clock FIAT PUNTO 1998 176 / 1.G User Guide
[x] Cancel search | Manufacturer: FIAT, Model Year: 1998, Model line: PUNTO, Model: FIAT PUNTO 1998 176 / 1.GPages: 225, PDF Size: 18.54 MB
Page 140 of 225
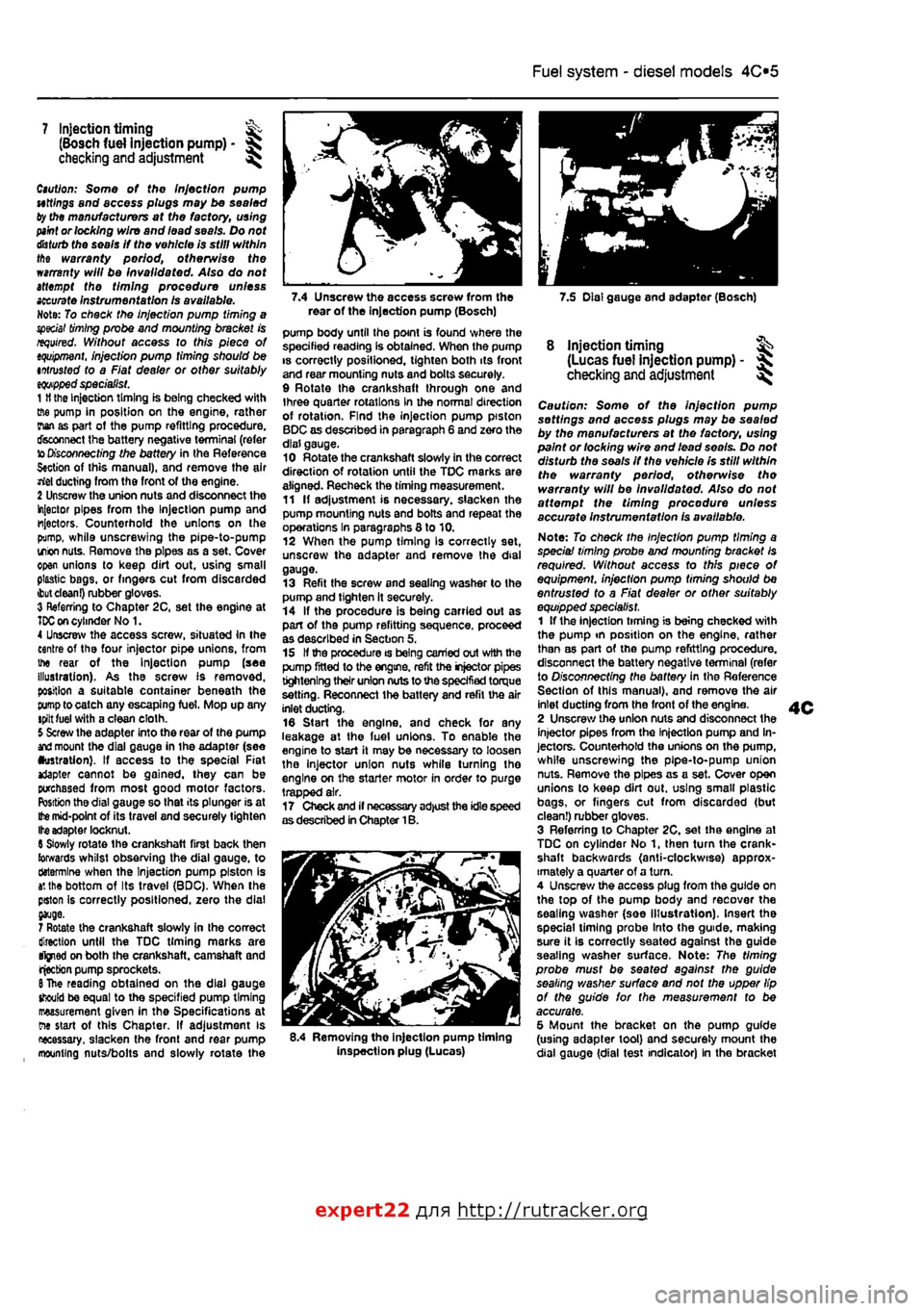
Fuel system - diesel models
4C*3
7.4 Unscrew the access screw from the 7.5 Dial gauge and adapter (Bosch) rear of the Injection pump (Bosch)
7 Injection timing ^ (Bosch fuel injection pump) -checking and adjustment ^
Caution: Some of the Injection pump uttlngs and access plugs may be sealed ty the manufacturers at the factory, using
paint
or locking wire and lead seals. Do not
disturb
the seals If the vehicle is still within the warranty period, otherwise the warranty will be invalidated. Also do not attempt the timing procedure unless
accurate
Instrumentation Is available. Note: To check the injection pump timing a special
timing
probe and mounting bracket is required. Without access to this piece of
tquipment.
injection pump timing should be intrusted to a Fiat dealer or other suitably
eqwpped
specialist. 1
H
the Injection timing is being checked with ffie pump in position on the engine, rather rian as part ot the pump refitting procedure, disconnect the battery negative terminal (refer to
Disconnecting
the battery in the Reference S«ction of this manual), and remove the air rtel ducting from the front of the engine. 2 Unscrew the union nuts and disconnect the injector pipes from the Injection pump and injectors. Counterhold the unions on the pump, while unscrewing the pipe-to-pump irion
nuts.
Remove the pipes as a set. Cover open unions to keep dirt out, using small plastic bags, or fingers cut from discarded
ibut clean!)
rubber gloves. 3 Referring to Chapter 2C, set the engine at
TDC on
cylinder No 1. 4 Unscrew the access screw, situated In the centre of the four injector pipe unions, from the rear of the Injection pump (see illustration). As the screw Is removed, position a suitable container beneath the
pump
to catch any escaping fuel, Mop up any tpilt fuel with a clean cloth. 5 Screw the adapter into the rear of the pump
and
mount the dial gauge in ihe adapter (see •ustration). If access to the special Fiat *Japter cannot be gained, they can be purchased from most good motor factors. Position the dial gauge so that its plunger is at
Ifce
mid-point of its travel and securely tighten Ite adapter locknut. 6 Slowly rotate the crankshaft first back then towards whilst observing the dial gauge, to ctotermlne when the Injection pump piston is
a',
the bottom of Its travel (BDC), When the pston Is correctly positioned, zero the dial
7 Rotate the crankshaft slowly in the correct direction until the TDC timing marks are tfjned on both the crankshaft, camshaft and rjecbon pump sprockets.
