front suspension FIAT 500 1967 1.G Workshop Manual
[x] Cancel search | Manufacturer: FIAT, Model Year: 1967, Model line: 500, Model: FIAT 500 1967 1.GPages: 128, PDF Size: 9.01 MB
Page 73 of 128
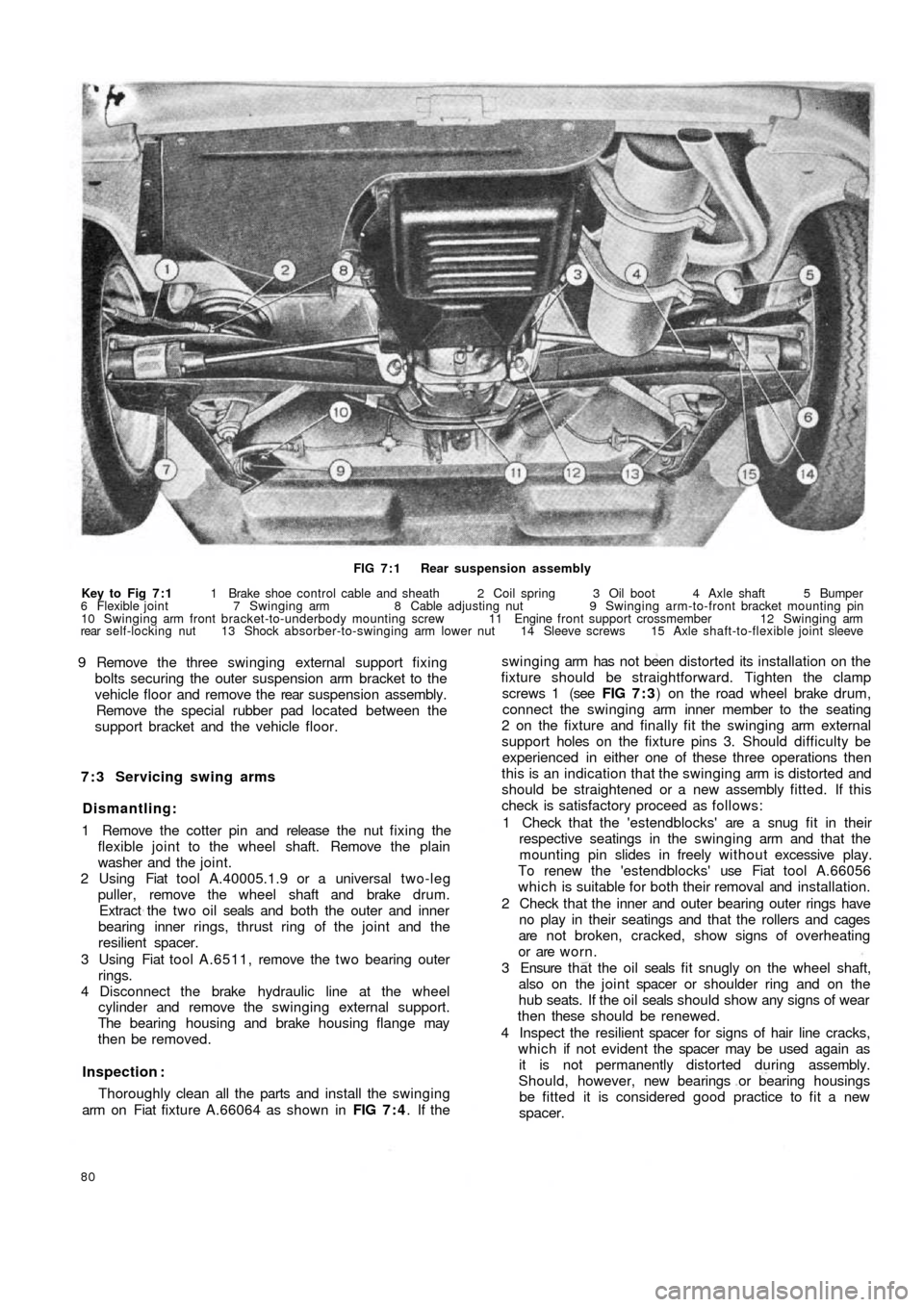
FIG 7 : 1 Rear suspension assembly
Key to Fig 7 : 1 1 Brake shoe control cable and sheath 2 Coil spring 3 Oil boot 4 Axle shaft 5 Bumper
6 Flexible joint 7 Swinging arm 8 Cable adjusting nut 9 Swinging arm-to-front bracket mounting pin
10 Swinging arm front bracket-to-underbody mounting screw 11 Engine front support crossmember 12 Swinging arm
rear self-locking nut 13 Shock absorber-to-swinging arm lower nut 14 Sleeve screws 15 Axle shaft-to-flexible joint sleeve
9 Remove the three swinging external support fixing
bolts securing the outer suspension arm bracket to the
vehicle floor and remove the rear suspension assembly.
Remove the special rubber pad located between the
support bracket and the vehicle floor.
7 : 3 Servicing swing arms
Dismantling:
1 Remove the cotter pin and release the nut fixing the
flexible joint to the wheel shaft. Remove the plain
washer and the joint.
2 Using Fiat tool A.40005.1.9 or a universal two-leg
puller, remove the wheel shaft and brake drum.
Extract the t w o oil seals and both the outer and inner
bearing inner rings, thrust ring of the joint and the
resilient spacer.
3 Using Fiat tool A.6511, remove the t w o bearing outer
rings.
4 Disconnect the brake hydraulic line at the wheel
cylinder and remove the swinging external support.
The bearing housing and brake housing flange may
then be removed.
Inspection :
Thoroughly clean all the parts and install the swinging
arm on Fiat fixture A.66064 as shown in FIG 7 : 4. If the
80
swinging arm has not been distorted its installation on the
fixture should be straightforward. Tighten the clamp
screws 1 (see FIG 7 : 3) on the road wheel brake drum,
connect the swinging arm inner member to the seating
2 on the fixture and finally fit the swinging arm external
support holes on the fixture pins 3. Should difficulty be
experienced in either one of these three operations then
this is an indication that the swinging arm is distorted and
should be straightened or a new assembly fitted. If this
check is satisfactory proceed as follows:
1 Check that the 'estendblocks' are a snug fit in their
respective seatings in the swinging arm and that the
mounting pin slides in freely w it h ou t excessive play.
To renew the 'estendblocks' use Fiat tool A.66056
which is suitable for both their removal and installation.
2 Check that the inner and outer bearing outer rings have
no play in their seatings and that the rollers and cages
are not broken, cracked, show signs of overheating
or are worn.
3 Ensure t h a t the o i l seals f i t snugly on the wheel shaft,
also on the joint spacer or shoulder ring and on the
hub seats. If the oil seals should show any signs of wear
then these should be renewed.
4 Inspect the resilient spacer for signs of hair line cracks,
which if not evident the spacer may be used again as
it is not permanently distorted during assembly.
Should, however, new bearings or bearing housings
be fitted it is considered good practice to fit a new
spacer.
