wheel alignment DATSUN 610 1969 Workshop Manual
[x] Cancel search | Manufacturer: DATSUN, Model Year: 1969, Model line: 610, Model: DATSUN 610 1969Pages: 171, PDF Size: 10.63 MB
Page 6 of 171
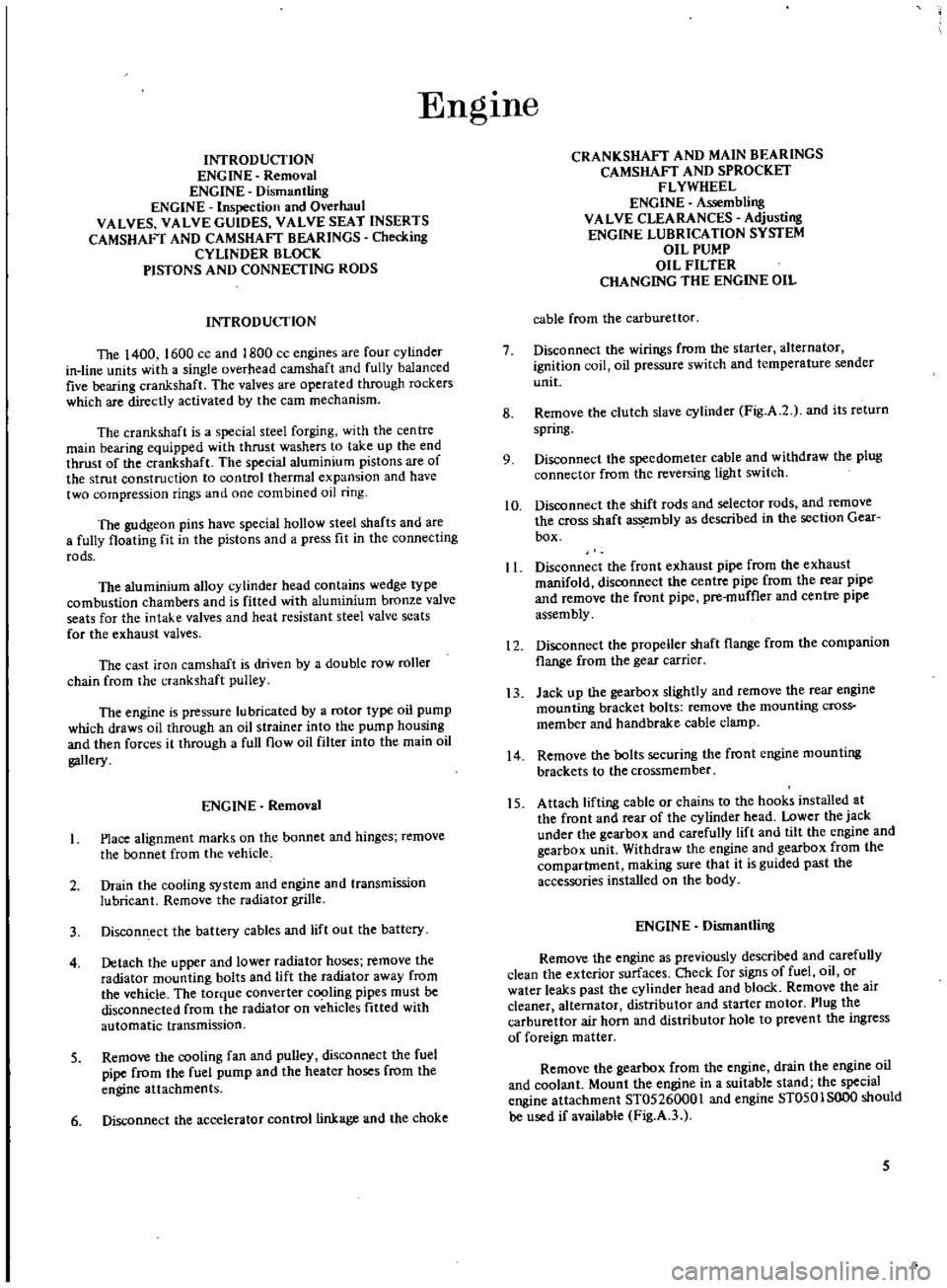
EngIne
INTRODUCTION
ENGINE
Removal
ENGINE
DismantUng
ENGINE
Inspection
and
Overhaul
VALVES
VALVE
GUIDES
VALVE
SEAT
INSERTS
CAMSHAFT
AND
CAMSHAFT
BEARINGS
Checking
CYliNDER
BLOCK
PtSTONS
AND
CONNECTING
RODS
INTRODUCTION
The
1400
1600
cc
and
1800
cc
engines
are
four
cylinder
in
line
units
with
a
single
overhead
camshaft
and
fully
balanced
five
bearing
crankshaft
The
valves
are
operated
through
rockers
which
are
directly
activated
by
the
earn
mechanism
The
crankshaft
is
a
special
steel
forging
with
the
centre
main
bearing
equipped
with
thrust
washers
to
take
up
the
end
thrust
of
the
crankshaft
The
special
aluminium
pistons
are
of
the
strut
construction
to
control
thermal
expansion
and
have
two
compression
rings
and
one
combined
oil
ring
The
gudgeon
pins
have
special
hollow
steel
shafts
and
are
a
fully
floating
fit
in
the
pistons
and
a
press
fit
in
the
connecting
rods
The
aluminium
alloy
cylinder
head
contains
wedge
type
combustion
chambers
and
is
fitted
with
aluminium
bronze
valve
seats
for
the
intake
valves
and
heat
resistant
steel
valve
seats
for
the
exhaust
valves
The
cast
iron
camshaft
is
driven
by
a
double
row
roller
chain
from
the
crankshaft
pulley
The
engine
is
pressure
lubricated
by
a
rotor
type
oil
pump
which
draws
oil
through
an
oil
strainer
into
the
pump
housing
and
then
forces
it
through
a
full
flow
oil
filter
into
the
main
oil
gallery
ENGINE
Removal
Place
alignment
marks
on
the
bonnet
and
hinges
remove
the
bonnet
from
the
vehicle
2
Drain
the
cooling
system
and
engine
and
transmission
lubricant
Remove
the
radiator
grille
3
Discon
ect
the
battery
cables
and
lift
out
the
battery
4
Detach
the
upper
and
lower
radiator
hoses
remove
the
radiator
mounting
bolts
and
lift
the
radiator
away
from
the
vehicle
The
torque
converter
c
jng
pipes
must
be
disconnected
from
the
radiator
on
vehicles
fitted
with
automatic
transmission
S
Remove
the
COOling
fan
and
pulley
disconnect
the
fuel
pipe
from
the
fuel
pump
and
the
heater
hoses
from
the
engine
attachments
6
Disconnect
the
accelerator
control
linkage
and
the
choke
CRANKSHAFT
AND
MAIN
BEARINGS
CAMSHAFT
AND
SPROCKET
FLYWHEEL
ENGINE
Assembling
VALVE
CLEARANCES
Adjusting
ENGINE
LUBRICATION
SYSTEM
OIL
PUMP
OIL
FILTER
CHANGING
THE
ENGINE
OIL
cable
from
the
carburettor
7
Disconnect
the
wirings
from
the
starter
alternator
ignition
coil
oil
pressure
switch
and
temperature
sender
unit
8
Remove
the
clutch
slave
cylinder
Fig
A
2
and
its
return
spring
9
Disconnect
the
speedometer
cable
and
withdraw
the
plug
connector
from
the
reversing
light
switch
10
Disconnect
the
shift
rods
and
seJector
rods
and
remove
the
cross
shaft
assembly
as
described
in
the
section
Gear
box
II
Disconnect
the
front
exhaust
pipe
from
the
exhaust
manifold
disconnect
the
centre
pipe
from
the
rear
pipe
and
remove
the
front
pipe
pre
muffler
and
centre
pipe
assembly
12
Disconnect
the
propeUer
shaft
flange
from
the
companion
flange
from
the
gear
carrier
13
Jack
up
the
gearbox
slightly
and
remove
the
rear
engine
mounting
bracket
bolts
remove
the
mounting
cross
member
and
handbrake
cable
c1amp
14
Remove
the
bolts
securing
the
front
engine
mounting
brackets
to
the
crossmember
15
Attach
lifting
cable
or
chains
to
the
hooks
installed
at
the
front
and
rear
of
the
cylinder
head
Lower
the
jack
under
the
gearbox
and
carefully
lift
and
tilt
the
engine
and
gearbox
unit
Withdraw
the
engine
and
gearbox
from
the
compartment
making
sure
that
it
is
guided
past
the
accessories
installed
on
the
body
ENGINE
Dismantling
Remove
the
engine
as
previously
described
and
carefully
clean
the
exterior
surfaces
Cbeck
for
signs
of
fuel
oil
or
water
leaks
past
the
cylinder
head
and
block
Remove
the
air
cleaner
alternator
distributor
and
starter
motor
Plug
the
carburettor
air
horn
and
distributor
hole
to
prevent
the
ingress
of
foreign
matter
Remove
the
gearbox
from
the
engine
drain
the
engine
oil
and
coolant
Mount
the
engine
in
a
suitable
stand
the
special
engine
attachment
ST05260001
and
engine
ST0501SOO0
should
be
used
if
available
Fig
A
3
5
Page 18 of 171
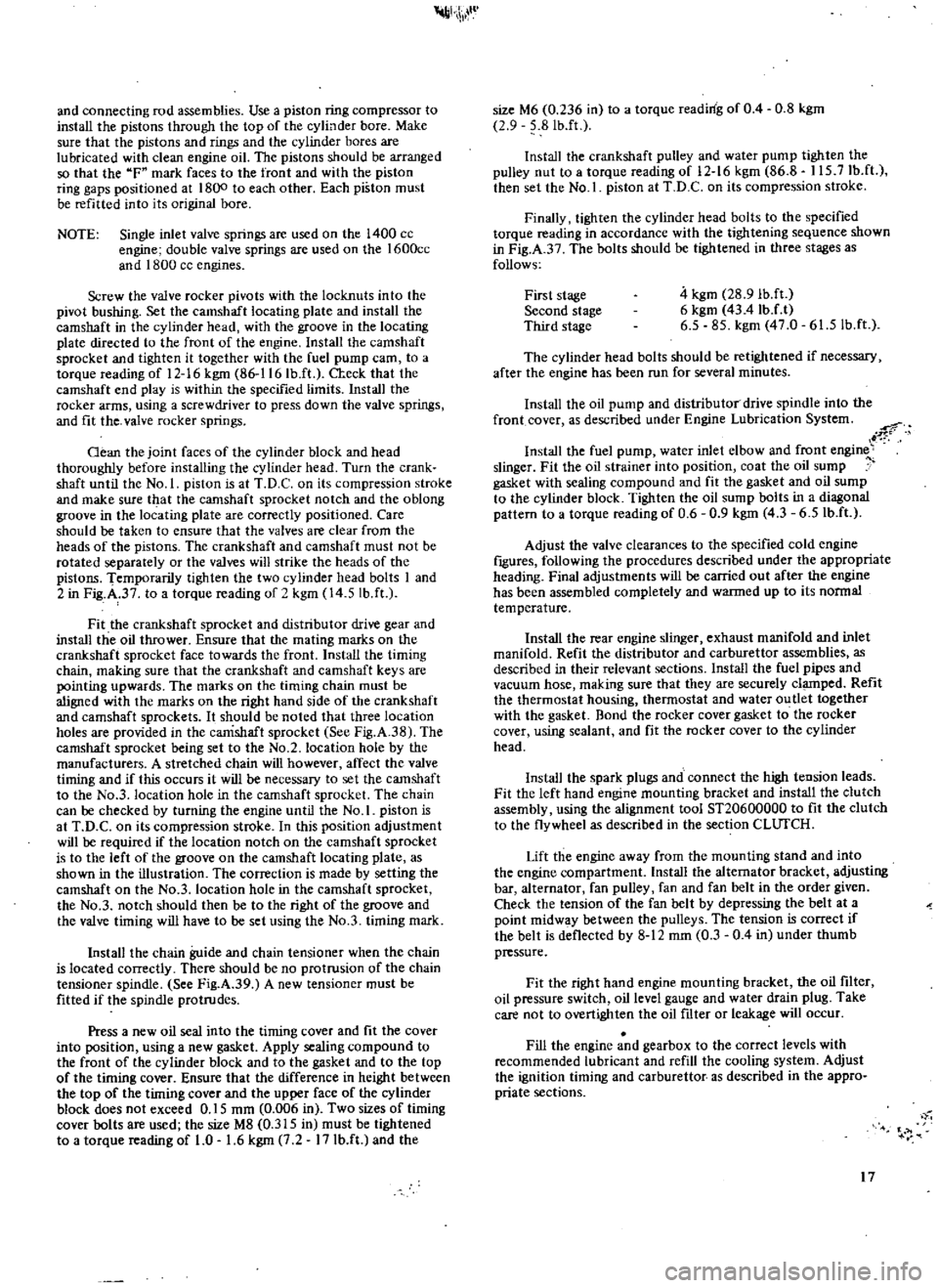
h
W
and
connecting
rod
assemblies
Use
a
piston
ring
compressor
to
install
the
pistons
through
the
top
of
the
cylbder
bore
Make
sure
that
the
pistons
and
rings
and
the
cylinder
bores
are
lubricated
with
clean
engine
oil
The
pistons
should
be
arranged
so
that
the
F
mark
faces
to
the
front
and
with
the
piston
ring
gaps
positioned
at
1800
to
each
other
Each
piston
must
be
refitted
into
its
original
bore
NOTE
Single
inlet
valve
springs
are
used
on
the
1400
cc
engine
double
valve
springs
are
used
on
the
1600cc
and
1800
cc
engines
Screw
the
valve
rocker
pivots
with
the
locknuts
into
the
pivot
bushing
Set
the
camshaft
locating
plate
and
install
the
camshaft
in
the
cylinder
head
with
the
groove
in
the
locating
plate
directed
to
the
front
of
the
engine
Install
the
camshaft
sprocket
and
tighten
it
together
with
the
fuel
pump
earn
to
a
torque
reading
of
12
16
kgm
86
116
IbJt
a
eck
that
the
camshaft
end
play
is
within
the
specified
limits
Install
the
rocker
arms
using
a
screwdriver
to
press
down
the
valve
springs
and
fit
the
valve
rocker
springs
Gean
the
joint
faces
of
the
cylinder
block
and
head
thoroughly
before
installing
the
cylinder
head
Turn
the
crank
shaft
until
the
No
1
piston
is
at
T
D
C
on
its
compression
stroke
and