6
The reading obtained on the dial gauge should be equal to the specified pump timing measurement given in the Specifications at ew start of this Chapter, If adjustment is necessary, slacken the fronl and rear pump mounting nuts/bolts and slowly rotate the
pump body until the point is found where the specified reading Is obtained. When the pump is correctly posilioned, tighten both its front and rear mounting nuts and bolts securely. 9 Rotate the crankshaft through one and three quarter rotations in the normal direction of rotation. Find the injection pump piston BDC as described in paragraph 6 and zero the dial gauge. 10 Rotate the crankshaft slowly in the correct direction of rotation until the TDC marks are aligned. Recheck the timing measurement. 11 If adjustment is necessary, slacken the pump mounting nuts and bolts and repeat the operations In paragraphs 8 to 10. 12 When the pump timing Is correctly set, unscrew the adapter and remove the dial gauge. 13 Refit the screw and sealing washer to the pump and tighten it securely. 14 If the procedure is being carried out as part of the pump refitting sequence, proceed as described in Section 5, 15 If the procedure is being carried out with the pump fitted to the engine, refit the injector pipes tightening their union nuts to the specified torque setting. Reconnect the battery and refit the air inlet ducting. 16 Start the engine, and check for any leakage at the luel unions. To enable the engine to start it may be necessary to loosen the injector union nuts while turning tho engine on the starter motor in order to purge trapped air. 17 Check and if necessary adjust the idle speed as described in Chapter 1B.
8.4 Removing the injection pump timing inspection plug (Lucas)
8 injection timing ^ (Lucas fuel injection pump) - ^ checking
and
adjustment ^
Caution: Some of the injection pump settings and access plugs may be sealed by the manufacturers at the factory, using paint or locking wire and lead seo/s. Do not disturb the seals if the vehicle Is still within the warranty period, otherwise tho warranty will be Invalidated. Also do not affempf the timing procedure unless accurate instrumentation is available.
Note: To check the Injection pump timing a speciai timing probe and mounting bracket Is required. Without access to this piece of equipment, injection pump timing should be entrusted to a Fiat dealer or other suitably equipped specialist. 1 If the injection timing is being checked with the pump tn position on the engine, rather than as part of the pump refitting procedure, disconnect the battery negative terminal (refer to Disconnecting the battery in the Reference Section of this manual), and remove the air inlet ducting from the front of the engine. 2 Unscrew the union nuts and disconnect the injector pipes from the Injection pump and In-jectors. Counterhold the unions on the pump, while unscrewing the pipe-to-pump union nuts. Remove the pipes as a set. Cover open unions to keep dirt out. using smalt plastic bags, or fingers cut from discarded (but clean!) rubber gloves. 3 Referring to Chapter 2C, set the engine at TDC on cylinder No 1, then turn the crank-shaft backwards (anti-clockwise) approx-imately a quarter of a turn. 4 Unscrew the access plug from the guide on the top of the pump body and recover the sealing washer (soe Illustration). Insert the special liming probe Into the guide, making sure it Ib correctly seated against the guide seating washer surface. Note: The timing probe must be seated against the guide sealing washer surface and not the upper lip of the guide for the measurement to be accurate. 5 Mount the bracket on the pump guide (using adapter tool) and securely mount the dial gauge {dial test indicator) In the bracket
expert22 fl/i* http://rutracker.org
Page 141 of 225

Fuel system - diesel models 4C*3
8.5 Dial gauge (1), mounting bracket (2) and setting rod (3) In position on the injection pump (Lucas)
so that Its tip Is In contact with the bracket linkage (see Illustration). Position the dial gauge so that its plunger is at the mid-point of its travel and zero the gauge. 6 Rotate the crankshaft slowly in the correct direction of rotation (clockwise) until the crankshaft is positioned at TDC on No 1 piston with ell the sprocket timing marks aligned. 7 Check the reading on the dial gauge which should correspond to the value marked on the pump (there is a tolerance of * 0.04 mm). The timing value may be marked on a plastic disc attached to the front of the pump, or alternatively on a tag attached to Ihe pump control lever (see illustrations). 8 If adjustment is necessary, slacken the front pump mounting nuts/bolt and the raar mounting bolt, then slowly rotate tne pump body until the point is found where the specified reading is obtained on the dial gauge (access to the lower front bolt is gained through the hole in the injection pump sprocket). When the pump Is correctly positioned, tighten both its front mounting nuta/bolt and the rear bolt to their specified torque settings. 9 Withdraw the timing probe slightly, so that it
positioned clear of the pump rotor dowel. Rotato the crankshaft ihrough one and three quarter rotations in the normal direction of rotation. 10 Slide the timing probe back Into position ensuring that it Is correctly seated against the guide sealing washer surface, not (he upper Hp, then zero the dial gauge. 11 Rotate the crankshaft slowly in the correct direction ol rotation to the TDC position and recheck the timing measurement 12 If adjustment Is necessary, slacken the pump mounting nuts and bolt and repeat the operations in paragraphs 6 to 11. 13 When the pump timing is correctly set. remove the dial gauge and mounting bracket and withdraw the timing probe. 14 Refit the screw and sealing washer to the guide and tighten it securely.
8.7a Pump timing value (x) marked on plastic diso (Lucas)
15 If the procedure is being carried out as part of the pump refilling sequence, proceed as described in Section 5. 16 If the procedure is being carried out with the pump fitted to the engine, refit the injector pipes tightening their union nuts to the specified torque setting. Reconnect the battery and refit the air inlet ducting. 17 Start the engine, and check for any leakage at the fuel unions. To enable the engine to start it may be necessary to loosen tho injector union nuts while turning the engine on the starter motor in order to purge trapped air. 18 Check and If necessary adjust the Idle speed as described In Chapter 1B.
9 Fuel Injectors -testing, removal and refitting Sk ^
A
Warning: Exercise extreme caution when working on the fuel injectors. Never expose the hands or any part of the body to Injector spray, as the high working pressure can cause the fuel to pen ot rate the skin, with possibly fatal results. You are strongly advised to have any work which involves testing the injectors under pressure carried out by a dealer or fuel Injection specie list.
Testing 1 Injectors do deteriorate with prolonged uso, and it is reasonable to expect them to need reconditioning or renewal after 60 000 miles
8.7b Pump timing values marked on label (1) and tag (2) (Lucas)
(100 000 km) or so. Accurate testing, overhaul and calibration of the Injectors must be left to a specialist. A defective injector which Is causing knocking or smoking can be located without dismantling as follows. 2 Run the engine at a fast idle. Slacken each Injector union In turn, placing rag around the union to catch spilt fuel, and being careful not to exposa the skin to any spray. When tho union on the defective Injector is slackened, the knocking or smoking will stop.
Removal 3 Remove ihe air Inlet ducting from tho front part of the onglne. 4 Carefully clean around the Injectors and injector pipe union nuts. 5 Pull the leak-off pipes from the injectors (see illustration). 6 Unscrow the union nuts securing Ihe injector pipes to the fuel Injection pump. Counterhold the unions on the pump when unscrewing the nuts. Cover open unions lo keep dirt out, using small plastic bags, or fingers cut from discarded (but clean!) rubber gloves. 7 Unscrew the union nuts and disconnect the pipes from the ln|ectors, If necessary, the Injector pipes may be completely removed-Note carefully the locations of the pipe clamps, for use when refitting. Cover tho onds ot (he injectors, to prevent dirt ingress. 8 Unscrew the injectors using a deep socket or box spanner, and remove Ihem from the cylinder head (see Illustration). 9 Recover the tire seal washers from the cy-linder head and discard them (see illustration).