Page 76 of 128
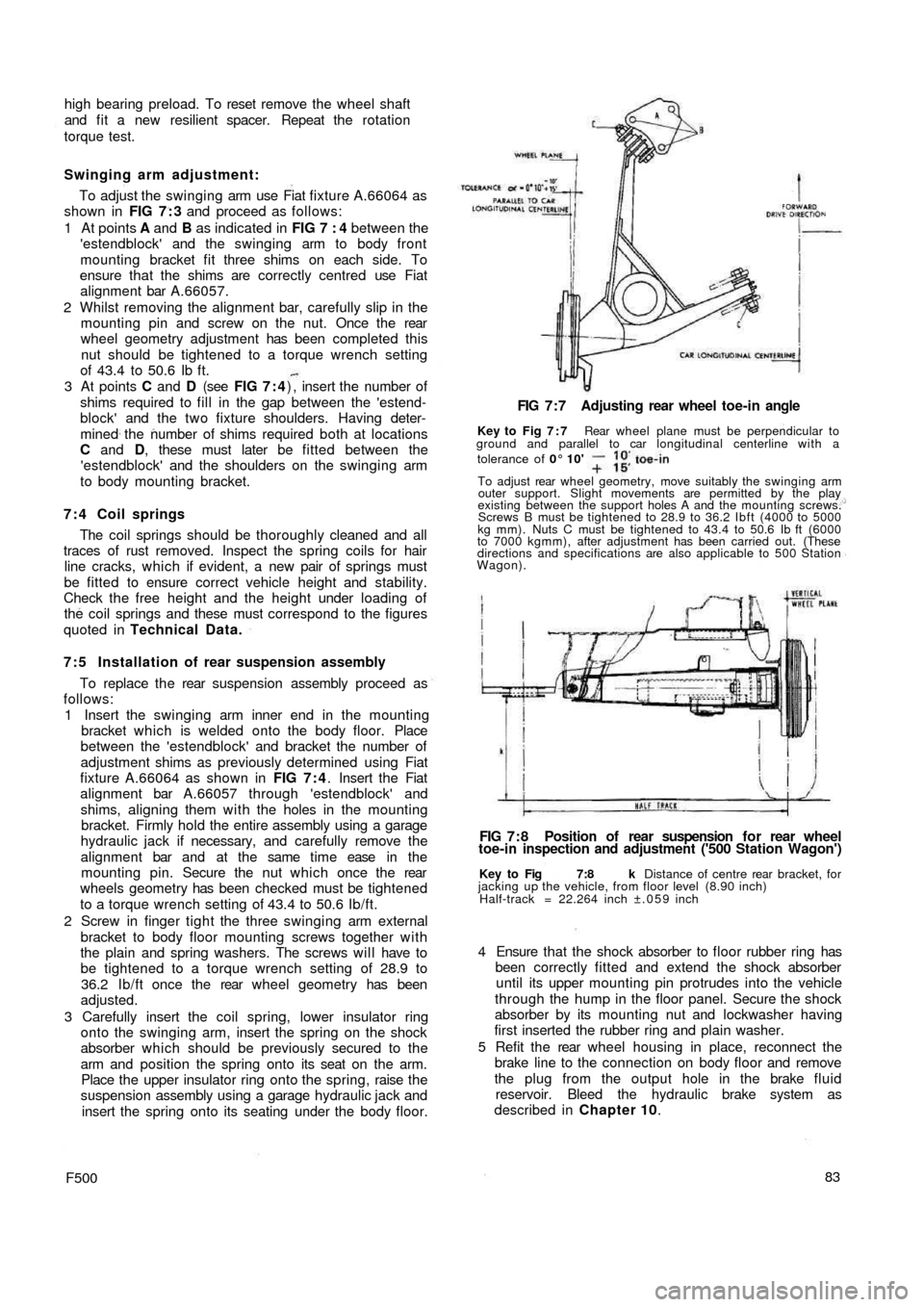
high bearing preload. To reset remove the wheel shaft
and fit a new resilient spacer. Repeat the rotation
torque test.
Swinging arm adjustment:
To adjust the swinging arm use Fiat fixture A.66064 as
shown in FIG 7 : 3 and proceed as follows:
1 At points A and B as indicated in FIG 7 : 4 between the
'estendblock' and the swinging arm to body front
mounting bracket fit three shims on each side. To
ensure that the shims are correctly centred use Fiat
alignment bar A.66057.
2 Whilst removing the alignment bar, carefully slip in the
mounting pin and screw on the nut. Once the rear
wheel geometry adjustment has been completed this
nut should be tightened to a torque wrench setting
of 43.4 to 50.6 Ib ft.
3 At points C and D (see FIG 7 : 4) , insert the number of
shims required to fill in the gap between the 'estend-
block' and the two fixture shoulders. Having deter-
mined the number of shims required both at locations
C and D, these must later be fitted between the
'estendblock' and the shoulders on the swinging arm
to body mounting bracket.
7 : 4 Coil springs
The coil springs should be thoroughly cleaned and all
traces of rust removed. Inspect the spring coils for hair
line cracks, which if evident, a new pair of springs must
be fitted to ensure correct vehicle height and stability.
Check the free
height and the height under loading of
the coil springs and these must correspond to the figures
quoted in Technical Data.
7:5 Installation of rear suspension assembly
To replace the rear suspension assembly proceed as
follows:
1 Insert the swinging arm inner end in the mounting
bracket which is welded onto the body floor. Place
between the 'estendblock' and bracket the number of
adjustment shims as previously determined using Fiat
fixture A.66064 as shown in FIG 7 : 4. Insert the Fiat
alignment bar A.66057 through 'estendblock' and
shims, aligning them with the holes in the mounting
bracket. Firmly hold the entire assembly using a garage
hydraulic jack if necessary, and carefully remove the
alignment bar and at the same time ease in t h e
mounting pin. Secure the nut which once the rear
wheels geometry has been checked must be tightened
to a torque wrench setting of 43.4 to 50.6 Ib/ft.
2 Screw in finger tight the three swinging arm external
bracket to body floor mounting screws together w i t h
the plain and spring washers. The screws will have to
be tightened to a torque wrench setting of 28.9 to
36.2 Ib/ft once the rear wheel geometry has been
adjusted.
3 Carefully insert the coil spring, lower insulator ring
onto the swinging arm, insert the spring on the shock
absorber which should be previously secured to the
arm and position the spring onto its seat on the arm.
Place the upper insulator ring onto the spring, raise the
suspension assembly using a garage hydraulic jack and
insert the spring onto its seating under the body floor.
F50083 4 Ensure that the shock absorber to floor rubber ring has
been correctly fitted and extend the shock absorber
until its upper mounting pin protrudes into the vehicle
through the hump in the floor panel. Secure the shock
absorber by its mounting nut and lockwasher having
first inserted the rubber ring and plain washer.
5 Refit the rear wheel housing in place, reconnect the
brake line to the connection on body floor and remove
the plug from the output hole in the brake fluid
reservoir. Bleed the hydraulic brake system as
described in Chapter 10.
Key to Fig 7:8 k Distance of centre rear bracket, for
jacking up the vehicle, from floor level (8.90 inch)
Half-track = 22.264 inch ±.059 inch
FIG 7 : 8 Position of rear suspension f o r rear wheel
toe-in inspection and adjustment ('500 Station Wagon') FIG 7 : 7 Adjusting rear wheel toe-in angle
Key to Fig 7 : 7 Rear wheel plane must be perpendicular to
ground and parallel to car longitudinal centerline with a
tolerance of 0° 10'
To adjust rear wheel geometry, move suitably the swinging arm
outer support. Slight movements are permitted by the play
existing between the support holes A and the mounting screws.
Screws B must be tightened to 28.9 to 36.2 Ibft (4000 to 5000
kg mm). Nuts C must be tightened to 43.4 to 50.6 Ib ft (6000
to 7000 kgmm), after adjustment has been carried out. (These
directions and specifications are also applicable to 500 Station
Wagon).
