Engine fill system BMW M3 1993 E36 Owner's Manual
[x] Cancel search | Manufacturer: BMW, Model Year: 1993, Model line: M3, Model: BMW M3 1993 E36Pages: 759
Page 193 of 759
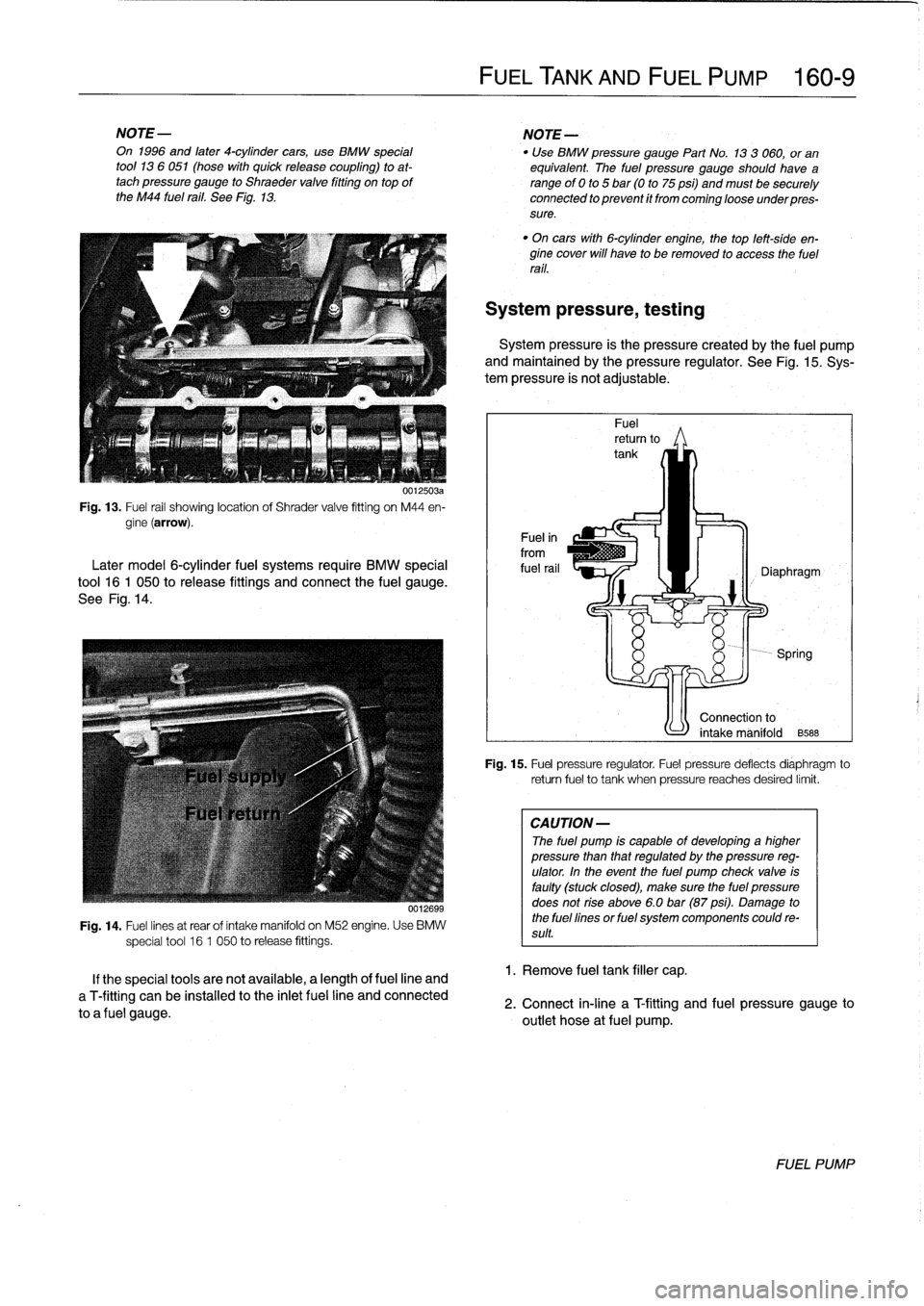
NOTE-
NOTE
-
On
1996
and
later
4-cylinder
cars,
use
BMW
special
"
Use
BMW
pressure
gauge
Part
No
.
133
060,or
an
tool
13
6051
(hose
with
quick
release
coupling)
toat-
equivalent
.
The
fuel
pressure
gauge
should
have
a
tach
pressure
gauge
to
Shraeder
valve
fitting
on
top
of
rangeof
0
to
5bar
(0
to
75
psi)
and
mustbe
securely
the
M44
fuel
rail
.
See
Fig
.
13
.
connected
to
prevent
it
from
coming
loose
under
pres-
sure
.
u012503a
Fig
.
13
.
Fuel
rail
showing
location
of
Shrader
valve
fitting
on
M44
en-
gine
(arrow)
.
Later
model
6-cylinder
fuel
systems
require
BMW
specíal
tool
16
1
050
to
release
fittings
and
connect
the
fuel
gauge
.
See
Fig
.
14
.
0012699
Fig
.
14
.
Fuel
lines
at
rear
of
íntake
manifold
on
M52
engine
.
Use
BMW
special
tool
16
1
050
to
release
fittings
.
If
the
special
tools
arenot
available,
a
length
offuel
line
and
a
T-fitting
can
be
installed
tothe
inlet
fuel
line
and
connected
to
a
fuel
gauge
.
FUEL
TANK
AND
FUEL
PUMP
160-
9
"
On
cars
with
6-cylinder
engine,
thetop
left-side
en-
Bine
cover
will
have
to
be
removed
to
access
the
fuel
rail
.
System
pressure,
testing
System
pressure
is
the
pressure
created
by
the
fuel
pump
and
maintained
by
the
pressure
regulator
.
See
Fig
.
15
.
Sys-
tem
pressure
is
not
adjustable
.
1
.
Remove
fuel
tank
filler
cap
.
Fig
.
15
.
Fuel
pressure
regulator
.
Fuel
pressure
deflects
diaphragm
to
retum
fuel
to
tank
when
pressure
reaches
desired
limit
.
CA
UTION-
The
fuel
pump
is
capable
of
developing
a
higher
pressure
than
that
regulated
by
the
pressure
reg-
ulator
.
In
the
event
the
fuel
pump
check
valve
is
faulty
(stuck
closed),
make
sure
the
fuel
pressure
does
not
rise
aboye
6
.0
bar(87
psi)
.
Damage
to
the
fuel
fines
or
fuel
system
components
could
re-
sult
.
2
.
Connect
in-fine
a
Tfitting
and
fuel
pressure
gauge
to
outlet
hose
atfuel
pump
.
FUEL
PUMP
Page 195 of 759
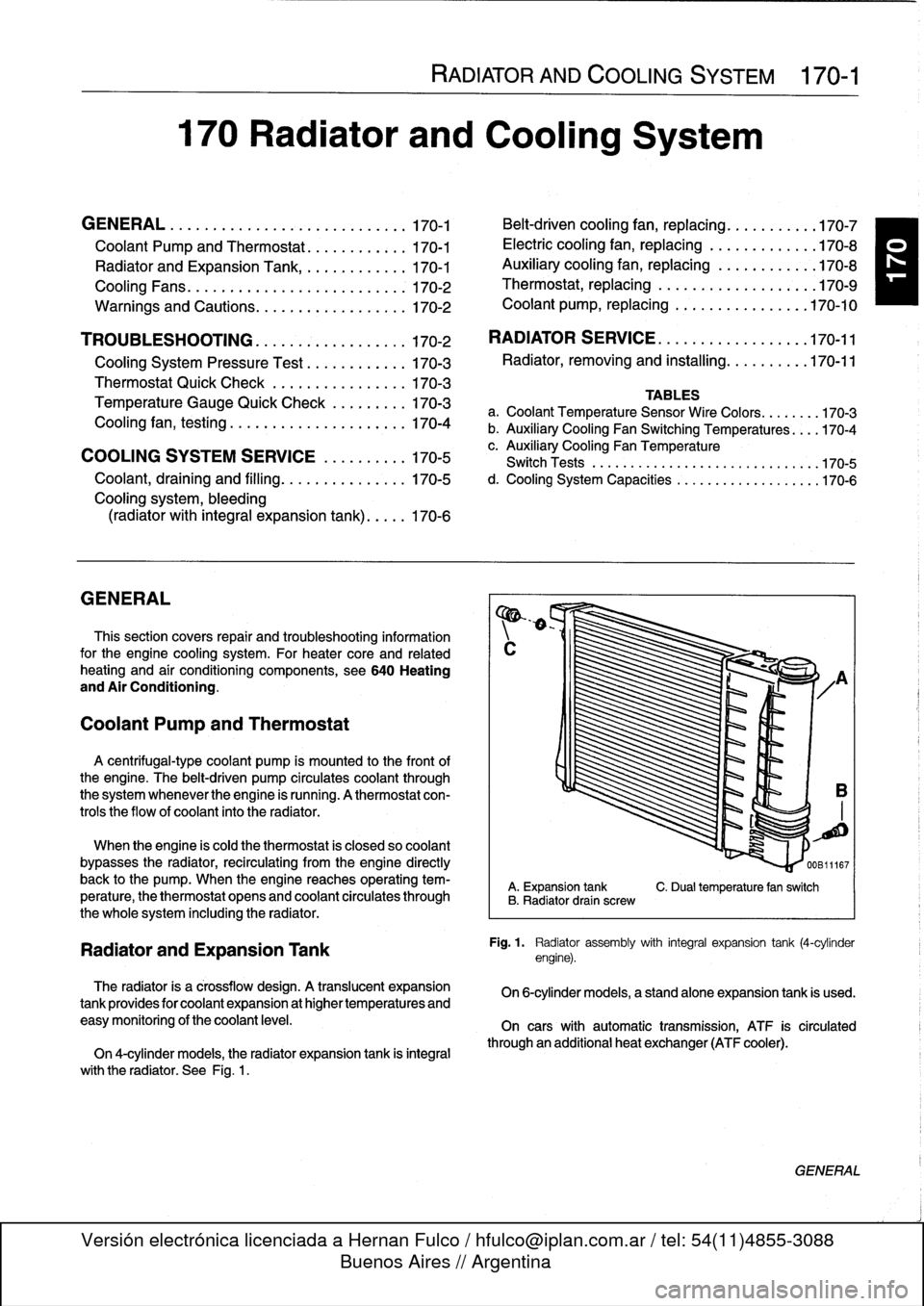
170
Radiator
and
Cooling
System
GENERAL
.
