module DODGE RAM 1500 1998 2.G Repair Manual
[x] Cancel search | Manufacturer: DODGE, Model Year: 1998, Model line: RAM 1500, Model: DODGE RAM 1500 1998 2.GPages: 2627
Page 451 of 2627
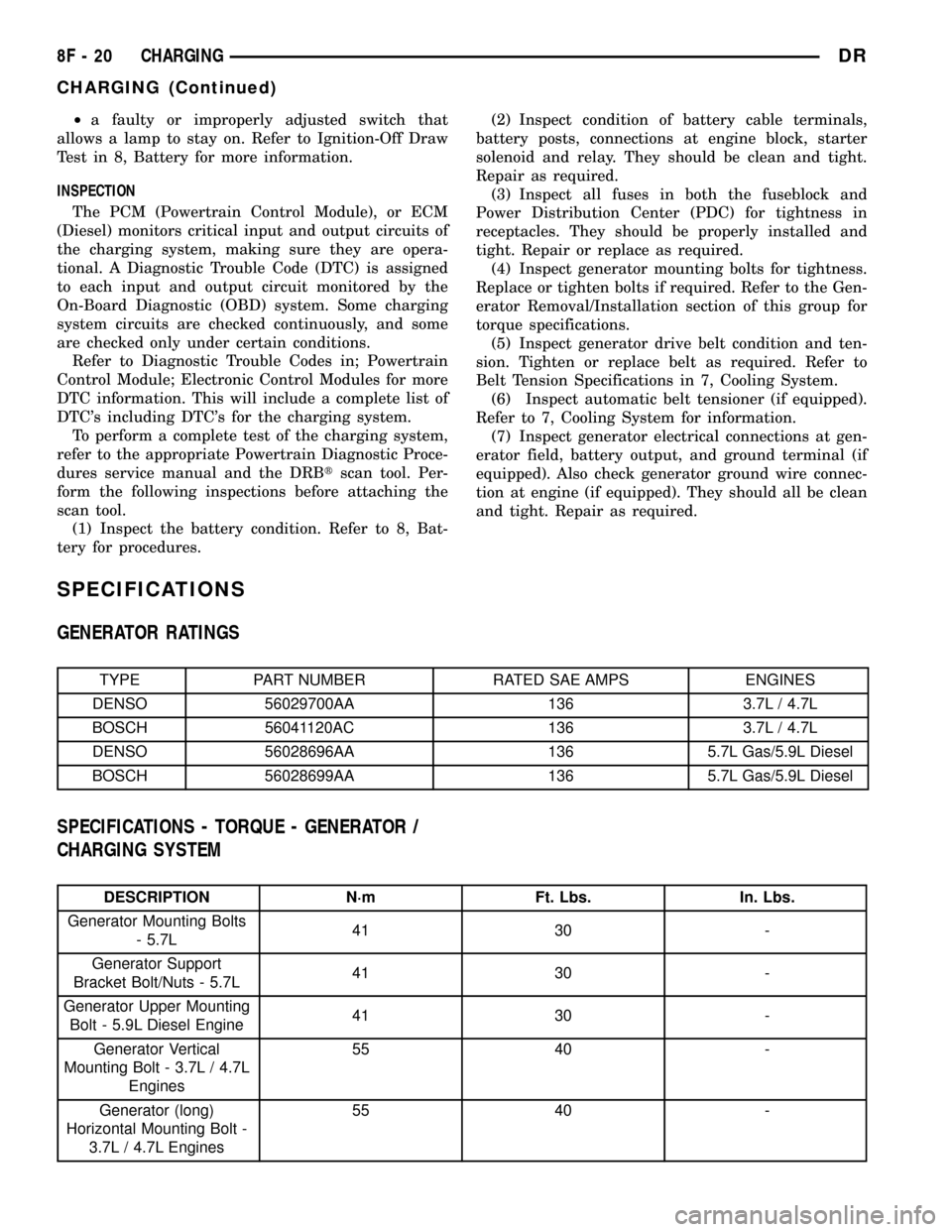
²a faulty or improperly adjusted switch that
allows a lamp to stay on. Refer to Ignition-Off Draw
Test in 8, Battery for more information.
INSPECTION
The PCM (Powertrain Control Module), or ECM
(Diesel) monitors critical input and output circuits of
the charging system, making sure they are opera-
tional. A Diagnostic Trouble Code (DTC) is assigned
to each input and output circuit monitored by the
On-Board Diagnostic (OBD) system. Some charging
system circuits are checked continuously, and some
are checked only under certain conditions.
Refer to Diagnostic Trouble Codes in; Powertrain
Control Module; Electronic Control Modules for more
DTC information. This will include a complete list of
DTC's including DTC's for the charging system.
To perform a complete test of the charging system,
refer to the appropriate Powertrain Diagnostic Proce-
dures service manual and the DRBtscan tool. Per-
form the following inspections before attaching the
scan tool.
(1) Inspect the battery condition. Refer to 8, Bat-
tery for procedures.(2) Inspect condition of battery cable terminals,
battery posts, connections at engine block, starter
solenoid and relay. They should be clean and tight.
Repair as required.
(3) Inspect all fuses in both the fuseblock and
Power Distribution Center (PDC) for tightness in
receptacles. They should be properly installed and
tight. Repair or replace as required.
(4) Inspect generator mounting bolts for tightness.
Replace or tighten bolts if required. Refer to the Gen-
erator Removal/Installation section of this group for
torque specifications.
(5) Inspect generator drive belt condition and ten-
sion. Tighten or replace belt as required. Refer to
Belt Tension Specifications in 7, Cooling System.
(6) Inspect automatic belt tensioner (if equipped).
Refer to 7, Cooling System for information.
(7) Inspect generator electrical connections at gen-
erator field, battery output, and ground terminal (if
equipped). Also check generator ground wire connec-
tion at engine (if equipped). They should all be clean
and tight. Repair as required.
SPECIFICATIONS
GENERATOR RATINGS
TYPE PART NUMBER RATED SAE AMPS ENGINES
DENSO 56029700AA 136 3.7L / 4.7L
BOSCH 56041120AC 136 3.7L / 4.7L
DENSO 56028696AA 136 5.7L Gas/5.9L Diesel
BOSCH 56028699AA 136 5.7L Gas/5.9L Diesel
SPECIFICATIONS - TORQUE - GENERATOR /
CHARGING SYSTEM
DESCRIPTION N´m Ft. Lbs. In. Lbs.
