reset DATSUN 610 1969 Workshop Manual
[x] Cancel search | Manufacturer: DATSUN, Model Year: 1969, Model line: 610, Model: DATSUN 610 1969Pages: 171, PDF Size: 10.63 MB
Page 88 of 171
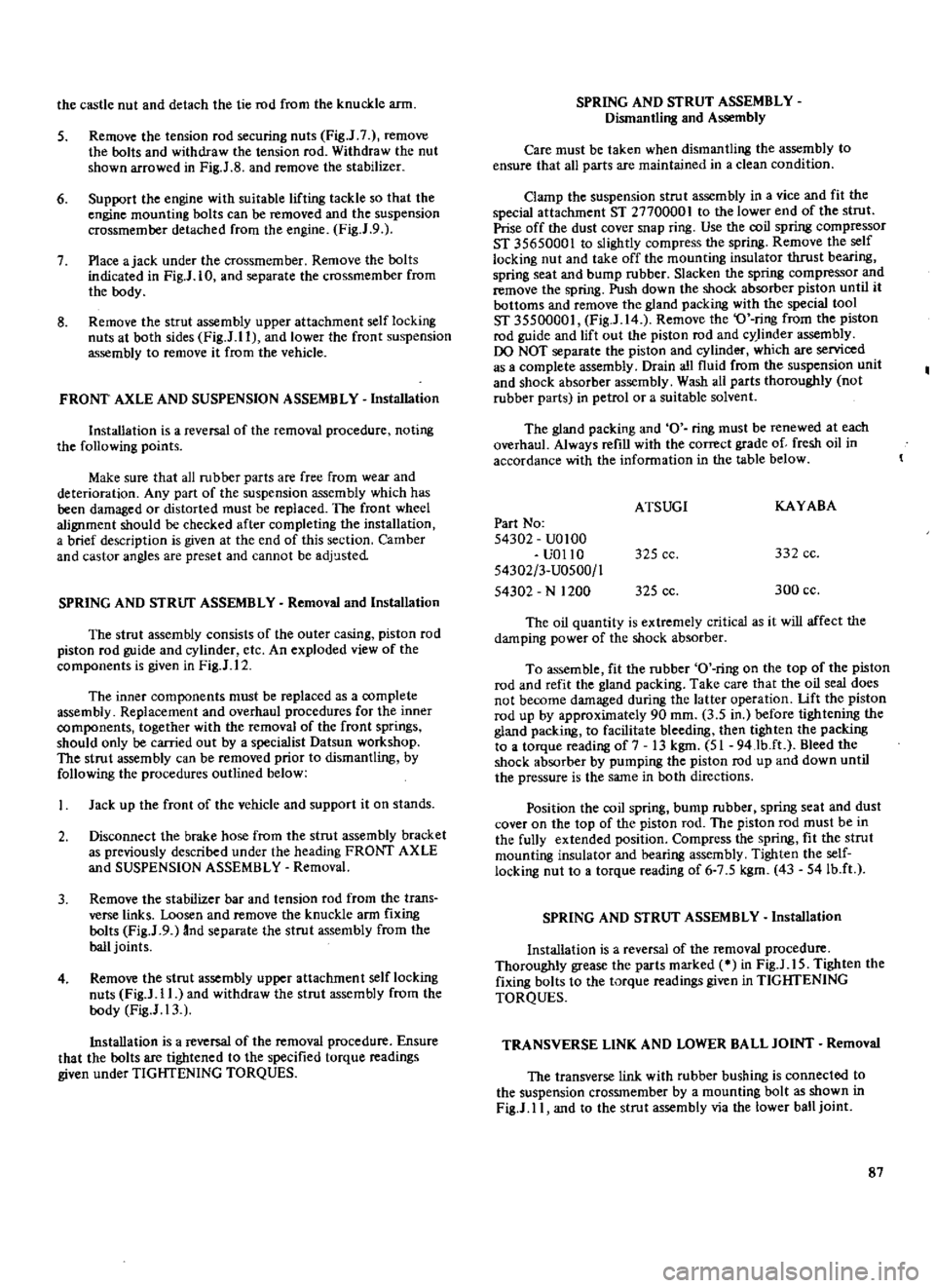
the
castle
nut
and
detach
the
tie
rod
from
the
knuckle
arm
5
Remove
the
tension
rod
securing
nuts
Fig
J
7
remove
the
bolts
and
withdraw
the
tension
rod
Withdraw
the
nut
shown
arrowed
in
FigJ
8
and
remove
the
stabilizer
6
Support
the
engine
with
suitable
lifting
tackle
so
that
the
engine
mounting
bolts
can
be
removed
and
the
suspension
crossmember
detached
from
the
engine
FigJ
9
7
Place
ajack
under
the
crossmember
Remove
the
bolts
indicated
in
Fig
J
IO
and
separate
the
crossmember
from
the
body
8
Remove
the
strut
assembly
upper
attachment
self
locking
nuts
at
both
sides
Fig
J
ll
and
lower
the
front
suspension
assembly
to
remove
it
from
the
vehicle
FRONT
AXLE
AND
SUSPENSION
ASSEMBLY
Installation
Installation
is
a
reversal
of
the
removal
procedure
noting
the
following
points
Make
sure
that
all
rubber
parts
are
free
from
wear
and
deterioration
Any
part
of
the
suspension
assembly
which
has
been
damaged
or
distorted
must
be
replaced
The
front
wheel
alignment
should
be
checked
after
completing
the
installation
a
brief
description
is
given
at
the
end
of
this
section
Camber
and
castor
angles
are
preset
and
cannot
be
adjusted
SPRING
AND
STRUf
ASSEMBLY
Removal
and
Installation
The
strut
assembly
consists
of
the
outer
casing
piston
rod
piston
rod
guide
and
cylinder
etc
An
exploded
view
of
the
components
is
given
in
Fig
J
12
The
inner
components
must
be
replaced
as
a
complete
assembly
Replacement
and
overhaul
procedures
for
the
inner
components
together
with
the
removal
of
the
front
springs
should
only
be
carried
out
by
a
specialist
Datsun
workshop
The
strut
assembly
can
be
removed
prior
to
dismantling
by
following
the
procedures
outlined
below
Jack
up
the
front
of
the
vehicle
and
support
it
on
stands
2
Disconnect
the
brake
hose
from
the
strut
assembly
bracket
as
previously
described
under
the
heading
FRONT
AXLE
and
SUSPENSION
ASSEMBLY
Removal
3
Remove
the
stabilizer
bar
and
tension
rod
from
the
trans
verse
links
Loosen
and
remove
the
knuckle
arm
fixing
bolts
Fig
J
9
And
separate
the
strut
assembly
from
the
ball
joints
4
Remove
the
strut
assembly
upper
attachment
self
locking
nuts
Fig
J
11
and
withdraw
the
strut
assembly
from
the
body
Fig
J
13
Installation
is
a
reversal
of
the
removal
procedure
Ensure
that
the
bolts
are
tightened
to
the
specified
torque
readings
given
under
TIGHTENING
TORQUES
SPRING
AND
STRUT
ASSEMBLY
Dismantling
and
Assembly
Care
must
be
