steering BMW X5 2004 E53 DSC System Workshop Manual
[x] Cancel search | Manufacturer: BMW, Model Year: 2004, Model line: X5, Model: BMW X5 2004 E53Pages: 24, PDF Size: 1.77 MB
Page 1 of 24
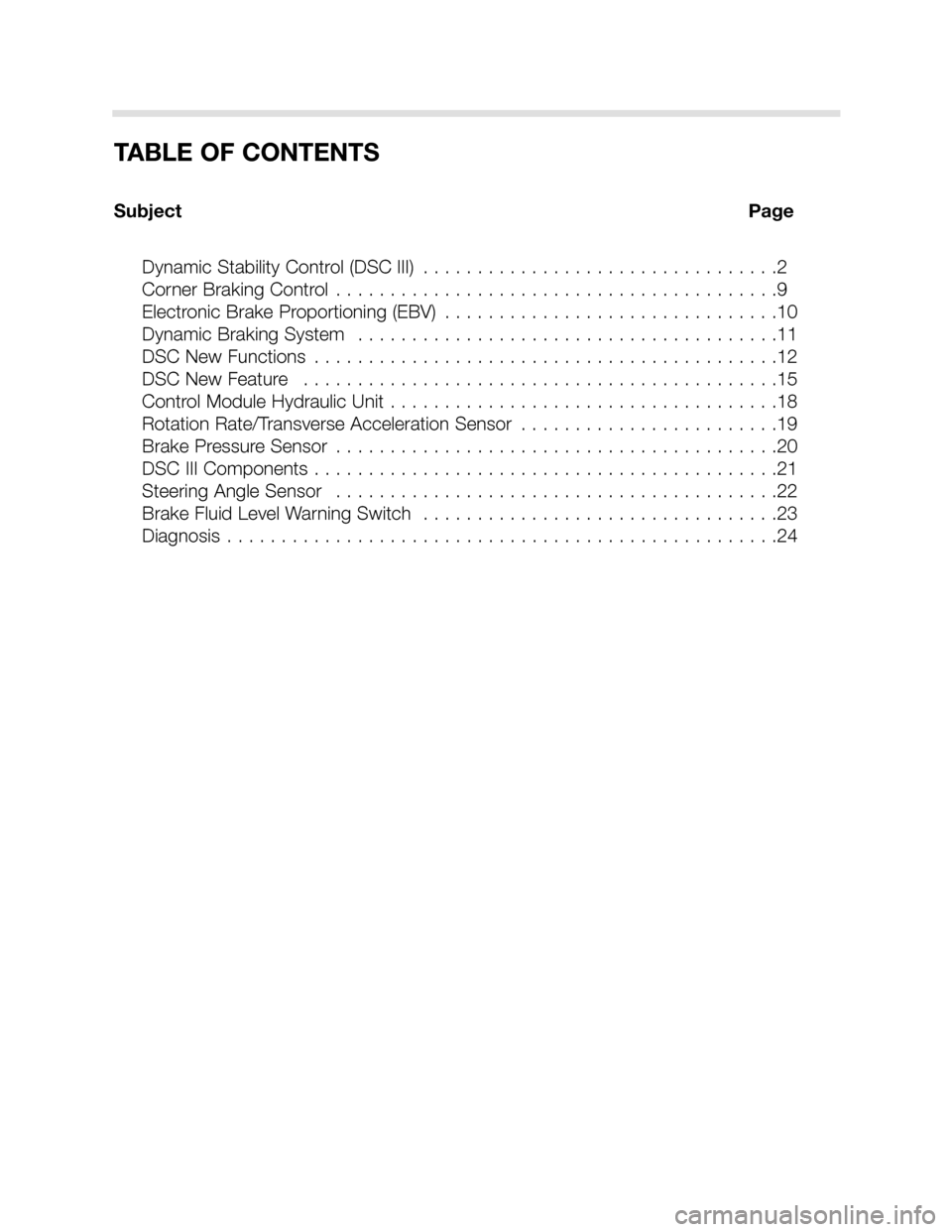
TABLE OF CONTENTS
Subject Page
Dynamic Stability Control (DSC III) . . . . . . . . . . . . . . . . . . . . . . . . . . . . . . . . .2
Corner Braking Control . . . . . . . . . . . . . . . . . . . . . . . . . . . . . . . . . . . . . . . . .9
Electronic Brake Proportioning (EBV) . . . . . . . . . . . . . . . . . . . . . . . . . . . . . . .10
Dynamic Braking System . . . . . . . . . . . . . . . . . . . . . . . . . . . . . . . . . . . . . . .11
DSC New Functions . . . . . . . . . . . . . . . . . . . . . . . . . . . . . . . . . . . . . . . . . . .12
DSC New Feature . . . . . . . . . . . . . . . . . . . . . . . . . . . . . . . . . . . . . . . . . . . .15
Control Module Hydraulic Unit . . . . . . . . . . . . . . . . . . . . . . . . . . . . . . . . . . . .18
