Steering CHRYSLER VOYAGER 2005 Service Manual
[x] Cancel search | Manufacturer: CHRYSLER, Model Year: 2005, Model line: VOYAGER, Model: CHRYSLER VOYAGER 2005Pages: 2339, PDF Size: 59.69 MB
Page 2232 of 2339
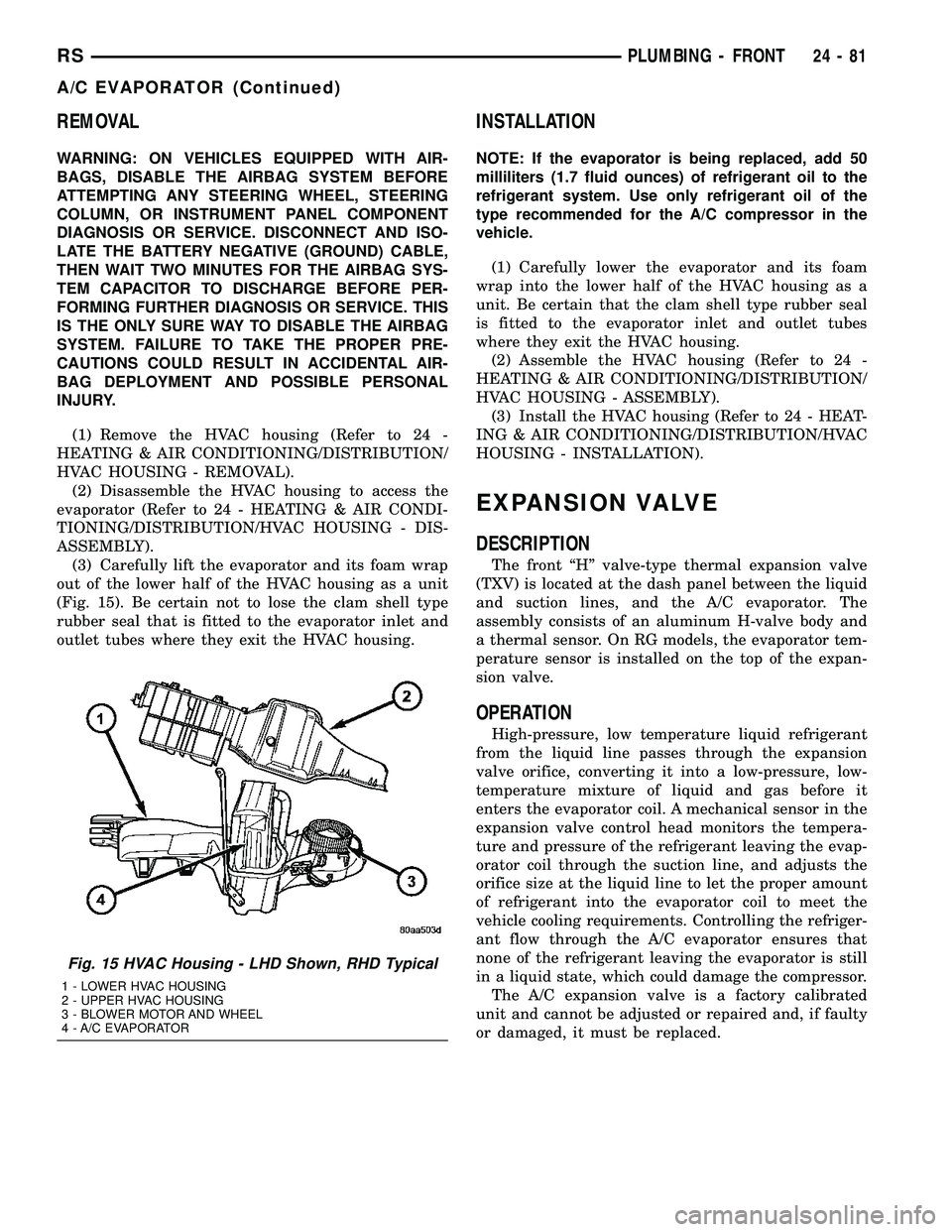
REMOVAL
WARNING: ON VEHICLES EQUIPPED WITH AIR-
BAGS, DISABLE THE AIRBAG SYSTEM BEFORE
ATTEMPTING ANY STEERING WHEEL, STEERING
COLUMN, OR INSTRUMENT PANEL COMPONENT
DIAGNOSIS OR SERVICE. DISCONNECT AND ISO-
LATE THE BATTERY NEGATIVE (GROUND) CABLE,
THEN WAIT TWO MINUTES FOR THE AIRBAG SYS-
TEM CAPACITOR TO DISCHARGE BEFORE PER-
FORMING FURTHER DIAGNOSIS OR SERVICE. THIS
IS THE ONLY SURE WAY TO DISABLE THE AIRBAG
SYSTEM. FAILURE TO TAKE THE PROPER PRE-
CAUTIONS COULD RESULT IN ACCIDENTAL AIR-
BAG DEPLOYMENT AND POSSIBLE PERSONAL
INJURY.
(1) Remove the HVAC housing (Refer to 24 -
HEATING & AIR CONDITIONING/DISTRIBUTION/
HVAC HOUSING - REMOVAL).
(2) Disassemble the HVAC housing to access the
evaporator (Refer to 24 - HEATING & AIR CONDI-
TIONING/DISTRIBUTION/HVAC HOUSING - DIS-
ASSEMBLY).
(3) Carefully lift the evaporator and its foam wrap
out of the lower half of the HVAC housing as a unit
(Fig. 15). Be certain not to lose the clam shell type
rubber seal that is fitted to the evaporator inlet and
outlet tubes where they exit the HVAC housing.
INSTALLATION
NOTE: If the evaporator is being replaced, add 50
milliliters (1.7 fluid ounces) of refrigerant oil to the
refrigerant system. Use only refrigerant oil of the
type recommended for the A/C compressor in the
vehicle.
(1) Carefully lower the evaporator and its foam
wrap into the lower half of the HVAC housing as a
unit. Be certain that the clam shell type rubber seal
is fitted to the evaporator inlet and outlet tubes
where they exit the HVAC housing.
(2) Assemble the HVAC housing (Refer to 24 -
HEATING & AIR CONDITIONING/DISTRIBUTION/
HVAC HOUSING - ASSEMBLY).
(3) Install the HVAC housing (Refer to 24 - HEAT-
ING & AIR CONDITIONING/DISTRIBUTION/HVAC
HOUSING - INSTALLATION).
EXPANSION VALVE
DESCRIPTION
The front ªHº valve-type thermal expansion valve
(TXV) is located at the dash panel between the liquid
and suction lines, and the A/C evaporator. The
assembly consists of an aluminum H-valve body and
a thermal sensor. On RG models, the evaporator tem-
perature sensor is installed on the top of the expan-
sion valve.
OPERATION
High-pressure, low temperature liquid refrigerant
from the liquid line passes through the expansion
valve orifice, converting it into a low-pressure, low-
temperature mixture of liquid and gas before it
enters the evaporator coil. A mechanical sensor in the
expansion valve control head monitors the tempera-
ture and pressure of the refrigerant leaving the evap-
orator coil through the suction line, and adjusts the
orifice size at the liquid line to let the proper amount
of refrigerant into the evaporator coil to meet the
vehicle cooling requirements. Controlling the refriger-
ant flow through the A/C evaporator ensures that
none of the refrigerant leaving the evaporator is still
in a liquid state, which could damage the compressor.
The A/C expansion valve is a factory calibrated
unit and cannot be adjusted or repaired and, if faulty
or damaged, it must be replaced.
Fig. 15 HVAC Housing - LHD Shown, RHD Typical
1 - LOWER HVAC HOUSING
2 - UPPER HVAC HOUSING
3 - BLOWER MOTOR AND WHEEL
4 - A/C EVAPORATOR
RSPLUMBING - FRONT24-81
A/C EVAPORATOR (Continued)
Page 2235 of 2339
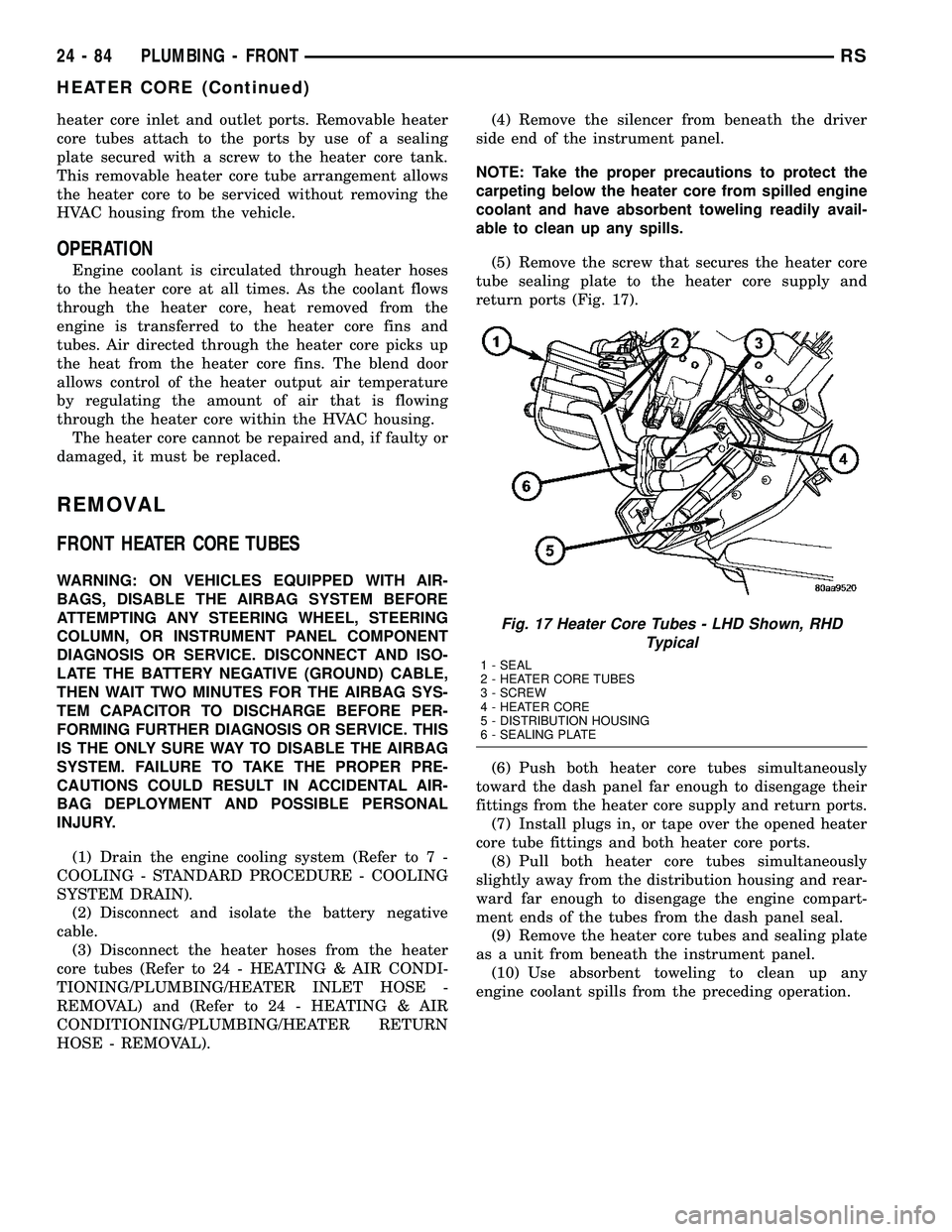
heater core inlet and outlet ports. Removable heater
core tubes attach to the ports by use of a sealing
plate secured with a screw to the heater core tank.
This removable heater core tube arrangement allows
the heater core to be serviced without removing the
HVAC housing from the vehicle.
OPERATION
Engine coolant is circulated through heater hoses
to the heater core at all times. As the coolant flows
through the heater core, heat removed from the
engine is transferred to the heater core fins and
tubes. Air directed through the heater core picks up
the heat from the heater core fins. The blend door
allows control of the heater output air temperature
by regulating the amount of air that is flowing
through the heater core within the HVAC housing.
The heater core cannot be repaired and, if faulty or
damaged, it must be replaced.
REMOVAL
FRONT HEATER CORE TUBES
WARNING: ON VEHICLES EQUIPPED WITH AIR-
BAGS, DISABLE THE AIRBAG SYSTEM BEFORE
ATTEMPTING ANY STEERING WHEEL, STEERING
COLUMN, OR INSTRUMENT PANEL COMPONENT
DIAGNOSIS OR SERVICE. DISCONNECT AND ISO-
LATE THE BATTERY NEGATIVE (GROUND) CABLE,
THEN WAIT TWO MINUTES FOR THE AIRBAG SYS-
TEM CAPACITOR TO DISCHARGE BEFORE PER-
FORMING FURTHER DIAGNOSIS OR SERVICE. THIS
IS THE ONLY SURE WAY TO DISABLE THE AIRBAG
SYSTEM. FAILURE TO TAKE THE PROPER PRE-
CAUTIONS COULD RESULT IN ACCIDENTAL AIR-
BAG DEPLOYMENT AND POSSIBLE PERSONAL
INJURY.
(1) Drain the engine cooling system (Refer to 7 -
COOLING - STANDARD PROCEDURE - COOLING
SYSTEM DRAIN).
(2) Disconnect and isolate the battery negative
cable.
(3) Disconnect the heater hoses from the heater
core tubes (Refer to 24 - HEATING & AIR CONDI-
TIONING/PLUMBING/HEATER INLET HOSE -
REMOVAL) and (Refer to 24 - HEATING & AIR
CONDITIONING/PLUMBING/HEATER RETURN
HOSE - REMOVAL).(4) Remove the silencer from beneath the driver
side end of the instrument panel.
NOTE: Take the proper precautions to protect the
carpeting below the heater core from spilled engine
coolant and have absorbent toweling readily avail-
able to clean up any spills.
(5) Remove the screw that secures the heater core
tube sealing plate to the heater core supply and
return ports (Fig. 17).
