sensor FIAT PUNTO 1995 176 / 1.G Service Manual
[x] Cancel search | Manufacturer: FIAT, Model Year: 1995, Model line: PUNTO, Model: FIAT PUNTO 1995 176 / 1.GPages: 225, PDF Size: 18.54 MB
Page 164 of 225
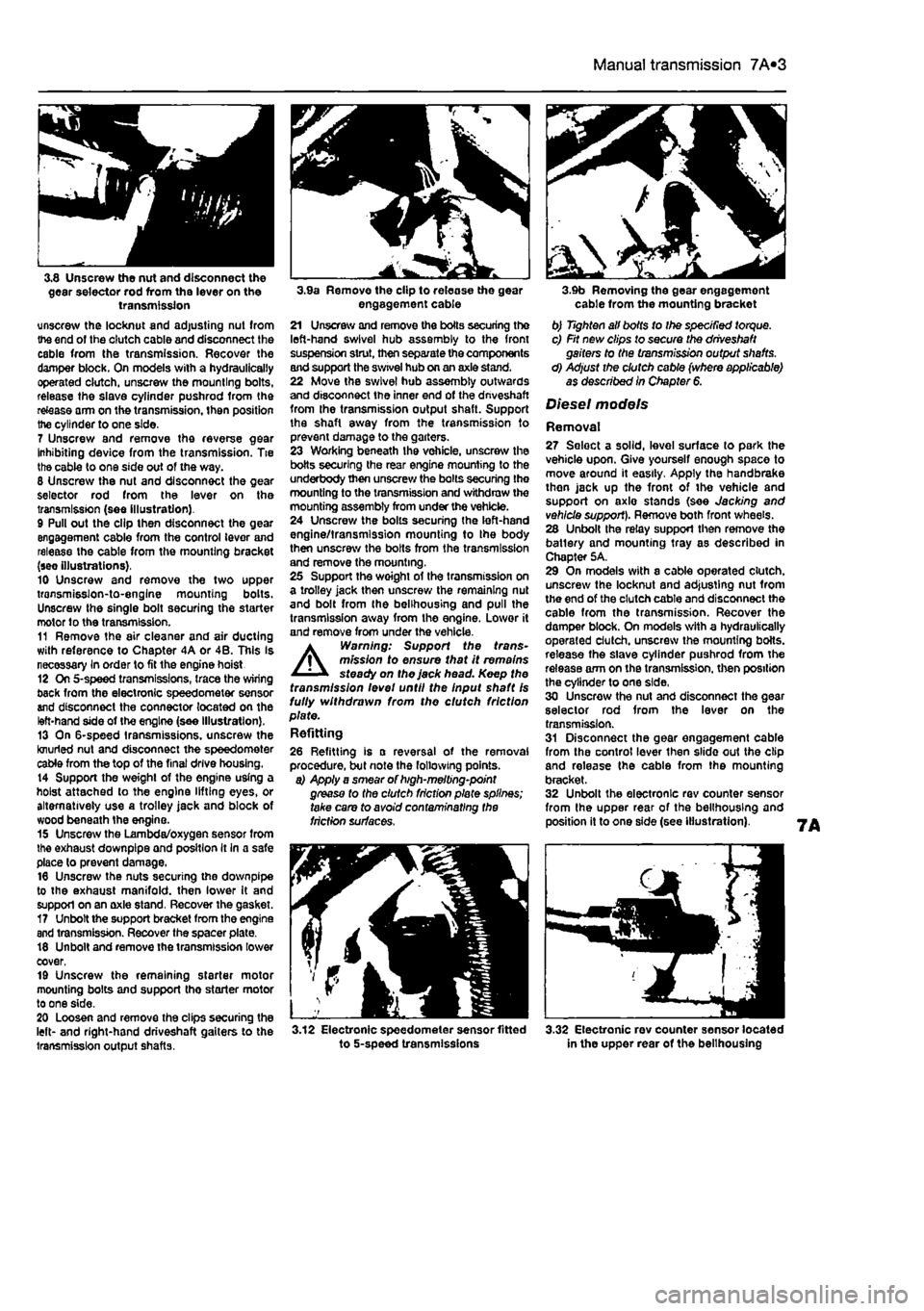
Manual transmission 7A*3
3,8 Unscrew the nut and disconnect the gear selector rod from the lever on the transmission unscrew the locknut and adjusting nut from the end of the clutch cable and disconnect the cable from the transmission. Recover the damper block. On models with a hydraulically operated clutch, unscrew the mounting bolts, release the slave cylinder pushrod from the re&ase arm on the transmission, then position the cylinder to one side.
7 Unscrew and remove the reverse gear Inhibiting device from the transmission. Tie the cable to one side out of the way. 8 Unscrew the nut and disconnect the gear selector rod from the lever on the transmission (see illustration). 9 Pull out the clip then disconnect the gear engagement cable from the control lever and release the cable from the mounting bracket (see illustrations). 10 Unscrew and remove the two upper transmisslon-to-englne mounting bolts. Unscrew the single bolt securing the starter motor to the transmission. 11 Remove the air cleaner and air ducting with reference to Chapter 4A or 4B. This Is necessary In order to fit the engine hoist 12 On 5-speed transmissions, trace the wiring back from the electronic speedometer sensor and disconnect the connector located on the left-hand side of the engine (see illustration). 13 On 6-speed transmissions, unscrew the knurled nut and disconnect the speedometer cable from the top of the final drive housing. 14 Support the weight of the engine using a hoist attached to the engine lifting eyes, or alternatively use a trolley jack and block of wood beneath Ihe engine. 15 Unscrew the Lambda/oxygen sensor from the exhaust downpipe and position It In a safe place to prevent damage. 16 Unscrew the nuts securing the downpipe to the exhaust manifold, then lower It and support on an axle stand. Recover the gasket. 17 Unbolt the support bracket from the engine and transmission. Recover the spacer plate. 18 Unbolt and remove the transmission lower cover, 19 Unscrew the remaining starter motor mounting bolts and support tho starter motor to one side. 20 Loosen and remove the clips securing the left- and right-hand driveshaft gaiters to the transmission output shafts.
3.9a Remove the clip to release the gear engagement cable 21 Unscrew and remove the boils securing the left-hand swivel hub assembly to the front suspension strut, then separate the components and support the swivel hub on an axle stand. 22 Move the swivel hub assembly outwards and disconnect the inner end of the dnveshaft from the transmission output shaft. Support the shaft away from the transmission to prevent damage to the garters. 23 Working beneath the vehicle, unscrew the botts securing the rear engine mounting to the underbody then unscrew the bolts securing the mounting to the transmission and withdraw the mounting assembly from under the vehicle. 24 Unscrew the bolts securing the left-hand engine/transmission mounting to Ihe body then unscrew the bolts from the transmission and remove the mounting. 25 Support the woight of the transmission on a trolley jack then unscrew the remaining nut and bolt from the belihousing and pull the transmission away from the engine. Lower it and remove from under the vehicle. A Warning: Support the trans-mission to ensure that it remains steady on the jack head. Keep the transmission levet until the Input shaft Is fully withdrawn from the clutch friction plate. Refitting
26 Refitting is a reversal of the removal procedure, but note the following points. a) Apply a smear of high-melting-point grease to the clutch friction plate splines; take care to avoid contaminating the friction surfaces.
3.12 Electronic speedometer sensor fitted to 5-speed transmissions
3.9b Removing the gear engagement cable from the mounting bracket b) Tighten all bolts to Ihe specified torque. c) Fit new clips to secure the driveshaft gaiters to the transmission output shafts. d) Adjust the clutch cable (where applicable) as described In Chapter 6.
Diesel models
Removal 27 Seloct a solid, level surface to park the vehicle upon. Give yourself enough space to move around it easily. Apply the handbrake then jack up the front of tho vehicle and support on axlo stands (see Jacking and vehicle support). Remove both front wheels. 28 Unbolt the relay support then remove the batlery and mounting tray as described in Chapter 5A. 29 On models with a cable operated clutch, unscrew the locknut and adjusting nut from the end of the clutch cable and disconnect the cable from the transmission. Recover the damper block. On models with a hydraulically operated clutch, unscrew the mounting botts. release the slave cylinder pushrod from the release arm on the transmission, then position the cylinder to one side, 30 Unscrew the nut and disconnect the gear selector rod from the lever on the transmission. 31 Disconnect the gear engagement cable from the control lever then slide out the clip and release the cable from the mounting bracket. 32 Unbolt the electronic rev counter sensor from the upper rear of the belihousing and position it to one side (see illustration).
