key DODGE RAM 1500 1998 2.G Workshop Manual
[x] Cancel search | Manufacturer: DODGE, Model Year: 1998, Model line: RAM 1500, Model: DODGE RAM 1500 1998 2.GPages: 2627
Page 2322 of 2627
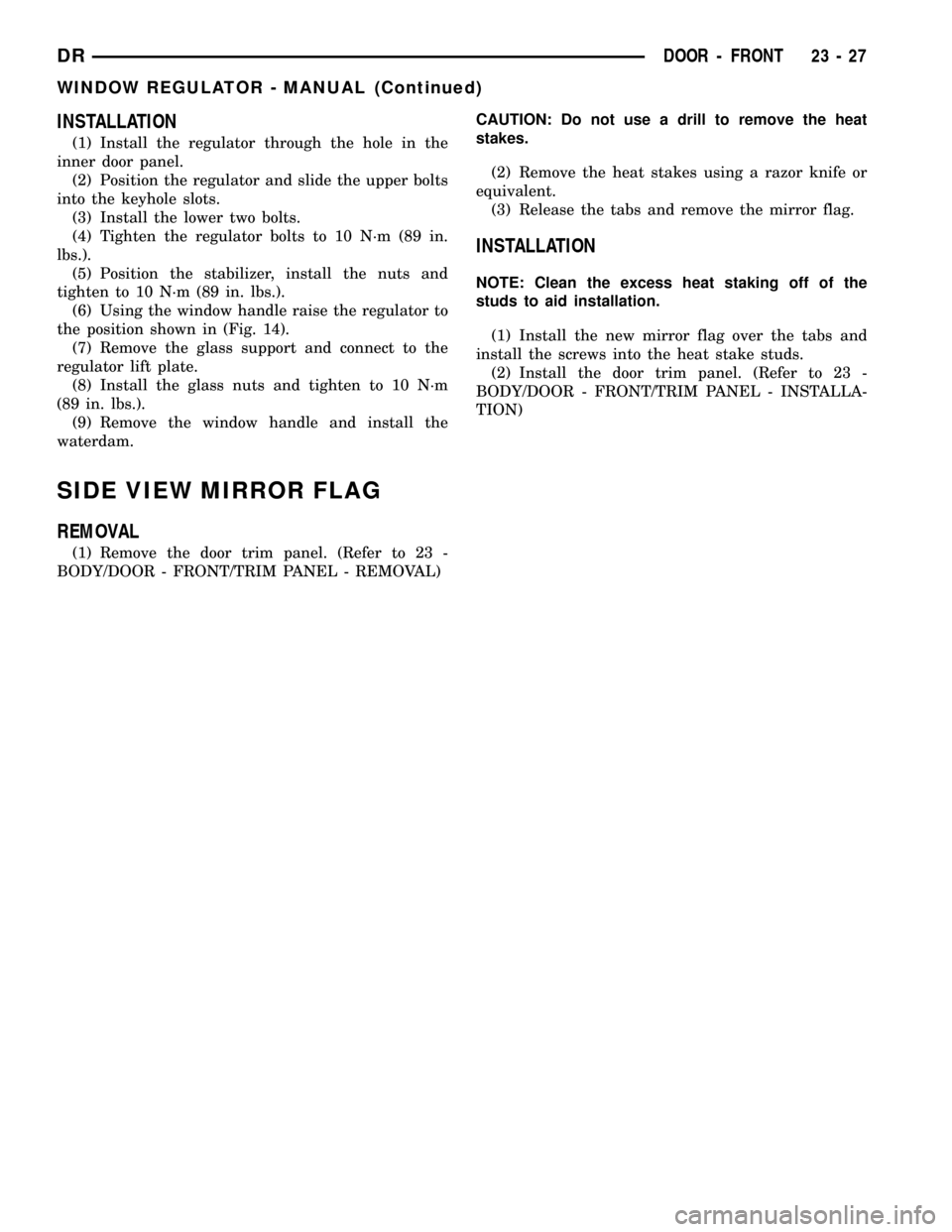
INSTALLATION
(1) Install the regulator through the hole in the
inner door panel.
(2) Position the regulator and slide the upper bolts
into the keyhole slots.
(3) Install the lower two bolts.
(4) Tighten the regulator bolts to 10 N´m (89 in.
lbs.).
(5) Position the stabilizer, install the nuts and
tighten to 10 N´m (89 in. lbs.).
(6) Using the window handle raise the regulator to
the position shown in (Fig. 14).
(7) Remove the glass support and connect to the
regulator lift plate.
(8) Install the glass nuts and tighten to 10 N´m
(89 in. lbs.).
(9) Remove the window handle and install the
waterdam.
SIDE VIEW MIRROR FLAG
REMOVAL
(1) Remove the door trim panel. (Refer to 23 -
BODY/DOOR - FRONT/TRIM PANEL - REMOVAL)CAUTION: Do not use a drill to remove the heat
stakes.
(2) Remove the heat stakes using a razor knife or
equivalent.
(3) Release the tabs and remove the mirror flag.
INSTALLATION
NOTE: Clean the excess heat staking off of the
studs to aid installation.
(1) Install the new mirror flag over the tabs and
install the screws into the heat stake studs.
(2) Install the door trim panel. (Refer to 23 -
BODY/DOOR - FRONT/TRIM PANEL - INSTALLA-
TION)
DRDOOR - FRONT 23 - 27
WINDOW REGULATOR - MANUAL (Continued)
Page 2325 of 2627

DOOR GLASS
REMOVAL
(1) Remove the glass run channels. (Refer to 23 -
BODY/DOORS - REAR/GLASS RUN CHANNEL -
REMOVAL)
(2) Remove the glass support and place the glass
into the bottom of the door.
(3) Separate the glass run weatherstrip from the
rear of the window opening.
(4) Remove the inner belt molding. (Refer to 23 -
BODY/WEATHERSTRIP/SEALS/FRONT DOOR
INNER BELT WEATHERSTRIP - REMOVAL)
(5) Remove the glass from the window opening.
INSTALLATION
(1) Install the glass through the window opening
and pace the glass into the bottom of the door.
(2) Install the inner belt molding. (Refer to 23 -
BODY/WEATHERSTRIP/SEALS/FRONT DOOR
INNER BELT WEATHERSTRIP - INSTALLATION)
(3) Stuff the glass run weatherstrip into the win-
dow frame.
(4) Secure the glass in the up position using a
wood wedge or equivalent.
(5) Install the glass run channels. (Refer to 23 -
BODY/DOORS - REAR/GLASS RUN CHANNEL -
INSTALLATION)
EXTERIOR HANDLE
REMOVAL
(1) Remove the front glass run channel. (Refer to
23 - BODY/DOORS - REAR/GLASS RUN CHANNEL
- REMOVAL)
(2) Disconnect the latch actuator rod. (Fig. 2)
(3) Remove the nuts and remove the handle.
INSTALLATION
(1) Install the latch and install the nuts.
(2) Connect the latch actuator rod.
(3) Install the front glass run channel. (Refer to 23
- BODY/DOORS - REAR/GLASS RUN CHANNEL -
INSTALLATION)
GLASS RUN CHANNEL
REMOVAL
(1) Remove the window regulator. (Refer to 23 -
BODY/DOORS - REAR/WINDOW REGULATOR -
REMOVAL)
(2) Remove the bottom screws and loosen the top
screws from bolt channels. (Fig. 3) and (Fig. 4)(3) Slide the channels up to disengage from the
keyhole slots.
(4) Separate the glass run weatherstrip from the
channel and remove the channels.
