change time BMW X5 2002 E53 M54 Engine Workshop Manual
[x] Cancel search | Manufacturer: BMW, Model Year: 2002, Model line: X5, Model: BMW X5 2002 E53Pages: 48, PDF Size: 2.52 MB
Page 8 of 48
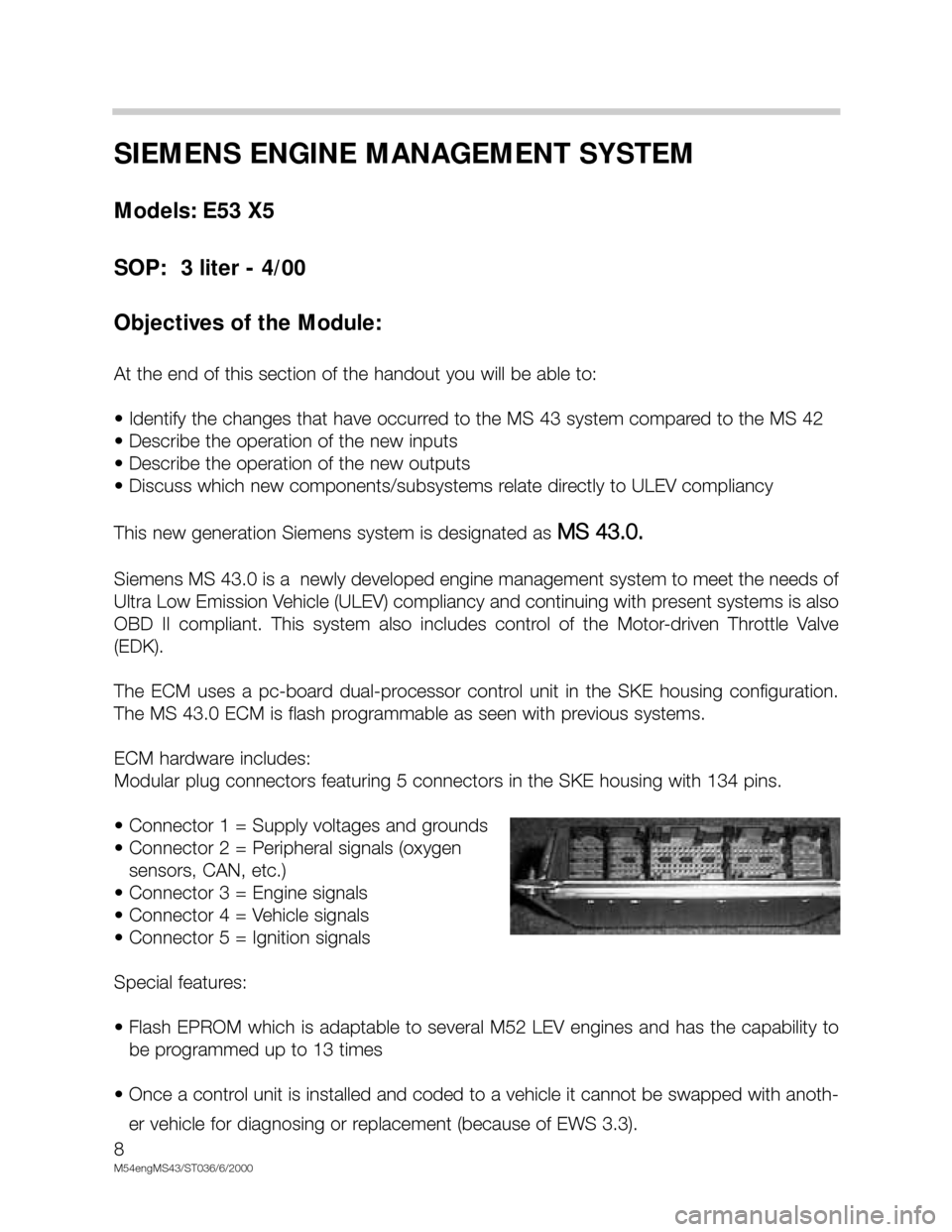
8
M54engMS43/ST036/6/2000
SIEMENS ENGINE MANAGEMENT SYSTEM
Models: E53 X5
SOP: 3 liter - 4/00
Objectives of the Module:
At the end of this section of the handout you will be able to:
• Identify the changes that have occurred to the MS 43 system compared to the MS 42
• Describe the operation of the new inputs
• Describe the operation of the new outputs
• Discuss which new components/subsystems relate directly to ULEV compliancy
This new generation Siemens system is designated as
MS 43.0.