3.32 Electronic rev counter sensor located in the upper rear of the belihousing
Page 165 of 225
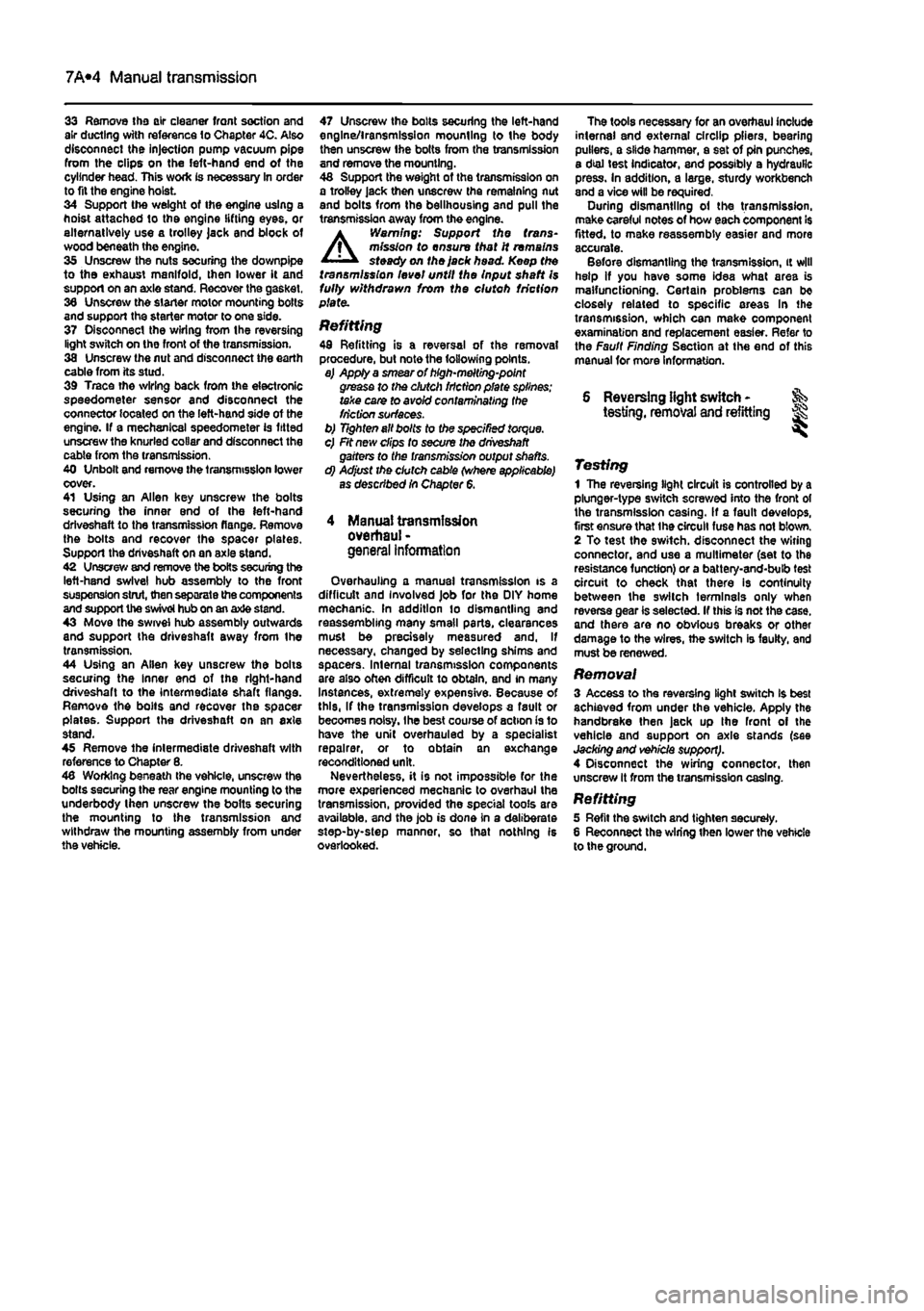
7A«4 Manual transmission
33 Remove lha air cleaner front section and air ducting with reference to Chapter 4C. Also disconnect the injection pump vacuum pipe from the clips on the left-hand end of the cylinder head. This work is necessary in order to fit the engine hoist 34 Support the weight of the engine using a hoist attached to the engine lifting eyes, or alternatively use a trolley Jack and block of wood beneath the engine. 35 Unscrew the nuts securing the downpipe to the exhaust manifold, then lower it and support on an axle stand. Recover the gasket. 36 Unscrew the starter motor mounting bolts and support the starter motor to one side. 37 Disconnect the wiring from the reversing light switch on the front of the transmission. 38 Unscrew the nut and disconnect the earth cable from its stud. 39 Trace the wiring back from the electronic speedometer sensor and disconnect the connector located on the left-hand side ot the engine. If a mechanical speedometer Is fitted unscrew the knurled collar and disconnect the cabte from the transmission. 40 Unbolt and remove the transmission lower cover. 41 Using an Allen key unscrew the bolts securing the inner end of the left-hand driveshaft to the transmission flange. Remove the bolts and recover the spacer plates. Support the driveshaft on an axle stand. 42 Unscrew and remove the bolts securing the left-hand swivel hub assembly to the front suspension strut, then separate the components and support the swivel hub on an axle stand. 43 Move the swrvel hub assembly outwards and support the driveshaft away from Ihe transmission. 44 Using an Allen key unscrew the bolts securing the Inner end of the right-hand driveshaft to the intermediate shaft flange. Remove the bolts and recover the spacer plates. Support the driveshaft on an axle stand. 45 Remove the intermediate driveshaft with reference to Chapter 8. 46 Working beneath the vehicle, unscrew the bolts securing the rear engine mounting to the underbody then unscrew the bolts securing the mounting to the transmission and withdraw the mounting assembly from under the vehicle.
47 Unscrew the bolts securing the left-hand engine/transmission mounting to the body then unscrew Ihe bolts from the transmission and remove the mounting. 48 Support the weight of the transmission on a trolley jack then unscrew the remaining nut and bolts from the bellhousing and pull the transmission away from the engine.
A
Warning: Support the trans-mission to ensure that It remains steady o/i the jack head. Keep the transmission level until the Input shaft
1$
fully withdrawn from the clutch friction plate.
Refitting 48 Refitting is a reversal of the removal procedure, but note the following points. a) Appiy a smear* of high-meiting-point grease to the clutch friction piate splines; take care to avoid contaminating the friction surfaces. b) Tighten all bolts to the specified torque. c) Fit new clips to secure the driveshaft gaiters to the transmission output shafts. d) Adjust the clutch cable (where applicable) as described In Chapter 6.
4 Manual transmission overhaul -general Infomtatlon
Overhauling a manual transmission is a difficult and Involved Job for the DIY home mechanic. In addition to dismantling and reassembling many small parts, clearances must be precisely measured and, if necessary, changed by selecting shims and spacers. Internal transmission components are also often difficult to obtain, and in many Instances, extremely expensive. Because of this, If the transmission develops a fault or becomes noisy. Ihe best course of action is to have the unit overhauled by a specialist repairer, or to obtain an exchange reconditioned unit. Nevertheless, it is not impossible for the more experienced mechanic to overhaul the transmission, provided the special tools are available, and the Job is done in a deliberate step-by-step manner, so that nothing is overlooked.
The tools necessary for an overhaul include internal and external clrclip pliers, bearing pullers, a slide hammer, a sat of pin punches, a dial test Indicator, and possibly a hydraulic press. In addition, a large, sturdy workbench 8od a vice will be required. During dismantling o1 the transmission, make careful notes of how each component
1$
fitted, to make reassembly easier and more accurate. Before dismantling the transmission, it will help if you have some idea what area is malfunctioning. Certain problems can be closely related to specific areas In the transmission, which can make component examination and replacement easier. Refer to the Fault Finding Section at the end of this manual for more Information.
5 Reversing light switch -testing, removal and refitting ||
Testing 1 The reversing light circuit is controlled by a plunger-type switch screwed into the front of the transmission casing. If a fault develops, first ensure that Ihe circuit fuse has not blown. 2 To test the switch, disconnect the wiring connector, and use a multimeter (set to the resistance function) or a battery-and-bulb test circuit to check that there is continuity between the switch terminals only when reverse gear is selected. If this is not the case, and there are no obvious breaks or other damage to the wires, the switch is faulty, and must be renewed.
Removal 3 Access to the reversing light switch Is best achieved from under the vehicle. Apply the handbrake then jack up Ihe front of the vehicle and support on axle stands (see Jacking and vehicle support). 4 Disconnect the wiring connector, then unscrew It from the transmission casing.
Refitting 5 Refit the switch and tighten securely. 6 Reconnect the wiring then lower the vehicle to the ground.
