engine overheat DATSUN 610 1969 Workshop Manual
[x] Cancel search | Manufacturer: DATSUN, Model Year: 1969, Model line: 610, Model: DATSUN 610 1969Pages: 171, PDF Size: 10.63 MB
Page 26 of 171
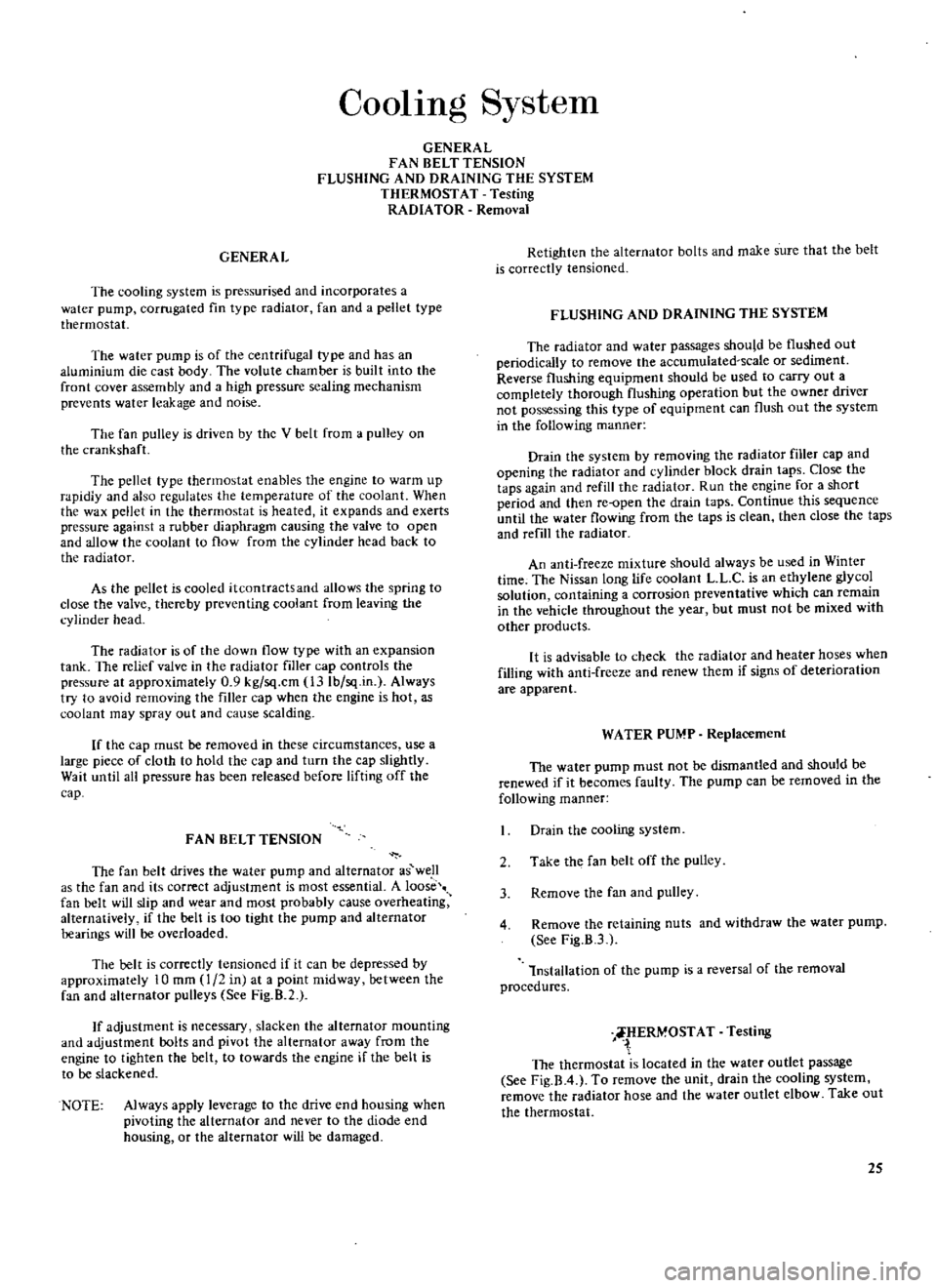
CoolIng
System
GENERAL
FAN
BELT
TENSION
FLUSHING
AND
DRAINING
THE
SYSTEM
THERMOSTAT
Testing
RADlA
TOR
Removal
GENERAL
The
cooling
system
is
pressurised
and
incorporates
a
water
pump
corrugated
fin
type
radiator
fan
and
a
pellet
type
thermostat
The
water
pump
is
of
the
centrifugal
type
and
has
an
aluminium
die
cast
body
The
volute
chamber
is
built
into
the
front
cover
assembly
and
a
high
pressure
sealing
mechanism
prevents
water
leakage
and
noise
The
fan
pulley
is
driven
by
the
V
belt
from
a
pulley
on
the
crankshaft
he
pellct
type
thermostat
enables
the
engine
to
warm
up
rapidlY
and
also
regulates
the
temperature
of
the
coolant
When
the
wax
pellet
in
the
thermostat
is
heated
it
expands
and
exerts
pressure
against
a
rubber
diaphragm
causing
the
valve
to
open
and
allow
the
coolant
to
flow
from
the
cylinder
head
back
to
the
radiator
As
the
pellet
is
cooled
itcontractsand
allows
the
spring
to
close
the
valve
thereby
preventing
coolant
from
leaving
the
cylinder
head
The
rad
ator
is
of
the
down
flow
type
with
an
expansion
tank
The
relIef
valve
in
the
radiator
filler
cap
controls
the
pressure
at
approximately
0
9
kg
sq
cm
l3Ib
sq
in
Always
try
to
avoid
removing
the
filler
cap
when
the
engine
is
hot
as
coolant
may
spray
out
and
cause
scalding
If
the
cap
must
be
removed
in
these
circumstances
use
a
lar
e
pic
c
of
cloth
to
hold
the
cap
and
turn
the
cap
sli
htlY
Walt
until
all
pressure
has
been
released
before
lifting
off
the
cap
F
AN
BELT
TENSION
The
fan
belt
drives
the
water
pump
and
alternator
as
