Power control DODGE RAM 1500 1998 2.G Manual Online
[x] Cancel search | Manufacturer: DODGE, Model Year: 1998, Model line: RAM 1500, Model: DODGE RAM 1500 1998 2.GPages: 2627
Page 547 of 2627
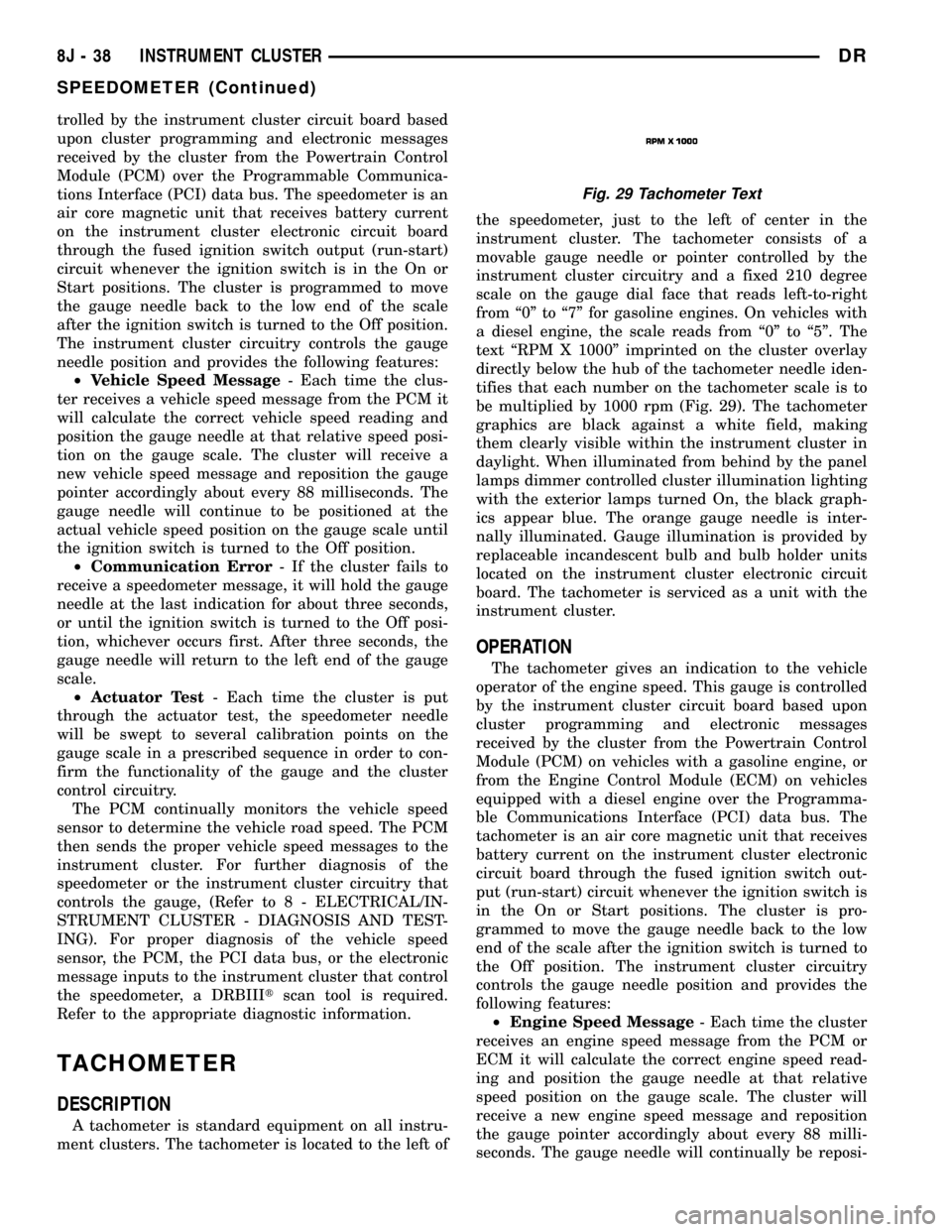
trolled by the instrument cluster circuit board based
upon cluster programming and electronic messages
received by the cluster from the Powertrain Control
Module (PCM) over the Programmable Communica-
tions Interface (PCI) data bus. The speedometer is an
air core magnetic unit that receives battery current
on the instrument cluster electronic circuit board
through the fused ignition switch output (run-start)
circuit whenever the ignition switch is in the On or
Start positions. The cluster is programmed to move
the gauge needle back to the low end of the scale
after the ignition switch is turned to the Off position.
The instrument cluster circuitry controls the gauge
needle position and provides the following features:
²Vehicle Speed Message- Each time the clus-
ter receives a vehicle speed message from the PCM it
will calculate the correct vehicle speed reading and
position the gauge needle at that relative speed posi-
tion on the gauge scale. The cluster will receive a
new vehicle speed message and reposition the gauge
pointer accordingly about every 88 milliseconds. The
gauge needle will continue to be positioned at the
actual vehicle speed position on the gauge scale until
the ignition switch is turned to the Off position.
²Communication Error- If the cluster fails to
receive a speedometer message, it will hold the gauge
needle at the last indication for about three seconds,
or until the ignition switch is turned to the Off posi-
tion, whichever occurs first. After three seconds, the
gauge needle will return to the left end of the gauge
scale.
²Actuator Test- Each time the cluster is put
through the actuator test, the speedometer needle
will be swept to several calibration points on the
gauge scale in a prescribed sequence in order to con-
firm the functionality of the gauge and the cluster
control circuitry.
The PCM continually monitors the vehicle speed
sensor to determine the vehicle road speed. The PCM
then sends the proper vehicle speed messages to the
instrument cluster. For further diagnosis of the
speedometer or the instrument cluster circuitry that
controls the gauge, (Refer to 8 - ELECTRICAL/IN-
STRUMENT CLUSTER - DIAGNOSIS AND TEST-
ING). For proper diagnosis of the vehicle speed
sensor, the PCM, the PCI data bus, or the electronic
message inputs to the instrument cluster that control
the speedometer, a DRBIIItscan tool is required.
Refer to the appropriate diagnostic information.
TACHOMETER
DESCRIPTION
A tachometer is standard equipment on all instru-
ment clusters. The tachometer is located to the left ofthe speedometer, just to the left of center in the
instrument cluster. The tachometer consists of a
movable gauge needle or pointer controlled by the
instrument cluster circuitry and a fixed 210 degree
scale on the gauge dial face that reads left-to-right
from ª0º to ª7º for gasoline engines. On vehicles with
a diesel engine, the scale reads from ª0º to ª5º. The
text ªRPM X 1000º imprinted on the cluster overlay
directly below the hub of the tachometer needle iden-
tifies that each number on the tachometer scale is to
be multiplied by 1000 rpm (Fig. 29). The tachometer
graphics are black against a white field, making
them clearly visible within the instrument cluster in
daylight. When illuminated from behind by the panel
lamps dimmer controlled cluster illumination lighting
with the exterior lamps turned On, the black graph-
ics appear blue. The orange gauge needle is inter-
nally illuminated. Gauge illumination is provided by
replaceable incandescent bulb and bulb holder units
located on the instrument cluster electronic circuit
board. The tachometer is serviced as a unit with the
instrument cluster.
