clock setting CHRYSLER CARAVAN 2003 Service Manual
[x] Cancel search | Manufacturer: CHRYSLER, Model Year: 2003, Model line: CARAVAN, Model: CHRYSLER CARAVAN 2003Pages: 2177, PDF Size: 59.81 MB
Page 307 of 2177
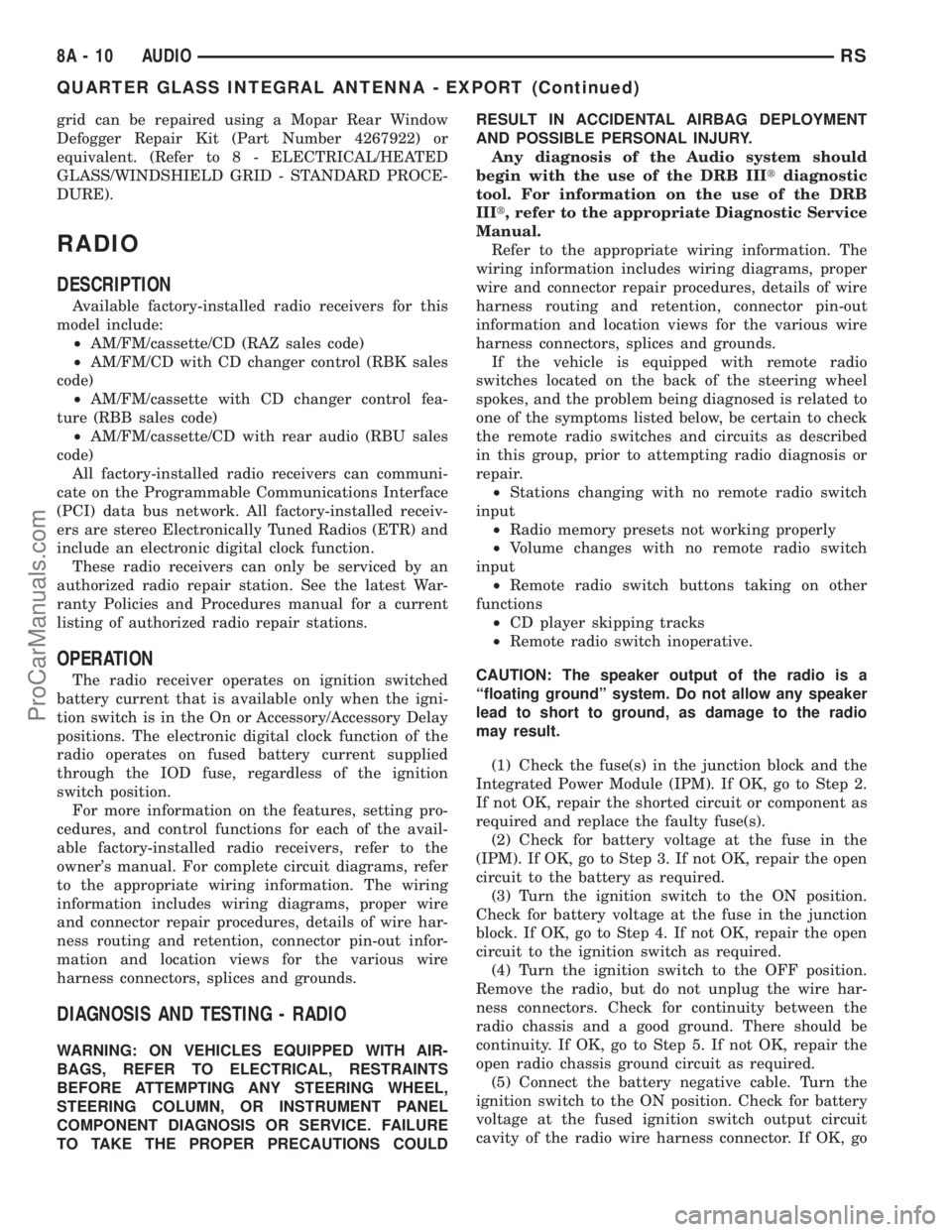
grid can be repaired using a Mopar Rear Window
Defogger Repair Kit (Part Number 4267922) or
equivalent. (Refer to 8 - ELECTRICAL/HEATED
GLASS/WINDSHIELD GRID - STANDARD PROCE-
DURE).
RADIO
DESCRIPTION
Available factory-installed radio receivers for this
model include:
²AM/FM/cassette/CD (RAZ sales code)
²AM/FM/CD with CD changer control (RBK sales
code)
²AM/FM/cassette with CD changer control fea-
ture (RBB sales code)
²AM/FM/cassette/CD with rear audio (RBU sales
code)
All factory-installed radio receivers can communi-
cate on the Programmable Communications Interface
(PCI) data bus network. All factory-installed receiv-
ers are stereo Electronically Tuned Radios (ETR) and
include an electronic digital clock function.
