brake light FIAT 500 1973 1.G Workshop Manual
[x] Cancel search | Manufacturer: FIAT, Model Year: 1973, Model line: 500, Model: FIAT 500 1973 1.GPages: 128, PDF Size: 9.01 MB
Page 76 of 128
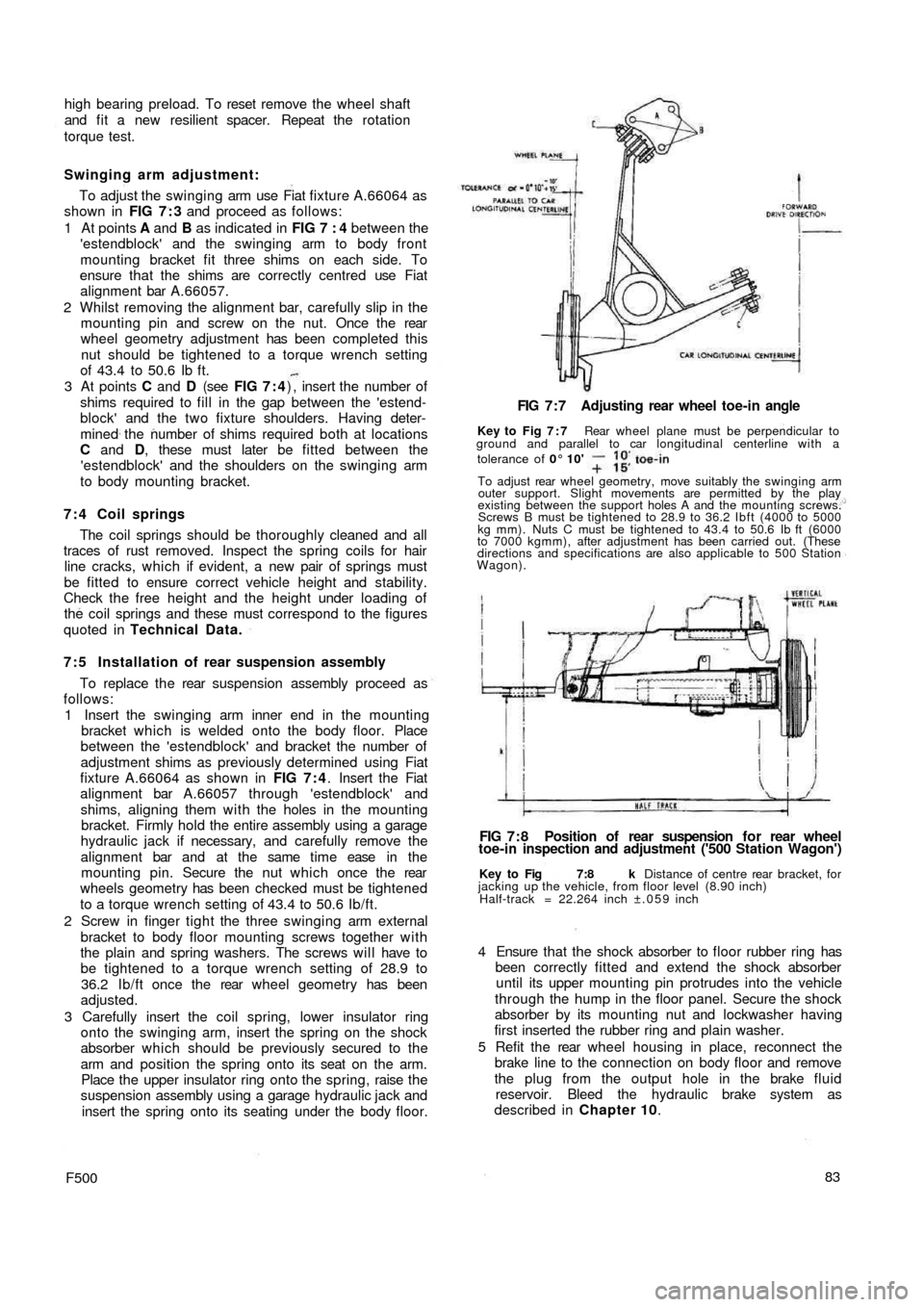
high bearing preload. To reset remove the wheel shaft
and fit a new resilient spacer. Repeat the rotation
torque test.
Swinging arm adjustment:
To adjust the swinging arm use Fiat fixture A.66064 as
shown in FIG 7 : 3 and proceed as follows:
1 At points A and B as indicated in FIG 7 : 4 between the
'estendblock' and the swinging arm to body front
mounting bracket fit three shims on each side. To
ensure that the shims are correctly centred use Fiat
alignment bar A.66057.
2 Whilst removing the alignment bar, carefully slip in the
mounting pin and screw on the nut. Once the rear
wheel geometry adjustment has been completed this
nut should be tightened to a torque wrench setting
of 43.4 to 50.6 Ib ft.
3 At points C and D (see FIG 7 : 4) , insert the number of
shims required to fill in the gap between the 'estend-
block' and the two fixture shoulders. Having deter-
mined the number of shims required both at locations
C and D, these must later be fitted between the
'estendblock' and the shoulders on the swinging arm
to body mounting bracket.
