air bleeding CHRYSLER CARAVAN 2005 Service Manual
[x] Cancel search | Manufacturer: CHRYSLER, Model Year: 2005, Model line: CARAVAN, Model: CHRYSLER CARAVAN 2005Pages: 2339, PDF Size: 59.69 MB
Page 119 of 2339
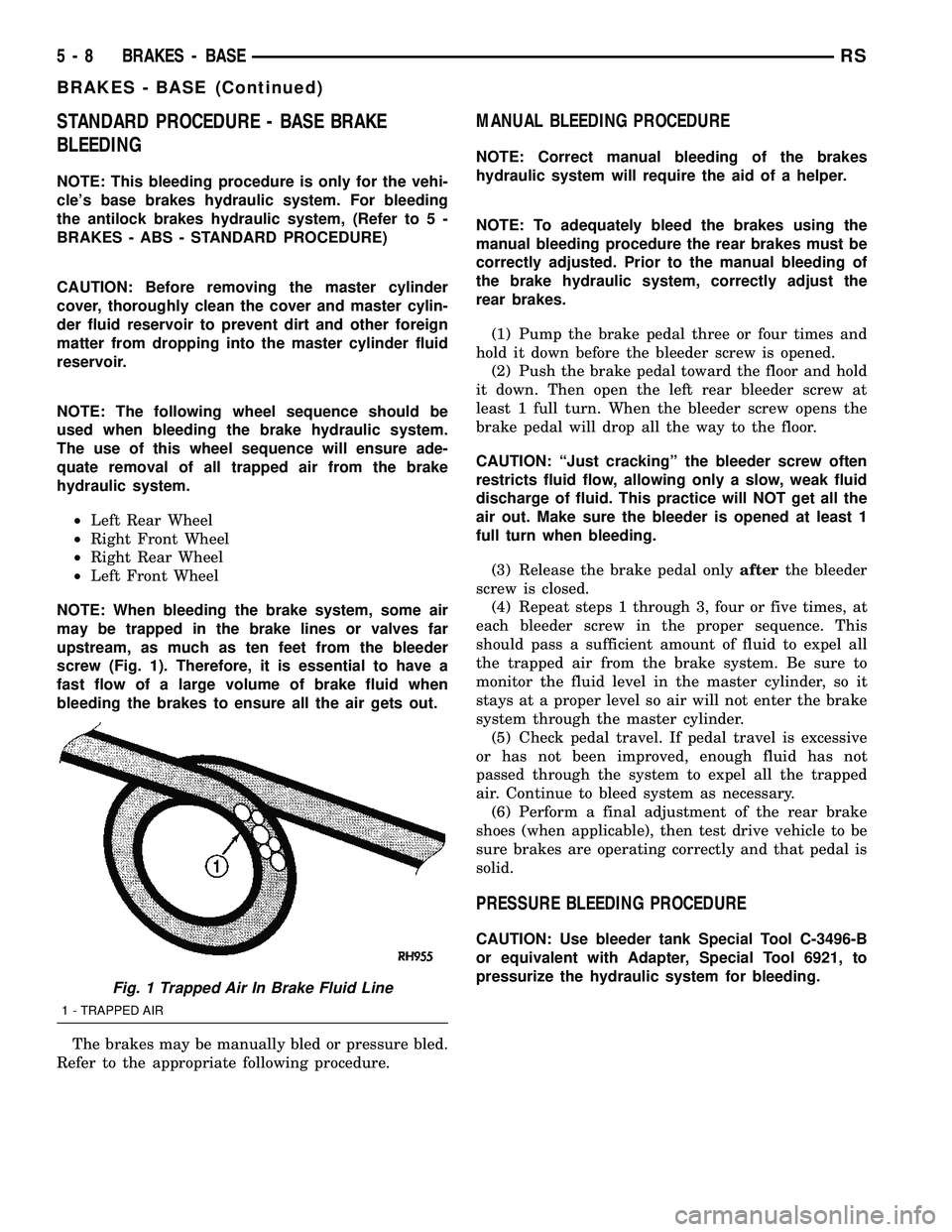
STANDARD PROCEDURE - BASE BRAKE
BLEEDING
NOTE: This bleeding procedure is only for the vehi-
cle's base brakes hydraulic system. For bleeding
the antilock brakes hydraulic system, (Refer to 5 -
BRAKES - ABS - STANDARD PROCEDURE)
CAUTION: Before removing the master cylinder
cover, thoroughly clean the cover and master cylin-
der fluid reservoir to prevent dirt and other foreign
matter from dropping into the master cylinder fluid
reservoir.
NOTE: The following wheel sequence should be
used when bleeding the brake hydraulic system.
The use of this wheel sequence will ensure ade-
quate removal of all trapped air from the brake
hydraulic system.
²Left Rear Wheel
²Right Front Wheel
²Right Rear Wheel
²Left Front Wheel
NOTE: When bleeding the brake system, some air
may be trapped in the brake lines or valves far
upstream, as much as ten feet from the bleeder
screw (Fig. 1). Therefore, it is essential to have a
fast flow of a large volume of brake fluid when
bleeding the brakes to ensure all the air gets out.
The brakes may be manually bled or pressure bled.
Refer to the appropriate following procedure.
MANUAL BLEEDING PROCEDURE
NOTE: Correct manual bleeding of the brakes
hydraulic system will require the aid of a helper.
NOTE: To adequately bleed the brakes using the
manual bleeding procedure the rear brakes must be
correctly adjusted. Prior to the manual bleeding of
the brake hydraulic system, correctly adjust the
rear brakes.
(1) Pump the brake pedal three or four times and
hold it down before the bleeder screw is opened.
(2) Push the brake pedal toward the floor and hold
it down. Then open the left rear bleeder screw at
least 1 full turn. When the bleeder screw opens the
brake pedal will drop all the way to the floor.
CAUTION: ªJust crackingº the bleeder screw often
restricts fluid flow, allowing only a slow, weak fluid
discharge of fluid. This practice will NOT get all the
air out. Make sure the bleeder is opened at least 1
full turn when bleeding.
(3) Release the brake pedal onlyafterthe bleeder
screw is closed.
(4) Repeat steps 1 through 3, four or five times, at
each bleeder screw in the proper sequence. This
should pass a sufficient amount of fluid to expel all
the trapped air from the brake system. Be sure to
monitor the fluid level in the master cylinder, so it
stays at a proper level so air will not enter the brake
system through the master cylinder.
(5) Check pedal travel. If pedal travel is excessive
or has not been improved, enough fluid has not
passed through the system to expel all the trapped
air. Continue to bleed system as necessary.
(6) Perform a final adjustment of the rear brake
shoes (when applicable), then test drive vehicle to be
sure brakes are operating correctly and that pedal is
solid.
PRESSURE BLEEDING PROCEDURE
CAUTION: Use bleeder tank Special Tool C-3496-B
or equivalent with Adapter, Special Tool 6921, to
pressurize the hydraulic system for bleeding.
Fig. 1 Trapped Air In Brake Fluid Line
1 - TRAPPED AIR
5 - 8 BRAKES - BASERS
BRAKES - BASE (Continued)
Page 120 of 2339
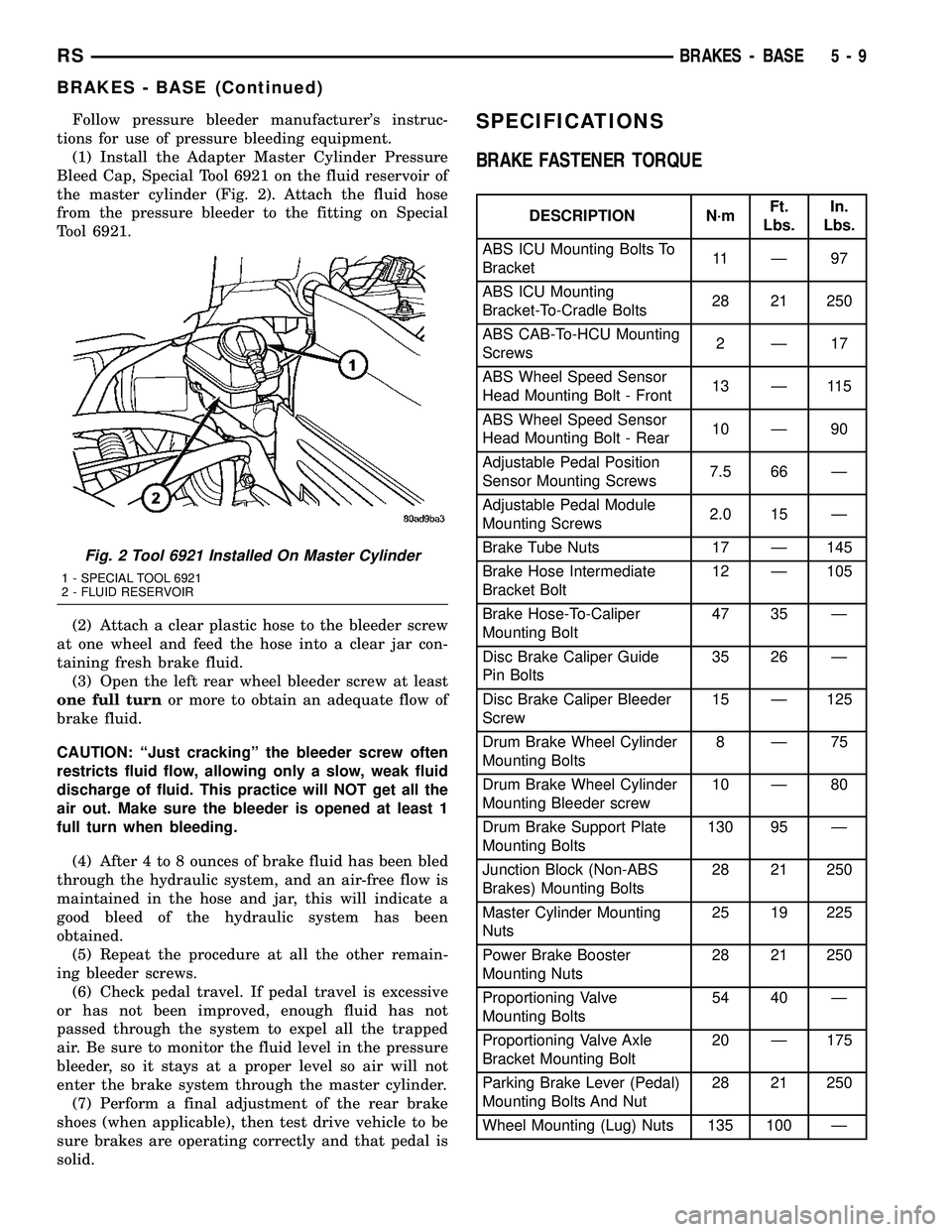
Follow pressure bleeder manufacturer's instruc-
tions for use of pressure bleeding equipment.
(1) Install the Adapter Master Cylinder Pressure
Bleed Cap, Special Tool 6921 on the fluid reservoir of
the master cylinder (Fig. 2). Attach the fluid hose
from the pressure bleeder to the fitting on Special
Tool 6921.
(2) Attach a clear plastic hose to the bleeder screw
at one wheel and feed the hose into a clear jar con-
taining fresh brake fluid.
(3) Open the left rear wheel bleeder screw at least
one full turnor more to obtain an adequate flow of
brake fluid.
CAUTION: ªJust crackingº the bleeder screw often
restricts fluid flow, allowing only a slow, weak fluid
discharge of fluid. This practice will NOT get all the
air out. Make sure the bleeder is opened at least 1
full turn when bleeding.
(4) After 4 to 8 ounces of brake fluid has been bled
through the hydraulic system, and an air-free flow is
maintained in the hose and jar, this will indicate a
good bleed of the hydraulic system has been
obtained.
(5) Repeat the procedure at all the other remain-
ing bleeder screws.
(6) Check pedal travel. If pedal travel is excessive
or has not been improved, enough fluid has not
passed through the system to expel all the trapped
air. Be sure to monitor the fluid level in the pressure
bleeder, so it stays at a proper level so air will not
enter the brake system through the master cylinder.
(7) Perform a final adjustment of the rear brake
shoes (when applicable), then test drive vehicle to be
sure brakes are operating correctly and that pedal is
solid.SPECIFICATIONS
BRAKE FASTENER TORQUE
DESCRIPTION N´mFt.
Lbs.In.
Lbs.
