Edk BMW X5 2003 E53 M62TU Engine Workshop Manual
[x] Cancel search | Manufacturer: BMW, Model Year: 2003, Model line: X5, Model: BMW X5 2003 E53Pages: 37, PDF Size: 3.87 MB
Page 1 of 37
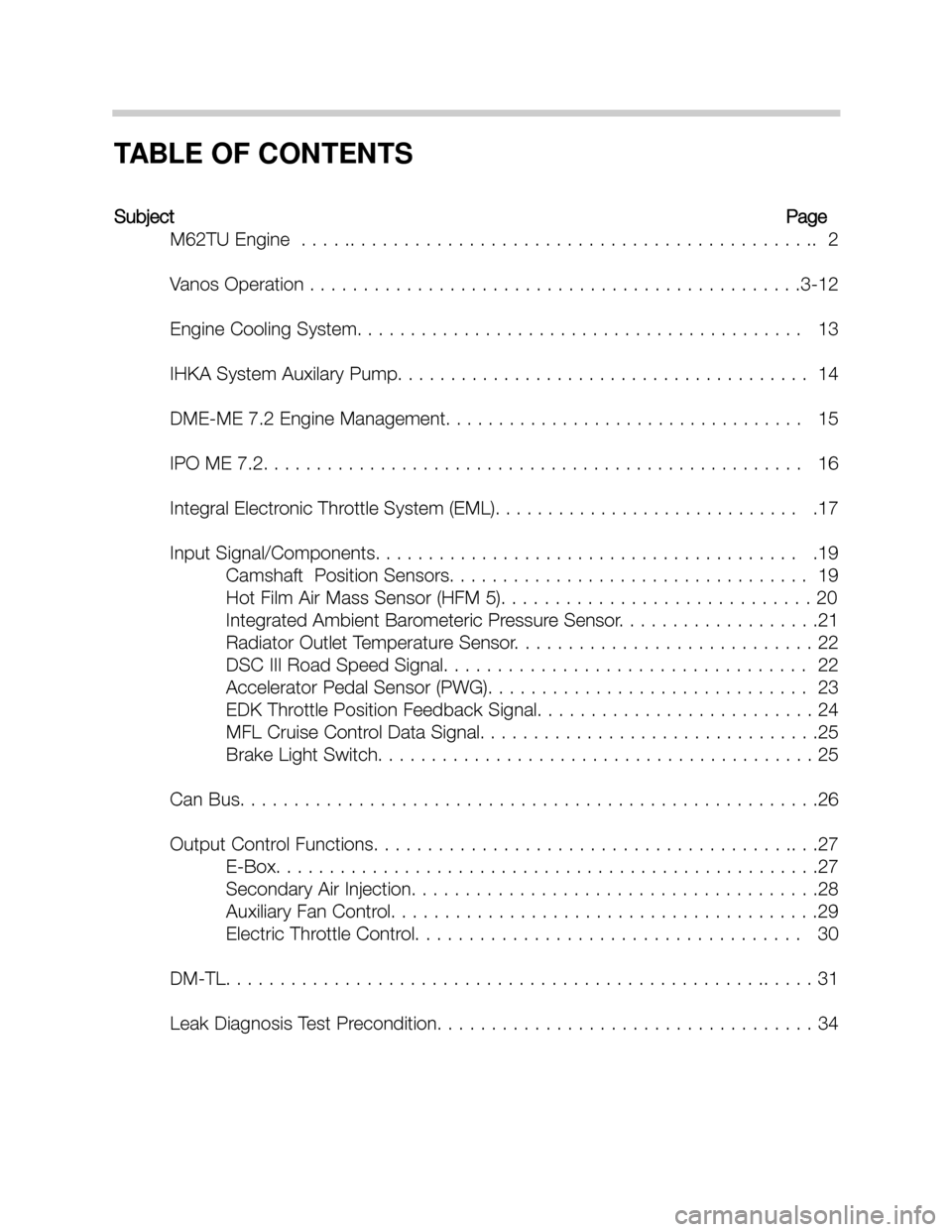
TABLE OF CONTENTS
SubjectPage
M62TU Engine . . . . .. . . . . . . . . . . . . . . . . . . . . . . . . . . . . . . . . . . . . . . . . . .. 2
Vanos Operation . . . . . . . . . . . . . . . . . . . . . . . . . . . . . . . . . . . . . . . . . . . . . .3-12
Engine Cooling System. . . . . . . . . . . . . . . . . . . . . . . . . . . . . . . . . . . . . . . . . . 13
IHKA System Auxilary Pump. . . . . . . . . . . . . . . . . . . . . . . . . . . . . . . . . . . . . . . 14
DME-ME 7.2 Engine Management. . . . . . . . . . . . . . . . . . . . . . . . . . . . . . . . . . 15
IPO ME 7.2. . . . . . . . . . . . . . . . . . . . . . . . . . . . . . . . . . . . . . . . . . . . . . . . . . . 16
Integral Electronic Throttle System (EML). . . . . . . . . . . . . . . . . . . . . . . . . . . . . .17
Input Signal/Components. . . . . . . . . . . . . . . . . . . . . . . . . . . . . . . . . . . . . . . . .19
Camshaft Position Sensors. . . . . . . . . . . . . . . . . . . . . . . . . . . . . . . . . . 19
Hot Film Air Mass Sensor (HFM 5). . . . . . . . . . . . . . . . . . . . . . . . . . . . . 20
Integrated Ambient Barometeric Pressure Sensor. . . . . . . . . . . . . . . . . . .21
Radiator Outlet Temperature Sensor. . . . . . . . . . . . . . . . . . . . . . . . . . . . 22
DSC III Road Speed Signal. . . . . . . . . . . . . . . . . . . . . . . . . . . . . . . . . . 22
Accelerator Pedal Sensor (PWG). . . . . . . . . . . . . . . . . . . . . . . . . . . . . . 23
