tow bar BMW M3 1995 E36 Workshop Manual
[x] Cancel search | Manufacturer: BMW, Model Year: 1995, Model line: M3, Model: BMW M3 1995 E36Pages: 759
Page 69 of 759
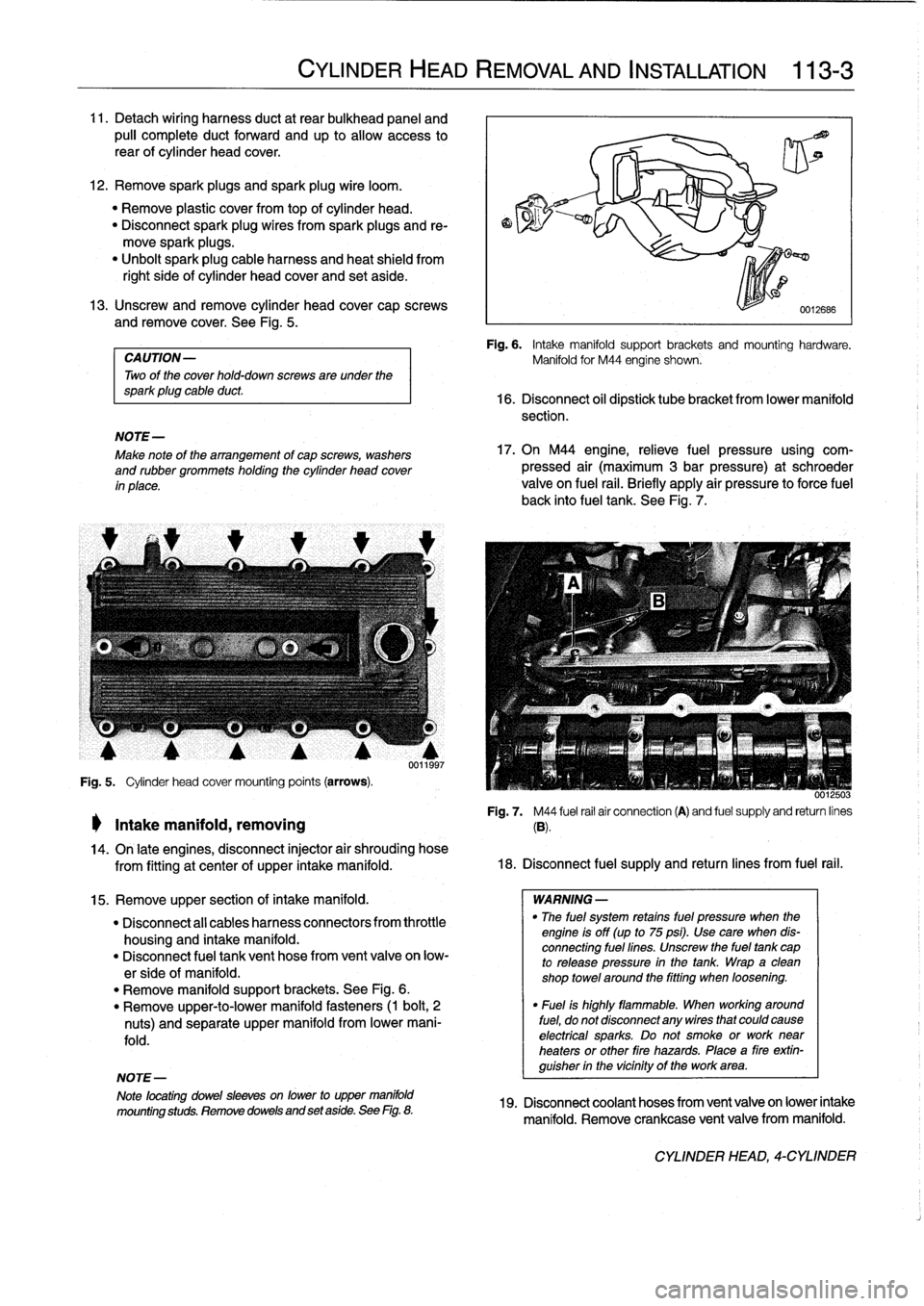
11
.
Detach
wiring
harness
duct
at
rear
bulkhead
panel
and
pull
complete
duct
forward
and
up
to
allow
access
to
rear
of
cylinder
head
cover
.
12
.
Remove
spark
plugs
and
spark
plugwire
loom
.
"
Remove
plastic
cover
from
top
of
cylinder
head
.
"
Disconnect
spark
plug
wires
fromspark
plugs
and
re-
move
spark
plugs
.
"
Unbolt
spark
plug
cable
harness
and
heat
shield
from
right
side
of
cylinder
head
cover
and
set
aside
.
13
.
Unscrew
andremove
cylinder
head
cover
cap
screws
and
remove
cover
.
See
Fig
.
5
.
CAUTION-
Two
of
the
cover
hold-down
screws
are
under
the
spark
plug
cable
duct
.
NOTE-
Make
note
of
the
arrangement
of
cap
screws,
washers
and
rubber
grommets
holding
the
cylinder
head
cover
in
place
.
Fig
.
5
.
Cylinder
head
cover
mounting
points
(arrows)
.
Fig
.
7
.
M44
fuel
rail
air
connection
(A)
and
fuel
supply
and
return
lines
Intake
manifold,
removing
(B)
.
14
.
On
late
engines,
disconnect
injector
air
shrouding
hose
from
fitting
at
center
of
upper
intake
manifold
.
18
.
Disconnect
fuel
supply
and
return
lines
from
fuel
rail
.
15
.
Remove
upper
section
of
intake
manifold
.