ABS ICU Mounting Bolts To
Bracket11 Ð 9 7
ABS ICU Mounting
Bracket-To-Cradle Bolts28 21 250
ABS CAB-To-HCU Mounting
Screws2Ð17
ABS Wheel Speed Sensor
Head Mounting Bolt - Front13 Ð 115
ABS Wheel Speed Sensor
Head Mounting Bolt - Rear10 Ð 90
Adjustable Pedal Position
Sensor Mounting Screws7.5 66 Ð
Adjustable Pedal Module
Mounting Screws2.0 15 Ð
Brake Tube Nuts 17 Ð 145
Brake Hose Intermediate
Bracket Bolt12 Ð 105
Brake Hose-To-Caliper
Mounting Bolt47 35 Ð
Disc Brake Caliper Guide
Pin Bolts35 26 Ð
Disc Brake Caliper Bleeder
Screw15 Ð 125
Drum Brake Wheel Cylinder
Mounting Bolts8Ð75
Drum Brake Wheel Cylinder
Mounting Bleeder screw10 Ð 80
Drum Brake Support Plate
Mounting Bolts130 95 Ð
Junction Block (Non-ABS
Brakes) Mounting Bolts28 21 250
Master Cylinder Mounting
Nuts25 19 225
Power Brake Booster
Mounting Nuts28 21 250
Proportioning Valve
Mounting Bolts54 40 Ð
Proportioning Valve Axle
Bracket Mounting Bolt20 Ð 175
Parking Brake Lever (Pedal)
Mounting Bolts And Nut28 21 250
Wheel Mounting (Lug) Nuts 135 100 Ð
Fig. 2 Tool 6921 Installed On Master Cylinder
1 - SPECIAL TOOL 6921
2 - FLUID RESERVOIR
RSBRAKES - BASE5-9
BRAKES - BASE (Continued)
Page 147 of 2339
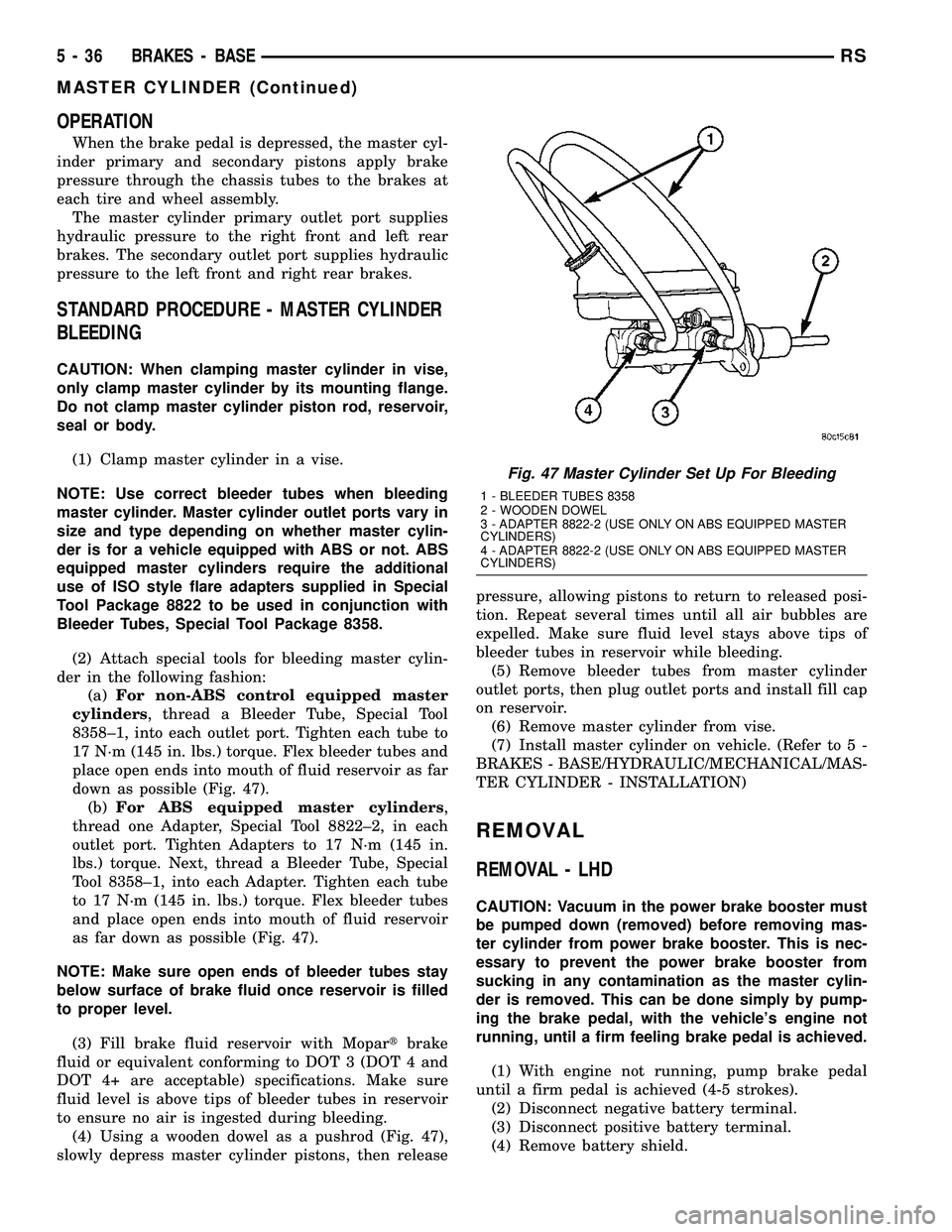
OPERATION
When the brake pedal is depressed, the master cyl-
inder primary and secondary pistons apply brake
pressure through the chassis tubes to the brakes at
each tire and wheel assembly.
The master cylinder primary outlet port supplies
hydraulic pressure to the right front and left rear
brakes. The secondary outlet port supplies hydraulic
pressure to the left front and right rear brakes.
STANDARD PROCEDURE - MASTER CYLINDER
BLEEDING
CAUTION: When clamping master cylinder in vise,
only clamp master cylinder by its mounting flange.
Do not clamp master cylinder piston rod, reservoir,
seal or body.
(1) Clamp master cylinder in a vise.
NOTE: Use correct bleeder tubes when bleeding
master cylinder. Master cylinder outlet ports vary in
size and type depending on whether master cylin-
der is for a vehicle equipped with ABS or not. ABS
equipped master cylinders require the additional
use of ISO style flare adapters supplied in Special
Tool Package 8822 to be used in conjunction with
Bleeder Tubes, Special Tool Package 8358.
(2) Attach special tools for bleeding master cylin-
der in the following fashion:
(a)For non-ABS control equipped master
cylinders, thread a Bleeder Tube, Special Tool
8358±1, into each outlet port. Tighten each tube to
17 N´m (145 in. lbs.) torque. Flex bleeder tubes and
place open ends into mouth of fluid reservoir as far
down as possible (Fig. 47).
(b)For ABS equipped master cylinders,
thread one Adapter, Special Tool 8822±2, in each
outlet port. Tighten Adapters to 17 N´m (145 in.
lbs.) torque. Next, thread a Bleeder Tube, Special
Tool 8358±1, into each Adapter. Tighten each tube
to 17 N´m (145 in. lbs.) torque. Flex bleeder tubes
and place open ends into mouth of fluid reservoir
as far down as possible (Fig. 47).
NOTE: Make sure open ends of bleeder tubes stay
below surface of brake fluid once reservoir is filled
to proper level.
(3) Fill brake fluid reservoir with Mopartbrake
fluid or equivalent conforming to DOT 3 (DOT 4 and
DOT 4+ are acceptable) specifications. Make sure
fluid level is above tips of bleeder tubes in reservoir
to ensure no air is ingested during bleeding.
(4) Using a wooden dowel as a pushrod (Fig. 47),
slowly depress master cylinder pistons, then releasepressure, allowing pistons to return to released posi-
tion. Repeat several times until all air bubbles are
expelled. Make sure fluid level stays above tips of
bleeder tubes in reservoir while bleeding.
(5) Remove bleeder tubes from master cylinder
outlet ports, then plug outlet ports and install fill cap
on reservoir.
(6) Remove master cylinder from vise.
(7) Install master cylinder on vehicle. (Refer to 5 -
BRAKES - BASE/HYDRAULIC/MECHANICAL/MAS-
TER CYLINDER - INSTALLATION)
REMOVAL
REMOVAL - LHD
CAUTION: Vacuum in the power brake booster must
be pumped down (removed) before removing mas-
ter cylinder from power brake booster. This is nec-
essary to prevent the power brake booster from
sucking in any contamination as the master cylin-
der is removed. This can be done simply by pump-
ing the brake pedal, with the vehicle's engine not
running, until a firm feeling brake pedal is achieved.
(1) With engine not running, pump brake pedal
until a firm pedal is achieved (4-5 strokes).
(2) Disconnect negative battery terminal.
(3) Disconnect positive battery terminal.
(4) Remove battery shield.
Fig. 47 Master Cylinder Set Up For Bleeding
1 - BLEEDER TUBES 8358
2 - WOODEN DOWEL
3 - ADAPTER 8822-2 (USE ONLY ON ABS EQUIPPED MASTER
CYLINDERS)
4 - ADAPTER 8822-2 (USE ONLY ON ABS EQUIPPED MASTER
CYLINDERS)
5 - 36 BRAKES - BASERS
MASTER CYLINDER (Continued)
Page 198 of 2339
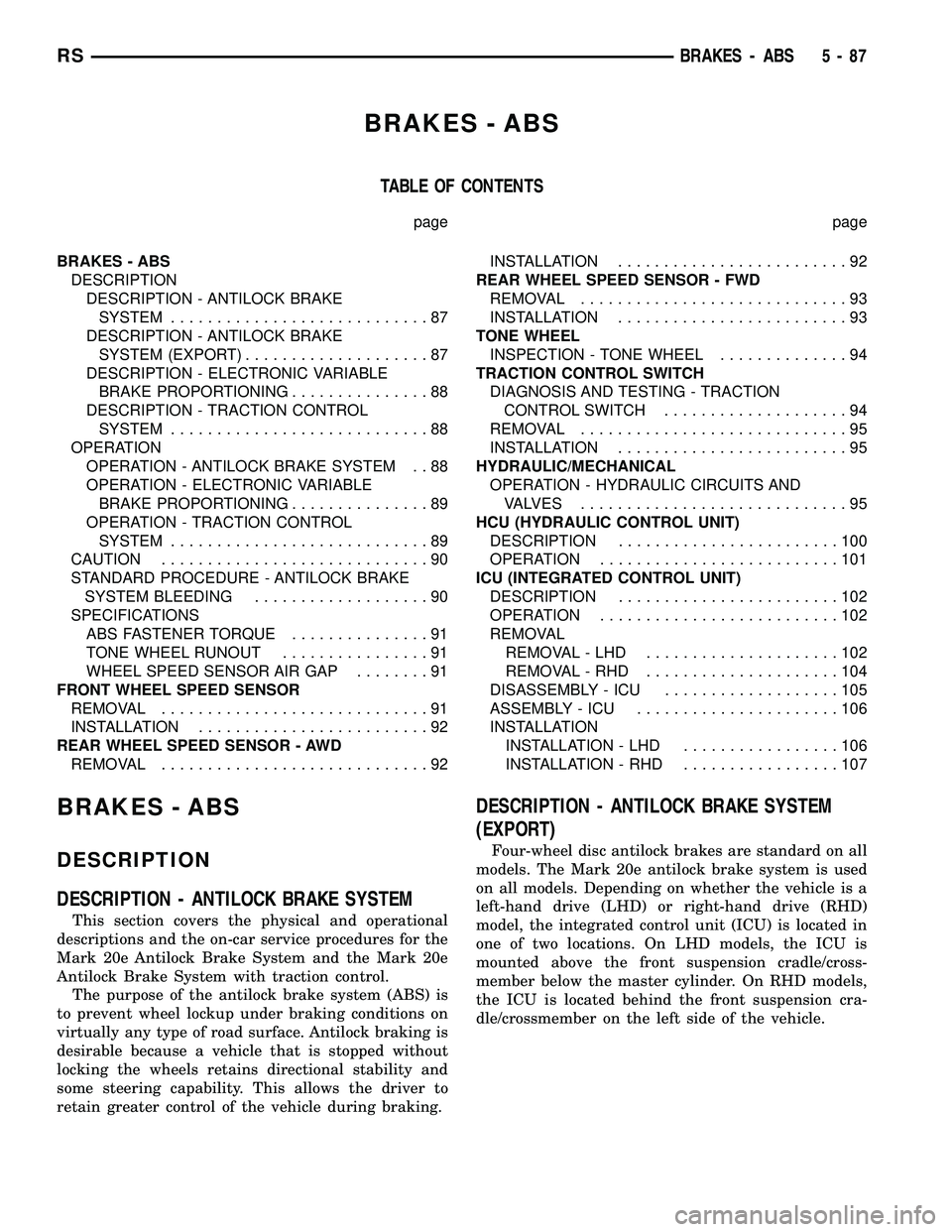
BRAKES - ABS
TABLE OF CONTENTS
page page
BRAKES - ABS
DESCRIPTION
DESCRIPTION - ANTILOCK BRAKE
SYSTEM............................87
DESCRIPTION - ANTILOCK BRAKE
SYSTEM (EXPORT)....................87
DESCRIPTION - ELECTRONIC VARIABLE
BRAKE PROPORTIONING...............88
DESCRIPTION - TRACTION CONTROL
SYSTEM............................88
OPERATION
OPERATION - ANTILOCK BRAKE SYSTEM . . 88
OPERATION - ELECTRONIC VARIABLE
BRAKE PROPORTIONING...............89
OPERATION - TRACTION CONTROL
SYSTEM............................89
CAUTION.............................90
STANDARD PROCEDURE - ANTILOCK BRAKE
SYSTEM BLEEDING...................90
SPECIFICATIONS
ABS FASTENER TORQUE...............91
TONE WHEEL RUNOUT................91
WHEEL SPEED SENSOR AIR GAP........91
FRONT WHEEL SPEED SENSOR
REMOVAL.............................91
INSTALLATION.........................92
REAR WHEEL SPEED SENSOR - AWD
REMOVAL.............................92INSTALLATION.........................92
REAR WHEEL SPEED SENSOR - FWD
REMOVAL.............................93
INSTALLATION.........................93
TONE WHEEL
INSPECTION - TONE WHEEL..............94
TRACTION CONTROL SWITCH
DIAGNOSIS AND TESTING - TRACTION
CONTROL SWITCH....................94
REMOVAL.............................95
INSTALLATION.........................95
HYDRAULIC/MECHANICAL
OPERATION - HYDRAULIC CIRCUITS AND
VALVES .............................95
HCU (HYDRAULIC CONTROL UNIT)
DESCRIPTION........................100
OPERATION..........................101
ICU (INTEGRATED CONTROL UNIT)
DESCRIPTION........................102
OPERATION..........................102
REMOVAL
REMOVAL - LHD.....................102
REMOVAL - RHD.....................104
DISASSEMBLY - ICU...................105
ASSEMBLY - ICU......................106
INSTALLATION
INSTALLATION - LHD.................106
INSTALLATION - RHD.................107
BRAKES - ABS
DESCRIPTION
DESCRIPTION - ANTILOCK BRAKE SYSTEM
This section covers the physical and operational
descriptions and the on-car service procedures for the
Mark 20e Antilock Brake System and the Mark 20e
Antilock Brake System with traction control.
The purpose of the antilock brake system (ABS) is
to prevent wheel lockup under braking conditions on
virtually any type of road surface. Antilock braking is
desirable because a vehicle that is stopped without
locking the wheels retains directional stability and
some steering capability. This allows the driver to
retain greater control of the vehicle during braking.