make
sure
that
the
camshaft
sprocket
notch
and
the
oblong
groove
in
the
locating
plate
are
correctly
positioned
Care
should
be
taken
to
ensure
that
the
valves
are
clear
from
the
heads
of
the
pistons
The
crankshaft
and
camshaft
must
not
be
rotated
separately
or
the
valves
will
strike
the
heads
of
the
pistons
Temporarily
tighten
the
two
cylinder
head
bolts
1
and
2
in
Fig
A
37
to
a
torque
reading
of
2
kgm
14
5
lb
ft
Fit
the
crankshaft
sprocket
and
distributor
drive
gear
and
install
the
oil
thrower
Ensure
that
the
mating
marks
on
the
crankshaft
sprocket
face
towards
the
front
Install
the
timing
chain
making
sure
that
the
crankshaft
and
camshaft
keys
are
XJinting
upwards
The
marks
on
the
timing
chain
must
be
aligned
with
the
marks
on
the
right
hand
side
of
the
crankshaft
and
camshaft
sprockets
It
should
be
noted
that
three
location
holes
are
provided
in
the
camshaft
sprocket
See
Fig
A
38
The
camshaft
sprocket
being
set
to
the
No
2
location
hole
by
the
manufacturers
A
stretched
chain
will
however
affect
the
valve
timing
and
if
this
occurs
it
will
be
necessary
to
set
the
camshaft
to
the
No
3
location
hole
in
the
camshaft
sprocket
The
chain
can
be
checked
by
turning
the
engine
until
the
No
1
piston
is
at
T
D
C
on
its
compression
stroke
In
this
position
adjustment
will
be
required
if
the
location
notch
on
the
camshaft
sprocket
is
to
the
left
of
the
groove
on
the
camshaft
locating
plate
as
shown
in
the
illustration
The
correction
is
made
by
setting
the
camshaft
on
the
No
3
location
hole
in
the
camshaft
sprocket
the
No
3
notch
should
then
be
to
the
right
of
the
groove
and
the
valve
timing
will
have
to
be
set
using
the
No
3
timing
mark
Install
the
chain
guide
and
chain
tensioner
when
the
chain
is
located
correctly
There
should
be
no
protrusion
of
the
chain
tensioner
spindle
See
Fig
A
39
A
new
tensioner
must
be
fitted
if
the
spindle
protrudes
Press
a
new
oil
seal
into
the
timing
cover
and
fit
the
cover
into
position
using
a
new
gasket
Apply
sealing
compound
to
the
front
of
the
cylinder
block
and
to
the
gasket
and
to
the
top
of
the
timing
cover
Ensure
that
the
difference
in
height
between
the
top
of
the
timing
cover
and
the
upper
face
of
the
cylinder
block
does
not
exceed
0
15
mm
0
006
in
Two
sizes
of
timing
cover
bolts
are
used
the
size
M8
0
315
in
must
be
tightened
to
a
torque
reading
of
1
0
1
6
kgm
7
2
17
Ib
ft
and
the
size
M6
0
236
in
to
a
torque
reading
of
0
4
0
8
kgm
2
9
81b
ft
Install
the
crankshaft
pulley
and
water
pump
tighten
the
pulley
nut
to
a
torque
reading
of
12
16
kgm
86
8
115
7Ib
ft
then
set
the
No
1
piston
at
T
D
C
on
its
compression
stroke
Finally
tighten
the
cylinder
head
bolts
to
the
specified
torque
reading
in
accordance
with
the
tightening
sequence
shown
in
Fig
A
3
The
bolts
should
be
tightened
in
three
stages
as
follows
First
stage
Second
stage
Third
stage
4
kgm
28
9
lbJt
6
kgm
43
4
IbJ
t
6
5
85
kgm
47
0
61
5lb
ft
The
cylinder
head
bolts
should
be
retightened
if
necessary
after
the
engine
has
been
run
for
several
minutes
Install
the
oil
pump
and
distributor
drive
spindle
into
the
front
cover
as
described
under
Engine
Lubrication
System
r
rf
i
Install
the
fuel
pump
water
inlet
elbow
and
front
engine
slinger
Fit
the
oil
strainer
into
position
coat
the
oil
sump
gasket
with
sealing
compound
and
fit
the
gasket
and
oil
sump
to
the
cylinder
block
Tighten
the
oil
sump
bolts
in
a
diagonal
pattern
to
a
torque
reading
of
0
6
0
9
kgm
4
3
6
5
IbJt
Adjust
the
valve
clearances
to
the
specified
cold
engine
ftgures
following
the
procedures
described
under
the
appropriate
heading
Final
adjustments
will
be
carried
out
after
the
engine
has
been
assembled
completely
and
warmed
up
to
its
nonnal
temperature
Install
the
rear
engine
slinger
exhaust
manifold
and
inlet
manifold
Refit
the
distributor
and
carburettor
assemblies
as
described
in
their
relevant
sections
Install
the
fuel
pipes
and
vacuum
hose
making
sure
that
they
are
securely
cl
ped
Refit
the
thermostat
housing
thermostat
and
water
outlet
together
with
the
gasket
Bond
the
rocker
cover
gasket
to
the
rocker
cover
using
sealant
and
fit
the
rocker
cover
to
the
cylinder
head
Install
the
spark
plugs
and
connect
the
high
tension
leads
Fit
the
left
hand
engine
mounting
bracket
and
install
the
clutch
assembly
using
the
alignment
tool
ST20600000
to
fit
the
clutch
to
the
flywheel
as
described
in
the
section
ClUfCR
Lift
the
engine
away
from
the
mounting
stand
and
into
the
engine
compartment
Install
the
alternator
bracket
adjusting
bar
alternator
fan
pulley
fan
and
fan
belt
in
the
order
given
Check
the
tension
of
the
fan
belt
by
depressing
the
belt
at
a
point
midw
y
between
the
pulleys
The
tension
is
correct
if
the
belt
is
deflected
by
8
12
mm
0
3
0
4
in
under
thumb
pressure
Fit
the
right
hand
engine
mounting
bracket
the
oil
filter
oil
pressure
switch
oil
level
gauge
and
water
drain
plug
Take
care
not
to
overtighten
the
oil
nIter
or
leakage
will
occur
Fill
the
engine
and
gearbox
to
the
correct
levels
with
recommended
lubricant
and
refill
the
cooling
system
Adjust
the
ignition
timing
and
carburettor
as
described
in
the
appro
priate
sections
17
Page 44 of 171
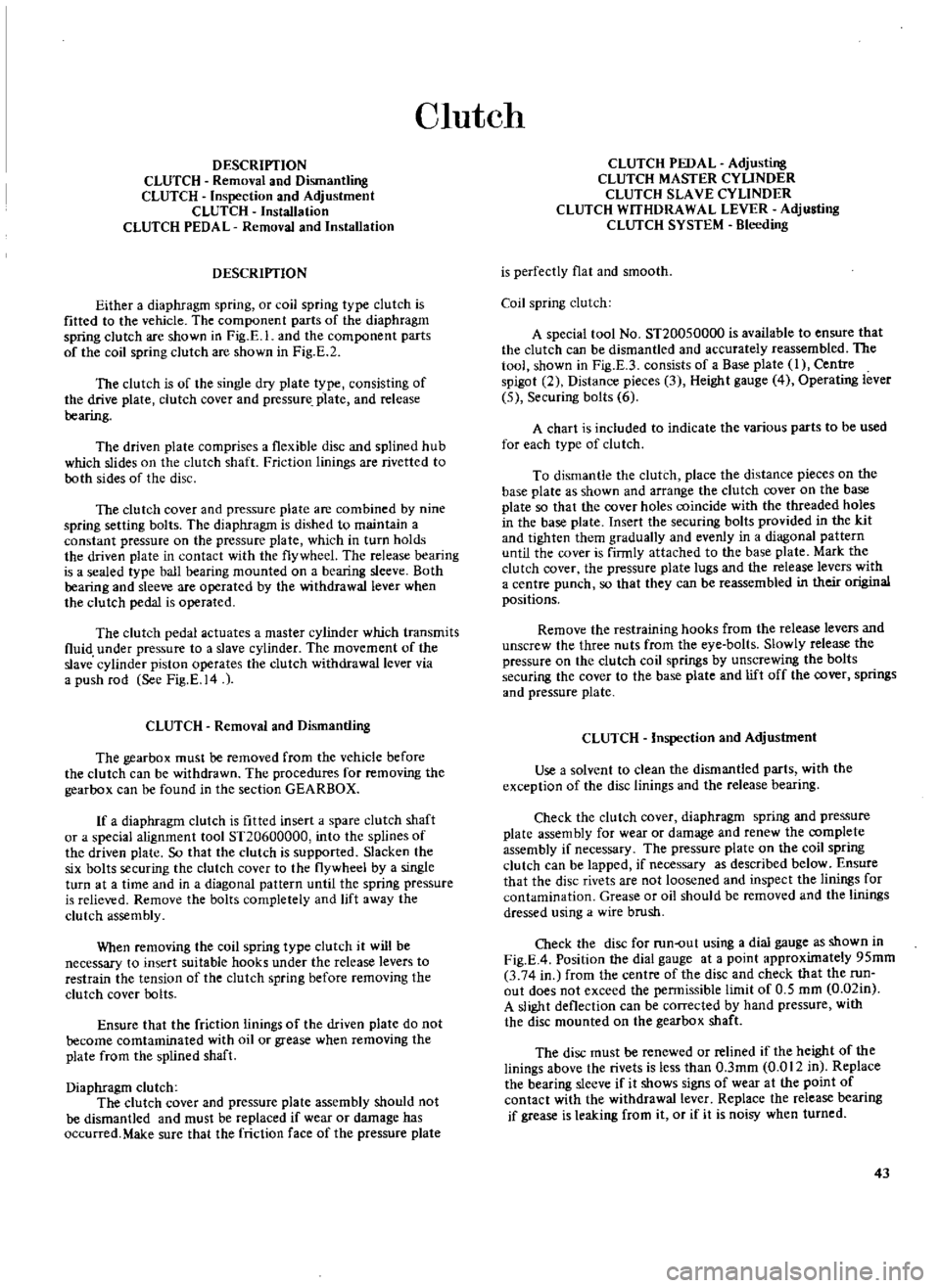
Clutch
DESCRIPTION
CLUTCH
Removal
and
Dismantling
CLUTCH
Inspection
and
Adjustment
CLUTCH
Installation
CLUTCH
PEDAL
Removal
and
Installation
DESCRIPTION
Either
a
diaphragm
spring
or
coil
spring
type
clutch
is
fitted
to
the
vehicle
The
component
parts
of
the
diaphragm
spring
clutch
are
shown
in
Fig
E
l
and
the
component
parts
of
the
coil
spring
clutch
are
shown
in
Fig
E
2
The