Fig. 2 EXTERIOR HANDLE
1 - LATCH ACTUATOR ROD
2-LATCH
3 - NUTS (2)
Fig. 3 FRONT RUN CHANNEL
1 - BOLTS
2 - FRONT RUN CHANNEL
23 - 30 DOORS - REARDR
Page 2326 of 2627
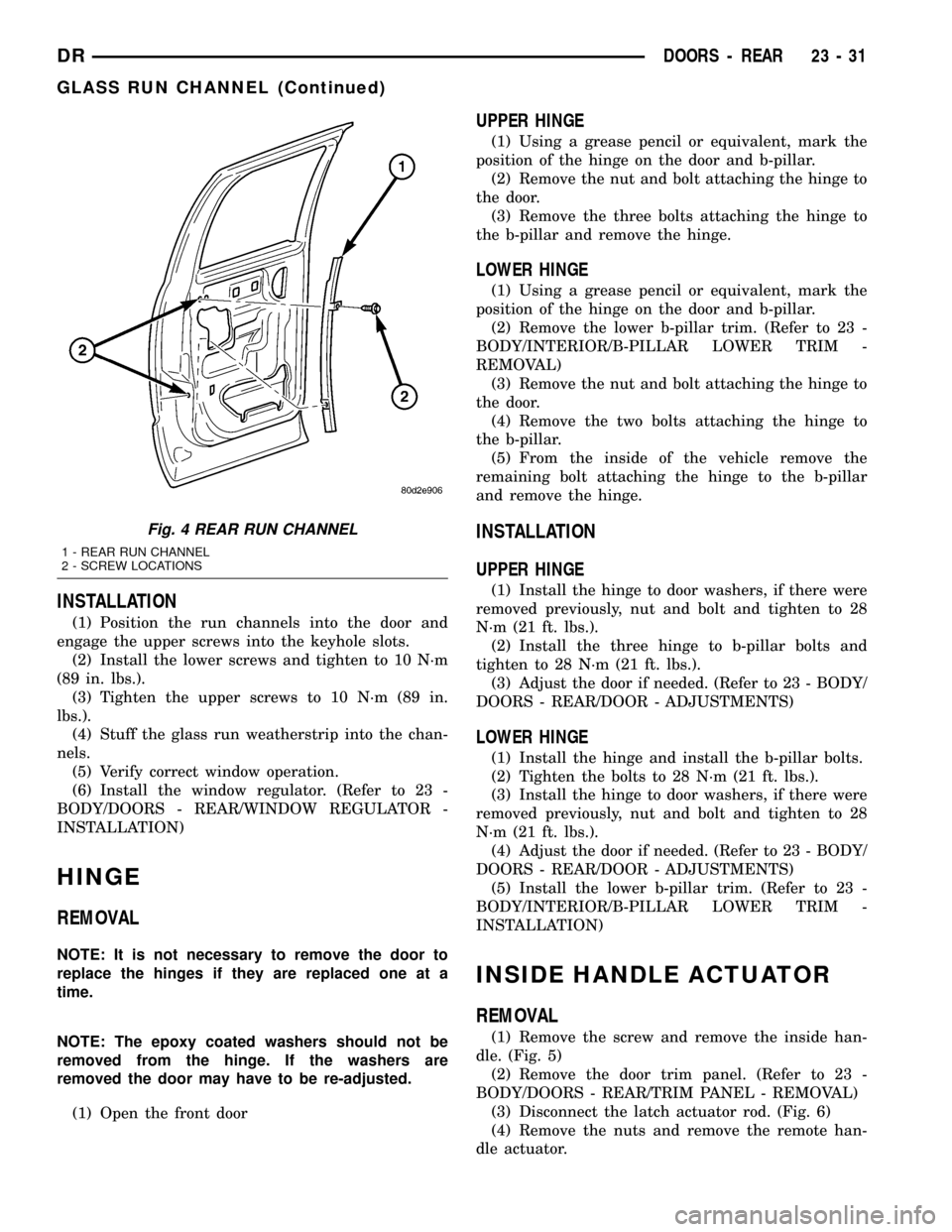
INSTALLATION
(1) Position the run channels into the door and
engage the upper screws into the keyhole slots.
(2) Install the lower screws and tighten to 10 N´m
(89 in. lbs.).
(3) Tighten the upper screws to 10 N´m (89 in.
lbs.).
(4) Stuff the glass run weatherstrip into the chan-
nels.
(5) Verify correct window operation.
(6) Install the window regulator. (Refer to 23 -
BODY/DOORS - REAR/WINDOW REGULATOR -
INSTALLATION)
HINGE
REMOVAL
NOTE: It is not necessary to remove the door to
replace the hinges if they are replaced one at a
time.
NOTE: The epoxy coated washers should not be
removed from the hinge. If the washers are
removed the door may have to be re-adjusted.
(1) Open the front door
UPPER HINGE
(1) Using a grease pencil or equivalent, mark the
position of the hinge on the door and b-pillar.
(2) Remove the nut and bolt attaching the hinge to
the door.
(3) Remove the three bolts attaching the hinge to
the b-pillar and remove the hinge.
LOWER HINGE
(1) Using a grease pencil or equivalent, mark the
position of the hinge on the door and b-pillar.
(2) Remove the lower b-pillar trim. (Refer to 23 -
BODY/INTERIOR/B-PILLAR LOWER TRIM -
REMOVAL)
(3) Remove the nut and bolt attaching the hinge to
the door.
(4) Remove the two bolts attaching the hinge to
the b-pillar.
(5) From the inside of the vehicle remove the
remaining bolt attaching the hinge to the b-pillar
and remove the hinge.
INSTALLATION
UPPER HINGE
(1) Install the hinge to door washers, if there were
removed previously, nut and bolt and tighten to 28
N´m (21 ft. lbs.).
(2) Install the three hinge to b-pillar bolts and
tighten to 28 N´m (21 ft. lbs.).
(3) Adjust the door if needed. (Refer to 23 - BODY/
DOORS - REAR/DOOR - ADJUSTMENTS)
LOWER HINGE
(1) Install the hinge and install the b-pillar bolts.
(2) Tighten the bolts to 28 N´m (21 ft. lbs.).
(3) Install the hinge to door washers, if there were
removed previously, nut and bolt and tighten to 28
N´m (21 ft. lbs.).
(4) Adjust the door if needed. (Refer to 23 - BODY/
DOORS - REAR/DOOR - ADJUSTMENTS)
(5) Install the lower b-pillar trim. (Refer to 23 -
BODY/INTERIOR/B-PILLAR LOWER TRIM -
INSTALLATION)
INSIDE HANDLE ACTUATOR
REMOVAL
(1) Remove the screw and remove the inside han-
dle. (Fig. 5)
(2) Remove the door trim panel. (Refer to 23 -
BODY/DOORS - REAR/TRIM PANEL - REMOVAL)
(3) Disconnect the latch actuator rod. (Fig. 6)
(4) Remove the nuts and remove the remote han-
dle actuator.