Rotation Rate/Transverse Acceleration Sensor . . . . . . . . . . . . . . . . . . . . . . . .19
Brake Pressure Sensor . . . . . . . . . . . . . . . . . . . . . . . . . . . . . . . . . . . . . . . . .20
DSC III Components . . . . . . . . . . . . . . . . . . . . . . . . . . . . . . . . . . . . . . . . . . .21
Steering Angle Sensor . . . . . . . . . . . . . . . . . . . . . . . . . . . . . . . . . . . . . . . . .22
Brake Fluid Level Warning Switch . . . . . . . . . . . . . . . . . . . . . . . . . . . . . . . . .23
Diagnosis . . . . . . . . . . . . . . . . . . . . . . . . . . . . . . . . . . . . . . . . . . . . . . . . . . .24
Page 6 of 24
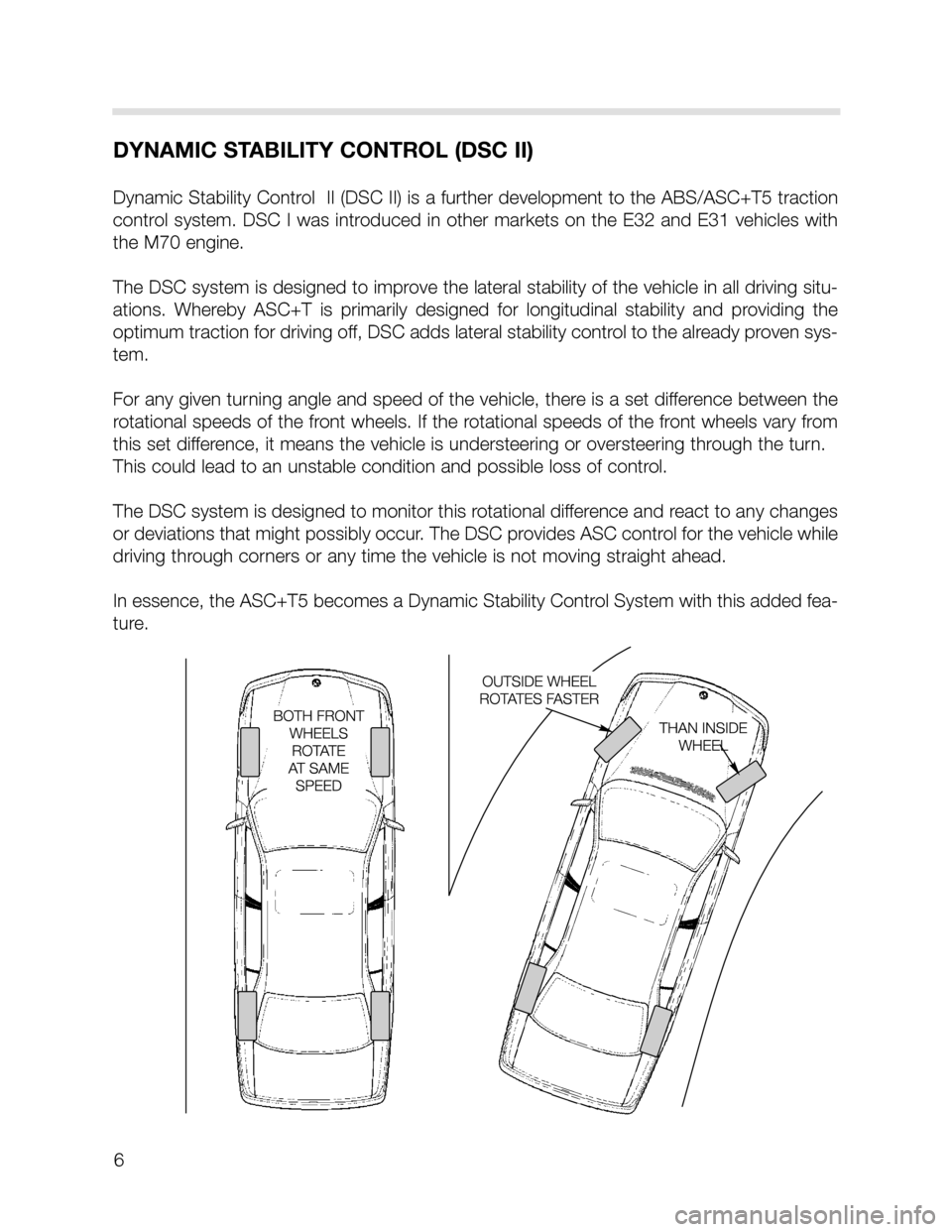
6
DYNAMIC STABILITY CONTROL (DSC II)
Dynamic Stability Control II (DSC II) is a further development to the ABS/ASC+T5 traction
control system. DSC I was introduced in other markets on the E32 and E31 vehicles with
the M70 engine.