clutch
is
of
the
single
dry
plate
type
consisting
of
the
drive
plate
clutch
coveT
and
pressure
plate
and
release
bearing
The
driven
plate
comprises
a
flexible
disc
and
splined
hub
which
slides
on
the
clutch
shaft
Friction
linings
are
rivetted
to
both
sides
of
the
disc
The
clutch
cover
and
pressure
plate
are
combined
by
nine
spring
setting
bolts
The
diaphragm
is
dished
to
maintain
a
constant
pressure
on
the
pressure
plate
which
in
turn
holds
the
driven
plate
in
contact
with
the
flywheel
The
release
bearing
is
a
sealed
type
ball
bearing
mounted
on
a
bearing
sleeve
Both
bearing
and
sleeve
are
operated
by
the
withdrawalleveT
when
the
clutch
pedal
is
operated
The
clutch
pedal
actuates
a
master
cylinder
which
transmits
fluid
under
pressure
to
a
slave
cylinder
The
movement
of
the
slave
cylinder
piston
operates
the
clutch
withdrawal
lever
via
a
push
rod
See
Fig
E
14
CLUTCH
Removal
and
Dismantling
The
gearbox
must
be
removed
from
the
vehicle
before
the
clutch
can
be
withdrawn
The
procedures
for
removing
the
gearbox
can
be
found
in
the
section
GEARBOX
If
a
diaphragm
clutch
is
fitted
insert
a
spare
clutch
shaft
or
a
special
alignment
tool
ST20600000
into
the
splines
of
the
driven
plate
So
that
the
dutch
is
supported
Slacken
the
six
bolts
securing
the
clutch
cover
to
the
flywheel
by
a
single
turn
at
a
time
and
in
a
diagonal
pattern
until
the
spring
pressure
is
relieved
Remove
the
bolts
completely
and
lift
away
the
clutch
assembly
When
removing
the
coil
spring
type
clutch
it
will
be
necessary
to
insert
suitable
hooks
under
the
release
levers
to
restrain
the
tension
of
the
clutch
spring
before
removing
the
clutch
cover
lx
llts
Ensure
that
the
friction
linings
of
the
driven
plate
do
not
become
comtaminated
with
oil
or
grease
when
removing
the
plate
from
the
splined
shaft
Diaphragm
clutch
The
clutch
cover
and
pressure
plate
assembly
should
not
be
dismantled
and
must
be
replaced
if
wear
or
damage
has
occurred
Make
sure
that
the
friction
face
of
the
pressure
plate
CLUTCH
PEDAL
Adjusting
CLUTCH
MASTER
CYLINDER
CLUTCH
SLAVE
CYLINDER
CLUTCH
WITHDRAWAL
LEVER
Adjusting
CLUTCH
SYSTEM
Bleeding
is
perfectly
flat
and
smooth
Coil
spring
clutch
A
special
tool
No
ST200S0000
is
available
to
ensure
that
the
clutch
can
be
dismantled
and
accurately
reassembled
The
tool
shown
in
Fig
E
3
consists
of
a
Base
plate
I
Centre
spigot
2
Distance
pieces
3
Height
gauge
4
Operating
lever
5
Securing
bolts
6
A
chart
is
included
to
indicate
the
various
parts
to
be
used
for
each
type
of
clutch
To
dismantle
the
clutch
place
the
distance
pieces
on
the
base
plate
as
shown
and
arrange
the
clutch
cover
on
the
base
plate
so
that
the
cover
holes
coincide
with
the
threaded
holes
in
the
base
plate
Insert
the
securing
bolts
provided
in
the
kit
and
tighten
them
gradually
and
evenly
in
a
diagonal
pattern
until
the
cover
is
firmly
attached
to
the
base
plate
Mark
the
clutch
cover
the
pressure
plate
lugs
and
the
release
levers
with
a
centre
punch
so
that
they
can
be
reassembled
in
their
original
positions
Remove
the
restraining
hooks
from
the
release
levers
and
unscrew
the
three
nuts
from
the
eye
bolts
Slowly
release
the
pressure
on
the
clutch
coil
springs
by
unscrewing
the
bolts
securing
the
cover
to
the
base
plate
and
lift
off
the
cover
springs
and
pressure
plate
CLUTCH
Inspection
and
Adjustment
Use
a
solvent
to
clean
the
dismantled
parts
with
the
exception
of
the
disc
linings
and
the
release
bearing
Check
the
clutch
cover
diaphragm
spring
and
pressure
plate
assembly
for
wear
or
damage
and
renew
the
complete
assembly
if
necessary
The
pressure
plate
on
the
coil
spring
clutch
can
be
lapped
if
necessary
as
described
below
Ensure
that
the
disc
rivets
are
not
loosened
and
inspect
the
linings
for
contamination
Grease
or
oil
should
be
removed
and
the
linings
dressed
using
a
wire
brush
Check
the
disc
for
run
ut
using
a
dial
gauge
as
shown
in
Fig
E
4
Position
the
dial
gauge
at
a
point
approximately
9Smm
3
74
in
from
the
centre
of
the
disc
and
check
that
the
run
out
does
not
exceed
the
permissible
limit
of
0
5
mm
0
02in
A
slight
deflection
can
be
corrected
by
hand
pressure
with
the
disc
mounted
on
the
gearbox
shaft
The
disc
must
be
renewed
or
relined
if
the
height
of
the
linings
above
the
rivets
is
less
than
0
3mm
0
012
in
Replace
the
bearing
sleeve
if
it
shows
signs
of
wear
at
the
point
of
contact
with
the
withdrawal
lever
Replace
the
release
bearing
if
grease
is
leaking
from
it
or
if
it
is
noisy
when
turned
43
Page 84 of 171
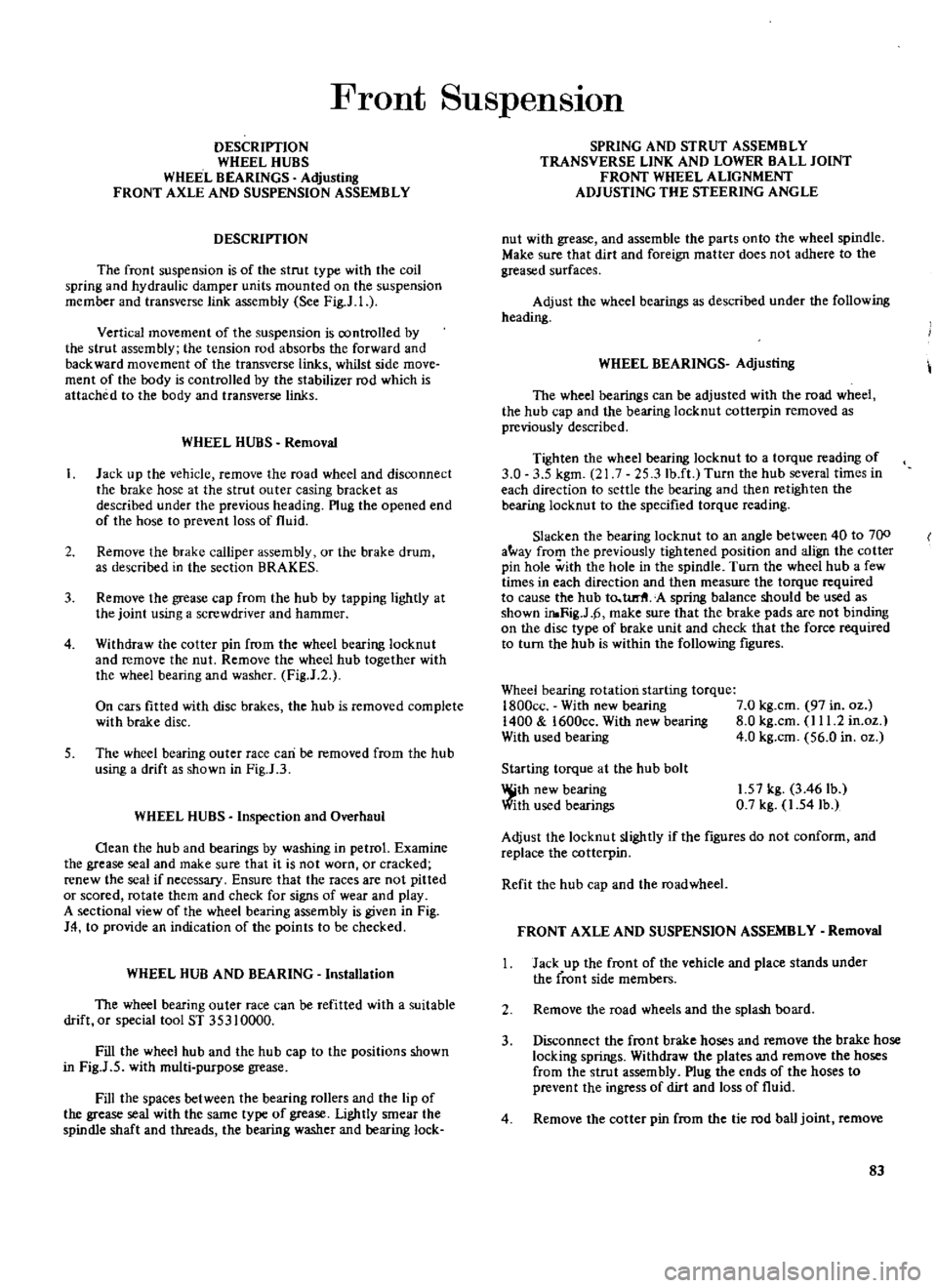
Front
SuspensIon
DESCRIPTION
WHEEL
HUBS
WHEEL
BEARINGS
Adjusting
FRONT
AXLE
AND
SUSPENSION
ASSEMBLY
DESCRIPTION
The
front
suspension
is
of
the
strut
type
with
the
coil
spring
and
hydraulic
damper
units
mounted
on
the
suspension
member
and
transverse
link
assembly
See
FigJ
1
Vertical
movement
of
the
suspension
is
controlled
by
the
strut
assembly
the
tension
rod
absorbs
the
forward
and
backward
movement
of
the
transverse
links
whilst
side
move
ment
of
the
body
is
controlled
by
the
stabilizer
rod
which
is
attached
to
the
body
and
transverse
links
WHEEL
HUBS
Removal
1
Jack
up
the
vehicle
remove
the
road
wheel
and
disconnect
the
brake
hose
at
the
strut
outer
casing
bracket
as
described
under
the
previous
heading
Plug
the
opened
end
of
the
hose
to
prevent
loss
of
fluid
2
Remove
the
brake
calliper
assembly
or
the
brake
drum
as
described
in
the
section
BRAKES
3
Remove
the
grease
cap
from
the
hub
by
tapping
lightly
at
the
joint
using
a
screwdriver
and
hammer
4
Withdraw
the
cotter
pin
from
the
wheel
bearing
locknut
and