Fig. 4 REAR RUN CHANNEL
1 - REAR RUN CHANNEL
2 - SCREW LOCATIONS
DRDOORS - REAR 23 - 31
GLASS RUN CHANNEL (Continued)
Page 2329 of 2627
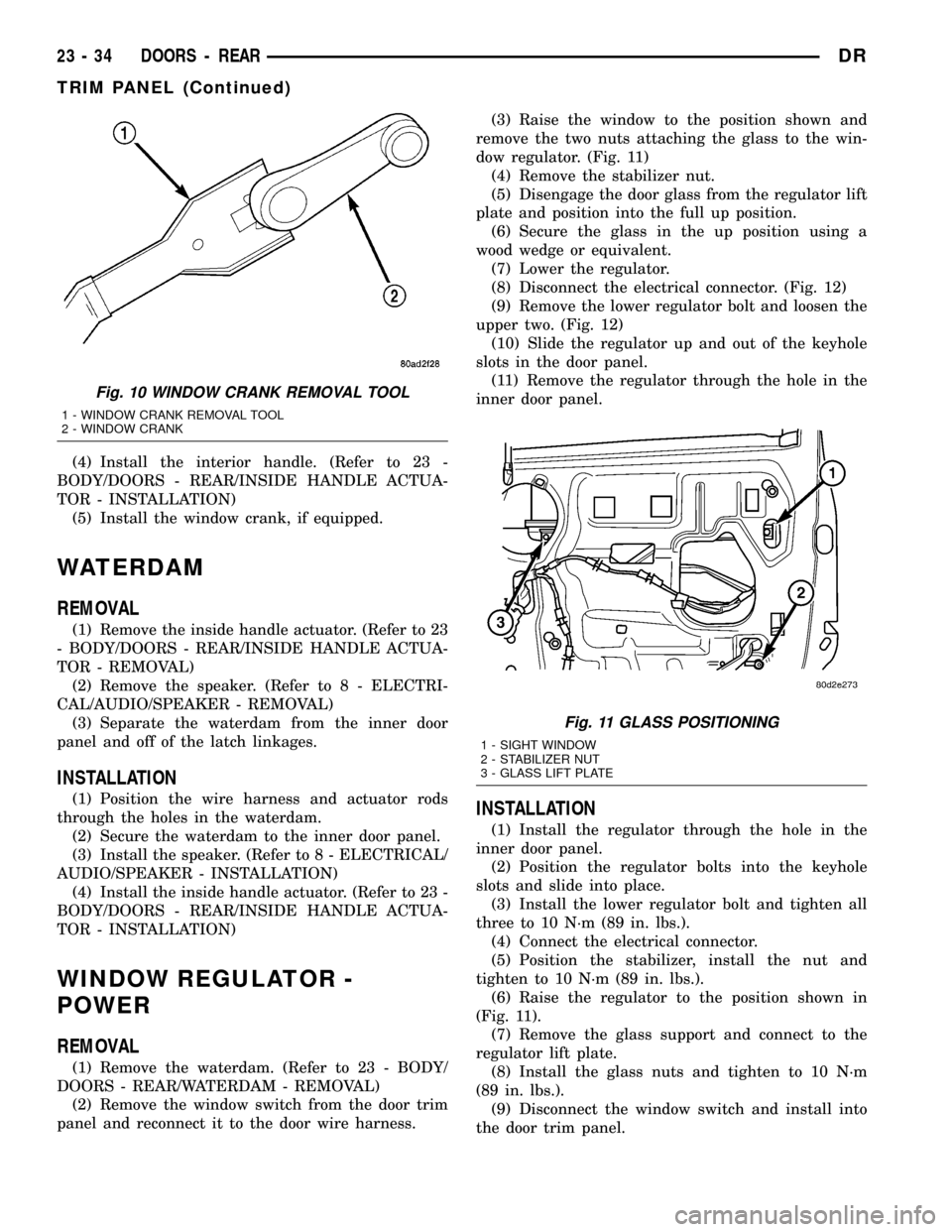
(4) Install the interior handle. (Refer to 23 -
BODY/DOORS - REAR/INSIDE HANDLE ACTUA-
TOR - INSTALLATION)
(5) Install the window crank, if equipped.
WATERDAM
REMOVAL
(1) Remove the inside handle actuator. (Refer to 23
- BODY/DOORS - REAR/INSIDE HANDLE ACTUA-
TOR - REMOVAL)
(2) Remove the speaker. (Refer to 8 - ELECTRI-
CAL/AUDIO/SPEAKER - REMOVAL)
(3) Separate the waterdam from the inner door
panel and off of the latch linkages.
INSTALLATION
(1) Position the wire harness and actuator rods
through the holes in the waterdam.
(2) Secure the waterdam to the inner door panel.
(3) Install the speaker. (Refer to 8 - ELECTRICAL/
AUDIO/SPEAKER - INSTALLATION)
(4) Install the inside handle actuator. (Refer to 23 -
BODY/DOORS - REAR/INSIDE HANDLE ACTUA-
TOR - INSTALLATION)
WINDOW REGULATOR -
POWER
REMOVAL
(1) Remove the waterdam. (Refer to 23 - BODY/
DOORS - REAR/WATERDAM - REMOVAL)
(2) Remove the window switch from the door trim
panel and reconnect it to the door wire harness.(3) Raise the window to the position shown and
remove the two nuts attaching the glass to the win-
dow regulator. (Fig. 11)
(4) Remove the stabilizer nut.
(5) Disengage the door glass from the regulator lift
plate and position into the full up position.
(6) Secure the glass in the up position using a
wood wedge or equivalent.
(7) Lower the regulator.
(8) Disconnect the electrical connector. (Fig. 12)
(9) Remove the lower regulator bolt and loosen the
upper two. (Fig. 12)
(10) Slide the regulator up and out of the keyhole
slots in the door panel.
(11) Remove the regulator through the hole in the
inner door panel.
INSTALLATION
(1) Install the regulator through the hole in the
inner door panel.
(2) Position the regulator bolts into the keyhole
slots and slide into place.
(3) Install the lower regulator bolt and tighten all
three to 10 N´m (89 in. lbs.).
(4) Connect the electrical connector.
(5) Position the stabilizer, install the nut and
tighten to 10 N´m (89 in. lbs.).
(6) Raise the regulator to the position shown in
(Fig. 11).
(7) Remove the glass support and connect to the
regulator lift plate.
(8) Install the glass nuts and tighten to 10 N´m
(89 in. lbs.).
(9) Disconnect the window switch and install into
the door trim panel.
Fig. 10 WINDOW CRANK REMOVAL TOOL
1 - WINDOW CRANK REMOVAL TOOL
2 - WINDOW CRANK
Fig. 11 GLASS POSITIONING
1 - SIGHT WINDOW
2 - STABILIZER NUT
3 - GLASS LIFT PLATE
23 - 34 DOORS - REARDR
TRIM PANEL (Continued)
Page 2330 of 2627
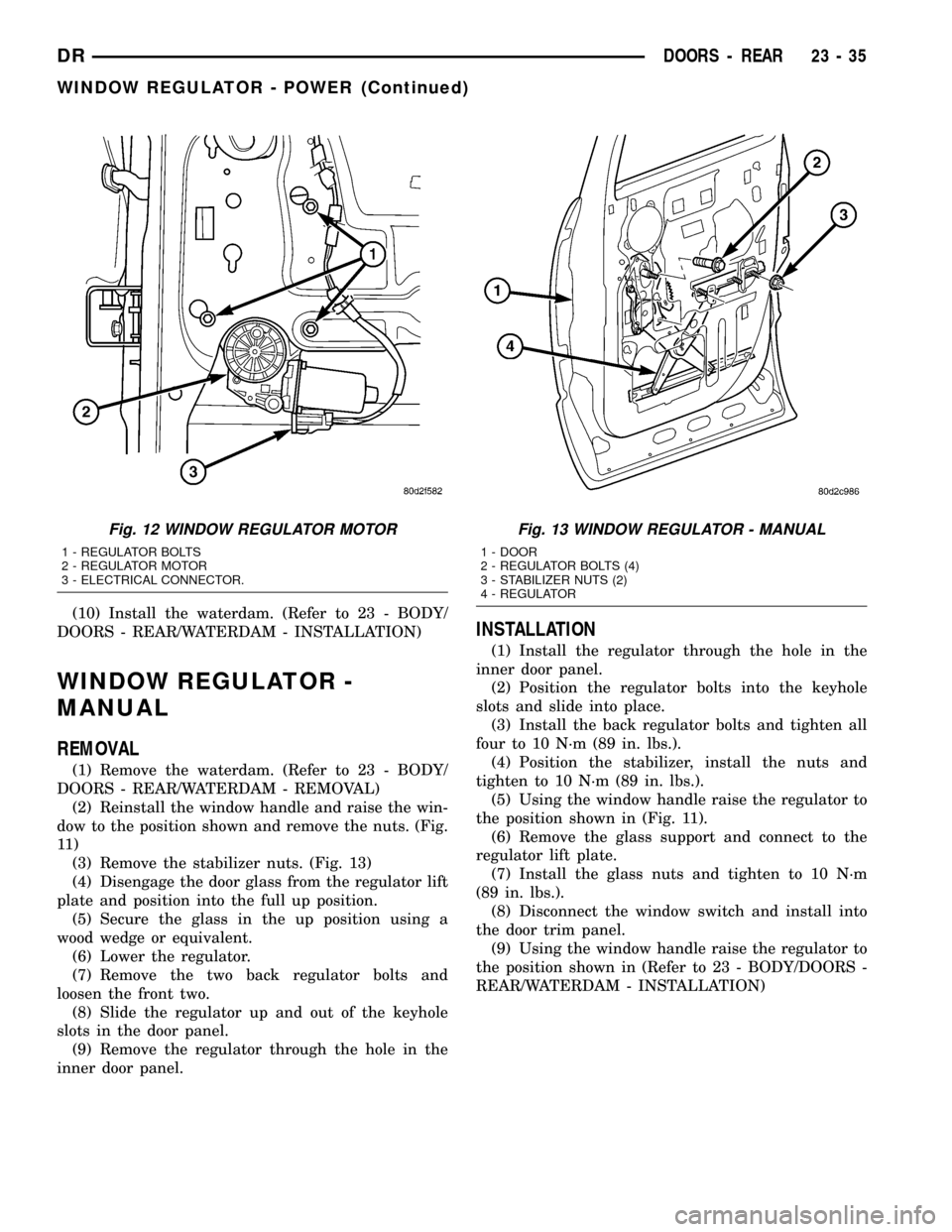
(10) Install the waterdam. (Refer to 23 - BODY/
DOORS - REAR/WATERDAM - INSTALLATION)
WINDOW REGULATOR -
MANUAL
REMOVAL
(1) Remove the waterdam. (Refer to 23 - BODY/
DOORS - REAR/WATERDAM - REMOVAL)
(2) Reinstall the window handle and raise the win-
dow to the position shown and remove the nuts. (Fig.
