relay CHRYSLER VOYAGER 2005 Service Manual
[x] Cancel search | Manufacturer: CHRYSLER, Model Year: 2005, Model line: VOYAGER, Model: CHRYSLER VOYAGER 2005Pages: 2339, PDF Size: 59.69 MB
Page 2187 of 2339
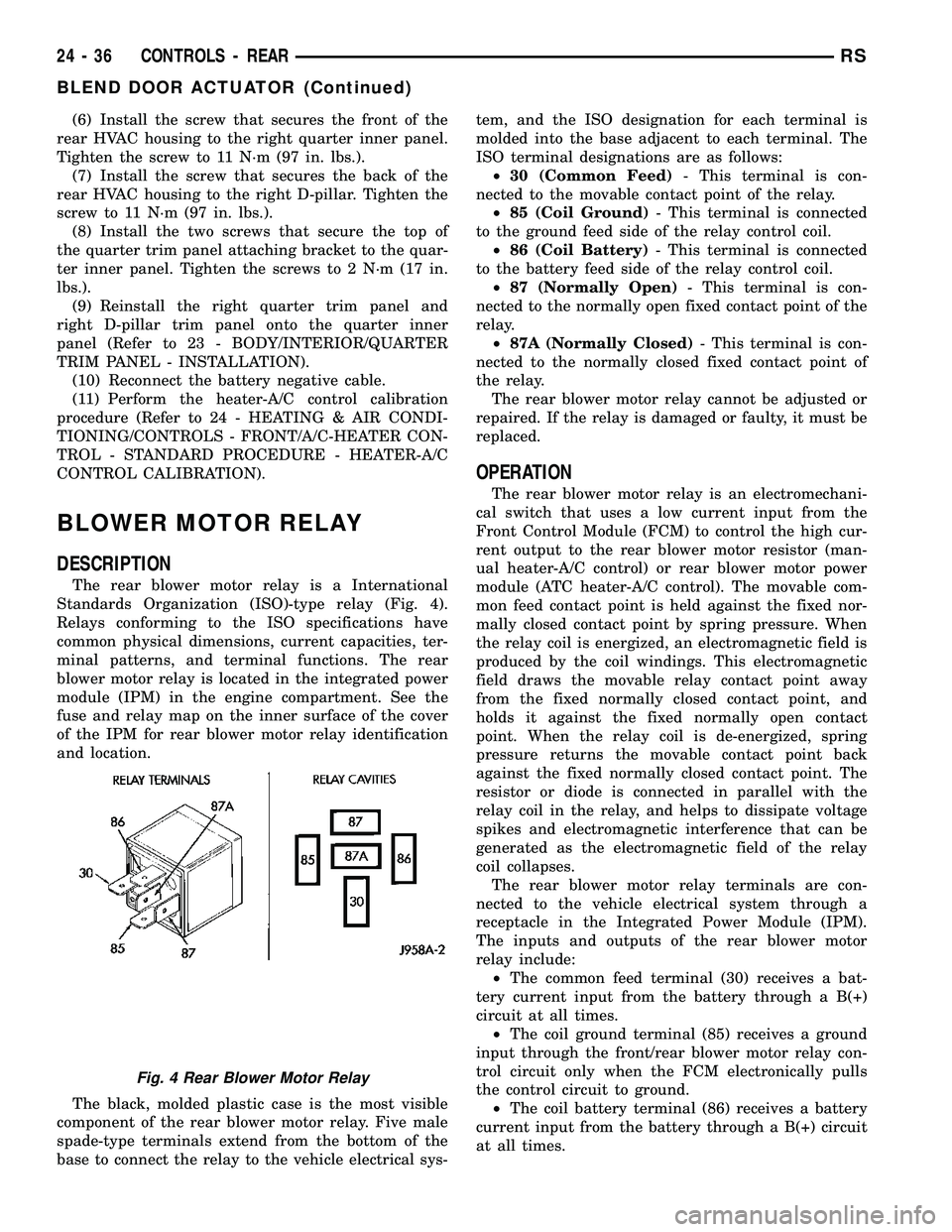
(6) Install the screw that secures the front of the
rear HVAC housing to the right quarter inner panel.
Tighten the screw to 11 N´m (97 in. lbs.).
(7) Install the screw that secures the back of the
rear HVAC housing to the right D-pillar. Tighten the
screw to 11 N´m (97 in. lbs.).
(8) Install the two screws that secure the top of
the quarter trim panel attaching bracket to the quar-
ter inner panel. Tighten the screws to 2 N´m (17 in.
lbs.).
(9) Reinstall the right quarter trim panel and
right D-pillar trim panel onto the quarter inner
panel (Refer to 23 - BODY/INTERIOR/QUARTER
TRIM PANEL - INSTALLATION).
(10) Reconnect the battery negative cable.
(11) Perform the heater-A/C control calibration
procedure (Refer to 24 - HEATING & AIR CONDI-
TIONING/CONTROLS - FRONT/A/C-HEATER CON-
TROL - STANDARD PROCEDURE - HEATER-A/C
CONTROL CALIBRATION).
BLOWER MOTOR RELAY
DESCRIPTION
The rear blower motor relay is a International
Standards Organization (ISO)-type relay (Fig. 4).
Relays conforming to the ISO specifications have
common physical dimensions, current capacities, ter-
minal patterns, and terminal functions. The rear
blower motor relay is located in the integrated power
module (IPM) in the engine compartment. See the
fuse and relay map on the inner surface of the cover
of the IPM for rear blower motor relay identification
and location.
The black, molded plastic case is the most visible
component of the rear blower motor relay. Five male
spade-type terminals extend from the bottom of the
base to connect the relay to the vehicle electrical sys-tem, and the ISO designation for each terminal is
molded into the base adjacent to each terminal. The
ISO terminal designations are as follows:
²30 (Common Feed)- This terminal is con-
nected to the movable contact point of the relay.
²85 (Coil Ground)- This terminal is connected
to the ground feed side of the relay control coil.
²86 (Coil Battery)- This terminal is connected
to the battery feed side of the relay control coil.
²87 (Normally Open)- This terminal is con-
nected to the normally open fixed contact point of the
relay.
²87A (Normally Closed)- This terminal is con-
nected to the normally closed fixed contact point of
the relay.
The rear blower motor relay cannot be adjusted or
repaired. If the relay is damaged or faulty, it must be
replaced.
OPERATION
The rear blower motor relay is an electromechani-
cal switch that uses a low current input from the
Front Control Module (FCM) to control the high cur-
rent output to the rear blower motor resistor (man-
ual heater-A/C control) or rear blower motor power
module (ATC heater-A/C control). The movable com-
mon feed contact point is held against the fixed nor-
mally closed contact point by spring pressure. When
the relay coil is energized, an electromagnetic field is
produced by the coil windings. This electromagnetic
field draws the movable relay contact point away
from the fixed normally closed contact point, and
holds it against the fixed normally open contact
point. When the relay coil is de-energized, spring
pressure returns the movable contact point back
against the fixed normally closed contact point. The
resistor or diode is connected in parallel with the
relay coil in the relay, and helps to dissipate voltage
spikes and electromagnetic interference that can be
generated as the electromagnetic field of the relay
coil collapses.
The rear blower motor relay terminals are con-
nected to the vehicle electrical system through a
receptacle in the Integrated Power Module (IPM).
The inputs and outputs of the rear blower motor
relay include:
²The common feed terminal (30) receives a bat-
tery current input from the battery through a B(+)
circuit at all times.
²The coil ground terminal (85) receives a ground
input through the front/rear blower motor relay con-
trol circuit only when the FCM electronically pulls
the control circuit to ground.
²The coil battery terminal (86) receives a battery
current input from the battery through a B(+) circuit
at all times.
Fig. 4 Rear Blower Motor Relay
24 - 36 CONTROLS - REARRS
BLEND DOOR ACTUATOR (Continued)
Page 2188 of 2339
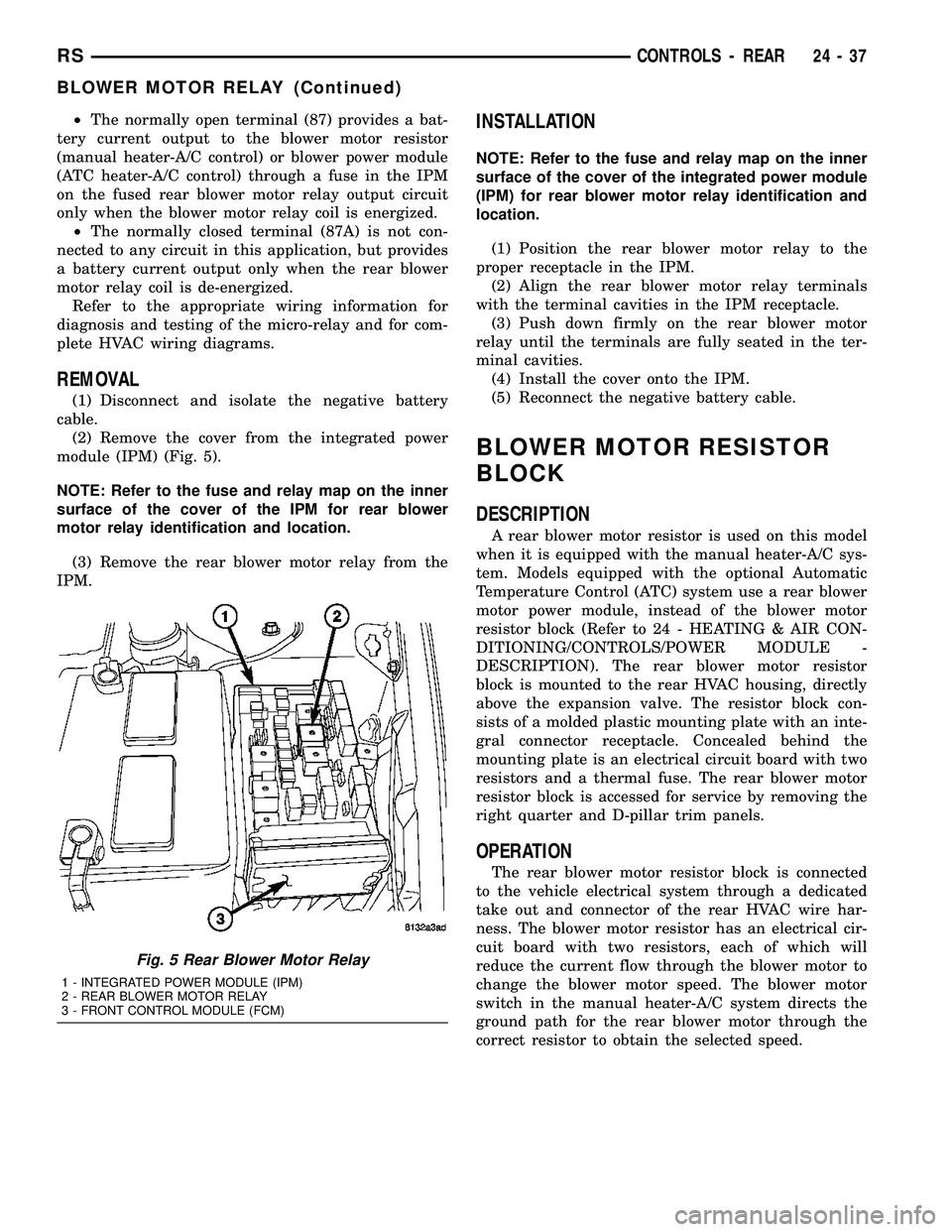
²The normally open terminal (87) provides a bat-
tery current output to the blower motor resistor
(manual heater-A/C control) or blower power module
(ATC heater-A/C control) through a fuse in the IPM
on the fused rear blower motor relay output circuit
only when the blower motor relay coil is energized.
