspection
.
Tablec
.
Inspection
II
Service
(continued)
Cabled
.
Scheduled
Maintenance-Time/Mileage
Intervais
MAINTENANCE
PROGRAM
020-7
e
~
e
e
i
:
l=
N
l
"
NM
I
«)
al
aN
-
11
>
O
Ó
I
Ó
I`
Ó
d
Ny
.
0
°
_
VÑ
Ñ
Ñ
1
ZG
NN
MAÍNTENANCE
TABLES
Page 51 of 759
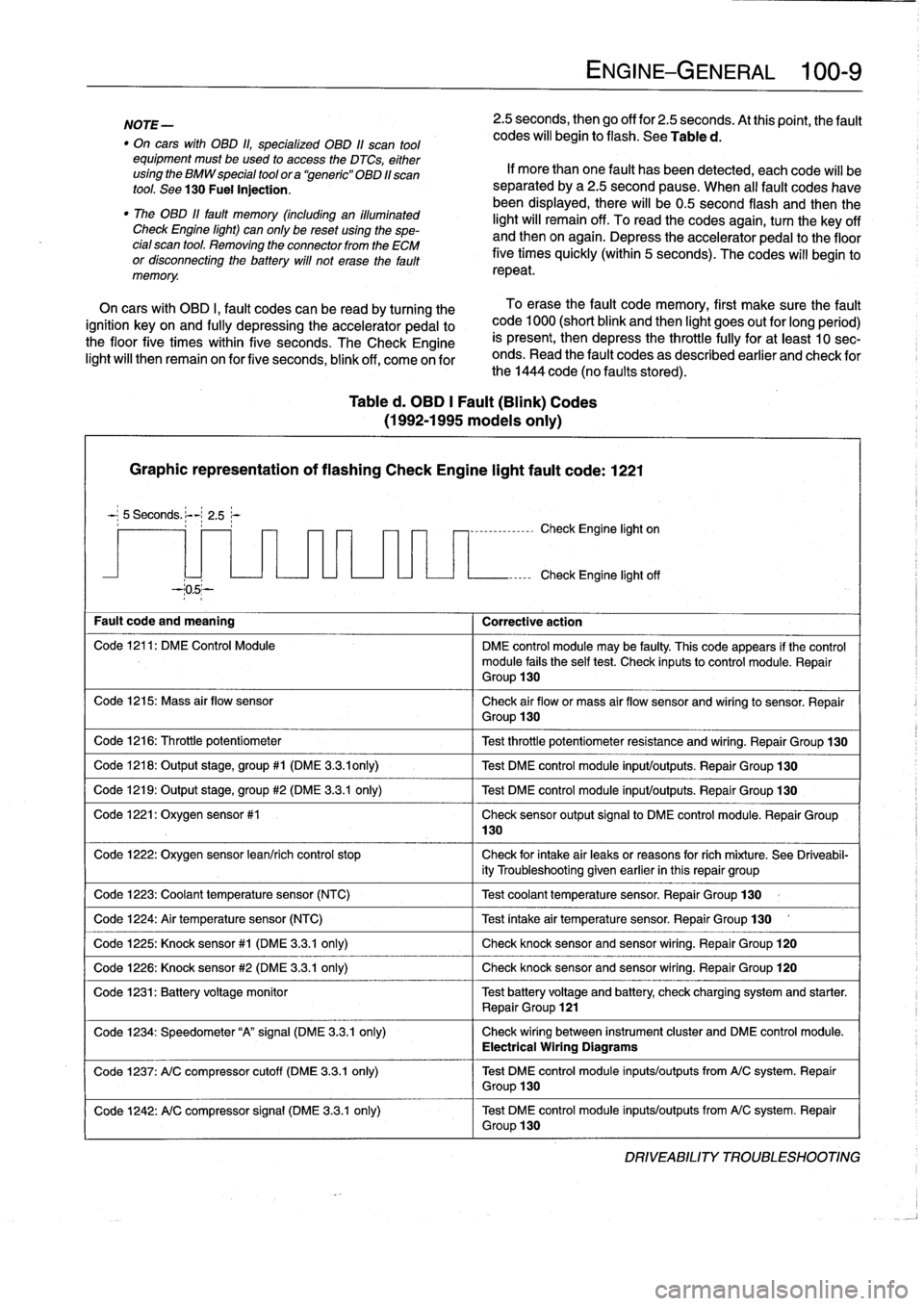
NOTE-
"
On
carswith
OBD
ti,
specialized
OBD
11
scan
tool
equipment
must
be
used
to
access
the
DTCs,
either
using
the
BMW
special
tool
ora
`generic"
OBD
11
scan
tool
.