7 : 4 Coil springs
The coil springs should be thoroughly cleaned and all
traces of rust removed. Inspect the spring coils for hair
line cracks, which if evident, a new pair of springs must
be fitted to ensure correct vehicle height and stability.
Check the free
height and the height under loading of
the coil springs and these must correspond to the figures
quoted in Technical Data.
7:5 Installation of rear suspension assembly
To replace the rear suspension assembly proceed as
follows:
1 Insert the swinging arm inner end in the mounting
bracket which is welded onto the body floor. Place
between the 'estendblock' and bracket the number of
adjustment shims as previously determined using Fiat
fixture A.66064 as shown in FIG 7 : 4. Insert the Fiat
alignment bar A.66057 through 'estendblock' and
shims, aligning them with the holes in the mounting
bracket. Firmly hold the entire assembly using a garage
hydraulic jack if necessary, and carefully remove the
alignment bar and at the same time ease in t h e
mounting pin. Secure the nut which once the rear
wheels geometry has been checked must be tightened
to a torque wrench setting of 43.4 to 50.6 Ib/ft.
2 Screw in finger tight the three swinging arm external
bracket to body floor mounting screws together w i t h
the plain and spring washers. The screws will have to
be tightened to a torque wrench setting of 28.9 to
36.2 Ib/ft once the rear wheel geometry has been
adjusted.
3 Carefully insert the coil spring, lower insulator ring
onto the swinging arm, insert the spring on the shock
absorber which should be previously secured to the
arm and position the spring onto its seat on the arm.
Place the upper insulator ring onto the spring, raise the
suspension assembly using a garage hydraulic jack and
insert the spring onto its seating under the body floor.
F50083 4 Ensure that the shock absorber to floor rubber ring has
been correctly fitted and extend the shock absorber
until its upper mounting pin protrudes into the vehicle
through the hump in the floor panel. Secure the shock
absorber by its mounting nut and lockwasher having
first inserted the rubber ring and plain washer.
5 Refit the rear wheel housing in place, reconnect the
brake line to the connection on body floor and remove
the plug from the output hole in the brake fluid
reservoir. Bleed the hydraulic brake system as
described in Chapter 10.
Key to Fig 7:8 k Distance of centre rear bracket, for
jacking up the vehicle, from floor level (8.90 inch)
Half-track = 22.264 inch ±.059 inch
FIG 7 : 8 Position of rear suspension f o r rear wheel
toe-in inspection and adjustment ('500 Station Wagon') FIG 7 : 7 Adjusting rear wheel toe-in angle
Key to Fig 7 : 7 Rear wheel plane must be perpendicular to