11 )
(3) Remove the stabilizer nuts. (Fig. 13)
(4) Disengage the door glass from the regulator lift
plate and position into the full up position.
(5) Secure the glass in the up position using a
wood wedge or equivalent.
(6) Lower the regulator.
(7) Remove the two back regulator bolts and
loosen the front two.
(8) Slide the regulator up and out of the keyhole
slots in the door panel.
(9) Remove the regulator through the hole in the
inner door panel.
INSTALLATION
(1) Install the regulator through the hole in the
inner door panel.
(2) Position the regulator bolts into the keyhole
slots and slide into place.
(3) Install the back regulator bolts and tighten all
four to 10 N´m (89 in. lbs.).
(4) Position the stabilizer, install the nuts and
tighten to 10 N´m (89 in. lbs.).
(5) Using the window handle raise the regulator to
the position shown in (Fig. 11).
(6) Remove the glass support and connect to the
regulator lift plate.
(7) Install the glass nuts and tighten to 10 N´m
(89 in. lbs.).
(8) Disconnect the window switch and install into
the door trim panel.
(9) Using the window handle raise the regulator to
the position shown in (Refer to 23 - BODY/DOORS -
REAR/WATERDAM - INSTALLATION)
Fig. 12 WINDOW REGULATOR MOTOR
1 - REGULATOR BOLTS
2 - REGULATOR MOTOR
3 - ELECTRICAL CONNECTOR.
Fig. 13 WINDOW REGULATOR - MANUAL
1 - DOOR
2 - REGULATOR BOLTS (4)
3 - STABILIZER NUTS (2)
4 - REGULATOR
DRDOORS - REAR 23 - 35
WINDOW REGULATOR - POWER (Continued)
Page 2391 of 2627
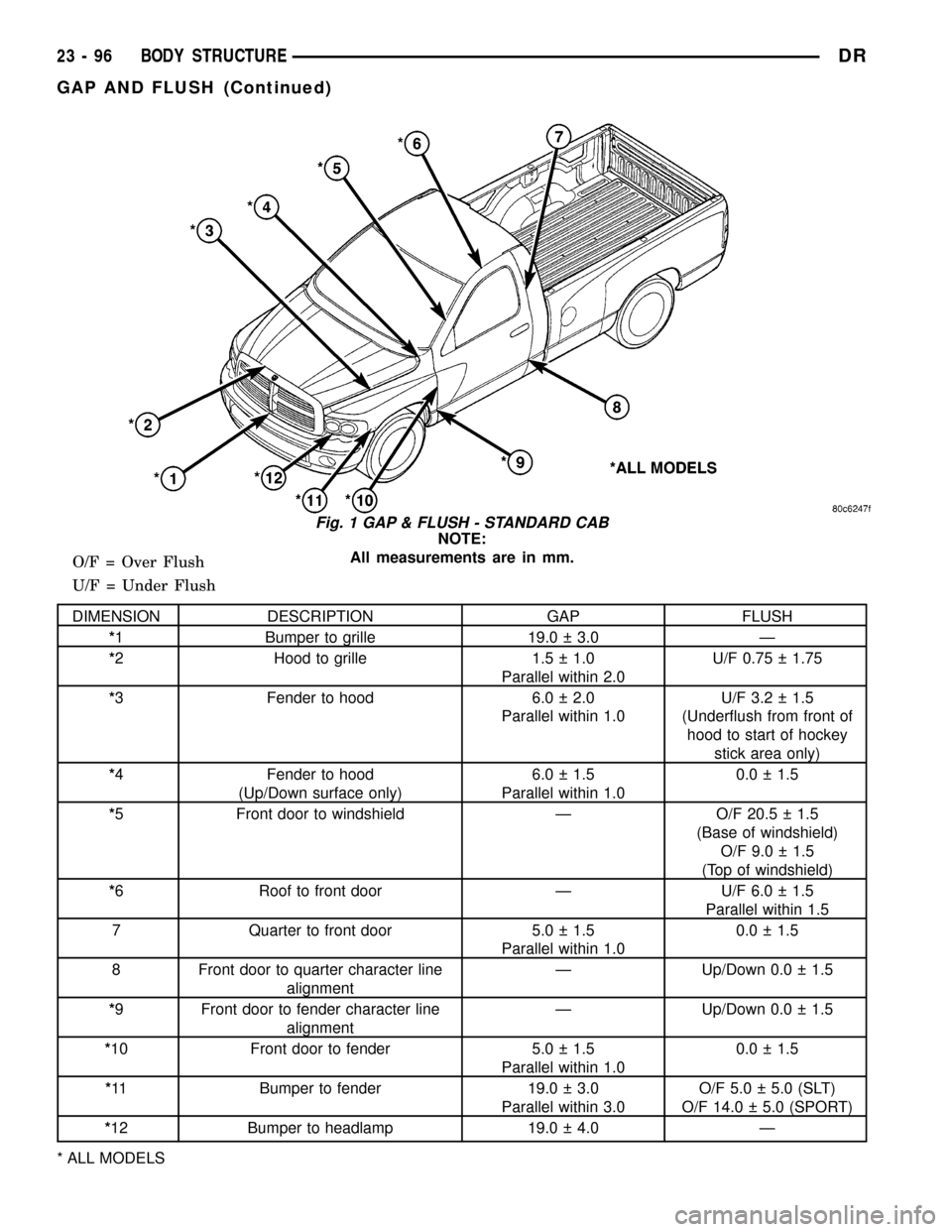
NOTE:
All measurements are in mm.