DESCRIPTION - ANTILOCK BRAKE SYSTEM
(EXPORT)
Four-wheel disc antilock brakes are standard on all
models. The Mark 20e antilock brake system is used
on all models. Depending on whether the vehicle is a
left-hand drive (LHD) or right-hand drive (RHD)
model, the integrated control unit (ICU) is located in
one of two locations. On LHD models, the ICU is
mounted above the front suspension cradle/cross-
member below the master cylinder. On RHD models,
the ICU is located behind the front suspension cra-
dle/crossmember on the left side of the vehicle.
RSBRAKES - ABS5-87
Page 201 of 2339
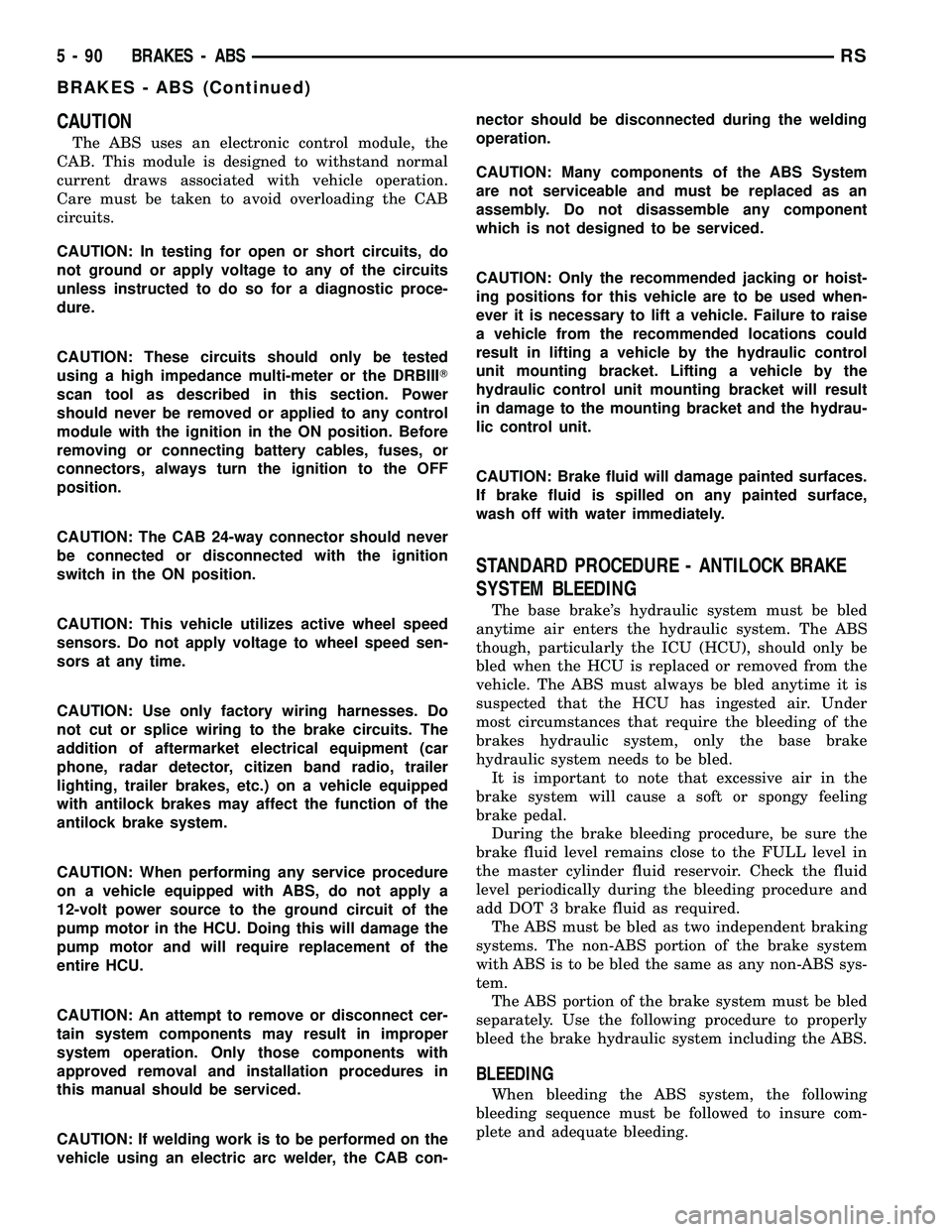
CAUTION
The ABS uses an electronic control module, the
CAB. This module is designed to withstand normal
current draws associated with vehicle operation.
Care must be taken to avoid overloading the CAB
circuits.
CAUTION: In testing for open or short circuits, do
not ground or apply voltage to any of the circuits
unless instructed to do so for a diagnostic proce-
dure.
CAUTION: These circuits should only be tested
using a high impedance multi-meter or the DRBIIIT
scan tool as described in this section. Power
should never be removed or applied to any control
module with the ignition in the ON position. Before
removing or connecting battery cables, fuses, or
connectors, always turn the ignition to the OFF
position.
CAUTION: The CAB 24-way connector should never
be connected or disconnected with the ignition
switch in the ON position.
CAUTION: This vehicle utilizes active wheel speed
sensors. Do not apply voltage to wheel speed sen-
sors at any time.
CAUTION: Use only factory wiring harnesses. Do
not cut or splice wiring to the brake circuits. The
addition of aftermarket electrical equipment (car
phone, radar detector, citizen band radio, trailer
lighting, trailer brakes, etc.) on a vehicle equipped
with antilock brakes may affect the function of the
antilock brake system.
CAUTION: When performing any service procedure
on a vehicle equipped with ABS, do not apply a
12-volt power source to the ground circuit of the
pump motor in the HCU. Doing this will damage the
pump motor and will require replacement of the
entire HCU.
CAUTION: An attempt to remove or disconnect cer-
tain system components may result in improper
system operation. Only those components with
approved removal and installation procedures in
this manual should be serviced.
CAUTION: If welding work is to be performed on the
vehicle using an electric arc welder, the CAB con-nector should be disconnected during the welding
operation.
CAUTION: Many components of the ABS System
are not serviceable and must be replaced as an
assembly. Do not disassemble any component
which is not designed to be serviced.
CAUTION: Only the recommended jacking or hoist-
ing positions for this vehicle are to be used when-
ever it is necessary to lift a vehicle. Failure to raise
a vehicle from the recommended locations could
result in lifting a vehicle by the hydraulic control
unit mounting bracket. Lifting a vehicle by the
hydraulic control unit mounting bracket will result
in damage to the mounting bracket and the hydrau-
lic control unit.
CAUTION: Brake fluid will damage painted surfaces.
If brake fluid is spilled on any painted surface,
wash off with water immediately.
STANDARD PROCEDURE - ANTILOCK BRAKE
SYSTEM BLEEDING
The base brake's hydraulic system must be bled
anytime air enters the hydraulic system. The ABS
though, particularly the ICU (HCU), should only be
bled when the HCU is replaced or removed from the
vehicle. The ABS must always be bled anytime it is
suspected that the HCU has ingested air. Under
most circumstances that require the bleeding of the
brakes hydraulic system, only the base brake
hydraulic system needs to be bled.
It is important to note that excessive air in the
brake system will cause a soft or spongy feeling
brake pedal.
During the brake bleeding procedure, be sure the
brake fluid level remains close to the FULL level in
the master cylinder fluid reservoir. Check the fluid
level periodically during the bleeding procedure and
add DOT 3 brake fluid as required.
The ABS must be bled as two independent braking
systems. The non-ABS portion of the brake system
with ABS is to be bled the same as any non-ABS sys-
tem.
The ABS portion of the brake system must be bled
separately. Use the following procedure to properly
bleed the brake hydraulic system including the ABS.
BLEEDING
When bleeding the ABS system, the following
bleeding sequence must be followed to insure com-
plete and adequate bleeding.
5 - 90 BRAKES - ABSRS
BRAKES - ABS (Continued)
Page 202 of 2339
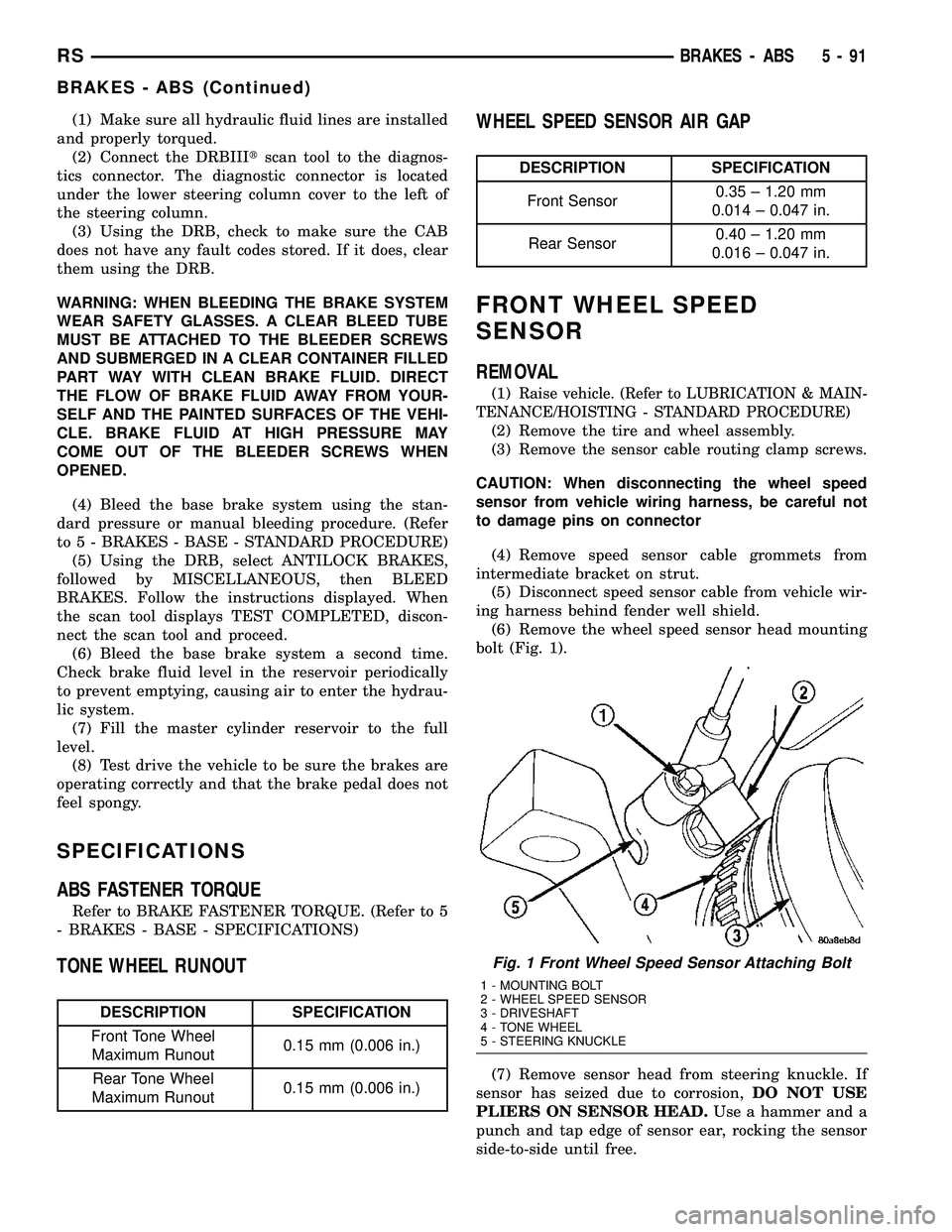
(1) Make sure all hydraulic fluid lines are installed
and properly torqued.
(2) Connect the DRBIIItscan tool to the diagnos-
tics connector. The diagnostic connector is located
under the lower steering column cover to the left of
the steering column.
(3) Using the DRB, check to make sure the CAB
does not have any fault codes stored. If it does, clear
them using the DRB.
WARNING: WHEN BLEEDING THE BRAKE SYSTEM
WEAR SAFETY GLASSES. A CLEAR BLEED TUBE
MUST BE ATTACHED TO THE BLEEDER SCREWS
AND SUBMERGED IN A CLEAR CONTAINER FILLED
PART WAY WITH CLEAN BRAKE FLUID. DIRECT
THE FLOW OF BRAKE FLUID AWAY FROM YOUR-
SELF AND THE PAINTED SURFACES OF THE VEHI-
CLE. BRAKE FLUID AT HIGH PRESSURE MAY
COME OUT OF THE BLEEDER SCREWS WHEN
OPENED.
(4) Bleed the base brake system using the stan-
dard pressure or manual bleeding procedure. (Refer
to 5 - BRAKES - BASE - STANDARD PROCEDURE)
(5) Using the DRB, select ANTILOCK BRAKES,
followed by MISCELLANEOUS, then BLEED
BRAKES. Follow the instructions displayed. When
the scan tool displays TEST COMPLETED, discon-
nect the scan tool and proceed.
(6) Bleed the base brake system a second time.
Check brake fluid level in the reservoir periodically
to prevent emptying, causing air to enter the hydrau-
lic system.
(7) Fill the master cylinder reservoir to the full
level.
(8) Test drive the vehicle to be sure the brakes are
operating correctly and that the brake pedal does not
feel spongy.
SPECIFICATIONS
ABS FASTENER TORQUE
Refer to BRAKE FASTENER TORQUE. (Refer to 5
- BRAKES - BASE - SPECIFICATIONS)
TONE WHEEL RUNOUT
DESCRIPTION SPECIFICATION
Front Tone Wheel
Maximum Runout0.15 mm (0.006 in.)
Rear Tone Wheel
Maximum Runout0.15 mm (0.006 in.)
WHEEL SPEED SENSOR AIR GAP
DESCRIPTION SPECIFICATION
Front Sensor0.35 ± 1.20 mm
0.014 ± 0.047 in.
Rear Sensor0.40 ± 1.20 mm
0.016 ± 0.047 in.
FRONT WHEEL SPEED
SENSOR
REMOVAL
(1)Raise vehicle. (Refer to LUBRICATION & MAIN-
TENANCE/HOISTING - STANDARD PROCEDURE)
(2) Remove the tire and wheel assembly.