taken
when
dismantling
the
assembly
to
ensure
that
aU
parts
are
maintained
in
a
clean
condition
Clamp
the
suspension
strut
assembly
in
a
vice
and
fit
the
special
attachment
ST
2770000
I
to
the
lower
end
of
the
strut
Prise
off
the
dust
cover
snap
ring
Use
the
coil
spring
compressor
ST
35650001
to
slightly
compress
the
spring
Remove
the
self
locking
nut
and
take
off
the
mounting
insulator
thrust
bearing
spring
seat
and
bump
rubber
Slacken
the
spring
compressor
and
remove
the
spring
Push
down
the
shock
absorber
piston
until
it
bottoms
and
remove
the
gland
packing
with
the
special
tool
ST
35500001
Fig
J
14
Remove
the
O
ring
from
the
piston
rod
guide
and
lift
out
the
piston
rod
and
cy
linder
assembly
00
NOT
separate
the
piston
and
cylinder
which
are
serviced
as
a
complete
assembly
Drain
all
fluid
from
the
suspension
unit
and
shock
absorber
assembly
Wash
all
parts
thoroughly
not
rubber
parts
in
petrol
or
a
suitable
solvent
The
gland
packing
and
0
ring
must
be
renewed
at
each
overhaul
Always
refill
with
the
correct
grade
of
fresh
oil
in
accordance
with
the
information
in
the
table
below
ATSUGI
KAYABA
Part
No
54302
UO
100
UOl10
325
cc
332
cc
54302
3
U0500
1
54302
N
1200
325
cc
300
cc
The
oil
quantity
is
extremely
critical
as
it
will
affect
the
damping
power
of
the
shock
absorber
To
assemble
fit
the
rubber
O
ring
on
the
top
of
the
piston
rod
and
refit
the
gland
packing
Take
care
that
the
oil
seal
does
not
become
damaged
during
the
latter
operation
Lift
the
piston
rod
up
by
approximately
90
mm
3
5
in
before
tightening
the
gland
packing
to
facilitate
bleeding
then
tighten
the
packing
to
a
torque
reading
of
7
13
kgm
51
94Jb
ft
Bleed
the
shock
absorber
by
pumping
the
piston
rod
up
and
down
until
the
pressure
is
the
same
in
both
directions
Position
the
coil
spring
bump
rubber
spring
seat
and
dust
cover
on
the
top
of
the
piston
rod
The
piston
rod
must
be
in
the
fully
extended
position
Compress
the
spring
fit
the
strut
mounting
insulator
and
bearing
assembly
Tighten
the
self
locking
nut
to
a
torque
reading
of
6
7
5
kgm
43
541b
ft
SPRING
AND
STRUT
ASSEMBLY
Installation
Installation
is
a
reversal
of
the
removal
procedure
Thoroughly
grease
the
parts
marked
in
Fig
J
15
Tighten
the
fixing
bolts
to
the
torque
readings
given
in
TIGHfENING
TORQUES
TRANSVERSE
LINK
AND
LOWER
BALL
JOINT
Removal
The
transverse
link
with
rubber
bushing
is
connected
to
the
suspension
crosSlTIember
by
a
mounting
bolt
as
shown
in
Fig
J
11
and
to
the
strut
assembly
via
the
lower
ball
joint
87
Page 89 of 171
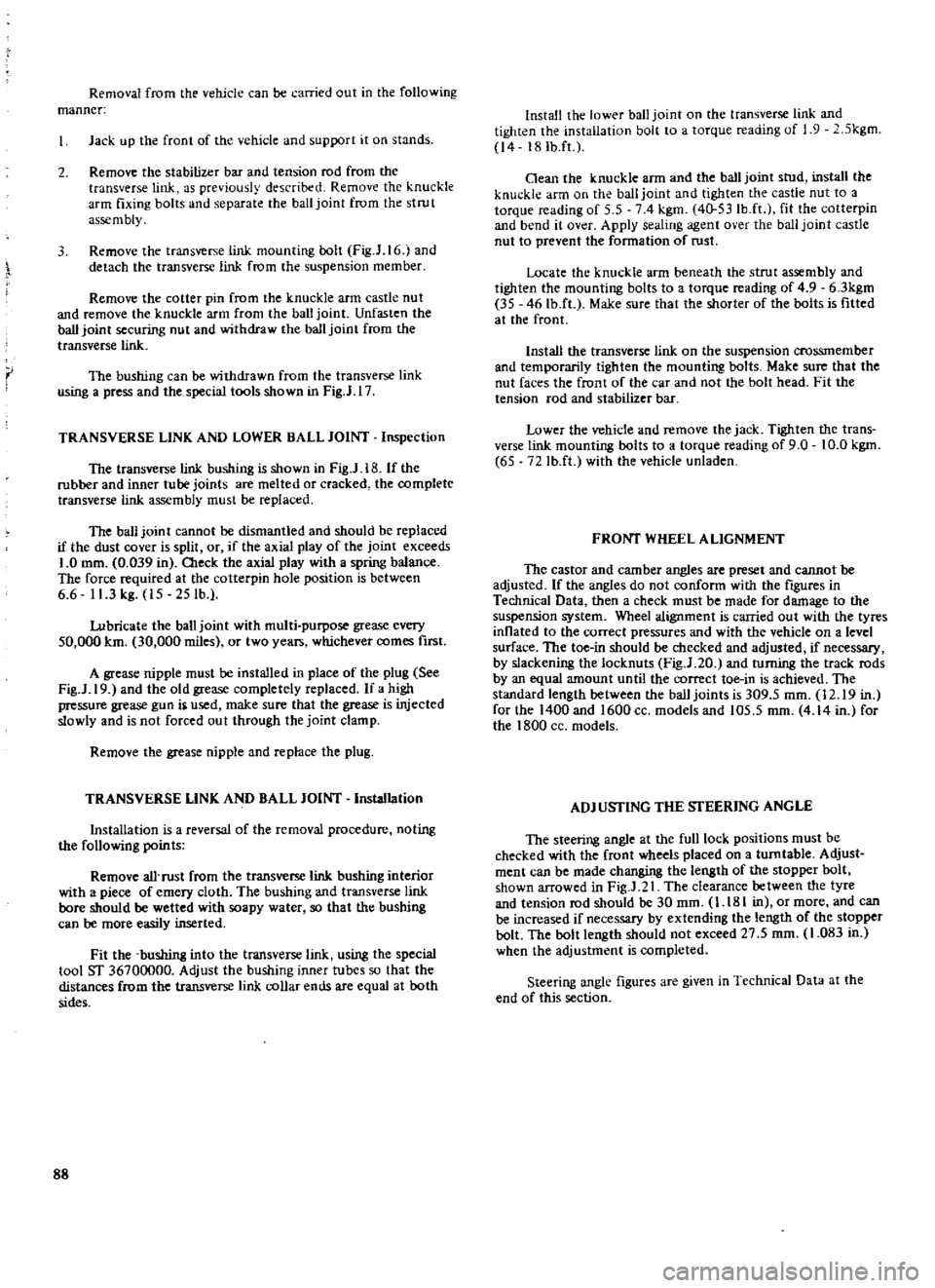
Removal
from
the
vehicle
can
be
carried
out
in
the
following
manner
