compression ratio FIAT 500 1973 1.G Workshop Manual
[x] Cancel search | Manufacturer: FIAT, Model Year: 1973, Model line: 500, Model: FIAT 500 1973 1.GPages: 128, PDF Size: 9.01 MB
Page 26 of 128
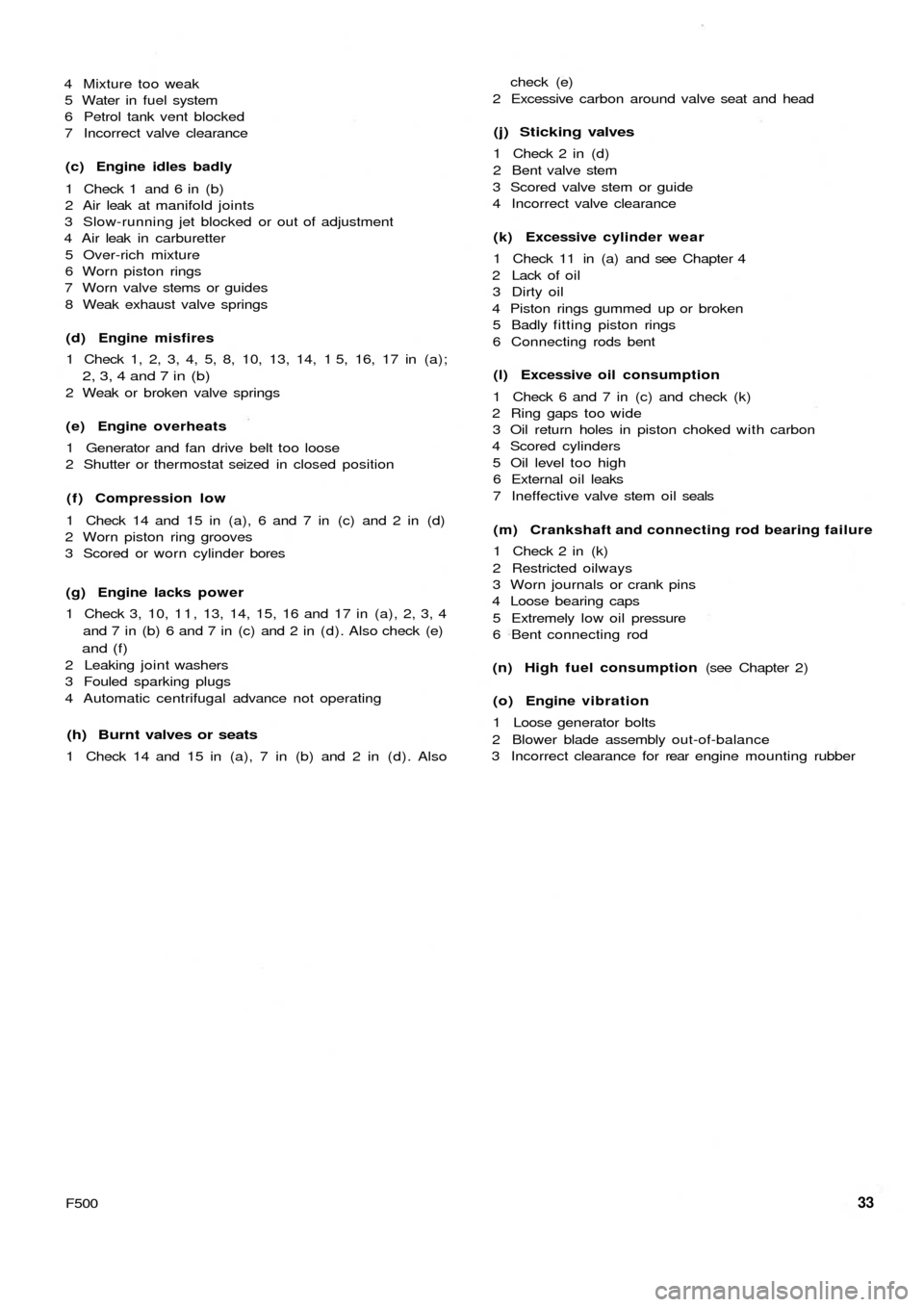
4 Mixture too weak
5 Water in fuel system
6 Petrol tank vent blocked
7 Incorrect valve clearance
(c) Engine idles badly
1 Check 1 and 6 in (b)
2 Air leak at manifold joints
3 Slow-running jet blocked or out of adjustment
4 Air leak in carburetter
5 Over-rich mixture
6 Worn piston rings
7 Worn valve stems or guides
8 Weak exhaust valve springs
(d) Engine misfires
1 Check 1, 2, 3, 4, 5, 8, 10, 13, 14, 1 5, 16, 17 in (a);
2, 3, 4 and 7 in (b)
2 Weak or broken valve springs
(e) Engine overheats
1 Generator and fan drive belt too loose
2 Shutter or thermostat seized in closed position
(f) Compression low
1 Check 14 and 15 in (a), 6 and 7 in (c) and 2 in (d)
2 Worn piston ring grooves
3 Scored or worn cylinder bores
(g) Engine lacks power
1 Check 3, 10, 1 1 , 13, 14, 15, 16 and 17 in (a), 2, 3, 4
and 7 in (b) 6 and 7 in (c) and 2 in (d). Also check (e)
and (f)
2 Leaking joint washers
3 Fouled sparking plugs
4 Automatic centrifugal advance not operating
(h) Burnt valves or seats
1 Check 14 and 15 in (a), 7 in (b) and 2 in (d). Alsocheck (e)