Page 168 of 225
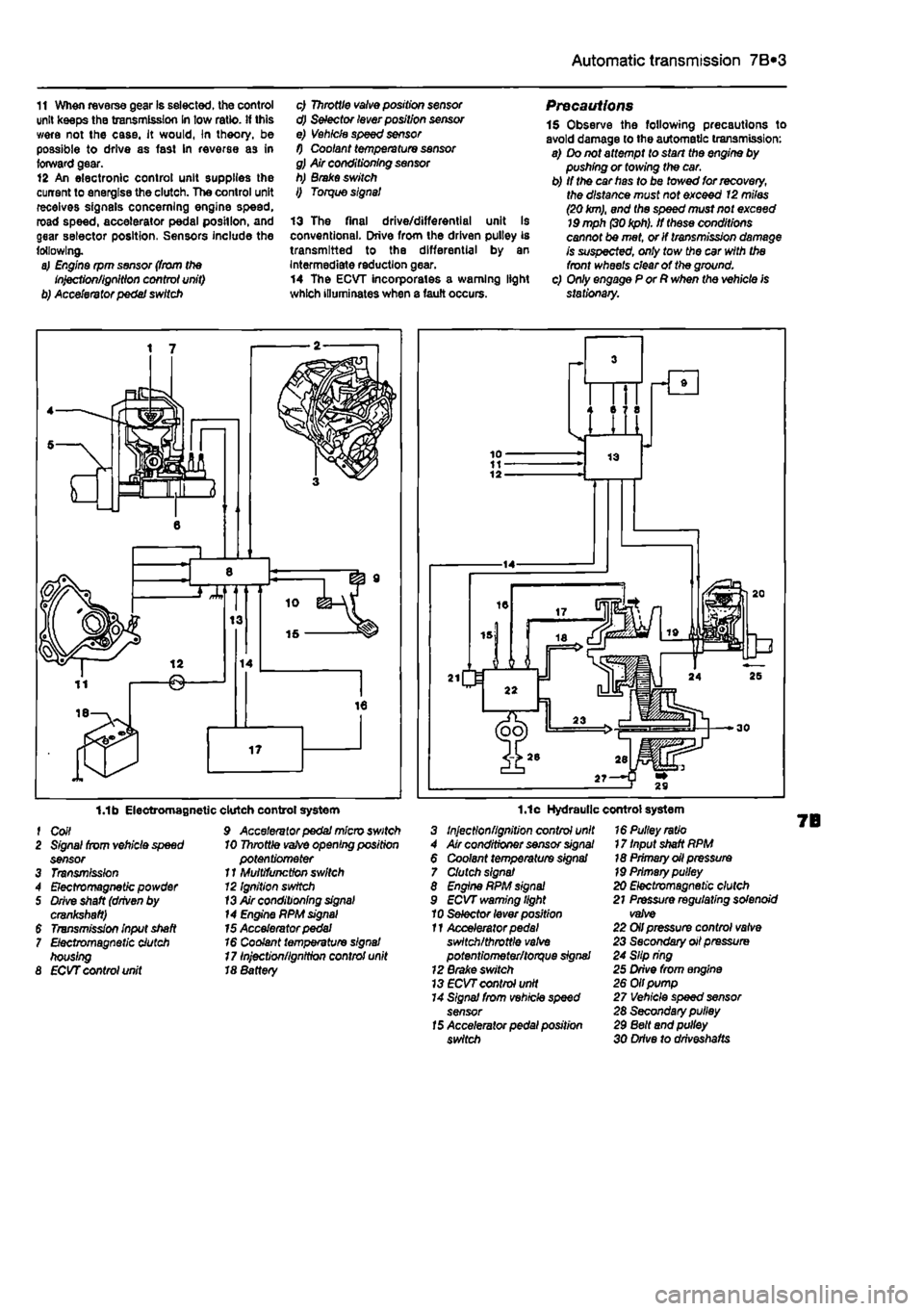
Automatic transmission 7B*3
11 When reverse gear Is selected, the control unit keeps the transmission In tow ratio, if this were not the case, it would, In theory, be possible to drive as fast In reverse as in forward gear. 12 An electronic control unit supplies the current to energise the clutch. The control unit receives signals concerning engine speed, road speed, accelerator pedal position, and gear selector position, Sensors include the following. a) Engine rpm sensor (from the Injection/ignition control unit) b) Accelerator pedal switch
c) Throttle valve position sensor d) Selector lever position sensor e) Vehicle speed sensor f) Coolant temperature sensor g) Air conditioning sensor h) Brake switch I) Torque signal
13 The final drive/differential unit Is conventional. Drive from the driven pulley is transmitted to the differential by an Intermediate reduction gear. 14 The ECVT incorporates a warning light which illuminates when a fault occurs.
Precautions 1$ Observe the following precautions to avoid damage to the automatic transmission: a) Do not attempt to start the engine by pushing or towing the car. b) If the car has to be towed for recovery, the distance must not exceed 12 miles (20
km),
and the speed must not exceed
19
mph
(30 kph).
If these conditions cannot be met, or If transmission damage is suspected, only tow the car with the front wheels clear of the ground. c) Only engage P or R when the vehicle is stationary.
1.1b Electromagnetic f Coil 2 Signal from vehicle speed sensor 3 Transmission 4 Electromagnetic powder 5 Drive shaft (driven by crankshaft) $ Transmission input shaft 7 Electromagnetic clutch housing 8 ECVT control unit
clutch control system 9 Accelerator pedal micro switch 10 Throttle
vafve
opening position potentiometer 11 Multifunction switch 12 Ignition switch
13
Air conditioning
signal
14 Engine PPM
signal
15 Accelerator pedal 16 Coolant temperature signal 17 Injection/ignition control unit 18 8attery
1.1c Hydraulic control system 3 Injection/ignition control unit 4 Air conditioner sensor
signal
6 Coolant temperature signal 7 Clutch signal 8 Engine RPM
signal
9 ECVT warning light 10 Selector lever position 11 Accelerator
pedal
switch/throttle
valve
potentiometer/torque signal 12 Brake switch 13
ECVT
control unit 14 Signal from vehicle speed sensor
15
Accelerator pedal position switch
16 Pulley ratio 17 Input shaft RPM 18 Primary oil pressure
19
Primary pulley 20 Electromagnetic clutch 21 Pressure regulating solenoid valve 22 Oil pressure control valve 23 Secondary oil pressure 24 Slip ring 25 Drive from engine 26 Oil pump 27 Vehicle speed sensor 28 Secondary pulley 29 Belt and pulley 30 Drive to drlveshafts
Page 169 of 225
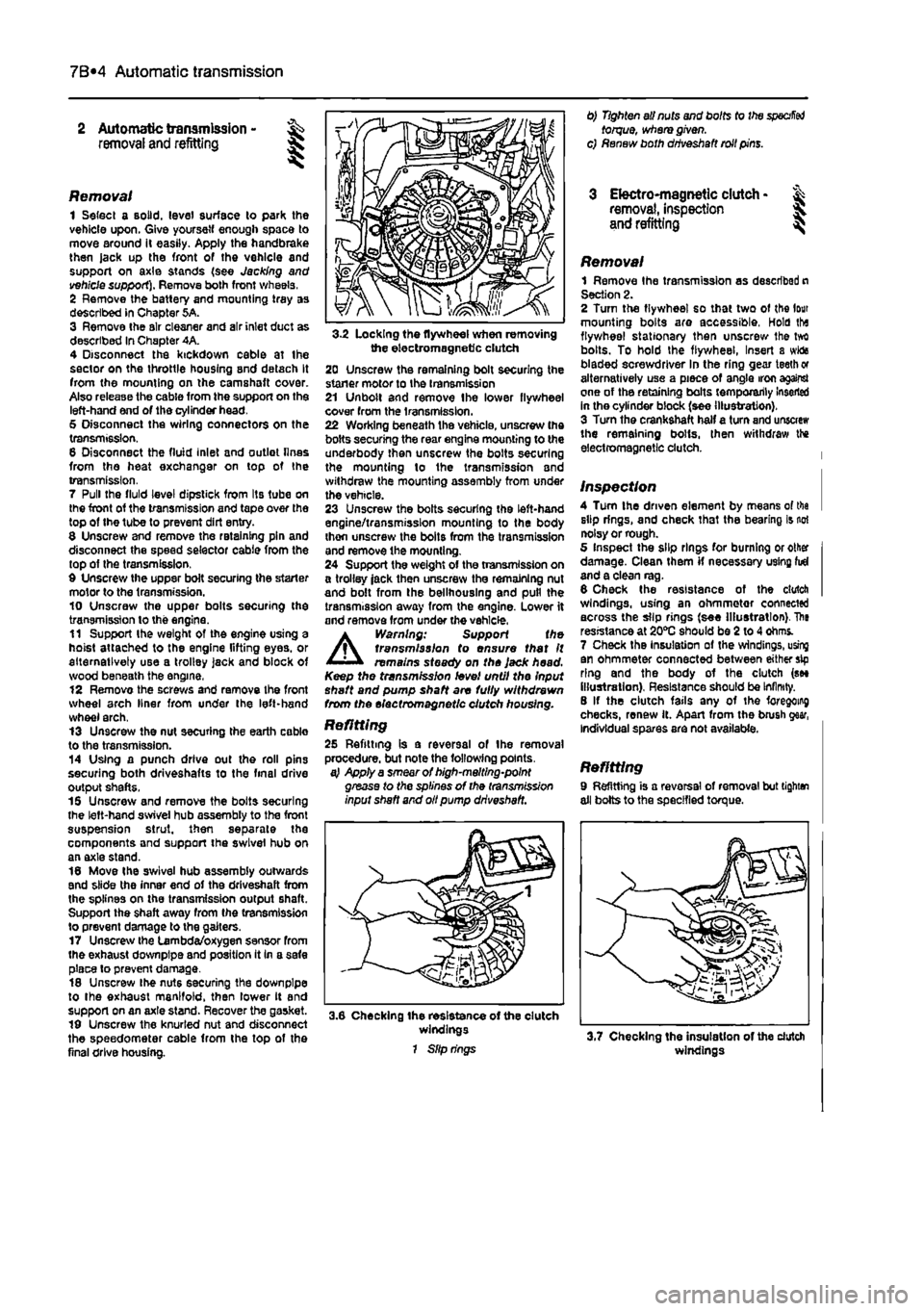
7B*4 Automatic transmission
2 Automatic transmission - ^ removal and refitting St
Removal 1 Select a solid, level surface to park the vehicle upon. Give yourself enough space to move around it easily. Apply the handbrake then jack up the front of the vehicle and support on axle stands (see Jacking and vehicle support). Remove both front wheels, 2 Remove the battery and mounting tray as described In Chapter 5A. 3 Remove the air cleaner and air inlet duct as described In Chapter 4A. 4 Disconnect the kickdown cable at the sector on the throttle housing and detach It from the mounting on the camshaft cover. Also release the cable from the support on the left-hand end of the cylinder head. 5 Disconnect the wiring connectors on the transmission. 6 Disconnect the fluid inlet and outlet Unas from the heat exchanger on top of the transmission. 7 Pull the fluid level dipstick from Its tube on the front of the transmission and tape over the top of the tube to prevent dirt entry. 8 Unscrew and remove the retaining pin and disconnect the speed selector cable from the top of the transmission. 9 Unscrew the upper bolt securing the starter motor to the transmission. 10 Unscrew the upper bolts securing the transmission to the engine. 11 Support the weight of the engine using a hoist attached to the engine lifting eyes, or alternatively UBO a trolley jack and block of wood beneath the engine, 12 Remove the screws and remove the front wheel arch liner from under the left-hand wheel arch. 13 Unscrew the nut securing the earth cablo to the transmission. 14 Using a punch drive out the roll pins securing both driveshafts to the final drive output shafts. 15 Unscrew and remove the bolts securing the left-hand swivel hub assembly to the front suspension strut, then separate the components and support the swivel hub on an axle stand. 16 Move the swivel hub assembly outwards and slide the inner end of the driveshaft from the splines on the transmission output shaft. Support the shaft away from the transmission to prevent damage to the gaiters. 17 Unscrew the lambdafoxygen sensor from the exhaust downpipe and position it In a safe place to prevent damage. 18 Unscrew ihe nuts securing the downpipe to Ihe exhaust manifold, then lower It and suppon on an axle stand. Recover the gasket. 19 Unscrew the knurled nut and disconnect the speedometer cable from the top of the final drive housing.