OPERATION
The tachometer gives an indication to the vehicle
operator of the engine speed. This gauge is controlled
by the instrument cluster circuit board based upon
cluster programming and electronic messages
received by the cluster from the Powertrain Control
Module (PCM) on vehicles with a gasoline engine, or
from the Engine Control Module (ECM) on vehicles
equipped with a diesel engine over the Programma-
ble Communications Interface (PCI) data bus. The
tachometer is an air core magnetic unit that receives
battery current on the instrument cluster electronic
circuit board through the fused ignition switch out-
put (run-start) circuit whenever the ignition switch is
in the On or Start positions. The cluster is pro-
grammed to move the gauge needle back to the low
end of the scale after the ignition switch is turned to
the Off position. The instrument cluster circuitry
controls the gauge needle position and provides the
following features:
²Engine Speed Message- Each time the cluster
receives an engine speed message from the PCM or
ECM it will calculate the correct engine speed read-
ing and position the gauge needle at that relative
speed position on the gauge scale. The cluster will
receive a new engine speed message and reposition
the gauge pointer accordingly about every 88 milli-
seconds. The gauge needle will continually be reposi-
Fig. 29 Tachometer Text
8J - 38 INSTRUMENT CLUSTERDR
SPEEDOMETER (Continued)
Page 548 of 2627
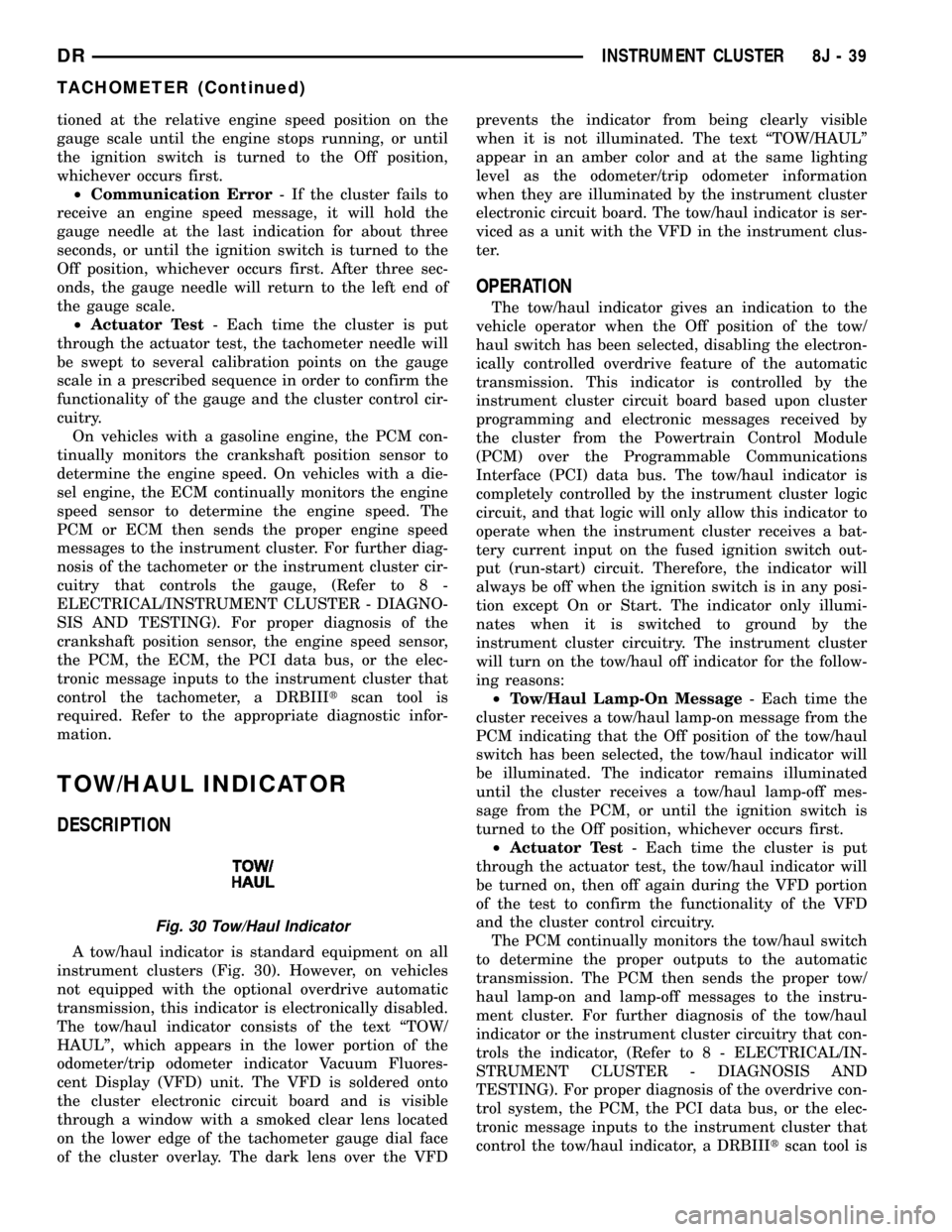
tioned at the relative engine speed position on the
gauge scale until the engine stops running, or until
the ignition switch is turned to the Off position,
whichever occurs first.
²Communication Error- If the cluster fails to
receive an engine speed message, it will hold the
gauge needle at the last indication for about three
seconds, or until the ignition switch is turned to the
Off position, whichever occurs first. After three sec-
onds, the gauge needle will return to the left end of
the gauge scale.
²Actuator Test- Each time the cluster is put
through the actuator test, the tachometer needle will
be swept to several calibration points on the gauge
scale in a prescribed sequence in order to confirm the
functionality of the gauge and the cluster control cir-
cuitry.
On vehicles with a gasoline engine, the PCM con-
tinually monitors the crankshaft position sensor to
determine the engine speed. On vehicles with a die-
sel engine, the ECM continually monitors the engine
speed sensor to determine the engine speed. The
PCM or ECM then sends the proper engine speed
messages to the instrument cluster. For further diag-
nosis of the tachometer or the instrument cluster cir-
cuitry that controls the gauge, (Refer to 8 -
ELECTRICAL/INSTRUMENT CLUSTER - DIAGNO-
SIS AND TESTING). For proper diagnosis of the
crankshaft position sensor, the engine speed sensor,
the PCM, the ECM, the PCI data bus, or the elec-
tronic message inputs to the instrument cluster that
control the tachometer, a DRBIIItscan tool is
required. Refer to the appropriate diagnostic infor-
mation.
TOW/HAUL INDICATOR
DESCRIPTION
A tow/haul indicator is standard equipment on all
instrument clusters (Fig. 30). However, on vehicles
not equipped with the optional overdrive automatic
transmission, this indicator is electronically disabled.
The tow/haul indicator consists of the text ªTOW/
HAULº, which appears in the lower portion of the
odometer/trip odometer indicator Vacuum Fluores-
cent Display (VFD) unit. The VFD is soldered onto
the cluster electronic circuit board and is visible
through a window with a smoked clear lens located
on the lower edge of the tachometer gauge dial face
of the cluster overlay. The dark lens over the VFDprevents the indicator from being clearly visible
when it is not illuminated. The text ªTOW/HAULº
appear in an amber color and at the same lighting
level as the odometer/trip odometer information
when they are illuminated by the instrument cluster
electronic circuit board. The tow/haul indicator is ser-
viced as a unit with the VFD in the instrument clus-
ter.
OPERATION
The tow/haul indicator gives an indication to the
vehicle operator when the Off position of the tow/
haul switch has been selected, disabling the electron-
ically controlled overdrive feature of the automatic
transmission. This indicator is controlled by the
instrument cluster circuit board based upon cluster
programming and electronic messages received by
the cluster from the Powertrain Control Module
(PCM) over the Programmable Communications
Interface (PCI) data bus. The tow/haul indicator is
completely controlled by the instrument cluster logic
circuit, and that logic will only allow this indicator to
operate when the instrument cluster receives a bat-
tery current input on the fused ignition switch out-
put (run-start) circuit. Therefore, the indicator will
always be off when the ignition switch is in any posi-
tion except On or Start. The indicator only illumi-
nates when it is switched to ground by the
instrument cluster circuitry. The instrument cluster
will turn on the tow/haul off indicator for the follow-
ing reasons:
²Tow/Haul Lamp-On Message- Each time the
cluster receives a tow/haul lamp-on message from the
PCM indicating that the Off position of the tow/haul
switch has been selected, the tow/haul indicator will
be illuminated. The indicator remains illuminated
until the cluster receives a tow/haul lamp-off mes-
sage from the PCM, or until the ignition switch is
turned to the Off position, whichever occurs first.
²Actuator Test- Each time the cluster is put
through the actuator test, the tow/haul indicator will
be turned on, then off again during the VFD portion
of the test to confirm the functionality of the VFD
and the cluster control circuitry.
The PCM continually monitors the tow/haul switch
to determine the proper outputs to the automatic
transmission. The PCM then sends the proper tow/
haul lamp-on and lamp-off messages to the instru-
ment cluster. For further diagnosis of the tow/haul
indicator or the instrument cluster circuitry that con-
trols the indicator, (Refer to 8 - ELECTRICAL/IN-
STRUMENT CLUSTER - DIAGNOSIS AND
TESTING). For proper diagnosis of the overdrive con-
trol system, the PCM, the PCI data bus, or the elec-
tronic message inputs to the instrument cluster that
control the tow/haul indicator, a DRBIIItscan tool is
Fig. 30 Tow/Haul Indicator
DRINSTRUMENT CLUSTER 8J - 39
TACHOMETER (Continued)
Page 549 of 2627
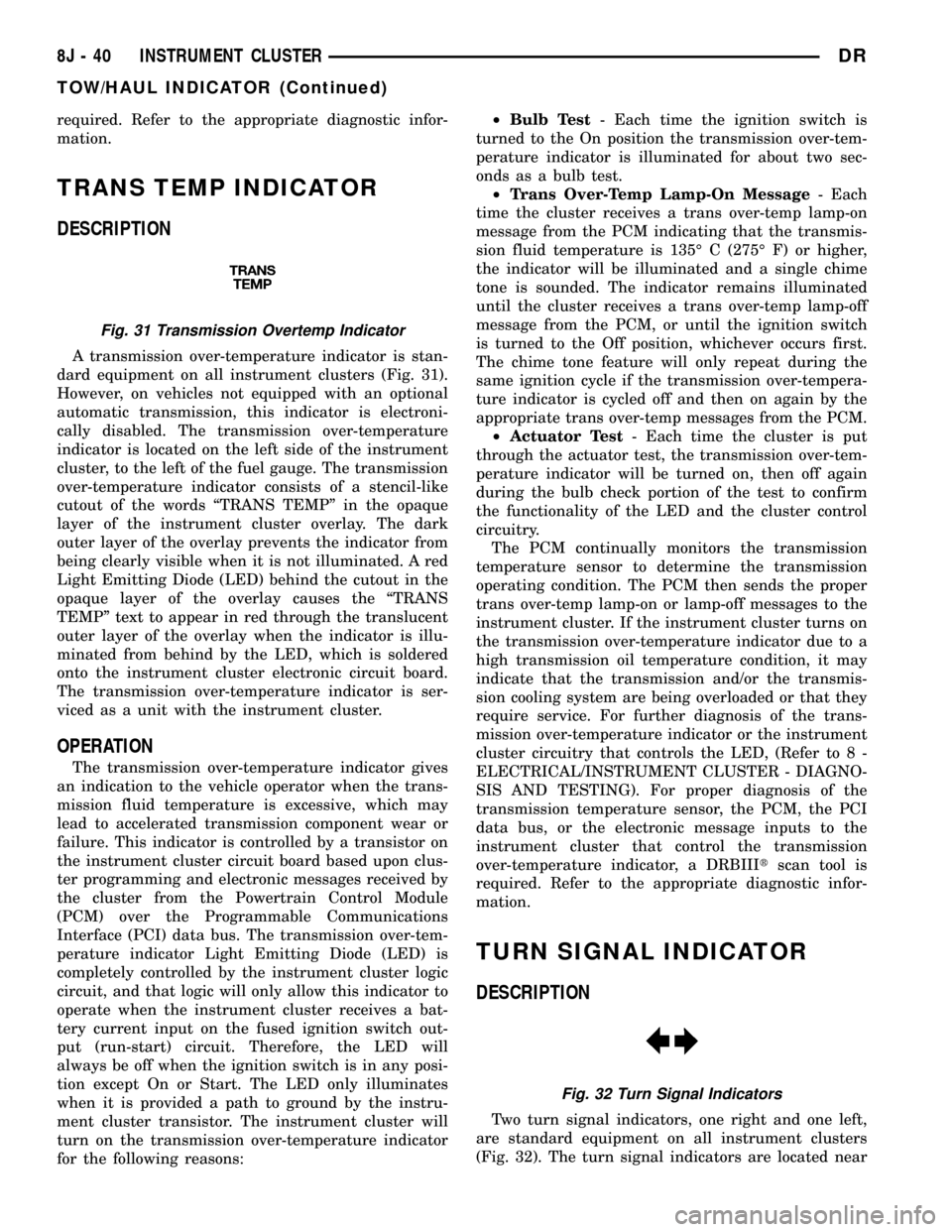
required. Refer to the appropriate diagnostic infor-
mation.
