ignition BMW X5 2002 E53 M62TU Engine Workshop Manual
[x] Cancel search | Manufacturer: BMW, Model Year: 2002, Model line: X5, Model: BMW X5 2002 E53Pages: 37, PDF Size: 3.87 MB
Page 19 of 37
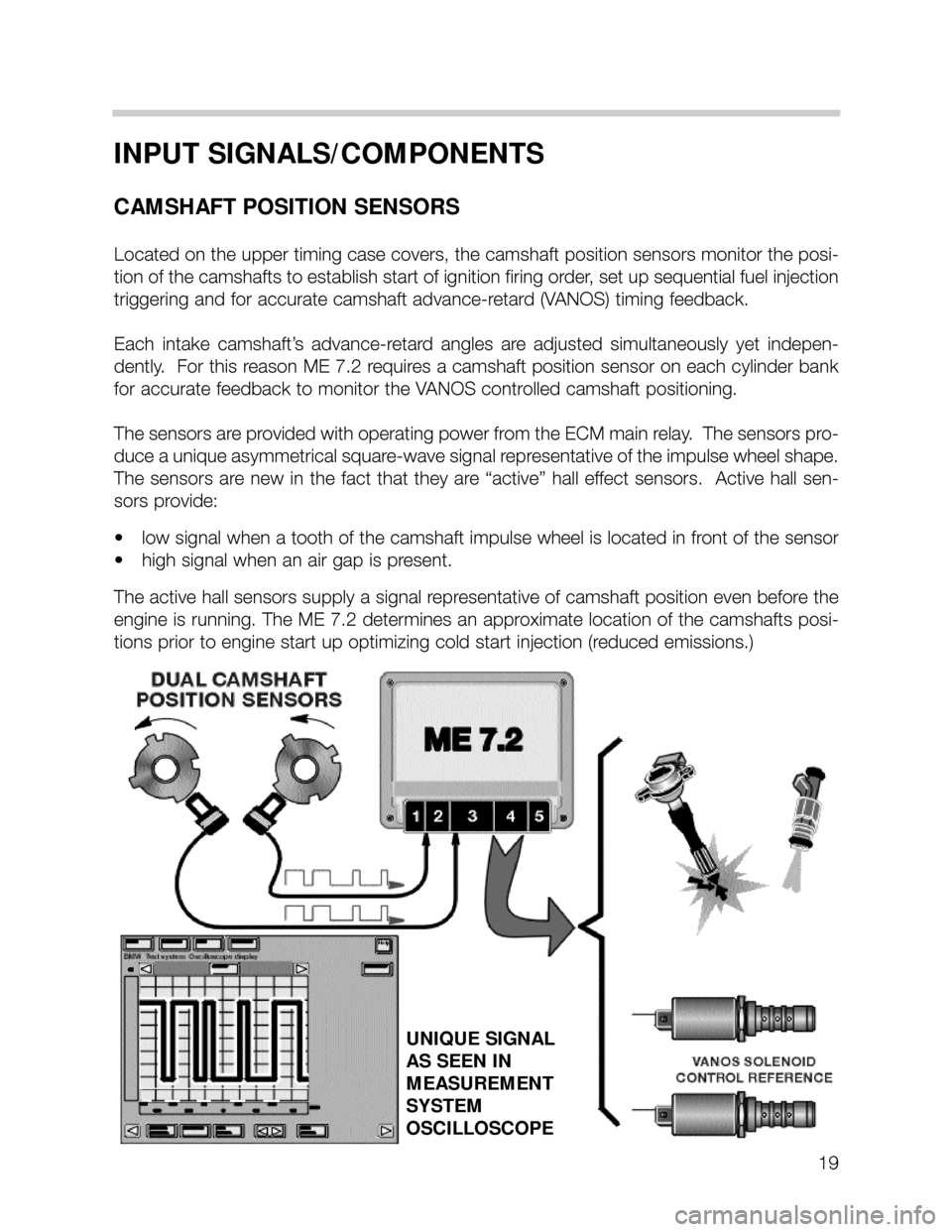
19
INPUT SIGNALS/COMPONENTS
CAMSHAFT POSITION SENSORS
Located on the upper timing case covers, the camshaft position sensors monitor the posi-
tion of the camshafts to establish start of ignition firing order, set up sequential fuel injection
triggering and for accurate camshaft advance-retard (VANOS) timing feedback.
Each intake camshaft’s advance-retard angles are adjusted simultaneously yet indepen-
dently. For this reason ME 7.2 requires a camshaft position sensor on each cy linder bank
for accurate feedback to monitor the VANOS controlled camshaft positioning.
The sensors are provided with operating power from the ECM main relay. The sensors pro-
duce a unique asymmetrical square-wave signal representative of the impulse wheel shape.
The sensors are new in the fact that they are “active” hall effect sensors. Active hall sen-
sors provide:
• low signal when a tooth of the camshaft impulse wheel is located in front of the sensor
• high signal when an air gap is present.
The active hall sensors supply a signal representative of camshaft position even before the
engine is running. The ME 7.2 determines an approximate location of the camshafts posi-
tions prior to engine start up optimizing cold start injection (reduced emissions.)
