Ignition switch DODGE RAM 1500 1998 2.G Workshop Manual
[x] Cancel search | Manufacturer: DODGE, Model Year: 1998, Model line: RAM 1500, Model: DODGE RAM 1500 1998 2.GPages: 2627
Page 2501 of 2627
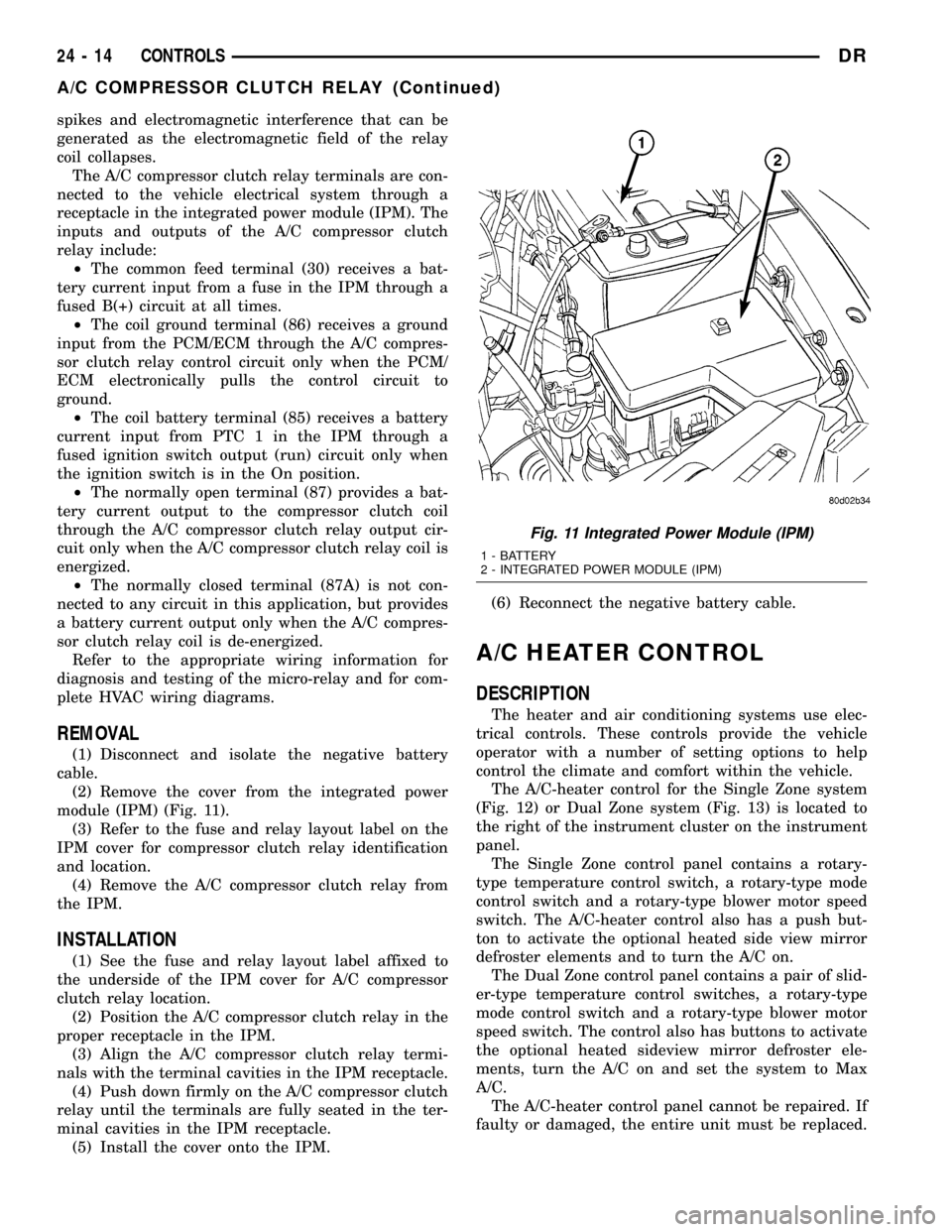
spikes and electromagnetic interference that can be
generated as the electromagnetic field of the relay
coil collapses.
The A/C compressor clutch relay terminals are con-
nected to the vehicle electrical system through a
receptacle in the integrated power module (IPM). The
inputs and outputs of the A/C compressor clutch
relay include:
²The common feed terminal (30) receives a bat-
tery current input from a fuse in the IPM through a
fused B(+) circuit at all times.
²The coil ground terminal (86) receives a ground
input from the PCM/ECM through the A/C compres-
sor clutch relay control circuit only when the PCM/
ECM electronically pulls the control circuit to
ground.
²The coil battery terminal (85) receives a battery
current input from PTC 1 in the IPM through a
fused ignition switch output (run) circuit only when
the ignition switch is in the On position.
²The normally open terminal (87) provides a bat-
tery current output to the compressor clutch coil
through the A/C compressor clutch relay output cir-
cuit only when the A/C compressor clutch relay coil is
energized.
²The normally closed terminal (87A) is not con-
nected to any circuit in this application, but provides
a battery current output only when the A/C compres-
sor clutch relay coil is de-energized.
Refer to the appropriate wiring information for
diagnosis and testing of the micro-relay and for com-
plete HVAC wiring diagrams.
REMOVAL
(1) Disconnect and isolate the negative battery
cable.
(2) Remove the cover from the integrated power
module (IPM) (Fig. 11).
(3) Refer to the fuse and relay layout label on the
IPM cover for compressor clutch relay identification
and location.
(4) Remove the A/C compressor clutch relay from
the IPM.
INSTALLATION
(1) See the fuse and relay layout label affixed to
the underside of the IPM cover for A/C compressor
clutch relay location.
(2) Position the A/C compressor clutch relay in the
proper receptacle in the IPM.
(3) Align the A/C compressor clutch relay termi-
nals with the terminal cavities in the IPM receptacle.
(4) Push down firmly on the A/C compressor clutch
relay until the terminals are fully seated in the ter-
minal cavities in the IPM receptacle.
(5) Install the cover onto the IPM.(6) Reconnect the negative battery cable.
A/C HEATER CONTROL
DESCRIPTION
The heater and air conditioning systems use elec-
trical controls. These controls provide the vehicle
operator with a number of setting options to help
control the climate and comfort within the vehicle.
The A/C-heater control for the Single Zone system
(Fig. 12) or Dual Zone system (Fig. 13) is located to
the right of the instrument cluster on the instrument
panel.
The Single Zone control panel contains a rotary-
type temperature control switch, a rotary-type mode
control switch and a rotary-type blower motor speed
switch. The A/C-heater control also has a push but-
ton to activate the optional heated side view mirror
defroster elements and to turn the A/C on.
The Dual Zone control panel contains a pair of slid-
er-type temperature control switches, a rotary-type
mode control switch and a rotary-type blower motor
speed switch. The control also has buttons to activate
the optional heated sideview mirror defroster ele-
ments, turn the A/C on and set the system to Max
A/C.
The A/C-heater control panel cannot be repaired. If
faulty or damaged, the entire unit must be replaced.
Fig. 11 Integrated Power Module (IPM)
1 - BATTERY
2 - INTEGRATED POWER MODULE (IPM)
24 - 14 CONTROLSDR
A/C COMPRESSOR CLUTCH RELAY (Continued)
Page 2507 of 2627
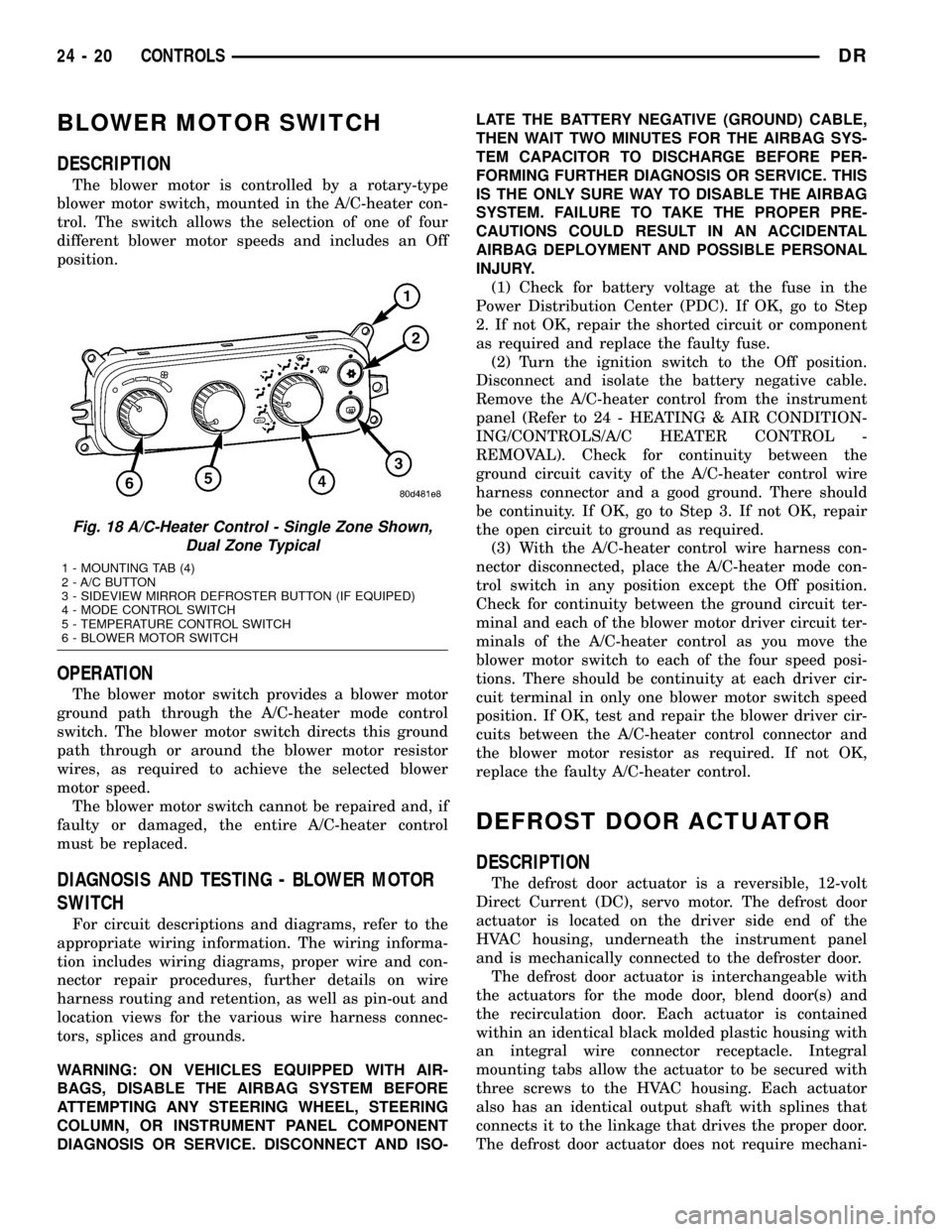
BLOWER MOTOR SWITCH
DESCRIPTION
The blower motor is controlled by a rotary-type
blower motor switch, mounted in the A/C-heater con-
trol. The switch allows the selection of one of four
different blower motor speeds and includes an Off
position.
OPERATION
The blower motor switch provides a blower motor
ground path through the A/C-heater mode control
switch. The blower motor switch directs this ground
path through or around the blower motor resistor
wires, as required to achieve the selected blower
motor speed.
The blower motor switch cannot be repaired and, if
faulty or damaged, the entire A/C-heater control
must be replaced.
DIAGNOSIS AND TESTING - BLOWER MOTOR
SWITCH
For circuit descriptions and diagrams, refer to the
appropriate wiring information. The wiring informa-
tion includes wiring diagrams, proper wire and con-
nector repair procedures, further details on wire
harness routing and retention, as well as pin-out and
location views for the various wire harness connec-
tors, splices and grounds.
WARNING: ON VEHICLES EQUIPPED WITH AIR-
BAGS, DISABLE THE AIRBAG SYSTEM BEFORE
ATTEMPTING ANY STEERING WHEEL, STEERING
COLUMN, OR INSTRUMENT PANEL COMPONENT
DIAGNOSIS OR SERVICE. DISCONNECT AND ISO-LATE THE BATTERY NEGATIVE (GROUND) CABLE,
THEN WAIT TWO MINUTES FOR THE AIRBAG SYS-
TEM CAPACITOR TO DISCHARGE BEFORE PER-
FORMING FURTHER DIAGNOSIS OR SERVICE. THIS
IS THE ONLY SURE WAY TO DISABLE THE AIRBAG
SYSTEM. FAILURE TO TAKE THE PROPER PRE-
CAUTIONS COULD RESULT IN AN ACCIDENTAL
AIRBAG DEPLOYMENT AND POSSIBLE PERSONAL
INJURY.
(1) Check for battery voltage at the fuse in the
Power Distribution Center (PDC). If OK, go to Step
2. If not OK, repair the shorted circuit or component
as required and replace the faulty fuse.
(2) Turn the ignition switch to the Off position.
Disconnect and isolate the battery negative cable.
Remove the A/C-heater control from the instrument
panel (Refer to 24 - HEATING & AIR CONDITION-
ING/CONTROLS/A/C HEATER CONTROL -
REMOVAL). Check for continuity between the
ground circuit cavity of the A/C-heater control wire
harness connector and a good ground. There should
be continuity. If OK, go to Step 3. If not OK, repair
the open circuit to ground as required.
(3) With the A/C-heater control wire harness con-
nector disconnected, place the A/C-heater mode con-
trol switch in any position except the Off position.
Check for continuity between the ground circuit ter-
minal and each of the blower motor driver circuit ter-
minals of the A/C-heater control as you move the
blower motor switch to each of the four speed posi-
tions. There should be continuity at each driver cir-
cuit terminal in only one blower motor switch speed
position. If OK, test and repair the blower driver cir-
cuits between the A/C-heater control connector and
the blower motor resistor as required. If not OK,
replace the faulty A/C-heater control.
DEFROST DOOR ACTUATOR
DESCRIPTION
The defrost door actuator is a reversible, 12-volt
Direct Current (DC), servo motor. The defrost door
actuator is located on the driver side end of the
HVAC housing, underneath the instrument panel
and is mechanically connected to the defroster door.
