check engine light DATSUN 610 1969 Workshop Manual
[x] Cancel search | Manufacturer: DATSUN, Model Year: 1969, Model line: 610, Model: DATSUN 610 1969Pages: 171, PDF Size: 10.63 MB
Page 6 of 171
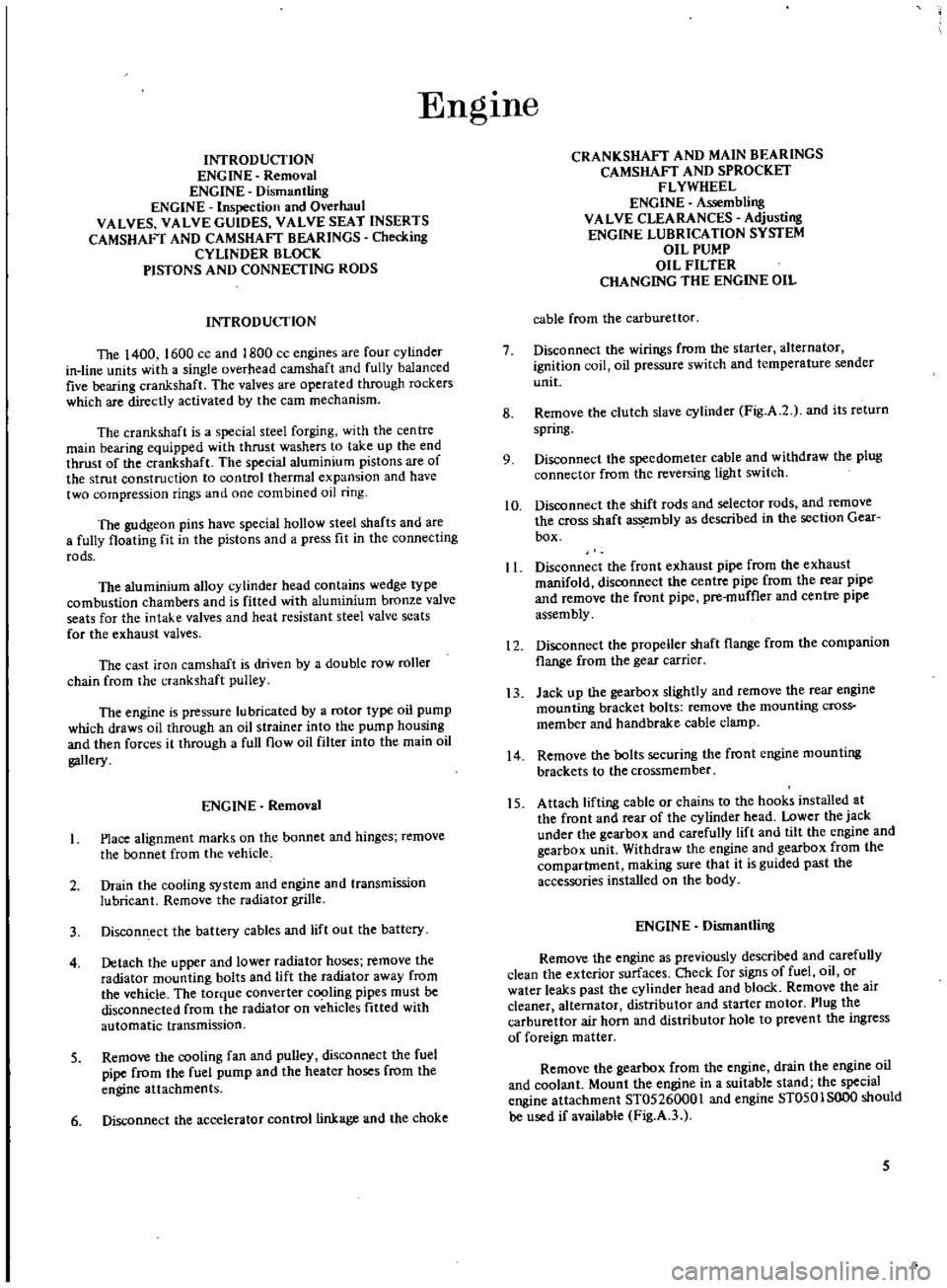
EngIne
INTRODUCTION
ENGINE
Removal
ENGINE
DismantUng
ENGINE
Inspection
and
Overhaul
VALVES
VALVE
GUIDES
VALVE
SEAT
INSERTS
CAMSHAFT
AND
CAMSHAFT
BEARINGS
Checking
CYliNDER
BLOCK
PtSTONS
AND
CONNECTING
RODS
INTRODUCTION
The
1400
1600
cc
and
1800
cc
engines
are
four
cylinder
in
line
units
with
a
single
overhead
camshaft
and
fully
balanced
five
bearing
crankshaft
The
valves
are
operated
through
rockers
which
are
directly
activated
by
the
earn
mechanism
The
crankshaft
is
a
special
steel
forging
with
the
centre
main
bearing
equipped
with
thrust
washers
to
take
up
the
end
thrust
of
the
crankshaft
The
special
aluminium
pistons
are
of
the
strut
construction
to
control
thermal
expansion
and
have
two
compression
rings
and
one
combined
oil
ring
The
gudgeon
pins
have
special
hollow
steel
shafts
and
are
a
fully
floating
fit
in
the
pistons
and
a
press
fit
in
the
connecting
rods
The
aluminium
alloy
cylinder
head
contains
wedge
type
combustion
chambers
and
is
fitted
with
aluminium
bronze
valve
seats
for
the
intake
valves
and
heat
resistant
steel
valve
seats
for
the
exhaust
valves
The
cast
iron
camshaft
is
driven
by
a
double
row
roller
chain
from
the
crankshaft
pulley
The
engine
is
pressure
lubricated
by
a
rotor
type
oil
pump
which
draws
oil
through
an
oil
strainer
into
the
pump
housing
and
then
forces
it
through
a
full
flow
oil
filter
into
the
main
oil
gallery
ENGINE
Removal
Place
alignment
marks
on
the
bonnet
and
hinges
remove
the
bonnet
from
the
vehicle
2
Drain
the
cooling
system
and
engine
and
transmission
lubricant
Remove
the
radiator
grille
3
Discon
ect
the
battery
cables
and
lift
out
the
battery
4
Detach
the
upper
and
lower
radiator
hoses
remove
the
radiator
mounting
bolts
and
lift
the
radiator
away
from
the
vehicle
The
torque
converter
c
jng
pipes
must
be
disconnected
from
the
radiator
on
vehicles
fitted
with
automatic
transmission
S
Remove
the
COOling
fan
and
pulley
disconnect
the
fuel
pipe
from
the
fuel
pump
and
the
heater
hoses
from
the
engine
attachments
6
Disconnect
the
accelerator
control
linkage
and
the
choke
CRANKSHAFT
AND
MAIN
BEARINGS
CAMSHAFT
AND
SPROCKET
FLYWHEEL
ENGINE
Assembling
VALVE
CLEARANCES
Adjusting
ENGINE
LUBRICATION
SYSTEM
OIL
PUMP
OIL
FILTER
CHANGING
THE
ENGINE
OIL
cable
from
the
carburettor
7
Disconnect
the
wirings
from
the
starter
alternator
ignition
coil
oil
pressure
switch
and
temperature
sender
unit
8
Remove
the
clutch
slave
cylinder
Fig
A
2
and
its
return
spring
9
Disconnect
the
speedometer
cable
and
withdraw
the
plug
connector
from
the
reversing
light
switch
10
Disconnect
the
shift
rods
and
seJector
rods
and
remove
the
cross
shaft
assembly
as
described
in
the
section
Gear
box
II
Disconnect
the
front
exhaust
pipe
from
the
exhaust
manifold
disconnect
the
centre
pipe
from
the
rear
pipe
and
remove
the
front
pipe
pre
muffler
and
centre
pipe
assembly
12
Disconnect
the
propeUer
shaft
flange
from
the
companion
flange
from
the
gear
carrier
13
Jack
up
the
gearbox
slightly
and
remove
the
rear
engine
mounting
bracket
bolts
remove
the
mounting
cross
member
and
handbrake
cable
c1amp
14
Remove
the
bolts
securing
the
front
engine
mounting
brackets
to
the
crossmember
15
Attach
lifting
cable
or
chains
to
the
hooks
installed
at
the
front
and
rear
of
the
cylinder
head
Lower
the
jack
under
the
gearbox
and
carefully
lift
and
tilt
the
engine
and
gearbox
unit
Withdraw
the
engine
and
gearbox
from
the
compartment
making
sure
that
it
is
guided
past
the
accessories
installed
on
the
body
ENGINE
Dismantling
Remove
the
engine
as
previously
described
and
carefully
clean
the
exterior
surfaces
Cbeck
for
signs
of
fuel
oil
or
water
leaks
past
the
cylinder
head
and
block
Remove
the
air
cleaner
alternator
distributor
and
starter
motor
Plug
the
carburettor
air
horn
and
distributor
hole
to
prevent
the
ingress
of
foreign
matter
Remove
the
gearbox
from
the
engine
drain
the
engine
oil
and
coolant
Mount
the
engine
in
a
suitable
stand
the
special
engine
attachment
ST05260001
and
engine
ST0501SOO0
should
be
used
if
available
Fig
A
3
5
Page 30 of 171
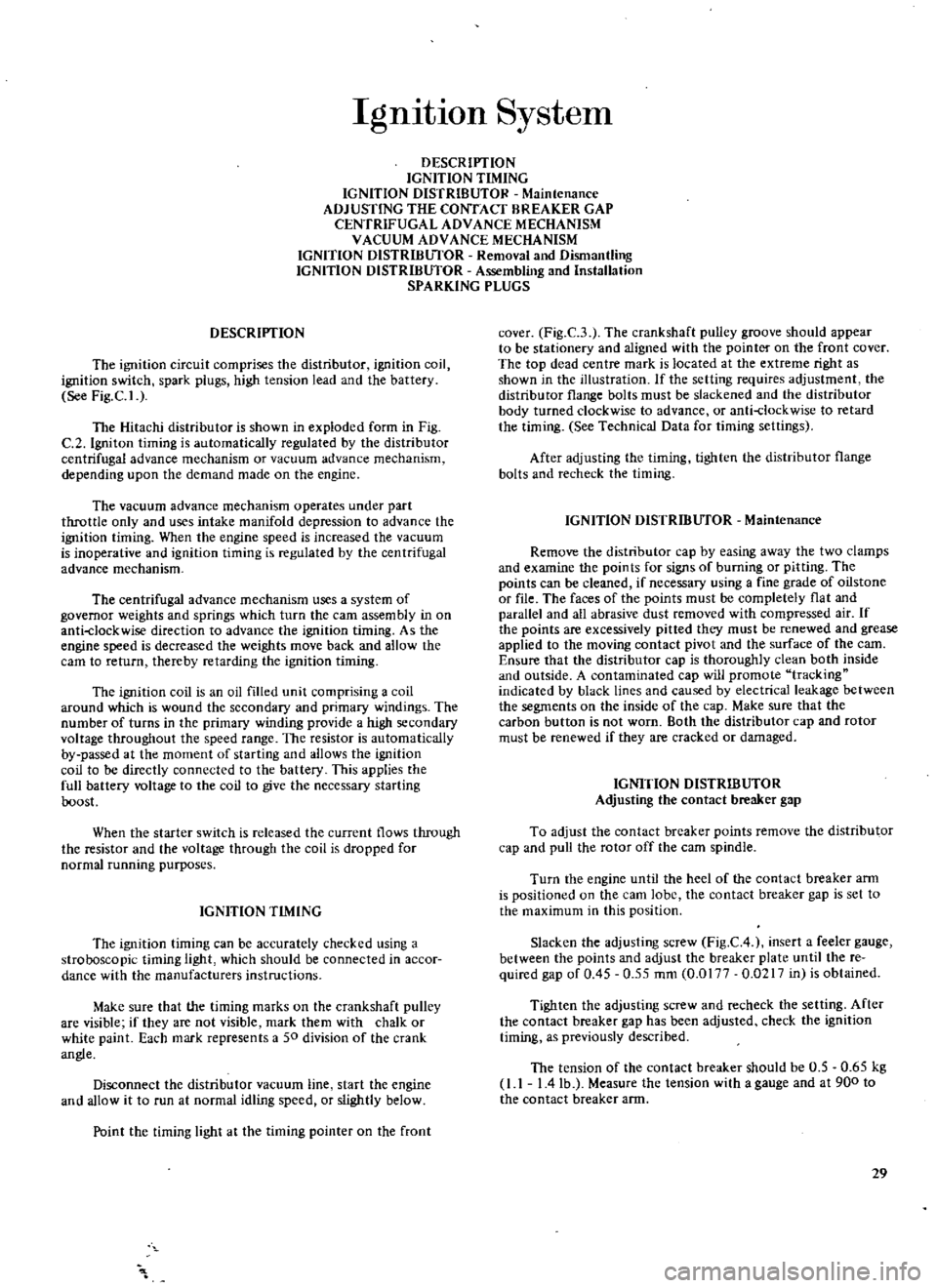
IgnItIon
System
DESCRII
TION
IGNITION
TIMING
IGNITION
DISTRIBUTOR
Maintenance
ADJUSTING
THE
CONTACT
BREAKER
GAP
CENTRIFUGAL
ADVANCE
MECHANISM
VACUUM
ADVANCE
MECHANISM
IGNITION
DISTRIBUTOR
Removal
and
Dismantling
IGNITION
DISTRIBUTOR
Assembling
and
Installation
SPARKING
PLUGS
DESCRII
TION
The
ignition
circuit
comprises
the
distributor
ignition
coil
ignition
switch
spark
plugs
high
tension
lead
and
the
battery
See
Fig
C
1
The
Hitachi
distributor
is
shown
in
exploded
form
in
Fig
C
2
19niton
timing
is
automatically
regulated
by
the
distributor
centrifugal
advance
mechanism
or
vacuum
advance
mechanism
depending
upon
the
demand
made
on
the
engine
The
vacuum
advance
mechanism
operates
under
part
throttle
only
and
uses
intake
manifold
depression
to
advance
the
ignition
timing
When
the
engine
speed
is
increased
the
vacuum
is
inoperative
and
ignition
timing
is
regulated
by
the
centrifugal
advance
mechanism
The
centrifugal
advance
mechanism
uses
a
system
of
governor
weights
and
springs
which
turn
the
carn
assembly
in
on
anti
clockwise
direction
to
advance
the
ignition
timing
As
the
engine
speed
is
decreased
the
weights
move
back
and
allow
the
cam
to
return
thereby
retarding
the
ignition
timing
The
ignition
coil
is
an
oil
filled
unit
comprising
a
coil
around
which
is
wound
the
secondary
and
primary
windings
The
number
of
turns
in
the
primary
winding
provide
a
high
secondary
voltage
throughout
the
speed
range
The
resistor
is
automatically
by
passed
at
the
moment
of
starting
and
allows
the
ignition
coil
to
be
directly
connected
to
the
battery
This
applies
the
full
battery
voltage
to
the
coil
to
give
the
necessary
staTting
boost
When
the
starter
