check engine light FIAT 500 1957 1.G User Guide
[x] Cancel search | Manufacturer: FIAT, Model Year: 1957, Model line: 500, Model: FIAT 500 1957 1.GPages: 128, PDF Size: 9.01 MB
Page 44 of 128
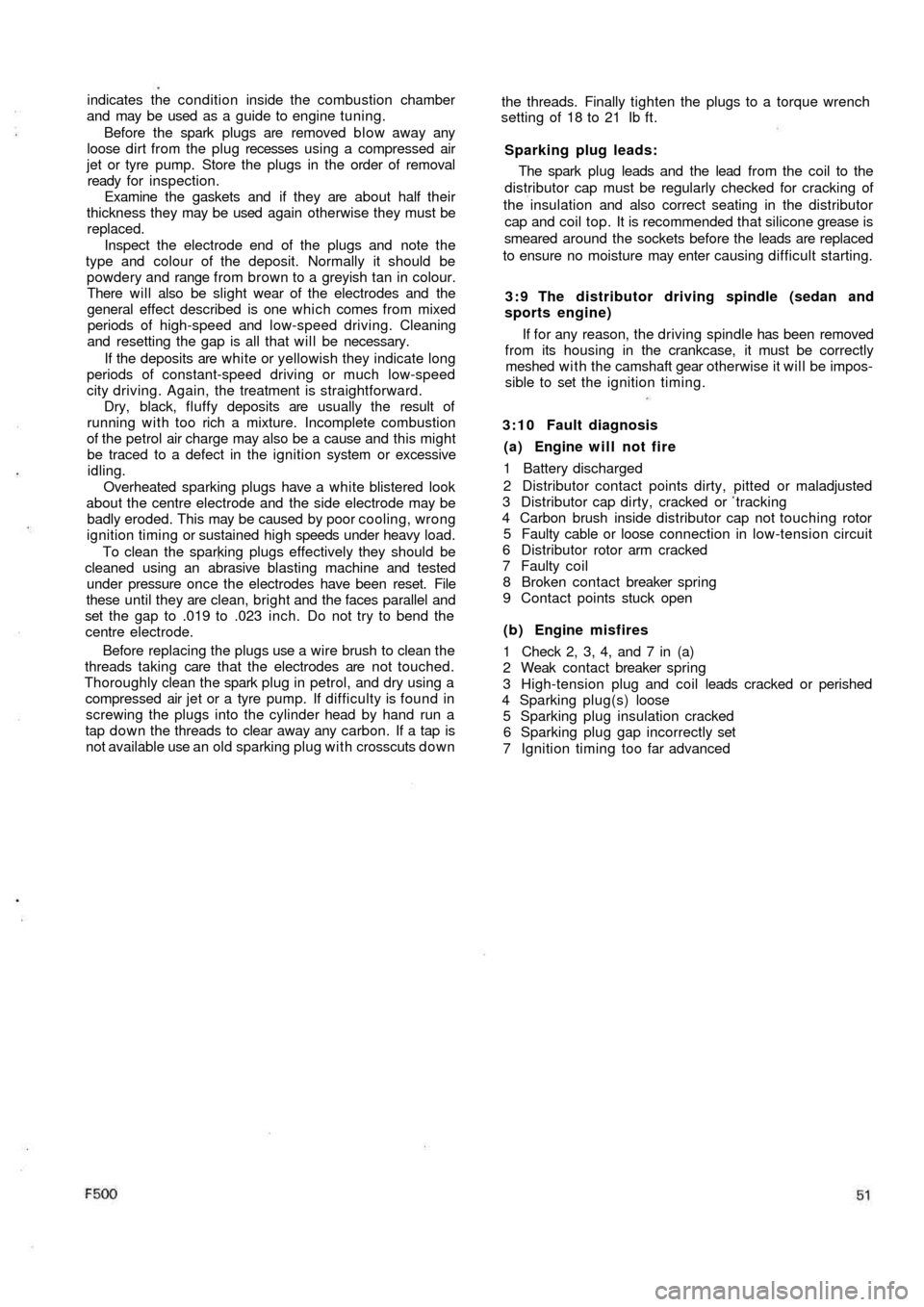
indicates the condition inside the combustion chamber
and may be used as a guide to engine tuning.
Before the spark plugs are removed b l o w away any
loose dirt from the plug recesses using a compressed air
jet or tyre pump. Store the plugs in the order of removal
ready for inspection.
Examine the gaskets and if they are about half their
thickness they may be used again otherwise they must be
replaced.
Inspect the electrode end of the plugs and note the
type and colour of the deposit. Normally it should be
powdery and range from b r o w n to a greyish tan in colour.
There will also be slight wear of the electrodes and the
general effect described is one which comes from mixed
periods of high-speed and low-speed driving. Cleaning
and resetting the gap is all that will be necessary.
If the deposits are white or yellowish they indicate long
periods of constant-speed driving or much low-speed
city driving. Again, the treatment is straightforward.
Dry, black, fluffy deposits are usually the result of
running with too rich a mixture. Incomplete combustion
of the petrol air charge may also be a cause and this might
be traced to a defect in the ignition system or excessive
idling.
Overheated sparking plugs have a white blistered look
about the centre electrode and the side electrode may be
badly eroded. This may be caused by poor cooling, wrong
ignition timing or sustained high speeds under heavy load.
To clean the sparking plugs effectively they should be
cleaned using an abrasive blasting machine and tested
under pressure once the electrodes have been reset. File
these until they are clean, bright and the faces parallel and
set the gap to .019 to .023 inch. Do not try to bend the
centre electrode.
Before replacing the plugs use a wire brush to clean the
threads taking care that the electrodes are not touched.
Thoroughly clean the spark plug in petrol, and dry using a
compressed air jet or a tyre pump. If difficulty is found in
screwing the plugs into the cylinder head by hand run a
tap d o w n the threads to clear away any carbon. If a tap is
not available use an old sparking plug with crosscuts d o w nthe threads. Finally tighten the plugs to a torque wrench
setting of 18 to 21 Ib ft.
Sparking plug leads:
The spark plug leads and the lead from the coil to the
distributor cap must be regularly checked for cracking of
the insulation and also correct seating in the distributor
cap and coil top. It is recommended that silicone grease is
smeared around the sockets before the leads are replaced
to ensure no moisture may enter causing difficult starting.
3 : 9 The distributor driving spindle (sedan and
sports engine)
If for any reason, the driving spindle has been removed
from its housing in the crankcase, it must be correctly
meshed w i t h the camshaft gear otherwise it
will be impos-
sible to set the ignition timing.
