washer fluid DATSUN 610 1969 Workshop Manual
[x] Cancel search | Manufacturer: DATSUN, Model Year: 1969, Model line: 610, Model: DATSUN 610 1969Pages: 171, PDF Size: 10.63 MB
Page 84 of 171
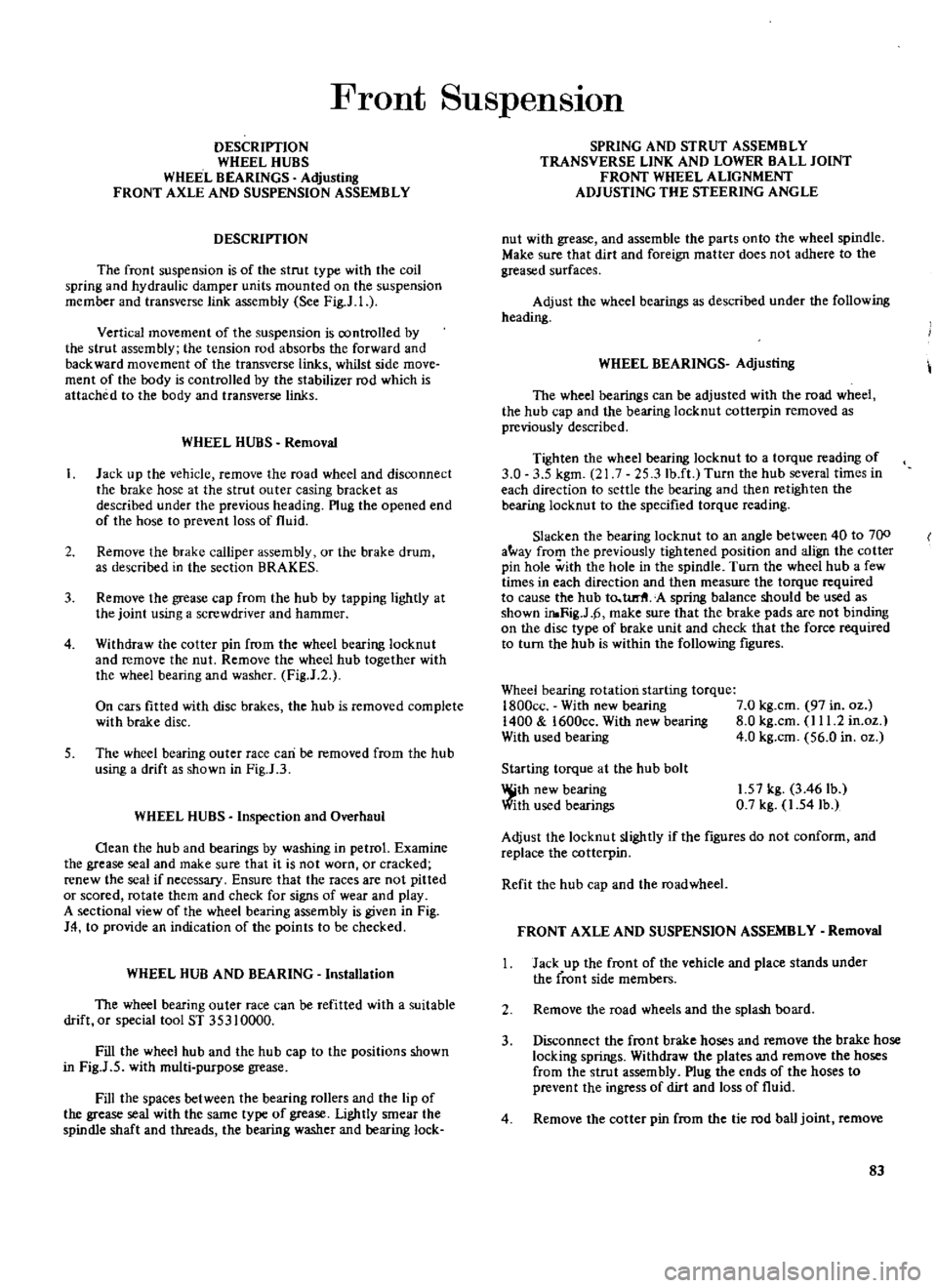
Front
SuspensIon
DESCRIPTION
WHEEL
HUBS
WHEEL
BEARINGS
Adjusting
FRONT
AXLE
AND
SUSPENSION
ASSEMBLY
DESCRIPTION
The
front
suspension
is
of
the
strut
type
with
the
coil
spring
and
hydraulic
damper
units
mounted
on
the
suspension
member
and
transverse
link
assembly
See
FigJ
1
Vertical
movement
of
the
suspension
is
controlled
by
the
strut
assembly
the
tension
rod
absorbs
the
forward
and
backward
movement
of
the
transverse
links
whilst
side
move
ment
of
the
body
is
controlled
by
the
stabilizer
rod
which
is
attached
to
the
body
and
transverse
links
WHEEL
HUBS
Removal
1
Jack
up
the
vehicle
remove
the
road
wheel
and
disconnect
the
brake
hose
at
the
strut
outer
casing
bracket
as
described
under
the
previous
heading
Plug
the
opened
end
of
the
hose
to
prevent
loss
of
fluid
2
Remove
the
brake
calliper
assembly
or
the
brake
drum
as
described
in
the
section
BRAKES
3
Remove
the
grease
cap
from
the
hub
by
tapping
lightly
at
the
joint
using
a
screwdriver
and
hammer
4
Withdraw
the
cotter
pin
from
the
wheel
bearing
locknut
and
remove
the
nut
Remove
the
wheel
hub
together
with
the
wheel
bearing
and
washer
Fig
J
2
On
cars
fitted
with
disc
brakes
the
hub
is
removed
complete
with
brake
disc
5
The
wheel
bearing
outer
race
can
be
removed
from
the
hub
using
a
drift
as
shown
in
Fig
I
3
WHEEL
HUBS
Inspection
and
Overhaul
Gean
the
hub
and
bearings
by
washing
in
petrol
Examine
the
grease
seal
and
make
sure
that
it
is
not
worn
or
cracked
renew
the
seal
if
necessary
Ensure
that
the
races
are
not
pitted
or
scored
rotate
them
and
check
for
signs
of
wear
and
play
A
sectional
view
of
the
wheel
bearing
assembly
is
given
in
Fig
14
to
provide
an
indication
of
the
points
to
be
checked
WHEEL
HUB
AND
BEARING
Installation
The
wheel
bearing
outer
race
can
be
refitted
with
a
suitable
drift
or
special
tool
ST
35310000
Fill
the
wheel
hub
and
the
hub
cap
to
the
positions
shown
in
Fig
J
5
with
multi
purpose
grease
Fill
the
spaces
between
the
bearing
rollers
and
the
lip
of
the
grease
seal
with
the
same
type
of
grease
Lightly
smear
the
spindle
shaft
and
threads
the
bearing
washer
and