switch
is
released
the
current
flows
through
the
resistor
and
the
voltage
through
the
coil
is
dropped
for
normal
running
purposes
IGNITION
TIMING
The
ignition
timing
can
be
accurately
checked
using
a
stroboscopic
timing
light
which
should
be
connected
in
accor
dance
with
the
manufacturers
instructions
Make
sure
that
the
timing
marks
on
the
crankshaft
pulley
are
visible
if
they
are
not
visible
mark
them
with
chalk
or
white
paint
Each
mark
represents
a
50
division
of
the
crank
angle
Disconnect
the
distributor
vacuum
line
start
the
engine
and
allow
it
to
run
at
normal
idling
speed
or
slightly
below
Point
the
timing
light
at
the
timing
pointer
on
the
front
cover
Fig
C
3
The
crankshaft
pulley
groove
should
appear
to
be
stationery
and
aligned
with
the
pointer
on
the
front
cover
The
top
dead
centre
mark
is
located
at
the
extreme
right
as
shown
in
the
illustration
If
the
setting
requires
adjustment
the
distributor
flange
bolts
must
be
slackened
and
the
distributor
body
turned
clockwise
to
advance
or
anti
clockwise
to
retard
the
timing
See
Technical
Data
for
timing
settings
After
adjusting
the
timing
tighten
the
distributor
flange
bolts
and
recheck
the
timing
IGNITION
DISTRIBUTOR
Maintenance
Remove
the
distributor
cap
by
easing
away
the
two
clamps
and
examine
the
points
for
signs
of
burning
or
pitting
The
points
can
be
cleaned
if
necessary
using
a
fine
grade
of
oilstone
or
file
The
faces
of
the
points
must
be
completely
flat
and
parallel
and
all
abrasive
dust
removed
with
compressed
air
If
the
points
are
excessively
pitted
they
must
be
renewed
and
grease
applied
to
the
moving
contact
pivot
and
the
surface
of
the
cam
Ensure
that
the
distributor
cap
is
thoroughly
clean
both
inside
and
outside
A
contaminated
cap
will
promote
tracking
indicated
by
black
lines
and
caused
by
electrical
leakage
between
the
segments
on
the
inside
of
the
cap
Make
sure
that
the
carbon
button
is
not
worn
Both
the
distributor
cap
and
rotor
must
be
renewed
if
they
are
cracked
or
damaged
IGNITION
DISTRIBUTOR
Adjusting
the
contact
breaker
gap
To
adjust
the
contact
breaker
points
remove
the
distributor
cap
and
pull
the
rotor
off
the
cam
spindle
Turn
the
engine
until
the
heel
of
the
contact
breaker
arm
is
positioned
on
the
cam
lobe
the
contact
breaker
gap
is
set
to
the
maximum
in
this
position
Slacken
the
adjusting
screw
Fig
CA
insert
a
feeler
gauge
between
the
points
and
adjust
the
breaker
plate
until
the
re
quired
gap
of
0
45
0
55
mm
0
0177
0
0217
in
is
obtained
Tighten
the
adjusting
screw
and
recheck
the
setting
After
the
contact
breaker
gap
has
been
adjusted
check
the
ignition
timing
as
previously
described
The
tension
of
the
contact
breaker
should
be
0
5
0
65
kg
I
I
I
4
lb
Measure
the
tension
with
a
gauge
and
at
900
to
the
contact
breaker
arm
29
Page 32 of 171
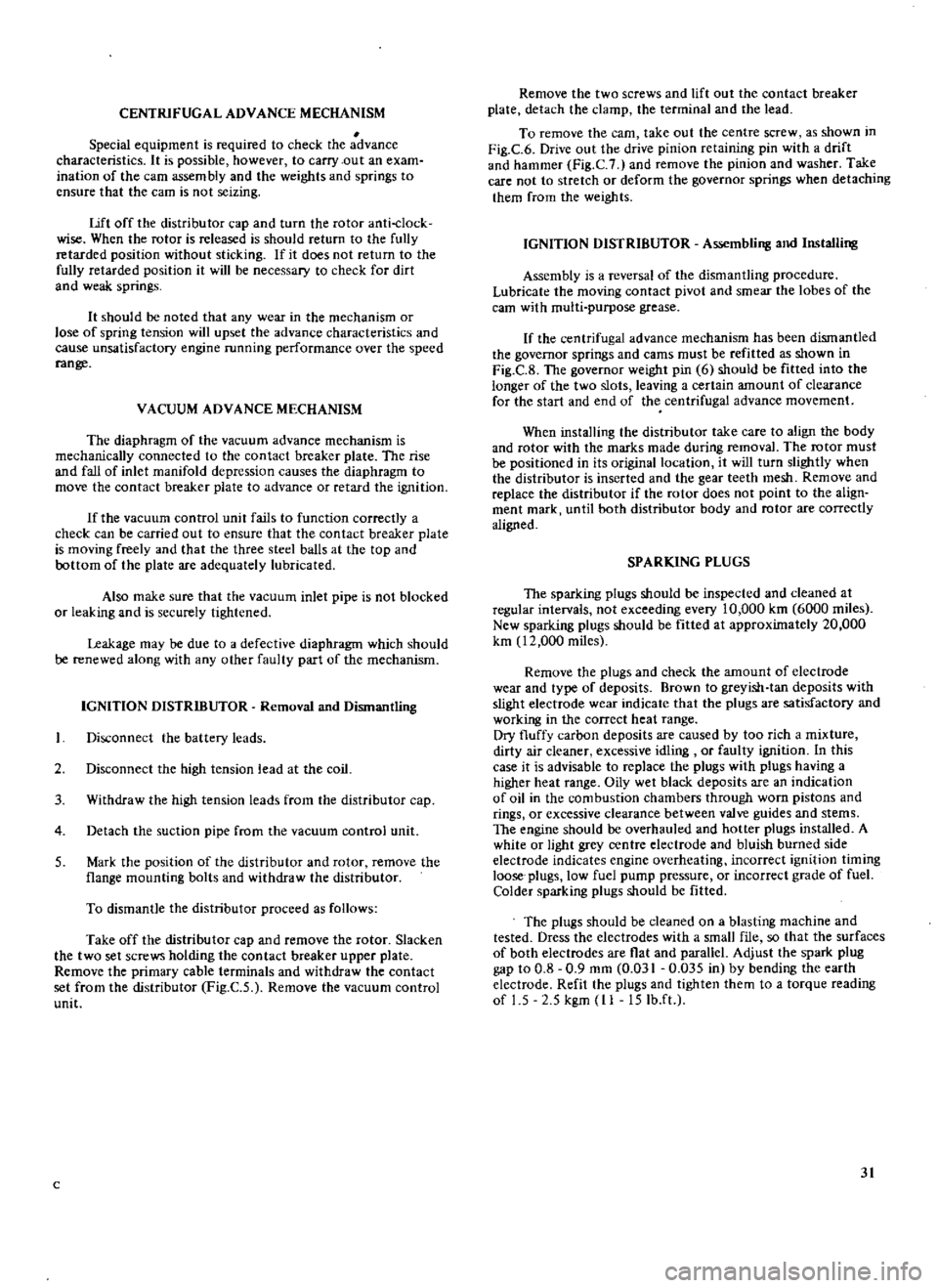
CENTRIFUGAL
ADVANCE
MECHANISM
Special
equipment
is
required
to
check
the
advance
characteristics
It
is
possible
however
to
carry
out
an
exam
ination
of
the
caffi
assembly
and
the
weights
and
springs
to
ensure
that
the
earn
is
not
seizing
Lift
off
the
distributor
cap
and
turn
the
rotor
anti
clock
wise
When
the
rotor
is
released
is
should
return
to
the
fully
retarded
position
without
sticking
If
it
does
not
return
to
the
fully
retarded
position
it
will
be
necessary
to
check
for
dirt
and
weak
springs
It
should
be
noted
that
any
wear
in
the
mechanism
or
lose
of
spring
tension
will
upset
the
advance
characteristics
and
cause
unsatisfactory
engine
running
performance
over
the
speed
range
VACUUM
ADVANCE
MECHANISM
The
diaphragm
of
the
vacuum
advance
mechanism
is
mechanically
connected
to
the
contact
breaker
plate
The
rise
and
fall
of
inlet
manifold
depression
causes
the
diaphragm
to
move
the
contact
breaker
plate
to
advance
or
retard
the
ignition
If
the
vacuum
control
unit
fails
to
function
correctly
a
check
can
be
carried
out
to
ensure
that
the
contact
breaker
plate
is
moving
freely
and
that
the
three
steel
balls
at
the
top
and
oottom
of
the
plate
are
adequately
lubricated
Also
make
sure
that
the
vacuum
inlet
pipe
is
not
blocked
or
leaking
and
is
securely
tightened
Leakage
may
be
due
to
a
defective
diaphragm
which
should
be
renewed
along
with
any
other
faulty
part
of
the
mechanism
IGNITION
DlSTRffiUTOR
Removal
and
Dismantling
Disconnect
the
battery
leads
2
Disconnect
the
high
tension
lead
at
the
coil
3
Withdraw
the
high
tension
leads
from
the
distributor
cap
4
Detach
the
suction
pipe
from
the
vacuum
control
unit
5
Mark
the
position
of
the
distributor
and
rotor
remove
the
flange
mounting
bolts
and
withdraw
the
distributor
To
dismantle
the
distributor
proceed
as
follows
Take
off
the
distributor
cap
and
remove
the
rotor
Slacken
the
two
set
screws
holding
the
contact
breaker
upper
plate
Remove
the
primary
cable
terminals
and
withdraw
the
contact
set
from
the
distributor
Fig
C
S
Remove
the
vacuum
control
unit
c
Remove
the
two
screws
and
lift
out
the
contact
breaker
plate
detach
the
clamp
the
terminal
and
the
lead
To
remove
the
cam
take
out
the
centre
screw
as
shown
in
Fig
e
6
Drive
out
the
drive
pinion
retaining
pin
with
a
drift
and
hammer
Fig
e
and
remove
the
pinion
and
washer
Take
care
not
to
stretch
or
deform
the
governor
springs
when
detaching
them
from
the
weights
IGNITION
DISTRIBUTOR
Assembling
and
Installing
Assembly
is
a
reversal
of
the
dismantling
procedure
Lubricate
the
moving
contact
pivot
and
smear
the
lobes
of
the
cam
with
multi
purpose
grease
If
the
centrifugal
advance
mechanism
has
been
dismantled
the
governor
springs
and
cams
must
be
refitted
as
shown
in
Fig
e
8
The
governor
weight
pin
6
should
be
fitted
into
the
longer
of
the
two
slots
leaving
a
certain
amount
of
clearance
for
the
start
and
end
of
the
centrifugal
advance
movement
When
installing
the
distributor
take
care
to
align
the
body
and
rotor
with
the
marks
made
during
removal
The
rotor
must
be
positioned
in
its
original
location
it
will
turn
slightly
when
the
distributor
is
inserted
and
the
gear
teeth
mesh