(6) Push both heater core tubes simultaneously
toward the dash panel far enough to disengage their
fittings from the heater core supply and return ports.
(7) Install plugs in, or tape over the opened heater
core tube fittings and both heater core ports.
(8) Pull both heater core tubes simultaneously
slightly away from the distribution housing and rear-
ward far enough to disengage the engine compart-
ment ends of the tubes from the dash panel seal.
(9) Remove the heater core tubes and sealing plate
as a unit from beneath the instrument panel.
(10) Use absorbent toweling to clean up any
engine coolant spills from the preceding operation.
Fig. 17 Heater Core Tubes - LHD Shown, RHD
Typical
1 - SEAL
2 - HEATER CORE TUBES
3 - SCREW
4 - HEATER CORE
5 - DISTRIBUTION HOUSING
6 - SEALING PLATE
24 - 84 PLUMBING - FRONTRS
HEATER CORE (Continued)
Page 2236 of 2339
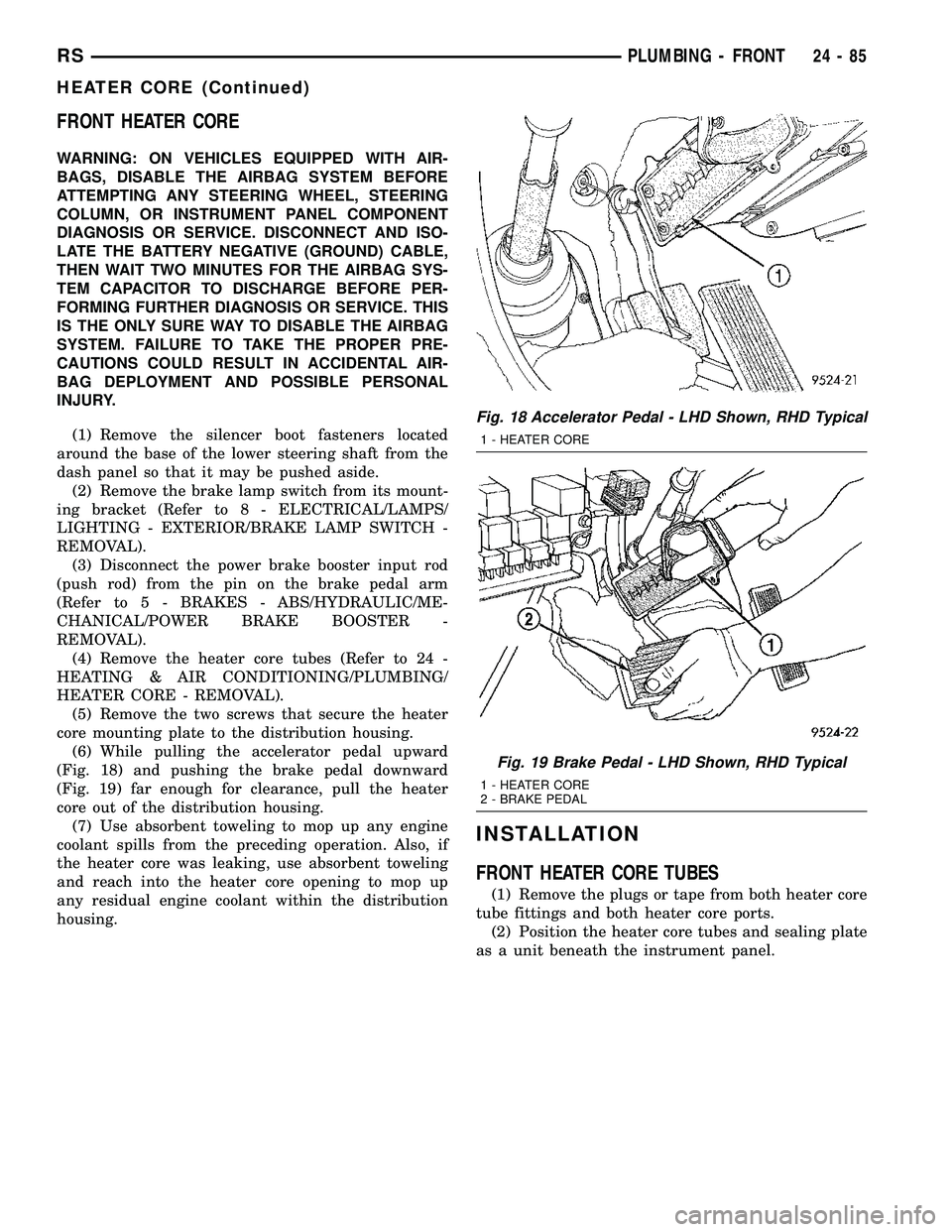
FRONT HEATER CORE
WARNING: ON VEHICLES EQUIPPED WITH AIR-
BAGS, DISABLE THE AIRBAG SYSTEM BEFORE
ATTEMPTING ANY STEERING WHEEL, STEERING
COLUMN, OR INSTRUMENT PANEL COMPONENT
DIAGNOSIS OR SERVICE. DISCONNECT AND ISO-
LATE THE BATTERY NEGATIVE (GROUND) CABLE,
THEN WAIT TWO MINUTES FOR THE AIRBAG SYS-
TEM CAPACITOR TO DISCHARGE BEFORE PER-
FORMING FURTHER DIAGNOSIS OR SERVICE. THIS
IS THE ONLY SURE WAY TO DISABLE THE AIRBAG
SYSTEM. FAILURE TO TAKE THE PROPER PRE-
CAUTIONS COULD RESULT IN ACCIDENTAL AIR-
BAG DEPLOYMENT AND POSSIBLE PERSONAL
INJURY.
(1) Remove the silencer boot fasteners located
around the base of the lower steering shaft from the
dash panel so that it may be pushed aside.
(2) Remove the brake lamp switch from its mount-
ing bracket (Refer to 8 - ELECTRICAL/LAMPS/
LIGHTING - EXTERIOR/BRAKE LAMP SWITCH -
REMOVAL).
(3) Disconnect the power brake booster input rod
(push rod) from the pin on the brake pedal arm
(Refer to 5 - BRAKES - ABS/HYDRAULIC/ME-
CHANICAL/POWER BRAKE BOOSTER -
REMOVAL).
(4) Remove the heater core tubes (Refer to 24 -
HEATING & AIR CONDITIONING/PLUMBING/
HEATER CORE - REMOVAL).
(5) Remove the two screws that secure the heater
core mounting plate to the distribution housing.
(6) While pulling the accelerator pedal upward
(Fig. 18) and pushing the brake pedal downward
(Fig. 19) far enough for clearance, pull the heater
core out of the distribution housing.
(7) Use absorbent toweling to mop up any engine
coolant spills from the preceding operation. Also, if
the heater core was leaking, use absorbent toweling
and reach into the heater core opening to mop up
any residual engine coolant within the distribution
housing.
INSTALLATION
FRONT HEATER CORE TUBES
(1) Remove the plugs or tape from both heater core
tube fittings and both heater core ports.
(2) Position the heater core tubes and sealing plate
as a unit beneath the instrument panel.
Fig. 18 Accelerator Pedal - LHD Shown, RHD Typical
1 - HEATER CORE
Fig. 19 Brake Pedal - LHD Shown, RHD Typical
1 - HEATER CORE
2 - BRAKE PEDAL
RSPLUMBING - FRONT24-85
HEATER CORE (Continued)
Page 2237 of 2339
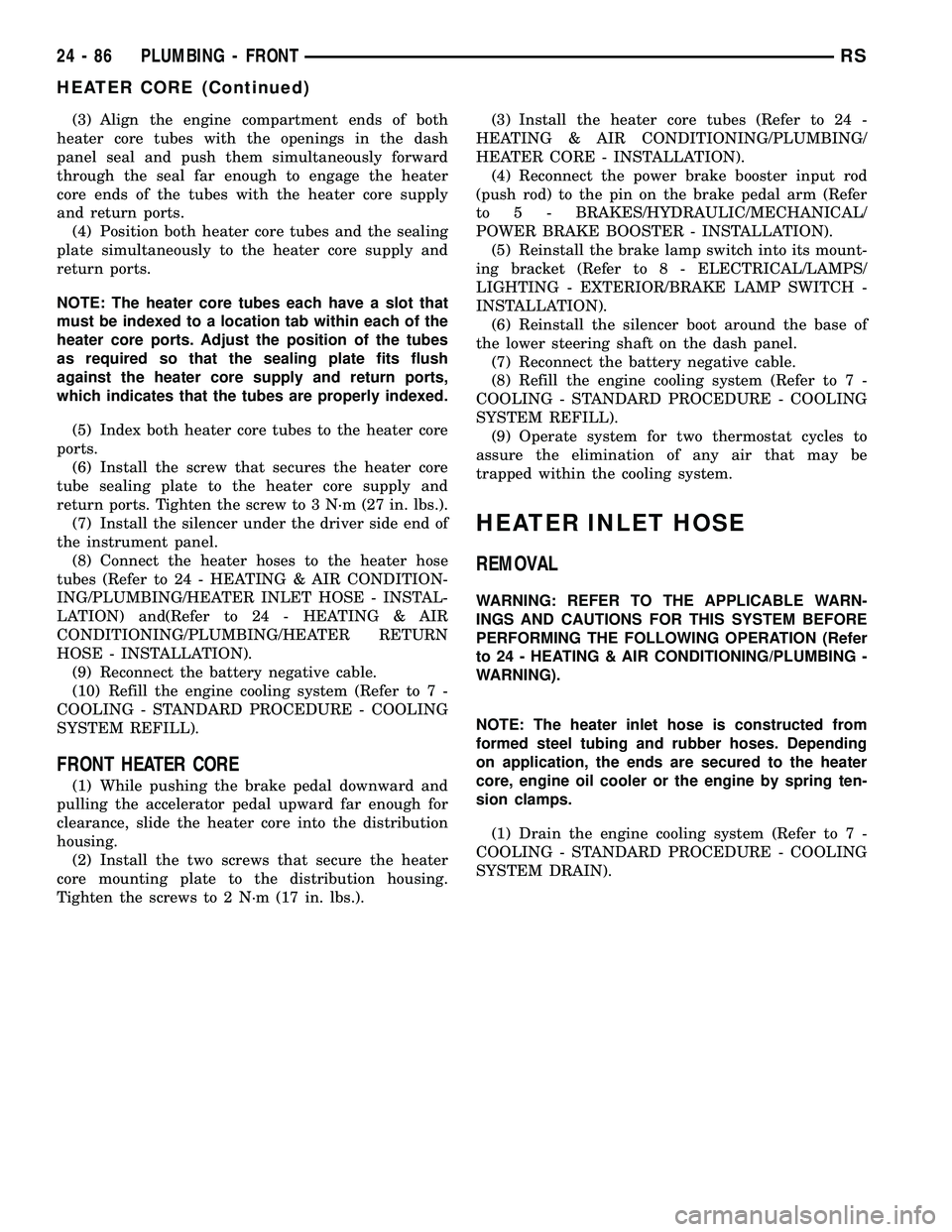
(3) Align the engine compartment ends of both
heater core tubes with the openings in the dash
panel seal and push them simultaneously forward
through the seal far enough to engage the heater
core ends of the tubes with the heater core supply
and return ports.
(4) Position both heater core tubes and the sealing
plate simultaneously to the heater core supply and
return ports.
NOTE: The heater core tubes each have a slot that
must be indexed to a location tab within each of the
heater core ports. Adjust the position of the tubes
as required so that the sealing plate fits flush
against the heater core supply and return ports,
which indicates that the tubes are properly indexed.
(5) Index both heater core tubes to the heater core
ports.
(6) Install the screw that secures the heater core
tube sealing plate to the heater core supply and
return ports. Tighten the screw to 3 N´m (27 in. lbs.).
(7) Install the silencer under the driver side end of
the instrument panel.
(8) Connect the heater hoses to the heater hose
tubes (Refer to 24 - HEATING & AIR CONDITION-
ING/PLUMBING/HEATER INLET HOSE - INSTAL-
LATION) and(Refer to 24 - HEATING & AIR
CONDITIONING/PLUMBING/HEATER RETURN
HOSE - INSTALLATION).
(9) Reconnect the battery negative cable.
(10) Refill the engine cooling system (Refer to 7 -
COOLING - STANDARD PROCEDURE - COOLING
SYSTEM REFILL).
FRONT HEATER CORE
(1) While pushing the brake pedal downward and
pulling the accelerator pedal upward far enough for
clearance, slide the heater core into the distribution
housing.
(2) Install the two screws that secure the heater
core mounting plate to the distribution housing.
Tighten the screws to 2 N´m (17 in. lbs.).(3) Install the heater core tubes (Refer to 24 -
HEATING & AIR CONDITIONING/PLUMBING/
HEATER CORE - INSTALLATION).
(4) Reconnect the power brake booster input rod
(push rod) to the pin on the brake pedal arm (Refer
to 5 - BRAKES/HYDRAULIC/MECHANICAL/
POWER BRAKE BOOSTER - INSTALLATION).
(5) Reinstall the brake lamp switch into its mount-
ing bracket (Refer to 8 - ELECTRICAL/LAMPS/
LIGHTING - EXTERIOR/BRAKE LAMP SWITCH -
INSTALLATION).
(6) Reinstall the silencer boot around the base of
the lower steering shaft on the dash panel.
(7) Reconnect the battery negative cable.
(8) Refill the engine cooling system (Refer to 7 -
COOLING - STANDARD PROCEDURE - COOLING
SYSTEM REFILL).
(9) Operate system for two thermostat cycles to
assure the elimination of any air that may be
trapped within the cooling system.
HEATER INLET HOSE
REMOVAL
WARNING: REFER TO THE APPLICABLE WARN-
INGS AND CAUTIONS FOR THIS SYSTEM BEFORE
PERFORMING THE FOLLOWING OPERATION (Refer
to 24 - HEATING & AIR CONDITIONING/PLUMBING -
WARNING).
NOTE: The heater inlet hose is constructed from
formed steel tubing and rubber hoses. Depending
on application, the ends are secured to the heater
core, engine oil cooler or the engine by spring ten-
sion clamps.
