display BMW X5 2001 E53 Level Control System Manual
[x] Cancel search | Manufacturer: BMW, Model Year: 2001, Model line: X5, Model: BMW X5 2001 E53Pages: 57, PDF Size: 1.89 MB
Page 53 of 57
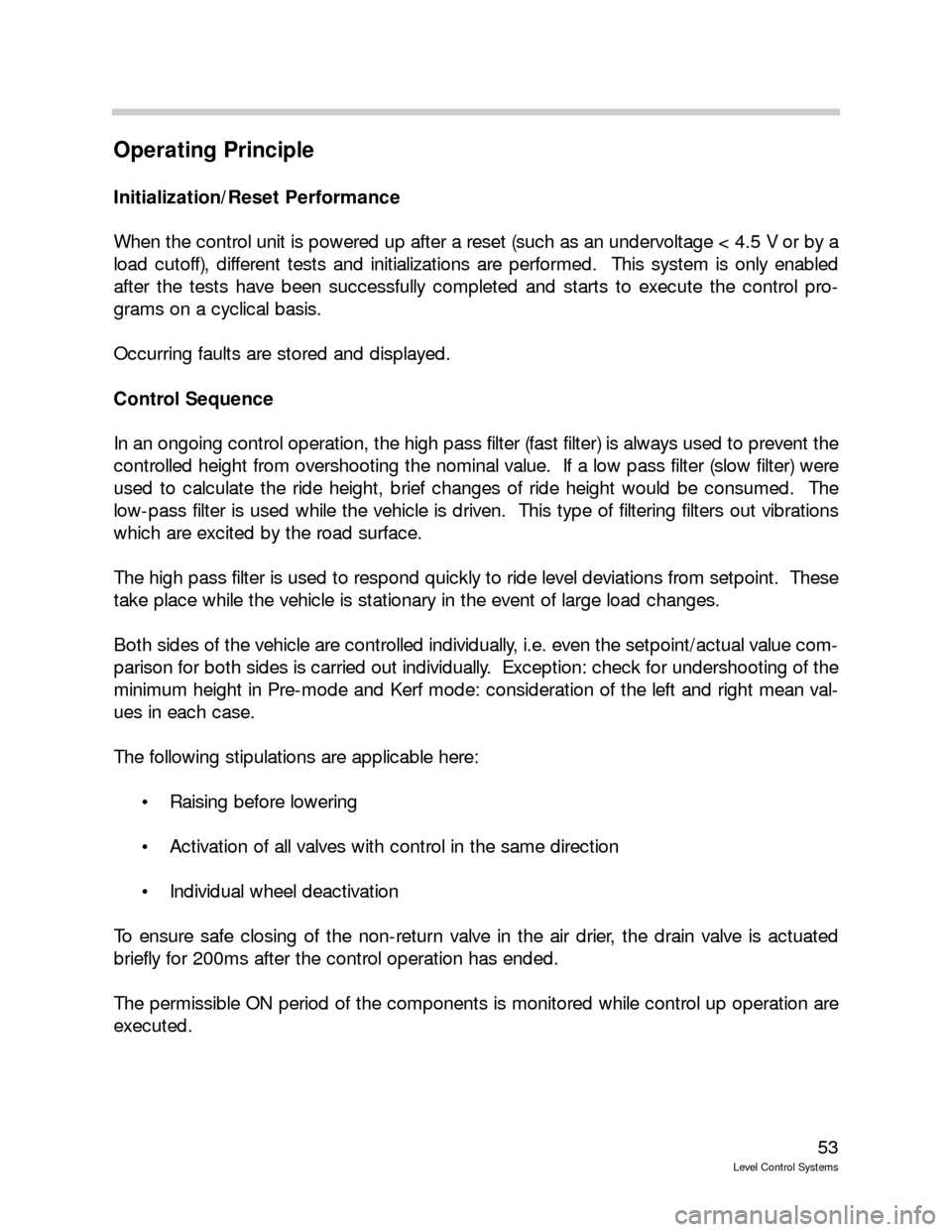
53
Level Control Systems
Operating Principle
Initialization/Reset Performance
When the control unit is powered up after a reset (such as an undervoltage < 4.5 V or by a
load cutoff), different tests and initializations are performed. This system is only enabled
after the tests have been successfully completed and starts to execute the control pro-
grams on a cyclical basis.
Occurring faults are stored and displayed.
Control Sequence
In an ongoing control operation, the high pass filter (fast filter) is always used to prevent the
controlled height from overshooting the nominal value. If a low pass filter (slow filter) were
used to calculate the ride height, brief changes of ride height would be consumed. The
low-pass filter is used while the vehicle is driven. This type of filtering filters out vibrations
which are excited by the road surface.
The high pass filter is used to respond quickly to ride level deviations from setpoint. These
take place while the vehicle is stationary in the event of large load changes.
Both sides of the vehicle are controlled individually, i.e. even the setpoint/actual value com-
parison for both sides is carried out individually. Exception: check for undershooting of the
minimum height in Pre-mode and Kerf mode: consideration of the left and right mean val-
ues in each case.