bearing
lock
SPRING
AND
STRUT
ASSEMBLY
TRANSVERSE
LINK
AND
LOWER
BALL
JOINT
FRONT
WHEEL
ALIGNMENT
ADJUSTING
THE
STEERING
ANGLE
nut
with
grease
and
assemble
the
parts
onto
the
wheel
spindle
Make
sure
that
dirt
and
foreign
matter
does
not
adhere
to
the
greased
surfaces
Adjust
the
wheel
bearings
as
described
under
the
following
heading
WHEEL
BEARINGS
Adjusting
The
wheel
bearings
can
be
adjusted
with
the
road
wheel
the
hub
cap
and
the
bearing
locknut
cotterpin
removed
as
previously
described
Tighten
the
wheel
bearing
locknut
to
a
torque
reading
of
3
0
3
5
kgm
21
7
25
3lb
ft
Turn
the
hub
several
times
in
each
direction
to
settle
the
bearing
and
then
retighten
the
bearing
locknut
to
the
specified
torque
reading
Slacken
the
bearing
locknut
to
an
angle
between
40
to
700
a
ay
from
the
previously
tightened
position
and
align
the
cotter
pin
hole
with
the
hole
in
the
spindle
Turn
the
wheel
hub
a
few
times
in
each
direction
and
then
measure
the
torque
required
to
cause
the
hub
to
turlI
A
spring
balance
should
be
used
as
shown
m
Rig
J
p
make
sure
that
the
brake
pads
are
not
binding
on
the
disc
type
of
brake
unit
and
check
that
the
force
required
to
turn
the
hub
is
within
the
following
fIgures
Wheel
bearing
rotation
starting
torque
1800ce
With
new
bearing
7
0
kg
cm
97
in
oz
1400
1600cc
With
new
bearing
8
0
kg
cm
111
2
in
oz
With
used
bearing
4
0
kg
cm
56
0
in
oz
Starting
torque
at
the
hub
bolt
lWth
new
bearing
ith
used
bearings
1
57
kg
3
46
lb
0
7
kg
1
541b
Adjust
the
locknut
slightly
if
the
fIgures
do
not
conform
and
replace
the
cotterpin
Refit
the
hub
cap
and
the
road
wheel
FRONT
AXLE
AND
SUSPENSION
ASSEMBLY
Removal
Jack
up
the
front
of
the
vehicle
and
place
stands
under
the
ront
side
members
Remove
the
road
wheels
and
the
splash
board
3
Disconnect
the
front
brake
hoses
and
remove
the
brake
hose
locking
springs
Withdraw
the
plates
and
remove
the
hoses
from
the
strut
assembly
Plug
the
ends
of
the
hoses
to
prevent
the
ingress
of
dirt
and
loss
of
fluid
4
Remove
the
cotter
pin
from
the
tie
rod
ball
joint
remove
83
Page 100 of 171
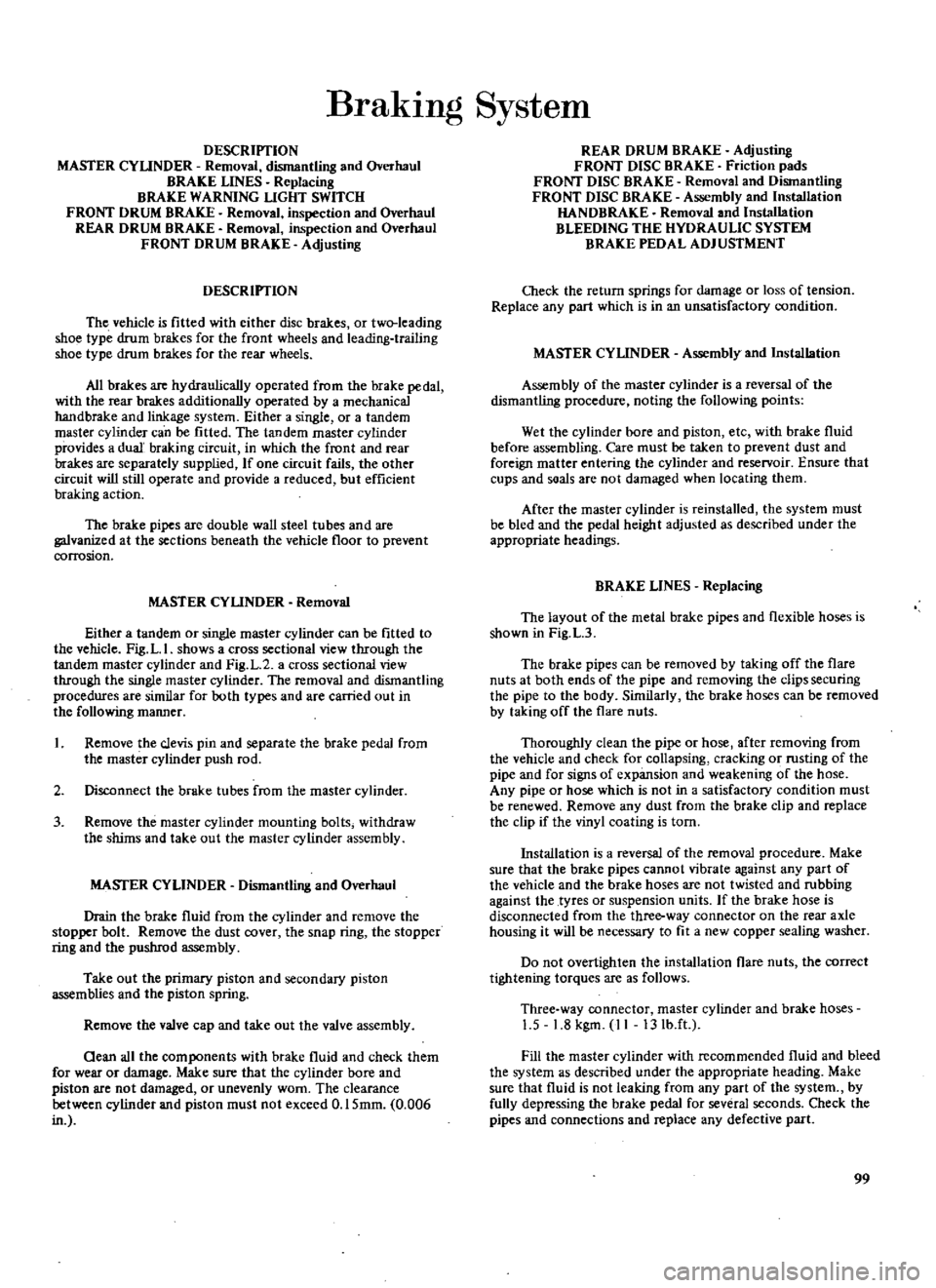
BrakIng
System
DESCRIPTION
MASTER
CYLINDER
Removal
dismantling
and
Overhaul
BRAKE
LINES
Replacing
BRAKE
WARNING
LIGHT
SWITCH
FRONT
DRUM
BRAKE
Removal
inspection
and
Overhaul
REAR
DRUM
BRAKE
Removal
inspection