.
.....
.
...
.
.
.
.
.
....
.
.
.
.
.
.
.
.170-1
Coolant
Pump
and
Thermostat
........
.
.
.
.
170-1
Radiator
and
Expansion
Tank
.........
.
...
170-1
Cooling
Fans
.
....
.
.
.
.
.
.
.
.
.
.....
.
......
170-2
Warnings
and
Cautions
.
.
.
.
.
.
.
.
.
.
.
.
...
.
.
.
170-2
TROUBLESHOOTING
...
.
.
.
...
.
.
.
.
.
.
.
.
.170-2
Cooling
System
Pressure
Test
...
.
.
.
.
.
.
.
.
.
170-3
Thermostat
Quick
Check
.
.
.
.
...
.
.
.
.
.
.
.
.
.
170-3
Temperature
Gauge
Quick
Check
.
.
.
.
.
.
.
.
.
170-3
Cooling
fan,
testing
.
.
.
.
........
.
.
.
.
.
.
.
.
.
170-4
COOLING
SYSTEM
SERVICE
.
.
.
.
.
.
.
.
.
.
170-5
Coolant,draining
and
filling
.
.
......
.
.
.
.
.
..
170-5
Cooling
system,
bleeding
(radiator
with
integral
expansion
tank)
.....
170-6
GENERAL
This
section
covers
repair
and
troubleshooting
information
for
the
engine
cooling
system
.
For
heater
core
and
related
heating
and
air
conditioning
components,
see640
Heating
and
Air
Conditioning
.
Coolant
Pump
and
Thermostat
A
centrifuga¡-type
coolant
pump
is
mounted
to
the
front
of
the
engíne
.
The
belt-driven
pump
circulates
coolant
through
the
system
whenever
the
engíne
is
running
.
A
thermostat
con-
trols
the
flow
of
coolant
into
the
radiator
.
When
the
engíne
is
cold
the
thermostat
is
closed
so
coolant
bypasses
the
radiator,
recirculating
from
the
engíne
directly
back
to
the
pump
.
When
the
engíne
reaches
operating
tem-
perature,
the
thermostat
opens
and
coolant
circulates
through
the
whole
system
including
the
radiator
.
Radiator
and
Expansion
Tank
The
radiator
is
a
crossflow
design
.
A
translucent
expansion
tank
provides
for
coolant
expansion
at
higher
temperatures
and
easy
monitoringof
the
coolant
leve¡
.
On
4-cylinder
modeis,
the
radiator
expansion
tank
is
integral
with
the
radiator
.
See
Fig
.
1
.
RADIATOR
AND
COOLING
SYSTEM
170-1
Belt-driven
cooling
fan,
replacing
.
.......
.
.
.
170-7
Electric
cooling
fan,
replacing
.
.
.
.....
.
.
.
.
.
170-8
Auxiliary
cooling
fan,
replacing
.
.
.....
.
.
.
.
.
170-8
Thermostat,
replacing
.
.
.
.
.
.
.
.
.
.....
.
.
.
.
.
170-9
Coolant
pump,
replacing
..........
.
.
.
.
.
.
170-10
RADIATOR
SERVICE
.....
.
......
.
.
.
.
.
.
170-11
Radiator,
removing
and
installing
....
.
.
.
.
.
.
170-11
TABLES
a
.
Coolant
Temperature
Sensor
Wire
Colors
...
.
..
.
.
170-3b
.
Auxiliary
Cooling
Fan
Switching
Temperatures
.:.
.170-4
c
.
Auxiliary
Cooling
Fan
Temperature
Switch
Tests
..
..
.
...
...
.
.............
.
..
.
.
170-5d
.
Cooling
System
Capacities
..............
..
.
.
.
170-6
A
.
Expansion
tank
C
.
Dualtemperature
fan
switch
B
.
Radiator
drain
screw
Fig
.
1
.
Radiator
assembly
with
integral
expansion
tank
(4-cylinder
engine)
.
On
6-cylinder
models,
a
standalone
expansion
tank
is
used
.
On
cars
with
automatic
transmission,
ATF
is
circulated
through
an
additional
heat
exchanger
(ATF
cooler)
.
GENERAL
Page 199 of 759
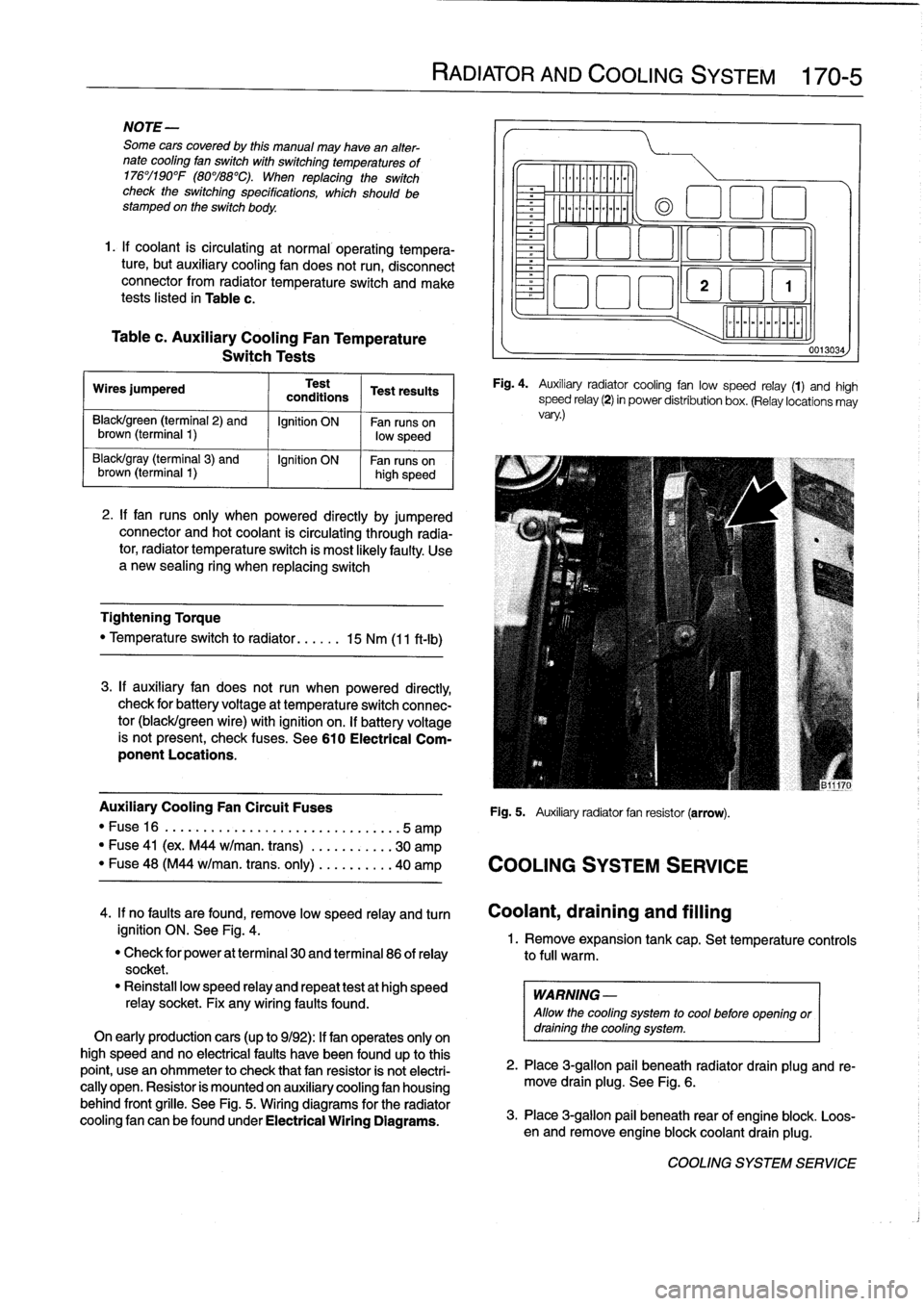
NOTE-
Some
cars
covered
by
this
manual
may
have
an
alter-
nate
cooling
fan
switchwith
switching
temperatures
of
176%190W
(80%88°C)
.
When
replacing
the
switch
check
theswitching
specifications,
whichshouldbe
stamped
on
the
switch
body
.
1
.
