ground clearance CHRYSLER CARAVAN 2005 Service Manual
[x] Cancel search | Manufacturer: CHRYSLER, Model Year: 2005, Model line: CARAVAN, Model: CHRYSLER CARAVAN 2005Pages: 2339, PDF Size: 59.69 MB
Page 39 of 2339
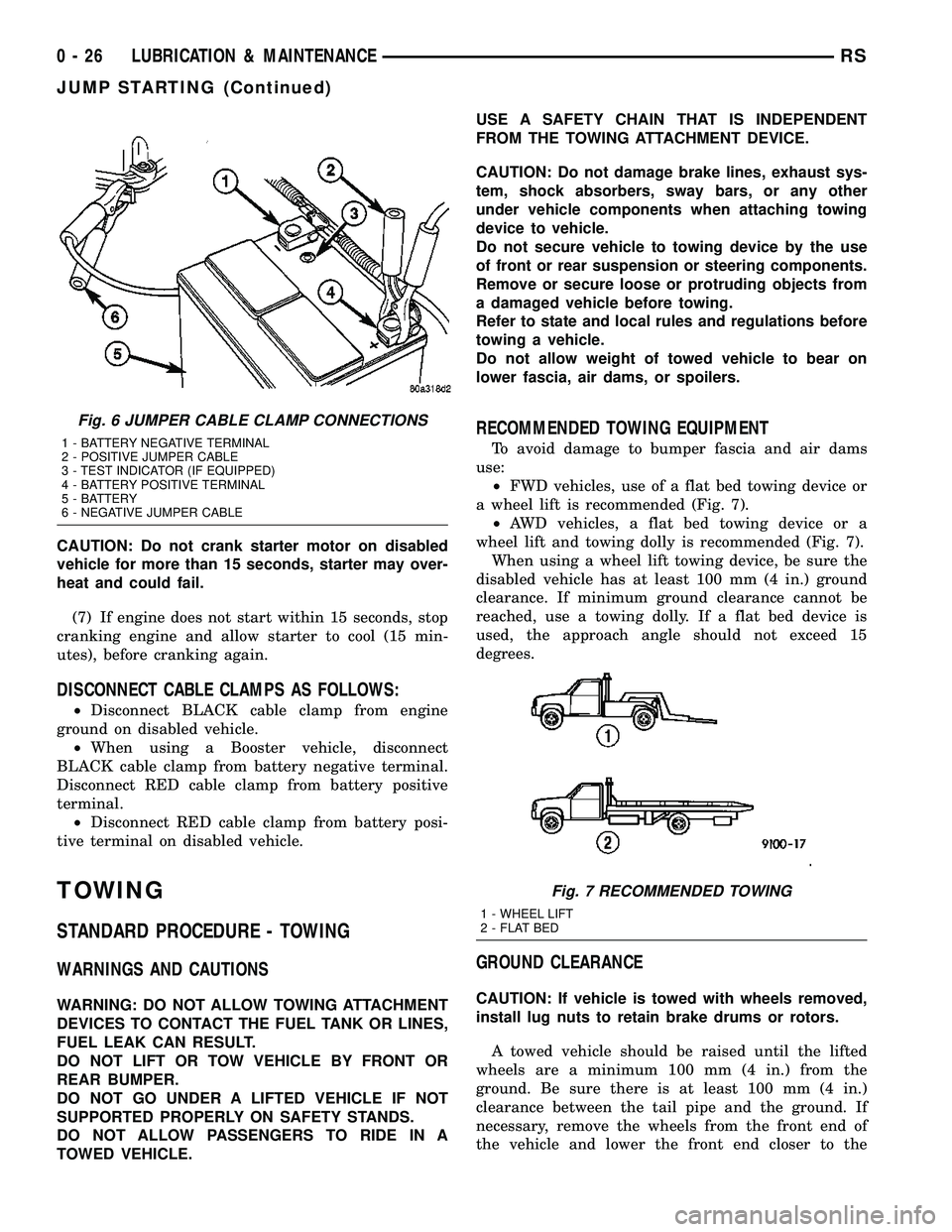
CAUTION: Do not crank starter motor on disabled
vehicle for more than 15 seconds, starter may over-
heat and could fail.
(7) If engine does not start within 15 seconds, stop
cranking engine and allow starter to cool (15 min-
utes), before cranking again.
DISCONNECT CABLE CLAMPS AS FOLLOWS:
²Disconnect BLACK cable clamp from engine
ground on disabled vehicle.
²When using a Booster vehicle, disconnect
BLACK cable clamp from battery negative terminal.
Disconnect RED cable clamp from battery positive
terminal.
²Disconnect RED cable clamp from battery posi-
tive terminal on disabled vehicle.
TOWING
STANDARD PROCEDURE - TOWING
WARNINGS AND CAUTIONS
WARNING: DO NOT ALLOW TOWING ATTACHMENT
DEVICES TO CONTACT THE FUEL TANK OR LINES,
FUEL LEAK CAN RESULT.
DO NOT LIFT OR TOW VEHICLE BY FRONT OR
REAR BUMPER.
DO NOT GO UNDER A LIFTED VEHICLE IF NOT
SUPPORTED PROPERLY ON SAFETY STANDS.
DO NOT ALLOW PASSENGERS TO RIDE IN A
TOWED VEHICLE.USE A SAFETY CHAIN THAT IS INDEPENDENT
FROM THE TOWING ATTACHMENT DEVICE.
CAUTION: Do not damage brake lines, exhaust sys-
tem, shock absorbers, sway bars, or any other
under vehicle components when attaching towing
device to vehicle.
Do not secure vehicle to towing device by the use
of front or rear suspension or steering components.
Remove or secure loose or protruding objects from
a damaged vehicle before towing.
Refer to state and local rules and regulations before
towing a vehicle.
Do not allow weight of towed vehicle to bear on
lower fascia, air dams, or spoilers.
RECOMMENDED TOWING EQUIPMENT
To avoid damage to bumper fascia and air dams
use:
²FWD vehicles, use of a flat bed towing device or
a wheel lift is recommended (Fig. 7).
²AWD vehicles, a flat bed towing device or a
wheel lift and towing dolly is recommended (Fig. 7).
When using a wheel lift towing device, be sure the
disabled vehicle has at least 100 mm (4 in.) ground
clearance. If minimum ground clearance cannot be
reached, use a towing dolly. If a flat bed device is
used, the approach angle should not exceed 15
degrees.
GROUND CLEARANCE
CAUTION: If vehicle is towed with wheels removed,
install lug nuts to retain brake drums or rotors.
