drain bolt FIAT PUNTO 1998 176 / 1.G User Guide
[x] Cancel search | Manufacturer: FIAT, Model Year: 1998, Model line: PUNTO, Model: FIAT PUNTO 1998 176 / 1.GPages: 225, PDF Size: 18.54 MB
Page 83 of 225
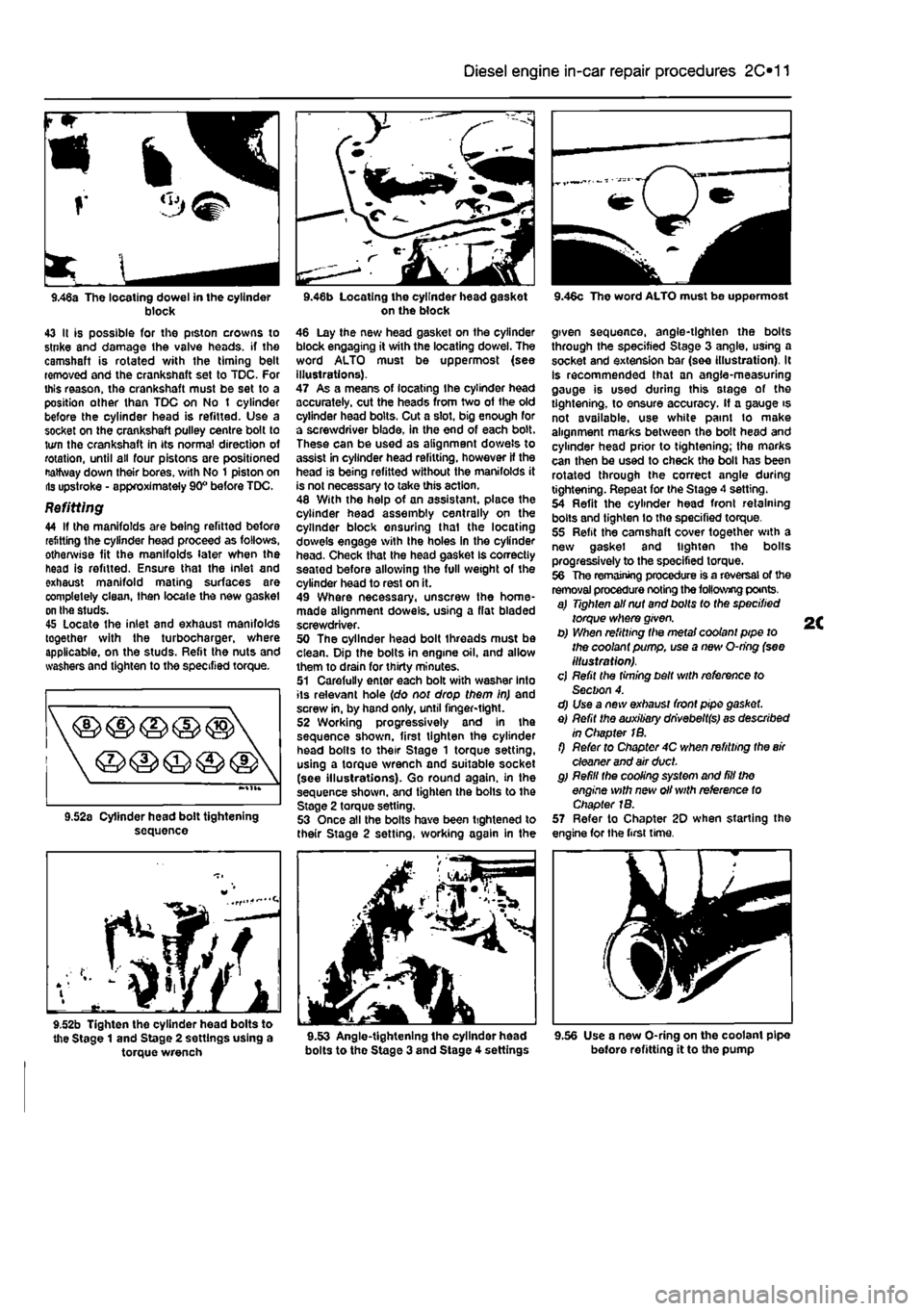
Diesel engine in-car repair procedures 2C*11
r
<3^
9.46a The locating dowel in the cylinder block 43 It is possible for the ptston crowns to stnke and damage the valve heads, if the camshaft is rotated v/ith the timing belt removed and the crankshaft set to TDC. For this reason, the crankshaft must be set to a position other than TDC on No t cylinder before the cylinder head is refitted. Use a socket on the crankshaft pulley centre bolt to turn the crankshaft in its normal direction of rotation, until all four pistons are positioned Halfway down their bores, v/ith No 1 piston on lis upstroke - approximately 90° before TDC.