3-2 Locking the flywheel when removing the electromagnetic clutch 20 Unscrew the remaining bolt securing the staner motor to the transmission 21 Unbolt and remove Ihe lower flywheel cover from the transmission. 22 Working beneath the vehicle, unscrew the bolts securing the rear engine mounting to the underbody then unscrew the bolts securing the mounting lo the transmission and withdraw the mounting assembly from under the vehicle. 23 Unscrew the bolts securing the left-hand engine/transmission mounting to the body thon unscrew the bolts from the transmission and remove the mounting. 24 Support the weight of the transmission on a trolley jack then unscrew the remaining nut and bolt from the bellhouslng and pull the transmission away from the engine. Lower it and remove from under the vehicle.
A
Warning: Support the transmission to ensure that It remains steady on the Jack head. Keep the transmission level until the Input shaft and pump shaft are fully withdrawn from the electromagnetic clutch housing.
Refitting 25 Refitting is a reversal of the removal procedure, but note the following points. a} Apply a smear of high-melting-point grease to the splines of the transmission input shaft and oil pump driveshaft.
3.6 Checking the resistance of the clutch windings 1 Slip rings
0) Tighten all nuts and bolts to the
specified
torque, where given, c) Renew both driveshaft roll pins.
3 Electro-magnetic clutch • & removal, inspection 5. and refitting ^
Removal 1 Remove Ihe transmission as described n Section 2. 2 Turn the flywheel so that two of the lour mounting bolts are accessible, Hold tha flywheel stationary then unscrew Ihe tvrt bolts. To hold the flywheel, Insert a wida bladed screwdriver In the ring gear teeth or alternatively use a piece of angle iron against one of the retaining bolts temporarily Inserted in the cylinder block (see illustration). 3 Turn the crankshaft half a turn and unscrew the remaining bolts, then withdraw the electromagnetic clutch.
Inspection 4 Turn the driven element by means of tha slip rings, and check that the bearing is not noisy or rough. 5 Inspect the slip rings for burning or other damage. Clean them if necessary using fid and a clean rag. 6 Check the resistance of the clutch windings, using an ohmmetor connected across the slip rings (see Illustration). The resistance at 20*0 should be 2 to 4 ohms. 7 Check the Insulation of the windings, using an ohmmeter connected between either sip ring and the body of the clutch (see illustration). Resistance should be Infinity. 8 If the clutch fails any of the foregoing checks, renew it. Apart from the brush gear, Individual spares are not available.
Refitting 9 Refitting is a reversal of removal but tighten all bolts to the specified torque.
windings
Page 178 of 225
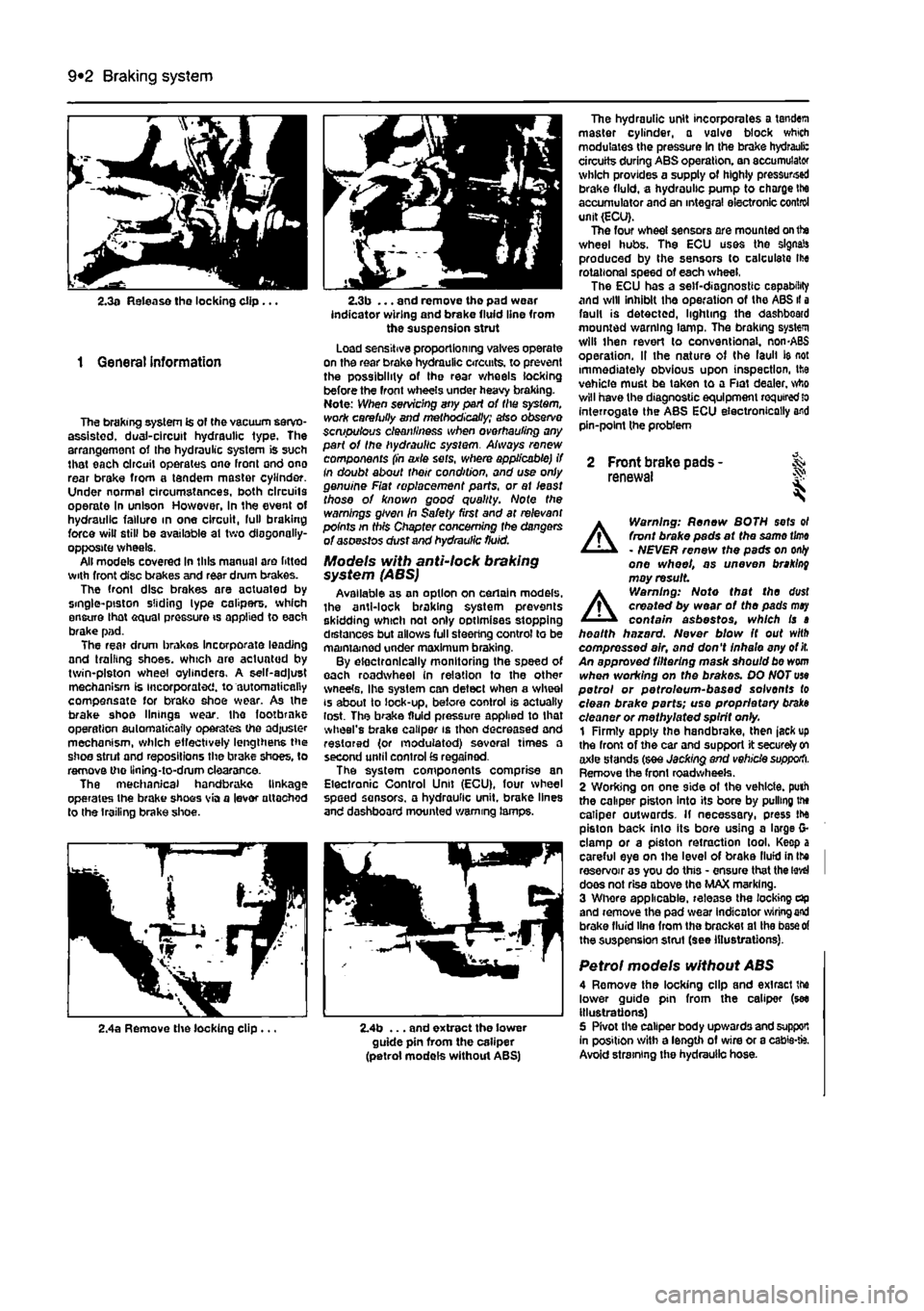
9*2 Braking system
2.3a Release tho locking clip ...
1 General information
The braking system is of the vacuum servo-assisted. dual-circuit hydraulic type. The arrangement of Ihe hydraulic system is such that each circuit operates one front ond ono rear brake from a tandem master cylinder. Under normal circumstances, both circuits operate In unison However, in the event of hydraulic failure in one circuit, lull braking force will still be available at two diagonally-opposite wheels. All models covered in this manual are fitted with front disc brakes and rear drum brakes. The front disc brakes are aotuated by single-piston sliding lype calipers, which ensure lhat equal pressure is applied to each brake pad. The rear drum brakes incorporate leading and trailing shoes, which are actuated by twin-piston wheel cylinders. A self-adjust mechanism is incorporated, to automatically compensate for brako shoe wear. As the brake shoe linings wear, the footbrnke operation automatically operates the adjuster mechanism, which effectively lengthens the shoe strut and repositions the brake shoes, to remove the llning-to-drum clearance. The mechanical handbrake linkage operates the brake shoos via a lever attached to the trailing brake shoe.
2.3b ... and remove the pad wear indicator wiring and brake fluid line from the suspension strut Load sensitive proportioning valves operate on the rear brake hydraulic circuits, to prevent the possibility of the rear wheels locking before the front wheels under heavy braking. Note: When servicing any part of the system, work carefully and methodically; also observe scmpulous cleanliness when overhauling any part of the hydraulic sysiem. Always renew components (in axle sets, where applicable) if In doubt about their condition, and use only genuine Fiat replacement parts, or at least those of known good quality. Note the warnings given in Safety first and at relevant points in this Chapter concerning fhe dangers of asoestos dust and hydraulic fluid.
Models with anti-lock braking system (ABS) Available as an option on certain models, the anti-lock braking system prevents skidding which not only optimises stopping distances but allows full steering control to be maintained under maximum braking. By electronically monitoring the speed of each roadwheel in relation to the other wneete, Ihe system can detect when a wheel is about to lock-up, before control is actually lost. The brake fluid pressure applied to that wheel's brake caliper is then decreased and restored (or modulated) several times a second until control
£s
regained. The system components comprise an Electronic Control Unit (ECU), four wheel speed sensors, a hydraulic unit, brake lines and dashboard mounted warning lamps.