Remove
and
replace
the
distributor
if
the
rotor
does
not
point
to
the
align
ment
mark
until
both
distributor
body
and
rotor
are
correctly
aligned
SPARKING
PLUGS
The
sparking
plugs
should
be
inspected
and
cleaned
at
regular
intervals
not
exceeding
every
10
000
km
6000
miles
New
sparking
plugs
should
be
fitted
at
approximately
20
000
km
12
000
miles
Remove
the
plugs
and
check
the
amount
of
electrode
wear
and
type
of
deposits
Brown
to
greyish
tan
deposits
with
slight
electrode
wear
indicate
that
the
plugs
are
satisfactory
and
working
in
the
correct
heat
range
Dry
fluffy
carbon
deposits
are
caused
by
too
rich
a
mixture
dirty
air
cleaner
excessive
idling
or
faulty
ignition
In
this
case
it
is
advisable
to
replace
the
plugs
with
plugs
having
a
higher
heat
range
Oily
wet
black
deposits
are
an
indication
of
oil
in
the
combustion
chambers
through
worn
pistons
and
rings
or
excessive
clearance
between
valve
guides
and
stems
The
engine
should
be
overhauled
and
hotter
plugs
installed
A
white
or
light
grey
centre
electrode
and
bluish
burned
side
electrode
indicates
engine
overheating
incorrect
ignition
timing
loose
plugs
low
fuel
pump
pressure
or
incorrect
grade
of
fuel
Colder
sparking
plugs
should
be
fitted
The
plugs
should
be
cleaned
on
a
blasting
machine
and
tested
Dress
the
electrodes
with
a
small
file
so
that
the
surfaces
of
both
electrodes
are
flat
and
parallel
Adjust
the
spark
plug
gap
to
0
8
0
9
mm
0
031
0
035
in
by
bending
the
earth
electrode
Refit
the
plugs
and
tighten
them
to
a
torque
reading
of
1
5
2
5
kgm
II
15Ib
ft
31
Page 34 of 171
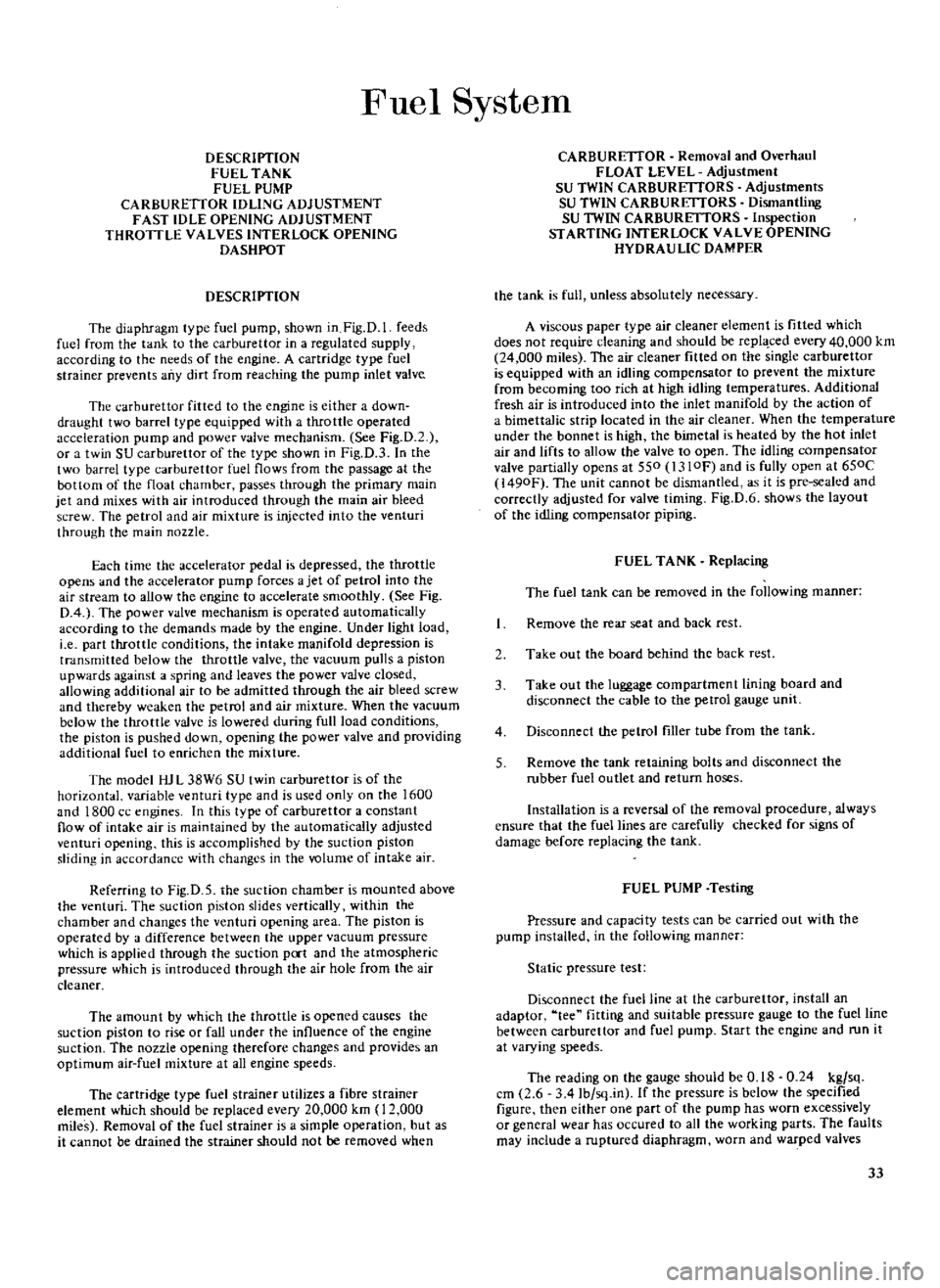
Fuel
System
DESCRIPTION
FUEL
TANK
FUEL
PUMP
CARBURETTOR
IDLING
ADJUSTMENT
FAST
IDLE
OPENING
ADJUSTMENT
THROTTLE
VALVES
INTERLOCK
OPENING
DASHPOT
DESCRIPTION
The
diaphragm
type
fuel
pump
shown
in
Fig
D
1
feeds
fuel
from
the
tank
to
the
carburettor
in
a
regulated
supply
according
to
the
needs
of
the
engine
A
cartridge
type
fuel
strainer
prevents
any
dirt
from
reaching
the
pump
inlet
valve
The
carburettor
fitted
to
the
engine
is
either
a
down
draught
two
barrel
type
equipped
with
a
throttle
operated
acceleration
pump
and
power
valve
mechanism
See
Fig
D
2
or
a
twin
SU
carburettor
of
the
type
shown
in
Fig
D
3
In
the
two
barrel
type
carburettor
fuel
flows
from
the
passage
at
the
bottom
of
the
float
chamber
passes
through
the
primary
main
jet
and
mixes
with
air
introduced
through
the
main
air
bleed
screw
The
petrol
and
air
mixture
is
injected
into
the
venturi
through
the
main
nozzle
Each
time
the
accelerator
pedal
is
depressed
the
throttle
opens
and
the
accelerator
pump
forces
a
jet
of
petrol
into
the
air
stream
to
allow
the
engine
to
accelerate
smoothly
See
Fig
0
4
The
power
valve
mechanism
is
operated
automatically
according
to
the
demands
made
by
the
engine
Under
light
load
i
e
part
throttle
conditions
the
intake
manifold
depression
is
transmitted
below
the
throttle
valve
the
vacuum
pulls
a
piston
upwards
against
a
spring
and
leaves
the
power
valve
closed
allowing
additional
air
to
be
admitted
through
the
air
bleed
screw
and
thereby
weaken
the
petrol
and
air
mixture
When
the
vacuum
below
the
throttle
vaJve
is
lowered
during
full
load
conditions
the
piston
is
pushed
down
opening
the
power
valve
and
providing
additional
fuel
to
enrichen
the
mixture
The
model
HJ
L
38W6
SU
twin
carburettor
is
of
the
horizontal
variable
venturi
type
and
is
used
only
on
the
1600
and
1800
cc
engines
In
this
type
of
carburettor
a
constant
flow
of
intake
air
is
maintained
by
the
automatically
adjusted
venturi
opening
this
is
accomplished
by
the
suction
piston
sliding
in
accordance
with
changes
in
the
volume
of
intake
air
Referring
to
Fig
D
5
the
suction
chamber
is
mounted
above
the
venturi
The
suction
piston
slides
vertically
within
the
chamber
and
changes
the
venturi
opening
area
The
piston
is
operated
by
a
difference
between
the
upper
vacuum
pressure
which
is
applied
through
the
suction
poct
and
the
atmospheric
pressure
which
is
introduced
through
the
air
hole
from
the
air
cleaner
The
amount
by
which
the
throttle
is
opened
causes
the
suction
piston
to
rise
or
fall
under
the
intluence
of
the
engine
suction
The
pozzle
opening
therefore
changes
and
provides
an
optimum
air
fuel
mixture
at
all
engine
speeds
The
cartridge
type
fuel
strainer
utilizes
a
fibre
strainer
element
which
should
be
replaced
every
20
000
km
12
000
miles
Removal
of
the
fuel
strainer
is
a
simple
operation
but
as
it
cannot
be
drained
the
strainer
should
not
be
removed
when
CARBURETIOR
Removal
and
Overhaul
FLOAT
LEVEL
Adjustment
SU
TWIN
CARBURmORS
Adjustments
SU
TWIN
CARBURmORS
Dismantling
SU
TWIN
CARBURETTORS
Inspection
STARTING
INTERLOCK
VALVE
OPENING
HYDRAULIC
DAMPER
the
tank
is
full
unless
absolutely
necessary
A
viscous
paper
type
air
cleaner
element
is
fitted
which
does
not
require
cleaning
and
should
be
repl
ced
every
40
000
km
24
000
miles
The
air
cleaner
fitted
on
the
single
carburettor
is
equipped
with
an
idling
compensator
to
prevent
the
mixture
from
becoming
too
rich
at
high
idling
temperatures
Additional
fresh
air
is
introduced
into
the
inlet
manifold
by
the
action
of
a
bimettalic
strip
located
in
the
air
cleaner
When
the
temperature
under
the
bonnet
is
high
the
bimetal
is
heated
by
the
hot
inlet
air
and
lifts
to
allow
the
valve
to
open
The
idling
compensator
valve
partially
opens
at
550
I310F
and
is
fully
open
at
650C
l490F
The
unit
cannot
be
dismantled
as
it
is
pre
sealed
and
correctly
adjusted
for
valve
timing
Fig
D
6
shows
the
layout
of
the
idling
compensator
piping
FUEL
TANK
Replacing
The
fuel
tank
can
be
removed
in
the
following
manner
Remove
the
rear
seat
and
back
rest
2
Take
out
the
board
behind
the
back
rest
3
Take
out
the
luggage
compartment
lining
board
and
disconnect
the
cable
to
the
petrol
gauge
unit
4
Disconnect
the
petrol
filler
tube
from
the
tank
5
Remove
the
tank
retaining
bolts
and
disconnect
the
rubber
fuel
outlet
and
return
hoses
Installation
is
a
reversal
of
the
removal
procedure
always