2 Excessive carbon around valve seat and head
(j) Sticking valves
1 Check 2 in (d)
2 Bent valve stem
3 Scored valve stem or guide
4 Incorrect valve clearance
(k) Excessive cylinder wear
1 Check 11 in (a) and see Chapter 4
2 Lack of oil
3 Dirty oil
4 Piston rings gummed up or broken
5 Badly fitting piston rings
6 Connecting rods bent
(l) Excessive oil consumption
1 Check 6 and 7 in (c) and check (k)
2 Ring gaps too wide
3 Oil return holes in piston choked with carbon
4 Scored cylinders
5 Oil level too high
6 External oil leaks
7 Ineffective valve stem oil seals
(m) Crankshaft and connecting rod bearing failure
1 Check 2 in (k)
2 Restricted oilways
3 Worn journals or crank pins
4 Loose bearing caps
5 Extremely low oil pressure
6 Bent connecting rod
(n) High fuel consumption (see Chapter 2)
(o) Engine vibration
1 Loose generator bolts
2 Blower blade assembly out-of-balance
3 Incorrect clearance for rear engine mounting rubber
F50033
Page 85 of 128
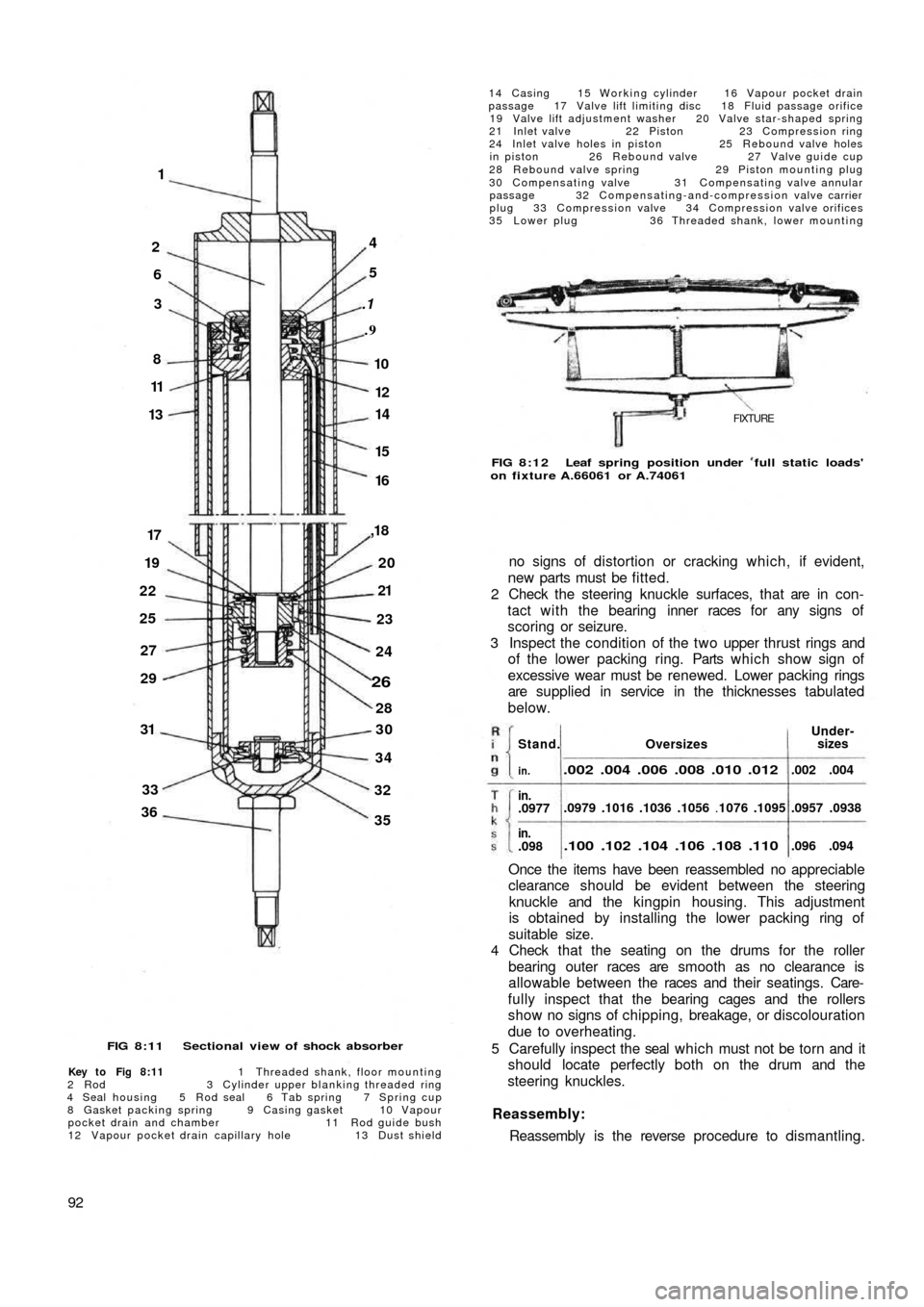
1
2
6
3
8
11
13
17
19
22
25
27
29
31
33
36
35 323430 28
26
24232120 ,1816 15 14 12 10 .9 .15 4
FIG 8:11 Sectional view of shock absorber
Key to Fig 8:11 1 Threaded shank, floor mounting
2 R o d 3 Cylinder upper blanking threaded ring
4 Seal housing 5 Rod seal 6 Tab spring 7 Spring cup