EDK Throttle Position Feedback Signal. . . . . . . . . . . . . . . . . . . . . . . . . . 24
MFL Cruise Control Data Signal. . . . . . . . . . . . . . . . . . . . . . . . . . . . . . . .25
Brake Light Switch. . . . . . . . . . . . . . . . . . . . . . . . . . . . . . . . . . . . . . . . . 25
Can Bus. . . . . . . . . . . . . . . . . . . . . . . . . . . . . . . . . . . . . . . . . . . . . . . . . . . . . .26
Output Control Functions. . . . . . . . . . . . . . . . . . . . . . . . . . . . . . . . . . . . . . .. . .27
E-Box. . . . . . . . . . . . . . . . . . . . . . . . . . . . . . . . . . . . . . . . . . . . . . . . . . .27
Secondary Air Injection. . . . . . . . . . . . . . . . . . . . . . . . . . . . . . . . . . . . . .28
Auxiliary Fan Control. . . . . . . . . . . . . . . . . . . . . . . . . . . . . . . . . . . . . . . .29
Electric Throttle Control. . . . . . . . . . . . . . . . . . . . . . . . . . . . . . . . . . . . 30
DM-TL. . . . . . . . . . . . . . . . . . . . . . . . . . . . . . . . . . . . . . . . . . . . . . . . . .. . . . . 31
Leak Diagnosis Test Precondition. . . . . . . . . . . . . . . . . . . . . . . . . . . . . . . . . . . 34
Page 2 of 37
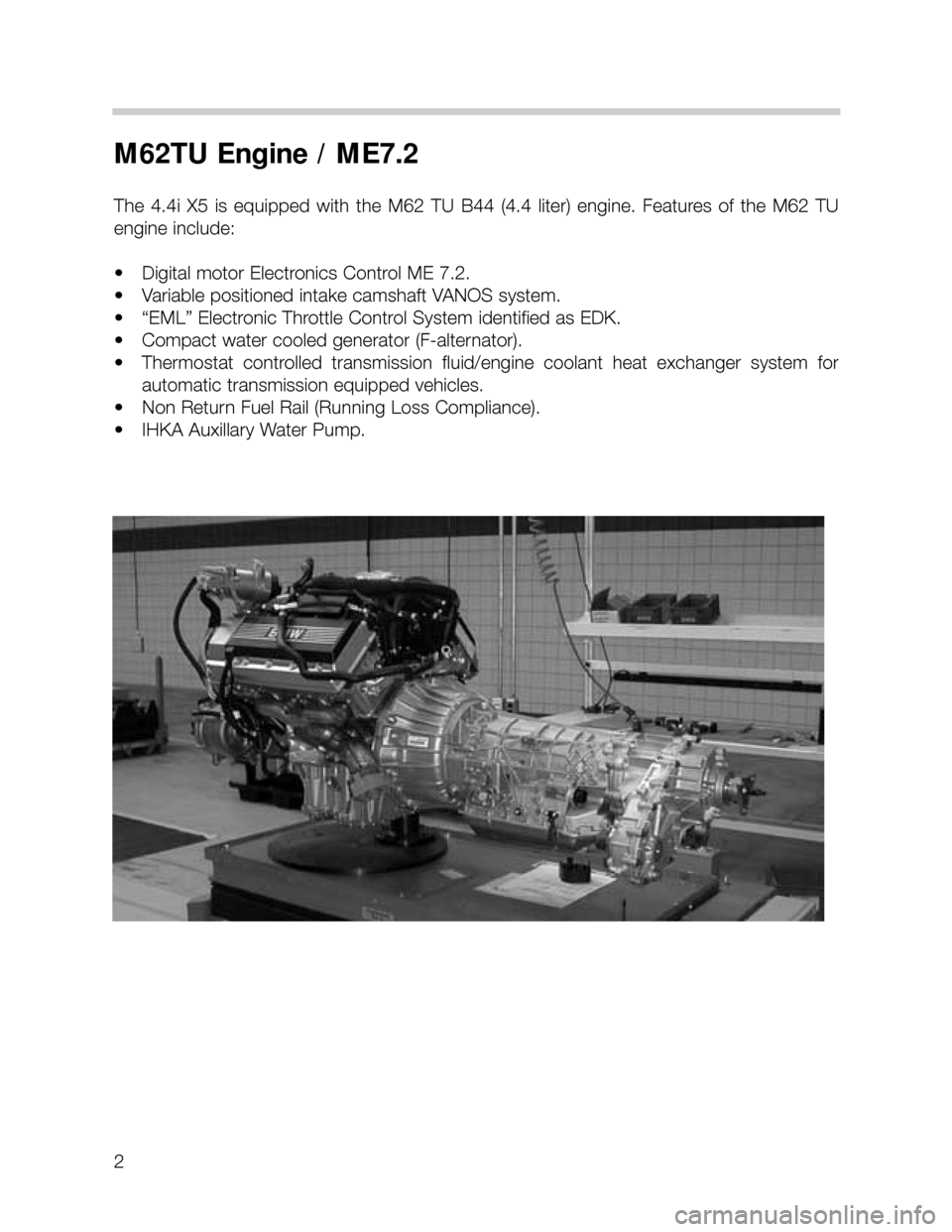
2
M62TU Engine / ME7.2
The 4.4i X5 is equipped with the M62 TU B44 (4.4 liter) engine. Features of the M62 TU
engine include:
• Digital motor Electronics Control ME 7.2.
• Variable positioned intake camshaft VANOS system.
• “EML” Electronic Throttle Control System identified as EDK.
• Compact water cooled generator (F-alternator).
• Thermostat controlled transmission fluid/engine coolant heat exchanger system for
automatic transmission equipped vehicles.
• Non Return Fuel Rail (Running Loss Compliance).
• IHKA Auxillary Water Pump.