remove
the
nut
Remove
the
wheel
hub
together
with
the
wheel
bearing
and
washer
Fig
J
2
On
cars
fitted
with
disc
brakes
the
hub
is
removed
complete
with
brake
disc
5
The
wheel
bearing
outer
race
can
be
removed
from
the
hub
using
a
drift
as
shown
in
Fig
I
3
WHEEL
HUBS
Inspection
and
Overhaul
Gean
the
hub
and
bearings
by
washing
in
petrol
Examine
the
grease
seal
and
make
sure
that
it
is
not
worn
or
cracked
renew
the
seal
if
necessary
Ensure
that
the
races
are
not
pitted
or
scored
rotate
them
and
check
for
signs
of
wear
and
play
A
sectional
view
of
the
wheel
bearing
assembly
is
given
in
Fig
14
to
provide
an
indication
of
the
points
to
be
checked
WHEEL
HUB
AND
BEARING
Installation
The
wheel
bearing
outer
race
can
be
refitted
with
a
suitable
drift
or
special
tool
ST
35310000
Fill
the
wheel
hub
and
the
hub
cap
to
the
positions
shown
in
Fig
J
5
with
multi
purpose
grease
Fill
the
spaces
between
the
bearing
rollers
and
the
lip
of
the
grease
seal
with
the
same
type
of
grease
Lightly
smear
the
spindle
shaft
and
threads
the
bearing
washer
and
bearing
lock
SPRING
AND
STRUT
ASSEMBLY
TRANSVERSE
LINK
AND
LOWER
BALL
JOINT
FRONT
WHEEL
ALIGNMENT
ADJUSTING
THE
STEERING
ANGLE
nut
with
grease
and
assemble
the
parts
onto
the
wheel
spindle
Make
sure
that
dirt
and
foreign
matter
does
not
adhere
to
the
greased
surfaces
Adjust
the
wheel
bearings
as
described
under
the
following
heading
WHEEL
BEARINGS
Adjusting
The
wheel
bearings
can
be
adjusted
with
the
road
wheel
the
hub
cap
and
the
bearing
locknut
cotterpin
removed
as
previously
described
Tighten
the
wheel
bearing
locknut
to
a
torque
reading
of
3
0
3
5
kgm
21
7
25
3lb
ft
Turn
the
hub
several
times
in
each
direction
to
settle
the
bearing
and
then
retighten
the
bearing
locknut
to
the
specified
torque
reading
Slacken
the
bearing
locknut
to
an
angle
between
40
to
700
a
ay
from
the
previously
tightened
position
and
align
the
cotter
pin
hole
with
the
hole
in
the
spindle
Turn
the
wheel
hub
a
few
times
in
each
direction
and
then
measure
the
torque
required
to
cause
the
hub
to
turlI
A
spring
balance
should
be
used
as
shown
m
Rig
J
p
make
sure
that
the
brake
pads
are
not
binding
on
the
disc
type
of
brake
unit
and
check
that
the
force
required
to
turn
the
hub
is
within
the
following
fIgures
Wheel
bearing
rotation
starting
torque
1800ce
With
new
bearing
7
0
kg
cm
97
in
oz
1400
1600cc
With
new
bearing
8
0
kg
cm
111
2
in
oz
With
used
bearing
4
0
kg
cm
56
0
in
oz
Starting
torque
at
the
hub
bolt
lWth
new
bearing
ith
used
bearings
1
57
kg
3
46
lb
0
7
kg
1
541b
Adjust
the
locknut
slightly
if
the
fIgures
do
not
conform
and
replace
the
cotterpin
Refit
the
hub
cap
and
the
road
wheel
FRONT
AXLE
AND
SUSPENSION
ASSEMBLY
Removal
Jack
up
the
front
of
the
vehicle
and
place
stands
under
the
ront
side
members
Remove
the
road
wheels
and
the
splash
board
3
Disconnect
the
front
brake
hoses
and
remove
the
brake
hose
locking
springs
Withdraw
the
plates
and
remove
the
hoses
from
the
strut
assembly
Plug
the
ends
of
the
hoses
to
prevent
the
ingress
of
dirt
and
loss
of
fluid
4
Remove
the
cotter
pin
from
the
tie
rod
ball
joint
remove
83
Page 88 of 171
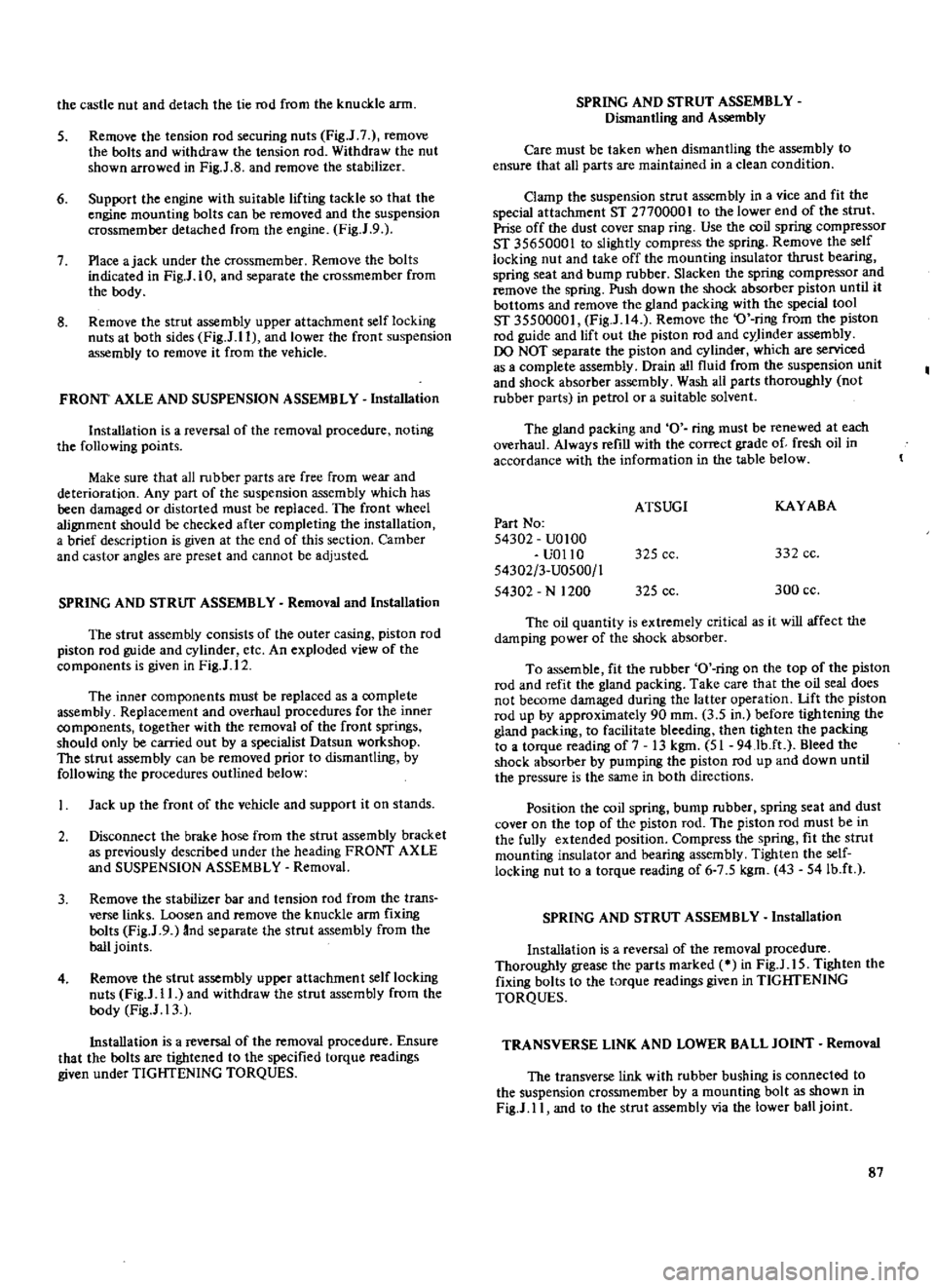
the
castle
nut
and
detach
the
tie
rod
from
the
knuckle
arm
5
Remove
the
tension
rod
securing
nuts
Fig
J
7
remove
the
bolts
and
withdraw
the
tension
rod
Withdraw
the
nut
shown
arrowed
in
FigJ
8
and
remove
the
stabilizer
6
Support
the
engine
with
suitable
lifting
tackle
so
that
the
engine
mounting
bolts
can
be
removed
and
the
suspension
crossmember
detached
from
the
engine
FigJ
9
7
Place
ajack
under
the
crossmember
Remove
the
bolts
indicated
in
Fig
J
IO
and
separate
the
crossmember
from
the
body
8
Remove
the
strut
assembly
upper
attachment
self
locking
nuts
at
both
sides
Fig
J
ll
and
lower
the
front
suspension
assembly
to
remove
it
from
the
vehicle
FRONT
AXLE
AND
SUSPENSION
ASSEMBLY
Installation
Installation
is
a
reversal
of
the
removal
procedure
noting
the
following
points
Make
sure
that
all
rubber
parts
are
free
from
wear
and
deterioration
Any
part
of
the
suspension
assembly
which
has
been
damaged
or
distorted
must
be
replaced
The
front
wheel
alignment
should
be
checked
after
completing
the
installation
a
brief
description
is
given
at
the
end
of
this
section
Camber
and
castor
angles
are
preset
and
cannot
be
adjusted
SPRING
AND
STRUf
ASSEMBLY
Removal
and
Installation
The
strut
assembly
consists
of
the
outer
casing
piston
rod
piston
rod
guide
and
cylinder
etc
An
exploded
view
of
the
components
is
given
in
Fig
J
12
The
inner
components
must
be
replaced
as
a
complete
assembly
Replacement
and
overhaul
procedures
for
the
inner
components
together
with
the
removal
of
the
front
springs
should
only
be
carried
out
by
a
specialist
Datsun
workshop
The
strut
assembly
can
be
removed
prior
to
dismantling
by
following
the
procedures
outlined
below
Jack
up
the
front
of
the
vehicle
and
support
it
on
stands
2
Disconnect
the
brake
hose
from
the
strut
assembly
bracket
as
previously
described
under
the
heading
FRONT
AXLE
and
SUSPENSION
ASSEMBLY
Removal
3
Remove
the
stabilizer
bar
and
tension
rod
from
the
trans
verse
links
Loosen
and
remove
the
knuckle
arm
fixing
bolts
Fig
J
9
And
separate
the
strut
assembly
from
the
ball
joints
4
Remove
the
strut
assembly
upper
attachment
self
locking
nuts
Fig
J
11
and
withdraw
the
strut
assembly
from
the
body
Fig
J
13
Installation
is
a
reversal
of
the
removal
procedure
Ensure
that
the
bolts
are
tightened
to
the
specified
torque
readings
given
under
TIGHTENING
TORQUES
SPRING
AND
STRUT
ASSEMBLY
Dismantling
and
Assembly