See
130
Fuel
Injection
.
"
The
08D
11
fault
memory
(including
an
iiluminated
Check
Engine
light)
can
only
be
reset
using
the
spe-
cial
scan
tool
.
Removing
the
connector
from
the
ECM
or
disconnecting
the
battery
will
not
erase
the
fault
memory
.
Table
d
.
OBD
1
Fault
(Blink)
Codes
(1992-1995
modeis
only)
Graphic
representation
of
flashing
Check
Engine
light
fault
code
:
1221
5
Seconds
.
:-
2
.5~-
--05--
Fault
code
and
meaning
1
Corrective
action
Code
1216
:
Throttle
potentiometer
Code
1218
:
Output
stage,
group#1
(DME
3
.3
.ionly)
Code
1219
:
Output
stage,
group
#2
(DME
3
.3.1
only)
Code
1221
:
Oxygen
sensor
#1
Code
1224
:
Air
temperature
sensor
(NTC)
Code
1226
:
Knock
sensor
#2
(DME
3
.3
.1
only)
130
ENGINE-GENERAL
100-
9
2
.5
seconds,
then
go
off
for
2
.5
seconds
.
At
thispoint,
the
fault
codes
will
begin
to
flash
.
See
Table
d
.
If
more
than
one
fault
has
been
detected,
eachcode
will
be
separated
by
a2
.5
second
pause
.
When
al¡
fault
codes
havebeen
displayed,
there
will
be0
.5
second
flash
and
thenthe
light
will
remain
off
.
To
read
the
codes
again,
turn
the
key
off
and
then
on
again
.
Depress
theaccelerator
pedal
to
the
floor
five
times
quickly
(within
5
seconds)
.
The
codes
will
begin
to
repeat
.
On
cars
with
OBD
I,
fault
codes
can
be
read
by
turning
the
To
erase
the
fault
code
memory,
first
make
sure
the
fault
ignition
key
on
and
fully
depressing
theaccelerator
pedal
to
code
1000
(short
blink
and
then
light
goes
out
for
long
period)
the
floor
five
times
within
five
seconds
.
TheCheck
Engine
is
present,
then
depress
the
throttle
fully
for
at
least
10
sec-
light
will
then
remain
on
for
five
seconds,
blink
off,
come
on
for
onds
.
Read
the
fault
codes
as
described
earlier
and
check
for
the
1444
code
(no
faults
stored)
.
-,--------------
Check
Engine
light
on
Check
Engine
light
off
Code
1211
:
DM
E
Control
Module
DME
control
module
may
be
faulty
.
This
code
appears
if
the
control
module
fails
the
self
test
.
Check
inputsto
control
module
.
Repair
Group
130
Code
1215
:
Mass
air
flow
sensor
Check
air
flow
or
mass
air
flow
sensor
and
wiring
to
sensor
.
Repair
Group
130
Test
throttle
potentiometer
resistance
and
wiring
.
Repair
Group
130
Test
DME
control
module
input/outputs
.
Repair
Group
130
Test
DME
control
module
input/outputs
.
Repair
Group
130
Check
sensor
output
signal
to
DME
control
module
.
Repair
Group
Code
1222
:
Oxygen
sensor
lean/rich
control
stop
Check
for
intake
air
leaks
or
reasons
forrich
míxture
.
See
Driveabil-
ity
Troubleshooting
given
earlier
in
this
repair
group
Code
1223
:
Coolant
temperaturesensor
(NTC)
1
Test
coolant
temperature
sensor
.
Repair
Group
130
Test
intake
air
temperature
sensor
.
Repair
Group
130
Code
1225
:
Knock
sensor#1
(DME
3
.3
.1
only)
1
Check
knocksensorand
sensor
wiring
.
Repair
Group
120
Check
knocksensor
and
sensor
wiring
.