Page 15 of 37
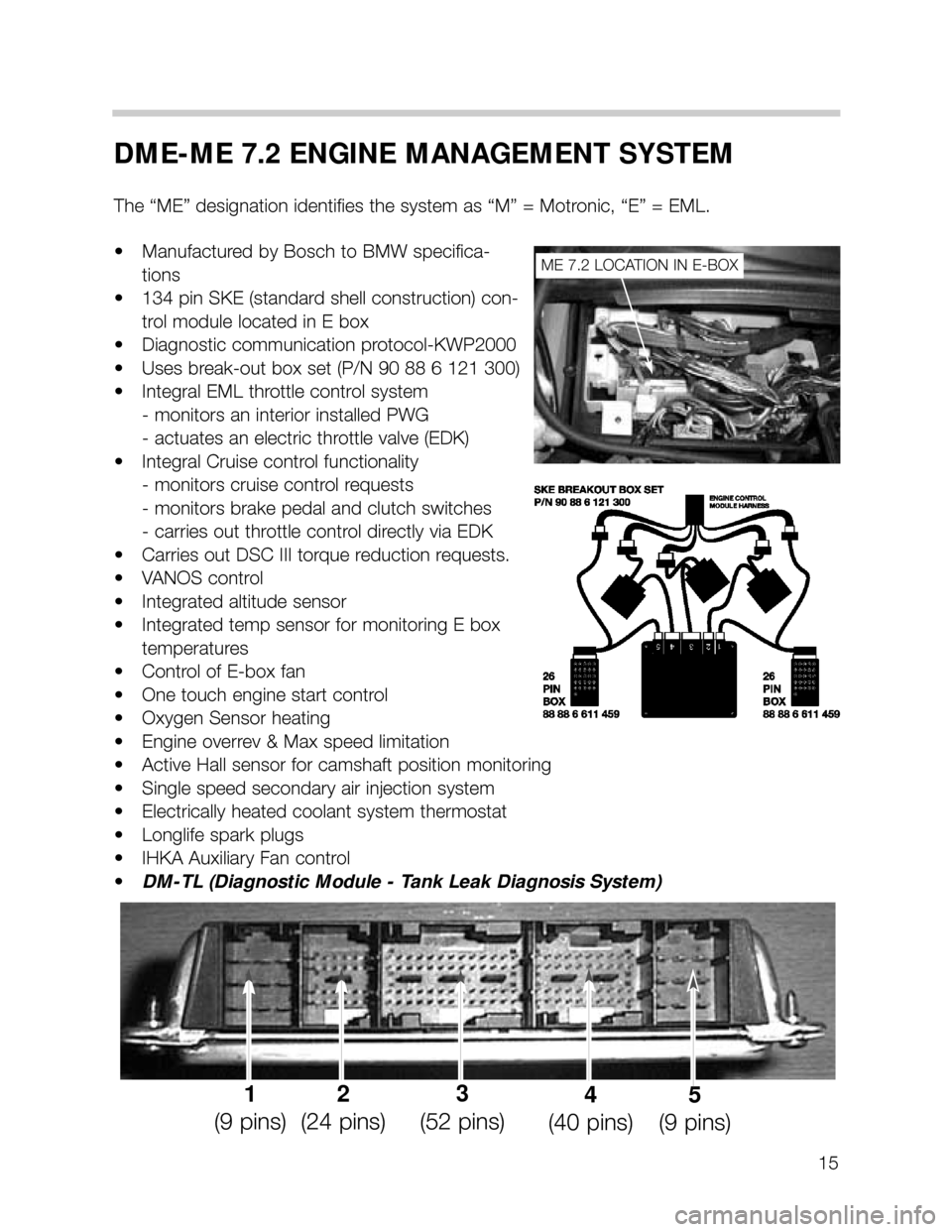
15
DME-ME 7.2 ENGINE MANAGEMENT SYSTEM
The “ME” designation identifies the system as “M” = Motronic, “E” = EML.
• Manufactured by Bosch to BMW specifica-
tions
• 134 pin SKE (standard shell construction) con-
trol module located in E box
• Diagnostic communication protocol-KWP2000
• Uses break-out box set (P/N 90 88 6 121 300)
• Integral EML throttle control system
- monitors an interior installed PWG
- actuates an electric throttle valve (EDK)
• Integral Cruise control functionality
- monitors cruise control requests
- monitors brake pedal and clutch switches
- carries out throttle control directly via EDK
• Carries out DSC III torque reduction requests.