Generator Mounting Bolts
- 5.7L41 30 -
Generator Support
Bracket Bolt/Nuts - 5.7L41 30 -
Generator Upper Mounting
Bolt - 5.9L Diesel Engine41 30 -
Generator Vertical
Mounting Bolt - 3.7L / 4.7L
Engines55 40 -
Generator (long)
Horizontal Mounting Bolt -
3.7L / 4.7L Engines55 40 -
8F - 20 CHARGINGDR
CHARGING (Continued)
Page 456 of 2627
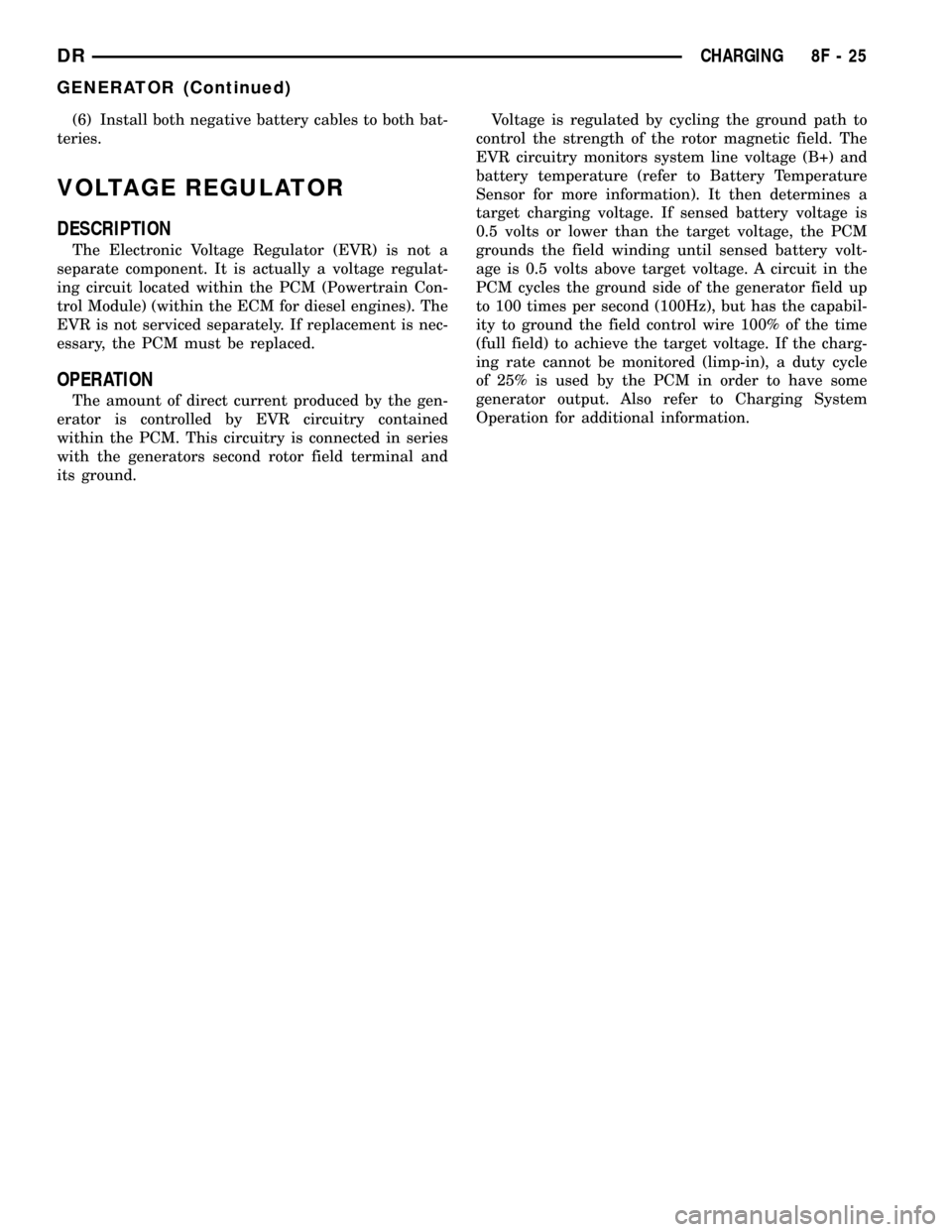
(6) Install both negative battery cables to both bat-
teries.
VOLTAGE REGULATOR
DESCRIPTION
The Electronic Voltage Regulator (EVR) is not a
separate component. It is actually a voltage regulat-
ing circuit located within the PCM (Powertrain Con-
trol Module) (within the ECM for diesel engines). The
EVR is not serviced separately. If replacement is nec-
essary, the PCM must be replaced.
OPERATION
The amount of direct current produced by the gen-
erator is controlled by EVR circuitry contained
within the PCM. This circuitry is connected in series
with the generators second rotor field terminal and
its ground.Voltage is regulated by cycling the ground path to
control the strength of the rotor magnetic field. The
EVR circuitry monitors system line voltage (B+) and
battery temperature (refer to Battery Temperature
Sensor for more information). It then determines a
target charging voltage. If sensed battery voltage is
0.5 volts or lower than the target voltage, the PCM
grounds the field winding until sensed battery volt-
age is 0.5 volts above target voltage. A circuit in the
PCM cycles the ground side of the generator field up
to 100 times per second (100Hz), but has the capabil-
ity to ground the field control wire 100% of the time
(full field) to achieve the target voltage. If the charg-
ing rate cannot be monitored (limp-in), a duty cycle
of 25% is used by the PCM in order to have some
generator output. Also refer to Charging System
Operation for additional information.
DRCHARGING 8F - 25
GENERATOR (Continued)
Page 468 of 2627
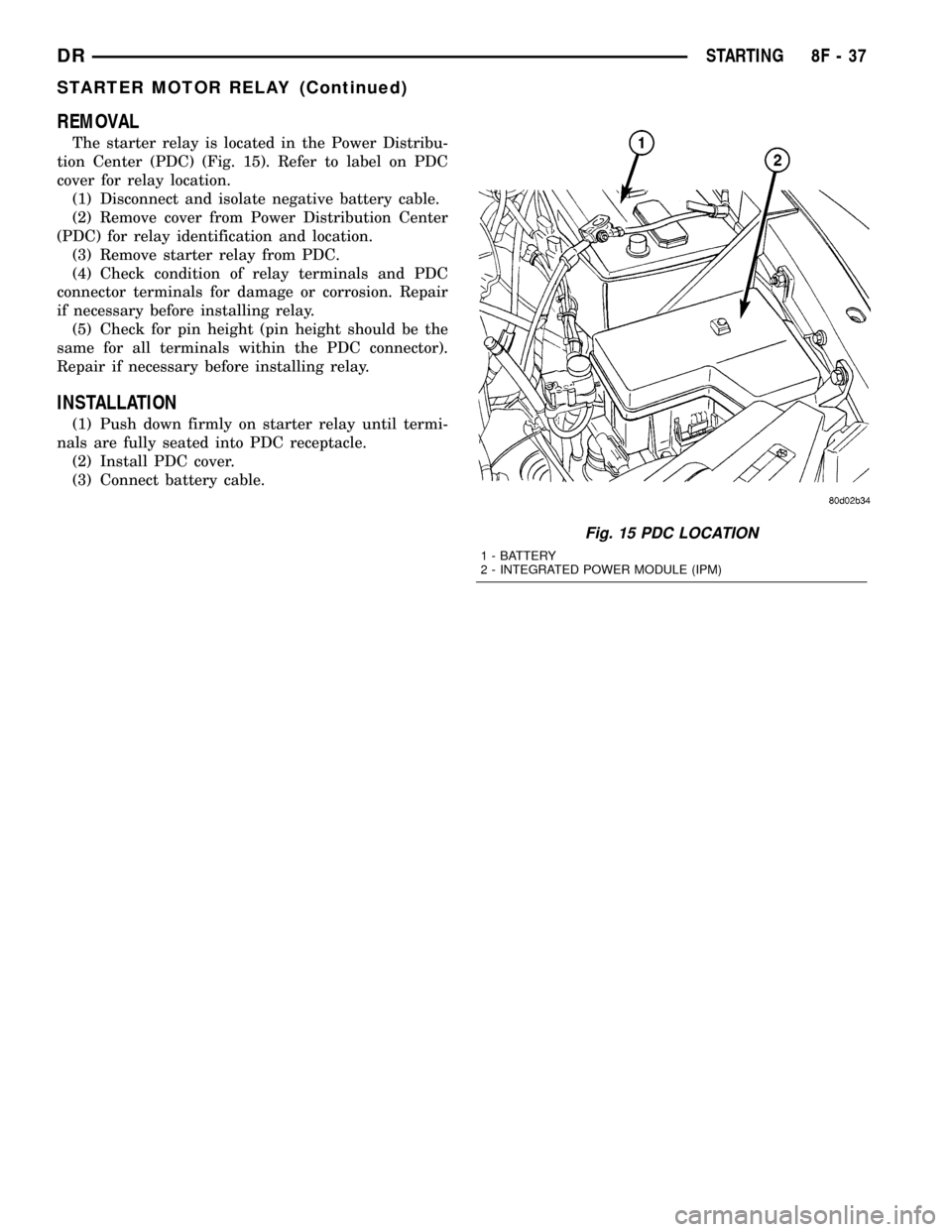
REMOVAL
The starter relay is located in the Power Distribu-
tion Center (PDC) (Fig. 15). Refer to label on PDC
cover for relay location.
(1) Disconnect and isolate negative battery cable.
(2) Remove cover from Power Distribution Center
(PDC) for relay identification and location.
(3) Remove starter relay from PDC.
(4) Check condition of relay terminals and PDC
connector terminals for damage or corrosion. Repair
if necessary before installing relay.
(5) Check for pin height (pin height should be the
same for all terminals within the PDC connector).
Repair if necessary before installing relay.
INSTALLATION
(1) Push down firmly on starter relay until termi-
nals are fully seated into PDC receptacle.
(2) Install PDC cover.
(3) Connect battery cable.