TRANS TEMP INDICATOR
DESCRIPTION
A transmission over-temperature indicator is stan-
dard equipment on all instrument clusters (Fig. 31).
However, on vehicles not equipped with an optional
automatic transmission, this indicator is electroni-
cally disabled. The transmission over-temperature
indicator is located on the left side of the instrument
cluster, to the left of the fuel gauge. The transmission
over-temperature indicator consists of a stencil-like
cutout of the words ªTRANS TEMPº in the opaque
layer of the instrument cluster overlay. The dark
outer layer of the overlay prevents the indicator from
being clearly visible when it is not illuminated. A red
Light Emitting Diode (LED) behind the cutout in the
opaque layer of the overlay causes the ªTRANS
TEMPº text to appear in red through the translucent
outer layer of the overlay when the indicator is illu-
minated from behind by the LED, which is soldered
onto the instrument cluster electronic circuit board.
The transmission over-temperature indicator is ser-
viced as a unit with the instrument cluster.
OPERATION
The transmission over-temperature indicator gives
an indication to the vehicle operator when the trans-
mission fluid temperature is excessive, which may
lead to accelerated transmission component wear or
failure. This indicator is controlled by a transistor on
the instrument cluster circuit board based upon clus-
ter programming and electronic messages received by
the cluster from the Powertrain Control Module
(PCM) over the Programmable Communications
Interface (PCI) data bus. The transmission over-tem-
perature indicator Light Emitting Diode (LED) is
completely controlled by the instrument cluster logic
circuit, and that logic will only allow this indicator to
operate when the instrument cluster receives a bat-
tery current input on the fused ignition switch out-
put (run-start) circuit. Therefore, the LED will
always be off when the ignition switch is in any posi-
tion except On or Start. The LED only illuminates
when it is provided a path to ground by the instru-
ment cluster transistor. The instrument cluster will
turn on the transmission over-temperature indicator
for the following reasons:²Bulb Test- Each time the ignition switch is
turned to the On position the transmission over-tem-
perature indicator is illuminated for about two sec-
onds as a bulb test.
²Trans Over-Temp Lamp-On Message- Each
time the cluster receives a trans over-temp lamp-on
message from the PCM indicating that the transmis-
sion fluid temperature is 135É C (275É F) or higher,
the indicator will be illuminated and a single chime
tone is sounded. The indicator remains illuminated
until the cluster receives a trans over-temp lamp-off
message from the PCM, or until the ignition switch
is turned to the Off position, whichever occurs first.
The chime tone feature will only repeat during the
same ignition cycle if the transmission over-tempera-
ture indicator is cycled off and then on again by the
appropriate trans over-temp messages from the PCM.
²Actuator Test- Each time the cluster is put
through the actuator test, the transmission over-tem-
perature indicator will be turned on, then off again
during the bulb check portion of the test to confirm
the functionality of the LED and the cluster control
circuitry.
The PCM continually monitors the transmission
temperature sensor to determine the transmission
operating condition. The PCM then sends the proper
trans over-temp lamp-on or lamp-off messages to the
instrument cluster. If the instrument cluster turns on
the transmission over-temperature indicator due to a
high transmission oil temperature condition, it may
indicate that the transmission and/or the transmis-
sion cooling system are being overloaded or that they
require service. For further diagnosis of the trans-
mission over-temperature indicator or the instrument
cluster circuitry that controls the LED, (Refer to 8 -
ELECTRICAL/INSTRUMENT CLUSTER - DIAGNO-
SIS AND TESTING). For proper diagnosis of the
transmission temperature sensor, the PCM, the PCI
data bus, or the electronic message inputs to the
instrument cluster that control the transmission
over-temperature indicator, a DRBIIItscan tool is
required. Refer to the appropriate diagnostic infor-
mation.
TURN SIGNAL INDICATOR
DESCRIPTION
Two turn signal indicators, one right and one left,
are standard equipment on all instrument clusters
(Fig. 32). The turn signal indicators are located near
Fig. 31 Transmission Overtemp Indicator
Fig. 32 Turn Signal Indicators
8J - 40 INSTRUMENT CLUSTERDR
TOW/HAUL INDICATOR (Continued)
Page 551 of 2627
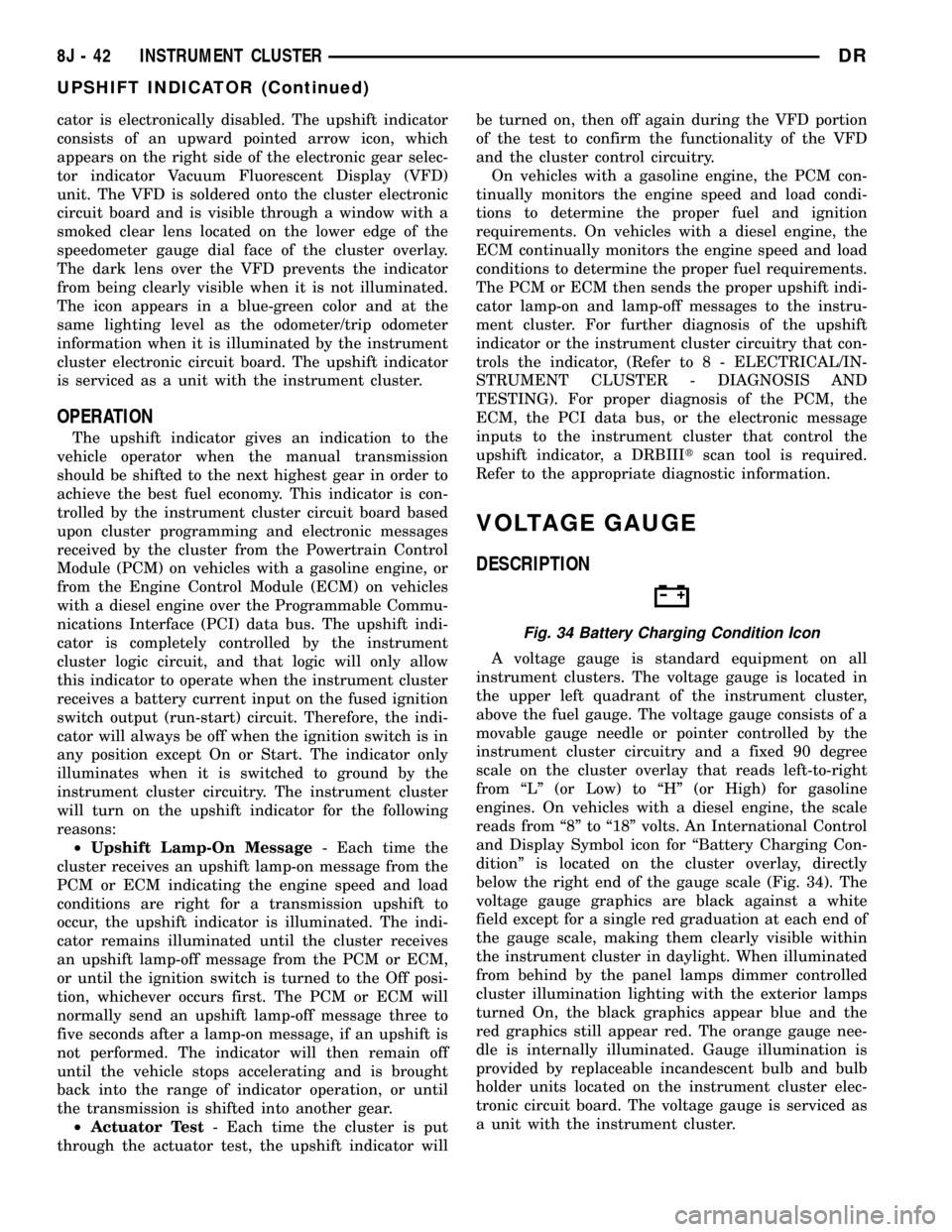
cator is electronically disabled. The upshift indicator
consists of an upward pointed arrow icon, which
appears on the right side of the electronic gear selec-
tor indicator Vacuum Fluorescent Display (VFD)
unit. The VFD is soldered onto the cluster electronic
circuit board and is visible through a window with a
smoked clear lens located on the lower edge of the
speedometer gauge dial face of the cluster overlay.
The dark lens over the VFD prevents the indicator
from being clearly visible when it is not illuminated.
The icon appears in a blue-green color and at the
same lighting level as the odometer/trip odometer
information when it is illuminated by the instrument
cluster electronic circuit board. The upshift indicator
is serviced as a unit with the instrument cluster.