If
coolant
is
circulating
at
normal
operating
tempera-
ture,
but
auxiliary
cooling
fan
does
not
run,
disconnect
connector
from
radiator
temperature
switch
and
make
tests
listed
in
Table
c
.
Table
c
.
Auxiliary
Cooling
Fan
Temperature
Switch
Tests
Wires
jumpered
Test
Test
resuits
conditions
Black/green
(terminal2)
and
Ignition
ON
Fan
runs
on
brown
(terminal
1)
low
speed
Black/gray
(terminal
3)
and
Ignition
ON
Fan
runson
brown
(terminal
I
1)
high
speed
2
.
If
fan
runs
only
when
powered
directly
by
jumpered
connector
and
hot
coolant
is
circulating
through
radia-
tor,
radiator
temperature
switch
is
most
likelyfaulty
.
Use
a
new
sealing
ring
when
replacing
switch
Tightening
Torque
"
Temperature
switch
to
radiator
......
15
Nm
(11
ft-Ib)
3
.
If
auxiliary
fan
does
notrun
when
powered
directly,
check
for
battery
voltage
at
temperature
switch
connec-
tor
(black/green
wire)
with
ignition
on
.
If
battery
voltage
is
not
present,
check
fuses
.
See
610
Electrical
Com-
ponent
Locations
.
RADIATOR
AND
COOLING
SYSTEM
170-
5
~r~nmm
a
00
0
Fig
.
4
.
Auxiliary
radiator
cooling
fan
low
speed
relay
(1)
and
high
speed
relay
(2)
in
power
distribution
box
.
(Relay
locations
may
vary
.)
Auxiliary
Cooling
Fan
Circuit
Fuses
Fig
.
5
.
Auxiliary
radiator
fan
resistor
(arrow)
.
"
Fuse16
.
...................
..
..
...
...
.5
amp
"
Fuse
41
(ex
.
M44
w/man
.
trans)
.
..
.
..
.....
30
amp
"
Fuse
48
(M44
w/man
.
trans
.
only)
..
.
..
.....
40
amp
COOLING
SYSTEM
SERVICE
0013034
4
.
If
no
faults
are
found,
remove
low
speed
relay
and
turn
Coolant,draining
and
filling
ignition
ON
.
See
Fig
.
4
.
1
.
Remove
expansion
tank
cap
.
Set
temperature
controls
"
Check
for
power
at
terminal
30
and
terminal
86
of
relay
to
full
warm
.
socket
.
"
Reinstall
low
speed
relay
and
repeat
testat
high
speed
WARNING
-
relay
socket
.
Fix
any
wiring
faults
found
.
Allow
the
cooling
system
to
cool
before
openlng
or
On
early
productioncars
(up
to
9/92)
:
If
fan
operates
only
on
draining
the
cooling
system
.
high
speed
and
no
electrical
faults
have
been
foundup
to
this
point,
usean
ohmmeter
to
check
that
fan
resistor
is
not
electri-
2
.
Place
3
ra
allo
ug
.
beneath
radiator
drain
plug
and
re-
cally
open
.
Resistor
is
mounted
on
auxiliary
cooling
fan
housing
move
drain
plg
.
See
Fig
.
6
.
behind
front
grille
.
See
Fig
.
5
.
Wiring
diagrams
for
the
radiator
cooling
fan
canbefoundunder
Electrical
Wiring
Diagrams
.
3
.
Place
3-g
pail
beneath
rear
of
engine
blo
.
Loos-
en
and
re
mlon
ove
engine
blockcoolant
drain
plug
k
.
COOLING
SYSTEM
SERVICE
Page 200 of 759
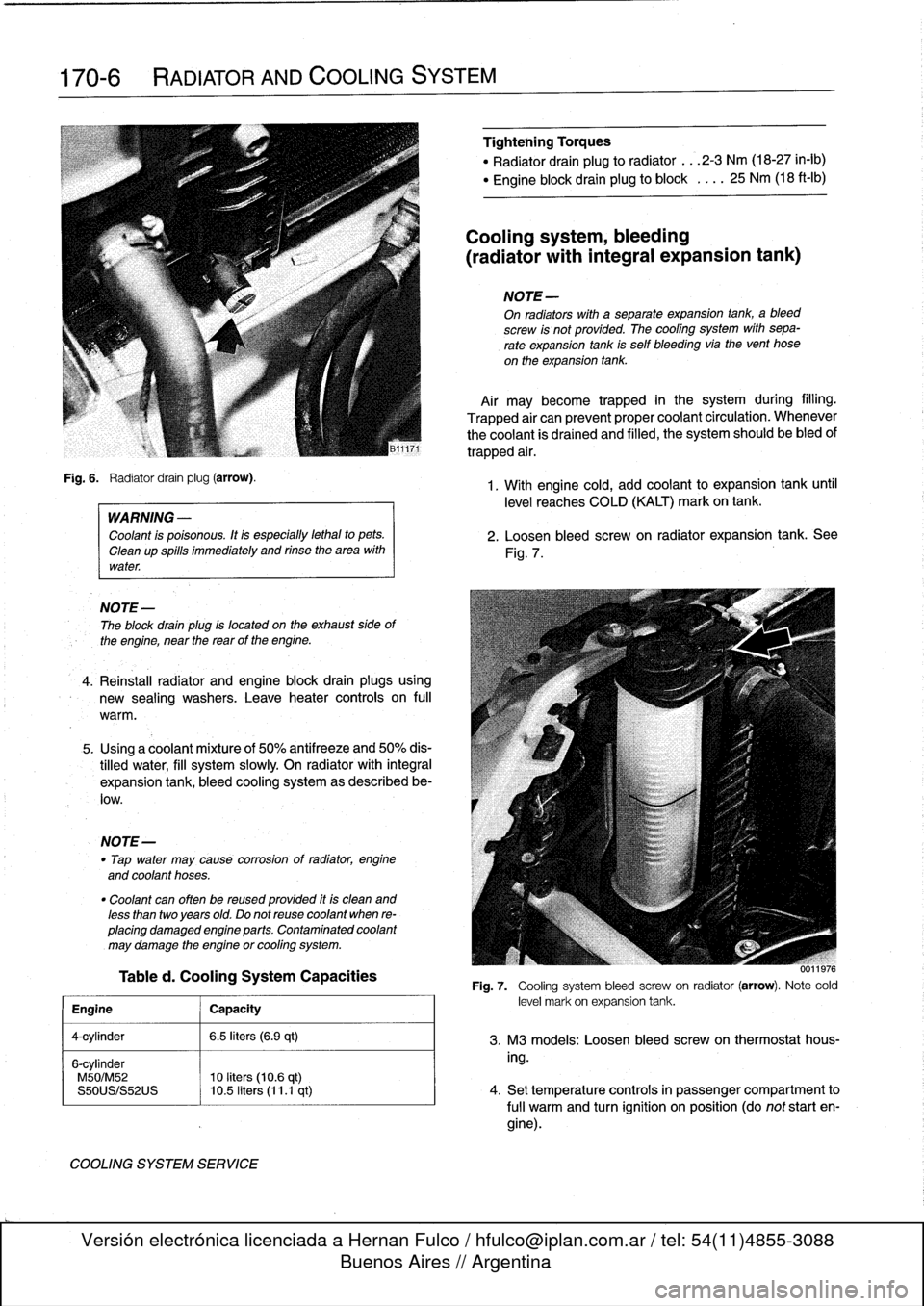
170-6
RADIATOR
AND
COOLING
SYSTEM
Fig
.
6
.
Radiator
drain
plug
(arrow)
.
WARNING
-
Coolant
is
poisonous
.
Itis
especially
lethal
to
pets
.
Cleanup
spills
immediately
and
rinse
the
area
with
water
.
NOTE
-
The
block
drain
plug
is
located
on
the
exhaust
side
of
the
engine,
near
the
reas
of
the
engine
.
4
.
Reinstall
radiator
and
engine
block
drain
plugsusing
new
sealing
washers
.
Leave
heater
controis
on
full
warm
.
5
.
Using
a
coolantmixture
of
50%
antifreeze
and
50%
dis-
tilled
water,
fill
system
slowly
On
radiator
with
integral
expansion
tank,
bleed
cooling
system
as
described
be-
low
.
NOTE-
"
Tap
water
may
cause
corrosion
of
radiator,
engine
and
coolant
hoses
.
"
Coolant
can
often
be
reused
provided
itis
clean
and
less
than
twoyears
old
.
Do
not
reuse
coolant
when
re-
placing
damaged
engine
parts
.
Contaminated
coolant
may
damage
the
engine
or
cooling
system
.
Tabled
.
Cooling
System
Capacities
Engine
j
Capacity
4-cylinder
1
6
.5
liters
(6.9
qt)
6-cylinder
M50/M52
10
liters
(10
.6
qt)
S50US/S52US
10
.5
liters
(11
.1
qt)
COOLING
SYSTEM
SERVICE
Tightehing
Torques
"
Radiator
drain
plug
to
radiator
...
2-3
Nm
(18-27
in-lb)
"
Engine
block
drain
plug
to
block
.
.
..
25
Nm
(18
ft-Ib)
Cooling
system,
bleeding
(radiator
with
integral
expansion
tank)
NOTE
-
On
radiators
with
a
separate
expansion
tank,
ableed
screw
is
not
provided
.
The
cooling
system
with
sepa-
rate
expansion
tank
is
self
bleeding
via
the
vent
hose
on
the
expansion
tank
.
Air
maybecome
trapped
in
the
system
during
filling
.