Fig. 15 PDC LOCATION
1 - BATTERY
2 - INTEGRATED POWER MODULE (IPM)
DRSTARTING 8F - 37
STARTER MOTOR RELAY (Continued)
Page 472 of 2627
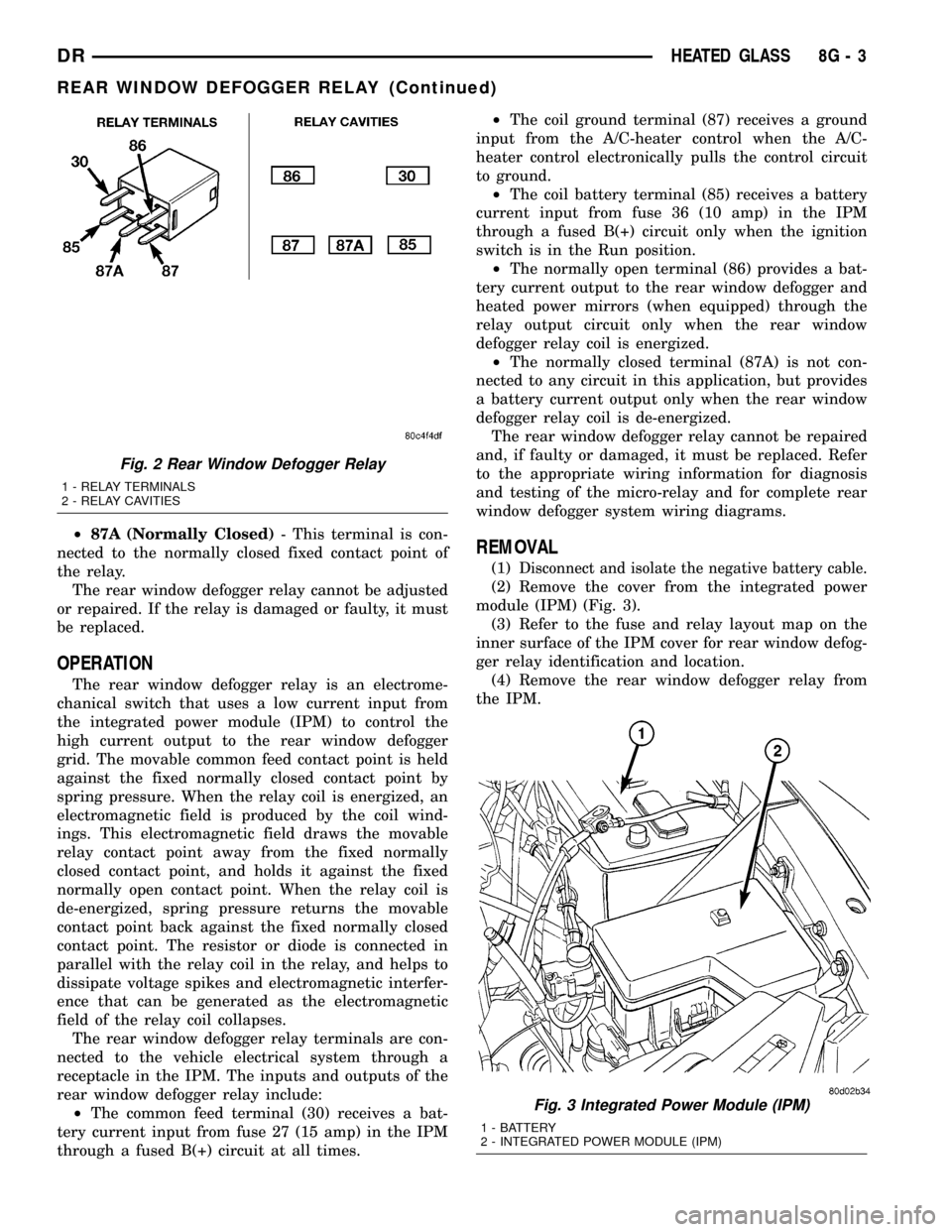
²87A (Normally Closed)- This terminal is con-
nected to the normally closed fixed contact point of
the relay.
The rear window defogger relay cannot be adjusted
or repaired. If the relay is damaged or faulty, it must
be replaced.
OPERATION
The rear window defogger relay is an electrome-
chanical switch that uses a low current input from
the integrated power module (IPM) to control the
high current output to the rear window defogger
grid. The movable common feed contact point is held
against the fixed normally closed contact point by
spring pressure. When the relay coil is energized, an
electromagnetic field is produced by the coil wind-
ings. This electromagnetic field draws the movable
relay contact point away from the fixed normally
closed contact point, and holds it against the fixed
normally open contact point. When the relay coil is
de-energized, spring pressure returns the movable
contact point back against the fixed normally closed
contact point. The resistor or diode is connected in
parallel with the relay coil in the relay, and helps to
dissipate voltage spikes and electromagnetic interfer-
ence that can be generated as the electromagnetic
field of the relay coil collapses.
The rear window defogger relay terminals are con-
nected to the vehicle electrical system through a
receptacle in the IPM. The inputs and outputs of the
rear window defogger relay include:
²The common feed terminal (30) receives a bat-
tery current input from fuse 27 (15 amp) in the IPM
through a fused B(+) circuit at all times.²The coil ground terminal (87) receives a ground
input from the A/C-heater control when the A/C-
heater control electronically pulls the control circuit
to ground.
²The coil battery terminal (85) receives a battery
current input from fuse 36 (10 amp) in the IPM
through a fused B(+) circuit only when the ignition
switch is in the Run position.
²The normally open terminal (86) provides a bat-
tery current output to the rear window defogger and
heated power mirrors (when equipped) through the
relay output circuit only when the rear window
defogger relay coil is energized.
²The normally closed terminal (87A) is not con-
nected to any circuit in this application, but provides
a battery current output only when the rear window
defogger relay coil is de-energized.
The rear window defogger relay cannot be repaired
and, if faulty or damaged, it must be replaced. Refer
to the appropriate wiring information for diagnosis
and testing of the micro-relay and for complete rear
window defogger system wiring diagrams.
REMOVAL
(1)Disconnect and isolate the negative battery cable.
(2) Remove the cover from the integrated power
module (IPM) (Fig. 3).
(3) Refer to the fuse and relay layout map on the
inner surface of the IPM cover for rear window defog-
ger relay identification and location.
(4) Remove the rear window defogger relay from
the IPM.
Fig. 2 Rear Window Defogger Relay
1 - RELAY TERMINALS
2 - RELAY CAVITIES
Fig. 3 Integrated Power Module (IPM)
1 - BATTERY
2 - INTEGRATED POWER MODULE (IPM)
DRHEATED GLASS 8G - 3
REAR WINDOW DEFOGGER RELAY (Continued)
Page 473 of 2627
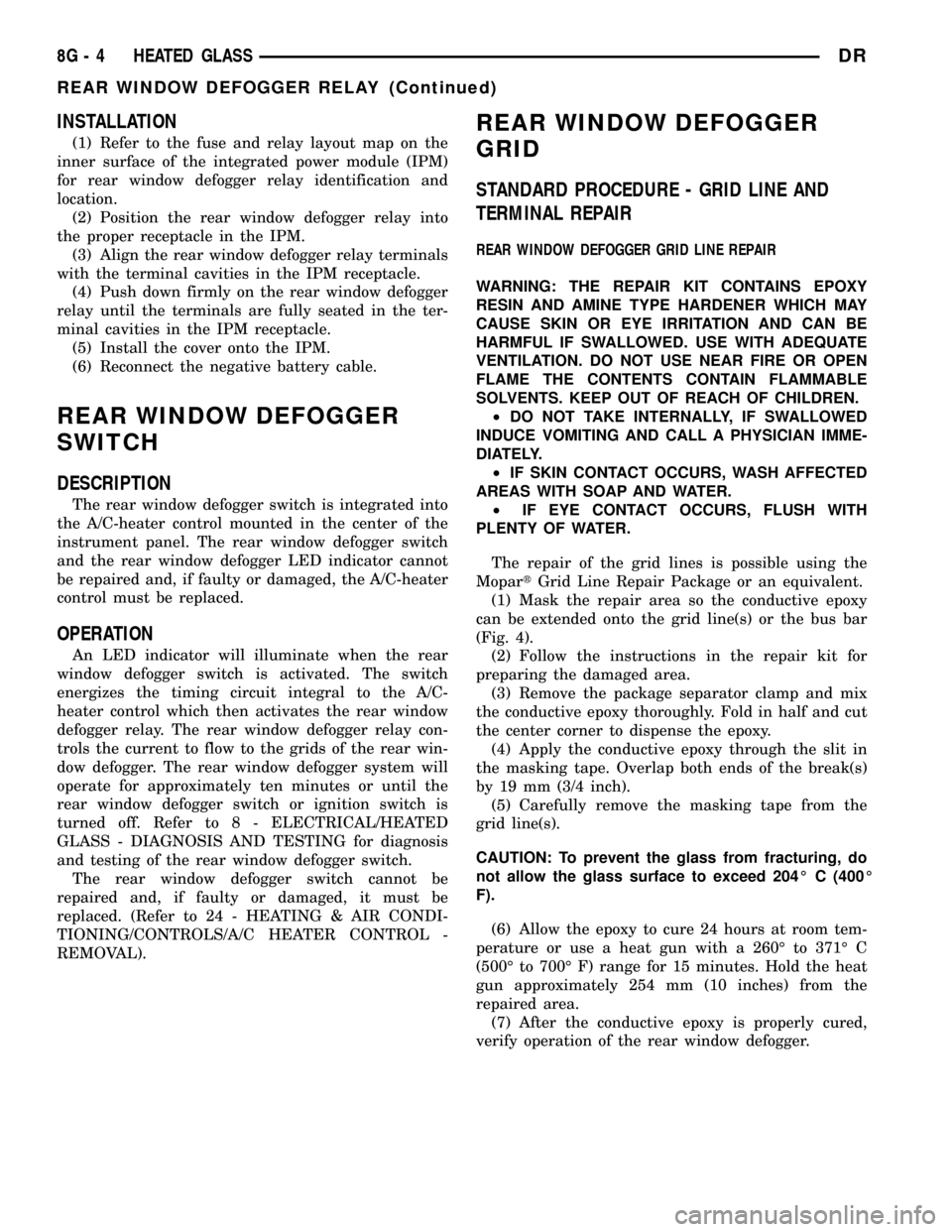
INSTALLATION
(1) Refer to the fuse and relay layout map on the
inner surface of the integrated power module (IPM)
for rear window defogger relay identification and
location.