9.5 Disconnecting the Injector leak-off pipes 9.8 Removing an injector
Page 149 of 225
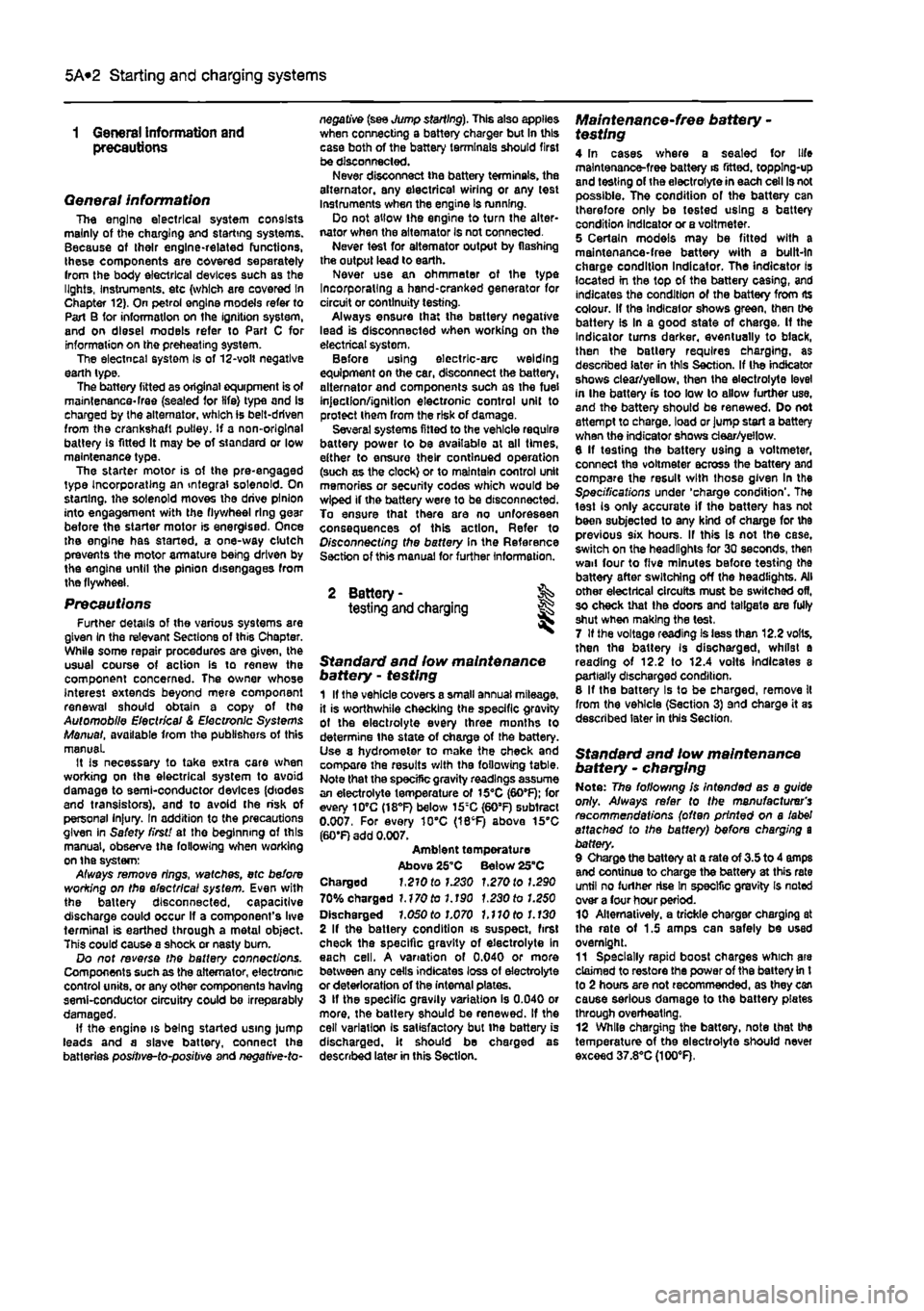
5A«2 Starting and charging systems
1 General information and precautions
General information The engine electrical system consists mainly of the charging and starting systems. Because of their engine-related functions, these components are covered separately from the body electrical devices such as the Ilght3, Instalments, etc (which are covered In Chapter 12). On petrol engine models refer to Part B for information on the ignition system, and on diesel models refer to Part C for information on the preheating system. The electncal system Is of 12-volt negative earth type. The battery fitted as original equipment is of maintenance* free (sealed for life} type and Is charged by the alternator, which is belt-driven from the crankshaft pulley. If a non-original battery is fitted It may be of standard or low maintenance type. The starter motor is of the pre-engaged type Incorporating an integral solenoid. On starting, the solenoid moves the drive pinion into engagement with the flywheel ring gear before the starter motor is energised. Once the engine has started, a one-way clutch prevents the motor armature being driven by the engine until the pinion disengages from the flywheel.
Precautions Further details of the various systems are given In the relevant Sections of this Chapter. While some repair procedures are given, the usual course of action is to renew the component concerned. The owner whose interest extends beyond mere component renewal should obtain a copy of the Automobile Electrical & Electronic Systems Manual, available from the publishers of this manual It Is necessary to take extra care when working on the electrical system to avoid damage to semiconductor devices (diodes and transistors), and to avoid the risk of personal injury. In addition to the precautions given in Safety first! at the beginning of this manual, observe the following when working on the system: Always remove rings, watches, etc before working on the electrical system. Even with the battery disconnected, capacitlve discharge could occur If a component's live terminal is earthed through a metal object. This could cause a shock or nasty bum. Do not reverse the battery connections. Components such as the alternator, electronic control units, or any other components having semi-conductor circuitry could be irreparably damaged. If the engine is being started using jump leads and a slave battery, connect the batteries positive-to-posibve and negative-to-
negative (see Jump starting). This also applies when connecting a battery charger but In this case both of the battery terminals should first be disconnected. Never disconnect the battery terminals, the alternator, any electrical wiring or any test Instalments when the engine Is running. Do not allow the engine to turn the alter-nator when the alternator Is not connected. Never test for alternator output by flashing the output lead to earth. Never use an ohmmeter ot the type Incorporating a hand-cranked generator for circuit or continuity testing. Always ensure that the battery negative lead is disconnected when working on the electrical system. Before using electric-arc welding equipment on the car, disconnect the battery, alternator and components such as the fuel Injection/ignition electronic control unit to protect them from the risk of damage. Several systems fitted to the vehicle require battery power to be available at all times, either to ensure their continued operation (such as the clock) or to maintain control unit memories or security codos which would be wiped if the battery were to be disconnected. To ensure that there are no unforeseen consequences of this action. Refer to Disconnecting the battery In the Reference Section of this manual for further Information.