The hydraulic unit incorporates a tandem master cylinder, a valve block which modulates the pressure in the brake hydrauli: circuits during ABS operation, an accumulator which provides a supply of highly pressursed brake fluid, a hydraulic pump to charge Ihe accumulator and an integral electronic control unit (ECU). The four wheel sensors are mounted on the wheel hubs. The ECU uses the signals produced by the sensors to calculate Ihe rotational speed of each wheel, The ECU has a self-diagnostic capability and will inhibit the operation of the ABS il a fault is detected, lighting the dashboard mounted warning lamp. The braking system will then revert lo conventional. non-ABS operation. II the nature of the laull ie not immediately obvious upon inspection, the vehicle must be taken to a Fiat dealer, who will have the diagnostic equipment
required
lo interrogate the ABS ECU electronically and pin-point the problem
2 Front brake pads - & renewal S
A
Warning: Renew BOTH sets ol front brake pads at the same
time
- NEVER renew the pads on
only
one wheel, as uneven braking may result
A
Warning: Note that the dust created by wear of the pads
may
contain asbestos, which is a health hazard. Never blow It out with compressed air, and don't inhale any of
it.
An approved filtering mask should be worn when working on the brakes. DO NOT use petrol or petroleum-based solvents to clean brake parts; use proprietary braks cleaner or methylated spirit only. 1 Firmly apply the handbrake, then jack up the front of the car and support it securely
on
axle stands (see Jacking and vehicle supporti. Remove the front roadwheeis. 2 Wording on one side of the vehicle, puth the caliper piston into its bore by pulling the caliper outwards. If necessary, press the piston back into its bore using a large G-clamp or a piston retraction tool. Keep a careful eye on the level of brake llufd in Ihe I reservoir as you do this - ensure that the
level
I does not rise above the MAX marking. 3 Whore applicable, release the locking dp and remove the pad wear indicator
wiring end
brake fluid line from the bracket at Ihe
base of
the suspension strut (see illustrations).
Petrol models without ABS 4 Remove the locking clip and exlracl the lower guide pin from the caliper (see illustrations) 5 Pivot the caliper body upwards and support In position with a length of wire or a cabie-fc. Avoid straining the hydraulic hose.
2,4a Remove the locking clip ... 2.4b ... and extract the lower guide pin from the caliper (petrol models without ABS)
Page 190 of 225
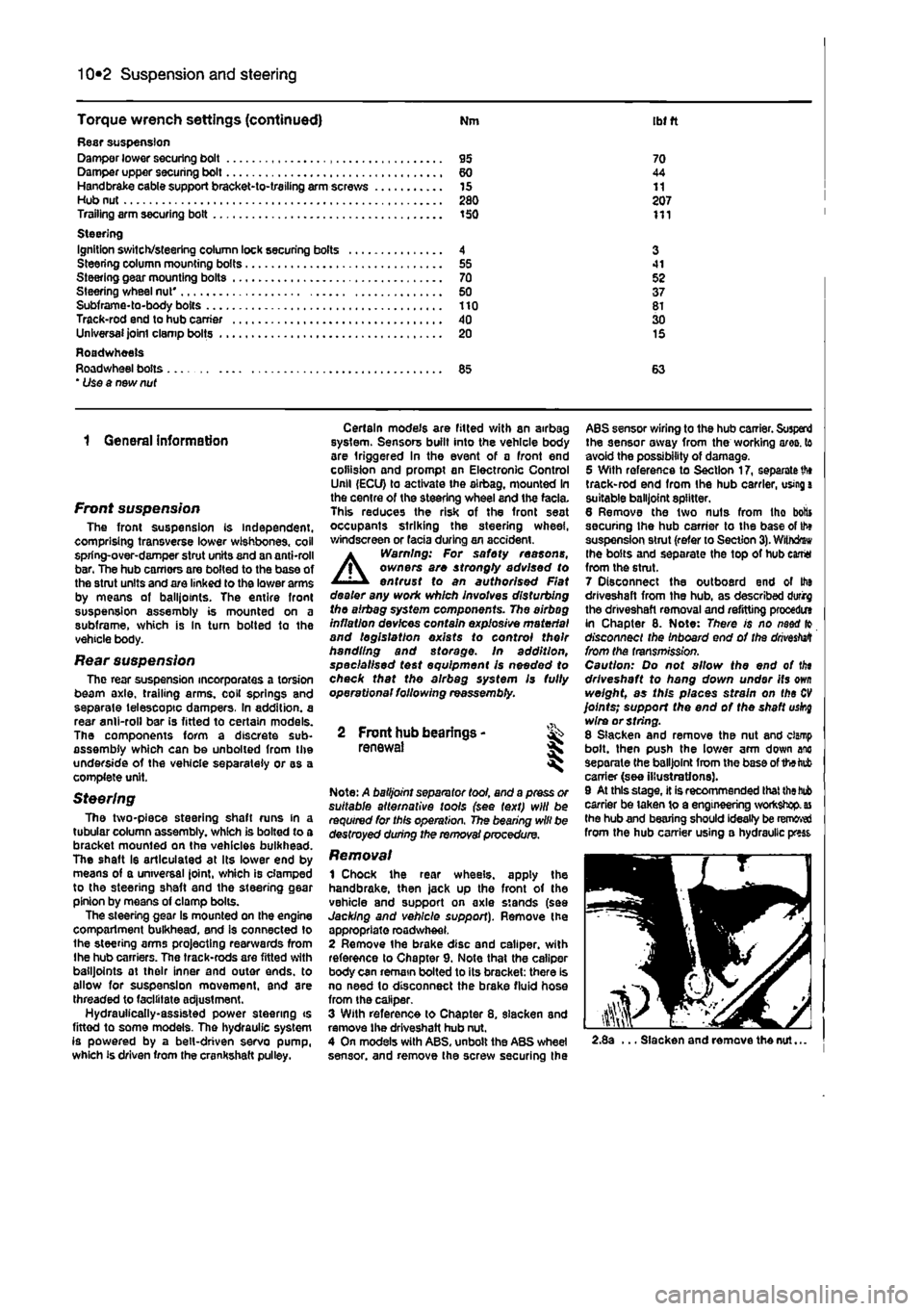
Suspension and steering 10*2
Torque wrench settings (continued) Nm ibt ft Rasr suspension Damper lower securing bolt 95 70 Damper upper securing bolt 60 44 Handbrake cable support bracket-to-trailing arm screws 15 11 Hub nut 280 207 Trailing arm securing bolt 150 111 Steering Ignition switch/steering column lock securing bolts 4 3 Steering column mounting bolts 55 41 Steering gear mounting bolts 70 52 Steering wheel nut' 50 37 Subframe-to-body bolts 110 81 Track-rod end to hub carrier 40 30 Unlversaijointclampbolts 20 15 Roadwheels Roadwheel bolts 85 63 * Use a new nut
1 General information
Front suspension The front suspension is independent, comprising transverse lower wishbones, coil spring-over-damper strut units and an anti-roll bar. The hub carriors are bolted to the base of the stmt units and are linked to the lower arms by means ot balliotnts. The entire front suspension assembly is mounted on a subframe, which is In turn botted to the vehicle body.
Rear suspension The rear suspension incorporates a torsion beam axle, trailing arms, coil springs and separate telescopic dampers. In addition, a rear anil-roll bar is fitted to certain models. The components form a discrete sub-assembly which can be unboiled from the underside of the vehicle separately or as a complete unit.
Steering The two-piece steering shaft runs in a tubular column assembly, which is bolted to a bracket mounted on the vehicles bulkhead. The shaft Is articulated at its lower end by means of a universal Joint, which is clamped to the steering shaft and the steering gear pinion by moans of clamp bolts. The steering gear is mounted on the engine compartment bulkhead, and is connected to the steering arms projecting rearwards from Ihe hub carriers. The track-rods are fitted with balljoints at their inner and outer ends, to allow for suspension movement, and are threaded to facilitate ad|ustment. Hydrauiically-assisted power steering ts fittod to some models. The hydraulic system is powered by a belt-driven servo pump, which is driven from the crankshaft pulley.
Certain models are fitted with an airbag system. Sensors built into the vehicle body are triggered in the event of a front end collision and prompt an Electronic Control Unll (ECU) to activate the airbag, mounted In the centre of the steering wheel and the facia. This reduces the risk of the front seat occupants striking the steering wheel, windscreen or facia during an accident.
A
Warning: For safety reasons, owners are strongty advised to entrust to an authorised Flat dealer any work which involves disturbing the airbag system components. The airbag inflation devices contain explosive material and legislation exists to control their handling and storage, in addition, specialised test equipment Is needed to check that the airbag system Is fully operational following reassembly.
2 Front hub bearings -renewal *
Note: A balljoint separator tool, and a press or suitable alternative tools (see text) will be required for this operation. The bearing will be destroyed during the removal procedure.
Removal 1 Chock the rear wheels, apply the handbrake, then jack up the front of the vehicle and support on axle stands (see Jacking and vehicle support). Remove the appropriate roadwheel. 2 Remove the brake disc and caliper, with reference to Chapter 9. Note that the caliper body can remain bolted to its bracket: there is no need lo disconnect the brake fluid hose from the caliper. 3 With reference to Chapter 8. slacken and remove the driveshaft hub nut. 4 On models with ABS, unbolt the ABS wheel sensor, and remove the screw securing the
ABS sensor wiring to the hub carrier. Suspend the sensor away from the working ares, to avoid the possibility of damage. 5 With reference to Section 17, separate
th»
track-rod end from the hub carrier, using
a
suitable balljoint splitter. 6 Remove the two nuts from tho botts securing Ihe hub carrier to the base of th» suspension strut (refer to Section
3).
