sensor BMW X5 2001 E53 M62TU Engine Workshop Manual
[x] Cancel search | Manufacturer: BMW, Model Year: 2001, Model line: X5, Model: BMW X5 2001 E53Pages: 37, PDF Size: 3.9 MB
Page 8 of 37
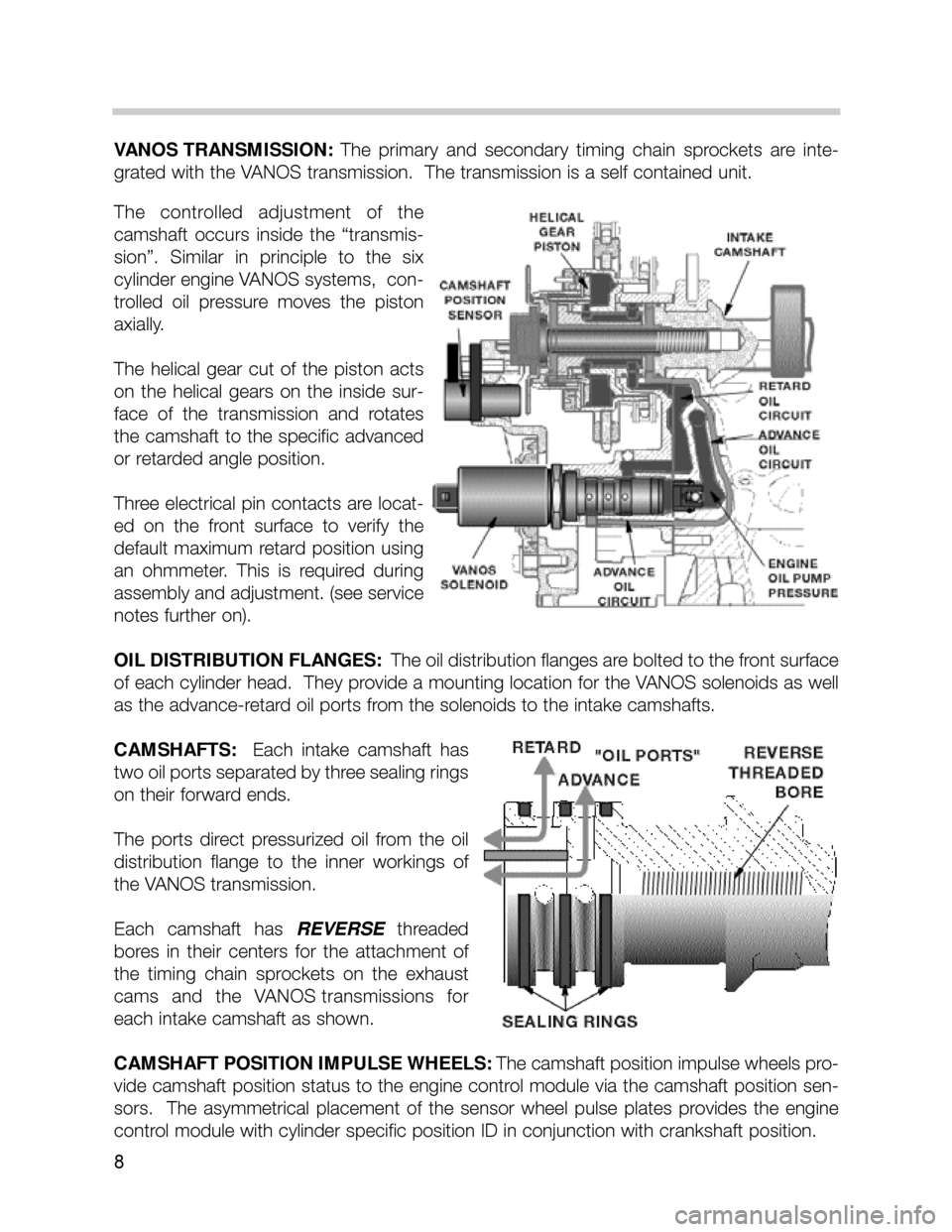
VANOS TRANSMISSION:The primary and secondary timing chain sprockets are inte-
grated with the VANOS transmission. The transmission is a self contained unit.
The controlled adjustment of the
camshaft occurs inside the “transmis-
sion”. Similar in principle to the six
cylinder engine VANOS systems, con-
trolled oil pressure moves the piston
axially.
The helical gear cut of the piston acts
on the helical gears on the inside sur-
face of the transmission and rotates
the camshaft to the specific advanced
or retarded angle position.
Three electrical pin contacts are locat-
ed on the front surface to verify the
default maximum retard position using
an ohmmeter. This is required during
assembly and adjustment. (see service
notes further on).
OIL DISTRIBUTION FLANGES:The oil distribution flanges are bolted to the front surface
of each cylinder head. They provide a mounting location for the VANOS solenoids as well
as the advance-retard oil ports from the solenoids to the intake camshafts.
CAMSHAFTS: Each intake camshaft has
two oil ports separated by three sealing rings
on their forward ends.
The ports direct pressurized oil from the oil
distribution flange to the inner workings of
the VANOS transmission.
Each camshaft has REVERSEthreaded
bores in their centers for the attachment of
the timing chain sprockets on the exhaust
cams and the VANOS transmissions for
each intake camshaft as shown.
CAMSHAFT POSITION IMPULSE WHEELS:The camshaft position impulse wheels pro-
vide camshaft position status to the engine control module via the camshaft position sen-
sors. The asymmetrical placement of the sensor wheel pulse plates provides the engine
control module with cylinder specific position ID in conjunction with crankshaft position.