Trapped
air
can
prevent
proper
coolant
circulation
.
Whenever
the
coolant
is
drained
and
filled,
the
system
should
be
bled
of
trapped
air
.
1
.
With
engine
cold,
add
coolant
to
expansion
tank
until
level
reaches
COLD
(KALT)
mark
on
tank
.
2
.
Loosen
bleed
screw
on
radiator
expansion
tank
.
See
Fig
.
7
.
0011976
Fig
.
7
.
Cooling
system
bleed
screwon
radiator
(arrow)
.
Note
cold
level
mark
on
expansion
tank
.
3
.
M3
models
:
Loosen
bleed
screw
on
thermostathous-
ing
.
4
.
Set
temperature
controls
in
passenger
compartment
to
fui¡
warm
and
turn
ignition
on
position
(do
not
start
en-
gine)
.
Page 203 of 759
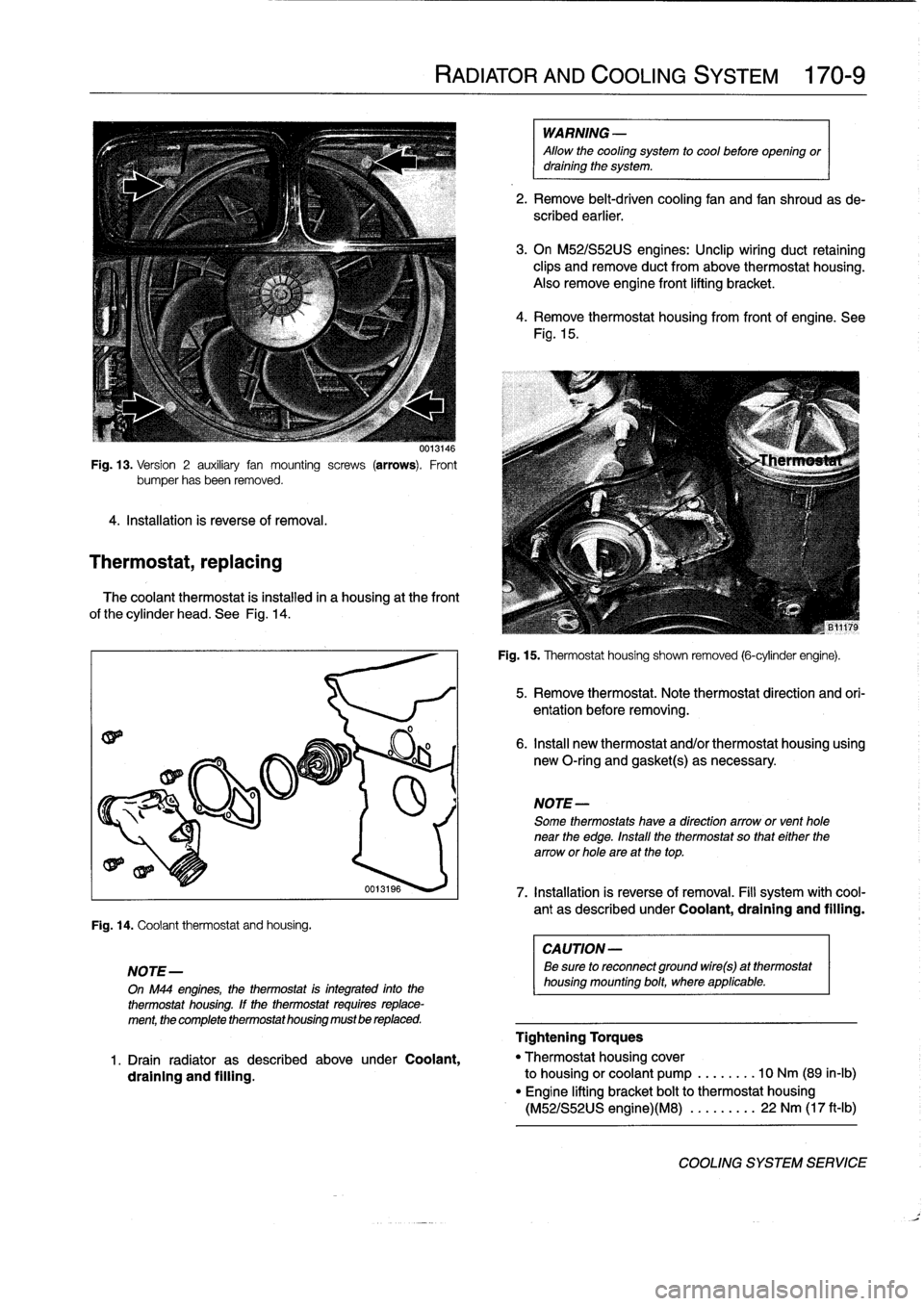
Fig
.
13
.
Version
2
auxiliary
fan
mounting
screws
(arrows)
.
Front
bumper
hasbeen
removed
.
4
.
Installation
is
reverse
of
removal
.
Thermostat,
replacing
0013146
The
coolant
thermostat
is
instalied
in
a
housing
at
the
front
of
the
cylinder
head
.
See
Fig
.
14
.
Fig
.
14
.
Coolantthermostat
and
housíng
.
NOTE-
On
M44
engines,
the
thermostat
is
integrated
into
the
thermostat
housíng
.
If
the
thermostat
requiresreplace-
ment,
the
complete
thermostathousing
mustbe
replaced
.
RADIATOR
AND
COOLING
SYSTEM
170-
9
WARNING
-
Allow
the
cooling
system
to
cool
before
opening
ordraining
the
system
.
2
.
Remove
belt-driven
cooling
fan
and
fan
shroudas
de-
scribed
earlier
.
3
.
On
M52/S52US
engines
:
Unclip
wiring
duct
retaining
clips
and
remove
duct
from
above
thermostat
housing
.
Also
remove
engine
front
lifting
bracket
.
4
.
Remove
thermostat
housing
from
front
of
engine
.
See
Fig
.
15
.
Fig
.
15
.
Thermostat
housíng
shown
removed
(6-cylinder
engine)
.
NOTE-
Some
thermostats
have
a
direction
arrowor
venthole
near
the
edge
.
Install
the
thermostat
so
that
either
the
arrow
or
hole
are
at
thetop
.
CAUTION
-
Be
sure
to
reconnect
ground
wire(s)
at
thermostat
housing
mounting
bolt,
where
applicable
.
5
.
Remove
thermostat
.
Note
thermostat
direction
and
ori-
entation
before
removing
.
6
.
Insta¡¡
new
thermostat
and/or
thermostat
housing
using
new
O-ring
and
gasket(s)
as
necessary
.
oo131ss
7
.
Installation
is
reverseof
removal
.
Fill
system
with
cool-
ant
as
described
under
Coolant,draining
and
filling
.
Tightening
Torques
1
.
Drain
radiator
as
described
above
under
Coolant,
"
Thermostat
housing
cover
draining
and
filling
.
to
housing
orcoolant
pump
..
..
....
10
Nm
(89
in-lb)
"
Engine
lifting
bracket
bolt
to
thermostat
housing
(M52/S52US
engine)(M8)
....
..
...
22
Nm
(17
ft-Ib)
COOLING
SYSTEM
SERVICE
Page 216 of 759
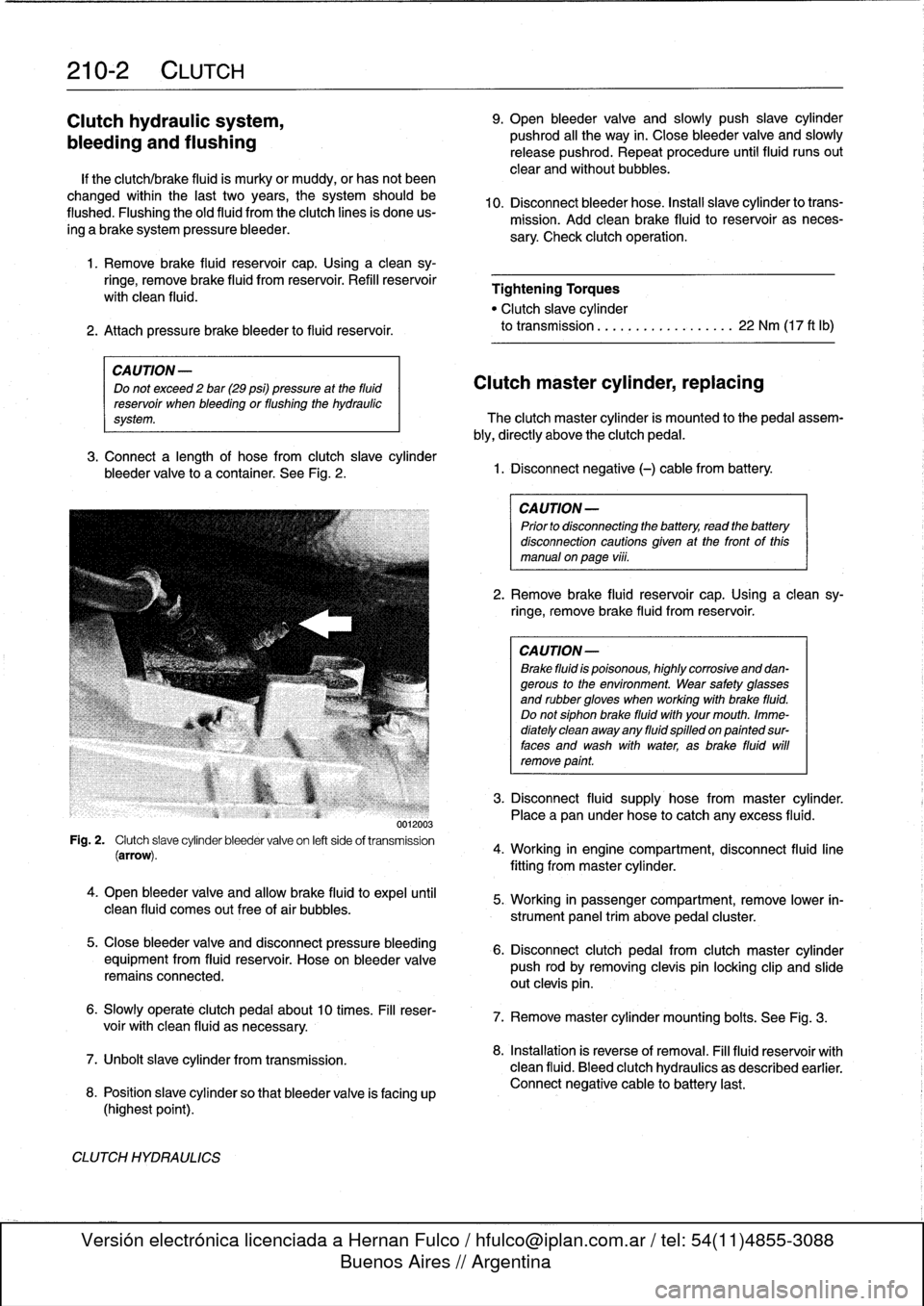
210-2
CLUTCH
Clutch
hydraulic
system,
bleeding
and
flushing
If
the
clutch/brake
fluid
is
murky
or
muddy,
or
has
not
been
changed
within
the
last
two
years,
the
system
should
be
flushed
.