Refitting 44 If the manifolds are being refitted before refitting the cylinder head proceed as follows, otherwise fit the manifolds later when the head is refitted. Ensure thai the inlet and exhaust manifold mating surfaces are completely clean, then locale the new gasket on the studs. 45 Locate the inlet and exhaust manifolds together with the turbocharger, where applicable, on the studs. Refit the nuts and washers and tighten to the specified torque.
sequence
f^/f
9.52b Tighten the cylinder head bolts to the Stage 1 and Stage 2 settings using a torque wrench
on the block 46 Lay the new head gasket on the cylinder block engaging it with the locating dowel. The word ALTO must be uppermost (see illustrations). 47 As a means of locating Ihe cylinder head accurately, cut the heads from two of the old cylinder head bolts. Cut a slot, big enough for a screwdriver blade, in the end of each bolt. These can be used as alignment dowels to assist in cylinder head refitting, however If the head is being refitted without the manifolds it is not necessary to take this action. 48 With the help of an assistant, place the cylinder head assembly centrally on the cylinder block ensuring thai the locating dowels engage with Ihe holes in the cylinder head. Check that the head gasket Is correctly seatod before allowing the full weight of the cylinder head to rest on it. 49 Where necessary, unscrew the home-made alignment dowels, using a flat bladed screwdriver. 50 The oyllnder head bolt threads must be clean. Dip the bolts in engine oil. and allow them to drain for thirty minutes. 51 Carefully enter each bolt with washer into its relevant hole (do not drop them in) and screw in, by hand only, until finger-tight. 52 Working progressively and In the sequence shown, first tighten the cylinder head bolts to their Stage 1 torque setting, using a torque wrench and suitable socket (see illustrations). Go round again, in the sequence shown, and tighten the bolls to the Stage 2 torque setting. 53 Once all the bolts have been tightened to their Stage 2 setting, working again in the
bolts to the Stage 3 and Stage 4 settings
9.46c The word ALTO must be uppermost
given sequence, angle-tighten the bolts through the specified Stage 3 angle, using a socket and extension bar (see illustration). It Is recommended that an angle-measuring gauge is used during this stage of the tightening, to ensure accuracy. If a gauge is not available, use white paint to make alignment marks between the bolt head and cylinder head prior to tightening; the marks can then be used to check tho bolt has been rotated through the correct angle during tightening. Repeat for the Stage 4 setting. 54 Refit the cylinder head front retaining bolts and tighten lo the specified torque. 55 Refit the camshaft cover together with a new gasket and tighten the bolts progressively to the specified torque. 56 The remaining procedure is a reversal of the removal procedure noting the following points. a) Tighten all nut and bolts to the specified torque where given. b) When refitting the metal coolant pipe to the coolant pump, use a new O-ring (see illustration). cj Refit the timing belt with reference to Section 4. d) Use a new exhaust front pipe gasket. e) Refit the auxiliary dhvebeltfs) as described in Chapter 1B. f) Refer to Chapter 4C when refitting the
air
cleaner and air duct. g) Refill the cooling system and fill the engine with new oil with reference to Chapter 1B. 57 Refer to Chapter 20 when starting the engine for the first time.