Care
must
be
taken
when
dismantling
the
assembly
to
ensure
that
aU
parts
are
maintained
in
a
clean
condition
Clamp
the
suspension
strut
assembly
in
a
vice
and
fit
the
special
attachment
ST
2770000
I
to
the
lower
end
of
the
strut
Prise
off
the
dust
cover
snap
ring
Use
the
coil
spring
compressor
ST
35650001
to
slightly
compress
the
spring
Remove
the
self
locking
nut
and
take
off
the
mounting
insulator
thrust
bearing
spring
seat
and
bump
rubber
Slacken
the
spring
compressor
and
remove
the
spring
Push
down
the
shock
absorber
piston
until
it
bottoms
and
remove
the
gland
packing
with
the
special
tool
ST
35500001
Fig
J
14
Remove
the
O
ring
from
the
piston
rod
guide
and
lift
out
the
piston
rod
and
cy
linder
assembly
00
NOT
separate
the
piston
and
cylinder
which
are
serviced
as
a
complete
assembly
Drain
all
fluid
from
the
suspension
unit
and
shock
absorber
assembly
Wash
all
parts
thoroughly
not
rubber
parts
in
petrol
or
a
suitable
solvent
The
gland
packing
and
0
ring
must
be
renewed
at
each
overhaul
Always
refill
with
the
correct
grade
of
fresh
oil
in
accordance
with
the
information
in
the
table
below
ATSUGI
KAYABA
Part
No
54302
UO
100
UOl10
325
cc
332
cc
54302
3
U0500
1
54302
N
1200
325
cc
300
cc
The
oil
quantity
is
extremely
critical
as
it
will
affect
the
damping
power
of
the
shock
absorber
To
assemble
fit
the
rubber
O
ring
on
the
top
of
the
piston
rod
and
refit
the
gland
packing
Take
care
that
the
oil
seal
does
not
become
damaged
during
the
latter
operation
Lift
the
piston
rod
up
by
approximately
90
mm
3
5
in
before
tightening
the
gland
packing
to
facilitate
bleeding
then
tighten
the
packing
to
a
torque
reading
of
7
13
kgm
51
94Jb
ft
Bleed
the
shock
absorber
by
pumping
the
piston
rod
up
and
down
until
the
pressure
is
the
same
in
both
directions
Position
the
coil
spring
bump
rubber
spring
seat
and
dust
cover
on
the
top
of
the
piston
rod
The
piston
rod
must
be
in
the
fully
extended
position
Compress
the
spring
fit
the
strut
mounting
insulator
and
bearing
assembly
Tighten
the
self
locking
nut
to
a
torque
reading
of
6
7
5
kgm
43
541b
ft
SPRING
AND
STRUT
ASSEMBLY
Installation
Installation
is
a
reversal
of
the
removal
procedure
Thoroughly
grease
the
parts
marked
in
Fig
J
15
Tighten
the
fixing
bolts
to
the
torque
readings
given
in
TIGHfENING
TORQUES
TRANSVERSE
LINK
AND
LOWER
BALL
JOINT
Removal
The
transverse
link
with
rubber
bushing
is
connected
to
the
suspension
crosSlTIember
by
a
mounting
bolt
as
shown
in
Fig
J
11
and
to
the
strut
assembly
via
the
lower
ball
joint
87
Page 89 of 171
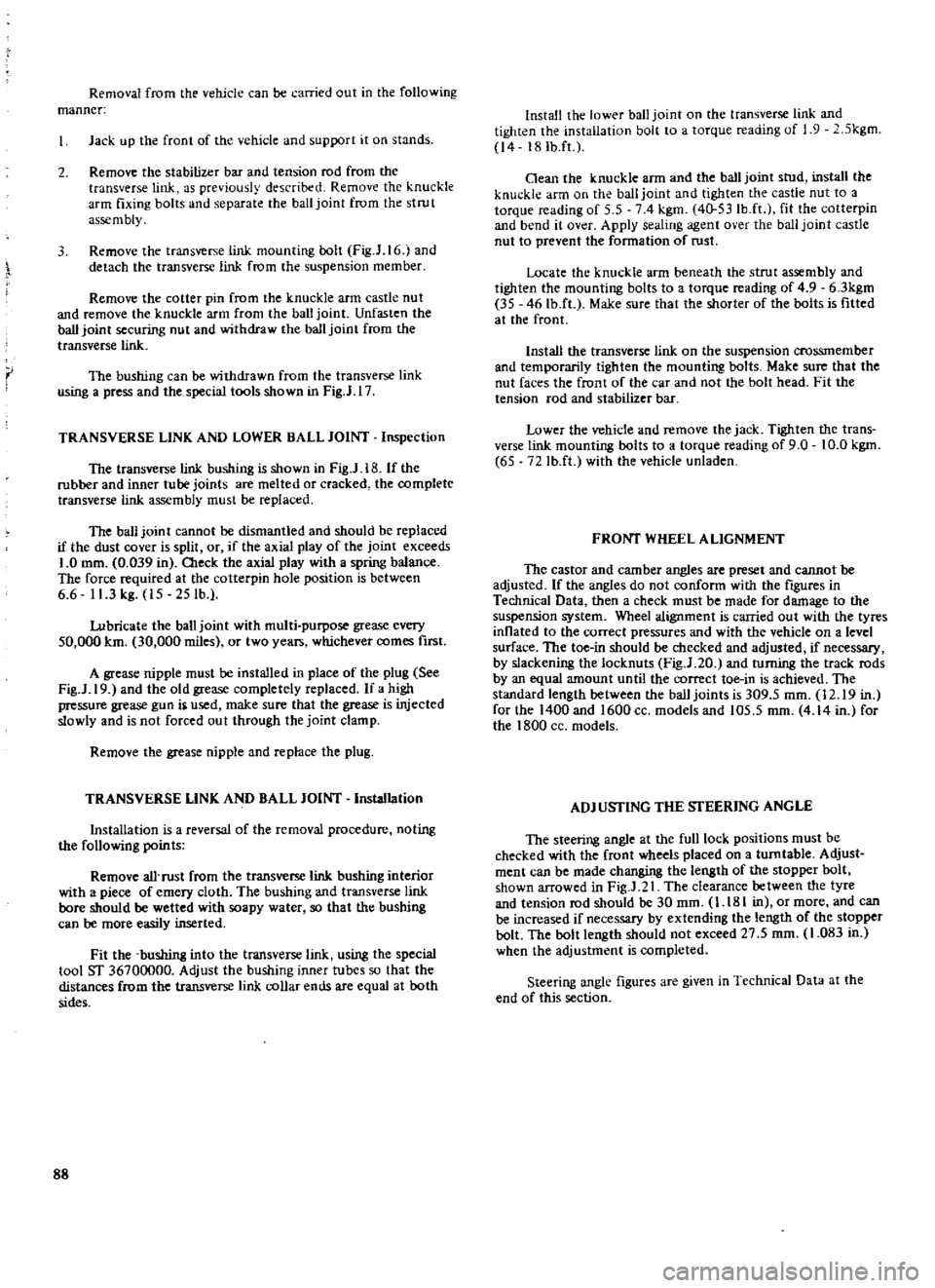
Removal
from
the
vehicle
can
be
carried
out
in
the
following
manner
Jack
up
the
front
of
the
vehicle
and
support
it
on
stands
2
Remove
the
stabilizer
bar
and
tension
rod
from
the
transverse
link
as
previously
described
Remove
the
knuckle
arm
fixing
bolts
and
separate
the
ball
joint
from
the
strut
asse
m
bly
3
Remove
the
transverse
link
mounting
bolt
Fig
J
16
and
detach
the
transverse
link
from
the
suspension
member
Remove
the
cotter
pin
from
the
knuckle
arm
castle
nut
and
remove
the
knuckle
arm
from
the
ban
joint
Unfasten
the
ball
joint
securing
nut
and
withdraw
the
ball
joint
from
the
transverse
link
r
The
bushing
can
be
withdrawn
from
the
transverse
link
using
a
press
and
the
special
tools
shown
in
Fig
J
17
TRANSVERSE
LINK
AND
LOWER
BALL
JOINT
Inspection
The
transverse
link
bushing
is
shown
in
Fig
J
18
If
the
rubber
and
inner
tube
joints
are
melted
or
cracked
the
complete
transverse
link
assembly
must
be
replaced
The
ban
joint
cannot
be
dismantled
and
should
be
replaced
if
the
dust
cover
is
split
or
if
the
axial
play
of
the
joint
exceeds
1
0
mm
0
039
in
Oleck
the
axial
play
with
a
spring
balance
The
force
required
at
the
cotterpin
hole
pOsition
is
between
6
6
1
I
3
kg
15
25
lb
Lubricate
the
ball
joint
with
multi
purpose
grease
every
50
000
km
30
000
miles
or
two
year
whichever
comes
first
A
grease
nipple
must
be
installed
in
place
of
the
plug
See
Fig
J
19
and
the
old
grease
completely
replaced
If
a
high
pressure
grease
gun
j
used
make
sure
that
the
grease
is
injected
slowly
and
is
not
forced
out
through
the
joint
clamp
Remove
the
grease
nipple
and
replace
the
plug
TRANSVERSE
LINK
AND
BALL
JOINT
Installation
Installation
is
a
reversal
of
the
removal
procedure
noting
the
following
points
Remove
all
rust
from
the
transverse
link
bushing
interior
with
a
piece
of
emery
cloth
The
bushing
and
transverse
link
bore
should
be
wetted
with
soapy
water
so
that
the
bushing
can
be
more
easily
inserted
Fit
the
bushing
into
the
transverse
link
using
the
special
tool
ST
36700000
Adjust
the
bushing
inner
tubes
so
that
the
distances
from
the
transverse
link
collar
ends
are
equal
at
both
sides
88
Install
the
lower
ball
joint
on
the
transverse
link
and
tighten
the
installation
bolt
to
a
torque
reading
of
1
9
5kgm
14
18Ib
ft
Oean
the
knuckle
arm
and
the
ball
joint
stud
install
the
knuckle
arm
on
the
ball
joint
and
tighten
the
castle
nut
to
a
torque
reading
of
5
5
74
kgm
4o
53Ib
ft
fit
the
cotterpin
and
bend
it
over
Apply
sealing
agent
over
the
ball
joint
castle
nut
to
prevent
the
formation
of
rust
Locate
the
knuckle
arm
beneath
the
strut
assembly
and
tighten
the
mounting
bolts
to
a
torque
reading
of
4
9
63kgm
35
46Ib
ft
Make
sure
that
the
shorter
of
the
bolts
is
fitted
at
the
front
Install
the
transverse
link
on
the
suspension
crossrnember
and
temporarily
tighten
the
mounting
bolts
Make
sure
that
the
nut
faces
the
front
of
the
car
and
not
the
bolt
head
Fit
the
tension
rod
and
stabilizer
bar
Lower
the
vehicle
and