well
as
the
fan
and
its
correct
adjustment
is
most
essential
A
loose
fan
belt
will
sl
ip
and
Y
e
r
and
most
probably
cause
overheating
alternatively
If
the
belt
IS
too
tight
the
pump
and
alternator
bearings
will
be
overloaded
The
belt
is
correctly
tensioned
if
it
can
be
depressed
by
approximately
10
mm
1
2
in
at
a
point
midway
between
the
fan
and
alternator
pulleys
See
Fig
R2
If
adjustment
is
neces
ary
slacken
the
alternator
mounting
and
adjustment
bolts
and
pivot
the
alternator
away
from
the
engine
to
tighten
the
belt
to
towards
the
engine
if
the
belt
is
to
be
slackened
NOTE
Always
apply
leverage
to
the
drive
end
housing
when
pivoting
the
alternator
and
never
to
the
diode
end
housing
or
the
alternator
will
be
damaged
Retighten
the
alternator
bolts
and
make
SUfe
that
the
belt
is
correctly
tensioned
FLUSHING
AND
DRAINING
THE
SYSTEM
The
radiator
and
water
passages
should
be
flushed
out
periodically
to
remove
the
accumulated
scale
or
sediment
Reverse
flushing
equipment
should
be
used
to
carry
out
a
completely
thorough
flushing
operation
but
the
owner
drivef
not
possessing
this
type
of
equipment
can
flush
out
the
system
in
the
following
manner
Drain
the
system
by
removing
the
radiator
filler
cap
and
opening
the
radiator
and
cylinder
block
drain
taps
Close
the
taps
again
and
refill
the
radiator
Run
the
engine
for
a
ShOft
period
and
then
rc
open
the
drain
taps
Continue
this
sequence
until
the
water
flowing
from
the
taps
is
clean
then
close
the
taps
and
refill
the
radiator
An
anti
freeze
mixture
should
always
be
used
in
Winter
time
The
Niss3n
long
life
coolant
L
L
c
is
an
ethylene
glycol
solution
containing
a
corrosion
preventative
which
can
remain
in
the
vehicle
throughout
the
year
but
must
not
be
mixed
with
other
products