ensure
that
the
fuel
lines
arc
carefully
checked
for
signs
of
damage
before
replacing
the
tank
FUEL
PUMP
Testing
Pressure
and
capacity
tests
can
be
carried
out
with
the
pump
installed
in
the
following
manner
Static
pressure
test
Disconnect
the
fuel
line
at
the
carburettor
install
an
adaptor
tee
fitting
and
suitable
pressure
gauge
to
the
fuel
line
between
carburettor
and
fuel
pump
Start
the
engine
and
run
it
at
varying
speeds
The
reading
on
the
gauge
should
be
0
18
0
24
kg
sq
cm
2
6
34
Ib
sq
in
If
the
pressure
is
below
the
specified
figure
then
either
one
part
of
the
pump
has
worn
excessively
or
general
wear
has
occured
to
all
the
working
parts
The
faults
may
include
a
ruptured
diaphragm
worn
and
warped
valves
33
Page 40 of 171
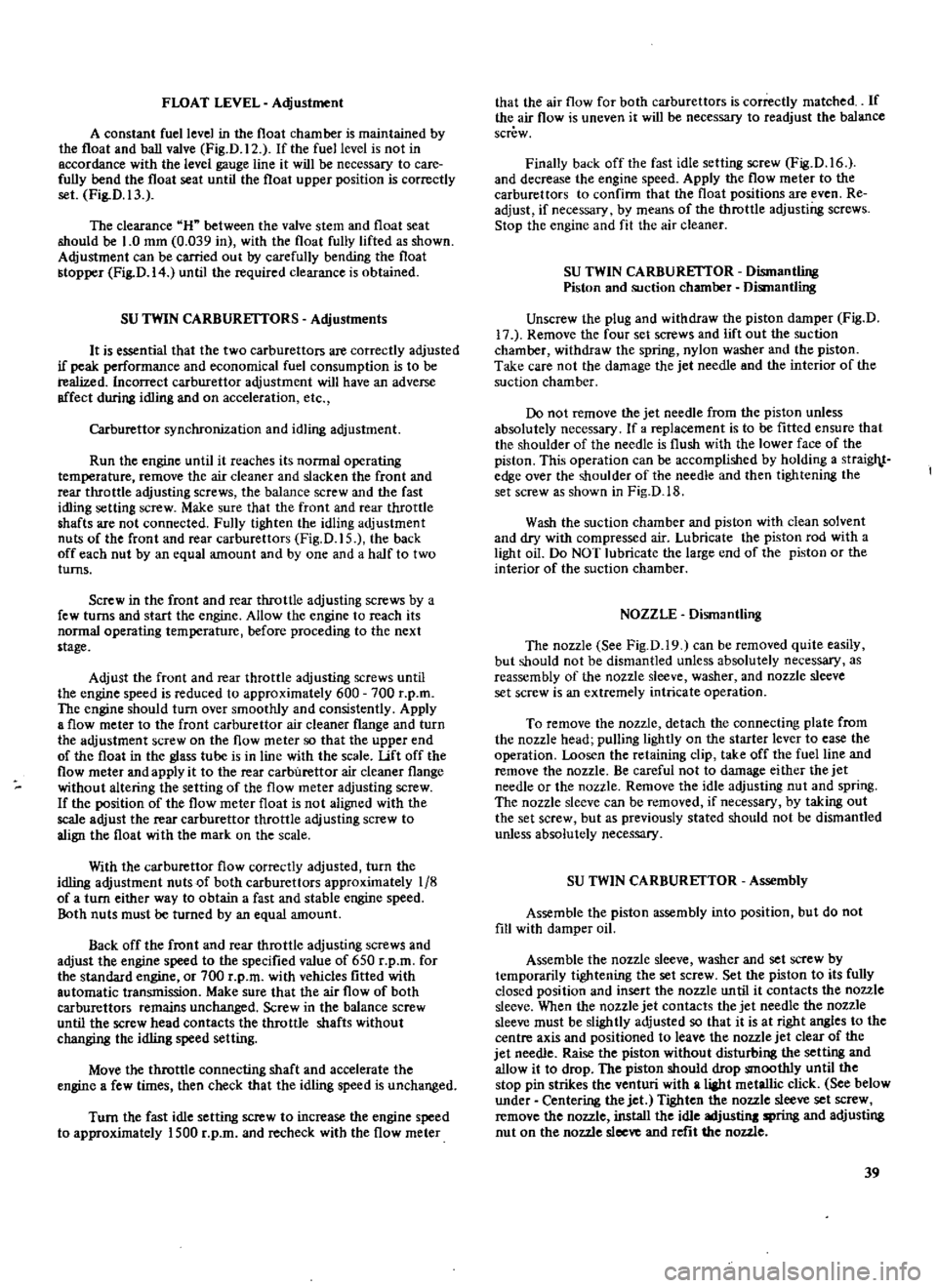
FLOAT
LEVEL
Adjustment
A
constant
fuel
level
in
the
float
chamber
is
maintained
by
the
float
and
ball
valve
Fig
D
12
If
the
fuel
level
is
not
in
accordance
with
the
level
gauge
line
it
will
be
necessary
to
care
fully
bend
the
float
seat
until
the
float
upper
position
is
correctly
set
Fig
D
13
The
clearance
H
between
the
valve
stem
and
float
seat
should
be
1
0
mm
0
039
in
with
the
float
fully
lifted
as
shown
Adjustment
can
be
carried
out
by
carefully
bending
the
float
stopper
Fig
D
14
until
the
required
clearance
is
obtained
SU
TWIN
CARBURETTORS
Adjustments
It
is
essential
that
the
two
carburettors
are
correctly
adjusted
if
peak
m3l1ce
and
economical
fuel
consumption
is
to
be
realized
Incorrect
carburettor
a
ljustment
will
have
an
adverse
affect
during
idling
and
on
acceleration
etc
Carburettor
synchronization
and
idling
adjustment
Run
the
engine
until
it
reaches
its
normal
operating
temperature
remove
the
air
cleaner
and
slacken
the
front
and
rear
throttle
adjusting
screws
the
balance
screw
and
the
fast
idling
setting
screw
Make
sure
that
the
front
and
rear
throttle
shafts
are
not
connected
Fully
tighten
the
idling
adjustment
nuts
of
the
front
and
rear
carburettors
Fig
D
15
the
back
off
each
nut
by
an
equal
amount
and
by
one
and
a
half
to
two
tUrns
Screw
in
the
front
and
rear
throttle
adjusting
screws
by
a
few
turns
and
start
the
engine
Allow
the
engine
to
reach
its
normal
operating
temperature
before
proceding
to
the
next
stage
Adjust
the
front
and
rear
throttle
adjusting
screws
until
the
engine
speed
is
reduced
to
approximately
600
700
r
p
m
The
engine
should
turn
over
smoothly
and
consistently
Apply
a
flow
meter
to
the
front
carburettor
air
cleaner
flange
and
turn
the
adjustment
screw
on
the
flow
meter
so
that
the
upper
end
of
the
float
in
the
glass
tube
is
in
line
with
the
scale
Uft
off
the
flow
meter
and
apply
it
to
the
rear
carburettor
air
cleaner
flange
without
altering
the
setting
of
the
flow
meter
adjusting
screw
If
the
position
of
the
flow
meter
float
is
not
aligned
with
the
scale
adjust
the
rear
carburettor
throttle
adjusting
screw
to
align
the
float
with
the
mark
on
the
scale
With
the
carburettor
flow
correctly
adjusted
turn
the
idling
adjustment
nuts
of
both
carburettors
approximately
1
8
of
a
turn
either
way
to
obtain
a
fast
and
stable
engine
speed
Both
nuts
must
be
turned
by
an
equal
amount
Back
off
the
front
and
rear
throttle
adjusting
screws
and
adjust
the
engine
speed
to
the
specified
value
of
650
r
p
m
for
the
standard
engine
or
700
r
p
m
with
vehicles
fitted
with
automatic
transmission
Make
sure
that
the
air
flow
of
both
carburettors
remains
unchanged
Screw
in
the
balance
screw
until
the
screw
head
contacts
the
throttle
shafts
without
changing
the
idling
speed
setting
Move
the
throttle
connecting
shaft
and
accelerate
the
engine
a
few
times
then
check
that
the
idling
speed
is
unchanged
Turn
the
fast
idle
setting
screw
to
increase
the
engine
speed
to
approximately
1500
r
p
m
and
recheck
with
the
flow
meter
that
the
air
flow
for
both
carburettors
is
correctly
matched
If
the
air
flow
is
uneven
it
will
be
necessary
to
readjust
the
balance
screw
Finally
back
off
the
fast
idle
setting
screw
Fig
D
16
and
decrease
the
engine
speed
Apply
the
flow
meter
to
the
carburettors
to
confirm
that
the
float
positions
are
even
Re
adjust
if
necessary
by
means
of
the
throttle
adjusting
screws
Stop
the
engine
and
fit
the
air
cleaner
SU
TWIN
CARBURETTOR
Dismantling
Piston
and
suction
chamber
Dismantling
Unscrew
the
plug
and
withdraw
the
piston
damper
Fig
D
17
Remove
the
four
set
screws
and
lift
out
the
suction
chamber
withdraw
the
spring
nylon
washer
and
the
piston
Take
care
not
the
damage
the
jet
needle
and
the
interior
of
the
suction
chamber
Do
not
remove
the
jet
needle
from
the
piston
unless
absolutely
necessary
If
a
replacement
is
to
be
fitted
ensure
that
the
shoulder
of
the
needle
is
flush
with
the
lower
face
of
the
piston
This
operation
can
be
accomplished
by
holding
a
strai
edge
over
the
shoulder
of
the
needle
and
then
tightening
the
set
screw
as
shown
in
Fig
D
18
Wash
the
suction
chamber
and
piston
with
dean
solvent
and
dry
with
compressed
air
Lubricate
the
piston
rod
with
a
light
oil
Do
NOT
lubricate
the
large
end
of
the
piston
or
the
interior
of
the
suction
chamber
NOZZLE
Dismantling
The
nozzle
See
Fig
D
19
can
be
removed
quite
easily
but
should
not
be
dismantled
unless
absolutely
necessary
as
reassembly
of
the
nozzle
sleeve
washer
and
nozzle
sleeve
set
screw
is
an
extremely
intricate
operation
To
remove
the
nozzle
detach
the
connecting
plate
from
the
nozzle
head
pulling
lightly
on
the
starter
lever
to
ease
the
operation
Loosen
the
retaining
clip
take
off
the
fuel
line
and
remove
the
nozzle
Be
careful
not
to
damage
either
the
jet
needle
oc
the
nozzle
Remove
the
idle
adjusting
nut
and
spring
The
nozzle
sleeve
can
be
removed
if
necessary
by
taking
out
the
set
screw
but
as
previously
stated
should
not
be
dismantled
unless
absolutely
necessary
SU
TWIN
CARBUREfTOR
Assembly
Assemble
the
piston
assembly
into
position
but
do
not
fill
with
damper
oil
Assemble
the
nozzle
sleeve
washec
and
set
screw
by
temporarily
tightening
the
set
screw
Set
the
piston
to
its
fully
closed