Siemens MS 43.0 is a newly developed engine management system to meet the needs of
Ultra Low Emission Vehicle (ULEV) compliancy and continuing with present systems is also
OBD II compliant. This system also includes control of the Motor-driven Throttle Valve
(EDK).
The ECM uses a pc-board dual-processor control unit in the SKE housing configuration.
The MS 43.0 ECM is flash programmable as seen with previous systems.
ECM hardware includes:
Modular plug connectors featuring 5 connectors in the SKE housing with 134 pins.
• Connector 1 = Supply voltages and grounds
• Connector 2 = Peripheral signals (oxygen
sensors, CAN, etc.)
• Connector 3 = Engine signals
• Connector 4 = Vehicle signals
• Connector 5 = Ignition signals
Special features:
• Flash EPROM which is adaptable to several M52 LEV engines and has the capability to
be programmed up to 13 times
• Once a control unit is installed and coded to a vehicle it cannot be swapped with anoth-
er vehicle for diagnosing or replacement (because of EWS 3.3).
Page 22 of 48
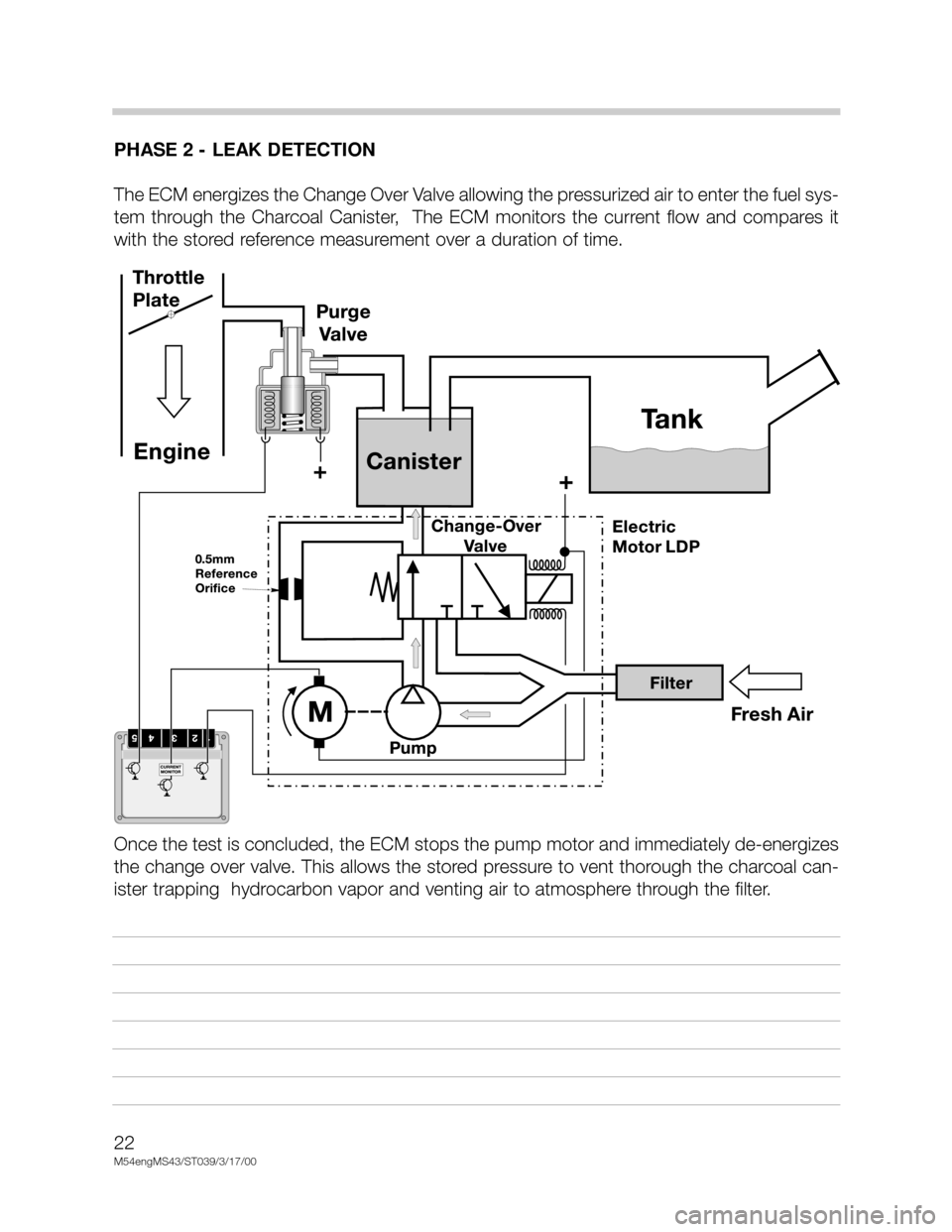
22
M54engMS43/ST039/3/17/00
PHASE 2 - LEAK DETECTION
The ECM energizes the Change Over Valve allowing the pressurized air to enter the fuel sys-
tem through the Charcoal Canister, The ECM monitors the current flow and compares it