3:10 Fault diagnosis
(a) Engine w i l l not fire
1 Battery discharged
2 Distributor contact points dirty, pitted or maladjusted
3 Distributor cap dirty, cracked or tracking
4 Carbon brush inside distributor cap not touching rotor
5 Faulty cable or loose connection in low-tension circuit
6 Distributor rotor arm cracked
7 Faulty coil
8 Broken contact breaker spring
9 Contact points stuck open
(b) Engine misfires
1 Check 2, 3, 4, and 7 in (a)
2 Weak contact breaker spring
3 High-tension plug and coil leads cracked or perished
4 Sparking plug(s) loose
5 Sparking plug insulation cracked
6 Sparking plug gap incorrectly set
7 Ignition timing too far advanced
Page 67 of 128
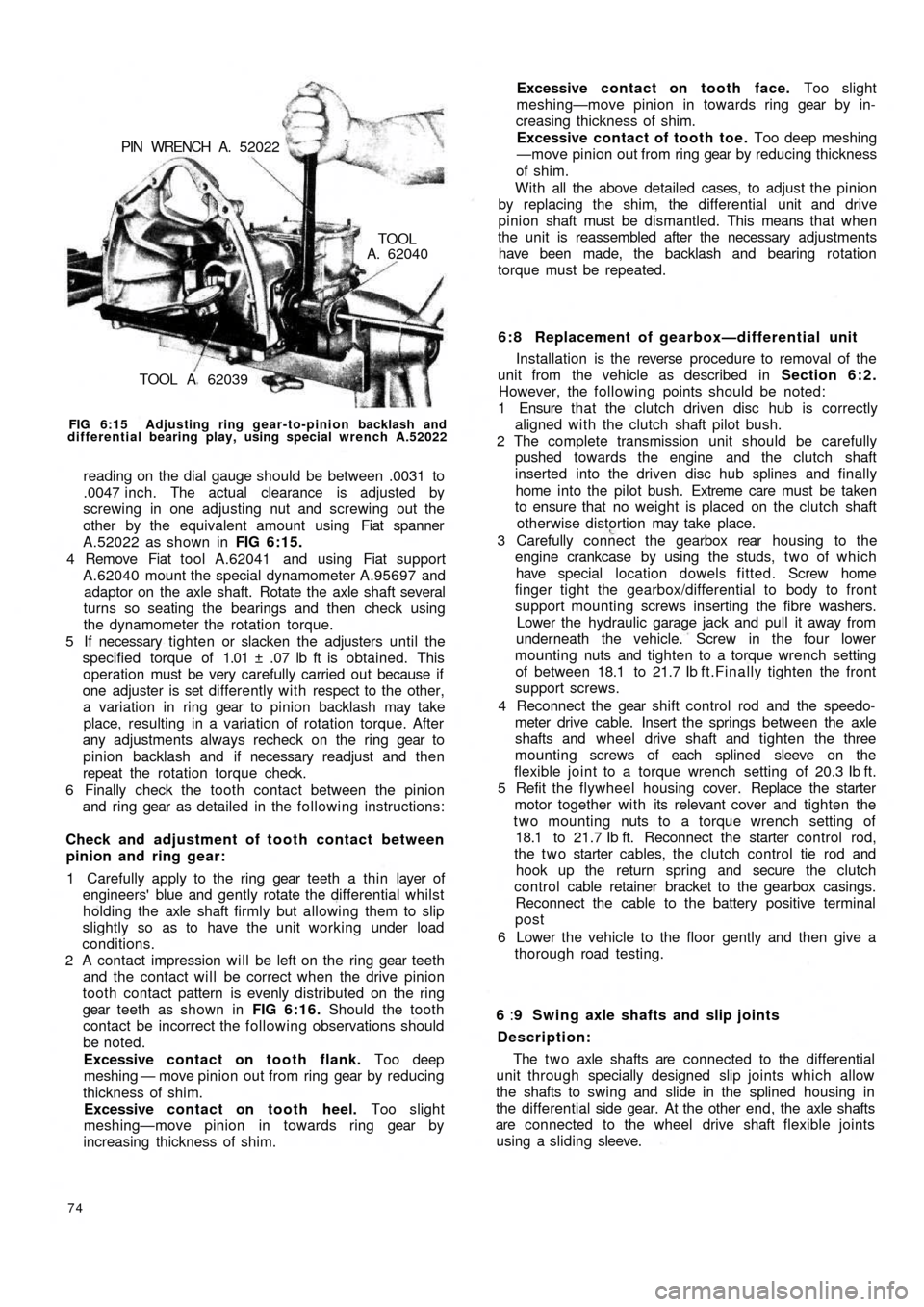
TOOL A 62039
TOOLA. 62040 PIN WRENCH A. 52022
FIG 6:15 Adjusting ring gear-to-pinion backlash and
differential bearing play, using special wrench A.52022
reading on the dial gauge should be between .0031 to
.0047 inch. The actual clearance is adjusted by
screwing in one adjusting nut and screwing out the
other by the equivalent amount using Fiat spanner
A.52022 as shown in FIG 6:15.
4 Remove Fiat tool A.62041 and using Fiat support
A.62040 mount the special dynamometer A.95697 and
adaptor on the axle shaft. Rotate the axle shaft several
turns so seating the bearings and then check using
the dynamometer the rotation torque.
5 If necessary tighten or slacken the adjusters until the
specified torque of 1.01 ± .07 lb ft is obtained. This
operation must be very carefully carried out because if
one adjuster is set differently with respect to the other,
a variation in ring gear to pinion backlash may take
place, resulting in a variation of rotation torque. After
any adjustments always recheck on the ring gear to
pinion backlash and if necessary readjust and then
repeat the rotation torque check.
6 Finally check the tooth contact between the pinion
and ring gear as detailed in the following instructions:
Check and adjustment of tooth contact between
pinion and ring gear:
1 Carefully apply to the ring gear teeth a thin layer of
engineers' blue and gently rotate the differential whilst
holding the axle shaft firmly but allowing them to slip
slightly so as to have the unit working under load
conditions.
2 A contact impression will be left on the ring gear teeth
and the contact will be correct when the drive pinion
tooth contact pattern is evenly distributed on the ring
gear teeth as shown in FIG 6:16. Should the tooth
contact be incorrect the following observations should
be noted.
Excessive contact on tooth flank. Too deep
meshing — move pinion out from ring gear by reducing
thickness of shim.
Excessive contact on tooth heel. Too slight
meshing—move pinion in towards ring gear by
increasing thickness of shim.
74
6 : 8 Replacement of gearbox—differential unit
Installation is the reverse procedure to removal of the
unit from the vehicle as described in Section 6:2.