Jack
up
the
front
of
the
vehicle
and
support
it
on
stands
2
Remove
the
stabilizer
bar
and
tension
rod
from
the
transverse
link
as
previously
described
Remove
the
knuckle
arm
fixing
bolts
and
separate
the
ball
joint
from
the
strut
asse
m
bly
3
Remove
the
transverse
link
mounting
bolt
Fig
J
16
and
detach
the
transverse
link
from
the
suspension
member
Remove
the
cotter
pin
from
the
knuckle
arm
castle
nut
and
remove
the
knuckle
arm
from
the
ban
joint
Unfasten
the
ball
joint
securing
nut
and
withdraw
the
ball
joint
from
the
transverse
link
r
The
bushing
can
be
withdrawn
from
the
transverse
link
using
a
press
and
the
special
tools
shown
in
Fig
J
17
TRANSVERSE
LINK
AND
LOWER
BALL
JOINT
Inspection
The
transverse
link
bushing
is
shown
in
Fig
J
18
If
the
rubber
and
inner
tube
joints
are
melted
or
cracked
the
complete
transverse
link
assembly
must
be
replaced
The
ban
joint
cannot
be
dismantled
and
should
be
replaced
if
the
dust
cover
is
split
or
if
the
axial
play
of
the
joint
exceeds
1
0
mm
0
039
in
Oleck
the
axial
play
with
a
spring
balance
The
force
required
at
the
cotterpin
hole
pOsition
is
between
6
6
1
I
3
kg
15
25
lb
Lubricate
the
ball
joint
with
multi
purpose
grease
every
50
000
km
30
000
miles
or
two
year
whichever
comes
first
A
grease
nipple
must
be
installed
in
place
of
the
plug
See
Fig
J
19
and
the
old
grease
completely
replaced
If
a
high
pressure
grease
gun
j
used
make
sure
that
the
grease
is
injected
slowly
and
is
not
forced
out
through
the
joint
clamp
Remove
the
grease
nipple
and
replace
the
plug
TRANSVERSE
LINK
AND
BALL
JOINT
Installation
Installation
is
a
reversal
of
the
removal
procedure
noting
the
following
points
Remove
all
rust
from
the
transverse
link
bushing
interior
with
a
piece
of
emery
cloth
The
bushing
and
transverse
link
bore
should
be
wetted
with
soapy
water
so
that
the
bushing
can
be
more
easily
inserted
Fit
the
bushing
into
the
transverse
link
using
the
special
tool
ST
36700000
Adjust
the
bushing
inner
tubes
so
that
the
distances
from
the
transverse
link
collar
ends
are
equal
at
both
sides
88
Install
the
lower
ball
joint
on
the
transverse
link
and
tighten
the
installation
bolt
to
a
torque
reading
of
1
9
5kgm
14
18Ib
ft
Oean
the
knuckle
arm
and
the
ball
joint
stud
install
the
knuckle
arm
on
the
ball
joint
and
tighten
the
castle
nut
to
a
torque
reading
of
5
5
74
kgm
4o
53Ib
ft
fit
the
cotterpin
and
bend
it
over
Apply
sealing
agent
over
the
ball
joint
castle
nut
to
prevent
the
formation
of
rust
Locate
the
knuckle
arm
beneath
the
strut
assembly
and
tighten
the
mounting
bolts
to
a
torque
reading
of
4
9
63kgm
35
46Ib
ft
Make
sure
that
the
shorter
of
the