remove
the
jack
Tighten
the
trans
verse
link
mounting
bolts
to
a
torque
reading
of
9
0
10
0
kgm
65
72
Ib
ft
with
the
vehicle
unladen
FRONT
WHEEL
ALIGNMENT
The
castor
and
camber
angles
are
preset
and
cannot
be
adjusted
If
the
angles
do
not
conform
with
the
fIgures
in
Techni
al
Data
then
a
check
must
be
made
for
damage
to
the
uspenSlon
system
Wheel
alignment
is
carried
out
with
the
tyres
mflated
to
the
correct
pressures
and
with
the
vehicle
on
a
level
surface
The
toe
in
should
be
checked
and
adjusted
if
necessary
by
slackening
the
locknuts
FigJ
20
and
turning
the
track
rods
by
an
equal
amount
until
the
correct
toe
in
is
achieved
The
standard
length
between
the
ball
joints
is
309
5
mm
12
19
in
for
the
1400
and
1600
cc
models
and
105
5
mm
4
14
in
for
the
1800
cc
models
ADJ
USTING
THE
STEERING
ANGLE
The
steering
angle
at
the
full
lock
positions
must
be
checked
with
the
front
wheels
placed
on
a
turntable
Adjust
ment
can
be
made
changing
the
length
of
the
stopper
bolt
shown
arrowed
in
FigJ
21
The
clearance
between
the
tyre
and
tension
rod
should
be
30
mm
1
181
in
or
more
and
can
be
increased
if
necessary
by
extending
the
length
of
the
stopper
bolt
The
bolt
length
should
not
exceed
27
5
mm
1
083
in
when
the
adjustment
is
completed
Steering
angle
figures
are
given
in
Technical
Data
at
the
end
of
this
section
Page 90 of 171
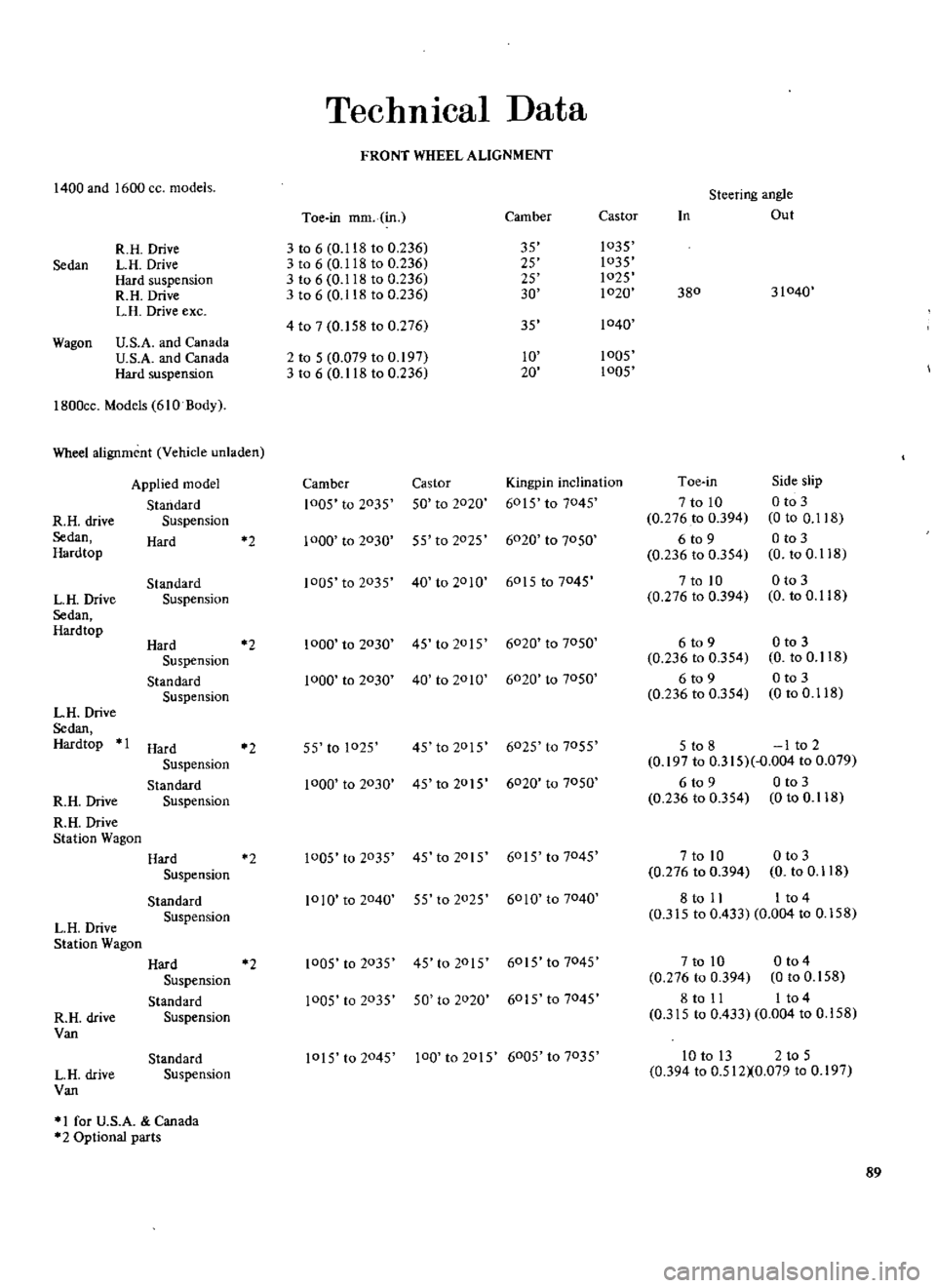
TechnICal
Data
FRONT
WHEEL
ALIGNMENT
1400
and
1600
cc
models
Sedan
Toe
in
mm
in
Camber
Castor
R
H
Drive
3
to
6
0
118
to
0
236
35
1035
LH
Drive
3
to
6
0
118
to
0
236
25
1035
Hard
suspension
3
to
6
0
118
to
0
236
25
1025
R
H
Drive
3
to
6
0
118
to
0
236
30
1020
L
R
Drive
exc
4
to
7
0
158
to
0
276
35
1040
U
S
A
and
Canada
U
S
A
and
Canada
2
to
5
0
079
to
0
197
10
1005
Hard
suspension
3
to
6
0
118
to
0
236
20
1005
Steering
angle
In
Out
380
31040
Wagon
1800cc
Models
610
Body
Wheel
alignment
Vehicle
unladen
Applied
model
Camber
Castor
Kingpin
inclination
Toe
in
Side
slip
Standard
1005
to
2035
50
to
2020
6015
to
7045
7
to
10
o
to
3
R
H
drive
Suspension
0
276
to
0
394
0
to
0
118
Sedan
Hard
2
1000
to
2030
55
to
2025
6020
to
7050
6
to
9
o
to
3
Hardtop
0
236
to
0
354
0
to
0
118
Standard
1005
to
2035
40
to
2010
6015
to
7045
7
to
10
o
to
3
L
H
Drive
Suspension
0
276
to
0
394
0
to
0
118
Sedan
Hardtop
Hard
2
1000
to
2030
45
to
2015
6020
to
7050
6
to
9
o
to
3
Suspension
0
236
to
0
354
0
to
0
118
Standard
1000
to
2030
40
to
2010
6020
to
7050
6
to
9
o
to
3
Suspension
0
236
to
0
354
0
to
0
118
LH
Drive
Sedan
Hardtop
Hard
2
55
to
1025
45
to
2015
6025
to
7055
5
to
8
I
to
2
Suspension
0
197
to
0
315
0
004
to
0
079
Standard
1000
to
2030
45
to
2015
6020
to
7050
6
to
9
o
to
3
R
H
Drive
Suspension
0
236
to
0
354
0
to
0
118
R
H
Drive
Station
Wagon
Hard
2
1005
to
2035
45
to
2015
6015
to
7045
7
to
10
o
to
3
Suspension
0
276
to
0
394
0
to
0
118
Standard
1010
to
2040
55
to
2025
6010
to
7040
8
to
11
I
t04
L
H
Drive
Suspension
0
315
to
0
433
0
004
to
0
158
Station
Wagon
Hard
2
1005
to
2035
45
to
2015
6015
to
7045
7
to
10
o
t04
Suspension
0
276
to
0
394
0
to
0
158
Standard
1005
to
2035
50
to
2020
6015
to
7045
8
to
11
I
t04
R
H
drive
Suspension
0
315
to
0
433
0
004
to
0
158
Van
Standard
1015
to
2045
100
to
2015
6005
to
7035
10
to
I3
2
to
5
L
H
drive
Suspension
0
394
to
0
512XO
079
to
0
197
Van
I
for
U
S
A
Canada
2
Optional
parts
89
Page 94 of 171
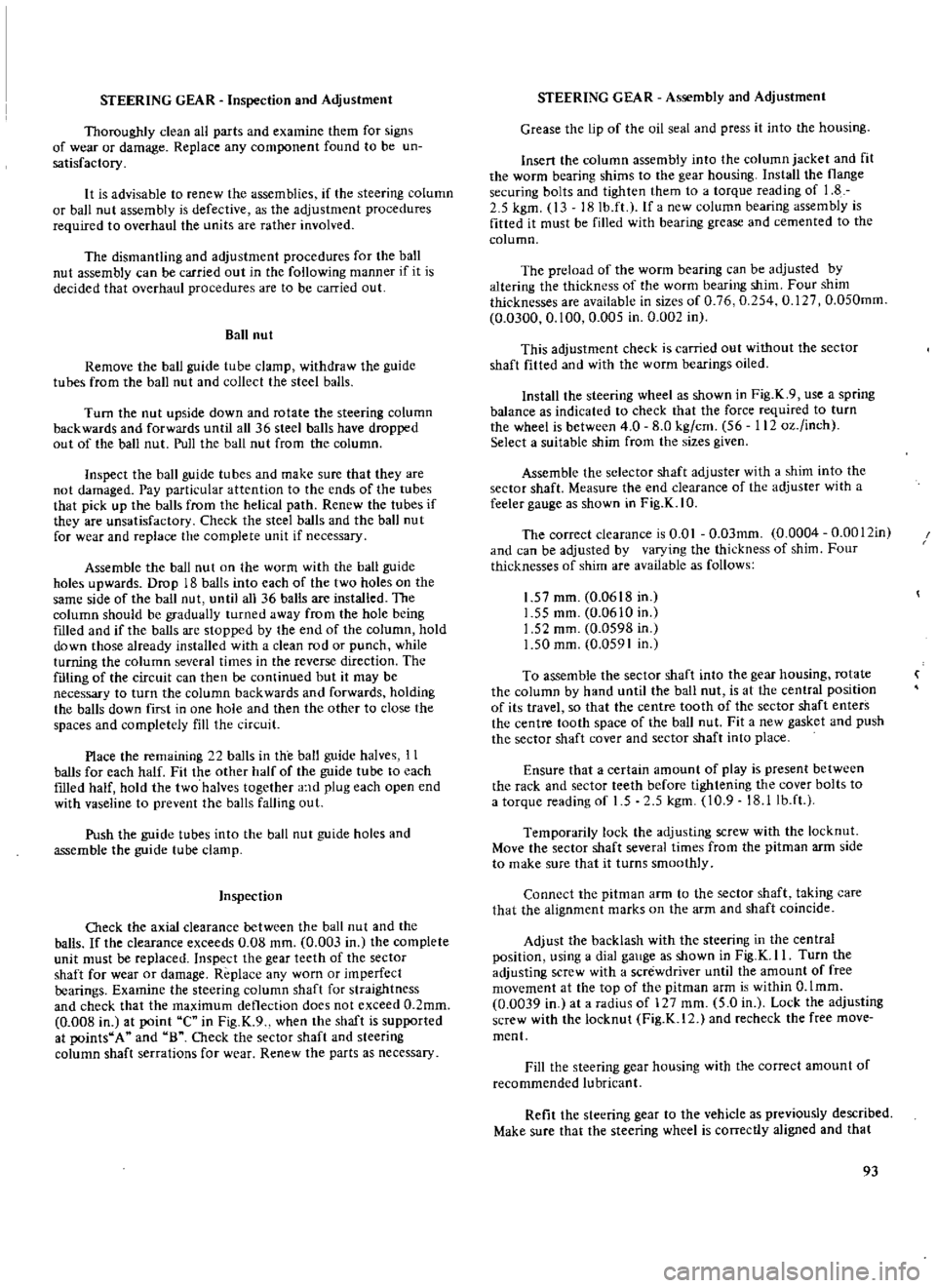
STEERING
GEAR
Inspection
and
Adjustment
Thoroughly
clean
all
parts
and
examine
them
for
signs
of
wear
or
damage
Replace
any
comIK
nent
found
to
be
un
satisfactory
It
is
advisable
to
renew
the
assemblies
if
the
steering
column
or
ball
nut
assembly
is
defective
as
the
adjustment
procedures
required
to
overhaul
the
units
are
rather
involved
The
dismantling
and
adjustment
procedures
for
the
ball
nut
assembly
can
be
carried
out
in
the
following
manner
if
it
is
decided
that
overhaul
procedures
are
to
be
carried
out
Ball
nut
Remove
the
ball
guide
tube
clamp
withdraw
the
guide
tubes
from
the
ball
nut
and
collect
the
steel
balls
Turn
the
nut
upside
down
and
rotate
the
steering
column
backwards
and
forwards
until
all
36
steel
balls
have
dropped
out
of
the
ball
nut
Pull
the
ball
nut
from
the
column
Inspect
the
ball
guide
tubes
and
make
sure
that
they
are
not
damaged
Pay
particular
attention
to
the
ends
of
the
tubes
that
pick
up
the
balls
from
the
helical
path
Renew
the
tubes
if
they
are
unsatisfactory
Check
the
steel
balls
and
the
ball
nut
for
wear
and
replace
the
complete
unit
if
necessary
Assemble
the
ball
nut
on
the
worm
with
the
ball
guide
holes
upwards
Drop
18
balls
into
each
of
the
two
holes
on
the
same
side
of
the
ball
nut
until
all
36
balls
are
installed
The
column
should
be
gradually
turned
away
from
the
hole
being
filled
and
if
the
balls
are
stopped
by
the
end
of
the
column
hold
down
those
already
installed
with
a
clean
rod
or
punch
while
turning
the
column
several
times
in
the
reverse
direction
The
filling
of
the
circuit
can
then
be
continued
but
it
may
be
necessary
to
turn
the
column
backwards
and
forwards
holding
the
balls
down
first
in
one
hole
and
then
the
other
to
close
the
spaces
and
completely
fill
the
circuit
Place
the
remaining
22
balls
in
the
ball
guide
halves
11
balls
for
each
half
Fit
the
other
half
of
the
guide
tube
to
each
f11led
half
hold
the
two
halves
together
a
ld
plug
each
open
end
with
vaseline
to
prevent
the
balls
falling
out
Push
the
guide
tubes
into
the
ball
nut
guide
holes
and
assemble
the
guide
tube
clamp
Inspection
Oteck
the
axial
clearance
between
the
ball
nut
and
the
balls
If
the