(3) Remove the sensor cable routing clamp screws.
CAUTION: When disconnecting the wheel speed
sensor from vehicle wiring harness, be careful not
to damage pins on connector
(4) Remove speed sensor cable grommets from
intermediate bracket on strut.
(5) Disconnect speed sensor cable from vehicle wir-
ing harness behind fender well shield.
(6) Remove the wheel speed sensor head mounting
bolt (Fig. 1).
(7) Remove sensor head from steering knuckle. If
sensor has seized due to corrosion,DO NOT USE
PLIERS ON SENSOR HEAD.Use a hammer and a
punch and tap edge of sensor ear, rocking the sensor
side-to-side until free.
Fig. 1 Front Wheel Speed Sensor Attaching Bolt
1 - MOUNTING BOLT
2 - WHEEL SPEED SENSOR
3 - DRIVESHAFT
4 - TONE WHEEL
5 - STEERING KNUCKLE
RSBRAKES - ABS5-91
BRAKES - ABS (Continued)
Page 2303 of 2339
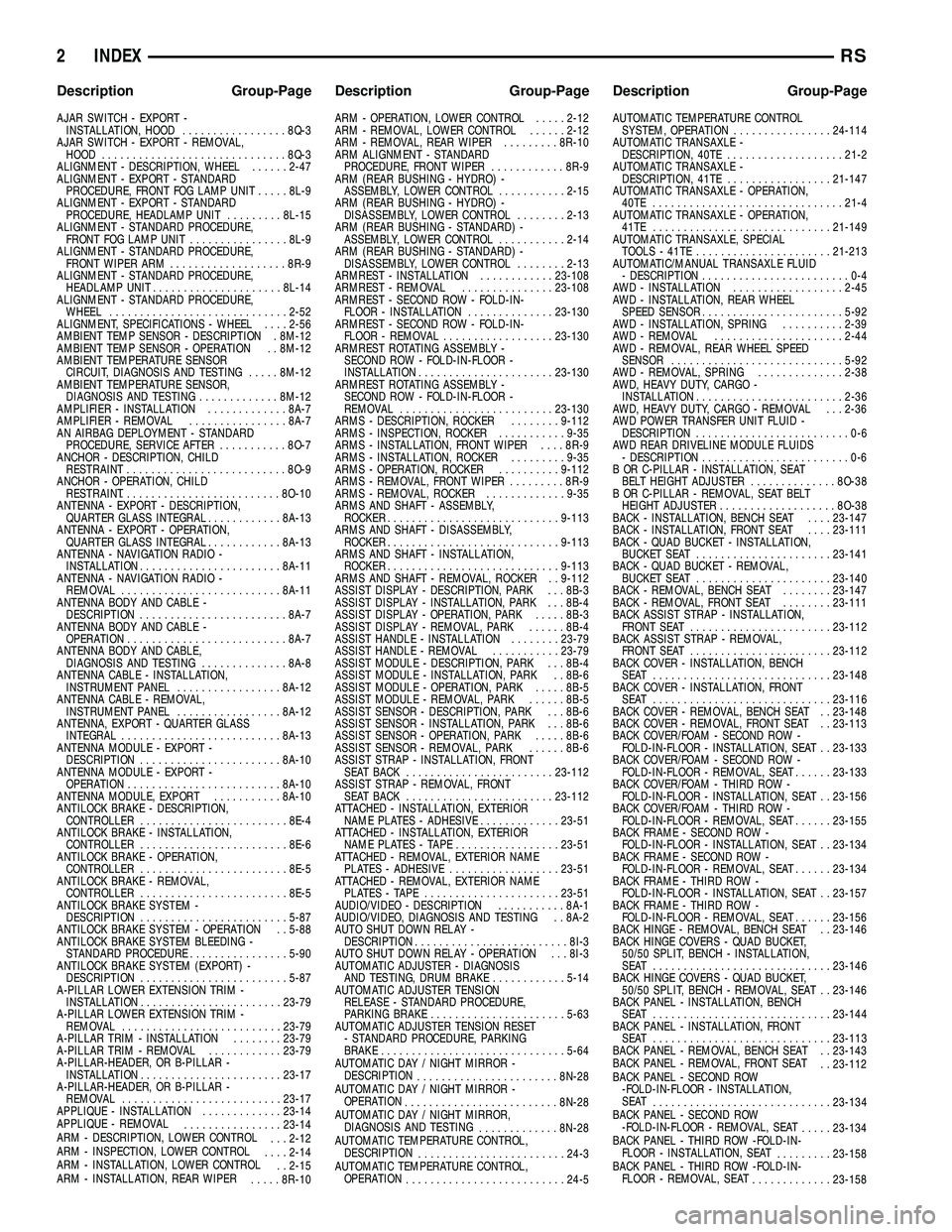
AJAR SWITCH - EXPORT -INSTALLATION, HOOD .................8Q-3
AJAR SWITCH - EXPORT - REMOVAL, HOOD .............................. 8Q-3
ALIGNMENT - DESCRIPTION, WHEEL ......2-47
ALIGNMENT - EXPORT - STANDARD PROCEDURE, FRONT FOG LAMP UNIT .....8L-9
ALIGNMENT - EXPORT - STANDARD PROCEDURE, HEADLAMP UNIT .........8L-15
ALIGNMENT - STANDARD PROCEDURE, FRONT FOG LAMP UNIT ................8L-9
ALIGNMENT - STANDARD PROCEDURE, FRONT WIPER ARM ................... 8R-9
ALIGNMENT - STANDARD PROCEDURE, HEADLAMP UNIT ..................... 8L-14
ALIGNMENT - STANDARD PROCEDURE, WHEEL ............................. 2-52
ALIGNMENT, SPECIFICATIONS - WHEEL ....2-56
AMBIENT TEMP SENSOR - DESCRIPTION . 8M-12
AMBIENT TEMP SENSOR - OPERATION . . 8M-12
AMBIENT TEMPERATURE SENSOR CIRCUIT, DIAGNOSIS AND TESTING .....8M-12
AMBIENT TEMPERATURE SENSOR, DIAGNOSIS AND TESTING .............8M-12
AMPLIFIER - INSTALLATION .............8A-7
AMPLIFIER - REMOVAL ................8A-7
AN AIRBAG DEPLOYMENT - STANDARD PROCEDURE, SERVICE AFTER ...........8O-7
ANCHOR - DESCRIPTION, CHILD RESTRAINT .......................... 8O-9
ANCHOR - OPERATION, CHILD RESTRAINT .......................... 8O-10
ANTENNA - EXPORT - DESCRIPTION, QUARTER GLASS INTEGRAL ............8A-13
ANTENNA - EXPORT - OPERATION, QUARTER GLASS INTEGRAL ............8A-13
ANTENNA - NAVIGATION RADIO - INSTALLATION ....................... 8A-11
ANTENNA - NAVIGATION RADIO - REMOVAL .......................... 8A-11
ANTENNA BODY AND CABLE - DESCRIPTION ........................ 8A-7
ANTENNA BODY AND CABLE - OPERATION .......................... 8A-7
ANTENNA BODY AND CABLE, DIAGNOSIS AND TESTING ..............8A-8
ANTENNA CABLE - INSTALLATION, INSTRUMENT PANEL .................8A-12
ANTENNA CABLE - REMOVAL, INSTRUMENT PANEL .................8A-12
ANTENNA, EXPORT - QUARTER GLASS INTEGRAL .......................... 8A-13
ANTENNA MODULE - EXPORT - DESCRIPTION ....................... 8A-10
ANTENNA MODULE - EXPORT - OPERATION ......................... 8A-10
ANTENNA MODULE, EXPORT ...........8A-10
ANTILOCK BRAKE - DESCRIPTION, CONTROLLER ........................ 8E-4
ANTILOCK BRAKE - INSTALLATION, CONTROLLER ........................ 8E-6
ANTILOCK BRAKE - OPERATION, CONTROLLER ........................ 8E-5
ANTILOCK BRAKE - REMOVAL, CONTROLLER ........................ 8E-5
ANTILOCK BRAKE SYSTEM - DESCRIPTION ........................ 5-87
ANTILOCK BRAKE SYSTEM - OPERATION . . 5-88
ANTILOCK BRAKE SYSTEM BLEEDING - STANDARD PROCEDURE ................5-90
ANTILOCK BRAKE SYSTEM (EXPORT) - DESCRIPTION ........................ 5-87
A-PILLAR LOWER EXTENSION TRIM - INSTALLATION ....................... 23-79
A-PILLAR LOWER EXTENSION TRIM - REMOVAL .......................... 23-79
A-PILLAR TRIM - INSTALLATION ........23-79
A-PILLAR TRIM - REMOVAL ............23-79
A-PILLAR-HEADER, OR B-PILLAR - INSTALLATION ....................... 23-17
A-PILLAR-HEADER, OR B-PILLAR - REMOVAL .......................... 23-17
APPLIQUE - INSTALLATION .............23-14
APPLIQUE - REMOVAL ................23-14
ARM - DESCRIPTION, LOWER CONTROL . . . 2-12
ARM - INSPECTION, LOWER CONTROL ....2-14
ARM - INSTALLATION, LOWER CONTROL . . 2-15
ARM - INSTALLATION, REAR WIPER .....8R-10 ARM - OPERATION, LOWER CONTROL
.....2-12
ARM - REMOVAL, LOWER CONTROL ......2-12
ARM - REMOVAL, REAR WIPER .........8R-10
ARM ALIGNMENT - STANDARD PROCEDURE, FRONT WIPER ............8R-9
ARM (REAR BUSHING - HYDRO) - ASSEMBLY, LOWER CONTROL ...........2-15
ARM (REAR BUSHING - HYDRO) - DISASSEMBLY, LOWER CONTROL ........2-13
ARM (REAR BUSHING - STANDARD) - ASSEMBLY, LOWER CONTROL ...........2-14
ARM (REAR BUSHING - STANDARD) - DISASSEMBLY, LOWER CONTROL ........2-13
ARMREST - INSTALLATION ............23-108
ARMREST - REMOVAL ...............23-108
ARMREST - SECOND ROW - FOLD-IN- FLOOR - INSTALLATION ..............23-130
ARMREST - SECOND ROW - FOLD-IN- FLOOR - REMOVAL .................. 23-130
ARMREST ROTATING ASSEMBLY - SECOND ROW - FOLD-IN-FLOOR -
INSTALLATION ...................... 23-130
ARMREST ROTATING ASSEMBLY - SECOND ROW - FOLD-IN-FLOOR -
REMOVAL ......................... 23-130
ARMS - DESCRIPTION, ROCKER ........9-112
ARMS - INSPECTION, ROCKER ...........9-35
ARMS - INSTALLATION, FRONT WIPER ....8R-9
ARMS - INSTALLATION, ROCKER .........9-35
ARMS - OPERATION, ROCKER ..........9-112
ARMS - REMOVAL, FRONT WIPER .........8R-9
ARMS - REMOVAL, ROCKER .............9-35
ARMS AND SHAFT - ASSEMBLY, ROCKER ............................ 9-113
ARMS AND SHAFT - DISASSEMBLY, ROCKER ............................ 9-113
ARMS AND SHAFT - INSTALLATION, ROCKER ............................ 9-113
ARMS AND SHAFT - REMOVAL, ROCKER . . 9-112
ASSIST DISPLAY - DESCRIPTION, PARK . . . 8B-3
ASSIST DISPLAY - INSTALLATION, PARK . . . 8B-4
ASSIST DISPLAY - OPERATION, PARK .....8B-3
ASSIST DISPLAY - REMOVAL, PARK ......8B-4
ASSIST HANDLE - INSTALLATION ........23-79
ASSIST HANDLE - REMOVAL ...........23-79
ASSIST MODULE - DESCRIPTION, PARK . . . 8B-4
ASSIST MODULE - INSTALLATION, PARK . . 8B-6
ASSIST MODULE - OPERATION, PARK .....8B-5
ASSIST MODULE - REMOVAL, PARK ......8B-5
ASSIST SENSOR - DESCRIPTION, PARK . . . 8B-6
ASSIST SENSOR - INSTALLATION, PARK . . . 8B-6
ASSIST SENSOR - OPERATION, PARK .....8B-6
ASSIST SENSOR - REMOVAL, PARK ......8B-6
ASSIST STRAP - INSTALLATION, FRONT SEAT BACK ........................ 23-112
ASSIST STRAP - REMOVAL, FRONT SEAT BACK ........................ 23-112
ATTACHED - INSTALLATION, EXTERIOR NAME PLATES - ADHESIVE .............23-51
ATTACHED - INSTALLATION, EXTERIOR NAME PLATES - TAPE .................23-51
ATTACHED - REMOVAL, EXTERIOR NAME PLATES - ADHESIVE .................. 23-51
ATTACHED - REMOVAL, EXTERIOR NAME PLATES - TAPE ...................... 23-51
AUDIO/VIDEO - DESCRIPTION ...........8A-1
AUDIO/VIDEO, DIAGNOSIS AND TESTING . . 8A-2
AUTO SHUT DOWN RELAY - DESCRIPTION ......................... 8I-3
AUTO SHUT DOWN RELAY - OPERATION . . . 8I-3
AUTOMATIC ADJUSTER - DIAGNOSIS AND TESTING, DRUM BRAKE ............5-14
AUTOMATIC ADJUSTER TENSION RELEASE - STANDARD PROCEDURE,
PARKING BRAKE ...................... 5-63
AUTOMATIC ADJUSTER TENSION RESET - STANDARD PROCEDURE, PARKING
BRAKE .............................. 5-64
AUTOMATIC DAY / NIGHT MIRROR - DESCRIPTION ....................... 8N-28
AUTOMATIC DAY / NIGHT MIRROR - OPERATION ......................... 8N-28
AUTOMATIC DAY / NIGHT MIRROR, DIAGNOSIS AND TESTING .............8N-28
AUTOMATIC TEMPERATURE CONTROL, DESCRIPTION ........................ 24-3
AUTOMATIC TEMPERATURE CONTROL, OPERATION .......................... 24-5AUTOMATIC TEMPERATURE CONTROL
SYSTEM, OPERATION ................24-114
AUTOMATIC TRANSAXLE - DESCRIPTION, 40TE ................... 21-2
AUTOMATIC TRANSAXLE - DESCRIPTION, 41TE .................21-147
AUTOMATIC TRANSAXLE - OPERATION, 40TE ............................... 21-4
AUTOMATIC TRANSAXLE - OPERATION, 41TE ............................. 21-149
AUTOMATIC TRANSAXLE, SPECIAL TOOLS - 41TE ...................... 21-213
AUTOMATIC/MANUAL TRANSAXLE FLUID - DESCRIPTION ........................0-4
AWD - INSTALLATION ..................2-45
AWD - INSTALLATION, REAR WHEEL SPEED SENSOR ....................... 5-92
AWD - INSTALLATION, SPRING ..........2-39