and
Overhaul
FRONT
DRUM
BRAKE
Adjusting
DESCRIPTION
The
vehicle
is
fitted
with
either
disc
brakes
or
two
leading
shoe
type
drum
brakes
for
the
front
wheels
and
leading
trailing
shoe
type
drum
brakes
for
the
rear
wheels
All
brakes
are
hydraulically
operated
from
the
brake
pedal
with
the
rear
brakes
additionally
operated
by
a
mechanical
handbrake
and
linkage
system
Either
a
single
or
a
tandem
master
cylinder
can
be
fitted
The
tandem
master
cylinder
provides
a
dual
braking
circuit
in
which
the
front
and
rear
brakes
are
separately
supplied
If
ODe
circuit
fails
the
other
circuit
will
still
operate
and
provide
a
reduced
but
efficient
braking
action
The
brake
pipes
are
double
wall
steel
tubes
and
are
galvanized
at
the
sections
beneath
the
vehicle
floor
to
prevent
corrosion
MASTER
CYLINDER
Removal
Either
a
tandem
or
single
master
cylinder
can
be
fitted
to
the
vehicle
Fig
L
I
shows
a
cross
sectional
view
through
the
tandem
master
cylinder
and
Fig
L
2
a
cross
sectional
view
through
the
single
master
cylinder
The
removal
and
dismantling
procedures
are
similar
for
both
types
and
are
carried
out
in
the
following
manner
1
Remove
the
clevis
pin
and
separate
the
brake
pedal
from
the
master
cylinder
push
rod
2
Disconnect
the
brake
tubes
from
the
master
cylinder
3
Remove
the
master
cylinder
mounting
bolts
withdraw
the
shims
and
take
out
the
master
cylinder
assembly
MASfER
CYLINDER
Dismantling
and
Overhaul
Drain
the
brake
fluid
from
the
cylinder
and
remove
the
stopper
bolt
Remove
the
dust
cover
the
snap
ring
the
stopper
ring
and
the
pusbrod
assembly
Take
out
the
primary
piston
and
secondary
piston
assemblies
and
the
piston
spring
Remove
the
valve
cap
and
take
out
the
valve
assembly
Oean
all
the
components
with
brake
fluid
and
check
them
for
wear
or
damage
Make
sure
that
the
cylinder
bore
and
piston
are
not
damaged
or
unevenly
worn
The
clearance
between
cylinder
and
piston
must
not
exceed
0
15mm
0
006
in
REAR
DRUM
BRAKE
Adjusting
FRONT
DISC
BRAKE
Friction
pads
FRONT
DISC
BRAKE
Removal
and
Dismantling
FRONT
DISC
BRAKE
Assembly
and
Installation
HANDBRAKE
Removal
and
Installation
BLEEDING
THE
HYDRAULIC
SYSTEM
BRAKE
PEDAL
ADJUSTMENT
Check
the
return
springs
for
damage
or
loss
of
tension
Replace
any
part
which
is
in
an
unsatisfactory
condition
MASfER
CYLINDER
Assembly
and
Installation