"
Disconnect
ali
cables
harness
connectors
from
throttle
housing
and
intake
manifold
.
"
Disconnect
fuel
tank
vent
hose
fromvent
valve
on
low-
er
sitie
of
manifold
.
"
Remove
manifold
support
brackets
.
See
Fig
.
6
.
"
Remove
upper-to-lower
manifold
fasteners
(1
bolt,
2
nuts)
and
separate
upper
manifold
from
lowermani-
fold
.
Note
locating
dowei
sleeves
on
lower
to
upper
manifold
mounting
studs
.
Remove
dowels
and
set
aside
.
See
Fig
.
8
.
CYLINDER
HEAD
REMOVAL
AND
INSTALLATION
113-3
0012686
Fig
.
6
.
Intake
manifold
support
brackets
and
mountinghardware
.
Manifold
for
M44
engine
shows
.
16
.
Disconnect
oil
dipstick
tube
bracket
from
lower
manifold
section
.
17
.
On
M44
engine,
relieve
fuel
pressure
using
com-
pressed
air
(maximum
3
bar
pressure)
at
schroeder
valve
on
fuel
rail
.
Briefly
apply
air
pressure
to
force
fuel
back
intofuel
tank
.
See
Fig
.
7
.
WARNING
-
"
The
fuel
system
retains
fuel
pressure
when
the
engine
is
off
(up
to
75
psi)
.
Use
care
when
dis-
connecting
fuel
lines
.
Unscrew
the
fuel
tank
cap
to
retease
pressure
in
the
tank
.
Wrap
a
clean
shop
towel
around
the
fitting
when
loosening
.
"
Fuel
is
highly
flammable
.
When
working
around
fuel,
do
not
disconnect
any
wires
that
could
cause
electrical
sparks
.
Do
not
smoke
or
worknear
heaters
or
other
tire
hazards
.
Placea
tire
extin-
guisher
in
the
vicinity
of
the
work
area
.
19
.
Disconnect
coolant
hoses
from
vent
valve
on
lower
intake
manifold
.
Remove
crankcase
vent
valve
from
manifold
.
CYLINDER
HEAD,
4-CYLINDER
Page 156 of 759
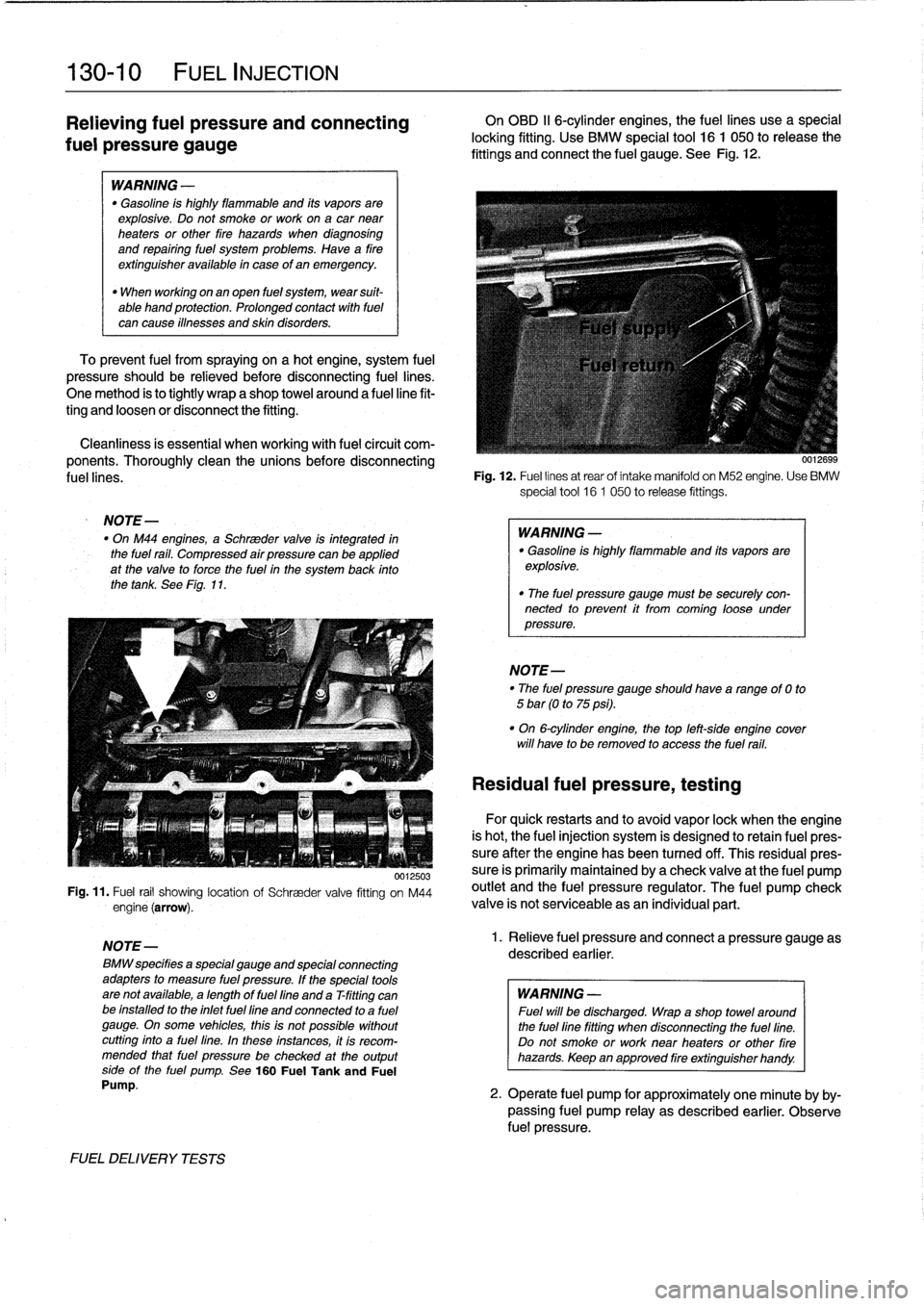
130-
1
0
FUEL
INJECTION
Relleving
fuel
pressure
and
connecting
fuel
pressure
gauge
WARNING
-
"
Gasoline
is
highly
flammable
and
its
vaporsare
explosive
.