Page 12 of 37
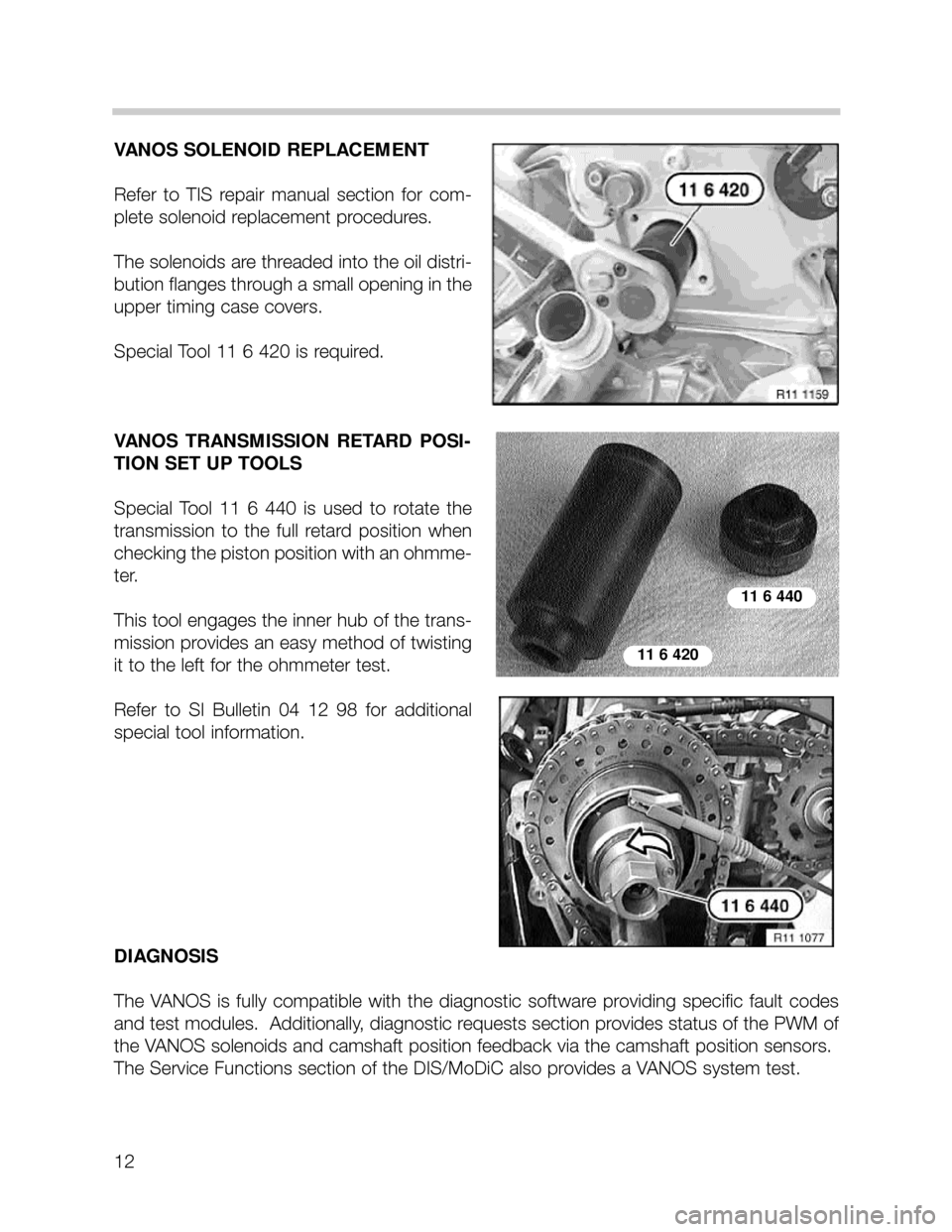
12
VANOS SOLENOID REPLACEMENT
Refer to TIS repair manual section for com-
plete solenoid replacement procedures.
The solenoids are threaded into the oil distri-
bution flanges through a small opening in the
upper timing case covers.
Special Tool 11 6 420 is required.
VANOS TRANSMISSION RETARD POSI-
TION SET UP TOOLS
Special Tool 11 6 440 is used to rotate the
transmission to the full retard position when
checking the piston position with an ohmme-
ter.
This tool engages the inner hub of the trans-
mission provides an easy method of twisting
it to the left for the ohmmeter test.
Refer to SI Bulletin 04 12 98 for additional
special tool information.
DIAGNOSIS
The VANOS is fully compatible with the diagnostic software providing specific fault codes
and test modules. Additionally, diagnostic requests section provides status of the PWM of
the VANOS solenoids and camshaft position feedback via the camshaft position sensors.
The Service Functions section of the DIS/MoDiC also provides a VANOS system test.
11 6 440
11 6 420
Page 15 of 37
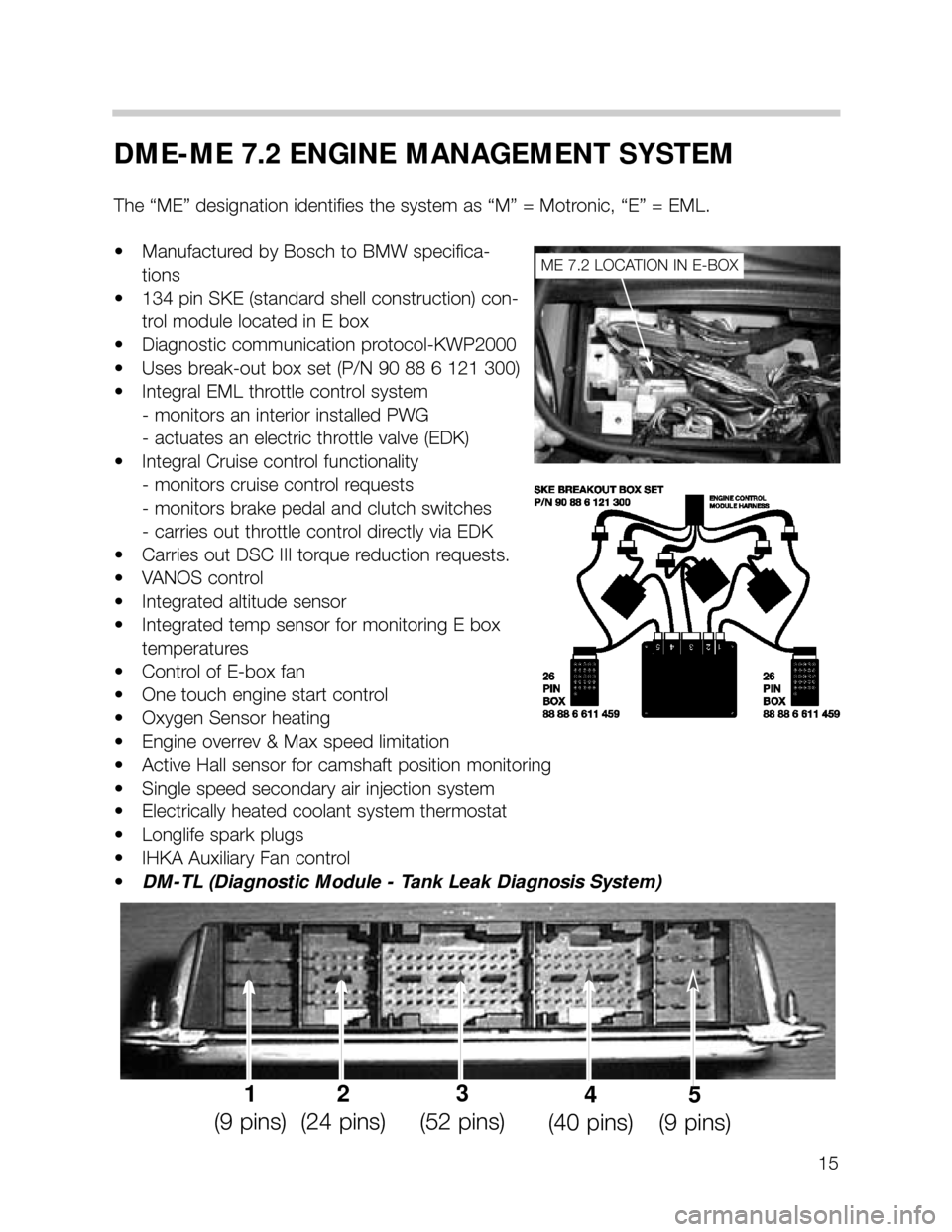
15
DME-ME 7.2 ENGINE MANAGEMENT SYSTEM
The “ME” designation identifies the system as “M” = Motronic, “E” = EML.
• Manufactured by Bosch to BMW specifica-
tions
• 134 pin SKE (standard shell construction) con-
trol module located in E box