Assembly
of
the
master
cylinder
is
a
reversal
of
the
dismantling
procedure
noting
the
following
points
Wet
the
cylinder
bore
and
piston
etc
with
brake
fluid
before
assembling
Care
must
be
taken
to
prevent
dust
and
foreign
matter
entering
the
cylinder
and
reservoir
Ensure
that
cups
and
soals
are
not
damaged
when
locating
them
After
the
master
cylinder
is
reinstalled
the
system
must
be
bled
and
the
pedal
height
adjusted
as
described
under
the
appropriate
headings
BRAKE
LINES
Replacing
The
layout
of
the
metal
brake
pipes
and
flexible
hoses
is
shown
in
Fig
L
3
The
brake
pipes
can
be
removed
by
taking
off
the
flare
nuts
at
both
ends
of
the
pipe
and
removing
the
clips
securing
the
pipe
to
the
body
Similarly
the
brake
hoses
can
be
removed
by
taking
off
the
flare
nuts
Thoroughly
clean
the
pipe
or
hose
after
removing
from
the
vehicle
and
check
for
collapsing
cracking
or
rusting
of
the
pipe
and
for
signs
of
expansion
and
weakening
of
the
hose
Any
pipe
or
hose
which
is
not
in
a
satisfactory
condition
must
be
renewed
Remove
any
dust
from
the
brake
clip
and
replace
the
clip
if
the
vinyl
coating
is
torn
Installation
is
a
reversal
of
the
removal
procedure
Make
sure
that
the
brake
pipes
cannot
vibrate
against
any
part
of
the
vehicle
and
the
brake
hoses
are
not
twisted
and
rubbing
against
the
tyres
or
suspension
units
If
the
brake
hose
is
disconnected
from
the
three
way
connector
on
the
rear
axle
housing
it
will
be
necessary
to
fit
a
new
copper
sealing
washer
Do
not
overtighten
the
installation
flare
nuts
the
correct
tightening
torques
are
as
follows
Three
way
connector
master
cylinder
and
brake
hoses
1
5
1
8
kgm
II
13Ib
ft
Fill
the
master
cylinder
with
recommended
fluid
and
bleed
the
system
as
described
under
the
appropriate
heading
Make
sure
that
fluid
is
not
leaking
from
any
part
of
the
system
by
fully
depressing
the
brake
pedal
for
several
seconds
Check
the
pipes
and
connections
and
replace
any
defective
part
99
Page 104 of 171
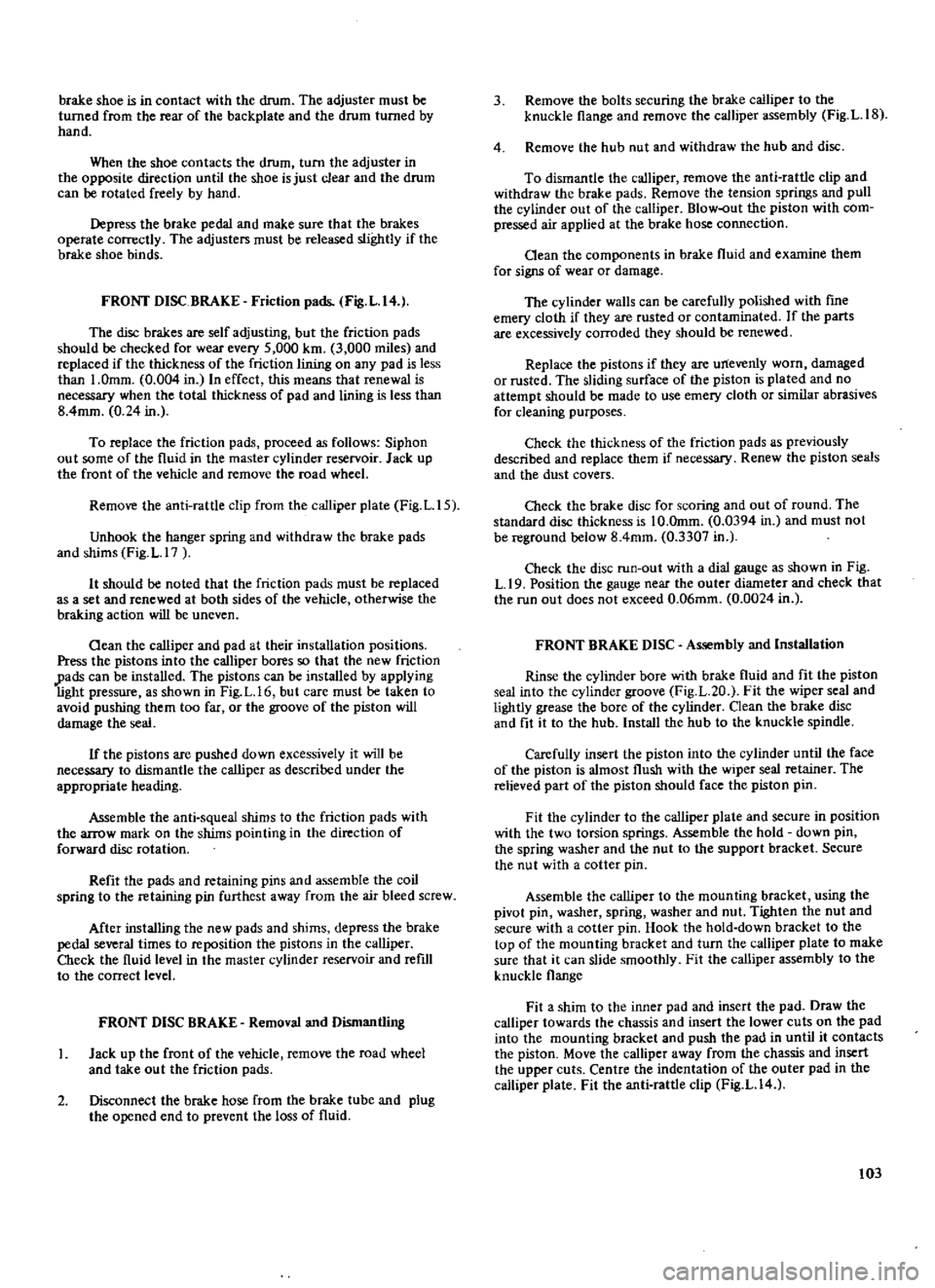
brake
shoe
is
in
contact
with
the
drum
The
adjuster
must
be
turned
from
the
rear
of
the
backplate
and
the
drum
turned
by
hand
When
the
shoe
contacts
the
drum
turn
the
adjuster
in
the
opposite
direction
until
the
shoe
is
just
clear
and
the
drum
can
be
rotated
freely
by
hand
Depress
the
brake
pedal
and
make
sure