ground and parallel to car longitudinal centerline with a
tolerance of 0° 10'
To adjust rear wheel geometry, move suitably the swinging arm
outer support. Slight movements are permitted by the play
existing between the support holes A and the mounting screws.
Screws B must be tightened to 28.9 to 36.2 Ibft (4000 to 5000
kg mm). Nuts C must be tightened to 43.4 to 50.6 Ib ft (6000
to 7000 kgmm), after adjustment has been carried out. (These
directions and specifications are also applicable to 500 Station
Wagon).
Page 87 of 128
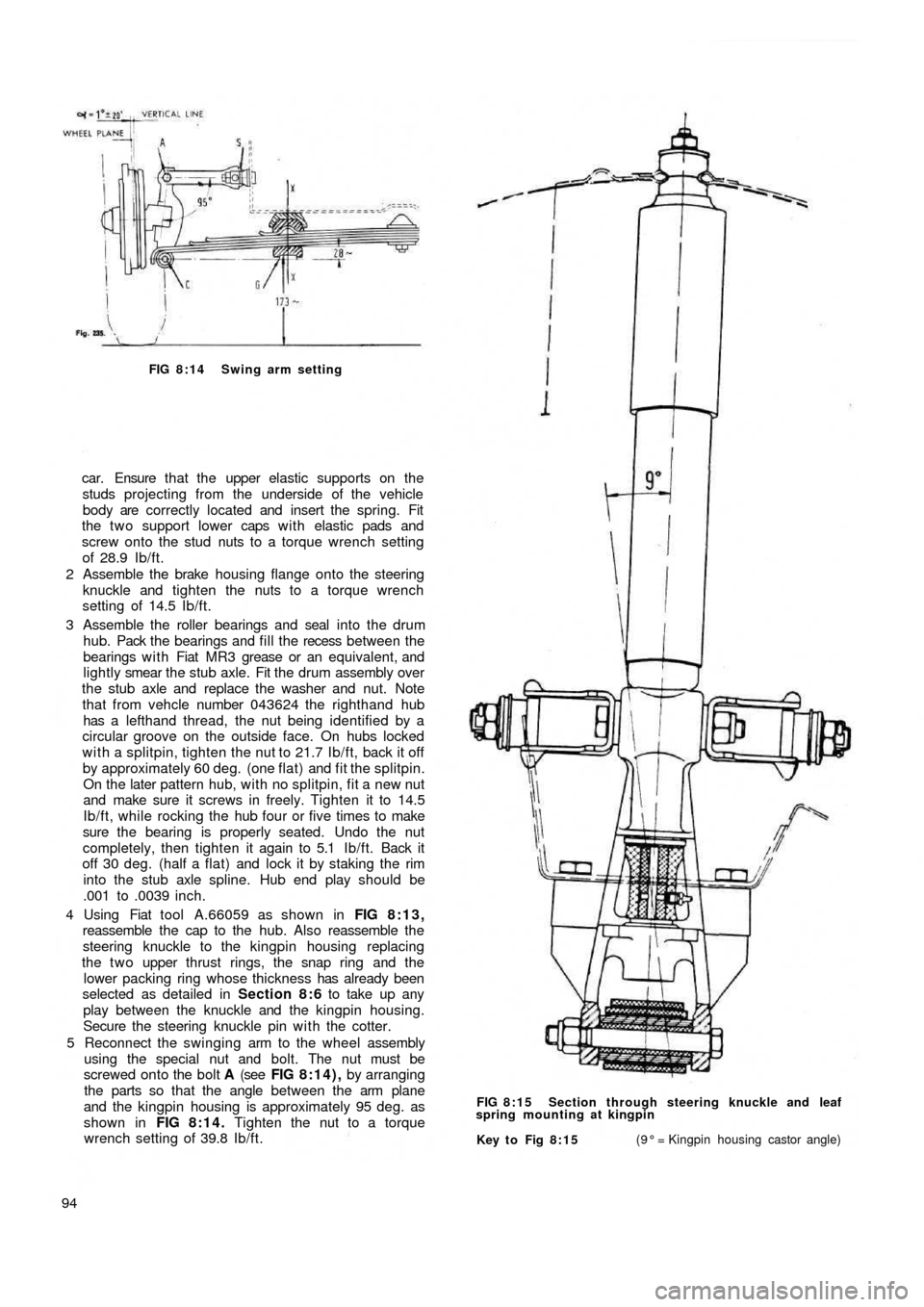
FIG 8:14 Swing arm setting
car. Ensure t h a t the upper elastic supports on the
studs projecting from the underside of the vehicle
body are correctly located and insert the spring. Fit
the two support lower caps w i t h elastic pads and
screw onto the stud nuts to a torque wrench setting
of 28.9 Ib/ft.
2 Assemble the brake housing flange onto the steering
knuckle and tighten the nuts to a torque wrench
setting of 14.5 Ib/ft.
3 Assemble the roller bearings and seal into the drum
hub. Pack the bearings and fill the recess between the
bearings w i t h Fiat MR3 grease or an equivalent, and
lightly smear the stub axle. Fit the drum assembly over
the stub axle and replace the washer and nut. Note
that from vehcle number 043624 the righthand hub
has a lefthand thread, the nut being identified by a
circular groove on the outside face. On hubs locked
with a splitpin, tighten the nut to 21.7 Ib/ft, back it off
by approximately 60 deg. (one flat) and fit the splitpin.
On the later pattern hub, with no splitpin, fit a new nut
and make sure it screws in freely. Tighten it to 14.5
Ib/ft, while rocking the hub four or five times to make
sure the bearing is properly seated. Undo the nut
completely, then tighten it again to 5.1 Ib/ft. Back it
off 30 deg. (half a flat) and lock it by staking the rim
into the stub axle spline. Hub end play should be
.001 to .0039 inch.
4 Using Fiat tool A.66059 as shown in FIG 8:13,
reassemble the cap to the hub. Also reassemble the
steering knuckle to the kingpin housing replacing
the t w o upper
thrust rings, the snap ring and the
lower packing ring whose thickness has already been
selected as detailed in Section 8:6 to take up any
play between the knuckle and the kingpin housing.
Secure the steering knuckle pin with the cotter.
5 Reconnect the swinging arm to the wheel assembly
using the special nut and bolt. The nut must be
screwed onto the bolt A (see FIG 8:14), by arranging
the parts so that the angle between the arm plane
and the kingpin housing is approximately 95 deg. as
shown in FIG 8:14. Tighten the nut to a torque
wrench setting of 39.8 Ib/ft.