• Diagnostic communication protocol-KWP2000
• Uses break-out box set (P/N 90 88 6 121 300)
• Integral EML throttle control system
- monitors an interior installed PWG
- actuates an electric throttle valve (EDK)
• Integral Cruise control functionality
- monitors cruise control requests
- monitors brake pedal and clutch switches
- carries out throttle control directly via EDK
• Carries out DSC III torque reduction requests.
• VANOS control
• Integrated altitude sensor
• Integrated temp sensor for monitoring E box
temperatures
• Control of E-box fan
• One touch engine start control
• Oxygen Sensor heating
• Engine overrev & Max speed limitation
• Active Hall sensor for camshaft position monitoring
• Single speed secondary air injection system
• Electrically heated coolant system thermostat
• Longlife spark plugs
• IHKA Auxiliary Fan control
•DM-TL (Diagnostic Module - Tank Leak Diagnosis System)
ME 7.2 LOCATION IN E-BOX
1
(9 pins)2
(24 pins)3
(52 pins)4
(40 pins)5
(9 pins)
Page 19 of 37
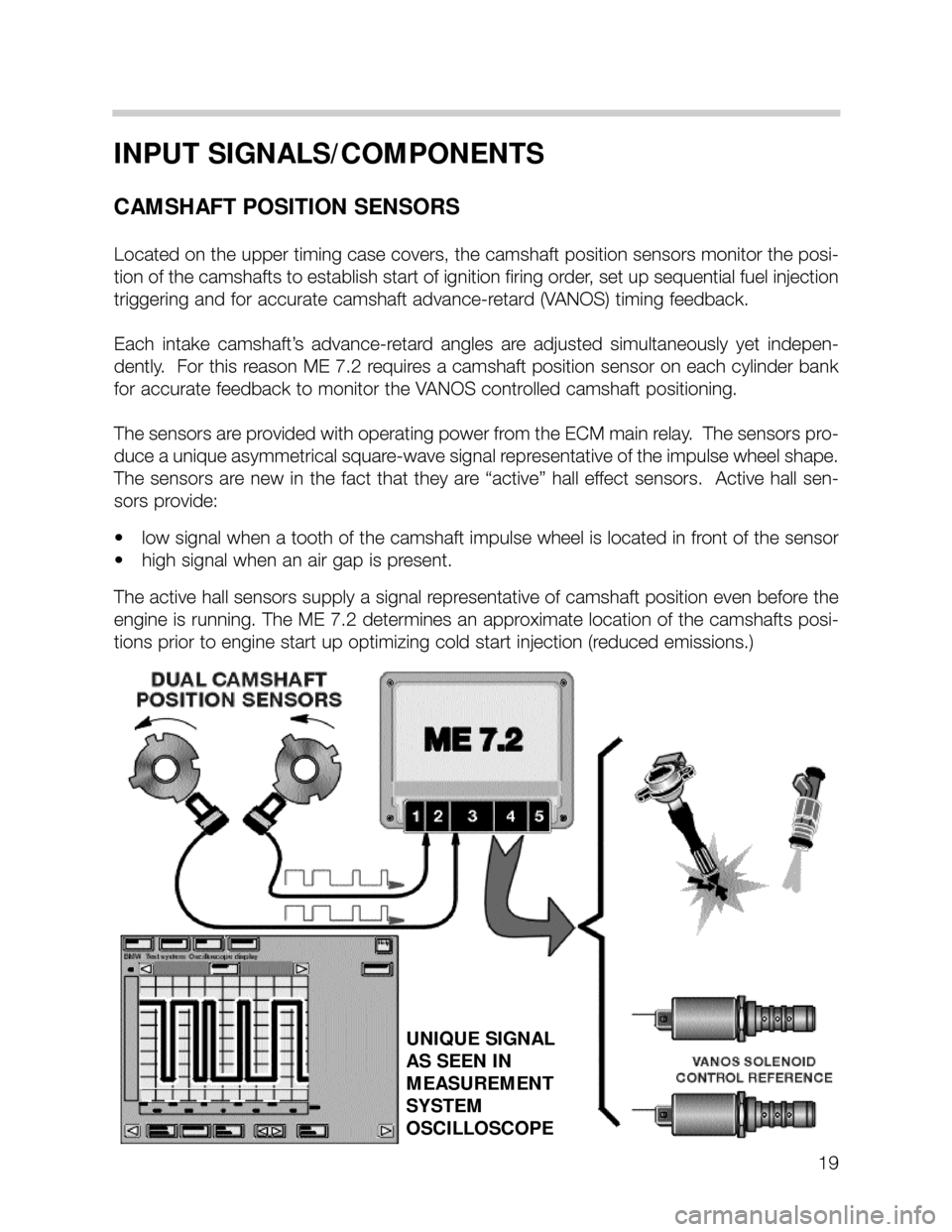
19
INPUT SIGNALS/COMPONENTS
CAMSHAFT POSITION SENSORS
Located on the upper timing case covers, the camshaft position sensors monitor the posi-
tion of the camshafts to establish start of ignition firing order, set up sequential fuel injection
triggering and for accurate camshaft advance-retard (VANOS) timing feedback.