with the stored reference measurement over a duration of time.
Once the test is concluded, the ECM stops the pump motor and immediately de-energizes
the change over valve. This allows the stored pressure to vent thorough the charcoal can-
ister trapping hydrocarbon vapor and venting air to atmosphere through the filter.
Page 37 of 48
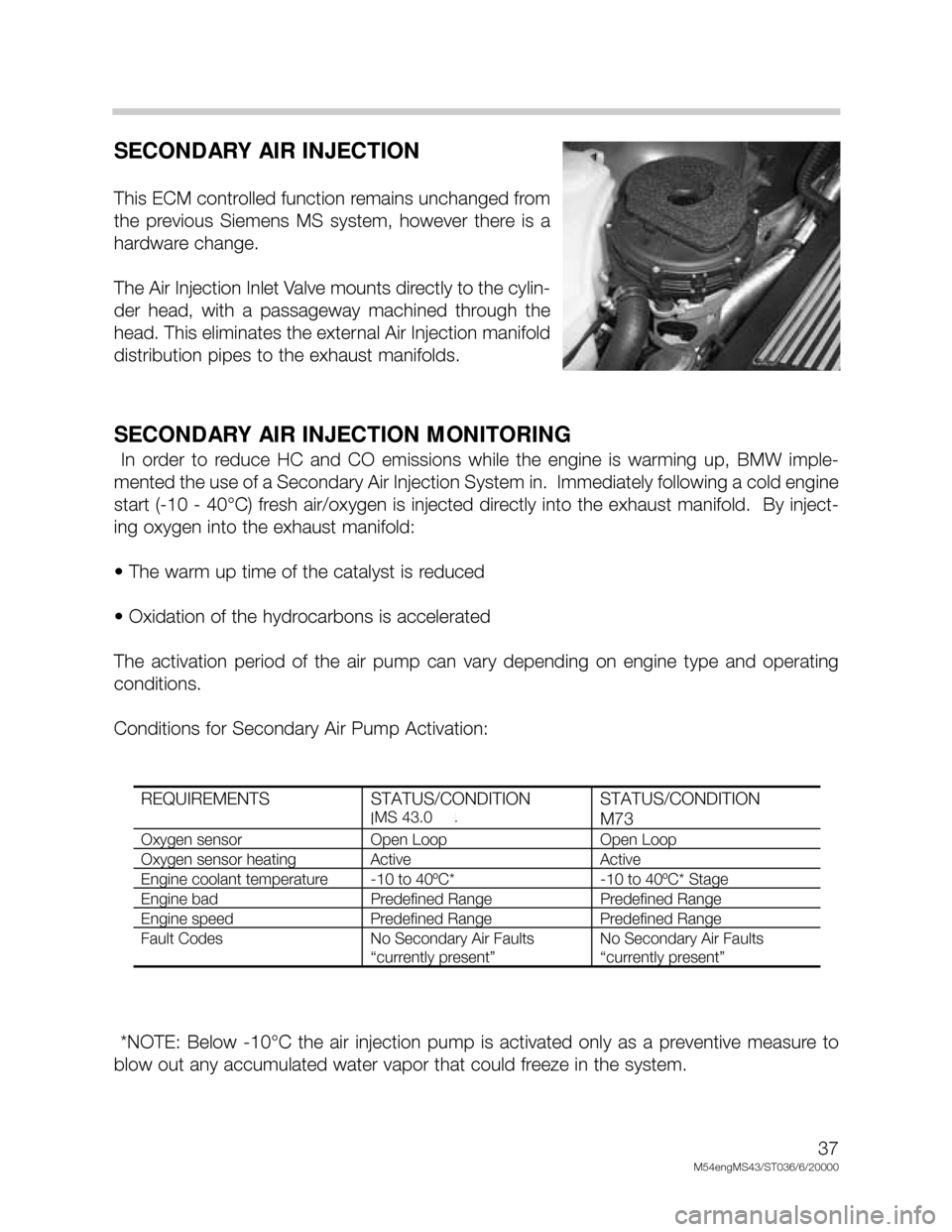
37
M54engMS43/ST036/6/20000
SECONDARY AIR INJECTION
This ECM controlled function remains unchanged from
the previous Siemens MS system, however there is a
hardware change.
The Air Injection Inlet Valve mounts directly to the cylin-
der head, with a passageway machined through the
head. This eliminates the external Air Injection manifold
distribution pipes to the exhaust manifolds.
SECONDARY AIR INJECTION MONITORING
In order to reduce HC and CO emissions while the engine is warming up, BMW imple-
mented the use of a Secondary Air Injection System in. Immediately following a cold engine
start (-10 - 40°C) fresh air/oxygen is injected directly into the exhaust manifold. By inject-
ing oxygen into the exhaust manifold:
• The warm up time of the catalyst is reduced
• Oxidation of the hydrocarbons is accelerated
The activation period of the air pump can vary depending on engine type and operating