(2) Position the rear window defogger relay into
the proper receptacle in the IPM.
(3) Align the rear window defogger relay terminals
with the terminal cavities in the IPM receptacle.
(4) Push down firmly on the rear window defogger
relay until the terminals are fully seated in the ter-
minal cavities in the IPM receptacle.
(5) Install the cover onto the IPM.
(6) Reconnect the negative battery cable.
REAR WINDOW DEFOGGER
SWITCH
DESCRIPTION
The rear window defogger switch is integrated into
the A/C-heater control mounted in the center of the
instrument panel. The rear window defogger switch
and the rear window defogger LED indicator cannot
be repaired and, if faulty or damaged, the A/C-heater
control must be replaced.
OPERATION
An LED indicator will illuminate when the rear
window defogger switch is activated. The switch
energizes the timing circuit integral to the A/C-
heater control which then activates the rear window
defogger relay. The rear window defogger relay con-
trols the current to flow to the grids of the rear win-
dow defogger. The rear window defogger system will
operate for approximately ten minutes or until the
rear window defogger switch or ignition switch is
turned off. Refer to 8 - ELECTRICAL/HEATED
GLASS - DIAGNOSIS AND TESTING for diagnosis
and testing of the rear window defogger switch.
The rear window defogger switch cannot be
repaired and, if faulty or damaged, it must be
replaced. (Refer to 24 - HEATING & AIR CONDI-
TIONING/CONTROLS/A/C HEATER CONTROL -
REMOVAL).
REAR WINDOW DEFOGGER
GRID
STANDARD PROCEDURE - GRID LINE AND
TERMINAL REPAIR
REAR WINDOW DEFOGGER GRID LINE REPAIR
WARNING: THE REPAIR KIT CONTAINS EPOXY
RESIN AND AMINE TYPE HARDENER WHICH MAY
CAUSE SKIN OR EYE IRRITATION AND CAN BE
HARMFUL IF SWALLOWED. USE WITH ADEQUATE
VENTILATION. DO NOT USE NEAR FIRE OR OPEN
FLAME THE CONTENTS CONTAIN FLAMMABLE
SOLVENTS. KEEP OUT OF REACH OF CHILDREN.
²DO NOT TAKE INTERNALLY, IF SWALLOWED
INDUCE VOMITING AND CALL A PHYSICIAN IMME-
DIATELY.
²IF SKIN CONTACT OCCURS, WASH AFFECTED
AREAS WITH SOAP AND WATER.
²IF EYE CONTACT OCCURS, FLUSH WITH
PLENTY OF WATER.
The repair of the grid lines is possible using the
MopartGrid Line Repair Package or an equivalent.
(1) Mask the repair area so the conductive epoxy
can be extended onto the grid line(s) or the bus bar
(Fig. 4).
(2) Follow the instructions in the repair kit for
preparing the damaged area.
(3) Remove the package separator clamp and mix
the conductive epoxy thoroughly. Fold in half and cut
the center corner to dispense the epoxy.
(4) Apply the conductive epoxy through the slit in
the masking tape. Overlap both ends of the break(s)
by 19 mm (3/4 inch).
(5) Carefully remove the masking tape from the
grid line(s).
CAUTION: To prevent the glass from fracturing, do
not allow the glass surface to exceed 204É C (400É
F).
(6) Allow the epoxy to cure 24 hours at room tem-
perature or use a heat gun with a 260É to 371É C
(500É to 700É F) range for 15 minutes. Hold the heat
gun approximately 254 mm (10 inches) from the
repaired area.
(7) After the conductive epoxy is properly cured,
verify operation of the rear window defogger.
8G - 4 HEATED GLASSDR
REAR WINDOW DEFOGGER RELAY (Continued)
Page 476 of 2627
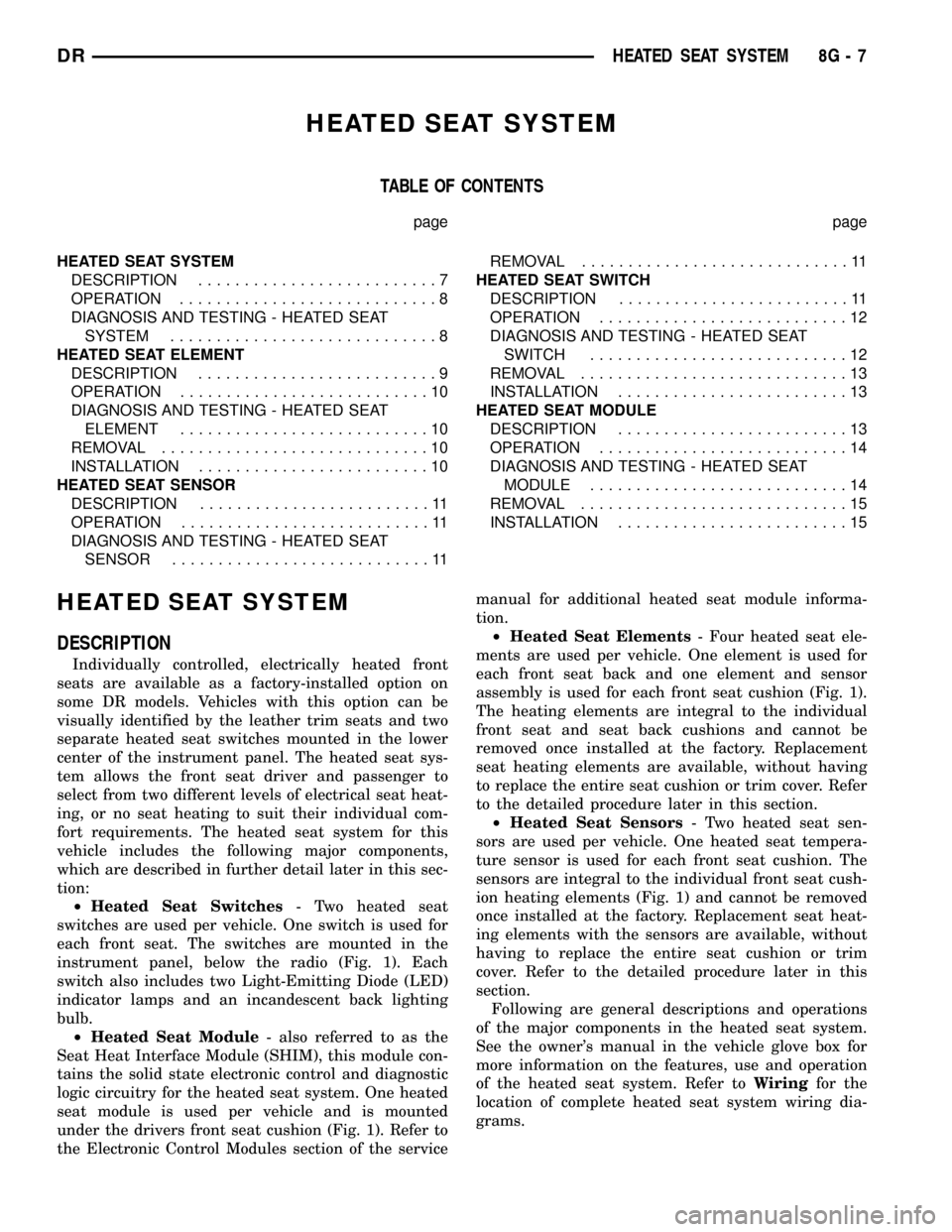
HEATED SEAT SYSTEM
TABLE OF CONTENTS
page page
HEATED SEAT SYSTEM
DESCRIPTION..........................7
OPERATION............................8
DIAGNOSIS AND TESTING - HEATED SEAT
SYSTEM.............................8
HEATED SEAT ELEMENT
DESCRIPTION..........................9
OPERATION...........................10
DIAGNOSIS AND TESTING - HEATED SEAT
ELEMENT...........................10
REMOVAL.............................10
INSTALLATION.........................10
HEATED SEAT SENSOR
DESCRIPTION.........................11
OPERATION...........................11
DIAGNOSIS AND TESTING - HEATED SEAT
SENSOR............................11REMOVAL.............................11
HEATED SEAT SWITCH
DESCRIPTION.........................11
OPERATION...........................12
DIAGNOSIS AND TESTING - HEATED SEAT