A towed vehicle should be raised until the lifted
wheels are a minimum 100 mm (4 in.) from the
ground. Be sure there is at least 100 mm (4 in.)
clearance between the tail pipe and the ground. If
necessary, remove the wheels from the front end of
the vehicle and lower the front end closer to the
Fig. 6 JUMPER CABLE CLAMP CONNECTIONS
1 - BATTERY NEGATIVE TERMINAL
2 - POSITIVE JUMPER CABLE
3 - TEST INDICATOR (IF EQUIPPED)
4 - BATTERY POSITIVE TERMINAL
5 - BATTERY
6 - NEGATIVE JUMPER CABLE
Fig. 7 RECOMMENDED TOWING
1 - WHEEL LIFT
2 - FLAT BED
0 - 26 LUBRICATION & MAINTENANCERS
JUMP STARTING (Continued)
Page 40 of 2339
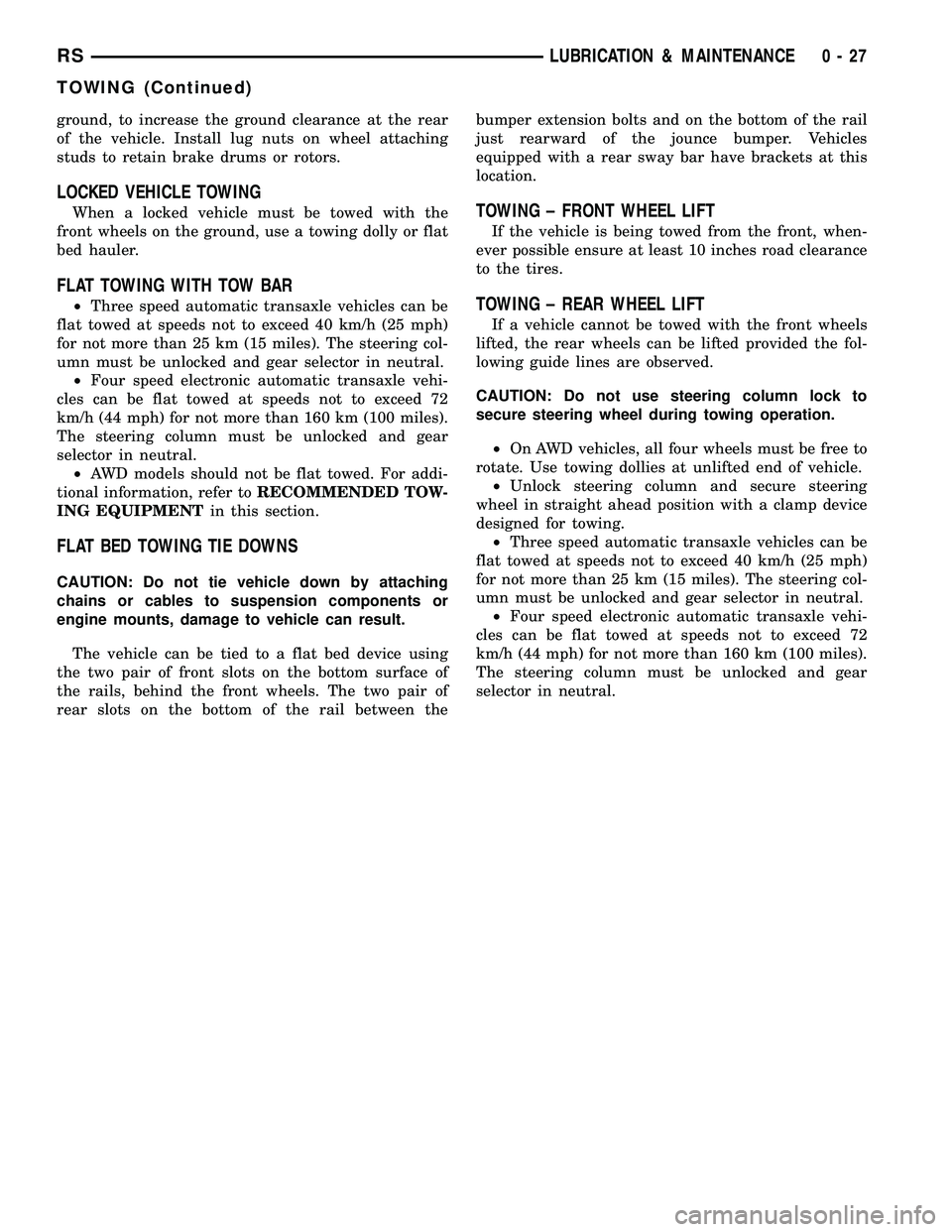
ground, to increase the ground clearance at the rear
of the vehicle. Install lug nuts on wheel attaching
studs to retain brake drums or rotors.
LOCKED VEHICLE TOWING
When a locked vehicle must be towed with the
front wheels on the ground, use a towing dolly or flat
bed hauler.
FLAT TOWING WITH TOW BAR
²Three speed automatic transaxle vehicles can be
flat towed at speeds not to exceed 40 km/h (25 mph)
for not more than 25 km (15 miles). The steering col-
umn must be unlocked and gear selector in neutral.
²Four speed electronic automatic transaxle vehi-
cles can be flat towed at speeds not to exceed 72
km/h (44 mph) for not more than 160 km (100 miles).
The steering column must be unlocked and gear
selector in neutral.
²AWD models should not be flat towed. For addi-
tional information, refer toRECOMMENDED TOW-
ING EQUIPMENTin this section.
FLAT BED TOWING TIE DOWNS
CAUTION: Do not tie vehicle down by attaching
chains or cables to suspension components or
engine mounts, damage to vehicle can result.
The vehicle can be tied to a flat bed device using
the two pair of front slots on the bottom surface of
the rails, behind the front wheels. The two pair of
rear slots on the bottom of the rail between thebumper extension bolts and on the bottom of the rail
just rearward of the jounce bumper. Vehicles
equipped with a rear sway bar have brackets at this
location.
TOWING ± FRONT WHEEL LIFT
If the vehicle is being towed from the front, when-
ever possible ensure at least 10 inches road clearance
to the tires.
TOWING ± REAR WHEEL LIFT
If a vehicle cannot be towed with the front wheels
lifted, the rear wheels can be lifted provided the fol-
lowing guide lines are observed.
CAUTION: Do not use steering column lock to
secure steering wheel during towing operation.
²On AWD vehicles, all four wheels must be free to
rotate. Use towing dollies at unlifted end of vehicle.
²Unlock steering column and secure steering
wheel in straight ahead position with a clamp device
designed for towing.
²Three speed automatic transaxle vehicles can be
flat towed at speeds not to exceed 40 km/h (25 mph)
for not more than 25 km (15 miles). The steering col-
umn must be unlocked and gear selector in neutral.
²Four speed electronic automatic transaxle vehi-
cles can be flat towed at speeds not to exceed 72
km/h (44 mph) for not more than 160 km (100 miles).
The steering column must be unlocked and gear
selector in neutral.