²The normally closed terminal (87A) is not con-
nected to any circuit in this application, but provides
a battery current output only when the rear blower
motor relay coil is de-energized.
Refer to the appropriate wiring information for
diagnosis and testing of the micro-relay and for com-
plete HVAC wiring diagrams.
REMOVAL
(1) Disconnect and isolate the negative battery
cable.
(2) Remove the cover from the integrated power
module (IPM) (Fig. 5).
NOTE: Refer to the fuse and relay map on the inner
surface of the cover of the IPM for rear blower
motor relay identification and location.
(3) Remove the rear blower motor relay from the
IPM.
INSTALLATION
NOTE: Refer to the fuse and relay map on the inner
surface of the cover of the integrated power module
(IPM) for rear blower motor relay identification and
location.
(1) Position the rear blower motor relay to the
proper receptacle in the IPM.
(2) Align the rear blower motor relay terminals
with the terminal cavities in the IPM receptacle.
(3) Push down firmly on the rear blower motor
relay until the terminals are fully seated in the ter-
minal cavities.
(4) Install the cover onto the IPM.
(5) Reconnect the negative battery cable.
BLOWER MOTOR RESISTOR
BLOCK
DESCRIPTION
A rear blower motor resistor is used on this model
when it is equipped with the manual heater-A/C sys-
tem. Models equipped with the optional Automatic
Temperature Control (ATC) system use a rear blower
motor power module, instead of the blower motor
resistor block (Refer to 24 - HEATING & AIR CON-
DITIONING/CONTROLS/POWER MODULE -
DESCRIPTION). The rear blower motor resistor
block is mounted to the rear HVAC housing, directly
above the expansion valve. The resistor block con-
sists of a molded plastic mounting plate with an inte-
gral connector receptacle. Concealed behind the
mounting plate is an electrical circuit board with two
resistors and a thermal fuse. The rear blower motor
resistor block is accessed for service by removing the
right quarter and D-pillar trim panels.
OPERATION
The rear blower motor resistor block is connected
to the vehicle electrical system through a dedicated
take out and connector of the rear HVAC wire har-
ness. The blower motor resistor has an electrical cir-
cuit board with two resistors, each of which will
reduce the current flow through the blower motor to
change the blower motor speed. The blower motor
switch in the manual heater-A/C system directs the
ground path for the rear blower motor through the
correct resistor to obtain the selected speed.
Fig. 5 Rear Blower Motor Relay
1 - INTEGRATED POWER MODULE (IPM)
2 - REAR BLOWER MOTOR RELAY
3 - FRONT CONTROL MODULE (FCM)
RSCONTROLS - REAR24-37
BLOWER MOTOR RELAY (Continued)
Page 2189 of 2339
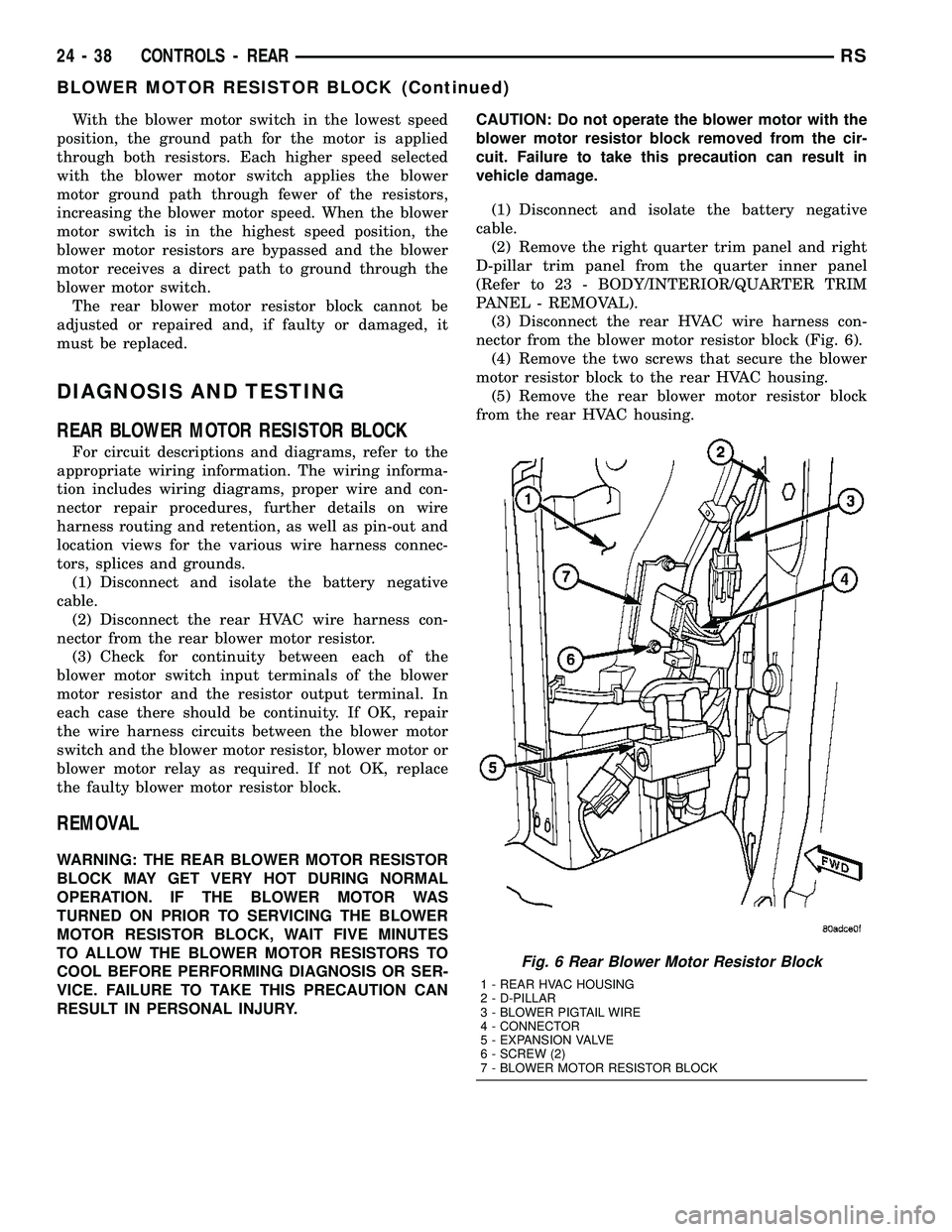
With the blower motor switch in the lowest speed
position, the ground path for the motor is applied
through both resistors. Each higher speed selected
with the blower motor switch applies the blower
motor ground path through fewer of the resistors,
increasing the blower motor speed. When the blower
motor switch is in the highest speed position, the
blower motor resistors are bypassed and the blower
motor receives a direct path to ground through the
blower motor switch.
The rear blower motor resistor block cannot be
adjusted or repaired and, if faulty or damaged, it
must be replaced.
DIAGNOSIS AND TESTING
REAR BLOWER MOTOR RESISTOR BLOCK
For circuit descriptions and diagrams, refer to the
appropriate wiring information. The wiring informa-
tion includes wiring diagrams, proper wire and con-
nector repair procedures, further details on wire
harness routing and retention, as well as pin-out and
location views for the various wire harness connec-
tors, splices and grounds.
(1) Disconnect and isolate the battery negative
cable.
(2) Disconnect the rear HVAC wire harness con-
nector from the rear blower motor resistor.
(3) Check for continuity between each of the
blower motor switch input terminals of the blower
motor resistor and the resistor output terminal. In
each case there should be continuity. If OK, repair
the wire harness circuits between the blower motor
switch and the blower motor resistor, blower motor or
blower motor relay as required. If not OK, replace
the faulty blower motor resistor block.
REMOVAL
WARNING: THE REAR BLOWER MOTOR RESISTOR
BLOCK MAY GET VERY HOT DURING NORMAL
OPERATION. IF THE BLOWER MOTOR WAS
TURNED ON PRIOR TO SERVICING THE BLOWER
MOTOR RESISTOR BLOCK, WAIT FIVE MINUTES
TO ALLOW THE BLOWER MOTOR RESISTORS TO
COOL BEFORE PERFORMING DIAGNOSIS OR SER-
VICE. FAILURE TO TAKE THIS PRECAUTION CAN
RESULT IN PERSONAL INJURY.CAUTION: Do not operate the blower motor with the
blower motor resistor block removed from the cir-
cuit. Failure to take this precaution can result in
vehicle damage.
(1) Disconnect and isolate the battery negative
cable.
(2) Remove the right quarter trim panel and right
D-pillar trim panel from the quarter inner panel
(Refer to 23 - BODY/INTERIOR/QUARTER TRIM
PANEL - REMOVAL).
(3) Disconnect the rear HVAC wire harness con-
nector from the blower motor resistor block (Fig. 6).
(4) Remove the two screws that secure the blower
motor resistor block to the rear HVAC housing.
(5) Remove the rear blower motor resistor block
from the rear HVAC housing.
Fig. 6 Rear Blower Motor Resistor Block
1 - REAR HVAC HOUSING
2 - D-PILLAR
3 - BLOWER PIGTAIL WIRE
4 - CONNECTOR
5 - EXPANSION VALVE
6 - SCREW (2)
7 - BLOWER MOTOR RESISTOR BLOCK
24 - 38 CONTROLS - REARRS
BLOWER MOTOR RESISTOR BLOCK (Continued)
Page 2192 of 2339
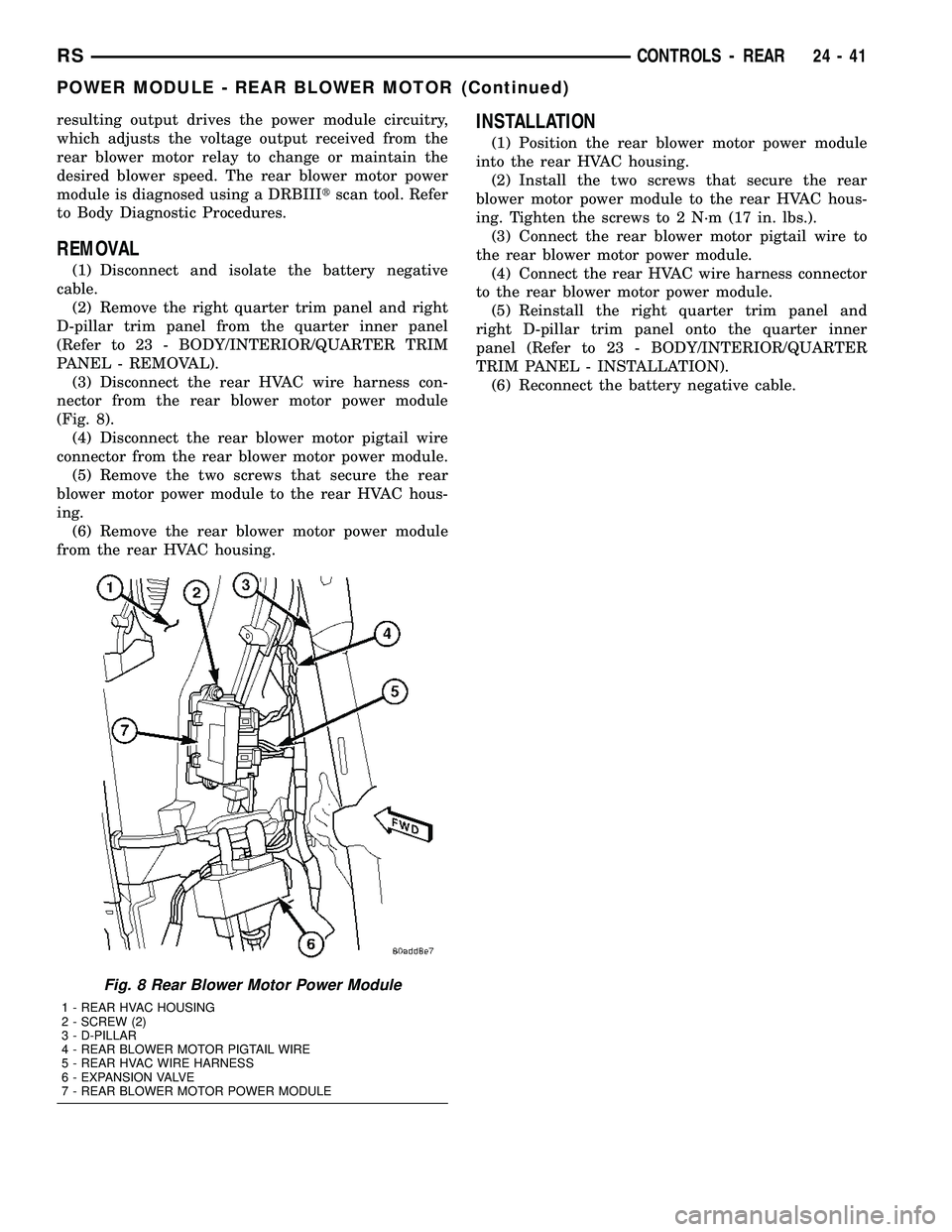
resulting output drives the power module circuitry,
which adjusts the voltage output received from the
rear blower motor relay to change or maintain the
desired blower speed. The rear blower motor power
module is diagnosed using a DRBIIItscan tool. Refer
to Body Diagnostic Procedures.