Do
not
smoke
orwork
on
acarnear
heaters
or
other
fire
hazards
when
diagnosing
and
repairing
fuel
system
problems
.
Have
a
fire
extinguisher
available
in
case
of
an
emergency
.
"
When
working
onanopen
fuel
system,
wear
suit-
able
hand
protection
.
Prolonged
contact
with
fuel
can
cause
illnesses
and
skin
disorders
.
To
prevent
fuel
from
spraying
on
a
hot
engine,
system
fuel
pressure
should
be
relieved
before
disconnecting
fuel
lines
.
One
method
is
to
tightly
wrap
a
shop
towel
around
a
fuelline
fit-
ting
and
loosenor
disconnect
the
fitting
.
Cleanliness
is
essential
when
working
with
fuelcircuit
com-
ponents
.
Thoroughly
clean
theunionsbefore
disconnecting
fuellines
.
NOTE-
"
OnM44
engines,
a
Schrmder
valve
is
integrated
in
the
fuel
rail
.
Compressed
air
pressure
canbe
applied
at
the
valve
to
force
the
fuel
in
the
system
back
into
the
tank
.
See
Fig
.
11
.
0012503
Fig
.
11
.
Fuel
rail
showing
location
of
Schraeder
valve
fitting
on
M44
engine
(arrow)
.
NOTE-
B~
specifies
a
special
gauge
and
special
connecting
adapters
to
measure
fuel
pressure
.
If
the
special
tools
arenot
available,
a
length
of
fuel
fine
and
a
T-fitting
canbe
installed
to
the
inlet
fuel
fine
and
connected
to
a
fuel
gauge
.
On
some
vehicles,
thisis
not
possible
without
cutting
finto
a
fuel
lino
.
In
these
lnstances,
it
Is
recom-
mended
that
fuel
pressure
be
checked
at
theoutput
sidoof
the
fuel
pump
.
See
160
Fuel
Tankand
Fuel
Pump
.
FUELDELIVERY
TESTS
On
OBD
II
6-cylinder
engines,
the
fuel
lines
use
a
special
locking
fitting
.
Use
BMW
special
tool
16
1
050
to
release
the
fittings
and
connect
the
fuel
gauge
.
See
Fig
.
12
.
0012699
Fig
.
12
.
Fuel
linos
at
rear
of
intake
manifold
on
M52
engine
.
Use
BMW
special
tool
16
1
050
torelease
fittings
.
WARNING
-
"
Gasoline
is
highly
flammable
and
its
vapors
are
explosive
.
"
The
fuel
pressure
gauge
must
be
securely
con-nected
to
prevent
it
from
coming
loose
under
pressure
.
NOTE-
"
The
fuel
pressure
gauge
should
have
arangoof
0
to
5
bar
(0
to
75
psi)
.
"
On
6-cylinder
engine,
thetop
left-sido
engine
cover
will
have
to
be
removed
to
access
the
fuel
rail
.
Residual
fuel
pressure,
testing
For
quick
restarts
and
to
avoid
vapor
lock
when
the
engine
is
hot,
the
fuel
injection
system
is
designed
to
retain
fuel
pres-
sure
after
the
engine
has
been
turned
off
.
Thís
residualpres-
sure
is
primarily
maíntained
by
a
check
valve
at
the
fuel
pump
outiet
and
the
fuel
pressure
regulator
.
The
fuel
pump
check
valve
is
not
serviceable
asan
individual
part
.
1.
Relieve
fuel
pressure
and
connect
a
pressure
gauge
as
described
earlier
.
WARNING
-
Fuel
will
be
discharged
.
Wrap
a
shop
towel
around
the
fuellino
fitting
when
disconnecting
the
fuel
fine
.
Do
not
smoke
or
worknear
heaters
or
other
fire
hazards
.
Keep
an
approved
fire
extinguisher
handy
.
2
.
Operate
fuel
pump
for
approximately
one
minuto
by
by-
passing
fuel
pump
relay
as
described
earlier
.
Observe
fuel
pressure
.