2 Battery- % testing and charging
Standard and tow maintenance battery - testing 1 If the vehicle covers a small annual mileage, it is worthwhile checking the specific gravity of the electrolyte every three months to determine the state of charge of the battery. Use a hydrometer to make the check and compare the results with the following table, Note that the specific gravity readings assume an electrolyte temperature of 15*C (60'F); for every 10*C (18°f) below 158C (60aF) subtract 0.007, For every 108C (16'F) above 15"C (60'F) add 0.007. Ambient temperature Above 26"C Below 25DC Charged 1,210 to 1£30 1,270 to 1.290 70% charged 1.170to1.l90 1.230to1.250 Discharged 1.050toJ.070 1.110 to 1.130 2 If the battery condition is suspect, first check the specific gravity of electrolyte In each cell. A variation of 0.040 or more between any cells indicates loss of electrolyte or deterioration of the internal plates. 3 If the specific gravity variation is 0.040 or more, the battery should be renewed. If the cell variation Is satisfactory but the battery is discharged, it should be charged as described later in this Section.
Maintenance-free battery -testing 4 In cases where a sealed tor life maintenance-free battery is fitted, topplng-up and testing of the electrolyte in each cell Is not possible. The condition of the battery can therefore only be tested using a battery condition Indicator or a voltmeter. 5 Certain models may be fitted with a maintenance-free battery with a built-in charge condition Indicator. The indicator Is located in the top of the battery casing, and indicates the condition of the battery from its colour. If the Indicator shows green, then the battery is In a good state of charge. If the Indicator turns darker, eventually to black, then the battery requires charging, as described later in this Section. If Ihe indicator shows clear/yellow, then the electrolyte level in Ihe battery is too low to allow further use, and tho battery should be renewed. Do not attempt to charge, load or Jump start a battery when the indicator shows dear/yellow. 6 If testing the battery using a voltmeter, connect the voltmeter across the battery and compare the result with those given In the Specifications under 'charge condition'. The test is only accurate if the battery has not been subjected to any kind of charge for the previous six hours. If this is not the esse, switch on the headlights for 30 seconds, then wait four to five minutes baforo testing the battery after switching off the headlights. All other electrical circuits must be switched off, so check that the doors and tailgate are fully shut when making the test, 7 It the voltage reading Is less than 12.2 voHs, then the battery Is discharged, whilst a reading of 12.2 to 12.4 volts indicates 8 partially discharged condition. 6 If the battery Is to be charged, remove It from the vehicle (Section 3) and charge it as described later In this Section.
Standard and low maintenance battery - charging Note: The following is Intended as a guide only. Always refer to the manufacturer's recommendations (often printed on a label attached to the battery) before charging a battery. 9 Charge the battery at a rate of 3.5 to 4 amps and continue to charge the battery at this rate until no further rise In specific gravity Is noted over a four hour period. 10 Alternatively, a trickle charger charging at the rate of 1.5 amps can safely be used overnight. 11 Specially rapid boost charges which are claimed to restore the power of the battery in t to 2 hours are not recommended, as they can cause serious damage to the battery plates through overheating, 12 While charging the battery, note that the temperature of the electrolyte should never exceed 37.8*C(100°F),
Page 170 of 225
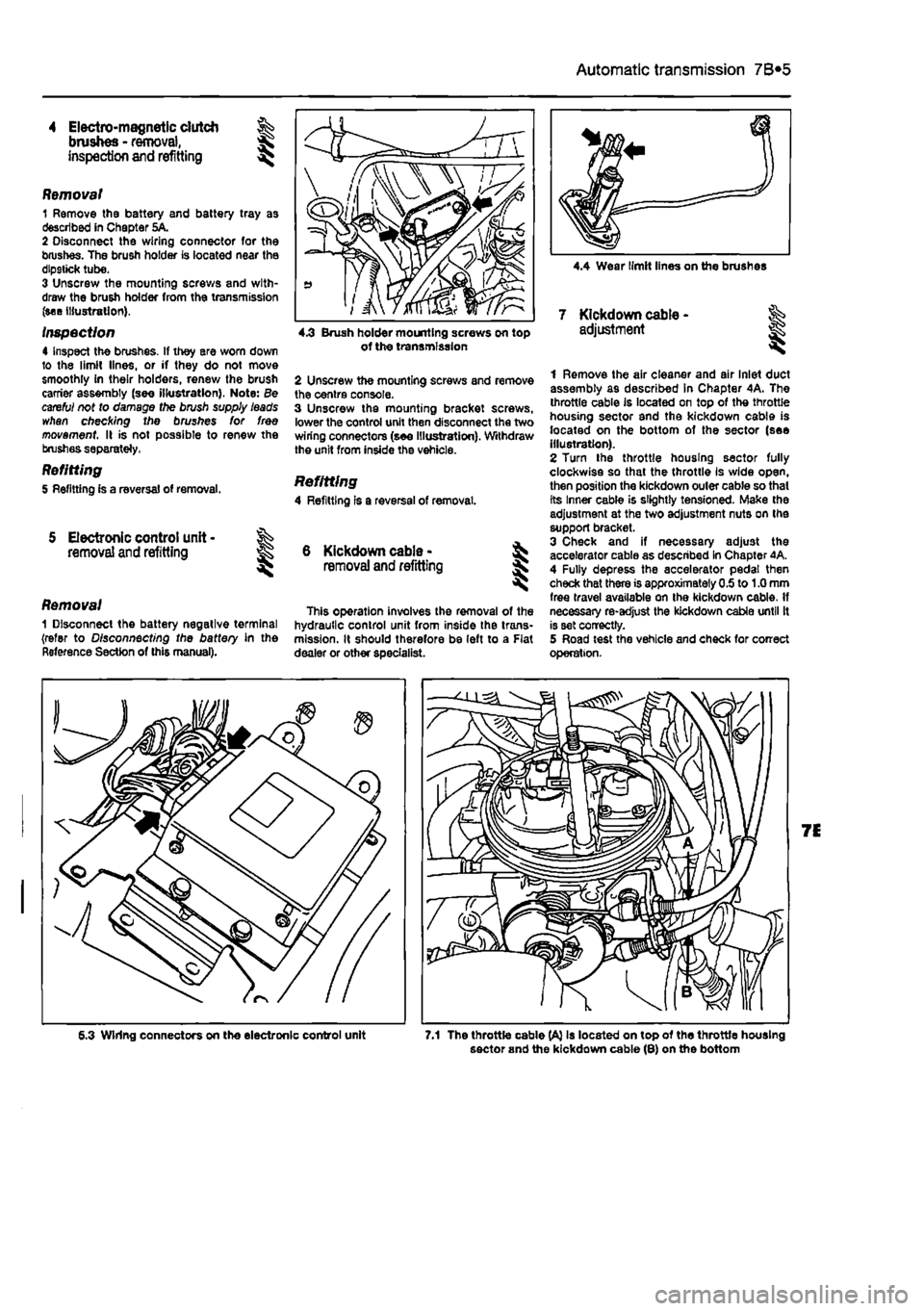
Automatic transmission 7B«5
4 Electro-magnetic dutch brushes - removal, inspection and refitting
Removal 1 Remove the battery and battery tray as described in Chapter 5A. 2 Disconnect the wiring connector for the brushes. The brush holder is located near the dlp9tick tube. 3 Unscrew the mounting screws and with-draw the brush holder from the transmission (see illustration).
inspection 4 Inspect the brushes. If they ere worn down to the limit lines, or if they do not move smoothly in their holders, renew the brush carrier assembly (see illustration}. Note: Be careful not to damage the brush supply leads whan checking the brushes for free movement II is not possible to renew the brushes separately,
Refitting 5 Refitting is a reversal of removal.