It
is
advisable
to
check
the
radiator
and
heater
hoses
when
filling
with
anti
freeze
and
renew
them
if
signs
of
deterioration
are
apparent
WATER
PUMP
Replacement
The
water
pump
must
not
be
dismantled
and
should
be
renewed
if
it
becomes
faulty
The
pump
can
be
removed
in
the
following
manner
Drain
the
cooling
system
2
Take
the
fan
belt
off
the
pulley
3
Remove
the
fan
and
pulley
4
Remove
the
retaining
nuts
and
withdraw
the
water
pump
See
Fig
B
3
lnstallation
of
the
pump
is
a
reversal
of
the
removal
procedures
rERMOST
ATTesting
The
thermostat
is
located
in
the
water
outlet
passage
See
Fig
B
4
To
remove
the
unit
drain
the
cooling
system
remove
the
radiator
hose
and
the
water
outlet
elbow
Take
out
the
thermostat
25
Page 32 of 171
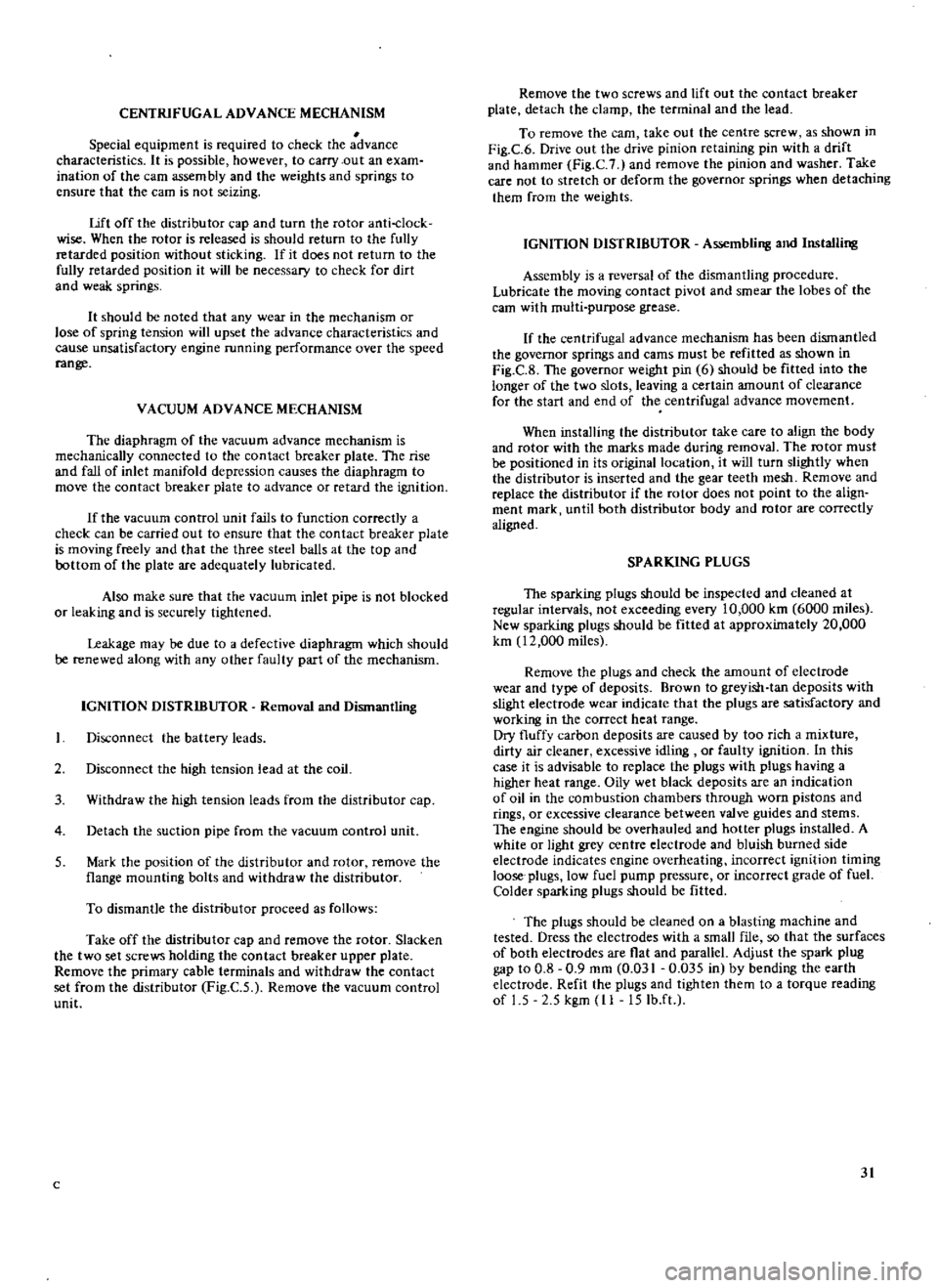
CENTRIFUGAL
ADVANCE
MECHANISM
Special
equipment
is
required
to
check
the
advance
characteristics
It
is
possible
however
to
carry
out
an
exam
ination
of
the
caffi
assembly
and
the
weights
and
springs
to
ensure
that
the
earn
is
not
seizing
Lift
off
the
distributor
cap
and
turn
the
rotor
anti
clock
wise
When
the
rotor
is
released
is
should
return
to
the
fully
retarded
position
without
sticking
If
it
does
not
return
to
the
fully
retarded
position
it
will
be
necessary
to
check
for
dirt
and
weak
springs
It
should
be
noted
that
any
wear
in
the
mechanism
or
lose
of
spring
tension
will
upset
the
advance
characteristics
and
cause
unsatisfactory
engine
running
performance
over
the
speed
range
VACUUM
ADVANCE
MECHANISM
The
diaphragm
of
the
vacuum
advance
mechanism
is
mechanically
connected
to
the
contact
breaker
plate
The
rise
and
fall
of
inlet
manifold
depression
causes
the
diaphragm
to
move
the
contact
breaker
plate
to
advance
or
retard
the
ignition
If
the
vacuum
control