that
the
brakes
operate
correctly
The
adjusters
must
be
released
slightly
if
the
brake
shoe
binds
FRONT
DISC
BRAKE
Friction
pads
Fig
L
14
The
disc
brakes
are
self
adjusting
but
the
friction
pads
should
be
checked
for
wear
every
5
000
km
3
000
miles
and
replaced
if
the
thickness
of
the
friction
lining
on
any
pad
is
less
than
1
0mm
0
004
in
In
effect
this
means
that
renewal
is
necessary
when
the
total
thickness
of
pad
and
lining
is
less
than
8
4mm
0
24
in
To
replace
the
friction
pads
proceed
as
follows
Siphon
out
some
of
the
fluid
in
the
master
cylinder
reservoir
Jack
up
the
front
of
the
vehicle
and
remove
the
road
wheel
Remove
the
anti
rattle
clip
from
the
calliper
plate
Fig
L
lS
Unhook
the
hanger
spring
and
withdraw
the
brake
pads
and
shims
Fig
L
17
It
should
be
noted
that
the
friction
pads
must
be
replaced
as
a
set
and
renewed
at
both
sides
of
the
vehicle
otherwise
the
braking
action
will
be
uneven
Oean
the
calliper
and
pad
at
their
installation
positions
Press
the
pistons
into
the
calliper
bores
so
that
the
new
friction
Pads
can
be
installed
The
pistons
can
be
installed
by
applying
light
pressure
as
shown
in
Fig
L
16
but
care
must
be
taken
to
avoid
pushing
them
too
far
or
the
groove
of
the
piston
will
damage
the
seal
If
the
pistons
are
pushed
down
excessively
it
will
be
necessary
to
dismantle
the
calliper
as
described
under
the
appropriate
heading
Assemble
the
anti
squeal
shims
to
the
friction
pads
with
the
arrow
mark
on
the
shims
pointing
in
the
direction
of
forward
disc
rotation
Refit
the
pads
and
retaining
pins
and
assemble
the
coil
spring
to
the
retaining
pin
furthest
away
from
the
air
bleed
screw
After
installing
the
new
pads
and
shims
depress
the
brake
pedal
several
times
to
reposition
the
pistons
in
the
calliper
O1eck
the
fluid
level
in
the
master
cylinder
reservoir
and
refill
to
the
correct
level
FRONT
DISC
BRAKE
Removal
and
Dismantling
1
Jack
up
the
front
of
the
vehicle
remove
the
road
wheel
and
take
out
the
friction
pads
2
Disconnect
the
brake
hose
from
the
brake
tube
and
plug
the
opened
end
to
prevent
the
loss
of
fluid
3
Remove
the
bolts
securing
the
brake
calliper
to
the
knuckle
flange
and
remove
the
calliper
assembly
Fig
L
IS
4
Remove
the
hub
nut
and
withdraw
the
hub
and
disc
To
dismantle
the
calliper
remove
the
anti
rattle
clip
and
withdraw
the