8 Gasket packing spring 9 Casing gasket 10 Vapour
pocket drain and chamber 11 Rod guide bush
12 Vapour pocket drain capillary hole 13 Dust shield
92
14 Casing 15 Working cylinder 16 Vapour pocket drain
passage 17 Valve lift limiting disc 18 Fluid passage orifice
19 Valve lift adjustment washer 20 Valve star-shaped spring
21 Inlet valve 22 Piston 23 Compression ring
24 Inlet valve holes in piston 25 Rebound valve holes
in piston 26 Rebound valve 27 Valve guide cup
28 Rebound valve spring 29 Piston mounting plug
30 Compensating valve 31 Compensating valve annular
passage 32 Compensating-and-compression valve carrier
plug 33 Compression valve 34 Compression valve orifices
35 Lower plug 36 Threaded shank, lower mounting
FIXTURE
FIG 8:12 Leaf spring position under full static loads'
on fixture A.66061 or A.74061
no signs of distortion or cracking which, if evident,
new parts must be fitted.
2 Check the steering knuckle surfaces, that are in con-
tact with the bearing inner races for any signs of
scoring or seizure.
3 Inspect the condition of the two upper thrust rings and
of the lower packing ring. Parts which show sign of
excessive wear must be renewed. Lower packing rings
are supplied in service in the thicknesses tabulated
below.