The defrost door actuator is interchangeable with
the actuators for the mode door, blend door(s) and
the recirculation door. Each actuator is contained
within an identical black molded plastic housing with
an integral wire connector receptacle. Integral
mounting tabs allow the actuator to be secured with
three screws to the HVAC housing. Each actuator
also has an identical output shaft with splines that
connects it to the linkage that drives the proper door.
The defrost door actuator does not require mechani-
Fig. 18 A/C-Heater Control - Single Zone Shown,
Dual Zone Typical
1 - MOUNTING TAB (4)
2 - A/C BUTTON
3 - SIDEVIEW MIRROR DEFROSTER BUTTON (IF EQUIPED)
4 - MODE CONTROL SWITCH
5 - TEMPERATURE CONTROL SWITCH
6 - BLOWER MOTOR SWITCH
24 - 20 CONTROLSDR
Page 2515 of 2627
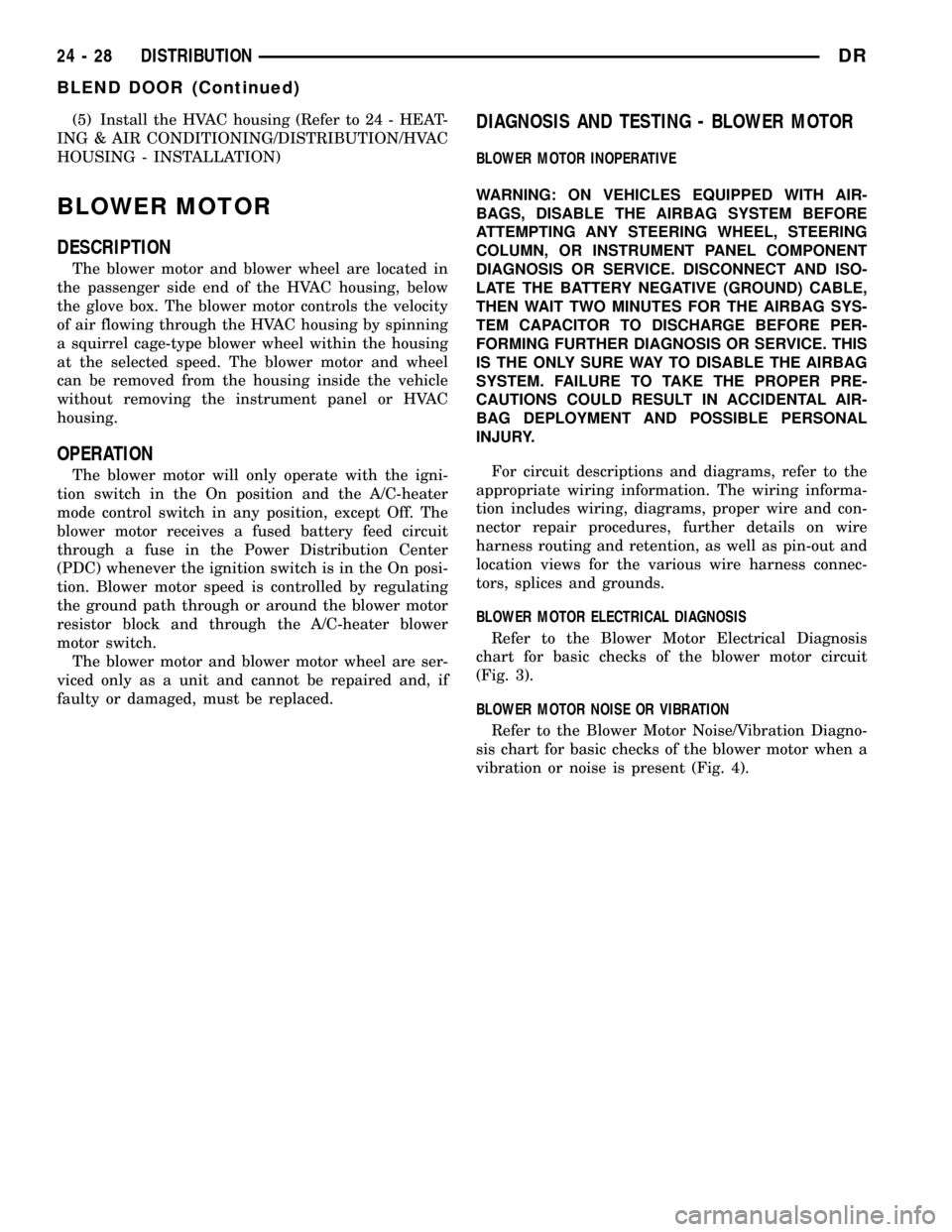
(5) Install the HVAC housing (Refer to 24 - HEAT-
ING & AIR CONDITIONING/DISTRIBUTION/HVAC
HOUSING - INSTALLATION)
BLOWER MOTOR
DESCRIPTION
The blower motor and blower wheel are located in
the passenger side end of the HVAC housing, below
the glove box. The blower motor controls the velocity
of air flowing through the HVAC housing by spinning
a squirrel cage-type blower wheel within the housing
at the selected speed. The blower motor and wheel
can be removed from the housing inside the vehicle
without removing the instrument panel or HVAC
housing.
OPERATION
The blower motor will only operate with the igni-
tion switch in the On position and the A/C-heater
mode control switch in any position, except Off. The
blower motor receives a fused battery feed circuit
through a fuse in the Power Distribution Center
(PDC) whenever the ignition switch is in the On posi-
tion. Blower motor speed is controlled by regulating
the ground path through or around the blower motor
resistor block and through the A/C-heater blower
motor switch.
The blower motor and blower motor wheel are ser-
viced only as a unit and cannot be repaired and, if
faulty or damaged, must be replaced.
DIAGNOSIS AND TESTING - BLOWER MOTOR
BLOWER MOTOR INOPERATIVE
WARNING: ON VEHICLES EQUIPPED WITH AIR-
BAGS, DISABLE THE AIRBAG SYSTEM BEFORE
ATTEMPTING ANY STEERING WHEEL, STEERING
COLUMN, OR INSTRUMENT PANEL COMPONENT
DIAGNOSIS OR SERVICE. DISCONNECT AND ISO-
LATE THE BATTERY NEGATIVE (GROUND) CABLE,
THEN WAIT TWO MINUTES FOR THE AIRBAG SYS-
TEM CAPACITOR TO DISCHARGE BEFORE PER-
FORMING FURTHER DIAGNOSIS OR SERVICE. THIS
IS THE ONLY SURE WAY TO DISABLE THE AIRBAG
SYSTEM. FAILURE TO TAKE THE PROPER PRE-
CAUTIONS COULD RESULT IN ACCIDENTAL AIR-
BAG DEPLOYMENT AND POSSIBLE PERSONAL
INJURY.
For circuit descriptions and diagrams, refer to the
appropriate wiring information. The wiring informa-
tion includes wiring, diagrams, proper wire and con-
nector repair procedures, further details on wire
harness routing and retention, as well as pin-out and
location views for the various wire harness connec-
tors, splices and grounds.
BLOWER MOTOR ELECTRICAL DIAGNOSIS
Refer to the Blower Motor Electrical Diagnosis
chart for basic checks of the blower motor circuit
(Fig. 3).
BLOWER MOTOR NOISE OR VIBRATION
Refer to the Blower Motor Noise/Vibration Diagno-
sis chart for basic checks of the blower motor when a
vibration or noise is present (Fig. 4).
24 - 28 DISTRIBUTIONDR
BLEND DOOR (Continued)
Page 2562 of 2627
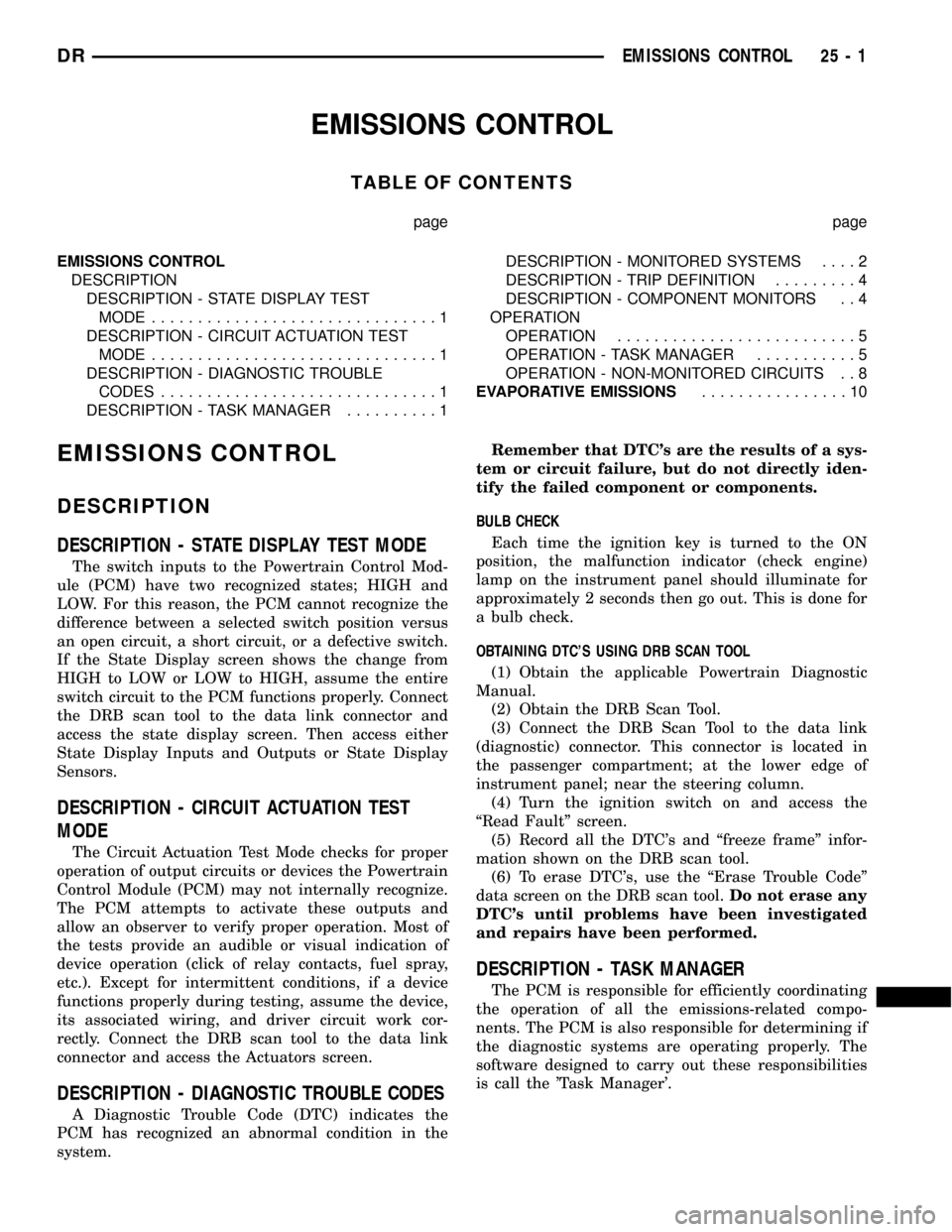
EMISSIONS CONTROL
TABLE OF CONTENTS
page page
EMISSIONS CONTROL
DESCRIPTION
DESCRIPTION - STATE DISPLAY TEST
MODE...............................1
DESCRIPTION - CIRCUIT ACTUATION TEST
MODE...............................1
DESCRIPTION - DIAGNOSTIC TROUBLE
CODES..............................1
DESCRIPTION - TASK MANAGER..........1DESCRIPTION - MONITORED SYSTEMS....2
DESCRIPTION - TRIP DEFINITION.........4
DESCRIPTION - COMPONENT MONITORS . . 4
OPERATION
OPERATION..........................5
OPERATION - TASK MANAGER...........5
OPERATION - NON-MONITORED CIRCUITS . . 8
EVAPORATIVE EMISSIONS................10
EMISSIONS CONTROL
DESCRIPTION
DESCRIPTION - STATE DISPLAY TEST MODE
The switch inputs to the Powertrain Control Mod-
ule (PCM) have two recognized states; HIGH and
LOW. For this reason, the PCM cannot recognize the
difference between a selected switch position versus
an open circuit, a short circuit, or a defective switch.
If the State Display screen shows the change from
HIGH to LOW or LOW to HIGH, assume the entire
switch circuit to the PCM functions properly. Connect
the DRB scan tool to the data link connector and
access the state display screen. Then access either
State Display Inputs and Outputs or State Display
Sensors.
DESCRIPTION - CIRCUIT ACTUATION TEST
MODE
The Circuit Actuation Test Mode checks for proper
operation of output circuits or devices the Powertrain
Control Module (PCM) may not internally recognize.
The PCM attempts to activate these outputs and
allow an observer to verify proper operation. Most of
the tests provide an audible or visual indication of
device operation (click of relay contacts, fuel spray,
etc.). Except for intermittent conditions, if a device
functions properly during testing, assume the device,
its associated wiring, and driver circuit work cor-
rectly. Connect the DRB scan tool to the data link
connector and access the Actuators screen.
DESCRIPTION - DIAGNOSTIC TROUBLE CODES
A Diagnostic Trouble Code (DTC) indicates the
PCM has recognized an abnormal condition in the
system.Remember that DTC's are the results of a sys-
tem or circuit failure, but do not directly iden-
tify the failed component or components.
BULB CHECK
Each time the ignition key is turned to the ON
position, the malfunction indicator (check engine)
lamp on the instrument panel should illuminate for
approximately 2 seconds then go out. This is done for
a bulb check.
OBTAINING DTC'S USING DRB SCAN TOOL
(1) Obtain the applicable Powertrain Diagnostic
Manual.
(2) Obtain the DRB Scan Tool.
(3) Connect the DRB Scan Tool to the data link
(diagnostic) connector. This connector is located in
the passenger compartment; at the lower edge of
instrument panel; near the steering column.
(4) Turn the ignition switch on and access the
ªRead Faultº screen.
(5) Record all the DTC's and ªfreeze frameº infor-
mation shown on the DRB scan tool.
(6) To erase DTC's, use the ªErase Trouble Codeº
data screen on the DRB scan tool.Do not erase any
DTC's until problems have been investigated
and repairs have been performed.