Page 255 of 759
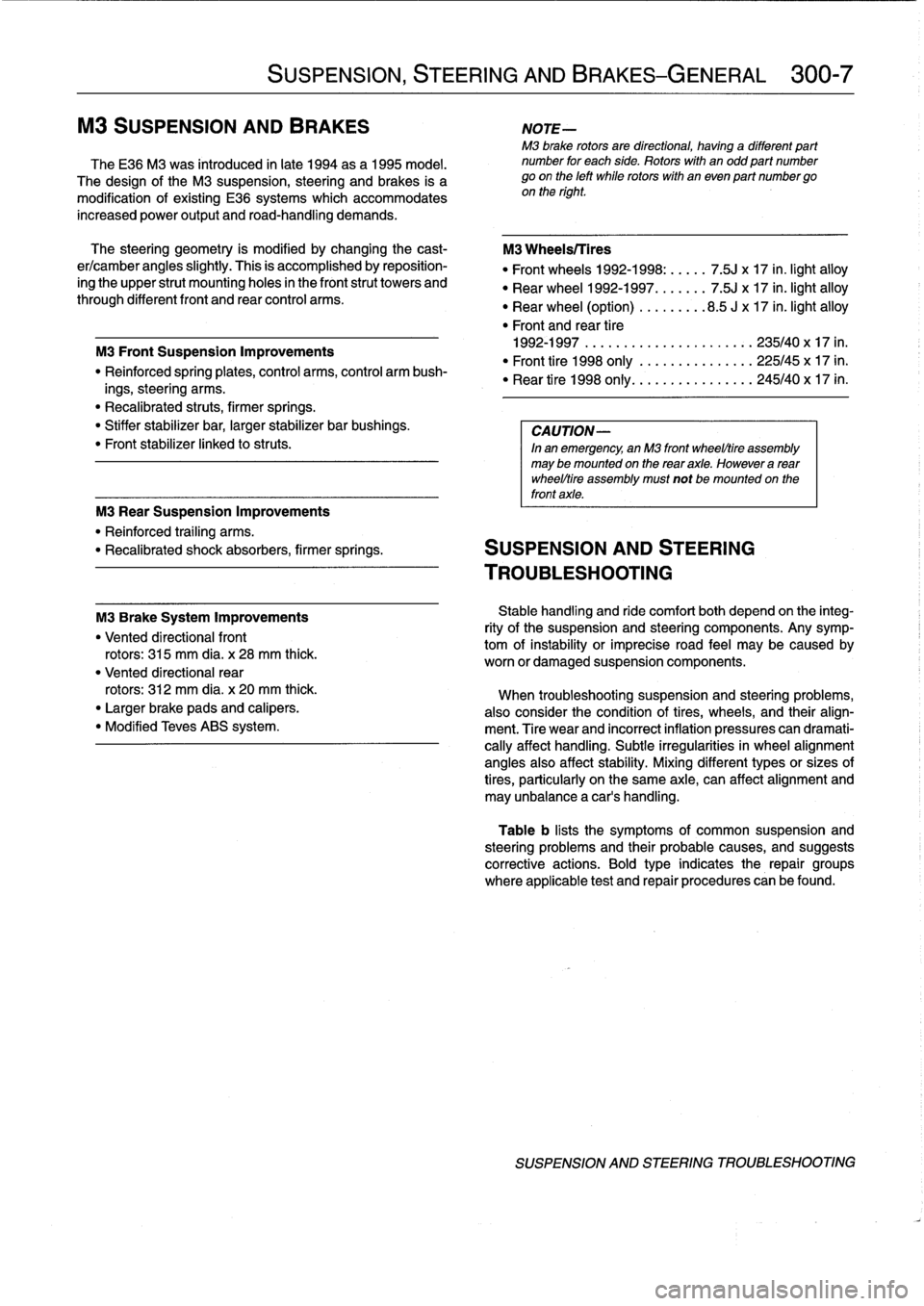
increased
power
output
and
road-handling
demands
.
The
steering
geometry
is
modified
by
changing
the
cast-
er/camber
angles
slightly
.
This
is
accomplishedby
reposition-
ing
the
upper
strut
mounting
holes
in
the
frontstrut
towers
and
through
different
front
and
rear
control
arms
.
M3
Brake
System
Improvements
"
Vented
directionalfront
rotors
:
315
mm
dia
.
x
28
mm
thick
.
"
Vented
directional
rear
rotors
:
312
mm
dia
.
x20
mm
thick
.
"
Larger
brake
pads
and
calipers
.
"
Modified
Teves
ABS
system
.
SUSPENSION,
STEERING
AND
BRAKES-GENERAL
300-
7
M3
SUSPENSION
AND
BRAKES
NOTE-
M3
brake
rotors
are
directional,
having
a
different
part
TheE36
M3
was
introduced
in
late
1994
as
a
1995
model
.
number
for
each
side
.
Rotors
with
an
odd
part
number
The
design
of
the
M3
suspension,
steering
and
brakes
is
a
go
on
the
left
while
rotors
with
en
even
part
numbergo
modification
of
existing
E36
systems
which
accommodates
on
the
right
.
M3
Front
SuspensionImprovements
"
Reinforced
spring
plates,control
arms,
control
arm
bush-
ings,
steering
arms
.
"
Recalibrated
struts,
firmer
springs
.
"
Stiffer
stabilizerbar,
larger
stabilizer
bar
bushings
.
"
Front
stabilizer
linked
to
struts
.
M3
Wheels/Tires
"
Front
wheels
1992-1998
:.....
7
.5J
x
17
in
.
light
alloy
"
Rear
wheel
1992-1997
.......
7
.5J
x17
in
.
light
alloy
"
Rear
wheel
(option)
........
.8
.5
Jx17
in
.
light
alloy
"
Front
and
rear
tire
1992-1997
.............
.
.
.
...
...
235/40
x
17
in
.
"
Front
tire
1998
only
......
...
.
.
.
...
225/45
x
17
in
.
"
Rear
tire
1998
only
.......
.
.
.
...
...
245/40
x
17
in
.
CAUTION-
In
en
emergency,
an
M3
front
wheel/tire
assembly
may
be
mounted
on
the
rearaxle
.
However
a
rear
wheel/tire
assemblymust
not
be
mounted
on
the
front
axle
.
M3
RearSuspensionImprovements
"
Reinforced
trailing
arms
.
"
Recalibrated
shock
absorbers,
firmer
springs
.