These radio receivers can only be serviced by an
authorized radio repair station. See the latest War-
ranty Policies and Procedures manual for a current
listing of authorized radio repair stations.
OPERATION
The radio receiver operates on ignition switched
battery current that is available only when the igni-
tion switch is in the On or Accessory/Accessory Delay
positions. The electronic digital clock function of the
radio operates on fused battery current supplied
through the IOD fuse, regardless of the ignition
switch position.
For more information on the features, setting pro-
cedures, and control functions for each of the avail-
able factory-installed radio receivers, refer to the
owner's manual. For complete circuit diagrams, refer
to the appropriate wiring information. The wiring
information includes wiring diagrams, proper wire
and connector repair procedures, details of wire har-
ness routing and retention, connector pin-out infor-
mation and location views for the various wire
harness connectors, splices and grounds.
DIAGNOSIS AND TESTING - RADIO
WARNING: ON VEHICLES EQUIPPED WITH AIR-
BAGS, REFER TO ELECTRICAL, RESTRAINTS
BEFORE ATTEMPTING ANY STEERING WHEEL,
STEERING COLUMN, OR INSTRUMENT PANEL
COMPONENT DIAGNOSIS OR SERVICE. FAILURE
TO TAKE THE PROPER PRECAUTIONS COULDRESULT IN ACCIDENTAL AIRBAG DEPLOYMENT
AND POSSIBLE PERSONAL INJURY.
Any diagnosis of the Audio system should
begin with the use of the DRB IIItdiagnostic
tool. For information on the use of the DRB
IIIt, refer to the appropriate Diagnostic Service
Manual.
Refer to the appropriate wiring information. The
wiring information includes wiring diagrams, proper
wire and connector repair procedures, details of wire
harness routing and retention, connector pin-out
information and location views for the various wire
harness connectors, splices and grounds.
If the vehicle is equipped with remote radio
switches located on the back of the steering wheel
spokes, and the problem being diagnosed is related to
one of the symptoms listed below, be certain to check
the remote radio switches and circuits as described
in this group, prior to attempting radio diagnosis or
repair.
²Stations changing with no remote radio switch
input
²Radio memory presets not working properly
²Volume changes with no remote radio switch
input
²Remote radio switch buttons taking on other
functions
²CD player skipping tracks
²Remote radio switch inoperative.
CAUTION: The speaker output of the radio is a
ªfloating groundº system. Do not allow any speaker
lead to short to ground, as damage to the radio
may result.
(1) Check the fuse(s) in the junction block and the
Integrated Power Module (IPM). If OK, go to Step 2.
If not OK, repair the shorted circuit or component as
required and replace the faulty fuse(s).
(2) Check for battery voltage at the fuse in the
(IPM). If OK, go to Step 3. If not OK, repair the open
circuit to the battery as required.
(3) Turn the ignition switch to the ON position.
Check for battery voltage at the fuse in the junction
block. If OK, go to Step 4. If not OK, repair the open
circuit to the ignition switch as required.
(4) Turn the ignition switch to the OFF position.
Remove the radio, but do not unplug the wire har-
ness connectors. Check for continuity between the
radio chassis and a good ground. There should be
continuity. If OK, go to Step 5. If not OK, repair the
open radio chassis ground circuit as required.
