check gauges DODGE RAM 1500 1998 2.G User Guide
[x] Cancel search | Manufacturer: DODGE, Model Year: 1998, Model line: RAM 1500, Model: DODGE RAM 1500 1998 2.GPages: 2627
Page 530 of 2627
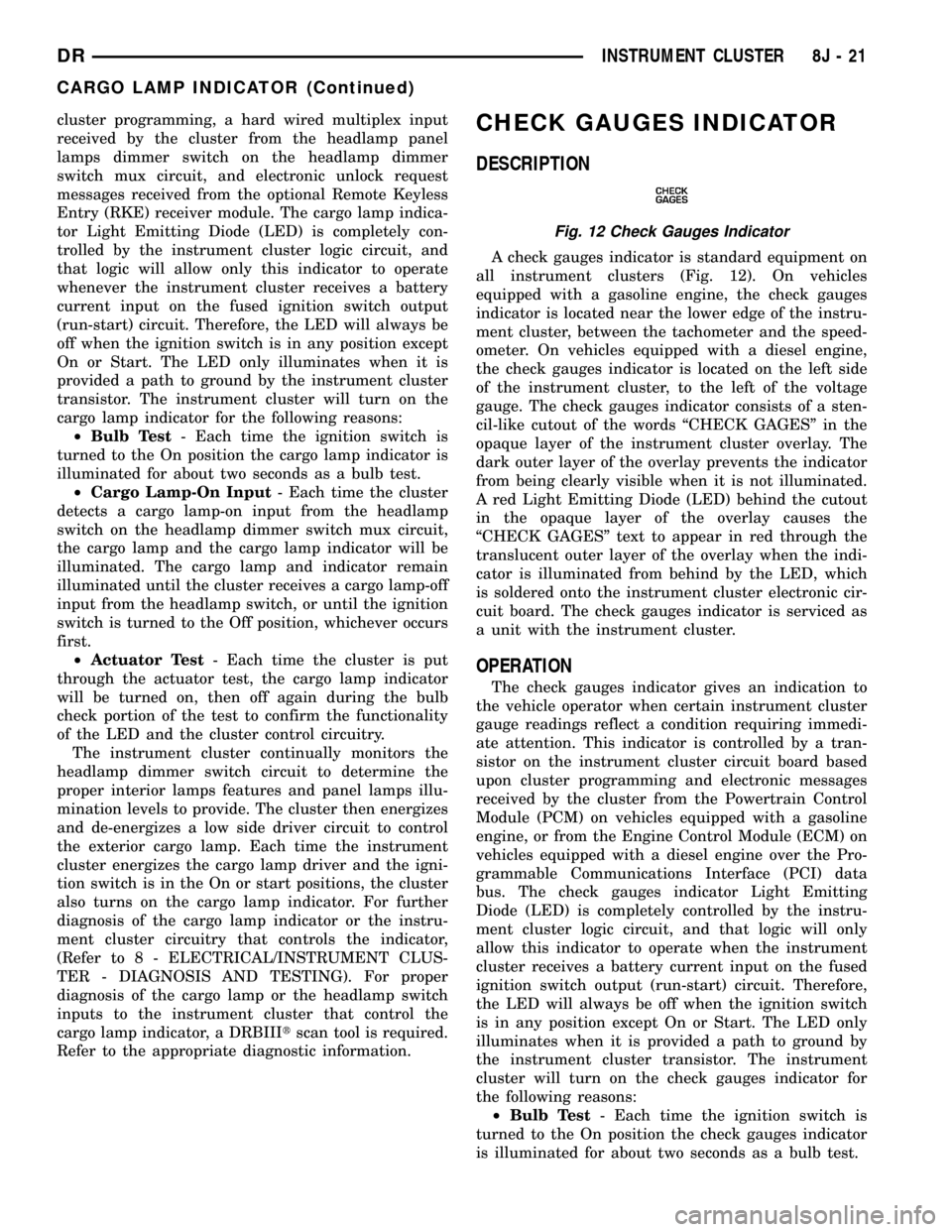
cluster programming, a hard wired multiplex input
received by the cluster from the headlamp panel
lamps dimmer switch on the headlamp dimmer
switch mux circuit, and electronic unlock request
messages received from the optional Remote Keyless
Entry (RKE) receiver module. The cargo lamp indica-
tor Light Emitting Diode (LED) is completely con-
trolled by the instrument cluster logic circuit, and
that logic will allow only this indicator to operate
whenever the instrument cluster receives a battery
current input on the fused ignition switch output
(run-start) circuit. Therefore, the LED will always be
off when the ignition switch is in any position except
On or Start. The LED only illuminates when it is
provided a path to ground by the instrument cluster
transistor. The instrument cluster will turn on the
cargo lamp indicator for the following reasons:
²Bulb Test- Each time the ignition switch is
turned to the On position the cargo lamp indicator is
illuminated for about two seconds as a bulb test.
²Cargo Lamp-On Input- Each time the cluster
detects a cargo lamp-on input from the headlamp
switch on the headlamp dimmer switch mux circuit,
the cargo lamp and the cargo lamp indicator will be
illuminated. The cargo lamp and indicator remain
illuminated until the cluster receives a cargo lamp-off
input from the headlamp switch, or until the ignition
switch is turned to the Off position, whichever occurs
first.
²Actuator Test- Each time the cluster is put
through the actuator test, the cargo lamp indicator
will be turned on, then off again during the bulb
check portion of the test to confirm the functionality
of the LED and the cluster control circuitry.
The instrument cluster continually monitors the
headlamp dimmer switch circuit to determine the
proper interior lamps features and panel lamps illu-
mination levels to provide. The cluster then energizes
and de-energizes a low side driver circuit to control
the exterior cargo lamp. Each time the instrument
cluster energizes the cargo lamp driver and the igni-
tion switch is in the On or start positions, the cluster
also turns on the cargo lamp indicator. For further
diagnosis of the cargo lamp indicator or the instru-
ment cluster circuitry that controls the indicator,
(Refer to 8 - ELECTRICAL/INSTRUMENT CLUS-
TER - DIAGNOSIS AND TESTING). For proper
diagnosis of the cargo lamp or the headlamp switch
inputs to the instrument cluster that control the
cargo lamp indicator, a DRBIIItscan tool is required.
Refer to the appropriate diagnostic information.CHECK GAUGES INDICATOR
DESCRIPTION
A check gauges indicator is standard equipment on
all instrument clusters (Fig. 12). On vehicles
equipped with a gasoline engine, the check gauges
indicator is located near the lower edge of the instru-
ment cluster, between the tachometer and the speed-
ometer. On vehicles equipped with a diesel engine,
the check gauges indicator is located on the left side
of the instrument cluster, to the left of the voltage
gauge. The check gauges indicator consists of a sten-
cil-like cutout of the words ªCHECK GAGESº in the
opaque layer of the instrument cluster overlay. The
dark outer layer of the overlay prevents the indicator
from being clearly visible when it is not illuminated.
A red Light Emitting Diode (LED) behind the cutout
in the opaque layer of the overlay causes the
ªCHECK GAGESº text to appear in red through the
translucent outer layer of the overlay when the indi-
cator is illuminated from behind by the LED, which
is soldered onto the instrument cluster electronic cir-
cuit board. The check gauges indicator is serviced as
a unit with the instrument cluster.
OPERATION
The check gauges indicator gives an indication to
the vehicle operator when certain instrument cluster
gauge readings reflect a condition requiring immedi-
ate attention. This indicator is controlled by a tran-
sistor on the instrument cluster circuit board based
upon cluster programming and electronic messages
received by the cluster from the Powertrain Control
Module (PCM) on vehicles equipped with a gasoline
engine, or from the Engine Control Module (ECM) on
vehicles equipped with a diesel engine over the Pro-
grammable Communications Interface (PCI) data
bus. The check gauges indicator Light Emitting
Diode (LED) is completely controlled by the instru-
ment cluster logic circuit, and that logic will only
allow this indicator to operate when the instrument
cluster receives a battery current input on the fused
ignition switch output (run-start) circuit. Therefore,
the LED will always be off when the ignition switch
is in any position except On or Start. The LED only
illuminates when it is provided a path to ground by
the instrument cluster transistor. The instrument
cluster will turn on the check gauges indicator for
the following reasons:
²Bulb Test- Each time the ignition switch is
turned to the On position the check gauges indicator
is illuminated for about two seconds as a bulb test.