Each intake camshaft’s advance-retard angles are adjusted simultaneously yet indepen-
dently. For this reason ME 7.2 requires a camshaft position sensor on each cy linder bank
for accurate feedback to monitor the VANOS controlled camshaft positioning.
The sensors are provided with operating power from the ECM main relay. The sensors pro-
duce a unique asymmetrical square-wave signal representative of the impulse wheel shape.
The sensors are new in the fact that they are “active” hall effect sensors. Active hall sen-
sors provide:
• low signal when a tooth of the camshaft impulse wheel is located in front of the sensor
• high signal when an air gap is present.
The active hall sensors supply a signal representative of camshaft position even before the
engine is running. The ME 7.2 determines an approximate location of the camshafts posi-
tions prior to engine start up optimizing cold start injection (reduced emissions.)
UNIQUE SIGNAL
AS SEEN IN
MEASUREMENT
SYSTEM
OSCILLOSCOPE
Page 20 of 37
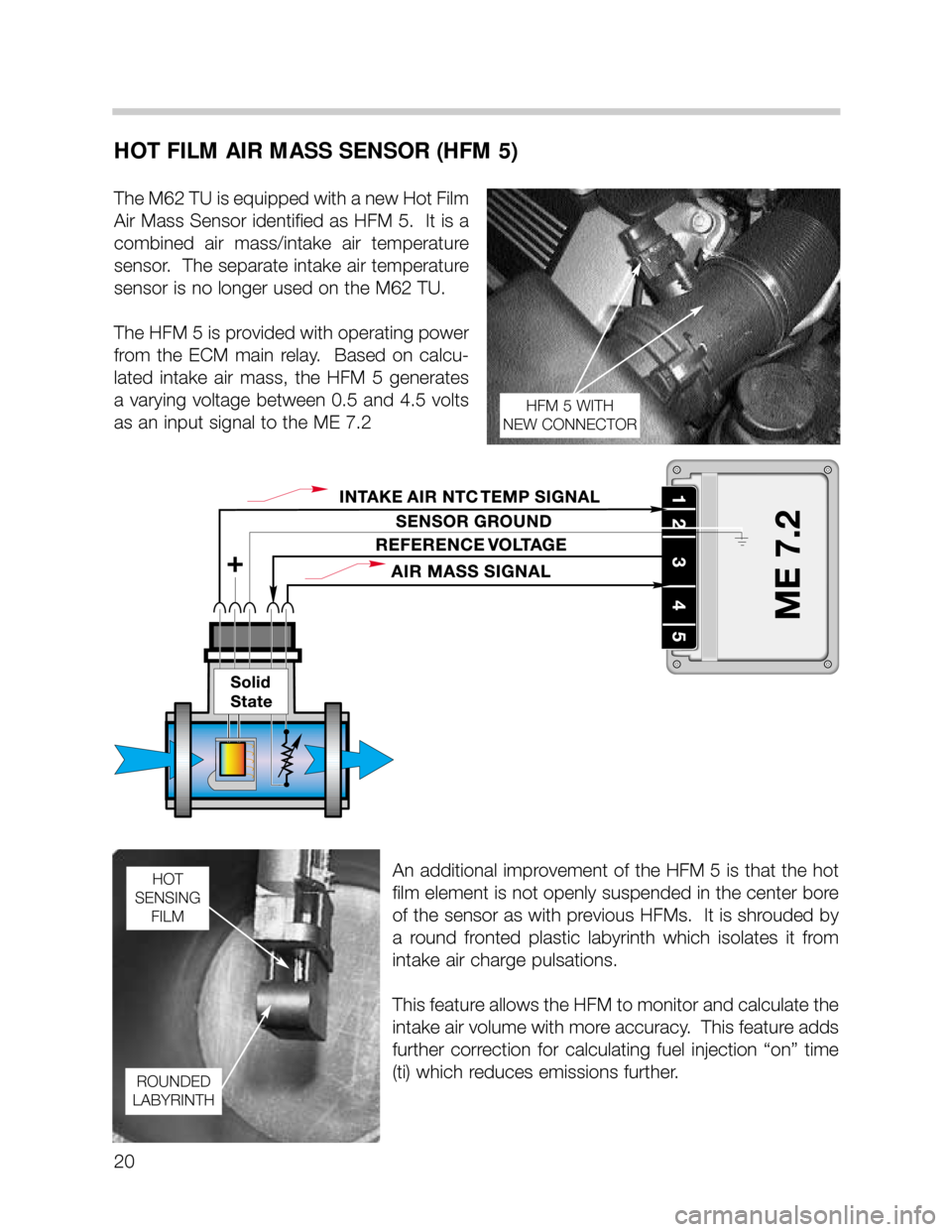
20
HOT FILM AIR MASS SENSOR (HFM 5)
The M62 TU is equipped with a new Hot Film
Air Mass Sensor identified as HFM 5. It is a
combined air mass/intake air temperature
sensor. The separate intake air temperature
sensor is no longer used on the M62 TU.
The HFM 5 is provided with operating power
from the ECM main relay. Based on calcu-
lated intake air mass, the HFM 5 generates
a varying voltage between 0.5 and 4.5 volts
as an input signal to the ME 7.2
An additional improvement of the HFM 5 is that the hot
film element is not openly suspended in the center bore
of the sensor as with previous HFMs. It is shrouded by
a round fronted plastic labyrinth which isolates it from
intake air charge pulsations.