The DSC system is designed to improve the lateral stability of the vehicle in all driving situ-
ations. Whereby ASC+T is primarily designed for longitudinal stability and providing the
optimum traction for driving off, DSC adds lateral stability control to the already proven sys-
tem.
For any given turning angle and speed of the vehicle, there is a set difference between the
rotational speeds of the front wheels. If the rotational speeds of the front wheels vary from
this set difference, it means the vehicle is understeering or oversteering through the turn.
This could lead to an unstable condition and possible loss of control.
The DSC system is designed to monitor this rotational difference and react to any changes
or deviations that might possibly occur. The DSC provides ASC control for the vehicle while
driving through corners or any time the vehicle is not moving straight ahead.
In essence, the ASC+T5 becomes a Dynamic Stability Control System with this added fea-
ture.
Page 7 of 24
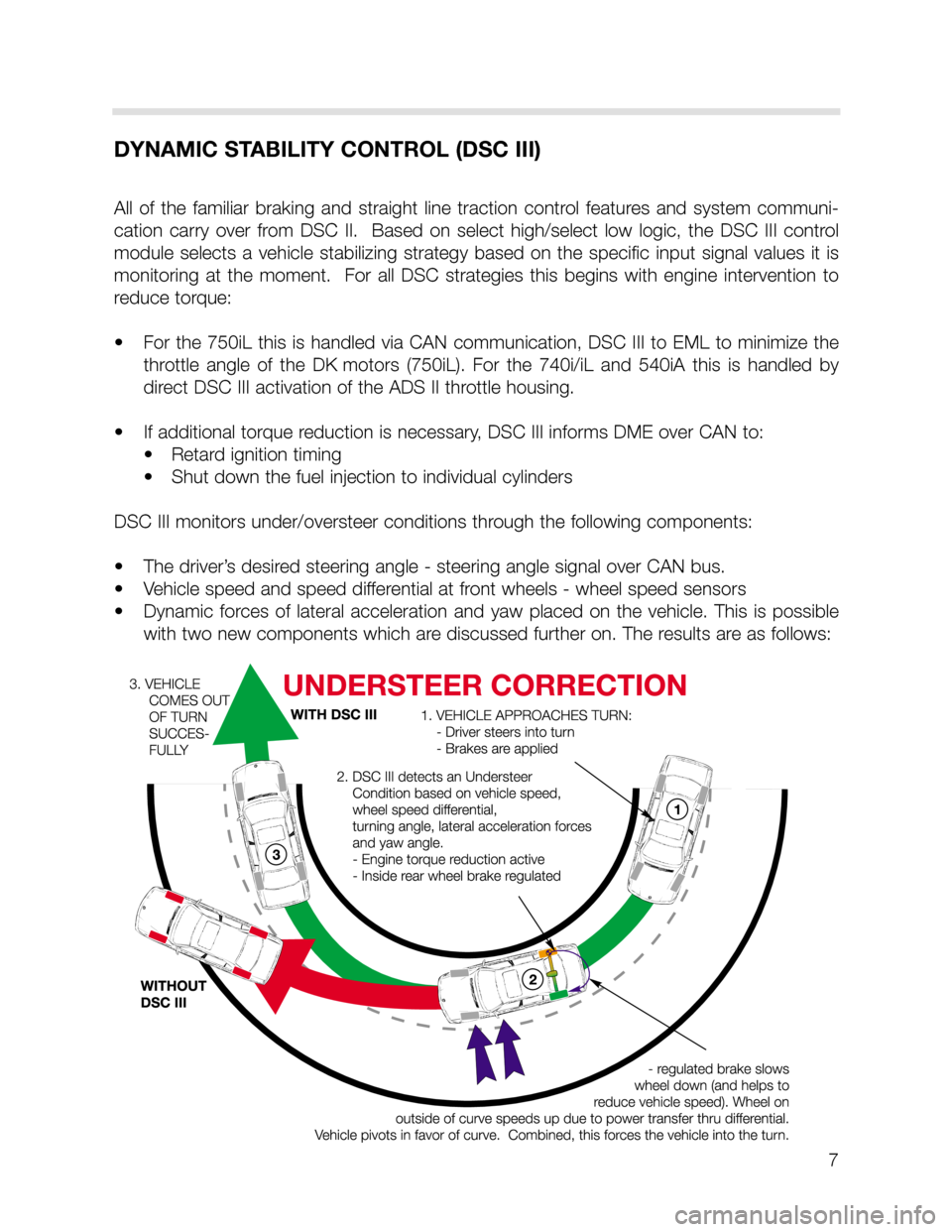
7
DYNAMIC STABILITY CONTROL (DSC III)
All of the familiar braking and straight line traction control features and system communi-
cation carry over from DSC II. Based on select high/select low logic, the DSC III control
module selects a vehicle stabilizing strategy based on the specific input signal values it is