Repair
Group
120
Code
1231
:
Batteryvoltage
monitor
Test
battery
voltage
and
battery
check
charging
system
and
starter
.
Repair
Group
121
Code
1234
:
Speedometer
"A"signal
(DME
3
.3
.1
only)
Check
wiring
between
instrument
cluster
and
DME
control
module
.
Electrical
Wiring
Diagrams
Code
1237
:
A/C
compressor
cutoff
(DME
3
.3
.1
only)
Test
DME
control
module
inputs/outputs
from
A/C
system
.
Repair
Group
130
Code
1242
:
A/C
compressor
signal
(DME
3
.3.1
only)
Test
DME
control
module
inputs/outputs
from
A/C
system
.
Repair
Group
130
DRIVEABILITY
TROLIBLESHOOTING
Page 100 of 759
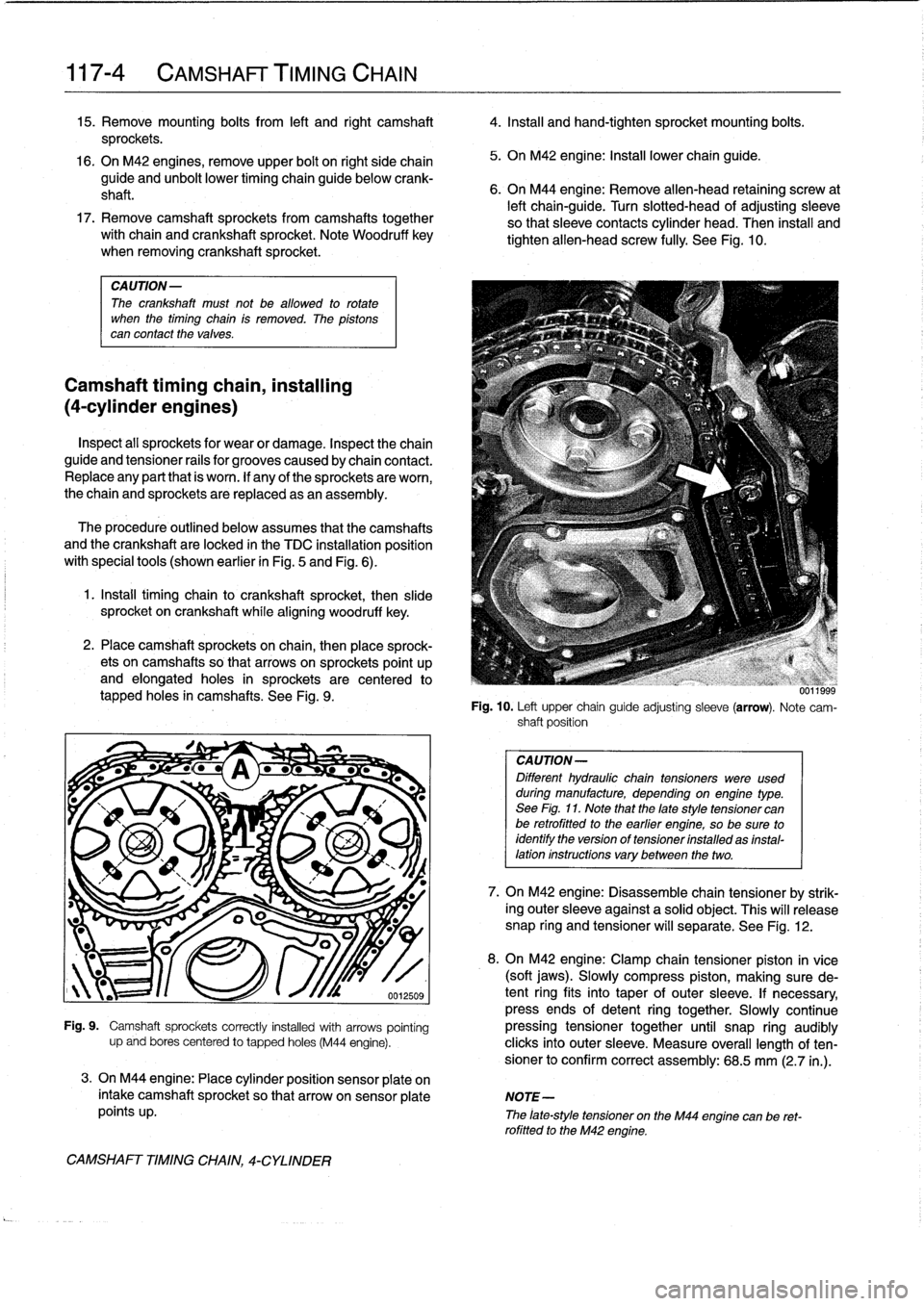
117-
4
CAMSHAFT
TIMING
CHAIN
15
.