Page 77 of 128
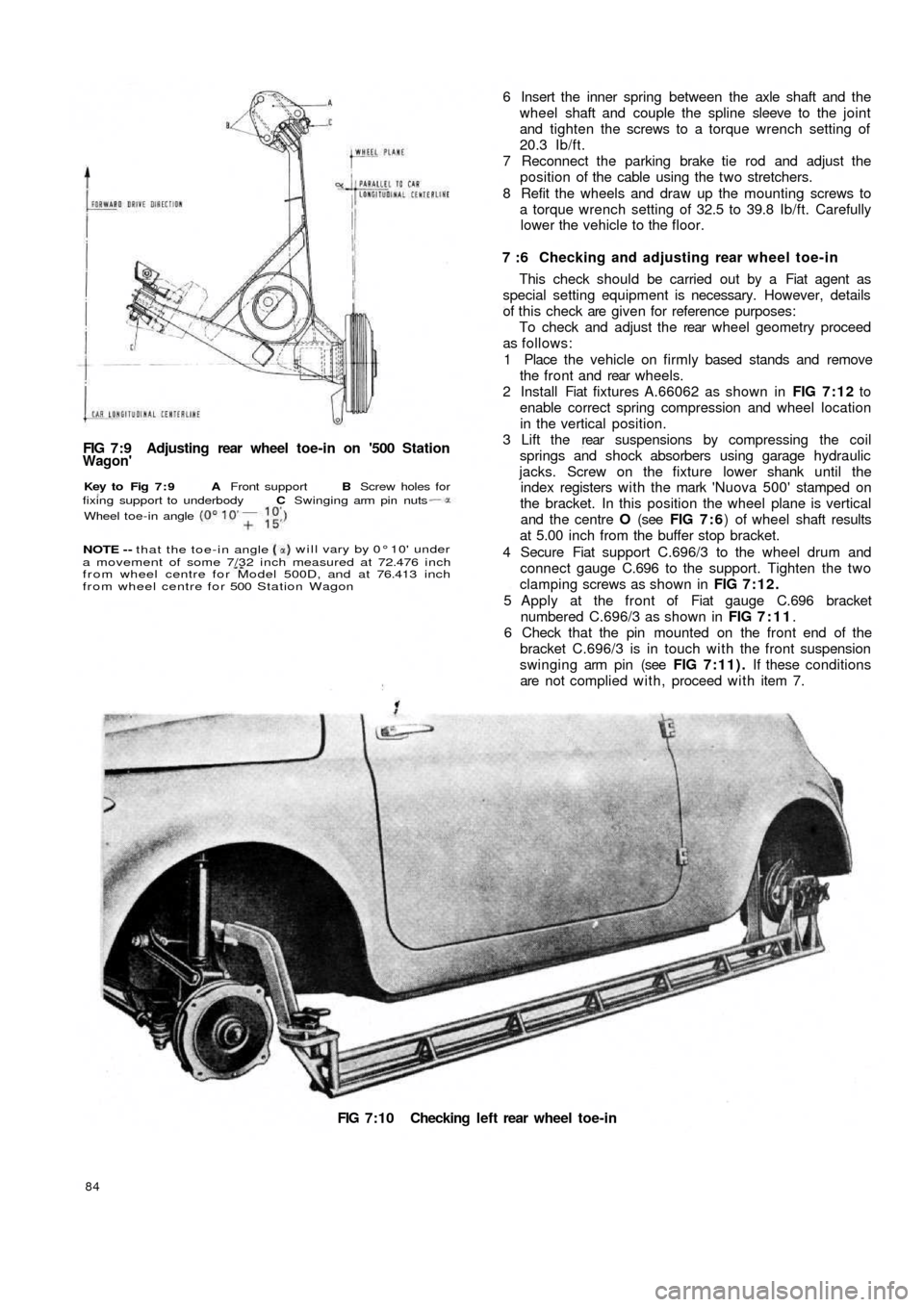
FIG 7:9 Adjusting rear wheel toe-in on '500 StationWagon'
FIG 7:10 Checking left rear wheel toe-in
84
6 Insert the inner spring between the axle shaft and the
wheel shaft and couple the spline sleeve to the joint
and tighten the screws to a torque wrench setting of
20.3 Ib/ft.
7 Reconnect the parking brake tie rod and adjust the
position of the cable using the two stretchers.
8 Refit the wheels and draw up the mounting screws to
a torque wrench setting of 32.5 to 39.8 Ib/ft. Carefully
lower the vehicle to the floor.
7 :6 Checking and adjusting rear wheel toe-in
This check should be carried out by a Fiat agent as
special setting equipment is necessary. However, details
of this check are given for reference purposes:
To check and adjust the rear wheel geometry proceed
as follows:
1 Place the vehicle on firmly based stands and remove
the front and rear wheels.
2 Install Fiat fixtures A.66062 as shown in FIG 7:12 to
enable correct spring compression and wheel location
in the vertical position.
3 Lift the rear suspensions by compressing the coil
springs and shock absorbers using garage hydraulic
jacks. Screw on the fixture lower shank until the
index registers with the mark 'Nuova 500' stamped on
the bracket. In this position the wheel plane is vertical
and the centre O (see FIG 7 : 6) of wheel shaft results
at 5.00 inch from the buffer stop bracket.
4 Secure Fiat support C.696/3 to the wheel drum and
connect gauge C.696 to the support. Tighten the two
clamping screws as shown in FIG 7:12.
5 Apply at the front of Fiat gauge C.696 bracket
numbered C.696/3 as shown in FIG 7:11.
6 Check that the pin mounted on the front end of the
bracket C.696/3 is in touch with the front suspension
swinging arm pin (see FIG 7:11). If these conditions
are not complied with, proceed with item 7.
Wheel toe-in angle
will vary by 0° 10' under
a movement of some 7/32 inch measured at 72.476 inch
from wheel centre for Model 500D, and at 76.413 inch
from wheel centre for 500 Station Wagon NOTE - - that the toe-in angle
Key to Fig 7 : 9 A Front support B Screw holes for
fixing support to underbody C Swinging arm pin nuts
Page 79 of 128
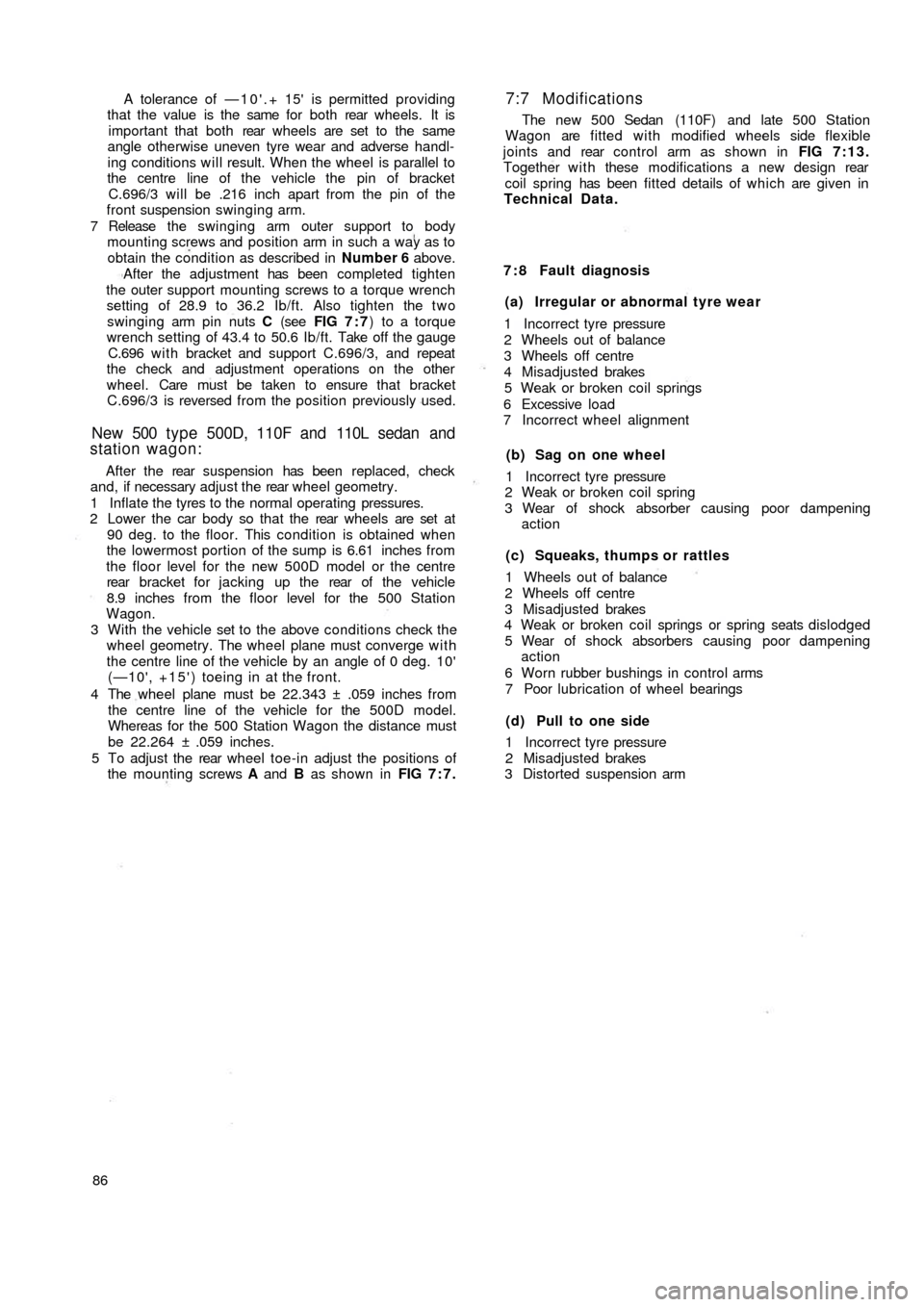
A tolerance of —10'.+ 15' is permitted providing
that the value is the same for both rear wheels. It is
important that both rear wheels are set to the same
angle otherwise uneven tyre wear and adverse handl-
ing conditions will result. When the wheel is parallel to
the centre line of the vehicle the pin of bracket
C.696/3 will be .216 inch apart from the pin of the
front suspension swinging arm.