This feature allows the HFM to monitor and calculate the
intake air volume with more accuracy. This feature adds
further correction for calculating fuel injection “on” time
(ti) which reduces emissions further.
HFM 5 WITH
NEW CONNECTOR
HOT
SENSING
FILM
ROUNDED
LABYRINTH
Page 21 of 37
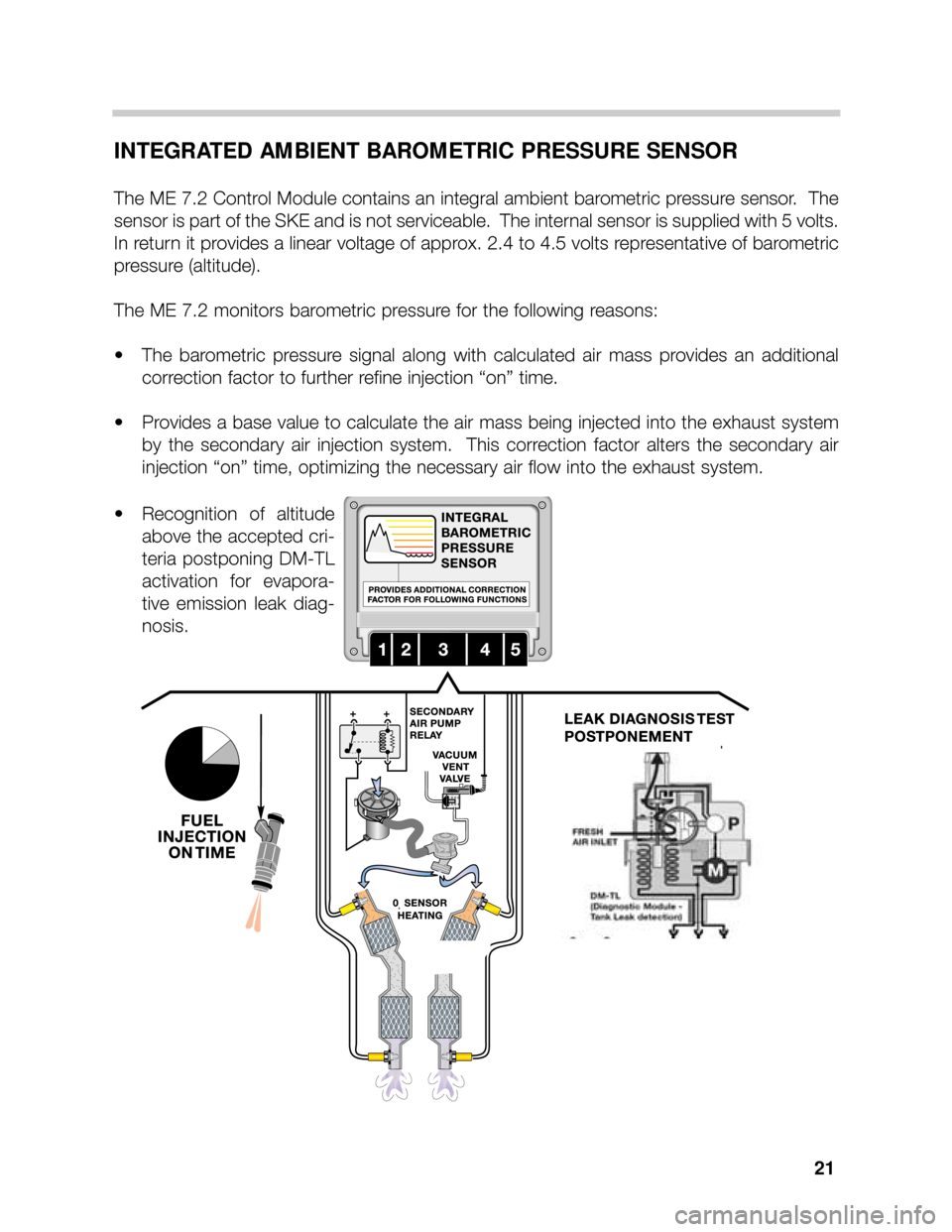
11
INTEGRATED AMBIENT BAROMETRIC PRESSURE SENSOR
The ME 7.2 Control Module contains an integral ambient barometric pressure sensor. The
sensor is part of the SKE and is not serviceable. The internal sensor is supplied with 5 volts.
In return it provides a linear voltage of approx. 2.4 to 4.5 volts representative of barometric
pressure (altitude).
The ME 7.2 monitors barometric pressure for the following reasons:
• The barometric pressure signal along with calculated air mass provides an additional
correction factor to further refine injection “on” time.
• Provides a base value to calculate the air mass being injected into the exhaust system
by the secondary air injection system. This correction factor alters the secondary air
injection “on” time, optimizing the necessary air flow into the exhaust system.
• Recognition of altitude
above the accepted cri-
teria postponing DM-TL
activation for evapora-
tive emission leak diag-
nosis.