brake
pads
Remove
the
tension
springs
and
pull
the
cylinder
out
of
the
calliper
Blow
out
the
piston
with
com
pressed
air
applied
at
the
brake
hose
connection
Oean
the
components
in
brake
fluid
and
examine
them
for
signs
of
wear
or
damage
The
cylinder
walls
can
be
carefully
polished
with
fine
emery
cloth
if
they
are
rusted
or
contaminated
If
the
parts
are
excessively
corroded
they
should
be
renewed
Replace
the
pistons
if
they
are
unevenly
worn
damaged
or
rusted
The
sliding
surface
of
the
piston
is
plated
and
no
attempt
should
be
made
to
use
emery
cloth
or
similar
abrasives
for
cleaning
purposes
Check
the
thickness
of
the
friction
pads
as
previously
described
and
replace
them
if
necessary
Renew
the
piston
seals
and
the
dust
covers
O1eck
the
brake
disc
for
scoring
and
out
of
round
The
standard
disc
thickness
is
10
Omm
0
0394
in
and
must
not
be
reground
below
8
4mm
0
3307
in
Check
the
disc
run
out
with
a
dial
gauge
as
shown
in
Fig
L
19
Position
the
gauge
near
the
outer
diameter
and
check
that
the
run
out
does
not
exceed
0
06mm
0
0024
in
FRONT
BRAKE
DISC
Assembly
and
Installation
Rinse
the
cylinder
bore
with
brake
fluid
and
fit
the
piston
seal
into
the
cylinder
groove
Fig
L
20
Fit
the
wiper
seal
and
lightly
grease
the
bore
of
the
cylinder
Clean
the
brake
disc
and
fit
it
to
the
hub
Install
the
hub
to
the
knuckle
spindle
Carefully
insert
the
piston
into
the
cylinder
until
the
face
of
the
piston
is
almost
flush
with
the
wiper
seal
retainer
The
relieved
part
of
the
piston
should
face
the
piston
pin
Fit
the
cylinder
to
the
calliper
plate
and
secure
in
position
with
the
two
torsion
springs
Assemble
the
hold
down
pin
the
spring
washer
and
the
nut
to
the
support
bracket
Secure
the
nut
with
a
cotter
pin
Assemble
the
calliper
to
the
mounting
bracket
using
the
pivot
pin
washer
spring
washer
and
nut
Tighten
the
nut
and
secure
with
a
cotter
pin
Hook
the
hold
down
bracket
to
the
top
of
the
mounting
bracket
and
turn
the
calliper
plate
to
make
sure
that
it
can
slide
smoothly
Fit
the
calliper
assembly
to
the
knuckle
flange
Fit
a
shim
to
the
inner
pad
and
insert
the
pad
Draw
the
calliper
towards
the
chassis
and
insert
the
lower
cuts
on
the
pad
into
the
mounting
bracket
and
push
the
pad
in
until
it
contacts
the
piston
Move
the
calliper
away
from
the
chassis
and
insert
the
upper
cuts