(5) Connect the battery negative cable. Turn the
ignition switch to the ON position. Check for battery
voltage at the fused ignition switch output circuit
cavity of the radio wire harness connector. If OK, go
8A - 10 AUDIORS
QUARTER GLASS INTEGRAL ANTENNA - EXPORT (Continued)
ProCarManuals.com
Page 1244 of 2177
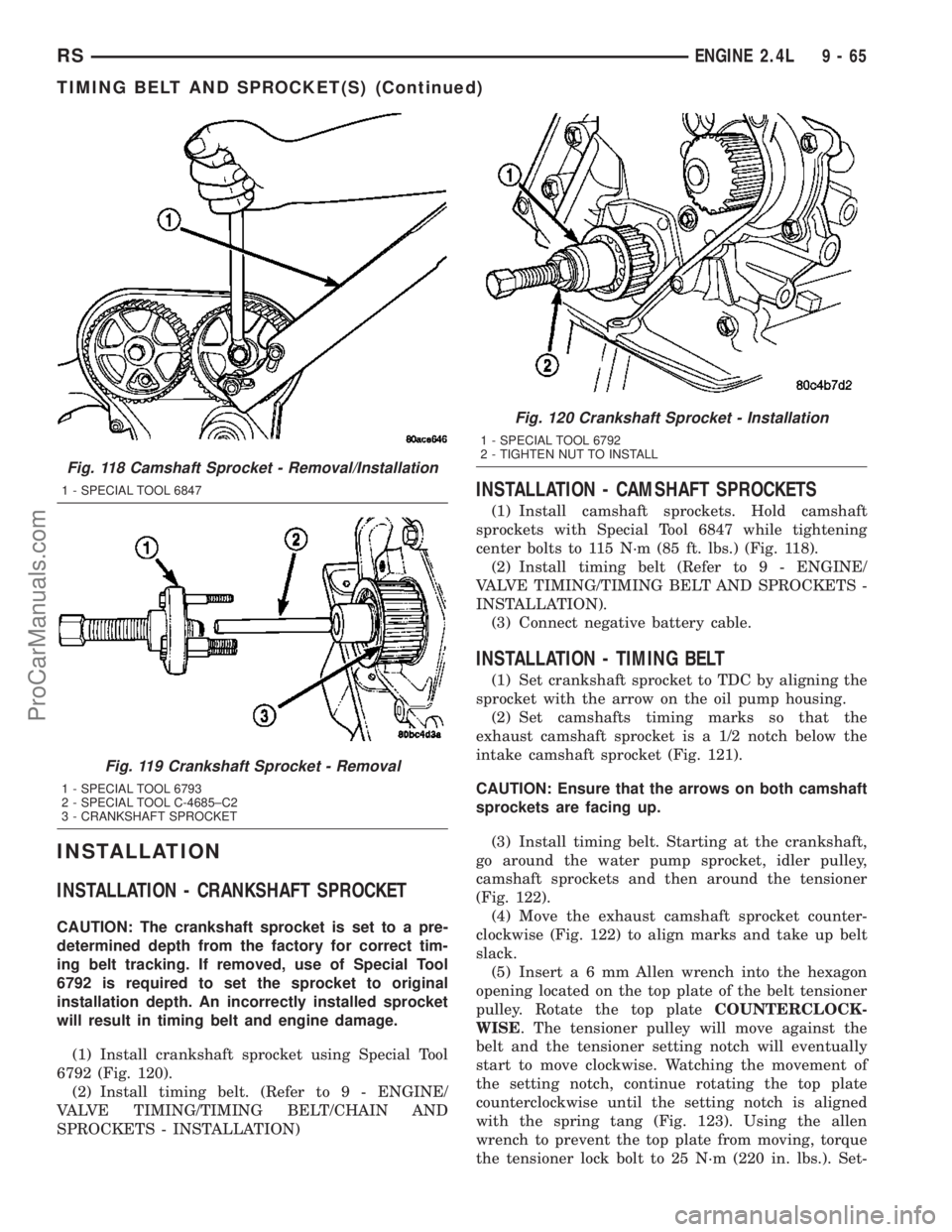
INSTALLATION
INSTALLATION - CRANKSHAFT SPROCKET
CAUTION: The crankshaft sprocket is set to a pre-
determined depth from the factory for correct tim-
ing belt tracking. If removed, use of Special Tool
6792 is required to set the sprocket to original
installation depth. An incorrectly installed sprocket
will result in timing belt and engine damage.
(1) Install crankshaft sprocket using Special Tool
6792 (Fig. 120).
(2) Install timing belt. (Refer to 9 - ENGINE/
VALVE TIMING/TIMING BELT/CHAIN AND
SPROCKETS - INSTALLATION)
INSTALLATION - CAMSHAFT SPROCKETS
(1) Install camshaft sprockets. Hold camshaft
sprockets with Special Tool 6847 while tightening
center bolts to 115 N´m (85 ft. lbs.) (Fig. 118).
(2) Install timing belt (Refer to 9 - ENGINE/
VALVE TIMING/TIMING BELT AND SPROCKETS -
INSTALLATION).
(3) Connect negative battery cable.
INSTALLATION - TIMING BELT
(1) Set crankshaft sprocket to TDC by aligning the
sprocket with the arrow on the oil pump housing.
(2) Set camshafts timing marks so that the
exhaust camshaft sprocket is a 1/2 notch below the
intake camshaft sprocket (Fig. 121).
CAUTION: Ensure that the arrows on both camshaft
sprockets are facing up.
(3) Install timing belt. Starting at the crankshaft,
go around the water pump sprocket, idler pulley,
camshaft sprockets and then around the tensioner
(Fig. 122).
(4) Move the exhaust camshaft sprocket counter-
clockwise (Fig. 122) to align marks and take up belt
slack.