O/F = Over Flush
U/F = Under Flush
DIMENSION DESCRIPTION GAP FLUSH
*1 Bumper to grille 19.0 3.0 Ð
*2 Hood to grille 1.5 1.0
Parallel within 2.0U/F 0.75 1.75
*3 Fender to hood 6.0 2.0
Parallel within 1.0U/F 3.2 1.5
(Underflush from front of
hood to start of hockey
stick area only)
*4 Fender to hood
(Up/Down surface only)6.0 1.5
Parallel within 1.00.0 1.5
*5 Front door to windshield Ð O/F 20.5 1.5
(Base of windshield)
O/F 9.0 1.5
(Top of windshield)
*6 Roof to front door Ð U/F 6.0 1.5
Parallel within 1.5
7 Quarter to front door 5.0 1.5
Parallel within 1.00.0 1.5
8 Front door to quarter character line
alignmentÐ Up/Down 0.0 1.5
*9 Front door to fender character line
alignmentÐ Up/Down 0.0 1.5
*10 Front door to fender 5.0 1.5
Parallel within 1.00.0 1.5
*11 Bumper to fender 19.0 3.0
Parallel within 3.0O/F 5.0 5.0 (SLT)
O/F 14.0 5.0 (SPORT)
*12 Bumper to headlamp 19.0 4.0 Ð
* ALL MODELS
Fig. 1 GAP & FLUSH - STANDARD CAB
23 - 96 BODY STRUCTUREDR
GAP AND FLUSH (Continued)
Page 2496 of 2627
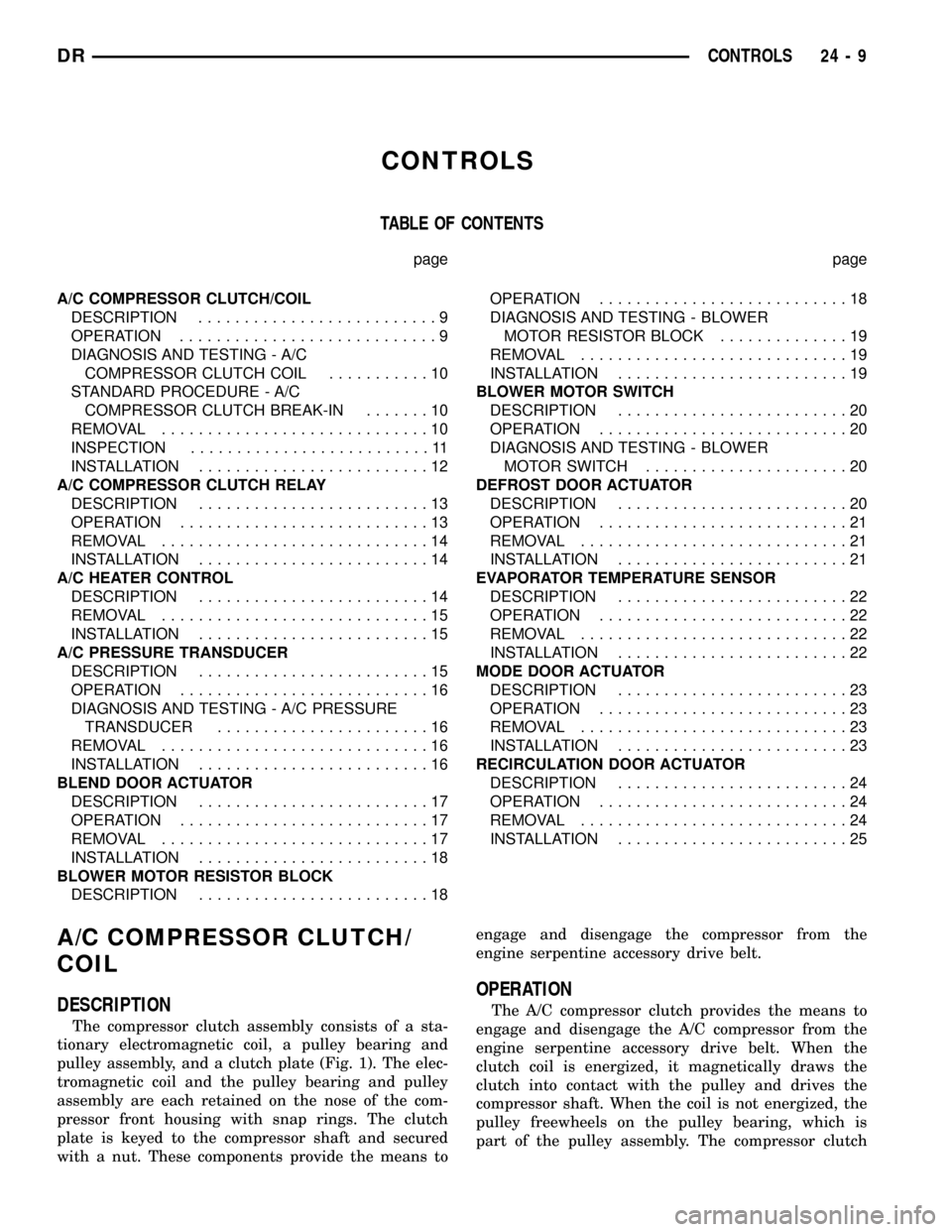
CONTROLS
TABLE OF CONTENTS
page page
A/C COMPRESSOR CLUTCH/COIL
DESCRIPTION..........................9
OPERATION............................9
DIAGNOSIS AND TESTING - A/C
COMPRESSOR CLUTCH COIL...........10
STANDARD PROCEDURE - A/C
COMPRESSOR CLUTCH BREAK-IN.......10
REMOVAL.............................10
INSPECTION..........................11
INSTALLATION.........................12
A/C COMPRESSOR CLUTCH RELAY
DESCRIPTION.........................13
OPERATION...........................13
REMOVAL.............................14
INSTALLATION.........................14
A/C HEATER CONTROL
DESCRIPTION.........................14
REMOVAL.............................15
INSTALLATION.........................15
A/C PRESSURE TRANSDUCER
DESCRIPTION.........................15
OPERATION...........................16
DIAGNOSIS AND TESTING - A/C PRESSURE
TRANSDUCER.......................16
REMOVAL.............................16
INSTALLATION.........................16
BLEND DOOR ACTUATOR
DESCRIPTION.........................17
OPERATION...........................17
REMOVAL.............................17
INSTALLATION.........................18
BLOWER MOTOR RESISTOR BLOCK
DESCRIPTION.........................18OPERATION...........................18
DIAGNOSIS AND TESTING - BLOWER
MOTOR RESISTOR BLOCK..............19
REMOVAL.............................19
INSTALLATION.........................19
BLOWER MOTOR SWITCH
DESCRIPTION.........................20
OPERATION...........................20
DIAGNOSIS AND TESTING - BLOWER
MOTOR SWITCH......................20
DEFROST DOOR ACTUATOR
DESCRIPTION.........................20
OPERATION...........................21
REMOVAL.............................21
INSTALLATION.........................21
EVAPORATOR TEMPERATURE SENSOR
DESCRIPTION.........................22
OPERATION...........................22
REMOVAL.............................22
INSTALLATION.........................22
MODE DOOR ACTUATOR
DESCRIPTION.........................23
OPERATION...........................23
REMOVAL.............................23
INSTALLATION.........................23
RECIRCULATION DOOR ACTUATOR
DESCRIPTION.........................24
OPERATION...........................24
REMOVAL.............................24
INSTALLATION.........................25
A/C COMPRESSOR CLUTCH/
COIL
DESCRIPTION
The compressor clutch assembly consists of a sta-
tionary electromagnetic coil, a pulley bearing and
pulley assembly, and a clutch plate (Fig. 1). The elec-
tromagnetic coil and the pulley bearing and pulley
assembly are each retained on the nose of the com-
pressor front housing with snap rings. The clutch
plate is keyed to the compressor shaft and secured
with a nut. These components provide the means toengage and disengage the compressor from the
engine serpentine accessory drive belt.