REMOVAL
(1) Disconnect and isolate the battery negative
cable.
(2) Remove the right quarter trim panel and right
D-pillar trim panel from the quarter inner panel
(Refer to 23 - BODY/INTERIOR/QUARTER TRIM
PANEL - REMOVAL).
(3) Disconnect the rear HVAC wire harness con-
nector from the rear blower motor power module
(Fig. 8).
(4) Disconnect the rear blower motor pigtail wire
connector from the rear blower motor power module.
(5) Remove the two screws that secure the rear
blower motor power module to the rear HVAC hous-
ing.
(6) Remove the rear blower motor power module
from the rear HVAC housing.
INSTALLATION
(1) Position the rear blower motor power module
into the rear HVAC housing.
(2) Install the two screws that secure the rear
blower motor power module to the rear HVAC hous-
ing. Tighten the screws to 2 N´m (17 in. lbs.).
(3) Connect the rear blower motor pigtail wire to
the rear blower motor power module.
(4) Connect the rear HVAC wire harness connector
to the rear blower motor power module.
(5) Reinstall the right quarter trim panel and
right D-pillar trim panel onto the quarter inner
panel (Refer to 23 - BODY/INTERIOR/QUARTER
TRIM PANEL - INSTALLATION).
(6) Reconnect the battery negative cable.
Fig. 8 Rear Blower Motor Power Module
1 - REAR HVAC HOUSING
2 - SCREW (2)
3 - D-PILLAR
4 - REAR BLOWER MOTOR PIGTAIL WIRE
5 - REAR HVAC WIRE HARNESS
6 - EXPANSION VALVE
7 - REAR BLOWER MOTOR POWER MODULE
RSCONTROLS - REAR24-41
POWER MODULE - REAR BLOWER MOTOR (Continued)
Page 2197 of 2339
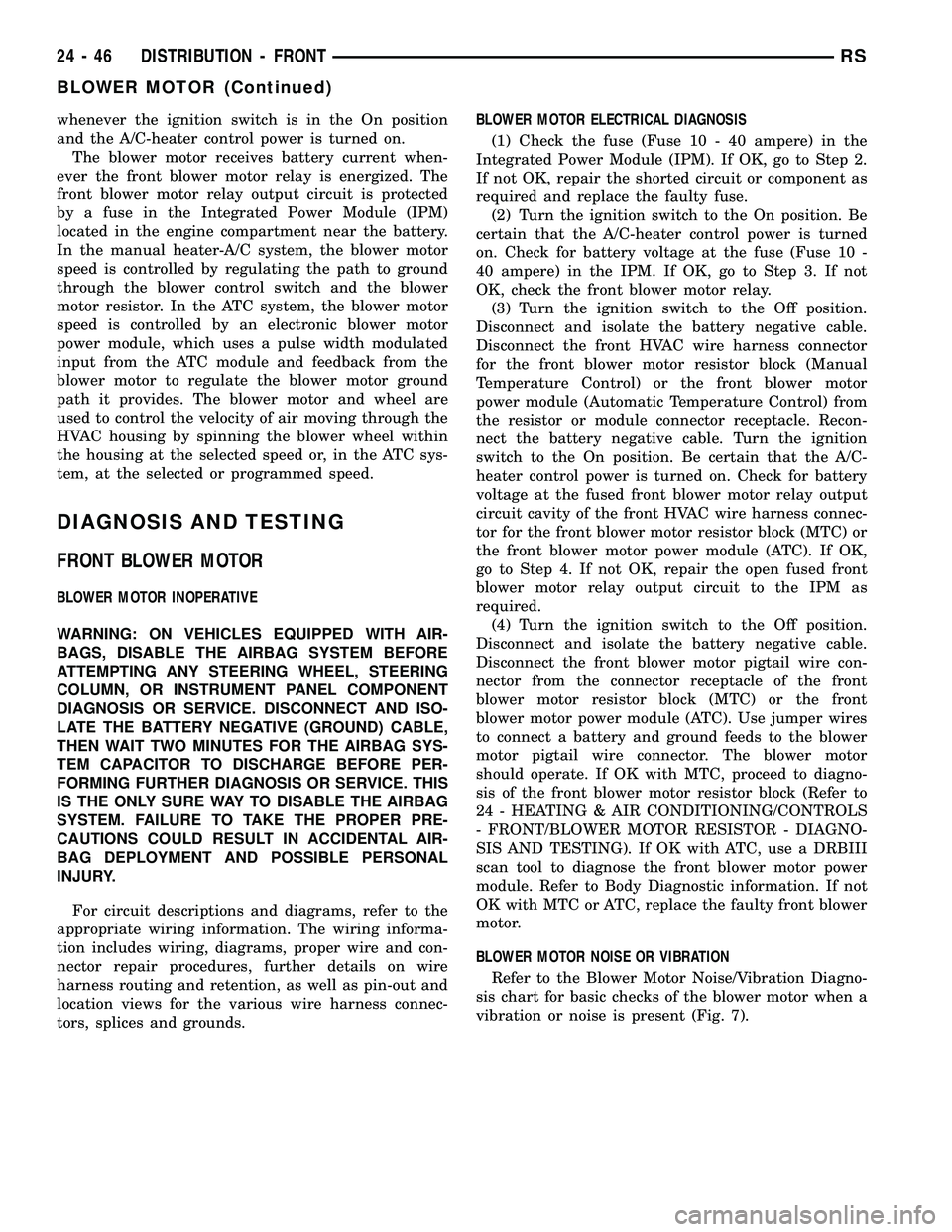
whenever the ignition switch is in the On position
and the A/C-heater control power is turned on.
The blower motor receives battery current when-
ever the front blower motor relay is energized. The
front blower motor relay output circuit is protected
by a fuse in the Integrated Power Module (IPM)
located in the engine compartment near the battery.
In the manual heater-A/C system, the blower motor
speed is controlled by regulating the path to ground
through the blower control switch and the blower
motor resistor. In the ATC system, the blower motor
speed is controlled by an electronic blower motor
power module, which uses a pulse width modulated
input from the ATC module and feedback from the
blower motor to regulate the blower motor ground
path it provides. The blower motor and wheel are
used to control the velocity of air moving through the
HVAC housing by spinning the blower wheel within
the housing at the selected speed or, in the ATC sys-
tem, at the selected or programmed speed.
DIAGNOSIS AND TESTING
FRONT BLOWER MOTOR
BLOWER MOTOR INOPERATIVE
WARNING: ON VEHICLES EQUIPPED WITH AIR-
BAGS, DISABLE THE AIRBAG SYSTEM BEFORE
ATTEMPTING ANY STEERING WHEEL, STEERING
COLUMN, OR INSTRUMENT PANEL COMPONENT
DIAGNOSIS OR SERVICE. DISCONNECT AND ISO-
LATE THE BATTERY NEGATIVE (GROUND) CABLE,
THEN WAIT TWO MINUTES FOR THE AIRBAG SYS-
TEM CAPACITOR TO DISCHARGE BEFORE PER-
FORMING FURTHER DIAGNOSIS OR SERVICE. THIS
IS THE ONLY SURE WAY TO DISABLE THE AIRBAG
SYSTEM. FAILURE TO TAKE THE PROPER PRE-
CAUTIONS COULD RESULT IN ACCIDENTAL AIR-
BAG DEPLOYMENT AND POSSIBLE PERSONAL
INJURY.
For circuit descriptions and diagrams, refer to the
appropriate wiring information. The wiring informa-
tion includes wiring, diagrams, proper wire and con-
nector repair procedures, further details on wire
harness routing and retention, as well as pin-out and
location views for the various wire harness connec-
tors, splices and grounds.BLOWER MOTOR ELECTRICAL DIAGNOSIS
(1) Check the fuse (Fuse 10 - 40 ampere) in the
Integrated Power Module (IPM). If OK, go to Step 2.
If not OK, repair the shorted circuit or component as
required and replace the faulty fuse.
(2) Turn the ignition switch to the On position. Be
certain that the A/C-heater control power is turned
on. Check for battery voltage at the fuse (Fuse 10 -
40 ampere) in the IPM. If OK, go to Step 3. If not
OK, check the front blower motor relay.
(3) Turn the ignition switch to the Off position.
Disconnect and isolate the battery negative cable.
Disconnect the front HVAC wire harness connector
for the front blower motor resistor block (Manual
Temperature Control) or the front blower motor
power module (Automatic Temperature Control) from
the resistor or module connector receptacle. Recon-
nect the battery negative cable. Turn the ignition
switch to the On position. Be certain that the A/C-
heater control power is turned on. Check for battery
voltage at the fused front blower motor relay output
circuit cavity of the front HVAC wire harness connec-
tor for the front blower motor resistor block (MTC) or
the front blower motor power module (ATC). If OK,
go to Step 4. If not OK, repair the open fused front
blower motor relay output circuit to the IPM as
required.
(4) Turn the ignition switch to the Off position.
Disconnect and isolate the battery negative cable.
Disconnect the front blower motor pigtail wire con-
nector from the connector receptacle of the front
blower motor resistor block (MTC) or the front
blower motor power module (ATC). Use jumper wires
to connect a battery and ground feeds to the blower
motor pigtail wire connector. The blower motor
should operate. If OK with MTC, proceed to diagno-
sis of the front blower motor resistor block (Refer to
24 - HEATING & AIR CONDITIONING/CONTROLS
- FRONT/BLOWER MOTOR RESISTOR - DIAGNO-
SIS AND TESTING). If OK with ATC, use a DRBIII
scan tool to diagnose the front blower motor power
module. Refer to Body Diagnostic information. If not
OK with MTC or ATC, replace the faulty front blower
motor.
BLOWER MOTOR NOISE OR VIBRATION
Refer to the Blower Motor Noise/Vibration Diagno-
sis chart for basic checks of the blower motor when a
vibration or noise is present (Fig. 7).