bolts
is
fitted
at
the
front
Install
the
transverse
link
on
the
suspension
crossrnember
and
temporarily
tighten
the
mounting
bolts
Make
sure
that
the
nut
faces
the
front
of
the
car
and
not
the
bolt
head
Fit
the
tension
rod
and
stabilizer
bar
Lower
the
vehicle
and
remove
the
jack
Tighten
the
trans
verse
link
mounting
bolts
to
a
torque
reading
of
9
0
10
0
kgm
65
72
Ib
ft
with
the
vehicle
unladen
FRONT
WHEEL
ALIGNMENT
The
castor
and
camber
angles
are
preset
and
cannot
be
adjusted
If
the
angles
do
not
conform
with
the
fIgures
in
Techni
al
Data
then
a
check
must
be
made
for
damage
to
the
uspenSlon
system
Wheel
alignment
is
carried
out
with
the
tyres
mflated
to
the
correct
pressures
and
with
the
vehicle
on
a
level
surface
The
toe
in
should
be
checked
and
adjusted
if
necessary
by
slackening
the
locknuts
FigJ
20
and
turning
the
track
rods
by
an
equal
amount
until
the
correct
toe
in
is
achieved
The
standard
length
between
the
ball
joints
is
309
5
mm
12
19
in
for
the
1400
and
1600
cc
models
and
105
5
mm
4
14
in
for
the
1800
cc
models
ADJ
USTING
THE
STEERING
ANGLE
The
steering
angle
at
the
full
lock
positions
must
be
checked
with
the
front
wheels
placed
on
a
turntable
Adjust
ment
can
be
made
changing
the
length
of
the
stopper
bolt
shown
arrowed
in
FigJ
21
The
clearance
between
the
tyre
and
tension
rod
should
be
30
mm
1
181
in
or
more
and
can
be
increased
if
necessary
by
extending
the
length
of
the
stopper
bolt
The
bolt
length
should
not
exceed
27
5
mm
1
083
in
when
the
adjustment
is
completed
Steering
angle
figures
are
given
in
Technical
Data
at
the
end
of
this
section
Page 127 of 171
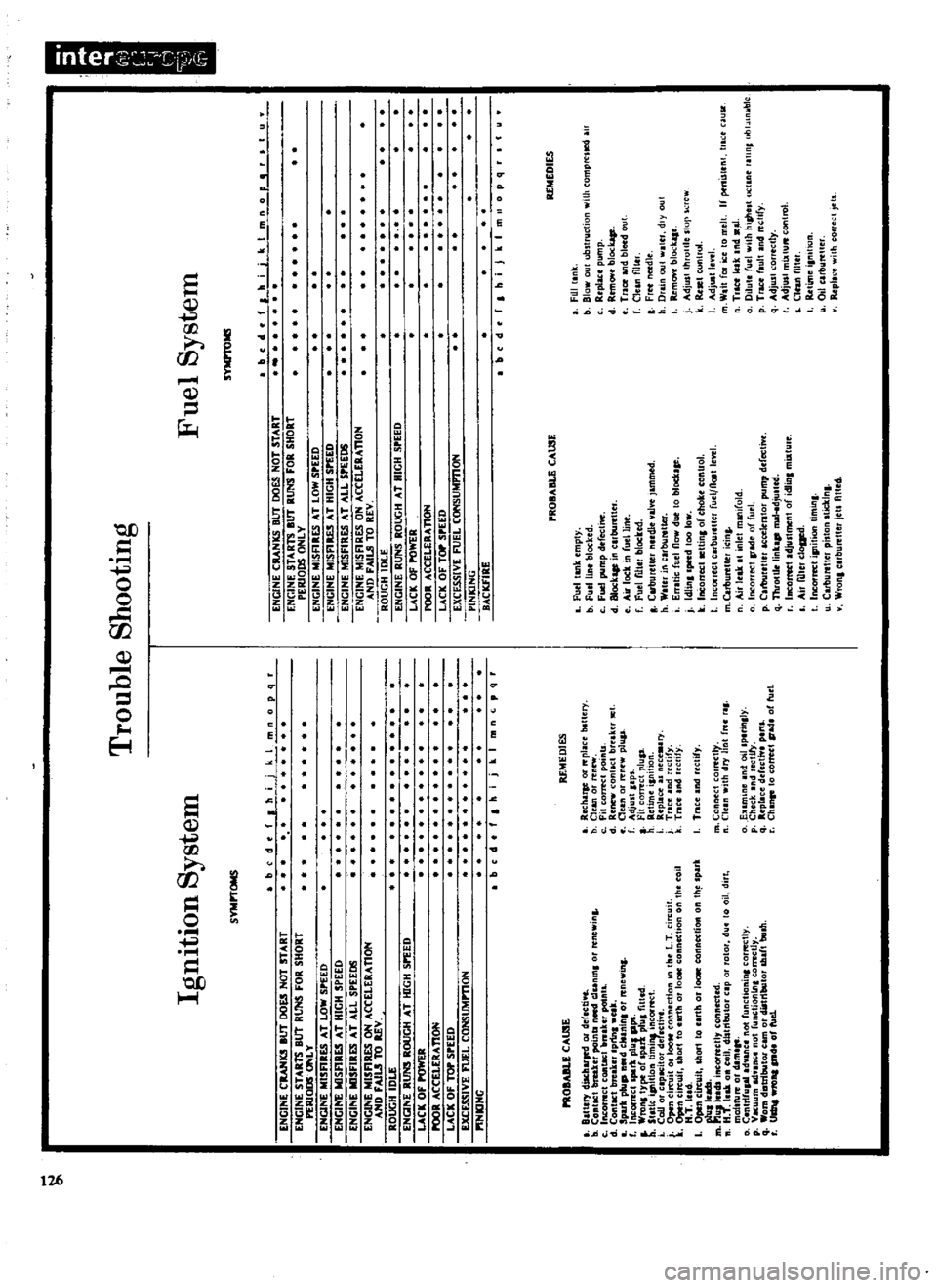
Trouble
Shooting
Ignition
System
SYMnONS
be
d
t
f
I
h
ENGINE
CRANKS
IUT
DOES
NOT
nART
ENGINE
STARTS
BUT
RUNS
FOR
SHORT
PERIODS
ONLY
ENGINE
MISfiRES
AT
LOW
SPEED
ENCINE
WlSflRES
AT
HIGH
SPEED
ENGINE
MISFIRES
AT
ALL
SPEEDS
ENCINE
MISfiRES
ON
ACCELERATION
AND
FAI
TO
REV
ROUGH
IDLE
ENGINE
RUNS
ROUCH
AT
toGH
SPEED
UCK
OF
POWER
POOR
ACCELERAnON
LACK
OF
TOP
SPEED
EXCESSIVE
FUEL
CONSUMmON
PlNKlNC
PROBABLE
CAU5E
t
Bani
dilcharFd
01
defective
b
COJlIllCl
nabr
poinb
nCiCCl
c1Unlftl
renewlna
c
Incorrect
cantlel
ltn
ktr
potftu
d
ConllCt
maker
Iprtn
wuk
Spark
plup
n
d
ch
ntnl
nnewlJIl
r
Jncorrec
llpulpl1llPpI
WronllypeoCap
rtpllllflttad
h
Slltlc
I
lllon
limina
Incorrect
I
Coli
c
plCilor
defC
tl
t
g
o
o
c
o
c
t1o
t
n
h
CllIl
the
toil
H
T
lud
I
Open
cimail
lIlort
nnh
1
conneclion
Ih
spart
m
l
1ulludslnCClfRcllyc
oIIJlCC
tcd
H
T
Ink
coil
dbtribulor
elp
due
oil
din
mol
t
I
o
d
ml
C
ntrlfuplld
anee
not
unetionln
eOll
lctly
p
VKuum
Id
e
not
funclionill
cOIYKtly
q
om
datrlbutw