However, the following points should be noted:
1 Ensure that the clutch driven disc hub is correctly
aligned with the clutch shaft pilot bush.
2 The complete transmission unit should be carefully
pushed towards the engine and the clutch shaft
inserted into the driven disc hub splines and finally
home into the pilot bush. Extreme care must be taken
to ensure that no weight is placed on the clutch shaft
otherwise distortion may take place.
3 Carefully connect the gearbox rear housing to the
engine crankcase by using the studs, t w o of which
have special location dowels fitted. Screw home
finger tight the gearbox/differential to body to front
support mounting screws inserting the fibre washers.
Lower the hydraulic garage jack and pull it away from
underneath the vehicle. Screw in the four lower
mounting nuts and tighten to a torque wrench setting
of between 18.1 to 21.7 Ib f t.Finally tighten the front
support screws.
4 Reconnect the gear shift control rod and the speedo-
meter drive cable. Insert the springs between the axle
shafts and wheel drive shaft and tighten the
three
mounting screws of each splined sleeve on the
flexible joint to a torque wrench setting of 20.3 Ib ft.
5 Refit the flywheel housing cover. Replace the starter
motor together with its relevant cover and tighten the
two mounting nuts to a torque wrench setting of
18.1 to 21.7 Ib ft. Reconnect the starter control rod,
the t w o starter cables, the clutch control tie rod and
hook up the return spring and secure the clutch
control cable retainer bracket to the gearbox casings.
Reconnect the cable to the battery positive terminal
post
6 Lower the vehicle to the floor gently and then give a
thorough road testing.
6 :9 Swing axle shafts and slip joints
Description:
The t w o axle shafts are connected to the differential
unit through specially designed slip joints which allow
the shafts to swing and slide in the splined housing in
the differential side gear. At the other end, the axle shafts
are connected to the wheel drive shaft flexible joints
using a sliding sleeve. Excessive contact on tooth face. Too slight
meshing—move pinion in towards ring gear by in-
creasing thickness of shim.
Excessive contact of tooth toe. Too deep meshing
—move pinion out from ring gear by reducing thickness
of shim.
With all the above detailed cases, to adjust the pinion
by replacing the shim, the differential unit and drive
pinion shaft must be dismantled. This means that when
the unit is reassembled after the necessary adjustments
have been made, the backlash and bearing rotation
torque must be repeated.
Page 105 of 128
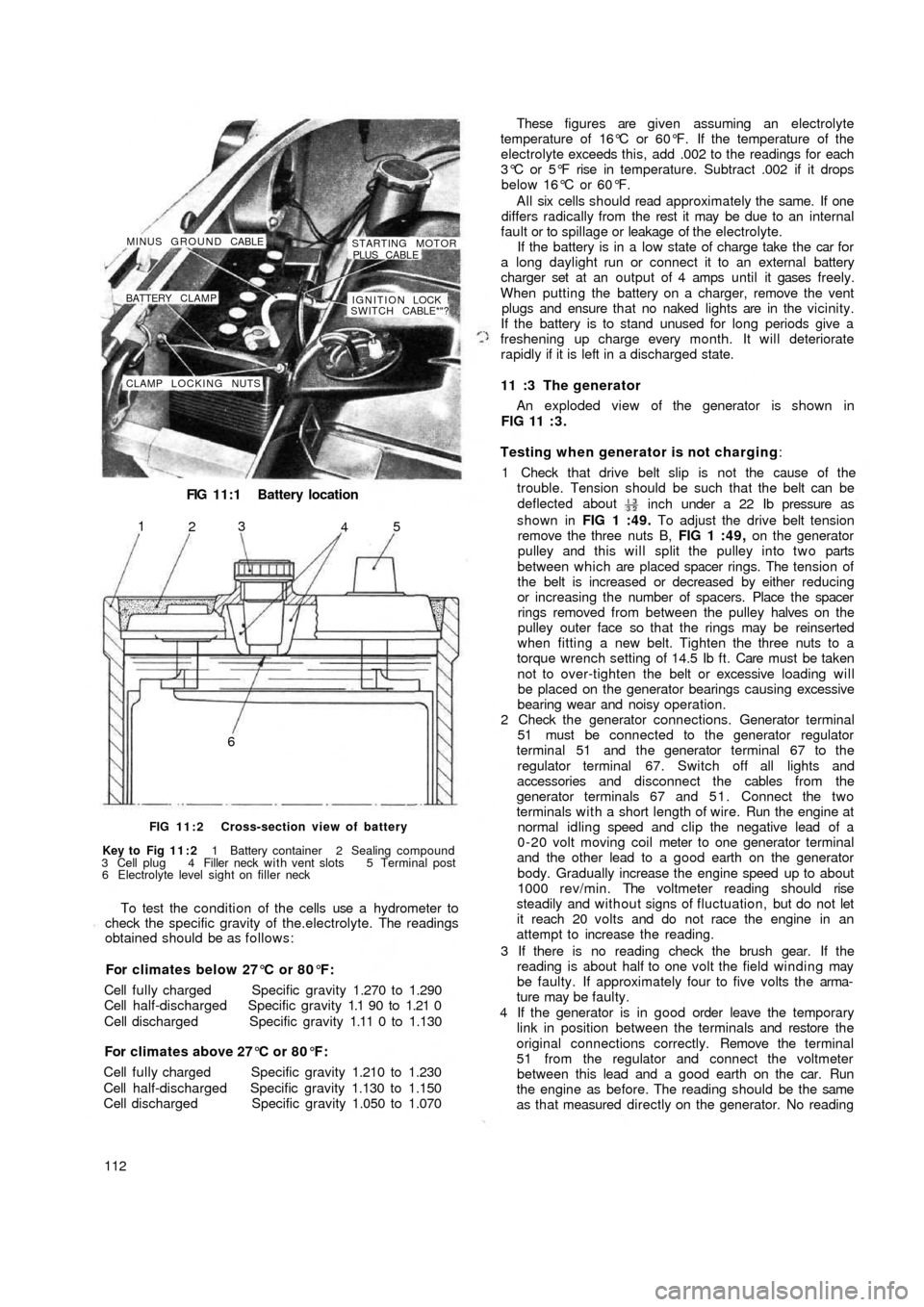
FIG 11:1 Battery location
CLAMP LOCKING NUTSIGNITION LOCK !