OPERATION
The upshift indicator gives an indication to the
vehicle operator when the manual transmission
should be shifted to the next highest gear in order to
achieve the best fuel economy. This indicator is con-
trolled by the instrument cluster circuit board based
upon cluster programming and electronic messages
received by the cluster from the Powertrain Control
Module (PCM) on vehicles with a gasoline engine, or
from the Engine Control Module (ECM) on vehicles
with a diesel engine over the Programmable Commu-
nications Interface (PCI) data bus. The upshift indi-
cator is completely controlled by the instrument
cluster logic circuit, and that logic will only allow
this indicator to operate when the instrument cluster
receives a battery current input on the fused ignition
switch output (run-start) circuit. Therefore, the indi-
cator will always be off when the ignition switch is in
any position except On or Start. The indicator only
illuminates when it is switched to ground by the
instrument cluster circuitry. The instrument cluster
will turn on the upshift indicator for the following
reasons:
²Upshift Lamp-On Message- Each time the
cluster receives an upshift lamp-on message from the
PCM or ECM indicating the engine speed and load
conditions are right for a transmission upshift to
occur, the upshift indicator is illuminated. The indi-
cator remains illuminated until the cluster receives
an upshift lamp-off message from the PCM or ECM,
or until the ignition switch is turned to the Off posi-
tion, whichever occurs first. The PCM or ECM will
normally send an upshift lamp-off message three to
five seconds after a lamp-on message, if an upshift is
not performed. The indicator will then remain off
until the vehicle stops accelerating and is brought
back into the range of indicator operation, or until
the transmission is shifted into another gear.
²Actuator Test- Each time the cluster is put
through the actuator test, the upshift indicator willbe turned on, then off again during the VFD portion
of the test to confirm the functionality of the VFD
and the cluster control circuitry.
On vehicles with a gasoline engine, the PCM con-
tinually monitors the engine speed and load condi-
tions to determine the proper fuel and ignition
requirements. On vehicles with a diesel engine, the
ECM continually monitors the engine speed and load
conditions to determine the proper fuel requirements.
The PCM or ECM then sends the proper upshift indi-
cator lamp-on and lamp-off messages to the instru-
ment cluster. For further diagnosis of the upshift
indicator or the instrument cluster circuitry that con-
trols the indicator, (Refer to 8 - ELECTRICAL/IN-
STRUMENT CLUSTER - DIAGNOSIS AND
TESTING). For proper diagnosis of the PCM, the
ECM, the PCI data bus, or the electronic message
inputs to the instrument cluster that control the
upshift indicator, a DRBIIItscan tool is required.
Refer to the appropriate diagnostic information.
VOLTAGE GAUGE
DESCRIPTION
A voltage gauge is standard equipment on all
instrument clusters. The voltage gauge is located in
the upper left quadrant of the instrument cluster,
above the fuel gauge. The voltage gauge consists of a
movable gauge needle or pointer controlled by the
instrument cluster circuitry and a fixed 90 degree
scale on the cluster overlay that reads left-to-right
from ªLº (or Low) to ªHº (or High) for gasoline
engines. On vehicles with a diesel engine, the scale
reads from ª8º to ª18º volts. An International Control
and Display Symbol icon for ªBattery Charging Con-
ditionº is located on the cluster overlay, directly
below the right end of the gauge scale (Fig. 34). The
voltage gauge graphics are black against a white
field except for a single red graduation at each end of
the gauge scale, making them clearly visible within
the instrument cluster in daylight. When illuminated
from behind by the panel lamps dimmer controlled
cluster illumination lighting with the exterior lamps
turned On, the black graphics appear blue and the
red graphics still appear red. The orange gauge nee-
dle is internally illuminated. Gauge illumination is
provided by replaceable incandescent bulb and bulb
holder units located on the instrument cluster elec-
tronic circuit board. The voltage gauge is serviced as
a unit with the instrument cluster.
Fig. 34 Battery Charging Condition Icon
8J - 42 INSTRUMENT CLUSTERDR
UPSHIFT INDICATOR (Continued)
Page 552 of 2627
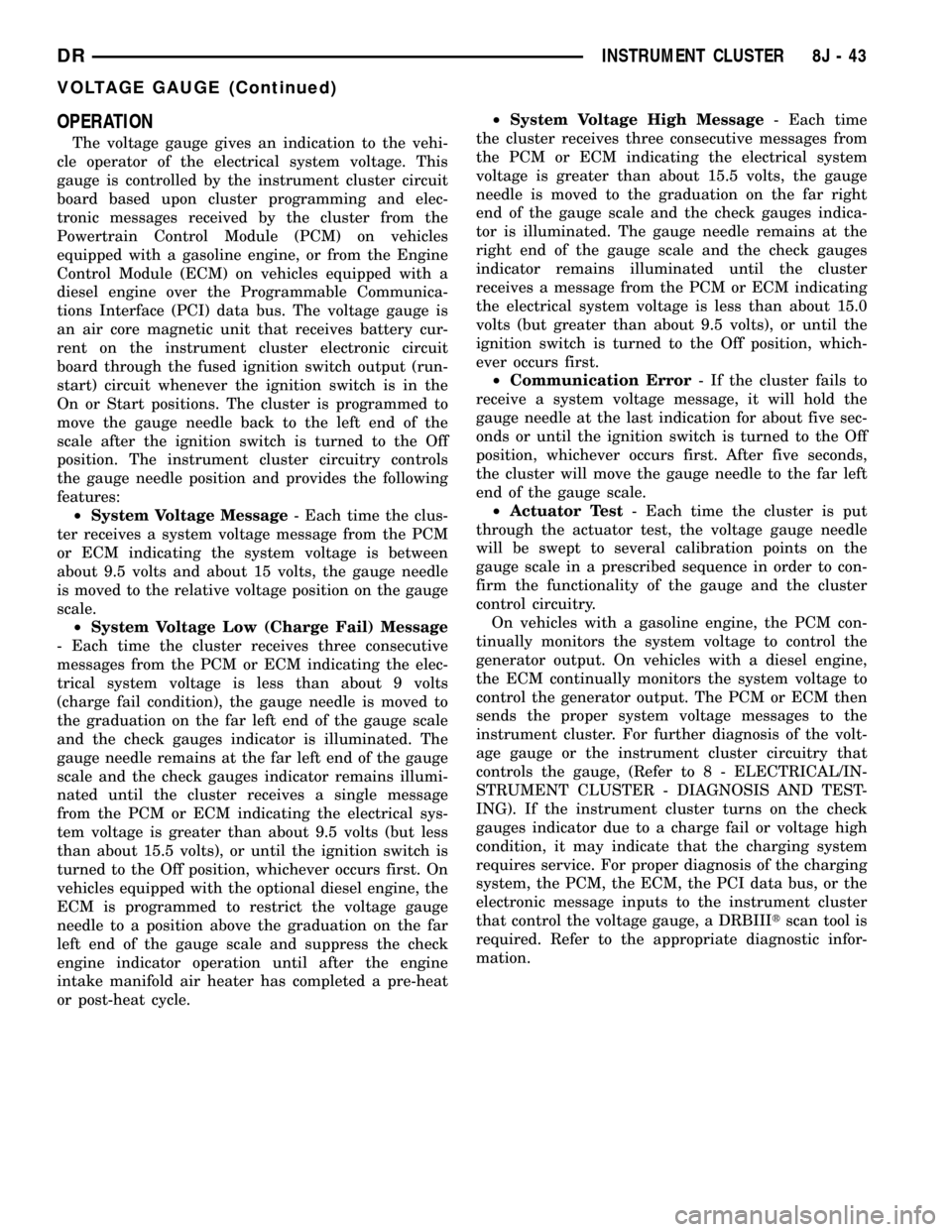
OPERATION
The voltage gauge gives an indication to the vehi-
cle operator of the electrical system voltage. This
gauge is controlled by the instrument cluster circuit
board based upon cluster programming and elec-
tronic messages received by the cluster from the
Powertrain Control Module (PCM) on vehicles
equipped with a gasoline engine, or from the Engine
Control Module (ECM) on vehicles equipped with a
diesel engine over the Programmable Communica-
tions Interface (PCI) data bus. The voltage gauge is
an air core magnetic unit that receives battery cur-
rent on the instrument cluster electronic circuit
board through the fused ignition switch output (run-
start) circuit whenever the ignition switch is in the
On or Start positions. The cluster is programmed to
move the gauge needle back to the left end of the
scale after the ignition switch is turned to the Off
position. The instrument cluster circuitry controls
the gauge needle position and provides the following
features:
²System Voltage Message- Each time the clus-
ter receives a system voltage message from the PCM
or ECM indicating the system voltage is between
about 9.5 volts and about 15 volts, the gauge needle
is moved to the relative voltage position on the gauge
scale.
²System Voltage Low (Charge Fail) Message
- Each time the cluster receives three consecutive
messages from the PCM or ECM indicating the elec-
trical system voltage is less than about 9 volts
(charge fail condition), the gauge needle is moved to
the graduation on the far left end of the gauge scale
and the check gauges indicator is illuminated. The
gauge needle remains at the far left end of the gauge
scale and the check gauges indicator remains illumi-
nated until the cluster receives a single message
from the PCM or ECM indicating the electrical sys-
tem voltage is greater than about 9.5 volts (but less
than about 15.5 volts), or until the ignition switch is
turned to the Off position, whichever occurs first. On
vehicles equipped with the optional diesel engine, the
ECM is programmed to restrict the voltage gauge
needle to a position above the graduation on the far
left end of the gauge scale and suppress the check
engine indicator operation until after the engine
intake manifold air heater has completed a pre-heat
or post-heat cycle.²System Voltage High Message- Each time
the cluster receives three consecutive messages from
the PCM or ECM indicating the electrical system
voltage is greater than about 15.5 volts, the gauge
needle is moved to the graduation on the far right
end of the gauge scale and the check gauges indica-
tor is illuminated. The gauge needle remains at the
right end of the gauge scale and the check gauges
indicator remains illuminated until the cluster
receives a message from the PCM or ECM indicating
the electrical system voltage is less than about 15.0
volts (but greater than about 9.5 volts), or until the
ignition switch is turned to the Off position, which-
ever occurs first.