unit
fails
to
function
correctly
a
check
can
be
carried
out
to
ensure
that
the
contact
breaker
plate
is
moving
freely
and
that
the
three
steel
balls
at
the
top
and
oottom
of
the
plate
are
adequately
lubricated
Also
make
sure
that
the
vacuum
inlet
pipe
is
not
blocked
or
leaking
and
is
securely
tightened
Leakage
may
be
due
to
a
defective
diaphragm
which
should
be
renewed
along
with
any
other
faulty
part
of
the
mechanism
IGNITION
DlSTRffiUTOR
Removal
and
Dismantling
Disconnect
the
battery
leads
2
Disconnect
the
high
tension
lead
at
the
coil
3
Withdraw
the
high
tension
leads
from
the
distributor
cap
4
Detach
the
suction
pipe
from
the
vacuum
control
unit
5
Mark
the
position
of
the
distributor
and
rotor
remove
the
flange
mounting
bolts
and
withdraw
the
distributor
To
dismantle
the
distributor
proceed
as
follows
Take
off
the
distributor
cap
and
remove
the
rotor
Slacken
the
two
set
screws
holding
the
contact
breaker
upper
plate
Remove
the
primary
cable
terminals
and
withdraw
the
contact
set
from
the
distributor
Fig
C
S
Remove
the
vacuum
control
unit
c
Remove
the
two
screws
and
lift
out
the
contact
breaker
plate
detach
the
clamp
the
terminal
and
the
lead
To
remove
the
cam
take
out
the
centre
screw
as
shown
in
Fig
e
6
Drive
out
the
drive
pinion
retaining
pin
with
a
drift
and
hammer
Fig
e
and
remove
the
pinion
and
washer
Take
care
not
to
stretch
or
deform
the
governor
springs
when
detaching
them
from
the
weights
IGNITION
DISTRIBUTOR
Assembling
and
Installing
Assembly
is
a
reversal
of
the
dismantling
procedure
Lubricate
the
moving
contact
pivot
and
smear
the
lobes
of
the
cam
with
multi
purpose
grease
If
the
centrifugal
advance
mechanism
has
been
dismantled
the
governor
springs
and
cams
must
be
refitted
as
shown
in
Fig
e
8
The