AWD - REMOVAL ..................... 2-44
AWD - REMOVAL, REAR WHEEL SPEED SENSOR ............................ 5-92
AWD - REMOVAL, SPRING ..............2-38
AWD, HEAVY DUTY, CARGO - INSTALLATION ........................ 2-36
AWD, HEAVY DUTY, CARGO - REMOVAL . . . 2-36
AWD POWER TRANSFER UNIT FLUID - DESCRIPTION .........................0-6
AWD REAR DRIVELINE MODULE FLUIDS - DESCRIPTION ........................0-6
B OR C-PILLAR - INSTALLATION, SEAT BELT HEIGHT ADJUSTER ..............8O-38
B OR C-PILLAR - REMOVAL, SEAT BELT HEIGHT ADJUSTER ................... 8O-38
BACK - INSTALLATION, BENCH SEAT ....23-147
BACK - INSTALLATION, FRONT SEAT ....23-111
BACK - QUAD BUCKET - INSTALLATION, BUCKET SEAT ...................... 23-141
BACK - QUAD BUCKET - REMOVAL, BUCKET SEAT ...................... 23-140
BACK - REMOVAL, BENCH SEAT ........23-147
BACK - REMOVAL, FRONT SEAT ........23-111
BACK ASSIST STRAP - INSTALLATION, FRONT SEAT ....................... 23-112
BACK ASSIST STRAP - REMOVAL, FRONT SEAT ....................... 23-112
BACK COVER - INSTALLATION, BENCH SEAT ............................. 23-148
BACK COVER - INSTALLATION, FRONT SEAT ............................. 23-116
BACK COVER - REMOVAL, BENCH SEAT . . 23-148
BACK COVER - REMOVAL, FRONT SEAT . . 23-113
BACK COVER/FOAM - SECOND ROW - FOLD-IN-FLOOR - INSTALLATION, SEAT . . 23-133
BACK COVER/FOAM - SECOND ROW - FOLD-IN-FLOOR - REMOVAL, SEAT ......23-133
BACK COVER/FOAM - THIRD ROW - FOLD-IN-FLOOR - INSTALLATION, SEAT . . 23-156
BACK COVER/FOAM - THIRD ROW - FOLD-IN-FLOOR - REMOVAL, SEAT ......23-155
BACK FRAME - SECOND ROW - FOLD-IN-FLOOR - INSTALLATION, SEAT . . 23-134
BACK FRAME - SECOND ROW - FOLD-IN-FLOOR - REMOVAL, SEAT ......23-134
BACK FRAME - THIRD ROW - FOLD-IN-FLOOR - INSTALLATION, SEAT . . 23-157
BACK FRAME - THIRD ROW - FOLD-IN-FLOOR - REMOVAL, SEAT ......23-156
BACK HINGE - REMOVAL, BENCH SEAT . . 23-146
BACK HINGE COVERS - QUAD BUCKET, 50/50 SPLIT, BENCH - INSTALLATION,
SEAT ............................. 23-146
BACK HINGE COVERS - QUAD BUCKET, 50/50 SPLIT, BENCH - REMOVAL, SEAT . . 23-146
BACK PANEL - INSTALLATION, BENCH SEAT ............................. 23-144
BACK PANEL - INSTALLATION, FRONT SEAT ............................. 23-113
BACK PANEL - REMOVAL, BENCH SEAT . . 23-143
BACK PANEL - REMOVAL, FRONT SEAT . . 23-112
BACK PANEL - SECOND ROW -FOLD-IN-FLOOR - INSTALLATION,
SEAT ............................. 23-134
BACK PANEL - SECOND ROW -FOLD-IN-FLOOR - REMOVAL, SEAT .....23-134
BACK PANEL - THIRD ROW -FOLD-IN- FLOOR - INSTALLATION, SEAT .........23-158
BACK PANEL - THIRD ROW -FOLD-IN- FLOOR - REMOVAL, SEAT .............23-158
2 INDEXRS
Description Group-Page Description Group-Page Description Group-Page
Page 2305 of 2339
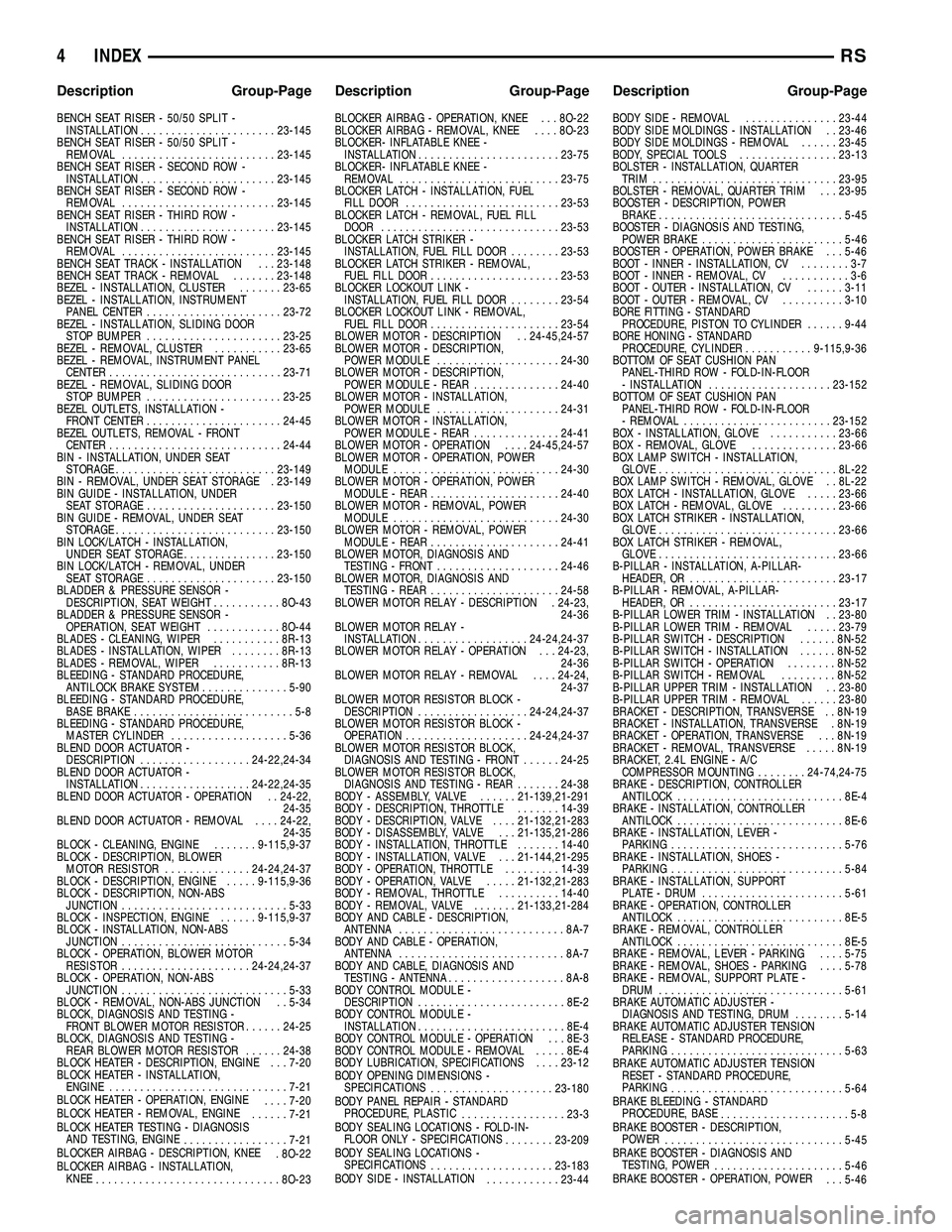
BENCH SEAT RISER - 50/50 SPLIT -INSTALLATION ...................... 23-145
BENCH SEAT RISER - 50/50 SPLIT - REMOVAL ......................... 23-145
BENCH SEAT RISER - SECOND ROW - INSTALLATION ...................... 23-145
BENCH SEAT RISER - SECOND ROW - REMOVAL ......................... 23-145
BENCH SEAT RISER - THIRD ROW - INSTALLATION ...................... 23-145
BENCH SEAT RISER - THIRD ROW - REMOVAL ......................... 23-145
BENCH SEAT TRACK - INSTALLATION . . . 23-148
BENCH SEAT TRACK - REMOVAL .......23-148
BEZEL - INSTALLATION, CLUSTER .......23-65
BEZEL - INSTALLATION, INSTRUMENT PANEL CENTER ...................... 23-72
BEZEL - INSTALLATION, SLIDING DOOR STOP BUMPER ...................... 23-25
BEZEL - REMOVAL, CLUSTER ...........23-65
BEZEL - REMOVAL, INSTRUMENT PANEL CENTER ............................ 23-71
BEZEL - REMOVAL, SLIDING DOOR STOP BUMPER ...................... 23-25
BEZEL OUTLETS, INSTALLATION - FRONT CENTER ...................... 24-45
BEZEL OUTLETS, REMOVAL - FRONT CENTER ............................ 24-44
BIN - INSTALLATION, UNDER SEAT STORAGE .......................... 23-149
BIN - REMOVAL, UNDER SEAT STORAGE . 23-149
BIN GUIDE - INSTALLATION, UNDER SEAT STORAGE ..................... 23-150
BIN GUIDE - REMOVAL, UNDER SEAT STORAGE .......................... 23-150
BIN LOCK/LATCH - INSTALLATION, UNDER SEAT STORAGE ...............23-150
BIN LOCK/LATCH - REMOVAL, UNDER SEAT STORAGE ..................... 23-150
BLADDER & PRESSURE SENSOR - DESCRIPTION, SEAT WEIGHT ...........8O-43
BLADDER & PRESSURE SENSOR - OPERATION, SEAT WEIGHT ............8O-44
BLADES - CLEANING, WIPER ...........8R-13
BLADES - INSTALLATION, WIPER ........8R-13
BLADES - REMOVAL, WIPER ...........8R-13
BLEEDING - STANDARD PROCEDURE, ANTILOCK BRAKE SYSTEM ..............5-90
BLEEDING - STANDARD PROCEDURE, BASE BRAKE ..........................5-8
BLEEDING - STANDARD PROCEDURE, MASTER CYLINDER ................... 5-36
BLEND DOOR ACTUATOR - DESCRIPTION .................. 24-22,24-34
BLEND DOOR ACTUATOR - INSTALLATION .................. 24-22,24-35
BLEND DOOR ACTUATOR - OPERATION . . 24-22, 24-35
BLEND DOOR ACTUATOR - REMOVAL ....24-22,
24-35
BLOCK - CLEANING, ENGINE .......9-115,9-37
BLOCK - DESCRIPTION, BLOWER MOTOR RESISTOR ..............24-24,24-37
BLOCK - DESCRIPTION, ENGINE .....9-115,9-36
BLOCK - DESCRIPTION, NON-ABS JUNCTION ........................... 5-33
BLOCK - INSPECTION, ENGINE ......9-115,9-37
BLOCK - INSTALLATION, NON-ABS JUNCTION ........................... 5-34
BLOCK - OPERATION, BLOWER MOTOR RESISTOR ..................... 24-24,24-37
BLOCK - OPERATION, NON-ABS JUNCTION ........................... 5-33
BLOCK - REMOVAL, NON-ABS JUNCTION . . 5-34
BLOCK, DIAGNOSIS AND TESTING - FRONT BLOWER MOTOR RESISTOR ......24-25
BLOCK, DIAGNOSIS AND TESTING - REAR BLOWER MOTOR RESISTOR ......24-38
BLOCK HEATER - DESCRIPTION, ENGINE . . . 7-20
BLOCK HEATER - INSTALLATION, ENGINE ............................. 7-21
BLOCK HEATER - OPERATION, ENGINE ....7-20
BLOCK HEATER - REMOVAL, ENGINE ......7-21
BLOCK HEATER TESTING - DIAGNOSIS AND TESTING, ENGINE .................7-21
BLOCKER AIRBAG - DESCRIPTION, KNEE . 8O-22
BLOCKER AIRBAG - INSTALLATION, KNEE .............................. 8O-23BLOCKER AIRBAG - OPERATION, KNEE . . . 8O-22
BLOCKER AIRBAG - REMOVAL, KNEE
....8O-23
BLOCKER- INFLATABLE KNEE - INSTALLATION ....................... 23-75
BLOCKER- INFLATABLE KNEE - REMOVAL .......................... 23-75
BLOCKER LATCH - INSTALLATION, FUEL FILL DOOR ......................... 23-53
BLOCKER LATCH - REMOVAL, FUEL FILL DOOR ............................. 23-53
BLOCKER LATCH STRIKER - INSTALLATION, FUEL FILL DOOR ........23-53
BLOCKER LATCH STRIKER - REMOVAL, FUEL FILL DOOR ..................... 23-53
BLOCKER LOCKOUT LINK - INSTALLATION, FUEL FILL DOOR ........23-54
BLOCKER LOCKOUT LINK - REMOVAL, FUEL FILL DOOR ..................... 23-54
BLOWER MOTOR - DESCRIPTION . . 24-45,24-57
BLOWER MOTOR - DESCRIPTION, POWER MODULE .................... 24-30
BLOWER MOTOR - DESCRIPTION, POWER MODULE - REAR ..............24-40
BLOWER MOTOR - INSTALLATION, POWER MODULE .................... 24-31
BLOWER MOTOR - INSTALLATION, POWER MODULE - REAR ..............24-41
BLOWER MOTOR - OPERATION ....24-45,24-57
BLOWER MOTOR - OPERATION, POWER MODULE ........................... 24-30
BLOWER MOTOR - OPERATION, POWER MODULE - REAR ..................... 24-40
BLOWER MOTOR - REMOVAL, POWER MODULE ........................... 24-30
BLOWER MOTOR - REMOVAL, POWER MODULE - REAR ..................... 24-41
BLOWER MOTOR, DIAGNOSIS AND TESTING - FRONT .................... 24-46
BLOWER MOTOR, DIAGNOSIS AND TESTING - REAR ..................... 24-58
BLOWER MOTOR RELAY - DESCRIPTION . 24-23, 24-36
BLOWER MOTOR RELAY - INSTALLATION .................. 24-24,24-37
BLOWER MOTOR RELAY - OPERATION . . . 24-23, 24-36
BLOWER MOTOR RELAY - REMOVAL ....24-24,
24-37
BLOWER MOTOR RESISTOR BLOCK - DESCRIPTION .................. 24-24,24-37
BLOWER MOTOR RESISTOR BLOCK - OPERATION .................... 24-24,24-37
BLOWER MOTOR RESISTOR BLOCK, DIAGNOSIS AND TESTING - FRONT ......24-25
BLOWER MOTOR RESISTOR BLOCK, DIAGNOSIS AND TESTING - REAR .......24-38
BODY - ASSEMBLY, VALVE ......21-139,21-291
BODY - DESCRIPTION, THROTTLE .......14-39