94
Key to Fig 8:15(9° = Kingpin housing castor angle) FIG 8:15 Section through steering knuckle and leaf
spring mounting at kingpin
Page 97 of 128
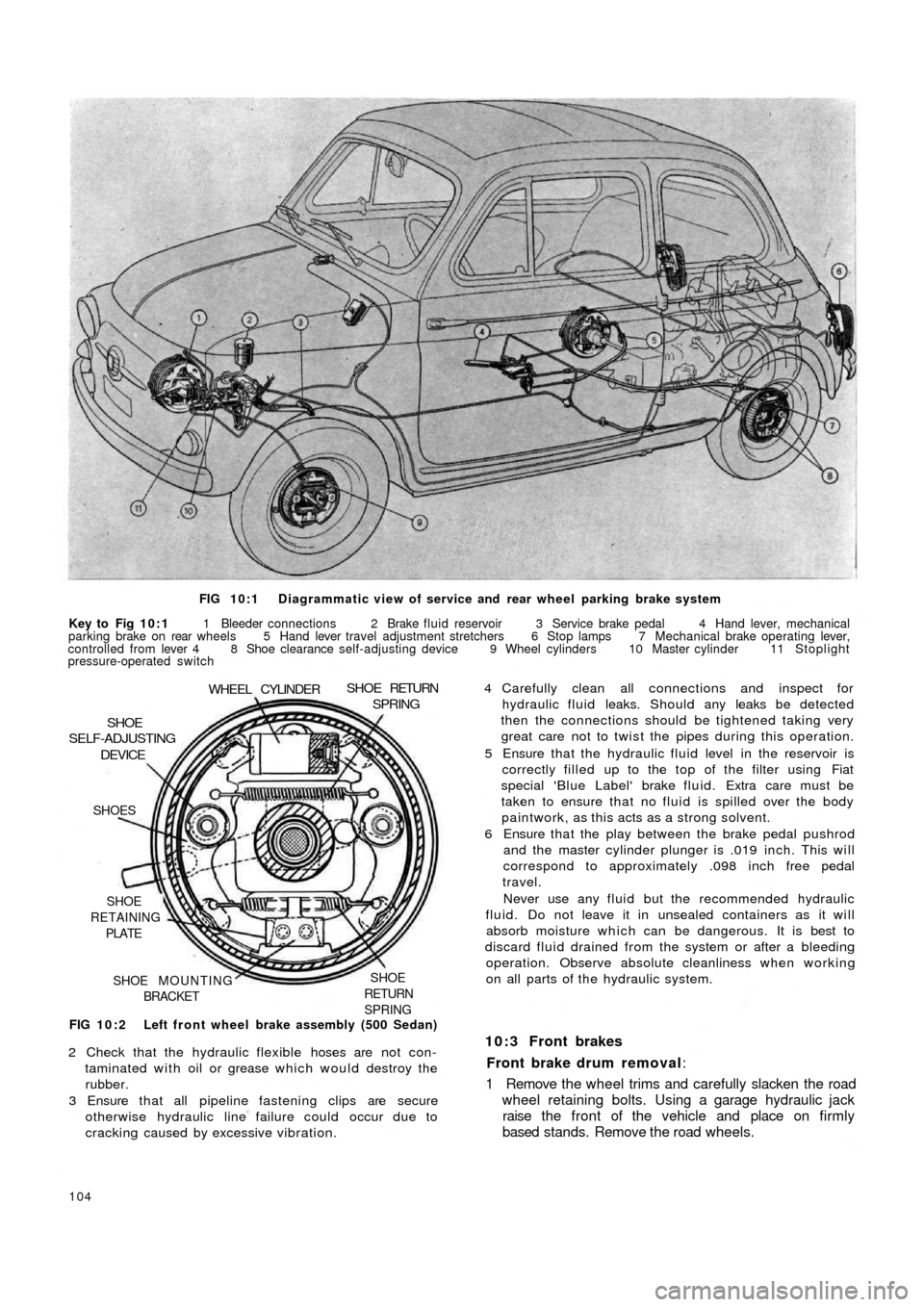
FIG 10:1 Diagrammatic view of service and rear wheel parking brake system
Key to Fig 10:1 1 Bleeder connections 2 Brake fluid reservoir 3 Service brake pedal 4 Hand lever, mechanical
parking brake on rear wheels 5 Hand lever travel adjustment stretchers 6 Stop lamps 7 Mechanical brake operating lever,
controlled from lever 4 8 Shoe clearance self-adjusting device 9 Wheel cylinders 10 Master cylinder 11 Stoplight
pressure-operated switch
FIG 10:2 Left front wheel brake assembly (500 Sedan)
SHOE
RETURN
SPRINGSHOE MOUNTING
BRACKET SHOE
RETAINING
PLATE SHOES
DEVICESHOE
SELF-ADJUSTING
WHEEL CYLINDERSHOE RETURNSPRING
2 Check that the hydraulic flexible hoses are not con-
taminated with oil or grease which would destroy the
rubber.
3 Ensure that all pipeline fastening clips are secure
otherwise hydraulic line failure could occur due to
cracking caused by excessive vibration.
104
4 Carefully clean all connections and inspect for
hydraulic fluid leaks. Should any leaks be detected
then the connections should be tightened taking very
great care not to twist the pipes during this operation.
5 Ensure that the hydraulic fluid level in the reservoir is
correctly filled up to the top of the filter using Fiat
special 'Blue Label' brake fluid. Extra care must be
taken to ensure that no fluid is spilled over the body
paintwork, as this acts as a strong solvent.
6 Ensure that the play between the brake pedal pushrod
and the master cylinder plunger is .019 inch. This will
correspond to approximately .098 inch free pedal
travel.
Never use any fluid but the recommended hydraulic
fluid. Do not leave it in unsealed containers as it will
absorb moisture which can be dangerous. It is best to
discard fluid drained from the system or after a bleeding
operation. Observe absolute cleanliness when working
on all parts of the hydraulic system.
10:3 Front brakes
Front brake drum removal:
1 Remove the wheel trims and carefully slacken the road
wheel retaining bolts. Using a garage hydraulic jack
raise the front of the vehicle and place on firmly
based stands. Remove the road wheels.