(5) Inserta6mmAllen wrench into the hexagon
opening located on the top plate of the belt tensioner
pulley. Rotate the top plateCOUNTERCLOCK-
WISE. The tensioner pulley will move against the
belt and the tensioner setting notch will eventually
start to move clockwise. Watching the movement of
the setting notch, continue rotating the top plate
counterclockwise until the setting notch is aligned
with the spring tang (Fig. 123). Using the allen
wrench to prevent the top plate from moving, torque
the tensioner lock bolt to 25 N´m (220 in. lbs.). Set-
Fig. 118 Camshaft Sprocket - Removal/Installation
1 - SPECIAL TOOL 6847
Fig. 119 Crankshaft Sprocket - Removal
1 - SPECIAL TOOL 6793
2 - SPECIAL TOOL C-4685±C2
3 - CRANKSHAFT SPROCKET
Fig. 120 Crankshaft Sprocket - Installation
1 - SPECIAL TOOL 6792
2 - TIGHTEN NUT TO INSTALL
RSENGINE 2.4L9-65
TIMING BELT AND SPROCKET(S) (Continued)
ProCarManuals.com
Page 1245 of 2177
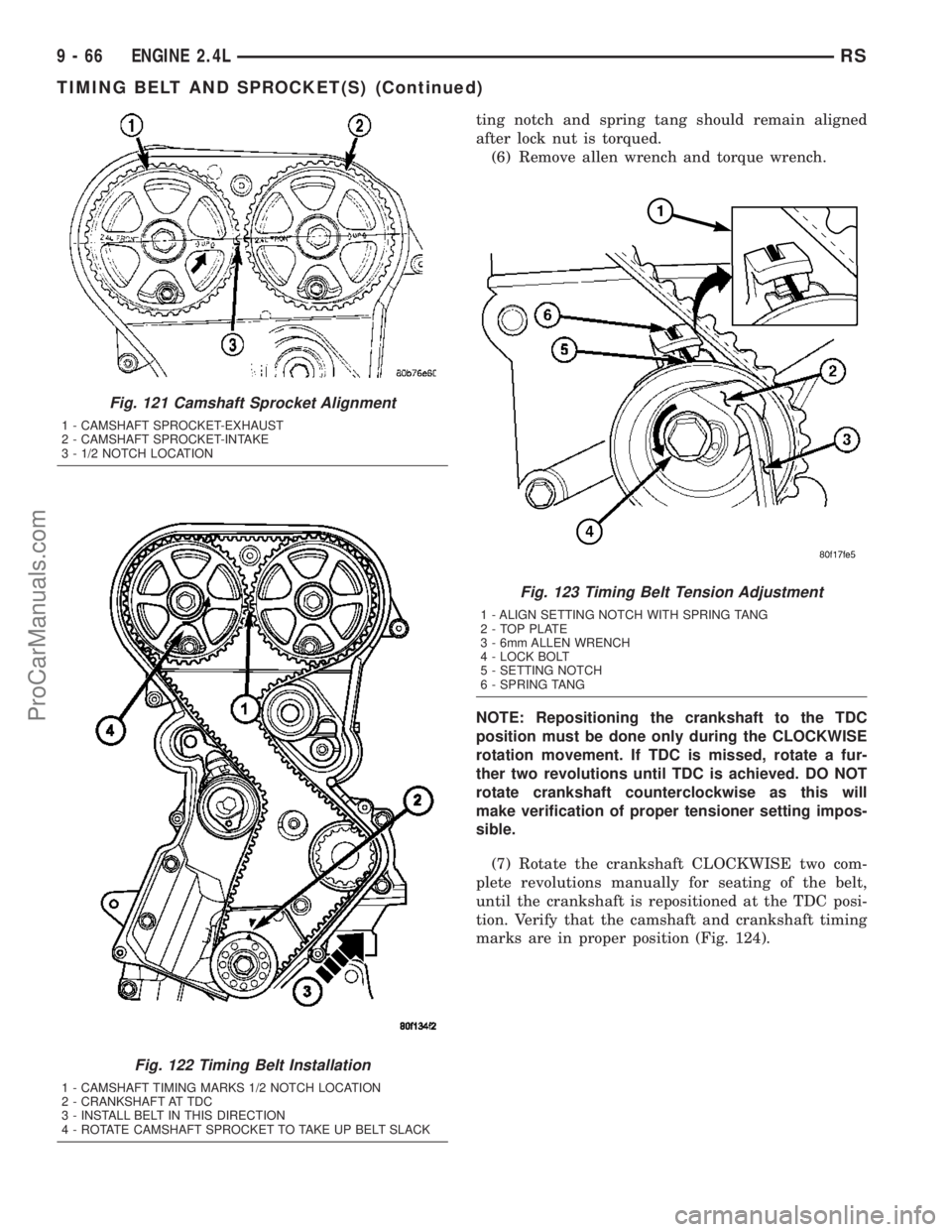
ting notch and spring tang should remain aligned
after lock nut is torqued.