24 - 46 DISTRIBUTION - FRONTRS
BLOWER MOTOR (Continued)
Page 2208 of 2339
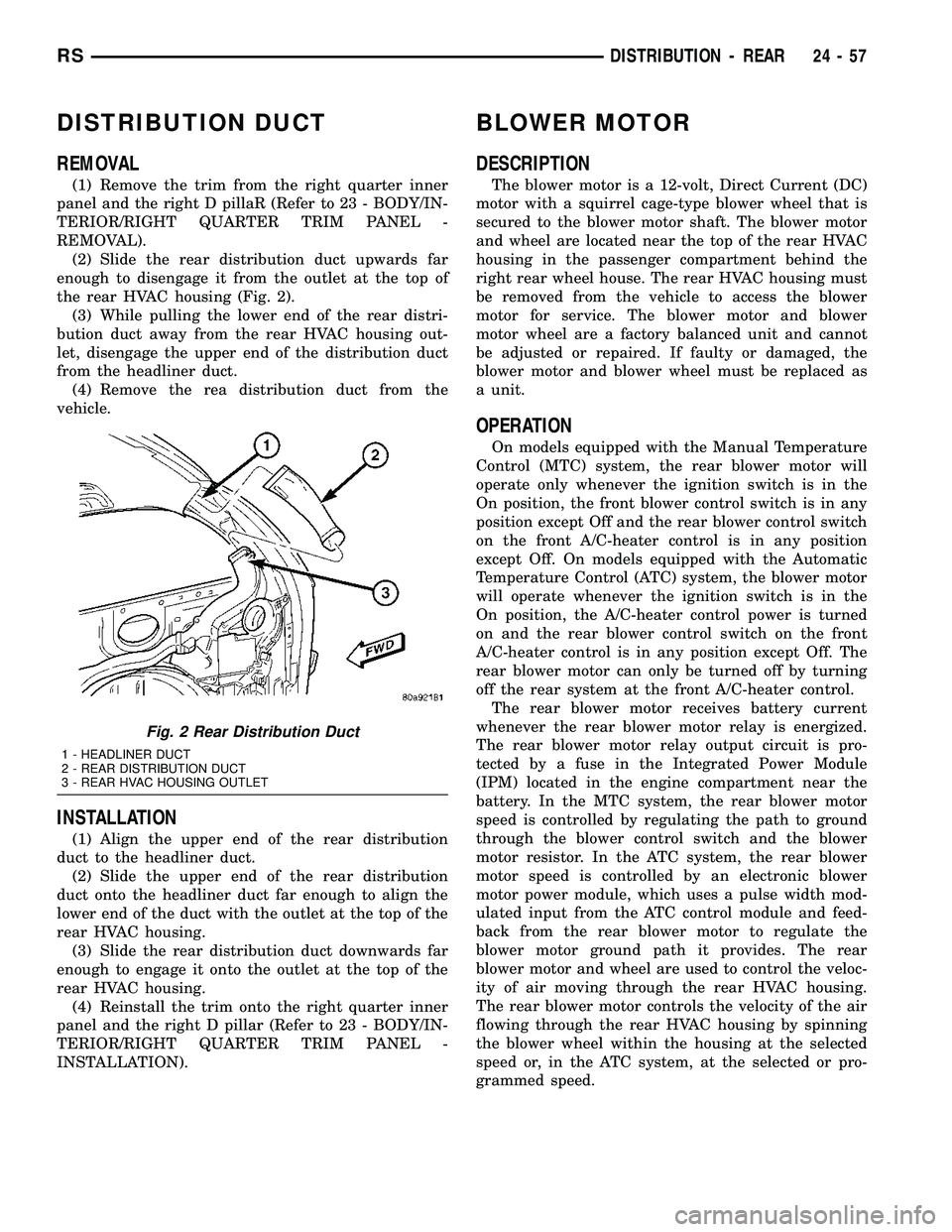
DISTRIBUTION DUCT
REMOVAL
(1) Remove the trim from the right quarter inner
panel and the right D pillaR (Refer to 23 - BODY/IN-
TERIOR/RIGHT QUARTER TRIM PANEL -
REMOVAL).
(2) Slide the rear distribution duct upwards far
enough to disengage it from the outlet at the top of
the rear HVAC housing (Fig. 2).
(3) While pulling the lower end of the rear distri-
bution duct away from the rear HVAC housing out-
let, disengage the upper end of the distribution duct
from the headliner duct.
(4) Remove the rea distribution duct from the
vehicle.
INSTALLATION
(1) Align the upper end of the rear distribution
duct to the headliner duct.
(2) Slide the upper end of the rear distribution
duct onto the headliner duct far enough to align the
lower end of the duct with the outlet at the top of the
rear HVAC housing.
(3) Slide the rear distribution duct downwards far
enough to engage it onto the outlet at the top of the
rear HVAC housing.
(4) Reinstall the trim onto the right quarter inner
panel and the right D pillar (Refer to 23 - BODY/IN-
TERIOR/RIGHT QUARTER TRIM PANEL -
INSTALLATION).
BLOWER MOTOR
DESCRIPTION
The blower motor is a 12-volt, Direct Current (DC)
motor with a squirrel cage-type blower wheel that is
secured to the blower motor shaft. The blower motor
and wheel are located near the top of the rear HVAC
housing in the passenger compartment behind the
right rear wheel house. The rear HVAC housing must
be removed from the vehicle to access the blower
motor for service. The blower motor and blower
motor wheel are a factory balanced unit and cannot
be adjusted or repaired. If faulty or damaged, the
blower motor and blower wheel must be replaced as
a unit.
OPERATION
On models equipped with the Manual Temperature
Control (MTC) system, the rear blower motor will
operate only whenever the ignition switch is in the
On position, the front blower control switch is in any
position except Off and the rear blower control switch
on the front A/C-heater control is in any position
except Off. On models equipped with the Automatic
Temperature Control (ATC) system, the blower motor
will operate whenever the ignition switch is in the
On position, the A/C-heater control power is turned
on and the rear blower control switch on the front
A/C-heater control is in any position except Off. The
rear blower motor can only be turned off by turning
off the rear system at the front A/C-heater control.
The rear blower motor receives battery current
whenever the rear blower motor relay is energized.
The rear blower motor relay output circuit is pro-
tected by a fuse in the Integrated Power Module
(IPM) located in the engine compartment near the
battery. In the MTC system, the rear blower motor
speed is controlled by regulating the path to ground
through the blower control switch and the blower
motor resistor. In the ATC system, the rear blower
motor speed is controlled by an electronic blower
motor power module, which uses a pulse width mod-
ulated input from the ATC control module and feed-
back from the rear blower motor to regulate the
blower motor ground path it provides. The rear
blower motor and wheel are used to control the veloc-
ity of air moving through the rear HVAC housing.
The rear blower motor controls the velocity of the air
flowing through the rear HVAC housing by spinning
the blower wheel within the housing at the selected
speed or, in the ATC system, at the selected or pro-
grammed speed.
Fig. 2 Rear Distribution Duct
1 - HEADLINER DUCT
2 - REAR DISTRIBUTION DUCT
3 - REAR HVAC HOUSING OUTLET
RSDISTRIBUTION - REAR24-57
Page 2209 of 2339
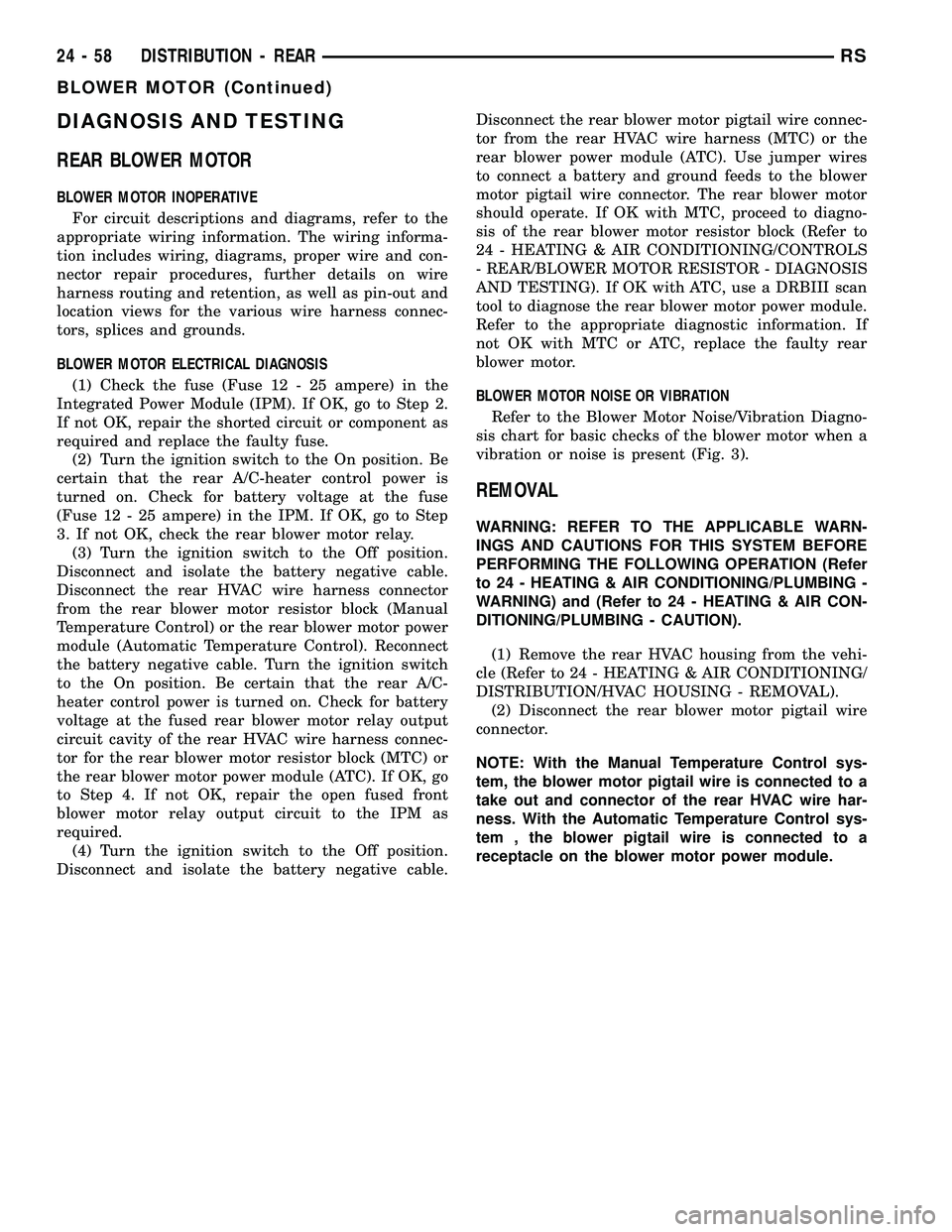
DIAGNOSIS AND TESTING
REAR BLOWER MOTOR
BLOWER MOTOR INOPERATIVE
For circuit descriptions and diagrams, refer to the
appropriate wiring information. The wiring informa-
tion includes wiring, diagrams, proper wire and con-
nector repair procedures, further details on wire
harness routing and retention, as well as pin-out and
location views for the various wire harness connec-
tors, splices and grounds.
BLOWER MOTOR ELECTRICAL DIAGNOSIS
(1) Check the fuse (Fuse 12 - 25 ampere) in the
Integrated Power Module (IPM). If OK, go to Step 2.
If not OK, repair the shorted circuit or component as
required and replace the faulty fuse.
(2) Turn the ignition switch to the On position. Be
certain that the rear A/C-heater control power is
turned on. Check for battery voltage at the fuse
(Fuse 12 - 25 ampere) in the IPM. If OK, go to Step
3. If not OK, check the rear blower motor relay.
(3) Turn the ignition switch to the Off position.