9.56 Use a new O-ring on the coolant pipe before refitting it to the pump
Page 85 of 225
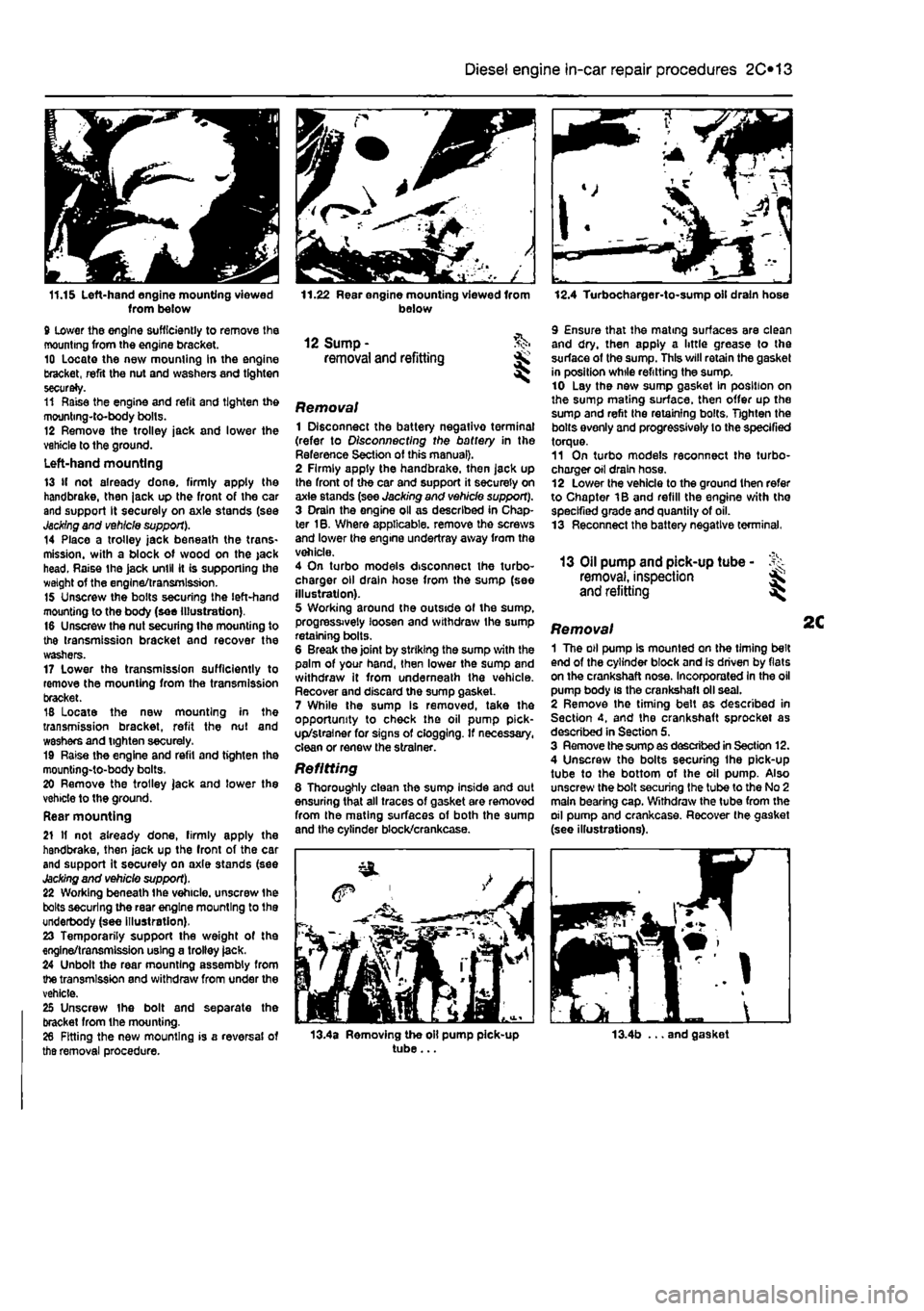
11.15 Left-hand engine mounting viewed from below 9 lower the engine sufficiently to remove the mounting from the engine bracket. 10 Locate the new mounting in the engine bracket, refit the nut and washers and tighten securely. 11 Raise the engine and refit and tighten the mounting-to-body bolts. 12 Remove the trolley jack and lower the vehicle to the ground. Left-hand mounting 13 If not already done, firmly apply the handbrake, then jack up the front of the car and support It securely on axle stands (see
Jacking
and vehicle support). 14 Place a trolley jack beneath the trans-mission. with a block of wood on the jack head. Raise the jack until it is supporting the weight of the engine/transmission. 15 Unscrew the bolts securing the left-hand mounting to the body (see Illustration). 16 Unscrew the nut securing the mounting to the transmission bracket and recover the washers. 17 Lower the transmission sufficiently to remove the mounting from the transmission bracket. 18 Locate the new mounting in the transmission bracket, refit the nut and washers and tighten securely. 19 Raise the engine and refil and tighten the mounting-to-body bolts. 20 Remove the trolley jack and lower the vehicle to the ground. Rear mounting 21 If not already done, firmly apply the handbrake, then jack up the front of the car and support it securely on axle stands (see
Jacking
and vehicle support). 22 Working beneath the vehicle, unscrew the bolts securing the rear engine mounting to the underbody (see illustration). 23 Temporarily support the weight of the engine/transmission using a trolley jack. 24 Unbolt the rear mounting assembly from the transmission and withdraw from under the vehicle. 25 Unscrew the bolt and separate the bracket from the mounting. 28 Fitting the new mounting is a reversal of tha removal procedure.
Diesel engine in-car repair procedures 2C*11
11.22 Rear engine mounting viewed from below
12 Sump -removal and refitting