(6) Remove allen wrench and torque wrench.
NOTE: Repositioning the crankshaft to the TDC
position must be done only during the CLOCKWISE
rotation movement. If TDC is missed, rotate a fur-
ther two revolutions until TDC is achieved. DO NOT
rotate crankshaft counterclockwise as this will
make verification of proper tensioner setting impos-
sible.
(7) Rotate the crankshaft CLOCKWISE two com-
plete revolutions manually for seating of the belt,
until the crankshaft is repositioned at the TDC posi-
tion. Verify that the camshaft and crankshaft timing
marks are in proper position (Fig. 124).
Fig. 121 Camshaft Sprocket Alignment
1 - CAMSHAFT SPROCKET-EXHAUST
2 - CAMSHAFT SPROCKET-INTAKE
3 - 1/2 NOTCH LOCATION
Fig. 122 Timing Belt Installation
1 - CAMSHAFT TIMING MARKS 1/2 NOTCH LOCATION
2 - CRANKSHAFT AT TDC
3 - INSTALL BELT IN THIS DIRECTION
4 - ROTATE CAMSHAFT SPROCKET TO TAKE UP BELT SLACK
Fig. 123 Timing Belt Tension Adjustment
1 - ALIGN SETTING NOTCH WITH SPRING TANG
2 - TOP PLATE
3 - 6mm ALLEN WRENCH
4 - LOCK BOLT
5 - SETTING NOTCH
6 - SPRING TANG
9 - 66 ENGINE 2.4LRS
TIMING BELT AND SPROCKET(S) (Continued)
ProCarManuals.com
Page 2145 of 2177
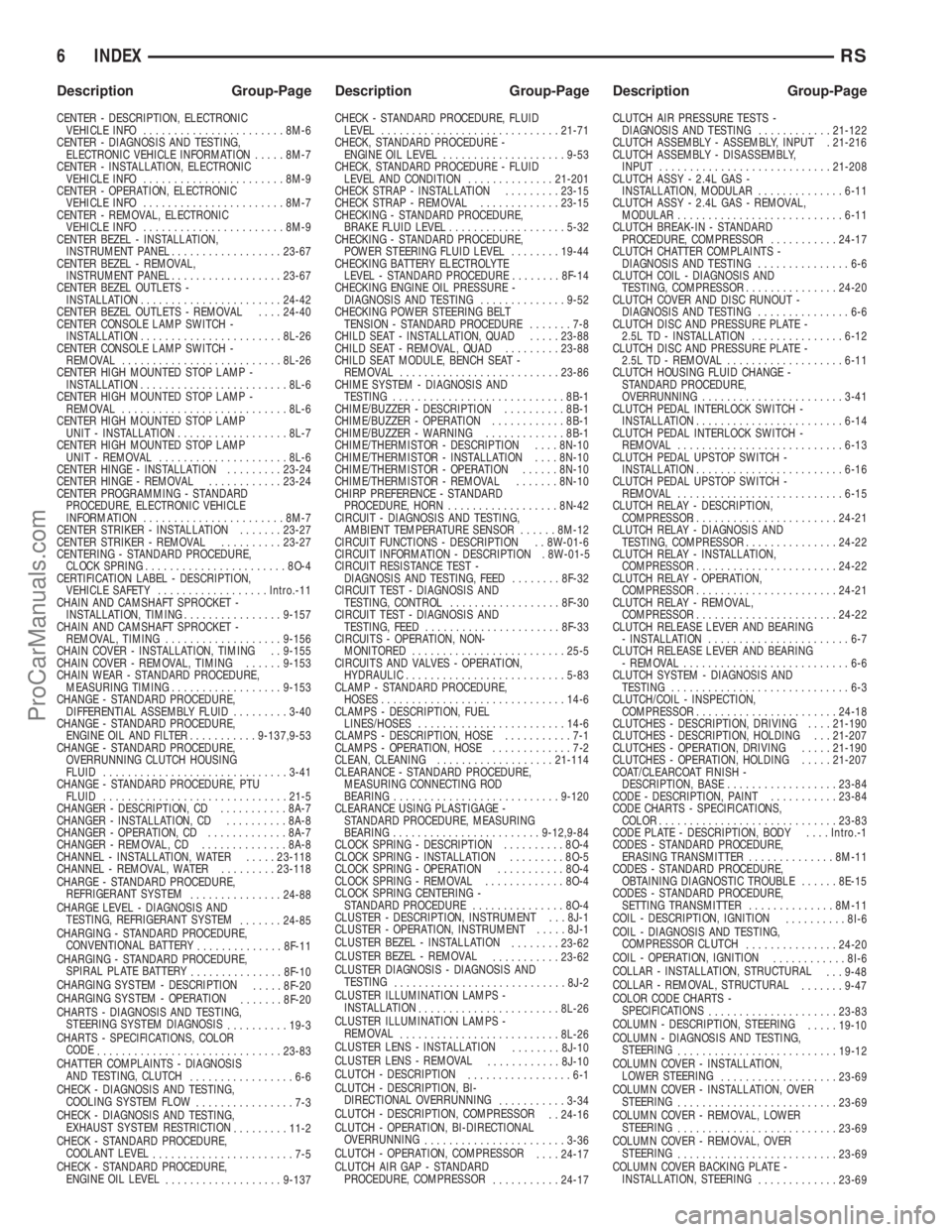
CENTER - DESCRIPTION, ELECTRONIC
VEHICLE INFO.......................8M-6
CENTER - DIAGNOSIS AND TESTING,
ELECTRONIC VEHICLE INFORMATION.....8M-7
CENTER - INSTALLATION, ELECTRONIC
VEHICLE INFO.......................8M-9
CENTER - OPERATION, ELECTRONIC
VEHICLE INFO.......................8M-7
CENTER - REMOVAL, ELECTRONIC
VEHICLE INFO.......................8M-9
CENTER BEZEL - INSTALLATION,
INSTRUMENT PANEL..................23-67
CENTER BEZEL - REMOVAL,
INSTRUMENT PANEL..................23-67
CENTER BEZEL OUTLETS -
INSTALLATION.......................24-42
CENTER BEZEL OUTLETS - REMOVAL....24-40
CENTER CONSOLE LAMP SWITCH -
INSTALLATION.......................8L-26
CENTER CONSOLE LAMP SWITCH -
REMOVAL..........................8L-26
CENTER HIGH MOUNTED STOP LAMP -
INSTALLATION........................8L-6
CENTER HIGH MOUNTED STOP LAMP -
REMOVAL...........................8L-6
CENTER HIGH MOUNTED STOP LAMP
UNIT - INSTALLATION..................8L-7
CENTER HIGH MOUNTED STOP LAMP
UNIT - REMOVAL.....................8L-6
CENTER HINGE - INSTALLATION.........23-24
CENTER HINGE - REMOVAL............23-24
CENTER PROGRAMMING - STANDARD
PROCEDURE, ELECTRONIC VEHICLE
INFORMATION.......................8M-7
CENTER STRIKER - INSTALLATION.......23-27
CENTER STRIKER - REMOVAL..........23-27
CENTERING - STANDARD PROCEDURE,
CLOCK SPRING.......................8O-4
CERTIFICATION LABEL - DESCRIPTION,
VEHICLE SAFETY..................Intro.-11
CHAIN AND CAMSHAFT SPROCKET -
INSTALLATION, TIMING................9-157