21
Page 22 of 37
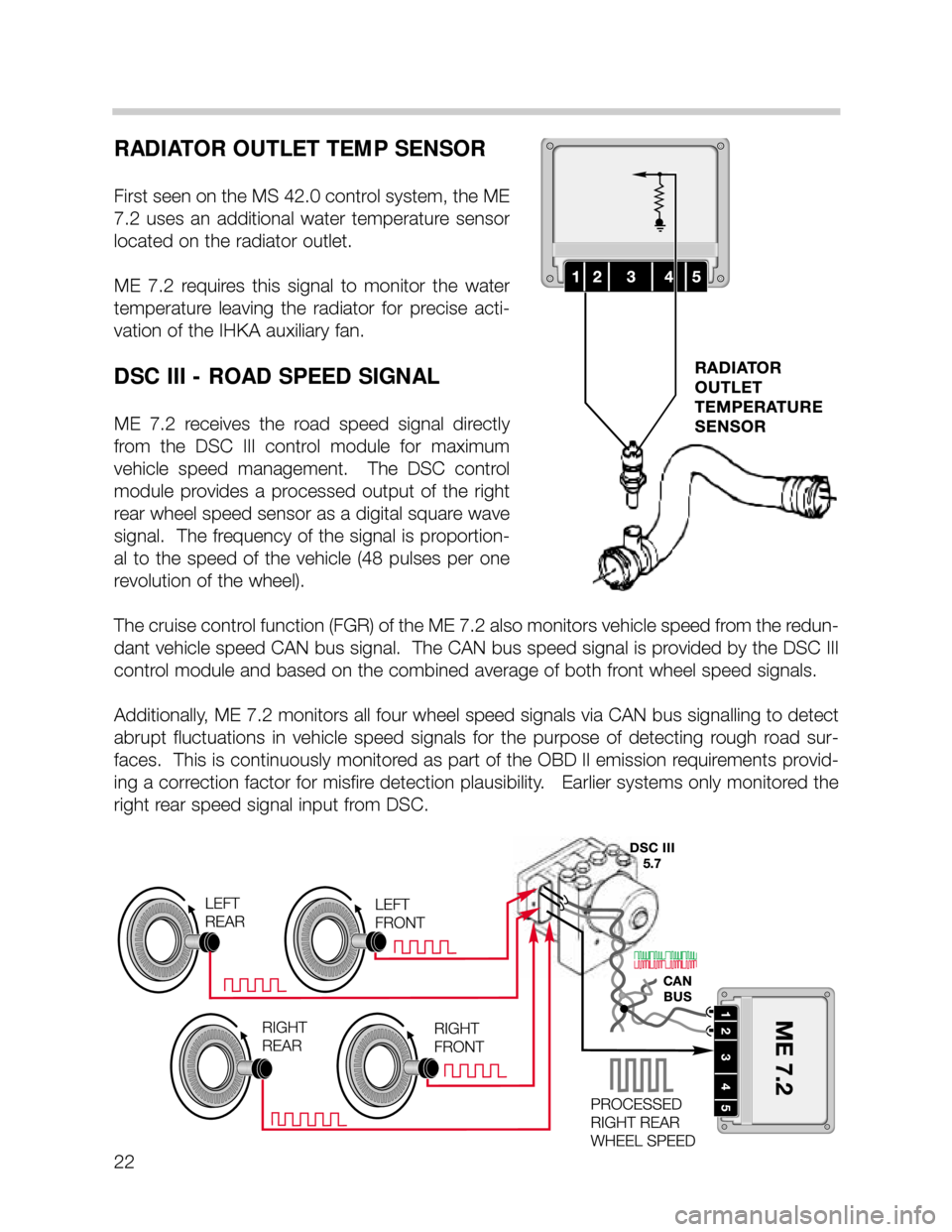
22
RADIATOR OUTLET TEMP SENSOR
First seen on the MS 42.0 control system, the ME
7.2 uses an additional water temperature sensor
located on the radiator outlet.
ME 7.2 requires this signal to monitor the water
temperature leaving the radiator for precise acti-
vation of the IHKA auxiliary fan.
DSC III - ROAD SPEED SIGNAL
ME 7.2 receives the road speed signal directly
from the DSC III control module for maximum
vehicle speed management. The DSC control
module provides a processed output of the right
rear wheel speed sensor as a digital square wave
signal. The frequency of the signal is proportion-
al to the speed of the vehicle (48 pulses per one
revolution of the wheel).
The cruise control function (FGR) of the ME 7.2 also monitors vehicle speed from the redun-
dant vehicle speed CAN bus signal. The CAN bus speed signal is provided by the DSC III
control module and based on the combined average of both front wheel speed signals.
Additionally, ME 7.2 monitors all four wheel speed signals via CAN bus signalling to detect
abrupt fluctuations in vehicle speed signals for the purpose of detecting rough road sur-
faces. This is continuously monitored as part of the OBD II emission requirements provid-
ing a correction factor for misfire detection plausibility. Earlier systems only monitored the
right rear speed signal input from DSC.
Page 23 of 37
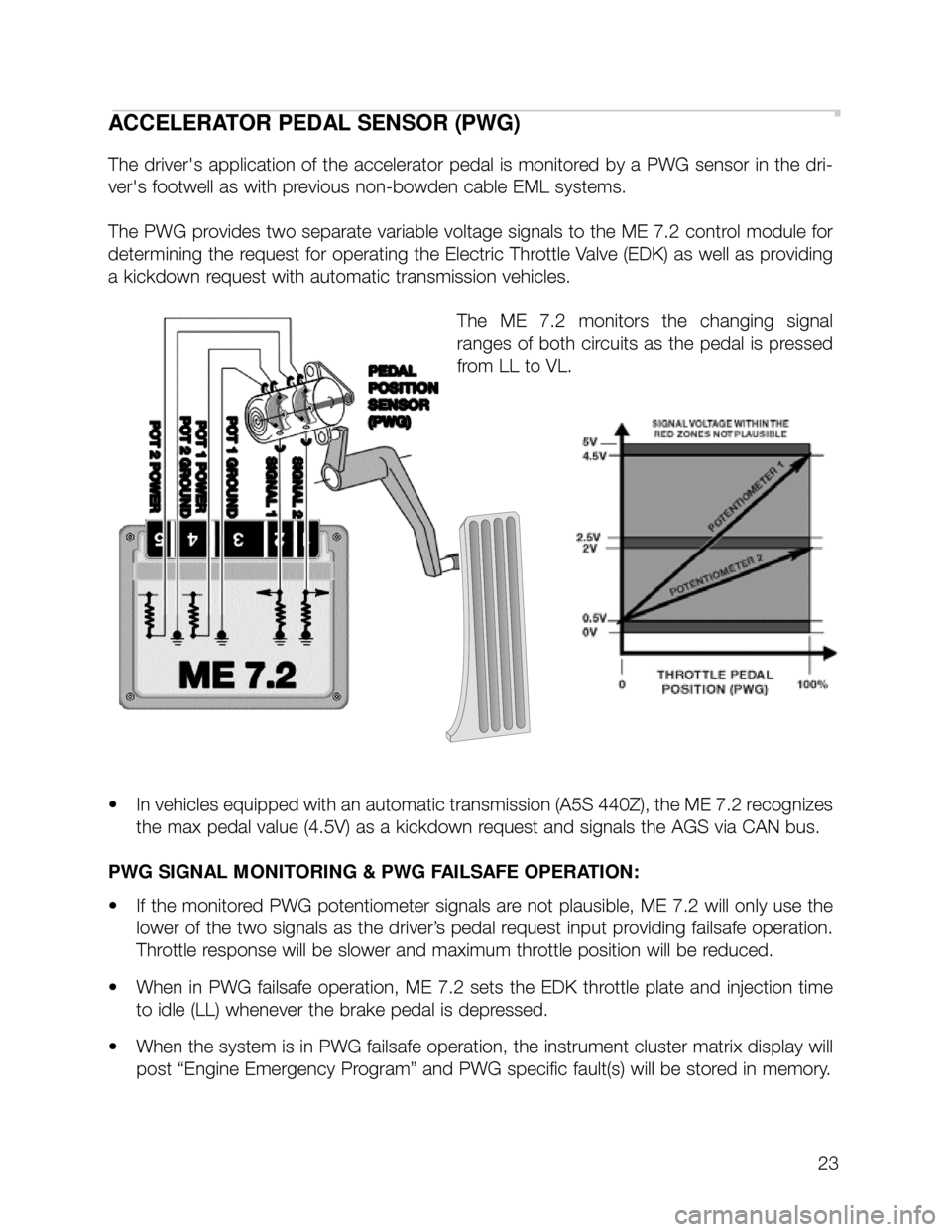
23
ACCELERATOR PEDAL SENSOR (PWG)
The driver's application of the accelerator pedal is monitored by a PWG sensor in the dri-
ver's footwell as with previous non-bowden cable EML systems.