Removal 1 Disconnect the battery negativo terminal (refer to Disconnecting the battery in the Reference Section of this manual). 2 Firmly apply the handbrake, then jack up the front of the car and support it securely on axie stands (see Jacking and vehicle support). 3 Drain the engine oil as described in Chap-ter 1B. Where applicable, remove the screws and lower the engine undertray away from the vehicle. 4 On turbo models disconnect the turbo-charger oil drain hose from the sump (see illustration). 5 Working around the outside of the sump, progressively loosen and withdraw the sump retaining bolts. 6 Break the joint by striking the sump with the palm of your hand, then lower the sump and withdraw it from underneath the vehicle. Recover and discard the sump gasket. 7 While the sump Is removed, take the opportunity to check the oil pump pick-up/strainer for signs of clogging. If necessary, clean or renew the strainer.
Refitting 8 Thoroughly clean the sump inside and out ensuring that all traces of gasket are removed from the mating surfaces of both the sump and the cylinder block/crankcase.
12.4 Turbocharger-to-sump oil drain hose
9 Ensure that the mating surfaces are clean and dry, then apply a little grease to the surface of the sump. This will retain the gasket in position while refitting the sump. 10 Lay the new sump gasket In position on the sump mating surface, then offer up the sump and refit the retaining bolts. Tighten the bolts evenly and progressively lo the specified torque. 11 On turbo models reconnect the turbo-charger oil drain hose. 12 Lower the vehicle to the ground then refer to Chapter 1B and refill the engine with the specified grade and quantity of oil. 13 Reconnect the battery negative terminal.
13 Oil pump and pick-up tube -removal, inspection and refitting
Removal 1 The oil pump Is mounted on the timing belt end of the cylinder block and is driven by flats on the crankshaft nose. Incorporated In the oil pump body is the crankshaft oil seal. 2 Remove the timing belt as described in Section 4, and the crankshaft sprocket as described in Section 5. 3 Remove the sump as described in Section 12. 4 Unscrew the bolts securing Ihe pick-up tube to the bottom of the oil pump. Also unscrew the bolt securing the tube to the No 2 main bearing cap. Withdraw the tube from the oil pump and crankcase. Recover the gasket (see illustrations).