CHAIN AND CAMSHAFT SPROCKET -
REMOVAL, TIMING...................9-156
CHAIN COVER - INSTALLATION, TIMING . . 9-155
CHAIN COVER - REMOVAL, TIMING......9-153
CHAIN WEAR - STANDARD PROCEDURE,
MEASURING TIMING..................9-153
CHANGE - STANDARD PROCEDURE,
DIFFERENTIAL ASSEMBLY FLUID.........3-40
CHANGE - STANDARD PROCEDURE,
ENGINE OIL AND FILTER...........9-137,9-53
CHANGE - STANDARD PROCEDURE,
OVERRUNNING CLUTCH HOUSING
FLUID..............................3-41
CHANGE - STANDARD PROCEDURE, PTU
FLUID..............................21-5
CHANGER - DESCRIPTION, CD...........8A-7
CHANGER - INSTALLATION, CD..........8A-8
CHANGER - OPERATION, CD.............8A-7
CHANGER - REMOVAL, CD..............8A-8
CHANNEL - INSTALLATION, WATER.....23-118
CHANNEL - REMOVAL, WATER.........23-118
CHARGE - STANDARD PROCEDURE,
REFRIGERANT SYSTEM
...............24-88
CHARGE LEVEL - DIAGNOSIS AND
TESTING, REFRIGERANT SYSTEM
.......24-85
CHARGING - STANDARD PROCEDURE,
CONVENTIONAL BATTERY
..............8F-11
CHARGING - STANDARD PROCEDURE,
SPIRAL PLATE BATTERY
...............8F-10
CHARGING SYSTEM - DESCRIPTION
.....8F-20
CHARGING SYSTEM - OPERATION
.......8F-20
CHARTS - DIAGNOSIS AND TESTING,
STEERING SYSTEM DIAGNOSIS
..........19-3
CHARTS - SPECIFICATIONS, COLOR
CODE
..............................23-83
CHATTER COMPLAINTS - DIAGNOSIS
AND TESTING, CLUTCH
.................6-6
CHECK - DIAGNOSIS AND TESTING,
COOLING SYSTEM FLOW
................7-3
CHECK - DIAGNOSIS AND TESTING,
EXHAUST SYSTEM RESTRICTION
.........11-2
CHECK - STANDARD PROCEDURE,
COOLANT LEVEL
.......................7-5
CHECK - STANDARD PROCEDURE,
ENGINE OIL LEVEL
...................9-137CHECK - STANDARD PROCEDURE, FLUID
LEVEL.............................21-71
CHECK, STANDARD PROCEDURE -
ENGINE OIL LEVEL....................9-53
CHECK, STANDARD PROCEDURE - FLUID
LEVEL AND CONDITION..............21-201
CHECK STRAP - INSTALLATION.........23-15
CHECK STRAP - REMOVAL.............23-15
CHECKING - STANDARD PROCEDURE,
BRAKE FLUID LEVEL...................5-32
CHECKING - STANDARD PROCEDURE,
POWER STEERING FLUID LEVEL........19-44
CHECKING BATTERY ELECTROLYTE
LEVEL - STANDARD PROCEDURE........8F-14
CHECKING ENGINE OIL PRESSURE -
DIAGNOSIS AND TESTING..............9-52
CHECKING POWER STEERING BELT
TENSION - STANDARD PROCEDURE.......7-8
CHILD SEAT - INSTALLATION, QUAD.....23-88
CHILD SEAT - REMOVAL, QUAD.........23-88
CHILD SEAT MODULE, BENCH SEAT -
REMOVAL..........................23-86
CHIME SYSTEM - DIAGNOSIS AND
TESTING............................8B-1
CHIME/BUZZER - DESCRIPTION..........8B-1
CHIME/BUZZER - OPERATION............8B-1
CHIME/BUZZER - WARNING.............8B-1
CHIME/THERMISTOR - DESCRIPTION....8N-10