• VANOS control
• Integrated altitude sensor
• Integrated temp sensor for monitoring E box
temperatures
• Control of E-box fan
• One touch engine start control
• Oxygen Sensor heating
• Engine overrev & Max speed limitation
• Active Hall sensor for camshaft position monitoring
• Single speed secondary air injection system
• Electrically heated coolant system thermostat
• Longlife spark plugs
• IHKA Auxiliary Fan control
•DM-TL (Diagnostic Module - Tank Leak Diagnosis System)
ME 7.2 LOCATION IN E-BOX
1
(9 pins)2
(24 pins)3
(52 pins)4
(40 pins)5
(9 pins)
Page 17 of 37
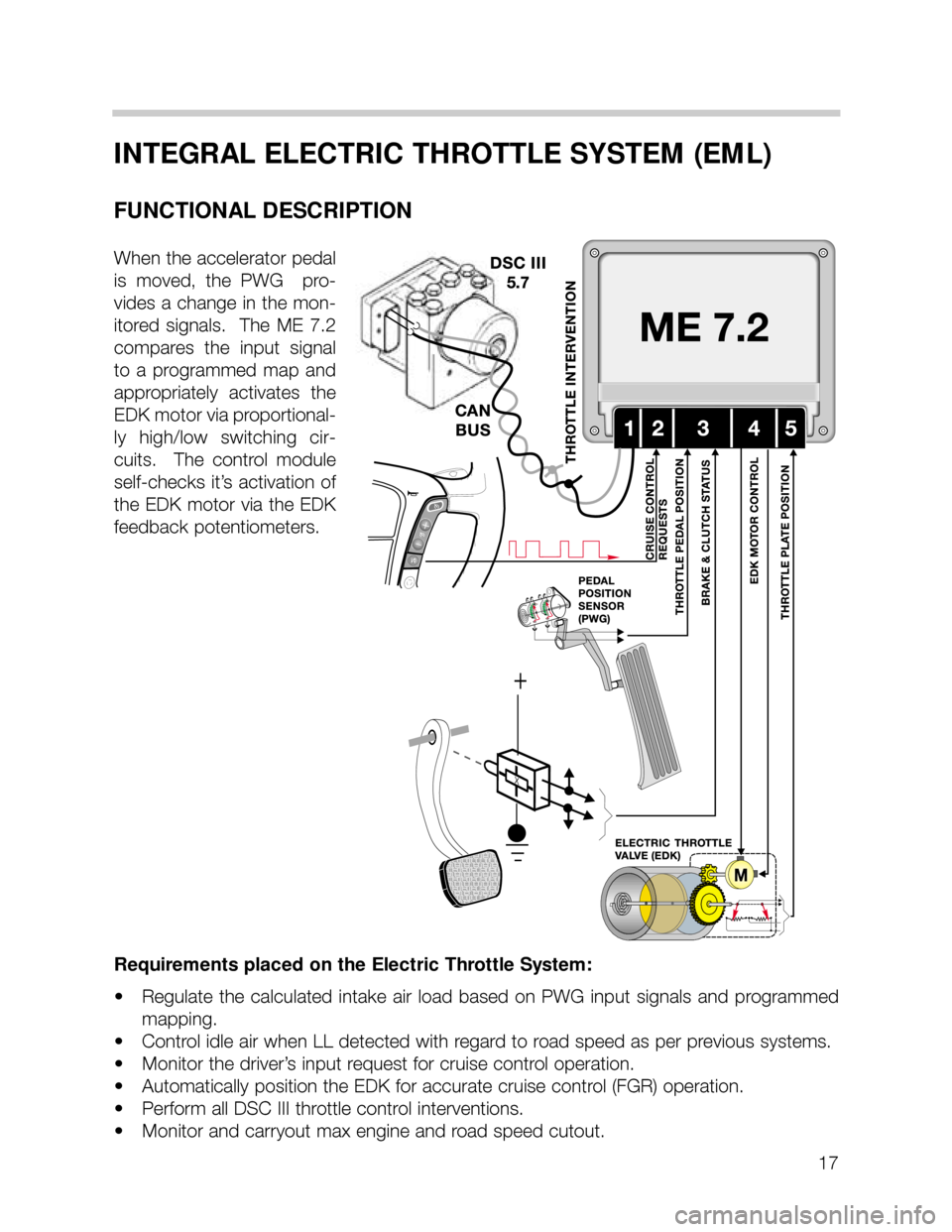
17
INTEGRAL ELECTRIC THROTTLE SYSTEM (EML)
FUNCTIONAL DESCRIPTION
When the accelerator pedal
is moved, the PWG pro-
vides a change in the mon-
itored signals. The ME 7.2
compares the input signal
to a programmed map and
appropriately activates the
EDK motor via proportional-
ly high/low switching cir-
cuits. The control module
self-checks it’s activation of
the EDK motor via the EDK
feedback potentiometers.
Requirements placed on the Electric Throttle System:
• Regulate the calculated intake air load based on PWG input signals and programmed
mapping.
• Control idle air when LL detected with regard to road speed as per previous systems.
• Monitor the driver’s input request for cruise control operation.
• Automatically position the EDK for accurate cruise control (FGR) operation.
• Perform all DSC III throttle control interventions.
• Monitor and carryout max engine and road speed cutout.
Page 18 of 37
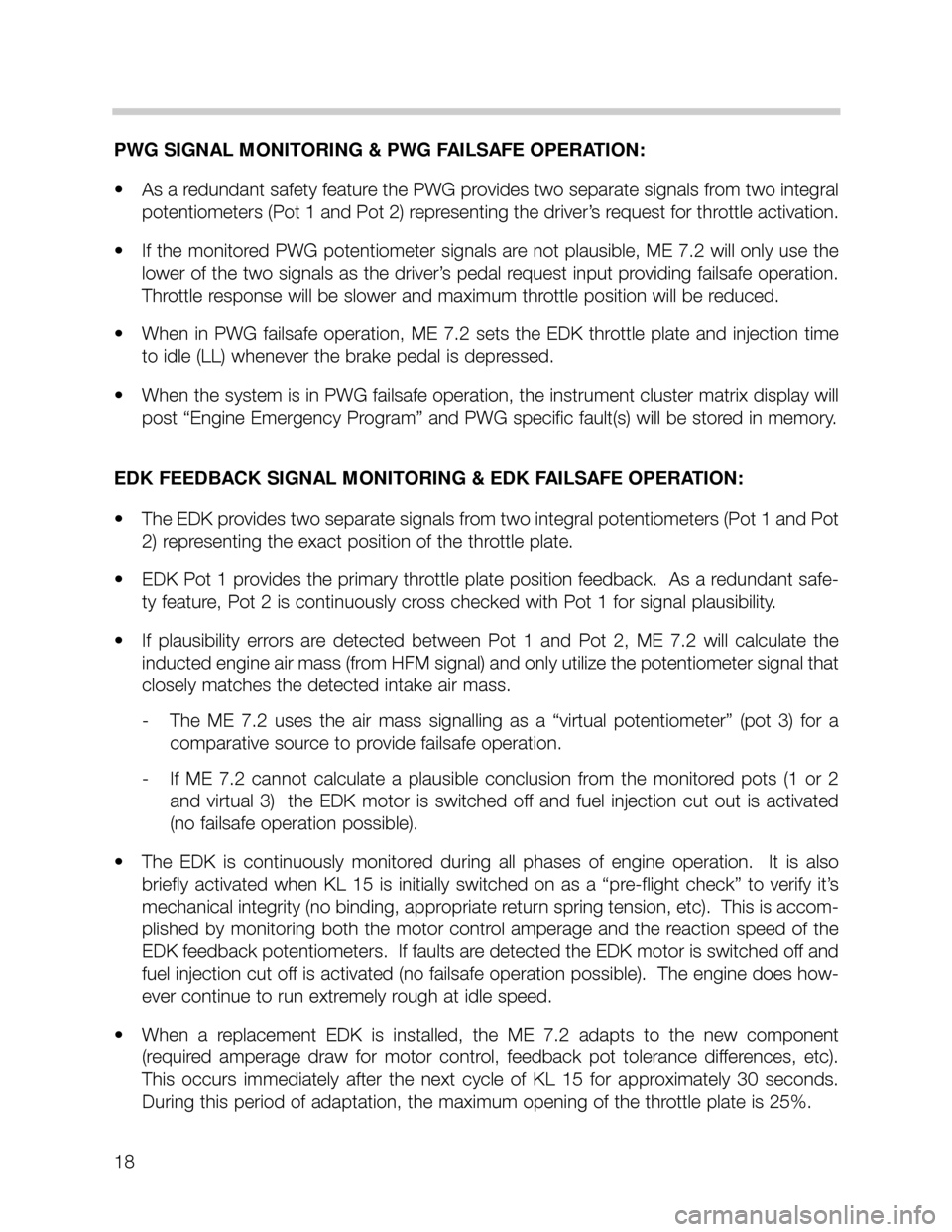
18
PWG SIGNAL MONITORING & PWG FAILSAFE OPERATION:
• As a redundant safety feature the PWG provides two separate signals from two integral
potentiometers (Pot 1 and Pot 2) representing the driver’s request for throttle activation.