7 Release the swinging arm outer support to body
mounting screws and position arm in such a way as to
obtain the condition as described in Number 6 above.
After the adjustment has been completed tighten
the outer support mounting screws to a torque wrench
setting of 28.9 to 36.2 Ib/ft. Also tighten the two
swinging arm pin nuts C (see FIG 7 : 7) to a torque
wrench setting of 43.4 to 50.6 Ib/ft. Take off the gauge
C.696 w i t h bracket and support C.696/3, and repeat
the check and adjustment operations on the other
wheel. Care must be taken to ensure that bracket
C.696/3 is reversed from the position previously used.
New 500 type 500D, 110F and 110L sedan and
station wagon:
After the rear suspension has been replaced, check
and, if necessary adjust the rear wheel geometry.
1 Inflate the tyres to the normal operating pressures.
2 Lower the car body so that the rear wheels are set at
90 deg. to the floor. This condition is obtained when
the lowermost portion of the sump is 6.61 inches from
the floor level for the new 500D model or the centre
rear bracket for jacking up the rear of t h e vehicle
8.9 inches from the floor level for the 500 Station
Wagon.
3 With the vehicle set to the above conditions check the
wheel geometry. The wheel plane must converge w i t h
the centre line of the vehicle by an angle of 0 deg. 10'
(—10', +15') toeing in at the front.
4 The wheel plane must be 22.343 ± .059 inches from
the centre line of the vehicle for the 500D model.
Whereas for the 500 Station Wagon the distance must
be 22.264 ± .059 inches.
5 To adjust the rear wheel toe-in adjust the positions of
the mounting screws A and B as shown in FIG 7:7.
86
7:7 Modifications
The new 500 Sedan (110F) and late 500 Station
Wagon are fitted with modified wheels side flexible
joints and rear control arm as shown in FIG 7:13.
Together w i t h these modifications a new design rear
coil spring has been fitted details of which are given in
Technical Data.
7 : 8 Fault diagnosis
(a) Irregular or abnormal tyre wear
1 Incorrect tyre pressure
2 Wheels out of balance
3 Wheels off centre
4 Misadjusted brakes
5 Weak or broken coil springs
6 Excessive load
7 Incorrect wheel alignment
(b) Sag on one wheel
1 Incorrect tyre pressure
2 Weak or broken coil spring
3 Wear of shock absorber causing poor dampening
action
(c) Squeaks, thumps or rattles
1 Wheels out of balance
2 Wheels off centre
3 Misadjusted brakes
4 Weak or broken coil springs or spring seats dislodged
5 Wear of shock absorbers causing poor dampening
action
6 Worn rubber bushings in control arms
7 Poor lubrication of wheel bearings
(d) Pull to one side
1 Incorrect tyre pressure
2 Misadjusted brakes
3 Distorted suspension arm
Page 80 of 128
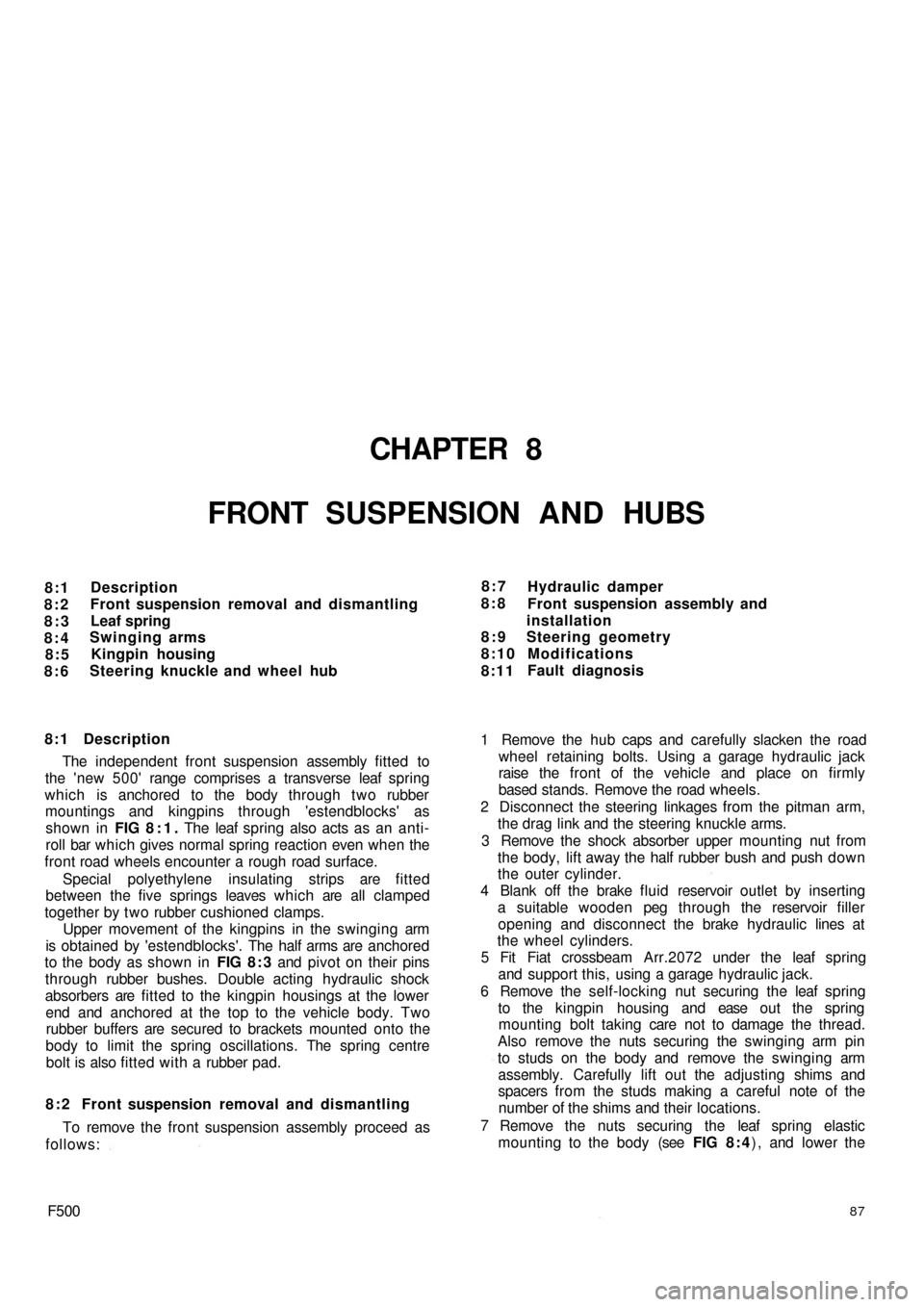
CHAPTER 8
FRONT SUSPENSION AND HUBS
8:1
8:2
8:3
8:4
8:5
8:6Description
Front suspension removal and dismantling
Leaf spring
Swinging arms
Kingpin housing
Steering knuckle and wheel hub
8:1 Description
The independent front suspension assembly fitted to
the 'new 500' range comprises a transverse leaf spring
which is anchored to the body through two rubber
mountings and kingpins through 'estendblocks' as
shown in FIG 8:1. The leaf spring also acts as an anti-
roll bar which gives normal spring reaction even when the
front road wheels encounter a rough road surface.