Disconnect and isolate the battery negative cable.
Disconnect the rear HVAC wire harness connector
from the rear blower motor resistor block (Manual
Temperature Control) or the rear blower motor power
module (Automatic Temperature Control). Reconnect
the battery negative cable. Turn the ignition switch
to the On position. Be certain that the rear A/C-
heater control power is turned on. Check for battery
voltage at the fused rear blower motor relay output
circuit cavity of the rear HVAC wire harness connec-
tor for the rear blower motor resistor block (MTC) or
the rear blower motor power module (ATC). If OK, go
to Step 4. If not OK, repair the open fused front
blower motor relay output circuit to the IPM as
required.
(4) Turn the ignition switch to the Off position.
Disconnect and isolate the battery negative cable.Disconnect the rear blower motor pigtail wire connec-
tor from the rear HVAC wire harness (MTC) or the
rear blower power module (ATC). Use jumper wires
to connect a battery and ground feeds to the blower
motor pigtail wire connector. The rear blower motor
should operate. If OK with MTC, proceed to diagno-
sis of the rear blower motor resistor block (Refer to
24 - HEATING & AIR CONDITIONING/CONTROLS
- REAR/BLOWER MOTOR RESISTOR - DIAGNOSIS
AND TESTING). If OK with ATC, use a DRBIII scan
tool to diagnose the rear blower motor power module.
Refer to the appropriate diagnostic information. If
not OK with MTC or ATC, replace the faulty rear
blower motor.
BLOWER MOTOR NOISE OR VIBRATION
Refer to the Blower Motor Noise/Vibration Diagno-
sis chart for basic checks of the blower motor when a
vibration or noise is present (Fig. 3).
REMOVAL
WARNING: REFER TO THE APPLICABLE WARN-
INGS AND CAUTIONS FOR THIS SYSTEM BEFORE
PERFORMING THE FOLLOWING OPERATION (Refer
to 24 - HEATING & AIR CONDITIONING/PLUMBING -
WARNING) and (Refer to 24 - HEATING & AIR CON-
DITIONING/PLUMBING - CAUTION).
(1) Remove the rear HVAC housing from the vehi-
cle (Refer to 24 - HEATING & AIR CONDITIONING/
DISTRIBUTION/HVAC HOUSING - REMOVAL).
(2) Disconnect the rear blower motor pigtail wire
connector.
NOTE: With the Manual Temperature Control sys-
tem, the blower motor pigtail wire is connected to a
take out and connector of the rear HVAC wire har-
ness. With the Automatic Temperature Control sys-
tem , the blower pigtail wire is connected to a
receptacle on the blower motor power module.
24 - 58 DISTRIBUTION - REARRS
BLOWER MOTOR (Continued)
Page 2277 of 2339
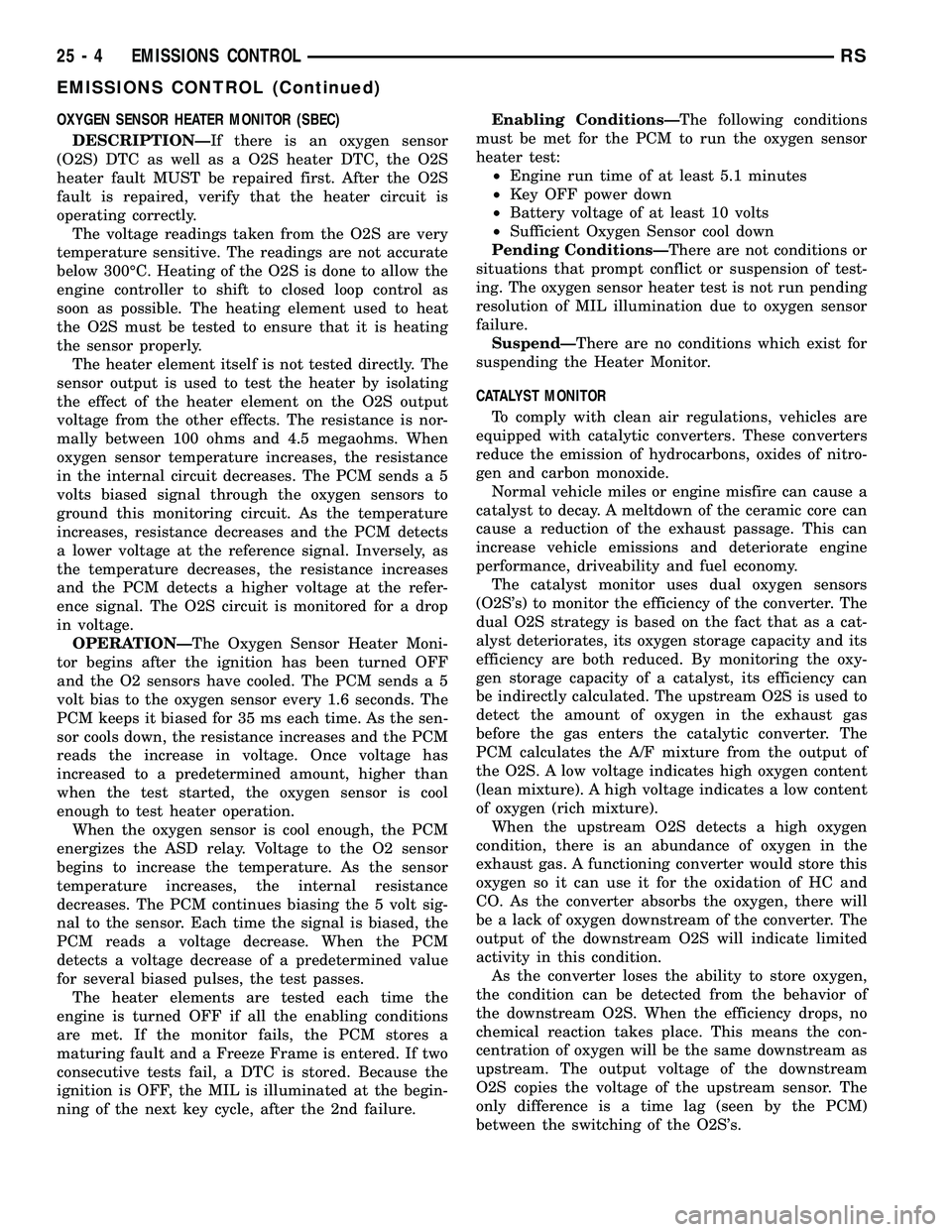
OXYGEN SENSOR HEATER MONITOR (SBEC)
DESCRIPTIONÐIf there is an oxygen sensor
(O2S) DTC as well as a O2S heater DTC, the O2S
heater fault MUST be repaired first. After the O2S
fault is repaired, verify that the heater circuit is
operating correctly.
The voltage readings taken from the O2S are very
temperature sensitive. The readings are not accurate
below 300ÉC. Heating of the O2S is done to allow the
engine controller to shift to closed loop control as
soon as possible. The heating element used to heat
the O2S must be tested to ensure that it is heating
the sensor properly.
The heater element itself is not tested directly. The
sensor output is used to test the heater by isolating
the effect of the heater element on the O2S output
voltage from the other effects. The resistance is nor-
mally between 100 ohms and 4.5 megaohms. When
oxygen sensor temperature increases, the resistance
in the internal circuit decreases. The PCM sends a 5
volts biased signal through the oxygen sensors to
ground this monitoring circuit. As the temperature
increases, resistance decreases and the PCM detects
a lower voltage at the reference signal. Inversely, as
the temperature decreases, the resistance increases
and the PCM detects a higher voltage at the refer-
ence signal. The O2S circuit is monitored for a drop
in voltage.
OPERATIONÐThe Oxygen Sensor Heater Moni-
tor begins after the ignition has been turned OFF
and the O2 sensors have cooled. The PCM sends a 5
volt bias to the oxygen sensor every 1.6 seconds. The
PCM keeps it biased for 35 ms each time. As the sen-
sor cools down, the resistance increases and the PCM
reads the increase in voltage. Once voltage has
increased to a predetermined amount, higher than
when the test started, the oxygen sensor is cool
enough to test heater operation.
When the oxygen sensor is cool enough, the PCM
energizes the ASD relay. Voltage to the O2 sensor
begins to increase the temperature. As the sensor
temperature increases, the internal resistance
decreases. The PCM continues biasing the 5 volt sig-
nal to the sensor. Each time the signal is biased, the
PCM reads a voltage decrease. When the PCM
detects a voltage decrease of a predetermined value
for several biased pulses, the test passes.
The heater elements are tested each time the
engine is turned OFF if all the enabling conditions
are met. If the monitor fails, the PCM stores a
maturing fault and a Freeze Frame is entered. If two
consecutive tests fail, a DTC is stored. Because the
ignition is OFF, the MIL is illuminated at the begin-
ning of the next key cycle, after the 2nd failure.Enabling ConditionsÐThe following conditions
must be met for the PCM to run the oxygen sensor
heater test:
²Engine run time of at least 5.1 minutes
²Key OFF power down
²Battery voltage of at least 10 volts
²Sufficient Oxygen Sensor cool down
Pending ConditionsÐThere are not conditions or
situations that prompt conflict or suspension of test-
ing. The oxygen sensor heater test is not run pending
resolution of MIL illumination due to oxygen sensor
failure.
SuspendÐThere are no conditions which exist for
suspending the Heater Monitor.
CATALYST MONITOR
To comply with clean air regulations, vehicles are
equipped with catalytic converters. These converters
reduce the emission of hydrocarbons, oxides of nitro-
gen and carbon monoxide.
Normal vehicle miles or engine misfire can cause a
catalyst to decay. A meltdown of the ceramic core can
cause a reduction of the exhaust passage. This can
increase vehicle emissions and deteriorate engine
performance, driveability and fuel economy.
The catalyst monitor uses dual oxygen sensors
(O2S's) to monitor the efficiency of the converter. The
dual O2S strategy is based on the fact that as a cat-
alyst deteriorates, its oxygen storage capacity and its
efficiency are both reduced. By monitoring the oxy-
gen storage capacity of a catalyst, its efficiency can
be indirectly calculated. The upstream O2S is used to
detect the amount of oxygen in the exhaust gas
before the gas enters the catalytic converter. The
PCM calculates the A/F mixture from the output of
the O2S. A low voltage indicates high oxygen content
(lean mixture). A high voltage indicates a low content
of oxygen (rich mixture).
When the upstream O2S detects a high oxygen
condition, there is an abundance of oxygen in the
exhaust gas. A functioning converter would store this
oxygen so it can use it for the oxidation of HC and
CO. As the converter absorbs the oxygen, there will
be a lack of oxygen downstream of the converter. The
output of the downstream O2S will indicate limited
activity in this condition.
As the converter loses the ability to store oxygen,
the condition can be detected from the behavior of
the downstream O2S. When the efficiency drops, no
chemical reaction takes place. This means the con-
centration of oxygen will be the same downstream as
upstream. The output voltage of the downstream
O2S copies the voltage of the upstream sensor. The
only difference is a time lag (seen by the PCM)
between the switching of the O2S's.