position
and
insert
the
nozzle
until
it
contacts
the
nozzle
sleeve
When
the
nozzle
jet
contacts
the
jet
needle
the
nozzle
sleeve
must
be
slightly
adjusted
so
that
it
is
at
right
angles
to
the
centre
axis
and
positioned
to
leave
the
nozzle
jet
clear
of
the
jet
needle
Raise
the
piston
without
disturbing
the
setting
and
allow
it
to
drop
The
piston
should
drop
smoothly
until
the
stop
pin
strikes
the
venturi
with
a
liaht
metallic
click
See
below
under
Centering
the
jet
Tighten
the
nozzle
sleeve
set
screw
remove
the
nozzle
install
the
idle
adjustinJ
spring
and
adjusting
nut
on
the
nozzle
sleeve
and
refit
the
nozzle
39
Page 43 of 171
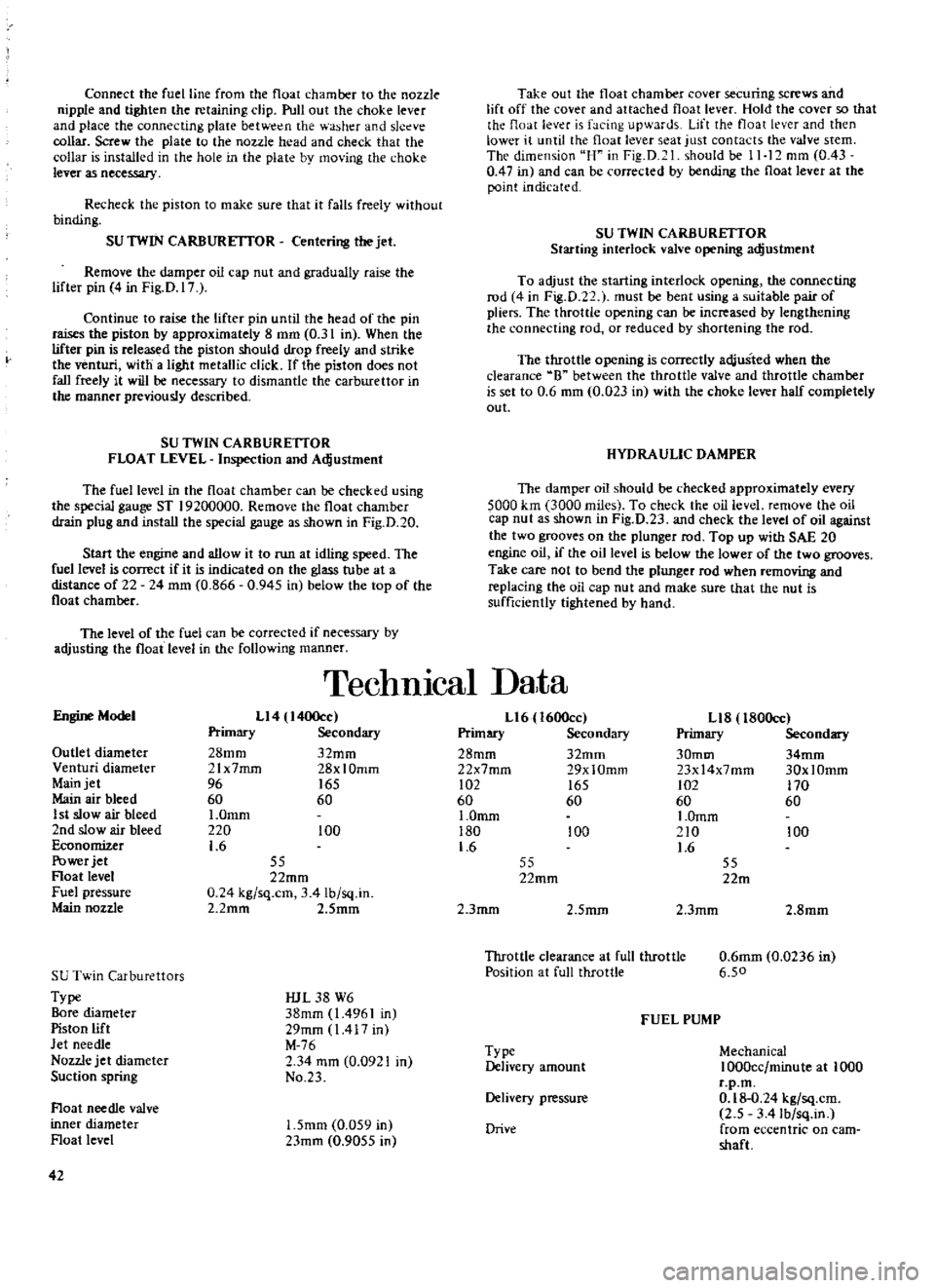
Connect
the
fuel
line
from
the
float
chamber
to
the
nozzle
nipple
and
tighten
the
retaining
clip
Pull
out
the
choke
lever
and
place
the
connecting
plaie
betw
n
the
washer
and
sleeve
collar
Screw
the
plate
to
the
nozzle
head
and
check
that
the
collar
is
installed
in
the
hole
in
the
plate
by
mo
ing
the
choke
lever
as
necessary
Recheck
the
piston
to
make
sure
that
it
falls
freely
without
binding
SU
TWIN
CARBURETTOR
Centering
the
jet
Remove
the
damper
oil
cap
nut
and
gradually
raise
the
lifter
pin
4
in
Fig
D
17
Continue
to
raise
the
lifter
pin
until
the
head
of
the
pin
raises
the
piston
by
approximately
8
mm
0
31
in
When
the
lifter
pin
is
released
the
piston
should
drop
freely
and
strike
the
venturi
with
a
light
metallic
click
If
the
pi
ston
does
not
fall
freely
it
will
be
necessary
to
dismantle
the
carburettor
in
the
manner
previously
described
SU
TWIN
CARBURETTOR
FLOAT
LEVEL
Inspection
and
Adjustment
The
fuel
level
in
the
float
chamber
can
be
checked
using
the
special
gauge
ST
19200000
Remove
the
float
chamber
drain
plug
and
install
the
special
gauge
as
shown
in
Fig
D
20
Start
the
engine
and
allow
it
to
run
at
idling
speed
The
fuel
level
is
conect
if
it
is
indicated
on
the
glass
tu
be
at
a
distance
of
22
24
mm
0
866
0
945
in
below
the
top
of
the
float
chamber
The
level
of
the
fuel
can
be
corrected
if
necessary
by
adjusting
the
float
level
in
the
following
manner
Take
out
the
float
chamber
coveT
securing
screws
and
lift
off
the
cover
and
attached
float
lever
Hold
the
cover
so
that
the
float
lev
r
is
facing
upwards
Lift
the
float
lever
and
then
lower
it
until
the
float
lever
seat
just
contacts
the
valve
stem
The
dimension
uH
in
Fig
D
1
should
be
11
12
mm
0
43
0
47
in
and
can
be
corrected
by
bending
the
float
lever
at
the
point
indicated
SU
TWIN
CARBURETTOR
Starting
interlock
valve
opening
adjustment
To
adjust
the
starting
interlock
opening
the
connecting
rod
4
in
Fig
D
22
1
must
be
bent
using
a
suitable
pair
of
pliers
The
throttle
opening
can
be
increased
by
lengthening
the
connecting
rod
or
reduced
by
shortening
the
rod
The
throttle
opening
is
correctly
adjusted
when
the
clearance
8
between
the
throttle
valve
and
throttle
chamber
is
set
to
0
6
mm
0
023
in
with
the
choke
lever
half
completely
out
HYDRAULIC
DAMPER
The
damper
oil
should
be
checked
approximately
every
5000
km
3000
miles
To
check
the
oil
level
remove
the
oil
cap
nut
as
shown
in
Fig
D
23
and
check
the
level
of
oil
against
the
two
grooves
on
the
plunger
rod
Top
up
with
SAE
20
engine
oil
if
the
oil
level
is
below
the
lower
of
the
two
grooves
Take
care
not
to
bend
the
plunger
rod
when
removing
and
replacing
the
oil
cap
nut
and
make
sure
that
the
nut
is
sufficiently
tightened
by
hand
TechnIcal
Data
Engine
Model
Ll4
I400cc
Primary
Secondary
28mm
32mm
21x7mrn
28xlOmm
96
165
60
60
I
Omm
220
100
1
6
Outlet
diameter
Venturi
diameter
Main
jet
Main
air
bleed
1
st
slow
air
bleed
2nd
slow
air
bleed
Economizer
Power
jet
Float
level
Fuel
pressure
Main
nozzle
55
22mm
0
24
kg
sq
cm
3
41b
sq
in
2
2mm
2
Smm
SU
Twin
Carburettors
Type
Bore
diameter
Piston
lift
Jet
needle
Nozzle
jet
diameter
Suction
spring
IUL
38
W6
38mm
1
4961
in
29mm
1417
in
M
76
2
34
mm
0
0921
in
No
23
Float
needle
valve
inner
diameter
Float
level
1
5mm
0
059
in
23mm
0
9055
in
42
Ll6
1600cc
Primary
Secondary
28mm
32mm
22x7mm
29xlOmm
102
165
60
60
1
0mm
180
100
1
6
Ll8
l80Occ
Primary
Secondary
30mm
34mm
23x14x7mm
30xlOmm
102
170
60
60
I
Omm
210
100
1
6
55
22mm
55
22m
2
3mm
2
5mm
2
3mm
2
8mm
Throttle
clearance
at
full
throttle
Position
at
full
throttle
0
6mm
0
0236
in
6
50
FUEL
PUMP
Type
Delivery
amount
Mechanical
1000cc
minute
at
1000
r
p
m
0
18
0
24
kg
sq
cm
2
5
3
41b
sq
in
from
eccentric
on
cam
shaft
Delivery
pressure
Drive
Page 88 of 171
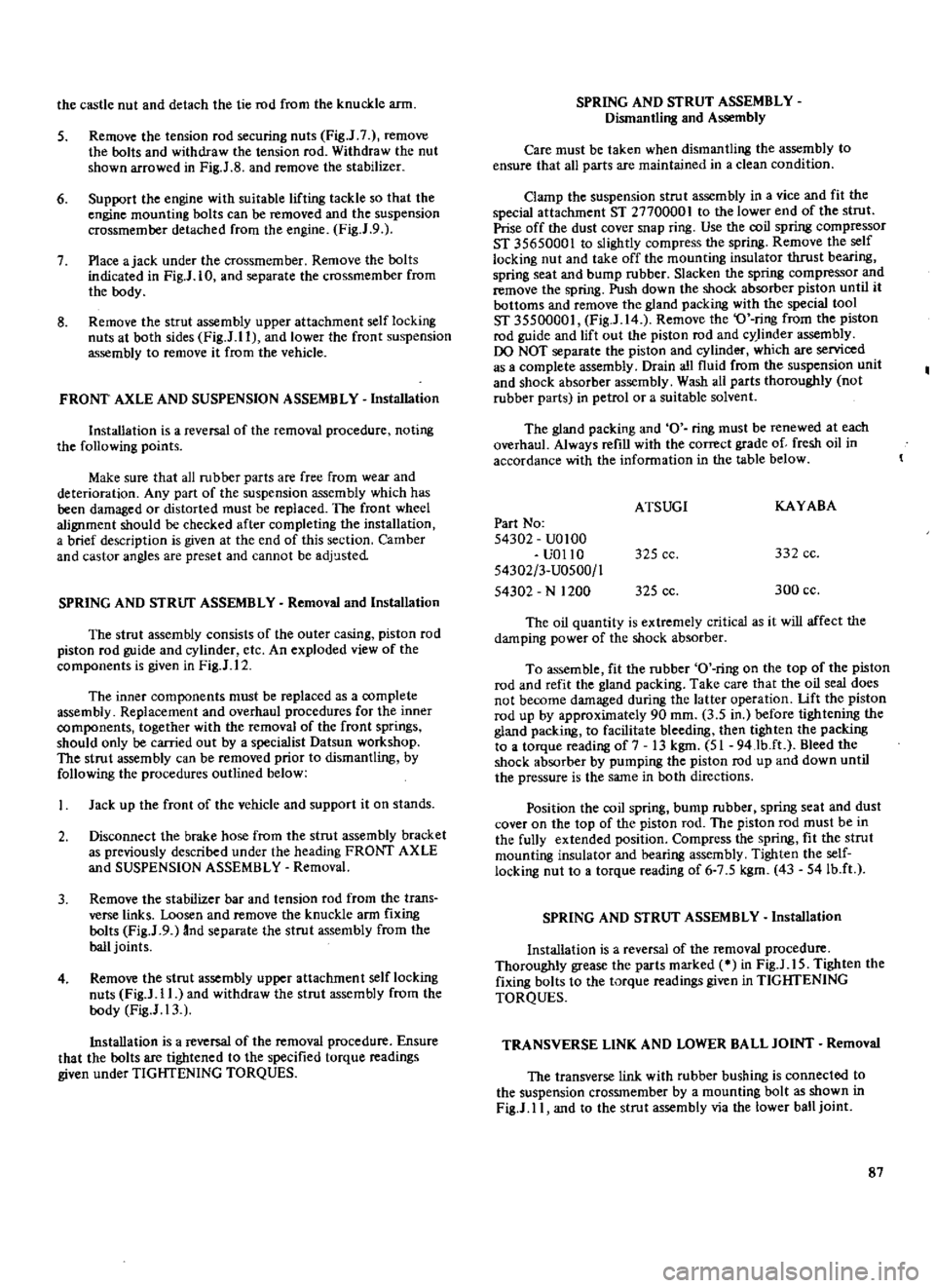
the
castle
nut
and
detach
the
tie
rod
from
the
knuckle
arm
5
Remove
the
tension
rod
securing
nuts
Fig
J
7
remove
the
bolts
and
withdraw
the
tension
rod
Withdraw
the
nut
shown
arrowed
in
FigJ
8
and
remove
the
stabilizer
6
Support
the
engine
with
suitable
lifting
tackle
so
that
the
engine
mounting
bolts
can
be
removed
and
the
suspension
crossmember
detached
from
the
engine
FigJ
9
7
Place
ajack
under
the
crossmember
Remove
the
bolts
indicated
in
Fig
J
IO
and
separate
the
crossmember
from
the
body
8
Remove
the
strut
assembly
upper
attachment
self
locking
nuts
at
both
sides
Fig
J
ll
and
lower
the
front
suspension
assembly
to
remove
it
from
the
vehicle
FRONT
AXLE
AND
SUSPENSION
ASSEMBLY
Installation
Installation
is
a
reversal
of
the
removal
procedure
noting
the
following
points
Make
sure
that
all
rubber
parts
are
free
from
wear
and
deterioration
Any
part
of
the
suspension
assembly
which
has
been
damaged
or
distorted
must
be
replaced
The
front
wheel
alignment
should
be
checked
after
completing
the
installation
a
brief
description
is
given
at
the
end
of
this
section
Camber
and
castor
angles
are
preset
and
cannot
be
adjusted
SPRING
AND
STRUf
ASSEMBLY
Removal
and
Installation
The
strut
assembly
consists
of
the
outer
casing
piston
rod
piston
rod
guide
and
cylinder
etc
An
exploded
view
of
the
components
is
given
in
Fig
J
12
The
inner
components
must
be
replaced
as
a
complete
assembly
Replacement
and
overhaul
procedures
for
the
inner
components
together
with
the
removal
of
the
front
springs