Page 99 of 128
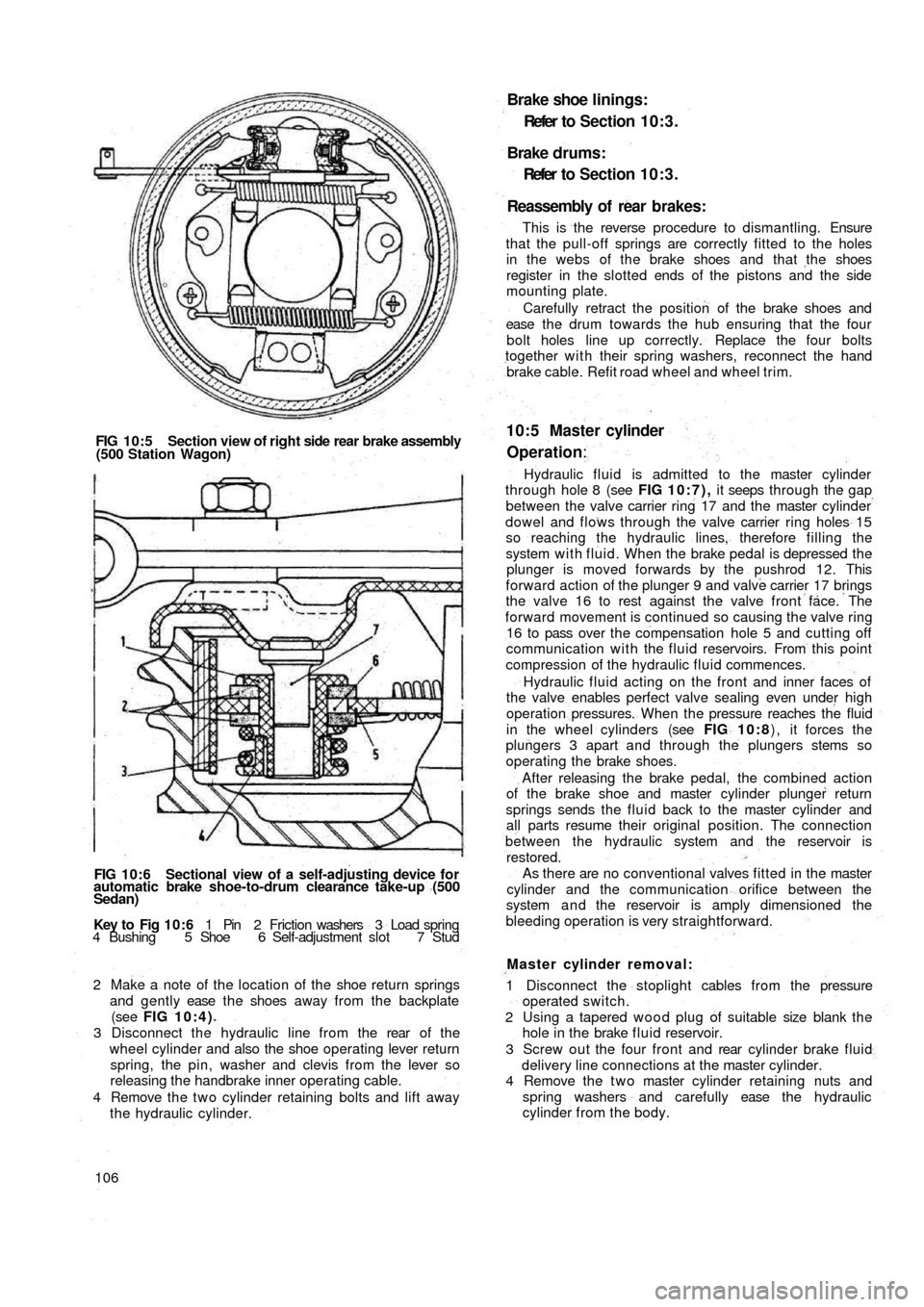
FIG 10:5 Section view of right side rear brake assembly
(500 Station Wagon)
FIG 10:6 Sectional view of a self-adjusting device for
automatic brake shoe-to-drum clearance take-up (500
Sedan)
Key to Fig 1 0 : 6 1 Pin 2 Friction washers 3 Load spring
4 Bushing 5 Shoe 6 Self-adjustment slot 7 Stud
2 Make a note of the location of the shoe return springs
and gently ease t h e shoes away from the backplate
(see FIG 10:4)
3 Disconnect the hydraulic line from the rear of t h e
wheel cylinder and also the shoe operating lever return
spring, the pin, washer and clevis from the lever so
releasing the handbrake inner operating cable.
4 Remove the t w o cylinder retaining bolts and lift away
the hydraulic cylinder.
106
Brake shoe linings:
Refer t o Section 10:3.
Brake drums:
Refer to Section 10:3.
Reassembly of rear brakes:
This is the reverse procedure to dismantling. Ensure
that the pull-off springs are correctly fitted to the holes
in the webs of the brake shoes and that the shoes
register in the slotted ends of the pistons and the side
mounting plate.
Carefully retract the position of the brake shoes and
ease t h e d r u m towards the hub ensuring that the four
bolt holes line up correctly. Replace the four bolts
together with their spring washers, reconnect the hand
brake cable. Refit road wheel and wheel trim.
10:5 Master cylinder
Operation:
Hydraulic fluid is admitted to the master cylinder
through hole 8 (see FIG 10:7), it seeps through the gap
between the valve carrier ring 17 and the master cylinder
dowel and flows through the valve carrier ring holes 15
so reaching the hydraulic lines, therefore filling the
system w i t h fluid. When the brake pedal is depressed the
plunger is moved forwards by the pushrod 12. This
forward action of the plunger 9 and valve carrier 17 brings
the valve 16 to rest against the valve front face. The
forward movement is continued so causing the valve ring
16 to pass over the compensation hole 5 and cutting off
communication with the fluid reservoirs. From this point
compression of the hydraulic fluid commences.