25 - 4 EMISSIONS CONTROLRS
EMISSIONS CONTROL (Continued)
Page 2302 of 2339
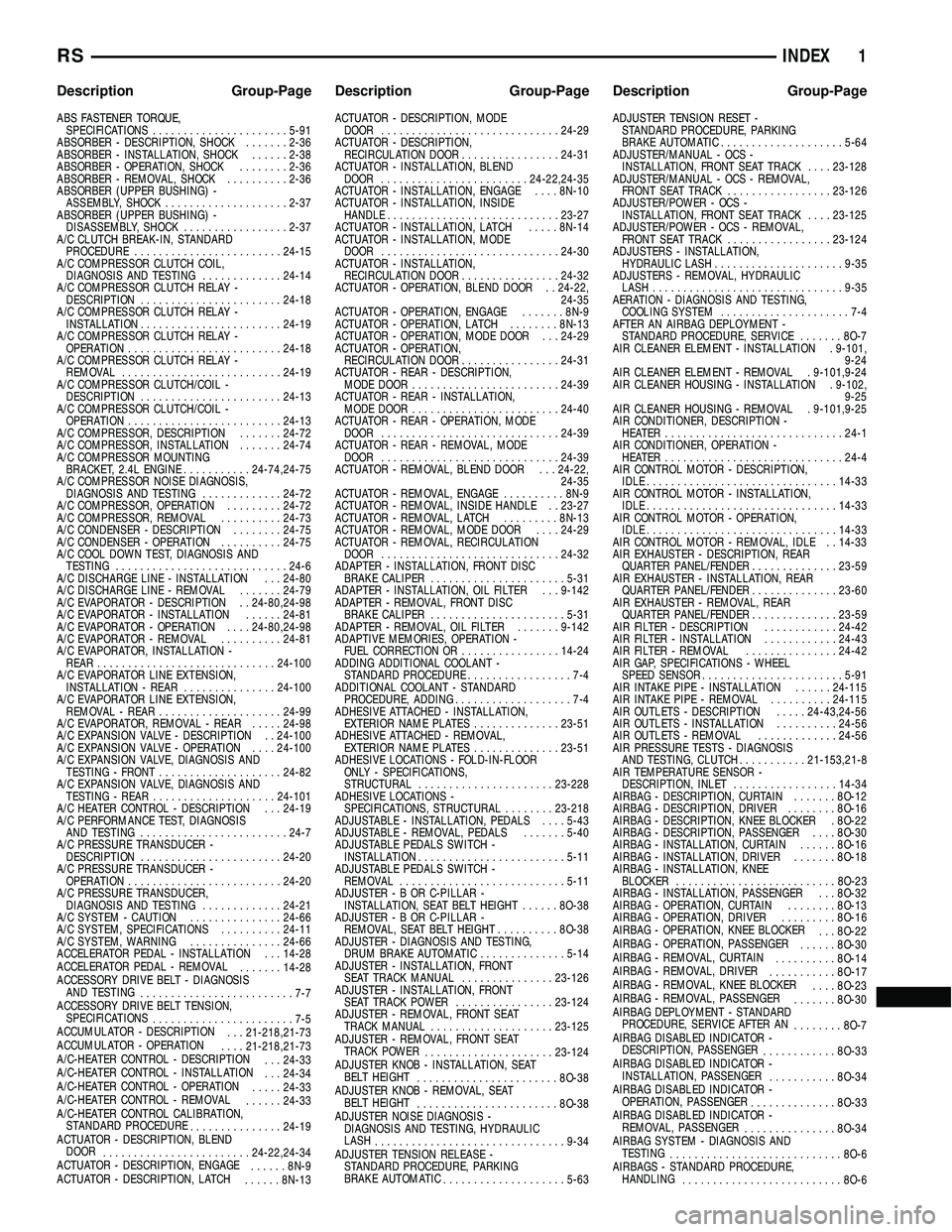
INDEX
ABS FASTENER TORQUE,SPECIFICATIONS ...................... 5-91
ABSORBER - DESCRIPTION, SHOCK .......2-36
ABSORBER - INSTALLATION, SHOCK ......2-38
ABSORBER - OPERATION, SHOCK ........2-36
ABSORBER - REMOVAL, SHOCK ..........2-36
ABSORBER (UPPER BUSHING) - ASSEMBLY, SHOCK .................... 2-37
ABSORBER (UPPER BUSHING) - DISASSEMBLY, SHOCK .................2-37
A/C CLUTCH BREAK-IN, STANDARD PROCEDURE ........................ 24-15
A/C COMPRESSOR CLUTCH COIL, DIAGNOSIS AND TESTING .............24-14
A/C COMPRESSOR CLUTCH RELAY - DESCRIPTION ....................... 24-18
A/C COMPRESSOR CLUTCH RELAY - INSTALLATION ....................... 24-19
A/C COMPRESSOR CLUTCH RELAY - OPERATION ......................... 24-18
A/C COMPRESSOR CLUTCH RELAY - REMOVAL .......................... 24-19
A/C COMPRESSOR CLUTCH/COIL - DESCRIPTION ....................... 24-13
A/C COMPRESSOR CLUTCH/COIL - OPERATION ......................... 24-13
A/C COMPRESSOR, DESCRIPTION .......24-72
A/C COMPRESSOR, INSTALLATION .......24-74
A/C COMPRESSOR MOUNTING BRACKET, 2.4L ENGINE ...........24-74,24-75
A/C COMPRESSOR NOISE DIAGNOSIS, DIAGNOSIS AND TESTING .............24-72
A/C COMPRESSOR, OPERATION .........24-72
A/C COMPRESSOR, REMOVAL ..........24-73
A/C CONDENSER - DESCRIPTION ........24-75
A/C CONDENSER - OPERATION ..........24-75
A/C COOL DOWN TEST, DIAGNOSIS AND TESTING ............................ 24-6
A/C DISCHARGE LINE - INSTALLATION . . . 24-80
A/C DISCHARGE LINE - REMOVAL .......24-79
A/C EVAPORATOR - DESCRIPTION . . 24-80,24-98
A/C EVAPORATOR - INSTALLATION ......24-81
A/C EVAPORATOR - OPERATION ....24-80,24-98
A/C EVAPORATOR - REMOVAL ..........24-81
A/C EVAPORATOR, INSTALLATION - REAR ............................. 24-100
A/C EVAPORATOR LINE EXTENSION, INSTALLATION - REAR ...............24-100
A/C EVAPORATOR LINE EXTENSION, REMOVAL - REAR .................... 24-99
A/C EVAPORATOR, REMOVAL - REAR .....24-98
A/C EXPANSION VALVE - DESCRIPTION . . 24-100
A/C EXPANSION VALVE - OPERATION ....24-100
A/C EXPANSION VALVE, DIAGNOSIS AND TESTING - FRONT .................... 24-82
A/C EXPANSION VALVE, DIAGNOSIS AND TESTING - REAR .................... 24-101
A/C HEATER CONTROL - DESCRIPTION . . . 24-19
A/C PERFORMANCE TEST, DIAGNOSIS AND TESTING ........................ 24-7
A/C PRESSURE TRANSDUCER - DESCRIPTION ....................... 24-20
A/C PRESSURE TRANSDUCER - OPERATION ......................... 24-20
A/C PRESSURE TRANSDUCER, DIAGNOSIS AND TESTING .............24-21
A/C SYSTEM - CAUTION ...............24-66
A/C SYSTEM, SPECIFICATIONS ..........24-11
A/C SYSTEM, WARNING ...............24-66
ACCELERATOR PEDAL - INSTALLATION . . . 14-28
ACCELERATOR PEDAL - REMOVAL .......14-28
ACCESSORY DRIVE BELT - DIAGNOSIS AND TESTING .........................7-7
ACCESSORY DRIVE BELT TENSION, SPECIFICATIONS .......................7-5
ACCUMULATOR - DESCRIPTION . . . 21-218,21-73
ACCUMULATOR - OPERATION ....21-218,21-73
A/C-HEATER CONTROL - DESCRIPTION . . . 24-33
A/C-HEATER CONTROL - INSTALLATION . . . 24-34
A/C-HEATER CONTROL - OPERATION .....24-33
A/C-HEATER CONTROL - REMOVAL ......24-33
A/C-HEATER CONTROL CALIBRATION, STANDARD PROCEDURE ...............24-19
ACTUATOR - DESCRIPTION, BLEND DOOR ........................ 24-22,24-34
ACTUATOR - DESCRIPTION, ENGAGE ......8N-9
ACTUATOR - DESCRIPTION, LATCH ......8N-13 ACTUATOR - DESCRIPTION, MODE
DOOR ............................. 24-29
ACTUATOR - DESCRIPTION, RECIRCULATION DOOR ................24-31
ACTUATOR - INSTALLATION, BLEND DOOR ........................ 24-22,24-35
ACTUATOR - INSTALLATION, ENGAGE ....8N-10
ACTUATOR - INSTALLATION, INSIDE HANDLE ............................ 23-27
ACTUATOR - INSTALLATION, LATCH .....8N-14
ACTUATOR - INSTALLATION, MODE DOOR ............................. 24-30
ACTUATOR - INSTALLATION, RECIRCULATION DOOR ................24-32
ACTUATOR - OPERATION, BLEND DOOR . . 24-22, 24-35
ACTUATOR - OPERATION, ENGAGE .......8N-9
ACTUATOR - OPERATION, LATCH ........8N-13
ACTUATOR - OPERATION, MODE DOOR . . . 24-29
ACTUATOR - OPERATION, RECIRCULATION DOOR ................24-31
ACTUATOR - REAR - DESCRIPTION, MODE DOOR ........................ 24-39
ACTUATOR - REAR - INSTALLATION, MODE DOOR ........................ 24-40
ACTUATOR - REAR - OPERATION, MODE DOOR ............................. 24-39
ACTUATOR - REAR - REMOVAL, MODE DOOR ............................. 24-39
ACTUATOR - REMOVAL, BLEND DOOR . . . 24-22, 24-35
ACTUATOR - REMOVAL, ENGAGE ..........8N-9
ACTUATOR - REMOVAL, INSIDE HANDLE . . 23-27
ACTUATOR - REMOVAL, LATCH .........8N-13
ACTUATOR - REMOVAL, MODE DOOR ....24-29
ACTUATOR - REMOVAL, RECIRCULATION DOOR ............................. 24-32
ADAPTER - INSTALLATION, FRONT DISC BRAKE CALIPER ...................... 5-31
ADAPTER - INSTALLATION, OIL FILTER . . . 9-142
ADAPTER - REMOVAL, FRONT DISC BRAKE CALIPER ...................... 5-31
ADAPTER - REMOVAL, OIL FILTER .......9-142
ADAPTIVE MEMORIES, OPERATION - FUEL CORRECTION OR ................14-24
ADDING ADDITIONAL COOLANT - STANDARD PROCEDURE .................7-4
ADDITIONAL COOLANT - STANDARD PROCEDURE, ADDING ...................7-4
ADHESIVE ATTACHED - INSTALLATION, EXTERIOR NAME PLATES ..............23-51
ADHESIVE ATTACHED - REMOVAL, EXTERIOR NAME PLATES ..............23-51
ADHESIVE LOCATIONS - FOLD-IN-FLOOR ONLY - SPECIFICATIONS,
STRUCTURAL ...................... 23-228
ADHESIVE LOCATIONS - SPECIFICATIONS, STRUCTURAL ........23-218
ADJUSTABLE - INSTALLATION, PEDALS ....5-43
ADJUSTABLE - REMOVAL, PEDALS .......5-40
ADJUSTABLE PEDALS SWITCH - INSTALLATION ........................ 5-11
ADJUSTABLE PEDALS SWITCH - REMOVAL ........................... 5-11
ADJUSTE R-BOR C-PILLAR -
INSTALLATION, SEAT BELT HEIGHT ......8O-38
ADJUSTE R-BOR C-PILLAR -
REMOVAL, SEAT BELT HEIGHT ..........8O-38
ADJUSTER - DIAGNOSIS AND TESTING, DRUM BRAKE AUTOMATIC ..............5-14
ADJUSTER - INSTALLATION, FRONT SEAT TRACK MANUAL ...............23-126
ADJUSTER - INSTALLATION, FRONT SEAT TRACK POWER ................23-124
ADJUSTER - REMOVAL, FRONT SEAT TRACK MANUAL .................... 23-125
ADJUSTER - REMOVAL, FRONT SEAT TRACK POWER ..................... 23-124
ADJUSTER KNOB - INSTALLATION, SEAT BELT HEIGHT ....................... 8O-38
ADJUSTER KNOB - REMOVAL, SEAT BELT HEIGHT ....................... 8O-38
ADJUSTER NOISE DIAGNOSIS - DIAGNOSIS AND TESTING, HYDRAULIC
LASH ............................... 9-34
ADJUSTER TENSION RELEASE - STANDARD PROCEDURE, PARKING
BRAKE AUTOMATIC .................... 5-63ADJUSTER TENSION RESET -