SWITCH CABLE*"? BATTERY CLAMP MINUS GROUND CABLE
STARTING MOTOR
PLUS CABLE
65
4 3
2 1
FIG 11:2 Cross-section view of battery
Key to Fig 11:2 1 Battery container 2 Sealing compound
3 Cell plug 4 Filler neck with vent slots 5 Terminal post
6 Electrolyte level sight on filler neck
To test the condition of the cells use a hydrometer to
check the specific gravity of the.electrolyte. The readings
obtained should be as follows:
For climates below 27°C or 80°F:
Cell fully charged Specific gravity 1.270 to 1.290
Cell half-discharged Specific gravity 1.1 90 to 1.21 0
Cell discharged Specific gravity 1.11 0 to 1.130
For climates above 27°C or 80°F:
Cell fully charged Specific gravity 1.210 to 1.230
Cell half-discharged Specific gravity 1.130 to 1.150
Cell discharged Specific gravity 1.050 to 1.070
112These figures are given assuming an electrolyte
temperature of 16°C or 60°F. If the temperature of the
electrolyte exceeds this, add .002 to the readings for each
3°C or 5°F rise in temperature. Subtract .002 if it drops
below 16°C or 60°F.
All six cells should read approximately the same. If one
differs radically from the rest it may be due to an internal
fault or to spillage or leakage of the electrolyte.
If the battery is in a low state of charge take the car for
a long daylight run or connect it to an external battery
charger set at an output of 4 amps until it gases freely.
When putting the battery on a charger, remove the vent
plugs and ensure that no naked lights are in the vicinity.
If the battery is to stand unused for long periods give a
freshening up charge every month. It will deteriorate
rapidly if it is left in a discharged state.
11 :3 The generator
An exploded view of the generator is shown in
FIG 11 : 3 .
Testing when generator is not charging:
1 Check that drive belt slip is not the cause of the
trouble. Tension should be such that the belt can be
deflected about
inch under a 22 Ib pressure as
shown in FIG 1 :49. To adjust the drive belt tension
remove the three nuts B, FIG 1 :49, on the generator
pulley and this will split the pulley into two parts
between which are placed spacer rings. The tension of
the belt is increased or decreased by either reducing
or increasing the number of spacers. Place the spacer
rings removed from between the pulley halves on the
pulley outer face so that the rings may be reinserted
when fitting a new belt. Tighten the three nuts to a
torque wrench setting of 14.5 Ib ft. Care must be taken
not to over-tighten the belt or excessive loading will
be placed on the generator bearings causing excessive
bearing wear and noisy operation.
2 Check the generator connections. Generator terminal
51 must be connected to the generator regulator
terminal 51 and the generator terminal 67 to the
regulator terminal 67. Switch off all lights and
accessories and disconnect the cables from the
generator terminals 67 and 5 1 . Connect the two
terminals with a short length of wire. Run the engine at
normal idling speed and clip the negative lead of a
0-20 volt moving coil meter to one generator terminal
and the other lead to a good earth on the generator
body. Gradually increase the
engine speed up to about
1000 rev/min. The voltmeter reading should rise
steadily and without signs of fluctuation, but do not let
it reach 20 volts and do not race the engine in an
attempt to increase the reading.
3 If there is no reading check the brush gear. If the
reading is about half to one volt the field winding may
be faulty. If approximately four to five volts the arma-
ture may be faulty.
4 If the generator is in good order leave the temporary
link in position between the terminals and restore the
original connections correctly. Remove the terminal
51 from the regulator and connect the voltmeter
between this lead and a good earth on the car. Run
the engine as before. The reading should be the same
as that measured directly on the generator. No reading
Page 108 of 128
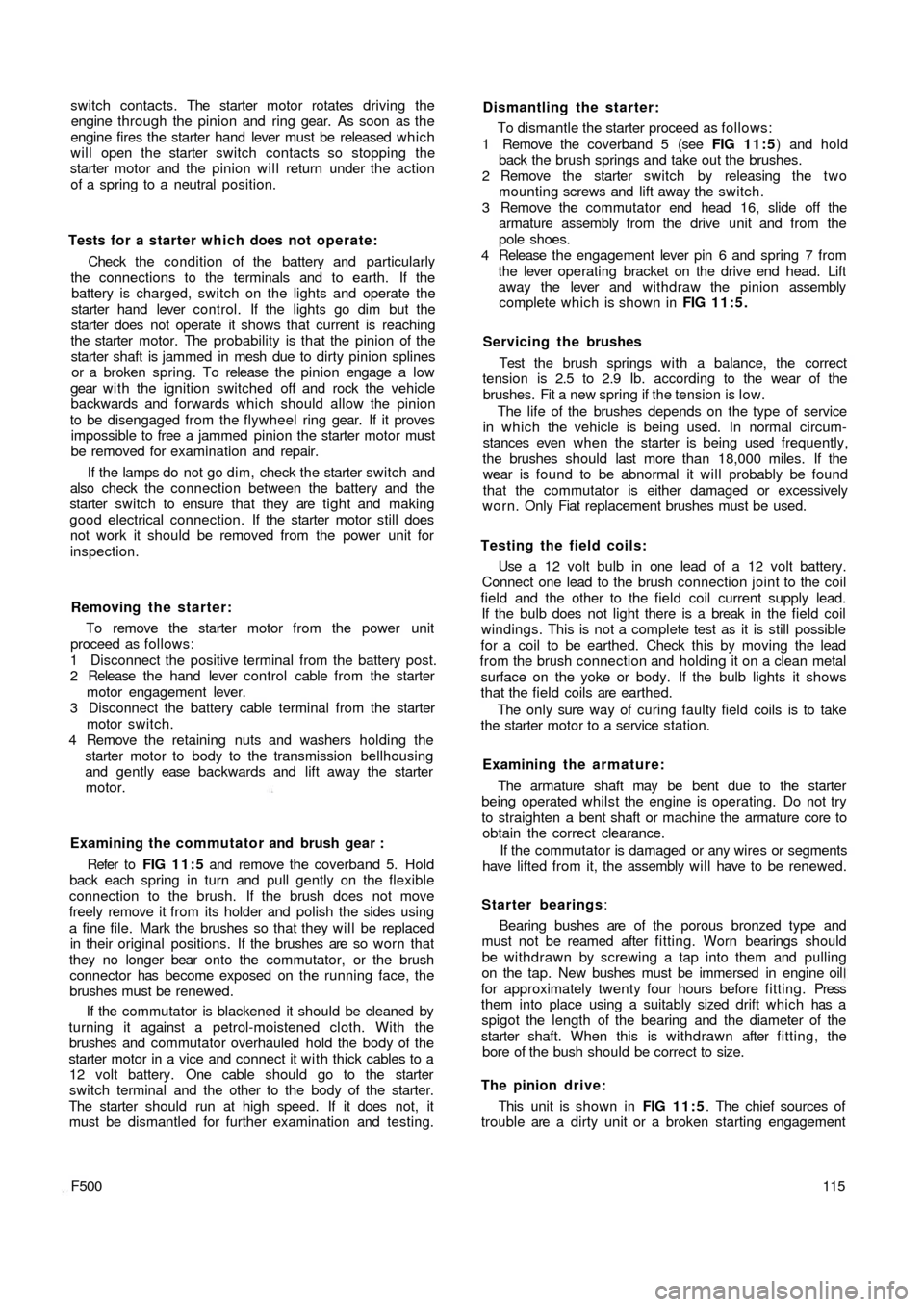
switch contacts. The starter motor rotates driving the
engine through the pinion and ring gear. As soon as the
engine fires the starter hand lever must be released which
will open the starter switch contacts so stopping the
starter motor and the pinion will return under the action
of a spring to a neutral position.