SUSPENSION
AND
STEERING
TROUBLESHOOTING
Stable
handling
and
ride
comfort
both
depend
on
the
integ-
rity
of
the
suspension
and
steering
components
.
Any
symp-
tom
of
instability
or
imprecise
road
feel
may
be
caused
by
worn
or
damaged
suspension
components
.
When
troubleshooting
suspension
and
steering
problems,
also
consider
the
condition
of
tires,
wheels,
and
their
align-
ment
.
Tire
wear
and
incorrect
inflation
pressures
can
dramati-
cally
affect
handling
.
Subtie
irregularities
in
wheel
alignment
angles
also
affect
stabílity
.
Mixing
different
types
or
sizes
of
tires,
particularly
on
the
same
axle,
can
affect
alignment
and
may
unbalancea
car's
handling
.
Table
b
lists
the
symptoms
of
common
suspension
and
steering
problems
and
their
probable
causes,
and
suggests
corrective
actions
.
Bold
type
indicates
the
repair
groups
where
applicable
test
and
repair
procedures
can
befound
.
SUSPENSION
AND
STEERING
TROUBLESHOOTING
Page 259 of 759
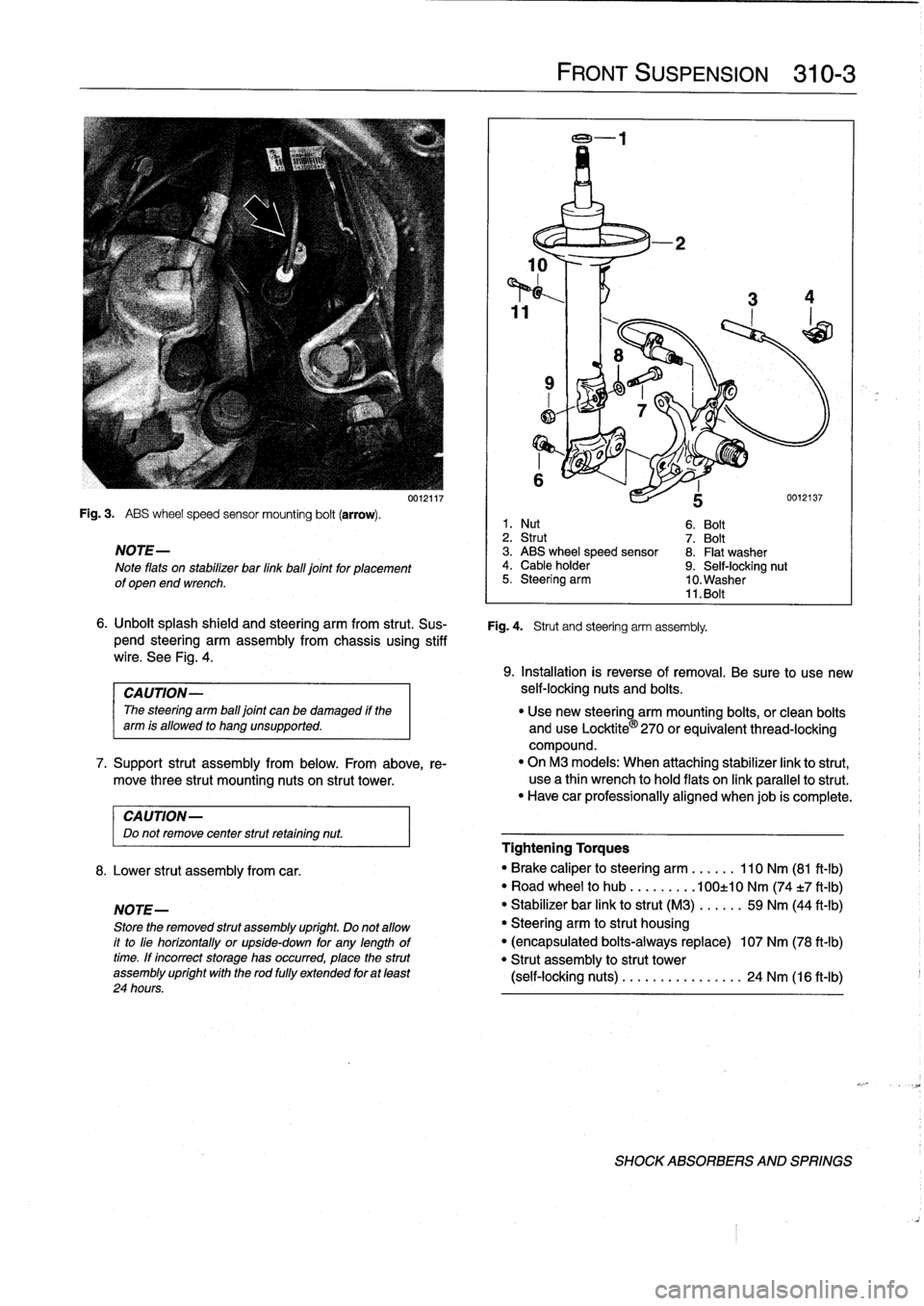
Fig
.
3
.
ABS
wheel
speed
sensor
mounting
bolt
(arrow)
.
NOTE-
Note
flats
on
stabilizer
bar
linkball
joint
for
placement
of
open
end
wrench
.
CAUTION-
Do
not
remove
center
strut
retaining
nut
.
8
.
Lower
strut
assembly
from
car
.
NOTE-
Store
the
removed
strut
assembly
upríght
.
Do
not
allow
it
to
líe
horizontally
or
upside-down
for
any
lengthoftime
.
If
íncorrect
storage
has
occurred,
place
the
strut
assembly
upríght
wíth
the
rod
fully
extended
for
at
least
24
hours
.