Remove
mounting
bolts
from
left
and
right
camshaft
4
.
Insta¡¡
and
hand-tighten
sprocket
mounting
bolts
.
sprockets
.
16
.
On
M42
engines,
remove
upper
bolt
on
right
side
chainguide
and
unbolt
lower
timing
chainguide
below
crank-
shaft
.
17
.
Remove
camshaft
sprockets
from
camshafts
together
with
chain
and
crankshaft
sprocket
.
NoteWoodruffkey
when
removing
crankshaftsprocket
.
CA
UTION-
The
crankshaft
must
not
be
allowed
to
rotate
when
the
timing
chaín
is
removed
.
The
pistons
can
contact
the
valves
.
Camshaft
timing
chain,
installing
(4-cylinder
engines)
Inspectal¡
sprockets
for
wear
or
damage
.
Inspect
the
chain
guide
and
tensioner
rails
for
grooves
caused
by
chain
contact
.
Replace
any
partthat
is
worn
.
If
any
of
the
sprockets
are
worn,
the
chain
and
sprocketsare
replaced
asan
assembly
.
The
procedure
outlined
below
assumes
that
the
camshafts
and
the
crankshaft
arelocked
in
the
TDC
installation
positionwithspecial
tools
(shown
earlier
in
Fig
.
5
and
Fig
.
6)
.
1
.
Install
timing
chain
to
crankshaft
sprocket,
then
slide
sprocket
on
crankshaft
whílealigníng
woodruff
key
.
2
.
Place
camshaft
sprockets
on
chain,
then
place
sprock-
ets
oncamshafts
so
that
arrows
on
sprockets
point
up
and
elongatedholes
in
sprockets
are
centered
lo
tapped
holes
in
camshafts
.
See
Fig
.
9
.
.
I
Pa
-
s
~_
a
Ge
..
.
0012509
5
.
On
M42
engine
:
Install
lowerchainguide
.
6
.
On
M44
engine
:
Remove
allen-head
retaining
screw
at
left
chain-guide
.
Turn
slotted-head
of
adjusting
sleeve
so
that
sleeve
contacts
cylinder
head
.
Then
install
and
tighten'allen-head
screw
fully
.
See
Fig
.
10
.
Fig
.
10
.
Left
upper
chain
guide
adjusting
sleeve
(arrow)
.
Note
cam-
shaft
position
CAUTION-
Different
hydraulic
chaintensioners
were
used
duringmanufacture,
depending
onengíne
type
.
See
Fig
.
11
.
Note
that
the
late
style
tensioner
canbe
retrofitted
to
the
earlier
engíne,
so
be
sure
to
identify
the
versíon
of
tensioner
ínstalled
as
ínstal-
lation
instructions
vary
between
the
two
.
7
.
On
M42
engine
:
Disassemble
chain
tensioner
by
strik-
ing
outer
sleeve
against
a
solid
object
.
This
will
release
snap
ring
and
tensioner
will
separate
.
See
Fig
.
12
.
8
.
On
M42
engine
:
Clamp
chain
tensioner
piston
in
vice
(soft
jaws)
.
Slowly
compress
piston,
making
sure
de-
tent
ring
fits
into
taper
of
outer
sleeve
.
If
necessary,
press
ends
of
detent
ring
together
.
Slowly
continueFig
.
9
.
Camshaft
sprockets
correctly
installed
with
arrows
pointing
pressing
tensioner
together
until
snap
ring
audibly
upand
bores
centered
to
tapped
holes
(M44
engine)
.
clicks
into
outer
sleeve
.
Measure
overall
length
of
ten-
sionerto
confirm
correct
assembly
:
68
.5
mm
(2
.7
in
.)
.
3
.