governor
weight
pin
6
should
be
fitted
into
the
longer
of
the
two
slots
leaving
a
certain
amount
of
clearance
for
the
start
and
end
of
the
centrifugal
advance
movement
When
installing
the
distributor
take
care
to
align
the
body
and
rotor
with
the
marks
made
during
removal
The
rotor
must
be
positioned
in
its
original
location
it
will
turn
slightly
when
the
distributor
is
inserted
and
the
gear
teeth
mesh
Remove
and
replace
the
distributor
if
the
rotor
does
not
point
to
the
align
ment
mark
until
both
distributor
body
and
rotor
are
correctly
aligned
SPARKING
PLUGS
The
sparking
plugs
should
be
inspected
and
cleaned
at
regular
intervals
not
exceeding
every
10
000
km
6000
miles
New
sparking
plugs
should
be
fitted
at
approximately
20
000
km
12
000
miles
Remove
the
plugs
and
check
the
amount
of
electrode
wear
and
type
of
deposits
Brown
to
greyish
tan
deposits
with
slight
electrode
wear
indicate
that
the
plugs
are
satisfactory
and
working
in
the
correct
heat
range
Dry
fluffy
carbon
deposits
are
caused
by
too
rich
a
mixture
dirty
air
cleaner
excessive
idling
or
faulty
ignition
In
this
case
it
is
advisable
to
replace
the
plugs
with
plugs
having
a
higher
heat
range
Oily
wet
black
deposits
are
an
indication
of
oil
in
the
combustion
chambers
through
worn
pistons
and
rings
or
excessive
clearance
between
valve
guides
and
stems
The
engine
should
be
overhauled
and
hotter
plugs
installed
A
white
or
light
grey
centre
electrode
and
bluish
burned
side
electrode
indicates
engine
overheating
incorrect
ignition
timing
loose
plugs
low
fuel
pump
pressure
or
incorrect
grade
of
fuel
Colder
sparking
plugs
should
be
fitted
The
plugs
should
be
cleaned
on
a
blasting
machine
and
tested
Dress
the
electrodes
with
a
small
file
so
that
the
surfaces
of
both