Centre
the
indentation
of
the
outer
pad
in
the
calliper
plate
Fit
the
anti
rattle
clip
Fig
L
14
103
Page 168 of 171
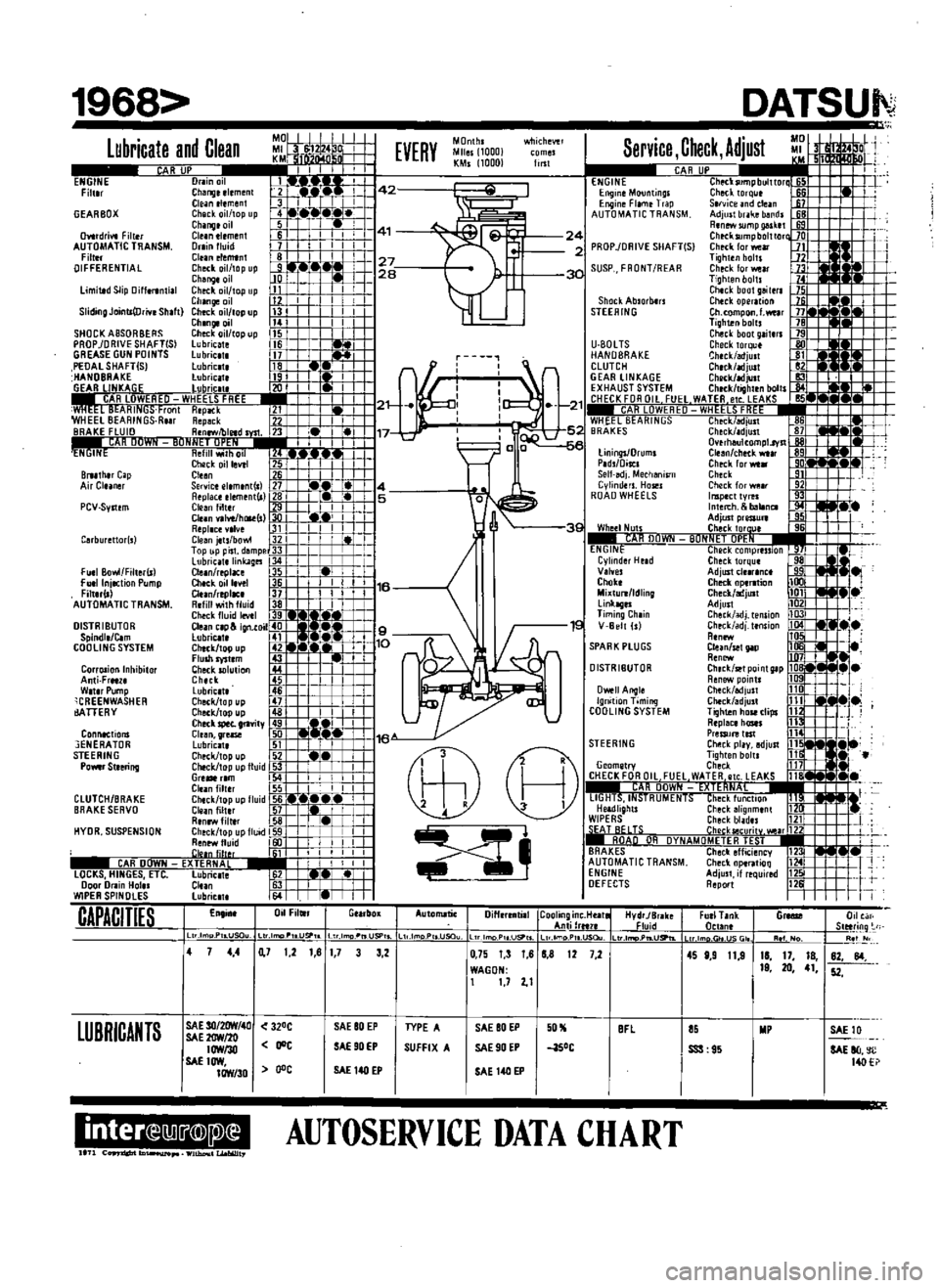
MO
MI
1224
D
I
KM
f
fMn
n
r
A
A
JP
I
I
T
I
I
I
Drain
ill
Changeelemenl
I
42
Cleantlement
3
I
II
r
I
Check
il
topup
4
I
Chinnloil
511
1
11
41
Gle
nelern
n
Ii
I
Orainlluid
7
I
I
I
I
Clunertmtn
81
1
I
I
I
I
I
27
Check
ailltop
up
Jf71
r
I
JIO
WI
28
Change
il
I
ill
limittdSlip
DiHlranti
1
Clleck
ilftopup
1J
I
I
I
Changelil
11
i
ill
ShdmgJolntt
Df
YlShlft
Check
11IIOpup
n
II
I
I
ChangeDl1
1
I
I
I
I
SHOCKASSORBERS
Check
Il
topup
5
PROP
DRIVESHAFTISI
lubncate
Hi
1
GREASE
GUN
POINTS
lubnCIl
it
PEOAlSHAFT
Sj
Lubrlc
te
18
HANDBHAKE
lubnc
1t
I
I
r
1
t
R
IINKAl
iF
luhncll
2u
I
I
i
I
ARlUWIORED
WHEELS
FREE
1m
I
I
i
1121
wHEE
L
tll
AHINli
ronl
HepitCk
211
t
f
WHEEl
BEARINGS
Rur
Repack
77
U
I
BRAKE
FLUID
R
nfWfbletd
1
I
lf
13
117
I
t
I
AH
UUWI
f
t1UN
11Itl
ih1tl
1
i
lcl
Check
oillevtl
B
l
r1i
BI1I1I1
r
Cap
Cleen
1ifj
j
I
Air
Cluner
Service
el
m
nt
l
J7
4
Replace
element
l
l
B
L
5
Cteenfilter
1
C
l
I
I
I
4
Clun
va
vellllR
I
I1
I
I
I
Repl
cH
lve
1
I
I
I
I
Cleen
jets
bOM
R
t
I
Top
liP
pisl
dempe
l
I
r
L
LlIbncatelinkages
I
I
L
Ctean
replace
5
j
I
Ch
ckoill
ve1
Ei
l
j
16
Clun
replac
n
11
R
fill
witll
fluid
38
I
Check
fluid
levll
IlL
t
I
CI
ign
toil
t
i
I
t
1
l
9
CheCk
top
u
p
10
Flulhryst
m
y
Cllecksolullon
44
Chltk
45
Lubrlc
tt
46
i
Clleck
top
up
L
L
Check
topup
4
aJdM
Cllltkspet
gl1vity
i
CI
en
gr
1S
liD
116
Lubriclt
1il
If
I
II
Clleck
topup
52
1
i
Chtck
topuplluid
3
I
I
Gre
rlm
4
I
1
I
I
I
Clunfiltlr
55
L
I
I
I
Chick
top
up
fluid
I6
w
W
e
I
ofi
Ldtir
1
Renewfiltlr
58
I
Check
topupflu
d
i91
i
I
i
Renrwfluid
I
I
I
I
I
ilinlil1r
11
I
I
I
I
I
I
CAR
DOWN
E
TERNAL
j
II
1
I
1
lOCKS
HINGES
Ell
Lubrictt
S21
r
1
el
L
Door
Dram
Hol
l
Clun
f
J
I
I
WIPER
SPINDLES
lubrictt
64
W
I
I
En
in
Dil
Filwr
GttrbOK
1968
Lubricate
and
Clean
ENGINE
Filt
r
GEARBOX
Dvttdrivt
Filt
r
AUTOMATIC
TRANSM
Filt
r
DIFFERENTIAL
PCV
Syllem
rburettor
s
FUll
Bowl
Filter
S1
Fu
llnjectionPump
Fittll
ll
AUTOMATIC
TRANSM
DISTRIBUTOR
Spindl
Ctm
COOLING
SYSTEM
CorrDlionlnllibitor
Anti
Frltl
W
t
rPump
CREENWASHER
ArrERY
Connections
3ENERATOR
STEERING
POMrStlering
CLUTCH
BRAKE
BRAKE
SERVO
HYDR
SUSPENSION
CAPACITIES
LUBRICANTS
Il
D
P
LUSClu
Service
Check
Adjust
CAR
UP
I
l