Once the items have been reassembled no appreciable
clearance should be evident between the steering
knuckle and the kingpin housing. This adjustment
is obtained by installing the lower packing ring of
suitable size.
4 Check that the seating on the drums for the roller
bearing outer races are smooth as no clearance is
allowable between the races and their seatings. Care-
fully inspect that the bearing cages and the rollers
show no signs of chipping, breakage, or discolouration
due to overheating.
5 Carefully inspect the seal which must not be torn and it
should locate perfectly both on the drum and the
steering knuckles.
Reassembly:
Reassembly is the reverse procedure to dismantling.
OversizesUnder-
sizes
.002 .004 .006 .008 .010 .012
.0979 .1016 .1036 .1056 .1076 .1095
.100 .102 .104 .106 .108 .110
.002 .004
.0957 .0938
.096 .094
Stand.
in.
in..0977
in..098
Page 86 of 128
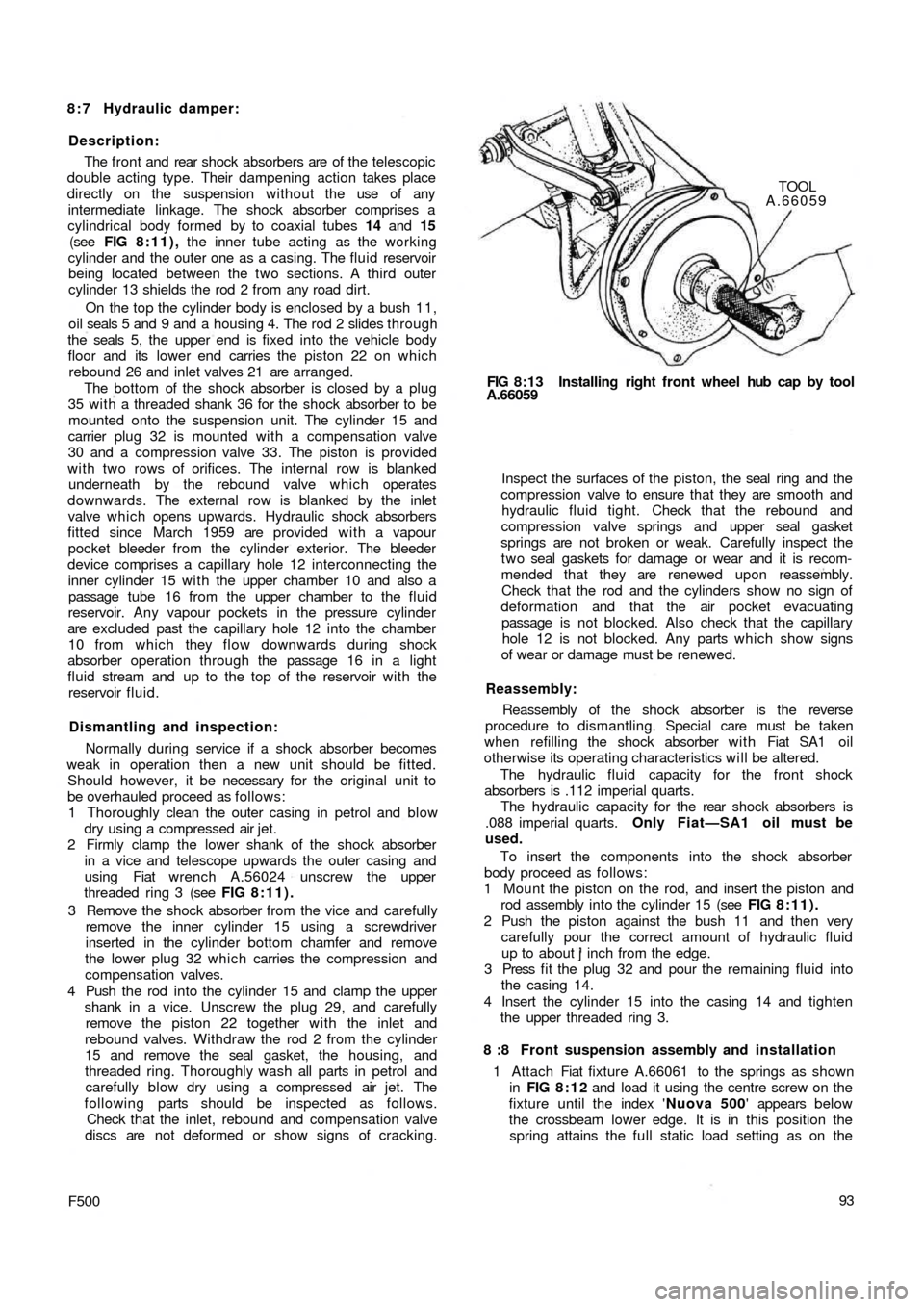
8 : 7 Hydraulic damper:
Description:
The front and rear shock absorbers are of the telescopic
double acting type. Their dampening action takes place
directly on the suspension without the use of any
intermediate linkage. The shock absorber comprises a
cylindrical body formed by to coaxial tubes 14 and 15
(see FIG 8:11), the inner tube acting as the working
cylinder and the outer one as a casing. The fluid reservoir
being located between the two sections. A third outer
cylinder 13 shields the rod 2 from any road dirt.