OPERATION
The A/C compressor clutch provides the means to
engage and disengage the A/C compressor from the
engine serpentine accessory drive belt. When the
clutch coil is energized, it magnetically draws the
clutch into contact with the pulley and drives the
compressor shaft. When the coil is not energized, the
pulley freewheels on the pulley bearing, which is
part of the pulley assembly. The compressor clutch
DRCONTROLS 24 - 9
Page 2497 of 2627
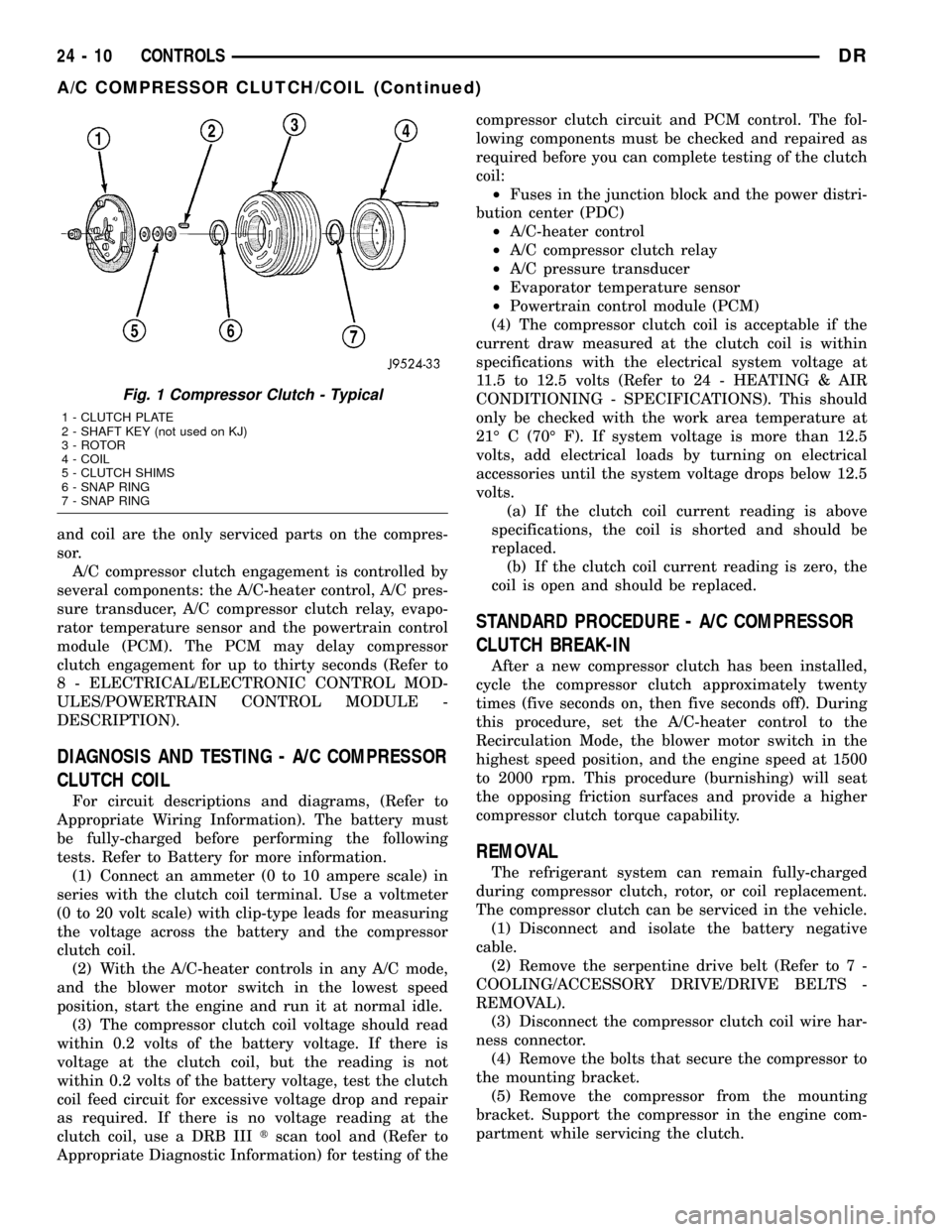
and coil are the only serviced parts on the compres-
sor.
A/C compressor clutch engagement is controlled by
several components: the A/C-heater control, A/C pres-
sure transducer, A/C compressor clutch relay, evapo-
rator temperature sensor and the powertrain control
module (PCM). The PCM may delay compressor
clutch engagement for up to thirty seconds (Refer to
8 - ELECTRICAL/ELECTRONIC CONTROL MOD-
ULES/POWERTRAIN CONTROL MODULE -
DESCRIPTION).
DIAGNOSIS AND TESTING - A/C COMPRESSOR
CLUTCH COIL
For circuit descriptions and diagrams, (Refer to
Appropriate Wiring Information). The battery must
be fully-charged before performing the following
tests. Refer to Battery for more information.
(1) Connect an ammeter (0 to 10 ampere scale) in
series with the clutch coil terminal. Use a voltmeter
(0 to 20 volt scale) with clip-type leads for measuring
the voltage across the battery and the compressor
clutch coil.
(2) With the A/C-heater controls in any A/C mode,
and the blower motor switch in the lowest speed
position, start the engine and run it at normal idle.
(3) The compressor clutch coil voltage should read
within 0.2 volts of the battery voltage. If there is
voltage at the clutch coil, but the reading is not
within 0.2 volts of the battery voltage, test the clutch
coil feed circuit for excessive voltage drop and repair
as required. If there is no voltage reading at the
clutch coil, use a DRB IIItscan tool and (Refer to
Appropriate Diagnostic Information) for testing of thecompressor clutch circuit and PCM control. The fol-
lowing components must be checked and repaired as
required before you can complete testing of the clutch
coil:
²Fuses in the junction block and the power distri-
bution center (PDC)
²A/C-heater control
²A/C compressor clutch relay
²A/C pressure transducer
²Evaporator temperature sensor
²Powertrain control module (PCM)
(4) The compressor clutch coil is acceptable if the
current draw measured at the clutch coil is within
specifications with the electrical system voltage at
11.5 to 12.5 volts (Refer to 24 - HEATING & AIR
CONDITIONING - SPECIFICATIONS). This should
only be checked with the work area temperature at
21É C (70É F). If system voltage is more than 12.5
volts, add electrical loads by turning on electrical
accessories until the system voltage drops below 12.5
volts.
(a) If the clutch coil current reading is above
specifications, the coil is shorted and should be
replaced.
(b) If the clutch coil current reading is zero, the
coil is open and should be replaced.
STANDARD PROCEDURE - A/C COMPRESSOR
CLUTCH BREAK-IN
After a new compressor clutch has been installed,
cycle the compressor clutch approximately twenty
times (five seconds on, then five seconds off). During
this procedure, set the A/C-heater control to the
Recirculation Mode, the blower motor switch in the
highest speed position, and the engine speed at 1500
to 2000 rpm. This procedure (burnishing) will seat
the opposing friction surfaces and provide a higher
compressor clutch torque capability.
REMOVAL
The refrigerant system can remain fully-charged
during compressor clutch, rotor, or coil replacement.
The compressor clutch can be serviced in the vehicle.
(1) Disconnect and isolate the battery negative
cable.
(2) Remove the serpentine drive belt (Refer to 7 -
COOLING/ACCESSORY DRIVE/DRIVE BELTS -
REMOVAL).
(3) Disconnect the compressor clutch coil wire har-
ness connector.
(4) Remove the bolts that secure the compressor to
the mounting bracket.
(5) Remove the compressor from the mounting
bracket. Support the compressor in the engine com-
partment while servicing the clutch.