Fig. 12 Check Gauges Indicator
DRINSTRUMENT CLUSTER 8J - 21
CARGO LAMP INDICATOR (Continued)
Page 531 of 2627
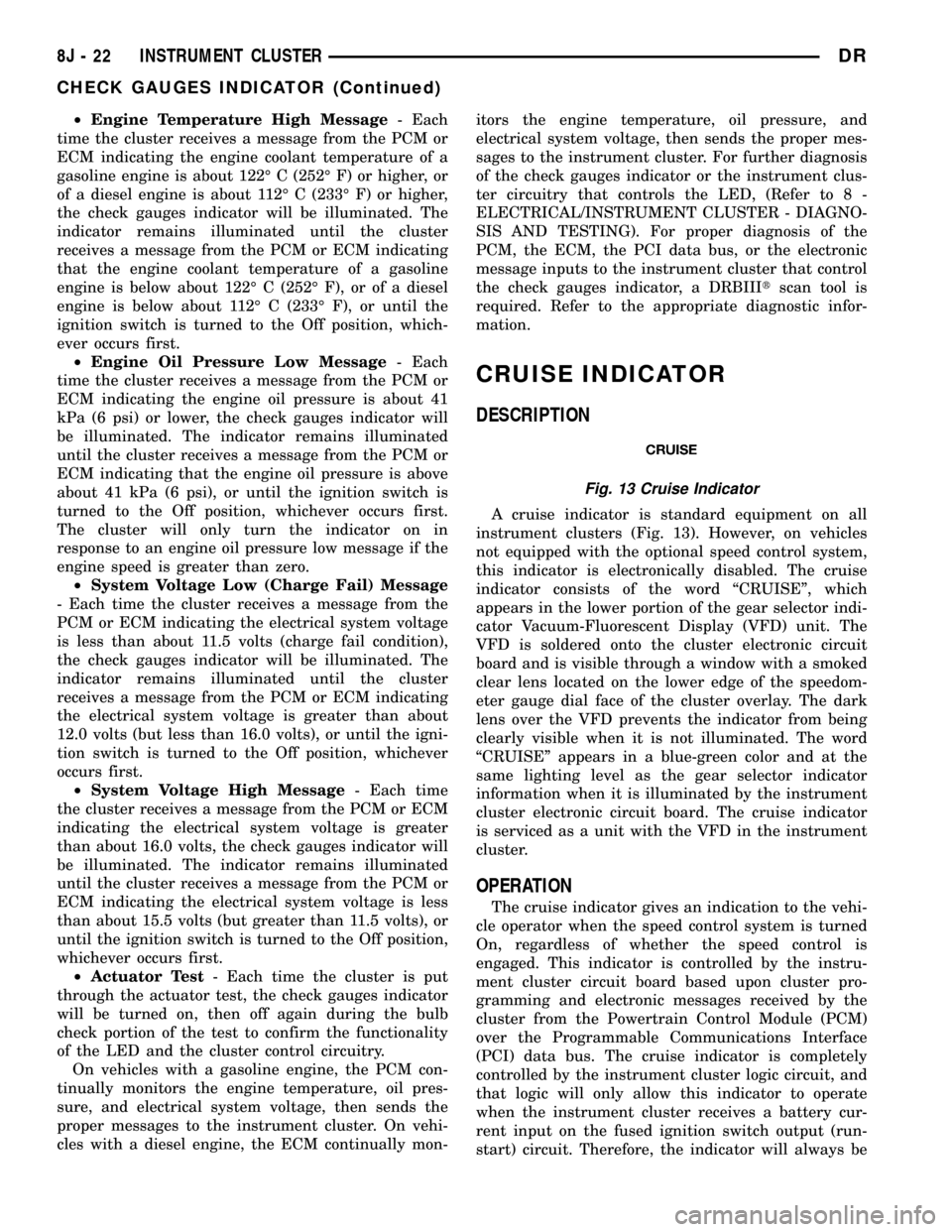
²Engine Temperature High Message- Each
time the cluster receives a message from the PCM or
ECM indicating the engine coolant temperature of a
gasoline engine is about 122É C (252É F) or higher, or
of a diesel engine is about 112É C (233É F) or higher,
the check gauges indicator will be illuminated. The
indicator remains illuminated until the cluster
receives a message from the PCM or ECM indicating
that the engine coolant temperature of a gasoline
engine is below about 122É C (252É F), or of a diesel
engine is below about 112É C (233É F), or until the
ignition switch is turned to the Off position, which-
ever occurs first.
²Engine Oil Pressure Low Message- Each
time the cluster receives a message from the PCM or
ECM indicating the engine oil pressure is about 41
kPa (6 psi) or lower, the check gauges indicator will
be illuminated. The indicator remains illuminated
until the cluster receives a message from the PCM or
ECM indicating that the engine oil pressure is above
about 41 kPa (6 psi), or until the ignition switch is
turned to the Off position, whichever occurs first.
The cluster will only turn the indicator on in
response to an engine oil pressure low message if the
engine speed is greater than zero.
²System Voltage Low (Charge Fail) Message
- Each time the cluster receives a message from the
PCM or ECM indicating the electrical system voltage
is less than about 11.5 volts (charge fail condition),
the check gauges indicator will be illuminated. The
indicator remains illuminated until the cluster
receives a message from the PCM or ECM indicating
the electrical system voltage is greater than about
12.0 volts (but less than 16.0 volts), or until the igni-
tion switch is turned to the Off position, whichever
occurs first.
²System Voltage High Message- Each time
the cluster receives a message from the PCM or ECM
indicating the electrical system voltage is greater
than about 16.0 volts, the check gauges indicator will
be illuminated. The indicator remains illuminated
until the cluster receives a message from the PCM or
ECM indicating the electrical system voltage is less
than about 15.5 volts (but greater than 11.5 volts), or
until the ignition switch is turned to the Off position,
whichever occurs first.
²Actuator Test- Each time the cluster is put
through the actuator test, the check gauges indicator
will be turned on, then off again during the bulb
check portion of the test to confirm the functionality
of the LED and the cluster control circuitry.
On vehicles with a gasoline engine, the PCM con-
tinually monitors the engine temperature, oil pres-
sure, and electrical system voltage, then sends the
proper messages to the instrument cluster. On vehi-
cles with a diesel engine, the ECM continually mon-itors the engine temperature, oil pressure, and
electrical system voltage, then sends the proper mes-
sages to the instrument cluster. For further diagnosis
of the check gauges indicator or the instrument clus-
ter circuitry that controls the LED, (Refer to 8 -
ELECTRICAL/INSTRUMENT CLUSTER - DIAGNO-
SIS AND TESTING). For proper diagnosis of the
PCM, the ECM, the PCI data bus, or the electronic
message inputs to the instrument cluster that control
the check gauges indicator, a DRBIIItscan tool is
required. Refer to the appropriate diagnostic infor-
mation.
CRUISE INDICATOR
DESCRIPTION
A cruise indicator is standard equipment on all
instrument clusters (Fig. 13). However, on vehicles
not equipped with the optional speed control system,
this indicator is electronically disabled. The cruise
indicator consists of the word ªCRUISEº, which
appears in the lower portion of the gear selector indi-
cator Vacuum-Fluorescent Display (VFD) unit. The
VFD is soldered onto the cluster electronic circuit
board and is visible through a window with a smoked
clear lens located on the lower edge of the speedom-
eter gauge dial face of the cluster overlay. The dark
lens over the VFD prevents the indicator from being
clearly visible when it is not illuminated. The word
ªCRUISEº appears in a blue-green color and at the
same lighting level as the gear selector indicator
information when it is illuminated by the instrument
cluster electronic circuit board. The cruise indicator
is serviced as a unit with the VFD in the instrument
cluster.
OPERATION
The cruise indicator gives an indication to the vehi-
cle operator when the speed control system is turned
On, regardless of whether the speed control is
engaged. This indicator is controlled by the instru-
ment cluster circuit board based upon cluster pro-
gramming and electronic messages received by the
cluster from the Powertrain Control Module (PCM)
over the Programmable Communications Interface
(PCI) data bus. The cruise indicator is completely
controlled by the instrument cluster logic circuit, and
that logic will only allow this indicator to operate
when the instrument cluster receives a battery cur-
rent input on the fused ignition switch output (run-
start) circuit. Therefore, the indicator will always be
Fig. 13 Cruise Indicator
8J - 22 INSTRUMENT CLUSTERDR
CHECK GAUGES INDICATOR (Continued)
Page 533 of 2627
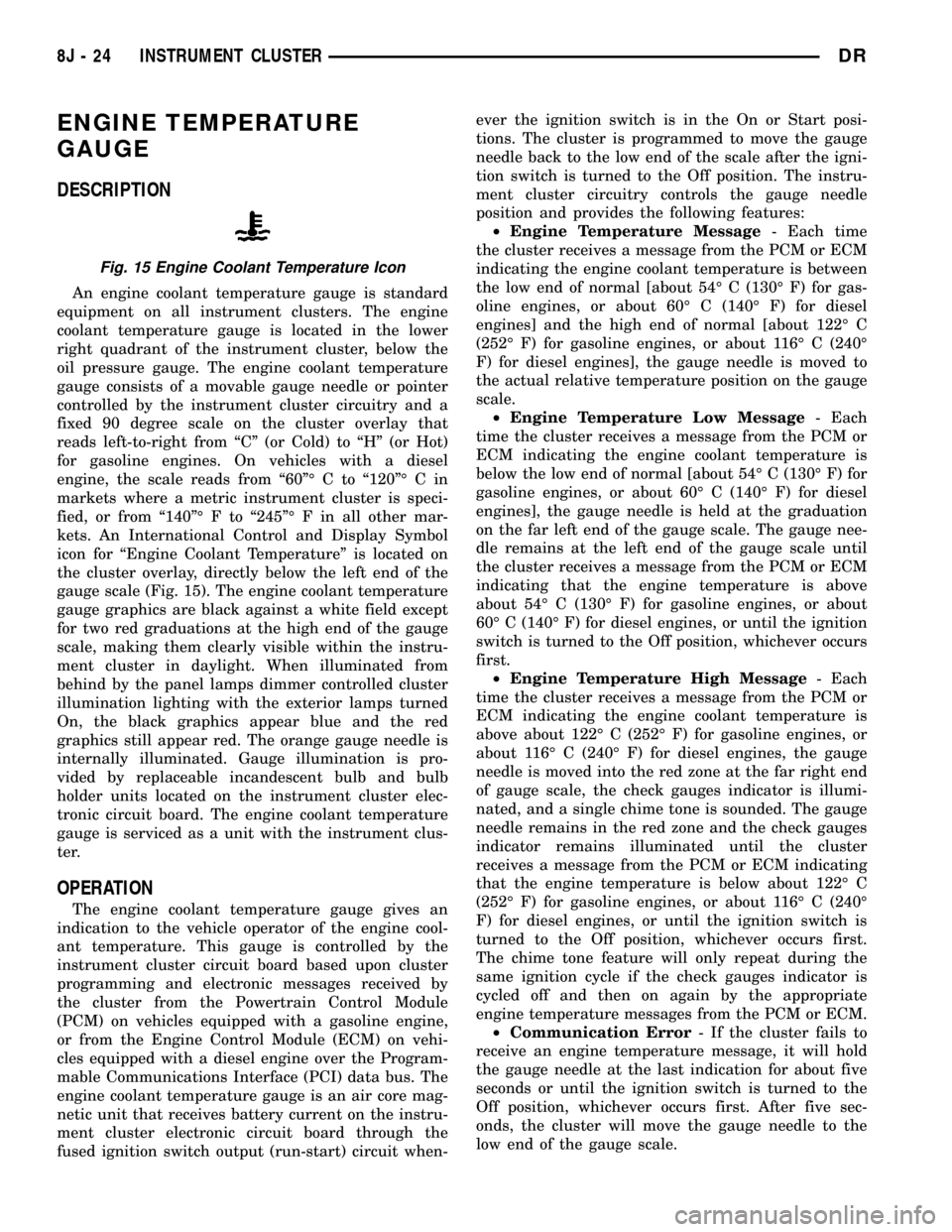
ENGINE TEMPERATURE
GAUGE
DESCRIPTION
An engine coolant temperature gauge is standard
equipment on all instrument clusters. The engine
coolant temperature gauge is located in the lower
right quadrant of the instrument cluster, below the
oil pressure gauge. The engine coolant temperature
gauge consists of a movable gauge needle or pointer
controlled by the instrument cluster circuitry and a
fixed 90 degree scale on the cluster overlay that
reads left-to-right from ªCº (or Cold) to ªHº (or Hot)
for gasoline engines. On vehicles with a diesel
engine, the scale reads from ª60ºÉ C to ª120ºÉ C in
markets where a metric instrument cluster is speci-
fied, or from ª140ºÉ F to ª245ºÉ F in all other mar-
kets. An International Control and Display Symbol
icon for ªEngine Coolant Temperatureº is located on
the cluster overlay, directly below the left end of the
gauge scale (Fig. 15). The engine coolant temperature
gauge graphics are black against a white field except
for two red graduations at the high end of the gauge
scale, making them clearly visible within the instru-
ment cluster in daylight. When illuminated from
behind by the panel lamps dimmer controlled cluster
illumination lighting with the exterior lamps turned
On, the black graphics appear blue and the red
graphics still appear red. The orange gauge needle is
internally illuminated. Gauge illumination is pro-
vided by replaceable incandescent bulb and bulb
holder units located on the instrument cluster elec-
tronic circuit board. The engine coolant temperature
gauge is serviced as a unit with the instrument clus-
ter.