SWITCH............................12
REMOVAL.............................13
INSTALLATION.........................13
HEATED SEAT MODULE
DESCRIPTION.........................13
OPERATION...........................14
DIAGNOSIS AND TESTING - HEATED SEAT
MODULE............................14
REMOVAL.............................15
INSTALLATION.........................15
HEATED SEAT SYSTEM
DESCRIPTION
Individually controlled, electrically heated front
seats are available as a factory-installed option on
some DR models. Vehicles with this option can be
visually identified by the leather trim seats and two
separate heated seat switches mounted in the lower
center of the instrument panel. The heated seat sys-
tem allows the front seat driver and passenger to
select from two different levels of electrical seat heat-
ing, or no seat heating to suit their individual com-
fort requirements. The heated seat system for this
vehicle includes the following major components,
which are described in further detail later in this sec-
tion:
²Heated Seat Switches- Two heated seat
switches are used per vehicle. One switch is used for
each front seat. The switches are mounted in the
instrument panel, below the radio (Fig. 1). Each
switch also includes two Light-Emitting Diode (LED)
indicator lamps and an incandescent back lighting
bulb.
²Heated Seat Module- also referred to as the
Seat Heat Interface Module (SHIM), this module con-
tains the solid state electronic control and diagnostic
logic circuitry for the heated seat system. One heated
seat module is used per vehicle and is mounted
under the drivers front seat cushion (Fig. 1). Refer to
the Electronic Control Modules section of the servicemanual for additional heated seat module informa-
tion.
²Heated Seat Elements- Four heated seat ele-
ments are used per vehicle. One element is used for
each front seat back and one element and sensor
assembly is used for each front seat cushion (Fig. 1).
The heating elements are integral to the individual
front seat and seat back cushions and cannot be
removed once installed at the factory. Replacement
seat heating elements are available, without having
to replace the entire seat cushion or trim cover. Refer
to the detailed procedure later in this section.
²Heated Seat Sensors- Two heated seat sen-
sors are used per vehicle. One heated seat tempera-
ture sensor is used for each front seat cushion. The
sensors are integral to the individual front seat cush-
ion heating elements (Fig. 1) and cannot be removed
once installed at the factory. Replacement seat heat-
ing elements with the sensors are available, without
having to replace the entire seat cushion or trim
cover. Refer to the detailed procedure later in this
section.
Following are general descriptions and operations
of the major components in the heated seat system.
See the owner's manual in the vehicle glove box for
more information on the features, use and operation
of the heated seat system. Refer toWiringfor the
location of complete heated seat system wiring dia-
grams.
DRHEATED SEAT SYSTEM 8G - 7
Page 477 of 2627
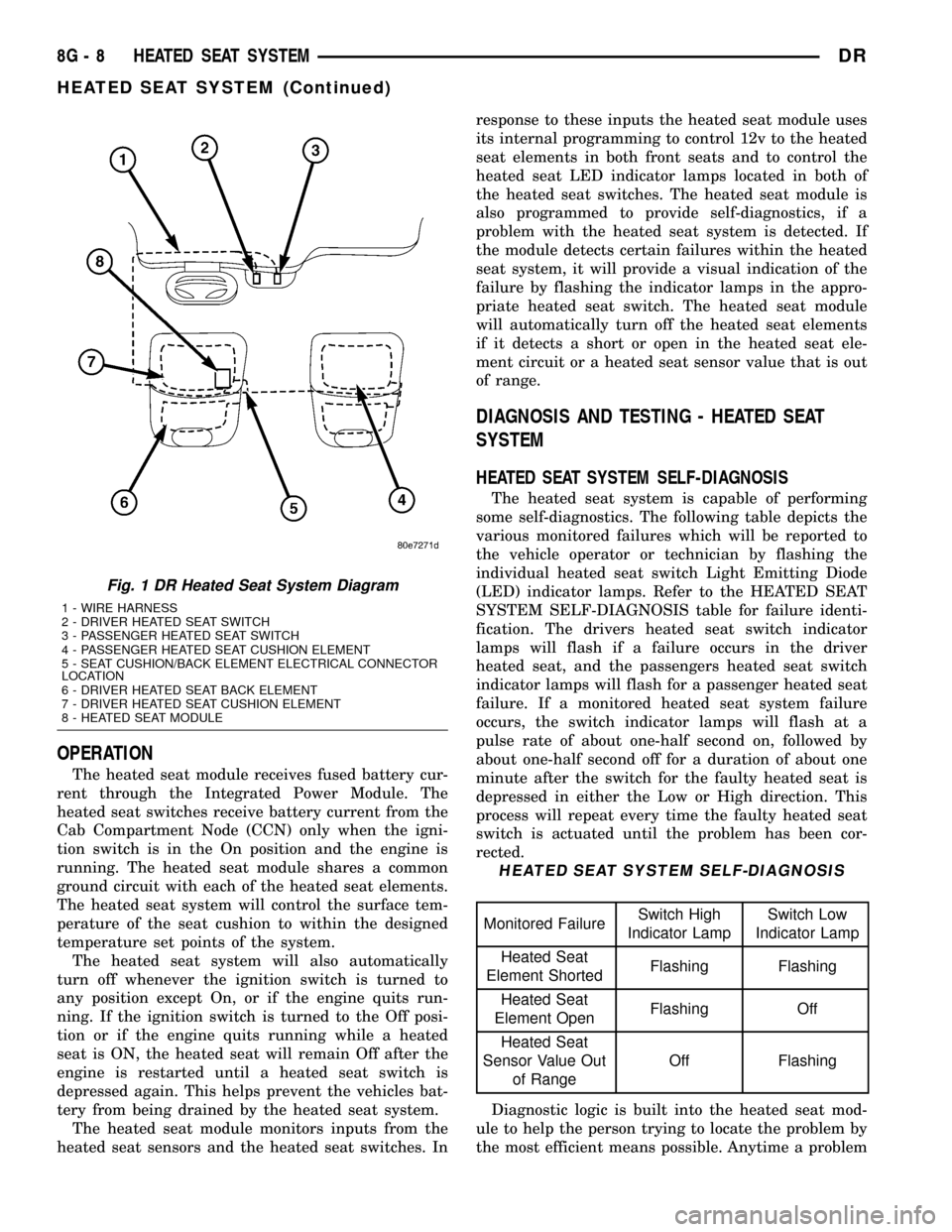
OPERATION
The heated seat module receives fused battery cur-
rent through the Integrated Power Module. The
heated seat switches receive battery current from the
Cab Compartment Node (CCN) only when the igni-
tion switch is in the On position and the engine is
running. The heated seat module shares a common
ground circuit with each of the heated seat elements.
The heated seat system will control the surface tem-
perature of the seat cushion to within the designed
temperature set points of the system.
The heated seat system will also automatically
turn off whenever the ignition switch is turned to
any position except On, or if the engine quits run-
ning. If the ignition switch is turned to the Off posi-
tion or if the engine quits running while a heated
seat is ON, the heated seat will remain Off after the
engine is restarted until a heated seat switch is
depressed again. This helps prevent the vehicles bat-
tery from being drained by the heated seat system.