should
only
be
carried
out
by
a
specialist
Datsun
workshop
The
strut
assembly
can
be
removed
prior
to
dismantling
by
following
the
procedures
outlined
below
Jack
up
the
front
of
the
vehicle
and
support
it
on
stands
2
Disconnect
the
brake
hose
from
the
strut
assembly
bracket
as
previously
described
under
the
heading
FRONT
AXLE
and
SUSPENSION
ASSEMBLY
Removal
3
Remove
the
stabilizer
bar
and
tension
rod
from
the
trans
verse
links
Loosen
and
remove
the
knuckle
arm
fixing
bolts
Fig
J
9
And
separate
the
strut
assembly
from
the
ball
joints
4
Remove
the
strut
assembly
upper
attachment
self
locking
nuts
Fig
J
11
and
withdraw
the
strut
assembly
from
the
body
Fig
J
13
Installation
is
a
reversal
of
the
removal
procedure
Ensure
that
the
bolts
are
tightened
to
the
specified
torque
readings
given
under
TIGHTENING
TORQUES
SPRING
AND
STRUT
ASSEMBLY
Dismantling
and
Assembly
Care
must
be
taken
when
dismantling
the
assembly
to
ensure
that
aU
parts
are
maintained
in
a
clean
condition
Clamp
the
suspension
strut
assembly
in
a
vice
and
fit
the
special
attachment
ST
2770000
I
to
the
lower
end
of
the
strut
Prise
off
the
dust
cover
snap
ring
Use
the
coil
spring
compressor
ST
35650001
to
slightly
compress
the
spring
Remove
the
self
locking
nut
and
take
off
the
mounting
insulator
thrust
bearing
spring
seat
and
bump
rubber
Slacken
the
spring
compressor
and
remove
the
spring
Push
down
the
shock
absorber
piston
until
it
bottoms
and
remove
the
gland
packing
with
the
special
tool
ST
35500001
Fig
J
14
Remove
the
O
ring
from
the
piston
rod
guide
and
lift
out
the
piston
rod
and
cy
linder
assembly
00
NOT
separate
the
piston
and
cylinder
which
are
serviced
as
a
complete
assembly
Drain
all
fluid
from
the
suspension
unit
and
shock
absorber
assembly
Wash
all
parts
thoroughly
not
rubber
parts
in
petrol
or
a
suitable
solvent
The
gland
packing
and
0
ring
must
be
renewed
at
each
overhaul
Always
refill
with
the
correct
grade
of
fresh
oil
in
accordance
with
the
information
in
the
table
below
ATSUGI
KAYABA
Part
No
54302
UO
100
UOl10
325
cc
332
cc
54302
3
U0500
1
54302
N
1200
325
cc
300
cc
The
oil
quantity
is
extremely
critical
as
it
will
affect
the
damping
power
of
the
shock
absorber
To
assemble
fit
the
rubber
O
ring
on
the
top
of
the
piston
rod
and
refit
the
gland
packing
Take
care
that
the
oil
seal
does
not
become
damaged
during
the
latter
operation
Lift
the
piston
rod
up
by
approximately
90
mm
3
5
in
before
tightening
the
gland
packing
to
facilitate
bleeding
then
tighten
the
packing
to
a
torque
reading
of
7
13
kgm
51
94Jb
ft
Bleed
the
shock
absorber
by
pumping
the
piston
rod
up
and
down
until
the
pressure
is
the
same
in
both
directions
Position
the
coil
spring
bump
rubber
spring
seat
and
dust
cover
on
the
top
of
the
piston
rod
The
piston
rod
must
be
in
the
fully
extended
position
Compress
the
spring
fit
the
strut
mounting
insulator
and
bearing
assembly
Tighten
the
self
locking
nut
to
a
torque
reading
of
6
7
5
kgm
43
541b
ft
SPRING
AND
STRUT
ASSEMBLY
Installation
Installation
is
a
reversal
of
the
removal
procedure
Thoroughly
grease
the
parts
marked
in
Fig
J
15
Tighten
the
fixing
bolts
to
the
torque
readings
given
in
TIGHfENING
TORQUES
TRANSVERSE
LINK
AND
LOWER
BALL
JOINT
Removal
The
transverse
link
with
rubber
bushing
is
connected
to
the
suspension
crosSlTIember
by
a
mounting
bolt
as
shown
in
Fig
J
11
and
to
the
strut
assembly
via
the
lower
ball
joint
87
Page 110 of 171
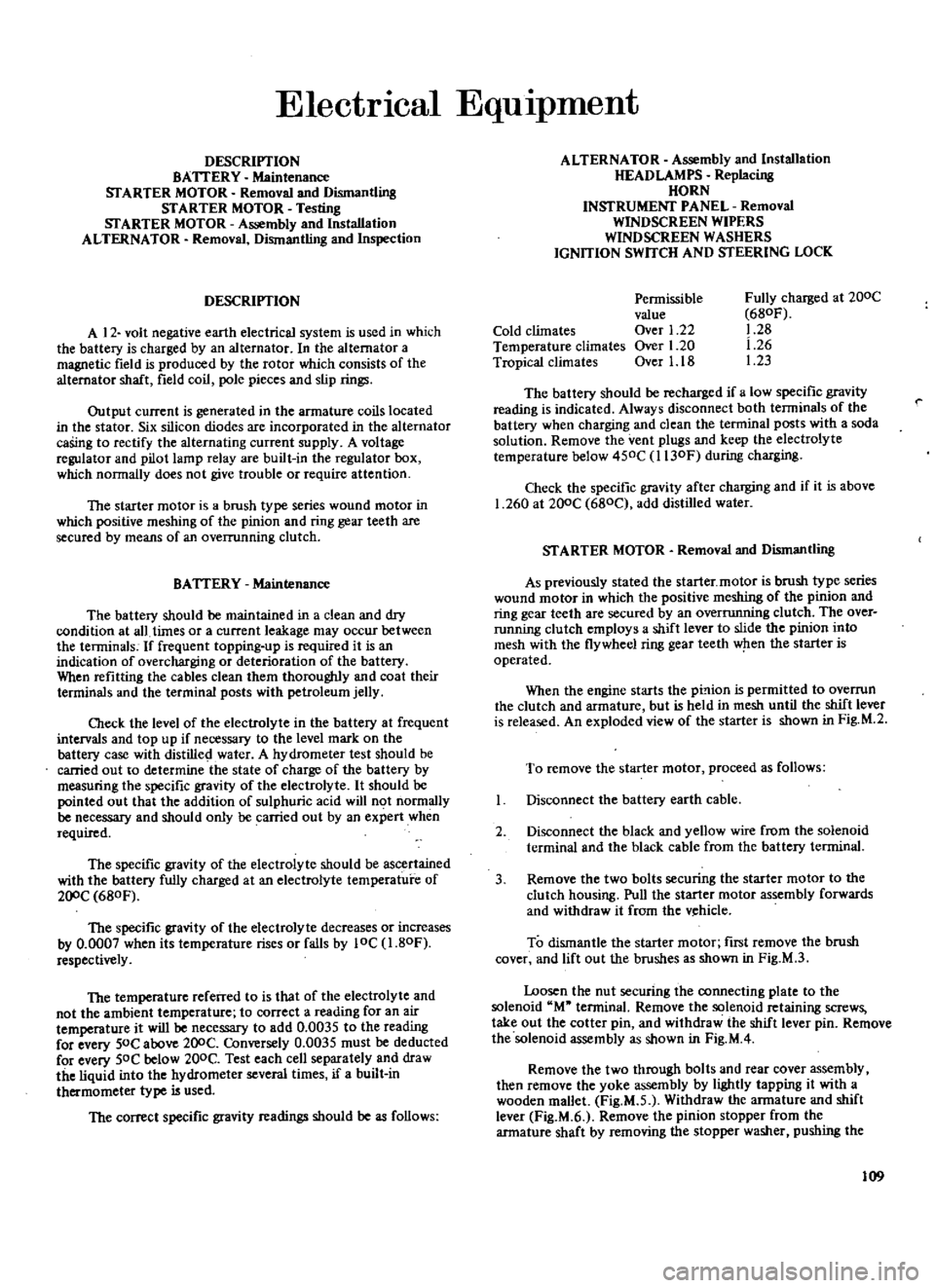
ElectrIcal
EquIpment
DESCRIPTION
BATTERY
Maintenance
STARTER
MOTOR
Removal
and
Dismantling
STARTER
MOTOR
Testing
STARTER
MOTOR
Assembly
and
Installation
ALTERNATOR
Removal
Dismantling
and
Inspection
DESCRIPTION
A
12
volt
negative
earth
electrical
system
is
used
in
which
the
battery
is
charged
by
an
alternator
In
the
alternator
a
magnetic
field
is
produced
by
the
rotor
which
consists
of
the
alternator
shaft
field
coil
p
le
pieces
and
slip
rings
Output
current
is
generated
in
the
armature
coils
located
in
the
stator
Six
silicon
diodes
are
incorporated
in
the
alternator
caSing
to
rectify
the
alternating
current
supply
A
voltage
regulator
and
pilot
lamp
relay
are
built
in
the
regulator
box
which
nonnally
does
not
give
trouble
or
require
attention
The
starter
motor
is
a
brush
type
series
wound
motor
in
which
positive
meshing
of
the
pinion
and
ring
gear
teeth
are
secured
by
means
of
an
overrunning
clutch
BATTERY
Maintenance
The
battery
should
be
maintained
in
a
clean
and
dry
condition
at
all
times
or
a
current
leakage
may
occur
between
the
terminals
If
frequent
topping
up
is
required
it
is
an
indication
of
overcharging
or
deterioration
of
the
battery
When
refitting
the
cables
clean
them
thoroughly
and
coat
their
terminals
and
the
terminal
posts
with
petroleum
jelly
Check
the
level
of
the
electrolyte
in
the
battery
at
frequent
intervals
and
top
up
if
necessary
to
the
level
mark
on
the
battery
case
with
distilled
water
A
hydrometer
test
should
be
carried
out
to
determine
the
state
of
charge
of
the
battery
by
measuring
the
specific
gravity
of
the
electrolyte
It
should
be
pointed
out
that
the
addition
of
sulphuric
acid
will
not
normally
be
necessary
and
should
only
be
carried
out
by
an
expert
when
required
The
specific
gravity
of
the
electrolyte
should
be
ascertained
with
the
battery
fully
charged
at
an
electrolyte
temperature
of
200C
680F
The
specific
gravity
of
the
electrolyte
decreases
or
increases
by
0
0007
when
its
temperature
rises
or
falls
by
10C
1
80F
respectively
The
temperature
referred
to
is
that
of
the
electrolyte
and
not
the
ambient
temperature
to
correct
a
reading
for
an
air
temperature
it
will
be
necessary
to
add
0
0035
to
the
reading
for
every
50C
above
200C
Conversely
0
0035
must
be
deducted
for
every
SOC
below
200C
Test
each
cell
separately
and
draw
the
liquid
into
the
hydrometer
several
times
if
a
built
in
thermometer
type
is
used
The
correct
specific
gravity
readings
should
be
as
follows
ALTERNATOR
Assembly
and
Installation
HEAD
LAMPS
Replacing
HORN
INSTRUMENT