OPERATION
The engine coolant temperature gauge gives an
indication to the vehicle operator of the engine cool-
ant temperature. This gauge is controlled by the
instrument cluster circuit board based upon cluster
programming and electronic messages received by
the cluster from the Powertrain Control Module
(PCM) on vehicles equipped with a gasoline engine,
or from the Engine Control Module (ECM) on vehi-
cles equipped with a diesel engine over the Program-
mable Communications Interface (PCI) data bus. The
engine coolant temperature gauge is an air core mag-
netic unit that receives battery current on the instru-
ment cluster electronic circuit board through the
fused ignition switch output (run-start) circuit when-ever the ignition switch is in the On or Start posi-
tions. The cluster is programmed to move the gauge
needle back to the low end of the scale after the igni-
tion switch is turned to the Off position. The instru-
ment cluster circuitry controls the gauge needle
position and provides the following features:
²Engine Temperature Message- Each time
the cluster receives a message from the PCM or ECM
indicating the engine coolant temperature is between
the low end of normal [about 54É C (130É F) for gas-
oline engines, or about 60É C (140É F) for diesel
engines] and the high end of normal [about 122É C
(252É F) for gasoline engines, or about 116É C (240É
F) for diesel engines], the gauge needle is moved to
the actual relative temperature position on the gauge
scale.
²Engine Temperature Low Message- Each
time the cluster receives a message from the PCM or
ECM indicating the engine coolant temperature is
below the low end of normal [about 54É C (130É F) for
gasoline engines, or about 60É C (140É F) for diesel
engines], the gauge needle is held at the graduation
on the far left end of the gauge scale. The gauge nee-
dle remains at the left end of the gauge scale until
the cluster receives a message from the PCM or ECM
indicating that the engine temperature is above
about 54É C (130É F) for gasoline engines, or about
60É C (140É F) for diesel engines, or until the ignition
switch is turned to the Off position, whichever occurs
first.
²Engine Temperature High Message- Each
time the cluster receives a message from the PCM or
ECM indicating the engine coolant temperature is
above about 122É C (252É F) for gasoline engines, or
about 116É C (240É F) for diesel engines, the gauge
needle is moved into the red zone at the far right end
of gauge scale, the check gauges indicator is illumi-
nated, and a single chime tone is sounded. The gauge
needle remains in the red zone and the check gauges
indicator remains illuminated until the cluster
receives a message from the PCM or ECM indicating
that the engine temperature is below about 122É C
(252É F) for gasoline engines, or about 116É C (240É
F) for diesel engines, or until the ignition switch is
turned to the Off position, whichever occurs first.
The chime tone feature will only repeat during the
same ignition cycle if the check gauges indicator is
cycled off and then on again by the appropriate
engine temperature messages from the PCM or ECM.
²Communication Error- If the cluster fails to
receive an engine temperature message, it will hold
the gauge needle at the last indication for about five
seconds or until the ignition switch is turned to the
Off position, whichever occurs first. After five sec-
onds, the cluster will move the gauge needle to the
low end of the gauge scale.
Fig. 15 Engine Coolant Temperature Icon
8J - 24 INSTRUMENT CLUSTERDR
Page 534 of 2627
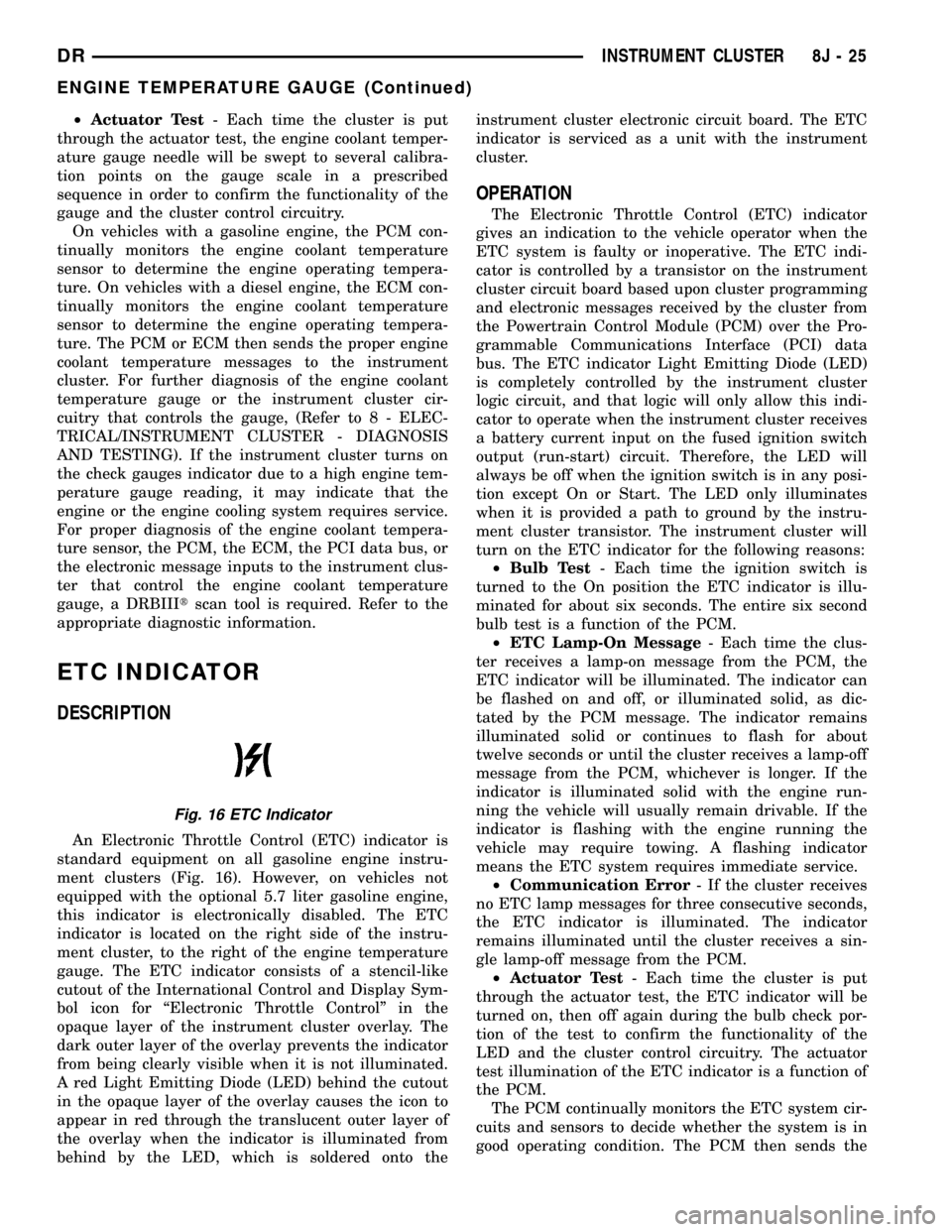
²Actuator Test- Each time the cluster is put
through the actuator test, the engine coolant temper-
ature gauge needle will be swept to several calibra-
tion points on the gauge scale in a prescribed
sequence in order to confirm the functionality of the
gauge and the cluster control circuitry.