Withdrew the bolts and separate the top of hub earrtt from the strut. 7 Disconnect the outboard end of Ito driveshaft from the hub, as described durirg the driveshaft removal and refitting procedm in Chapter 8. Note: There is no naod fo disconnect the Inboard end of the
drivestett
from the transmission. Caution: Do not allow the end of tin driveshaft to hang down under its
own
weight, as this places strain on the
CV
joints; support the end of the shaft uskg wire or string. 8 Slacken and remove the nut and clamp bolt, then push the lower arm down anc separate the balljoint from the base of the tab carrier (see illustrations). 9 At this stage, it is recommended that
the bub
carrier be taken to a engineering workshop,
as
the hub and bearing should ideally be removed from the hub carrier using a hydraulic press
2.8a ... Slacken and remove the nut...
Page 191 of 225
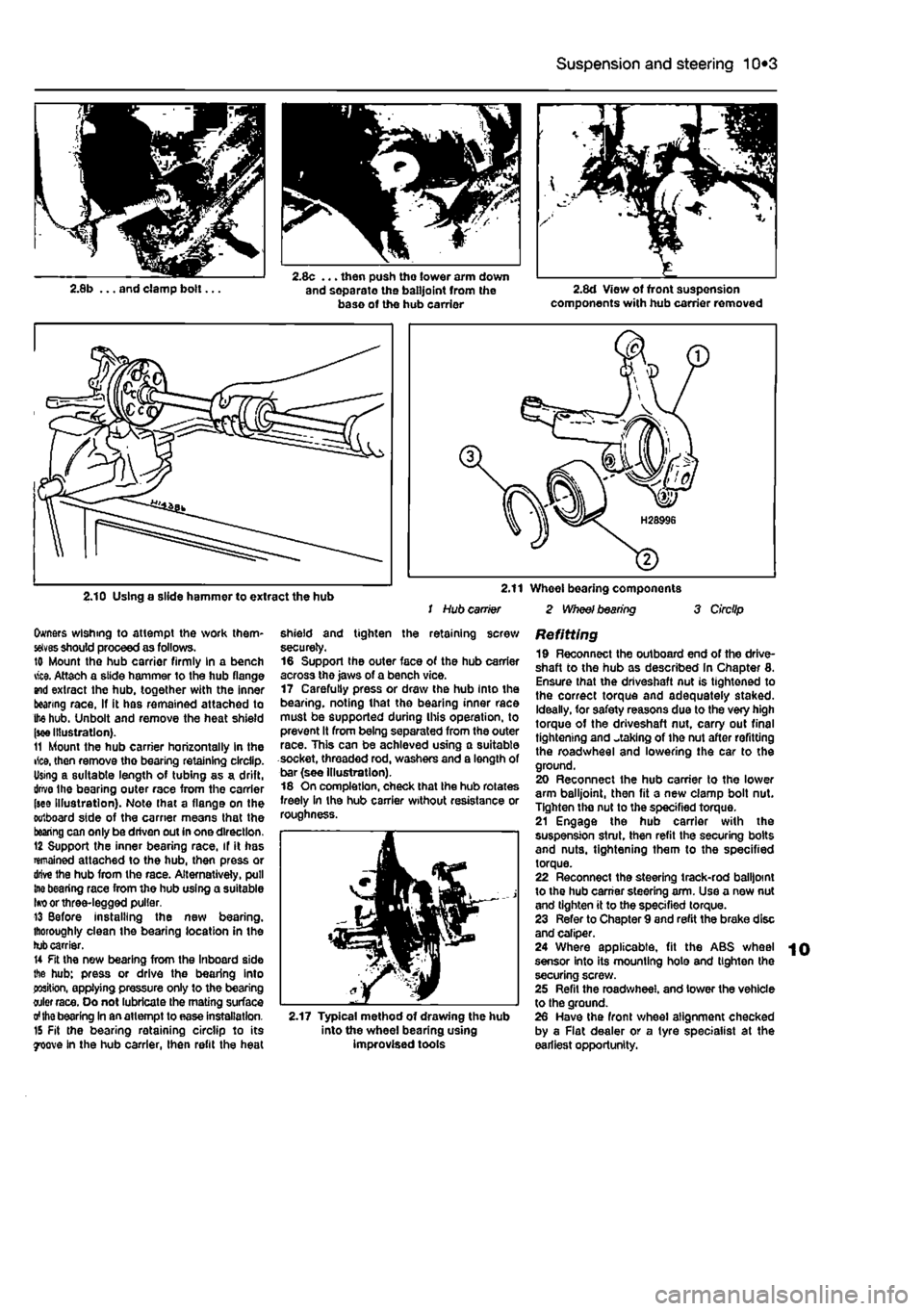
Suspension and steering 10*3
2.10 Using a slide hammer to extract the hub 2.11 Wheel bearing components / Hub carrier 2 Wheel bearing 3 Circlip
Owners wishing to attempt the work them-
selves
should proceed as follows. 10 Mount tho hub carrier firmly In a bench vice. Attach a slide hammer to the hub flange and extract the hub. together with the inner bearing race, If it has remained attached to the hub. Unbolt and remove the heat shield
(see
Illustration). 11 Mount the hub carrier horizontally in the rice, then remove tho bearing retaining circlip. Using a suitable length of tubing as a drift, drive Ihe bearing outer race from the carrier (see Illustration). Note that a flange on the outboard side of the carrier means that the bearing can only be driven out in one direction. 12 Support the inner bearing race, if it has remained attached to the hub, then press or drive the hub from the race. Alternatively, pull trie bearing race from the hub using a suitable Iw or three-legged puller. 13 Before Installing the new bearing, thoroughly clean the bearing location in the tub carrier. U Fit the new bearing from the Inboard side the hub: press or drive the bearing into position, applying pressure only to the bearing oiler race. Oo not lubricate the mating surface
ol the
bearing In an attempt to ease installation. 15 Fit the bearing retaining circlip to its 700ve in the hub carrier, then refit the heat
shield and tighten the retaining screw securely. 16 Support the outer face of the hub carrier across the jaws of a bench vice. 17 Carefully press or draw the hub into the bearing, noting that the bearing inner race must be supported during Ihis operation, to prevent It from being separated from the outer race. This can be achieved using a suitable socket, threaded rod, washers and a length of bar (see Illustration). 18 On completion, check that the hub rotates freely in the hub carrier without resistance or roughness.
2.17 Typical method of drawing the hub into the wheel bearing using improvised tools
Refitting 19 Reconnect the outboard end of the drive-shaft to the hub as described In Chapter 8. Ensure that the driveshaft nut is tightened to the correct torque and adequately staked. Ideally, for safety reasons due to the very high torque of the driveshaft nut, carry out final tightening and staking of the nut after refitting the roadwheel and lowering the car to the ground. 20 Reconnect the hub carrier to the lower arm balljoint, then fit a new clamp bolt nut. Tighten tho nut to the specified torque. 21 Engage the hub carrier with the suspension strut, then refit the securing bolts and nuts, tightening them to the specified torque. 22 Reconnect the steering track-rod balljoint to the hub carrier steering arm. Use a new nut and tighten it to the specified torque. 23 Refer to Chapter 9 and refit the brake disc and caliper. 24 Where applicable, fit the ABS wheel sensor into its mounting hole and tighten the securing screw. 25 Refit the roadwheel, and tower the vehicle to the ground. 26 Have the front wheel alignment checked by a Fiat dealer or a tyre specialist at the earliest opportunity.