monitoring at the moment. For all DSC strategies this begins with engine intervention to
reduce torque:
•For the 750iL this is handled via CAN communication, DSC III to EML to minimize the
throttle angle of the DK motors (750iL). For the 740i/iL and 540iA this is handled by
direct DSC III activation of the ADS II throttle housing.
• If additional torque reduction is necessary, DSC III informs DME over CAN to:
• Retard ignition timing
• Shut down the fuel injection to individual cylinders
DSC III monitors under/oversteer conditions through the following components:
• The driver’s desired steering angle - steering angle signal over CAN bus.
• Vehicle speed and speed differential at front wheels - wheel speed sensors
• Dynamic forces of lateral acceleration and yaw placed on the vehicle. This is possible
with two new components which are discussed further on. The results are as follows:
Page 12 of 24
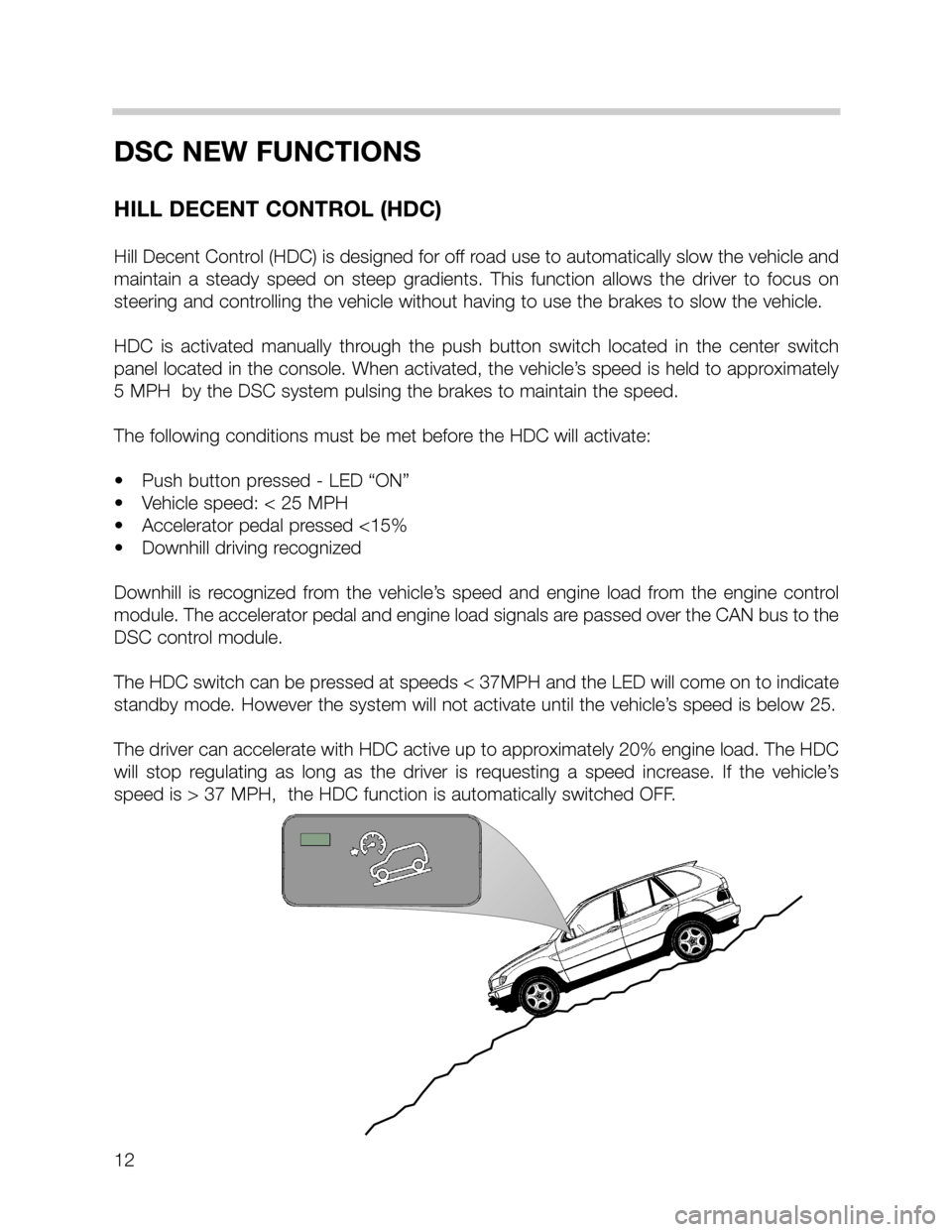
12
DSC NEW FUNCTIONS
HILL DECENT CONTROL (HDC)
Hill Decent Control (HDC) is designed for off road use to automatically slow the vehicle and
maintain a steady speed on steep gradients. This function allows the driver to focus on
steering and controlling the vehicle without having to use the brakes to slow the vehicle.
HDC is activated manually through the push button switch located in the center switch