• If the monitored PWG potentiometer signals are not plausible, ME 7.2 will only use the
lower of the two signals as the driver’s pedal request input providing failsafe operation.
Throttle response will be slower and maximum throttle position will be reduced.
• When in PWG failsafe operation, ME 7.2 sets the EDK throttle plate and injection time
to idle (LL) whenever the brake pedal is depressed.
• When the system is in PWG failsafe operation, the instrument cluster matrix display will
post “Engine Emergency Program” and PWG specific fault(s) will be stored in memory.
EDK FEEDBACK SIGNAL MONITORING & EDK FAILSAFE OPERATION:
• The EDK provides two separate signals from two integral potentiometers (Pot 1 and Pot
2) representing the exact position of the throttle plate.
• EDK Pot 1 provides the primary throttle plate position feedback. As a redundant safe-
ty feature, Pot 2 is continuously cross checked with Pot 1 for signal plausibility.
• If plausibility errors are detected between Pot 1 and Pot 2, ME 7.2 will calculate the
inducted engine air mass (from HFM signal) and only utilize the potentiometer signal that
closely matches the detected intake air mass.
- The ME 7.2 uses the air mass signalling as a “virtual potentiometer” (pot 3) for a
comparative source to provide failsafe operation.
- If ME 7.2 cannot calculate a plausible conclusion from the monitored pots (1 or 2
and virtual 3) the EDK motor is switched off and fuel injection cut out is activated
(no failsafe operation possible).
• The EDK is continuously monitored during all phases of engine operation. It is also
briefly activated when KL 15 is initially switched on as a “pre-flight check” to verify it’s
mechanical integrity (no binding, appropriate return spring tension, etc). This is accom-
plished by monitoring both the motor control amperage and the reaction speed of the
EDK feedback potentiometers. If faults are detected the EDK motor is switched off and
fuel injection cut off is activated (no failsafe operation possible). The engine does how-