²Communication Error- If the cluster fails to
receive a system voltage message, it will hold the
gauge needle at the last indication for about five sec-
onds or until the ignition switch is turned to the Off
position, whichever occurs first. After five seconds,
the cluster will move the gauge needle to the far left
end of the gauge scale.
²Actuator Test- Each time the cluster is put
through the actuator test, the voltage gauge needle
will be swept to several calibration points on the
gauge scale in a prescribed sequence in order to con-
firm the functionality of the gauge and the cluster
control circuitry.
On vehicles with a gasoline engine, the PCM con-
tinually monitors the system voltage to control the
generator output. On vehicles with a diesel engine,
the ECM continually monitors the system voltage to
control the generator output. The PCM or ECM then
sends the proper system voltage messages to the
instrument cluster. For further diagnosis of the volt-
age gauge or the instrument cluster circuitry that
controls the gauge, (Refer to 8 - ELECTRICAL/IN-
STRUMENT CLUSTER - DIAGNOSIS AND TEST-
ING). If the instrument cluster turns on the check
gauges indicator due to a charge fail or voltage high
condition, it may indicate that the charging system
requires service. For proper diagnosis of the charging
system, the PCM, the ECM, the PCI data bus, or the
electronic message inputs to the instrument cluster
that control the voltage gauge, a DRBIIItscan tool is
required. Refer to the appropriate diagnostic infor-
mation.
DRINSTRUMENT CLUSTER 8J - 43
VOLTAGE GAUGE (Continued)
Page 557 of 2627
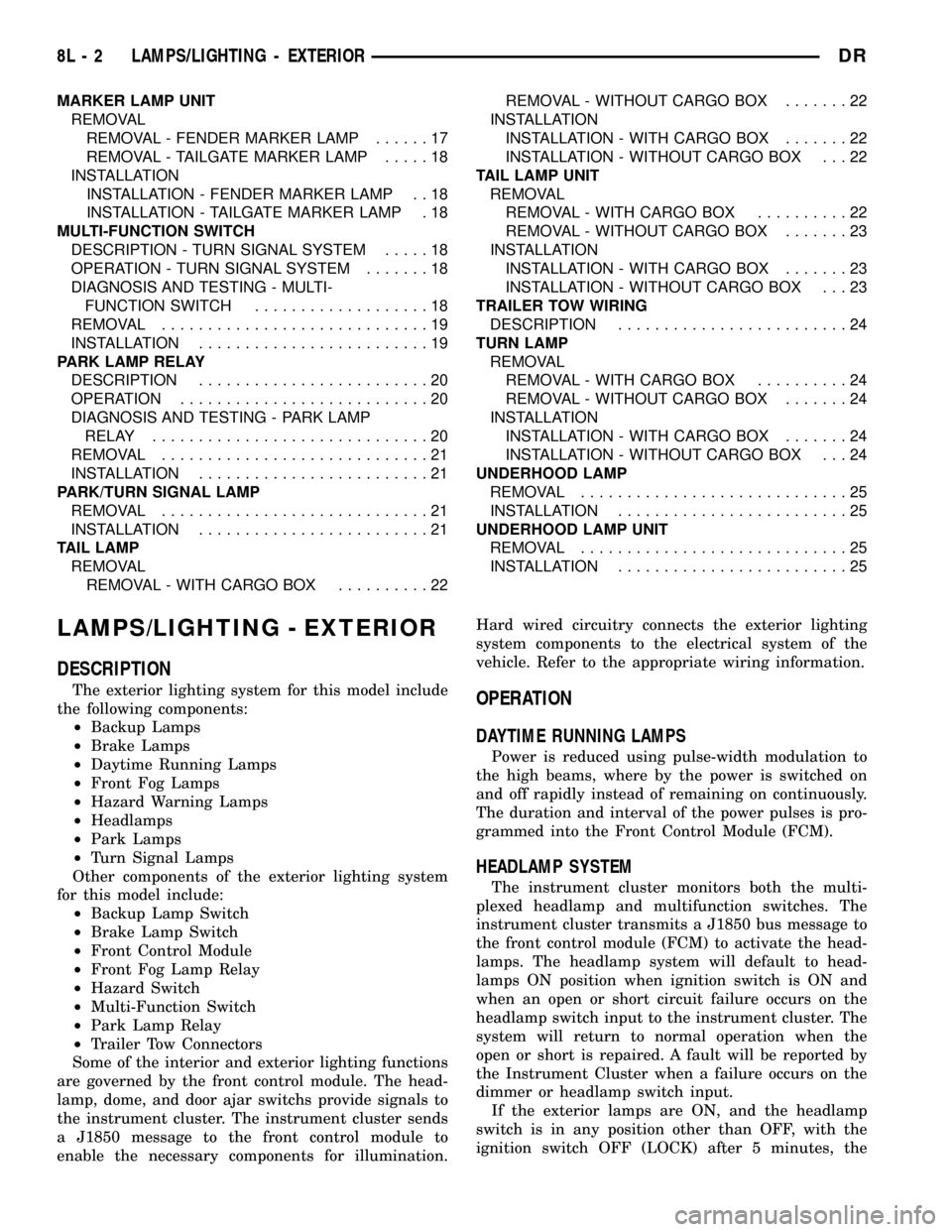
MARKER LAMP UNIT
REMOVAL
REMOVAL - FENDER MARKER LAMP......17
REMOVAL - TAILGATE MARKER LAMP.....18
INSTALLATION
INSTALLATION - FENDER MARKER LAMP . . 18
INSTALLATION - TAILGATE MARKER LAMP . 18
MULTI-FUNCTION SWITCH
DESCRIPTION - TURN SIGNAL SYSTEM.....18
OPERATION - TURN SIGNAL SYSTEM.......18
DIAGNOSIS AND TESTING - MULTI-
FUNCTION SWITCH...................18
REMOVAL.............................19
INSTALLATION.........................19
PARK LAMP RELAY
DESCRIPTION.........................20
OPERATION...........................20
DIAGNOSIS AND TESTING - PARK LAMP
RELAY..............................20
REMOVAL.............................21
INSTALLATION.........................21
PARK/TURN SIGNAL LAMP
REMOVAL.............................21
INSTALLATION.........................21
TAIL LAMP
REMOVAL
REMOVAL - WITH CARGO BOX..........22REMOVAL - WITHOUT CARGO BOX.......22
INSTALLATION
INSTALLATION - WITH CARGO BOX.......22
INSTALLATION - WITHOUT CARGO BOX . . . 22
TAIL LAMP UNIT
REMOVAL
REMOVAL - WITH CARGO BOX..........22
REMOVAL - WITHOUT CARGO BOX.......23
INSTALLATION
INSTALLATION - WITH CARGO BOX.......23
INSTALLATION - WITHOUT CARGO BOX . . . 23
TRAILER TOW WIRING
DESCRIPTION.........................24
TURN LAMP
REMOVAL
REMOVAL - WITH CARGO BOX..........24
REMOVAL - WITHOUT CARGO BOX.......24
INSTALLATION
INSTALLATION - WITH CARGO BOX.......24
INSTALLATION - WITHOUT CARGO BOX . . . 24
UNDERHOOD LAMP
REMOVAL.............................25
INSTALLATION.........................25
UNDERHOOD LAMP UNIT
REMOVAL.............................25
INSTALLATION.........................25
LAMPS/LIGHTING - EXTERIOR
DESCRIPTION
The exterior lighting system for this model include
the following components:
²Backup Lamps
²Brake Lamps
²Daytime Running Lamps
²Front Fog Lamps
²Hazard Warning Lamps
²Headlamps
²Park Lamps
²Turn Signal Lamps
Other components of the exterior lighting system
for this model include:
²Backup Lamp Switch
²Brake Lamp Switch
²Front Control Module
²Front Fog Lamp Relay
²Hazard Switch
²Multi-Function Switch
²Park Lamp Relay
²Trailer Tow Connectors
Some of the interior and exterior lighting functions
are governed by the front control module. The head-
lamp, dome, and door ajar switchs provide signals to
the instrument cluster. The instrument cluster sends
a J1850 message to the front control module to
enable the necessary components for illumination.Hard wired circuitry connects the exterior lighting
system components to the electrical system of the
vehicle. Refer to the appropriate wiring information.OPERATION
DAYTIME RUNNING LAMPS
Power is reduced using pulse-width modulation to
the high beams, where by the power is switched on
and off rapidly instead of remaining on continuously.
The duration and interval of the power pulses is pro-
grammed into the Front Control Module (FCM).
HEADLAMP SYSTEM
The instrument cluster monitors both the multi-
plexed headlamp and multifunction switches. The
instrument cluster transmits a J1850 bus message to
the front control module (FCM) to activate the head-
lamps. The headlamp system will default to head-
lamps ON position when ignition switch is ON and
when an open or short circuit failure occurs on the
headlamp switch input to the instrument cluster. The
system will return to normal operation when the
open or short is repaired. A fault will be reported by
the Instrument Cluster when a failure occurs on the
dimmer or headlamp switch input.