The heated seat module monitors inputs from the
heated seat sensors and the heated seat switches. Inresponse to these inputs the heated seat module uses
its internal programming to control 12v to the heated
seat elements in both front seats and to control the
heated seat LED indicator lamps located in both of
the heated seat switches. The heated seat module is
also programmed to provide self-diagnostics, if a
problem with the heated seat system is detected. If
the module detects certain failures within the heated
seat system, it will provide a visual indication of the
failure by flashing the indicator lamps in the appro-
priate heated seat switch. The heated seat module
will automatically turn off the heated seat elements
if it detects a short or open in the heated seat ele-
ment circuit or a heated seat sensor value that is out
of range.
DIAGNOSIS AND TESTING - HEATED SEAT
SYSTEM
HEATED SEAT SYSTEM SELF-DIAGNOSIS
The heated seat system is capable of performing
some self-diagnostics. The following table depicts the
various monitored failures which will be reported to
the vehicle operator or technician by flashing the
individual heated seat switch Light Emitting Diode
(LED) indicator lamps. Refer to the HEATED SEAT
SYSTEM SELF-DIAGNOSIS table for failure identi-
fication. The drivers heated seat switch indicator
lamps will flash if a failure occurs in the driver
heated seat, and the passengers heated seat switch
indicator lamps will flash for a passenger heated seat
failure. If a monitored heated seat system failure
occurs, the switch indicator lamps will flash at a
pulse rate of about one-half second on, followed by
about one-half second off for a duration of about one
minute after the switch for the faulty heated seat is
depressed in either the Low or High direction. This
process will repeat every time the faulty heated seat
switch is actuated until the problem has been cor-
rected.
HEATED SEAT SYSTEM SELF-DIAGNOSIS
Monitored FailureSwitch High
Indicator LampSwitch Low
Indicator Lamp
Heated Seat
Element ShortedFlashing Flashing
Heated Seat
Element OpenFlashing Off
Heated Seat
Sensor Value Out
of RangeOff Flashing
Diagnostic logic is built into the heated seat mod-
ule to help the person trying to locate the problem by
the most efficient means possible. Anytime a problem
Fig. 1 DR Heated Seat System Diagram
1 - WIRE HARNESS
2 - DRIVER HEATED SEAT SWITCH
3 - PASSENGER HEATED SEAT SWITCH
4 - PASSENGER HEATED SEAT CUSHION ELEMENT
5 - SEAT CUSHION/BACK ELEMENT ELECTRICAL CONNECTOR
LOCATION
6 - DRIVER HEATED SEAT BACK ELEMENT
7 - DRIVER HEATED SEAT CUSHION ELEMENT
8 - HEATED SEAT MODULE
8G - 8 HEATED SEAT SYSTEMDR
HEATED SEAT SYSTEM (Continued)
Page 478 of 2627
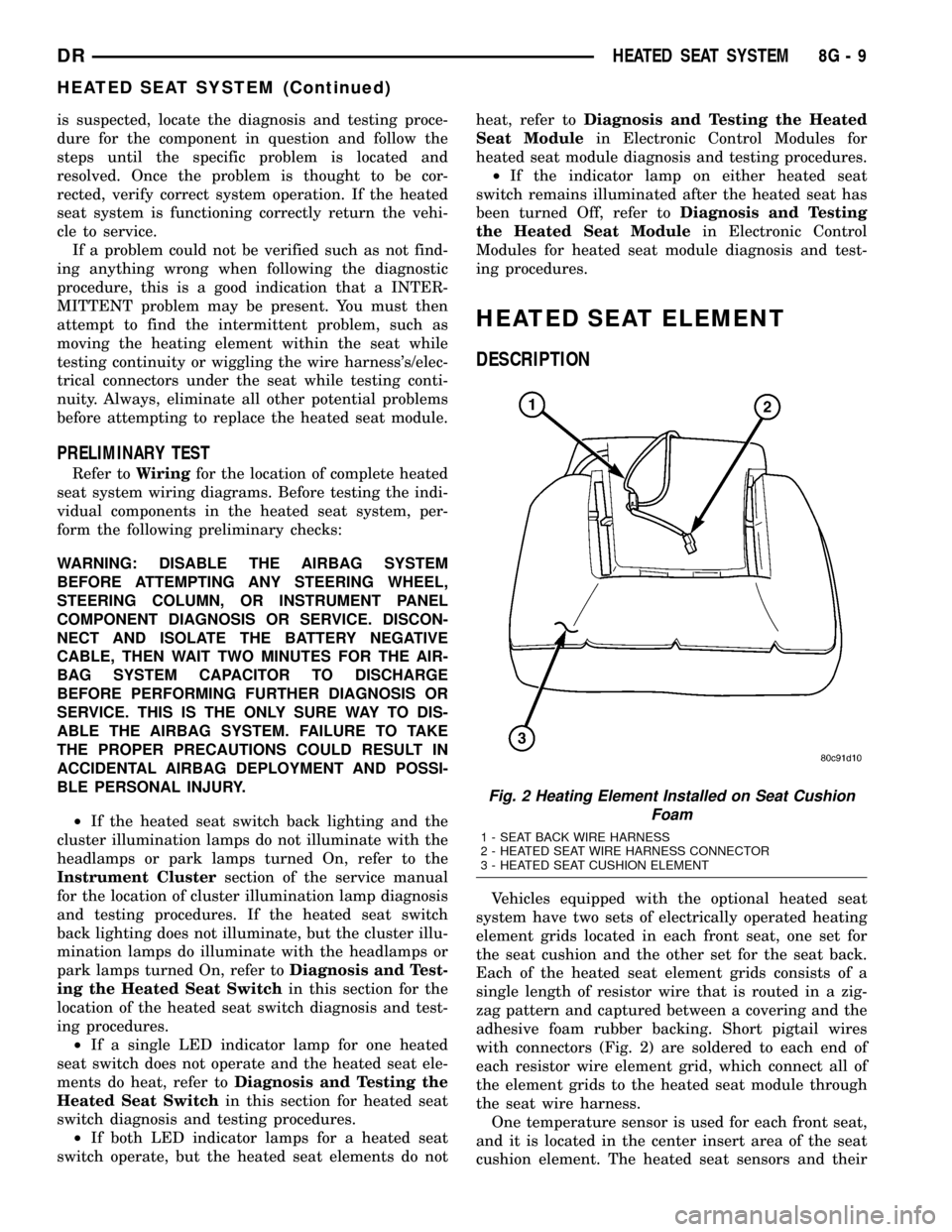
is suspected, locate the diagnosis and testing proce-
dure for the component in question and follow the
steps until the specific problem is located and
resolved. Once the problem is thought to be cor-
rected, verify correct system operation. If the heated
seat system is functioning correctly return the vehi-
cle to service.
If a problem could not be verified such as not find-
ing anything wrong when following the diagnostic
procedure, this is a good indication that a INTER-
MITTENT problem may be present. You must then
attempt to find the intermittent problem, such as
moving the heating element within the seat while
testing continuity or wiggling the wire harness's/elec-
trical connectors under the seat while testing conti-
nuity. Always, eliminate all other potential problems
before attempting to replace the heated seat module.
PRELIMINARY TEST
Refer toWiringfor the location of complete heated
seat system wiring diagrams. Before testing the indi-
vidual components in the heated seat system, per-
form the following preliminary checks:
WARNING: DISABLE THE AIRBAG SYSTEM
BEFORE ATTEMPTING ANY STEERING WHEEL,
STEERING COLUMN, OR INSTRUMENT PANEL
COMPONENT DIAGNOSIS OR SERVICE. DISCON-
NECT AND ISOLATE THE BATTERY NEGATIVE
CABLE, THEN WAIT TWO MINUTES FOR THE AIR-
BAG SYSTEM CAPACITOR TO DISCHARGE
BEFORE PERFORMING FURTHER DIAGNOSIS OR
SERVICE. THIS IS THE ONLY SURE WAY TO DIS-
ABLE THE AIRBAG SYSTEM. FAILURE TO TAKE
THE PROPER PRECAUTIONS COULD RESULT IN
ACCIDENTAL AIRBAG DEPLOYMENT AND POSSI-
BLE PERSONAL INJURY.