PANEL
Removal
WINDSCREEN
WIPERS
WINDSCREEN
WASHERS
IGNITION
SWITCH
AND
STEERING
LOCK
Cold
climates
Temperature
climates
Tropical
climates
Permissible
value
Over
1
22
Over
1
20
Over
1
18
Fully
charged
at
200C
680F
1
28
1
26
1
23
The
battery
should
be
recharged
if
a
low
specific
gravity
reading
is
indicated
Always
disconnect
both
terminals
of
the
battery
when
charging
and
clean
the
terminal
posts
with
a
soda
solution
Remove
the
vent
plugs
and
keep
the
electrolyte
temperature
below
450C
l130F
during
charging
Check
the
specific
gravity
after
charging
and
if
it
is
above
1
260
at
200C
680C
add
distilled
water
STARTER
MOTOR
Removal
and
Dismantling
As
previously
stated
the
starter
motor
is
brush
type
series
wound
motor
in
which
the
positive
meshing
of
the
pinion
and
ring
gear
teeth
are
secured
by
an
overrunning
clutch
The
over
running
clutch
employs
a
shift
lever
to
slide
the
pinion
into
mesh
with
the
flywheel
ring
gear
teeth
when
the
starter
is
operated
When
the
engine
starts
the
pL
lion
is
permitted
to
overrun
the
clutch
and
armature
but
is
held
in
mesh
until
the
shift
lever
is
released
An
exploded
view
of
the
starter
is
shown
in
Fig
M
2
To
remove
the
starter
motor
proceed
as
follows
Disconnect
the
battery
earth
cable
2
Disconnect
the
black
and
yellow
wire
from
the
solenoid
terminal
and
the
black
cable
from
the
battery
terminal
3
Remove
the
two
bolts
securing
the
starter
motor
to
the
clutch
housing
Pull
the
starter
motor
assembly
forwards
and
withdraw
it
from
the
v
hicle
To
dismantle
the
starter
motor
ftrst
remove
the
brush
cover
and
lift
out
the
brushes
as
shown
in
Fig
M
3
Loosen
the
nut
securing
the
connecting
plate
to
the
solenoid
M
terminal
Remove
the
solenoid
retaining
screws
take
out
the
cotter
pin
and
withdraw
the
shift
lever
pin
Remove
the
solenoid
assembly
as
shown
in
Fig
M
4
Remove
the
two
through
bolts
and
rear
cover
assembly
then
remove
the
yoke
assembly
by
lightly
tapping
it
with
a
wooden
mallet
Fig
M
S
Withdraw
the
armature
and
shift
lever
Fig
M
6
Remove
the
pinion
stopper
from
the
armature
shaft
by
removing
the
stopper
washer
pushing
the
109
Page 112 of 171
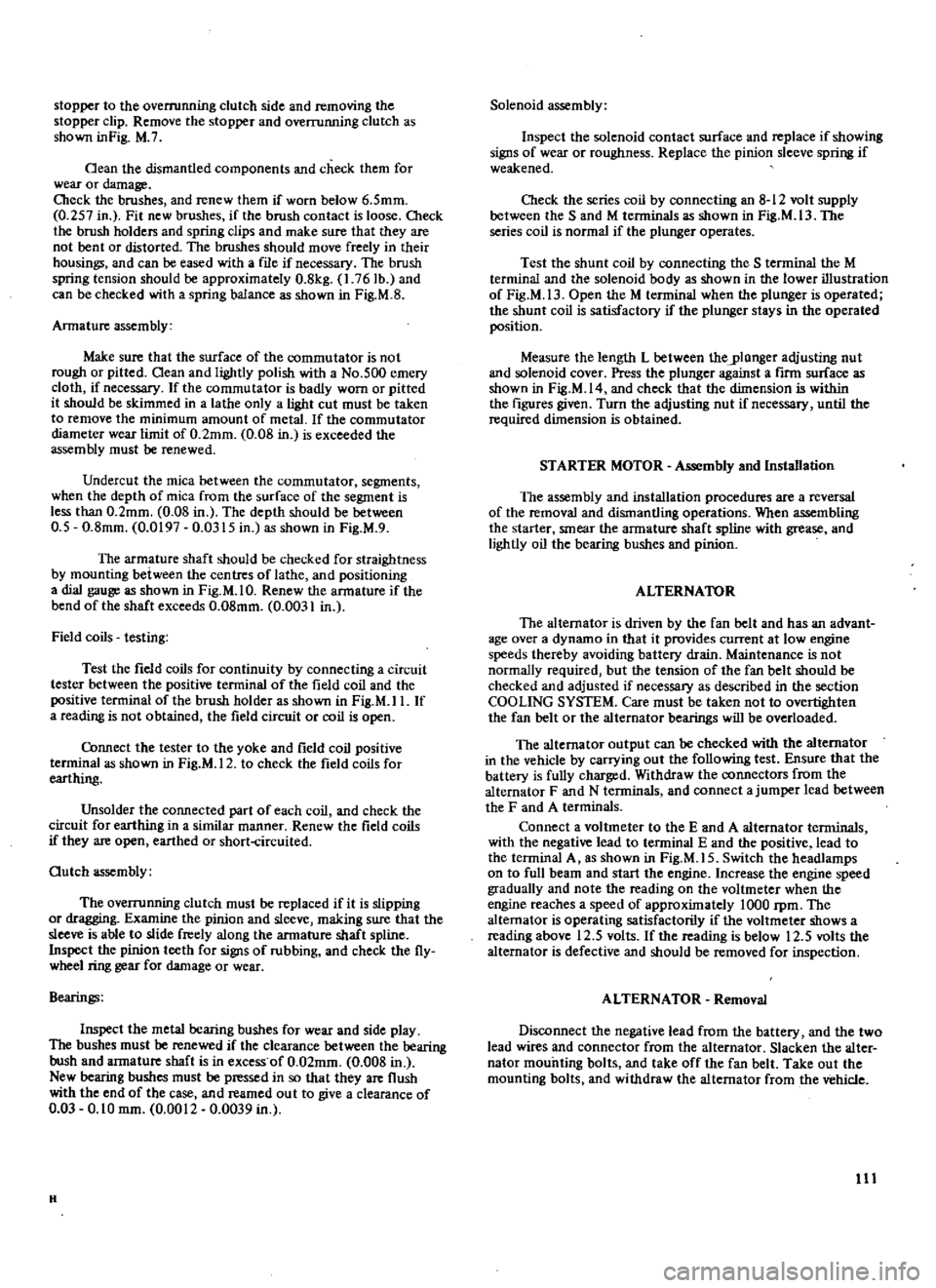
stopper
to
the
overrunning
clutch
side
and
removing
the
stopper
clip
Remove
the
stopper
and
overrunning
clutch
as
shown
inFig
M
7
Oean
the
dismantled
components
and
check
them
for
wear
or
damage
Cbeck
the
brushes
and
renew
them
if
worn
below
6
5mm
0
257
in
Fit
new
brushes
if
the
brush
contact
is
loose
Cbeck
the
brush
holders
and
spring
clips
and
make
sure
that
they
are
not
bent
or
distorted
The
brushes
should
move
freely
in
their
housings
and
can
be
eased
with
a
file
if
necessary
The
brush
spring
tension
should
be
approximately
0
8kg
1
76Ib
and
can
be
checked
with
a
spring
balance
as
shown
in
Fig
M
S
Armature
assembly
Make
sure
that
the
surface
of
the
commutator
is
not
rough
or
pitted
Oean
and
lightly
polish
with
a
No
500
emery
cloth
if
necessary
If
the
commutator
is
badly
worn
or
pitted
it
should
be
skimmed
in
a
lathe
only
a
light
cut
must
be
taken
to
remove
the
minimum
amount
of
metal
If
the
commutator
diameter
wear
limit
of
0
2mm
0
OS
in
is
exceeded
the
assembly
must
be
renewed
Undercut
the
mica
between
the
commutator
segments
when
the
depth
of
mica
from
the
surface
of
the
segment
is
less
than
0
2mm
0
08
in
The
depth
should
be
between
0
5
0
8mm
0
0197
0
0315
in
as
shown
in
Fig
M
9
The
armature
shaft
should
be
checked
for
straightness
by
mounting
between
the
centres
of
lathe
and
positioning
a
dial
gauge
as
shown
in
Fig
M
I
O
Renew
the
armature
if
the
bend
of
the
shaft
exceeds
0
08mm
0
0031
in
Field
coils
testing
Test
the
field
coils
for
continuity
by
connecting
a
circuit
tester
between
the
positive
terminal
of
the
field
coil
and
the
positive
terminal
of
the
brush
holder
as
shown
in
Fig
M
I
I
If
a
reading
is
not
obtained
the
field
circuit
or
coil
is
open
Cbnnect
the
tester
to
the
yoke
and
field
coil
positive
teoninal
as
shown
in
Fig
M
12
to
check
the
field
coils
for
earthing
Unsolder
the
connected
part
of
each
coil
and
check
the
circuit
for
earthing
in
a
similar
manner
Renew
the
field
coils
if
they
are
open
earthed
or
short
circuited
Outch
assembly
The
overrunning
clutch
must
be
replaced
if
it
is
slipping
or
dragging
Examine
the
pinion
and
sleeve
making
sure
that
the
sleeve
is
able
to
slide
freely
along
the
armature
shaft
spline
Inspect
the
pinion
teeth
for
signs
of
rubbing
and
check
the
fly
wheel
ring
gear
for
damage
or
wear
Bearings
Inspect
the
metal
bearing
bushes
for
wear
and
side
play
The
bushes
must
be
renewed
if
the
clearance
between
the
bearing
bush
and
armature
shaft
is
in
excess
of
0
02mm
0
008
in
New
bearing
bushes
must
be
pressed
in
so
that
they
are
flush
with
the
end
of
the
case
and
reamed
ou
t
to
give
a
clearance
of
0
03
0
10
mm
0
0012
0
0039
in
H
Solenoid
assembly
Inspect
the
solenoid
contact
surface
and
replace
if
showing
signs
of
wear
or
roughness
Replace
the
pinion
sleeve
spring
if
weakened
Check
the
series
coil
by
connecting
an
8
12
volt
supply
between
the
Sand
M
terminals
as
shown
in
Fig
M
13
The
series
coil
is
normal
if
the
plunger
operates
Test
the
shunt
coil
by
connecting
the
S
terminal
the
M
terminal
and
the
solenoid
body
as
shown
in
the
lower
illustration
of
Fig
M
13
Open
the
M
terminal
when
the
plunger
is
operated
the
shunt
coil
is
satisfactory
if
the
plunger
stays
in
the
operated
position
Measure
the
length
L
between
theylonger
adjusting
nut
and
solenoid
cover
Press
the
plunger
against
a
firm
surface
as
shown
in
Fig
M
14
and
check
that
the
dimension
is
within
the
figures
given
Turn
the
adjusting
nut
if
necessary
until
the
required
dimension
is
obtained
STARTER
MOTOR
Assembly
and
Installation
The
assembly
and
installation
procedures
are
a
reversal
of
the
removal
and
dismantling
operations
When
assembling
the
starter
smear
the
armature
shaft
spline
with
grease
and
lightly
oil
the
bearing
bushes
and
pinion
ALTERNATOR
The
alternator
is
driven
by
the
fan
belt
and
has
an
advant
age
over
a
dynamo