(1) Drain the engine cooling system (Refer to 7 -
COOLING - STANDARD PROCEDURE - COOLING
SYSTEM DRAIN).
24 - 86 PLUMBING - FRONTRS
HEATER CORE (Continued)
Page 2275 of 2339
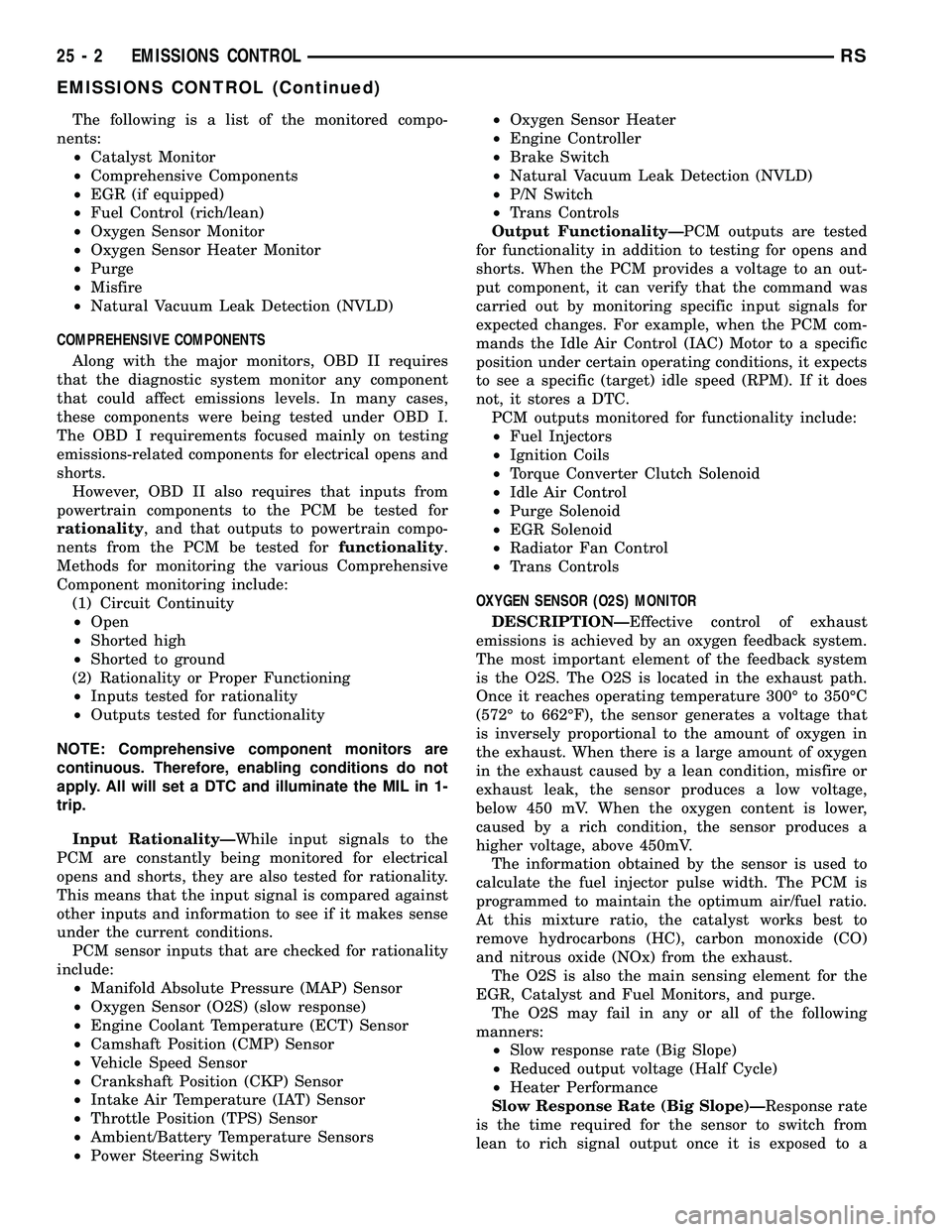
The following is a list of the monitored compo-
nents:
²Catalyst Monitor
²Comprehensive Components
²EGR (if equipped)
²Fuel Control (rich/lean)
²Oxygen Sensor Monitor
²Oxygen Sensor Heater Monitor
²Purge
²Misfire
²Natural Vacuum Leak Detection (NVLD)
COMPREHENSIVE COMPONENTS
Along with the major monitors, OBD II requires
that the diagnostic system monitor any component
that could affect emissions levels. In many cases,
these components were being tested under OBD I.
The OBD I requirements focused mainly on testing
emissions-related components for electrical opens and
shorts.
However, OBD II also requires that inputs from
powertrain components to the PCM be tested for
rationality, and that outputs to powertrain compo-
nents from the PCM be tested forfunctionality.
Methods for monitoring the various Comprehensive
Component monitoring include:
(1) Circuit Continuity
²Open
²Shorted high
²Shorted to ground
(2) Rationality or Proper Functioning
²Inputs tested for rationality
²Outputs tested for functionality
NOTE: Comprehensive component monitors are
continuous. Therefore, enabling conditions do not
apply. All will set a DTC and illuminate the MIL in 1-
trip.
Input RationalityÐWhile input signals to the
PCM are constantly being monitored for electrical
opens and shorts, they are also tested for rationality.
This means that the input signal is compared against
other inputs and information to see if it makes sense
under the current conditions.
PCM sensor inputs that are checked for rationality
include:
²Manifold Absolute Pressure (MAP) Sensor
²Oxygen Sensor (O2S) (slow response)
²Engine Coolant Temperature (ECT) Sensor
²Camshaft Position (CMP) Sensor
²Vehicle Speed Sensor
²Crankshaft Position (CKP) Sensor
²Intake Air Temperature (IAT) Sensor
²Throttle Position (TPS) Sensor
²Ambient/Battery Temperature Sensors
²Power Steering Switch²Oxygen Sensor Heater
²Engine Controller
²Brake Switch
²Natural Vacuum Leak Detection (NVLD)
²P/N Switch
²Trans Controls
Output FunctionalityÐPCM outputs are tested
for functionality in addition to testing for opens and
shorts. When the PCM provides a voltage to an out-
put component, it can verify that the command was
carried out by monitoring specific input signals for
expected changes. For example, when the PCM com-
mands the Idle Air Control (IAC) Motor to a specific
position under certain operating conditions, it expects
to see a specific (target) idle speed (RPM). If it does
not, it stores a DTC.
PCM outputs monitored for functionality include:
²Fuel Injectors
²Ignition Coils
²Torque Converter Clutch Solenoid
²Idle Air Control
²Purge Solenoid
²EGR Solenoid
²Radiator Fan Control
²Trans Controls
OXYGEN SENSOR (O2S) MONITOR
DESCRIPTIONÐEffective control of exhaust
emissions is achieved by an oxygen feedback system.
The most important element of the feedback system
is the O2S. The O2S is located in the exhaust path.
Once it reaches operating temperature 300É to 350ÉC
(572É to 662ÉF), the sensor generates a voltage that
is inversely proportional to the amount of oxygen in
the exhaust. When there is a large amount of oxygen
in the exhaust caused by a lean condition, misfire or
exhaust leak, the sensor produces a low voltage,
below 450 mV. When the oxygen content is lower,
caused by a rich condition, the sensor produces a
higher voltage, above 450mV.
The information obtained by the sensor is used to
calculate the fuel injector pulse width. The PCM is
programmed to maintain the optimum air/fuel ratio.
At this mixture ratio, the catalyst works best to
remove hydrocarbons (HC), carbon monoxide (CO)
and nitrous oxide (NOx) from the exhaust.
The O2S is also the main sensing element for the
EGR, Catalyst and Fuel Monitors, and purge.
The O2S may fail in any or all of the following
manners:
²Slow response rate (Big Slope)
²Reduced output voltage (Half Cycle)
²Heater Performance
Slow Response Rate (Big Slope)ÐResponse rate
is the time required for the sensor to switch from
lean to rich signal output once it is exposed to a
25 - 2 EMISSIONS CONTROLRS
EMISSIONS CONTROL (Continued)
Page 2276 of 2339
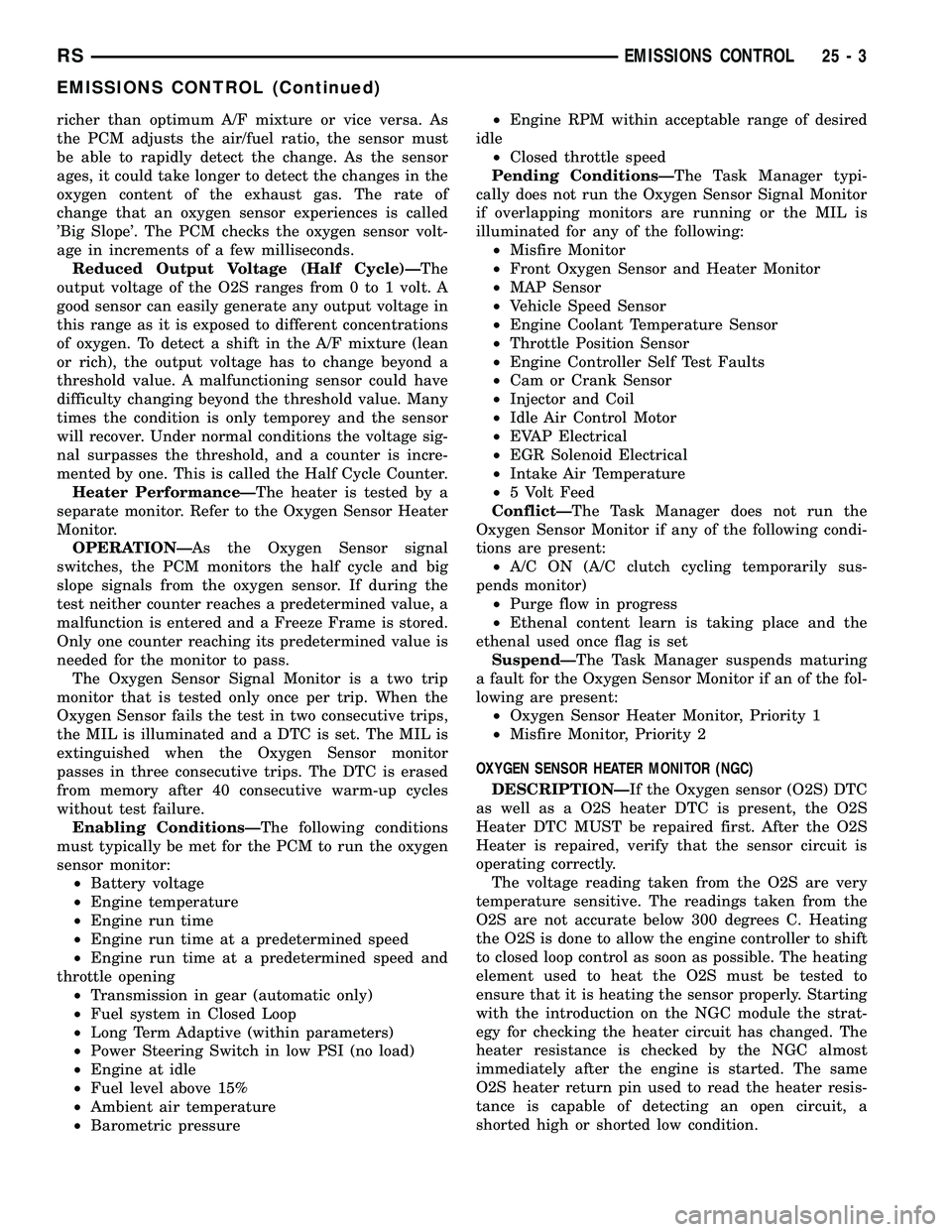
richer than optimum A/F mixture or vice versa. As
the PCM adjusts the air/fuel ratio, the sensor must
be able to rapidly detect the change. As the sensor
ages, it could take longer to detect the changes in the
oxygen content of the exhaust gas. The rate of
change that an oxygen sensor experiences is called
'Big Slope'. The PCM checks the oxygen sensor volt-
age in increments of a few milliseconds.
Reduced Output Voltage (Half Cycle)ÐThe
output voltage of the O2S ranges from 0 to 1 volt. A
good sensor can easily generate any output voltage in
this range as it is exposed to different concentrations
of oxygen. To detect a shift in the A/F mixture (lean
or rich), the output voltage has to change beyond a
threshold value. A malfunctioning sensor could have
difficulty changing beyond the threshold value. Many
times the condition is only temporey and the sensor
will recover. Under normal conditions the voltage sig-
nal surpasses the threshold, and a counter is incre-
mented by one. This is called the Half Cycle Counter.
Heater PerformanceÐThe heater is tested by a
separate monitor. Refer to the Oxygen Sensor Heater
Monitor.
OPERATIONÐAs the Oxygen Sensor signal
switches, the PCM monitors the half cycle and big
slope signals from the oxygen sensor. If during the
test neither counter reaches a predetermined value, a
malfunction is entered and a Freeze Frame is stored.
Only one counter reaching its predetermined value is
needed for the monitor to pass.
The Oxygen Sensor Signal Monitor is a two trip
monitor that is tested only once per trip. When the
Oxygen Sensor fails the test in two consecutive trips,
the MIL is illuminated and a DTC is set. The MIL is
extinguished when the Oxygen Sensor monitor
passes in three consecutive trips. The DTC is erased
from memory after 40 consecutive warm-up cycles
without test failure.