If the exterior lamps are ON, and the headlamp
switch is in any position other than OFF, with the
ignition switch OFF (LOCK) after 5 minutes, the
8L - 2 LAMPS/LIGHTING - EXTERIORDR
Page 563 of 2627
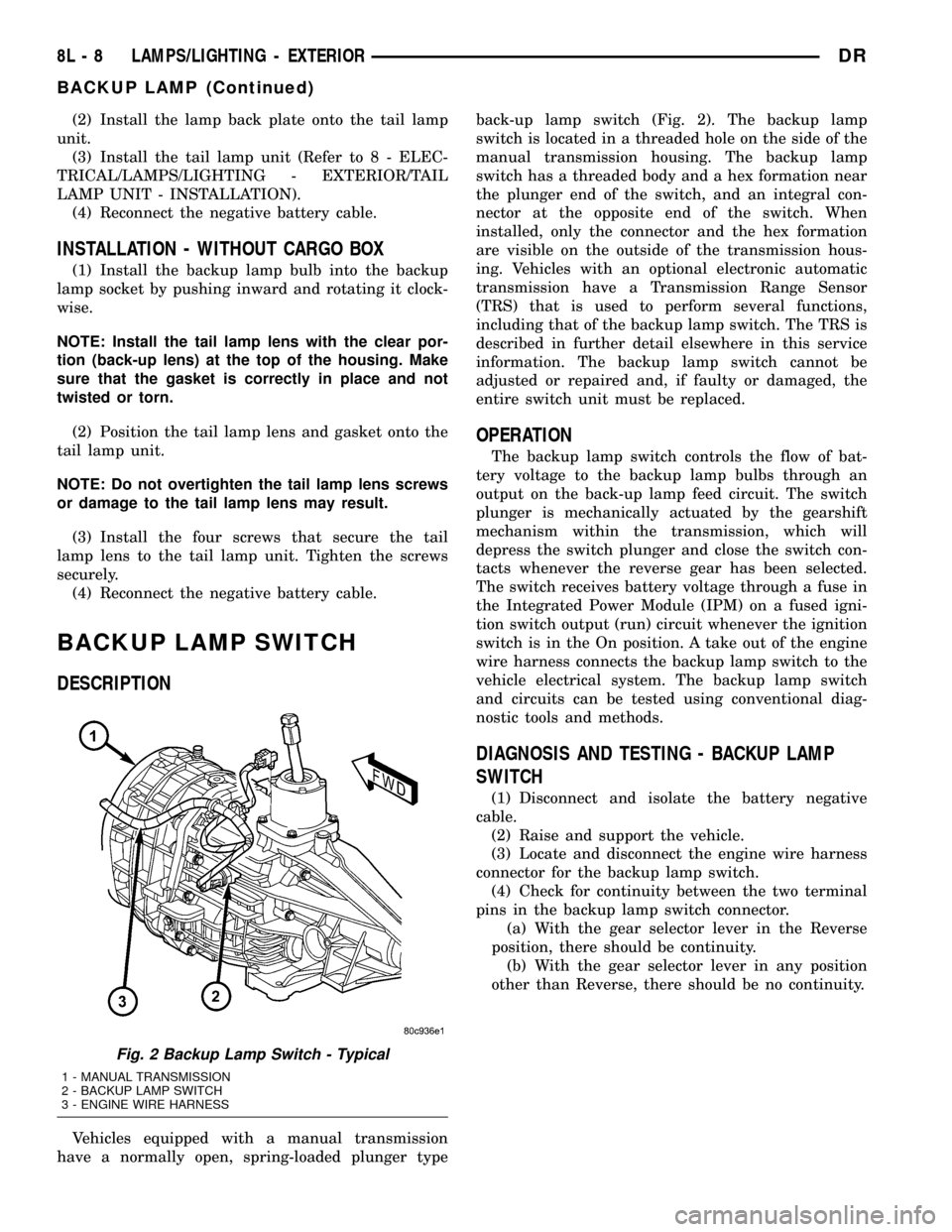
(2) Install the lamp back plate onto the tail lamp
unit.
(3) Install the tail lamp unit (Refer to 8 - ELEC-
TRICAL/LAMPS/LIGHTING - EXTERIOR/TAIL
LAMP UNIT - INSTALLATION).
(4) Reconnect the negative battery cable.
INSTALLATION - WITHOUT CARGO BOX
(1) Install the backup lamp bulb into the backup
lamp socket by pushing inward and rotating it clock-
wise.
NOTE: Install the tail lamp lens with the clear por-
tion (back-up lens) at the top of the housing. Make
sure that the gasket is correctly in place and not
twisted or torn.
(2) Position the tail lamp lens and gasket onto the
tail lamp unit.
NOTE: Do not overtighten the tail lamp lens screws
or damage to the tail lamp lens may result.
(3) Install the four screws that secure the tail
lamp lens to the tail lamp unit. Tighten the screws
securely.
(4) Reconnect the negative battery cable.
BACKUP LAMP SWITCH
DESCRIPTION
Vehicles equipped with a manual transmission
have a normally open, spring-loaded plunger typeback-up lamp switch (Fig. 2). The backup lamp
switch is located in a threaded hole on the side of the
manual transmission housing. The backup lamp
switch has a threaded body and a hex formation near
the plunger end of the switch, and an integral con-
nector at the opposite end of the switch. When
installed, only the connector and the hex formation
are visible on the outside of the transmission hous-
ing. Vehicles with an optional electronic automatic
transmission have a Transmission Range Sensor
(TRS) that is used to perform several functions,
including that of the backup lamp switch. The TRS is
described in further detail elsewhere in this service
information. The backup lamp switch cannot be
adjusted or repaired and, if faulty or damaged, the
entire switch unit must be replaced.
OPERATION
The backup lamp switch controls the flow of bat-
tery voltage to the backup lamp bulbs through an
output on the back-up lamp feed circuit. The switch
plunger is mechanically actuated by the gearshift
mechanism within the transmission, which will
depress the switch plunger and close the switch con-
tacts whenever the reverse gear has been selected.
The switch receives battery voltage through a fuse in
the Integrated Power Module (IPM) on a fused igni-
tion switch output (run) circuit whenever the ignition
switch is in the On position. A take out of the engine
wire harness connects the backup lamp switch to the
vehicle electrical system. The backup lamp switch
and circuits can be tested using conventional diag-
nostic tools and methods.
DIAGNOSIS AND TESTING - BACKUP LAMP
SWITCH
(1) Disconnect and isolate the battery negative
cable.
(2) Raise and support the vehicle.
(3) Locate and disconnect the engine wire harness
connector for the backup lamp switch.
(4) Check for continuity between the two terminal
pins in the backup lamp switch connector.
(a) With the gear selector lever in the Reverse
position, there should be continuity.
(b) With the gear selector lever in any position
other than Reverse, there should be no continuity.
Fig. 2 Backup Lamp Switch - Typical
1 - MANUAL TRANSMISSION
2 - BACKUP LAMP SWITCH
3 - ENGINE WIRE HARNESS
8L - 8 LAMPS/LIGHTING - EXTERIORDR
BACKUP LAMP (Continued)
Page 564 of 2627
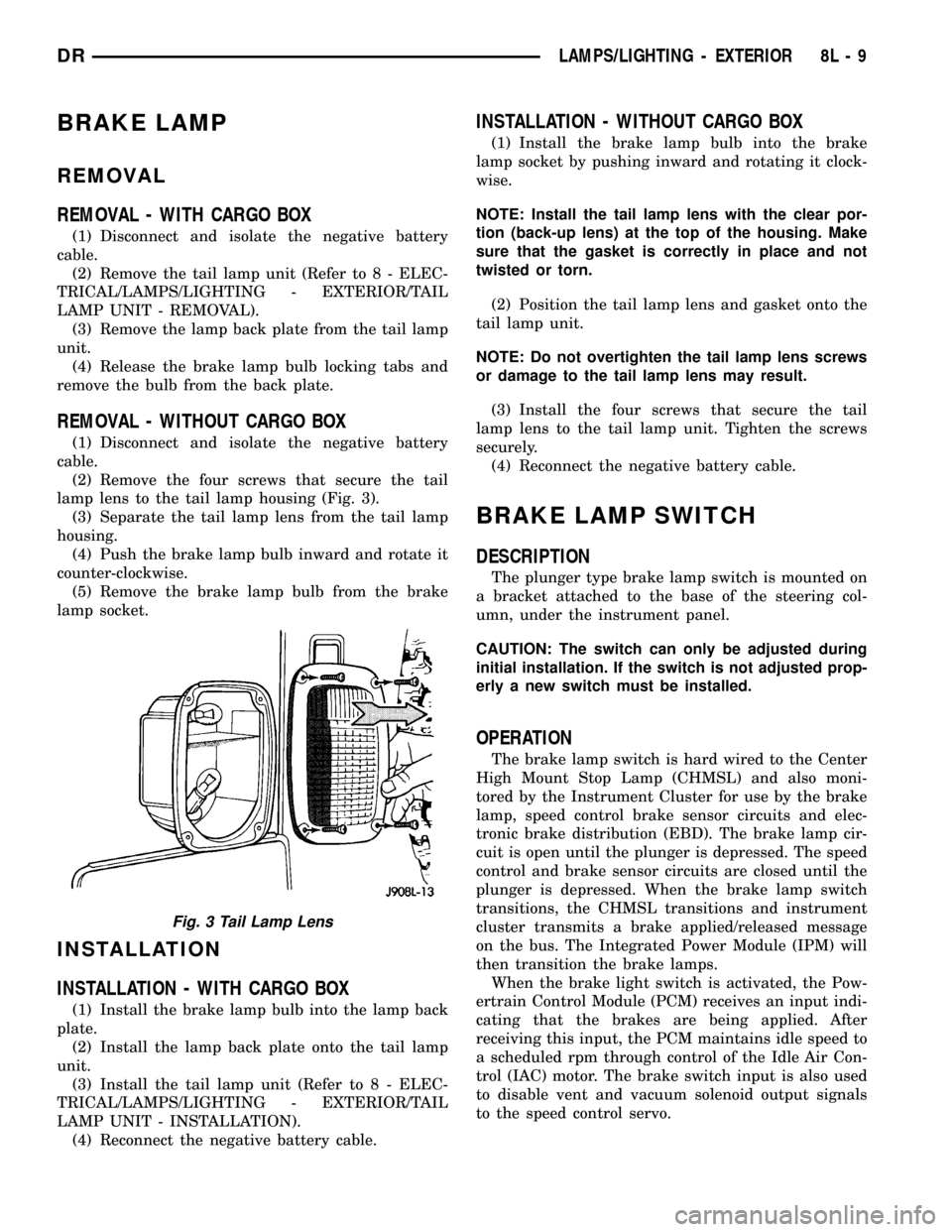
BRAKE LAMP
REMOVAL
REMOVAL - WITH CARGO BOX
(1) Disconnect and isolate the negative battery
cable.