panel located in the console. When activated, the vehicle’s speed is held to approximately
5 MPH by the DSC system pulsing the brakes to maintain the speed.
The following conditions must be met before the HDC will activate:
• Push button pressed - LED “ON”
• Vehicle speed: < 25 MPH
• Accelerator pedal pressed <15%
• Downhill driving recognized
Downhill is recognized from the vehicle’s speed and engine load from the engine control
module. The accelerator pedal and engine load signals are passed over the CAN bus to the
DSC control module.
The HDC switch can be pressed at speeds < 37MPH and the LED will come on to indicate
standby mode. However the system will not activate until the vehicle’s speed is below 25.
The driver can accelerate with HDC active up to approximately 20% engine load. The HDC
will stop regulating as long as the driver is requesting a speed increase. If the vehicle’s
speed is > 37 MPH, the HDC function is automatically switched OFF.
Page 15 of 24
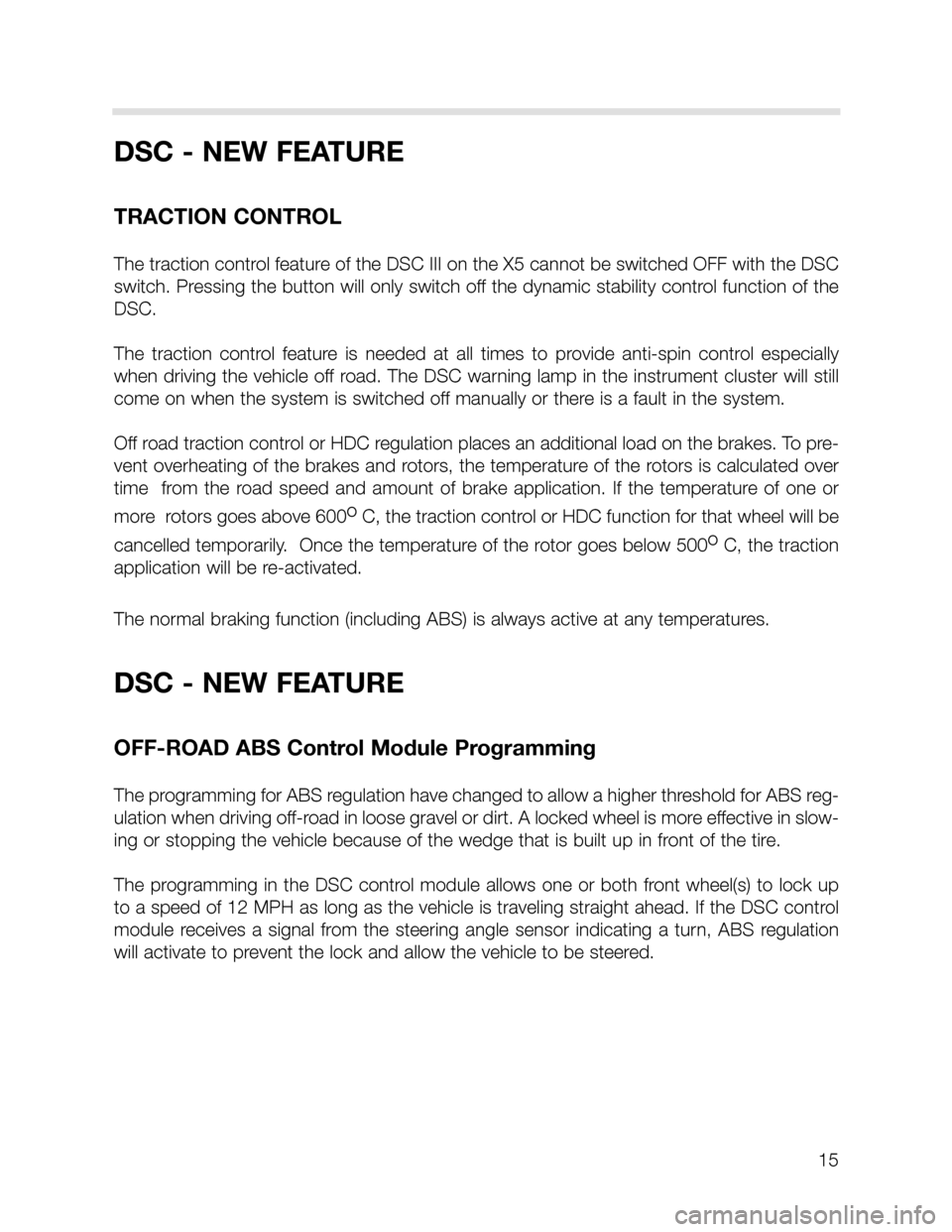
15
DSC - NEW FEATURE
TRACTION CONTROL
The traction control feature of the DSC III on the X5 cannot be switched OFF with the DSC
switch. Pressing the button will only switch off the dynamic stability control function of the
DSC.
The traction control feature is needed at all times to provide anti-spin control especially
when driving the vehicle off road. The DSC warning lamp in the instrument cluster will still
come on when the system is switched off manually or there is a fault in the system.
Off road traction control or HDC regulation places an additional load on the brakes. To pre-
vent overheating of the brakes and rotors, the temperature of the rotors is calculated over
time from the road speed and amount of brake application. If the temperature of one or
more rotors goes above 600o
C, the traction control or HDC function for that wheel will be
cancelled temporarily. Once the temperature of the rotor goes below 500o
C, the traction
application will be re-activated.
The normal braking function (including ABS) is always active at any temperatures.
DSC - NEW FEATURE
OFF-ROAD ABS Control Module Programming
The programming for ABS regulation have changed to allow a higher threshold for ABS reg-
ulation when driving off-road in loose gravel or dirt. A locked wheel is more effective in slow-
ing or stopping the vehicle because of the wedge that is built up in front of the tire.
The programming in the DSC control module allows one or both front wheel(s) to lock up
to a speed of 12 MPH as long as the vehicle is traveling straight ahead. If the DSC control
module receives a signal from the steering angle sensor indicating a turn, ABS regulation
will activate to prevent the lock and allow the vehicle to be steered.