STANDARD PROCEDURE, PARKING
BRAKE AUTOMATIC .................... 5-64
ADJUSTER/MANUAL - OCS - INSTALLATION, FRONT SEAT TRACK ....23-128
ADJUSTER/MANUAL - OCS - REMOVAL, FRONT SEAT TRACK .................23-126
ADJUSTER/POWER - OCS - INSTALLATION, FRONT SEAT TRACK ....23-125
ADJUSTER/POWER - OCS - REMOVAL, FRONT SEAT TRACK .................23-124
ADJUSTERS - INSTALLATION, HYDRAULIC LASH ..................... 9-35
ADJUSTERS - REMOVAL, HYDRAULIC LASH ............................... 9-35
AERATION - DIAGNOSIS AND TESTING, COOLING SYSTEM .....................7-4
AFTER AN AIRBAG DEPLOYMENT - STANDARD PROCEDURE, SERVICE .......8O-7
AIR CLEANER ELEMENT - INSTALLATION . 9-101, 9-24
AIR CLEANER ELEMENT - REMOVAL . 9-101,9-24
AIR CLEANER HOUSING - INSTALLATION . 9-102, 9-25
AIR CLEANER HOUSING - REMOVAL . 9-101,9-25
AIR CONDITIONER, DESCRIPTION - HEATER ............................. 24-1
AIR CONDITIONER, OPERATION - HEATER ............................. 24-4
AIR CONTROL MOTOR - DESCRIPTION, IDLE ............................... 14-33
AIR CONTROL MOTOR - INSTALLATION, IDLE ............................... 14-33
AIR CONTROL MOTOR - OPERATION, IDLE ............................... 14-33
AIR CONTROL MOTOR - REMOVAL, IDLE . . 14-33
AIR EXHAUSTER - DESCRIPTION, REAR QUARTER PANEL/FENDER ..............23-59
AIR EXHAUSTER - INSTALLATION, REAR QUARTER PANEL/FENDER ..............23-60
AIR EXHAUSTER - REMOVAL, REAR QUARTER PANEL/FENDER ..............23-59
AIR FILTER - DESCRIPTION ............24-42
AIR FILTER - INSTALLATION ............24-43
AIR FILTER - REMOVAL ...............24-42
AIR GAP, SPECIFICATIONS - WHEEL SPEED SENSOR ....................... 5-91
AIR INTAKE PIPE - INSTALLATION ......24-115
AIR INTAKE PIPE - REMOVAL ..........24-115
AIR OUTLETS - DESCRIPTION .....24-43,24-56
AIR OUTLETS - INSTALLATION ..........24-56
AIR OUTLETS - REMOVAL .............24-56
AIR PRESSURE TESTS - DIAGNOSIS AND TESTING, CLUTCH ...........21-153,21-8
AIR TEMPERATURE SENSOR - DESCRIPTION, INLET .................14-34
AIRBAG - DESCRIPTION, CURTAIN .......8O-12
AIRBAG - DESCRIPTION, DRIVER ........8O-16
AIRBAG - DESCRIPTION, KNEE BLOCKER . 8O-22
AIRBAG - DESCRIPTION, PASSENGER ....8O-30
AIRBAG - INSTALLATION, CURTAIN ......8O-16
AIRBAG - INSTALLATION, DRIVER .......8O-18
AIRBAG - INSTALLATION, KNEE BLOCKER .......................... 8O-23
AIRBAG - INSTALLATION, PASSENGER . . . 8O-32
AIRBAG - OPERATION, CURTAIN ........8O-13
AIRBAG - OPERATION, DRIVER .........8O-16
AIRBAG - OPERATION, KNEE BLOCKER . . . 8O-22
AIRBAG - OPERATION, PASSENGER ......8O-30
AIRBAG - REMOVAL, CURTAIN ..........8O-14
AIRBAG - REMOVAL, DRIVER ...........8O-17
AIRBAG - REMOVAL, KNEE BLOCKER ....8O-23
AIRBAG - REMOVAL, PASSENGER .......8O-30
AIRBAG DEPLOYMENT - STANDARD PROCEDURE, SERVICE AFTER AN ........8O-7
AIRBAG DISABLED INDICATOR - DESCRIPTION, PASSENGER ............8O-33
AIRBAG DISABLED INDICATOR - INSTALLATION, PASSENGER ...........8O-34
AIRBAG DISABLED INDICATOR - OPERATION, PASSENGER ..............8O-33
AIRBAG DISABLED INDICATOR - REMOVAL, PASSENGER ...............8O-34
AIRBAG SYSTEM - DIAGNOSIS AND TESTING ............................ 8O-6
AIRBAGS - STANDARD PROCEDURE, HANDLING .......................... 8O-6
RS INDEX1
Description Group-Page Description Group-Page Description Group-Page
Page 2303 of 2339
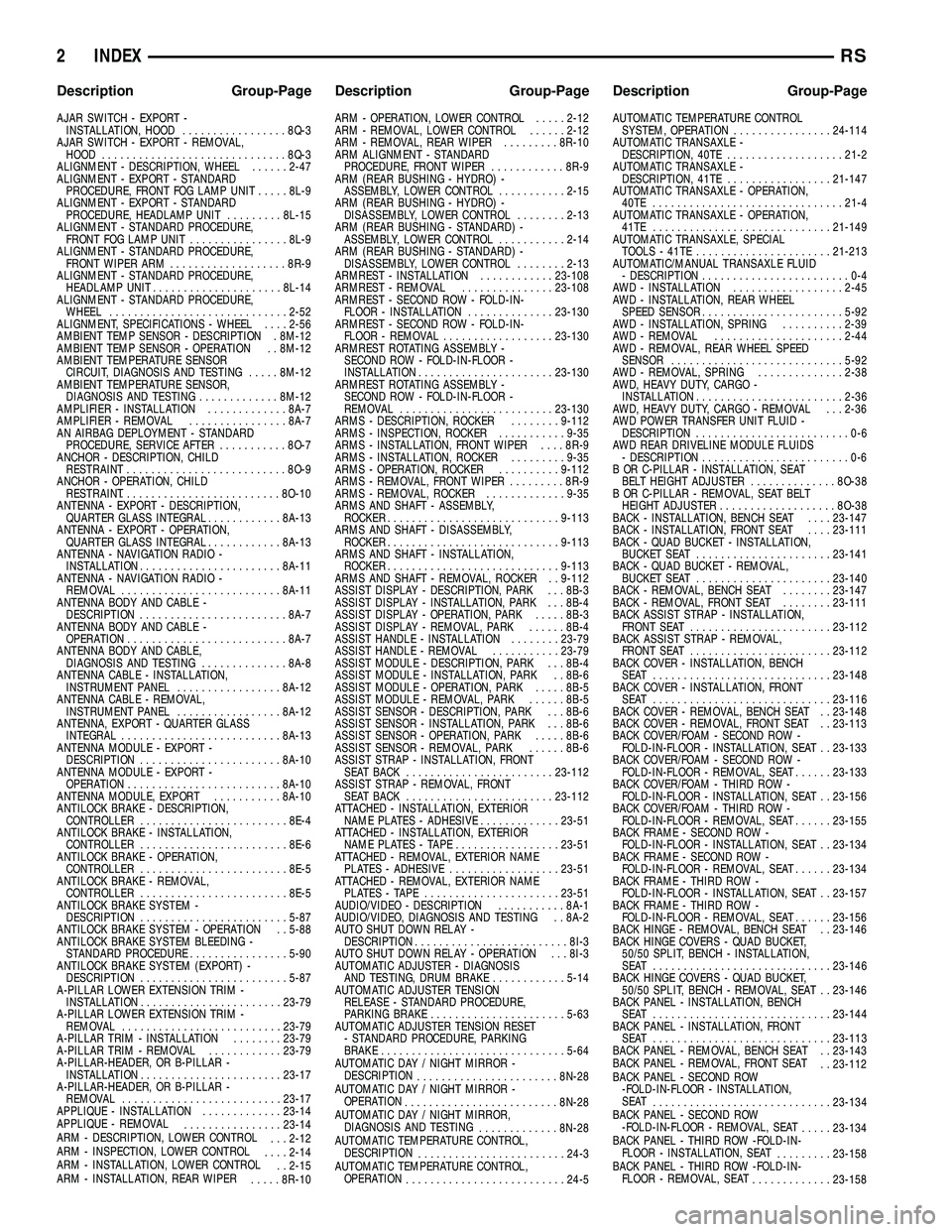
AJAR SWITCH - EXPORT -INSTALLATION, HOOD .................8Q-3
AJAR SWITCH - EXPORT - REMOVAL, HOOD .............................. 8Q-3
ALIGNMENT - DESCRIPTION, WHEEL ......2-47
ALIGNMENT - EXPORT - STANDARD PROCEDURE, FRONT FOG LAMP UNIT .....8L-9
ALIGNMENT - EXPORT - STANDARD PROCEDURE, HEADLAMP UNIT .........8L-15
ALIGNMENT - STANDARD PROCEDURE, FRONT FOG LAMP UNIT ................8L-9
ALIGNMENT - STANDARD PROCEDURE, FRONT WIPER ARM ................... 8R-9
ALIGNMENT - STANDARD PROCEDURE, HEADLAMP UNIT ..................... 8L-14
ALIGNMENT - STANDARD PROCEDURE, WHEEL ............................. 2-52
ALIGNMENT, SPECIFICATIONS - WHEEL ....2-56
AMBIENT TEMP SENSOR - DESCRIPTION . 8M-12
AMBIENT TEMP SENSOR - OPERATION . . 8M-12
AMBIENT TEMPERATURE SENSOR CIRCUIT, DIAGNOSIS AND TESTING .....8M-12
AMBIENT TEMPERATURE SENSOR, DIAGNOSIS AND TESTING .............8M-12
AMPLIFIER - INSTALLATION .............8A-7
AMPLIFIER - REMOVAL ................8A-7
AN AIRBAG DEPLOYMENT - STANDARD PROCEDURE, SERVICE AFTER ...........8O-7
ANCHOR - DESCRIPTION, CHILD RESTRAINT .......................... 8O-9
ANCHOR - OPERATION, CHILD RESTRAINT .......................... 8O-10
ANTENNA - EXPORT - DESCRIPTION, QUARTER GLASS INTEGRAL ............8A-13
ANTENNA - EXPORT - OPERATION, QUARTER GLASS INTEGRAL ............8A-13
ANTENNA - NAVIGATION RADIO - INSTALLATION ....................... 8A-11
ANTENNA - NAVIGATION RADIO - REMOVAL .......................... 8A-11
ANTENNA BODY AND CABLE - DESCRIPTION ........................ 8A-7
ANTENNA BODY AND CABLE - OPERATION .......................... 8A-7
ANTENNA BODY AND CABLE, DIAGNOSIS AND TESTING ..............8A-8
ANTENNA CABLE - INSTALLATION, INSTRUMENT PANEL .................8A-12
ANTENNA CABLE - REMOVAL, INSTRUMENT PANEL .................8A-12
ANTENNA, EXPORT - QUARTER GLASS INTEGRAL .......................... 8A-13
ANTENNA MODULE - EXPORT - DESCRIPTION ....................... 8A-10
ANTENNA MODULE - EXPORT - OPERATION ......................... 8A-10
ANTENNA MODULE, EXPORT ...........8A-10
ANTILOCK BRAKE - DESCRIPTION, CONTROLLER ........................ 8E-4
ANTILOCK BRAKE - INSTALLATION, CONTROLLER ........................ 8E-6
ANTILOCK BRAKE - OPERATION, CONTROLLER ........................ 8E-5
ANTILOCK BRAKE - REMOVAL, CONTROLLER ........................ 8E-5
ANTILOCK BRAKE SYSTEM - DESCRIPTION ........................ 5-87
ANTILOCK BRAKE SYSTEM - OPERATION . . 5-88
ANTILOCK BRAKE SYSTEM BLEEDING - STANDARD PROCEDURE ................5-90
ANTILOCK BRAKE SYSTEM (EXPORT) - DESCRIPTION ........................ 5-87
A-PILLAR LOWER EXTENSION TRIM - INSTALLATION ....................... 23-79
A-PILLAR LOWER EXTENSION TRIM - REMOVAL .......................... 23-79
A-PILLAR TRIM - INSTALLATION ........23-79
A-PILLAR TRIM - REMOVAL ............23-79
A-PILLAR-HEADER, OR B-PILLAR - INSTALLATION ....................... 23-17
A-PILLAR-HEADER, OR B-PILLAR - REMOVAL .......................... 23-17
APPLIQUE - INSTALLATION .............23-14
APPLIQUE - REMOVAL ................23-14
ARM - DESCRIPTION, LOWER CONTROL . . . 2-12
ARM - INSPECTION, LOWER CONTROL ....2-14
ARM - INSTALLATION, LOWER CONTROL . . 2-15
ARM - INSTALLATION, REAR WIPER .....8R-10 ARM - OPERATION, LOWER CONTROL
.....2-12
ARM - REMOVAL, LOWER CONTROL ......2-12