clearance
exceeds
0
08
mrn
0
003
in
the
complete
unit
must
be
replaced
Inspect
the
gear
teeth
of
the
sector
shaft
for
wear
or
damage
Replace
any
worn
or
imperfect
bearings
Examine
the
steering
column
shaft
for
straightness
and
check
that
the
maximum
deflection
does
not
exceed
0
2mm
0
008
in
at
point
C
in
Fig
K
9
when
the
shaft
is
supported
at
points
A
and
B
Check
the
sector
shaft
and
steering
column
shaft
serrations
for
wear
Renew
the
parts
as
necessary
STEERING
GEAR
Assembly
and
Adjustment
Grease
the
lip
of
the
oil
seal
and
press
it
into
the
housing
Insert
the
column
assembly
into
the
column
jacket
and
fit
the
worm
bearing
shims
to
the
gear
housing
Install
the
flange
securing
bolts
and
tighten
them
to
a
torque
reading
of
1
8
2
5
kgm
13
18lb
ft
If
a
new
column
bearing
assembly
is
fitted
it
must
be
filled
with
bearing
grease
and
cemented
to
the
column
The
preload
of
the
worm
bearing
can
be
adjusted
by
altering
the
thickness
of
the
worm
bearing
shim
Four
shim
thicknesses
are
available
in
sizes
of
0
76
0
254
0
127
0
050mm
0
0300
0
100
0
005
in
0
002
in
This
adjustment
check
is
carried
out
without
the
sector
shaft
fitted
and
with
the
worm
bearings
oiled
Install
the
steering
wheel
as
shown
in
Fig
K
9
use
a
spring
balance
as
indicated
to
check
that
the
force
required
to
turn
the
wheel
is
between
4
0
8
0
kg
cm
56
l120z
inch
Select
a
suitable
shim
from
the
sizes
given
Assemble
the
selector
shaft
adjuster
with
a
shim
into
the
sector
shaft
Measure
the
end
clearance
of
the
adjuster
with
a
feeler
gauge
as
shown
in
Fig
K
1
O
The
correct
clearance
is
0
01
0
03mm
0
0004
O
0012in
and
can
be
adjusted
by
varying
the
thickness
of
shim
Four
thicknesses
of
shim
are
available
as
follows
1
57
mm
0
0618
in
1
55
mm
0
0610
in
1
52
mm
0
0598
in
1
50
mm
0
0591
in
To
assemble
the
sector
shaft
into
the
gear
housing
rotate
the
column
by
hand
until
the
ball
nut
is
at
the
central
position
of
its
travel
so
that
the
centre
tooth
of
the
sector
shaft
enters
the
centre
tooth
space
of
the
ball
nut
Fit
a
new
gasket
and
push
the
sector
shaft
cover
and
sector
shaft
into
place
Ensure
that
a
certain
amount
of
play
is
present
between
the
rack
and
sector
teeth
before
tightening
the
cover
bolts
to
a
torque
reading
of
1
5
2
5
kgm
10
9
18
llb
ft
Temporarily
lock
the
adjusting
screw
with
the
locknut
Move
the
sector
shaft
several
times
from
the
pitman
arm
side
to
make
sure
that
it
turns
smoothly
Connect
the
pitman
arm
to
the
sector
shaft
taking
care
that
the
alignment
marks
on
the
arm
and
shaft
coincide
Adjust
the
backlash
with
the
steering
in
the
central
position
using
a
dial
gauge
as
shown
in
Fig
K
II
Turn
the
adjusting
screw
with
a
screwdriver
until
the
amount
of
free
movement
at
the
top
of
the
pitman
arm
is
within
O
lmm
0
0039
in
at
a
radius
of
127
mm
5
0
in
Lock
the
adjusting
screw
with
the
locknut
Fig
K
12
and
recheck
the
free
move
ment
Fill
the
steering
gear
housing
with
the
correct
amount
of
recommended
lubricant
Refit
the
steering
gear
to
the
vehicle
as
previously
described
Make
sure
that
the
steering
wheel
is
correctly
aligned
and
that
93
Page 96 of 171
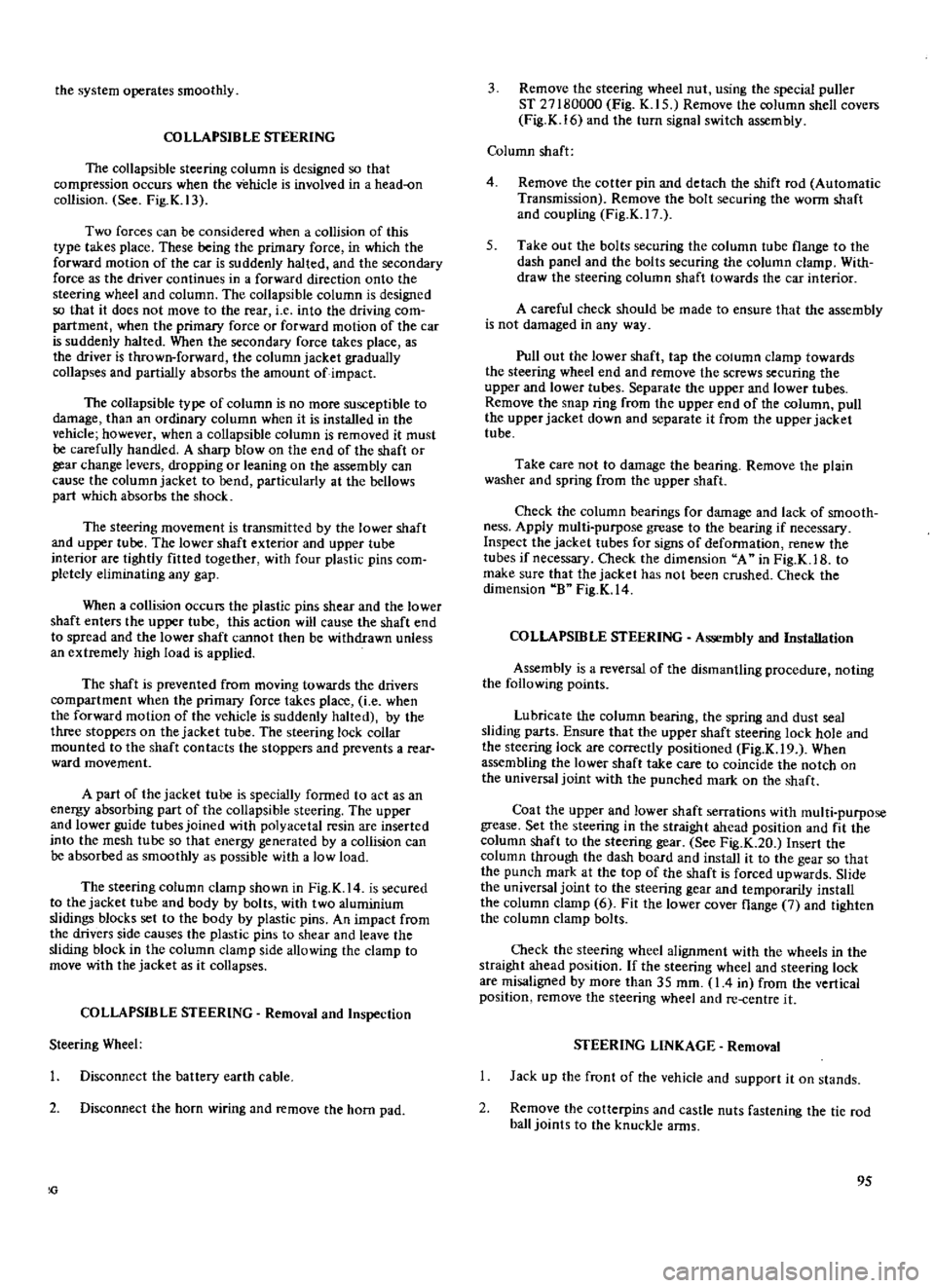
the
system
operates
smoothly
COLLAPSIBLE
STEERING
The
collapsible
steering
column
is
designed
so
that
compression
occurs
when
the
vehicle
is
involved
in
a
head
on
collision
See
Fig
K
13
Two
forces
can
be
considered
when
a
collision
of
this
type
takes
place
These
being
the
primary
force
in
which
the
forward
motion
of
the
car
is
suddenly
halted
and
the
secondary
force
as
the
driver
continues
in
a
forward
direction
onto
the
steering
wheel
and
column
The
collapsible
column
is
designed
so
that
it
does
not
move
to
the
rear
i
e
into
the
driving
com
partment
when
the
primary
force
or
forward
motion
of
the
car
is
suddenly
halted
When
the
secondary
force
takes
place
as
the
driver
is
thrown
forward
the
column
jacket
gradually
collapses
and
partially
absorbs
the
amount
of
impact
The
collapsible
type
of
column
is
no
more
susceptible
to
damage
than
an
ordinary
column
when
it
is
installed
in
the
vehicle
however
when
a
collapsible
column
is
removed
it
must
be
carefully
handled
A
sharp
blow
on
the
end
of
the
shaft
or
gear
change
levers
dropping
or
leaning
on
the
assembly
can
cause
the
column
jacket
to
bend
particularly
at
the
bellows
part
which
absorbs
the
shock
The
steering
movement
is
transmitted
by
the
lower
shaft
and
upper
tube
The
lower
shaft
exterior
and
upper
tube
interior
are
tightly
fitted
together
with
four
plastic
pins
com
pletely
eliminating
any
gap
When
a
collision
occurs
the
plastic
pins
shear
and
the
lower
shaft
enters
the
upper
tube
this
action
will
cause
the
shaft
end
to
spread
and
the
lower
shaft
cannot
then
be
withdrawn
unless
an
extremely
high
load
is
applied
The
shaft
is
prevented
from
moving
towards
the
drivers
compartment
when
the
primary
force
takes
place
i
e
when
the
forward
motion
of
the
vehicle
is
suddenly
halted
by
the
three
stoppers
on
the
jacket
tube
The
steering
lock
collar
mounted
to
the
shaft
contacts
the
stoppers
and
prevents
a
rear
ward
movement
A
part
of
the
jacket
tube
is
specially
formed
to
act
as
an
energy
absorbing
part
of
the
collapsible
steering
The
upper
and
lower
guide
tubes
joined
with
polyacetal
resin
are
inserted
into
the
mesh
tube
so
that
energy
generated
by
a
collision
can
be
absorbed
as
smoothly
as
possible
with
a
low
load
The
steering
column
clamp
shown
in
Fig
K
14
is
secured
to
the
jacket
tube
and
body
by
bolts
with
two
aluminium
slidings
blocks
set
to
the
body
by
plastic
pins
An
impact
from
the
drivers
side
causes