Flushing
the
old
fluid
from
the
clutch
lines
is
done
us-
ing
a
brake
system
pressure
bleeder
.
1
.
Remove
brake
fluíd
reservoir
cap
.
Usinga
clean
sy-
ringe,
remove
brake
fluid
from
reservoir
.
Refill
reservoir
with
clean
fluid
.
2
.
Attach
pressure
brake
bleeder
to
fluid
reservoír
.
CA
UTION-
Do
not
exceed
2
bar
(29
psi)
pressure
at
the
fluid
reservoir
when
bleeding
or
flushing
the
hydraulic
system
.
3
.
Connect
a
length
of
hose
from
clutch
slave
cylinder
bleeder
valve
lo
a
container
.
See
Fig
.
2
.
0012003
Fig
.
2
.
Clutch
slave
cylinder
bleeder
valve
on
left
side
of
transmission
(arrow)
.
4
.
Open
bleeder
valve
and
allow
brake
fluid
to
expel
until
clean
fluid
comes
out
free
of
air
bubbles
.
5
.
Close
bleeder
valve
and
disconnect
pressure
bleeding
equipment
from
fluid
reservoir
.
Hose
on
bleeder
valve
remainsconnected
.
6
.
Slowly
operate
clutch
pedal
about10
times
.
Fill
reser-
voir
with
clean
fluid
asnecessary
.
7
.
Unbolt
slavecylinder
from
transmission
.
8
.
Position
slave
cylinder
so
that
bleeder
valve
is
facing
up
(highest
point)
.
CLUTCH
HYDRAULICS
9
.
Open
bleeder
valve
and
slowly
push
slave
cylinder
pushrod
al¡
the
way
in
.
Close
bleeder
valve
and
slowly
release
pushrod
.
Repeat
procedure
until
fluid
runs
out
clear
and
without
bubbles
.
10
.
Disconnect
bleeder
hose
.
Instan
slavecylinder
lo
trans-
mission
.
Add
cleanbrake
fluid
to
reservoir
as
neces-
sary
.
Check
clutch
operation
.
Tightening
Torques
"
Clutch
slave
cylinder
to
transmission
................
..
22
Nm
(17
ft
lb)
Clutch
master
cylinder,
replacing
The
clutch
master
cylinder
is
mounted
to
the
pedal
assem-
bly,
directly
above
the
clutch
pedal
.
1
.
Disconnect
negative
(-)
cable
from
battery
.
CAUTION-
Prior
to
disconnectiog
the
battery,
read
the
battery
disconnection
cautionsgiven
at
the
front
of
this
manual
on
page
viii
.
2
.
Remove
brake
fluid
reservoir
cap
.
Usinga
clean
sy-
ringe,
remove
brake
fluid
from
reservoir
.
CA
UTION-
Brake
fluid
is
poisonous,
highly
corrosive
and
dan-gerous
to
the
environment
.
Wear
safety
glasses
and
rubbergloves
when
working
with
brake
fluid
.
Do
notsiphonbrake
fluid
with
your
mouth
.
Imme-
diately
clean
away
any
fluid
spilled
on
painted
sur-
faces
and
wash
with
water,
asbrake
fluid
will
remove
point
.
3
.
Disconnect
fluid
supply
hose
from
master
cylinder
.
Placea
pan
under
hose
to
catch
any
excess
fluid
.
4
.
Working
in
engine
compartment,
disconnect
fluid
line
fitting
frommaster
cylinder
.
5
.
Working
in
passenger
compartment,
remove
lower
in-
strument
panel
trim
above
pedal
cluster
.
6
.
Disconnect
clutch
pedal
from
clutch
master
cylinder
push
rod
by
removing
clevis
pin
locking
clip
and
slide
out
clevis
pin
.
7
.
Remove
master
cylinder
mounting
bolts
.
See
Fig
.
3
.
8
.
Installation
is
reverse
of
removal
.
Fill
fluid
reservoir
with
clean
fluid
.
Bleed
clutch
hydraulics
as
described
earlier
.
Connect
negative
cable
to
battery
last
.
Page 267 of 759
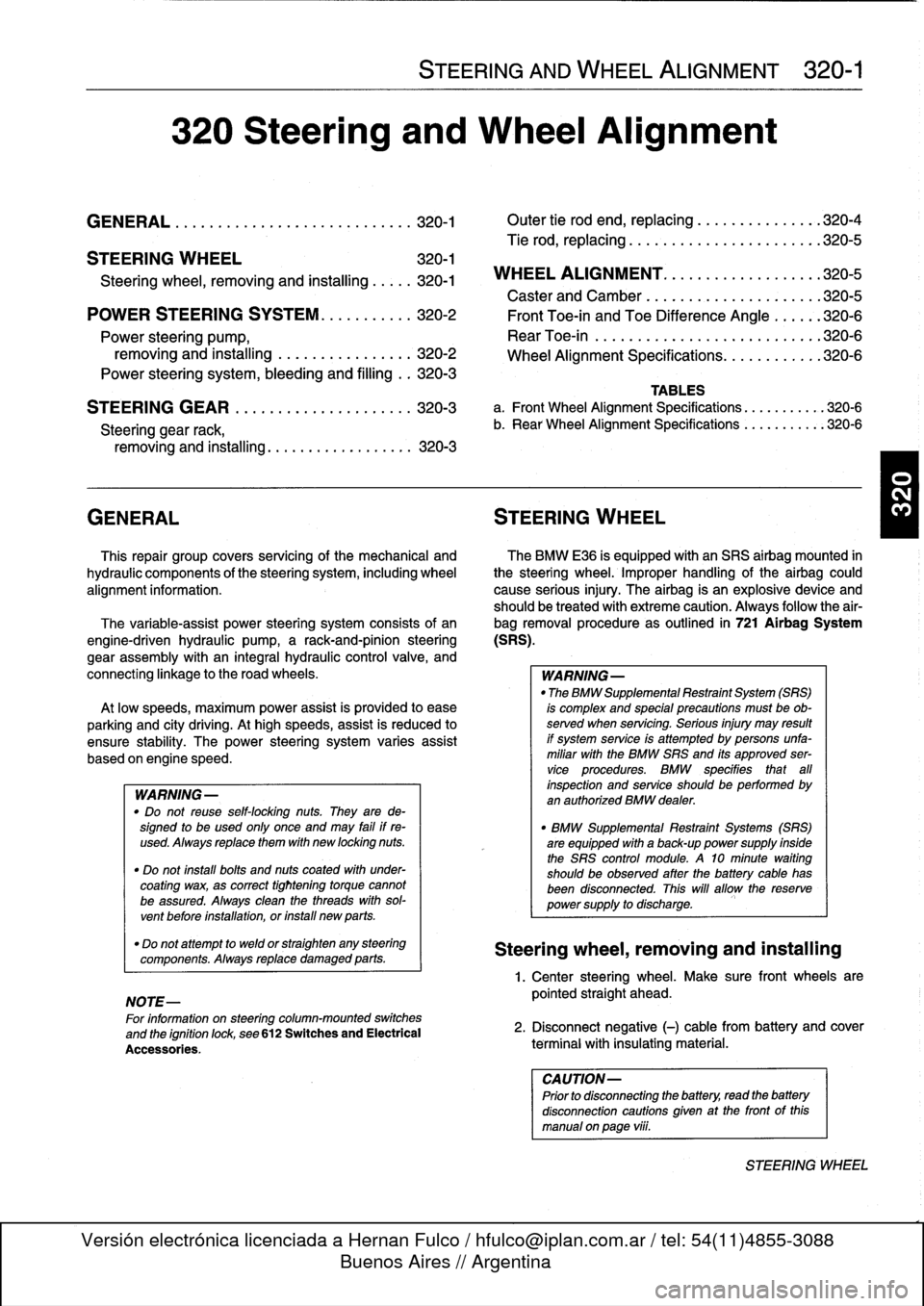
320
Steering
and
Wheel
Alignment
GENERAL
...