Special polyethylene insulating strips are fitted
between the five springs leaves which are all clamped
together by t w o rubber cushioned clamps.
Upper movement of the kingpins in the swinging arm
is obtained by 'estendblocks'. The half arms are anchored
to the body as shown in FIG 8 : 3 and pivot on their pins
through rubber bushes. Double acting hydraulic shock
absorbers are fitted to the kingpin housings at the lower
end and anchored at the top to the vehicle body. Two
rubber buffers are secured to brackets mounted onto the
body to limit the spring oscillations. The spring centre
bolt is also fitted with a rubber pad.
8 : 2 Front suspension removal and
dismantling
To remove the front suspension assembly proceed as
follows:
F50087
1 Remove the hub caps and carefully slacken the road
wheel retaining bolts. Using a garage hydraulic jack
raise the front of the vehicle and place on firmly
based stands. Remove the road wheels.
2 Disconnect the steering linkages from the pitman arm,
the drag link and the steering knuckle arms.
3 Remove the shock absorber upper mounting nut from
the body, lift away the half rubber bush and push d o w n
the outer cylinder.
4 Blank off the brake fluid reservoir outlet by inserting
a suitable wooden peg through the reservoir filler
opening and disconnect the brake hydraulic lines at
the wheel cylinders.
5 Fit Fiat crossbeam Arr.2072 under the leaf spring
and support this, using a garage hydraulic jack.
6 Remove the self-locking nut securing the leaf spring
to the kingpin housing and ease o u t the spring
mounting bolt taking care not to damage the thread.
Also remove the nuts securing the swinging arm pin
to studs on the body and remove the swinging arm
assembly. Carefully lift out the adjusting shims and
spacers from the studs making a careful note of the
number of the shims and their locations.
7 Remove the nuts securing the leaf spring elastic
mounting to the body (see FIG 8 : 4) , and lower the 8:7
8:8
8:9
8:10
8:11Hydraulic damper
Front suspension assembly and
installation
Steering geometry
Modifications
Fault diagnosis
Page 81 of 128
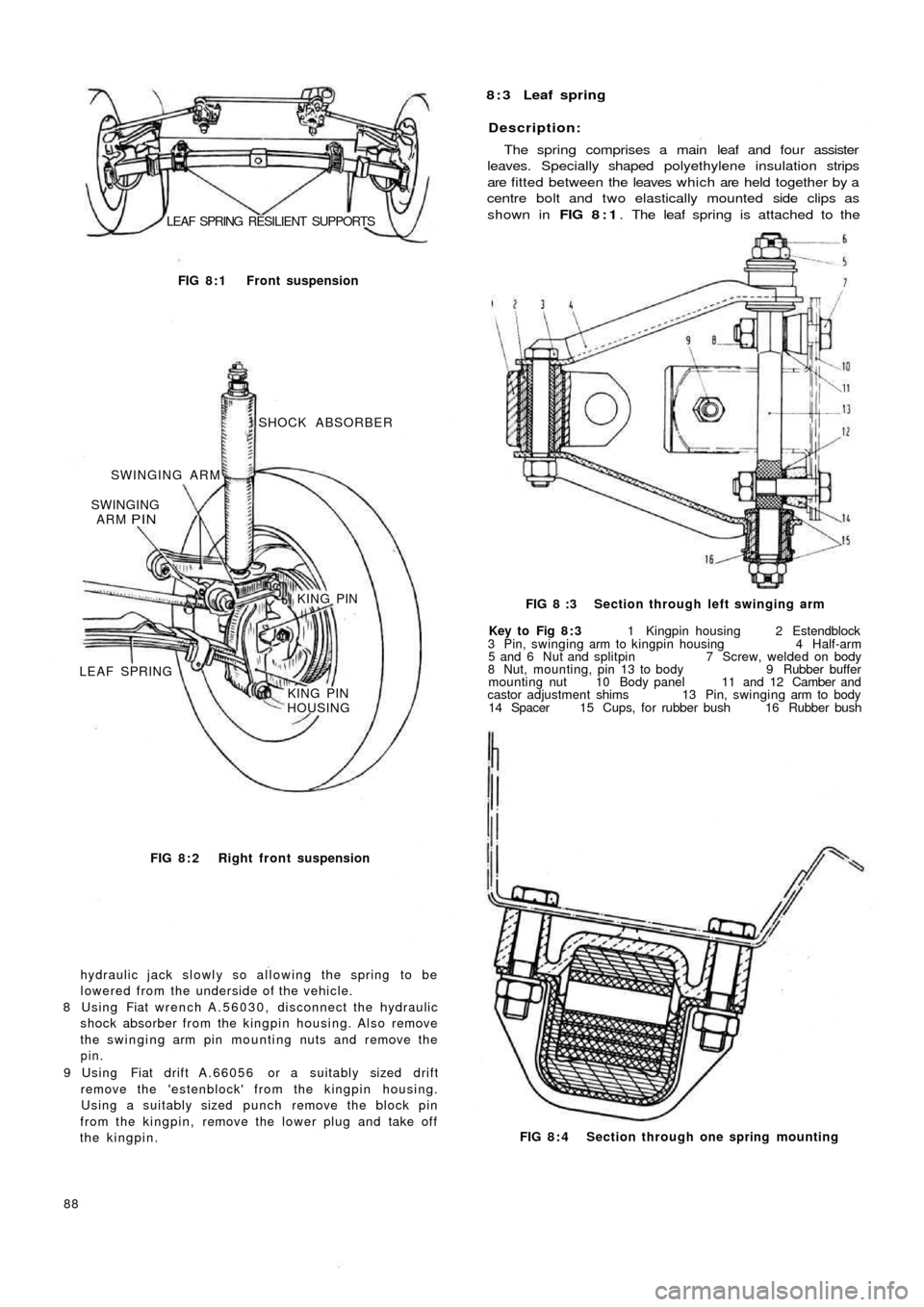
LEAF SPRING RESILIENT SUPPORTS
FIG 8 : 1 Front suspension
SHOCK ABSORBER
SWINGING ARM
SWINGING
ARM
PIN
KING PIN
LEAF SPRING
KING PIN
HOUSING
FIG 8 : 2 Right front suspension
hydraulic jack slowly so allowing the spring to be
lowered from the underside of the vehicle.
8 Using Fiat wrench A.56030, disconnect the hydraulic
shock absorber from the kingpin housing. Also remove
the swinging arm pin mounting nuts and remove the
pin.
9 Using Fiat drift A.66056 or a suitably sized drift
remove the 'estenblock' from the kingpin housing.
Using a suitably sized punch remove the block pin
from the kingpin, remove the lower plug and take off
the kingpin.