Page 22 of 24
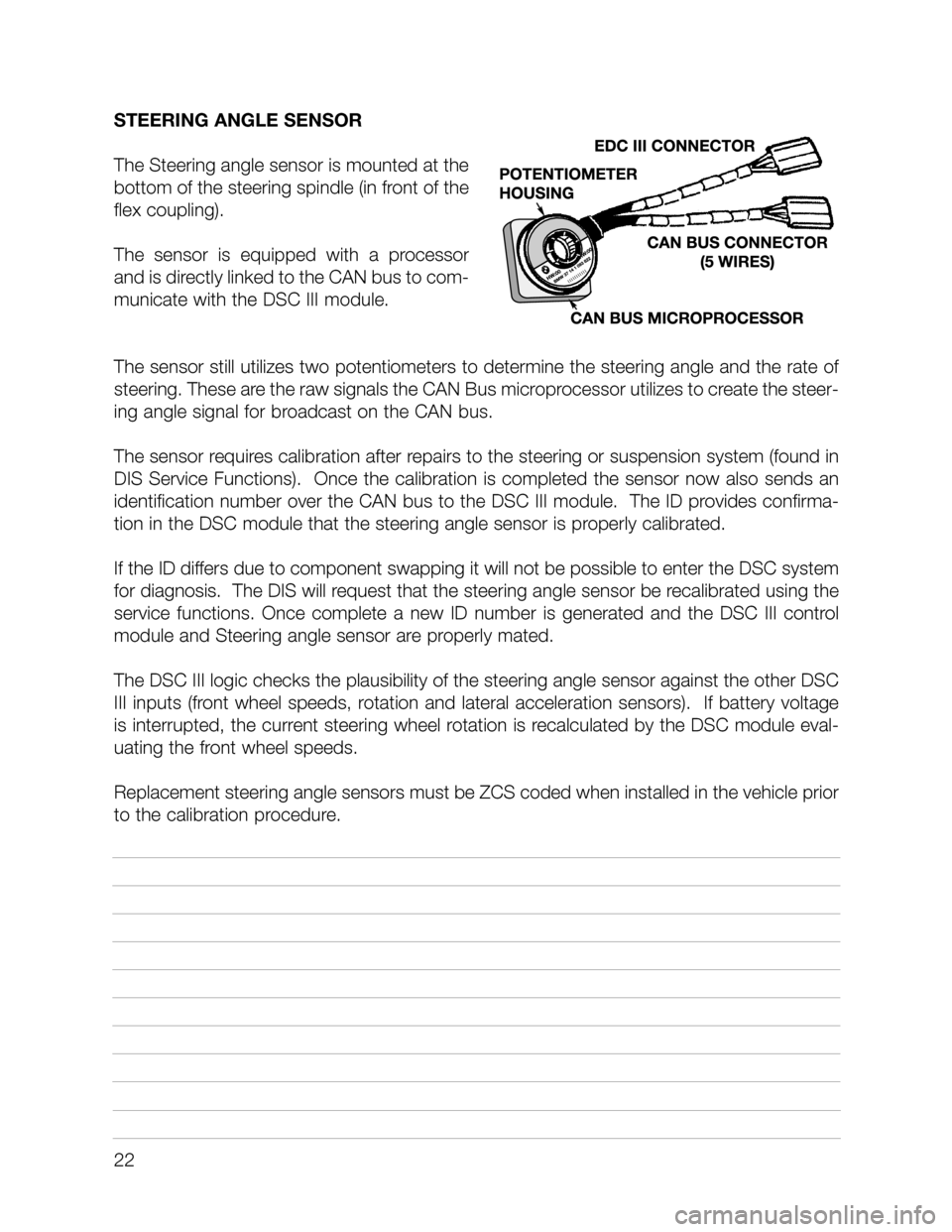
STEERING ANGLE SENSOR
The Steering angle sensor is mounted at the
bottom of the steering spindle (in front of the
flex coupling).
The sensor is equipped with a processor
and is directly linked to the CAN bus to com-
municate with the DSC III module.
The sensor still utilizes two potentiometers to determine the steering angle and the rate of
steering. These are the raw signals the CAN Bus microprocessor utilizes to create the steer-
ing angle signal for broadcast on the CAN bus.
The sensor requires calibration after repairs to the steering or suspension system (found in
DIS Service Functions). Once the calibration is completed the sensor now also sends an
identification number over the CAN bus to the DSC III module. The ID provides confirma-
tion in the DSC module that the steering angle sensor is properly calibrated.
If the ID differs due to component swapping it will not be possible to enter the DSC system
for diagnosis. The DIS will request that the steering angle sensor be recalibrated using the
service functions. Once complete a new ID number is generated and the DSC III control
module and Steering angle sensor are properly mated.
The DSC III logic checks the plausibility of the steering angle sensor against the other DSC
III inputs (front wheel speeds, rotation and lateral acceleration sensors). If battery voltage
is interrupted, the current steering wheel rotation is recalculated by the DSC module eval-
uating the front wheel speeds.
Replacement steering angle sensors must be ZCS coded when installed in the vehicle prior
to the calibration procedure.