.
.
.
...
.
....
.
.
.
.
.
.
.
.
.
...
.
.
320-1
Outer
tie
rod
end,
replacing
.
...
.
.
.
.
.
.
.
...
.
320-4
Tie
rod,
replacing
.
.
.
.
.
.
.
.......
.
.
.
.
.
...
.
320-5
STEERING
WHEEL
320-1
Steering
wheel,
removing
and
installing
.....
320-1
WHEEL
ALIGNMENT
.
.
.
.........
.
.....
.320-5
POWER
STEERING
SYSTEM
.
.
.
.
.
.
.....
320-2
Front
Toe-in
and
Toe
Difference
Angle
.
.
...
.
320-6
Power
steering
pump,
Rear
Toe-in
.
.
.
.
.
.
.
...
.
................
320-6
removing
and
installing
..
.
.
.
.
.
.
.
.
.
.....
320-2
Wheel
Alignment
Specifications
.....
.
......
320-6
Power
steering
system,
bleeding
and
filling
.
.
320-3
STEERING
GEAR
.
.
.
.
...
.
.
.
.
.
.
.
.
.
.....
320-3
Steering
gear
rack,
removing
and
installing
.
...
.
..
.
..
..
..
.
..
.
320-3
GENERAL
STEERING
WHEEL
This
repair
group
covers
servicing
of
the
mechanical
and
The
BMW
E36
is
equipped
with
an
SRS
airbag
mounted
in
hydraulic
components
of
the
steering
system,
including
wheel
the
steering
wheel
.
Improper
handling
of
the
airbag
could
alignment
information
.
cause
serious
injury
.
The
airbag
is
an
explosivedevice
and
should
be
treated
with
extreme
caution
.
Always
follow
the
air-
The
variable-assist
power
steering
system
consistsof
an
bag
removal
procedure
as
outlined
in
721
Airbag
System
engine-driven
hydraulic
pump,
a
rack-and-pinion
steering
(SRS)
.
gear
assembly
with
an
integral
hydraulic
control
valve,
and
connecting
linkage
to
the
road
wheels
.
WARNING-
"
The
BMW
Supplemental
Restraint
System
(SRS)
At
lowspeeds,
maximum
power
assist
is
provided
to
ease
is
complex
and
special
precautions
must
be
ob-
parking
and
city
driving
.
At
high
speeds,
assist
is
reduced
to
served
when
servicing
.
Serious
injury
may
result
ensure
stability
.
The
power
steering
system
varies
assist
if
system
service
is
attempted
by
persons
unfa-
based
on
engine
speed
.
miliar
with
the
BMW
SRS
and
its
approved
ser-
vice
procedures
.
BMW
specifies
that
all
ING-
inspection
and
service
shouldbe
performed
by
WARN
an
authorized
BMW
dealer
.
"
Do
not
reuse
self-locking
nuts
.
They
are
de-signed
to
beused
only
once
and
may
failif
re-
"
BMW
Supplemental
Restraint
Systems
(SRS)
used
.
Always
replace
them
with
new
locking
nuts
.
are
equipped
with
a
back-up
power
supply
inside
the
SRS
control
module
.
A
10minute
waiting
"
Do
not
ínstall
bolts
and
nuts
coated
with
under-
shouldbe
observed
after
the
battery
cable
has
coating
wax,
as
correct
tightening
torque
cannot
been
disconnected
.
This
will
allow
the
reserve
be
assured
.
Always
clean
the
threads
with
sol-
power
supply
to
discharge
.
vent
before
installation,
or
install
new
parts
.
"
Do
not
attempt
to
weldor
straighten
any
steering
components
.
Always
replace
damaged
parts
.
NOTE-
For
information
on
steering
column-mounted
switches
and
the
ignition
lock,
see
612
Switches
and
Electrical
Accessories
.
STEERING
AND
WHEEL
ALIGNMENT
320-1
Caster
and
Camber
.
.
.
.
.
...........
.
....
320-5
TABLES
a
.
Front
Wheel
Alignment
Specifications
.
...
.......
320-6
b
.
Rear
Wheel
Alignment
Specifications
.
...
.......
320-6
Steering
wheel,
removing
and
installing
1
.
Center
steering
wheel
.
Make
sure
front
wheelsare
pointed
straight
ahead
.
2
.
Disconnect
negative
(-)
cable
from
battery
and
cover
terminal
with
insulating
material
.
CAUTION-
Prior
to
disconnectiog
the
battery,
read
the
battery
disconnection
cautions
given
at
the
front
of
this
manual
on
page
viii
.
STEERING
WHEEL
Page 269 of 759
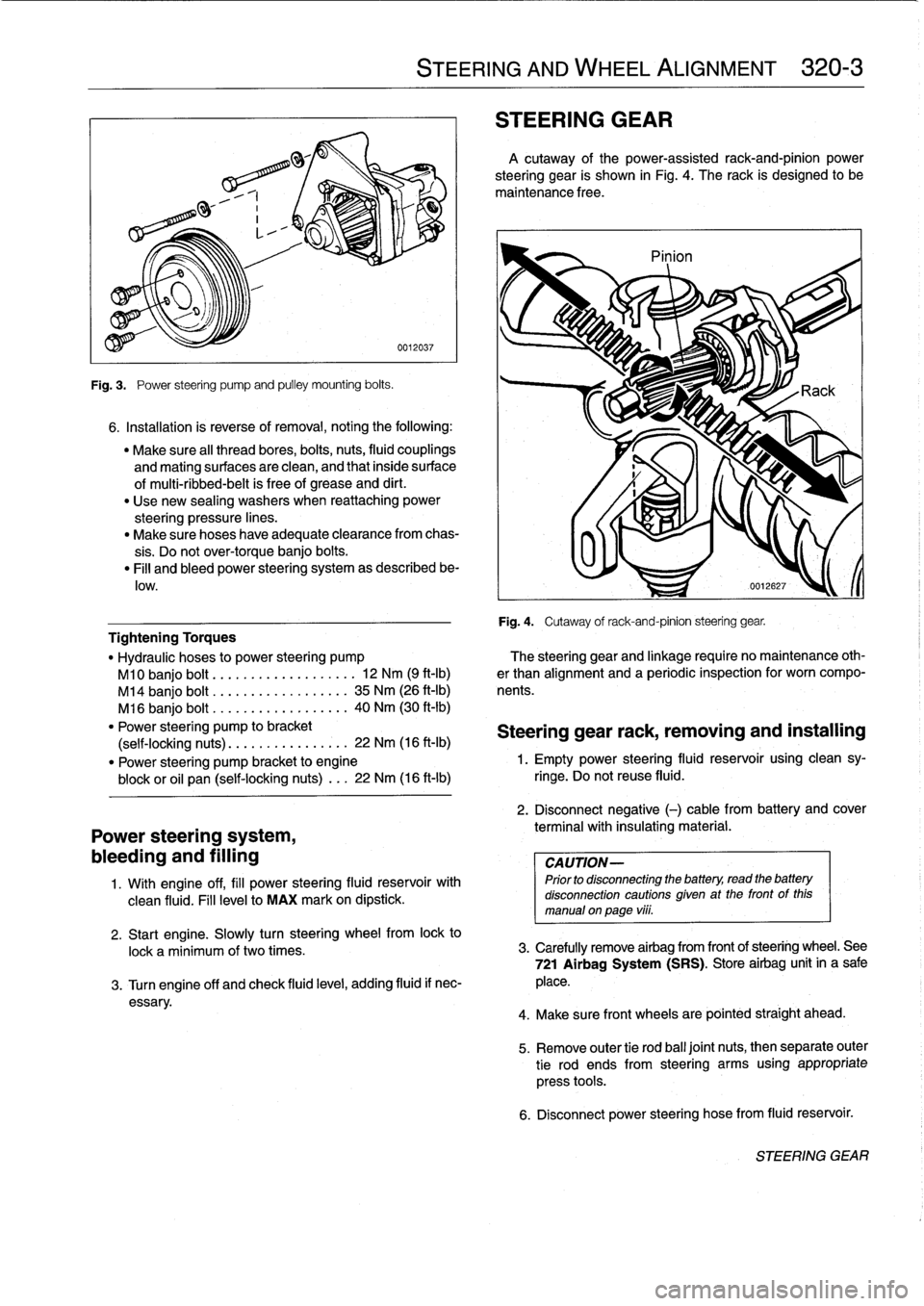
Fig
.
3
.
Power
steering
pump
and
pulley
mounting
bolts
.
6
.
Installation
is
reverse
of
removal,
noting
the
following
:
"
Make
sure
al¡
thread
bores,
bolts,
nuts,
fluid
couplings
and
mating
surfaces
are
clean,
and
that
inside
surface
of
multi-ribbed-belt
is
free
of
grease
and
dirt
.
"
Use
new
sealing
washers
when
reattaching
power
steering
pressure
lines
.
"
Make
sure
hoses
have
adequate
clearance
from
chas-
sis
.
Do
not
over-torque
banjo
bolts
.
"
Fill
and
bleed
power
steering
system
as
described
be-
low
.
Power
steering
system,
bleeding
and
filling
1
.
Wíth
engine
off,
fill
power
steering
fluid
reservoir
with
clean
fluid
.