RSLUBRICATION & MAINTENANCE0-27
TOWING (Continued)
Page 1340 of 2339
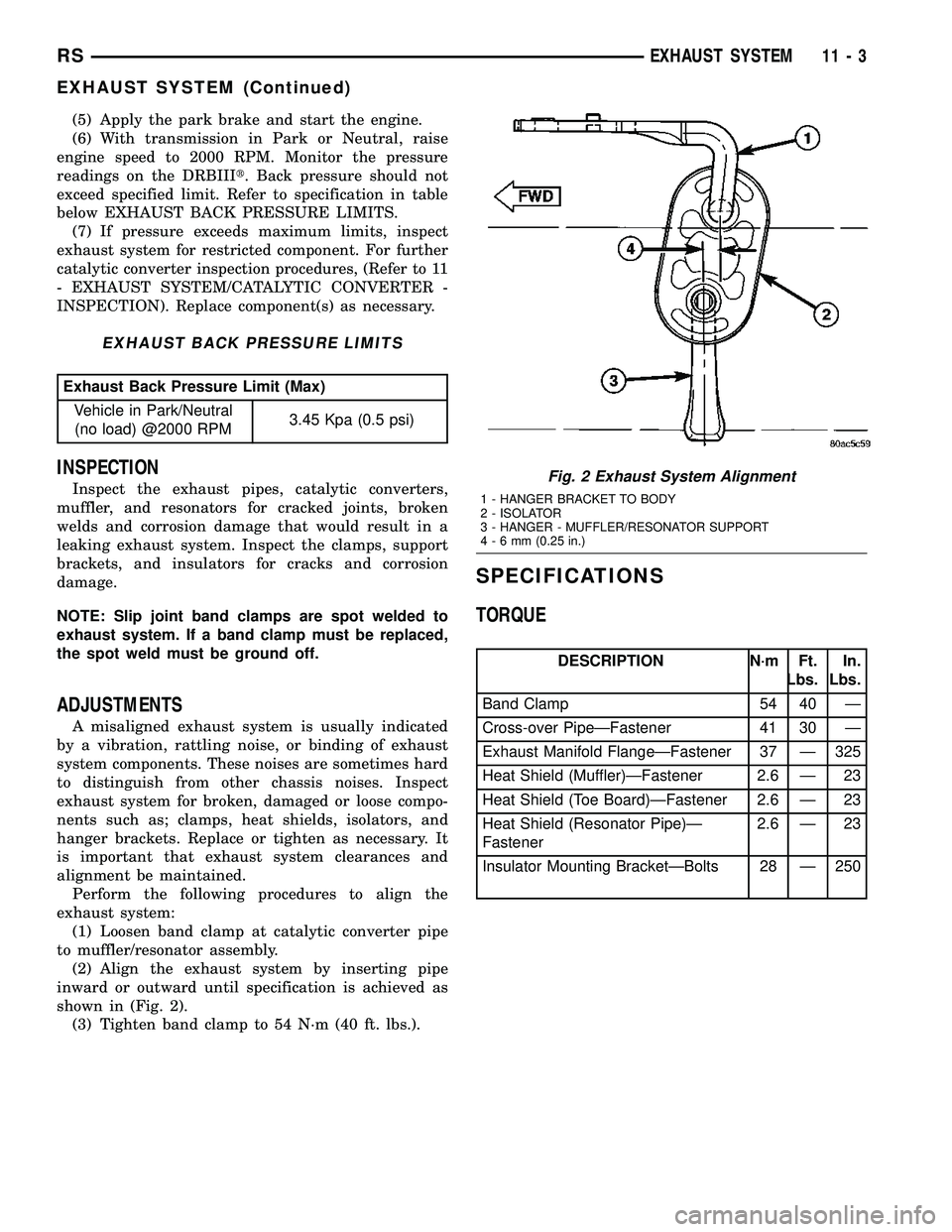
(5) Apply the park brake and start the engine.
(6) With transmission in Park or Neutral, raise
engine speed to 2000 RPM. Monitor the pressure
readings on the DRBIIIt. Back pressure should not
exceed specified limit. Refer to specification in table
below EXHAUST BACK PRESSURE LIMITS.
(7) If pressure exceeds maximum limits, inspect
exhaust system for restricted component. For further
catalytic converter inspection procedures, (Refer to 11
- EXHAUST SYSTEM/CATALYTIC CONVERTER -
INSPECTION). Replace component(s) as necessary.
EXHAUST BACK PRESSURE LIMITS
Exhaust Back Pressure Limit (Max)
Vehicle in Park/Neutral
(no load) @2000 RPM3.45 Kpa (0.5 psi)
INSPECTION
Inspect the exhaust pipes, catalytic converters,
muffler, and resonators for cracked joints, broken
welds and corrosion damage that would result in a
leaking exhaust system. Inspect the clamps, support
brackets, and insulators for cracks and corrosion
damage.
NOTE: Slip joint band clamps are spot welded to
exhaust system. If a band clamp must be replaced,
the spot weld must be ground off.
ADJUSTMENTS
A misaligned exhaust system is usually indicated
by a vibration, rattling noise, or binding of exhaust
system components. These noises are sometimes hard
to distinguish from other chassis noises. Inspect
exhaust system for broken, damaged or loose compo-
nents such as; clamps, heat shields, isolators, and
hanger brackets. Replace or tighten as necessary. It
is important that exhaust system clearances and
alignment be maintained.
Perform the following procedures to align the
exhaust system:
(1) Loosen band clamp at catalytic converter pipe
to muffler/resonator assembly.
(2) Align the exhaust system by inserting pipe
inward or outward until specification is achieved as
shown in (Fig. 2).
(3) Tighten band clamp to 54 N´m (40 ft. lbs.).
SPECIFICATIONS
TORQUE
DESCRIPTION N´m Ft.
Lbs.In.
Lbs.
Band Clamp 54 40 Ð
Cross-over PipeÐFastener 41 30 Ð
Exhaust Manifold FlangeÐFastener 37 Ð 325
Heat Shield (Muffler)ÐFastener 2.6 Ð 23
Heat Shield (Toe Board)ÐFastener 2.6 Ð 23
Heat Shield (Resonator Pipe)Ð
Fastener2.6 Ð 23
Insulator Mounting BracketÐBolts 28 Ð 250
Fig. 2 Exhaust System Alignment
1 - HANGER BRACKET TO BODY
2 - ISOLATOR
3 - HANGER - MUFFLER/RESONATOR SUPPORT
4-6mm(0.25 in.)
RSEXHAUST SYSTEM11-3
EXHAUST SYSTEM (Continued)
Page 2236 of 2339
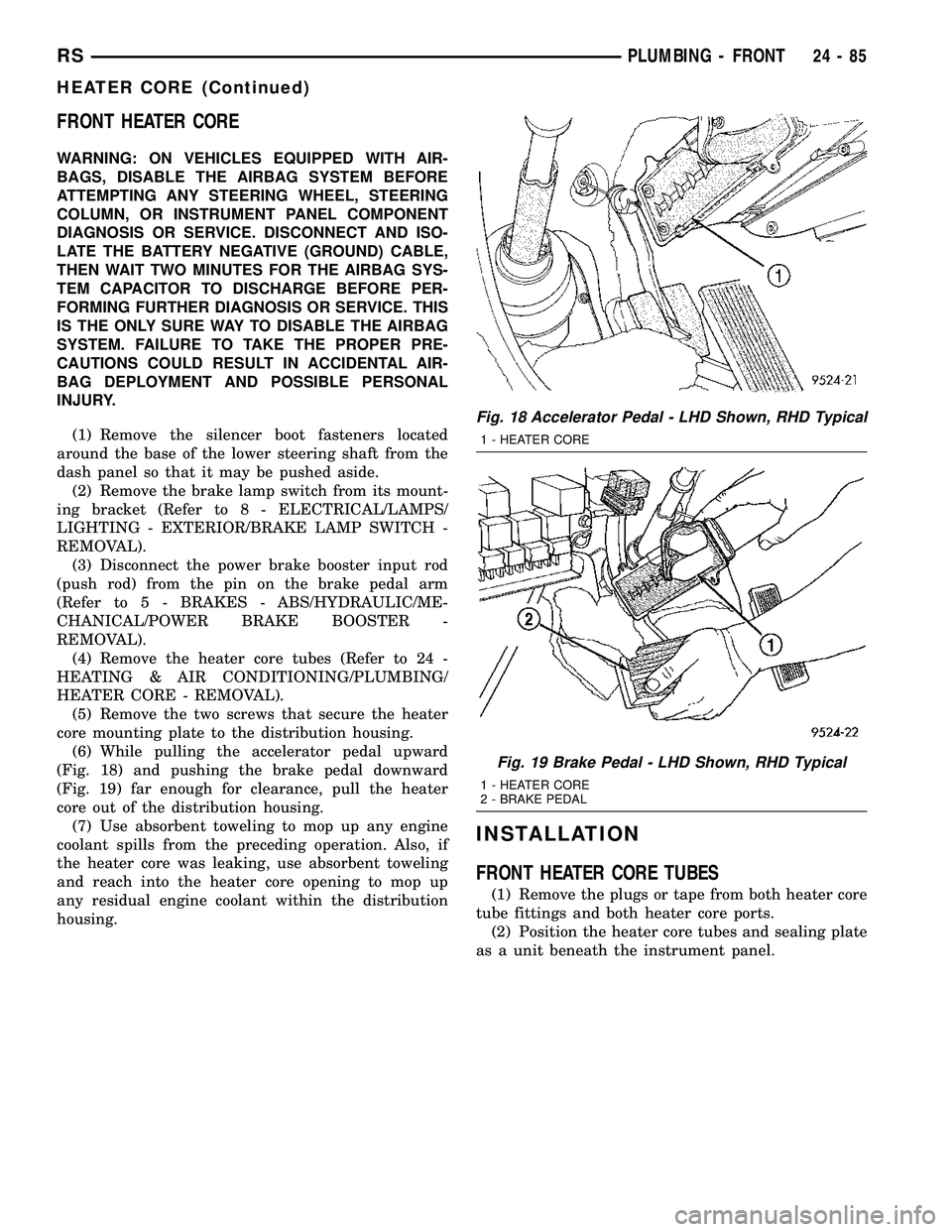
FRONT HEATER CORE
WARNING: ON VEHICLES EQUIPPED WITH AIR-
BAGS, DISABLE THE AIRBAG SYSTEM BEFORE
ATTEMPTING ANY STEERING WHEEL, STEERING
COLUMN, OR INSTRUMENT PANEL COMPONENT
DIAGNOSIS OR SERVICE. DISCONNECT AND ISO-
LATE THE BATTERY NEGATIVE (GROUND) CABLE,
THEN WAIT TWO MINUTES FOR THE AIRBAG SYS-
TEM CAPACITOR TO DISCHARGE BEFORE PER-
FORMING FURTHER DIAGNOSIS OR SERVICE. THIS
IS THE ONLY SURE WAY TO DISABLE THE AIRBAG
SYSTEM. FAILURE TO TAKE THE PROPER PRE-
CAUTIONS COULD RESULT IN ACCIDENTAL AIR-
BAG DEPLOYMENT AND POSSIBLE PERSONAL
INJURY.