On
M44
engine
:
Place
cylinder
position
sensor
plate
on
intake
camshaft
sprocket
so
that
arrowonsensor
plate
NOTE-
points
up
.
The
¡ate-style
tensioner
on
the
M44
engine
can
be
ret-rofittedto
the
M42
engíne
.
CAMSHAFT
TIMING
CHAIN,
4-CYLINDER
Page 102 of 759
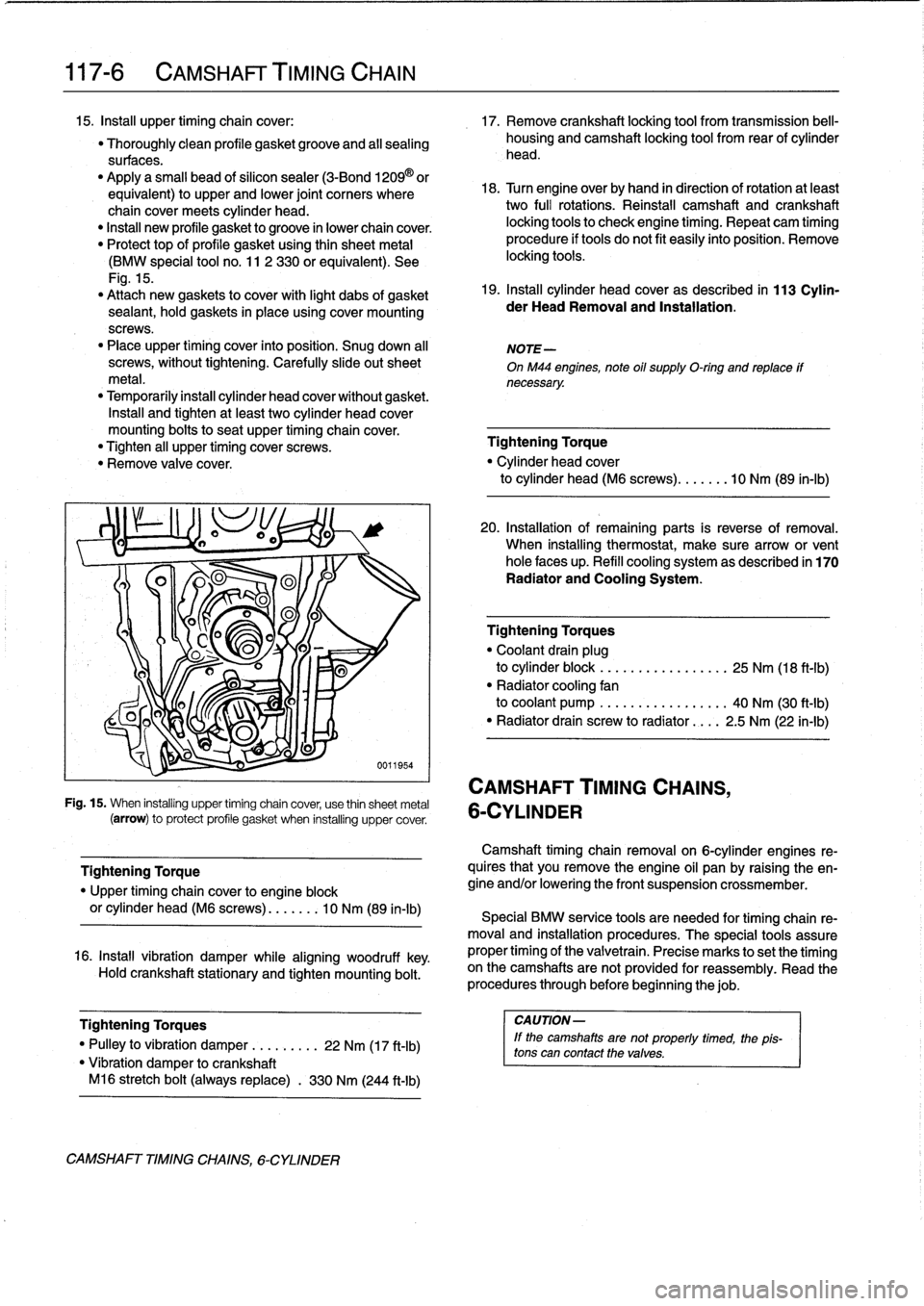
117-
6
CAMSHAFT
TIMING
CHAIN
15
.