DESCRIPTION - TASK MANAGER
The PCM is responsible for efficiently coordinating
the operation of all the emissions-related compo-
nents. The PCM is also responsible for determining if
the diagnostic systems are operating properly. The
software designed to carry out these responsibilities
is call the 'Task Manager'.
DREMISSIONS CONTROL 25 - 1
Page 2563 of 2627
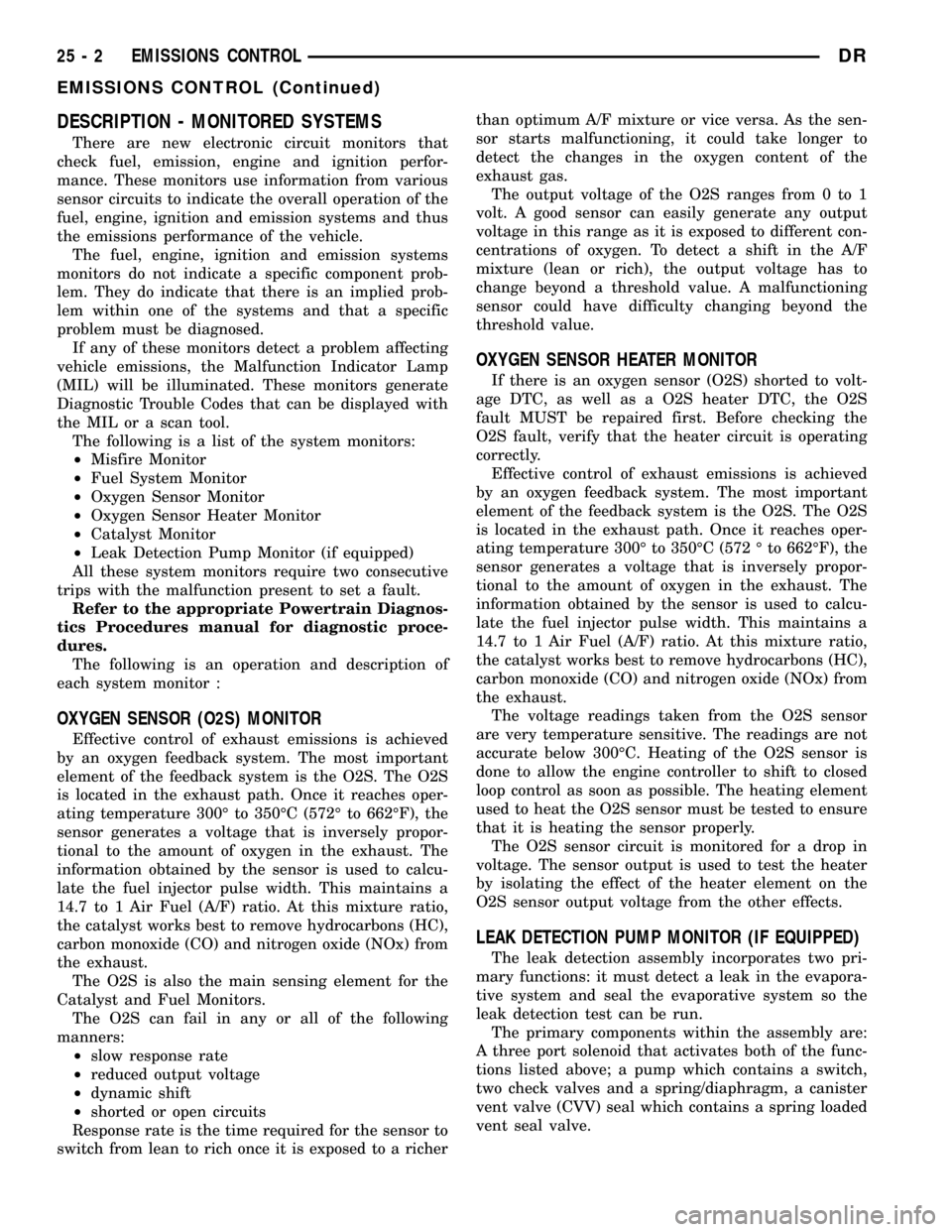
DESCRIPTION - MONITORED SYSTEMS
There are new electronic circuit monitors that
check fuel, emission, engine and ignition perfor-
mance. These monitors use information from various
sensor circuits to indicate the overall operation of the
fuel, engine, ignition and emission systems and thus
the emissions performance of the vehicle.
The fuel, engine, ignition and emission systems
monitors do not indicate a specific component prob-
lem. They do indicate that there is an implied prob-
lem within one of the systems and that a specific
problem must be diagnosed.
If any of these monitors detect a problem affecting
vehicle emissions, the Malfunction Indicator Lamp
(MIL) will be illuminated. These monitors generate
Diagnostic Trouble Codes that can be displayed with
the MIL or a scan tool.
The following is a list of the system monitors:
²Misfire Monitor
²Fuel System Monitor
²Oxygen Sensor Monitor
²Oxygen Sensor Heater Monitor
²Catalyst Monitor
²Leak Detection Pump Monitor (if equipped)
All these system monitors require two consecutive
trips with the malfunction present to set a fault.
Refer to the appropriate Powertrain Diagnos-
tics Procedures manual for diagnostic proce-
dures.
The following is an operation and description of
each system monitor :
OXYGEN SENSOR (O2S) MONITOR
Effective control of exhaust emissions is achieved
by an oxygen feedback system. The most important
element of the feedback system is the O2S. The O2S
is located in the exhaust path. Once it reaches oper-
ating temperature 300É to 350ÉC (572É to 662ÉF), the
sensor generates a voltage that is inversely propor-
tional to the amount of oxygen in the exhaust. The
information obtained by the sensor is used to calcu-
late the fuel injector pulse width. This maintains a
14.7 to 1 Air Fuel (A/F) ratio. At this mixture ratio,
the catalyst works best to remove hydrocarbons (HC),
carbon monoxide (CO) and nitrogen oxide (NOx) from
the exhaust.
The O2S is also the main sensing element for the
Catalyst and Fuel Monitors.
The O2S can fail in any or all of the following
manners:
²slow response rate
²reduced output voltage
²dynamic shift
²shorted or open circuits
Response rate is the time required for the sensor to
switch from lean to rich once it is exposed to a richerthan optimum A/F mixture or vice versa. As the sen-
sor starts malfunctioning, it could take longer to
detect the changes in the oxygen content of the
exhaust gas.
The output voltage of the O2S ranges from 0 to 1
volt. A good sensor can easily generate any output
voltage in this range as it is exposed to different con-
centrations of oxygen. To detect a shift in the A/F
mixture (lean or rich), the output voltage has to
change beyond a threshold value. A malfunctioning
sensor could have difficulty changing beyond the
threshold value.
OXYGEN SENSOR HEATER MONITOR
If there is an oxygen sensor (O2S) shorted to volt-
age DTC, as well as a O2S heater DTC, the O2S
fault MUST be repaired first. Before checking the
O2S fault, verify that the heater circuit is operating
correctly.
Effective control of exhaust emissions is achieved
by an oxygen feedback system. The most important
element of the feedback system is the O2S. The O2S
is located in the exhaust path. Once it reaches oper-
ating temperature 300É to 350ÉC (572 É to 662ÉF), the
sensor generates a voltage that is inversely propor-
tional to the amount of oxygen in the exhaust. The
information obtained by the sensor is used to calcu-
late the fuel injector pulse width. This maintains a
14.7 to 1 Air Fuel (A/F) ratio. At this mixture ratio,
the catalyst works best to remove hydrocarbons (HC),
carbon monoxide (CO) and nitrogen oxide (NOx) from
the exhaust.
The voltage readings taken from the O2S sensor
are very temperature sensitive. The readings are not
accurate below 300ÉC. Heating of the O2S sensor is
done to allow the engine controller to shift to closed
loop control as soon as possible. The heating element
used to heat the O2S sensor must be tested to ensure
that it is heating the sensor properly.
The O2S sensor circuit is monitored for a drop in
voltage. The sensor output is used to test the heater
by isolating the effect of the heater element on the
O2S sensor output voltage from the other effects.
LEAK DETECTION PUMP MONITOR (IF EQUIPPED)
The leak detection assembly incorporates two pri-
mary functions: it must detect a leak in the evapora-
tive system and seal the evaporative system so the
leak detection test can be run.
The primary components within the assembly are:
A three port solenoid that activates both of the func-
tions listed above; a pump which contains a switch,
two check valves and a spring/diaphragm, a canister
vent valve (CVV) seal which contains a spring loaded
vent seal valve.
25 - 2 EMISSIONS CONTROLDR
EMISSIONS CONTROL (Continued)
Page 2569 of 2627
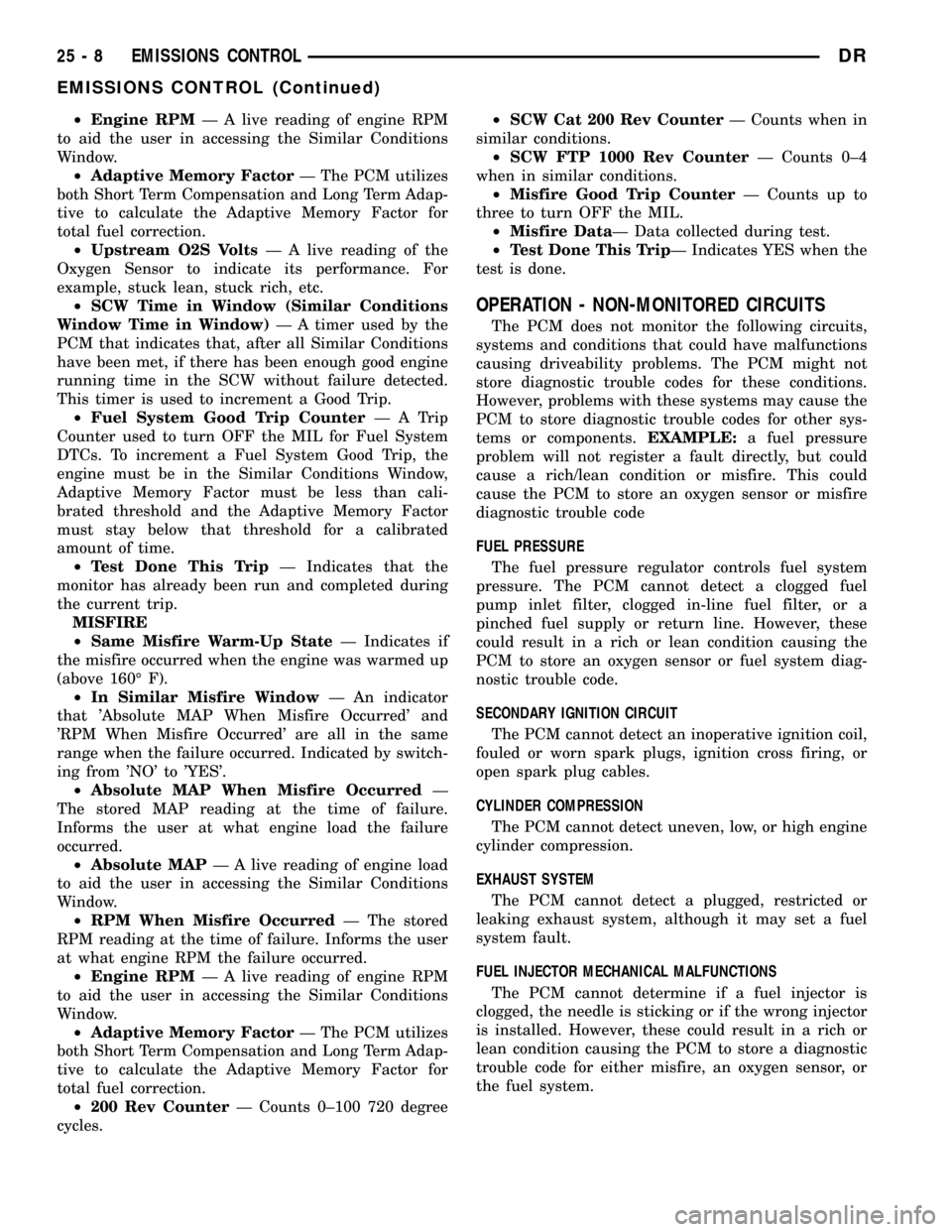
²Engine RPMÐ A live reading of engine RPM
to aid the user in accessing the Similar Conditions
Window.
²Adaptive Memory FactorÐ The PCM utilizes
both Short Term Compensation and Long Term Adap-
tive to calculate the Adaptive Memory Factor for
total fuel correction.
²Upstream O2S VoltsÐ A live reading of the
Oxygen Sensor to indicate its performance. For
example, stuck lean, stuck rich, etc.
²SCW Time in Window (Similar Conditions
Window Time in Window)Ð A timer used by the
PCM that indicates that, after all Similar Conditions
have been met, if there has been enough good engine
running time in the SCW without failure detected.
This timer is used to increment a Good Trip.
²Fuel System Good Trip CounterÐATrip
Counter used to turn OFF the MIL for Fuel System
DTCs. To increment a Fuel System Good Trip, the
engine must be in the Similar Conditions Window,
Adaptive Memory Factor must be less than cali-
brated threshold and the Adaptive Memory Factor
must stay below that threshold for a calibrated
amount of time.
²Test Done This TripÐ Indicates that the
monitor has already been run and completed during
the current trip.
MISFIRE
²Same Misfire Warm-Up StateÐ Indicates if
the misfire occurred when the engine was warmed up
(above 160É F).
²In Similar Misfire WindowÐ An indicator
that 'Absolute MAP When Misfire Occurred' and
'RPM When Misfire Occurred' are all in the same
range when the failure occurred. Indicated by switch-
ing from 'NO' to 'YES'.
²Absolute MAP When Misfire OccurredÐ
The stored MAP reading at the time of failure.
Informs the user at what engine load the failure
occurred.
²Absolute MAPÐ A live reading of engine load
to aid the user in accessing the Similar Conditions
Window.
²RPM When Misfire OccurredÐ The stored
RPM reading at the time of failure. Informs the user
at what engine RPM the failure occurred.
²Engine RPMÐ A live reading of engine RPM
to aid the user in accessing the Similar Conditions
Window.
²Adaptive Memory FactorÐ The PCM utilizes
both Short Term Compensation and Long Term Adap-
tive to calculate the Adaptive Memory Factor for
total fuel correction.