BODY - DESCRIPTION, VALVE ....21-132,21-283
BODY - DISASSEMBLY, VALVE . . . 21-135,21-286
BODY - INSTALLATION, THROTTLE .......14-40
BODY - INSTALLATION, VALVE . . . 21-144,21-295
BODY - OPERATION, THROTTLE .........14-39
BODY - OPERATION, VALVE .....21-132,21-283
BODY - REMOVAL, THROTTLE ..........14-40
BODY - REMOVAL, VALVE .......21-133,21-284
BODY AND CABLE - DESCRIPTION, ANTENNA ........................... 8A-7
BODY AND CABLE - OPERATION, ANTENNA ........................... 8A-7
BODY AND CABLE, DIAGNOSIS AND TESTING - ANTENNA ................... 8A-8
BODY CONTROL MODULE - DESCRIPTION ........................ 8E-2
BODY CONTROL MODULE - INSTALLATION ........................ 8E-4
BODY CONTROL MODULE - OPERATION . . . 8E-3
BODY CONTROL MODULE - REMOVAL .....8E-4
BODY LUBRICATION, SPECIFICATIONS ....23-12
BODY OPENING DIMENSIONS - SPECIFICATIONS .................... 23-180
BODY PANEL REPAIR - STANDARD PROCEDURE, PLASTIC .................23-3
BODY SEALING LOCATIONS - FOLD-IN- FLOOR ONLY - SPECIFICATIONS ........23-209
BODY SEALING LOCATIONS - SPECIFICATIONS .................... 23-183
BODY SIDE - INSTALLATION ............23-44BODY SIDE - REMOVAL
...............23-44
BODY SIDE MOLDINGS - INSTALLATION . . 23-46
BODY SIDE MOLDINGS - REMOVAL ......23-45
BODY, SPECIAL TOOLS ................23-13
BOLSTER - INSTALLATION, QUARTER TRIM .............................. 23-95
BOLSTER - REMOVAL, QUARTER TRIM . . . 23-95
BOOSTER - DESCRIPTION, POWER BRAKE .............................. 5-45
BOOSTER - DIAGNOSIS AND TESTING, POWER BRAKE ....................... 5-46
BOOSTER - OPERATION, POWER BRAKE . . . 5-46
BOOT - INNER - INSTALLATION, CV ........3-7
BOOT - INNER - REMOVAL, CV ...........3-6
BOOT - OUTER - INSTALLATION, CV ......3-11
BOOT - OUTER - REMOVAL, CV ..........3-10
BORE FITTING - STANDARD PROCEDURE, PISTON TO CYLINDER ......9-44
BORE HONING - STANDARD PROCEDURE, CYLINDER ...........9-115,9-36
BOTTOM OF SEAT CUSHION PAN PANEL-THIRD ROW - FOLD-IN-FLOOR
- INSTALLATION .................... 23-152
BOTTOM OF SEAT CUSHION PAN PANEL-THIRD ROW - FOLD-IN-FLOOR
- REMOVAL ........................ 23-152
BOX - INSTALLATION, GLOVE ...........23-66
BOX - REMOVAL, GLOVE ..............23-66
BOX LAMP SWITCH - INSTALLATION, GLOVE ............................. 8L-22
BOX LAMP SWITCH - REMOVAL, GLOVE . . 8L-22
BOX LATCH - INSTALLATION, GLOVE .....23-66
BOX LATCH - REMOVAL, GLOVE .........23-66
BOX LATCH STRIKER - INSTALLATION, GLOVE ............................. 23-66
BOX LATCH STRIKER - REMOVAL, GLOVE ............................. 23-66
B-PILLAR - INSTALLATION, A-PILLAR- HEADER, OR ........................ 23-17
B-PILLAR - REMOVAL, A-PILLAR- HEADER, OR ........................ 23-17
B-PILLAR LOWER TRIM - INSTALLATION . . 23-80
B-PILLAR LOWER TRIM - REMOVAL .....23-79
B-PILLAR SWITCH - DESCRIPTION ......8N-52
B-PILLAR SWITCH - INSTALLATION ......8N-52
B-PILLAR SWITCH - OPERATION ........8N-52
B-PILLAR SWITCH - REMOVAL .........8N-52
B-PILLAR UPPER TRIM - INSTALLATION . . 23-80
B-PILLAR UPPER TRIM - REMOVAL ......23-80
BRACKET - DESCRIPTION, TRANSVERSE . . 8N-19
BRACKET - INSTALLATION, TRANSVERSE . 8N-19
BRACKET - OPERATION, TRANSVERSE . . . 8N-19
BRACKET - REMOVAL, TRANSVERSE .....8N-19
BRACKET, 2.4L ENGINE - A/C COMPRESSOR MOUNTING ........24-74,24-75
BRAKE - DESCRIPTION, CONTROLLER ANTILOCK ........................... 8E-4
BRAKE - INSTALLATION, CONTROLLER ANTILOCK ........................... 8E-6
BRAKE - INSTALLATION, LEVER - PARKING ............................ 5-76
BRAKE - INSTALLATION, SHOES - PARKING ............................ 5-84
BRAKE - INSTALLATION, SUPPORT PLATE - DRUM ....................... 5-61
BRAKE - OPERATION, CONTROLLER ANTILOCK ........................... 8E-5
BRAKE - REMOVAL, CONTROLLER ANTILOCK ........................... 8E-5
BRAKE - REMOVAL, LEVER - PARKING ....5-75
BRAKE - REMOVAL, SHOES - PARKING ....5-78
BRAKE - REMOVAL, SUPPORT PLATE - DRUM .............................. 5-61
BRAKE AUTOMATIC ADJUSTER - DIAGNOSIS AND TESTING, DRUM ........5-14
BRAKE AUTOMATIC ADJUSTER TENSION RELEASE - STANDARD PROCEDURE,
PARKING ............................ 5-63
BRAKE AUTOMATIC ADJUSTER TENSION RESET - STANDARD PROCEDURE,
PARKING ............................ 5-64
BRAKE BLEEDING - STANDARD PROCEDURE, BASE .....................5-8
BRAKE BOOSTER - DESCRIPTION, POWER ............................. 5-45
BRAKE BOOSTER - DIAGNOSIS AND TESTING, POWER ..................... 5-46
BRAKE BOOSTER - OPERATION, POWER . . . 5-46
4 INDEXRS
Description Group-Page Description Group-Page Description Group-Page
Page 2310 of 2339
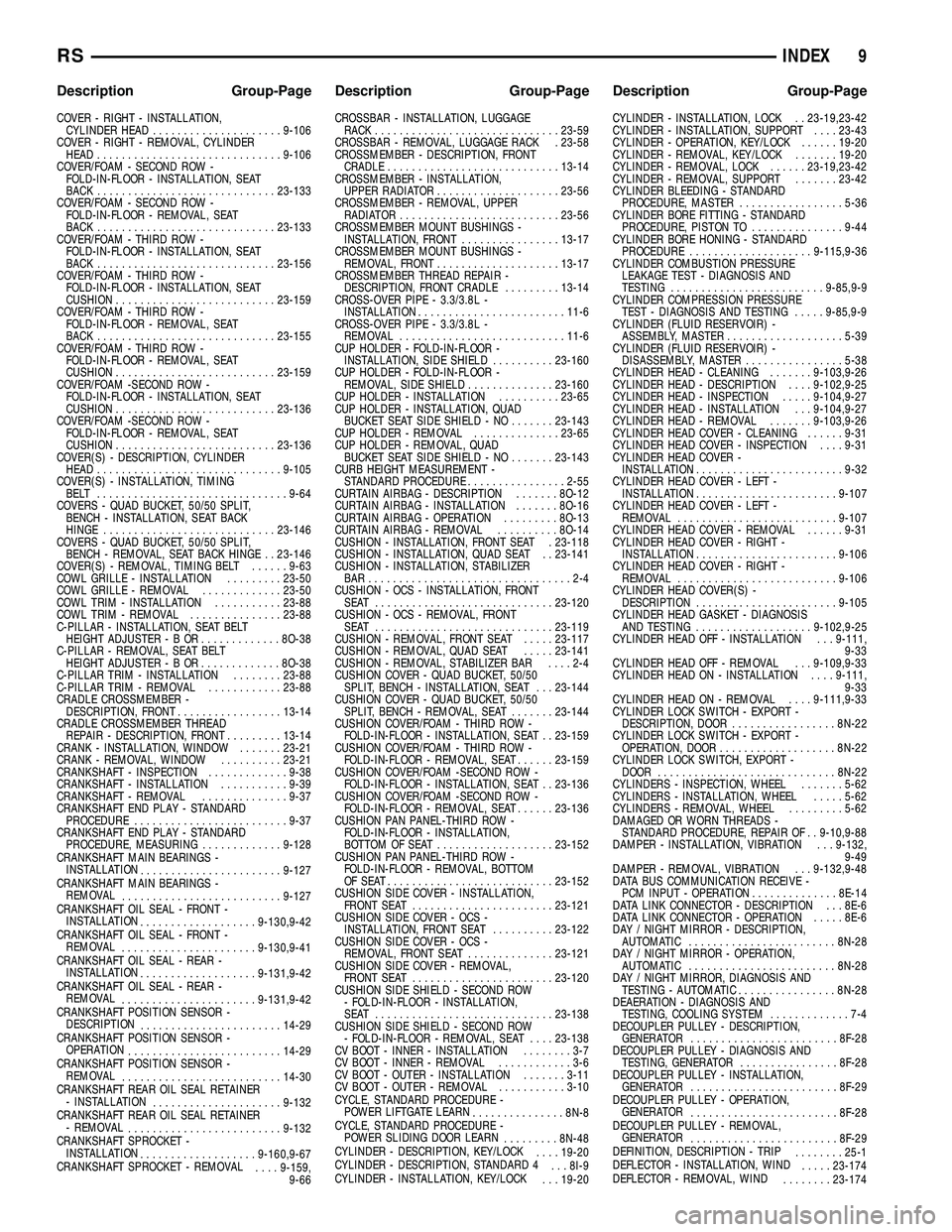
COVER - RIGHT - INSTALLATION,CYLINDER HEAD ..................... 9-106
COVER - RIGHT - REMOVAL, CYLINDER HEAD .............................. 9-106
COVER/FOAM - SECOND ROW - FOLD-IN-FLOOR - INSTALLATION, SEAT
BACK ............................. 23-133
COVER/FOAM - SECOND ROW - FOLD-IN-FLOOR - REMOVAL, SEAT
BACK ............................. 23-133
COVER/FOAM - THIRD ROW - FOLD-IN-FLOOR - INSTALLATION, SEAT
BACK ............................. 23-156
COVER/FOAM - THIRD ROW - FOLD-IN-FLOOR - INSTALLATION, SEAT
CUSHION .......................... 23-159
COVER/FOAM - THIRD ROW - FOLD-IN-FLOOR - REMOVAL, SEAT
BACK ............................. 23-155
COVER/FOAM - THIRD ROW - FOLD-IN-FLOOR - REMOVAL, SEAT
CUSHION .......................... 23-159
COVER/FOAM -SECOND ROW - FOLD-IN-FLOOR - INSTALLATION, SEAT
CUSHION .......................... 23-136
COVER/FOAM -SECOND ROW - FOLD-IN-FLOOR - REMOVAL, SEAT
CUSHION .......................... 23-136
COVER(S) - DESCRIPTION, CYLINDER HEAD .............................. 9-105
COVER(S) - INSTALLATION, TIMING BELT ............................... 9-64
COVERS - QUAD BUCKET, 50/50 SPLIT, BENCH - INSTALLATION, SEAT BACK
HINGE ............................ 23-146
COVERS - QUAD BUCKET, 50/50 SPLIT, BENCH - REMOVAL, SEAT BACK HINGE. . . 23-146
COVER(S) - REMOVAL, TIMING BELT ......9-63
COWL GRILLE - INSTALLATION .........23-50
COWL GRILLE - REMOVAL .............23-50
COWL TRIM - INSTALLATION ...........23-88
COWL TRIM - REMOVAL ...............23-88
C-PILLAR - INSTALLATION, SEAT BELT HEIGHT ADJUSTE R-BOR............. 8O-38
C-PILLAR - REMOVAL, SEAT BELT HEIGHT ADJUSTE R-BOR............. 8O-38
C-PILLAR TRIM - INSTALLATION ........23-88
C-PILLAR TRIM - REMOVAL ............23-88
CRADLE CROSSMEMBER - DESCRIPTION, FRONT .................13-14
CRADLE CROSSMEMBER THREAD REPAIR - DESCRIPTION, FRONT .........13-14
CRANK - INSTALLATION, WINDOW .......23-21
CRANK - REMOVAL, WINDOW ..........23-21
CRANKSHAFT - INSPECTION .............9-38
CRANKSHAFT - INSTALLATION ...........9-39
CRANKSHAFT - REMOVAL ..............9-37
CRANKSHAFT END PLAY - STANDARD PROCEDURE ......................... 9-37
CRANKSHAFT END PLAY - STANDARD PROCEDURE, MEASURING .............9-128
CRANKSHAFT MAIN BEARINGS - INSTALLATION ....................... 9-127
CRANKSHAFT MAIN BEARINGS - REMOVAL .......................... 9-127
CRANKSHAFT OIL SEAL - FRONT - INSTALLATION ................... 9-130,9-42
CRANKSHAFT OIL SEAL - FRONT - REMOVAL ...................... 9-130,9-41
CRANKSHAFT OIL SEAL - REAR - INSTALLATION ................... 9-131,9-42
CRANKSHAFT OIL SEAL - REAR - REMOVAL ...................... 9-131,9-42
CRANKSHAFT POSITION SENSOR - DESCRIPTION ....................... 14-29
CRANKSHAFT POSITION SENSOR - OPERATION ......................... 14-29
CRANKSHAFT POSITION SENSOR - REMOVAL .......................... 14-30
CRANKSHAFT REAR OIL SEAL RETAINER - INSTALLATION ..................... 9-132
CRANKSHAFT REAR OIL SEAL RETAINER - REMOVAL ......................... 9-132
CRANKSHAFT SPROCKET - INSTALLATION ................... 9-160,9-67
CRANKSHAFT SPROCKET - REMOVAL ....9-159,
9-66 CROSSBAR - INSTALLATION, LUGGAGE
RACK .............................. 23-59
CROSSBAR - REMOVAL, LUGGAGE RACK . 23-58
CROSSMEMBER - DESCRIPTION, FRONT CRADLE ............................ 13-14
CROSSMEMBER - INSTALLATION, UPPER RADIATOR .................... 23-56
CROSSMEMBER - REMOVAL, UPPER RADIATOR .......................... 23-56