Enabling ConditionsÐThe following conditions
must typically be met for the PCM to run the oxygen
sensor monitor:
²Battery voltage
²Engine temperature
²Engine run time
²Engine run time at a predetermined speed
²Engine run time at a predetermined speed and
throttle opening
²Transmission in gear (automatic only)
²Fuel system in Closed Loop
²Long Term Adaptive (within parameters)
²Power Steering Switch in low PSI (no load)
²Engine at idle
²Fuel level above 15%
²Ambient air temperature
²Barometric pressure²Engine RPM within acceptable range of desired
idle
²Closed throttle speed
Pending ConditionsÐThe Task Manager typi-
cally does not run the Oxygen Sensor Signal Monitor
if overlapping monitors are running or the MIL is
illuminated for any of the following:
²Misfire Monitor
²Front Oxygen Sensor and Heater Monitor
²MAP Sensor
²Vehicle Speed Sensor
²Engine Coolant Temperature Sensor
²Throttle Position Sensor
²Engine Controller Self Test Faults
²Cam or Crank Sensor
²Injector and Coil
²Idle Air Control Motor
²EVAP Electrical
²EGR Solenoid Electrical
²Intake Air Temperature
²5 Volt Feed
ConflictÐThe Task Manager does not run the
Oxygen Sensor Monitor if any of the following condi-
tions are present:
²A/C ON (A/C clutch cycling temporarily sus-
pends monitor)
²Purge flow in progress
²Ethenal content learn is taking place and the
ethenal used once flag is set
SuspendÐThe Task Manager suspends maturing
a fault for the Oxygen Sensor Monitor if an of the fol-
lowing are present:
²Oxygen Sensor Heater Monitor, Priority 1
²Misfire Monitor, Priority 2
OXYGEN SENSOR HEATER MONITOR (NGC)
DESCRIPTIONÐIf the Oxygen sensor (O2S) DTC
as well as a O2S heater DTC is present, the O2S
Heater DTC MUST be repaired first. After the O2S
Heater is repaired, verify that the sensor circuit is
operating correctly.
The voltage reading taken from the O2S are very
temperature sensitive. The readings taken from the
O2S are not accurate below 300 degrees C. Heating
the O2S is done to allow the engine controller to shift
to closed loop control as soon as possible. The heating
element used to heat the O2S must be tested to
ensure that it is heating the sensor properly. Starting
with the introduction on the NGC module the strat-
egy for checking the heater circuit has changed. The
heater resistance is checked by the NGC almost
immediately after the engine is started. The same
O2S heater return pin used to read the heater resis-
tance is capable of detecting an open circuit, a
shorted high or shorted low condition.
RSEMISSIONS CONTROL25-3
EMISSIONS CONTROL (Continued)
Page 2304 of 2339
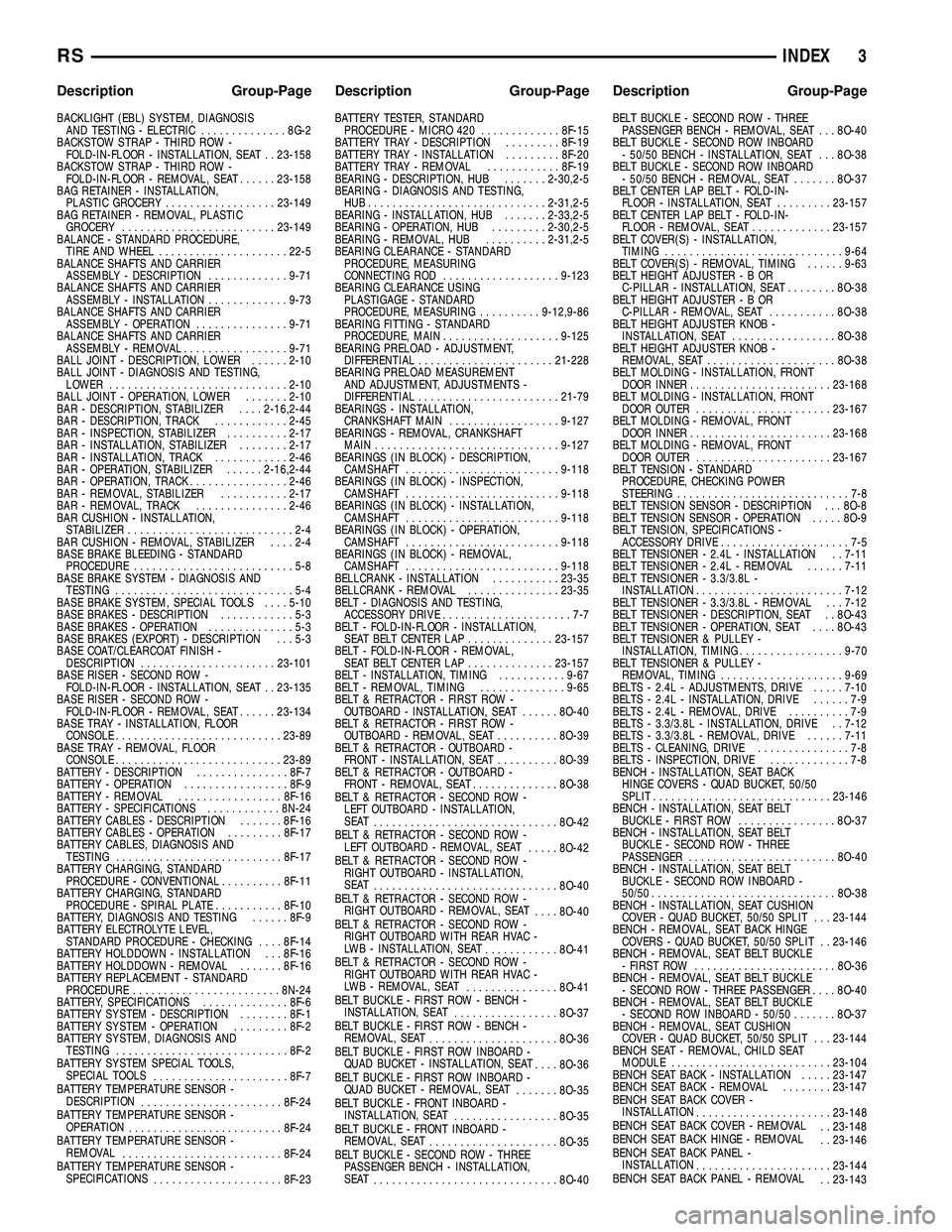
BACKLIGHT (EBL) SYSTEM, DIAGNOSISAND TESTING - ELECTRIC ..............8G-2
BACKSTOW STRAP - THIRD ROW - FOLD-IN-FLOOR - INSTALLATION, SEAT . . 23-158
BACKSTOW STRAP - THIRD ROW - FOLD-IN-FLOOR - REMOVAL, SEAT ......23-158
BAG RETAINER - INSTALLATION, PLASTIC GROCERY .................. 23-149
BAG RETAINER - REMOVAL, PLASTIC GROCERY ......................... 23-149
BALANCE - STANDARD PROCEDURE, TIRE AND WHEEL ..................... 22-5
BALANCE SHAFTS AND CARRIER ASSEMBLY - DESCRIPTION .............9-71
BALANCE SHAFTS AND CARRIER ASSEMBLY - INSTALLATION .............9-73
BALANCE SHAFTS AND CARRIER ASSEMBLY - OPERATION ...............9-71
BALANCE SHAFTS AND CARRIER ASSEMBLY - REMOVAL .................9-71
BALL JOINT - DESCRIPTION, LOWER ......2-10
BALL JOINT - DIAGNOSIS AND TESTING, LOWER ............................. 2-10
BALL JOINT - OPERATION, LOWER .......2-10
BAR - DESCRIPTION, STABILIZER ....2-16,2-44
BAR - DESCRIPTION, TRACK ............2-45
BAR - INSPECTION, STABILIZER ..........2-17
BAR - INSTALLATION, STABILIZER ........2-17
BAR - INSTALLATION, TRACK ............2-46
BAR - OPERATION, STABILIZER ......2-16,2-44
BAR - OPERATION, TRACK ................2-46
BAR - REMOVAL, STABILIZER ...........2-17
BAR - REMOVAL, TRACK ...............2-46
BAR CUSHION - INSTALLATION, STABILIZER ...........................2-4
BAR CUSHION - REMOVAL, STABILIZER ....2-4
BASE BRAKE BLEEDING - STANDARD PROCEDURE ..........................5-8
BASE BRAKE SYSTEM - DIAGNOSIS AND TESTING .............................5-4
BASE BRAKE SYSTEM, SPECIAL TOOLS ....5-10
BASE BRAKES - DESCRIPTION ............5-3
BASE BRAKES - OPERATION ..............5-3
BASE BRAKES (EXPORT) - DESCRIPTION . . . 5-3
BASE COAT/CLEARCOAT FINISH - DESCRIPTION ...................... 23-101
BASE RISER - SECOND ROW - FOLD-IN-FLOOR - INSTALLATION, SEAT . . 23-135
BASE RISER - SECOND ROW - FOLD-IN-FLOOR - REMOVAL, SEAT ......23-134
BASE TRAY - INSTALLATION, FLOOR CONSOLE ........................... 23-89
BASE TRAY - REMOVAL, FLOOR CONSOLE ........................... 23-89
BATTERY - DESCRIPTION ...............8F-7
BATTERY - OPERATION .................8F-9
BATTERY - REMOVAL .................8F-16
BATTERY - SPECIFICATIONS ............8N-24
BATTERY CABLES - DESCRIPTION .......8F-16
BATTERY CABLES - OPERATION .........8F-17
BATTERY CABLES, DIAGNOSIS AND TESTING ........................... 8F-17
BATTERY CHARGING, STANDARD PROCEDURE - CONVENTIONAL ..........8F-11
BATTERY CHARGING, STANDARD PROCEDURE - SPIRAL PLATE ...........8F-10
BATTERY, DIAGNOSIS AND TESTING ......8F-9
BATTERY ELECTROLYTE LEVEL, STANDARD PROCEDURE - CHECKING ....8F-14
BATTERY HOLDDOWN - INSTALLATION . . . 8F-16
BATTERY HOLDDOWN - REMOVAL .......8F-16
BATTERY REPLACEMENT - STANDARD PROCEDURE ........................ 8N-24
BATTERY, SPECIFICATIONS ..............8F-6
BATTERY SYSTEM - DESCRIPTION ........8F-1
BATTERY SYSTEM - OPERATION .........8F-2
BATTERY SYSTEM, DIAGNOSIS AND TESTING ............................ 8F-2
BATTERY SYSTEM SPECIAL TOOLS, SPECIAL TOOLS ...................... 8F-7
BATTERY TEMPERATURE SENSOR - DESCRIPTION ....................... 8F-24
BATTERY TEMPERATURE SENSOR - OPERATION ......................... 8F-24
BATTERY TEMPERATURE SENSOR - REMOVAL .......................... 8F-24
BATTERY TEMPERATURE SENSOR - SPECIFICATIONS ..................... 8F-23BATTERY TESTER, STANDARD
PROCEDURE - MICRO 420 .............8F-15
BATTERY TRAY - DESCRIPTION .........8F-19
BATTERY TRAY - INSTALLATION .........8F-20
BATTERY TRAY - REMOVAL ............8F-19
BEARING - DESCRIPTION, HUB .......2-30,2-5
BEARING - DIAGNOSIS AND TESTING, HUB............................. 2-31,2-5
BEARING - INSTALLATION, HUB .......2-33,2-5
BEARING - OPERATION, HUB .........2-30,2-5
BEARING - REMOVAL, HUB ..........2-31,2-5
BEARING CLEARANCE - STANDARD PROCEDURE, MEASURING
CONNECTING ROD ................... 9-123
BEARING CLEARANCE USING PLASTIGAGE - STANDARD
PROCEDURE, MEASURING ..........9-12,9-86
BEARING FITTING - STANDARD PROCEDURE, MAIN ................... 9-125
BEARING PRELOAD - ADJUSTMENT, DIFFERENTIAL ...................... 21-228
BEARING PRELOAD MEASUREMENT AND ADJUSTMENT, ADJUSTMENTS -
DIFFERENTIAL ....................... 21-79
BEARINGS - INSTALLATION, CRANKSHAFT MAIN .................. 9-127
BEARINGS - REMOVAL, CRANKSHAFT MAIN .............................. 9-127
BEARINGS (IN BLOCK) - DESCRIPTION, CAMSHAFT ......................... 9-118
BEARINGS (IN BLOCK) - INSPECTION, CAMSHAFT ......................... 9-118
BEARINGS (IN BLOCK) - INSTALLATION, CAMSHAFT ......................... 9-118
BEARINGS (IN BLOCK) - OPERATION, CAMSHAFT ......................... 9-118
BEARINGS (IN BLOCK) - REMOVAL, CAMSHAFT ......................... 9-118
BELLCRANK - INSTALLATION ...........23-35
BELLCRANK - REMOVAL ...............23-35
BELT - DIAGNOSIS AND TESTING, ACCESSORY DRIVE .....................7-7
BELT - FOLD-IN-FLOOR - INSTALLATION, SEAT BELT CENTER LAP ..............23-157
BELT - FOLD-IN-FLOOR - REMOVAL, SEAT BELT CENTER LAP ..............23-157
BELT - INSTALLATION, TIMING ...........9-67
BELT - REMOVAL, TIMING ..............9-65
BELT & RETRACTOR - FIRST ROW - OUTBOARD - INSTALLATION, SEAT ......8O-40
BELT & RETRACTOR - FIRST ROW - OUTBOARD - REMOVAL, SEAT ..........8O-39
BELT & RETRACTOR - OUTBOARD - FRONT - INSTALLATION, SEAT ..........8O-39
BELT & RETRACTOR - OUTBOARD - FRONT - REMOVAL, SEAT ..............8O-38
BELT & RETRACTOR - SECOND ROW - LEFT OUTBOARD - INSTALLATION,
SEAT .............................. 8O-42
BELT & RETRACTOR - SECOND ROW - LEFT OUTBOARD - REMOVAL, SEAT .....8O-42
BELT & RETRACTOR - SECOND ROW - RIGHT OUTBOARD - INSTALLATION,
SEAT .............................. 8O-40
BELT & RETRACTOR - SECOND ROW - RIGHT OUTBOARD - REMOVAL, SEAT ....8O-40