UNIQUE SIGNAL
AS SEEN IN
MEASUREMENT
SYSTEM
OSCILLOSCOPE
Page 30 of 37
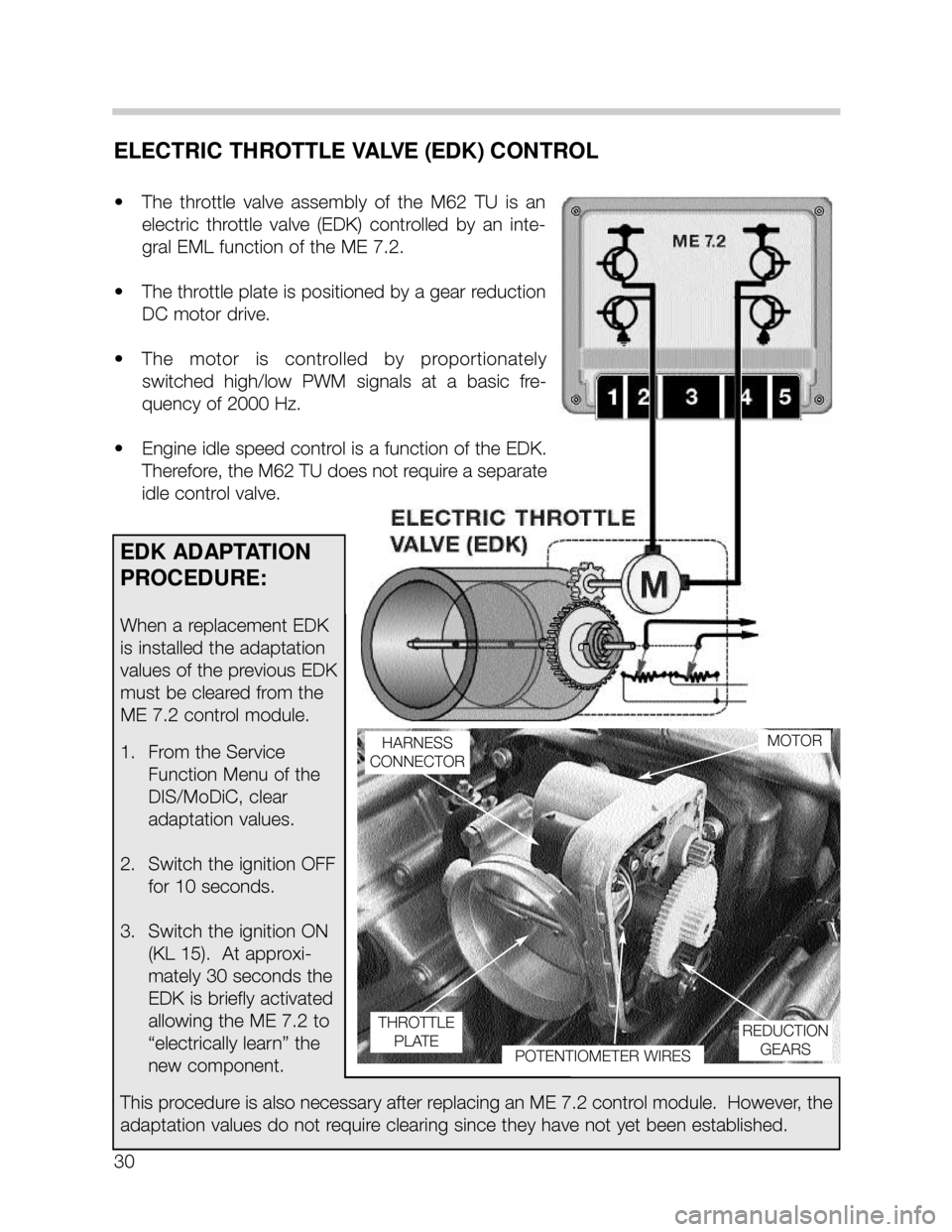
30
ELECTRIC THROTTLE VALVE (EDK) CONTROL
• The throttle valve assembly of the M62 TU is an
electric throttle valve (EDK) controlled by an inte-
gral EML function of the ME 7.2.
• The throttle plate is positioned by a gear reduction
DC motor drive.
• The motor is controlled by proportionately
switched high/low PWM signals at a basic fre-
quency of 2000 Hz.
• Engine idle speed control is a function of the EDK.
Therefore, the M62 TU does not require a separate
idle control valve.
HARNESS
CONNECTORMOTOR
REDUCTION
GEARS
POTENTIOMETER WIRES
THROTTLE
PLATE
EDK ADAPTATION
PROCEDURE:
When a replacement EDK
is installed the adaptation
values of the previous EDK
must be cleared from the
ME 7.2 control module.
1. From the Service
Function Menu of the
DIS/MoDiC, clear
adaptation values.
2. Switch the ignition OFF
for 10 seconds.
3. Switch the ignition ON
(KL 15). At approxi-
mately 30 seconds the
EDK is briefly activated
allowing the ME 7.2 to
“electrically learn” the
new component.