88FIG 8 : 4 Section through one spring mounting Key to Fig 8 : 3 1 Kingpin housing 2 Estendblock
3 Pin, swinging arm to kingpin housing 4 Half-arm
5 and 6 Nut and splitpin 7 Screw, welded on body
8 Nut, mounting, pin 13 to body 9 Rubber buffer
mounting nut 10 Body panel 11 and 12 Camber and
castor adjustment shims 13 Pin, swinging arm to body
14 Spacer 15 Cups, for rubber bush 16 Rubber bush FIG 8 :3 Section through left swinging arm
Description:
The spring comprises a main leaf and four assister
leaves. Specially shaped polyethylene insulation strips
are fitted between the leaves which are held together by a
centre bolt and two elastically mounted side clips as
shown in FIG 8 : 1. The leaf spring is attached to the 8 : 3 Leaf spring
Page 86 of 128
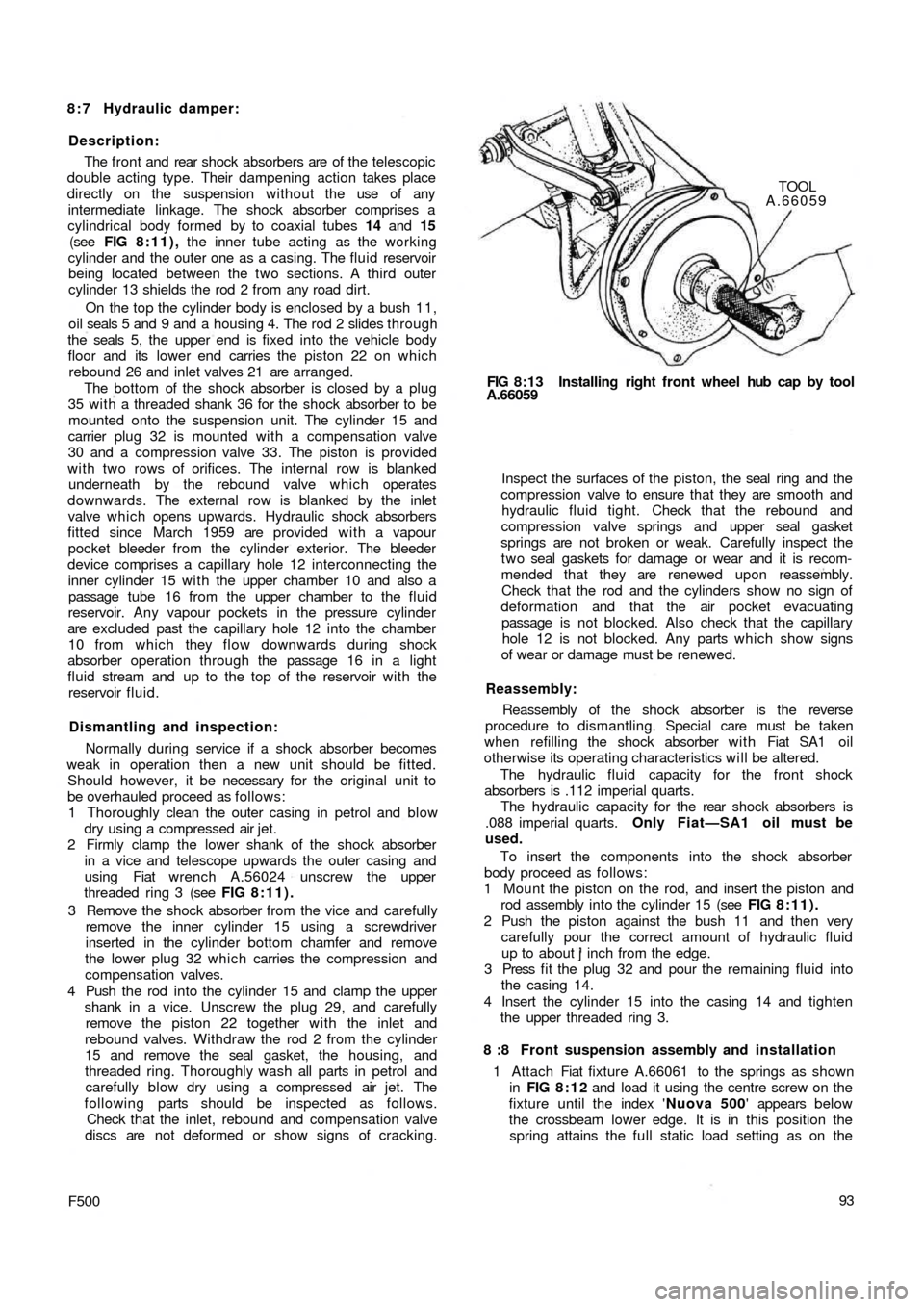
8 : 7 Hydraulic damper:
Description:
The front and rear shock absorbers are of the telescopic
double acting type. Their dampening action takes place
directly on the suspension without the use of any
intermediate linkage. The shock absorber comprises a
cylindrical body formed by to coaxial tubes 14 and 15
(see FIG 8:11), the inner tube acting as the working
cylinder and the outer one as a casing. The fluid reservoir
being located between the two sections. A third outer
cylinder 13 shields the rod 2 from any road dirt.
On the top the cylinder body is enclosed by a bush 1 1 ,
oil seals 5 and 9 and a housing 4. The rod 2 slides through
the seals 5, the upper end is fixed into the vehicle body
floor and its lower end carries the piston 22 on which
rebound 26 and inlet valves 21 are arranged.
The bottom of the shock absorber is closed by a plug
35 with a threaded shank 36 for the shock absorber to be
mounted onto the suspension unit. The cylinder 15 and
carrier plug 32 is mounted with a compensation valve
30 and a compression valve 33. The piston is provided
with two rows of orifices. The internal row is blanked
underneath by the rebound valve which operates
downwards. The external row is blanked by the inlet
valve which opens upwards. Hydraulic shock absorbers
fitted since March 1959 are provided w i t h a vapour
pocket bleeder from the cylinder exterior. The bleeder
device comprises a capillary
hole 12 interconnecting the
inner cylinder 15 with the upper chamber 10 and also a
passage tube 16 from the upper chamber to the fluid
reservoir. Any vapour pockets in the pressure cylinder
are excluded past the capillary hole 12 into the chamber
10 from which they flow downwards during shock
absorber operation through the passage 16 in a light
fluid stream and up to the top of the reservoir with the
reservoir fluid.
Dismantling and inspection:
Normally during service if a shock absorber becomes
weak in operation then a new unit should be fitted.
Should however, it be necessary for the original unit to
be overhauled proceed as follows:
1 Thoroughly clean the outer casing in petrol and blow
dry using a compressed air jet.
2 Firmly clamp the lower shank of the shock absorber
in a vice and telescope upwards the outer casing and
using Fiat wrench A.56024 unscrew the upper
threaded ring 3 (see FIG 8:11).
3 Remove the shock absorber from the vice and carefully
remove the inner cylinder 15 using a screwdriver
inserted in the cylinder bottom chamfer and remove
the lower plug 32 which carries the compression and
compensation valves.
4 Push the rod i n t o the cylinder 15 and clamp the upper
shank in a vice. Unscrew the plug 29, and carefully
remove the piston 22 together with the inlet and
rebound valves. Withdraw the rod 2 from the cylinder
15 and remove the seal gasket, the housing, and
threaded ring. Thoroughly wash all parts in petrol and
carefully blow dry using a c
ompressed air jet. The
following parts should be inspected as follows.
Check that the inlet, rebound and compensation valve
discs are not deformed or show signs of cracking.
F50093 Inspect the surfaces of the piston, the seal ring and the
compression valve to ensure that they are smooth and
hydraulic fluid tight. Check that the rebound and
compression valve springs and upper seal gasket
springs are not broken or weak. Carefully inspect the
t w o seal gaskets for damage or wear and it is recom-
mended that they are renewed upon reassembly.
Check that the rod and the cylinders show no sign of
deformation and that the air pocket evacuating
passage is not blocked. Also check that the capillary
hole 12 is not blocked. Any parts which show signs
of wear or damage must be renewed.
Reassembly:
Reassembly of the shock absorber is the reverse
procedure to dismantling. Special care must be taken
when refilling the shock absorber w i t h Fiat SA1 oil
otherwise its operating characteristics will be altered.
The hydraulic fluid capacity for the front shock
absorbers is .112 imperial quarts.
The hydraulic capacity for the rear shock absorbers is
.088 imperial quarts. Only Fiat—SA1 oil must be
used.
To insert the components into the shock absorber
body proceed as follows:
1 Mount the piston on the rod, and insert the piston and
rod assembly into the cylinder 15 (see FIG 8:11).
2 Push the piston against the bush 11 and then very
carefully pour the correct amount of hydraulic fluid
up to about j inch from the edge.