22
Page 24 of 24
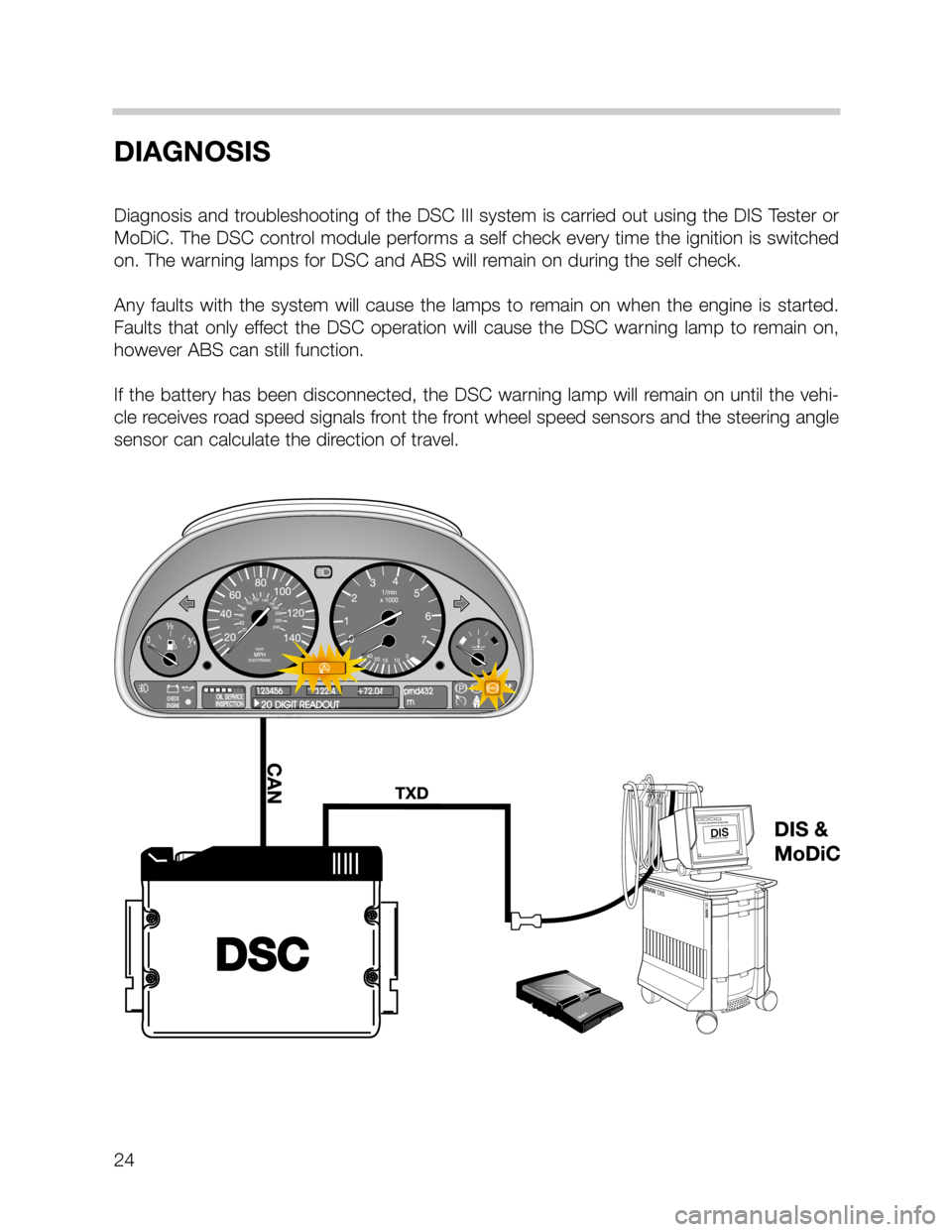
24
DIAGNOSIS
Diagnosis and troubleshooting of the DSC III system is carried out using the DIS Tester or
MoDiC. The DSC control module performs a self check every time the ignition is switched
on. The warning lamps for DSC and ABS will remain on during the self check.
Any faults with the system will cause the lamps to remain on when the engine is started.
Faults that only effect the DSC operation will cause the DSC warning lamp to remain on,
however ABS can still function.
If the battery has been disconnected, the DSC warning lamp will remain on until the vehi-
cle receives road speed signals front the front wheel speed sensors and the steering angle
sensor can calculate the direction of travel.