Fig. 1 Compressor Clutch - Typical
1 - CLUTCH PLATE
2 - SHAFT KEY (not used on KJ)
3 - ROTOR
4 - COIL
5 - CLUTCH SHIMS
6 - SNAP RING
7 - SNAP RING
24 - 10 CONTROLSDR
A/C COMPRESSOR CLUTCH/COIL (Continued)
Page 2562 of 2627
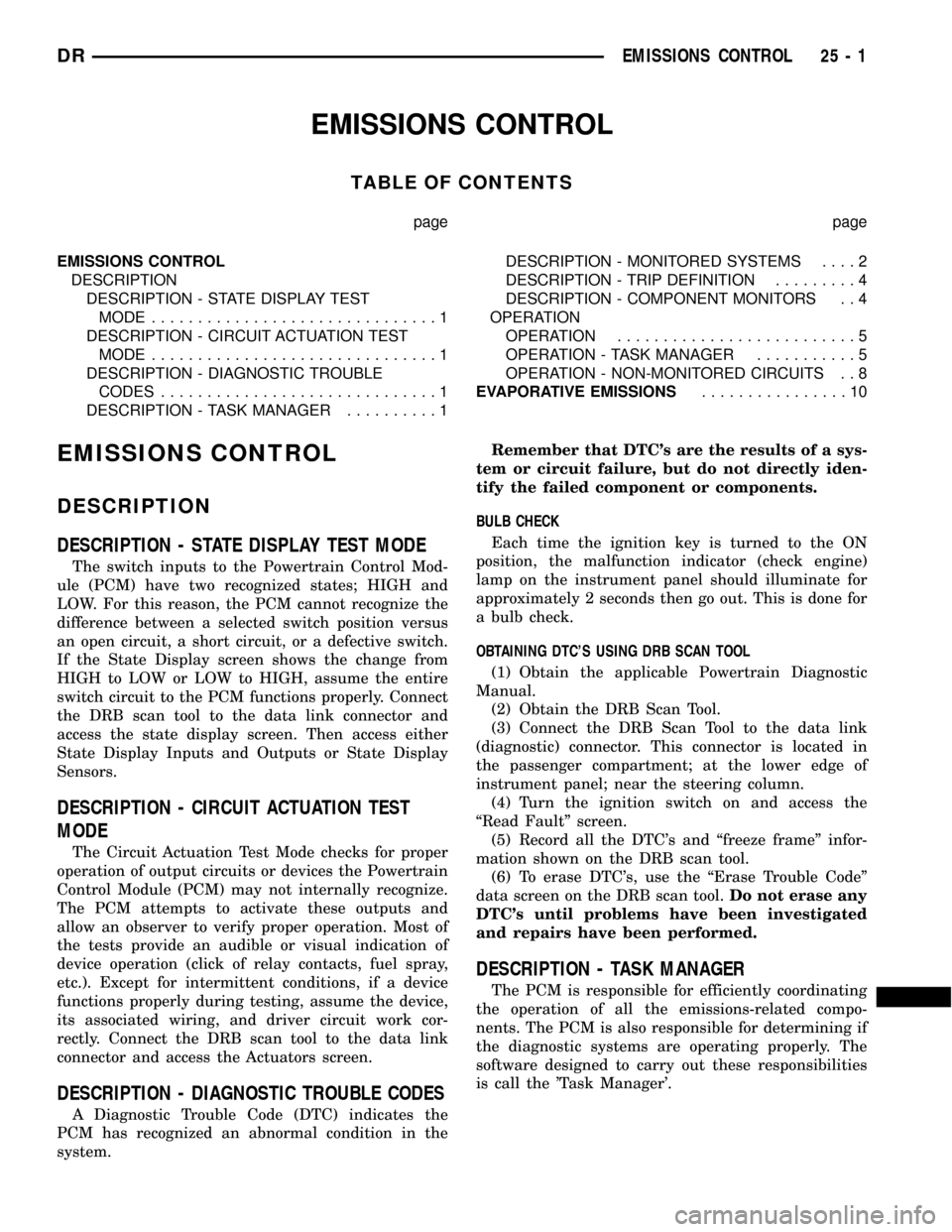
EMISSIONS CONTROL
TABLE OF CONTENTS
page page
EMISSIONS CONTROL
DESCRIPTION
DESCRIPTION - STATE DISPLAY TEST
MODE...............................1
DESCRIPTION - CIRCUIT ACTUATION TEST
MODE...............................1
DESCRIPTION - DIAGNOSTIC TROUBLE
CODES..............................1
DESCRIPTION - TASK MANAGER..........1DESCRIPTION - MONITORED SYSTEMS....2
DESCRIPTION - TRIP DEFINITION.........4
DESCRIPTION - COMPONENT MONITORS . . 4
OPERATION
OPERATION..........................5
OPERATION - TASK MANAGER...........5
OPERATION - NON-MONITORED CIRCUITS . . 8
EVAPORATIVE EMISSIONS................10
EMISSIONS CONTROL
DESCRIPTION
DESCRIPTION - STATE DISPLAY TEST MODE
The switch inputs to the Powertrain Control Mod-
ule (PCM) have two recognized states; HIGH and
LOW. For this reason, the PCM cannot recognize the
difference between a selected switch position versus
an open circuit, a short circuit, or a defective switch.
If the State Display screen shows the change from
HIGH to LOW or LOW to HIGH, assume the entire
switch circuit to the PCM functions properly. Connect
the DRB scan tool to the data link connector and
access the state display screen. Then access either
State Display Inputs and Outputs or State Display
Sensors.
DESCRIPTION - CIRCUIT ACTUATION TEST
MODE
The Circuit Actuation Test Mode checks for proper
operation of output circuits or devices the Powertrain
Control Module (PCM) may not internally recognize.
The PCM attempts to activate these outputs and
allow an observer to verify proper operation. Most of
the tests provide an audible or visual indication of
device operation (click of relay contacts, fuel spray,
etc.). Except for intermittent conditions, if a device
functions properly during testing, assume the device,
its associated wiring, and driver circuit work cor-
rectly. Connect the DRB scan tool to the data link
connector and access the Actuators screen.
DESCRIPTION - DIAGNOSTIC TROUBLE CODES
A Diagnostic Trouble Code (DTC) indicates the
PCM has recognized an abnormal condition in the
system.Remember that DTC's are the results of a sys-
tem or circuit failure, but do not directly iden-
tify the failed component or components.
BULB CHECK
Each time the ignition key is turned to the ON
position, the malfunction indicator (check engine)
lamp on the instrument panel should illuminate for
approximately 2 seconds then go out. This is done for
a bulb check.
OBTAINING DTC'S USING DRB SCAN TOOL
(1) Obtain the applicable Powertrain Diagnostic
Manual.
(2) Obtain the DRB Scan Tool.
(3) Connect the DRB Scan Tool to the data link
(diagnostic) connector. This connector is located in
the passenger compartment; at the lower edge of
instrument panel; near the steering column.
(4) Turn the ignition switch on and access the
ªRead Faultº screen.
(5) Record all the DTC's and ªfreeze frameº infor-
mation shown on the DRB scan tool.
(6) To erase DTC's, use the ªErase Trouble Codeº
data screen on the DRB scan tool.Do not erase any
DTC's until problems have been investigated
and repairs have been performed.
DESCRIPTION - TASK MANAGER
The PCM is responsible for efficiently coordinating
the operation of all the emissions-related compo-
nents. The PCM is also responsible for determining if
the diagnostic systems are operating properly. The
software designed to carry out these responsibilities
is call the 'Task Manager'.