BELT & RETRACTOR - SECOND ROW - RIGHT OUTBOARD WITH REAR HVAC -
LWB - INSTALLATION, SEAT ............8O-41
BELT & RETRACTOR - SECOND ROW - RIGHT OUTBOARD WITH REAR HVAC -
LWB - REMOVAL, SEAT ...............8O-41
BELT BUCKLE - FIRST ROW - BENCH - INSTALLATION, SEAT .................8O-37
BELT BUCKLE - FIRST ROW - BENCH - REMOVAL, SEAT ..................... 8O-36
BELT BUCKLE - FIRST ROW INBOARD - QUAD BUCKET - INSTALLATION, SEAT ....8O-36
BELT BUCKLE - FIRST ROW INBOARD - QUAD BUCKET - REMOVAL, SEAT .......8O-35
BELT BUCKLE - FRONT INBOARD - INSTALLATION, SEAT .................8O-35
BELT BUCKLE - FRONT INBOARD - REMOVAL, SEAT ..................... 8O-35
BELT BUCKLE - SECOND ROW - THREE PASSENGER BENCH - INSTALLATION,
SEAT .............................. 8O-40BELT BUCKLE - SECOND ROW - THREE
PASSENGER BENCH - REMOVAL, SEAT . . . 8O-40
BELT BUCKLE - SECOND ROW INBOARD - 50/50 BENCH - INSTALLATION, SEAT . . . 8O-38
BELT BUCKLE - SECOND ROW INBOARD - 50/50 BENCH - REMOVAL, SEAT .......8O-37
BELT CENTER LAP BELT - FOLD-IN- FLOOR - INSTALLATION, SEAT .........23-157
BELT CENTER LAP BELT - FOLD-IN- FLOOR - REMOVAL, SEAT .............23-157
BELT COVER(S) - INSTALLATION, TIMING ............................. 9-64
BELT COVER(S) - REMOVAL, TIMING ......9-63
BELT HEIGHT ADJUSTE R-BOR
C-PILLAR - INSTALLATION, SEAT ........8O-38
BELT HEIGHT ADJUSTE R-BOR
C-PILLAR - REMOVAL, SEAT ...........8O-38
BELT HEIGHT ADJUSTER KNOB - INSTALLATION, SEAT .................8O-38
BELT HEIGHT ADJUSTER KNOB - REMOVAL, SEAT ..................... 8O-38
BELT MOLDING - INSTALLATION, FRONT DOOR INNER ....................... 23-168
BELT MOLDING - INSTALLATION, FRONT DOOR OUTER ...................... 23-167
BELT MOLDING - REMOVAL, FRONT DOOR INNER ....................... 23-168
BELT MOLDING - REMOVAL, FRONT DOOR OUTER ...................... 23-167
BELT TENSION - STANDARD PROCEDURE, CHECKING POWER
STEERING ............................7-8
BELT TENSION SENSOR - DESCRIPTION . . . 8O-8
BELT TENSION SENSOR - OPERATION .....8O-9
BELT TENSION, SPECIFICATIONS - ACCESSORY DRIVE .....................7-5
BELT TENSIONER - 2.4L - INSTALLATION . . 7-11
BELT TENSIONER - 2.4L - REMOVAL ......7-11
BELT TENSIONER - 3.3/3.8L - INSTALLATION ........................ 7-12
BELT TENSIONER - 3.3/3.8L - REMOVAL . . . 7-12
BELT TENSIONER - DESCRIPTION, SEAT . . 8O-43
BELT TENSIONER - OPERATION, SEAT ....8O-43
BELT TENSIONER & PULLEY - INSTALLATION, TIMING .................9-70
BELT TENSIONER & PULLEY - REMOVAL, TIMING .................... 9-69
BELTS - 2.4L - ADJUSTMENTS, DRIVE .....7-10
BELTS - 2.4L - INSTALLATION, DRIVE ......7-9
BELTS - 2.4L - REMOVAL, DRIVE ..........7-9
BELTS - 3.3/3.8L - INSTALLATION, DRIVE . . 7-12
BELTS - 3.3/3.8L - REMOVAL, DRIVE ......7-11
BELTS - CLEANING, DRIVE ...............7-8
BELTS - INSPECTION, DRIVE .............7-8
BENCH - INSTALLATION, SEAT BACK HINGE COVERS - QUAD BUCKET, 50/50
SPLIT ............................. 23-146
BENCH - INSTALLATION, SEAT BELT BUCKLE - FIRST ROW ................8O-37
BENCH - INSTALLATION, SEAT BELT BUCKLE - SECOND ROW - THREE
PASSENGER ........................ 8O-40
BENCH - INSTALLATION, SEAT BELT BUCKLE - SECOND ROW INBOARD -
50/50 .............................. 8O-38
BENCH - INSTALLATION, SEAT CUSHION COVER - QUAD BUCKET, 50/50 SPLIT . . . 23-144
BENCH - REMOVAL, SEAT BACK HINGE COVERS - QUAD BUCKET, 50/50 SPLIT . . 23-146
BENCH - REMOVAL, SEAT BELT BUCKLE - FIRST ROW ....................... 8O-36
BENCH - REMOVAL, SEAT BELT BUCKLE - SECOND ROW - THREE PASSENGER ....8O-40
BENCH - REMOVAL, SEAT BELT BUCKLE - SECOND ROW INBOARD - 50/50 .......8O-37
BENCH - REMOVAL, SEAT CUSHION COVER - QUAD BUCKET, 50/50 SPLIT . . . 23-144
BENCH SEAT - REMOVAL, CHILD SEAT MODULE .......................... 23-104
BENCH SEAT BACK - INSTALLATION .....23-147
BENCH SEAT BACK - REMOVAL ........23-147
BENCH SEAT BACK COVER - INSTALLATION ...................... 23-148
BENCH SEAT BACK COVER - REMOVAL . . 23-148
BENCH SEAT BACK HINGE - REMOVAL . . 23-146
BENCH SEAT BACK PANEL - INSTALLATION ...................... 23-144
BENCH SEAT BACK PANEL - REMOVAL . . 23-143
RS INDEX3
Description Group-Page Description Group-Page Description Group-Page
Page 2307 of 2339
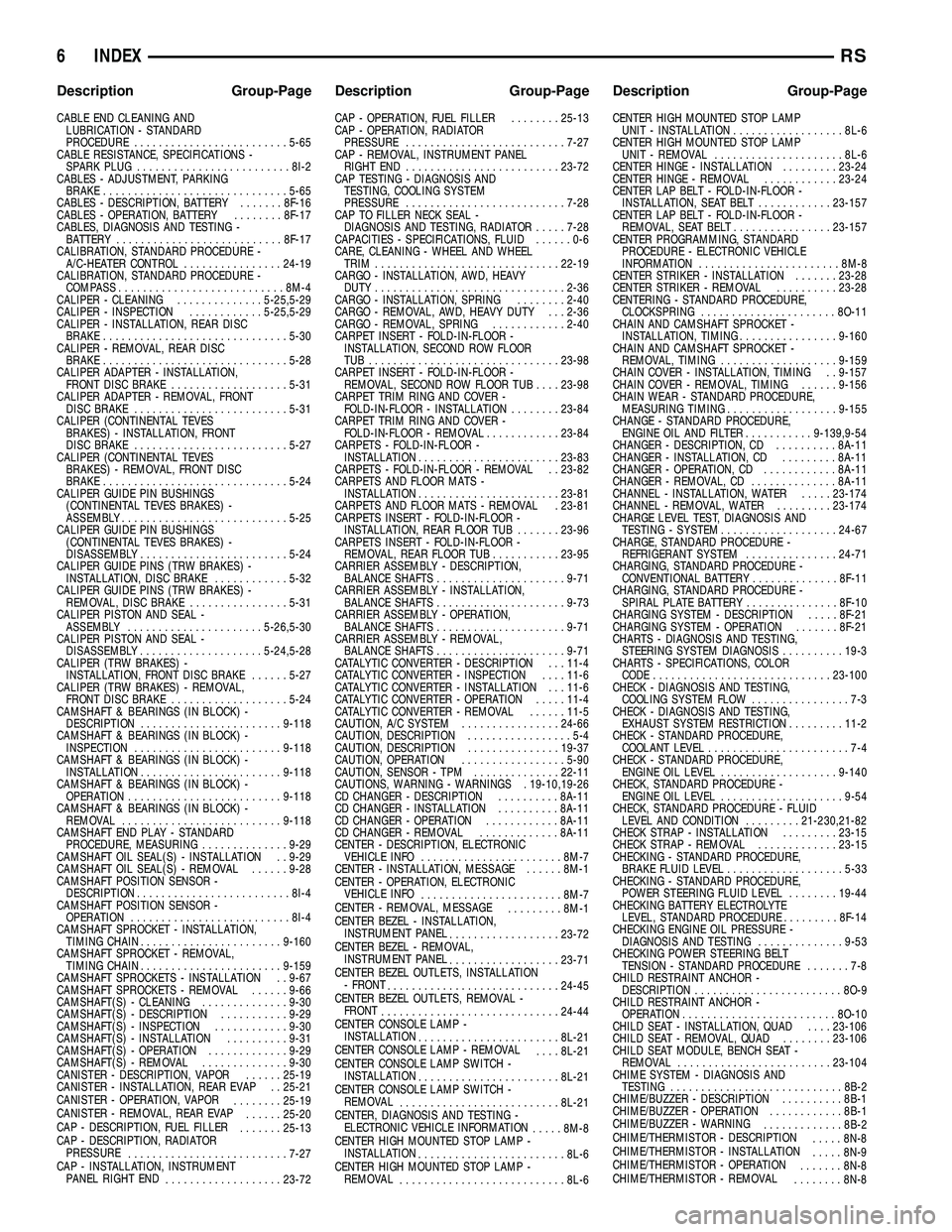
CABLE END CLEANING ANDLUBRICATION - STANDARD
PROCEDURE ......................... 5-65
CABLE RESISTANCE, SPECIFICATIONS - SPARK PLUG ......................... 8I-2
CABLES - ADJUSTMENT, PARKING BRAKE .............................. 5-65
CABLES - DESCRIPTION, BATTERY .......8F-16
CABLES - OPERATION, BATTERY ........8F-17
CABLES, DIAGNOSIS AND TESTING - BATTERY ........................... 8F-17
CALIBRATION, STANDARD PROCEDURE - A/C-HEATER CONTROL ................24-19
CALIBRATION, STANDARD PROCEDURE - COMPASS ........................... 8M-4
CALIPER - CLEANING ..............5-25,5-29
CALIPER - INSPECTION ............5-25,5-29
CALIPER - INSTALLATION, REAR DISC BRAKE .............................. 5-30
CALIPER - REMOVAL, REAR DISC BRAKE .............................. 5-28
CALIPER ADAPTER - INSTALLATION, FRONT DISC BRAKE ................... 5-31
CALIPER ADAPTER - REMOVAL, FRONT DISC BRAKE ......................... 5-31
CALIPER (CONTINENTAL TEVES BRAKES) - INSTALLATION, FRONT
DISC BRAKE ......................... 5-27
CALIPER (CONTINENTAL TEVES BRAKES) - REMOVAL, FRONT DISC
BRAKE .............................. 5-24
CALIPER GUIDE PIN BUSHINGS (CONTINENTAL TEVES BRAKES) -
ASSEMBLY ............................ 5-25
CALIPER GUIDE PIN BUSHINGS (CONTINENTAL TEVES BRAKES) -
DISASSEMBLY ........................ 5-24
CALIPER GUIDE PINS (TRW BRAKES) - INSTALLATION, DISC BRAKE ............5-32
CALIPER GUIDE PINS (TRW BRAKES) - REMOVAL, DISC BRAKE ................5-31
CALIPER PISTON AND SEAL - ASSEMBLY ...................... 5-26,5-30
CALIPER PISTON AND SEAL - DISASSEMBLY .................... 5-24,5-28
CALIPER (TRW BRAKES) - INSTALLATION, FRONT DISC BRAKE ......5-27
CALIPER (TRW BRAKES) - REMOVAL, FRONT DISC BRAKE ................... 5-24
CAMSHAFT & BEARINGS (IN BLOCK) - DESCRIPTION ....................... 9-118
CAMSHAFT & BEARINGS (IN BLOCK) - INSPECTION ........................ 9-118
CAMSHAFT & BEARINGS (IN BLOCK) - INSTALLATION ....................... 9-118
CAMSHAFT & BEARINGS (IN BLOCK) - OPERATION ......................... 9-118
CAMSHAFT & BEARINGS (IN BLOCK) - REMOVAL .......................... 9-118
CAMSHAFT END PLAY - STANDARD PROCEDURE, MEASURING ..............9-29
CAMSHAFT OIL SEAL(S) - INSTALLATION . . 9-29
CAMSHAFT OIL SEAL(S) - REMOVAL ......9-28
CAMSHAFT POSITION SENSOR - DESCRIPTION ......................... 8I-4
CAMSHAFT POSITION SENSOR - OPERATION .......................... 8I-4
CAMSHAFT SPROCKET - INSTALLATION, TIMING CHAIN ....................... 9-160
CAMSHAFT SPROCKET - REMOVAL, TIMING CHAIN ....................... 9-159
CAMSHAFT SPROCKETS - INSTALLATION . . 9-67
CAMSHAFT SPROCKETS - REMOVAL ......9-66
CAMSHAFT(S) - CLEANING ..............9-30
CAMSHAFT(S) - DESCRIPTION ...........9-29
CAMSHAFT(S) - INSPECTION ............9-30
CAMSHAFT(S) - INSTALLATION ..........9-31
CAMSHAFT(S) - OPERATION .............9-29
CAMSHAFT(S) - REMOVAL ..............9-30
CANISTER - DESCRIPTION, VAPOR ......25-19
CANISTER - INSTALLATION, REAR EVAP . . 25-21
CANISTER - OPERATION, VAPOR ........25-19
CANISTER - REMOVAL, REAR EVAP ......25-20
CAP - DESCRIPTION, FUEL FILLER .......25-13
CAP - DESCRIPTION, RADIATOR PRESSURE .......................... 7-27
CAP - INSTALLATION, INSTRUMENT PANEL RIGHT END ................... 23-72CAP - OPERATION, FUEL FILLER
........25-13
CAP - OPERATION, RADIATOR PRESSURE .......................... 7-27
CAP - REMOVAL, INSTRUMENT PANEL RIGHT END ......................... 23-72
CAP TESTING - DIAGNOSIS AND TESTING, COOLING SYSTEM
PRESSURE .......................... 7-28
CAP TO FILLER NECK SEAL - DIAGNOSIS AND TESTING, RADIATOR .....7-28
CAPACITIES - SPECIFICATIONS, FLUID ......0-6
CARE, CLEANING - WHEEL AND WHEEL TRIM .............................. 22-19
CARGO - INSTALLATION, AWD, HEAVY DUTY ............................... 2-36
CARGO - INSTALLATION, SPRING ........2-40
CARGO - REMOVAL, AWD, HEAVY DUTY . . . 2-36
CARGO - REMOVAL, SPRING ............2-40
CARPET INSERT - FOLD-IN-FLOOR - INSTALLATION, SECOND ROW FLOOR
TUB ............................... 23-98
CARPET INSERT - FOLD-IN-FLOOR - REMOVAL, SECOND ROW FLOOR TUB ....23-98
CARPET TRIM RING AND COVER - FOLD-IN-FLOOR - INSTALLATION ........23-84