Page 192 of 225
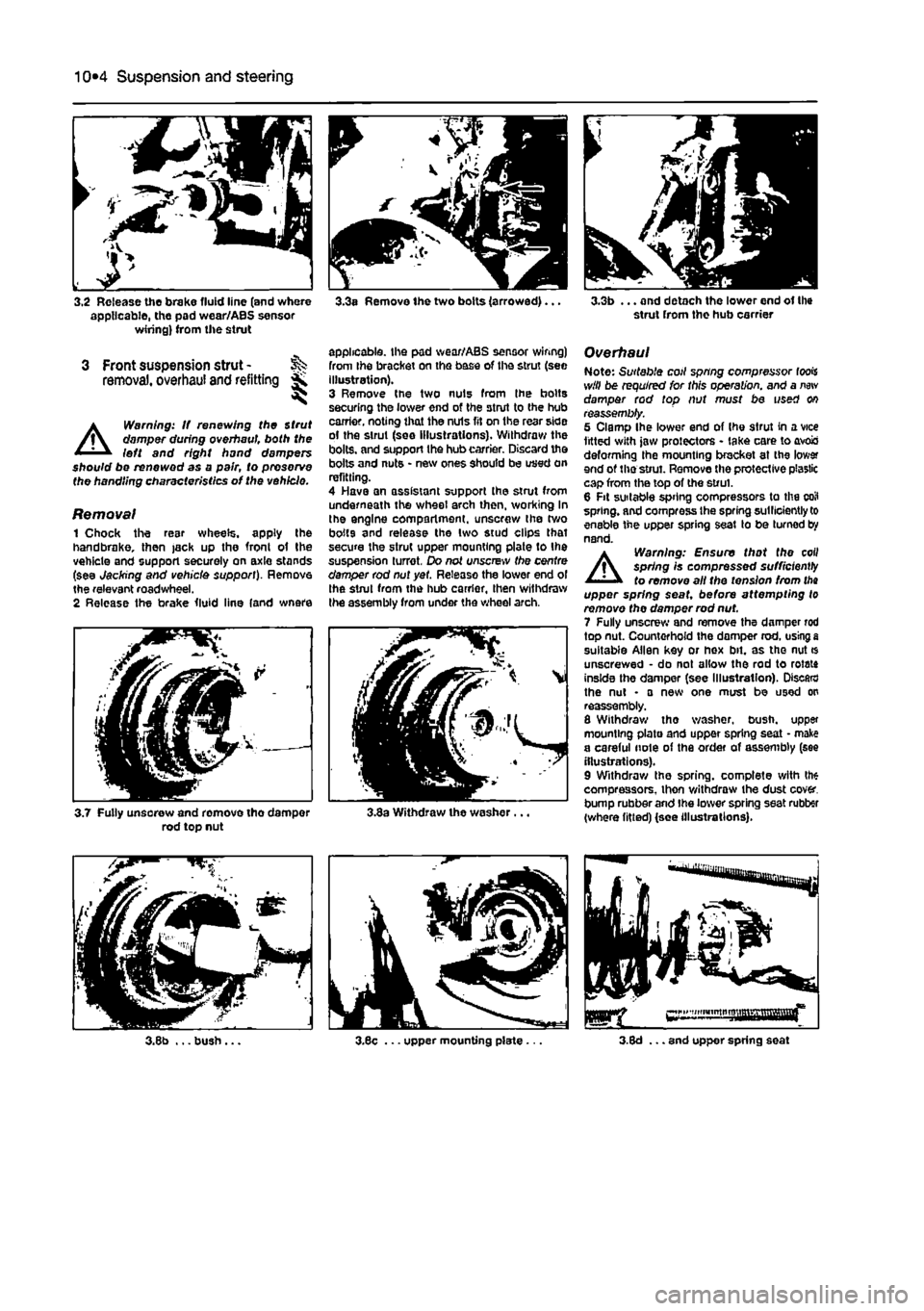
Suspension and steering 10*4
3.2 Release the brake fluid line (and where applicable, the pad wear/ABS sensor wiring) from the strut
3 Front suspension strut -removal, overhaul and refitting *
A
Warning: If renewing the Strut damper during overhaul both the left and right hand dampers should be renewed as a pair, to preserve the handling characteristics of the vehicle.
Removal 1 Chock the resr wheels, apply the handbrake, then jack up the fronl of the vehicle and support securely on axle stands (see Jacking and vehicle support). Remove the relevant roadwheel. 2 Release the brake fluid line (and wnere
3.3a Remove the two bolts (arrowed)...
applicable, the pad wear/ABS sensor wiring) from Ihe bracket on the base of the strut (see illustration). 3 Remove the two nuts from Ihe bolts securing the lower end of the strut to the hub carrier, noting that the nuls fit on the rear side of the strut (see illustrations). Withdraw the bolts, and support the hub carrier. Discard the bolts and nuts • new ones should be used on refitting. 4 Have an assistant support the strut from underneath the wheel arch then, working In the engine compartment, unscrew the two bolts and release the two stud clips that secure the strut upper mounting plate to the suspension turret. Do not unscrew the centre damper rod nut yet. Release the lower end ol the strut from the hub carrier, then withdraw the assembly from under the wheel arch.
3.7 Fully unsorew and remove tho damper rod top nut 3.3a Withdraw the washer.
3.3b ... and detach the lower end of the strut from the hub carrier
Overhaul Note: Suitable coil spring compressor fools will be required for this operation, and a
new
damper rod top nut must be used on reassembly. 5 Clamp Ihe lower end of Ihe strut in a vice fitted with jaw protectors - take care to avois deforming the mounting bracket at the lower end of the strut. Remove the protective plastic cap from the top of the strut. 6 Fit suitable spring compressors to the coil spring, and compress Ihe spring sutllciently to enable the upper spring seat to be turned by nand.
A
Warning: Ensure that the coil spring Is compressed sufficiently to remove all the tension from
tha
upper spring seat, before attempting to remove the damper rod nut. 7 Fully unscrew and remove the damper rod top nut. Countorhofd the domper rod. using
a
suitable Allen key or hex bit. as tho nut * unscrewed • do not allow the rod to rotate inside the damper (see Illustration). Discard the nut • a new one must be used on reassembly. 8 Withdraw tho washer, bush, upper mounting plate and upper spring seat • make a careful note of the order of assembly (see illustrations). 9 Withdraw the spring, complete with the compressors, thon v/ithdraw the dust cover, bump rubber and Ihe lower spring seat rubber (where fitted) (see illustrations).
Page 194 of 225
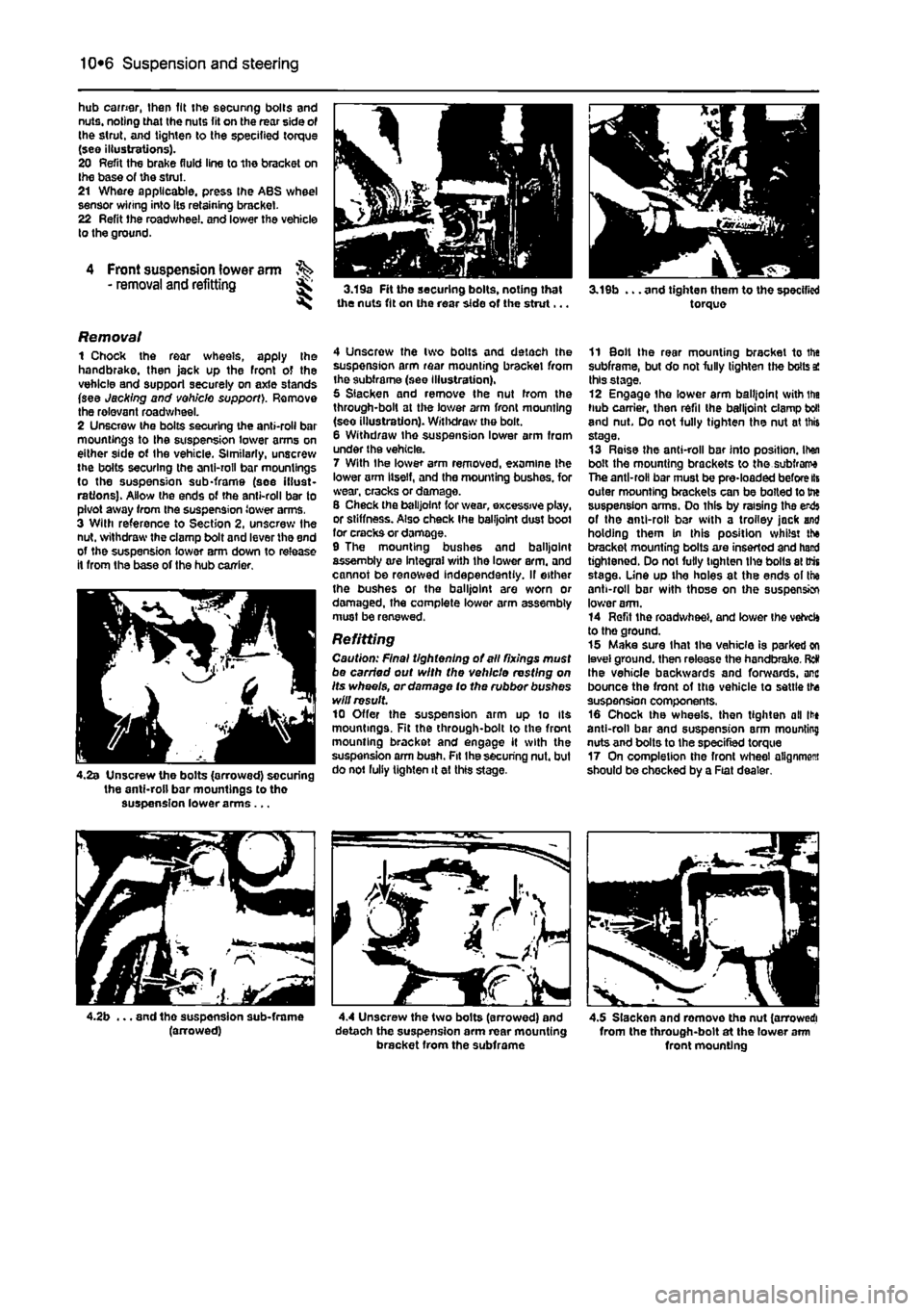
Suspension and steering 10*6
hub earner, then fit the securing bolts and nuts, noting that the nuts fit on the rear side of the strut, and tighten to the specified torque (see illustrations). 20 Refit the brake fluid line to the bracket on Ihe base of the strut. 21 Where applicable, press the ABS wheel sensor winng into its retaining bracket. 22 Refit the roadwheel. and lower the vehicle to the ground.
4 Front suspension lower arm - removal and refitting 3.19a Fit the securing bolts, noting that the nuts fit on the rear side of the strut...
Removal 1 Chock the rear wheels, apply the handbrake, then jack up the front of the vehicle and support securely on axle stands (see Jacking and vehicle support). Remove the relevant roadwheel. 2 Unscrew the bolts securing the anti-roll bar mountings to the suspension lower arms on either side ot Ihe vehicle. Similarly, unscrew the bolts securing the anti-roll bar mountings to the suspension sub-frame (see illust-rations). Allow the ends of the anti-roll bar to pivot away from the suspension lower arms. 3 With reference to Section 2, unscrew Ihe nut. withdraw the clamp bolt and lever the end of the suspension lower arm down to release it from the base of the hub carrier.