CROSSMEMBER MOUNT BUSHINGS - INSTALLATION, FRONT ................13-17
CROSSMEMBER MOUNT BUSHINGS - REMOVAL, FRONT .................... 13-17
CROSSMEMBER THREAD REPAIR - DESCRIPTION, FRONT CRADLE .........13-14
CROSS-OVER PIPE - 3.3/3.8L - INSTALLATION ........................ 11-6
CROSS-OVER PIPE - 3.3/3.8L - REMOVAL ........................... 11-6
CUP HOLDER - FOLD-IN-FLOOR - INSTALLATION, SIDE SHIELD ..........23-160
CUP HOLDER - FOLD-IN-FLOOR - REMOVAL, SIDE SHIELD ..............23-160
CUP HOLDER - INSTALLATION ..........23-65
CUP HOLDER - INSTALLATION, QUAD BUCKET SEAT SIDE SHIELD - NO .......23-143
CUP HOLDER - REMOVAL ..............23-65
CUP HOLDER - REMOVAL, QUAD BUCKET SEAT SIDE SHIELD - NO .......23-143
CURB HEIGHT MEASUREMENT - STANDARD PROCEDURE ................2-55
CURTAIN AIRBAG - DESCRIPTION .......8O-12
CURTAIN AIRBAG - INSTALLATION .......8O-16
CURTAIN AIRBAG - OPERATION .........8O-13
CURTAIN AIRBAG - REMOVAL ..........8O-14
CUSHION - INSTALLATION, FRONT SEAT . 23-118
CUSHION - INSTALLATION, QUAD SEAT . . 23-141
CUSHION - INSTALLATION, STABILIZER BAR.................................2-4
CUSHION - OCS - INSTALLATION, FRONT SEAT ............................. 23-120
CUSHION - OCS - REMOVAL, FRONT SEAT ............................. 23-119
CUSHION - REMOVAL, FRONT SEAT .....23-117
CUSHION - REMOVAL, QUAD SEAT .....23-141
CUSHION - REMOVAL, STABILIZER BAR ....2-4
CUSHION COVER - QUAD BUCKET, 50/50 SPLIT, BENCH - INSTALLATION, SEAT . . . 23-144
CUSHION COVER - QUAD BUCKET, 50/50 SPLIT, BENCH - REMOVAL, SEAT .......23-144
CUSHION COVER/FOAM - THIRD ROW - FOLD-IN-FLOOR - INSTALLATION, SEAT . . 23-159
CUSHION COVER/FOAM - THIRD ROW - FOLD-IN-FLOOR - REMOVAL, SEAT ......23-159
CUSHION COVER/FOAM -SECOND ROW - FOLD-IN-FLOOR - INSTALLATION, SEAT . . 23-136
CUSHION COVER/FOAM -SECOND ROW - FOLD-IN-FLOOR - REMOVAL, SEAT ......23-136
CUSHION PAN PANEL-THIRD ROW - FOLD-IN-FLOOR - INSTALLATION,
BOTTOM OF SEAT ................... 23-152
CUSHION PAN PANEL-THIRD ROW - FOLD-IN-FLOOR - REMOVAL, BOTTOM
OF SEAT........................... 23-152
CUSHION SIDE COVER - INSTALLATION, FRONT SEAT ....................... 23-121
CUSHION SIDE COVER - OCS - INSTALLATION, FRONT SEAT ..........23-122
CUSHION SIDE COVER - OCS - REMOVAL, FRONT SEAT ..............23-121
CUSHION SIDE COVER - REMOVAL, FRONT SEAT ....................... 23-120
CUSHION SIDE SHIELD - SECOND ROW - FOLD-IN-FLOOR - INSTALLATION,
SEAT ............................. 23-138
CUSHION SIDE SHIELD - SECOND ROW - FOLD-IN-FLOOR - REMOVAL, SEAT ....23-138
CV BOOT - INNER - INSTALLATION ........3-7
CV BOOT - INNER - REMOVAL ............3-6
CV BOOT - OUTER - INSTALLATION .......3-11
CV BOOT - OUTER - REMOVAL ...........3-10
CYCLE, STANDARD PROCEDURE - POWER LIFTGATE LEARN ...............8N-8
CYCLE, STANDARD PROCEDURE - POWER SLIDING DOOR LEARN .........8N-48
CYLINDER - DESCRIPTION, KEY/LOCK ....19-20
CYLINDER - DESCRIPTION, STANDARD 4 . . . 8I-9
CYLINDER - INSTALLATION, KEY/LOCK . . . 19-20CYLINDER - INSTALLATION, LOCK . . 23-19,23-42
CYLINDER - INSTALLATION, SUPPORT
....23-43
CYLINDER - OPERATION, KEY/LOCK ......19-20
CYLINDER - REMOVAL, KEY/LOCK .......19-20
CYLINDER - REMOVAL, LOCK ......23-19,23-42
CYLINDER - REMOVAL, SUPPORT .......23-42
CYLINDER BLEEDING - STANDARD PROCEDURE, MASTER .................5-36
CYLINDER BORE FITTING - STANDARD PROCEDURE, PISTON TO ...............9-44
CYLINDER BORE HONING - STANDARD PROCEDURE .................... 9-115,9-36
CYLINDER COMBUSTION PRESSURE LEAKAGE TEST - DIAGNOSIS AND
TESTING ......................... 9-85,9-9
CYLINDER COMPRESSION PRESSURE TEST - DIAGNOSIS AND TESTING .....9-85,9-9
CYLINDER (FLUID RESERVOIR) - ASSEMBLY, MASTER ................... 5-39
CYLINDER (FLUID RESERVOIR) - DISASSEMBLY, MASTER ................5-38
CYLINDER HEAD - CLEANING .......9-103,9-26
CYLINDER HEAD - DESCRIPTION ....9-102,9-25
CYLINDER HEAD - INSPECTION .....9-104,9-27
CYLINDER HEAD - INSTALLATION . . . 9-104,9-27
CYLINDER HEAD - REMOVAL .......9-103,9-26
CYLINDER HEAD COVER - CLEANING ......9-31
CYLINDER HEAD COVER - INSPECTION ....9-31
CYLINDER HEAD COVER - INSTALLATION ......................... 9-32
CYLINDER HEAD COVER - LEFT - INSTALLATION ....................... 9-107
CYLINDER HEAD COVER - LEFT - REMOVAL .......................... 9-107
CYLINDER HEAD COVER - REMOVAL ......9-31
CYLINDER HEAD COVER - RIGHT - INSTALLATION ....................... 9-106
CYLINDER HEAD COVER - RIGHT - REMOVAL .......................... 9-106
CYLINDER HEAD COVER(S) - DESCRIPTION ....................... 9-105
CYLINDER HEAD GASKET - DIAGNOSIS AND TESTING ................... 9-102,9-25
CYLINDER HEAD OFF - INSTALLATION . . . 9-111, 9-33
CYLINDER HEAD OFF - REMOVAL . . . 9-109,9-33
CYLINDER HEAD ON - INSTALLATION ....9-111,
9-33
CYLINDER HEAD ON - REMOVAL ....9-111,9-33
CYLINDER LOCK SWITCH - EXPORT - DESCRIPTION, DOOR .................8N-22
CYLINDER LOCK SWITCH - EXPORT - OPERATION, DOOR ................... 8N-22
CYLINDER LOCK SWITCH, EXPORT - DOOR ............................. 8N-22
CYLINDERS - INSPECTION, WHEEL .......5-62
CYLINDERS - INSTALLATION, WHEEL .....5-62
CYLINDERS - REMOVAL, WHEEL .........5-62
DAMAGED OR WORN THREADS - STANDARD PROCEDURE, REPAIR OF . . 9-10,9-88
DAMPER - INSTALLATION, VIBRATION . . . 9-132, 9-49
DAMPER - REMOVAL, VIBRATION . . . 9-132,9-48
DATA BUS COMMUNICATION RECEIVE - PCM INPUT - OPERATION ..............8E-14
DATA LINK CONNECTOR - DESCRIPTION . . . 8E-6
DATA LINK CONNECTOR - OPERATION .....8E-6
DAY / NIGHT MIRROR - DESCRIPTION, AUTOMATIC ........................ 8N-28
DAY / NIGHT MIRROR - OPERATION, AUTOMATIC ........................ 8N-28
DAY / NIGHT MIRROR, DIAGNOSIS AND TESTING - AUTOMATIC ................8N-28
DEAERATION - DIAGNOSIS AND TESTING, COOLING SYSTEM .............7-4
DECOUPLER PULLEY - DESCRIPTION, GENERATOR ........................ 8F-28
DECOUPLER PULLEY - DIAGNOSIS AND TESTING, GENERATOR ................8F-28
DECOUPLER PULLEY - INSTALLATION, GENERATOR ........................ 8F-29
DECOUPLER PULLEY - OPERATION, GENERATOR ........................ 8F-28
DECOUPLER PULLEY - REMOVAL, GENERATOR ........................ 8F-29
DEFINITION, DESCRIPTION - TRIP ........25-1
DEFLECTOR - INSTALLATION, WIND .....23-174
DEFLECTOR - REMOVAL, WIND ........23-174
RS INDEX9
Description Group-Page Description Group-Page Description Group-Page
Page 2321 of 2339
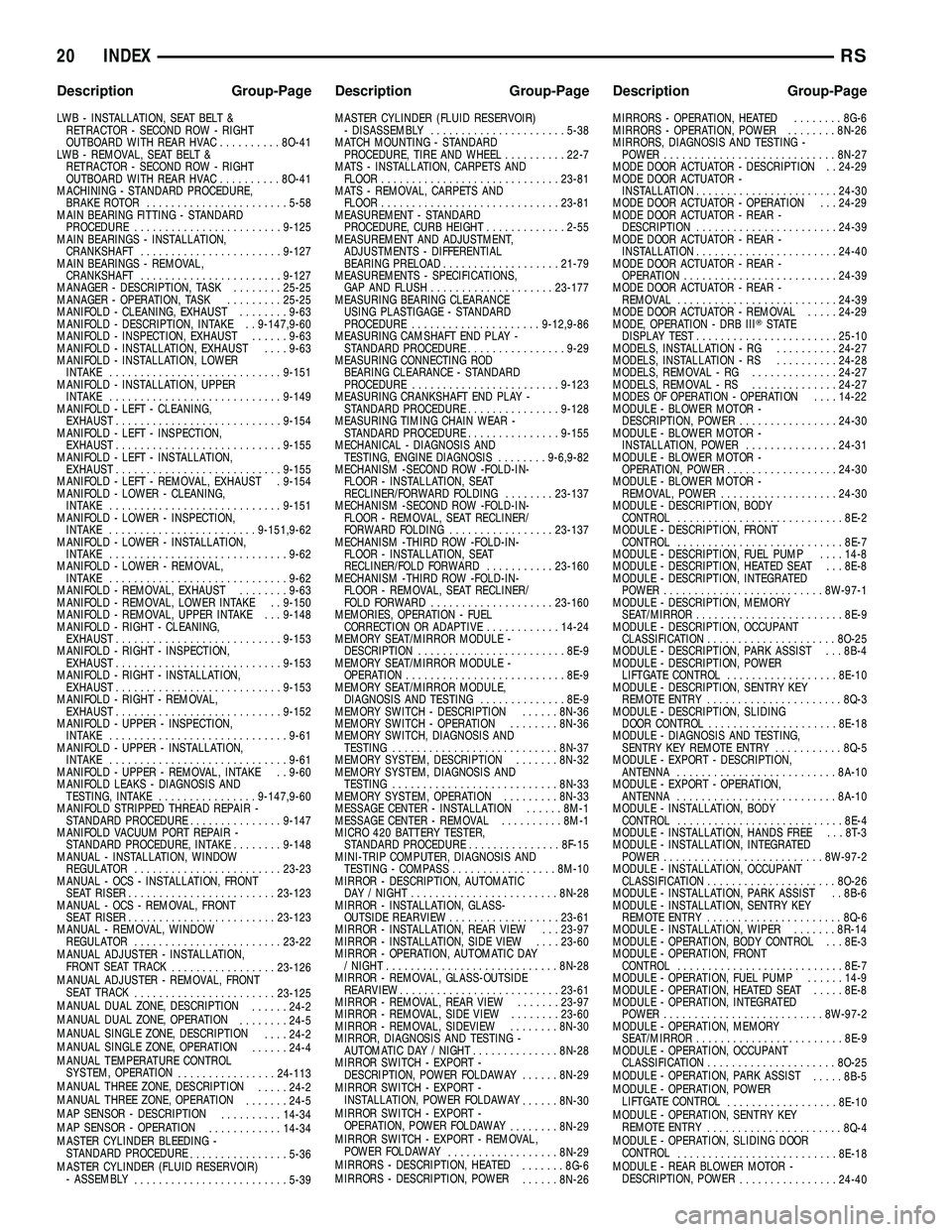
LWB - INSTALLATION, SEAT BELT &RETRACTOR - SECOND ROW - RIGHT
OUTBOARD WITH REAR HVAC ..........8O-41
LWB - REMOVAL, SEAT BELT & RETRACTOR - SECOND ROW - RIGHT
OUTBOARD WITH REAR HVAC ..........8O-41
MACHINING - STANDARD PROCEDURE, BRAKE ROTOR ....................... 5-58
MAIN BEARING FITTING - STANDARD PROCEDURE ........................ 9-125
MAIN BEARINGS - INSTALLATION, CRANKSHAFT ....................... 9-127
MAIN BEARINGS - REMOVAL, CRANKSHAFT ....................... 9-127
MANAGER - DESCRIPTION, TASK ........25-25
MANAGER - OPERATION, TASK .........25-25
MANIFOLD - CLEANING, EXHAUST ........9-63
MANIFOLD - DESCRIPTION, INTAKE . . 9-147,9-60
MANIFOLD - INSPECTION, EXHAUST ......9-63
MANIFOLD - INSTALLATION, EXHAUST ....9-63
MANIFOLD - INSTALLATION, LOWER INTAKE ............................ 9-151
MANIFOLD - INSTALLATION, UPPER INTAKE ............................ 9-149
MANIFOLD - LEFT - CLEANING, EXHAUST ........................... 9-154
MANIFOLD - LEFT - INSPECTION, EXHAUST ........................... 9-155
MANIFOLD - LEFT - INSTALLATION, EXHAUST ........................... 9-155
MANIFOLD - LEFT - REMOVAL, EXHAUST . 9-154
MANIFOLD - LOWER - CLEANING, INTAKE ............................ 9-151
MANIFOLD - LOWER - INSPECTION, INTAKE ........................ 9-151,9-62
MANIFOLD - LOWER - INSTALLATION, INTAKE ............................. 9-62
MANIFOLD - LOWER - REMOVAL, INTAKE ............................. 9-62
MANIFOLD - REMOVAL, EXHAUST ........9-63
MANIFOLD - REMOVAL, LOWER INTAKE . . 9-150
MANIFOLD - REMOVAL, UPPER INTAKE . . . 9-148
MANIFOLD - RIGHT - CLEANING, EXHAUST ........................... 9-153