DREMISSIONS CONTROL 25 - 1
Page 2567 of 2627
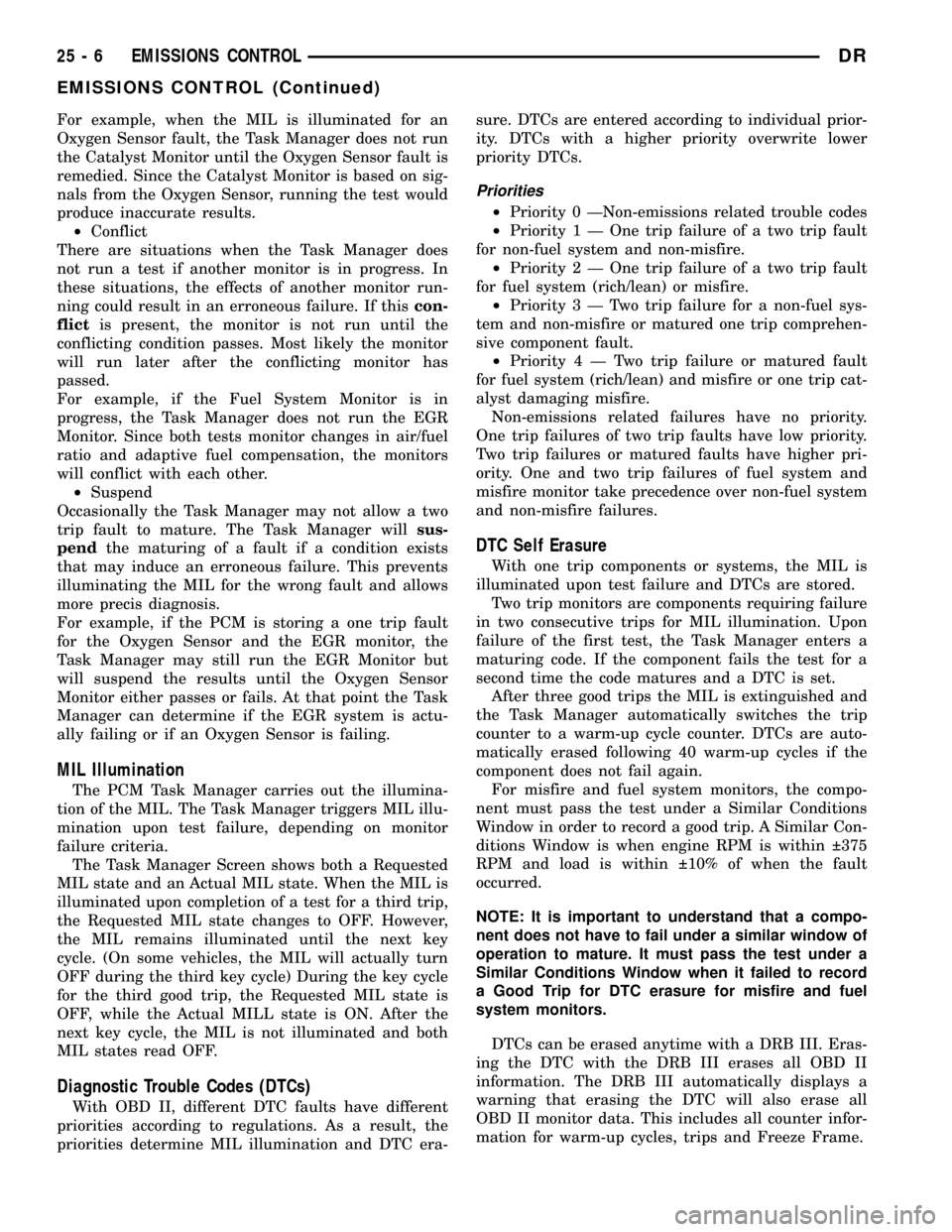
For example, when the MIL is illuminated for an
Oxygen Sensor fault, the Task Manager does not run
the Catalyst Monitor until the Oxygen Sensor fault is
remedied. Since the Catalyst Monitor is based on sig-
nals from the Oxygen Sensor, running the test would
produce inaccurate results.
²Conflict
There are situations when the Task Manager does
not run a test if another monitor is in progress. In
these situations, the effects of another monitor run-
ning could result in an erroneous failure. If thiscon-
flictis present, the monitor is not run until the
conflicting condition passes. Most likely the monitor
will run later after the conflicting monitor has
passed.
For example, if the Fuel System Monitor is in
progress, the Task Manager does not run the EGR
Monitor. Since both tests monitor changes in air/fuel
ratio and adaptive fuel compensation, the monitors
will conflict with each other.
²Suspend
Occasionally the Task Manager may not allow a two
trip fault to mature. The Task Manager willsus-
pendthe maturing of a fault if a condition exists
that may induce an erroneous failure. This prevents
illuminating the MIL for the wrong fault and allows
more precis diagnosis.
For example, if the PCM is storing a one trip fault
for the Oxygen Sensor and the EGR monitor, the
Task Manager may still run the EGR Monitor but
will suspend the results until the Oxygen Sensor
Monitor either passes or fails. At that point the Task
Manager can determine if the EGR system is actu-
ally failing or if an Oxygen Sensor is failing.
MIL Illumination
The PCM Task Manager carries out the illumina-
tion of the MIL. The Task Manager triggers MIL illu-
mination upon test failure, depending on monitor
failure criteria.
The Task Manager Screen shows both a Requested
MIL state and an Actual MIL state. When the MIL is
illuminated upon completion of a test for a third trip,
the Requested MIL state changes to OFF. However,
the MIL remains illuminated until the next key
cycle. (On some vehicles, the MIL will actually turn
OFF during the third key cycle) During the key cycle
for the third good trip, the Requested MIL state is
OFF, while the Actual MILL state is ON. After the
next key cycle, the MIL is not illuminated and both
MIL states read OFF.
Diagnostic Trouble Codes (DTCs)
With OBD II, different DTC faults have different
priorities according to regulations. As a result, the
priorities determine MIL illumination and DTC era-sure. DTCs are entered according to individual prior-
ity. DTCs with a higher priority overwrite lower
priority DTCs.
Priorities
²Priority 0 ÐNon-emissions related trouble codes
²Priority 1 Ð One trip failure of a two trip fault
for non-fuel system and non-misfire.
²Priority 2 Ð One trip failure of a two trip fault
for fuel system (rich/lean) or misfire.
²Priority3ÐTwotrip failure for a non-fuel sys-
tem and non-misfire or matured one trip comprehen-
sive component fault.
²Priority4ÐTwotrip failure or matured fault
for fuel system (rich/lean) and misfire or one trip cat-
alyst damaging misfire.
Non-emissions related failures have no priority.
One trip failures of two trip faults have low priority.
Two trip failures or matured faults have higher pri-
ority. One and two trip failures of fuel system and
misfire monitor take precedence over non-fuel system
and non-misfire failures.
DTC Self Erasure
With one trip components or systems, the MIL is
illuminated upon test failure and DTCs are stored.
Two trip monitors are components requiring failure
in two consecutive trips for MIL illumination. Upon
failure of the first test, the Task Manager enters a
maturing code. If the component fails the test for a
second time the code matures and a DTC is set.
After three good trips the MIL is extinguished and
the Task Manager automatically switches the trip
counter to a warm-up cycle counter. DTCs are auto-
matically erased following 40 warm-up cycles if the
component does not fail again.
For misfire and fuel system monitors, the compo-
nent must pass the test under a Similar Conditions
Window in order to record a good trip. A Similar Con-
ditions Window is when engine RPM is within 375
RPM and load is within 10% of when the fault
occurred.
NOTE: It is important to understand that a compo-
nent does not have to fail under a similar window of
operation to mature. It must pass the test under a
Similar Conditions Window when it failed to record
a Good Trip for DTC erasure for misfire and fuel
system monitors.
DTCs can be erased anytime with a DRB III. Eras-
ing the DTC with the DRB III erases all OBD II
information. The DRB III automatically displays a
warning that erasing the DTC will also erase all
OBD II monitor data. This includes all counter infor-
mation for warm-up cycles, trips and Freeze Frame.
25 - 6 EMISSIONS CONTROLDR
EMISSIONS CONTROL (Continued)