²200 Rev CounterÐ Counts 0±100 720 degree
cycles.²SCW Cat 200 Rev CounterÐ Counts when in
similar conditions.
²SCW FTP 1000 Rev CounterÐ Counts 0±4
when in similar conditions.
²Misfire Good Trip CounterÐ Counts up to
three to turn OFF the MIL.
²Misfire DataÐ Data collected during test.
²Test Done This TripÐ Indicates YES when the
test is done.
OPERATION - NON-MONITORED CIRCUITS
The PCM does not monitor the following circuits,
systems and conditions that could have malfunctions
causing driveability problems. The PCM might not
store diagnostic trouble codes for these conditions.
However, problems with these systems may cause the
PCM to store diagnostic trouble codes for other sys-
tems or components.EXAMPLE:a fuel pressure
problem will not register a fault directly, but could
cause a rich/lean condition or misfire. This could
cause the PCM to store an oxygen sensor or misfire
diagnostic trouble code
FUEL PRESSURE
The fuel pressure regulator controls fuel system
pressure. The PCM cannot detect a clogged fuel
pump inlet filter, clogged in-line fuel filter, or a
pinched fuel supply or return line. However, these
could result in a rich or lean condition causing the
PCM to store an oxygen sensor or fuel system diag-
nostic trouble code.
SECONDARY IGNITION CIRCUIT
The PCM cannot detect an inoperative ignition coil,
fouled or worn spark plugs, ignition cross firing, or
open spark plug cables.
CYLINDER COMPRESSION
The PCM cannot detect uneven, low, or high engine
cylinder compression.
EXHAUST SYSTEM
The PCM cannot detect a plugged, restricted or
leaking exhaust system, although it may set a fuel
system fault.
FUEL INJECTOR MECHANICAL MALFUNCTIONS
The PCM cannot determine if a fuel injector is
clogged, the needle is sticking or if the wrong injector
is installed. However, these could result in a rich or
lean condition causing the PCM to store a diagnostic
trouble code for either misfire, an oxygen sensor, or
the fuel system.
25 - 8 EMISSIONS CONTROLDR
EMISSIONS CONTROL (Continued)
Page 2594 of 2627
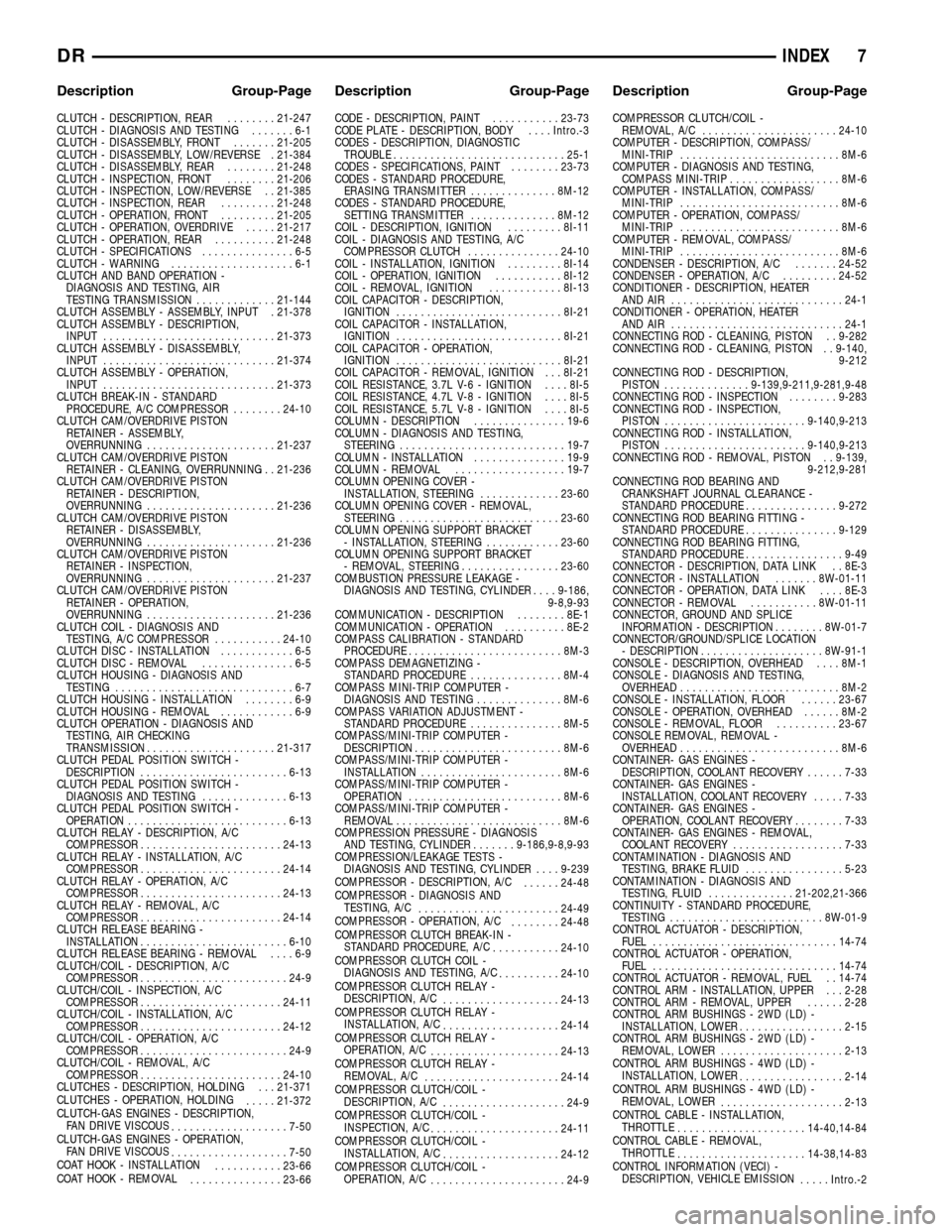
CLUTCH - DESCRIPTION, REAR........21-247
CLUTCH - DIAGNOSIS AND TESTING.......6-1
CLUTCH - DISASSEMBLY, FRONT.......21-205
CLUTCH - DISASSEMBLY, LOW/REVERSE . 21-384
CLUTCH - DISASSEMBLY, REAR........21-248
CLUTCH - INSPECTION, FRONT........21-206
CLUTCH - INSPECTION, LOW/REVERSE . . 21-385
CLUTCH - INSPECTION, REAR.........21-248
CLUTCH - OPERATION, FRONT.........21-205
CLUTCH - OPERATION, OVERDRIVE.....21-217
CLUTCH - OPERATION, REAR..........21-248
CLUTCH - SPECIFICATIONS...............6-5
CLUTCH - WARNING....................6-1
CLUTCH AND BAND OPERATION -
DIAGNOSIS AND TESTING, AIR
TESTING TRANSMISSION.............21-144
CLUTCH ASSEMBLY - ASSEMBLY, INPUT . 21-378
CLUTCH ASSEMBLY - DESCRIPTION,
INPUT............................21-373
CLUTCH ASSEMBLY - DISASSEMBLY,
INPUT............................21-374
CLUTCH ASSEMBLY - OPERATION,
INPUT............................21-373
CLUTCH BREAK-IN - STANDARD
PROCEDURE, A/C COMPRESSOR........24-10
CLUTCH CAM/OVERDRIVE PISTON
RETAINER - ASSEMBLY,
OVERRUNNING.....................21-237
CLUTCH CAM/OVERDRIVE PISTON
RETAINER - CLEANING, OVERRUNNING. . . 21-236
CLUTCH CAM/OVERDRIVE PISTON
RETAINER - DESCRIPTION,
OVERRUNNING.....................21-236
CLUTCH CAM/OVERDRIVE PISTON
RETAINER - DISASSEMBLY,
OVERRUNNING.....................21-236
CLUTCH CAM/OVERDRIVE PISTON
RETAINER - INSPECTION,
OVERRUNNING.....................21-237
CLUTCH CAM/OVERDRIVE PISTON
RETAINER - OPERATION,
OVERRUNNING.....................21-236
CLUTCH COIL - DIAGNOSIS AND
TESTING, A/C COMPRESSOR...........24-10
CLUTCH DISC - INSTALLATION............6-5
CLUTCH DISC - REMOVAL...............6-5
CLUTCH HOUSING - DIAGNOSIS AND
TESTING.............................6-7
CLUTCH HOUSING - INSTALLATION........6-9
CLUTCH HOUSING - REMOVAL............6-9
CLUTCH OPERATION - DIAGNOSIS AND
TESTING, AIR CHECKING
TRANSMISSION.....................21-317
CLUTCH PEDAL POSITION SWITCH -
DESCRIPTION........................6-13
CLUTCH PEDAL POSITION SWITCH -
DIAGNOSIS AND TESTING..............6-13
CLUTCH PEDAL POSITION SWITCH -
OPERATION..........................6-13
CLUTCH RELAY - DESCRIPTION, A/C
COMPRESSOR.......................24-13
CLUTCH RELAY - INSTALLATION, A/C
COMPRESSOR.......................24-14
CLUTCH RELAY - OPERATION, A/C
COMPRESSOR.......................24-13
CLUTCH RELAY - REMOVAL, A/C
COMPRESSOR.......................24-14
CLUTCH RELEASE BEARING -
INSTALLATION........................6-10
CLUTCH RELEASE BEARING - REMOVAL....6-9
CLUTCH/COIL - DESCRIPTION, A/C
COMPRESSOR........................24-9
CLUTCH/COIL - INSPECTION, A/C
COMPRESSOR.......................24-11
CLUTCH/COIL - INSTALLATION, A/C
COMPRESSOR.......................24-12
CLUTCH/COIL - OPERATION, A/C
COMPRESSOR........................24-9
CLUTCH/COIL - REMOVAL, A/C
COMPRESSOR.......................24-10
CLUTCHES - DESCRIPTION, HOLDING . . . 21-371
CLUTCHES - OPERATION, HOLDING
.....21-372
CLUTCH-GAS ENGINES - DESCRIPTION,
FAN DRIVE VISCOUS
...................7-50
CLUTCH-GAS ENGINES - OPERATION,
FAN DRIVE VISCOUS
...................7-50
COAT HOOK - INSTALLATION
...........23-66
COAT HOOK - REMOVAL
...............23-66CODE - DESCRIPTION, PAINT...........23-73
CODE PLATE - DESCRIPTION, BODY....Intro.-3
CODES - DESCRIPTION, DIAGNOSTIC
TROUBLE............................25-1
CODES - SPECIFICATIONS, PAINT........23-73
CODES - STANDARD PROCEDURE,
ERASING TRANSMITTER..............8M-12
CODES - STANDARD PROCEDURE,
SETTING TRANSMITTER..............8M-12
COIL - DESCRIPTION, IGNITION.........8I-11
COIL - DIAGNOSIS AND TESTING, A/C
COMPRESSOR CLUTCH...............24-10
COIL - INSTALLATION, IGNITION.........8I-14
COIL - OPERATION, IGNITION...........8I-12
COIL - REMOVAL, IGNITION............8I-13
COIL CAPACITOR - DESCRIPTION,
IGNITION...........................8I-21
COIL CAPACITOR - INSTALLATION,
IGNITION...........................8I-21
COIL CAPACITOR - OPERATION,
IGNITION...........................8I-21
COIL CAPACITOR - REMOVAL, IGNITION . . . 8I-21
COIL RESISTANCE, 3.7L V-6 - IGNITION....8I-5
COIL RESISTANCE, 4.7L V-8 - IGNITION....8I-5
COIL RESISTANCE, 5.7L V-8 - IGNITION....8I-5
COLUMN - DESCRIPTION...............19-6
COLUMN - DIAGNOSIS AND TESTING,
STEERING...........................19-7
COLUMN - INSTALLATION...............19-9
COLUMN - REMOVAL..................19-7
COLUMN OPENING COVER -
INSTALLATION, STEERING.............23-60
COLUMN OPENING COVER - REMOVAL,
STEERING..........................23-60
COLUMN OPENING SUPPORT BRACKET
- INSTALLATION, STEERING............23-60
COLUMN OPENING SUPPORT BRACKET
- REMOVAL, STEERING................23-60
COMBUSTION PRESSURE LEAKAGE -
DIAGNOSIS AND TESTING, CYLINDER....9-186,
9-8,9-93
COMMUNICATION - DESCRIPTION........8E-1
COMMUNICATION - OPERATION..........8E-2
COMPASS CALIBRATION - STANDARD
PROCEDURE.........................8M-3
COMPASS DEMAGNETIZING -
STANDARD PROCEDURE...............8M-4
COMPASS MINI-TRIP COMPUTER -
DIAGNOSIS AND TESTING..............8M-6
COMPASS VARIATION ADJUSTMENT -
STANDARD PROCEDURE...............8M-5
COMPASS/MINI-TRIP COMPUTER -
DESCRIPTION........................8M-6
COMPASS/MINI-TRIP COMPUTER -
INSTALLATION.......................8M-6
COMPASS/MINI-TRIP COMPUTER -
OPERATION.........................8M-6
COMPASS/MINI-TRIP COMPUTER -
REMOVAL...........................8M-6
COMPRESSION PRESSURE - DIAGNOSIS
AND TESTING, CYLINDER.......9-186,9-8,9-93
COMPRESSION/LEAKAGE TESTS -
DIAGNOSIS AND TESTING, CYLINDER....9-239
COMPRESSOR - DESCRIPTION, A/C
......24-48
COMPRESSOR - DIAGNOSIS AND
TESTING, A/C
.......................24-49
COMPRESSOR - OPERATION, A/C
........24-48
COMPRESSOR CLUTCH BREAK-IN -
STANDARD PROCEDURE, A/C
...........24-10
COMPRESSOR CLUTCH COIL -
DIAGNOSIS AND TESTING, A/C
..........24-10
COMPRESSOR CLUTCH RELAY -
DESCRIPTION, A/C
...................24-13
COMPRESSOR CLUTCH RELAY -
INSTALLATION, A/C
...................24-14
COMPRESSOR CLUTCH RELAY -
OPERATION, A/C
.....................24-13
COMPRESSOR CLUTCH RELAY -
REMOVAL, A/C
......................24-14
COMPRESSOR CLUTCH/COIL -
DESCRIPTION, A/C
....................24-9
COMPRESSOR CLUTCH/COIL -
INSPECTION, A/C
.....................24-11
COMPRESSOR CLUTCH/COIL -
INSTALLATION, A/C