Tests for a starter which does not operate:
Check the condition of the battery and particularly
the connections to the terminals and to earth. If the
battery is charged, switch on the lights and operate the
starter hand lever control. If the lights go dim but the
starter does not operate it shows that current is reaching
the starter motor. The probability is that the pinion of the
starter shaft is jammed in mesh due to dirty pinion splines
or a broken spring. To release the pinion engage a low
gear with the ignition switched off and rock the vehicle
backwards and forwards which should allow the pinion
to be disengaged from the flywheel ring gear. If it proves
impossible to free a jammed pinion the starter motor must
be removed for examination and repair.
If the lamps do not go dim, check the starter switch and
also check the connection between the battery and the
starter switch to ensure that they are tight and making
good electrical connection. If the starter motor still does
not work it should be removed from the power unit for
inspection.
Removing the starter:
To remove the starter motor from the power unit
proceed as follows:
1 Disconnect the positive terminal from the
battery post.
2 Release the hand lever control cable from the starter
motor engagement lever.
3 Disconnect the battery cable terminal from the starter
motor switch.
4 Remove the retaining nuts and washers holding the
starter motor to body to the transmission bellhousing
and gently ease backwards and lift away the starter
motor.
Examining the commutator and brush gear :
Refer to FIG 11:5 and remove the coverband 5. Hold
back each spring in turn and pull gently on the flexible
connection to the brush. If the brush does not move
freely remove it from its holder and polish the sides using
a fine file. Mark the brushes so that they will be replaced
in their original positions. If the brushes are so worn that
they no longer bear onto the commutator, or the brush
connector has become exposed on the running face, the
brushes must be renewed.
If the commutator is blackened it should be cleaned by
turning it against a petrol-moistened cloth. With the
brushes and commutator overhauled hold the body of the
starter motor in a vice and connect it with thick cables to a
12 volt battery. One cable should go to the starter
switch terminal and the other to the body of the starter.
The starter should run at high speed. If it does not, it
must be dismantled for further examination and testing.
F500115 Dismantling the starter:
To dismantle the starter proceed as follows:
1 Remove the coverband 5 (see FIG 11:5) and hold
back the brush springs and take out the brushes.
2 Remove the starter switch by releasing the t w o
mounting screws and lift away the switch.
3 Remove the commutator end head 16, slide off the
armature assembly from the drive unit and from the
pole shoes.
4 Release the engagement lever pin 6 and spring 7 from
the lever operating bracket on the drive end head. Lift
away the lever and withdraw the pinion assembly
complete which is shown in FIG 11:5.
Servicing the brushes
Test the brush springs with a balance, the correct
tension is 2.5 to 2.9 Ib. according to the wear of the
brushes. Fit a new spring if the tension is low.
The life of the brushes depends on the type of service
in which the vehicle is being used. In normal circum-
stances even when the starter is being used frequently,
the brushes should last more than 18,000 miles. If the
wear is found to be abnormal it will probably be found
that the commutator is either damaged or excessively
w o r n . Only Fiat replacement brushes must be used.
Testing the field coils:
Use a 12 volt bulb in one lead of a 12 volt battery.
Connect one lead to the brush connection joint to the coil
field and the other to the field coil current supply lead.
If the bulb does not light there is a break in the f i e l d coil
windings. This is not a complete test as it is still possible
for a coil to be earthed. Check this by moving the lead
from the brush connection and holding it on a clean
metal
surface on the yoke or body. If the bulb lights it shows
that the field coils are earthed.
The only sure way of curing faulty field coils is to take
the starter motor to a service station.
Examining the armature:
The armature shaft may be bent due to the starter
being operated whilst the engine is operating. Do not try
to straighten a bent shaft or machine the armature core to
obtain the correct clearance.
If the commutator is damaged or any wires or segments
have lifted from it, the assembly will have to be renewed.
Starter bearings:
Bearing bushes are of the porous bronzed type and
must not be reamed after fitting. Worn bearings should
be withdrawn by screwing a tap into them and pulling
on the tap. New bushes must be immersed in engine oil
for approximately twenty four hours before fitting. Press
them into place using a suitably sized drift which has a
spigot the length of the bearing and the diameter of the
starter shaft. When this is withdrawn after fitting, the
bore of the bush should be correct to size.