CARPET TRIM RING AND COVER - FOLD-IN-FLOOR - REMOVAL ............23-84
CARPETS - FOLD-IN-FLOOR - INSTALLATION ....................... 23-83
CARPETS - FOLD-IN-FLOOR - REMOVAL . . 23-82
CARPETS AND FLOOR MATS - INSTALLATION ....................... 23-81
CARPETS AND FLOOR MATS - REMOVAL . 23-81
CARPETS INSERT - FOLD-IN-FLOOR - INSTALLATION, REAR FLOOR TUB .......23-96
CARPETS INSERT - FOLD-IN-FLOOR - REMOVAL, REAR FLOOR TUB ...........23-95
CARRIER ASSEMBLY - DESCRIPTION, BALANCE SHAFTS ..................... 9-71
CARRIER ASSEMBLY - INSTALLATION, BALANCE SHAFTS ..................... 9-73
CARRIER ASSEMBLY - OPERATION, BALANCE SHAFTS ..................... 9-71
CARRIER ASSEMBLY - REMOVAL, BALANCE SHAFTS ..................... 9-71
CATALYTIC CONVERTER - DESCRIPTION . . . 11-4
CATALYTIC CONVERTER - INSPECTION ....11-6
CATALYTIC CONVERTER - INSTALLATION . . . 11-6
CATALYTIC CONVERTER - OPERATION .....11-4
CATALYTIC CONVERTER - REMOVAL ......11-5
CAUTION, A/C SYSTEM ................24-66
CAUTION, DESCRIPTION .................5-4
CAUTION, DESCRIPTION ...............19-37
CAUTION, OPERATION .................5-90
CAUTION, SENSOR - TPM ..............22-11
CAUTIONS, WARNING - WARNINGS . 19-10,19-26
CD CHANGER - DESCRIPTION ..........8A-11
CD CHANGER - INSTALLATION ..........8A-11
CD CHANGER - OPERATION ............8A-11
CD CHANGER - REMOVAL .............8A-11
CENTER - DESCRIPTION, ELECTRONIC VEHICLE INFO ....................... 8M-7
CENTER - INSTALLATION, MESSAGE ......8M-1
CENTER - OPERATION, ELECTRONIC VEHICLE INFO ....................... 8M-7
CENTER - REMOVAL, MESSAGE .........8M-1
CENTER BEZEL - INSTALLATION, INSTRUMENT PANEL .................. 23-72
CENTER BEZEL - REMOVAL, INSTRUMENT PANEL .................. 23-71
CENTER BEZEL OUTLETS, INSTALLATION - FRONT ............................ 24-45
CENTER BEZEL OUTLETS, REMOVAL - FRONT ............................. 24-44
CENTER CONSOLE LAMP - INSTALLATION ....................... 8L-21
CENTER CONSOLE LAMP - REMOVAL ....8L-21
CENTER CONSOLE LAMP SWITCH - INSTALLATION ....................... 8L-21
CENTER CONSOLE LAMP SWITCH - REMOVAL .......................... 8L-21
CENTER, DIAGNOSIS AND TESTING - ELECTRONIC VEHICLE INFORMATION .....8M-8
CENTER HIGH MOUNTED STOP LAMP - INSTALLATION ........................ 8L-6
CENTER HIGH MOUNTED STOP LAMP - REMOVAL ........................... 8L-6CENTER HIGH MOUNTED STOP LAMP
UNIT - INSTALLATION .................. 8L-6
CENTER HIGH MOUNTED STOP LAMP UNIT - REMOVAL ..................... 8L-6
CENTER HINGE - INSTALLATION .........23-24
CENTER HINGE - REMOVAL ............23-24
CENTER LAP BELT - FOLD-IN-FLOOR - INSTALLATION, SEAT BELT ............23-157
CENTER LAP BELT - FOLD-IN-FLOOR - REMOVAL, SEAT BELT ................23-157
CENTER PROGRAMMING, STANDARD PROCEDURE - ELECTRONIC VEHICLE
INFORMATION ....................... 8M-8
CENTER STRIKER - INSTALLATION .......23-28
CENTER STRIKER - REMOVAL ..........23-28
CENTERING - STANDARD PROCEDURE, CLOCKSPRING ...................... 8O-11
CHAIN AND CAMSHAFT SPROCKET - INSTALLATION, TIMING ................9-160
CHAIN AND CAMSHAFT SPROCKET - REMOVAL, TIMING ................... 9-159
CHAIN COVER - INSTALLATION, TIMING . . 9-157
CHAIN COVER - REMOVAL, TIMING ......9-156
CHAIN WEAR - STANDARD PROCEDURE, MEASURING TIMING .................. 9-155
CHANGE - STANDARD PROCEDURE, ENGINE OIL AND FILTER ...........9-139,9-54
CHANGER - DESCRIPTION, CD ..........8A-11
CHANGER - INSTALLATION, CD .........8A-11
CHANGER - OPERATION, CD ............8A-11
CHANGER - REMOVAL, CD ..............8A-11
CHANNEL - INSTALLATION, WATER .....23-174
CHANNEL - REMOVAL, WATER .........23-174
CHARGE LEVEL TEST, DIAGNOSIS AND TESTING - SYSTEM ................... 24-67
CHARGE, STANDARD PROCEDURE - REFRIGERANT SYSTEM ...............24-71
CHARGING, STANDARD PROCEDURE - CONVENTIONAL BATTERY ..............8F-11
CHARGING, STANDARD PROCEDURE - SPIRAL PLATE BATTERY ...............8F-10
CHARGING SYSTEM - DESCRIPTION .....8F-21
CHARGING SYSTEM - OPERATION .......8F-21
CHARTS - DIAGNOSIS AND TESTING, STEERING SYSTEM DIAGNOSIS ..........19-3
CHARTS - SPECIFICATIONS, COLOR CODE ............................. 23-100
CHECK - DIAGNOSIS AND TESTING, COOLING SYSTEM FLOW ................7-3
CHECK - DIAGNOSIS AND TESTING, EXHAUST SYSTEM RESTRICTION .........11-2
CHECK - STANDARD PROCEDURE, COOLANT LEVEL .......................7-4
CHECK - STANDARD PROCEDURE, ENGINE OIL LEVEL ................... 9-140
CHECK, STANDARD PROCEDURE - ENGINE OIL LEVEL .................... 9-54
CHECK, STANDARD PROCEDURE - FLUID LEVEL AND CONDITION .........21-230,21-82
CHECK STRAP - INSTALLATION .........23-15
CHECK STRAP - REMOVAL .............23-15
CHECKING - STANDARD PROCEDURE, BRAKE FLUID LEVEL ................... 5-33
CHECKING - STANDARD PROCEDURE, POWER STEERING FLUID LEVEL ........19-44
CHECKING BATTERY ELECTROLYTE LEVEL, STANDARD PROCEDURE .........8F-14
CHECKING ENGINE OIL PRESSURE - DIAGNOSIS AND TESTING ..............9-53
CHECKING POWER STEERING BELT TENSION - STANDARD PROCEDURE .......7-8
CHILD RESTRAINT ANCHOR - DESCRIPTION ........................ 8O-9
CHILD RESTRAINT ANCHOR - OPERATION ......................... 8O-10
CHILD SEAT - INSTALLATION, QUAD ....23-106
CHILD SEAT - REMOVAL, QUAD ........23-106
CHILD SEAT MODULE, BENCH SEAT - REMOVAL ......................... 23-104
CHIME SYSTEM - DIAGNOSIS AND TESTING ............................ 8B-2
CHIME/BUZZER - DESCRIPTION ..........8B-1
CHIME/BUZZER - OPERATION ............8B-1
CHIME/BUZZER - WARNING .............8B-2
CHIME/THERMISTOR - DESCRIPTION .....8N-8
CHIME/THERMISTOR - INSTALLATION .....8N-9
CHIME/THERMISTOR - OPERATION .......8N-8
CHIME/THERMISTOR - REMOVAL ........8N-8
6 INDEXRS
Description Group-Page Description Group-Page Description Group-Page
Page 2308 of 2339
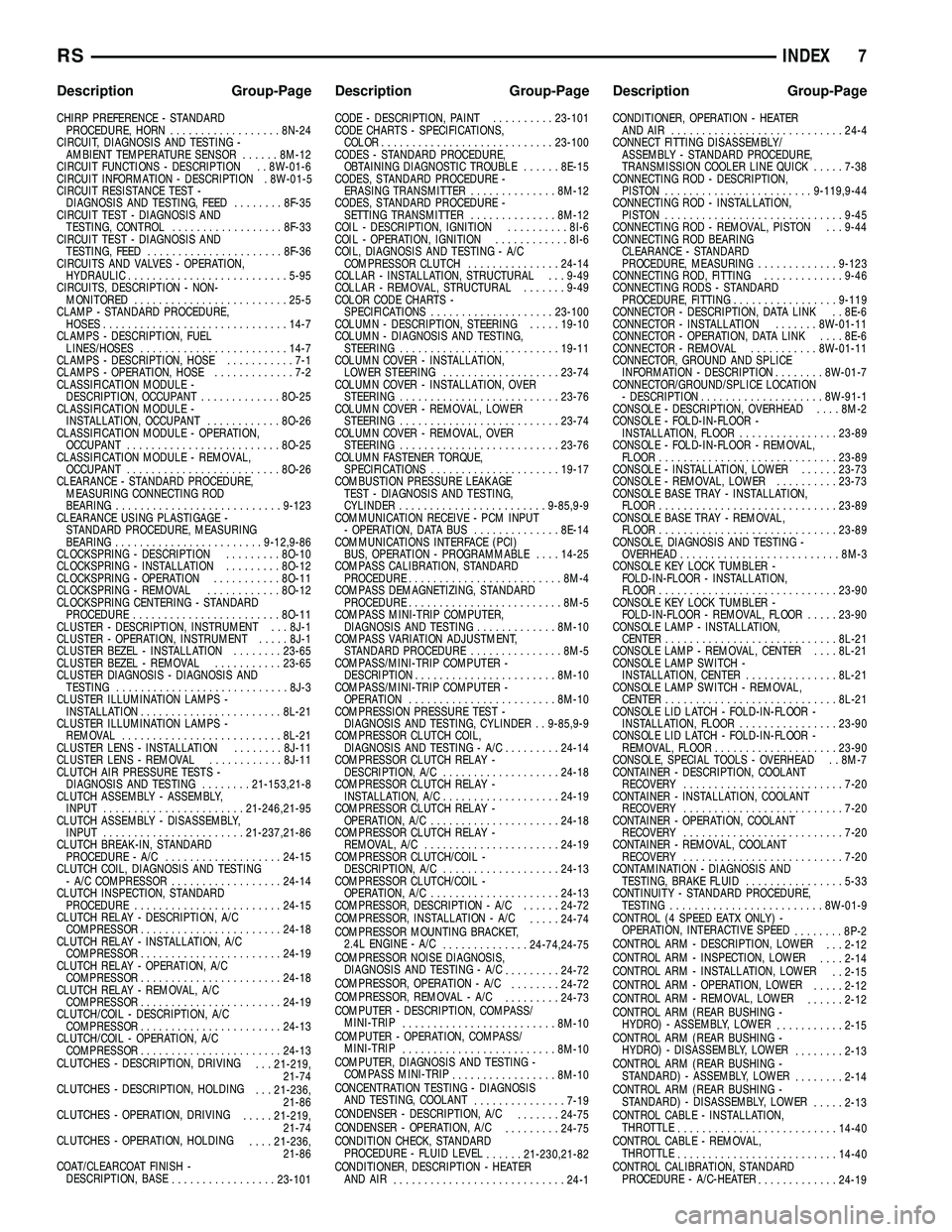
CHIRP PREFERENCE - STANDARDPROCEDURE, HORN .................. 8N-24
CIRCUIT, DIAGNOSIS AND TESTING - AMBIENT TEMPERATURE SENSOR ......8M-12
CIRCUIT FUNCTIONS - DESCRIPTION . . 8W-01-6
CIRCUIT INFORMATION - DESCRIPTION . 8W-01-5
CIRCUIT RESISTANCE TEST - DIAGNOSIS AND TESTING, FEED ........8F-35
CIRCUIT TEST - DIAGNOSIS AND TESTING, CONTROL .................. 8F-33
CIRCUIT TEST - DIAGNOSIS AND TESTING, FEED ...................... 8F-36
CIRCUITS AND VALVES - OPERATION, HYDRAULIC .......................... 5-95
CIRCUITS, DESCRIPTION - NON- MONITORED ......................... 25-5
CLAMP - STANDARD PROCEDURE, HOSES .............................. 14-7
CLAMPS - DESCRIPTION, FUEL LINES/HOSES ........................ 14-7
CLAMPS - DESCRIPTION, HOSE ...........7-1
CLAMPS - OPERATION, HOSE .............7-2
CLASSIFICATION MODULE - DESCRIPTION, OCCUPANT .............8O-25
CLASSIFICATION MODULE - INSTALLATION, OCCUPANT ............8O-26
CLASSIFICATION MODULE - OPERATION, OCCUPANT ......................... 8O-25
CLASSIFICATION MODULE - REMOVAL, OCCUPANT ......................... 8O-26
CLEARANCE - STANDARD PROCEDURE, MEASURING CONNECTING ROD
BEARING ............................ 9-123
CLEARANCE USING PLASTIGAGE - STANDARD PROCEDURE, MEASURING
BEARING ........................ 9-12,9-86
CLOCKSPRING - DESCRIPTION .........8O-10
CLOCKSPRING - INSTALLATION .........8O-12
CLOCKSPRING - OPERATION ...........8O-11
CLOCKSPRING - REMOVAL ............8O-12
CLOCKSPRING CENTERING - STANDARD PROCEDURE ........................ 8O-11
CLUSTER - DESCRIPTION, INSTRUMENT . . . 8J-1
CLUSTER - OPERATION, INSTRUMENT .....8J-1
CLUSTER BEZEL - INSTALLATION ........23-65
CLUSTER BEZEL - REMOVAL ...........23-65
CLUSTER DIAGNOSIS - DIAGNOSIS AND TESTING ............................ 8J-3
CLUSTER ILLUMINATION LAMPS - INSTALLATION ....................... 8L-21
CLUSTER ILLUMINATION LAMPS - REMOVAL .......................... 8L-21
CLUSTER LENS - INSTALLATION ........8J-11
CLUSTER LENS - REMOVAL ............8J-11
CLUTCH AIR PRESSURE TESTS - DIAGNOSIS AND TESTING ........21-153,21-8
CLUTCH ASSEMBLY - ASSEMBLY, INPUT ....................... 21-246,21-95
CLUTCH ASSEMBLY - DISASSEMBLY, INPUT ....................... 21-237,21-86
CLUTCH BREAK-IN, STANDARD PROCEDURE - A/C ................... 24-15
CLUTCH COIL, DIAGNOSIS AND TESTING - A/C COMPRESSOR .................. 24-14
CLUTCH INSPECTION, STANDARD PROCEDURE ........................ 24-15
CLUTCH RELAY - DESCRIPTION, A/C COMPRESSOR ....................... 24-18