(2) Remove the tail lamp unit (Refer to 8 - ELEC-
TRICAL/LAMPS/LIGHTING - EXTERIOR/TAIL
LAMP UNIT - REMOVAL).
(3) Remove the lamp back plate from the tail lamp
unit.
(4) Release the brake lamp bulb locking tabs and
remove the bulb from the back plate.
REMOVAL - WITHOUT CARGO BOX
(1) Disconnect and isolate the negative battery
cable.
(2) Remove the four screws that secure the tail
lamp lens to the tail lamp housing (Fig. 3).
(3) Separate the tail lamp lens from the tail lamp
housing.
(4) Push the brake lamp bulb inward and rotate it
counter-clockwise.
(5) Remove the brake lamp bulb from the brake
lamp socket.
INSTALLATION
INSTALLATION - WITH CARGO BOX
(1) Install the brake lamp bulb into the lamp back
plate.
(2) Install the lamp back plate onto the tail lamp
unit.
(3) Install the tail lamp unit (Refer to 8 - ELEC-
TRICAL/LAMPS/LIGHTING - EXTERIOR/TAIL
LAMP UNIT - INSTALLATION).
(4) Reconnect the negative battery cable.
INSTALLATION - WITHOUT CARGO BOX
(1) Install the brake lamp bulb into the brake
lamp socket by pushing inward and rotating it clock-
wise.
NOTE: Install the tail lamp lens with the clear por-
tion (back-up lens) at the top of the housing. Make
sure that the gasket is correctly in place and not
twisted or torn.
(2) Position the tail lamp lens and gasket onto the
tail lamp unit.
NOTE: Do not overtighten the tail lamp lens screws
or damage to the tail lamp lens may result.
(3) Install the four screws that secure the tail
lamp lens to the tail lamp unit. Tighten the screws
securely.
(4) Reconnect the negative battery cable.
BRAKE LAMP SWITCH
DESCRIPTION
The plunger type brake lamp switch is mounted on
a bracket attached to the base of the steering col-
umn, under the instrument panel.
CAUTION: The switch can only be adjusted during
initial installation. If the switch is not adjusted prop-
erly a new switch must be installed.
OPERATION
The brake lamp switch is hard wired to the Center
High Mount Stop Lamp (CHMSL) and also moni-
tored by the Instrument Cluster for use by the brake
lamp, speed control brake sensor circuits and elec-
tronic brake distribution (EBD). The brake lamp cir-
cuit is open until the plunger is depressed. The speed
control and brake sensor circuits are closed until the
plunger is depressed. When the brake lamp switch
transitions, the CHMSL transitions and instrument
cluster transmits a brake applied/released message
on the bus. The Integrated Power Module (IPM) will
then transition the brake lamps.
When the brake light switch is activated, the Pow-
ertrain Control Module (PCM) receives an input indi-
cating that the brakes are being applied. After
receiving this input, the PCM maintains idle speed to
a scheduled rpm through control of the Idle Air Con-
trol (IAC) motor. The brake switch input is also used
to disable vent and vacuum solenoid output signals
to the speed control servo.
Fig. 3 Tail Lamp Lens
DRLAMPS/LIGHTING - EXTERIOR 8L - 9
Page 565 of 2627
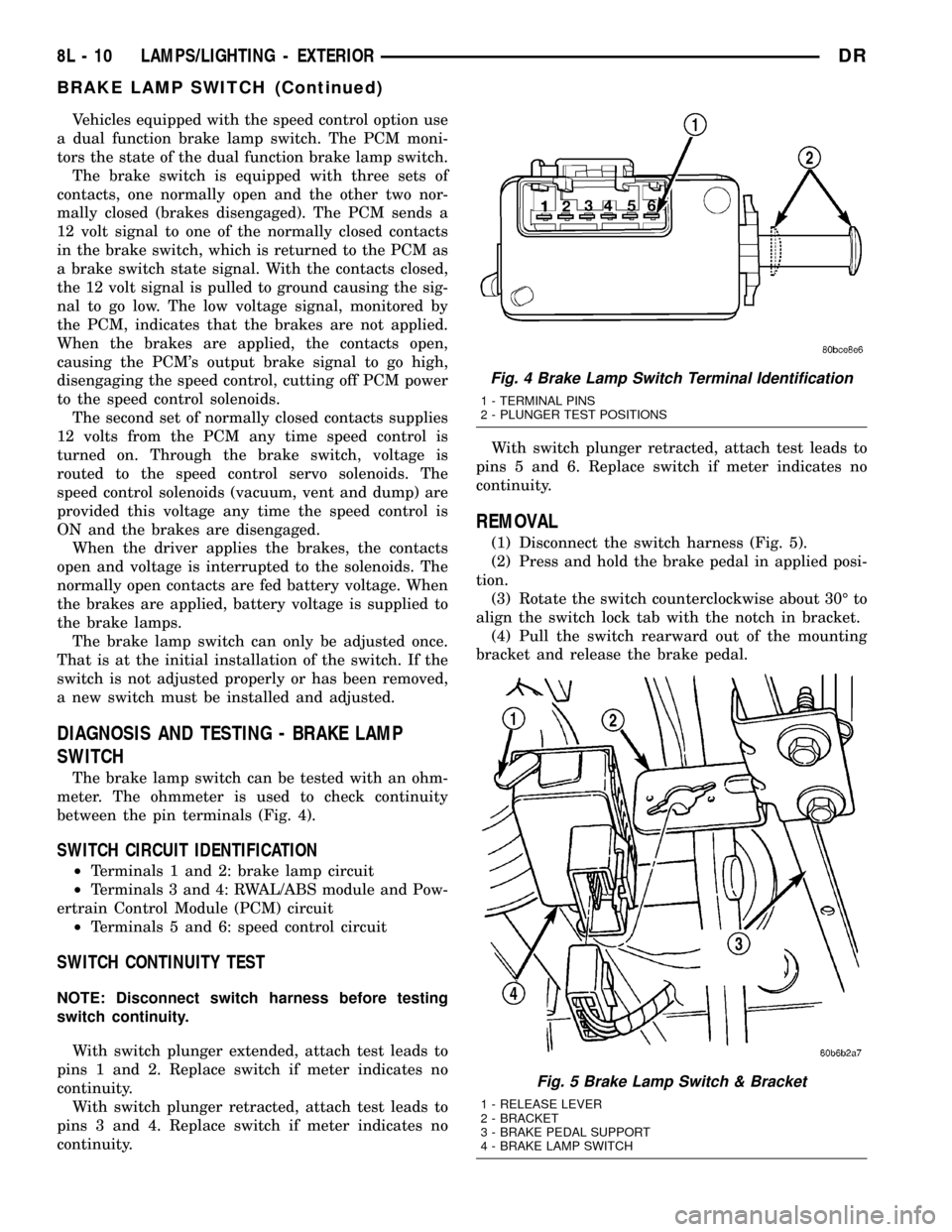
Vehicles equipped with the speed control option use
a dual function brake lamp switch. The PCM moni-
tors the state of the dual function brake lamp switch.
The brake switch is equipped with three sets of
contacts, one normally open and the other two nor-
mally closed (brakes disengaged). The PCM sends a
12 volt signal to one of the normally closed contacts
in the brake switch, which is returned to the PCM as
a brake switch state signal. With the contacts closed,
the 12 volt signal is pulled to ground causing the sig-
nal to go low. The low voltage signal, monitored by
the PCM, indicates that the brakes are not applied.
When the brakes are applied, the contacts open,
causing the PCM's output brake signal to go high,
disengaging the speed control, cutting off PCM power
to the speed control solenoids.
The second set of normally closed contacts supplies
12 volts from the PCM any time speed control is
turned on. Through the brake switch, voltage is
routed to the speed control servo solenoids. The
speed control solenoids (vacuum, vent and dump) are
provided this voltage any time the speed control is
ON and the brakes are disengaged.
When the driver applies the brakes, the contacts
open and voltage is interrupted to the solenoids. The
normally open contacts are fed battery voltage. When
the brakes are applied, battery voltage is supplied to
the brake lamps.
The brake lamp switch can only be adjusted once.
That is at the initial installation of the switch. If the
switch is not adjusted properly or has been removed,
a new switch must be installed and adjusted.
DIAGNOSIS AND TESTING - BRAKE LAMP
SWITCH
The brake lamp switch can be tested with an ohm-
meter. The ohmmeter is used to check continuity
between the pin terminals (Fig. 4).
SWITCH CIRCUIT IDENTIFICATION
²Terminals 1 and 2: brake lamp circuit
²Terminals 3 and 4: RWAL/ABS module and Pow-
ertrain Control Module (PCM) circuit
²Terminals 5 and 6: speed control circuit
SWITCH CONTINUITY TEST
NOTE: Disconnect switch harness before testing
switch continuity.
With switch plunger extended, attach test leads to
pins 1 and 2. Replace switch if meter indicates no
continuity.
With switch plunger retracted, attach test leads to
pins 3 and 4. Replace switch if meter indicates no
continuity.With switch plunger retracted, attach test leads to
pins 5 and 6. Replace switch if meter indicates no
continuity.