0012117
FRONT
SUSPENSION
310-3
6
.
Unbolt
splash
shield
and
steering
arm
from
strut
.
Sus-
Fig
.
4
.
Strut
and
steering
arm
assembly
.
pend
steering
arm
assembly
from
chassis
using
stiff
wire
.
See
Fig
.
4
.
1
.
Nut
6
.
Bolt
2
.
Strut
7
.
Bolt
3
.
ABS
wheel
speed
sensor
8
.
Flat
washer
4
.
Cable
holder
9
.
Self-locking
nut
5
.
Steering
arm
10
.
Washer
11
.
Bolt
9
.
Installation
is
reverse
of
removal
.
Be
sure
to
use
new
CAUTION-
self-locking
nuts
and
bolts
.
The
steering
arm
ball
joint
can
be
damaged
if
the
"
Use
new
steering
arm
mounting
bolts,
or
clean
bolts
arm
is
allowed
to
hang
unsupported
.
and
use
Locktite
®
270
orequivalent
thread-locking
compound
.
7
.
Support
strut
assembly
from
below
.
From
above,
re-
"
On
M3
models
:
When
attaching
stabilizer
link
to
strut,
move
three
strut
mounting
nuts
on
strut
tower
.
use
a
thin
wrench
to
hold
flats
on
link
parallelto
strut
.
"
Have
car
professionally
aligned
When
job
is
complete
.
Tightening
Torques
"
Brake
caliper
to
steering
arm
......
110
Nm
(81
ft-lb)
"
Road
wheel
to
hub
.........
100±10
Nm
(74
t7
ft-Ib)
"
Stabilizer
bar
link
to
strut
(M3)
.....
.
59
Nm
(44
ft-lb)
"
Steering
arm
to
strut
housing
"
(encapsulated
bolts-always
replace)
107
Nm
(78
ft-lb)
"
Strut
assembly
to
strut
tower
(self-locking
nuts)
........
...
..
..
.
24
Nm
(16
ft-Ib)
SHOCK
ABSORBERS
AND
SPRINGS
Page 263 of 759
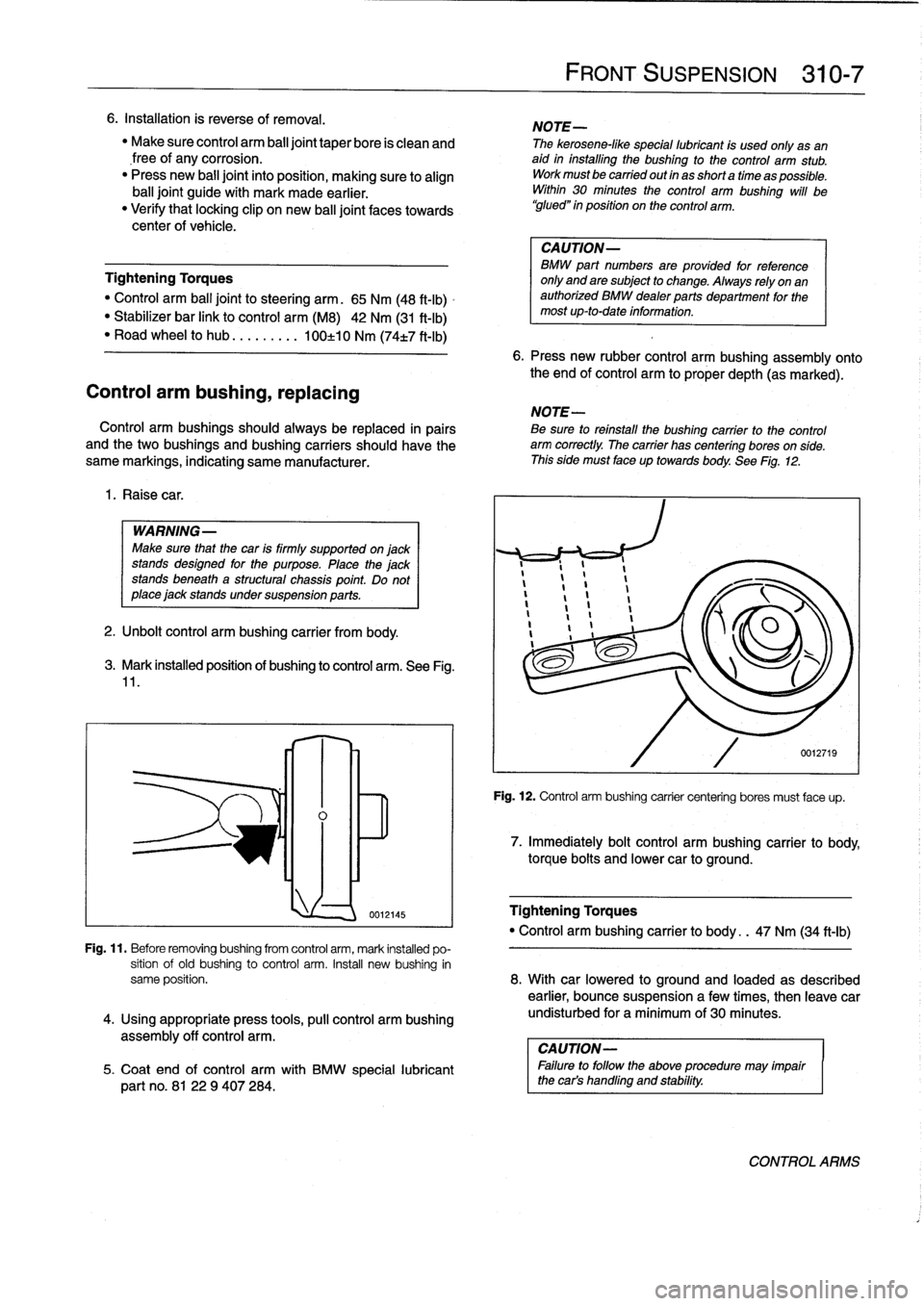
6
.