ever continue to run extremely rough at idle speed.
• When a replacement EDK is installed, the ME 7.2 adapts to the new component
(required amperage draw for motor control, feedback pot tolerance differences, etc).
This occurs immediately after the next cycle of KL 15 for approximately 30 seconds.
During this period of adaptation, the maximum opening of the throttle plate is 25%.
Page 23 of 37
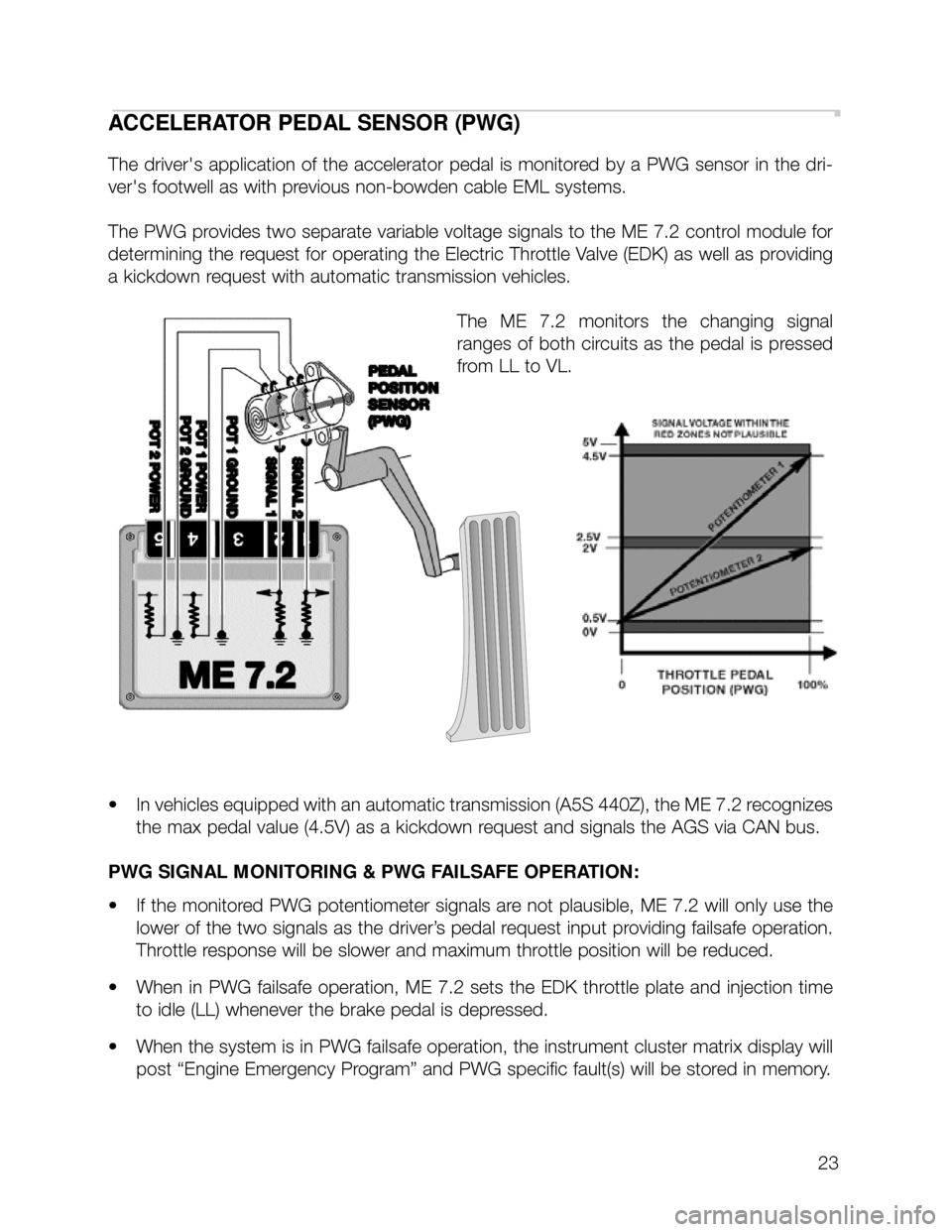
23
ACCELERATOR PEDAL SENSOR (PWG)
The driver's application of the accelerator pedal is monitored by a PWG sensor in the dri-
ver's footwell as with previous non-bowden cable EML systems.
The PWG provides two separate variable voltage signals to the ME 7.2 control module for
determining the request for operating the Electric Throttle Valve (EDK) as well as providing
a kickdown request with automatic transmission vehicles.
The ME 7.2 monitors the changing signal
ranges of both circuits as the pedal is pressed
from LL to VL.
• In vehicles equipped with an automatic transmission (A5S 440Z), the ME 7.2 recognizes
the max pedal value (4.5V) as a kickdown request and signals the AGS via CAN bus.
PWG SIGNAL MONITORING & PWG FAILSAFE OPERATION:
• If the monitored PWG potentiometer signals are not plausible, ME 7.2 will only use the
lower of the two signals as the driver’s pedal request input providing failsafe operation.
Throttle response will be slower and maximum throttle position will be reduced.
• When in PWG failsafe operation, ME 7.2 sets the EDK throttle plate and injection time
to idle (LL) whenever the brake pedal is depressed.
• When the system is in PWG failsafe operation, the instrument cluster matrix display will
post “Engine Emergency Program” and PWG specific fault(s) will be stored in memory.
Page 24 of 37
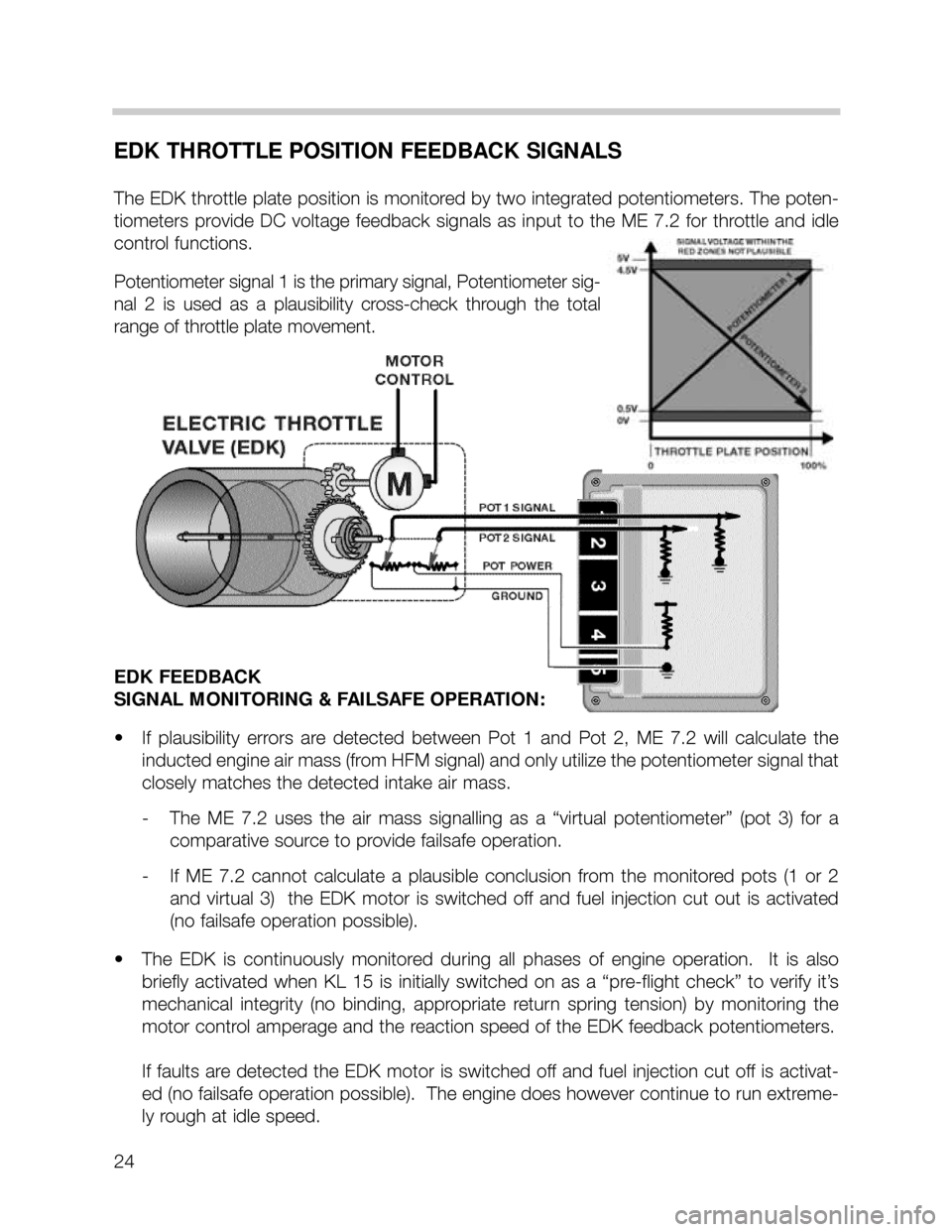
24
EDK THROTTLE POSITION FEEDBACK SIGNALS
The EDK throttle plate position is monitored by two integrated potentiometers. The poten-
tiometers provide DC voltage feedback signals as input to the ME 7.2 for throttle and idle
control functions.