electrodes
are
flat
and
parallel
Adjust
the
spark
plug
gap
to
0
8
0
9
mm
0
031
0
035
in
by
bending
the
earth
electrode
Refit
the
plugs
and
tighten
them
to
a
torque
reading
of
1
5
2
5
kgm
II
15Ib
ft
31
Page 126 of 171
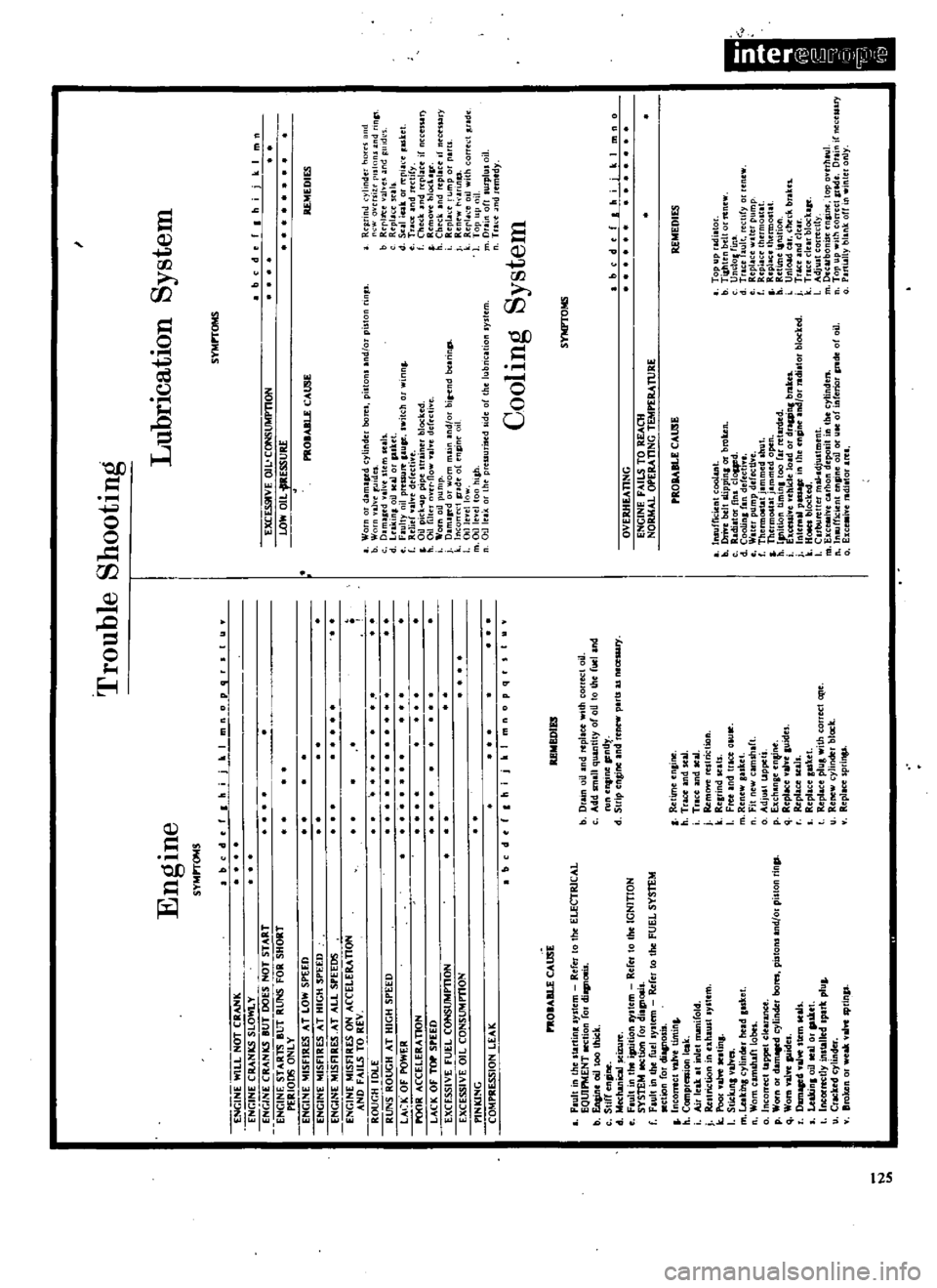
N
Engme
SYMPTOMS
I
Trouble
Shooting
Lubrication
System
SYMPTOMS
bed
t
f
I
h
i
1m
0
p
q
r
I
I
II
bed
t
f
I
h
Ii
I
m
n
ENGINE
WILL
NOT
CRANK
ENGINE
CRANKS
SLOWLY
ENGINE
CRANkS
BUT
OOES
NOT
START
ENGINE
STARTS
BUT
RUNS
FOR
SHORT
PERIODS
aNL
Y
ENGINE
I
tISFIRES
AT
LOW
SPEED
ENGINE
MISFIRES
AT
HIGH
SPEED
ENGINE
MISFIRES
AT
ALL
SPEEDS
ENGINE
MISFIRES
ON
ACCELERATION
AND
FAILS
TO
REV
ROUGH
IDLE
RUNS
ROUGH
AT
HIGH
SPEED
lACK
OF
POWER
POOR
CCElERA
nON
LACK
OF
TOP
SPEED
EXCESSIVE
FUEL
CONSUMmON
EXCESSIVE
OIL
CONSUMmON
PINKING
COMPRESSION
LEAK
PROIABLE
CAUSE
Faull
In
th
e
ltartinll
IYltem
Refer
to
the
ELECTRICAL
EQUIPMENT
leetion
fOI
dilllflOlIll
b
Eft
ineoiltoothick
Stiffenpne
d
Mechanieal
scimre
Flult
In
lhe
IpUlion
I
ltem
Refer
to
the
IGNITION
SYSTEM
IeCtion
for
di
I
f
Flult
the
fuellYlltm
Refer
to
the
FUEL
SYSTEM
Clion
or
di
l
OIII
Incomcl
tllvetlmln
h
ComprellllllIU
IClk
Air
leak
IRlel
JIlIIni
old
j
Reltriction
nhlu5t5ylltm
Ie
Poor
alYe
WIIIIIJ
I
Stick
tnlvall
n
m
Lclklnl
cylinder
held
Illke
Womcamlhlft
lobel
IncolTe
ttappetclurance
p
Worn
dlm
ed
cylinder
born
pUlon5
Ind
or
pll
f1np
q
Wom
nl
fC
paides
Damaced
a1wlttmseal
LeWnloilwaI
pu
e
Incorrectly
installed
apark
plu
CrICked
cylinder
Broken
weakv
w
sprinp
EXCES9lVE
OIL
CONSUMPTION
WW
OIL
ilRESSURE
PROIABLE
CAUSE
REMEDIES
I
Worn
dlmalJl
dcyhnderbon
P
v
lnd
orpulu
nnr
s
b
WorJl
valve
r
uides
C
D
m
led
valve
lIemluls
d
Lnlunr
oil
ul
pillet
e
Flulty
nil
P
uu
IluP
Iwnch
wmn
f
Relief
valve
defecuve
011
pick
up
pipellfline
blocked