The PWG provides two separate variable voltage signals to the ME 7.2 control module for
determining the request for operating the Electric Throttle Valve (EDK) as well as providing
a kickdown request with automatic transmission vehicles.
The ME 7.2 monitors the changing signal
ranges of both circuits as the pedal is pressed
from LL to VL.
• In vehicles equipped with an automatic transmission (A5S 440Z), the ME 7.2 recognizes
the max pedal value (4.5V) as a kickdown request and signals the AGS via CAN bus.
PWG SIGNAL MONITORING & PWG FAILSAFE OPERATION:
• If the monitored PWG potentiometer signals are not plausible, ME 7.2 will only use the
lower of the two signals as the driver’s pedal request input providing failsafe operation.
Throttle response will be slower and maximum throttle position will be reduced.
• When in PWG failsafe operation, ME 7.2 sets the EDK throttle plate and injection time
to idle (LL) whenever the brake pedal is depressed.
• When the system is in PWG failsafe operation, the instrument cluster matrix display will
post “Engine Emergency Program” and PWG specific fault(s) will be stored in memory.
Page 27 of 37
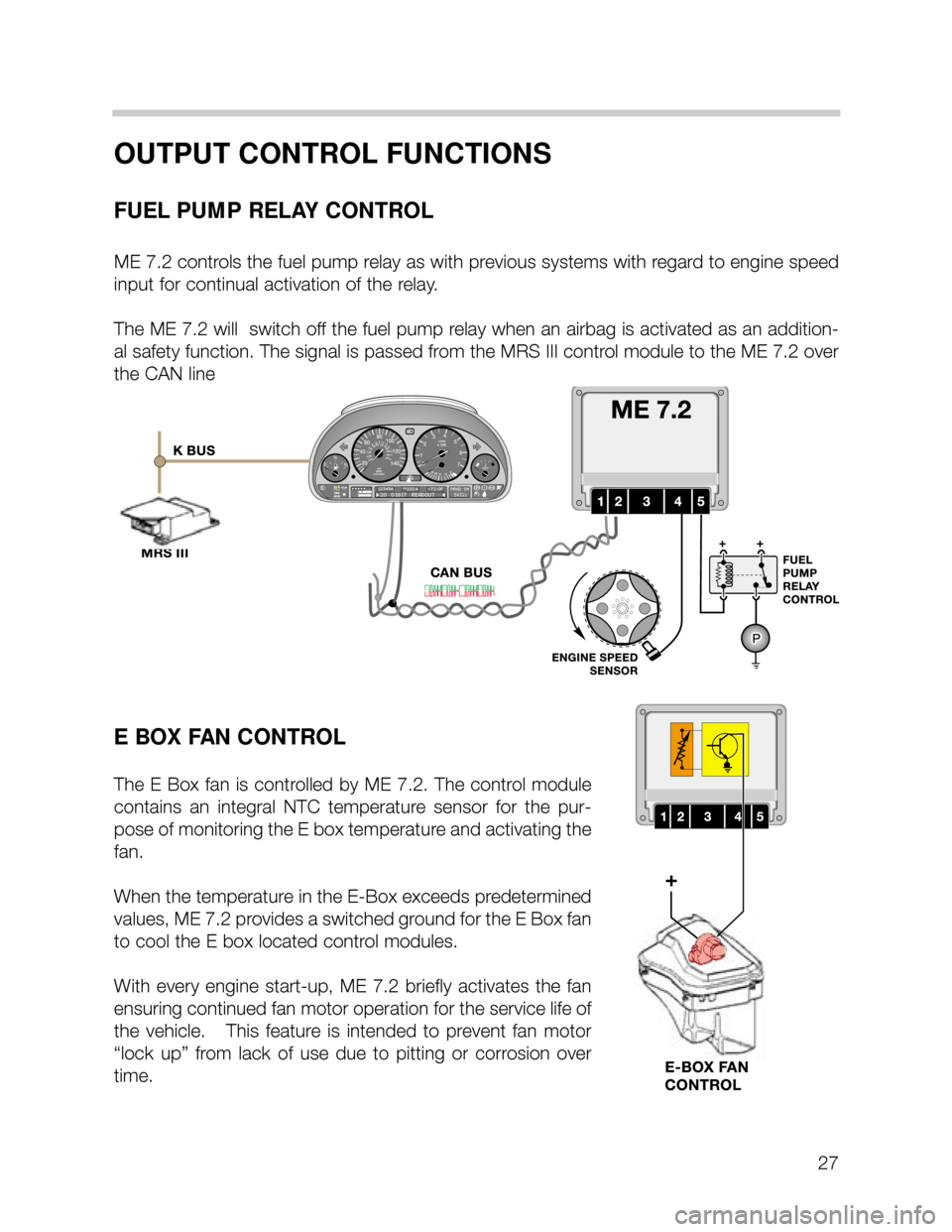
27
OUTPUT CONTROL FUNCTIONS
FUEL PUMP RELAY CONTROL
ME 7.2 controls the fuel pump relay as with previous systems with regard to engine speed
input for continual activation of the relay.