5 Electronic control unit • removal and refitting
Removal 1 Disconnect the battery negative terminal (refer to Disconnecting the battery in the Reference Section of this manual).
4.3 Brush holder mounting screws on top of tho transmission
2 Unscrew the mounting screws and remove the centre console. 3 Unscrew the mounting bracket screws, lower the control unit then disconnect the two wiring connectors (see Illustration). Withdraw the unit from inside the vehicle.
Refitting 4 Refitting Is a reversal of removal.
6 Kickdown cable -removal
and
refitting I
This operation involves the removal of the hydraulic control unit from inside the trans-mission. It should therefore be left to a Flat dealer or other specialist.
1 Remove the air cleaner and air Inlet duct assembly as described in Chapter 4A. The throttle cable is located on top of the throttle housing sector and the kickdown cable is located on the bottom of the sector (see Illustration). 2 Turn the throttle housing sector fully clockwise so that the throttle Is wide open, then position the kickdown outer cable so thai its Inner cable is slightly tensioned. Make the adjustment at the two adjustment nuts on the support bracket. 3 Check and if necessary adjust the accelerator cable as described In Chapter 4A. 4 Fully depress the accelerator pedal then check that there is approximately 0.5 to 1.0 mm free travel available on the kickdown cable. If necessary re-adjust the kickdown cable until It is set correctly. 5 Road test the vehicle and check for correct operation.
6.3 Wiring connectors on tho electronic control unit 7.1 The throttle cable (A} Is located on top of the throttle housing sector and the kickdown cable (8) on the bottom
Page 185 of 225
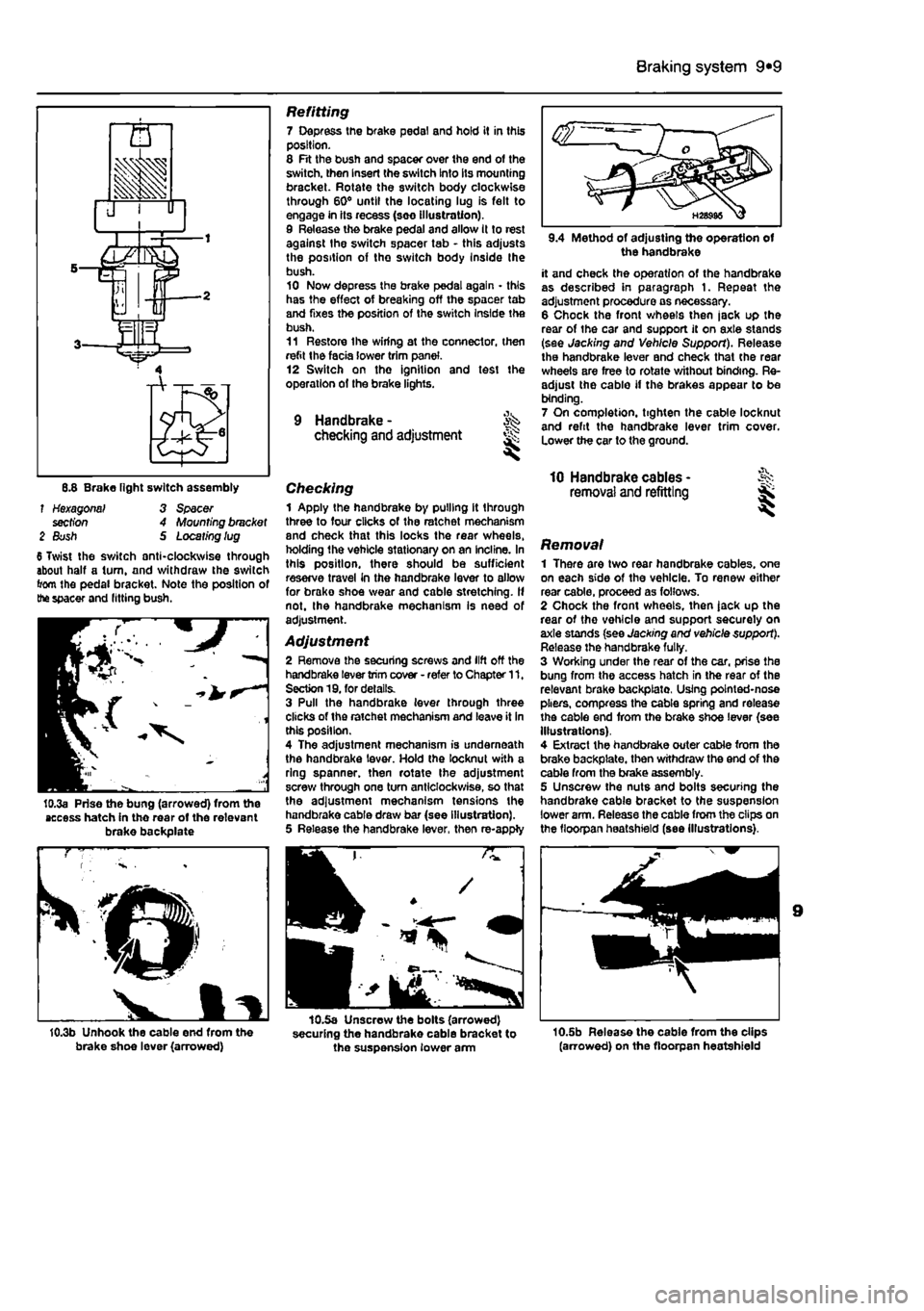
Braking system 9®9
6.8 Brake light switch assembly f Hexagonal' 3 Spacer section 4 Mounting bracket 2 Bush S Locating lug 6 Twist the switch anti-clockwise through about half a turn, and withdraw the switch from the pedal bracket. Note the position of the spacer and fitting bush.
10.3a Prise the bung (arrowed) from the access hatch in the rear of the relevant brake backplate
10.3b Unhook the cable end from the brake shoe lever (arrowed)
Refitting 7 Depress the brake pedal and hold it in this position. 8 Fit the bush and spacer over the end of the switch, then Insert the switch Into its mounting bracket. Rotate the switch body clockwise through 60° until the locating lug is felt to engage in its recess (seo illustration). 9 Release the brake pedal and allow It to rest against the switch spacer tab - this adjusts the position of the switch body Inside Ihe bush. 10 Now depress the brake pedal again - this has the effect of breaking off the spacer tab and fixes the position of the switch Inside the bush. 11 Restore Ihe wiring at the connector, then refit the facia lower trim panel. 12 Switch on the ignition and test the operation of the brake lights.