elm
Or
4iltributor
dldt
bluh
I
UllntWJlOlllpldl
off
ld
L
i
k
I
m
no
p
q
I
b
m
q
f
h
i
j
REMEDIES
I
aceh
tJe
oc
pllce
blHery
b
Clean
01
n
c
Fi
wrrecl
poin
d
Renew
blnker
ll
t
Clea
l
l
ne
plllll
f
Adjull
pt
Fit
cor
c
plu
l
h
aetUne
i
mtlon
I
a
plaCf
I
nece
r
j
Trice
Ind
recury
k
True
ndlecfity
Tnee
nd
leclity
m
Con
c
cOI
ct1r
Clca
wIth
dry
hn
fne
rl
EllImlne
and
Oillpllln
ly
p
Cheek
Ind
rectlly
q
aepllccddectkol
plnl
r
Chlnp
comct
Il
adl
of
fuel
Fuel
System
ENGINE
CRANKS
8lTf
DOES
NOT
START
ENGINE
STARTS
BUT
RUNS
FOR
SHORT
PERIODS
ONLY
ENGINE
MISARES
AT
LOW
SPEED
ENGINE
MISflRE5
AT
HIGH
SPEED
ENGINE
MISFIRES
AT
ALL
SPEEDS
ENGINE
MISAKES
ON
ACCELERA110N
AND
FAILS
TO
REV
ROUGH
IDLE
ENGINE
RUNS
ROUGH
AT
HIGH
SPEED
LACK
OF
POWER
POOR
ACCELERA110N
LACK
OF
TOP
SPEED
EXCESSIVE
flJEL
CONSUMmON
PINKING
BACKFIRE
PROBABLE
CAU5E
Fuel
tank
empty
b
Fu
llinc
blocked
Fuel
pumpd
fectiYe
d
Block
in
cllburene
Air
lock
in
fuel
line
f
Fuel
rut
r
blocked
I
Cuburetter
needle
nlve
jammed
h
Wile
CI
buRlt
r
Errltic
fllel
now
due
blocka
j
IdlinJlpeed
too
low
k
InConectlCtllnlofcttoke
conllol
1
lncorrectcarbuntterfuel
nOltlewl
m
C
muretler
Itlna
Ail
leak
It
Inlet
mlrurold
Incorrect
pade
offuet
p
Carburetter
accelerator
pumpdefect
e
q
Throlll
lintl
rrlIIl
djUlled
IncofftCl
Idjullmenl
of
IdlmJ
mutU
e
Aif
nltef
elogcd
Incorm
t
lpiitiOlluminJ
Clrburellel
Pll
un
lIitkln
Wron
cllburenerjetl
Atled
YMPtO
I
bell
f
1
h
I
j
k
I
m
nOli
I
I
I
0
b
f
h
i
J
k
I
m
REMEDIES
q
FLllllnk
b
Blow
ObSIf1rCllUll
ilh
compl
t
lIed
R
pll
pump
d
RemO
l
e
blockaJe
Trace
Uld
bleed
QUI
r
CIUl1fi1tef
K
Fretne
dle
h
Drlln
d
yout
Removeblockq
J
Adju
throlllelfOl
k
Reset
conllol
1
AdjUSlle
e
m
Wlit
fOI
melt
If
pt
nLS
n
nu
Tlact
lelklndse
a1
Dllu
e
fuel
with
hlah
I
rllln
ubl
ln
blc
p
Trace
fault
and
reeufy
q
AdjuII
correelly
Adju
mutufWconlrol
Clnnnlttr
Retjme
Ilftn
OdClrbulelle
Repllce
Wllh
Je
Page 154 of 171
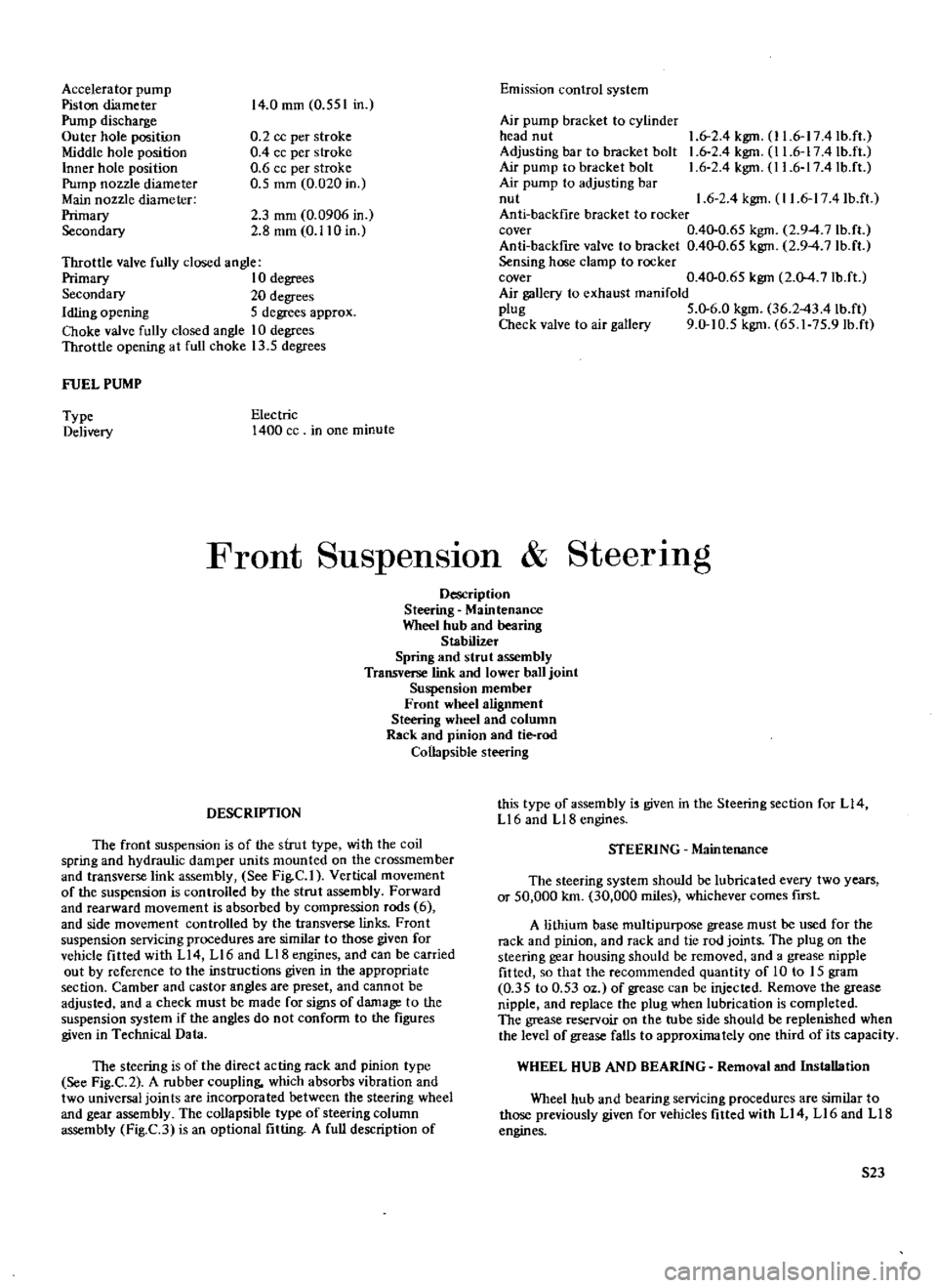
Accelerator
pump
Piston
diameter
Pump
discharge
Outer
hole
position
Middle
hole
position
Inner
hole
position
Pump
nozzle
diameter
Main
nozzle
diameter
Primary
Secondary
14
0
mm
0
551
in
0
2
cc
per
stroke
0
4
cc
per
stroke
0
6
cc
per
stroke
0
5
mm
0
020
in
2
3
mm
0
0906
in
2
8
mm
0
110
in
Throttle
valve
fully
closed
angle
Primary
10
degrees
Secondary
20
degrees
Idling
opening
5
degrees
approx
Choke
valve
fully
closed
angle
10
degrees
Throttle
opening
at
full
choke
13
5
degrees
FUEL
PUMP
Type
Delivery
Electric
1400
cc
in
one
minute
Emission
control
system
Air
pump
bracket
to
cylinder
head
nut
Adjusting
bar
to
bracket
bolt
Air
pump
to
bracket
bolt
Air
pump
to
adjusting
bar
nut
Anti
backfrre