...................24-12
COMPRESSOR CLUTCH/COIL -
OPERATION, A/C
......................24-9COMPRESSOR CLUTCH/COIL -
REMOVAL, A/C......................24-10
COMPUTER - DESCRIPTION, COMPASS/
MINI-TRIP..........................8M-6
COMPUTER - DIAGNOSIS AND TESTING,
COMPASS MINI-TRIP..................8M-6
COMPUTER - INSTALLATION, COMPASS/
MINI-TRIP..........................8M-6
COMPUTER - OPERATION, COMPASS/
MINI-TRIP..........................8M-6
COMPUTER - REMOVAL, COMPASS/
MINI-TRIP..........................8M-6
CONDENSER - DESCRIPTION, A/C.......24-52
CONDENSER - OPERATION, A/C.........24-52
CONDITIONER - DESCRIPTION, HEATER
AND AIR ............................24-1
CONDITIONER - OPERATION, HEATER
AND AIR ............................24-1
CONNECTING ROD - CLEANING, PISTON . . 9-282
CONNECTING ROD - CLEANING, PISTON . . 9-140,
9-212
CONNECTING ROD - DESCRIPTION,
PISTON..............9-139,9-211,9-281,9-48
CONNECTING ROD - INSPECTION........9-283
CONNECTING ROD - INSPECTION,
PISTON.......................9-140,9-213
CONNECTING ROD - INSTALLATION,
PISTON.......................9-140,9-213
CONNECTING ROD - REMOVAL, PISTON . . 9-139,
9-212,9-281
CONNECTING ROD BEARING AND
CRANKSHAFT JOURNAL CLEARANCE -
STANDARD PROCEDURE................9-272
CONNECTING ROD BEARING FITTING -
STANDARD PROCEDURE...............9-129
CONNECTING ROD BEARING FITTING,
STANDARD PROCEDURE................9-49
CONNECTOR - DESCRIPTION, DATA LINK . . 8E-3
CONNECTOR - INSTALLATION.......8W-01-11
CONNECTOR - OPERATION, DATA LINK....8E-3
CONNECTOR - REMOVAL...........8W-01-11
CONNECTOR, GROUND AND SPLICE
INFORMATION - DESCRIPTION........8W-01-7
CONNECTOR/GROUND/SPLICE LOCATION
- DESCRIPTION....................8W-91-1
CONSOLE - DESCRIPTION, OVERHEAD....8M-1
CONSOLE - DIAGNOSIS AND TESTING,
OVERHEAD..........................8M-2
CONSOLE - INSTALLATION, FLOOR......23-67
CONSOLE - OPERATION, OVERHEAD......8M-2
CONSOLE - REMOVAL, FLOOR..........23-67
CONSOLE REMOVAL, REMOVAL -
OVERHEAD..........................8M-6
CONTAINER- GAS ENGINES -
DESCRIPTION, COOLANT RECOVERY......7-33
CONTAINER- GAS ENGINES -
INSTALLATION, COOLANT RECOVERY.....7-33
CONTAINER- GAS ENGINES -
OPERATION, COOLANT RECOVERY........7-33
CONTAINER- GAS ENGINES - REMOVAL,
COOLANT RECOVERY..................7-33
CONTAMINATION - DIAGNOSIS AND
TESTING, BRAKE FLUID................5-23
CONTAMINATION - DIAGNOSIS AND
TESTING, FLUID..............21-202,21-366
CONTINUITY - STANDARD PROCEDURE,
TESTING.........................8W-01-9
CONTROL ACTUATOR - DESCRIPTION,
FUEL..............................14-74
CONTROL ACTUATOR - OPERATION,
FUEL..............................14-74
CONTROL ACTUATOR - REMOVAL, FUEL . . 14-74
CONTROL ARM - INSTALLATION, UPPER . . . 2-28
CONTROL ARM - REMOVAL, UPPER......2-28
CONTROL ARM BUSHINGS - 2WD (LD) -
INSTALLATION, LOWER.................2-15
CONTROL ARM BUSHINGS - 2WD (LD) -
REMOVAL, LOWER....................2-13
CONTROL ARM BUSHINGS - 4WD (LD) -
INSTALLATION, LOWER
.................2-14
CONTROL ARM BUSHINGS - 4WD (LD) -
REMOVAL, LOWER
....................2-13
CONTROL CABLE - INSTALLATION,
THROTTLE
.....................14-40,14-84
CONTROL CABLE - REMOVAL,
THROTTLE
.....................14-38,14-83
CONTROL INFORMATION (VECI) -
DESCRIPTION, VEHICLE EMISSION
.....Intro.-2
DRINDEX 7
Description Group-Page Description Group-Page Description Group-Page
Page 2596 of 2627
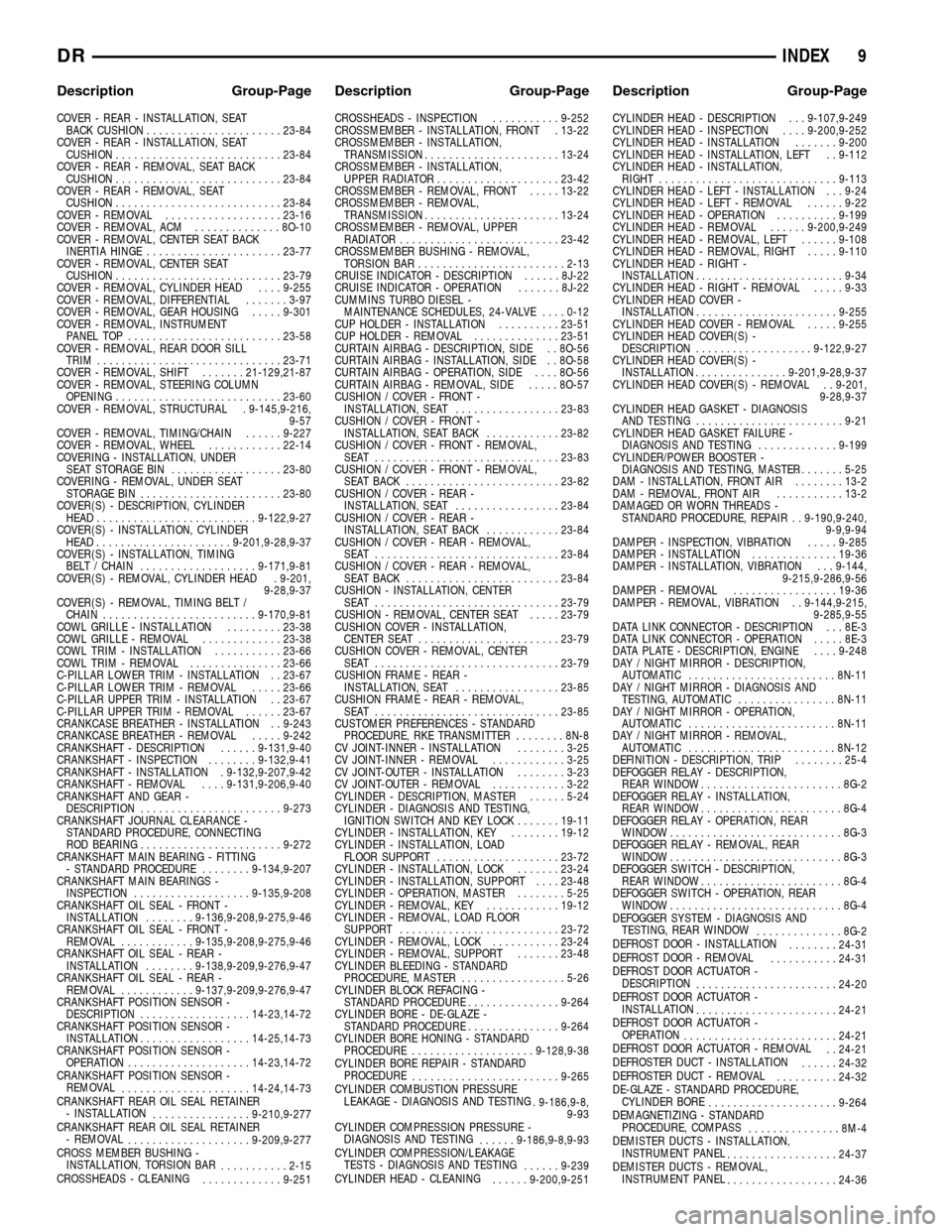
COVER - REAR - INSTALLATION, SEAT
BACK CUSHION......................23-84
COVER - REAR - INSTALLATION, SEAT
CUSHION...........................23-84
COVER - REAR - REMOVAL, SEAT BACK
CUSHION...........................23-84
COVER - REAR - REMOVAL, SEAT
CUSHION...........................23-84
COVER - REMOVAL...................23-16
COVER - REMOVAL, ACM..............8O-10
COVER - REMOVAL, CENTER SEAT BACK
INERTIA HINGE......................23-77
COVER - REMOVAL, CENTER SEAT
CUSHION...........................23-79
COVER - REMOVAL, CYLINDER HEAD....9-255
COVER - REMOVAL, DIFFERENTIAL.......3-97
COVER - REMOVAL, GEAR HOUSING.....9-301
COVER - REMOVAL, INSTRUMENT
PANEL TOP.........................23-58
COVER - REMOVAL, REAR DOOR SILL
TRIM..............................23-71
COVER - REMOVAL, SHIFT.......21-129,21-87
COVER - REMOVAL, STEERING COLUMN
OPENING...........................23-60
COVER - REMOVAL, STRUCTURAL . 9-145,9-216,
9-57
COVER - REMOVAL, TIMING/CHAIN......9-227
COVER - REMOVAL, WHEEL............22-14
COVERING - INSTALLATION, UNDER
SEAT STORAGE BIN..................23-80
COVERING - REMOVAL, UNDER SEAT
STORAGE BIN.......................23-80
COVER(S) - DESCRIPTION, CYLINDER
HEAD..........................9-122,9-27
COVER(S) - INSTALLATION, CYLINDER
HEAD......................9-201,9-28,9-37
COVER(S) - INSTALLATION, TIMING
BELT / CHAIN...................9-171,9-81
COVER(S) - REMOVAL, CYLINDER HEAD . 9-201,
9-28,9-37
COVER(S) - REMOVAL, TIMING BELT /
CHAIN.........................9-170,9-81
COWL GRILLE - INSTALLATION.........23-38
COWL GRILLE - REMOVAL.............23-38
COWL TRIM - INSTALLATION...........23-66
COWL TRIM - REMOVAL...............23-66
C-PILLAR LOWER TRIM - INSTALLATION . . 23-67
C-PILLAR LOWER TRIM - REMOVAL.....23-66
C-PILLAR UPPER TRIM - INSTALLATION . . 23-67
C-PILLAR UPPER TRIM - REMOVAL......23-67
CRANKCASE BREATHER - INSTALLATION . . 9-243
CRANKCASE BREATHER - REMOVAL.....9-242
CRANKSHAFT - DESCRIPTION......9-131,9-40
CRANKSHAFT - INSPECTION........9-132,9-41
CRANKSHAFT - INSTALLATION . 9-132,9-207,9-42
CRANKSHAFT - REMOVAL....9-131,9-206,9-40
CRANKSHAFT AND GEAR -
DESCRIPTION.......................9-273
CRANKSHAFT JOURNAL CLEARANCE -
STANDARD PROCEDURE, CONNECTING
ROD BEARING.......................9-272
CRANKSHAFT MAIN BEARING - FITTING
- STANDARD PROCEDURE........9-134,9-207
CRANKSHAFT MAIN BEARINGS -
INSPECTION...................9-135,9-208
CRANKSHAFT OIL SEAL - FRONT -
INSTALLATION........9-136,9-208,9-275,9-46
CRANKSHAFT OIL SEAL - FRONT -
REMOVAL............9-135,9-208,9-275,9-46
CRANKSHAFT OIL SEAL - REAR -
INSTALLATION........9-138,9-209,9-276,9-47
CRANKSHAFT OIL SEAL - REAR -
REMOVAL............9-137,9-209,9-276,9-47
CRANKSHAFT POSITION SENSOR -
DESCRIPTION..................14-23,14-72
CRANKSHAFT POSITION SENSOR -
INSTALLATION..................14-25,14-73
CRANKSHAFT POSITION SENSOR -
OPERATION....................14-23,14-72
CRANKSHAFT POSITION SENSOR -
REMOVAL
.....................14-24,14-73
CRANKSHAFT REAR OIL SEAL RETAINER
- INSTALLATION
................9-210,9-277
CRANKSHAFT REAR OIL SEAL RETAINER
- REMOVAL
....................9-209,9-277
CROSS MEMBER BUSHING -
INSTALLATION, TORSION BAR
...........2-15
CROSSHEADS - CLEANING
.............9-251CROSSHEADS - INSPECTION...........9-252
CROSSMEMBER - INSTALLATION, FRONT . 13-22
CROSSMEMBER - INSTALLATION,
TRANSMISSION......................13-24
CROSSMEMBER - INSTALLATION,
UPPER RADIATOR....................23-42
CROSSMEMBER - REMOVAL, FRONT.....13-22
CROSSMEMBER - REMOVAL,
TRANSMISSION......................13-24
CROSSMEMBER - REMOVAL, UPPER
RADIATOR..........................23-42
CROSSMEMBER BUSHING - REMOVAL,
TORSION BAR........................2-13
CRUISE INDICATOR - DESCRIPTION......8J-22
CRUISE INDICATOR - OPERATION.......8J-22
CUMMINS TURBO DIESEL -
MAINTENANCE SCHEDULES, 24-VALVE....0-12
CUP HOLDER - INSTALLATION..........23-51
CUP HOLDER - REMOVAL..............23-51
CURTAIN AIRBAG - DESCRIPTION, SIDE . . 8O-56
CURTAIN AIRBAG - INSTALLATION, SIDE . . 8O-58
CURTAIN AIRBAG - OPERATION, SIDE....8O-56
CURTAIN AIRBAG - REMOVAL, SIDE.....8O-57
CUSHION / COVER - FRONT -
INSTALLATION, SEAT.................23-83
CUSHION / COVER - FRONT -
INSTALLATION, SEAT BACK............23-82
CUSHION / COVER - FRONT - REMOVAL,
SEAT ..............................23-83
CUSHION / COVER - FRONT - REMOVAL,
SEAT BACK.........................23-82
CUSHION / COVER - REAR -
INSTALLATION, SEAT.................23-84
CUSHION / COVER - REAR -
INSTALLATION, SEAT BACK............23-84
CUSHION / COVER - REAR - REMOVAL,
SEAT ..............................23-84
CUSHION / COVER - REAR - REMOVAL,
SEAT BACK.........................23-84
CUSHION - INSTALLATION, CENTER
SEAT ..............................23-79
CUSHION - REMOVAL, CENTER SEAT.....23-79
CUSHION COVER - INSTALLATION,
CENTER SEAT.......................23-79