9 Handbrake - ^ checking and adjustment
Checking 1 Apply the handbrake by pulling it through three to four clicks of the ratchet mechanism and check that this locks the rear wheels, holding the vehicle stationary on an incline. In this position, there should be sufficient reserve travel in the handbrake lever to allow for brako shoe wear and cable stretching. If not. Ihe handbrake mechanism Is need of adjustment.
Adjustment 2 Remove the securing screws and lift off the handbrake lever trim cover - refer to Chapter 11. Section 19. for details. 3 Pull the handbrake lever through three clicks of the ratchet mechanism and leave it in this position. 4 The adjustment mechanism is underneath the handbrake lever. Hold the locknut with a ring spanner, then rotate the adjustment screw through one turn anticlockwise, so that the adjustment mechanism tensions the handbrake cable draw bar (see illustration). 5 Release the handbrake lever, then re-apply
10.5a Unscrew the bolts (arrowed) securing the handbrake cable bracket to the suspension lower arm
the handbrake it and check the operation of the handbrake as described in paragraph 1. Repeat the adjustment procedure as necessary. 6 Chock the front wheels then |ack up the rear of the car and support it on axle stands (see Jacking and Vehicle Support). Release the handbrake lever and check that the rear wheels are free to rotate v/ithout binding. Re-adjust the cable if the brakes appear to be binding. 7 On completion, tighten the cable locknut and refit the handbrake lever trim cover. Lower the car to the ground.
10 Handbrake cables -removal and refitting
Removal 1 There are two rear handbrake cables, one on each side of the vehicle. To renew either rear cable, proceed as follows. 2 Chock the front wheels, then jack up the rear of tho vehicle and support securely on axle stands (see Jacking and vehicle support). Release the handbrake fully, 3 Working under the rear of the car, prise the bung from the access hatch in the rear of the relevant brake backplato, Using pointed-nose pliers, compress the cable spring and release the cable end from the brake shoe lever (see Illustrations). 4 Extract the handbrake outer cable from the brake backplate. then withdraw the end of the cable from the brake assembly. 5 Unscrew the nuts and bolts securing the handbrake cable bracket to the suspension lower arm. Release the cable from the clips on the floorpan heatshield (see Illustrations).
10.5b Release the cable from the clips (arrowed) on the floorpsn heatshield
Page 217 of 225
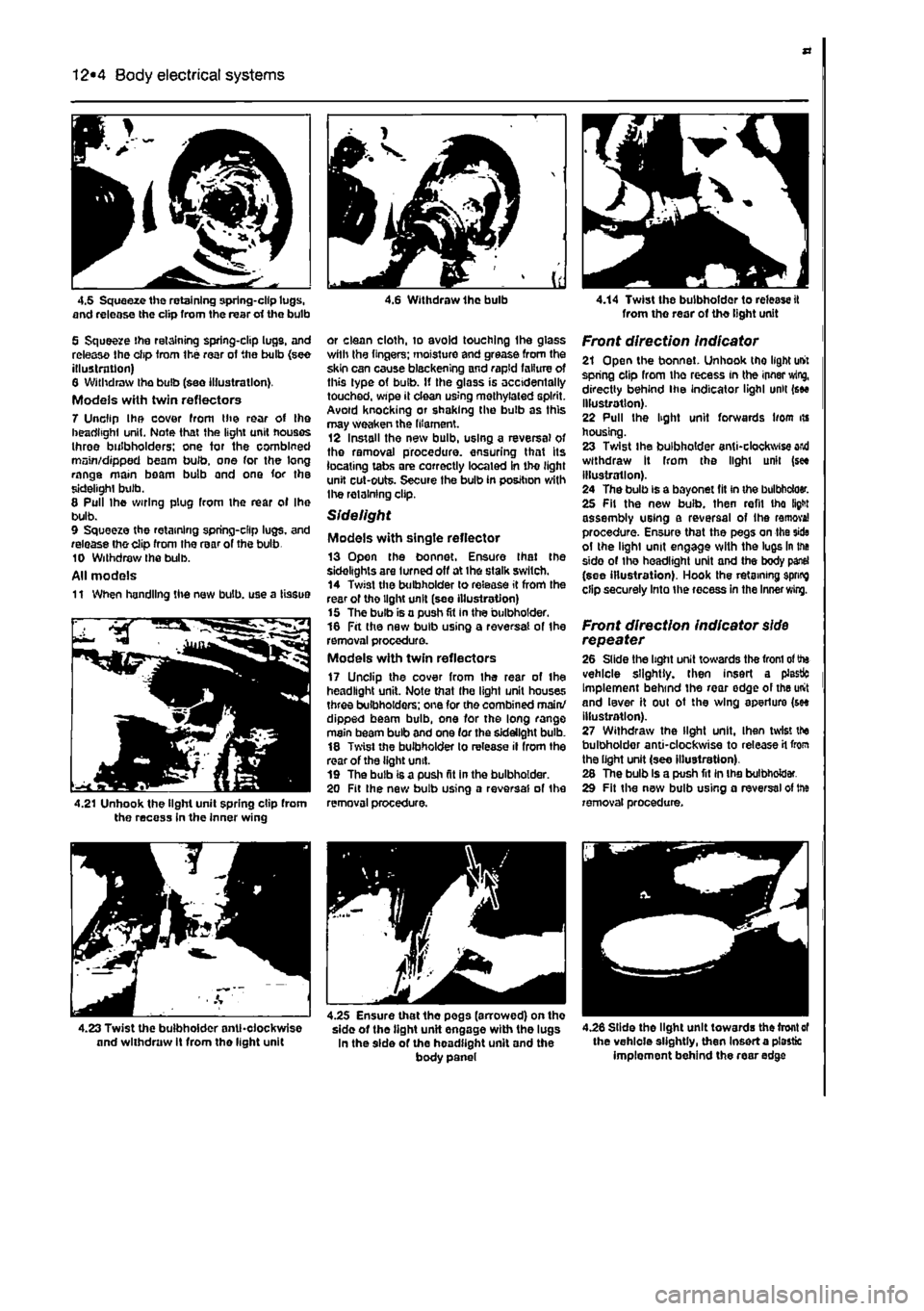
12*4 Body electrical systems
4.5 Squeeze the retaining spring-clip lugs, and release the clip from the rear erf the bulb
5 Squeeze the retaining spring-clip lugs, and release Ihe clip Irom the rear of the bulb {see illustration) 6 Withdraw the bulb (see illustration). Models with twin reflectors 7 Unclip Ihe cover from the rear of the headlight unit. Note that the light unit houses three bulbholders; one tor the combined main/dipped beam bulb, one for the long range main beam bulb and one for the sidelight bulb. 8 Pull Ihe wiring plug from the rear ol Ihe bulb. 9 Squeeze the retaining spring-clip lugs, and release tho clip from the rear of the bulb 10 Withdraw Ihe bulb. All models 11 When handling the new bulb, use a tissue
4.21 Unhook the light unit spring clip from the recess in the inner wing
4 6 Withdraw Ihe bulb
or clean cloth, to avoid touching Ihe glass wilh Ihe lingers; moisture and grease from the skin can cause blackening and rapid failure of this type of bulb. If the glass is accidentally touched, wipe it clean using methylated spirit. Avoid knocking or shaking the bulb as this may weaken the filament. 12 Install the new bulb, using a reversal of the removal procedure, ensuring that its locating tabs are correctly located in tho light unit cut-outs. Secure the bulb in position with Ihe retaining clip.