This procedure is also necessary after replacing an ME 7.2 control module. However, the
adaptation values do not require clearing since they have not yet been established.
Page 34 of 37
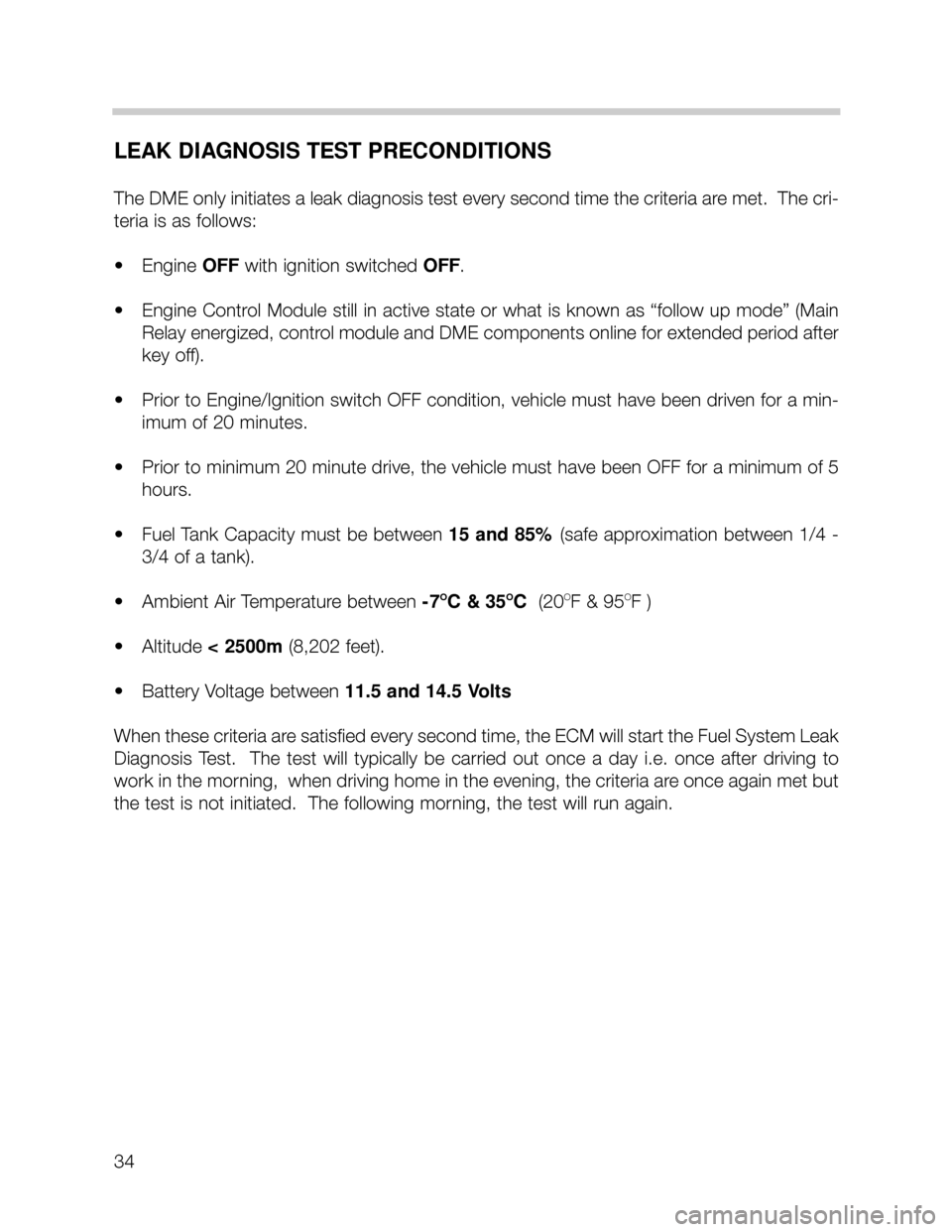
LEAK DIAGNOSIS TEST PRECONDITIONS
The DME only initiates a leak diagnosis test every second time the criteria are met. The cri-
teria is as follows:
• Engine OFF with ignition switched OFF.
• Engine Control Module still in active state or what is known as “follow up mode” (Main
Relay energized, control module and DME components online for extended period after
key off).
• Prior to Engine/Ignition switch OFF condition, vehicle must have been driven for a min-
imum of 20 minutes.
• Prior to minimum 20 minute drive, the vehicle must have been OFF for a minimum of 5
hours.
• Fuel Tank Capacity must be between 15 and 85%(safe approximation between 1/4 -
3/4 of a tank).
• Ambient Air Temperature between -7
OC & 35OC(20OF & 95OF )
• Altitude < 2500m(8,202 feet).
• Battery Voltage between 11.5 and 14.5 Volts
When these criteria are satisfied every second time, the ECM will start the Fuel System Leak
Diagnosis Test. The test will typically be carried out once a day i.e. once after driving to
work in the morning, when driving home in the evening, the criteria are once again met but
the test is not initiated. The following morning, the test will run again.
34