On vehicles with a gasoline engine, the PCM con-
tinually monitors the engine coolant temperature
sensor to determine the engine operating tempera-
ture. On vehicles with a diesel engine, the ECM con-
tinually monitors the engine coolant temperature
sensor to determine the engine operating tempera-
ture. The PCM or ECM then sends the proper engine
coolant temperature messages to the instrument
cluster. For further diagnosis of the engine coolant
temperature gauge or the instrument cluster cir-
cuitry that controls the gauge, (Refer to 8 - ELEC-
TRICAL/INSTRUMENT CLUSTER - DIAGNOSIS
AND TESTING). If the instrument cluster turns on
the check gauges indicator due to a high engine tem-
perature gauge reading, it may indicate that the
engine or the engine cooling system requires service.
For proper diagnosis of the engine coolant tempera-
ture sensor, the PCM, the ECM, the PCI data bus, or
the electronic message inputs to the instrument clus-
ter that control the engine coolant temperature
gauge, a DRBIIItscan tool is required. Refer to the
appropriate diagnostic information.
ETC INDICATOR
DESCRIPTION
An Electronic Throttle Control (ETC) indicator is
standard equipment on all gasoline engine instru-
ment clusters (Fig. 16). However, on vehicles not
equipped with the optional 5.7 liter gasoline engine,
this indicator is electronically disabled. The ETC
indicator is located on the right side of the instru-
ment cluster, to the right of the engine temperature
gauge. The ETC indicator consists of a stencil-like
cutout of the International Control and Display Sym-
bol icon for ªElectronic Throttle Controlº in the
opaque layer of the instrument cluster overlay. The
dark outer layer of the overlay prevents the indicator
from being clearly visible when it is not illuminated.
A red Light Emitting Diode (LED) behind the cutout
in the opaque layer of the overlay causes the icon to
appear in red through the translucent outer layer of
the overlay when the indicator is illuminated from
behind by the LED, which is soldered onto theinstrument cluster electronic circuit board. The ETC
indicator is serviced as a unit with the instrument
cluster.
OPERATION
The Electronic Throttle Control (ETC) indicator
gives an indication to the vehicle operator when the
ETC system is faulty or inoperative. The ETC indi-
cator is controlled by a transistor on the instrument
cluster circuit board based upon cluster programming
and electronic messages received by the cluster from
the Powertrain Control Module (PCM) over the Pro-
grammable Communications Interface (PCI) data
bus. The ETC indicator Light Emitting Diode (LED)
is completely controlled by the instrument cluster
logic circuit, and that logic will only allow this indi-
cator to operate when the instrument cluster receives
a battery current input on the fused ignition switch
output (run-start) circuit. Therefore, the LED will
always be off when the ignition switch is in any posi-
tion except On or Start. The LED only illuminates
when it is provided a path to ground by the instru-
ment cluster transistor. The instrument cluster will
turn on the ETC indicator for the following reasons:
²Bulb Test- Each time the ignition switch is
turned to the On position the ETC indicator is illu-
minated for about six seconds. The entire six second
bulb test is a function of the PCM.
²ETC Lamp-On Message- Each time the clus-
ter receives a lamp-on message from the PCM, the
ETC indicator will be illuminated. The indicator can
be flashed on and off, or illuminated solid, as dic-
tated by the PCM message. The indicator remains
illuminated solid or continues to flash for about
twelve seconds or until the cluster receives a lamp-off
message from the PCM, whichever is longer. If the
indicator is illuminated solid with the engine run-
ning the vehicle will usually remain drivable. If the
indicator is flashing with the engine running the
vehicle may require towing. A flashing indicator
means the ETC system requires immediate service.
²Communication Error- If the cluster receives
no ETC lamp messages for three consecutive seconds,
the ETC indicator is illuminated. The indicator
remains illuminated until the cluster receives a sin-
gle lamp-off message from the PCM.
²Actuator Test- Each time the cluster is put
through the actuator test, the ETC indicator will be
turned on, then off again during the bulb check por-
tion of the test to confirm the functionality of the
LED and the cluster control circuitry. The actuator
test illumination of the ETC indicator is a function of
the PCM.
The PCM continually monitors the ETC system cir-
cuits and sensors to decide whether the system is in
good operating condition. The PCM then sends the
Fig. 16 ETC Indicator
DRINSTRUMENT CLUSTER 8J - 25
ENGINE TEMPERATURE GAUGE (Continued)
Page 543 of 2627
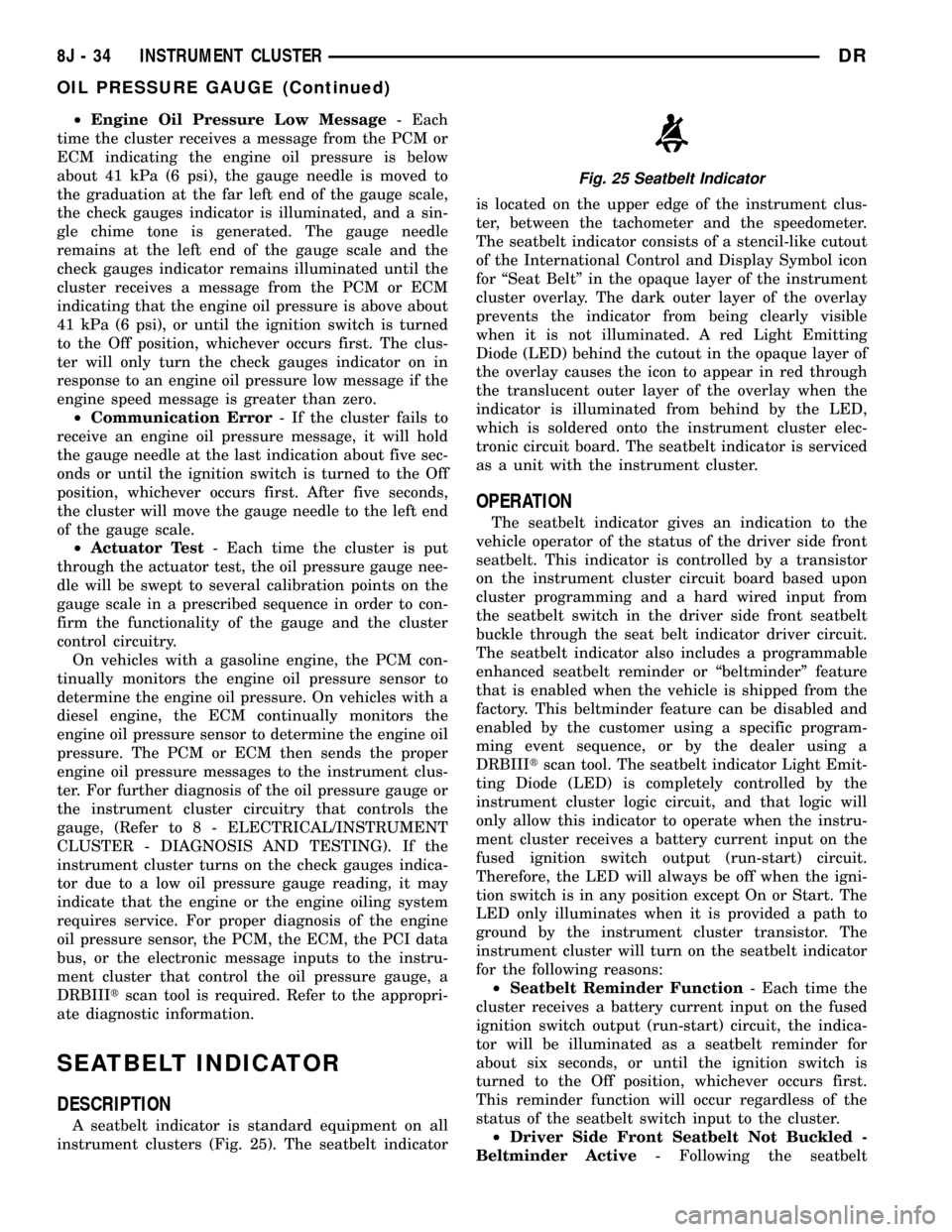
²Engine Oil Pressure Low Message- Each
time the cluster receives a message from the PCM or
ECM indicating the engine oil pressure is below
about 41 kPa (6 psi), the gauge needle is moved to
the graduation at the far left end of the gauge scale,
the check gauges indicator is illuminated, and a sin-
gle chime tone is generated. The gauge needle
remains at the left end of the gauge scale and the
check gauges indicator remains illuminated until the
cluster receives a message from the PCM or ECM
indicating that the engine oil pressure is above about
41 kPa (6 psi), or until the ignition switch is turned
to the Off position, whichever occurs first. The clus-
ter will only turn the check gauges indicator on in
response to an engine oil pressure low message if the
engine speed message is greater than zero.
²Communication Error- If the cluster fails to
receive an engine oil pressure message, it will hold
the gauge needle at the last indication about five sec-
onds or until the ignition switch is turned to the Off
position, whichever occurs first. After five seconds,
the cluster will move the gauge needle to the left end
of the gauge scale.
²Actuator Test- Each time the cluster is put
through the actuator test, the oil pressure gauge nee-
dle will be swept to several calibration points on the
gauge scale in a prescribed sequence in order to con-
firm the functionality of the gauge and the cluster
control circuitry.