Insta¡¡
upper
timing
chaincover
:
17
.
Remove
crankshaft
locking
tool
from
transmission
bell-
"
Thoroughly
clean
profile
gasketgroove
and
all
sealing
housing
and
camshaft
locking
tool
from
rear
of
cylinder
surfaces
.
head
.
"
Applya
small
bead
ofsilicon
sealer
(3-Bond
1209®
or
equivalent)
to
upper
and
lower
joint
comers
where
18
.
Turn
engine
over
by
hand
in
direction
of
rotation
at
least
chaincover
meets
cylinder
head
.
two
full
rotations
.
Reinstall
camshaft
and
crankshaft
"
Insta¡¡
new
profile
gasket
to
groove
in
lowerchain
cover
.
locking
tools
to
check
engine
timing
.
Repeat
cam
timing
"
Protect
top
of
profile
gasket
using
thin
sheetmetal
procedure
if
tools
do
not
fit
easily
into
position
.
Remove
(BMW
special
tool
no
.
11
2
330
or
equivalent)
.
See
locking
tools
.
Fig
.
15
.
"
Attach
new
gaskets
to
cover
with
light
dabs
of
gasket
19
.
Install
cylinder
head
cover
as
described
in
113
Cylin-
sealant,
hold
gaskets
in
placeusing
cover
mounting
der
HeadRemoval
and
Installation
.
screws
.
"
Place
upper
timing
cover
into
position
.
Snug
down
al¡
NOTE-
screws,
without
tightening
.
Carefully
slide
out
sheet
OnM44
engines,
note
oil
supply
O-ring
and
replace
ff
metal
.
necessary
.
"
Temporarily
install
cylinder
head
cover
without
gasket
.
Insta¡¡
and
tighten
at
least
two
cylinder
head
cover
mounting
bolts
to
seat
upper
timing
chaincover
.
"
Tighten
all
upper
timing
cover
screws
.
Tightening
Torque
"
Remove
valve
cover
.
"
Cylinder
head
cover
to
cylinder
head
(M6
screws)
...
..
.
.
10
Nm
(89
ín-Ib)
-
CAMSHAFT
TIMING
CHAINS,
Fig
.
15
.
When
installing
upper
timing
chain
cover,
use
thin
sheetmetal
6-CYLINDER
(arrow)
to
protect
profile
gasket
when
installing
uppercover
.
Tightening
Torque
"
Upper
timing
chaincover
to
engine
block
or
cylinder
head
(M6
screws)
....
.
..
10
Nm
(89
in-lb)
16
.
Install
vibration
damper
while
aligning
woodruff
key
.
Hold
crankshaft
stationary
and
tighten
mounting
bolt
.
Tightening
Torques
I
CAUTION-
"
Pulley
to
vibration
damper
..
.
.
.
....
22
Nm
(17
ft-Ib)
lf
the
camshaftsare
not
properly
timed,
the
1
pis-
tons
can
contact
thevalves
.
"
Vibration
damper
tocrankshaft
M16
stretch
bolt
(always
replace)
.
330
Nm
(244
ft-Ib)
CAMSHAFT
TIMINGCHAINS,
6-CYLINDER
20
.
Installation
of
remaining
parts
is
reverse
of
removal
.
When
installing
thermostat,
make
sure
arrow
or
vent
hole
faces
up
.
Refill
cooling
system
as
described
in
170
Radiator
and
Cooling
System
.
Tighteníng
Torques
"
Coolant
drain
plug
to
cylinder
block
.
..
.
.
.
...
.
..
.....
25
Nm
(18
ft-Ib)
"
Radiator
cooling
fan
to
coolant
pump
.
..
.
...
...
..
.....
40
Nm
(30
ft-Ib)
"
Radiator
drain
screw
to
radiator
....
2
.5
Nm
(22
in-lb)
Camshaft
timing
chainremovalon
6-cylinder
engines
re-
quires
that
you
Rmove
the
engine
oil
pan
by
raising
the
en-
gine
and/or
lowering
the
front
suspension
crossmember
.
Special
BMW
service
tools
are
needed
for
timing
chain
re-
moval
and
installation
procedures
.