Installation
is
reverse
of
removal
.
"
Make
sure
control
arm
ball
joint
taper
bore
is
clean
and
free
of
any
corrosion
.
"
Press
new
balljoint
into
position,
making
sure
to
align
balljoint
guide
with
mark
made
earlier
.
"
Verify
that
locking
clip
on
new
ball
joint
faces
towards
center
of
vehicle
.
Tightening
Torques
"
Control
arm
ball
jointto
steering
arm
.
65
Nm
(48
ft-Ib)
"
Stabilizer
bar
link
to
control
arm
(M8)
42
Nm
(31
ft-Ib)
"
Road
wheel
to
hub
.
...
...
.
.
100±10
Nm
(74t7
ft-lb)
Control
arm
bushing,
replacing
Control
arm
bushings
should
aiways
be
replaced
in
pairs
and
the
two
bushings
and
bushing
carriers
should
have
the
same
markings,
indicating
same
manufacturer
.
1
.
Raisecar
.
WARNING-
Make
sure
that
the
car
is
firmly
supportedonjackstandsdesigned
for
the
purpose
.
Place
the
jackstands
beneath
a
structural
chassis
point
.
Do
not
place
jack
stands
undersuspension
parts
.
2
.
Unbolt
control
arm
bushing
carrier
from
body
.
3
.
Mark
installed
position
of
bushing
to
control
arm
.
See
Fig
.
11
.
assembly
off
control
arm
.
lnl~
0012145
FRONT
SUSPENSION
310-
7
NOTE-
The
kerosene-like
special
lubricant
is
used
only
asan
aid
in
installing
the
bushing
to
the
control
arm
stub
.
Workmustbe
carried
out
in
as
short
a
time
as
possible
.
Within
30
minutes
the
control
arm
bushing
will
be
`glued"
in
position
on
the
control
arm
.
CAUTION-
BMW
part
numbers
areprovided
for
reference
only
and
are
subject
to
change
.
Always
rely
on
an
authorized
BMW
dealerparts
department
for
the
most
up-to-date
information
.
6
.
Press
new
rubber
control
arm
bushing
assembly
onto
the
end
of
control
arm
to
proper
depth
(as
marked)
.
NOTE-
Be
sure
toreinstall
the
bushing
carrier
to
the
control
arm
correctly
.
The
carrier
has
centering
bores
on
side
.
This
side
must
face
up
towards
body
.
See
Fig
.
12
.
Fig
.
12
.
Control
arm
bushing
carrier
centering
bores
must
face
up
.
7
.
Immediately
bolt
control
arm
bushing
carrier
to
body,
torque
boits
and
lower
car
to
ground
.
Tightening
Torques
"
Control
arm
bushing
carrier
to
body
.
.
47
Nm
(34
ft-ib)
Fig
.
11
.
Before
removingbushing
from
control
arm,
mark
installed
po-
sition
of
old
bushing
to
control
arm
.
Insta¡¡
new
bushing
in
same
position
.
8
.
With
car
lowered
to
ground
and
loaded
as
described
earlier,
bounce
suspensiona
few
times,
then
leave
car
4
.
Using
appropriate
press
tools,
pull
control
arm
bushing
undisturbed
for
a
minimum
of
30
minutes
.
CAUTION-
5
.
Coat
end
of
control
arm
with
BMW
special
lubricant
I
Failure
to
follow
the
above
procedure
may
impair
part
no
.
8122
9
407284
.
the
car's
handling
and
stability
.