3 Press f i t t h e plug 32 and pour the remaining fluid into
the casing 14.
4 Insert the cylinder 15 into the casing 14 and tighten
the upper threaded ring 3.
8 :8 Front suspension assembly and installation
1 Attach Fiat fixture A.66061 to the springs as shown
in FIG 8:12 and load it using the centre screw on the
fixture until the index 'Nuova 500' appears below
the crossbeam lower edge. It is in this position the
spring attains the full static load setting as on the FIG 8:13 Installing right front wheel hub cap by tool
A.66059TOOL
A.66059
Page 88 of 128
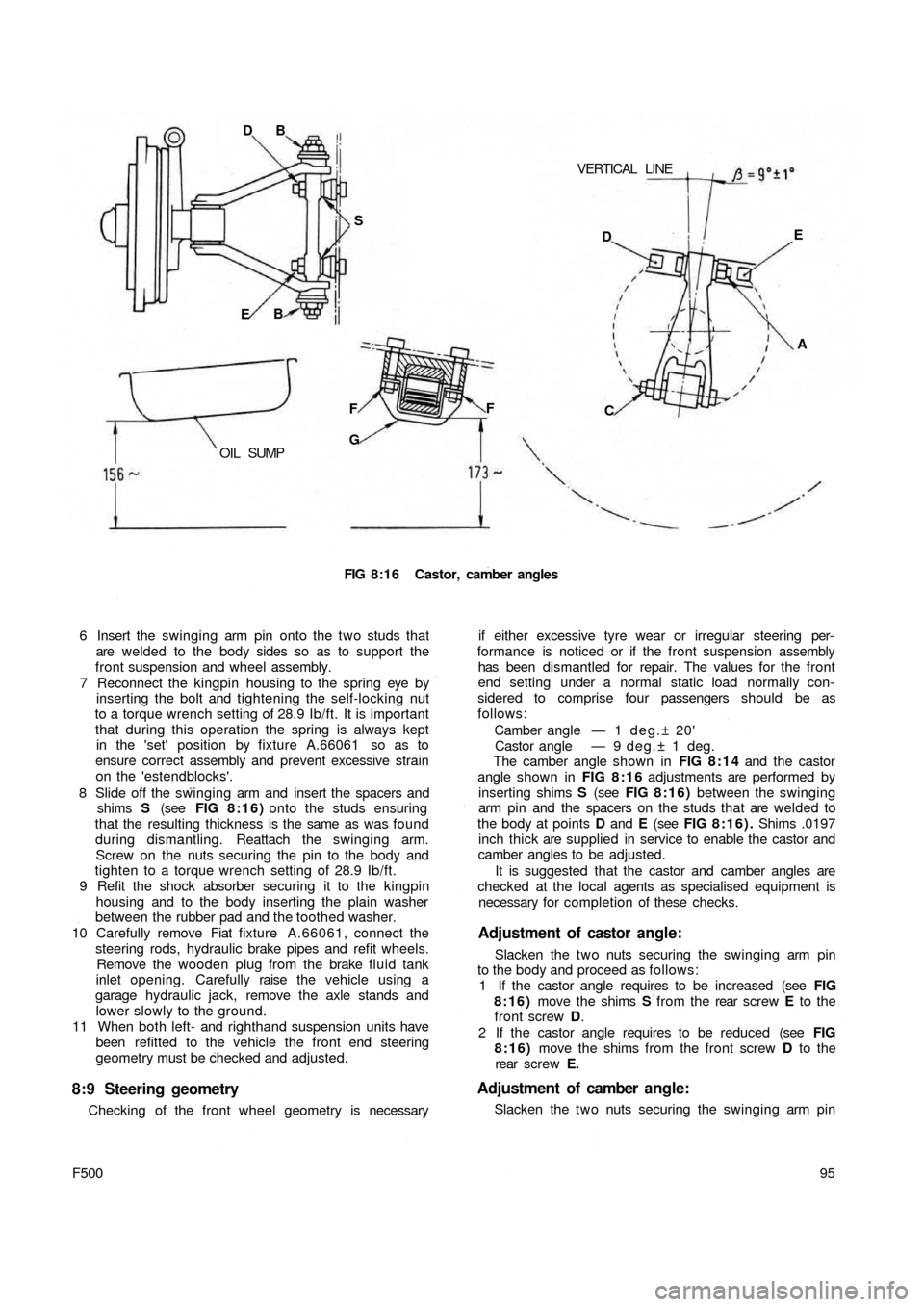
VERTICAL LINE DB
S
EB
OIL SUMPF
GF
FIG 8:16 Castor, camber angles
6 Insert the swinging arm pin onto the two studs that
are welded to the body sides so as to support the
front suspension and wheel assembly.
7 Reconnect the kingpin housing to the spring eye by
inserting the bolt and tightening the self-locking nut
to a torque wrench setting of 28.9 Ib/ft. It is important
that during this operation the spring is always kept
in the 'set' position by fixture A.66061 so as to
ensure correct assembly and prevent excessive strain
on the 'estendblocks'.
8 Slide off the swinging arm and insert the spacers and
shims S (see FIG 8:16) onto the studs ensuring
that the resulting thickness is the same as was found
during dismantling. Reattach the swinging arm.
Screw on the nuts securing the pin to the body and
tighten to a torque wrench setting of 28.9 Ib/ft.
9 Refit the shock absorber securing it to the kingpin
housing and to the body inserting the plain washer
between the rubber pad and the toothed washer.
10 Carefully remove Fiat fixture A.66061, connect the
steering rods, hydraulic brake pipes and refit wheels.
Remove the wooden plug from the brake fluid tank
inlet opening. Carefully raise the vehicle using a
garage hydraulic jack, remove the axle stands and
lower slowly to the ground.
11 When both left- and righthand suspension units have
been refitted to the vehicle the front end steering
geometry must be checked and adjusted.
8:9 Steering geometry
Checking of the front wheel geometry is necessary
95
F500
if either excessive tyre wear or irregular steering per-
formance is noticed or if the front suspension assembly
has been dismantled for repair. The values for the front
end setting under a normal static load normally con-
sidered to comprise four passengers should be as
follows:
Camber angle — 1 d e g . ± 20'
Castor angle — 9 deg.± 1 deg.
The camber angle shown in FIG 8:14 and the castor
angle shown in FIG 8 : 1 6 adjustments are performed by
inserting shims S (see FIG 8 : 1 6 ) between the swinging
arm pin and the spacers on the studs that are welded to
the body at points D and E (see FIG 8:16). Shims .0197
inch thick are supplied in service to enable the castor and
camber angles to be adjusted.
It is suggested that the castor and camber angles are
checked at the local agents as specialised equipment is
necessary for completion of these checks.
Adjustment of castor angle:
Slacken the t w o nuts securing the swinging arm pin
to the body and proceed as follows:
1 If the castor angle requires to be increased (see FIG
8:16) move the shims S from the rear screw E to the
front screw D.
2 If the castor angle requires to be reduced (see FIG
8:16) move the shims from the front screw D to the
rear screw E.
Adjustment of camber angle:
Slacken the t w o nuts securing the swinging arm pin DE
A
C
Page 89 of 128

to the body and proceed as follows:
1 If the camber angle requires to be increased (see FIG
8:16) add the same number of shims S on both
screws D and E.
2 If the camber angle requires to be reduced (see FIG
8:16) remove the same number of shims from both
screws D and E.
The addition or removal of shims at the t w o points D
and E permits camber adjustment to be made without
any disturbing of the castor angle.
8:10 Modifications
Checking and adjusting castor and camber angles:
When checking the castor and camber angle the
static loading should be such that the distance between
the semi-elliptic spring mountings G (see FIG 8:16)
and the floor level to be approximately 6.81 inches, also a
distance between the lowermost portion of the sump and
the floor level of approximately 6.14 inch for the Model
500D. For the 500 Station Wagon version the distance
between centre rear bracket for jacking-up the vehicle
and the floor level should be approximately 8.90 inches.
All other front wheel alignment specifications are the
same as for the remaining 500 saloon models.