On the top the cylinder body is enclosed by a bush 1 1 ,
oil seals 5 and 9 and a housing 4. The rod 2 slides through
the seals 5, the upper end is fixed into the vehicle body
floor and its lower end carries the piston 22 on which
rebound 26 and inlet valves 21 are arranged.
The bottom of the shock absorber is closed by a plug
35 with a threaded shank 36 for the shock absorber to be
mounted onto the suspension unit. The cylinder 15 and
carrier plug 32 is mounted with a compensation valve
30 and a compression valve 33. The piston is provided
with two rows of orifices. The internal row is blanked
underneath by the rebound valve which operates
downwards. The external row is blanked by the inlet
valve which opens upwards. Hydraulic shock absorbers
fitted since March 1959 are provided w i t h a vapour
pocket bleeder from the cylinder exterior. The bleeder
device comprises a capillary
hole 12 interconnecting the
inner cylinder 15 with the upper chamber 10 and also a
passage tube 16 from the upper chamber to the fluid
reservoir. Any vapour pockets in the pressure cylinder
are excluded past the capillary hole 12 into the chamber
10 from which they flow downwards during shock
absorber operation through the passage 16 in a light
fluid stream and up to the top of the reservoir with the
reservoir fluid.
Dismantling and inspection:
Normally during service if a shock absorber becomes
weak in operation then a new unit should be fitted.
Should however, it be necessary for the original unit to
be overhauled proceed as follows:
1 Thoroughly clean the outer casing in petrol and blow
dry using a compressed air jet.
2 Firmly clamp the lower shank of the shock absorber
in a vice and telescope upwards the outer casing and
using Fiat wrench A.56024 unscrew the upper
threaded ring 3 (see FIG 8:11).
3 Remove the shock absorber from the vice and carefully
remove the inner cylinder 15 using a screwdriver
inserted in the cylinder bottom chamfer and remove
the lower plug 32 which carries the compression and
compensation valves.
4 Push the rod i n t o the cylinder 15 and clamp the upper
shank in a vice. Unscrew the plug 29, and carefully
remove the piston 22 together with the inlet and
rebound valves. Withdraw the rod 2 from the cylinder
15 and remove the seal gasket, the housing, and
threaded ring. Thoroughly wash all parts in petrol and
carefully blow dry using a c
ompressed air jet. The
following parts should be inspected as follows.
Check that the inlet, rebound and compensation valve
discs are not deformed or show signs of cracking.
F50093 Inspect the surfaces of the piston, the seal ring and the
compression valve to ensure that they are smooth and
hydraulic fluid tight. Check that the rebound and
compression valve springs and upper seal gasket
springs are not broken or weak. Carefully inspect the
t w o seal gaskets for damage or wear and it is recom-
mended that they are renewed upon reassembly.
Check that the rod and the cylinders show no sign of
deformation and that the air pocket evacuating
passage is not blocked. Also check that the capillary
hole 12 is not blocked. Any parts which show signs
of wear or damage must be renewed.