lletksumpbulttortM
1
Clled
rque
i6
ServiceJndclean
J1
Adjult
brake
bandl
tB
RtnMsumpgal
tt
fiS
Check
llJmpbnlttort
PROP
lOAIVE
SHAFT
S
Check
lor
wear
JJ
Tiglltenbolu
Jl
Check
tor
wear
n
Tiglltenboltl
Clllckbootgeiltrl
Clleckoperltion
Ch
CQmpon
l
welr
Tighten
bolts
Clleclbootgaiterl
Checktorqu
Gheck
edjult
Clllck
ljust
CIIRCk
adjult
Clleck
tighltnbolts
W
M
KSI
1
t
heCklMliiili
86
Check
ldjust
81
Overllllulcompl
rvll
Cleen
chltkwtlr
R9
Check
for
wear
0
Check
9
Checkforwp
lr
192
Il1Ipecttyrel
1IJ
Illte
II
blIl1nCl
Adjultpres
lure
Cllecktorul
liON
ET
OPE
l
heckcompression
Checktorqul
AdjUltclttr
nc
CheckoptTltion
Check
lIljLllt
AdjUlI
Clleck
alIj
tension
adj
t
nsion
I
Clun
selpp
jt1
Renew
Chetk
tPoint
tp
Renew
pointl
Check
6djult
110
J
Check
edjult
ill
i
ii
j
Tiglltenhoseclips
112
R
plece
lIastl
ill
PreSSIJ
test
114
1
STEERING
Clleek
play
adjust
ill
j
i
itl
e
Ti9htenboltl
ill
ii
Geometry
Check
U1L
H
CHECK
FOR
Oil
FUEL
WATER
etc
LEAKS
1181
I
I
R
DOWN
FXIE
HNA
11
1
1
lIGHTS
If
isfHUMt
NTS
Check
flll
C
lOn
f
3
Headlights
Checkllhgnmlnt
112Cr
WIPERS
Checkbladu
11111
J
TS
r
h
kIl
CII
I
Jrl7
iI
An
UH
OVNAUOMFTER
I
ST
I
BRAKES
CheCkemCienCY
1
I
AUTOMATIC
TRANSM
Clleek
op
rttioQ
T
ENGINE
Adjust
if
required
12
DEFECTS
Report
12
EVERY
MOnthl
Miles
1000
KMs
1000
lIBt
wtJichewl
ENGINE
EngmlMountings
Engine
Film
Trap
AUTOMATIC
TRANSM
24
2
30
SUSP
FRONT
REAR
Shock
Ablorb
rs
STEERING
1
21
5
1
c
e
U
80lTS
HANDBRAKE
CLUTCH
GEAR
LINKAGE
EXHAUST
SYSTEM
f
HFf
K
FOR
Oil
FllE
1
CAH
LUWI
RI
If
WHEEL
BEARINGS
BRAKES
UningsJDruml
Plds
Discl
Selhdj
Meclleni5l11
Cylinders
Hosel
ROAD
WHEELS
3S
Whe
1
Nun
AHllIIWN
ENGINE
Cyllnd
r
Held
Vllyes
Clloke
MiKtulli
ldling
linkagel
Timing
Ch
in
16
V
Belt
Is
SPARK
PLUGS
OISTRIBUTOR
Owell
Angle
Ignition
Timing
COOLING
SYSTEM
8
X
Automatic
Diffrrrntill
ICoolinginc
Ht
lltel
AntilrH1f
Ltr
lmoP
Ugo
IL
dmo
PII
U
Ou
HydrJBrak
Fluid
4
7
1
21
81
7
ULlma
II
USP
ULlmD
USP
L
L
tmoP
USQu
127
2
4
4
SAE
3O
2OW
411
SAE
lfrN
2fJ
IOWI3O
SAE1OW
IOW
30
320C
JOe
o
e
SAE80
EP
SAE90EP
SAE
140
EP
mmDIIIII
Ifn
c
ID
WIthDv
1
LI
obWt7
3
LtrJ
PtLUSPtL
3
2
0
75
T
3
1
8
B
8
WAGON
1
1
72
1
TYPE
A
SUFFIX
A
SAE80
EP
SAE90EP
SAE
140EP
0
aSoC
BFl
AUTOSERVICE
DATA
CHART
DATSUI
D
FurlT
nk
n
tln
G
0
Slltring
Re
I
lm
r
JSGI
11
1
No
4S
8
9
11
9
11
17
18
19
20
41
82
84
52
SSS
95
SAElll
SAE
80
c
14O