The ME 7.2 will switch off the fuel pump relay when an airbag is activated as an addition-
al safety function. The signal is passed from the MRS III control module to the ME 7.2 over
the CAN line
E BOX FAN CONTROL
The E Box fan is controlled by ME 7.2. The control module
contains an integral NTC temperature sensor for the pur-
pose of monitoring the E box temperature and activating the
fan.
When the temperature in the E-Box exceeds predetermined
values, ME 7.2 provides a switched ground for the E Box fan
to cool the E box located control modules.
With every engine start-up, ME 7.2 briefly activates the fan
ensuring continued fan motor operation for the service life of
the vehicle. This feature is intended to prevent fan motor
“lock up” from lack of use due to pitting or corrosion over
time.
Page 28 of 37
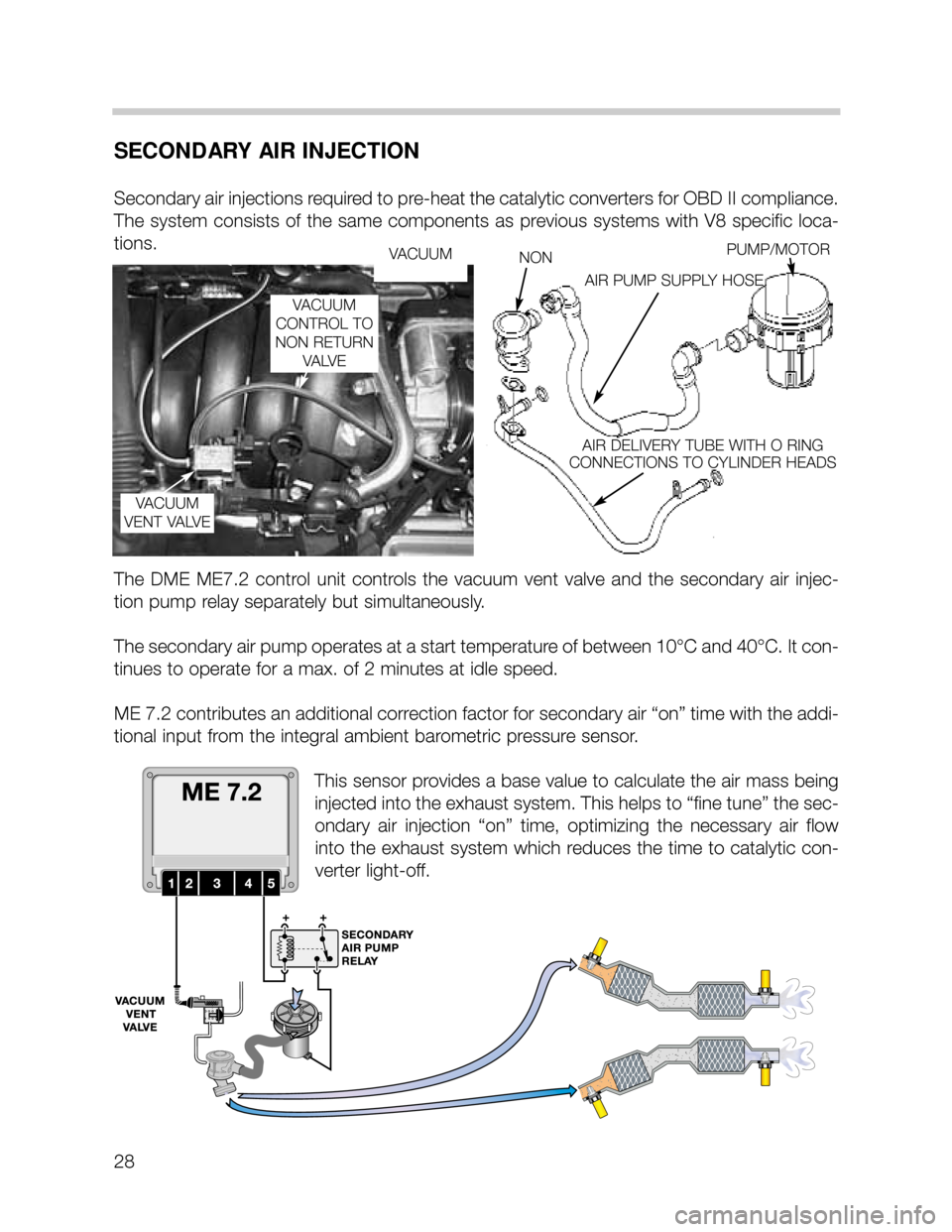
28
SECONDARY AIR INJECTION
Secondary air injections required to pre-heat the catalytic converters for OBD II compliance.
The system consists of the same components as previous systems with V8 specific loca-
tions.
The DME ME7.2 control unit controls the vacuum vent valve and the secondary air injec-
tion pump relay separately but simultaneously.
The secondary air pump operates at a start temperature of between 10°C and 40°C. It con-
tinues to operate for a max. of 2 minutes at idle speed.
ME 7.2 contributes an additional correction factor for secondary air “on” time with the addi-
tional input from the integral ambient barometric pressure sensor.
This sensor provides a base value to calculate the air mass being
injected into the exhaust system. This helps to “fine tune” the sec-
ondary air injection “on” time, optimizing the necessary air flow
into the exhaust system which reduces the time to catalytic con-
verter light-off.
VACUUM
VACUUM
VENT VALVENONPUMP/MOTOR
AIR PUMP SUPPLY HOSE
AIR DELIVERY TUBE WITH O RING
CONNECTIONS TO CYLINDER HEADS
VACUUM
CONTROL TO
NON RETURN
VA LV E