The following stipulations are applicable here:
Raising before lowering
Activation of all valves with control in the same direction
Individual wheel deactivation
To ensure safe closing of the non-return valve in the air drier, the drain valve is actuated
briefly for 200ms after the control operation has ended.
The permissible ON period of the components is monitored while control up operation are
executed.
Page 54 of 57
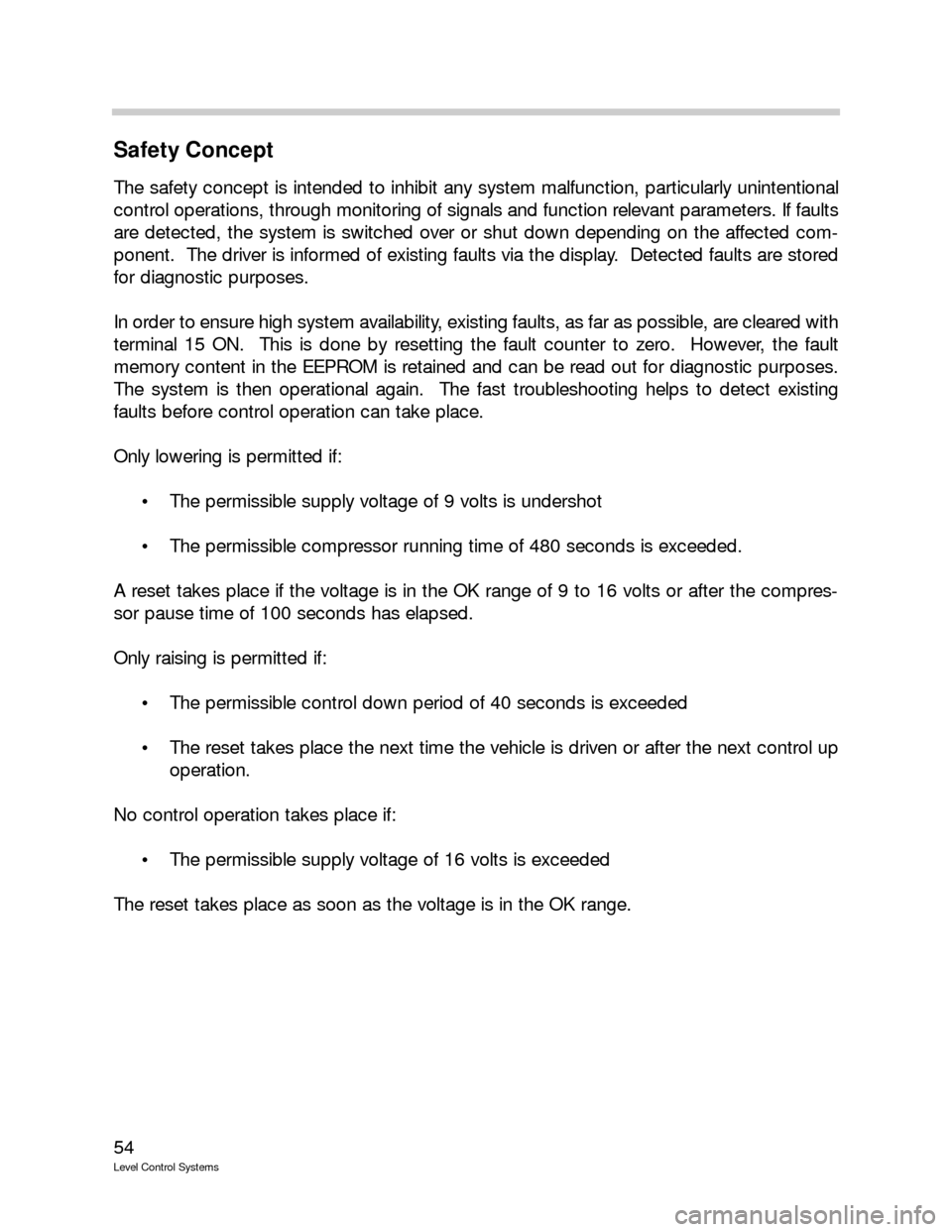
54
Level Control Systems
Safety Concept
The safety concept is intended to inhibit any system malfunction, particularly unintentional
control operations, through monitoring of signals and function relevant parameters. If faults
are detected, the system is switched over or shut down depending on the affected com-
ponent. The driver is informed of existing faults via the display. Detected faults are stored
for diagnostic purposes.
In order to ensure high system availability, existing faults, as far as possible, are cleared with
terminal 15 ON. This is done by resetting the fault counter to zero. However, the fault
memory content in the EEPROM is retained and can be read out for diagnostic purposes.
The system is then operational again. The fast troubleshooting helps to detect existing
faults before control operation can take place.
Only lowering is permitted if:
The permissible supply voltage of 9 volts is undershot
The permissible compressor running time of 480 seconds is exceeded.
A reset takes place if the voltage is in the OK range of 9 to 16 volts or after the compres-
sor pause time of 100 seconds has elapsed.
Only raising is permitted if:
The permissible control down period of 40 seconds is exceeded
The reset takes place the next time the vehicle is driven or after the next control up
operation.
No control operation takes place if:
The permissible supply voltage of 16 volts is exceeded
The reset takes place as soon as the voltage is in the OK range.