(1) Remove the silencer boot fasteners located
around the base of the lower steering shaft from the
dash panel so that it may be pushed aside.
(2) Remove the brake lamp switch from its mount-
ing bracket (Refer to 8 - ELECTRICAL/LAMPS/
LIGHTING - EXTERIOR/BRAKE LAMP SWITCH -
REMOVAL).
(3) Disconnect the power brake booster input rod
(push rod) from the pin on the brake pedal arm
(Refer to 5 - BRAKES - ABS/HYDRAULIC/ME-
CHANICAL/POWER BRAKE BOOSTER -
REMOVAL).
(4) Remove the heater core tubes (Refer to 24 -
HEATING & AIR CONDITIONING/PLUMBING/
HEATER CORE - REMOVAL).
(5) Remove the two screws that secure the heater
core mounting plate to the distribution housing.
(6) While pulling the accelerator pedal upward
(Fig. 18) and pushing the brake pedal downward
(Fig. 19) far enough for clearance, pull the heater
core out of the distribution housing.
(7) Use absorbent toweling to mop up any engine
coolant spills from the preceding operation. Also, if
the heater core was leaking, use absorbent toweling
and reach into the heater core opening to mop up
any residual engine coolant within the distribution
housing.
INSTALLATION
FRONT HEATER CORE TUBES
(1) Remove the plugs or tape from both heater core
tube fittings and both heater core ports.
(2) Position the heater core tubes and sealing plate
as a unit beneath the instrument panel.
Fig. 18 Accelerator Pedal - LHD Shown, RHD Typical
1 - HEATER CORE
Fig. 19 Brake Pedal - LHD Shown, RHD Typical
1 - HEATER CORE
2 - BRAKE PEDAL
RSPLUMBING - FRONT24-85
HEATER CORE (Continued)
Page 2308 of 2339
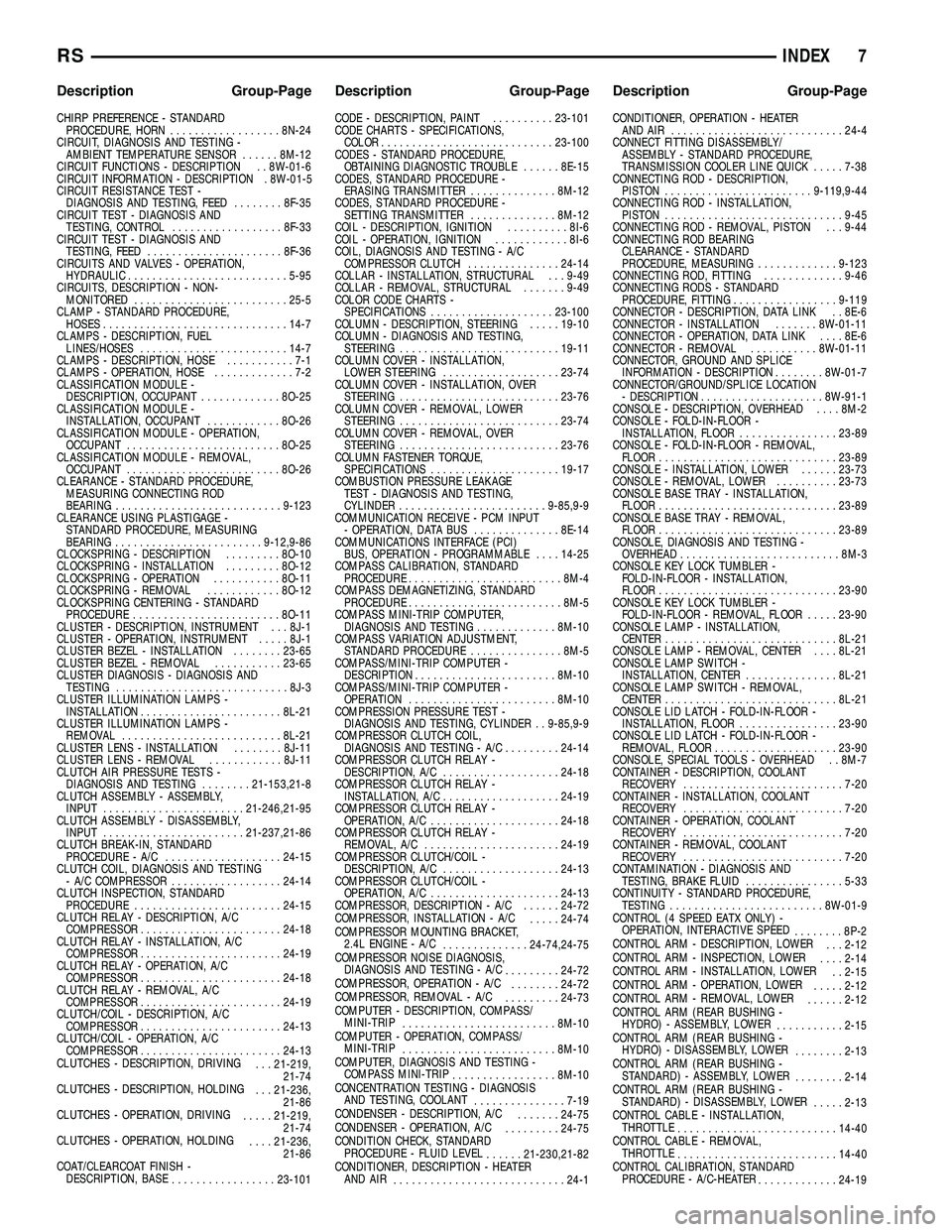
CHIRP PREFERENCE - STANDARDPROCEDURE, HORN .................. 8N-24
CIRCUIT, DIAGNOSIS AND TESTING - AMBIENT TEMPERATURE SENSOR ......8M-12
CIRCUIT FUNCTIONS - DESCRIPTION . . 8W-01-6
CIRCUIT INFORMATION - DESCRIPTION . 8W-01-5
CIRCUIT RESISTANCE TEST - DIAGNOSIS AND TESTING, FEED ........8F-35
CIRCUIT TEST - DIAGNOSIS AND TESTING, CONTROL .................. 8F-33
CIRCUIT TEST - DIAGNOSIS AND TESTING, FEED ...................... 8F-36
CIRCUITS AND VALVES - OPERATION, HYDRAULIC .......................... 5-95
CIRCUITS, DESCRIPTION - NON- MONITORED ......................... 25-5
CLAMP - STANDARD PROCEDURE, HOSES .............................. 14-7
CLAMPS - DESCRIPTION, FUEL LINES/HOSES ........................ 14-7
CLAMPS - DESCRIPTION, HOSE ...........7-1
CLAMPS - OPERATION, HOSE .............7-2
CLASSIFICATION MODULE - DESCRIPTION, OCCUPANT .............8O-25
CLASSIFICATION MODULE - INSTALLATION, OCCUPANT ............8O-26
CLASSIFICATION MODULE - OPERATION, OCCUPANT ......................... 8O-25
CLASSIFICATION MODULE - REMOVAL, OCCUPANT ......................... 8O-26
CLEARANCE - STANDARD PROCEDURE, MEASURING CONNECTING ROD
BEARING ............................ 9-123
CLEARANCE USING PLASTIGAGE - STANDARD PROCEDURE, MEASURING
BEARING ........................ 9-12,9-86
CLOCKSPRING - DESCRIPTION .........8O-10
CLOCKSPRING - INSTALLATION .........8O-12
CLOCKSPRING - OPERATION ...........8O-11
CLOCKSPRING - REMOVAL ............8O-12
CLOCKSPRING CENTERING - STANDARD PROCEDURE ........................ 8O-11
CLUSTER - DESCRIPTION, INSTRUMENT . . . 8J-1
CLUSTER - OPERATION, INSTRUMENT .....8J-1
CLUSTER BEZEL - INSTALLATION ........23-65
CLUSTER BEZEL - REMOVAL ...........23-65
CLUSTER DIAGNOSIS - DIAGNOSIS AND TESTING ............................ 8J-3
CLUSTER ILLUMINATION LAMPS - INSTALLATION ....................... 8L-21
CLUSTER ILLUMINATION LAMPS - REMOVAL .......................... 8L-21
CLUSTER LENS - INSTALLATION ........8J-11
CLUSTER LENS - REMOVAL ............8J-11
CLUTCH AIR PRESSURE TESTS - DIAGNOSIS AND TESTING ........21-153,21-8
CLUTCH ASSEMBLY - ASSEMBLY, INPUT ....................... 21-246,21-95
CLUTCH ASSEMBLY - DISASSEMBLY, INPUT ....................... 21-237,21-86
CLUTCH BREAK-IN, STANDARD PROCEDURE - A/C ................... 24-15
CLUTCH COIL, DIAGNOSIS AND TESTING - A/C COMPRESSOR .................. 24-14
CLUTCH INSPECTION, STANDARD PROCEDURE ........................ 24-15
CLUTCH RELAY - DESCRIPTION, A/C COMPRESSOR ....................... 24-18
CLUTCH RELAY - INSTALLATION, A/C COMPRESSOR ....................... 24-19