Potentiometer signal 1 is the primary signal, Potentiometer sig-
nal 2 is used as a plausibility cross-check through the total
range of throttle plate movement.
EDK FEEDBACK
SIGNAL MONITORING & FAILSAFE OPERATION:
• If plausibility errors are detected between Pot 1 and Pot 2, ME 7.2 will calculate the
inducted engine air mass (from HFM signal) and only utilize the potentiometer signal that
closely matches the detected intake air mass.
- The ME 7.2 uses the air mass signalling as a “virtual potentiometer” (pot 3) for a
comparative source to provide failsafe operation.
- If ME 7.2 cannot calculate a plausible conclusion from the monitored pots (1 or 2
and virtual 3) the EDK motor is switched off and fuel injection cut out is activated
(no failsafe operation possible).
• The EDK is continuously monitored during all phases of engine operation. It is also
briefly activated when KL 15 is initially switched on as a “pre-flight check” to verify it’s
mechanical integrity (no binding, appropriate return spring tension) by monitoring the
motor control amperage and the reaction speed of the EDK feedback potentiometers.
If faults are detected the EDK motor is switched off and fuel injection cut off is activat-
ed (no failsafe operation possible). The engine does however continue to run extreme-
ly rough at idle speed.
Page 25 of 37
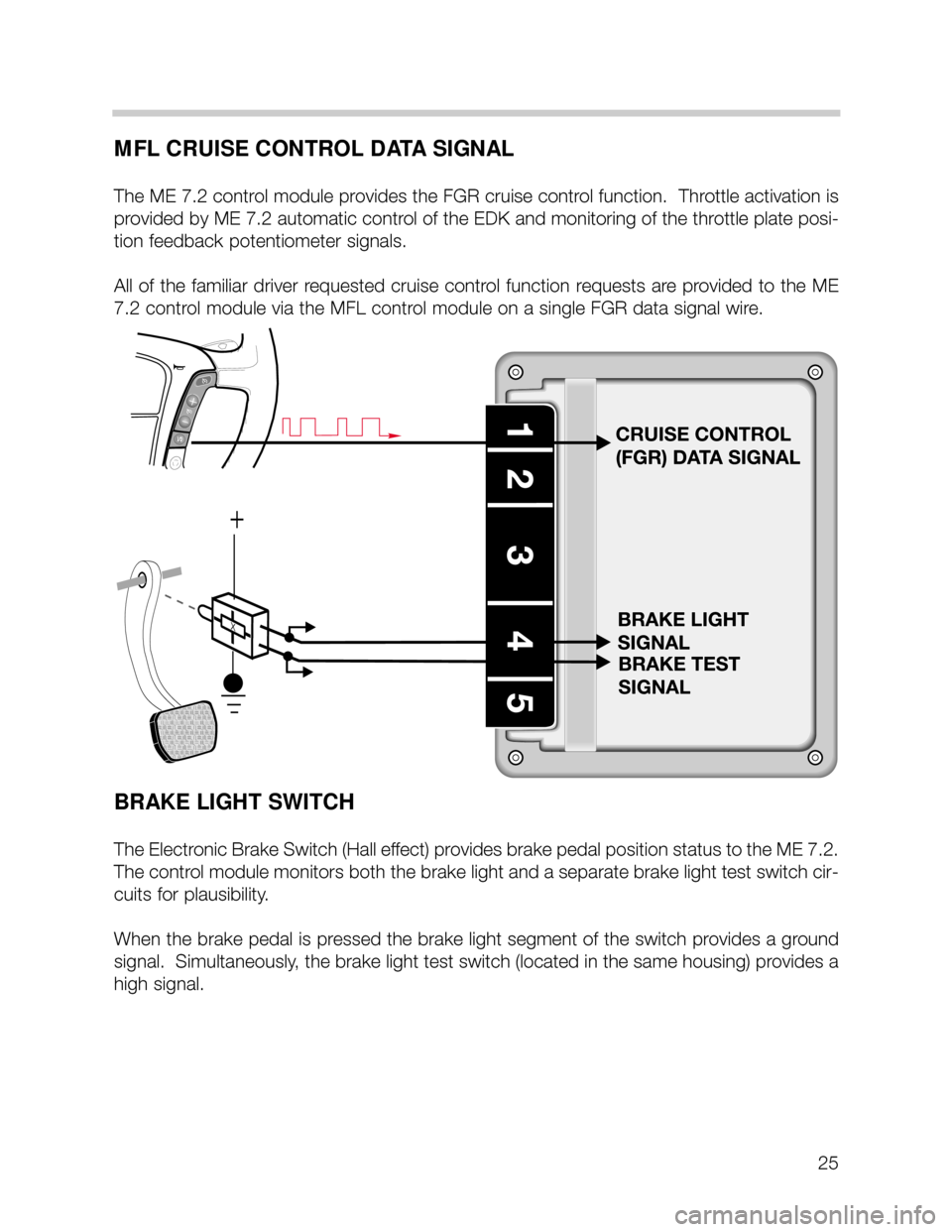
25
MFL CRUISE CONTROL DATA SIGNAL
The ME 7.2 control module provides the FGR cruise control function. Throttle activation is
provided by ME 7.2 automatic control of the EDK and monitoring of the throttle plate posi-
tion feedback potentiometer signals.