On vehicles with a gasoline engine, the PCM con-
tinually monitors the engine oil pressure sensor to
determine the engine oil pressure. On vehicles with a
diesel engine, the ECM continually monitors the
engine oil pressure sensor to determine the engine oil
pressure. The PCM or ECM then sends the proper
engine oil pressure messages to the instrument clus-
ter. For further diagnosis of the oil pressure gauge or
the instrument cluster circuitry that controls the
gauge, (Refer to 8 - ELECTRICAL/INSTRUMENT
CLUSTER - DIAGNOSIS AND TESTING). If the
instrument cluster turns on the check gauges indica-
tor due to a low oil pressure gauge reading, it may
indicate that the engine or the engine oiling system
requires service. For proper diagnosis of the engine
oil pressure sensor, the PCM, the ECM, the PCI data
bus, or the electronic message inputs to the instru-
ment cluster that control the oil pressure gauge, a
DRBIIItscan tool is required. Refer to the appropri-
ate diagnostic information.
SEATBELT INDICATOR
DESCRIPTION
A seatbelt indicator is standard equipment on all
instrument clusters (Fig. 25). The seatbelt indicatoris located on the upper edge of the instrument clus-
ter, between the tachometer and the speedometer.
The seatbelt indicator consists of a stencil-like cutout
of the International Control and Display Symbol icon
for ªSeat Beltº in the opaque layer of the instrument
cluster overlay. The dark outer layer of the overlay
prevents the indicator from being clearly visible
when it is not illuminated. A red Light Emitting
Diode (LED) behind the cutout in the opaque layer of
the overlay causes the icon to appear in red through
the translucent outer layer of the overlay when the
indicator is illuminated from behind by the LED,
which is soldered onto the instrument cluster elec-
tronic circuit board. The seatbelt indicator is serviced
as a unit with the instrument cluster.
OPERATION
The seatbelt indicator gives an indication to the
vehicle operator of the status of the driver side front
seatbelt. This indicator is controlled by a transistor
on the instrument cluster circuit board based upon
cluster programming and a hard wired input from
the seatbelt switch in the driver side front seatbelt
buckle through the seat belt indicator driver circuit.
The seatbelt indicator also includes a programmable
enhanced seatbelt reminder or ªbeltminderº feature
that is enabled when the vehicle is shipped from the
factory. This beltminder feature can be disabled and
enabled by the customer using a specific program-
ming event sequence, or by the dealer using a
DRBIIItscan tool. The seatbelt indicator Light Emit-
ting Diode (LED) is completely controlled by the
instrument cluster logic circuit, and that logic will
only allow this indicator to operate when the instru-
ment cluster receives a battery current input on the
fused ignition switch output (run-start) circuit.
Therefore, the LED will always be off when the igni-
tion switch is in any position except On or Start. The
LED only illuminates when it is provided a path to
ground by the instrument cluster transistor. The
instrument cluster will turn on the seatbelt indicator
for the following reasons:
²Seatbelt Reminder Function- Each time the
cluster receives a battery current input on the fused
ignition switch output (run-start) circuit, the indica-
tor will be illuminated as a seatbelt reminder for
about six seconds, or until the ignition switch is
turned to the Off position, whichever occurs first.
This reminder function will occur regardless of the
status of the seatbelt switch input to the cluster.
²Driver Side Front Seatbelt Not Buckled -
Beltminder Active- Following the seatbelt
Fig. 25 Seatbelt Indicator
8J - 34 INSTRUMENT CLUSTERDR
OIL PRESSURE GAUGE (Continued)
Page 552 of 2627
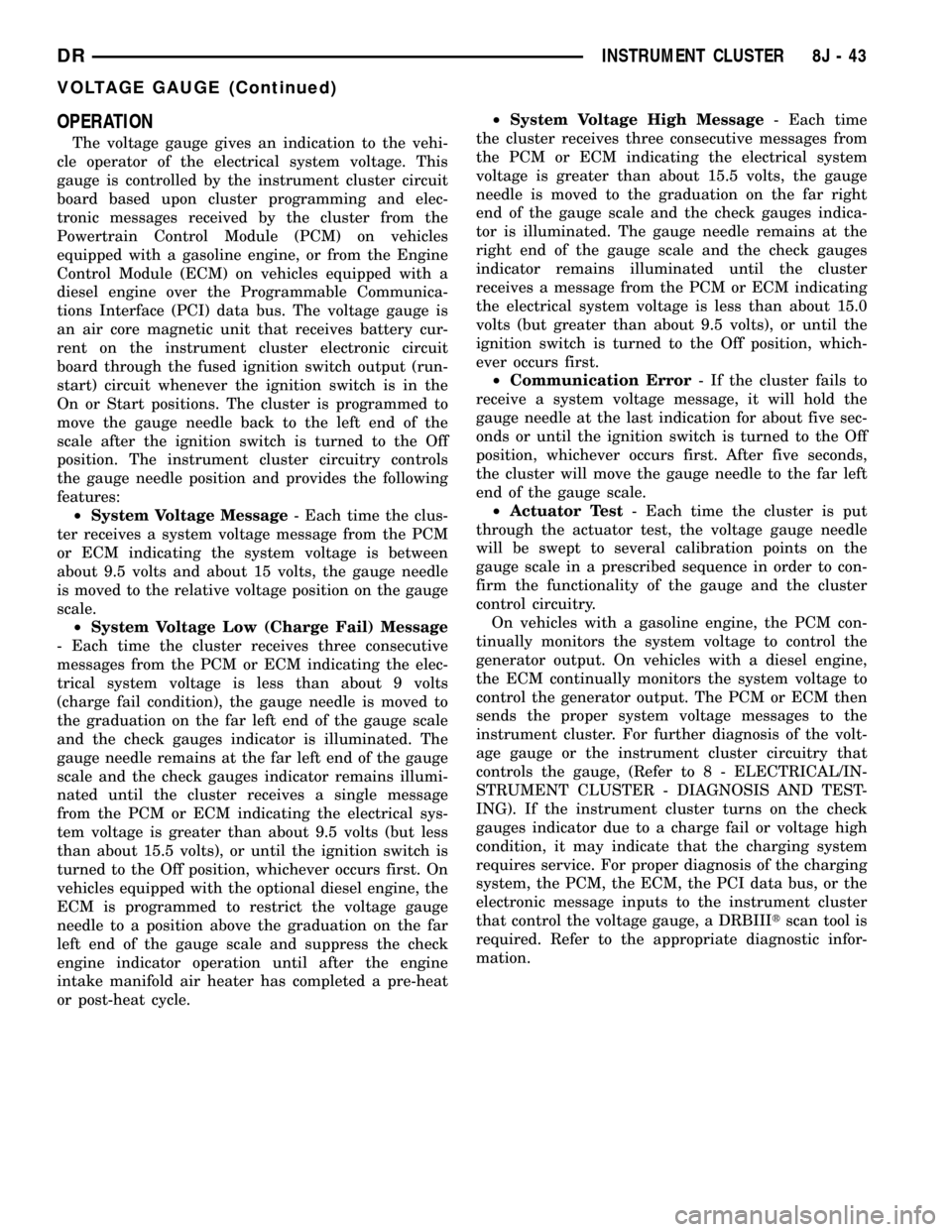
OPERATION
The voltage gauge gives an indication to the vehi-
cle operator of the electrical system voltage. This
gauge is controlled by the instrument cluster circuit
board based upon cluster programming and elec-
tronic messages received by the cluster from the
Powertrain Control Module (PCM) on vehicles
equipped with a gasoline engine, or from the Engine
Control Module (ECM) on vehicles equipped with a
diesel engine over the Programmable Communica-
tions Interface (PCI) data bus. The voltage gauge is
an air core magnetic unit that receives battery cur-
rent on the instrument cluster electronic circuit
board through the fused ignition switch output (run-
start) circuit whenever the ignition switch is in the
On or Start positions. The cluster is programmed to
move the gauge needle back to the left end of the
scale after the ignition switch is turned to the Off
position. The instrument cluster circuitry controls
the gauge needle position and provides the following
features:
²System Voltage Message- Each time the clus-
ter receives a system voltage message from the PCM
or ECM indicating the system voltage is between
about 9.5 volts and about 15 volts, the gauge needle
is moved to the relative voltage position on the gauge
scale.
²System Voltage Low (Charge Fail) Message
- Each time the cluster receives three consecutive
messages from the PCM or ECM indicating the elec-
trical system voltage is less than about 9 volts
(charge fail condition), the gauge needle is moved to
the graduation on the far left end of the gauge scale
and the check gauges indicator is illuminated. The
gauge needle remains at the far left end of the gauge
scale and the check gauges indicator remains illumi-
nated until the cluster receives a single message
from the PCM or ECM indicating the electrical sys-
tem voltage is greater than about 9.5 volts (but less
than about 15.5 volts), or until the ignition switch is
turned to the Off position, whichever occurs first. On
vehicles equipped with the optional diesel engine, the
ECM is programmed to restrict the voltage gauge
needle to a position above the graduation on the far
left end of the gauge scale and suppress the check
engine indicator operation until after the engine
intake manifold air heater has completed a pre-heat
or post-heat cycle.²System Voltage High Message- Each time
the cluster receives three consecutive messages from
the PCM or ECM indicating the electrical system
voltage is greater than about 15.5 volts, the gauge
needle is moved to the graduation on the far right
end of the gauge scale and the check gauges indica-
tor is illuminated. The gauge needle remains at the
right end of the gauge scale and the check gauges
indicator remains illuminated until the cluster
receives a message from the PCM or ECM indicating
the electrical system voltage is less than about 15.0
volts (but greater than about 9.5 volts), or until the
ignition switch is turned to the Off position, which-
ever occurs first.