in
that
it
provides
current
at
low
engine
speeds
thereby
avoiding
battery
drain
Maintenance
is
not
normally
required
but
the
tension
of
the
fan
belt
should
be
checked
and
adjusted
if
necessary
as
described
in
the
section
COOLING
SYSTEM
Care
must
be
taken
not
to
overtighten
the
fan
belt
or
the
alternator
bearings
will
be
overloaded
The
alternator
output
can
be
checked
with
the
alternator
in
the
vehicle
by
carrying
out
the
following
test
Ensure
that
the
battery
is
fully
charged
Withdraw
the
connectors
from
the
alternator
F
and
N
terminals
and
connect
a
jumper
lead
between
the
F
and
A
terminals
Connect
a
voltmeter
to
the
E
and
A
alternator
terminals
with
the
negative
lead
to
terminal
E
and
the
positive
lead
to
the
terminal
A
as
shown
in
Fig
M
IS
Switch
the
headlamps
on
to
full
beam
and
start
the
engine
Increase
the
engine
speed
gradually
and
note
the
reading
on
the
voltmeter
when
the
engine
reaches
a
speed
of
approximately
lOaD
rpm
The
alternator
is
operating
satisfactorily
if
the
voltmeter
shows
a
reading
above
12
5
volts
If
the
reading
is
below
12
5
volts
the
alternator
is
defective
and
should
be
removed
for
inspection
ALTERNATOR
Removal
Disconnect
the
negative
lead
from
the
battery
and
the
two
lead
wires
and
connector
from
the
alternator
Slacken
the
alter
nator
mounting
bolts
and
take
off
the
fan
belt
Take
out
the
mounting
bolts
and
withdraw
the
alternator
from
the
vehicle
III
Page 134 of 171
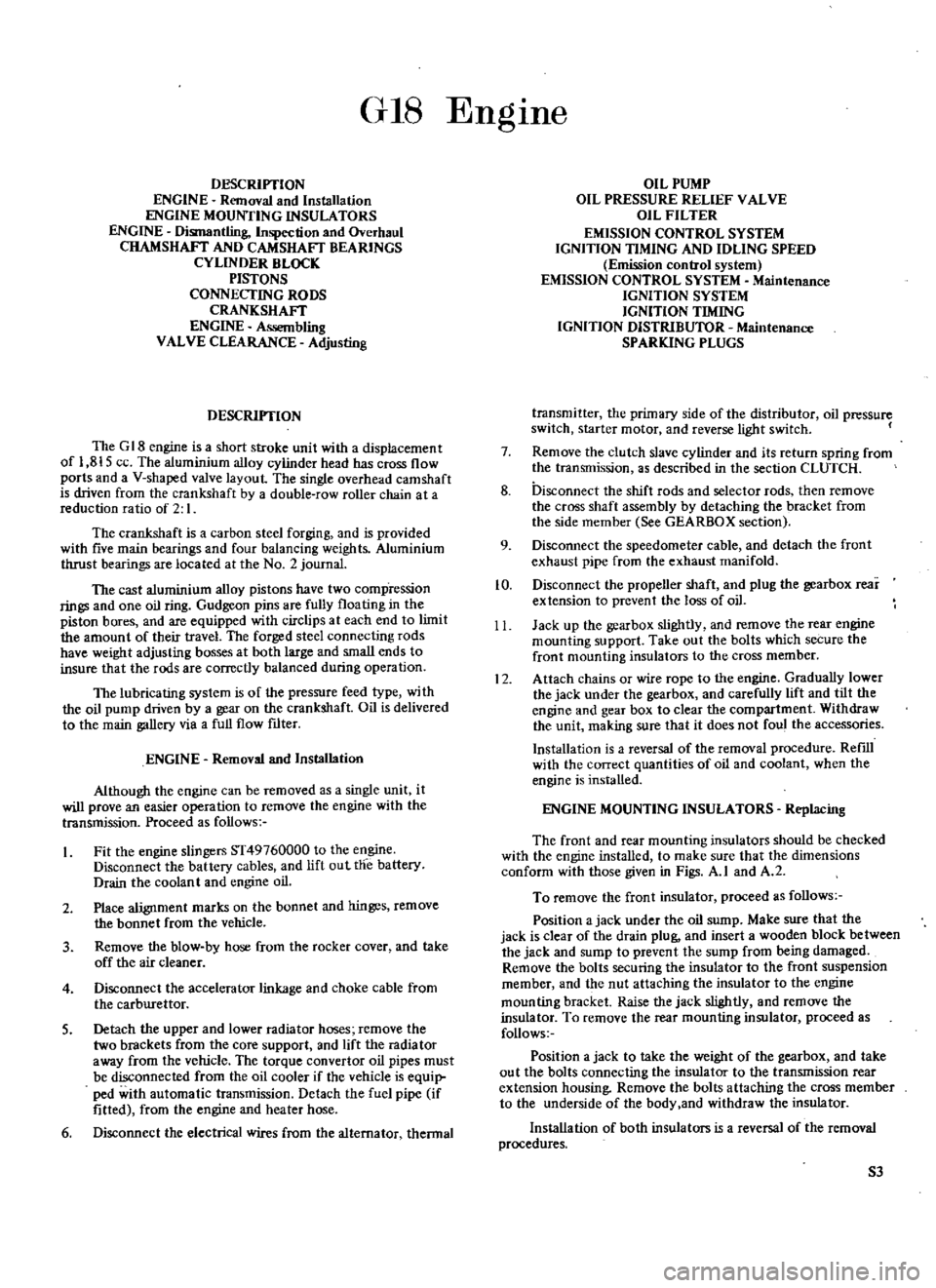
GIS
DESCRIYfION
ENGINE
Removal
and
Installation
ENGINE
MOUNTING
INSULATORS
ENGINE
Dismantling
Inspection
and
Overhaul
CHAMSHAFT
AND
CAMSHAFT
BEARINGS
CYLINDER
BLOCK
PISTONS
CONNECTING
RODS
CRANKSHAFT
ENGINE
Assembling
VALVE
CLEARANCE
Adjusting
DESCRIYfION
The
G
18
engine
is
a
short
stroke
unit
with
a
displacement
of
1
815
ce
The
aluminium
alloy
cylinder
head
has
cross
flow
ports
and
a
V
shaped
valve
layout
The
single
overhead
camshaft
is
driven
from
the
crankshaft
by
a
double
row
roller
chain
at
a
reduction
ratio
of
2
I
The
crankshaft
is
a
carbon
steel
forging
and
is
provided
with
five
main
bearings
and
four
balancing
weights
Aluminium
thrust
bearings
are
located
at
the
No
2
journal
The
cast
aluminium
alloy
pistons
have
two
comp
ression
rings
and
one
oil
ring
Gudgeon
pins
are
fully
floating
in
the
piston
bores
and
are
equipped
with
circlips
at
each
end
to
limit
the
amount
of
their
travel
The
forged
steel
connecting
rods
have
weight
adjusting
bosses
at
both
large
and
small
ends
to
insure
that
the
rods
are
correctly
balanced
during
operation
The
lubricating
system
is
of
the
pressure
feed
type
with
the
oil
pump
driven
by
a
gear
on
the
crankshaft
Oil
is
delivered
to
the
main
gallery
via
a
full
flow
ftlter
ENGINE
Removal
and
Installation
Although
the
engine
can
be
removed
as
a
single
unit
it
will
prove
an
easier
operation
to
remove
the
engine
with
the
transmission
Proceed
as
follows
Fit
the
engine
slingers
ST49760000
to
the
engine
Disconnect
the
battery
cables
and
lift
out
the
battery
Drain
the
coolant
and
engine
oil
2
Place
alignment
marks
on
the
bonnet
and
hinges
remove
the
bonnet
from
the
vehicle
3
Remove
the
blow
by
hose
from
the
rocker
cover
and
take
off
the
air
cleaner
4
Disconnect
the
accelerator
linkage
and
choke
cable
from
the
carburettor
S
Detach
the
upper
and
lower
radiator
hoses
remove
the
two
brackets
from
the
core
support
and
lift
the
radia
tor
away
from
the
vehicle
The
torque
convertor
oil
pipes
must
be
disconnected
from
the
oil
cooler
if
the
vehicle
is
equip
ped
with
automatic
transmission
Detach
the
fuel
pipe
if
fitted
from
the
engine
and
heater
hose
6
Disconnect
the
electrical
wires
from
the
alternator
thennal
EngIne
OIL
PUMP
OIL
PRESSURE
RELIEF
VALVE
OIL
FILTER
EMISSION
CONTROL
SYSTEM
IGNITION
TIMING
AND
IDLING
SPEED
Emission
control
system
EMISSION
CONTROL
SYSTEM
Maintenance
IGNITION
SYSTEM
IGNITION
TIMING
IGNITION
DISTRIBUTOR
Maintenance
SPARKING
PLUGS
transmitter
the
primary
side
of
the
distributor
oil
pressure
switch
starter
motor
and
reverse
light
switch
7
Remove
the
clutch
slave
cylinder
and
its
return
spring
from
the
transmission
as
described
in
the
section
CLUTCH
8
Disconnect
the
shift
rods
and
selector
rods
then
remove
the
cross
shaft
assembly
by
detaching
the
bracket
from
the
side
member
See
GEARBOX
section
9
Disconnect
the
speedometer
cable
and
detach
the
front
exhaust
pipe
from
the
exhaust
manifold
10
Disconnect
the
propeller
shaft
and
plug
the
gearbox
rear
extension
to
prevent
the
loss
of
oil
11
Jack
up
the
gearbox
slightly
and
remove
the
rear
engine
mounting
support
Take
out
the
bolts
which
secure
the
front
mounting
insulators
to
the
cross
member
12
Attach
chains
or
wire
rope
to
the
engine
Gradually
lower
the
jack
under
the
gearbox
and
carefully
lift
and
tilt
the
engine
and
gear
box
to
clear
the
compartment
Withdraw
the
unit
making
sure
that
it
does
not
foul
the
accessories
Installation
is
a
reversal
of
the
removal
procedure
RefIll
with
the
correct
quantities
of
oil
and
coolant
when
the
engine
is
installed
ENGINE
MOUNTING
INSULATORS
Replacing
The
front
and
rear
mounting
insulators
should
be
checked
with
the
engine
installed
to
make
sure
that
the
dimensions
conform
with
those
given
in
Figs
A
I
and
A
2
To
remove
the
front
insulator
proceed
as
follows
Position
a
jack
under
the
oil
sump
Make
sure
that
the
jack
is
clear
of
the
drain
plug
and
insert
a
wooden
block
between
the
jack
and
sump
to
prevent
the
sump
from
being
damaged
Remove
the
bolts
securing
the
insulator
to
the
front
suspension
member
and
the
nut
attaching
the
insulator
to
the
engine
mounting
bracket
Raise
the
jack
slightly
and
remove
the
insulator
To
remove
the
rear
mounting
insulator
proceed
as
follows
Position
a
jack
to
take
the
weight
of
the
gearbox
and
take
out
the
bolts
connecting
the
insulator
to
the
transmission
rear
extension
housing
Remove
the
bolts
attaching
the
cross
member
to
the
underside
of
the
body
and
withdraw
the
insulator
Installation
of
both
insulators
is
a
reversal
of
the
removal
procedures
S3