The pinion drive:
This unit is shown in FIG 11:5. The chief sources of
trouble are a dirty unit or a broken starting engagement
Page 116 of 128
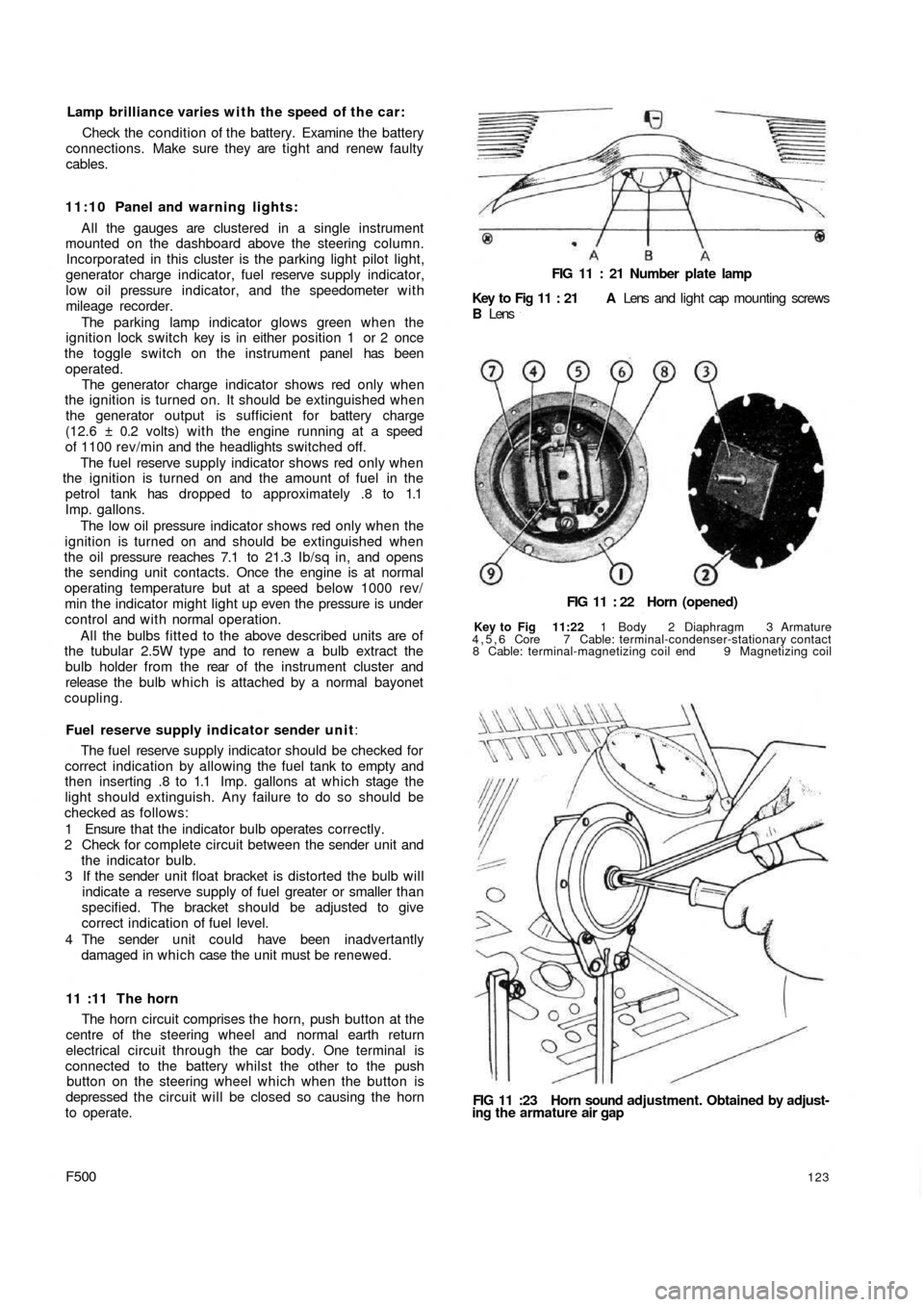
Lamp brilliance varies w i t h the speed of t h e car:
Check the condition of the battery. Examine the battery
connections. Make sure they are tight and renew faulty
cables.
11:10 Panel and warning lights:
All the gauges are clustered in a single instrument
mounted on the dashboard above the steering column.
Incorporated in this cluster is the parking light pilot light,
generator charge indicator, fuel reserve supply indicator,
low oil pressure indicator, and the speedometer w i t h
mileage recorder.
The parking lamp indicator glows green when the
ignition lock switch key is in either position 1 or 2 once
the toggle switch on the instrument panel has been
operated.
The generator charge indicator shows red only when
the ignition is turned on. It should be extinguished when
the generator output is sufficient for battery charge
(12.6 ± 0.2 volts) with the engine running at a speed
of 1100 rev/min and the headlights switched off.
The fuel reserve supply indicator shows red only when
the ignition is turned on and the amount of fuel in the
petrol tank has dropped to approximately .8 to 1.1
Imp. gallons.
The low oil pressure indicator shows red only when the
ignition is turned on and should be extinguished when
the oil pressure reaches 7.1 to 21.3 Ib/sq in, and opens
the sending unit contacts. Once the engine is at normal
operating temperature but at a speed below 1000 rev/
min the indicator might light up even the pressure is under
control and with normal operation.
All the bulbs fitted to the above described units are of
the tubular 2.5W type and to renew a bulb extract the
bulb holder from the rear of t h e instrument cluster and
release the bulb which is attached by a normal bayonet
coupling.
Fuel reserve supply indicator sender u n i t:
The fuel reserve supply indicator should be checked for
correct indication by allowing the fuel tank to empty and
then inserting .8 to 1.1 Imp. gallons at which stage the
light should extinguish. Any failure to do so should be
checked as follows:
1 Ensure that the indicator bulb operates correctly.
2 Check for complete circuit between the sender unit and
the indicator bulb.
3 If the sender unit float bracket is distorted the bulb
will
indicate a reserve supply of fuel greater or smaller than
specified. The bracket should be adjusted to give
correct indication of fuel level.
4 The sender unit could have been inadvertantly
damaged in which case the unit must be renewed.
11 :11 The horn
The horn circuit comprises the horn, push button at the
centre of the steering wheel and normal earth return
electrical circuit through the car body. One terminal is
connected to the battery whilst the other to the push
button on the steering wheel which when the button is
depressed the circuit will be closed so causing the horn
to operate.