bracket
to
rocker
cover
0
4Q
0
65
kgm
2
94
7
lb
ft
Anti
backfire
valve
to
bracket
0
4Q
O
65
kgm
2
94
7
lb
ft
Sensing
hose
clamp
to
rocker
cover
0
4Q
0
65
kgm
2
M
7
Ib
ft
Air
gallery
to
exhaust
manifold
plug
5
Q
6
0
kgm
36
243
4lb
ft
Check
valve
to
air
gallery
9
0
10
5
kgm
65
1
75
9Ib
ft
1
6
2
4
kgm
I
1
6
17
4Ib
ft
1
6
2
4
kgm
I
1
6
17
4Ib
ft
1
6
2
4
kgm
I
1
6
17
4
lb
ft
1
6
2
4
kgm
11
6
17
4Ib
ft
Front
SuspensIon
SteerIng
Description
Steering
Maintenance
Wheel
hub
and
bearing
Stabilizer
Spring
and
strut
assembly
Transverse
link
and
lower
ball
joint
Suspension
member
Front
wheel
alignment
Steering
wheel
and
column
Rack
and
pinion
and
tie
rod
Collapsible
steering
DESCRIPTION
The
front
suspension
is
of
the
strut
type
with
the
coil
spring
and
hydraulic
damper
units
mounted
on
the
crossmember
and
transverse
link
assembly
See
Fig
C
I
Vertical
movement
of
the
suspension
is
controlled
by
the
strut
assembly
Forward
and
rearward
movement
is
absorbed
by
compression
rods
6
and
side
movement
controlled
by
the
transverse
links
Front
suspension
servicing
procedures
are
similar
to
those
given
for
vehicle
fitted
with
L14
Ll6
and
LIB
engines
and
can
be
carried
out
by
reference
to
the
instructions
given
in
the
appropriate
section
Camber
and
castor
angles
are
preset
and
cannot
be
adjusted
and
a
check
must
be
made
for
signs
of
damage
to
the
suspension
system
if
the
angles
do
not
confonn
to
the
figures
given
in
Technical
Data
The
steering
is
of
the
direct
acting
rack
and
pinion
type
See
Fig
C
2
A
rubber
coupling
which
absorbs
vibration
and
two
universal
join
ts
are
incorpora
ted
between
the
steering
wheel
and
gear
assembly
The
collapsible
type
of
steering
column
assembly
Fig
C3
is
an
optional
fitting
A
full
description
of
this
type
of
assembly
i
given
in
the
Steering
section
for
L14
L16
and
L18
engines
STEERING
Maintenance
The
steering
system
should
be
lubricated
every
two
years
or
50
000
km
30
000
miles
whichever
comes
fIrst
A
lithium
base
multipurpose
grease
must
be
used
for
the
rack
and
pinion
and
rack
and
tie
rod
joints
The
plug
on
the
steering
gear
housing
should
be
removed
and
a
grease
nipple
fitted
so
that
the
recommended
quantity
of
10
to
15
gram
0
35
to
0
53
oz
of
grease
can
be
injected
Remove
the
grease
nipple
and
replace
the
plug
when
lubrication
is
completed
The
grease
reservoir
on
the
tube
side
should
be
replenished
when
the
level
of
grease
falls
to
approximately
one
third
ofits
capacity
WHEEL
HUB
AND
BEARING
Removal
and
Installation
Wheel
hub
and
bearing
servicing
procedures
are
similar
to
those
previously
given
for
vehicles
fitted
with
L14
LI6
and
LIB
engines
S23