8:11 Fault diagnosis
(a) Wheel bounce
1 Tyre casing faulty
2 Uneven tyre pressures
3 Wheels out of balance
4 Semi-elliptic mounting spring worn5 Weak or seized shock absorber
6 Wheel rim or tyre misaligned
(b) Suspension noise
1 Lack of lubrication
2 Noisy or inoperative shock absorbers
3 Worn or loose wheel bearings
(c) Pull to one side
1 Low or uneven tyre pressures
2 Incorrect front wheel alignment
3 Suspension arms distorted
4 Inoperative shock absorbers
5 Brakes binding
(d) Excessive t y r e wear
1 Incorrect tyre rotation during servicing periods
2 Incorrect camber angle
3 Incorrect toe-in
4 Incorrect tyre inflation
5 Excessive play at wheel bearings
6 Wheel wobble
7 Stiff suspension arms
8 Brakes out of adjustment
(e) Wheel wobble
1 Uneven tyre pressures
2 Loose or worn wheel bearings
3 Inoperative shock absorbers
4 Loose steering knuckle or kingpin housing
5 Incorrect front wheel alignment
6 Control arm rubber bushings, or kingpin housing and
semi-elliptic spring 'estendblock' worn
96
Page 95 of 128
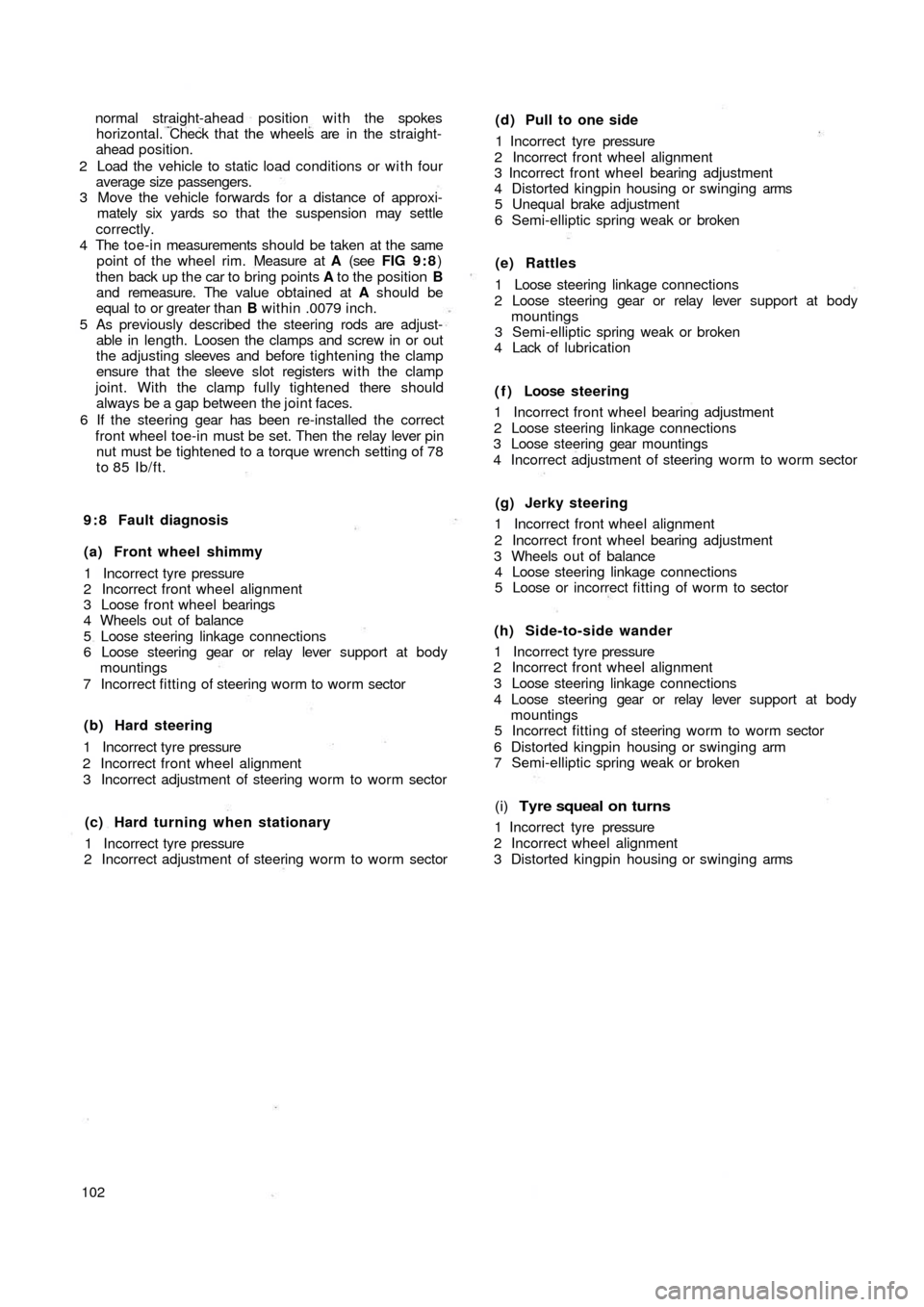
normal straight-ahead position with the spokes
horizontal. Check that the wheels are in the straight-
ahead position.
2 Load the vehicle to static load conditions or with four
average size passengers.
3 Move the vehicle forwards for a distance of approxi-
mately six yards so that the suspension may settle
correctly.
4 The toe-in measurements should be taken at the same
point of the wheel rim. Measure at A (see FIG 9 : 8)
then back up the car to bring points A to the position B
and remeasure. The value obtained at A should be
equal to or greater than B within .0079 inch.
5 As previously described the steering rods are adjust-
able in length. Loosen the clamps and screw in or out
the adjusting sleeves and before tightening the clamp
ensure that the sleeve slot registers w i t h the clamp
joint. With the clamp fully tightened there should
always be a gap between the joint faces.
6 If the steering gear has been re-installed the correct
front wheel toe-in must be set. Then the relay lever pin
nut must be tightened to a torque wrench setting of 78
to 85 Ib/ft.
9 : 8 Fault diagnosis
(a) Front wheel shimmy
1 Incorrect tyre pressure
2 Incorrect front wheel alignment
3 Loose front wheel bearings
4 Wheels out of balance
5 Loose steering linkage connections
6 Loose steering gear or relay lever support at body
mountings
7 Incorrect fitting of steering worm to worm sector
(b) Hard steering
1 Incorrect tyre pressure
2 Incorrect front wheel alignment
3 Incorrect adjustment of steering worm to worm sector
(c) Hard turning when stationary
1 Incorrect tyre pressure
2 Incorrect adjustment of steering worm to worm sector
102
(d) Pull to one side
1 Incorrect tyre pressure
2 Incorrect front wheel alignment
3 Incorrect front wheel bearing adjustment
4 Distorted kingpin housing or swinging arms
5 Unequal brake adjustment
6 Semi-elliptic spring weak or broken
(e) Rattles
1 Loose steering linkage connections
2 Loose steering gear or relay lever support at body
mountings
3 Semi-elliptic spring weak or broken
4 Lack of lubrication
( f ) Loose steering
1 Incorrect front wheel bearing adjustment
2 Loose steering linkage connections
3 Loose steering gear mountings
4 Incorrect adjustment of steering worm to worm sector
(g) Jerky steering
1 Incorrect front wheel alignment
2 Incorrect front wheel bearing adjustment
3 Wheels out of balance
4 Loose steering linkage connections
5 Loose or incorrect fitting of worm to sector
(h) Side-to-side wander
1 Incorrect tyre pressure
2 Incorrect front wheel alignment
3 Loose steering linkage connections
4 Loose steering gear or relay lever support at body
mountings
5 Incorrect fitting of steering worm to worm sector
6 Distorted kingpin housing or swinging arm
7 Semi-elliptic spring weak or broken
(i) Tyre squeal on turns
1 Incorrect tyre pressure
2 Incorrect wheel alignment
3 Distorted kingpin housing or swinging arms