h
011
filler
nver
flow
yaJYe
dcffe
WO
n
oil
pump
J
Dlmllfd
om
maUl
Ind
or
bl
nd
b
lnnll
l
lncorreCllndeofentpneoil
l
Oil
level
10
m
Oillevel
tnnhllh
Oillelk
the
preuunled
Ilde
of
the
lubn
IYSfem
p
Tldc
Rel1
f1nd
yllOde1
ne
OVCntZl
nd
nnJ
b
Rcpltte
v
lve
and
Iltd
c
Repl
cc
5c
l
d
Sullu
rt
pl
cp
aI
kCl
e
Trice
Ind
rtClify
f
heel
lod
replace
if
nccess
T
RemoYcblQChJC
h
Chcck
Ind
repllcclfncct
i
ry
i
Repll
e
rump
J
Renew
nnp
k
Rerl
ec
OIl
with
l
Top
up
oil
m
DTllnofllurpIUloil
Tn
ndremedy
Coolmg
System
b
r
h
j
I
m
p
q
d
REMEDIES
SYMI
IOMS
b
Drlm
oiJ
nd
rcpl
ce
with
ot
Add
smlll
quanllty
n
oil
to
the
fuel
Ind
rune
lmeFnd
d
SlfIpenJine
Ind
renew
p
ru
asn
celllry
I
bed
t
f
I
h
I
i
k
I
mn
0
OVERHEATING
ENGINE
FAILS
TO
REAOI
NORMAL
OPERATING
TEMPERAt
lRE
PROIAILE
CAUSE
REMEDIES
I
RetUne
enJine
h
Trace
ndseal
Tr
Ind
seal
j
RemO
f
t
rellnction
k
Relnnd
sel
I
Freelnd
trice
C
UIe
m
Renewguke
Fit
new
clmlhlrt
AdJult
t
appeti
p
bch
ngeenfin
q
Replacevalnluldes
Rtplace
seall
Repllccgukel
Repllcc
plulwlth
correct
Cl
Ie
Renew
cyhndcrblock
Repllce
5prLnp
I
IlIIIIfficien
coolant
b
DriYebellllippinIOfbrobn
c
RldiatOf
fUll
cloq
ed
d
Coo
inlflndefeclln
e
Wit
pl1mpdtfectlve
f
ThelTllOllatj
mmed
Ihul
Thermost
j
mmed
open
r
t
eti
I
kt
r
re
a
q
brake
j
lntel1laJp
se
lheenpne
ndforradi
torbloeked
11
HOItI
blocked
I
Carburetterm
djullmem
m
Excellive
arbon
depolit
in
thecylinden
In
ffici
enpneoil
uae
of
inferior
p1Ide
of
oil
Exce
inrldi
lorlrea
I
Topupradil
v
b
Ti
htenbdtorftnc
I
t
rmify
e
Repl
cwaterpump
f
Rcpll
e
thermoltll
I
Replleclhermolt
t
h
RetimeiaTUlion
i
Unload
ear
check
brl
ktt
j
Trace
ndclu
k
TfI
cdUrblockaae
L
AdjUllcorrc
cth
m
Decarbonise
fO
tne
top
overh
uJ
Top
up
wlth
correct
rade
Dr
inifneceUlry
PUIl
lly
blink
off
in
winter
only