²Communication Error- If the cluster fails to
receive a system voltage message, it will hold the
gauge needle at the last indication for about five sec-
onds or until the ignition switch is turned to the Off
position, whichever occurs first. After five seconds,
the cluster will move the gauge needle to the far left
end of the gauge scale.
²Actuator Test- Each time the cluster is put
through the actuator test, the voltage gauge needle
will be swept to several calibration points on the
gauge scale in a prescribed sequence in order to con-
firm the functionality of the gauge and the cluster
control circuitry.
On vehicles with a gasoline engine, the PCM con-
tinually monitors the system voltage to control the
generator output. On vehicles with a diesel engine,
the ECM continually monitors the system voltage to
control the generator output. The PCM or ECM then
sends the proper system voltage messages to the
instrument cluster. For further diagnosis of the volt-
age gauge or the instrument cluster circuitry that
controls the gauge, (Refer to 8 - ELECTRICAL/IN-
STRUMENT CLUSTER - DIAGNOSIS AND TEST-
ING). If the instrument cluster turns on the check
gauges indicator due to a charge fail or voltage high
condition, it may indicate that the charging system
requires service. For proper diagnosis of the charging
system, the PCM, the ECM, the PCI data bus, or the
electronic message inputs to the instrument cluster
that control the voltage gauge, a DRBIIItscan tool is
required. Refer to the appropriate diagnostic infor-
mation.
DRINSTRUMENT CLUSTER 8J - 43
VOLTAGE GAUGE (Continued)
Page 1290 of 2627
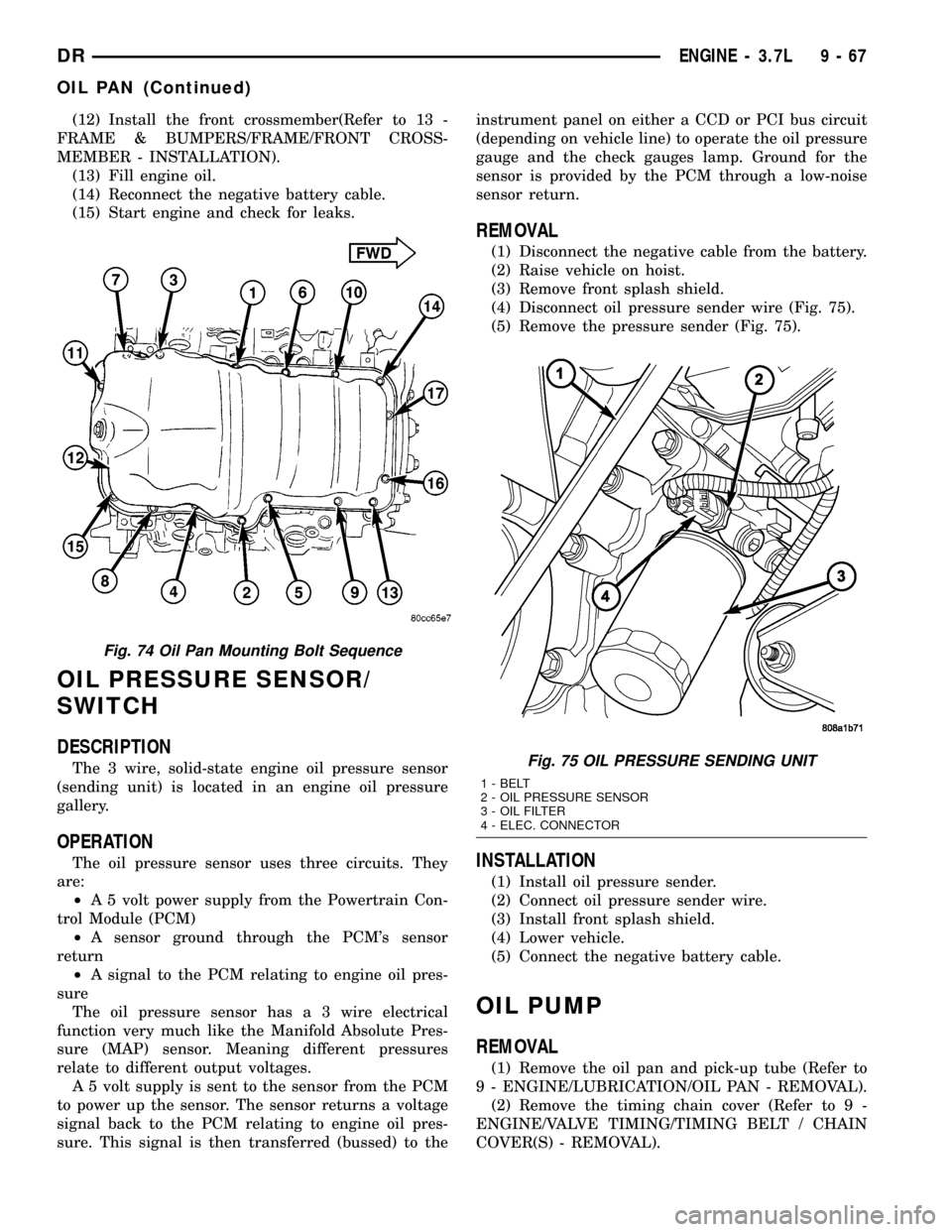
(12) Install the front crossmember(Refer to 13 -
FRAME & BUMPERS/FRAME/FRONT CROSS-
MEMBER - INSTALLATION).
(13) Fill engine oil.
(14) Reconnect the negative battery cable.
(15) Start engine and check for leaks.
OIL PRESSURE SENSOR/
SWITCH
DESCRIPTION
The 3 wire, solid-state engine oil pressure sensor
(sending unit) is located in an engine oil pressure
gallery.
OPERATION
The oil pressure sensor uses three circuits. They
are:
²A 5 volt power supply from the Powertrain Con-
trol Module (PCM)
²A sensor ground through the PCM's sensor
return
²A signal to the PCM relating to engine oil pres-
sure
The oil pressure sensor has a 3 wire electrical
function very much like the Manifold Absolute Pres-
sure (MAP) sensor. Meaning different pressures
relate to different output voltages.
A 5 volt supply is sent to the sensor from the PCM
to power up the sensor. The sensor returns a voltage
signal back to the PCM relating to engine oil pres-
sure. This signal is then transferred (bussed) to theinstrument panel on either a CCD or PCI bus circuit
(depending on vehicle line) to operate the oil pressure
gauge and the check gauges lamp. Ground for the
sensor is provided by the PCM through a low-noise
sensor return.
REMOVAL
(1) Disconnect the negative cable from the battery.
(2) Raise vehicle on hoist.
(3) Remove front splash shield.
(4) Disconnect oil pressure sender wire (Fig. 75).
(5) Remove the pressure sender (Fig. 75).
INSTALLATION
(1) Install oil pressure sender.
(2) Connect oil pressure sender wire.
(3) Install front splash shield.
(4) Lower vehicle.
(5) Connect the negative battery cable.
OIL PUMP
REMOVAL
(1) Remove the oil pan and pick-up tube (Refer to
9 - ENGINE/LUBRICATION/OIL PAN - REMOVAL).
(2) Remove the timing chain cover (Refer to 9 -
ENGINE/VALVE TIMING/TIMING BELT / CHAIN
COVER(S) - REMOVAL).
Fig. 74 Oil Pan Mounting Bolt Sequence
Fig. 75 OIL PRESSURE SENDING UNIT
1 - BELT
2 - OIL PRESSURE SENSOR
3 - OIL FILTER
4 - ELEC. CONNECTOR
DRENGINE - 3.7L 9 - 67
OIL PAN (Continued)
Page 1379 of 2627
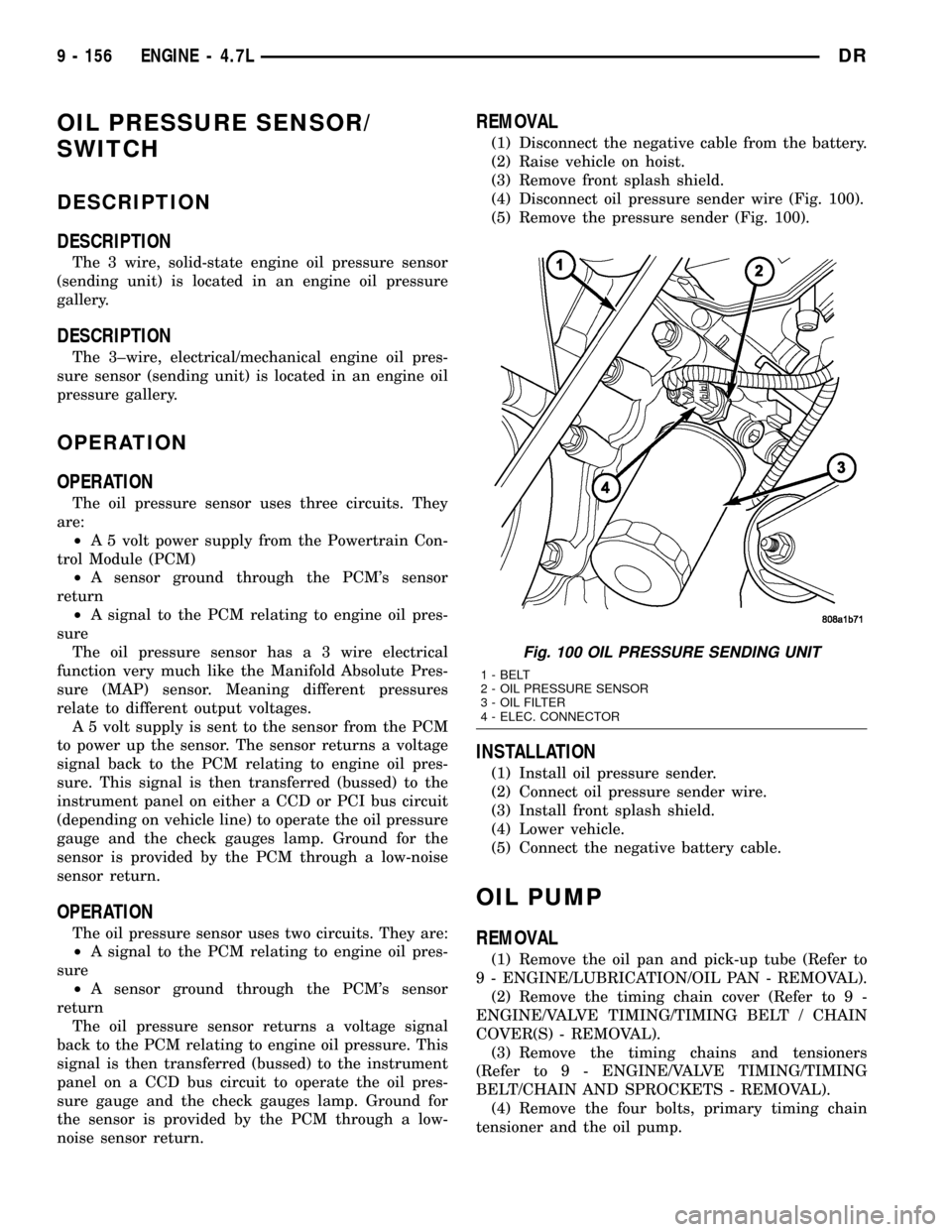
OIL PRESSURE SENSOR/
SWITCH
DESCRIPTION
DESCRIPTION
The 3 wire, solid-state engine oil pressure sensor
(sending unit) is located in an engine oil pressure
gallery.