F500
FIG 11 : 21 Number plate lamp
Key to Fig 11 : 21 A Lens and light cap mounting screws
B Lens
FIG 11 : 22 Horn (opened)
Key to Fig 11:22 1 Body 2 Diaphragm 3 Armature
4,5,6 Core 7 Cable: terminal-condenser-stationary contact
8 Cable: terminal-magnetizing coil end 9 Magnetizing coil
FIG 11 :23 Horn sound adjustment. Obtained by adjust-
ing the armature air gap
123
Page 117 of 128
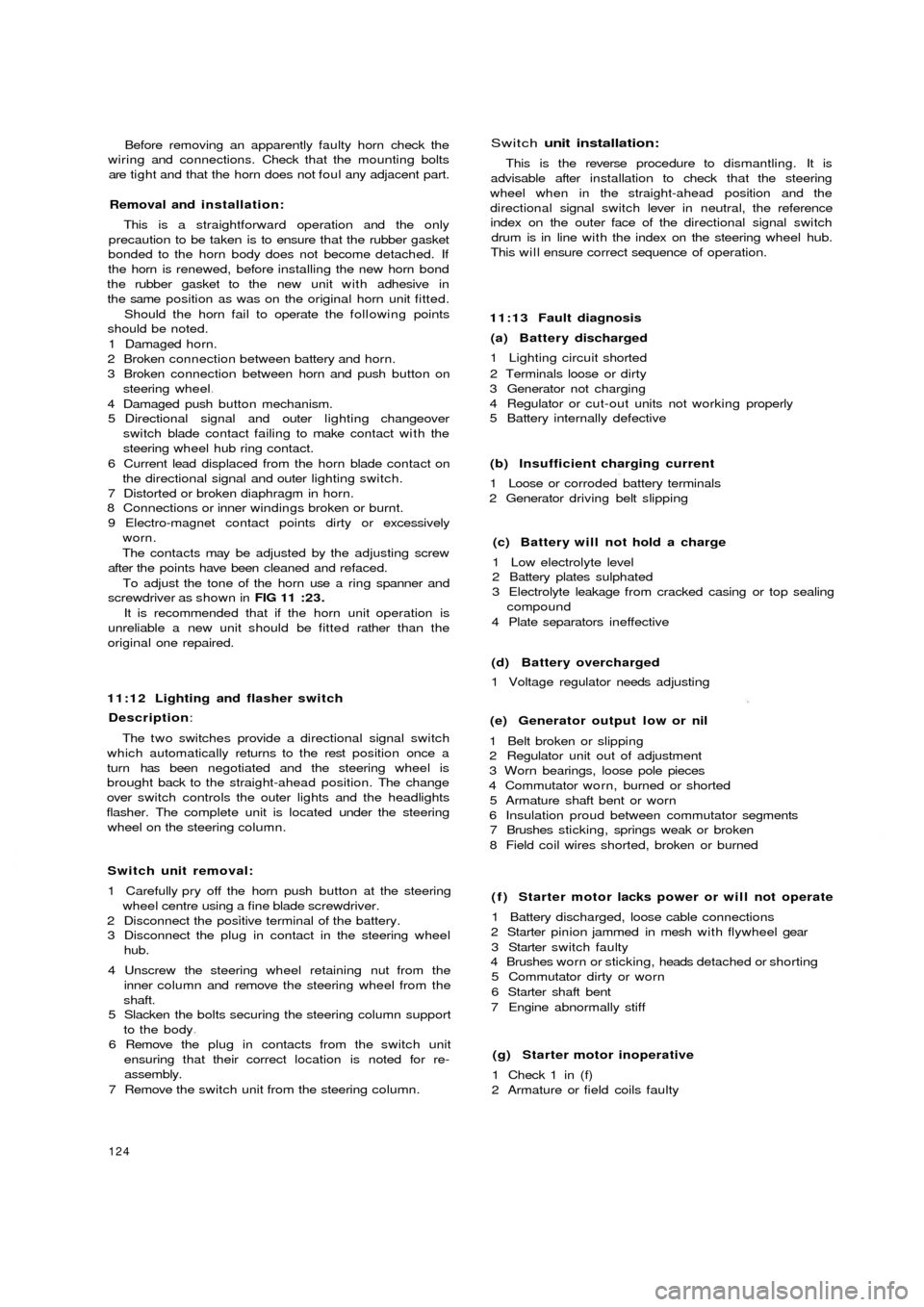
Before removing an apparently faulty horn check the
wiring and connections. Check that the mounting bolts
are tight and that the horn does not foul any adjacent part.
Removal and installation:
This is a straightforward operation and the only
precaution to be taken is to ensure that the rubber gasket
bonded to the horn body does not become detached. If
the horn is renewed, before installing the new horn bond
the rubber gasket to the new unit with adhesive in
the same position as was on the original horn unit fitted.
Should the horn fail to operate the following points
should be noted.
1 Damaged horn.
2 Broken connection between battery and horn.
3 Broken connection between horn and push button on
steering wheel
4 Damaged push button mechanism.
5 Directional signal and outer lighting changeover
switch blade contact failing to make contact with the
steering wheel hub ring contact.
6 Current lead displaced from the horn blade contact on
the directional signal and outer lighting switch.
7 Distorted or broken diaphragm in horn.
8 Connections or inner windings
broken or burnt.
9 Electro-magnet contact points dirty or excessively
worn.The contacts may be adjusted by the adjusting screw
after the points have been cleaned and refaced.
To adjust the tone of the horn use a ring spanner and
screwdriver as shown in FIG 11 :23.
It is recommended that if the horn unit operation is
unreliable a new unit should be fitted rather than the
original one repaired.
11:12 Lighting and flasher switch
Description:
The two switches provide a directional signal switch
which automatically returns to the rest position once a
turn has been negotiated and the steering wheel is
brought back to the straight-ahead position. The change
over switch controls the outer lights and the headlights
flasher. The complete unit is located under the steering
wheel on the steering column.
Switch unit removal:
1 Carefully pry off the horn push button at the steering
wheel centre using a fine blade screwdriver.
2 Disconnect the positive terminal of the battery.
3 Disconnect the plug in contact in the steering wheel
hub.
4 Unscrew the steering wheel retaining nut from the
inner column and remove the steering wheel from the
shaft.
5 Slacken the bolts securing the steering column support
to the body
6 Remove the plug in contacts from the switch unit
ensuring that their correct location is noted for re-
assembly.7 Remove the switch unit from the steering column.
124
Switch unit installation:
This is the reverse procedure to dismantling. It is
advisable after installation to check that the steering
wheel when in the straight-ahead position and the
directional signal switch lever in neutral, the reference
index on the outer face of the directional signal switch
drum is in line with the index on the steering wheel hub.
This will ensure correct sequence of operation.