²If the heated seat switch back lighting and the
cluster illumination lamps do not illuminate with the
headlamps or park lamps turned On, refer to the
Instrument Clustersection of the service manual
for the location of cluster illumination lamp diagnosis
and testing procedures. If the heated seat switch
back lighting does not illuminate, but the cluster illu-
mination lamps do illuminate with the headlamps or
park lamps turned On, refer toDiagnosis and Test-
ing the Heated Seat Switchin this section for the
location of the heated seat switch diagnosis and test-
ing procedures.
²If a single LED indicator lamp for one heated
seat switch does not operate and the heated seat ele-
ments do heat, refer toDiagnosis and Testing the
Heated Seat Switchin this section for heated seat
switch diagnosis and testing procedures.
²If both LED indicator lamps for a heated seat
switch operate, but the heated seat elements do notheat, refer toDiagnosis and Testing the Heated
Seat Modulein Electronic Control Modules for
heated seat module diagnosis and testing procedures.
²If the indicator lamp on either heated seat
switch remains illuminated after the heated seat has
been turned Off, refer toDiagnosis and Testing
the Heated Seat Modulein Electronic Control
Modules for heated seat module diagnosis and test-
ing procedures.
HEATED SEAT ELEMENT
DESCRIPTION
Vehicles equipped with the optional heated seat
system have two sets of electrically operated heating
element grids located in each front seat, one set for
the seat cushion and the other set for the seat back.
Each of the heated seat element grids consists of a
single length of resistor wire that is routed in a zig-
zag pattern and captured between a covering and the
adhesive foam rubber backing. Short pigtail wires
with connectors (Fig. 2) are soldered to each end of
each resistor wire element grid, which connect all of
the element grids to the heated seat module through
the seat wire harness.
One temperature sensor is used for each front seat,
and it is located in the center insert area of the seat
cushion element. The heated seat sensors and their
Fig. 2 Heating Element Installed on Seat Cushion
Foam
1 - SEAT BACK WIRE HARNESS
2 - HEATED SEAT WIRE HARNESS CONNECTOR
3 - HEATED SEAT CUSHION ELEMENT
DRHEATED SEAT SYSTEM 8G - 9
HEATED SEAT SYSTEM (Continued)
Page 479 of 2627
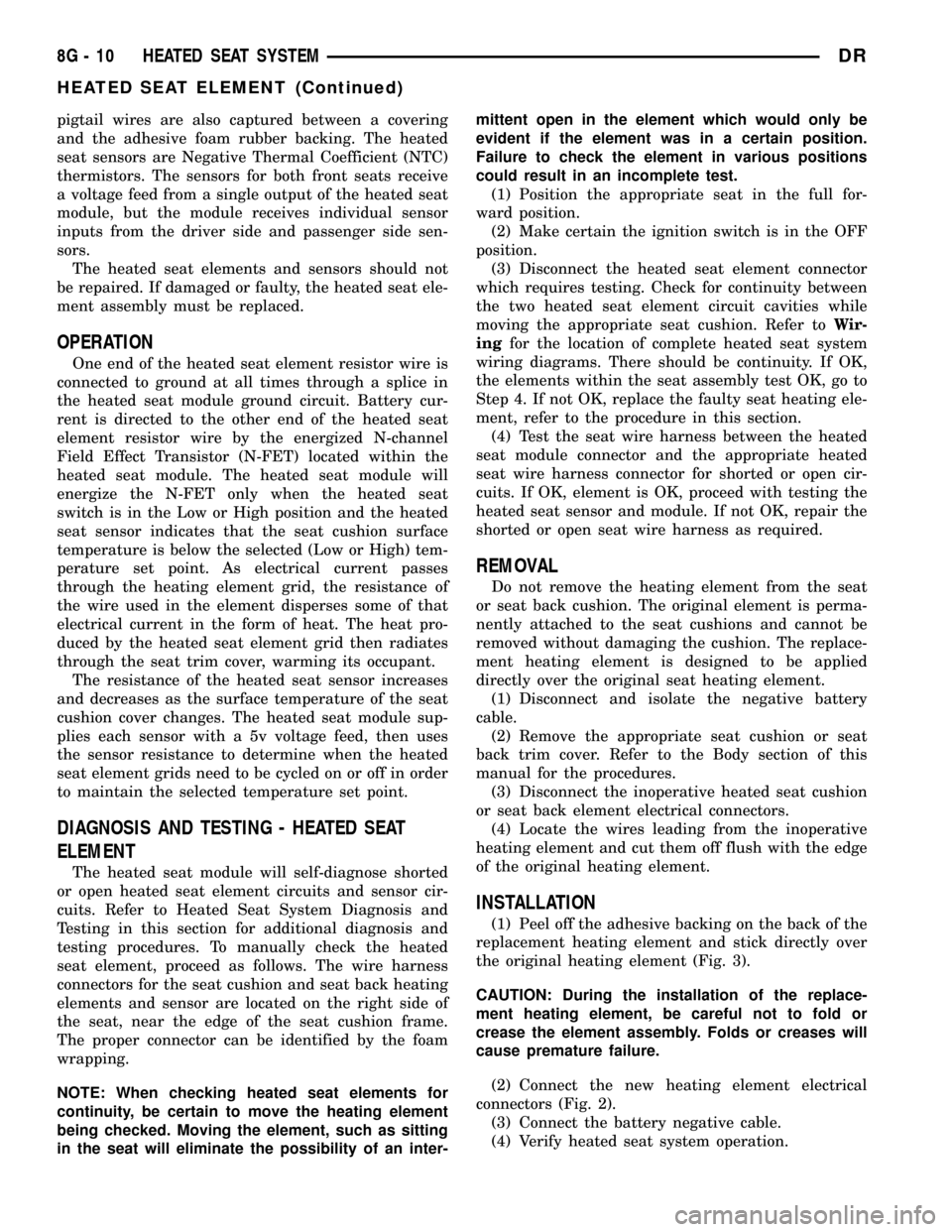
pigtail wires are also captured between a covering
and the adhesive foam rubber backing. The heated
seat sensors are Negative Thermal Coefficient (NTC)
thermistors. The sensors for both front seats receive
a voltage feed from a single output of the heated seat
module, but the module receives individual sensor
inputs from the driver side and passenger side sen-
sors.
The heated seat elements and sensors should not
be repaired. If damaged or faulty, the heated seat ele-
ment assembly must be replaced.
OPERATION
One end of the heated seat element resistor wire is
connected to ground at all times through a splice in
the heated seat module ground circuit. Battery cur-
rent is directed to the other end of the heated seat
element resistor wire by the energized N-channel
Field Effect Transistor (N-FET) located within the
heated seat module. The heated seat module will
energize the N-FET only when the heated seat
switch is in the Low or High position and the heated
seat sensor indicates that the seat cushion surface
temperature is below the selected (Low or High) tem-
perature set point. As electrical current passes
through the heating element grid, the resistance of
the wire used in the element disperses some of that
electrical current in the form of heat. The heat pro-
duced by the heated seat element grid then radiates
through the seat trim cover, warming its occupant.
The resistance of the heated seat sensor increases
and decreases as the surface temperature of the seat
cushion cover changes. The heated seat module sup-
plies each sensor with a 5v voltage feed, then uses
the sensor resistance to determine when the heated
seat element grids need to be cycled on or off in order
to maintain the selected temperature set point.
DIAGNOSIS AND TESTING - HEATED SEAT
ELEMENT
The heated seat module will self-diagnose shorted
or open heated seat element circuits and sensor cir-
cuits. Refer to Heated Seat System Diagnosis and
Testing in this section for additional diagnosis and
testing procedures. To manually check the heated
seat element, proceed as follows. The wire harness
connectors for the seat cushion and seat back heating
elements and sensor are located on the right side of
the seat, near the edge of the seat cushion frame.
The proper connector can be identified by the foam
wrapping.
NOTE: When checking heated seat elements for
continuity, be certain to move the heating element
being checked. Moving the element, such as sitting
in the seat will eliminate the possibility of an inter-mittent open in the element which would only be
evident if the element was in a certain position.
Failure to check the element in various positions
could result in an incomplete test.
(1) Position the appropriate seat in the full for-
ward position.
(2) Make certain the ignition switch is in the OFF
position.
(3) Disconnect the heated seat element connector
which requires testing. Check for continuity between
the two heated seat element circuit cavities while
moving the appropriate seat cushion. Refer toWir-
ingfor the location of complete heated seat system
wiring diagrams. There should be continuity. If OK,
the elements within the seat assembly test OK, go to
Step 4. If not OK, replace the faulty seat heating ele-
ment, refer to the procedure in this section.