CHIME/THERMISTOR - INSTALLATION....8N-10
CHIME/THERMISTOR - OPERATION......8N-10
CHIME/THERMISTOR - REMOVAL.......8N-10
CHIRP PREFERENCE - STANDARD
PROCEDURE, HORN..................8N-42
CIRCUIT - DIAGNOSIS AND TESTING,
AMBIENT TEMPERATURE SENSOR......8M-12
CIRCUIT FUNCTIONS - DESCRIPTION . . 8W-01-6
CIRCUIT INFORMATION - DESCRIPTION . 8W-01-5
CIRCUIT RESISTANCE TEST -
DIAGNOSIS AND TESTING, FEED........8F-32
CIRCUIT TEST - DIAGNOSIS AND
TESTING, CONTROL..................8F-30
CIRCUIT TEST - DIAGNOSIS AND
TESTING, FEED......................8F-33
CIRCUITS - OPERATION, NON-
MONITORED.........................25-5
CIRCUITS AND VALVES - OPERATION,
HYDRAULIC..........................5-83
CLAMP - STANDARD PROCEDURE,
HOSES..............................14-6
CLAMPS - DESCRIPTION, FUEL
LINES/HOSES........................14-6
CLAMPS - DESCRIPTION, HOSE...........7-1
CLAMPS - OPERATION, HOSE.............7-2
CLEAN, CLEANING...................21-114
CLEARANCE - STANDARD PROCEDURE,
MEASURING CONNECTING ROD
BEARING...........................9-120
CLEARANCE USING PLASTIGAGE -
STANDARD PROCEDURE, MEASURING
BEARING........................9-12,9-84
CLOCK SPRING - DESCRIPTION..........8O-4
CLOCK SPRING - INSTALLATION.........8O-5
CLOCK SPRING - OPERATION...........8O-4
CLOCK SPRING - REMOVAL.............8O-4
CLOCK SPRING CENTERING -
STANDARD PROCEDURE...............8O-4
CLUSTER - DESCRIPTION, INSTRUMENT . . . 8J-1
CLUSTER - OPERATION, INSTRUMENT.....8J-1
CLUSTER BEZEL - INSTALLATION
........23-62
CLUSTER BEZEL - REMOVAL
...........23-62
CLUSTER DIAGNOSIS - DIAGNOSIS AND
TESTING
............................8J-2
CLUSTER ILLUMINATION LAMPS -
INSTALLATION
.......................8L-26
CLUSTER ILLUMINATION LAMPS -
REMOVAL
..........................8L-26
CLUSTER LENS - INSTALLATION
........8J-10
CLUSTER LENS - REMOVAL
............8J-10
CLUTCH - DESCRIPTION
.................6-1
CLUTCH - DESCRIPTION, BI-
DIRECTIONAL OVERRUNNING
...........3-34
CLUTCH - DESCRIPTION, COMPRESSOR
. . 24-16
CLUTCH - OPERATION, BI-DIRECTIONAL
OVERRUNNING
.......................3-36
CLUTCH - OPERATION, COMPRESSOR
....24-17
CLUTCH AIR GAP - STANDARD
PROCEDURE, COMPRESSOR
...........24-17CLUTCH AIR PRESSURE TESTS -
DIAGNOSIS AND TESTING............21-122
CLUTCH ASSEMBLY - ASSEMBLY, INPUT . 21-216
CLUTCH ASSEMBLY - DISASSEMBLY,
INPUT............................21-208
CLUTCH ASSY - 2.4L GAS -
INSTALLATION, MODULAR..............6-11
CLUTCH ASSY - 2.4L GAS - REMOVAL,
MODULAR...........................6-11
CLUTCH BREAK-IN - STANDARD
PROCEDURE, COMPRESSOR...........24-17
CLUTCH CHATTER COMPLAINTS -
DIAGNOSIS AND TESTING...............6-6
CLUTCH COIL - DIAGNOSIS AND
TESTING, COMPRESSOR...............24-20