Hydraulic fluid acting on the front and inner faces of
the valve enables perfect valve sealing even under high
operation pressures. When the pressure reaches the fluid
in the wheel cylinders (see FIG 10:8) , it forces the
plungers 3 apart and through the plungers stems so
operating the brake shoes.
After releasing the brake pedal, the combined action
of the brake shoe and master cylinder plunger return
springs sends the fluid back to the master cylinder and
all parts resume their original position. The connection
between the hydraulic
system and the reservoir is
restored.
As there are no conventional valves fitted in the master
cylinder and the communication orifice between the
system a n d the reservoir is amply dimensioned the
bleeding operation is very straightforward.
Master cylinder removal:
1 Disconnect the stoplight cables from the pressure
operated switch.
2 Using a tapered w o o d plug of suitable size blank t h e
hole in the brake f l u i d reservoir.
3 Screw out the four front and rear cylinder brake fluid
delivery line connections at the master cylinder.
4 Remove the t w o master cylinder retaining nuts and
spring washers and carefully ease the hydraulic
cylinder from the body.
Page 100 of 128
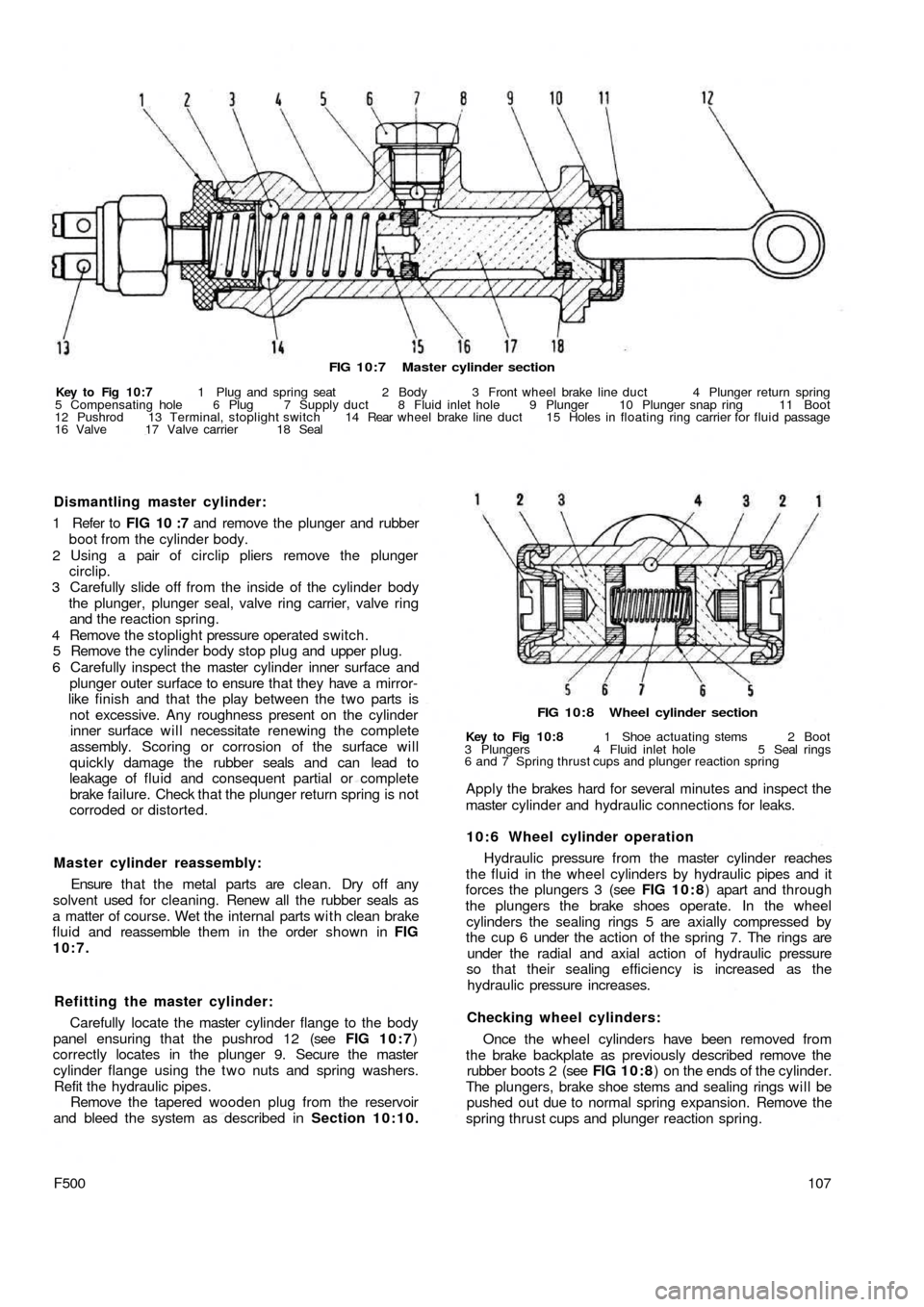
FIG 10:7 Master cylinder section
Key to Fig 10:7 1 Plug and spring seat 2 Body 3 Front wheel brake line duct 4 Plunger return spring
5 Compensating hole 6 Plug 7 Supply duct 8 Fluid inlet hole 9 Plunger 10 Plunger snap ring 11 Boot
12 Pushrod 13 Terminal, stoplight switch 14 Rear wheel brake line duct 15 Holes in floating ring carrier for fluid passage
16 Valve 17 Valve carrier 18 Seal
FIG 10:8 Wheel cylinder section
Key to Fig 10:8 1 Shoe actuating stems 2 Boot
3 Plungers 4 Fluid inlet hole 5 Seal rings
6 and 7 Spring thrust cups and plunger reaction spring
Apply the brakes hard for several minutes and inspect the
master cylinder and hydraulic connections for leaks.