DESCRIPTION
The 3±wire, electrical/mechanical engine oil pres-
sure sensor (sending unit) is located in an engine oil
pressure gallery.
OPERATION
OPERATION
The oil pressure sensor uses three circuits. They
are:
²A 5 volt power supply from the Powertrain Con-
trol Module (PCM)
²A sensor ground through the PCM's sensor
return
²A signal to the PCM relating to engine oil pres-
sure
The oil pressure sensor has a 3 wire electrical
function very much like the Manifold Absolute Pres-
sure (MAP) sensor. Meaning different pressures
relate to different output voltages.
A 5 volt supply is sent to the sensor from the PCM
to power up the sensor. The sensor returns a voltage
signal back to the PCM relating to engine oil pres-
sure. This signal is then transferred (bussed) to the
instrument panel on either a CCD or PCI bus circuit
(depending on vehicle line) to operate the oil pressure
gauge and the check gauges lamp. Ground for the
sensor is provided by the PCM through a low-noise
sensor return.
OPERATION
The oil pressure sensor uses two circuits. They are:
²A signal to the PCM relating to engine oil pres-
sure
²A sensor ground through the PCM's sensor
return
The oil pressure sensor returns a voltage signal
back to the PCM relating to engine oil pressure. This
signal is then transferred (bussed) to the instrument
panel on a CCD bus circuit to operate the oil pres-
sure gauge and the check gauges lamp. Ground for
the sensor is provided by the PCM through a low-
noise sensor return.
REMOVAL
(1) Disconnect the negative cable from the battery.
(2) Raise vehicle on hoist.
(3) Remove front splash shield.
(4) Disconnect oil pressure sender wire (Fig. 100).
(5) Remove the pressure sender (Fig. 100).
INSTALLATION
(1) Install oil pressure sender.
(2) Connect oil pressure sender wire.
(3) Install front splash shield.
(4) Lower vehicle.
(5) Connect the negative battery cable.
OIL PUMP
REMOVAL
(1) Remove the oil pan and pick-up tube (Refer to
9 - ENGINE/LUBRICATION/OIL PAN - REMOVAL).
(2) Remove the timing chain cover (Refer to 9 -
ENGINE/VALVE TIMING/TIMING BELT / CHAIN
COVER(S) - REMOVAL).
(3) Remove the timing chains and tensioners
(Refer to 9 - ENGINE/VALVE TIMING/TIMING
BELT/CHAIN AND SPROCKETS - REMOVAL).
(4) Remove the four bolts, primary timing chain
tensioner and the oil pump.
Fig. 100 OIL PRESSURE SENDING UNIT
1 - BELT
2 - OIL PRESSURE SENSOR
3 - OIL FILTER
4 - ELEC. CONNECTOR
9 - 156 ENGINE - 4.7LDR
Page 1844 of 2627
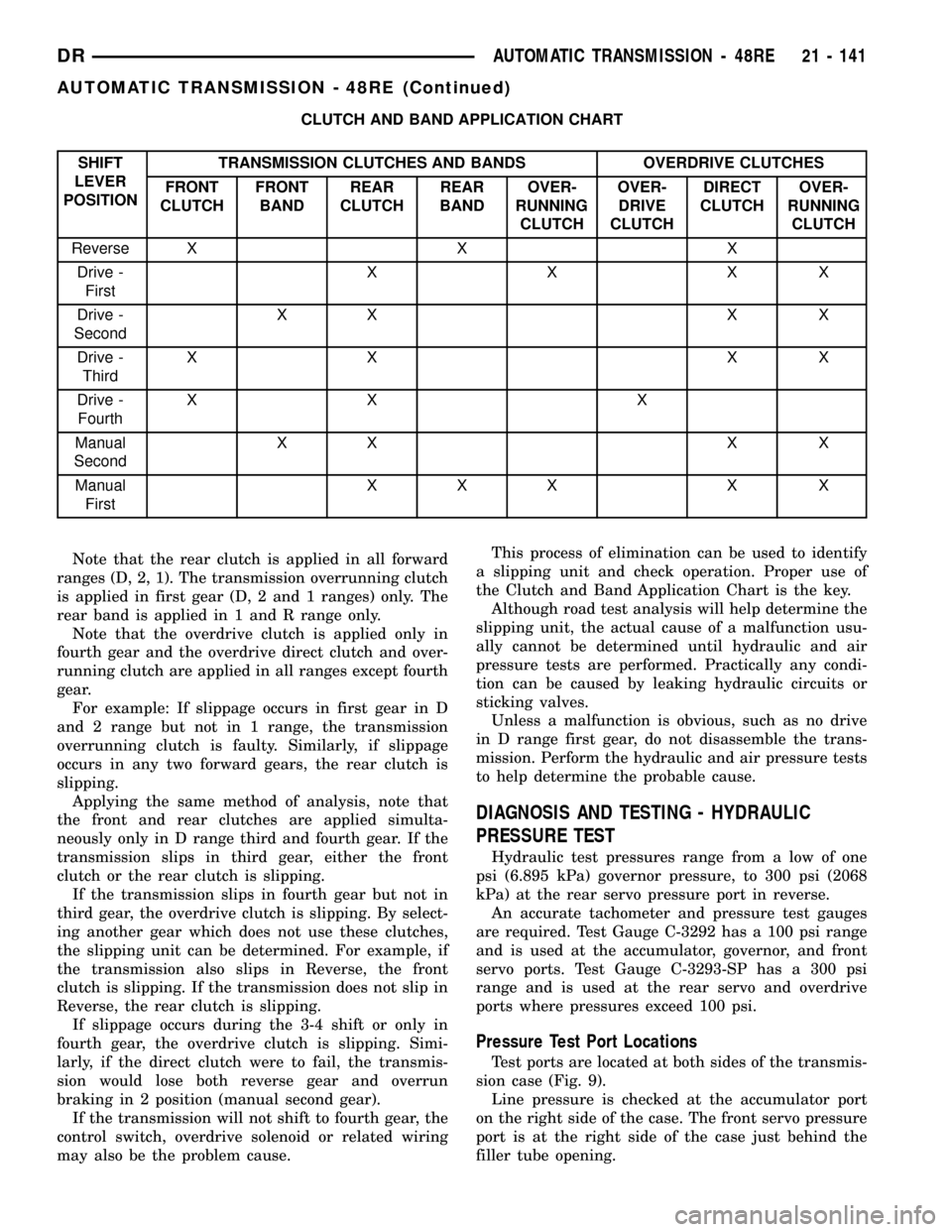
CLUTCH AND BAND APPLICATION CHART
SHIFT
LEVER
POSITIONTRANSMISSION CLUTCHES AND BANDS OVERDRIVE CLUTCHES
FRONT
CLUTCHFRONT
BANDREAR
CLUTCHREAR
BANDOVER-
RUNNING
CLUTCHOVER-
DRIVE
CLUTCHDIRECT
CLUTCHOVER-
RUNNING
CLUTCH
Reverse X X X
Drive -
FirstXXXX
Drive -
SecondXX X X
Drive -
ThirdXX XX
Drive -
FourthXX X
Manual
SecondXX X X
Manual
FirstXXX X X
Note that the rear clutch is applied in all forward
ranges (D, 2, 1). The transmission overrunning clutch
is applied in first gear (D, 2 and 1 ranges) only. The
rear band is applied in 1 and R range only.
Note that the overdrive clutch is applied only in
fourth gear and the overdrive direct clutch and over-
running clutch are applied in all ranges except fourth
gear.