CLUTCH COVER AND DISC RUNOUT -
DIAGNOSIS AND TESTING...............6-6
CLUTCH DISC AND PRESSURE PLATE -
2.5L TD - INSTALLATION...............6-12
CLUTCH DISC AND PRESSURE PLATE -
2.5L TD - REMOVAL...................6-11
CLUTCH HOUSING FLUID CHANGE -
STANDARD PROCEDURE,
OVERRUNNING.......................3-41
CLUTCH PEDAL INTERLOCK SWITCH -
INSTALLATION........................6-14
CLUTCH PEDAL INTERLOCK SWITCH -
REMOVAL...........................6-13
CLUTCH PEDAL UPSTOP SWITCH -
INSTALLATION........................6-16
CLUTCH PEDAL UPSTOP SWITCH -
REMOVAL...........................6-15
CLUTCH RELAY - DESCRIPTION,
COMPRESSOR........................24-21
CLUTCH RELAY - DIAGNOSIS AND
TESTING, COMPRESSOR...............24-22
CLUTCH RELAY - INSTALLATION,
COMPRESSOR.......................24-22
CLUTCH RELAY - OPERATION,
COMPRESSOR.......................24-21
CLUTCH RELAY - REMOVAL,
COMPRESSOR.......................24-22
CLUTCH RELEASE LEVER AND BEARING
- INSTALLATION.......................6-7
CLUTCH RELEASE LEVER AND BEARING
- REMOVAL...........................6-6
CLUTCH SYSTEM - DIAGNOSIS AND
TESTING.............................6-3
CLUTCH/COIL - INSPECTION,
COMPRESSOR.......................24-18
CLUTCHES - DESCRIPTION, DRIVING....21-190
CLUTCHES - DESCRIPTION, HOLDING . . . 21-207
CLUTCHES - OPERATION, DRIVING.....21-190
CLUTCHES - OPERATION, HOLDING.....21-207
COAT/CLEARCOAT FINISH -
DESCRIPTION, BASE..................23-84
CODE - DESCRIPTION, PAINT...........23-84
CODE CHARTS - SPECIFICATIONS,
COLOR.............................23-83
CODE PLATE - DESCRIPTION, BODY....Intro.-1
CODES - STANDARD PROCEDURE,
ERASING TRANSMITTER..............8M-11
CODES - STANDARD PROCEDURE,
OBTAINING DIAGNOSTIC TROUBLE......8E-15
CODES - STANDARD PROCEDURE,
SETTING TRANSMITTER..............8M-11
COIL - DESCRIPTION, IGNITION
..........8I-6
COIL - DIAGNOSIS AND TESTING,
COMPRESSOR CLUTCH
...............24-20
COIL - OPERATION, IGNITION
............8I-6
COLLAR - INSTALLATION, STRUCTURAL
. . . 9-48
COLLAR - REMOVAL, STRUCTURAL
.......9-47
COLOR CODE CHARTS -
SPECIFICATIONS
.....................23-83
COLUMN - DESCRIPTION, STEERING
.....19-10
COLUMN - DIAGNOSIS AND TESTING,
STEERING
..........................19-12
COLUMN COVER - INSTALLATION,
LOWER STEERING
...................23-69
COLUMN COVER - INSTALLATION, OVER
STEERING
..........................23-69
COLUMN COVER - REMOVAL, LOWER
STEERING
..........................23-69
COLUMN COVER - REMOVAL, OVER
STEERING
..........................23-69
COLUMN COVER BACKING PLATE -
INSTALLATION, STEERING
.............23-69
6 INDEXRS
Description Group-Page Description Group-Page Description Group-Page
ProCarManuals.com