10:6 Wheel cylinder operation
Hydraulic pressure from the master cylinder reaches
the fluid in the wheel cylinders by hydraulic pipes and it
forces the plungers 3 (see FIG 1 0 : 8) apart and through
the plungers the brake shoes operate. In the wheel
cylinders the sealing rings 5 are axially compressed by
the cup 6 under the action of the spring 7. The rings are
under the radial and axial action of hydraulic pressure
so that their sealing efficiency is increased as the
hydraulic pressure increases.
Checking wheel cylinders:
Once the wheel cylinders have been removed from
the brake backplate as previously described remove the
rubber boots 2 (see FIG 10:8) on the ends of the cylinder.
The plungers, brake shoe stems and sealing rings will be
pushed out due to normal spring expansion. Remove the
spring thrust cups and plunger reaction spring.
107F500
Master cylinder reassembly:
Ensure that the metal parts are clean. Dry off any
solvent used for cleaning. Renew all the rubber seals as
a matter of course. Wet the internal parts w i t h clean brake
fluid and reassemble them in the order shown in FIG
10:7.
Refitting the master cylinder:
Carefully locate the master cylinder flange to the body
panel ensuring that the pushrod 12 (see FIG 10:7)
correctly locates in the plunger 9. Secure the master
cylinder flange using the t w o nuts and spring washers.
Refit the hydraulic pipes.
Remove the tapered wooden plug from the reservoir
and bleed the system as described in Section 10:10. Dismantling master cylinder:
1 Refer to FIG 10 :7 and remove the plunger and rubber
boot from the cylinder body.
2 Using a pair of circlip pliers remove the plunger
circlip.
3 Carefully slide off from the inside of the cylinder body
the plunger, plunger seal, valve ring carrier, valve ring
and the reaction spring.
4 Remove the stoplight pressure operated switch.
5 Remove the cylinder body stop plug and upper plug.
6 Carefully inspect the master cylinder inner surface and
plunger outer surface to ensure that they have a mirror-
like finish and that the play between the two parts is
not excessive. Any roughness present on the cylinder
inner surface will necessitate renewing the complete
assembly. Scoring or corrosion of the surface will
quickly damage the rubber seals and can lead to
leakage of fluid and consequent partial or complete
brake failure. Check that the plunger return spring is not
corroded or distorted.
Page 101 of 128
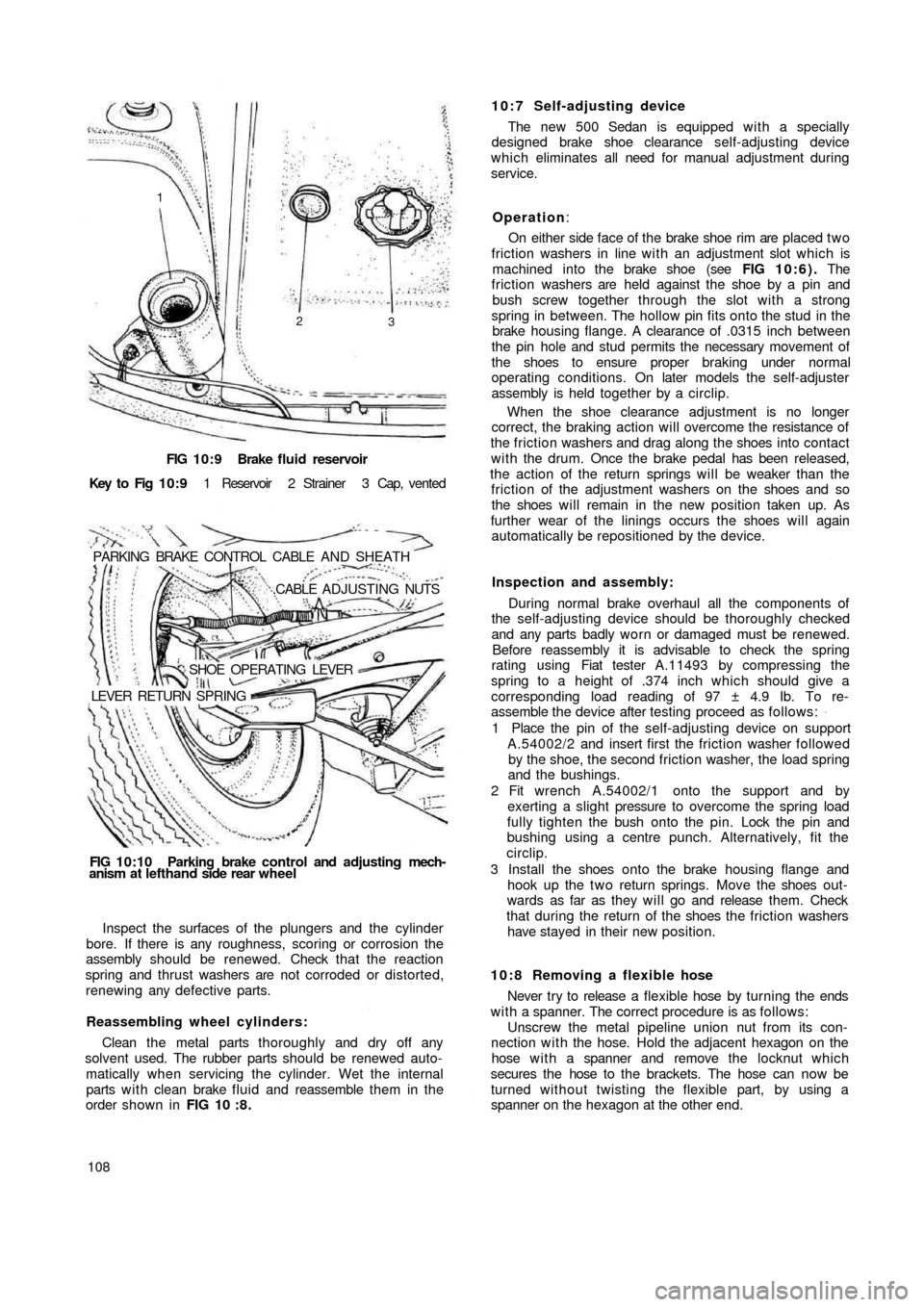
FIG 10:9 Brake fluid reservoir
Key to Fig 1 0 : 9 1 Reservoir 2 Strainer 3 Cap, vented
PARKING BRAKE CONTROL CABLE AND SHEATH
.CABLE ADJUSTING NUTS
SHOE OPERATING LEVER
LEVER RETURN SPRING
FIG 10:10 Parking brake control and adjusting mech-
anism at lefthand side rear wheel
Inspect the surfaces of the plungers and the cylinder
bore. If there is any roughness, scoring or corrosion the
assembly should be renewed. Check that the reaction
spring and thrust washers are not corroded or distorted,
renewing any defective parts.
Reassembling wheel cylinders:
Clean the metal parts thoroughly and dry off any