Fill
levelto
MAX
mark
on
dipstick
.
STEERING
AND
WHEEL
ALIGNMENT
320-
3
STEERING
GEAR
A
cutaway
of
the
power-assisted
rack-and-pinion
power
steering
gear
is
shown
in
Fig
.
4
.
The
rack
is
designed
to
be
maintenance
free
.
Pinion
Fig
.
4
.
Cutaway
of
rack-and-pinion
steering
gear
.
Tightening
Torques
"
Hydraulic
hoses
to
power
steering
pump
?he
steering
gear
and
linkage
require
no
maintenance
oth-
M10
banjo
bolt
.........
..
.
...
...
.
12
Nm
(9
ft-Ib)
er
than
alignment
and
a
periodic
inspection
for
worn
compo
M14
banjo
bolt
..............
..
..
35
Nm
(26
ft-Ib)
nents
.
M16
banjo
bolt
..............
...
.
40
Nm
(30
ft-Ib)
"
Power
steering
pump
to
bracket
Steering
gear
rack,
removing
and
installing
(self-locking
nuts)
.............
..
.
22
Nm
(16
ft-Ib)
"
Power
steering
pump
bracket
to
engine
1
.
Empty
power
steering
fluid
reservoir
using
clean
sy-
block
or
oil
pan
(self-locking
nuts)
...
22
Nm
(16
ft-lb)
ringe
.
Do
not
reuse
fluid
.
2
.
Disconnect
negative
(-)
cable
from
battery
and
cover
terminal
with
insulating
material
.
CAUTION-
Prior
to
disconnectiog
the
battery,
read
the
battery
disconnection
cautions
given
at
the
front
of
this
manual
on
page
viii
.
2
.
Start
engine
.
Slowly
turn
steering
wheelfrom
lock
to
lock
a
minimum
of
two
times
.
3
.
Carefully
remove
airbag
from
frontof
steering
wheel
.
See
721
Airbag
System
(SRS)
.
Store
airbag
unit
in
a
sale
3
.
Turn
engine
off
and
check
fluid
leve¡,
adding
fluid
if
nec-
place
.
essary
.
4
.
Make
sure
front
wheelsare
pointed
straight
ahead
.
5
.
Remove
outer
tie
rod
ball
joínt
nuts,
thenseparate
outer
tie
rod
ends
from
steering
arms
using
appropriate
press
tools
.
6
.
Disconnect
power
steering
hose
from
fluid
reservoir
.
STEERING
GEAR
Page 399 of 759
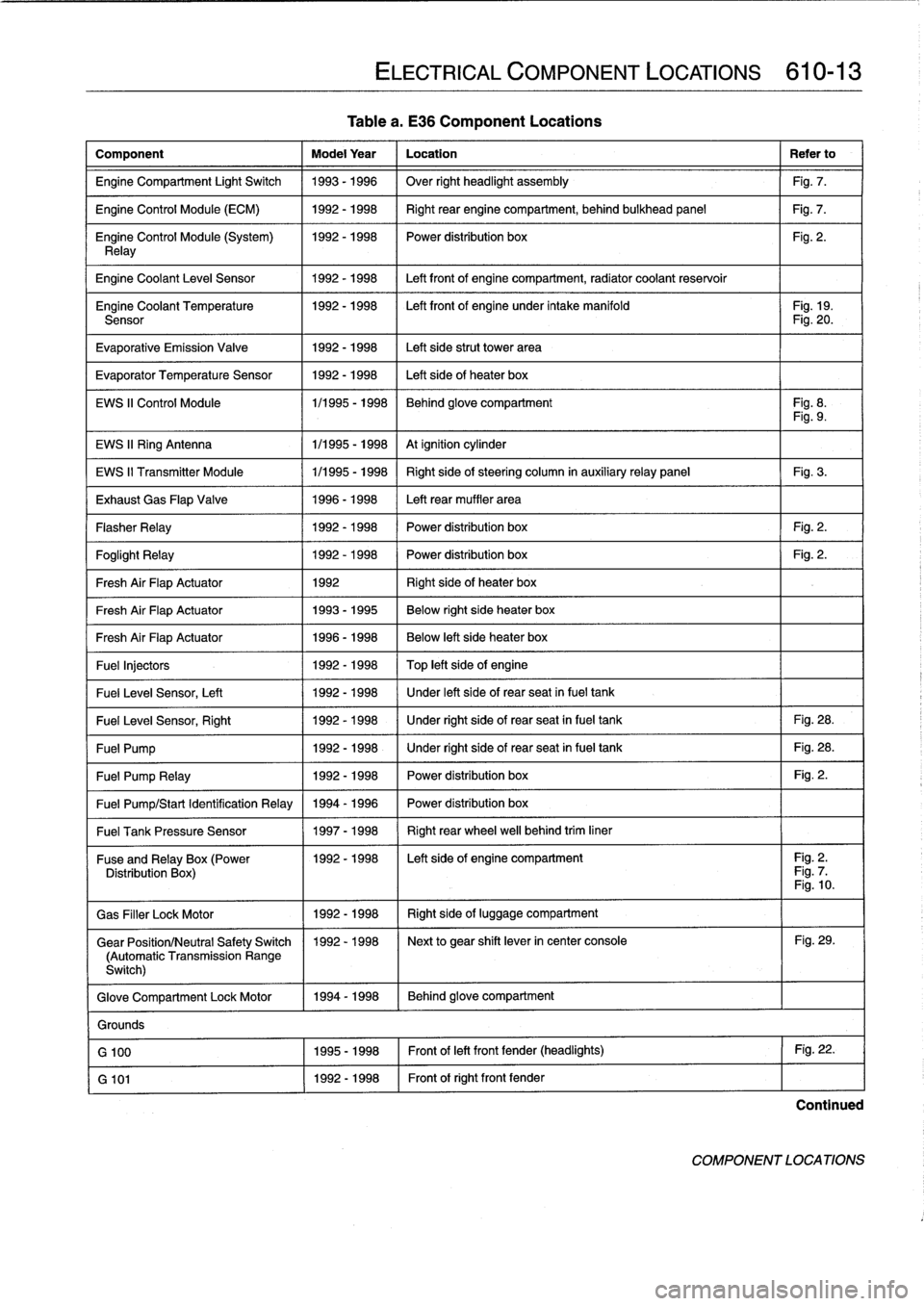
Tablea
.
E36
Component
Locations
Component
Model
Year
Location
Refer
to
Engine
Compartment
Light
Switch
1993-1996
Over
right
headlight
assembly
Fig
.
7
.
Engine
Control
Module
(ECM)
1992-1998
Right
rear
enginecompartment,
behind
bulkhead
panel
Fig
.
7
.
Engine
Control
Module
(System)
1992-1998
I
Power
distribution
box
Fig
.
2
.
Relay
Engine
Coolant
Leve¡
Sensor
1
1992-1998
1
Left
front
of
enginecompartment,
radiator
coolant
reservoir
Engine
Coolant
Temperature
1992-1998
I
Left
front
of
engine
under
intake
manifold
I
Fig
.
19
.
Sensor
Fig
.
20
.
Evaporative
Emission
Valve
1992-1998
Left
side
strut
Power
area
Evaporator
Temperature
Sensor
1992-1998
Left
side
of
heater
box
EWS
II
Control
Module
1/1995
-
1998
Behind
glove
compartment
Fig
.
8
.
Fig
.
9
.
EWS
II
Ring
Antenna
1
1/1995
-
1998
1
At
ignition
cylinder
EWS
II
Transmitter
Module
1/1995
-
1998
Right
side
of
steering
column
in
auxiliaryrelay
panel
Fig
.
3
.
Exhaust
Gas
Flap
Valve
1996-1998
Left
rear
muffler
area
Flasher
Relay
1992-1998
Power
distribution
box
Fig
.
2
.
Foglight
Relay
1
1992-1998
1
Power
distribution
box
1
Fig
.
2
.
Fresh
Air
FlapActuator
1
1992
1
Right
side
of
heater
box
Fresh
Air
FlapActuator
1
1993-1995
1
Below
right
side
heater
box
Fresh
Air
FlapActuator
1
1996-1998
Below
left
side
heater
box
Fuel
Injectors
1992
-
1998
Top
left
side
of
engine
Fuel
Leve¡
Sensor,
Left
1
1992-1998
/
Under
left
side
of
rear
seat
infuel
tank
Fuel
Leve¡
Sensor,
Right
1
1992-1998
1
Under
right
side
of
rear
seat
in
fuel
tank
1
Fig
.
28
.
Fuel
Pump
1
1992-1998
1
Under
right
side
of
rear
seat
in
fuel
tank
1
Fig
.
28
.
Fuel
Pump
Relay
1
1992-1998
1
Power
distribution
box
1
Fig
.
2
.
Fuel
Pump/Start
Identification
Relay
1994
-
1996
Power
distribution
box
Fuel
Tank
Pressure
Sensor
1
1997-1998
1
Right
rear
wheel
well
behind
trim
liner
ELECTRICAL
COMPONENT
LOCATIONS
610-13
Fuse
andRelay
x(Power
11992-1998
I
Left
side
of
engine
compartment
I
Fig
.
2
.
Distribution
Box
Fig
.
7
Fig
.
10
.
Gas
Filler
LockMotor
1992-1998
Right
side
of
luggage
compartment
Gear
Position/Neutral
Safety
Switch
1992-1998
Next
to
gear
shift
lever
in
center
console
Fig
.
29
.