ARM - REMOVAL, REAR WIPER .........8R-10
ARM ALIGNMENT - STANDARD PROCEDURE, FRONT WIPER ............8R-9
ARM (REAR BUSHING - HYDRO) - ASSEMBLY, LOWER CONTROL ...........2-15
ARM (REAR BUSHING - HYDRO) - DISASSEMBLY, LOWER CONTROL ........2-13
ARM (REAR BUSHING - STANDARD) - ASSEMBLY, LOWER CONTROL ...........2-14
ARM (REAR BUSHING - STANDARD) - DISASSEMBLY, LOWER CONTROL ........2-13
ARMREST - INSTALLATION ............23-108
ARMREST - REMOVAL ...............23-108
ARMREST - SECOND ROW - FOLD-IN- FLOOR - INSTALLATION ..............23-130
ARMREST - SECOND ROW - FOLD-IN- FLOOR - REMOVAL .................. 23-130
ARMREST ROTATING ASSEMBLY - SECOND ROW - FOLD-IN-FLOOR -
INSTALLATION ...................... 23-130
ARMREST ROTATING ASSEMBLY - SECOND ROW - FOLD-IN-FLOOR -
REMOVAL ......................... 23-130
ARMS - DESCRIPTION, ROCKER ........9-112
ARMS - INSPECTION, ROCKER ...........9-35
ARMS - INSTALLATION, FRONT WIPER ....8R-9
ARMS - INSTALLATION, ROCKER .........9-35
ARMS - OPERATION, ROCKER ..........9-112
ARMS - REMOVAL, FRONT WIPER .........8R-9
ARMS - REMOVAL, ROCKER .............9-35
ARMS AND SHAFT - ASSEMBLY, ROCKER ............................ 9-113
ARMS AND SHAFT - DISASSEMBLY, ROCKER ............................ 9-113
ARMS AND SHAFT - INSTALLATION, ROCKER ............................ 9-113
ARMS AND SHAFT - REMOVAL, ROCKER . . 9-112
ASSIST DISPLAY - DESCRIPTION, PARK . . . 8B-3
ASSIST DISPLAY - INSTALLATION, PARK . . . 8B-4
ASSIST DISPLAY - OPERATION, PARK .....8B-3
ASSIST DISPLAY - REMOVAL, PARK ......8B-4
ASSIST HANDLE - INSTALLATION ........23-79
ASSIST HANDLE - REMOVAL ...........23-79
ASSIST MODULE - DESCRIPTION, PARK . . . 8B-4
ASSIST MODULE - INSTALLATION, PARK . . 8B-6
ASSIST MODULE - OPERATION, PARK .....8B-5
ASSIST MODULE - REMOVAL, PARK ......8B-5
ASSIST SENSOR - DESCRIPTION, PARK . . . 8B-6
ASSIST SENSOR - INSTALLATION, PARK . . . 8B-6
ASSIST SENSOR - OPERATION, PARK .....8B-6
ASSIST SENSOR - REMOVAL, PARK ......8B-6
ASSIST STRAP - INSTALLATION, FRONT SEAT BACK ........................ 23-112
ASSIST STRAP - REMOVAL, FRONT SEAT BACK ........................ 23-112
ATTACHED - INSTALLATION, EXTERIOR NAME PLATES - ADHESIVE .............23-51
ATTACHED - INSTALLATION, EXTERIOR NAME PLATES - TAPE .................23-51
ATTACHED - REMOVAL, EXTERIOR NAME PLATES - ADHESIVE .................. 23-51
ATTACHED - REMOVAL, EXTERIOR NAME PLATES - TAPE ...................... 23-51
AUDIO/VIDEO - DESCRIPTION ...........8A-1
AUDIO/VIDEO, DIAGNOSIS AND TESTING . . 8A-2
AUTO SHUT DOWN RELAY - DESCRIPTION ......................... 8I-3
AUTO SHUT DOWN RELAY - OPERATION . . . 8I-3
AUTOMATIC ADJUSTER - DIAGNOSIS AND TESTING, DRUM BRAKE ............5-14
AUTOMATIC ADJUSTER TENSION RELEASE - STANDARD PROCEDURE,
PARKING BRAKE ...................... 5-63
AUTOMATIC ADJUSTER TENSION RESET - STANDARD PROCEDURE, PARKING
BRAKE .............................. 5-64
AUTOMATIC DAY / NIGHT MIRROR - DESCRIPTION ....................... 8N-28
AUTOMATIC DAY / NIGHT MIRROR - OPERATION ......................... 8N-28
AUTOMATIC DAY / NIGHT MIRROR, DIAGNOSIS AND TESTING .............8N-28
AUTOMATIC TEMPERATURE CONTROL, DESCRIPTION ........................ 24-3
AUTOMATIC TEMPERATURE CONTROL, OPERATION .......................... 24-5AUTOMATIC TEMPERATURE CONTROL
SYSTEM, OPERATION ................24-114
AUTOMATIC TRANSAXLE - DESCRIPTION, 40TE ................... 21-2
AUTOMATIC TRANSAXLE - DESCRIPTION, 41TE .................21-147
AUTOMATIC TRANSAXLE - OPERATION, 40TE ............................... 21-4
AUTOMATIC TRANSAXLE - OPERATION, 41TE ............................. 21-149
AUTOMATIC TRANSAXLE, SPECIAL TOOLS - 41TE ...................... 21-213
AUTOMATIC/MANUAL TRANSAXLE FLUID - DESCRIPTION ........................0-4
AWD - INSTALLATION ..................2-45
AWD - INSTALLATION, REAR WHEEL SPEED SENSOR ....................... 5-92
AWD - INSTALLATION, SPRING ..........2-39
AWD - REMOVAL ..................... 2-44
AWD - REMOVAL, REAR WHEEL SPEED SENSOR ............................ 5-92
AWD - REMOVAL, SPRING ..............2-38
AWD, HEAVY DUTY, CARGO - INSTALLATION ........................ 2-36
AWD, HEAVY DUTY, CARGO - REMOVAL . . . 2-36
AWD POWER TRANSFER UNIT FLUID - DESCRIPTION .........................0-6
AWD REAR DRIVELINE MODULE FLUIDS - DESCRIPTION ........................0-6
B OR C-PILLAR - INSTALLATION, SEAT BELT HEIGHT ADJUSTER ..............8O-38
B OR C-PILLAR - REMOVAL, SEAT BELT HEIGHT ADJUSTER ................... 8O-38
BACK - INSTALLATION, BENCH SEAT ....23-147
BACK - INSTALLATION, FRONT SEAT ....23-111
BACK - QUAD BUCKET - INSTALLATION, BUCKET SEAT ...................... 23-141
BACK - QUAD BUCKET - REMOVAL, BUCKET SEAT ...................... 23-140
BACK - REMOVAL, BENCH SEAT ........23-147
BACK - REMOVAL, FRONT SEAT ........23-111
BACK ASSIST STRAP - INSTALLATION, FRONT SEAT ....................... 23-112
BACK ASSIST STRAP - REMOVAL, FRONT SEAT ....................... 23-112
BACK COVER - INSTALLATION, BENCH SEAT ............................. 23-148
BACK COVER - INSTALLATION, FRONT SEAT ............................. 23-116
BACK COVER - REMOVAL, BENCH SEAT . . 23-148
BACK COVER - REMOVAL, FRONT SEAT . . 23-113
BACK COVER/FOAM - SECOND ROW - FOLD-IN-FLOOR - INSTALLATION, SEAT . . 23-133
BACK COVER/FOAM - SECOND ROW - FOLD-IN-FLOOR - REMOVAL, SEAT ......23-133
BACK COVER/FOAM - THIRD ROW - FOLD-IN-FLOOR - INSTALLATION, SEAT . . 23-156
BACK COVER/FOAM - THIRD ROW - FOLD-IN-FLOOR - REMOVAL, SEAT ......23-155
BACK FRAME - SECOND ROW - FOLD-IN-FLOOR - INSTALLATION, SEAT . . 23-134
BACK FRAME - SECOND ROW - FOLD-IN-FLOOR - REMOVAL, SEAT ......23-134
BACK FRAME - THIRD ROW - FOLD-IN-FLOOR - INSTALLATION, SEAT . . 23-157
BACK FRAME - THIRD ROW - FOLD-IN-FLOOR - REMOVAL, SEAT ......23-156
BACK HINGE - REMOVAL, BENCH SEAT . . 23-146
BACK HINGE COVERS - QUAD BUCKET, 50/50 SPLIT, BENCH - INSTALLATION,
SEAT ............................. 23-146
BACK HINGE COVERS - QUAD BUCKET, 50/50 SPLIT, BENCH - REMOVAL, SEAT . . 23-146
BACK PANEL - INSTALLATION, BENCH SEAT ............................. 23-144
BACK PANEL - INSTALLATION, FRONT SEAT ............................. 23-113
BACK PANEL - REMOVAL, BENCH SEAT . . 23-143
BACK PANEL - REMOVAL, FRONT SEAT . . 23-112
BACK PANEL - SECOND ROW -FOLD-IN-FLOOR - INSTALLATION,
SEAT ............................. 23-134
BACK PANEL - SECOND ROW -FOLD-IN-FLOOR - REMOVAL, SEAT .....23-134
BACK PANEL - THIRD ROW -FOLD-IN- FLOOR - INSTALLATION, SEAT .........23-158
BACK PANEL - THIRD ROW -FOLD-IN- FLOOR - REMOVAL, SEAT .............23-158
2 INDEXRS
Description Group-Page Description Group-Page Description Group-Page