4.2s Unscrew the bolts (arrowed) securing the anti-roll bar mountings to tho suspension lower arms...
4 Unscrow the two bolts and detach the suspension arm rear mounting bracket from the subframe (see Illustration). 5 Slacken and remove the nut from the through-bolt at the lower arm front mounting (seo illustration). Withdraw the bolt. 6 Withdraw Ihe suspension lower arm from under the vehicle. 7 With the lower arm removed, examine the lower arm Itself, and the mounting bushes, for wear, cracks or damage. S Check the balljoint for wear, excessive play, or stiffness. Also check Ihe balljoint dust boot for cracks or damage. 9 The mounting bushes and balljoint assembly are integral with the lower arm. and cannot be renewed independently. If either the bushes or the balljoint are worn or damaged, the complete lower arm assembly must be renewed.
Refitting Caution: Final tightening of all fixings must be carried out with the vehicle resting on Its wheels, or damage to the rubbor bushes will result 10 Offer the suspension arm up lo Its mountings. Fit the through-bolt to the front mounting bracket and engage it with the suspension arm bush. Fit Ihe securing nut. but do not fully tighten it at this stage.
. and tho suspension sub-frame (arrowed) 4.4 Unscrew the two bolts (arrowed) and detaoh the suspension arm rear mounting bracket from the subframe
3.19b ... and tighten them to the specified torque
11 Bolt Ihe rear mounting bracket to the subframe, but do not fully tighten the bolts a! this stage, 12 Engage the lower arm balljoint svith ifia hub carrier, then refii the balljoint clamp boll and nut. Do not fully tighten the nut at this stage. 13 Raise the anti-roll bar into position. Itan bolt the mounting brackets to the subfrarra The anti-roll bar must be pre-loaded before lis outer mounting brackets can be bolted to the suspension arms. Do this by raising tha erds of the anti-roll bar with a trolley jack and holding them in this position whilst the bracket mounting bolts are inserted and hand tightened. Do not fully tighten the bolls at trts stage, line up the holes at the ends of the anti-roll bar with those on the suspension lower arm. 14 Refit the roadwheel, and lower the vehrcfe to the ground. 15 Make sure that the vehicle is parked on level ground, then release the handbrake. Red the vehicle backwards and forwards, arc bounce the front of the vehicle to settle the suspension components. 16 Chock the wheels, then tighten all lit* anti-roll bar and suspension arm mounting nuts and bolts to the specified torque 17 On completion the front wheel alignment should be chocked by a Fiat dealer.
4.5 Slacken and romove tho nut (arrowed! from the through-bolt at the lower arm front mounting
Page 224 of 225
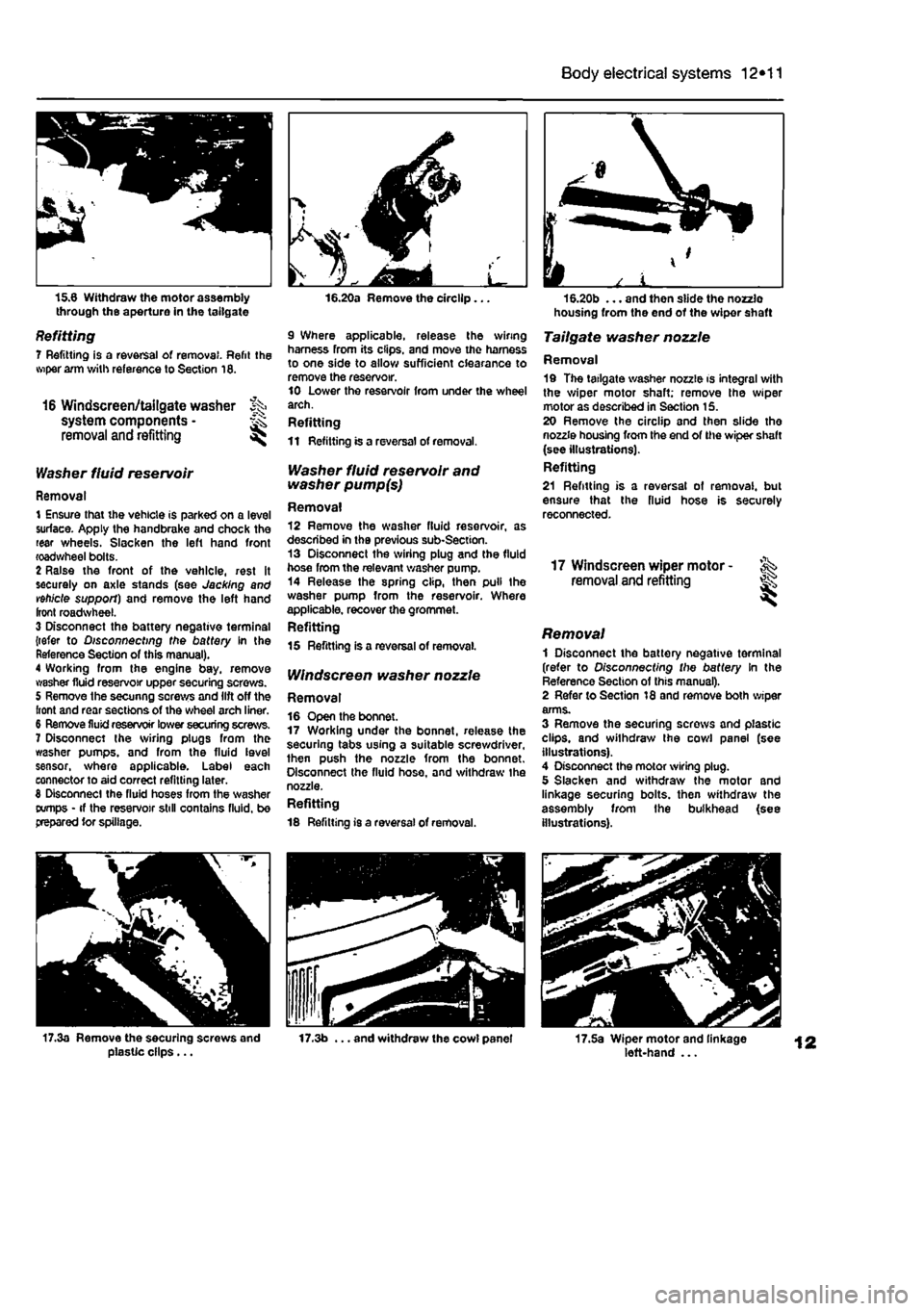
Body electrical systems 12*11
15.6 Withdraw the motor assembly through the aperture in the tailgate
Refitting 7 Refitting is a reversal of removal. Refit the wiper arm with reference to Section 16.
16 Windscreen/tailgate washer % system components • ^ removal and refitting ^
Washer fluid reservoir
Removal 1 Ensure that the vehicle is parked on a level surface. Apply the handbrake and chock the rear wheels. Slacken the left hand front roadwheel bolts. 2 Raise the front of the vehicle, rest it securely on axle stands (see Jacking and vehicle support) and remove the left hand front roadwheel. 3 Disconnect the battery negative terminal {refer to Disconnecting the battery In the Reference Section of this manual). 4 Working from the engine bay, remove washer fluid reservoir upper securing screws. 5 Remove the secunng screws and lift off the front and rear sections of the wheel arch liner. 6 Remove fluid reservoir lower securing screws. 7 Disconnect the sviring plugs from the washer pumps, and from the fluid level sensor, where applicable. Label each connector to aid correct refitting later. 8 Disconnect the fluid hoses from the washer tx/mps • if the reservoir still contains fluid, be prepared tor spillage.
16.20a Remove the circllp...
9 Where applicable, release the wiring harness from its clips, and move the harness to one side to allow sufficient clearance to remove the reservoir. 10 Lower the reservoir from under the wheel arch. Refitting 11 Refitting is a reversal of removal.
Washer fluid reservoir and washer pump(s)
Removal 12 Remove the washer fluid reservoir, as described in the previous sub-Section. 13 Disconnect the wiring plug and the fluid hose from the relevant washer pump. 14 Release the spring clip, then pull the washer pump from the reservoir. Where applicable, recover the grommet. Refitting 15 Refitting is a reversal of removal.
IV/nctecreen washer nozzle
Removal 16 Open the bonnet. 17 Working under the bonnet, release the securing tabs using a suitable screwdriver, then push the nozzle from the bonnet. Disconnect the fluid hose, and withdraw the nozzle. Refitting 18 Refitting is a reversal of removal.
housing from the end of the wiper shaft
Tailgate washer nozzle
Removal 19 The tailgate washer nozzle is integral with the wiper motor shaft; remove the wiper motor as described in Section 15. 20 Remove the circllp and then slide the nozzle housing from the end of the wiper shaft (see illustrations). Refitting 21 Refitting is a reversal of removal, but ensure that the fluid hose is securely reconnected.
17 Windscreen wiper motor -removal and refitting ^
Removal 1 Disconnect the battery negative terminal (refer to Disconnecting the battery In the Reference Section of this manual). 2 Refer to Section 18 and remove both wiper arms. 3 Remove the securing screws and plastic clips, and withdraw the cowl panel (see illustrations). 4 Disconnect the motor wiring plug. 5 Slacken and withdraw the motor and linkage securing bolts, then withdraw the assembly from the bulkhead (see illustrations).
17.3a Remove the securing screws and plasUc clips... 17.3b ... and withdraw the cowl panel 17.5a Wiper motor and linkage left-hand ...