11:13 Fault diagnosis
(a) Battery discharged
1 Lighting circuit shorted
2 Terminals loose or dirty
3 Generator not charging
4 Regulator or cut-out units not working properly
5 Battery internally defective
(b) Insufficient charging current
1 Loose or corroded battery terminals
2 Generator driving belt slipping
(c) Battery will not hold a charge
1 Low electrolyte level
2 Battery plates sulphated
3 Electrolyte leakage from cracked casing or top sealing
compound
4 Plate separators ineffective
(d) Battery overcharged
1 Voltage regulator needs adjusting
(e) Generator output low or nil
1 Belt broken or slipping
2 Regulator unit out of adjustment
3 Worn bearings, loose pole pieces
4 Commutator worn, burned or shorted
5 Armature shaft bent or worn
6 Insulation proud between commutator segments
7 Brushes sticking, springs weak or broken
8 Field coil wires shorted, broken or burned
( f ) Starter motor lacks power or will not operate
1 Battery discharged, loose cable connections
2 Starter pinion jammed in mesh with flywheel gear
3 Starter switch faulty
4 Brushes worn or sticking, heads detached or shorting
5 Commutator dirty or worn
6 Starter shaft bent
7 Engine abnormally stiff
(g) Starter motor inoperative
1 Check 1 in (f)
2 Armature or field coils faulty
Page 125 of 128
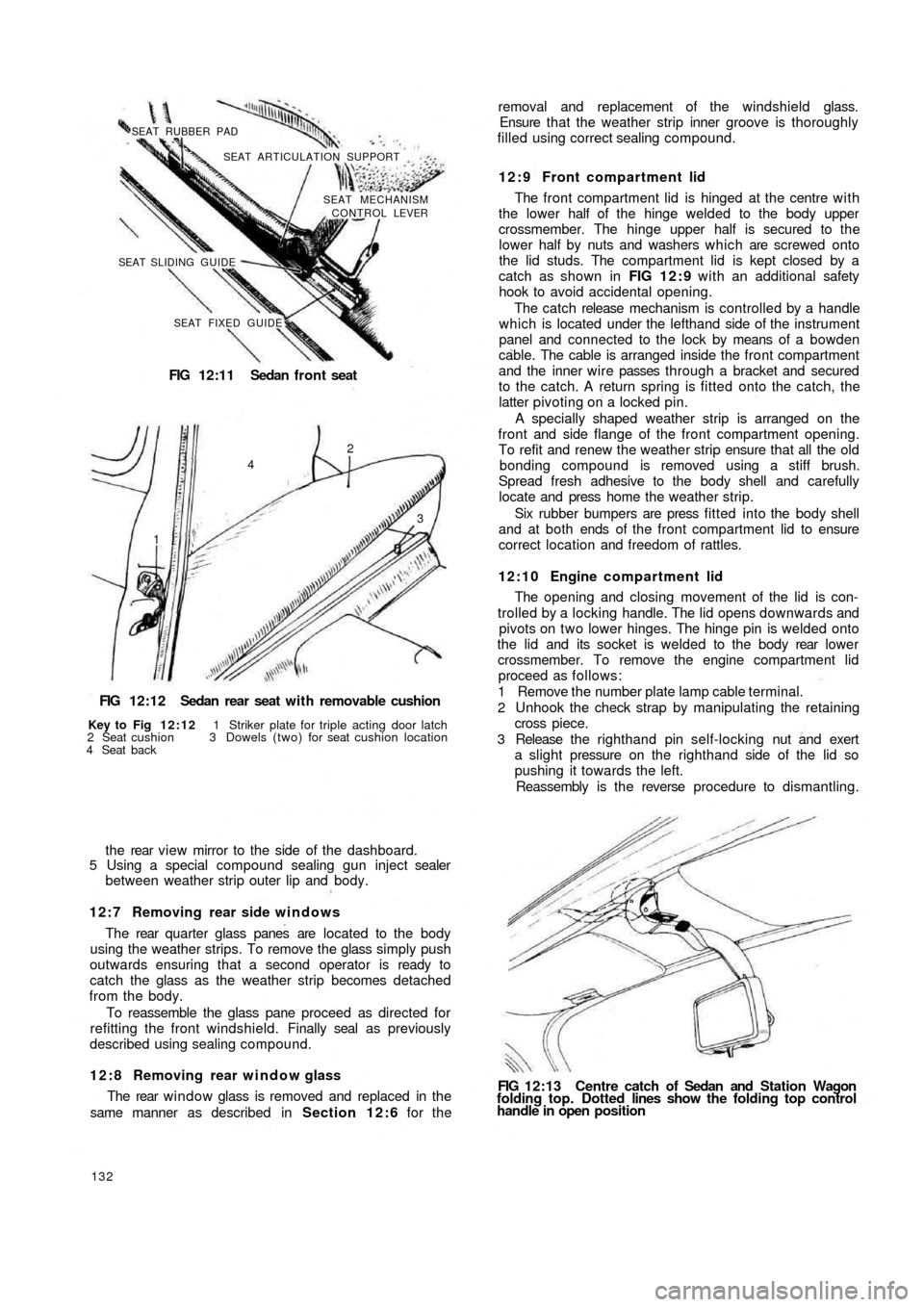
SEAT RUBBER PAD
SEAT ARTICULATION SUPPORT
SEAT MECHANISM
CONTROL LEVER
SEAT SLIDING GUIDE
SEAT FIXED GUIDE
FIG 12:11 Sedan front seat
42
3
1
FIG 12:12 Sedan rear seat w i t h removable cushion
Key to Fig 12:12 1 Striker plate for triple acting door latch
2 Seat cushion 3 Dowels (two) for seat cushion location
4 Seat back
t h e rear v i e w mirror to the side of the dashboard.
5 Using a special compound sealing gun inject sealer
between weather strip outer lip and body.
12:7 Removing rear side windows
The rear quarter glass panes are located to the body
using the weather strips. To remove the glass simply push
outwards ensuring that a second operator is ready to
catch the glass as the weather strip becomes detached
from the body.
To reassemble the glass pane proceed as directed for
refitting the front windshield. Finally seal as previously
described using sealing compound.
12:8 Removing rear window glass
The rear window glass is removed and replaced in the
same manner as described in Section 12:6 for the
132
FIG 12:13 Centre catch of Sedan and Station Wagon
folding top. Dotted lines show the folding top control
handle in open position removal and replacement of the windshield glass.
Ensure t h a t the weather strip inner groove is thoroughly
filled using correct sealing compound.
1 2 : 9 Front compartment lid
The front compartment lid is hinged at the centre w i t h
the lower half of the hinge welded to the body upper
crossmember. The hinge upper half is secured to the
lower half by nuts and washers which are screwed onto
the lid studs. The compartment lid is kept closed by a
catch as shown in FIG 1 2 : 9 with an additional safety
hook to avoid accidental opening.
The catch release mechanism is controlled by a handle
which is located under the lefthand side of the instrument
panel and connected to the lock by means of a bowden
cable. The cable is arranged inside the front compartment
and the inner wire passes through a bracket and secured
to the catch. A return spring is fitted onto the catch, the
latter pivoting on a locked pin.
A specially shaped weather strip is arranged on the
front and side flange of the front compartment opening.
To refit and renew the weather strip ensure that all the old
bonding compound is removed using a stiff brush.
Spread fresh adhesive to the body shell and carefully
locate and press home the weather strip.
Six rubber bumpers are press fitted into the body shell
and at both ends of the front compartment lid to ensure
correct location and freedom of rattles.
12:10 Engine compartment lid
The opening and closing movement of the lid is con-
trolled by a locking handle. The lid opens downwards and
pivots on two lower hinges. The hinge pin is welded onto
the lid and its socket is welded to the body rear lower
crossmember. To remove the engine compartment lid
proceed as follows:
1 Remove the number plate lamp cable terminal.
2 Unhook the check strap by manipulating the retaining
cross piece.
3 Release the righthand pin self-locking nut and exert
a slight pressure on the righthand side of the lid so
pushing it towards the left.
Reassembly is the reverse procedure to dismantling.