(Automatic
Transmission
Range
Switch)
Glove
Compartment
Lock
Motor
1994-1998
Behind
glove
compartment
Grounds
G
100
1995-1998
Front
of
left
front
fender
(headlights)
Fig
.
22
.
G
101
1992-1998
Front
of
right
front
fender
Continued
COMPONENT
LOCATIONS
Page 750 of 759
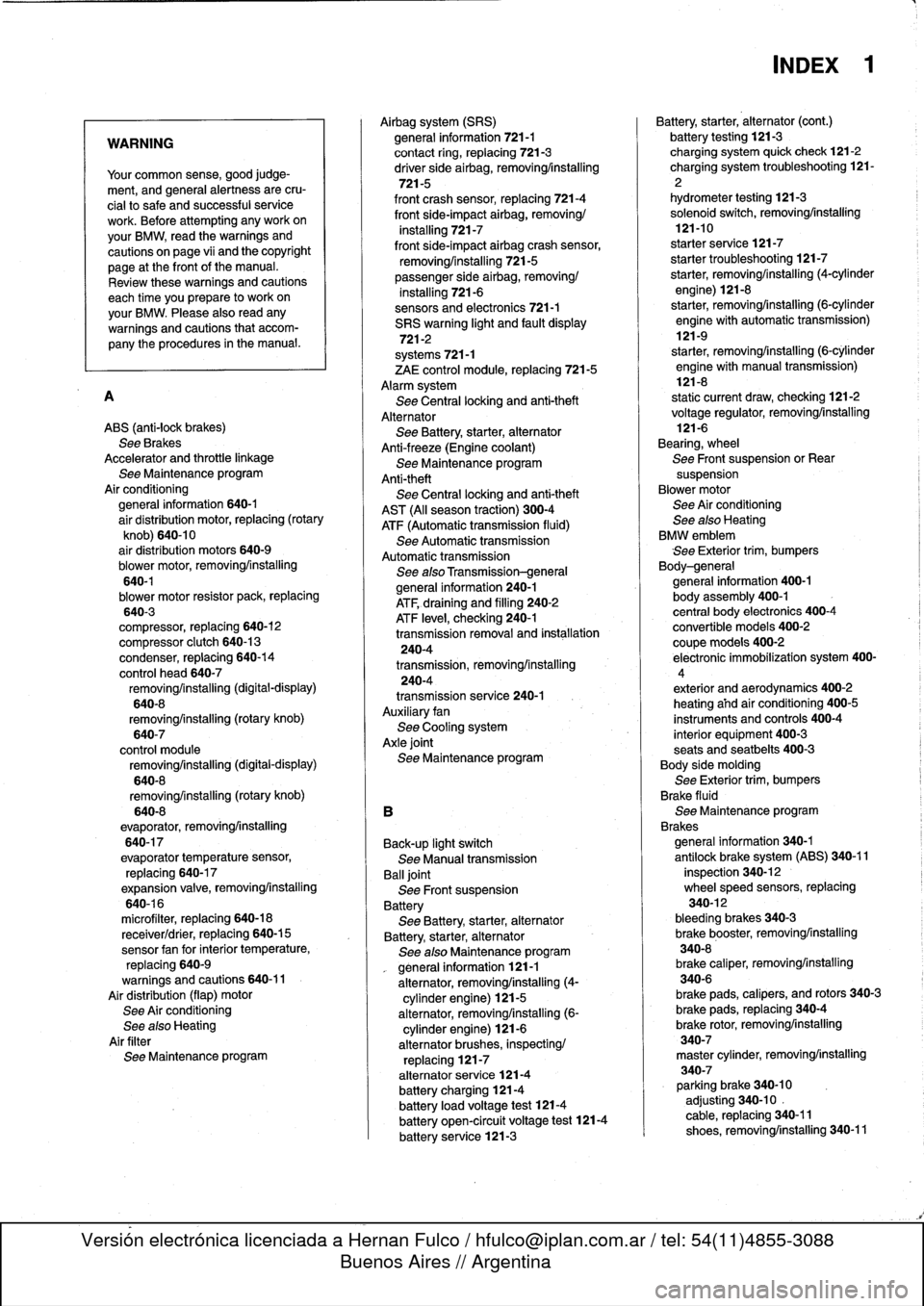
WARNING
Your
common
sense,
good
judge-
ment,
and
general
alertness
are
cru-
cial
to
safe
and
successful
service
work
.
Before
attempting
any
work
on
your
BMW,
read
the
warnings
and
cautions
on
page
vi¡
and
the
copyright
page
at
the
front
of
the
manual
.
Review
these
warnings
and
cautions
each
time
youprepare
to
work
on
your
BMW
.
Please
also
read
any
warnings
and
cautions
that
accom-
pany
the
procedures
in
the
manual
.
A
ABS
(anti-lock
brakes)
See
Brakes
Accelerator
and
throttle
linkage
See
Maintenance
program
Air
conditioning
general
information
640-1
air
distribution
motor,
replacing
(rotary
knob)
640-10
air
distribution
motors
640-9
blower
motor,
removing/installing
640-1blower
motor
resistor
pack,
replacing
640-3
compressor,
replacing
640-12
compressor
clutch
640-13
condenser,
replacing
640-14
control
head
640-7
removing/installing
(digital
-display)
640-8
removing/installing
(rotary
knob)
640-7
control
module
removing/installing
(digital-display)
640-8
removing/installing
(rotary
knob)
640-8
evaporator,
removinglinstalling
640-17
evaporator
temperature
sensor,
replacing
640-17
expansion
valve,
removing/installing
640-16
microfilter,
replacing
640-18
receiverldrier,
replacing
640-15
sensor
fan
forinterior
temperature,
replacing
640-9
warnings
and
cautions
640-11
Air
distribution
(flap)
motor
See
Air
conditioning
See
also
Heating
Air
filter
See
Maintenanceprogram
Airbag
system
(SRS)
general
information
721-1
contact
ring,
replacing
721-3
driver
side
airbag,removing/installing
721-5
front
crash
sensor,
replacing
721-4
front
side-impact
airbag,
removing/
installing
721-7
front
side-impact
airbag
crash
sensor,
removing/installing
721-5
passenger
side
airbag,
removing/
installing
721-6
sensors
and
electronics
721-1
SRS
warning
light
and
fault
display
721-2
systems
721-1
ZAE
control
module,
replacing
721-5
Alarm
system
See
Central
locking
and
anti-theft
Alternator
See
Battery,
starter,
alternator
Anti-freeze
(Engine
coolant)
See
Maintenance
program
Anti-theft
See
Central
lockíng
and
anti-theft
AST
(Al¡
season
traction)
300-4
ATF
(Automatic
transmission
fluid)
See
Automatic
transmission
Automatic
transmission
See
alsoTransmission-general
general
information
240-1
ATF,draining
and
filling
240-2
ATF
leve¡,
checking
240-1
transmission
removaland
ínstallation
240-4
transmission,
removinglinstalling
240-4
transmission
service
240-1
Auxiliary
fan
See
Cooling
system
Axle
joint
See
Maintenance
program
B
Back-up
light
switch
See
Manual
transmission
Balljoint
See
Front
suspension
Battery
See
Battery,
starter,
alternator
Battery,
starter,
alternator
See
also
Maintenance
program
general
information
121-1
alternator,
removing/installing
(4-
cylinder
engine)
121-5
alternator,
removinglinstalling
(6-
cylinder
engine)
121-6
alternator
brushes,
inspecting/
replacing
121-7
alternator
service
121-4
batterycharging
121-4
battery
load
voltage
test
121-4
batteryopen-circuit
voltage
test
121-4
battery
service
121-3
INDEX
1
Battery,
starter,
alternator
(cont
.)
battery
testing
121-3
charging
system
quick
check121-2
charging
system
troubleshooting
121-
2
hydrometer
testing
121-3
solenoid
switch,
removinglinstalling
121-10
starter
service
121-7
starter
troubleshooting
121-7
starter,
removing/installing(4-cylinder
engine)
121-8
starter,
removing/installing(6-cylinder
engine
with
automatic
transmission)
121-9
starter,
removing/installing
(6-cylinder
engine
with
manual
transmission)
121-8
static
current
draw,
checking
121-2
voltage
regulator,
removing/installing
121-6
Bearing,
wheel
See
Front
suspension
or
Rear
suspension
Blowermotor
See
Air
conditioning
See
also
Heatíng
BMW
emblem
See
Exterior
trim,
bumpers
Body-general
general
information
400-1
body
assembly
400-1
central
body
electronics
400-4
convertible
models
400-2
coupe
models
400-2
electronic
immobilizatíon
system
400-
4
exterior
and
aerodynamics
400-2
heating
afhdair
conditioning
400-5
instruments
and
controls
400-4
interior
equipment
400-3
seats
and
seatbelts
400-3
Body
side
molding
See
Exterior
trim,
bumpers
Brake
fluid
See
Maintenance
program
Brakes
general
information
340-1
antilock
brake
system
(ABS)
340-11
inspection
340-12
wheelspeed
sensors,
replacing
340-12
bleeding
brakes
340-3
brake
booster,
removinglinstalling
340-8
brake
caliper,
removing/installing
340-6
brake
pads,
calipers,
and
rotors
340-3
brake
pads,
replacing
340-4
brake
rotor,
removing/installing
340-7
master
cylinder,
removing/installing
340-7
parking
brake
340-10
adjusting
340-10
.
cable,
replacing
340-11
shoes,
removinglinstalling
340-11