CLUTCH RELAY - INSTALLATION, A/C COMPRESSOR ....................... 24-19
CLUTCH RELAY - OPERATION, A/C COMPRESSOR ....................... 24-18
CLUTCH RELAY - REMOVAL, A/C COMPRESSOR ....................... 24-19
CLUTCH/COIL - DESCRIPTION, A/C COMPRESSOR ....................... 24-13
CLUTCH/COIL - OPERATION, A/C COMPRESSOR ....................... 24-13
CLUTCHES - DESCRIPTION, DRIVING . . . 21-219,
21-74
CLUTCHES - DESCRIPTION, HOLDING . . . 21-236,
21-86
CLUTCHES - OPERATION, DRIVING .....21-219,
21-74
CLUTCHES - OPERATION, HOLDING ....21-236,
21-86
COAT/CLEARCOAT FINISH - DESCRIPTION, BASE .................23-101CODE - DESCRIPTION, PAINT
..........23-101
CODE CHARTS - SPECIFICATIONS, COLOR ............................ 23-100
CODES - STANDARD PROCEDURE, OBTAINING DIAGNOSTIC TROUBLE ......8E-15
CODES, STANDARD PROCEDURE - ERASING TRANSMITTER ..............8M-12
CODES, STANDARD PROCEDURE - SETTING TRANSMITTER ..............8M-12
COIL - DESCRIPTION, IGNITION ..........8I-6
COIL - OPERATION, IGNITION ............8I-6
COIL, DIAGNOSIS AND TESTING - A/C COMPRESSOR CLUTCH ...............24-14
COLLAR - INSTALLATION, STRUCTURAL . . . 9-49
COLLAR - REMOVAL, STRUCTURAL .......9-49
COLOR CODE CHARTS - SPECIFICATIONS .................... 23-100
COLUMN - DESCRIPTION, STEERING .....19-10
COLUMN - DIAGNOSIS AND TESTING, STEERING .......................... 19-11
COLUMN COVER - INSTALLATION, LOWER STEERING ................... 23-74
COLUMN COVER - INSTALLATION, OVER STEERING .......................... 23-76
COLUMN COVER - REMOVAL, LOWER STEERING .......................... 23-74
COLUMN COVER - REMOVAL, OVER STEERING .......................... 23-76
COLUMN FASTENER TORQUE, SPECIFICATIONS ..................... 19-17
COMBUSTION PRESSURE LEAKAGE TEST - DIAGNOSIS AND TESTING,
CYLINDER ........................ 9-85,9-9
COMMUNICATION RECEIVE - PCM INPUT - OPERATION, DATA BUS ..............8E-14
COMMUNICATIONS INTERFACE (PCI) BUS, OPERATION - PROGRAMMABLE ....14-25
COMPASS CALIBRATION, STANDARD PROCEDURE ......................... 8M-4
COMPASS DEMAGNETIZING, STANDARD PROCEDURE ......................... 8M-5
COMPASS MINI-TRIP COMPUTER, DIAGNOSIS AND TESTING .............8M-10
COMPASS VARIATION ADJUSTMENT, STANDARD PROCEDURE ...............8M-5
COMPASS/MINI-TRIP COMPUTER - DESCRIPTION ....................... 8M-10
COMPASS/MINI-TRIP COMPUTER - OPERATION ........................ 8M-10
COMPRESSION PRESSURE TEST - DIAGNOSIS AND TESTING, CYLINDER . . 9-85,9-9
COMPRESSOR CLUTCH COIL, DIAGNOSIS AND TESTING - A/ C.........24-14
COMPRESSOR CLUTCH RELAY - DESCRIPTION, A/C ................... 24-18
COMPRESSOR CLUTCH RELAY - INSTALLATION, A/C ................... 24-19
COMPRESSOR CLUTCH RELAY - OPERATION, A/C ..................... 24-18
COMPRESSOR CLUTCH RELAY - REMOVAL, A/C ...................... 24-19
COMPRESSOR CLUTCH/COIL - DESCRIPTION, A/C ................... 24-13
COMPRESSOR CLUTCH/COIL - OPERATION, A/C ..................... 24-13
COMPRESSOR, DESCRIPTION - A/C ......24-72
COMPRESSOR, INSTALLATION - A/C .....24-74
COMPRESSOR MOUNTING BRACKET, 2.4L ENGINE - A/C ..............24-74,24-75
COMPRESSOR NOISE DIAGNOSIS, DIAGNOSIS AND TESTING - A/C .........24-72
COMPRESSOR, OPERATION - A/C ........24-72
COMPRESSOR, REMOVAL - A/C .........24-73
COMPUTER - DESCRIPTION, COMPASS/ MINI-TRIP ......................... 8M-10
COMPUTER - OPERATION, COMPASS/ MINI-TRIP ......................... 8M-10
COMPUTER, DIAGNOSIS AND TESTING - COMPASS MINI-TRIP .................8M-10
CONCENTRATION TESTING - DIAGNOSIS AND TESTING, COOLANT ...............7-19
CONDENSER - DESCRIPTION, A/C .......24-75
CONDENSER - OPERATION, A/C .........24-75
CONDITION CHECK, STANDARD PROCEDURE - FLUID LEVEL ......21-230,21-82
CONDITIONER, DESCRIPTION - HEATER AND AIR ............................ 24-1CONDITIONER, OPERATION - HEATER
AND AIR ............................ 24-4
CONNECT FITTING DISASSEMBLY/ ASSEMBLY - STANDARD PROCEDURE,
TRANSMISSION COOLER LINE QUICK .....7-38
CONNECTING ROD - DESCRIPTION, PISTON ........................ 9-119,9-44
CONNECTING ROD - INSTALLATION, PISTON ............................. 9-45
CONNECTING ROD - REMOVAL, PISTON . . . 9-44
CONNECTING ROD BEARING CLEARANCE - STANDARD
PROCEDURE, MEASURING .............9-123
CONNECTING ROD, FITTING .............9-46
CONNECTING RODS - STANDARD PROCEDURE, FITTING .................9-119
CONNECTOR - DESCRIPTION, DATA LINK . . 8E-6
CONNECTOR - INSTALLATION .......8W-01-11
CONNECTOR - OPERATION, DATA LINK ....8E-6
CONNECTOR - REMOVAL ...........8W-01-11
CONNECTOR, GROUND AND SPLICE INFORMATION - DESCRIPTION ........8W-01-7
CONNECTOR/GROUND/SPLICE LOCATION - DESCRIPTION ....................8W -91-1
CONSOLE - DESCRIPTION, OVERHEAD ....8M-2
CONSOLE - FOLD-IN-FLOOR - INSTALLATION, FLOOR ................23-89
CONSOLE - FOLD-IN-FLOOR - REMOVAL, FLOOR ............................. 23-89
CONSOLE - INSTALLATION, LOWER ......23-73
CONSOLE - REMOVAL, LOWER ..........23-73
CONSOLE BASE TRAY - INSTALLATION, FLOOR ............................. 23-89
CONSOLE BASE TRAY - REMOVAL, FLOOR ............................. 23-89
CONSOLE, DIAGNOSIS AND TESTING - OVERHEAD .......................... 8M-3
CONSOLE KEY LOCK TUMBLER - FOLD-IN-FLOOR - INSTALLATION,
FLOOR ............................. 23-90
CONSOLE KEY LOCK TUMBLER - FOLD-IN-FLOOR - REMOVAL, FLOOR .....23-90
CONSOLE LAMP - INSTALLATION, CENTER ............................ 8L-21
CONSOLE LAMP - REMOVAL, CENTER ....8L-21
CONSOLE LAMP SWITCH - INSTALLATION, CENTER ...............8L-21
CONSOLE LAMP SWITCH - REMOVAL, CENTER ............................ 8L-21
CONSOLE LID LATCH - FOLD-IN-FLOOR - INSTALLATION, FLOOR ................23-90
CONSOLE LID LATCH - FOLD-IN-FLOOR - REMOVAL, FLOOR .................... 23-90
CONSOLE, SPECIAL TOOLS - OVERHEAD . . 8M-7
CONTAINER - DESCRIPTION, COOLANT RECOVERY .......................... 7-20
CONTAINER - INSTALLATION, COOLANT RECOVERY .......................... 7-20
CONTAINER - OPERATION, COOLANT RECOVERY .......................... 7-20
CONTAINER - REMOVAL, COOLANT RECOVERY .......................... 7-20
CONTAMINATION - DIAGNOSIS AND TESTING, BRAKE FLUID ................5-33
CONTINUITY - STANDARD PROCEDURE, TESTING .........................8W -01-9
CONTROL (4 SPEED EATX ONLY) - OPERATION, INTERACTIVE SPEED ........8P-2
CONTROL ARM - DESCRIPTION, LOWER . . . 2-12
CONTROL ARM - INSPECTION, LOWER ....2-14
CONTROL ARM - INSTALLATION, LOWER . . 2-15
CONTROL ARM - OPERATION, LOWER .....2-12
CONTROL ARM - REMOVAL, LOWER ......2-12
CONTROL ARM (REAR BUSHING - HYDRO) - ASSEMBLY, LOWER ...........2-15
CONTROL ARM (REAR BUSHING - HYDRO) - DISASSEMBLY, LOWER ........2-13
CONTROL ARM (REAR BUSHING - STANDARD) - ASSEMBLY, LOWER ........2-14
CONTROL ARM (REAR BUSHING - STANDARD) - DISASSEMBLY, LOWER .....2-13
CONTROL CABLE - INSTALLATION, THROTTLE .......................... 14-40
CONTROL CABLE - REMOVAL, THROTTLE .......................... 14-40
CONTROL CALIBRATION, STANDARD PROCEDURE - A/C-HEATER .............24-19
RS INDEX7
Description Group-Page Description Group-Page Description Group-Page
Page 2309 of 2339
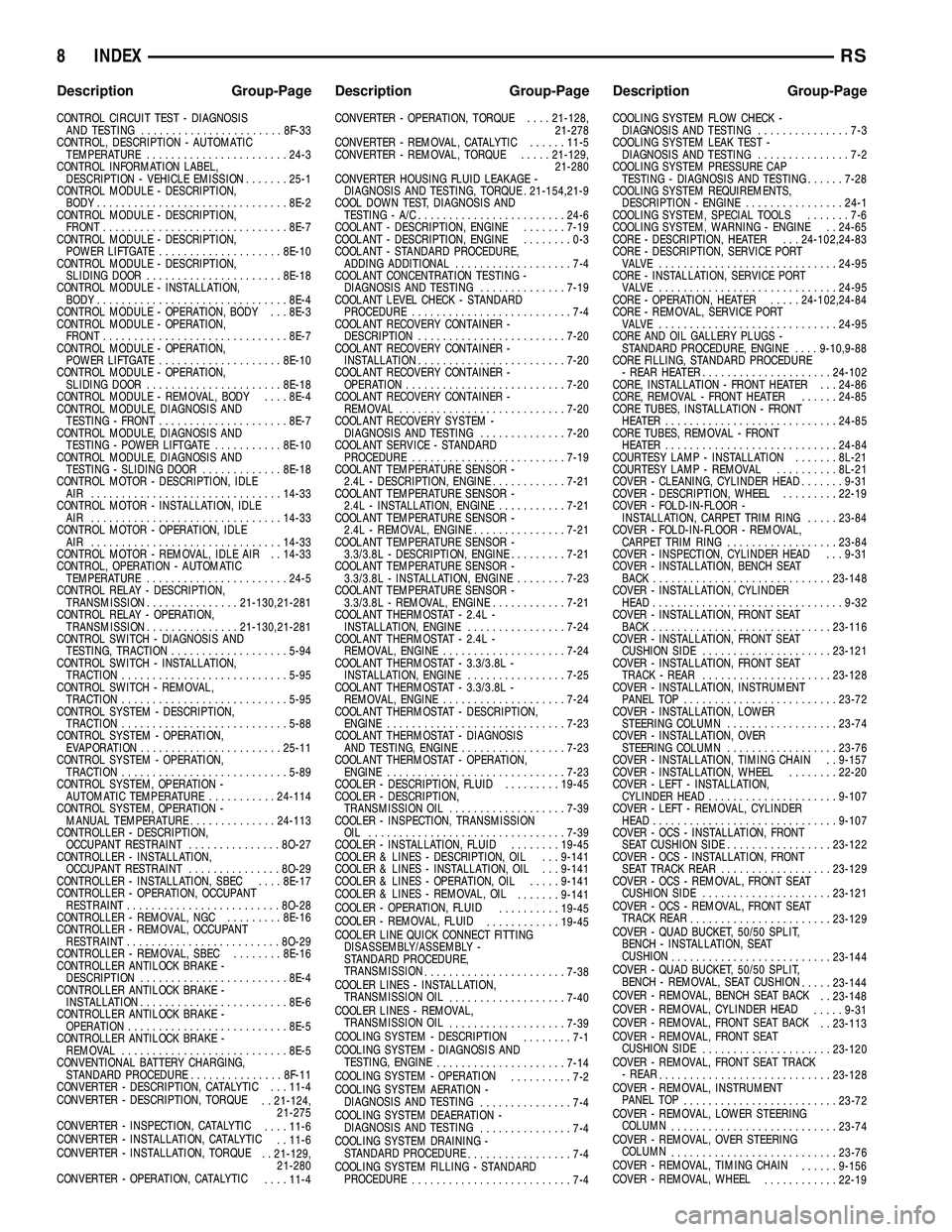
CONTROL CIRCUIT TEST - DIAGNOSISAND TESTING ....................... 8F-33
CONTROL, DESCRIPTION - AUTOMATIC TEMPERATURE ....................... 24-3
CONTROL INFORMATION LABEL, DESCRIPTION - VEHICLE EMISSION .......25-1
CONTROL MODULE - DESCRIPTION, BODY ............................... 8E-2
CONTROL MODULE - DESCRIPTION, FRONT .............................. 8E-7
CONTROL MODULE - DESCRIPTION, POWER LIFTGATE .................... 8E-10
CONTROL MODULE - DESCRIPTION, SLIDING DOOR ...................... 8E-18
CONTROL MODULE - INSTALLATION, BODY ............................... 8E-4
CONTROL MODULE - OPERATION, BODY . . . 8E-3
CONTROL MODULE - OPERATION, FRONT .............................. 8E-7
CONTROL MODULE - OPERATION, POWER LIFTGATE .................... 8E-10
CONTROL MODULE - OPERATION, SLIDING DOOR ...................... 8E-18
CONTROL MODULE - REMOVAL, BODY ....8E-4
CONTROL MODULE, DIAGNOSIS AND TESTING - FRONT ..................... 8E-7
CONTROL MODULE, DIAGNOSIS AND TESTING - POWER LIFTGATE ...........8E-10
CONTROL MODULE, DIAGNOSIS AND TESTING - SLIDING DOOR .............8E-18
CONTROL MOTOR - DESCRIPTION, IDLE AIR ............................... 14-33
CONTROL MOTOR - INSTALLATION, IDLE AIR ............................... 14-33
CONTROL MOTOR - OPERATION, IDLE AIR ............................... 14-33