CUSHION COVER - REMOVAL, CENTER
SEAT ..............................23-79
CUSHION FRAME - REAR -
INSTALLATION, SEAT.................23-85
CUSHION FRAME - REAR - REMOVAL,
SEAT ..............................23-85
CUSTOMER PREFERENCES - STANDARD
PROCEDURE, RKE TRANSMITTER........8N-8
CV JOINT-INNER - INSTALLATION........3-25
CV JOINT-INNER - REMOVAL............3-25
CV JOINT-OUTER - INSTALLATION........3-23
CV JOINT-OUTER - REMOVAL............3-22
CYLINDER - DESCRIPTION, MASTER......5-24
CYLINDER - DIAGNOSIS AND TESTING,
IGNITION SWITCH AND KEY LOCK.......19-11
CYLINDER - INSTALLATION, KEY........19-12
CYLINDER - INSTALLATION, LOAD
FLOOR SUPPORT....................23-72
CYLINDER - INSTALLATION, LOCK.......23-24
CYLINDER - INSTALLATION, SUPPORT....23-48
CYLINDER - OPERATION, MASTER........5-25
CYLINDER - REMOVAL, KEY............19-12
CYLINDER - REMOVAL, LOAD FLOOR
SUPPORT..........................23-72
CYLINDER - REMOVAL, LOCK...........23-24
CYLINDER - REMOVAL, SUPPORT.......23-48
CYLINDER BLEEDING - STANDARD
PROCEDURE, MASTER.................5-26
CYLINDER BLOCK REFACING -
STANDARD PROCEDURE...............9-264
CYLINDER BORE - DE-GLAZE -
STANDARD PROCEDURE...............9-264
CYLINDER BORE HONING - STANDARD
PROCEDURE....................9-128,9-38
CYLINDER BORE REPAIR - STANDARD
PROCEDURE
........................9-265
CYLINDER COMBUSTION PRESSURE
LEAKAGE - DIAGNOSIS AND TESTING
. 9-186,9-8,
9-93
CYLINDER COMPRESSION PRESSURE -
DIAGNOSIS AND TESTING
......9-186,9-8,9-93
CYLINDER COMPRESSION/LEAKAGE
TESTS - DIAGNOSIS AND TESTING
......9-239
CYLINDER HEAD - CLEANING
......9-200,9-251CYLINDER HEAD - DESCRIPTION . . . 9-107,9-249
CYLINDER HEAD - INSPECTION....9-200,9-252
CYLINDER HEAD - INSTALLATION.......9-200
CYLINDER HEAD - INSTALLATION, LEFT . . 9-112
CYLINDER HEAD - INSTALLATION,
RIGHT.............................9-113
CYLINDER HEAD - LEFT - INSTALLATION . . . 9-24
CYLINDER HEAD - LEFT - REMOVAL......9-22
CYLINDER HEAD - OPERATION..........9-199
CYLINDER HEAD - REMOVAL......9-200,9-249
CYLINDER HEAD - REMOVAL, LEFT......9-108
CYLINDER HEAD - REMOVAL, RIGHT.....9-110
CYLINDER HEAD - RIGHT -
INSTALLATION........................9-34
CYLINDER HEAD - RIGHT - REMOVAL.....9-33
CYLINDER HEAD COVER -
INSTALLATION.......................9-255
CYLINDER HEAD COVER - REMOVAL.....9-255
CYLINDER HEAD COVER(S) -
DESCRIPTION...................9-122,9-27
CYLINDER HEAD COVER(S) -
INSTALLATION...............9-201,9-28,9-37
CYLINDER HEAD COVER(S) - REMOVAL . . 9-201,
9-28,9-37
CYLINDER HEAD GASKET - DIAGNOSIS
AND TESTING........................9-21
CYLINDER HEAD GASKET FAILURE -
DIAGNOSIS AND TESTING.............9-199
CYLINDER/POWER BOOSTER -
DIAGNOSIS AND TESTING, MASTER........5-25
DAM - INSTALLATION, FRONT AIR........13-2
DAM - REMOVAL, FRONT AIR...........13-2
DAMAGED OR WORN THREADS -
STANDARD PROCEDURE, REPAIR . . 9-190,9-240,
9-9,9-94
DAMPER - INSPECTION, VIBRATION.....9-285
DAMPER - INSTALLATION..............19-36
DAMPER - INSTALLATION, VIBRATION . . . 9-144,
9-215,9-286,9-56
DAMPER - REMOVAL.................19-36
DAMPER - REMOVAL, VIBRATION . . 9-144,9-215,
9-285,9-55
DATA LINK CONNECTOR - DESCRIPTION . . . 8E-3
DATA LINK CONNECTOR - OPERATION.....8E-3
DATA PLATE - DESCRIPTION, ENGINE....9-248
DAY / NIGHT MIRROR - DESCRIPTION,
AUTOMATIC........................8N-11
DAY / NIGHT MIRROR - DIAGNOSIS AND
TESTING, AUTOMATIC................8N-11
DAY / NIGHT MIRROR - OPERATION,
AUTOMATIC........................8N-11
DAY / NIGHT MIRROR - REMOVAL,
AUTOMATIC........................8N-12
DEFINITION - DESCRIPTION, TRIP........25-4
DEFOGGER RELAY - DESCRIPTION,
REAR WINDOW.......................8G-2
DEFOGGER RELAY - INSTALLATION,
REAR WINDOW.......................8G-4
DEFOGGER RELAY - OPERATION, REAR
WINDOW............................8G-3
DEFOGGER RELAY - REMOVAL, REAR
WINDOW............................8G-3
DEFOGGER SWITCH - DESCRIPTION,
REAR WINDOW.......................8G-4
DEFOGGER SWITCH - OPERATION, REAR
WINDOW............................8G-4
DEFOGGER SYSTEM - DIAGNOSIS AND
TESTING, REAR WINDOW
..............8G-2
DEFROST DOOR - INSTALLATION
........24-31
DEFROST DOOR - REMOVAL
...........24-31
DEFROST DOOR ACTUATOR -
DESCRIPTION
.......................24-20
DEFROST DOOR ACTUATOR -
INSTALLATION
.......................24-21
DEFROST DOOR ACTUATOR -
OPERATION
.........................24-21
DEFROST DOOR ACTUATOR - REMOVAL
. . 24-21
DEFROSTER DUCT - INSTALLATION
......24-32
DEFROSTER DUCT - REMOVAL
..........24-32
DE-GLAZE - STANDARD PROCEDURE,
CYLINDER BORE
.....................9-264
DEMAGNETIZING - STANDARD
PROCEDURE, COMPASS
...............8M-4
DEMISTER DUCTS - INSTALLATION,
INSTRUMENT PANEL
..................24-37
DEMISTER DUCTS - REMOVAL,
INSTRUMENT PANEL
..................24-36
DRINDEX 9
Description Group-Page Description Group-Page Description Group-Page
Page 2598 of 2627
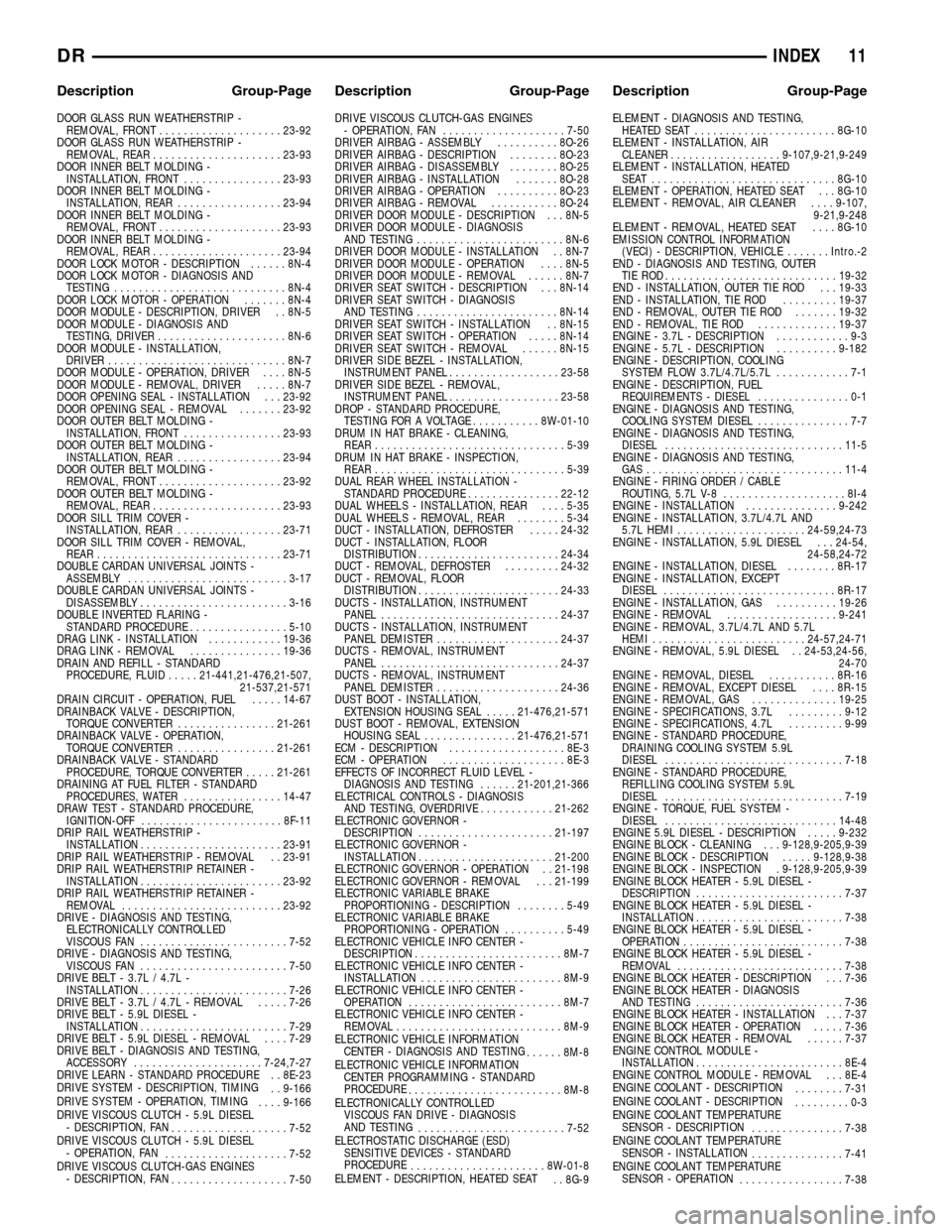
DOOR GLASS RUN WEATHERSTRIP -
REMOVAL, FRONT....................23-92
DOOR GLASS RUN WEATHERSTRIP -
REMOVAL, REAR.....................23-93
DOOR INNER BELT MOLDING -
INSTALLATION, FRONT................23-93
DOOR INNER BELT MOLDING -
INSTALLATION, REAR.................23-94
DOOR INNER BELT MOLDING -
REMOVAL, FRONT....................23-93
DOOR INNER BELT MOLDING -
REMOVAL, REAR.....................23-94
DOOR LOCK MOTOR - DESCRIPTION......8N-4
DOOR LOCK MOTOR - DIAGNOSIS AND
TESTING............................8N-4
DOOR LOCK MOTOR - OPERATION.......8N-4
DOOR MODULE - DESCRIPTION, DRIVER . . 8N-5
DOOR MODULE - DIAGNOSIS AND
TESTING, DRIVER.....................8N-6
DOOR MODULE - INSTALLATION,
DRIVER.............................8N-7
DOOR MODULE - OPERATION, DRIVER....8N-5
DOOR MODULE - REMOVAL, DRIVER.....8N-7
DOOR OPENING SEAL - INSTALLATION . . . 23-92
DOOR OPENING SEAL - REMOVAL.......23-92
DOOR OUTER BELT MOLDING -
INSTALLATION, FRONT................23-93
DOOR OUTER BELT MOLDING -
INSTALLATION, REAR.................23-94
DOOR OUTER BELT MOLDING -
REMOVAL, FRONT....................23-92
DOOR OUTER BELT MOLDING -
REMOVAL, REAR.....................23-93
DOOR SILL TRIM COVER -
INSTALLATION, REAR.................23-71
DOOR SILL TRIM COVER - REMOVAL,
REAR..............................23-71
DOUBLE CARDAN UNIVERSAL JOINTS -
ASSEMBLY..........................3-17
DOUBLE CARDAN UNIVERSAL JOINTS -
DISASSEMBLY........................3-16
DOUBLE INVERTED FLARING -
STANDARD PROCEDURE................5-10
DRAG LINK - INSTALLATION............19-36
DRAG LINK - REMOVAL...............19-36
DRAIN AND REFILL - STANDARD
PROCEDURE, FLUID.....21-441,21-476,21-507,
21-537,21-571
DRAIN CIRCUIT - OPERATION, FUEL.....14-67
DRAINBACK VALVE - DESCRIPTION,
TORQUE CONVERTER................21-261
DRAINBACK VALVE - OPERATION,
TORQUE CONVERTER................21-261
DRAINBACK VALVE - STANDARD
PROCEDURE, TORQUE CONVERTER.....21-261
DRAINING AT FUEL FILTER - STANDARD
PROCEDURES, WATER................14-47
DRAW TEST - STANDARD PROCEDURE,
IGNITION-OFF.......................8F-11
DRIP RAIL WEATHERSTRIP -
INSTALLATION.......................23-91
DRIP RAIL WEATHERSTRIP - REMOVAL . . 23-91
DRIP RAIL WEATHERSTRIP RETAINER -
INSTALLATION.......................23-92
DRIP RAIL WEATHERSTRIP RETAINER -
REMOVAL..........................23-92
DRIVE - DIAGNOSIS AND TESTING,
ELECTRONICALLY CONTROLLED
VISCOUS FAN........................7-52
DRIVE - DIAGNOSIS AND TESTING,
VISCOUS FAN........................7-50
DRIVE BELT - 3.7L / 4.7L -
INSTALLATION........................7-26
DRIVE BELT - 3.7L / 4.7L - REMOVAL.....7-26
DRIVE BELT - 5.9L DIESEL -
INSTALLATION........................7-29
DRIVE BELT - 5.9L DIESEL - REMOVAL....7-29
DRIVE BELT - DIAGNOSIS AND TESTING,
ACCESSORY.....................7-24,7-27
DRIVE LEARN - STANDARD PROCEDURE . . 8E-23
DRIVE SYSTEM - DESCRIPTION, TIMING
. . 9-166
DRIVE SYSTEM - OPERATION, TIMING
....9-166
DRIVE VISCOUS CLUTCH - 5.9L DIESEL
- DESCRIPTION, FAN
...................7-52
DRIVE VISCOUS CLUTCH - 5.9L DIESEL
- OPERATION, FAN
....................7-52
DRIVE VISCOUS CLUTCH-GAS ENGINES
- DESCRIPTION, FAN
...................7-50DRIVE VISCOUS CLUTCH-GAS ENGINES
- OPERATION, FAN....................7-50
DRIVER AIRBAG - ASSEMBLY..........8O-26
DRIVER AIRBAG - DESCRIPTION........8O-23
DRIVER AIRBAG - DISASSEMBLY........8O-25