MANIFOLD - RIGHT - INSPECTION, EXHAUST ........................... 9-153
MANIFOLD - RIGHT - INSTALLATION, EXHAUST ........................... 9-153
MANIFOLD - RIGHT - REMOVAL, EXHAUST ........................... 9-152
MANIFOLD - UPPER - INSPECTION, INTAKE ............................. 9-61
MANIFOLD - UPPER - INSTALLATION, INTAKE ............................. 9-61
MANIFOLD - UPPER - REMOVAL, INTAKE . . 9-60
MANIFOLD LEAKS - DIAGNOSIS AND TESTING, INTAKE ................ 9-147,9-60
MANIFOLD STRIPPED THREAD REPAIR - STANDARD PROCEDURE ...............9-147
MANIFOLD VACUUM PORT REPAIR - STANDARD PROCEDURE, INTAKE ........9-148
MANUAL - INSTALLATION, WINDOW REGULATOR ........................ 23-23
MANUAL - OCS - INSTALLATION, FRONT SEAT RISER ........................ 23-123
MANUAL - OCS - REMOVAL, FRONT SEAT RISER ........................ 23-123
MANUAL - REMOVAL, WINDOW REGULATOR ........................ 23-22
MANUAL ADJUSTER - INSTALLATION, FRONT SEAT TRACK .................23-126
MANUAL ADJUSTER - REMOVAL, FRONT SEAT TRACK ....................... 23-125
MANUAL DUAL ZONE, DESCRIPTION ......24-2
MANUAL DUAL ZONE, OPERATION ........24-5
MANUAL SINGLE ZONE, DESCRIPTION ....24-2
MANUAL SINGLE ZONE, OPERATION ......24-4
MANUAL TEMPERATURE CONTROL SYSTEM, OPERATION ................24-113
MANUAL THREE ZONE, DESCRIPTION .....24-2
MANUAL THREE ZONE, OPERATION .......24-5
MAP SENSOR - DESCRIPTION ..........14-34
MAP SENSOR - OPERATION ............14-34
MASTER CYLINDER BLEEDING - STANDARD PROCEDURE ................5-36
MASTER CYLINDER (FLUID RESERVOIR) - ASSEMBLY ......................... 5-39MASTER CYLINDER (FLUID RESERVOIR)
- DISASSEMBLY ...................... 5-38
MATCH MOUNTING - STANDARD PROCEDURE, TIRE AND WHEEL ..........22-7
MATS - INSTALLATION, CARPETS AND FLOOR ............................. 23-81
MATS - REMOVAL, CARPETS AND FLOOR ............................. 23-81
MEASUREMENT - STANDARD PROCEDURE, CURB HEIGHT .............2-55
MEASUREMENT AND ADJUSTMENT, ADJUSTMENTS - DIFFERENTIAL
BEARING PRELOAD ................... 21-79
MEASUREMENTS - SPECIFICATIONS, GAP AND FLUSH .................... 23-177
MEASURING BEARING CLEARANCE USING PLASTIGAGE - STANDARD
PROCEDURE ..................... 9-12,9-86
MEASURING CAMSHAFT END PLAY - STANDARD PROCEDURE ................9-29
MEASURING CONNECTING ROD BEARING CLEARANCE - STANDARD
PROCEDURE ........................ 9-123
MEASURING CRANKSHAFT END PLAY - STANDARD PROCEDURE ...............9-128
MEASURING TIMING CHAIN WEAR - STANDARD PROCEDURE ...............9-155
MECHANICAL - DIAGNOSIS AND TESTING, ENGINE DIAGNOSIS ........9-6,9-82
MECHANISM -SECOND ROW -FOLD-IN- FLOOR - INSTALLATION, SEAT
RECLINER/FORWARD FOLDING ........23-137
MECHANISM -SECOND ROW -FOLD-IN- FLOOR - REMOVAL, SEAT RECLINER/
FORWARD FOLDING .................23-137
MECHANISM -THIRD ROW -FOLD-IN- FLOOR - INSTALLATION, SEAT
RECLINER/FOLD FORWARD ...........23-160
MECHANISM -THIRD ROW -FOLD-IN- FLOOR - REMOVAL, SEAT RECLINER/
FOLD FORWARD .................... 23-160
MEMORIES, OPERATION - FUEL CORRECTION OR ADAPTIVE ............14-24
MEMORY SEAT/MIRROR MODULE - DESCRIPTION ........................ 8E-9
MEMORY SEAT/MIRROR MODULE - OPERATION .......................... 8E-9
MEMORY SEAT/MIRROR MODULE, DIAGNOSIS AND TESTING ..............8E-9
MEMORY SWITCH - DESCRIPTION ......8N-36
MEMORY SWITCH - OPERATION ........8N-36
MEMORY SWITCH, DIAGNOSIS AND TESTING ........................... 8N-37
MEMORY SYSTEM, DESCRIPTION .......8N-32
MEMORY SYSTEM, DIAGNOSIS AND TESTING ........................... 8N-33
MEMORY SYSTEM, OPERATION .........8N-33
MESSAGE CENTER - INSTALLATION ......8M-1
MESSAGE CENTER - REMOVAL ..........8M-1
MICRO 420 BATTERY TESTER, STANDARD PROCEDURE ...............8F-15
MINI-TRIP COMPUTER, DIAGNOSIS AND TESTING - COMPASS .................8M-10
MIRROR - DESCRIPTION, AUTOMATIC DAY / NIGHT ........................ 8N-28
MIRROR - INSTALLATION, GLASS- OUTSIDE REARVIEW .................. 23-61
MIRROR - INSTALLATION, REAR VIEW . . . 23-97
MIRROR - INSTALLATION, SIDE VIEW ....23-60
MIRROR - OPERATION, AUTOMATIC DAY / NIGHT ............................ 8N-28
MIRROR - REMOVAL, GLASS-OUTSIDE REARVIEW .......................... 23-61
MIRROR - REMOVAL, REAR VIEW .......23-97
MIRROR - REMOVAL, SIDE VIEW ........23-60
MIRROR - REMOVAL, SIDEVIEW ........8N-30
MIRROR, DIAGNOSIS AND TESTING - AUTOMATIC DAY / NIGHT ..............8N-28
MIRROR SWITCH - EXPORT - DESCRIPTION, POWER FOLDAWAY ......8N-29
MIRROR SWITCH - EXPORT - INSTALLATION, POWER FOLDAWAY ......8N-30
MIRROR SWITCH - EXPORT - OPERATION, POWER FOLDAWAY ........8N-29
MIRROR SWITCH - EXPORT - REMOVAL, POWER FOLDAWAY .................. 8N-29
MIRRORS - DESCRIPTION, HEATED .......8G-6
MIRRORS - DESCRIPTION, POWER ......8N-26 MIRRORS - OPERATION, HEATED
........8G-6
MIRRORS - OPERATION, POWER ........8N-26
MIRRORS, DIAGNOSIS AND TESTING - POWER ............................ 8N-27
MODE DOOR ACTUATOR - DESCRIPTION . . 24-29
MODE DOOR ACTUATOR - INSTALLATION ....................... 24-30
MODE DOOR ACTUATOR - OPERATION . . . 24-29
MODE DOOR ACTUATOR - REAR - DESCRIPTION ....................... 24-39
MODE DOOR ACTUATOR - REAR - INSTALLATION ....................... 24-40
MODE DOOR ACTUATOR - REAR - OPERATION ......................... 24-39
MODE DOOR ACTUATOR - REAR - REMOVAL .......................... 24-39
MODE DOOR ACTUATOR - REMOVAL .....24-29
MODE, OPERATION - DRB III TS TAT E
DISPLAY TEST ....................... 25-10
MODELS, INSTALLATION - RG ..........24-27
MODELS, INSTALLATION - RS ..........24-28
MODELS, REMOVAL - RG ..............24-27
MODELS, REMOVAL - RS ..............24-27
MODES OF OPERATION - OPERATION ....14-22
MODULE - BLOWER MOTOR - DESCRIPTION, POWER ................24-30
MODULE - BLOWER MOTOR - INSTALLATION, POWER ...............24-31
MODULE - BLOWER MOTOR - OPERATION, POWER .................. 24-30
MODULE - BLOWER MOTOR - REMOVAL, POWER ................... 24-30
MODULE - DESCRIPTION, BODY CONTROL ........................... 8E-2
MODULE - DESCRIPTION, FRONT CONTROL ........................... 8E-7
MODULE - DESCRIPTION, FUEL PUMP ....14-8
MODULE - DESCRIPTION, HEATED SEAT . . . 8E-8
MODULE - DESCRIPTION, INTEGRATED POWER ..........................8W -97-1
MODULE - DESCRIPTION, MEMORY SEAT/MIRROR ........................ 8E-9
MODULE - DESCRIPTION, OCCUPANT CLASSIFICATION ..................... 8O-25
MODULE - DESCRIPTION, PARK ASSIST . . . 8B-4
MODULE - DESCRIPTION, POWER LIFTGATE CONTROL .................. 8E-10
MODULE - DESCRIPTION, SENTRY KEY REMOTE ENTRY ...................... 8Q-3
MODULE - DESCRIPTION, SLIDING DOOR CONTROL ..................... 8E-18
MODULE - DIAGNOSIS AND TESTING, SENTRY KEY REMOTE ENTRY ...........8Q-5
MODULE - EXPORT - DESCRIPTION, ANTENNA .......................... 8A-10
MODULE - EXPORT - OPERATION, ANTENNA .......................... 8A-10
MODULE - INSTALLATION, BODY CONTROL ........................... 8E-4
MODULE - INSTALLATION, HANDS FREE . . . 8T-3
MODULE - INSTALLATION, INTEGRATED POWER ..........................8W -97-2
MODULE - INSTALLATION, OCCUPANT CLASSIFICATION ..................... 8O-26
MODULE - INSTALLATION, PARK ASSIST . . 8B-6
MODULE - INSTALLATION, SENTRY KEY REMOTE ENTRY ...................... 8Q-6
MODULE - INSTALLATION, WIPER .......8R-14
MODULE - OPERATION, BODY CONTROL . . . 8E-3
MODULE - OPERATION, FRONT CONTROL ........................... 8E-7
MODULE - OPERATION, FUEL PUMP ......14-9
MODULE - OPERATION, HEATED SEAT .....8E-8
MODULE - OPERATION, INTEGRATED POWER ..........................8W -97-2
MODULE - OPERATION, MEMORY SEAT/MIRROR ........................ 8E-9
MODULE - OPERATION, OCCUPANT CLASSIFICATION ..................... 8O-25
MODULE - OPERATION, PARK ASSIST .....8B-5
MODULE - OPERATION, POWER LIFTGATE CONTROL .................. 8E-10
MODULE - OPERATION, SENTRY KEY REMOTE ENTRY ...................... 8Q-4
MODULE - OPERATION, SLIDING DOOR CONTROL .......................... 8E-18
MODULE - REAR BLOWER MOTOR - DESCRIPTION, POWER ................24-40
20 INDEXRS
Description Group-Page Description Group-Page Description Group-Page