Sidelight
Models with single reflector 13 Open the bonnet. Ensure Ihat the sidelights are turned off at ihe stalk switch. 14 Twist the bulbholder lo release it from the rear of tho light unit (see illustration) 15 The bulb is a push fit in the bulbholder. 16 Fit the new bulb using a reversal of the removal procedure. Models with twin reflectors 17 Unclip the cover from Ihe rear of Ihe headlight unit. Note that Ihe light unit houses three bulbholders; one for the combined main/ dipped beam bulb, one for the long range main beam bulb and one (or the sidelight bulb. 18 Twist the bulbholder to release il from the rear of the light unit. 19 The bulb is a push fit in the bulbholder. 20 Fit Ihe new bulb using a reversal of the removal procedure.
4.14 Twist the bulbholder to release it from tho rear of tho light unit
Front direction indicator 21 Open the bonnet. Unhook tho light unit spring clip from the recess in the innsr wing, directly behind ihe indicator lighl unit (see illustration). 22 Pull the light unit forwards liom its housing. 23 Twist ihe bulbholder anti-clockwise and withdraw It from the light unit (see illustration). 24 The bulb is a bayonet fit in the bulbbdoer. 25 Fit the new bulb, then refil tho fight assembly using a reversal of Ihe remove! procedure. Ensure that the pegs on the side ol the lighl unit engage with the lugs in the side of the headlight unit and the body panel (see illustration). Hook the retaining spring clip securely Into the recess in the Inner
wing.
Front direction indicator
side
repeater 26 Slide the light unit towards the from
ol
the vehicle slightly, then insert a plastic Implement behind the rear edge of the unit and lever it oul ot the wing aperture (see illustration). 27 Withdraw the light unit. Ihen twist the bulbholder anti-clockwise to release
H
from the light unit (see illustration). 28 The bulb is a push fit in the bulbholder. 29 Fit the new bulb using a reversal of trie removal procedure.
4.26 Slide the light unit towards the front
of
the vehicle slightly, then Insert a plastic implement behind the rear edge
4.23 Twist the bulbholder anticlockwise and withdraw It from the light unit
4.25 Ensure that the pegs (arrowed) on tho sido of tho tight unit engage with the lugs In the side of the headlight unit and the body panel
Page 218 of 225
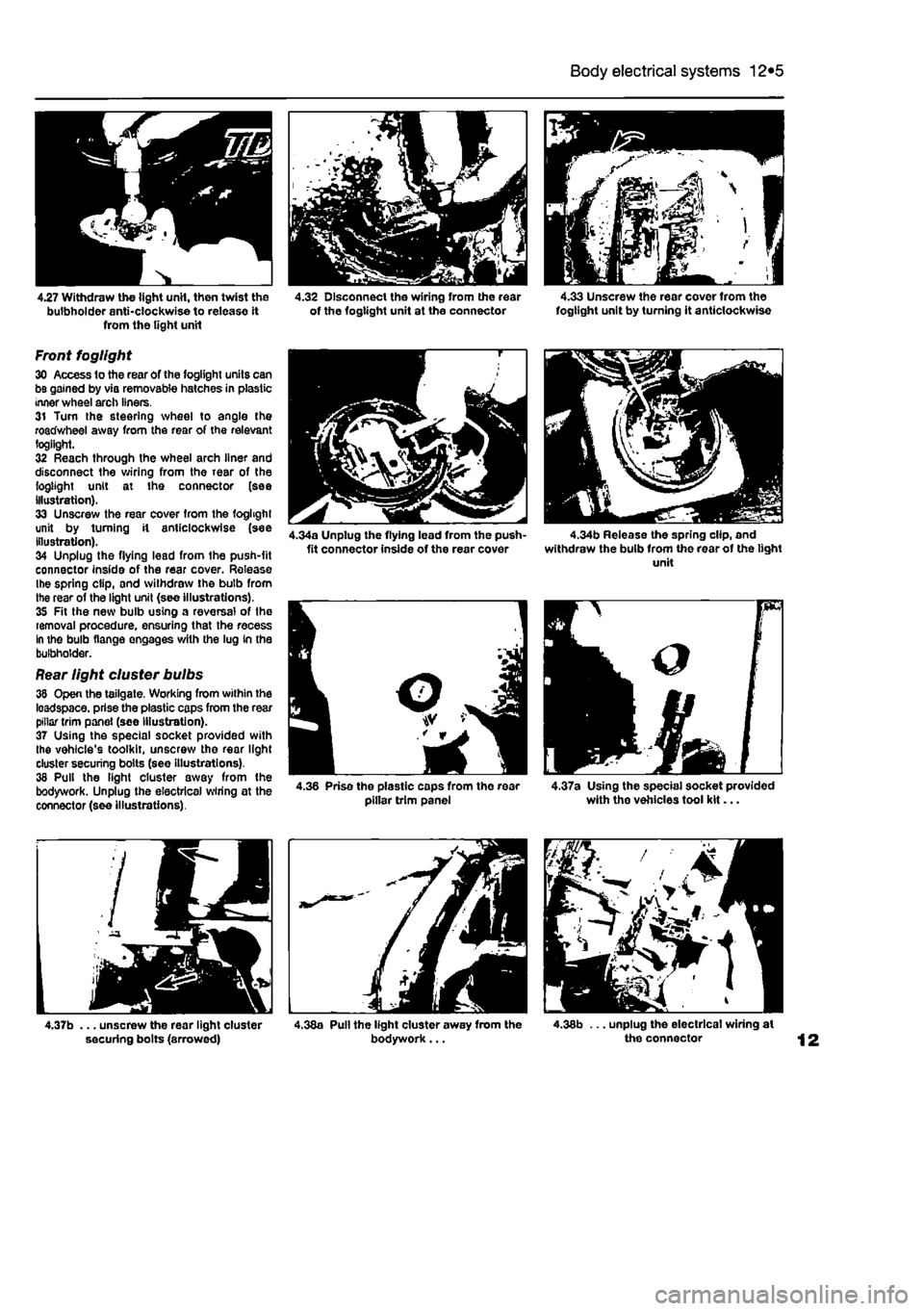
Body electrical systems 12*5
4.27 Withdraw the tight unH, then twist the bulbholder anti-clockwise to release it from the light unit
Front fogllght 30 Access to the rear of the fogllght units can be gained by via removable hatches in plastic inner wheel arch liners. 31 Turn the steering wheel to angle the roadwheel away from the rear of the relevant fogllght. 32 Reach through the wheel arch liner and disconnect the wiring from the rear of the fogllght unit at the connector (see illustration). 33 Unscrew the rear cover from the foghghl unit by turning it anticlockwise (see Illustration). 34 Unplug the flying lead from the push-fit connector inside of the rear cover. Release Ihe spring clip, and withdraw the bulb from the rear of the light unit (see illustrations). 35 Fit the new bulb using a reversal of Ihe removal procedure, ensuring that the recess In the bulb flange engages with the lug in the bulbholder.