DRIVER AIRBAG - INSTALLATION.......8O-28
DRIVER AIRBAG - OPERATION..........8O-23
DRIVER AIRBAG - REMOVAL...........8O-24
DRIVER DOOR MODULE - DESCRIPTION . . . 8N-5
DRIVER DOOR MODULE - DIAGNOSIS
AND TESTING........................8N-6
DRIVER DOOR MODULE - INSTALLATION . . 8N-7
DRIVER DOOR MODULE - OPERATION....8N-5
DRIVER DOOR MODULE - REMOVAL......8N-7
DRIVER SEAT SWITCH - DESCRIPTION . . . 8N-14
DRIVER SEAT SWITCH - DIAGNOSIS
AND TESTING.......................8N-14
DRIVER SEAT SWITCH - INSTALLATION . . 8N-15
DRIVER SEAT SWITCH - OPERATION.....8N-14
DRIVER SEAT SWITCH - REMOVAL......8N-15
DRIVER SIDE BEZEL - INSTALLATION,
INSTRUMENT PANEL..................23-58
DRIVER SIDE BEZEL - REMOVAL,
INSTRUMENT PANEL..................23-58
DROP - STANDARD PROCEDURE,
TESTING FOR A VOLTAGE...........8W-01-10
DRUM IN HAT BRAKE - CLEANING,
REAR...............................5-39
DRUM IN HAT BRAKE - INSPECTION,
REAR...............................5-39
DUAL REAR WHEEL INSTALLATION -
STANDARD PROCEDURE...............22-12
DUAL WHEELS - INSTALLATION, REAR....5-35
DUAL WHEELS - REMOVAL, REAR........5-34
DUCT - INSTALLATION, DEFROSTER.....24-32
DUCT - INSTALLATION, FLOOR
DISTRIBUTION.......................24-34
DUCT - REMOVAL, DEFROSTER.........24-32
DUCT - REMOVAL, FLOOR
DISTRIBUTION.......................24-33
DUCTS - INSTALLATION, INSTRUMENT
PANEL.............................24-37
DUCTS - INSTALLATION, INSTRUMENT
PANEL DEMISTER....................24-37
DUCTS - REMOVAL, INSTRUMENT
PANEL.............................24-37
DUCTS - REMOVAL, INSTRUMENT
PANEL DEMISTER....................24-36
DUST BOOT - INSTALLATION,
EXTENSION HOUSING SEAL.....21-476,21-571
DUST BOOT - REMOVAL, EXTENSION
HOUSING SEAL...............21-476,21-571
ECM - DESCRIPTION...................8E-3
ECM - OPERATION....................8E-3
EFFECTS OF INCORRECT FLUID LEVEL -
DIAGNOSIS AND TESTING......21-201,21-366
ELECTRICAL CONTROLS - DIAGNOSIS
AND TESTING, OVERDRIVE............21-262
ELECTRONIC GOVERNOR -
DESCRIPTION......................21-197
ELECTRONIC GOVERNOR -
INSTALLATION......................21-200
ELECTRONIC GOVERNOR - OPERATION . . 21-198
ELECTRONIC GOVERNOR - REMOVAL . . . 21-199
ELECTRONIC VARIABLE BRAKE
PROPORTIONING - DESCRIPTION........5-49
ELECTRONIC VARIABLE BRAKE
PROPORTIONING - OPERATION..........5-49
ELECTRONIC VEHICLE INFO CENTER -
DESCRIPTION........................8M-7
ELECTRONIC VEHICLE INFO CENTER -
INSTALLATION.......................8M-9
ELECTRONIC VEHICLE INFO CENTER -
OPERATION.........................8M-7
ELECTRONIC VEHICLE INFO CENTER -
REMOVAL...........................8M-9
ELECTRONIC VEHICLE INFORMATION
CENTER - DIAGNOSIS AND TESTING
......8M-8
ELECTRONIC VEHICLE INFORMATION
CENTER PROGRAMMING - STANDARD
PROCEDURE
.........................8M-8
ELECTRONICALLY CONTROLLED
VISCOUS FAN DRIVE - DIAGNOSIS
AND TESTING
........................7-52
ELECTROSTATIC DISCHARGE (ESD)
SENSITIVE DEVICES - STANDARD
PROCEDURE
......................8W-01-8
ELEMENT - DESCRIPTION, HEATED SEAT
. . 8G-9ELEMENT - DIAGNOSIS AND TESTING,
HEATED SEAT .......................8G-10
ELEMENT - INSTALLATION, AIR
CLEANER..................9-107,9-21,9-249
ELEMENT - INSTALLATION, HEATED
SEAT ..............................8G-10
ELEMENT - OPERATION, HEATED SEAT . . . 8G-10
ELEMENT - REMOVAL, AIR CLEANER....9-107,
9-21,9-248
ELEMENT - REMOVAL, HEATED SEAT....8G-10
EMISSION CONTROL INFORMATION
(VECI) - DESCRIPTION, VEHICLE.......Intro.-2
END - DIAGNOSIS AND TESTING, OUTER
TIE ROD............................19-32
END - INSTALLATION, OUTER TIE ROD . . . 19-33
END - INSTALLATION, TIE ROD.........19-37
END - REMOVAL, OUTER TIE ROD.......19-32
END - REMOVAL, TIE ROD.............19-37
ENGINE - 3.7L - DESCRIPTION............9-3
ENGINE - 5.7L - DESCRIPTION..........9-182
ENGINE - DESCRIPTION, COOLING
SYSTEM FLOW 3.7L/4.7L/5.7L............7-1
ENGINE - DESCRIPTION, FUEL
REQUIREMENTS - DIESEL...............0-1
ENGINE - DIAGNOSIS AND TESTING,
COOLING SYSTEM DIESEL...............7-7
ENGINE - DIAGNOSIS AND TESTING,
DIESEL.............................11-5
ENGINE - DIAGNOSIS AND TESTING,
GAS................................11-4
ENGINE - FIRING ORDER / CABLE
ROUTING, 5.7L V-8....................8I-4
ENGINE - INSTALLATION...............9-242
ENGINE - INSTALLATION, 3.7L/4.7L AND
5.7L HEMI.....................24-59,24-73
ENGINE - INSTALLATION, 5.9L DIESEL . . . 24-54,
24-58,24-72
ENGINE - INSTALLATION, DIESEL........8R-17
ENGINE - INSTALLATION, EXCEPT
DIESEL............................8R-17
ENGINE - INSTALLATION, GAS..........19-26
ENGINE - REMOVAL..................9-241
ENGINE - REMOVAL, 3.7L/4.7L AND 5.7L
HEMI.........................24-57,24-71
ENGINE - REMOVAL, 5.9L DIESEL . . 24-53,24-56,
24-70
ENGINE - REMOVAL, DIESEL...........8R-16
ENGINE - REMOVAL, EXCEPT DIESEL....8R-15
ENGINE - REMOVAL, GAS..............19-25
ENGINE - SPECIFICATIONS, 3.7L.........9-12
ENGINE - SPECIFICATIONS, 4.7L.........9-99
ENGINE - STANDARD PROCEDURE,
DRAINING COOLING SYSTEM 5.9L
DIESEL.............................7-18
ENGINE - STANDARD PROCEDURE,
REFILLING COOLING SYSTEM 5.9L
DIESEL.............................7-19
ENGINE - TORQUE, FUEL SYSTEM -
DIESEL............................14-48
ENGINE 5.9L DIESEL - DESCRIPTION.....9-232
ENGINE BLOCK - CLEANING . . . 9-128,9-205,9-39
ENGINE BLOCK - DESCRIPTION.....9-128,9-38
ENGINE BLOCK - INSPECTION . 9-128,9-205,9-39
ENGINE BLOCK HEATER - 5.9L DIESEL -
DESCRIPTION........................7-37
ENGINE BLOCK HEATER - 5.9L DIESEL -
INSTALLATION........................7-38
ENGINE BLOCK HEATER - 5.9L DIESEL -
OPERATION..........................7-38
ENGINE BLOCK HEATER - 5.9L DIESEL -
REMOVAL...........................7-38
ENGINE BLOCK HEATER - DESCRIPTION . . . 7-36
ENGINE BLOCK HEATER - DIAGNOSIS
AND TESTING........................7-36
ENGINE BLOCK HEATER - INSTALLATION . . . 7-37
ENGINE BLOCK HEATER - OPERATION.....7-36
ENGINE BLOCK HEATER - REMOVAL......7-37
ENGINE CONTROL MODULE -
INSTALLATION........................8E-4
ENGINE CONTROL MODULE - REMOVAL . . . 8E-4
ENGINE COOLANT - DESCRIPTION
........7-31
ENGINE COOLANT - DESCRIPTION
.........0-3
ENGINE COOLANT TEMPERATURE
SENSOR - DESCRIPTION
...............7-38
ENGINE COOLANT TEMPERATURE
SENSOR - INSTALLATION
...............7-41
ENGINE COOLANT TEMPERATURE
SENSOR - OPERATION
.................7-38
DRINDEX 11
Description Group-Page Description Group-Page Description Group-Page
Page 2603 of 2627
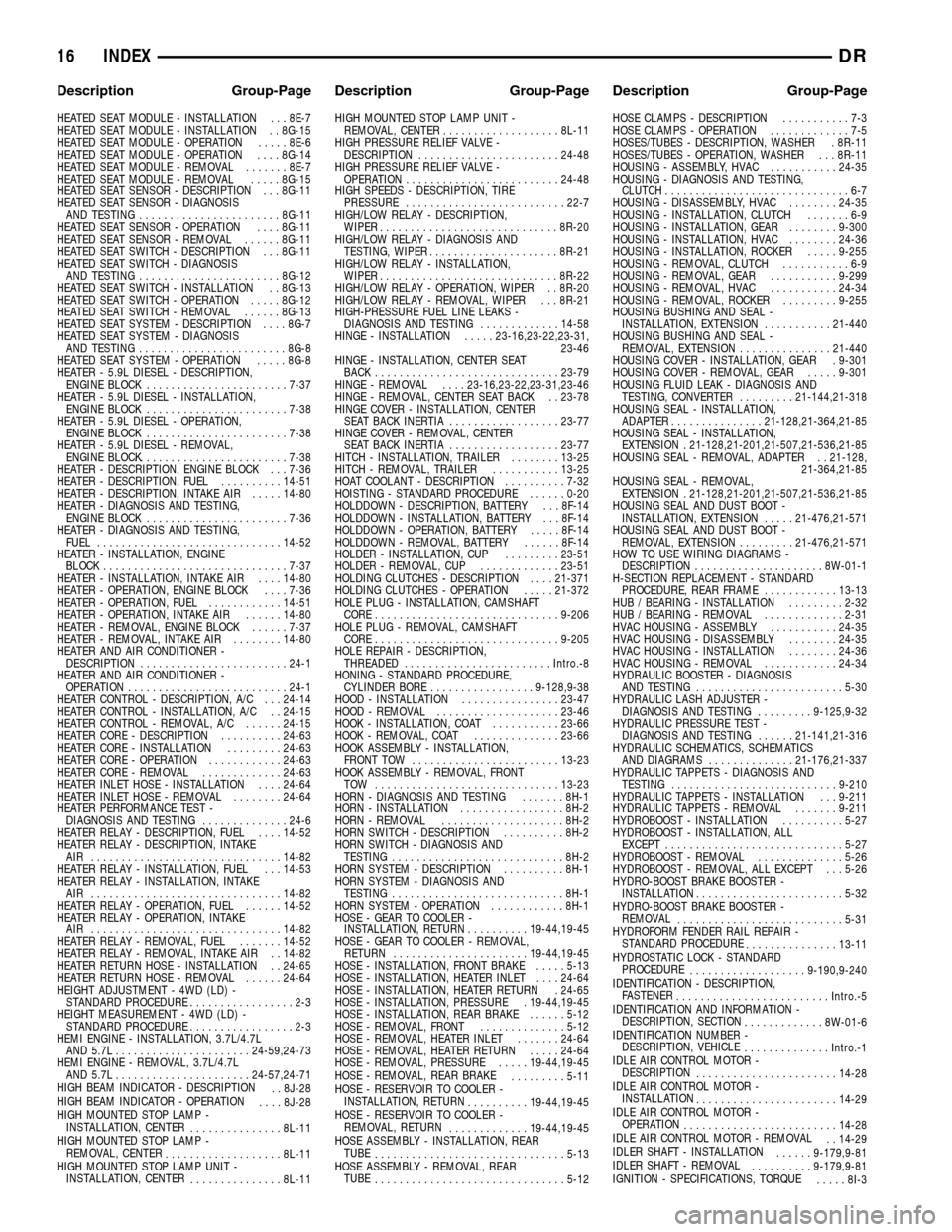
HEATED SEAT MODULE - INSTALLATION . . . 8E-7
HEATED SEAT MODULE - INSTALLATION . . 8G-15
HEATED SEAT MODULE - OPERATION.....8E-6
HEATED SEAT MODULE - OPERATION....8G-14
HEATED SEAT MODULE - REMOVAL.......8E-7
HEATED SEAT MODULE - REMOVAL.....8G-15
HEATED SEAT SENSOR - DESCRIPTION . . . 8G-11
HEATED SEAT SENSOR - DIAGNOSIS
AND TESTING.......................8G-11
HEATED SEAT SENSOR - OPERATION....8G-11
HEATED SEAT SENSOR - REMOVAL......8G-11
HEATED SEAT SWITCH - DESCRIPTION . . . 8G-11
HEATED SEAT SWITCH - DIAGNOSIS
AND TESTING.......................8G-12
HEATED SEAT SWITCH - INSTALLATION . . 8G-13
HEATED SEAT SWITCH - OPERATION.....8G-12
HEATED SEAT SWITCH - REMOVAL......8G-13
HEATED SEAT SYSTEM - DESCRIPTION....8G-7
HEATED SEAT SYSTEM - DIAGNOSIS
AND TESTING........................8G-8
HEATED SEAT SYSTEM - OPERATION.....8G-8
HEATER - 5.9L DIESEL - DESCRIPTION,
ENGINE BLOCK.......................7-37
HEATER - 5.9L DIESEL - INSTALLATION,
ENGINE BLOCK.......................7-38
HEATER - 5.9L DIESEL - OPERATION,
ENGINE BLOCK.......................7-38
HEATER - 5.9L DIESEL - REMOVAL,
ENGINE BLOCK.........................7-38
HEATER - DESCRIPTION, ENGINE BLOCK . . . 7-36
HEATER - DESCRIPTION, FUEL..........14-51
HEATER - DESCRIPTION, INTAKE AIR.....14-80
HEATER - DIAGNOSIS AND TESTING,
ENGINE BLOCK.......................7-36
HEATER - DIAGNOSIS AND TESTING,
FUEL..............................14-52
HEATER - INSTALLATION, ENGINE
BLOCK..............................7-37
HEATER - INSTALLATION, INTAKE AIR....14-80
HEATER - OPERATION, ENGINE BLOCK....7-36
HEATER - OPERATION, FUEL............14-51
HEATER - OPERATION, INTAKE AIR......14-80
HEATER - REMOVAL, ENGINE BLOCK......7-37
HEATER - REMOVAL, INTAKE AIR........14-80
HEATER AND AIR CONDITIONER -
DESCRIPTION........................24-1