Reassembly:
Reassembly of the shock absorber is the reverse
procedure to dismantling. Special care must be taken
when refilling the shock absorber w i t h Fiat SA1 oil
otherwise its operating characteristics will be altered.
The hydraulic fluid capacity for the front shock
absorbers is .112 imperial quarts.
The hydraulic capacity for the rear shock absorbers is
.088 imperial quarts. Only Fiat—SA1 oil must be
used.
To insert the components into the shock absorber
body proceed as follows:
1 Mount the piston on the rod, and insert the piston and
rod assembly into the cylinder 15 (see FIG 8:11).
2 Push the piston against the bush 11 and then very
carefully pour the correct amount of hydraulic fluid
up to about j inch from the edge.
3 Press f i t t h e plug 32 and pour the remaining fluid into
the casing 14.
4 Insert the cylinder 15 into the casing 14 and tighten
the upper threaded ring 3.
8 :8 Front suspension assembly and installation
1 Attach Fiat fixture A.66061 to the springs as shown
in FIG 8:12 and load it using the centre screw on the
fixture until the index 'Nuova 500' appears below
the crossbeam lower edge. It is in this position the
spring attains the full static load setting as on the FIG 8:13 Installing right front wheel hub cap by tool
A.66059TOOL
A.66059
Page 99 of 128
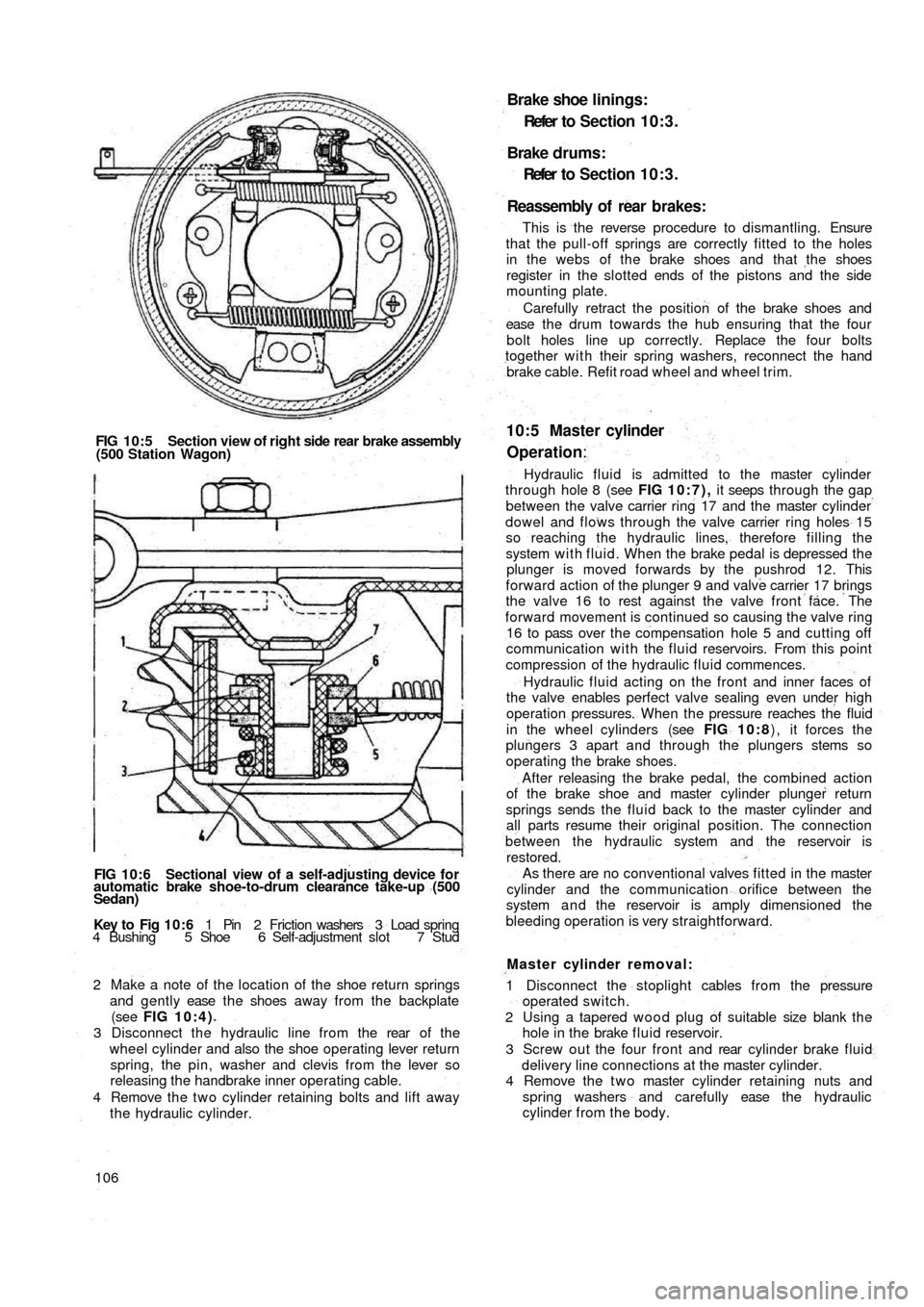
FIG 10:5 Section view of right side rear brake assembly
(500 Station Wagon)
FIG 10:6 Sectional view of a self-adjusting device for
automatic brake shoe-to-drum clearance take-up (500
Sedan)
Key to Fig 1 0 : 6 1 Pin 2 Friction washers 3 Load spring
4 Bushing 5 Shoe 6 Self-adjustment slot 7 Stud
2 Make a note of the location of the shoe return springs
and gently ease t h e shoes away from the backplate
(see FIG 10:4)
3 Disconnect the hydraulic line from the rear of t h e
wheel cylinder and also the shoe operating lever return
spring, the pin, washer and clevis from the lever so
releasing the handbrake inner operating cable.
4 Remove the t w o cylinder retaining bolts and lift away
the hydraulic cylinder.
106
Brake shoe linings:
Refer t o Section 10:3.
Brake drums:
Refer to Section 10:3.
Reassembly of rear brakes:
This is the reverse procedure to dismantling. Ensure
that the pull-off springs are correctly fitted to the holes
in the webs of the brake shoes and that the shoes