REMOVAL
(1) Disconnect the switch harness (Fig. 5).
(2) Press and hold the brake pedal in applied posi-
tion.
(3) Rotate the switch counterclockwise about 30É to
align the switch lock tab with the notch in bracket.
(4) Pull the switch rearward out of the mounting
bracket and release the brake pedal.
Fig. 4 Brake Lamp Switch Terminal Identification
1 - TERMINAL PINS
2 - PLUNGER TEST POSITIONS
Fig. 5 Brake Lamp Switch & Bracket
1 - RELEASE LEVER
2 - BRACKET
3 - BRAKE PEDAL SUPPORT
4 - BRAKE LAMP SWITCH
8L - 10 LAMPS/LIGHTING - EXTERIORDR
BRAKE LAMP SWITCH (Continued)
Page 568 of 2627
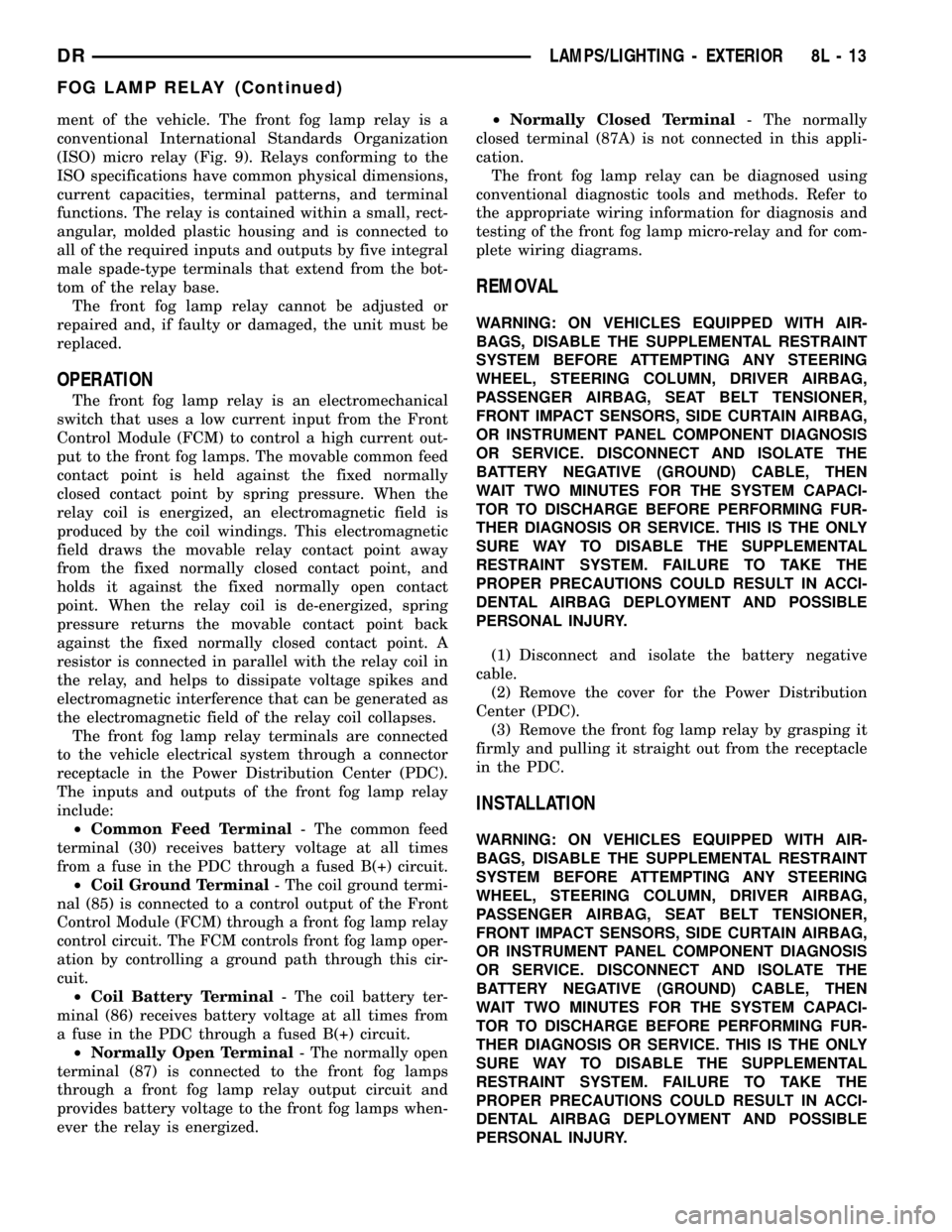
ment of the vehicle. The front fog lamp relay is a
conventional International Standards Organization
(ISO) micro relay (Fig. 9). Relays conforming to the
ISO specifications have common physical dimensions,
current capacities, terminal patterns, and terminal
functions. The relay is contained within a small, rect-
angular, molded plastic housing and is connected to
all of the required inputs and outputs by five integral
male spade-type terminals that extend from the bot-
tom of the relay base.
The front fog lamp relay cannot be adjusted or
repaired and, if faulty or damaged, the unit must be
replaced.
OPERATION
The front fog lamp relay is an electromechanical
switch that uses a low current input from the Front
Control Module (FCM) to control a high current out-
put to the front fog lamps. The movable common feed
contact point is held against the fixed normally
closed contact point by spring pressure. When the
relay coil is energized, an electromagnetic field is
produced by the coil windings. This electromagnetic
field draws the movable relay contact point away
from the fixed normally closed contact point, and
holds it against the fixed normally open contact
point. When the relay coil is de-energized, spring
pressure returns the movable contact point back
against the fixed normally closed contact point. A
resistor is connected in parallel with the relay coil in
the relay, and helps to dissipate voltage spikes and
electromagnetic interference that can be generated as
the electromagnetic field of the relay coil collapses.
The front fog lamp relay terminals are connected
to the vehicle electrical system through a connector
receptacle in the Power Distribution Center (PDC).
The inputs and outputs of the front fog lamp relay
include:
²Common Feed Terminal- The common feed
terminal (30) receives battery voltage at all times
from a fuse in the PDC through a fused B(+) circuit.
²Coil Ground Terminal- The coil ground termi-
nal (85) is connected to a control output of the Front
Control Module (FCM) through a front fog lamp relay
control circuit. The FCM controls front fog lamp oper-
ation by controlling a ground path through this cir-
cuit.
²Coil Battery Terminal- The coil battery ter-
minal (86) receives battery voltage at all times from
a fuse in the PDC through a fused B(+) circuit.
²Normally Open Terminal- The normally open
terminal (87) is connected to the front fog lamps
through a front fog lamp relay output circuit and
provides battery voltage to the front fog lamps when-
ever the relay is energized.²Normally Closed Terminal- The normally
closed terminal (87A) is not connected in this appli-
cation.
The front fog lamp relay can be diagnosed using
conventional diagnostic tools and methods. Refer to
the appropriate wiring information for diagnosis and
testing of the front fog lamp micro-relay and for com-
plete wiring diagrams.
REMOVAL
WARNING: ON VEHICLES EQUIPPED WITH AIR-
BAGS, DISABLE THE SUPPLEMENTAL RESTRAINT
SYSTEM BEFORE ATTEMPTING ANY STEERING
WHEEL, STEERING COLUMN, DRIVER AIRBAG,
PASSENGER AIRBAG, SEAT BELT TENSIONER,
FRONT IMPACT SENSORS, SIDE CURTAIN AIRBAG,
OR INSTRUMENT PANEL COMPONENT DIAGNOSIS
OR SERVICE. DISCONNECT AND ISOLATE THE
BATTERY NEGATIVE (GROUND) CABLE, THEN
WAIT TWO MINUTES FOR THE SYSTEM CAPACI-
TOR TO DISCHARGE BEFORE PERFORMING FUR-
THER DIAGNOSIS OR SERVICE. THIS IS THE ONLY
SURE WAY TO DISABLE THE SUPPLEMENTAL
RESTRAINT SYSTEM. FAILURE TO TAKE THE
PROPER PRECAUTIONS COULD RESULT IN ACCI-
DENTAL AIRBAG DEPLOYMENT AND POSSIBLE
PERSONAL INJURY.
(1) Disconnect and isolate the battery negative
cable.
(2) Remove the cover for the Power Distribution
Center (PDC).
(3) Remove the front fog lamp relay by grasping it
firmly and pulling it straight out from the receptacle
in the PDC.
INSTALLATION
WARNING: ON VEHICLES EQUIPPED WITH AIR-
BAGS, DISABLE THE SUPPLEMENTAL RESTRAINT
SYSTEM BEFORE ATTEMPTING ANY STEERING
WHEEL, STEERING COLUMN, DRIVER AIRBAG,
PASSENGER AIRBAG, SEAT BELT TENSIONER,
FRONT IMPACT SENSORS, SIDE CURTAIN AIRBAG,
OR INSTRUMENT PANEL COMPONENT DIAGNOSIS
OR SERVICE. DISCONNECT AND ISOLATE THE
BATTERY NEGATIVE (GROUND) CABLE, THEN
WAIT TWO MINUTES FOR THE SYSTEM CAPACI-
TOR TO DISCHARGE BEFORE PERFORMING FUR-
THER DIAGNOSIS OR SERVICE. THIS IS THE ONLY
SURE WAY TO DISABLE THE SUPPLEMENTAL
RESTRAINT SYSTEM. FAILURE TO TAKE THE
PROPER PRECAUTIONS COULD RESULT IN ACCI-
DENTAL AIRBAG DEPLOYMENT AND POSSIBLE
PERSONAL INJURY.
DRLAMPS/LIGHTING - EXTERIOR 8L - 13
FOG LAMP RELAY (Continued)