the
plastic
pins
to
shear
and
leave
the
sliding
block
in
the
column
clamp
side
allowing
the
clamp
to
move
with
the
jacket
as
it
collapses
COLLAPSffiLE
STEERING
Removal
and
Inspection
Steering
Wheel
I
Disconnect
the
battery
earth
cable
2
Disconnect
the
horn
wiring
and
remove
the
horn
pad
3
Remove
the
steering
wheel
nut
using
the
special
puller
ST
27180000
Eig
K
15
Remove
the
column
shell
covers
Fig
K
16
and
the
turn
signal
switch
assembly
Column
shaft
4
Remove
the
cotter
pin
and
detach
the
shift
rod
Automatic
Transmission
Remove
the
bolt
securing
the
worm
shaft
and
coupling
Fig
K
17
5
Take
out
the
bolts
securing
the
column
tube
flange
to
the
dash
panel
and
the
bolts
securing
the
column
clamp
With
draw
the
steering
column
shaft
towards
the
car
interior
A
careful
check
should
be
made
to
ensure
that
the
assembly
is
not
damaged
in
any
way
Pull
out
the
lower
shaft
tap
the
column
clamp
towards
the
steering
wheel
end
and
remove
the
screws
securing
the
upper
and
lower
tubes
Separate
the
upper
and
lower
tubes
Remove
the
snap
ring
from
the
upper
end
of
the
column
pull
the
upper
jacket
down
and
separate
it
from
the
upper
jacket
tube
Take
care
not
to
damage
the
bearing
Remove
the
plain
washer
and
spring
from
the
upper
shaft
Check
the
column
bearings
for
damage
and
lack
of
smooth
ness
Apply
multi
purpose
grease
to
the
bearing
if
necessary
Inspect
the
jacket
tubes
for
signs
of
deformation
renew
the
tubes
if
necessary
Check
the
dimension
A
in
Fig
K
1B
to
make
SUfe
that
the
jacket
has
not
been
crushed
Check
the
dimension
B
Fig
K
14
COLLAPSffiLE
STEERING
Assembly
and
Installation
Assembly
is
a
reversal
of
the
dismantling
procedure
noting
the
following
points
Lubricate
the
column
bearing
the
spring
and
dust
seal
sliding
parts
Ensure
that
the
upper
shaft
steering
lock
hole
and
the
steering
lock
are
correctly
positioned
Fig
K
19
When
assembling
the
lower
shaft
take
care
to
coincide
the
notch
on
the
universal
joint
with
the
punched
mark
on
the
shaft
Coat
the
upper
and
lower
shaft
serrations
with
multi
purpose
grease
Set
the
steering
in
the
straight
ahead
position
and
fit
the
column
shaft
to
the
steering
gear
See
Fig
K
20
Insert
the
column
through
the
dash
board
and
install
it
to
the
gear
so
that
the
punch
mark
at
the
top
of
the
shaft
is
forced
upwards
Slide
the
universal
joint
to
the
steering
gear
and
temporarily
install
the
column
clamp
6
Fit
the
lower
cover
flange
7
and
tighten
the
column
clamp
bolts
Check
the
steering
wheel
alignment
with
the
wheels
in
the
straight
ahead
position
If
the
steering
wheel
and
steering
lock
are
misaligned
by
more
than
35
mm
I
4
in
from
the
vertical
position
femove
the
steering
wheel
and
re
centre
it
STEERING
LINKAGE
Removal
Jack
up
the
front
of
the
vehicle
and
support
it
on
stands
2
Remove
the
cotterpins
and
castle
nuts
fastening
the
tie
rod
ball
joints
to
the
knuckle
arms
95
Page 98 of 171
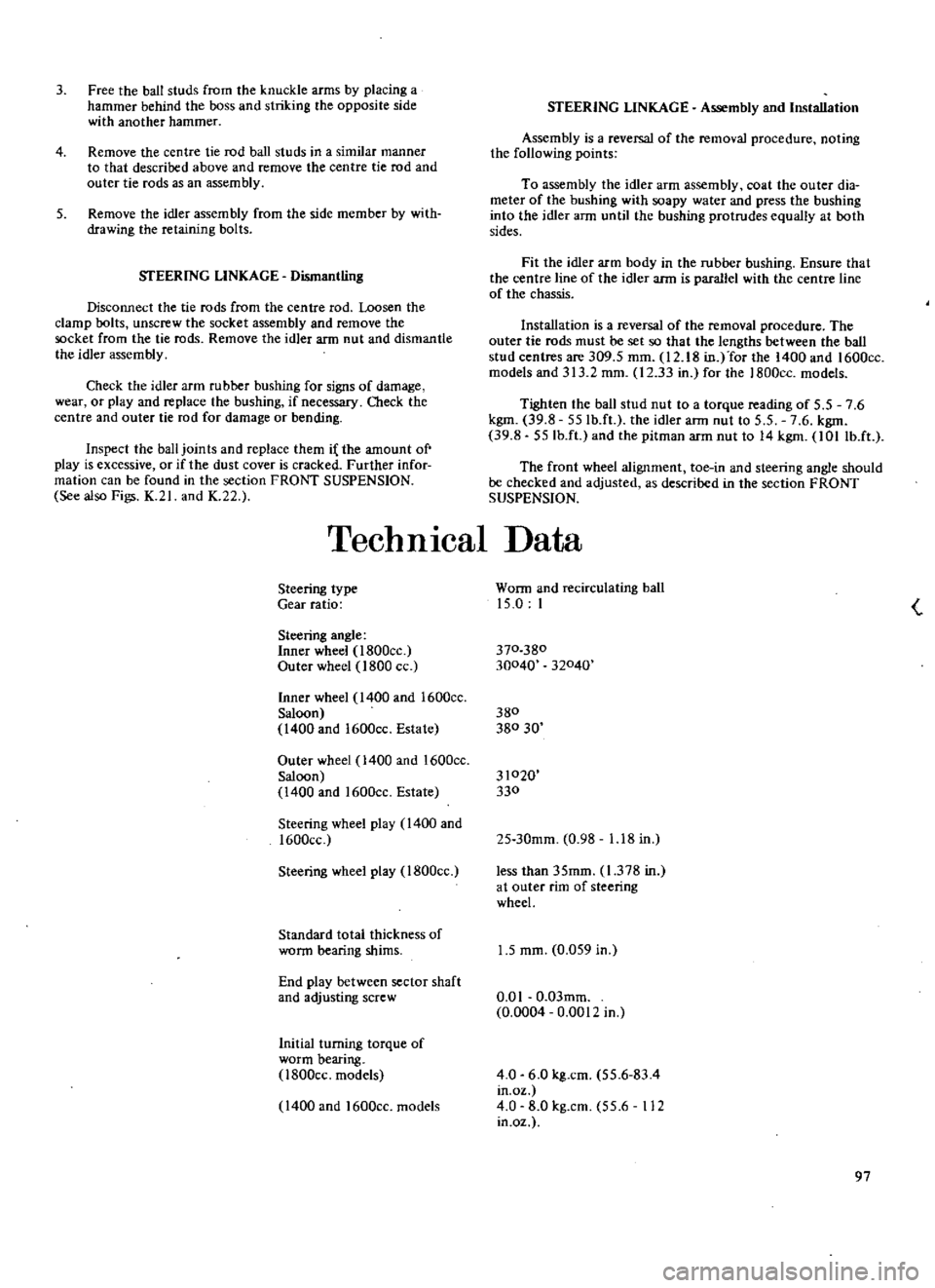
3
Free
the
ball
studs
from
the
knuckle
arms
by
placing
a
hammer
behind
the
boss
and
striking
the
opposite
side
with
another
hammer
4
Remove
the
centre
tie
rod
ball
studs
in
a
similar
manner
to
that
described
above
and
remove
the
centre
tie
rod
and
outer
tie
rods
as
an
assembly
5
Remove
the
idler
assembly
from
the
side
member
by
with
drawing
the
retaining
bolts
SfEERING
LINKAGE
Dismantling
Disconnect
the
tie
rods
from
the
centre
rod
Loosen
the
clamp
bolts
unscrew
the
socket
assembly
and
remove
the
socket
from
the
tie
rods
Remove
the
idler
arm
nut
and
dismantle
the
idler
assembly
Check
the
idler
arm
rubber
bushing
for
signs
of
damage
wear
or
play
and
replace
the
bushing
if
necessary
Oteck
the
centre
and
outer
tie
rod
for
damage
or
bending
Inspect
the
ball
joints
and
replace
them
i
the
amount
of
play
is
excessive
or
if
the
dust
cover
is
cracked
Further
infor
mation
can
be
found
in
the
section
FRONT
SUSPENSION
See
also
Figs
K
21
and
K
22
STEERING
LINKAGE
Assembly
and
Installation
Assembly
is
a
reversal
of
the
removal
procedure
noting
the
following
points
To
assembly
the
idler
arm
assembly
coat
the
outer
dia
meter
of
the
bushing
with
soapy
water
and
press
the
bushing
into
the
idler
arm
until
the
bushing
protrudes
equally
at
both
sides
Fit
the
idler
arm
body
in
the
rubber
bushing
Ensure
that
the
centre
line
of
the
idler
arm
is
parallel
with
the
centre
line
of
the
chassis
Installation
is
a
reversal
of
the
removal
procedure
The
outer
tie
rods
must
be
set
so
that
the
lengths
between
the
ball
stud
centres
are
309
5
mm
12
18
in
for
the
1400
and
1600cc
models
and
313
2
mm
12
33
in
for
the
1800cc
models
Tighten
the
ball
stud
nut
to
a
torque
reading
of
5
5
7
6
kgm
39
8
55Ib
ft
the
idler
ann
nut
to
5
5
7
6
kgm
39
8
55Ib
ft
and
the
pitman
arm
nut
to
14
kgm
lOllb
ft
The
front
wheel
alignment
toe
in
and
steering
angle
should
be
checked
and
adjusted
as
described
in
the
section
FRONT
SUSPENSION
TechnIcal
Data
Steering
type
Gear
ratio
Steering
angle
Inner
wheel
l800cc
Outer
wheel
1800
cc
Inner
wheel
1400
and
1600cc
Saloon
1400
and
1600cc
Estate
Outer
wheel
1400
and
1600cc
Saloon
1400
and
1600cc
Estate
Steering
wheel
play
1400
and
1600cc
Steering
wheel
play
1800cc
Standard
total
thickness
of
worm
bearing
shims
End
play
between
sector
shaft
and
adjusting
screw
Initial
turning
torque
of
worm
bearing
l800cc
models
1400
and
1600cc
models
Worm
and
recirculating
ball
15
0
I
370
380
30040
32040
380
380
30
31020
330
25
30mm
0
98
1
18
in
less
than
35mm
1
378
in
at
outer
rim
of
steering
wheel
1
5
mm
0
059
in
0
0
I
0
03mm
0
0004
0
0012
in
4
0
6
0
kg
cm
55
6
83
4
in
oz
4
0
8
0
kg
cm
55
6
112
in
oz
97