CONTROL MOTOR - REMOVAL, IDLE AIR . . 14-33
CONTROL, OPERATION - AUTOMATIC TEMPERATURE ....................... 24-5
CONTROL RELAY - DESCRIPTION, TRANSMISSION ............... 21-130,21-281
CONTROL RELAY - OPERATION, TRANSMISSION ............... 21-130,21-281
CONTROL SWITCH - DIAGNOSIS AND TESTING, TRACTION ................... 5-94
CONTROL SWITCH - INSTALLATION, TRACTION ........................... 5-95
CONTROL SWITCH - REMOVAL, TRACTION ........................... 5-95
CONTROL SYSTEM - DESCRIPTION, TRACTION ........................... 5-88
CONTROL SYSTEM - OPERATION, EVAPORATION ....................... 25-11
CONTROL SYSTEM - OPERATION, TRACTION ........................... 5-89
CONTROL SYSTEM, OPERATION - AUTOMATIC TEMPERATURE ...........24-114
CONTROL SYSTEM, OPERATION - MANUAL TEMPERATURE ..............24-113
CONTROLLER - DESCRIPTION, OCCUPANT RESTRAINT ...............8O-27
CONTROLLER - INSTALLATION, OCCUPANT RESTRAINT ...............8O-29
CONTROLLER - INSTALLATION, SBEC ....8E-17
CONTROLLER - OPERATION, OCCUPANT RESTRAINT ......................... 8O-28
CONTROLLER - REMOVAL, NGC .........8E-16
CONTROLLER - REMOVAL, OCCUPANT RESTRAINT ......................... 8O-29
CONTROLLER - REMOVAL, SBEC ........8E-16
CONTROLLER ANTILOCK BRAKE - DESCRIPTION ........................ 8E-4
CONTROLLER ANTILOCK BRAKE - INSTALLATION ........................ 8E-6
CONTROLLER ANTILOCK BRAKE - OPERATION .......................... 8E-5
CONTROLLER ANTILOCK BRAKE - REMOVAL ........................... 8E-5
CONVENTIONAL BATTERY CHARGING, STANDARD PROCEDURE ...............8F-11
CONVERTER - DESCRIPTION, CATALYTIC . . . 11-4
CONVERTER - DESCRIPTION, TORQUE . . 21-124,
21-275
CONVERTER - INSPECTION, CATALYTIC ....11-6
CONVERTER - INSTALLATION, CATALYTIC . . 11-6
CONVERTER - INSTALLATION, TORQUE . . 21-129,
21-280
CONVERTER - OPERATION, CATALYTIC ....11-4 CONVERTER - OPERATION, TORQUE
....21-128,
21-278
CONVERTER - REMOVAL, CATALYTIC ......11-5
CONVERTER - REMOVAL, TORQUE .....21-129,
21-280
CONVERTER HOUSING FLUID LEAKAGE - DIAGNOSIS AND TESTING, TORQUE . 21-154,21-9
COOL DOWN TEST, DIAGNOSIS AND TESTING - A/C ........................ 24-6
COOLANT - DESCRIPTION, ENGINE .......7-19
COOLANT - DESCRIPTION, ENGINE ........0-3
COOLANT - STANDARD PROCEDURE, ADDING ADDITIONAL ...................7-4
COOLANT CONCENTRATION TESTING - DIAGNOSIS AND TESTING ..............7-19
COOLANT LEVEL CHECK - STANDARD PROCEDURE ..........................7-4
COOLANT RECOVERY CONTAINER - DESCRIPTION ........................ 7-20
COOLANT RECOVERY CONTAINER - INSTALLATION ........................ 7-20
COOLANT RECOVERY CONTAINER - OPERATION .......................... 7-20
COOLANT RECOVERY CONTAINER - REMOVAL ........................... 7-20
COOLANT RECOVERY SYSTEM - DIAGNOSIS AND TESTING ..............7-20
COOLANT SERVICE - STANDARD PROCEDURE ......................... 7-19
COOLANT TEMPERATURE SENSOR - 2.4L - DESCRIPTION, ENGINE ............7-21
COOLANT TEMPERATURE SENSOR - 2.4L - INSTALLATION, ENGINE .............7-21
COOLANT TEMPERATURE SENSOR - 2.4L - REMOVAL, ENGINE ...............7-21
COOLANT TEMPERATURE SENSOR - 3.3/3.8L - DESCRIPTION, ENGINE .........7-21
COOLANT TEMPERATURE SENSOR - 3.3/3.8L - INSTALLATION, ENGINE ........7-23
COOLANT TEMPERATURE SENSOR - 3.3/3.8L - REMOVAL, ENGINE ............7-21
COOLANT THERMOSTAT - 2.4L - INSTALLATION, ENGINE ................7-24
COOLANT THERMOSTAT - 2.4L - REMOVAL, ENGINE .................... 7-24
COOLANT THERMOSTAT - 3.3/3.8L - INSTALLATION, ENGINE ................7-25
COOLANT THERMOSTAT - 3.3/3.8L - REMOVAL, ENGINE .................... 7-24
COOLANT THERMOSTAT - DESCRIPTION, ENGINE ............................. 7-23
COOLANT THERMOSTAT - DIAGNOSIS AND TESTING, ENGINE .................7-23
COOLANT THERMOSTAT - OPERATION, ENGINE ............................. 7-23
COOLER - DESCRIPTION, FLUID .........19-45
COOLER - DESCRIPTION, TRANSMISSION OIL ................... 7-39
COOLER - INSPECTION, TRANSMISSION OIL ................................ 7-39
COOLER - INSTALLATION, FLUID ........19-45
COOLER & LINES - DESCRIPTION, OIL . . . 9-141
COOLER & LINES - INSTALLATION, OIL . . . 9-141
COOLER & LINES - OPERATION, OIL .....9-141
COOLER & LINES - REMOVAL, OIL .......9-141
COOLER - OPERATION, FLUID ..........19-45
COOLER - REMOVAL, FLUID ............19-45
COOLER LINE QUICK CONNECT FITTING DISASSEMBLY/ASSEMBLY -
STANDARD PROCEDURE,
TRANSMISSION ....................... 7-38
COOLER LINES - INSTALLATION, TRANSMISSION OIL ................... 7-40
COOLER LINES - REMOVAL, TRANSMISSION OIL ................... 7-39
COOLING SYSTEM - DESCRIPTION ........7-1
COOLING SYSTEM - DIAGNOSIS AND TESTING, ENGINE ..................... 7-14
COOLING SYSTEM - OPERATION ..........7-2
COOLING SYSTEM AERATION - DIAGNOSIS AND TESTING ...............7-4
COOLING SYSTEM DEAERATION - DIAGNOSIS AND TESTING ...............7-4
COOLING SYSTEM DRAINING - STANDARD PROCEDURE .................7-4
COOLING SYSTEM FILLING - STANDARD PROCEDURE ..........................7-4 COOLING SYSTEM FLOW CHECK -
DIAGNOSIS AND TESTING ...............7-3
COOLING SYSTEM LEAK TEST - DIAGNOSIS AND TESTING ...............7-2
COOLING SYSTEM PRESSURE CAP TESTING - DIAGNOSIS AND TESTING ......7-28
COOLING SYSTEM REQUIREMENTS, DESCRIPTION - ENGINE ................24-1
COOLING SYSTEM, SPECIAL TOOLS .......7-6
COOLING SYSTEM, WARNING - ENGINE . . 24-65
CORE - DESCRIPTION, HEATER . . . 24-102,24-83
CORE - DESCRIPTION, SERVICE PORT VALVE ............................. 24-95
CORE - INSTALLATION, SERVICE PORT VALVE ............................. 24-95
CORE - OPERATION, HEATER .....24-102,24-84
CORE - REMOVAL, SERVICE PORT VALVE ............................. 24-95
CORE AND OIL GALLERY PLUGS - STANDARD PROCEDURE, ENGINE ....9-10,9-88
CORE FILLING, STANDARD PROCEDURE - REAR HEATER ..................... 24-102
CORE, INSTALLATION - FRONT HEATER . . . 24-86
CORE, REMOVAL - FRONT HEATER ......24-85
CORE TUBES, INSTALLATION - FRONT HEATER ............................ 24-85
CORE TUBES, REMOVAL - FRONT HEATER ............................ 24-84
COURTESY LAMP - INSTALLATION .......8L-21
COURTESY LAMP - REMOVAL ..........8L-21
COVER - CLEANING, CYLINDER HEAD .......9-31
COVER - DESCRIPTION, WHEEL .........22-19
COVER - FOLD-IN-FLOOR - INSTALLATION, CARPET TRIM RING .....23-84
COVER - FOLD-IN-FLOOR - REMOVAL, CARPET TRIM RING .................. 23-84
COVER - INSPECTION, CYLINDER HEAD . . . 9-31
COVER - INSTALLATION, BENCH SEAT BACK ............................. 23-148
COVER - INSTALLATION, CYLINDER HEAD ............................... 9-32
COVER - INSTALLATION, FRONT SEAT BACK ............................. 23-116
COVER - INSTALLATION, FRONT SEAT CUSHION SIDE ..................... 23-121
COVER - INSTALLATION, FRONT SEAT TRACK - REAR ..................... 23-128
COVER - INSTALLATION, INSTRUMENT PANEL TOP ......................... 23-72
COVER - INSTALLATION, LOWER STEERING COLUMN .................. 23-74
COVER - INSTALLATION, OVER STEERING COLUMN .................. 23-76
COVER - INSTALLATION, TIMING CHAIN . . 9-157
COVER - INSTALLATION, WHEEL ........22-20
COVER - LEFT - INSTALLATION, CYLINDER HEAD ..................... 9-107
COVER - LEFT - REMOVAL, CYLINDER HEAD .............................. 9-107
COVER - OCS - INSTALLATION, FRONT SEAT CUSHION SIDE .................23-122
COVER - OCS - INSTALLATION, FRONT SEAT TRACK REAR .................. 23-129
COVER - OCS - REMOVAL, FRONT SEAT CUSHION SIDE ..................... 23-121
COVER - OCS - REMOVAL, FRONT SEAT TRACK REAR ....................... 23-129
COVER - QUAD BUCKET, 50/50 SPLIT, BENCH - INSTALLATION, SEAT
CUSHION .......................... 23-144
COVER - QUAD BUCKET, 50/50 SPLIT, BENCH - REMOVAL, SEAT CUSHION .....23-144
COVER - REMOVAL, BENCH SEAT BACK . . 23-148
COVER - REMOVAL, CYLINDER HEAD .....9-31
COVER - REMOVAL, FRONT SEAT BACK . . 23-113
COVER - REMOVAL, FRONT SEAT CUSHION SIDE ..................... 23-120
COVER - REMOVAL, FRONT SEAT TRACK - REAR ............................ 23-128
COVER - REMOVAL, INSTRUMENT PANEL TOP ......................... 23-72
COVER - REMOVAL, LOWER STEERING COLUMN ........................... 23-74
COVER - REMOVAL, OVER STEERING COLUMN ........................... 23-76
COVER - REMOVAL, TIMING CHAIN ......9-156
COVER - REMOVAL, WHEEL ............22-19
8 INDEXRS
Description Group-Page Description Group-Page Description Group-Page