For example: If slippage occurs in first gear in D
and 2 range but not in 1 range, the transmission
overrunning clutch is faulty. Similarly, if slippage
occurs in any two forward gears, the rear clutch is
slipping.
Applying the same method of analysis, note that
the front and rear clutches are applied simulta-
neously only in D range third and fourth gear. If the
transmission slips in third gear, either the front
clutch or the rear clutch is slipping.
If the transmission slips in fourth gear but not in
third gear, the overdrive clutch is slipping. By select-
ing another gear which does not use these clutches,
the slipping unit can be determined. For example, if
the transmission also slips in Reverse, the front
clutch is slipping. If the transmission does not slip in
Reverse, the rear clutch is slipping.
If slippage occurs during the 3-4 shift or only in
fourth gear, the overdrive clutch is slipping. Simi-
larly, if the direct clutch were to fail, the transmis-
sion would lose both reverse gear and overrun
braking in 2 position (manual second gear).
If the transmission will not shift to fourth gear, the
control switch, overdrive solenoid or related wiring
may also be the problem cause.This process of elimination can be used to identify
a slipping unit and check operation. Proper use of
the Clutch and Band Application Chart is the key.
Although road test analysis will help determine the
slipping unit, the actual cause of a malfunction usu-
ally cannot be determined until hydraulic and air
pressure tests are performed. Practically any condi-
tion can be caused by leaking hydraulic circuits or
sticking valves.
Unless a malfunction is obvious, such as no drive
in D range first gear, do not disassemble the trans-
mission. Perform the hydraulic and air pressure tests
to help determine the probable cause.
DIAGNOSIS AND TESTING - HYDRAULIC
PRESSURE TEST
Hydraulic test pressures range from a low of one
psi (6.895 kPa) governor pressure, to 300 psi (2068
kPa) at the rear servo pressure port in reverse.
An accurate tachometer and pressure test gauges
are required. Test Gauge C-3292 has a 100 psi range
and is used at the accumulator, governor, and front
servo ports. Test Gauge C-3293-SP has a 300 psi
range and is used at the rear servo and overdrive
ports where pressures exceed 100 psi.
Pressure Test Port Locations
Test ports are located at both sides of the transmis-
sion case (Fig. 9).
Line pressure is checked at the accumulator port
on the right side of the case. The front servo pressure
port is at the right side of the case just behind the
filler tube opening.
DRAUTOMATIC TRANSMISSION - 48RE 21 - 141
AUTOMATIC TRANSMISSION - 48RE (Continued)
Page 1845 of 2627
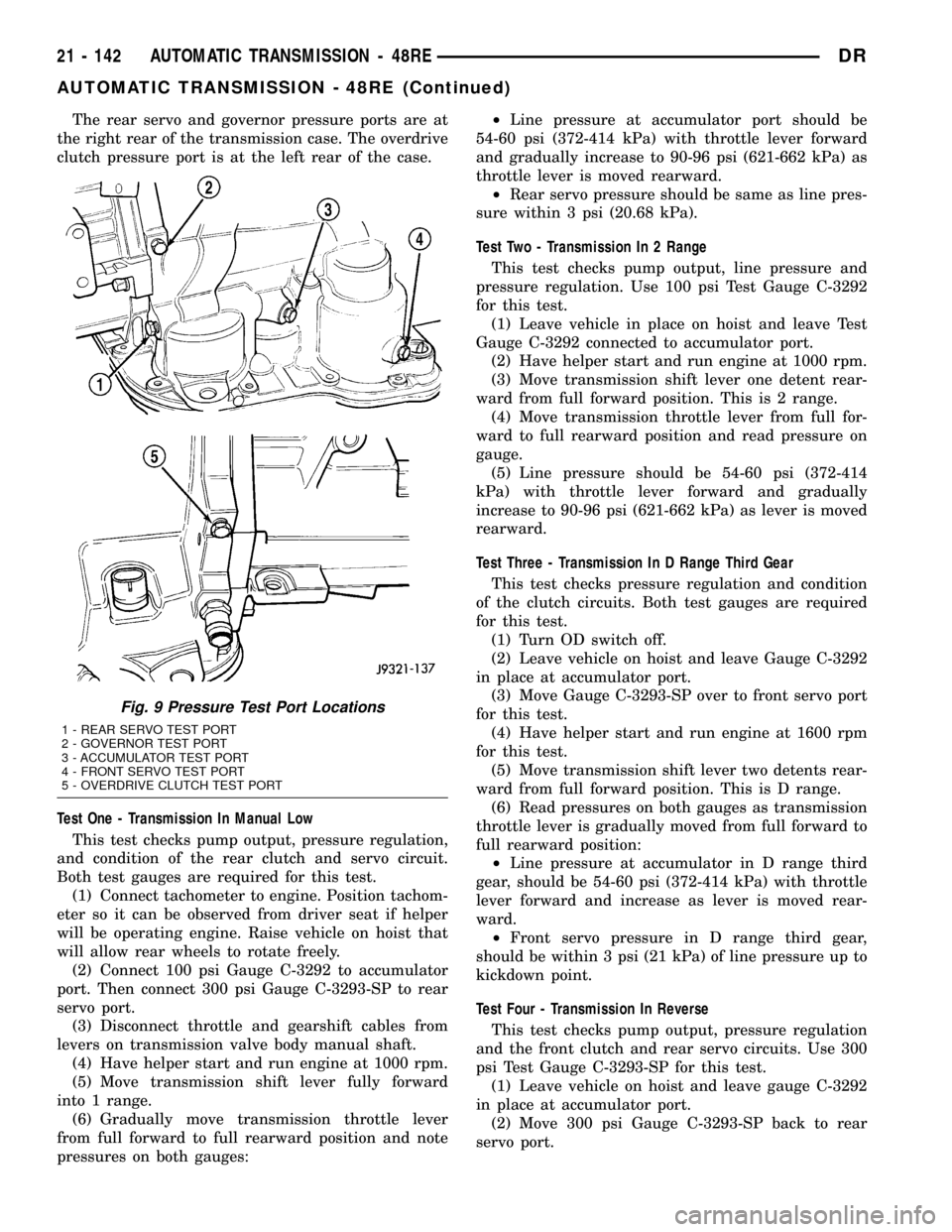
The rear servo and governor pressure ports are at
the right rear of the transmission case. The overdrive
clutch pressure port is at the left rear of the case.
Test One - Transmission In Manual Low
This test checks pump output, pressure regulation,
and condition of the rear clutch and servo circuit.
Both test gauges are required for this test.
(1) Connect tachometer to engine. Position tachom-
eter so it can be observed from driver seat if helper
will be operating engine. Raise vehicle on hoist that
will allow rear wheels to rotate freely.
(2) Connect 100 psi Gauge C-3292 to accumulator
port. Then connect 300 psi Gauge C-3293-SP to rear
servo port.
(3) Disconnect throttle and gearshift cables from
levers on transmission valve body manual shaft.
(4) Have helper start and run engine at 1000 rpm.
(5) Move transmission shift lever fully forward
into 1 range.
(6) Gradually move transmission throttle lever
from full forward to full rearward position and note
pressures on both gauges:²Line pressure at accumulator port should be
54-60 psi (372-414 kPa) with throttle lever forward
and gradually increase to 90-96 psi (621-662 kPa) as
throttle lever is moved rearward.
²Rear servo pressure should be same as line pres-
sure within 3 psi (20.68 kPa).
Test Two - Transmission In 2 Range
This test checks pump output, line pressure and
pressure regulation. Use 100 psi Test Gauge C-3292
for this test.
(1) Leave vehicle in place on hoist and leave Test
Gauge C-3292 connected to accumulator port.
(2) Have helper start and run engine at 1000 rpm.
(3) Move transmission shift lever one detent rear-
ward from full forward position. This is 2 range.
(4) Move transmission throttle lever from full for-
ward to full rearward position and read pressure on
gauge.
(5) Line pressure should be 54-60 psi (372-414
kPa) with throttle lever forward and gradually
increase to 90-96 psi (621-662 kPa) as lever is moved
rearward.
Test Three - Transmission In D Range Third Gear
This test checks pressure regulation and condition
of the clutch circuits. Both test gauges are required
for this test.
(1) Turn OD switch off.
(2) Leave vehicle on hoist and leave Gauge C-3292
in place at accumulator port.
(3) Move Gauge C-3293-SP over to front servo port
for this test.
(4) Have helper start and run engine at 1600 rpm
for this test.
(5) Move transmission shift lever two detents rear-
ward from full forward position. This is D range.
(6) Read pressures on both gauges as transmission
throttle lever is gradually moved from full forward to
full rearward position:
²Line pressure at accumulator in D range third
gear, should be 54-60 psi (372-414 kPa) with throttle
lever forward and increase as lever is moved rear-
ward.
²Front servo pressure in D range third gear,
should be within 3 psi (21 kPa) of line pressure up to
kickdown point.
Test Four - Transmission In Reverse
This test checks pump output, pressure regulation
and the front clutch and rear servo circuits. Use 300
psi Test Gauge C-3293-SP for this test.
(1) Leave vehicle on hoist and leave gauge C-3292
in place at accumulator port.
(2) Move 300 psi Gauge C-3293-SP back to rear
servo port.
Fig. 9 Pressure Test Port Locations
1 - REAR SERVO TEST PORT
2 - GOVERNOR TEST PORT
3 - ACCUMULATOR TEST PORT
4 - FRONT SERVO TEST PORT
5 - OVERDRIVE CLUTCH TEST PORT
21 - 142 AUTOMATIC TRANSMISSION - 48REDR
AUTOMATIC TRANSMISSION - 48RE (Continued)