CLUTCH RELAY - OPERATION, A/C COMPRESSOR ....................... 24-18
CLUTCH RELAY - REMOVAL, A/C COMPRESSOR ....................... 24-19
CLUTCH/COIL - DESCRIPTION, A/C COMPRESSOR ....................... 24-13
CLUTCH/COIL - OPERATION, A/C COMPRESSOR ....................... 24-13
CLUTCHES - DESCRIPTION, DRIVING . . . 21-219,
21-74
CLUTCHES - DESCRIPTION, HOLDING . . . 21-236,
21-86
CLUTCHES - OPERATION, DRIVING .....21-219,
21-74
CLUTCHES - OPERATION, HOLDING ....21-236,
21-86
COAT/CLEARCOAT FINISH - DESCRIPTION, BASE .................23-101CODE - DESCRIPTION, PAINT
..........23-101
CODE CHARTS - SPECIFICATIONS, COLOR ............................ 23-100
CODES - STANDARD PROCEDURE, OBTAINING DIAGNOSTIC TROUBLE ......8E-15
CODES, STANDARD PROCEDURE - ERASING TRANSMITTER ..............8M-12
CODES, STANDARD PROCEDURE - SETTING TRANSMITTER ..............8M-12
COIL - DESCRIPTION, IGNITION ..........8I-6
COIL - OPERATION, IGNITION ............8I-6
COIL, DIAGNOSIS AND TESTING - A/C COMPRESSOR CLUTCH ...............24-14
COLLAR - INSTALLATION, STRUCTURAL . . . 9-49
COLLAR - REMOVAL, STRUCTURAL .......9-49
COLOR CODE CHARTS - SPECIFICATIONS .................... 23-100
COLUMN - DESCRIPTION, STEERING .....19-10
COLUMN - DIAGNOSIS AND TESTING, STEERING .......................... 19-11
COLUMN COVER - INSTALLATION, LOWER STEERING ................... 23-74
COLUMN COVER - INSTALLATION, OVER STEERING .......................... 23-76
COLUMN COVER - REMOVAL, LOWER STEERING .......................... 23-74
COLUMN COVER - REMOVAL, OVER STEERING .......................... 23-76
COLUMN FASTENER TORQUE, SPECIFICATIONS ..................... 19-17
COMBUSTION PRESSURE LEAKAGE TEST - DIAGNOSIS AND TESTING,
CYLINDER ........................ 9-85,9-9
COMMUNICATION RECEIVE - PCM INPUT - OPERATION, DATA BUS ..............8E-14
COMMUNICATIONS INTERFACE (PCI) BUS, OPERATION - PROGRAMMABLE ....14-25
COMPASS CALIBRATION, STANDARD PROCEDURE ......................... 8M-4
COMPASS DEMAGNETIZING, STANDARD PROCEDURE ......................... 8M-5
COMPASS MINI-TRIP COMPUTER, DIAGNOSIS AND TESTING .............8M-10
COMPASS VARIATION ADJUSTMENT, STANDARD PROCEDURE ...............8M-5
COMPASS/MINI-TRIP COMPUTER - DESCRIPTION ....................... 8M-10
COMPASS/MINI-TRIP COMPUTER - OPERATION ........................ 8M-10
COMPRESSION PRESSURE TEST - DIAGNOSIS AND TESTING, CYLINDER . . 9-85,9-9
COMPRESSOR CLUTCH COIL, DIAGNOSIS AND TESTING - A/ C.........24-14
COMPRESSOR CLUTCH RELAY - DESCRIPTION, A/C ................... 24-18
COMPRESSOR CLUTCH RELAY - INSTALLATION, A/C ................... 24-19
COMPRESSOR CLUTCH RELAY - OPERATION, A/C ..................... 24-18
COMPRESSOR CLUTCH RELAY - REMOVAL, A/C ...................... 24-19
COMPRESSOR CLUTCH/COIL - DESCRIPTION, A/C ................... 24-13
COMPRESSOR CLUTCH/COIL - OPERATION, A/C ..................... 24-13
COMPRESSOR, DESCRIPTION - A/C ......24-72
COMPRESSOR, INSTALLATION - A/C .....24-74
COMPRESSOR MOUNTING BRACKET, 2.4L ENGINE - A/C ..............24-74,24-75
COMPRESSOR NOISE DIAGNOSIS, DIAGNOSIS AND TESTING - A/C .........24-72
COMPRESSOR, OPERATION - A/C ........24-72
COMPRESSOR, REMOVAL - A/C .........24-73
COMPUTER - DESCRIPTION, COMPASS/ MINI-TRIP ......................... 8M-10
COMPUTER - OPERATION, COMPASS/ MINI-TRIP ......................... 8M-10
COMPUTER, DIAGNOSIS AND TESTING - COMPASS MINI-TRIP .................8M-10
CONCENTRATION TESTING - DIAGNOSIS AND TESTING, COOLANT ...............7-19
CONDENSER - DESCRIPTION, A/C .......24-75
CONDENSER - OPERATION, A/C .........24-75
CONDITION CHECK, STANDARD PROCEDURE - FLUID LEVEL ......21-230,21-82
CONDITIONER, DESCRIPTION - HEATER AND AIR ............................ 24-1CONDITIONER, OPERATION - HEATER
AND AIR ............................ 24-4
CONNECT FITTING DISASSEMBLY/ ASSEMBLY - STANDARD PROCEDURE,
TRANSMISSION COOLER LINE QUICK .....7-38
CONNECTING ROD - DESCRIPTION, PISTON ........................ 9-119,9-44
CONNECTING ROD - INSTALLATION, PISTON ............................. 9-45
CONNECTING ROD - REMOVAL, PISTON . . . 9-44
CONNECTING ROD BEARING CLEARANCE - STANDARD
PROCEDURE, MEASURING .............9-123
CONNECTING ROD, FITTING .............9-46