Page 156 of 171
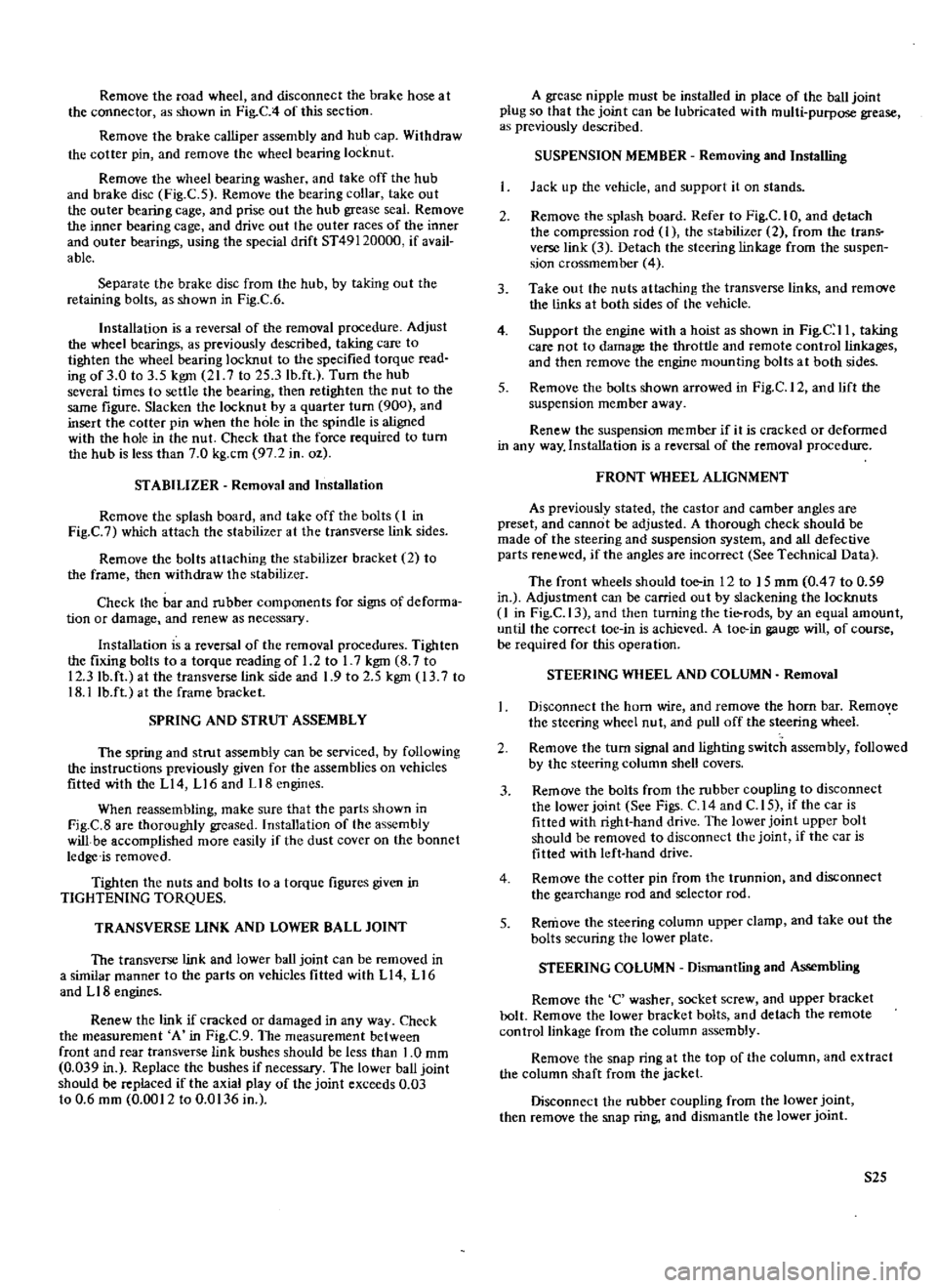
Remove
the
road
wheel
and
disconnect
the
brake
hose
at
the
connector
as
shown
in
Fig
C
4
of
this
section
Remove
the
brake
calliper
assembly
and
hub
cap
Withdraw
the
cotter
pin
and
remove
the
wheel
bearing
locknut
Remove
the
wheel
bearing
washer
and
take
off
the
hub
and
brake
disc
Fig
C
5
Remove
the
bearing
collar
take
out
the
outer
bearing
cage
and
prise
out
the
hub
grease
seal
Remove
the
inner
bearing
cage
and
drive
out
the
outer
races
of
the
inner
and
outer
bearings
using
the
special
drift
ST49120000
if
avail
able
Separate
the
brake
disc
from
the
hub
by
taking
out
the
retaining
bolts
as
shown
in
Fig
C
6
Installation
is
a
reversal
of
the
removal
procedure
Adjust
the
wheel
bearings
as
previously
described
taking
care
to
tighten
the
wheel
bearing
locknut
to
the
specified
torque
read
ing
of
3
0
to
3
5
kgm
21
7
to
25
3lb
ft
Turn
the
hub
several
times
to
settle
the
bearing
then
retighten
the
nut
to
the
same
figure
Slacken
the
locknut
by
a
quarter
turn
900
and
insert
the
cotter
pin
when
the
hole
in
the
spindle
is
aligned
with
the
hole
in
the
nut
Check
that
the
force
required
to
turn
the
hub
is
less
than
7
0
kg
cm
97
2
in
oz
STABILIZER
Removal
and
Installation
Remove
the
splash
board
and
take
off
the
bolts
I
in
Fig
C
7
which
attach
the
stabilizer
at
the
transverse
link
sides
Remove
the
bolts
attaching
the
stabilizer
bracket
2
to
the
frame
then
withdraw
the
stabilizer
Check
the
bar
and
rubber
components
for
signs
of
deforma
tion
or
damage
and
renew
as
necessary
Installation
is
a
reversal
of
the
removal
procedures
Tighten
the
fixing
bolts
to
a
torque
reading
of
1
2
to
I
7
kgm
8
7
to
12
3
lb
ft
at
the
transverse
link
side
and
1
9
to
2
5
kgm
13
7
to
18
llb
ft
at
the
frame
bracket
SPRING
AND
STRUT
ASSEMBLY
The
spring
and
strut
assembly
can
be
serviced
by
following
the
instructions
previously
given
for
the
assemblies
on
vehicles
fitted
with
the
L14
L16
and
Ll8engines
When
reassembling
make
sure
that
the
parts
shown
in
Fig
C
8
are
thomughly
greased
Installation
of
the
assembly
will
be
accomplished
more
easily
if
the
dust
cover
on
the
bonnet
ledge
is
removed
Tighten
the
nuts
and
bolts
to
a
torque
figures
given
in
TIGHTENING
TORQUES
TRANSVERSE
LINK
AND
LOWER
BALL
JOINT
The
transverse
link
and
lower
ball
joint
can
be
removed
in
a
similar
manner
to
the
parts
on
vehicles
fitted
with
L
14
L
16
and
L
18
engines
Renew
the
link
if
cracked
or
damaged
in
any
way
Check
the
measurement
A
in
Fig
C
9
The
measurement
between
front
and
rear
transverse
link
bushes
should
be
less
than
1
0
mm
0
039
in
Replace
the
bushes
if
necessary
The
lower
ball