Rear light cluster bulbs 38 Open the tailgate. Working from within the loadspace. prise the plastic caps from the rear pillar trim panel (see illustration). 37 Using the special socket provided with the vehicle's toolkit, unscrew the rear light cluster securing bolts (see illustrations). 38 Pull the light cluster away from the bodywork. Unplug the electrical wiring at the connector (see illustrations).
4.37b ... unscrew the rear light cluster securing bolts (arrowed)
4.32 Disconnect the wiring from the rear 4.33 Unscrew the rear cover from the of the fogtight unit at the connector fogllght unit by turning It anticlockwise
4.38a Pull the light cluster away from the 4.38b ... unplug the electrical wiring at bodywork... the connector
Page 220 of 225
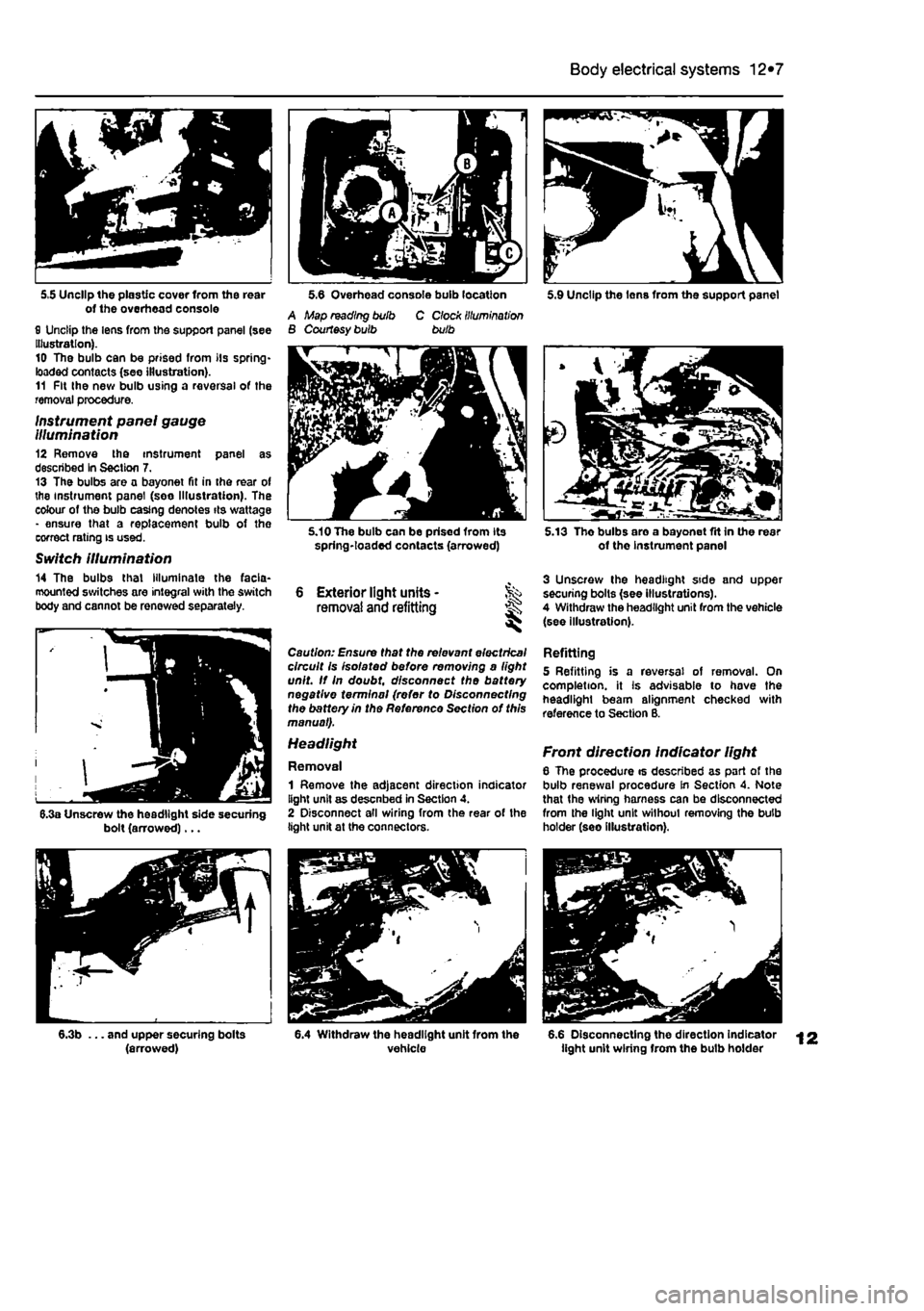
Body electrical systems 12*7
5,5 Unclip the plastic cover from the rear of the overhead console 0 Unclip the lens from the support panel (see Illustration). 10 The bulb can be prised from its spring-loaded contacts (see illustration). 11 Fit the new bulb using a reversal of the removal procedure.
Instrument panel gauge Illumination 12 Remove the instrument panel as described In Section 7. 13 The bulbs are a bayonet fit in the rear of the instrument panel (see Illustration). The colour of the bulb casing denotes its wattage - ensure that a replacement bulb of the correct rating is used.
Switch illumination 14 The bulbs that Illuminate the facia-mounted switches are integral with the switch body and cannot be renewed separately.
5.6 Overhead console bulb location 5.9 Unclip the Ions from the support panel A Map reading bulb B Courtesy bulb C Clock illumination bulb
6.3a Unscrew the headlight side securing bolt (arrowed)...
5.10 The bulb can be prised from its spring-loaded contacts (arrowed)
6 Exterior light units • removal and refitting ^ ^
Caution: Ensure that the relevant electrical circuit is isolated be/ore removing a light unit. If In doubt, disconnect the battery negative terminal (refer to Disconnecting the battery in the Reference Section of this manual).
1 Remove the adjacent direction indicator light unit as descnbed in Section 4. 2 Disconnect all wiring from the rear of the light unit at the connectors.
5.13 Tho bulbs are a bayonet fit in the rear of the instrument panel
3 Unscrew the headlight side and upper securing bolts (see illustrations). 4 Withdraw the headlight unit from the vehicle (see illustration).
Refitting 5 Refitting is a reversal of removal. On completion, it Is advisable to hove the headlight beam alignment checked with reference to Section B.
Front direction indicator light 6 The procedure is described as part of the bulb renewal procedure In Section 4. Note that the wiring harness can be disconnected from the light unit without removing the bulb holder (seo illustration).
6.3b ... and upper securing bolts (arrowed) 6.4 Withdraw the headlight unit from the vehicle 6.6 Disconnecting the direction indicator light unit wiring from the bulb holder