CONNECTING RODS - STANDARD PROCEDURE, FITTING .................9-119
CONNECTOR - DESCRIPTION, DATA LINK . . 8E-6
CONNECTOR - INSTALLATION .......8W-01-11
CONNECTOR - OPERATION, DATA LINK ....8E-6
CONNECTOR - REMOVAL ...........8W-01-11
CONNECTOR, GROUND AND SPLICE INFORMATION - DESCRIPTION ........8W-01-7
CONNECTOR/GROUND/SPLICE LOCATION - DESCRIPTION ....................8W -91-1
CONSOLE - DESCRIPTION, OVERHEAD ....8M-2
CONSOLE - FOLD-IN-FLOOR - INSTALLATION, FLOOR ................23-89
CONSOLE - FOLD-IN-FLOOR - REMOVAL, FLOOR ............................. 23-89
CONSOLE - INSTALLATION, LOWER ......23-73
CONSOLE - REMOVAL, LOWER ..........23-73
CONSOLE BASE TRAY - INSTALLATION, FLOOR ............................. 23-89
CONSOLE BASE TRAY - REMOVAL, FLOOR ............................. 23-89
CONSOLE, DIAGNOSIS AND TESTING - OVERHEAD .......................... 8M-3
CONSOLE KEY LOCK TUMBLER - FOLD-IN-FLOOR - INSTALLATION,
FLOOR ............................. 23-90
CONSOLE KEY LOCK TUMBLER - FOLD-IN-FLOOR - REMOVAL, FLOOR .....23-90
CONSOLE LAMP - INSTALLATION, CENTER ............................ 8L-21
CONSOLE LAMP - REMOVAL, CENTER ....8L-21
CONSOLE LAMP SWITCH - INSTALLATION, CENTER ...............8L-21
CONSOLE LAMP SWITCH - REMOVAL, CENTER ............................ 8L-21
CONSOLE LID LATCH - FOLD-IN-FLOOR - INSTALLATION, FLOOR ................23-90
CONSOLE LID LATCH - FOLD-IN-FLOOR - REMOVAL, FLOOR .................... 23-90
CONSOLE, SPECIAL TOOLS - OVERHEAD . . 8M-7
CONTAINER - DESCRIPTION, COOLANT RECOVERY .......................... 7-20
CONTAINER - INSTALLATION, COOLANT RECOVERY .......................... 7-20
CONTAINER - OPERATION, COOLANT RECOVERY .......................... 7-20
CONTAINER - REMOVAL, COOLANT RECOVERY .......................... 7-20
CONTAMINATION - DIAGNOSIS AND TESTING, BRAKE FLUID ................5-33
CONTINUITY - STANDARD PROCEDURE, TESTING .........................8W -01-9
CONTROL (4 SPEED EATX ONLY) - OPERATION, INTERACTIVE SPEED ........8P-2
CONTROL ARM - DESCRIPTION, LOWER . . . 2-12
CONTROL ARM - INSPECTION, LOWER ....2-14
CONTROL ARM - INSTALLATION, LOWER . . 2-15
CONTROL ARM - OPERATION, LOWER .....2-12
CONTROL ARM - REMOVAL, LOWER ......2-12
CONTROL ARM (REAR BUSHING - HYDRO) - ASSEMBLY, LOWER ...........2-15
CONTROL ARM (REAR BUSHING - HYDRO) - DISASSEMBLY, LOWER ........2-13
CONTROL ARM (REAR BUSHING - STANDARD) - ASSEMBLY, LOWER ........2-14
CONTROL ARM (REAR BUSHING - STANDARD) - DISASSEMBLY, LOWER .....2-13
CONTROL CABLE - INSTALLATION, THROTTLE .......................... 14-40
CONTROL CABLE - REMOVAL, THROTTLE .......................... 14-40
CONTROL CALIBRATION, STANDARD PROCEDURE - A/C-HEATER .............24-19
RS INDEX7
Description Group-Page Description Group-Page Description Group-Page
Page 2324 of 2339
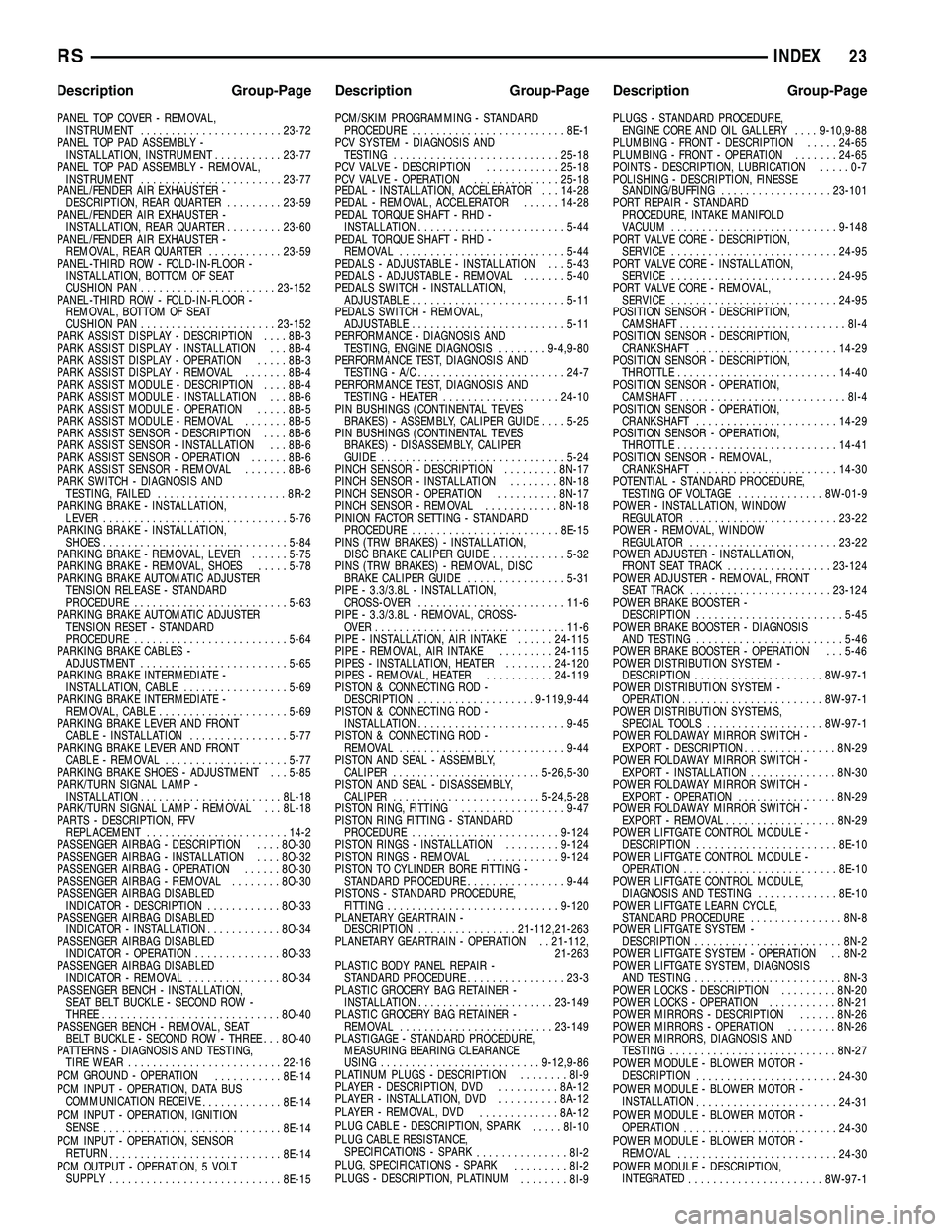
PANEL TOP COVER - REMOVAL,INSTRUMENT ....................... 23-72
PANEL TOP PAD ASSEMBLY - INSTALLATION, INSTRUMENT ...........23-77
PANEL TOP PAD ASSEMBLY - REMOVAL, INSTRUMENT ....................... 23-77
PANEL/FENDER AIR EXHAUSTER - DESCRIPTION, REAR QUARTER .........23-59
PANEL/FENDER AIR EXHAUSTER - INSTALLATION, REAR QUARTER .........23-60
PANEL/FENDER AIR EXHAUSTER - REMOVAL, REAR QUARTER ............23-59
PANEL-THIRD ROW - FOLD-IN-FLOOR - INSTALLATION, BOTTOM OF SEAT
CUSHION PAN ...................... 23-152
PANEL-THIRD ROW - FOLD-IN-FLOOR - REMOVAL, BOTTOM OF SEAT
CUSHION PAN ...................... 23-152
PARK ASSIST DISPLAY - DESCRIPTION ....8B-3
PARK ASSIST DISPLAY - INSTALLATION . . . 8B-4
PARK ASSIST DISPLAY - OPERATION .....8B-3
PARK ASSIST DISPLAY - REMOVAL .......8B-4
PARK ASSIST MODULE - DESCRIPTION ....8B-4
PARK ASSIST MODULE - INSTALLATION . . . 8B-6
PARK ASSIST MODULE - OPERATION .....8B-5
PARK ASSIST MODULE - REMOVAL .......8B-5
PARK ASSIST SENSOR - DESCRIPTION ....8B-6
PARK ASSIST SENSOR - INSTALLATION . . . 8B-6
PARK ASSIST SENSOR - OPERATION ......8B-6
PARK ASSIST SENSOR - REMOVAL .......8B-6
PARK SWITCH - DIAGNOSIS AND TESTING, FAILED ..................... 8R-2
PARKING BRAKE - INSTALLATION, LEVER .............................. 5-76
PARKING BRAKE - INSTALLATION, SHOES .............................. 5-84
PARKING BRAKE - REMOVAL, LEVER ......5-75