The
special
tools
assure
proper
timing
of
the
valvetrain
.
Precise
marks
to
setthe
timing
on
the
camshafts
arenot
provided
for
reassembly
.
Read
the
procedures
through
before
beginning
thejob
.
Page 109 of 759
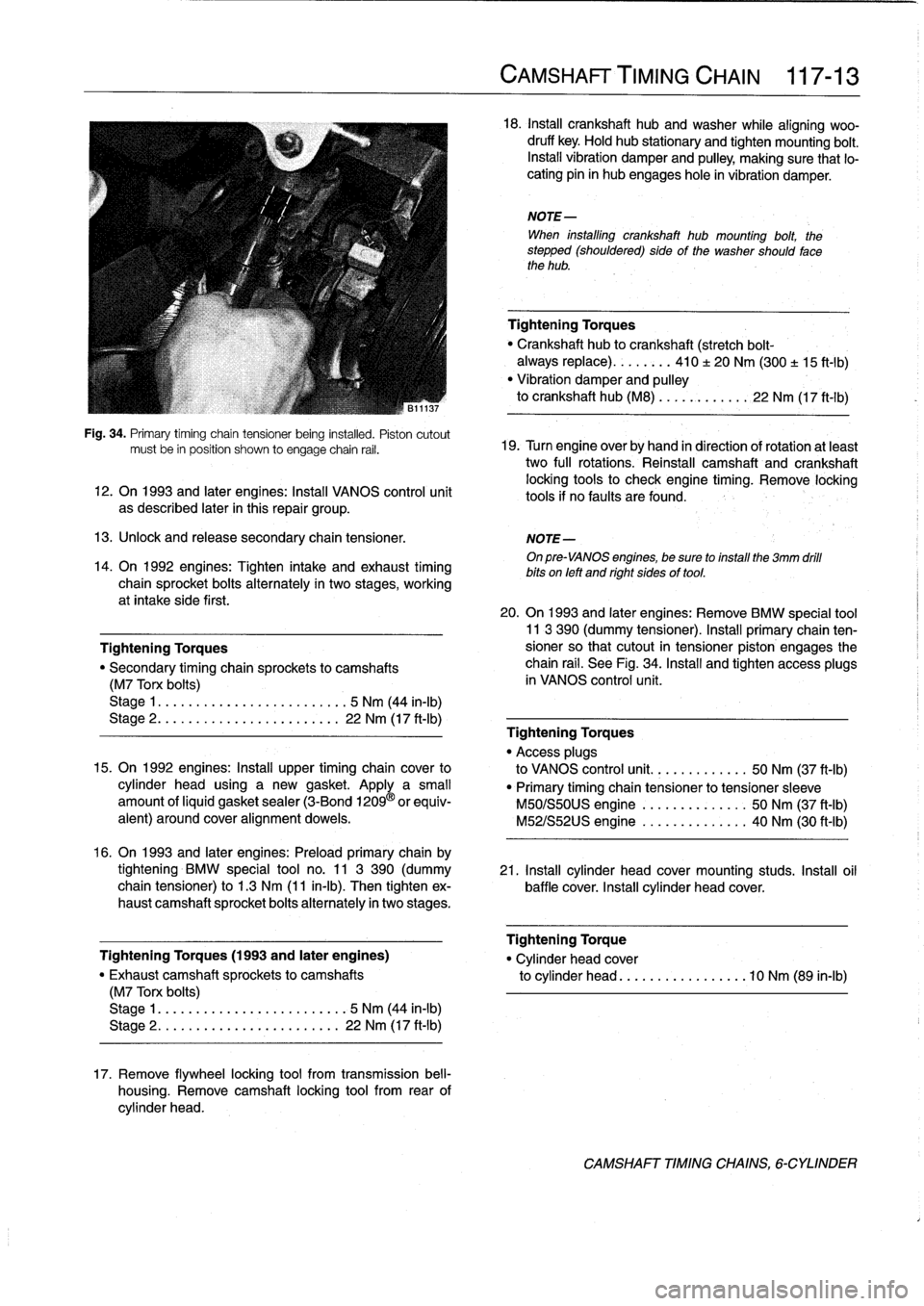
Fig
.
34
.