All of the familiar driver requested cruise control function requests are provided to the ME
7.2 control module via the MFL control module on a single FGR data signal wire.
BRAKE LIGHT SWITCH
The Electronic Brake Switch (Hall effect) provides brake pedal position status to the ME 7.2.
The control module monitors both the brake light and a separate brake light test switch cir-
cuits for plausibility.
When the brake pedal is pressed the brake light segment of the switch provides a ground
signal. Simultaneously, the brake light test switch (located in the same housing) provides a
high signal.
Page 30 of 37
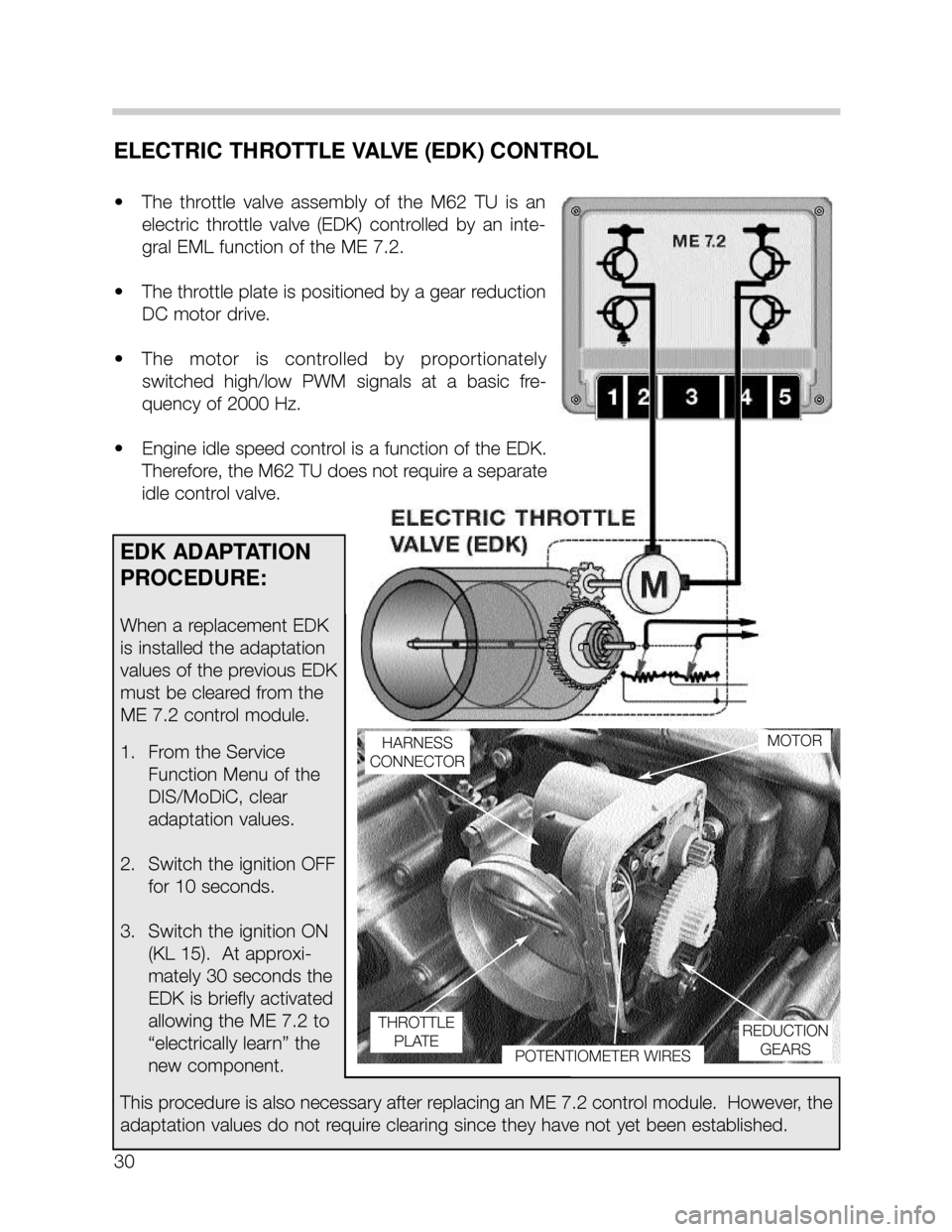
30
ELECTRIC THROTTLE VALVE (EDK) CONTROL
• The throttle valve assembly of the M62 TU is an
electric throttle valve (EDK) controlled by an inte-
gral EML function of the ME 7.2.
• The throttle plate is positioned by a gear reduction
DC motor drive.
• The motor is controlled by proportionately
switched high/low PWM signals at a basic fre-
quency of 2000 Hz.
• Engine idle speed control is a function of the EDK.
Therefore, the M62 TU does not require a separate
idle control valve.
HARNESS
CONNECTORMOTOR
REDUCTION
GEARS
POTENTIOMETER WIRES
THROTTLE
PLATE
EDK ADAPTATION
PROCEDURE:
When a replacement EDK
is installed the adaptation
values of the previous EDK
must be cleared from the
ME 7.2 control module.
1. From the Service
Function Menu of the
DIS/MoDiC, clear
adaptation values.
2. Switch the ignition OFF
for 10 seconds.
3. Switch the ignition ON
(KL 15). At approxi-
mately 30 seconds the
EDK is briefly activated
allowing the ME 7.2 to
“electrically learn” the
new component.
This procedure is also necessary after replacing an ME 7.2 control module. However, the
adaptation values do not require clearing since they have not yet been established.