solvent used. The rubber parts should be renewed auto-
matically when servicing the cylinder. Wet the internal
parts w i t h clean brake f l u i d and reassemble them in the
order shown in FIG 10 : 8 .
10810:7 Self-adjusting device
The new 500 Sedan is equipped with a specially
designed brake shoe clearance self-adjusting device
which eliminates all need for manual adjustment during
service.
Operation:
On either side face of the brake shoe rim are placed t w o
friction washers in line with an adjustment slot which is
machined into the brake shoe (see FIG 10:6). The
friction washers are held against the shoe by a pin and
bush screw together through the slot with a strong
spring in between. The hollow pin fits onto the stud in the
brake housing flange. A clearance of .0315 inch between
the pin hole and stud permits the necessary movement of
the shoes to ensure proper braking under normal
operating conditions. On later models the self-adjuster
assembly is held together by a circlip.
When the shoe clearance adjustment is no longer
correct, the braking action will overcome the resistance of
the friction washers and drag along the shoes into contact
with the drum. Once the brake pedal has been released,
the action of the return springs will be weaker than the
friction of the adjustment washers on the shoes and so
the shoes will remain in the new position taken up. As
further wear of the linings occurs the shoes will again
automatically be repositioned by the device.
Inspection and assembly:
During normal brake overhaul all the components of
the self-adjusting device should be thoroughly checked
and any parts badly worn or damaged must be renewed.
Before reassembly it is advisable to check the spring
rating using Fiat tester A.11493 by
compressing the
spring to a height of .374 inch which should give a
corresponding load reading of 97 ± 4.9 Ib. To re-
assemble the device after testing proceed as follows:
1 Place the pin of the self-adjusting device on support
A.54002/2 and insert first the friction washer followed
by the shoe, the second friction washer, the load spring
and the bushings.
2 Fit wrench A.54002/1 onto the support and by
exerting a slight pressure to overcome the spring load
fully tighten the bush onto the pin. Lock the pin and
bushing using a centre punch. Alternatively, fit the
circlip.
3 Install the shoes onto the brake housing flange and
hook up the t w o return springs. Move the shoes out-
wards as far as they will go and release them. Check
that during the return of the shoes the friction washers
have stayed in their new position.
10:8 Removing a flexible hose
Never try to release a flexible hose by turning the ends
w i t h a spanner. The correct procedure is as follows:
Unscrew the metal pipeline union nut from its con-
nection with the hose. Hold the adjacent hexagon on the
hose w i t h a spanner and remove the locknut which
secures the hose to the brackets. The hose can now be
turned without twisting the flexible part, by using a
spanner on the hexagon at the other end.
1
2
3