PARKING BRAKE - REMOVAL, SHOES .....5-78
PARKING BRAKE AUTOMATIC ADJUSTER TENSION RELEASE - STANDARD
PROCEDURE ......................... 5-63
PARKING BRAKE AUTOMATIC ADJUSTER TENSION RESET - STANDARD
PROCEDURE ......................... 5-64
PARKING BRAKE CABLES - ADJUSTMENT ........................ 5-65
PARKING BRAKE INTERMEDIATE - INSTALLATION, CABLE .................5-69
PARKING BRAKE INTERMEDIATE - REMOVAL, CABLE ..................... 5-69
PARKING BRAKE LEVER AND FRONT CABLE - INSTALLATION ................5-77
PARKING BRAKE LEVER AND FRONT CABLE - REMOVAL .................... 5-77
PARKING BRAKE SHOES - ADJUSTMENT . . . 5-85
PARK/TURN SIGNAL LAMP - INSTALLATION ....................... 8L-18
PARK/TURN SIGNAL LAMP - REMOVAL . . . 8L-18
PARTS - DESCRIPTION, FFV REPLACEMENT ....................... 14-2
PASSENGER AIRBAG - DESCRIPTION ....8O-30
PASSENGER AIRBAG - INSTALLATION ....8O-32
PASSENGER AIRBAG - OPERATION ......8O-30
PASSENGER AIRBAG - REMOVAL ........8O-30
PASSENGER AIRBAG DISABLED INDICATOR - DESCRIPTION ............8O-33
PASSENGER AIRBAG DISABLED INDICATOR - INSTALLATION ............8O-34
PASSENGER AIRBAG DISABLED INDICATOR - OPERATION ..............8O-33
PASSENGER AIRBAG DISABLED INDICATOR - REMOVAL ...............8O-34
PASSENGER BENCH - INSTALLATION, SEAT BELT BUCKLE - SECOND ROW -
THREE ............................. 8O-40
PASSENGER BENCH - REMOVAL, SEAT BELT BUCKLE - SECOND ROW - THREE . . . 8O-40
PATTERNS - DIAGNOSIS AND TESTING, TIRE WEAR ......................... 22-16
PCM GROUND - OPERATION ...........8E-14
PCM INPUT - OPERATION, DATA BUS COMMUNICATION RECEIVE .............8E-14
PCM INPUT - OPERATION, IGNITION SENSE ............................. 8E-14
PCM INPUT - OPERATION, SENSOR RETURN ............................ 8E-14
PCM OUTPUT - OPERATION, 5 VOLT SUPPLY ............................ 8E-15PCM/SKIM PROGRAMMING - STANDARD
PROCEDURE ......................... 8E-1
PCV SYSTEM - DIAGNOSIS AND TESTING ........................... 25-18
PCV VALVE - DESCRIPTION ............25-18
PCV VALVE - OPERATION ..............25-18
PEDAL - INSTALLATION, ACCELERATOR . . . 14-28
PEDAL - REMOVAL, ACCELERATOR ......14-28
PEDAL TORQUE SHAFT - RHD - INSTALLATION ........................ 5-44
PEDAL TORQUE SHAFT - RHD - REMOVAL ........................... 5-44
PEDALS - ADJUSTABLE - INSTALLATION . . . 5-43
PEDALS - ADJUSTABLE - REMOVAL .......5-40
PEDALS SWITCH - INSTALLATION, ADJUSTABLE ......................... 5-11
PEDALS SWITCH - REMOVAL, ADJUSTABLE ......................... 5-11
PERFORMANCE - DIAGNOSIS AND TESTING, ENGINE DIAGNOSIS ........9-4,9-80
PERFORMANCE TEST, DIAGNOSIS AND TESTING - A/C ........................ 24-7
PERFORMANCE TEST, DIAGNOSIS AND TESTING - HEATER ................... 24-10
PIN BUSHINGS (CONTINENTAL TEVES BRAKES) - ASSEMBLY, CALIPER GUIDE ....5-25
PIN BUSHINGS (CONTINENTAL TEVES BRAKES) - DISASSEMBLY, CALIPER
GUIDE .............................. 5-24
PINCH SENSOR - DESCRIPTION .........8N-17
PINCH SENSOR - INSTALLATION ........8N-18
PINCH SENSOR - OPERATION ..........8N-17
PINCH SENSOR - REMOVAL ............8N-18
PINION FACTOR SETTING - STANDARD PROCEDURE ........................ 8E-15
PINS (TRW BRAKES) - INSTALLATION, DISC BRAKE CALIPER GUIDE ............5-32
PINS (TRW BRAKES) - REMOVAL, DISC BRAKE CALIPER GUIDE ................5-31
PIPE - 3.3/3.8L - INSTALLATION, CROSS-OVER ........................ 11-6
PIPE - 3.3/3.8L - REMOVAL, CROSS- OVER ............................... 11-6
PIPE - INSTALLATION, AIR INTAKE ......24-115
PIPE - REMOVAL, AIR INTAKE .........24-115
PIPES - INSTALLATION, HEATER ........24-120
PIPES - REMOVAL, HEATER ...........24-119
PISTON & CONNECTING ROD - DESCRIPTION ................... 9-119,9-44
PISTON & CONNECTING ROD - INSTALLATION ........................ 9-45
PISTON & CONNECTING ROD - REMOVAL ........................... 9-44
PISTON AND SEAL - ASSEMBLY, CALIPER ........................ 5-26,5-30
PISTON AND SEAL - DISASSEMBLY, CALIPER ........................ 5-24,5-28
PISTON RING, FITTING .................9-47
PISTON RING FITTING - STANDARD PROCEDURE ........................ 9-124
PISTON RINGS - INSTALLATION .........9-124
PISTON RINGS - REMOVAL ............9-124