Primary
timíng
chain
tensioner
being
instafed
.
Pistoncutout
mustbe
in
position
shown
to
engage
chain
rail
.
12
.
On
1993
and
later
engines
:
Install
VANOS
control
unit
as
described
later
in
this
repair
group
.
13
.
Unlock
and
release
secondary
chaintensioner
.
NOTE-
On
pre-VANOS
engines,
be
sure
toinstall
the
3mm
drill
bits
on
left
and
right
sides
of
tool
.
14
.
On
1992
engines
:
Tighten
intake
and
exhaust
timing
chain
sprocket
bolts
alternately
in
two
stages,
working
at
intake
side
first
.
Tightening
Torques
"
Secondary
timing
chaira
sprockets
to
camshafts
(M7
Torx
bolts)
Stage
1
....
.
.
.
...
...............
5
Nm
(44
in-lb)
Stage
2
..
.
.
.
.
.
.
................
22
Nm
(17
ft-Ib)
15
.
On
1992
engines
:
Install
upper
timing
chaincover
to
cylinder
head
using
a
new
gasket
.
Apply
a
small
amount
ofliquid
gasket
sealer
(3-Bond
1209
®
orequiv-
alent)
around
coveralignment
dowels
.
16
.
On
1993
and
later
engines
:
Preloadprimary
chain
by
tightening
BMW
special
tool
no
.
11
3
390
(dummy
21
.
Install
cylinder
head
cover
mounting
studs
.
Insta¡¡
oil
chain
tensioner)
to
1
.3
Nm
(11
in-lb)
.
Then
tighten
ex-
baffle
cover
.
Install
cylinder
head
cover
.
haust
camshaft
sprocket
bolts
alternately
in
twostages
.
Tightening
Torques
(1993
and
later
engines)
"
Exhaust
camshaft
sprockets
to
camshafts
(M7
Torx
bolts)
Stage
1
..
...
..
..
................
5
Nm
(44
in-lb)
Stage
2
.....
.
.
...
..............
22
Nm
(17
ft-Ib)
17
.
Remove
flywheel
locking
tool
from
transmission
bell-
housing
.
Remove
camshaft
locking
tool
from
rear
of
cylinder
head
.
CAMSHAFT'TIMING
CHAIN
117-
1
3
18
.
Insta¡¡
crankshaft
hubandwasher
while
aligning
woo-
druff
key
.
Hold
hub
stationary
and
tighten
mounting
bolt
.
Install
vibration
damper
and
pulley,
making
sure
that
lo-
cating
pin
in
hub
engages
hole
in
vibration
damper
.
NOTE-
When
installing
crankshaft
hub
mounting
bolt,
the
stepped
(shouldered)
sideof
the
washer
should
fase
the
hub
.
Tightening
Torques
Crankshaft
hub
to
crankshaft
(stretch
bolt-
always
replace)
........
410
±
20
Nm
(300
±
15
ft-1b)
"
Vibration
damper
and
pulley
to
crankshaft
hub
(M8)
...
..
.
..
....
22
Nm
(17
ft-Ib)
19
.
Turn
engine
over
by
hand
in
direction
of
rotation
atleast
two
full
rotations
.
Reinstall
camshaft
and
crankshaft
locking
tools
to
check
engine
timing
.
Remove
locking
tools
if
no
faults
are
found
.
20
.
On
1993
and
later
engines
:
Remove
BMW
special
tool11
3
390
(dummy
tensioner)
.
Install
primary
chain
ten-sioner
so
that
cutout
in
tensioner
piston
engages
the
chain
rail
.
See
Fig
.
34
.
Install
and
tighten
access
plugs
in
VANOS
control
unit
.
Tightening
Torques
"
Access
plugs
to
VANOS
control
unit
..........
.
..
50
Nm
(37
ft-Ib)
"
Primary
timing
chain
tensioner
to
tensioner
sleeve
M50/S50US
engine
.......
.
..
..
.
.
50
Nm
(37
ft-Ib)
M52/S52US
engine
..........
..
.
.
40
Nm
(30
ft-Ib)
Tightening
Torque
"
Cylinder
head
cover
to
cylinder
head
............
...
.
.10
Nm
(89
in-lb)
CAMSHAFT
TIMINGCHAINS,
6-CYLINDER