conditions.
Conditions for Secondary Air Pump Activation:
*NOTE: Below -10°C the air injection pump is activated only as a preventive measure to
blow out any accumulated water vapor that could freeze in the system.
REQUIREMENTS STATUS/CONDITION
M52 & M44STATUS/CONDITION
M73
Oxygen sensor Open Loop Open Loop
Oxygen sensor heating Active Active
Engine coolant temperature -10 to 40ºC* -10 to 40ºC* Stage
Engine bad Predefined Range Predefined Range
Engine speed Predefined Range Predefined Range
Fault Codes No Secondary Air Faults
“currently present”
No Secondary Air Faults
“currently present”
MS 43.0
Page 38 of 48
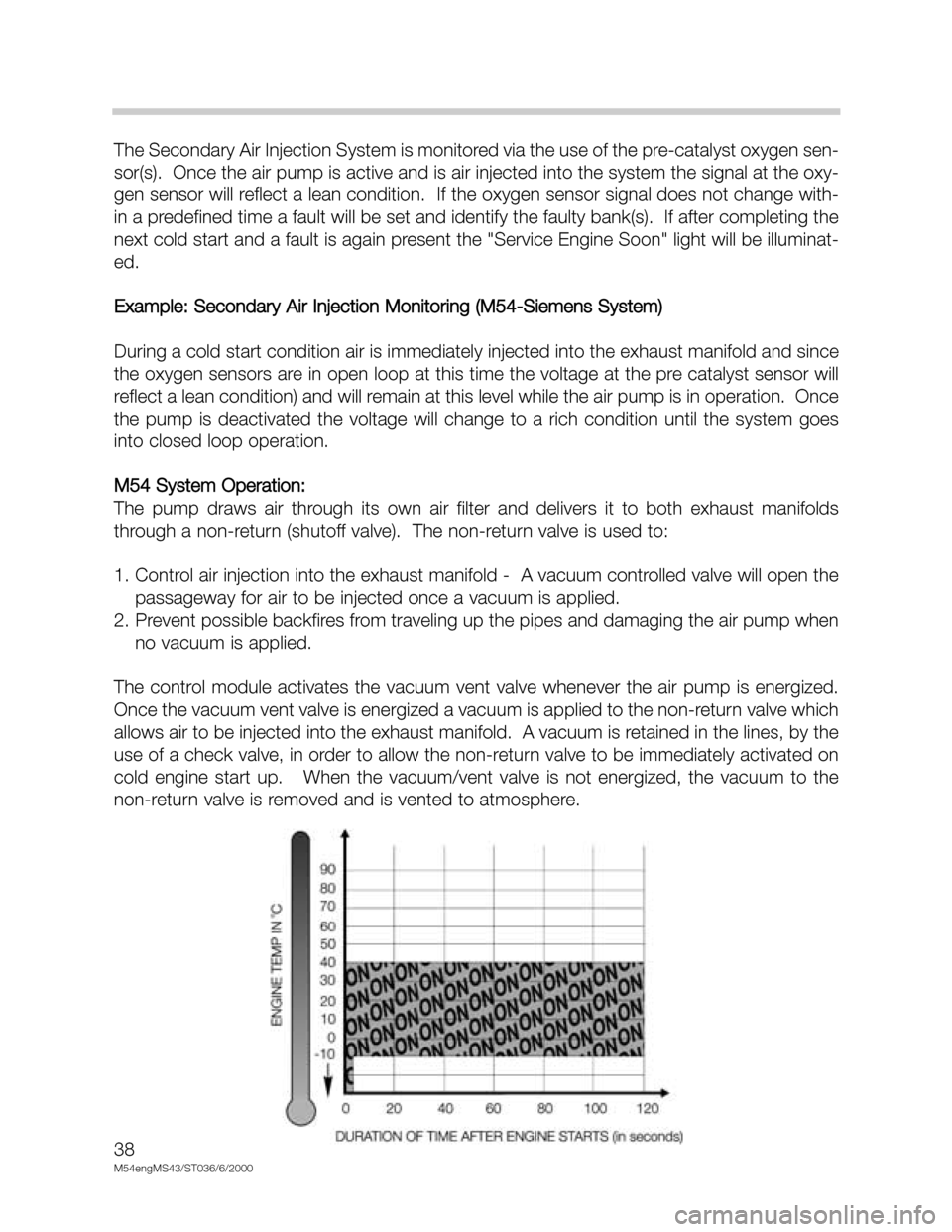
38
M54engMS43/ST036/6/2000
The Secondary Air Injection System is monitored via the use of the pre-catalyst oxygen sen-
sor(s). Once the air pump is active and is air injected into the system the signal at the oxy-
gen sensor will reflect a lean condition. If the oxygen sensor signal does not change with-
in a predefined time a fault will be set and identify the faulty bank(s). If after completing the
next cold start and a fault is again present the "Service Engine Soon" light will be illuminat-
ed.
Example: Secondary Air Injection Monitoring (M54-Siemens System)
During a cold start condition air is immediately injected into the exhaust manifold and since
the oxygen sensors are in open loop at this time the voltage at the pre catalyst sensor will
reflect a lean condition) and will remain at this level while the air pump is in operation. Once
the pump is deactivated the voltage will change to a rich condition until the system goes
into closed loop operation.
M54 System Operation:
The pump draws air through its own air filter and delivers it to both exhaust manifolds
through a non-return (shutoff valve). The non-return valve is used to:
1. Control air injection into the exhaust manifold - A vacuum controlled valve will open the
passageway for air to be injected once a vacuum is applied.
2. Prevent possible backfires from traveling up the pipes and damaging the air pump when
no vacuum is applied.
The control module activates the vacuum vent valve whenever the air pump is energized.
Once the vacuum vent valve is energized a vacuum is applied to the non-return valve which
allows air to be injected into the exhaust manifold. A vacuum is retained in the lines, by the
use of a check valve, in order to allow the non-return valve to be immediately activated on
cold engine start up. When the vacuum/vent valve is not energized, the vacuum to the
non-return valve is removed and is vented to atmosphere.