CONTROLARMS
Page 289 of 759
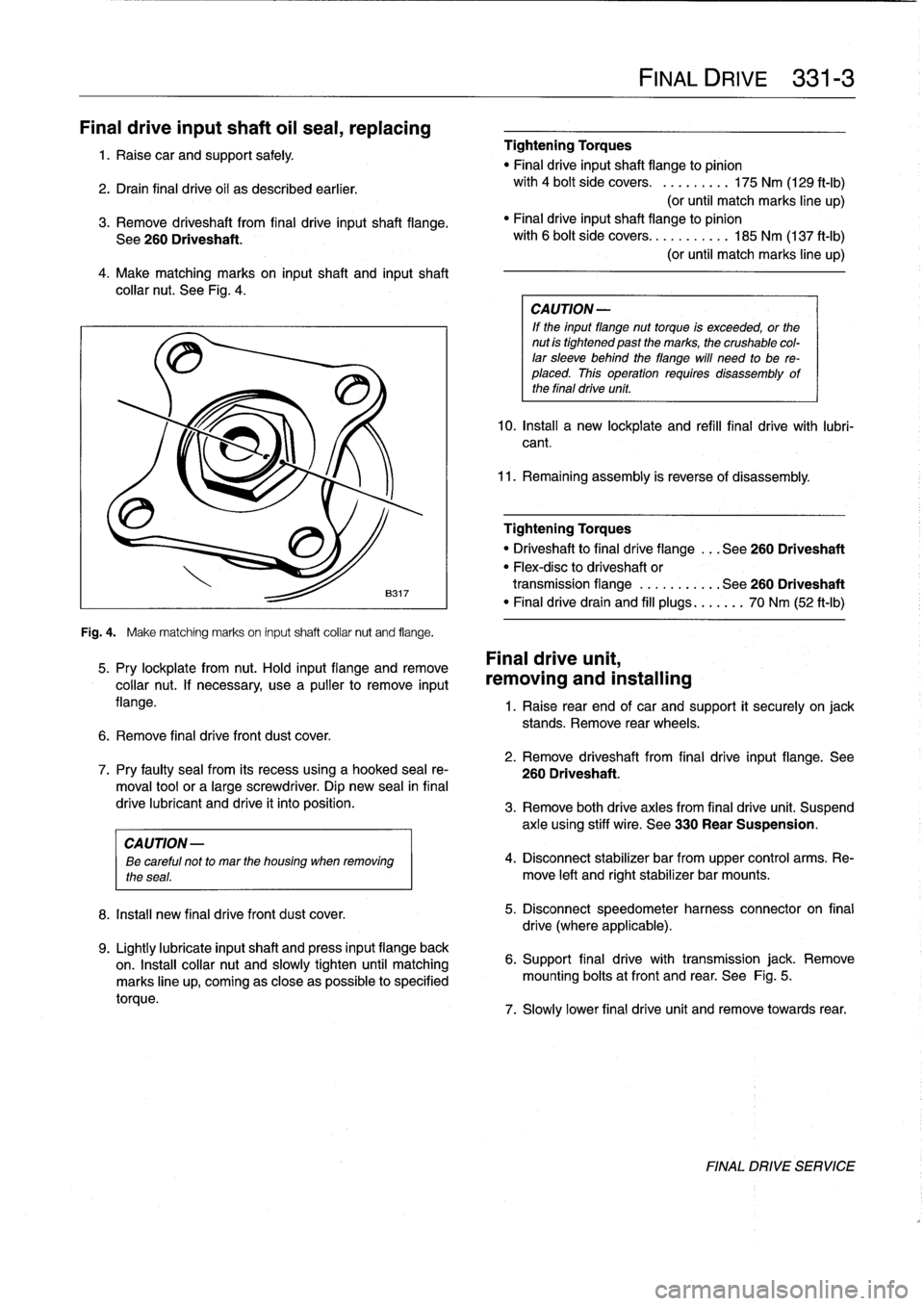
Final
driveinputshaft
oil
sea¡,
replacing
1
.
Raise
car
and
support
safely
.
2
.
Drain
final
drive
oil
as
described
earlier
.
3
.
Remove
driveshaft
from
final
drive
inputshaft
flange
.
See
260
Driveshaft
.
4
.
Make
matching
marks
on
input
shaft
and
inputshaft
collar
nut
.
See
Fig
.
4
.
Fig
.
4
.
Make
matching
marks
on
input
shaft
collar
nut
and
flange
.
5
.
Pry
lockplate
from
nut
.
Hold
input
flange
andremove
collar
nut
.
If
necessary,
usea
pullerto
remove
input
flange
.
6
.
Remove
final
drive
front
dust
cover
.
8
.
Install
new
final
drivefront
dust
cover
.
9
.
Lightly
lubricate
inputshaft
and
press
input
flange
back
on
.
Insta¡¡
collar
nut
and
slowly
tighten
until
matching
marks
line
up,
coming
as
close
aspossible
to
specified
torque
.
Tightening
Torques
"
Final
driveinputshaft
flange
to
pinion
with
4
bolt
side
covers
.
.........
175
Nm
(129
ft-Ib)
(or
until
match
marks
line
up)
"
Finaldriveinputshaft
flange
to
pinion
with
6
bolt
side
covers
...........
185
Nm
(137
ft-Ib)
(or
until
match
marks
line
up)
CA
UTION-
If
the
input
flange
nuttorque
is
exceeded,
or
the
nut
is
tightened
past
the
marks,
the
crushable
col-
lar
sleeve
behind
theflange
will
need
to
be
re-
placed
.
This
operation
requires
disassembly
of
the
final
drive
unit
.
10
.
Install
a
new
lockplate
and
refill
final
drive
with
lubri-
cant
.
11
.
Remaining
assembly
is
reverse
of
disassembly
.
Tightening
Torques
"
Driveshaftto
final
dríve
flange
...
See260
Driveshaft
"
Flex-disc
to
driveshaft
or
transmission
flange
...........
See260
Driveshaft
"
Finaldrivedrain
and
fill
plugs
...
.
..
.
70
Nm
(52
ft-Ib)
Final
drive
unit,
removing
and
installing
FINAL
DRIVE
331-
3
1
.
Raise
rear
end
of
car
and
support
it
securely
on
jack
stands
.
Remove
rear
wheels
.
2
.
Remove
driveshaft
from
final
drive
input
flange
.
See
7
.
Pry
faulty
sea¡
from
its
recess
using
a
hooked
sea¡
re-
260
Driveshaft
.
moval
toolor
a
large
screwdriver
.
Dip
new
sea¡
in
final
drive
lubricant
and
drive
it
into
position
.
3
.
Remove
both
drive
axles
from
final
drive
unit
.
Suspend
axle
using
stiff
wire
.
See
330
Rear
Suspension
.
CAUTION
-
ee
careful
not
to
mar
the
housing
when
removing
4
.
Disconnect
stabilizer
bar
from
upper
control
arms
.
Re-
the
seas
.
move
left
and
rightstabilizer
bar
mounts
.
5
.
Disconnect
speedometer
harness
connector
on
final
drive
(where
applicable)
.
6
.
Support
final
drive
with
transmission
jack
.
Remove
mounting
bolts
atfront
and
rear
.
See
Fig
.
5
.
7
.
Slowly
lower
final
drive
unit
and
remove
towards
rear
.
FINAL
DRIVE
SERVICE