PISTON TO CYLINDER BORE FITTING - STANDARD PROCEDURE ................9-44
PISTONS - STANDARD PROCEDURE, FITTING ............................ 9-120
PLANETARY GEARTRAIN - DESCRIPTION ................ 21-112,21-263
PLANETARY GEARTRAIN - OPERATION . . 21-112, 21-263
PLASTIC BODY PANEL REPAIR - STANDARD PROCEDURE ................23-3
PLASTIC GROCERY BAG RETAINER - INSTALLATION ...................... 23-149
PLASTIC GROCERY BAG RETAINER - REMOVAL ......................... 23-149
PLASTIGAGE - STANDARD PROCEDURE, MEASURING BEARING CLEARANCE
USING .......................... 9-12,9-86
PLATINUM PLUGS - DESCRIPTION ........8I-9
PLAYER - DESCRIPTION, DVD ..........8A-12
PLAYER - INSTALLATION, DVD ..........8A-12
PLAYER - REMOVAL, DVD .............8A-12
PLUG CABLE - DESCRIPTION, SPARK .....8I-10
PLUG CABLE RESISTANCE, SPECIFICATIONS - SPARK ...............8I-2
PLUG, SPECIFICATIONS - SPARK .........8I-2
PLUGS - DESCRIPTION, PLATINUM ........8I-9PLUGS - STANDARD PROCEDURE,
ENGINE CORE AND OIL GALLERY ....9-10,9-88
PLUMBING - FRONT - DESCRIPTION .....24-65
PLUMBING - FRONT - OPERATION .......24-65
POINTS - DESCRIPTION, LUBRICATION .....0-7
POLISHING - DESCRIPTION, FINESSE SANDING/BUFFING .................. 23-101
PORT REPAIR - STANDARD PROCEDURE, INTAKE MANIFOLD
VACUUM ........................... 9-148
PORT VALVE CORE - DESCRIPTION, SERVICE ........................... 24-95
PORT VALVE CORE - INSTALLATION, SERVICE ........................... 24-95
PORT VALVE CORE - REMOVAL, SERVICE ........................... 24-95
POSITION SENSOR - DESCRIPTION, CAMSHAFT ........................... 8I-4
POSITION SENSOR - DESCRIPTION, CRANKSHAFT ....................... 14-29
POSITION SENSOR - DESCRIPTION, THROTTLE .......................... 14-40
POSITION SENSOR - OPERATION, CAMSHAFT ........................... 8I-4
POSITION SENSOR - OPERATION, CRANKSHAFT ....................... 14-29
POSITION SENSOR - OPERATION, THROTTLE .......................... 14-41
POSITION SENSOR - REMOVAL, CRANKSHAFT ....................... 14-30
POTENTIAL - STANDARD PROCEDURE, TESTING OF VOLTAGE ..............8W-01-9
POWER - INSTALLATION, WINDOW REGULATOR ........................ 23-22
POWER - REMOVAL, WINDOW REGULATOR ........................ 23-22
POWER ADJUSTER - INSTALLATION, FRONT SEAT TRACK .................23-124
POWER ADJUSTER - REMOVAL, FRONT SEAT TRACK ....................... 23-124
POWER BRAKE BOOSTER - DESCRIPTION ........................ 5-45
POWER BRAKE BOOSTER - DIAGNOSIS AND TESTING ........................ 5-46
POWER BRAKE BOOSTER - OPERATION . . . 5-46
POWER DISTRIBUTION SYSTEM - DESCRIPTION .....................8W -97-1
POWER DISTRIBUTION SYSTEM - OPERATION .......................8W -97-1
POWER DISTRIBUTION SYSTEMS, SPECIAL TOOLS ...................8W -97-1
POWER FOLDAWAY MIRROR SWITCH - EXPORT - DESCRIPTION ...............8N-29
POWER FOLDAWAY MIRROR SWITCH - EXPORT - INSTALLATION ..............8N-30
POWER FOLDAWAY MIRROR SWITCH - EXPORT - OPERATION ................8N-29
POWER FOLDAWAY MIRROR SWITCH - EXPORT - REMOVAL .................. 8N-29
POWER LIFTGATE CONTROL MODULE - DESCRIPTION ....................... 8E-10
POWER LIFTGATE CONTROL MODULE - OPERATION ......................... 8E-10
POWER LIFTGATE CONTROL MODULE, DIAGNOSIS AND TESTING .............8E-10
POWER LIFTGATE LEARN CYCLE, STANDARD PROCEDURE ...............8N-8
POWER LIFTGATE SYSTEM - DESCRIPTION ........................ 8N-2
POWER LIFTGATE SYSTEM - OPERATION . . 8N-2
POWER LIFTGATE SYSTEM, DIAGNOSIS AND TESTING ........................ 8N-3
POWER LOCKS - DESCRIPTION .........8N-20
POWER LOCKS - OPERATION ...........8N-21
POWER MIRRORS - DESCRIPTION ......8N-26
POWER MIRRORS - OPERATION ........8N-26
POWER MIRRORS, DIAGNOSIS AND TESTING ........................... 8N-27
POWER MODULE - BLOWER MOTOR - DESCRIPTION ....................... 24-30
POWER MODULE - BLOWER MOTOR - INSTALLATION ....................... 24-31
POWER MODULE - BLOWER MOTOR - OPERATION ......................... 24-30
POWER MODULE - BLOWER MOTOR - REMOVAL .......................... 24-30
POWER MODULE - DESCRIPTION, INTEGRATED ......................8W -97-1
RS INDEX23
Description Group-Page Description Group-Page Description Group-Page