register in the slotted ends of the pistons and the side
mounting plate.
Carefully retract the position of the brake shoes and
ease t h e d r u m towards the hub ensuring that the four
bolt holes line up correctly. Replace the four bolts
together with their spring washers, reconnect the hand
brake cable. Refit road wheel and wheel trim.
10:5 Master cylinder
Operation:
Hydraulic fluid is admitted to the master cylinder
through hole 8 (see FIG 10:7), it seeps through the gap
between the valve carrier ring 17 and the master cylinder
dowel and flows through the valve carrier ring holes 15
so reaching the hydraulic lines, therefore filling the
system w i t h fluid. When the brake pedal is depressed the
plunger is moved forwards by the pushrod 12. This
forward action of the plunger 9 and valve carrier 17 brings
the valve 16 to rest against the valve front face. The
forward movement is continued so causing the valve ring
16 to pass over the compensation hole 5 and cutting off
communication with the fluid reservoirs. From this point
compression of the hydraulic fluid commences.
Hydraulic fluid acting on the front and inner faces of
the valve enables perfect valve sealing even under high
operation pressures. When the pressure reaches the fluid
in the wheel cylinders (see FIG 10:8) , it forces the
plungers 3 apart and through the plungers stems so
operating the brake shoes.
After releasing the brake pedal, the combined action
of the brake shoe and master cylinder plunger return
springs sends the fluid back to the master cylinder and
all parts resume their original position. The connection
between the hydraulic
system and the reservoir is
restored.
As there are no conventional valves fitted in the master
cylinder and the communication orifice between the
system a n d the reservoir is amply dimensioned the
bleeding operation is very straightforward.
Master cylinder removal:
1 Disconnect the stoplight cables from the pressure
operated switch.
2 Using a tapered w o o d plug of suitable size blank t h e
hole in the brake f l u i d reservoir.
3 Screw out the four front and rear cylinder brake fluid
delivery line connections at the master cylinder.
4 Remove the t w o master cylinder retaining nuts and
spring washers and carefully ease the hydraulic
cylinder from the body.