joint
should
be
replaced
if
the
axial
play
of
the
joint
exceeds
0
03
to
0
6
mm
0
0012
to
0
0136
in
A
grease
nipple
must
be
installed
in
place
of
the
ball
joint
plug
so
that
the
joint
can
be
lubricated
with
multi
purpose
grease
as
previously
described
SUSPENSION
MEMBER
Removing
and
Installing
Jack
up
the
vehicle
and
support
it
on
stands
2
Remove
the
splash
board
Refer
to
Fig
C
I
0
and
detach
the
compression
rod
I
the
stabilizer
2
from
the
trans
verse
link
3
Detach
the
steering
linkage
from
the
suspen
sion
crossmember
4
3
Take
out
the
nuts
attaching
the
transverse
links
and
remove
the
links
at
both
sides
of
the
vehicle
4
Support
the
engine
with
a
hoist
as
shown
in
Fig
C
II
taking
care
not
to
damage
the
throttle
and
remote
control
linkages
and
then
remove
the
engine
mounting
bolts
at
both
sides
5
Remove
the
bolts
shown
arrowed
in
Fig
C
12
and
lift
the
suspension
member
away
Renew
the
suspension
member
if
it
is
cracked
or
deformed
in
any
way
Installation
is
a
reversal
of
the
removal
procedure
FRONT
WHEEL
ALIGNMENT
As
previously
stated
the
castor
and
camber
angles
are
preset
and
cannot
be
adjusted
A
thorough
check
should
be
made
of
the
steering
and
suspension
system
and
all
defective
parts
renewed
if
the
angles
are
incorrect
See
Technical
Data
The
front
wheels
should
toe
in
12
to
15
mm
0
4
7
to
0
59
in
Adjustment
can
be
carried
out
by
slackening
the
locknuts
1
in
Fig
C
13
and
then
turning
the
tie
rods
by
an
equal
amount
until
the
correct
toe
in
is
achieved
A
toe
in
gauge
will
of
course
be
required
for
this
operation
STEERING
WHEEL
AND
COLUMN
Removal
Disconnect
the
horn
wire
and
remove
the
horn
bar
Remove
the
steering
wheel
nut
and
pull
off
the
steering
wheel
2
Remove
the
turn
signal
and
lighting
switch
assembly
followed
by
the
steering
column
shell
covers
3
Remove
the
bolts
from
the
rubber
coupling
to
disconnect
the
lower
joint
See
Figs
C
14
and
C
I
5
if
the
car
is
fitted
with
right
hand
drive
The
lower
joint
upper
bolt
should
be
removed
to
disconnect
the
joint
if
the
car
is
fitted
with
left
hand
drive
4
Remove
the
cotter
pin
from
the
trunnion
and
disconnect
the
gearchange
rod
and
selector
rod
5
Remove
the
steering
column
upper
clamp
and
take
out
the
bolts
securing
the
lower
plate
STEERING
COLUMN
Dismantling
and
Assembling
Remove
the
C
washer
socket
screw
and
upper
bracket
bolt
Remove
the
lower
bracket
bolts
and
detach
the
remote
control
linkage
from
the
column
assembly
Remove
the
snap
ring
at
the
top
of
the
column
and
extract
the
column
shaft
from
the
jacket
Disconnect
the
rubber
coupling
from
the
lower
joint
then
remove
the
snap
ring
and
dismantle
the
lower
joint
S25