(4) Test the seat wire harness between the heated
seat module connector and the appropriate heated
seat wire harness connector for shorted or open cir-
cuits. If OK, element is OK, proceed with testing the
heated seat sensor and module. If not OK, repair the
shorted or open seat wire harness as required.
REMOVAL
Do not remove the heating element from the seat
or seat back cushion. The original element is perma-
nently attached to the seat cushions and cannot be
removed without damaging the cushion. The replace-
ment heating element is designed to be applied
directly over the original seat heating element.
(1) Disconnect and isolate the negative battery
cable.
(2) Remove the appropriate seat cushion or seat
back trim cover. Refer to the Body section of this
manual for the procedures.
(3) Disconnect the inoperative heated seat cushion
or seat back element electrical connectors.
(4) Locate the wires leading from the inoperative
heating element and cut them off flush with the edge
of the original heating element.
INSTALLATION
(1) Peel off the adhesive backing on the back of the
replacement heating element and stick directly over
the original heating element (Fig. 3).
CAUTION: During the installation of the replace-
ment heating element, be careful not to fold or
crease the element assembly. Folds or creases will
cause premature failure.
(2) Connect the new heating element electrical
connectors (Fig. 2).
(3) Connect the battery negative cable.
(4) Verify heated seat system operation.
8G - 10 HEATED SEAT SYSTEMDR
HEATED SEAT ELEMENT (Continued)
Page 480 of 2627
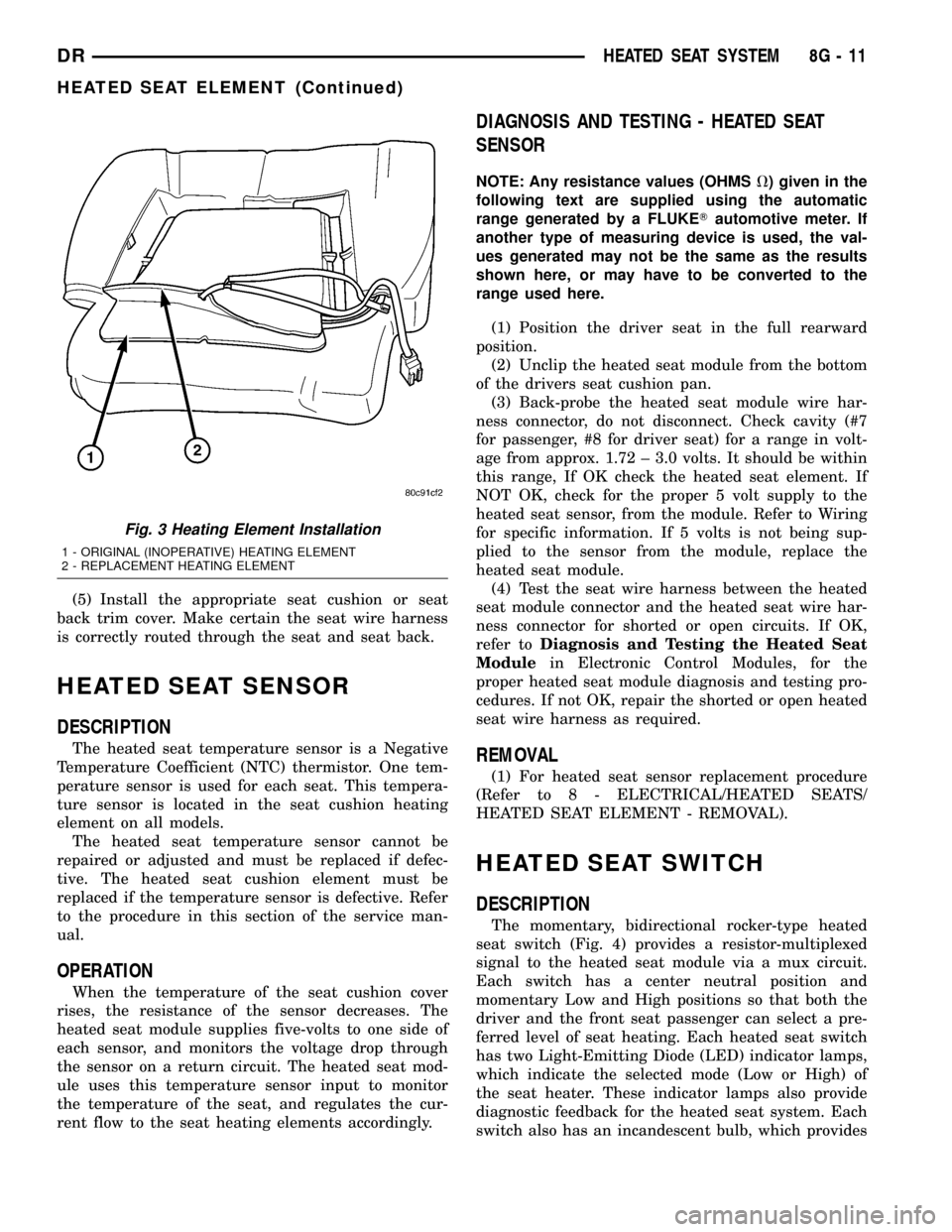
(5) Install the appropriate seat cushion or seat
back trim cover. Make certain the seat wire harness
is correctly routed through the seat and seat back.
HEATED SEAT SENSOR
DESCRIPTION
The heated seat temperature sensor is a Negative
Temperature Coefficient (NTC) thermistor. One tem-
perature sensor is used for each seat. This tempera-
ture sensor is located in the seat cushion heating
element on all models.
The heated seat temperature sensor cannot be
repaired or adjusted and must be replaced if defec-
tive. The heated seat cushion element must be
replaced if the temperature sensor is defective. Refer
to the procedure in this section of the service man-
ual.
OPERATION
When the temperature of the seat cushion cover
rises, the resistance of the sensor decreases. The
heated seat module supplies five-volts to one side of
each sensor, and monitors the voltage drop through
the sensor on a return circuit. The heated seat mod-
ule uses this temperature sensor input to monitor
the temperature of the seat, and regulates the cur-
rent flow to the seat heating elements accordingly.
DIAGNOSIS AND TESTING - HEATED SEAT
SENSOR
NOTE: Any resistance values (OHMSV) given in the
following text are supplied using the automatic
range generated by a FLUKETautomotive meter. If
another type of measuring device is used, the val-
ues generated may not be the same as the results
shown here, or may have to be converted to the
range used here.
(1) Position the driver seat in the full rearward
position.
(2) Unclip the heated seat module from the bottom
of the drivers seat cushion pan.
(3) Back-probe the heated seat module wire har-
ness connector, do not disconnect. Check cavity (#7
for passenger, #8 for driver seat) for a range in volt-
age from approx. 1.72 ± 3.0 volts. It should be within
this range, If OK check the heated seat element. If
NOT OK, check for the proper 5 volt supply to the
heated seat sensor, from the module. Refer to Wiring
for specific information. If 5 volts is not being sup-
plied to the sensor from the module, replace the
heated seat module.
(4) Test the seat wire harness between the heated
seat module connector and the heated seat wire har-
ness connector for shorted or open circuits. If OK,
refer toDiagnosis and Testing the Heated Seat
Modulein Electronic Control Modules, for the
proper heated seat module diagnosis and testing pro-
cedures. If not OK, repair the shorted or open heated
seat wire harness as required.
REMOVAL
(1) For heated seat sensor replacement procedure
(Refer to 8 - ELECTRICAL/HEATED SEATS/
HEATED SEAT ELEMENT - REMOVAL).
HEATED SEAT SWITCH
DESCRIPTION
The momentary, bidirectional rocker-type heated
seat switch (Fig. 4) provides a resistor-multiplexed
signal to the heated seat module via a mux circuit.
Each switch has a center neutral position and
momentary Low and High positions so that both the
driver and the front seat passenger can select a pre-
ferred level of seat heating. Each heated seat switch
has two Light-Emitting Diode (LED) indicator lamps,
which indicate the selected mode (Low or High) of
the seat heater. These indicator lamps also provide
diagnostic feedback for the heated seat system. Each
switch also has an incandescent bulb, which provides
Fig. 3 Heating Element Installation
1 - ORIGINAL (INOPERATIVE) HEATING ELEMENT
2 - REPLACEMENT HEATING ELEMENT
DRHEATED SEAT SYSTEM 8G - 11
HEATED SEAT ELEMENT (Continued)