HEATER AND AIR CONDITIONER -
OPERATION..........................24-1
HEATER CONTROL - DESCRIPTION, A/C . . . 24-14
HEATER CONTROL - INSTALLATION, A/C . . 24-15
HEATER CONTROL - REMOVAL, A/C......24-15
HEATER CORE - DESCRIPTION..........24-63
HEATER CORE - INSTALLATION.........24-63
HEATER CORE - OPERATION............24-63
HEATER CORE - REMOVAL.............24-63
HEATER INLET HOSE - INSTALLATION....24-64
HEATER INLET HOSE - REMOVAL........24-64
HEATER PERFORMANCE TEST -
DIAGNOSIS AND TESTING..............24-6
HEATER RELAY - DESCRIPTION, FUEL....14-52
HEATER RELAY - DESCRIPTION, INTAKE
AIR ...............................14-82
HEATER RELAY - INSTALLATION, FUEL . . . 14-53
HEATER RELAY - INSTALLATION, INTAKE
AIR ...............................14-82
HEATER RELAY - OPERATION, FUEL......14-52
HEATER RELAY - OPERATION, INTAKE
AIR ...............................14-82
HEATER RELAY - REMOVAL, FUEL.......14-52
HEATER RELAY - REMOVAL, INTAKE AIR . . 14-82
HEATER RETURN HOSE - INSTALLATION . . 24-65
HEATER RETURN HOSE - REMOVAL......24-64
HEIGHT ADJUSTMENT - 4WD (LD) -
STANDARD PROCEDURE.................2-3
HEIGHT MEASUREMENT - 4WD (LD) -
STANDARD PROCEDURE.................2-3
HEMI ENGINE - INSTALLATION, 3.7L/4.7L
AND 5.7L......................24-59,24-73
HEMI ENGINE - REMOVAL, 3.7L/4.7L
AND 5.7L......................24-57,24-71
HIGH BEAM INDICATOR - DESCRIPTION
. . 8J-28
HIGH BEAM INDICATOR - OPERATION
....8J-28
HIGH MOUNTED STOP LAMP -
INSTALLATION, CENTER
...............8L-11
HIGH MOUNTED STOP LAMP -
REMOVAL, CENTER
...................8L-11
HIGH MOUNTED STOP LAMP UNIT -
INSTALLATION, CENTER
...............8L-11HIGH MOUNTED STOP LAMP UNIT -
REMOVAL, CENTER...................8L-11
HIGH PRESSURE RELIEF VALVE -
DESCRIPTION.......................24-48
HIGH PRESSURE RELIEF VALVE -
OPERATION.........................24-48
HIGH SPEEDS - DESCRIPTION, TIRE
PRESSURE..........................22-7
HIGH/LOW RELAY - DESCRIPTION,
WIPER.............................8R-20
HIGH/LOW RELAY - DIAGNOSIS AND
TESTING, WIPER.....................8R-21
HIGH/LOW RELAY - INSTALLATION,
WIPER.............................8R-22
HIGH/LOW RELAY - OPERATION, WIPER . . 8R-20
HIGH/LOW RELAY - REMOVAL, WIPER . . . 8R-21
HIGH-PRESSURE FUEL LINE LEAKS -
DIAGNOSIS AND TESTING.............14-58
HINGE - INSTALLATION.....23-16,23-22,23-31,
23-46
HINGE - INSTALLATION, CENTER SEAT
BACK..............................23-79
HINGE - REMOVAL....23-16,23-22,23-31,23-46
HINGE - REMOVAL, CENTER SEAT BACK . . 23-78
HINGE COVER - INSTALLATION, CENTER
SEAT BACK INERTIA..................23-77
HINGE COVER - REMOVAL, CENTER
SEAT BACK INERTIA..................23-77
HITCH - INSTALLATION, TRAILER........13-25
HITCH - REMOVAL, TRAILER...........13-25
HOAT COOLANT - DESCRIPTION..........7-32
HOISTING - STANDARD PROCEDURE......0-20
HOLDDOWN - DESCRIPTION, BATTERY . . . 8F-14
HOLDDOWN - INSTALLATION, BATTERY . . . 8F-14
HOLDDOWN - OPERATION, BATTERY.....8F-14
HOLDDOWN - REMOVAL, BATTERY......8F-14
HOLDER - INSTALLATION, CUP.........23-51
HOLDER - REMOVAL, CUP.............23-51
HOLDING CLUTCHES - DESCRIPTION....21-371
HOLDING CLUTCHES - OPERATION.....21-372
HOLE PLUG - INSTALLATION, CAMSHAFT
CORE..............................9-206
HOLE PLUG - REMOVAL, CAMSHAFT
CORE..............................9-205
HOLE REPAIR - DESCRIPTION,
THREADED........................Intro.-8
HONING - STANDARD PROCEDURE,
CYLINDER BORE.................9-128,9-38
HOOD - INSTALLATION................23-47
HOOD - REMOVAL....................23-46
HOOK - INSTALLATION, COAT...........23-66
HOOK - REMOVAL, COAT..............23-66
HOOK ASSEMBLY - INSTALLATION,
FRONT TOW........................13-23
HOOK ASSEMBLY - REMOVAL, FRONT
TOW ..............................13-23
HORN - DIAGNOSIS AND TESTING.......8H-1
HORN - INSTALLATION.................8H-2
HORN - REMOVAL....................8H-2
HORN SWITCH - DESCRIPTION..........8H-2
HORN SWITCH - DIAGNOSIS AND
TESTING............................8H-2
HORN SYSTEM - DESCRIPTION..........8H-1
HORN SYSTEM - DIAGNOSIS AND
TESTING............................8H-1
HORN SYSTEM - OPERATION............8H-1
HOSE - GEAR TO COOLER -
INSTALLATION, RETURN..........19-44,19-45
HOSE - GEAR TO COOLER - REMOVAL,
RETURN......................19-44,19-45
HOSE - INSTALLATION, FRONT BRAKE.....5-13
HOSE - INSTALLATION, HEATER INLET....24-64
HOSE - INSTALLATION, HEATER RETURN . 24-65
HOSE - INSTALLATION, PRESSURE . 19-44,19-45
HOSE - INSTALLATION, REAR BRAKE......5-12
HOSE - REMOVAL, FRONT..............5-12
HOSE - REMOVAL, HEATER INLET.......24-64
HOSE - REMOVAL, HEATER RETURN.....24-64
HOSE - REMOVAL, PRESSURE.....19-44,19-45
HOSE - REMOVAL, REAR BRAKE
.........5-11
HOSE - RESERVOIR TO COOLER -
INSTALLATION, RETURN
..........19-44,19-45
HOSE - RESERVOIR TO COOLER -
REMOVAL, RETURN
.............19-44,19-45
HOSE ASSEMBLY - INSTALLATION, REAR
TUBE
...............................5-13
HOSE ASSEMBLY - REMOVAL, REAR
TUBE
...............................5-12HOSE CLAMPS - DESCRIPTION...........7-3
HOSE CLAMPS - OPERATION.............7-5
HOSES/TUBES - DESCRIPTION, WASHER . 8R-11
HOSES/TUBES - OPERATION, WASHER . . . 8R-11
HOUSING - ASSEMBLY, HVAC...........24-35
HOUSING - DIAGNOSIS AND TESTING,
CLUTCH..............................6-7
HOUSING - DISASSEMBLY, HVAC........24-35
HOUSING - INSTALLATION, CLUTCH.......6-9
HOUSING - INSTALLATION, GEAR........9-300
HOUSING - INSTALLATION, HVAC........24-36
HOUSING - INSTALLATION, ROCKER.....9-255
HOUSING - REMOVAL, CLUTCH...........6-9
HOUSING - REMOVAL, GEAR...........9-299
HOUSING - REMOVAL, HVAC...........24-34
HOUSING - REMOVAL, ROCKER.........9-255
HOUSING BUSHING AND SEAL -
INSTALLATION, EXTENSION...........21-440
HOUSING BUSHING AND SEAL -
REMOVAL, EXTENSION...............21-440
HOUSING COVER - INSTALLATION, GEAR . 9-301
HOUSING COVER - REMOVAL, GEAR.....9-301
HOUSING FLUID LEAK - DIAGNOSIS AND
TESTING, CONVERTER.........21-144,21-318
HOUSING SEAL - INSTALLATION,
ADAPTER...............21-128,21-364,21-85
HOUSING SEAL - INSTALLATION,
EXTENSION . 21-128,21-201,21-507,21-536,21-85
HOUSING SEAL - REMOVAL, ADAPTER . . 21-128,
21-364,21-85
HOUSING SEAL - REMOVAL,
EXTENSION . 21-128,21-201,21-507,21-536,21-85
HOUSING SEAL AND DUST BOOT -
INSTALLATION, EXTENSION.....21-476,21-571
HOUSING SEAL AND DUST BOOT -
REMOVAL, EXTENSION.........21-476,21-571
HOW TO USE WIRING DIAGRAMS -
DESCRIPTION.....................8W-01-1
H-SECTION REPLACEMENT - STANDARD
PROCEDURE, REAR FRAME............13-13
HUB / BEARING - INSTALLATION.........2-32
HUB / BEARING - REMOVAL.............2-31
HVAC HOUSING - ASSEMBLY...........24-35
HVAC HOUSING - DISASSEMBLY........24-35
HVAC HOUSING - INSTALLATION........24-36
HVAC HOUSING - REMOVAL............24-34
HYDRAULIC BOOSTER - DIAGNOSIS
AND TESTING........................5-30
HYDRAULIC LASH ADJUSTER -
DIAGNOSIS AND TESTING.........9-125,9-32
HYDRAULIC PRESSURE TEST -
DIAGNOSIS AND TESTING......21-141,21-316
HYDRAULIC SCHEMATICS, SCHEMATICS
AND DIAGRAMS..............21-176,21-337
HYDRAULIC TAPPETS - DIAGNOSIS AND
TESTING...........................9-210
HYDRAULIC TAPPETS - INSTALLATION . . . 9-211
HYDRAULIC TAPPETS - REMOVAL.......9-211
HYDROBOOST - INSTALLATION..........5-27
HYDROBOOST - INSTALLATION, ALL
EXCEPT.............................5-27
HYDROBOOST - REMOVAL..............5-26
HYDROBOOST - REMOVAL, ALL EXCEPT . . . 5-26
HYDRO-BOOST BRAKE BOOSTER -
INSTALLATION........................5-32
HYDRO-BOOST BRAKE BOOSTER -
REMOVAL
...........................5-31
HYDROFORM FENDER RAIL REPAIR -
STANDARD PROCEDURE
...............13-11
HYDROSTATIC LOCK - STANDARD
PROCEDURE
...................9-190,9-240
IDENTIFICATION - DESCRIPTION,
FASTENER
.........................Intro.-5
IDENTIFICATION AND INFORMATION -
DESCRIPTION, SECTION
.............8W-01-6
IDENTIFICATION NUMBER -
DESCRIPTION, VEHICLE
..............Intro.-1
IDLE AIR CONTROL MOTOR -
DESCRIPTION
.......................14-28
IDLE AIR CONTROL MOTOR -
INSTALLATION
.......................14-29
IDLE AIR CONTROL MOTOR -
OPERATION
.........................14-28
IDLE AIR CONTROL MOTOR - REMOVAL
. . 14-29
IDLER SHAFT - INSTALLATION
......9-179,9-81
IDLER SHAFT - REMOVAL
..........9-179,9-81
IGNITION - SPECIFICATIONS, TORQUE
.....8I-3
16 INDEXDR
Description Group-Page Description Group-Page Description Group-Page