13.4a Removing the oil pump pick-up tube... 13.4b ... and gasket
Page 87 of 225
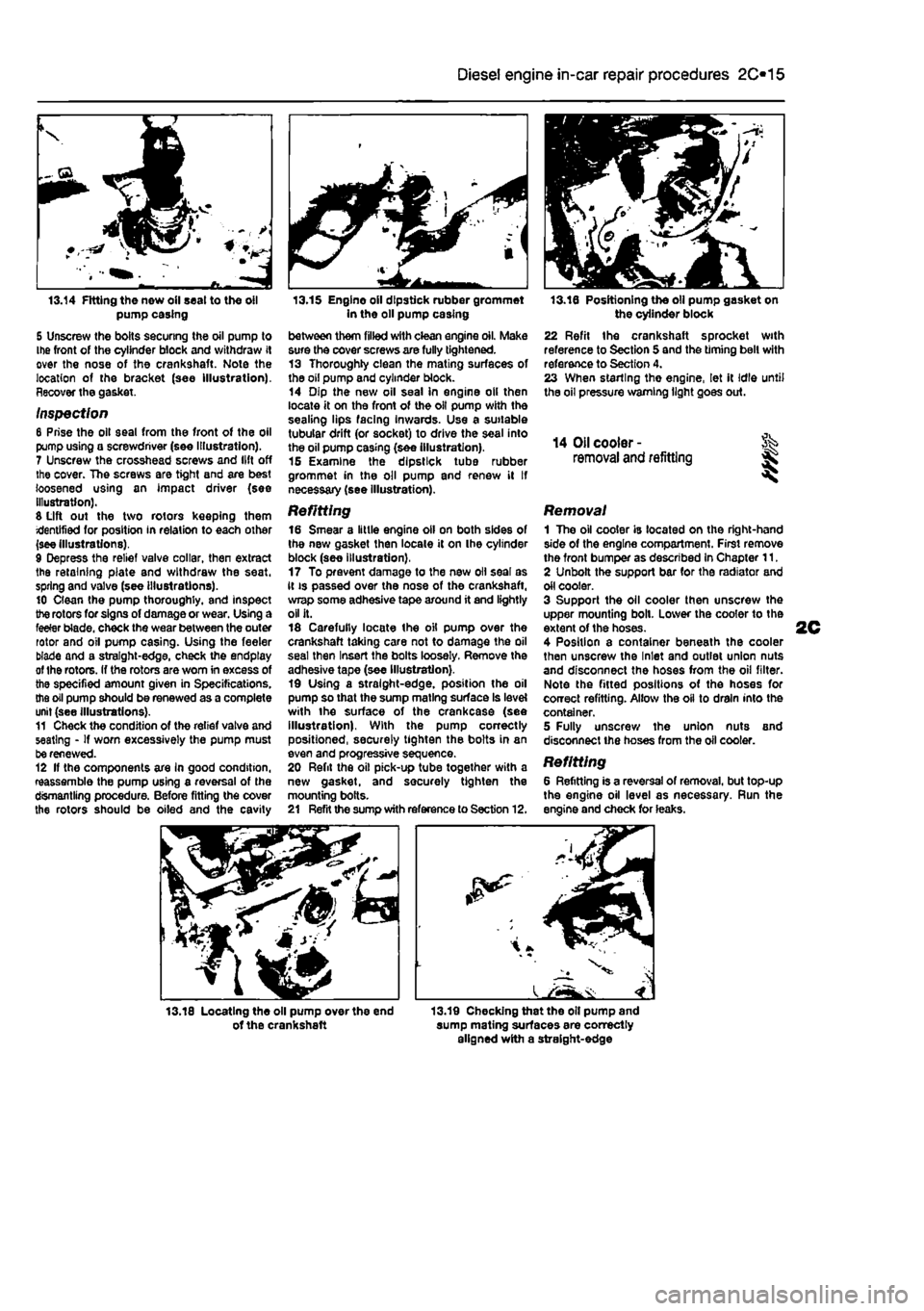
Diesel engine in-car repair procedures 2C*11
X
a 13.14 Fitting the new oil seal to the oil pump casing
S Unscrew the bolts securing the oil pump to Ihe front of the cylinder block and withdraw it over the nose of the crankshaft. Note the location of the bracket (see Illustration). Recover the gasket.
Inspection 8 Prise the oil seal from the front of the oil pump using a screwdriver (see Illustration). 7 Unscrew the crosshead screws and lift off the cover. The screws are tight and are best loosened using an impact driver (see illustration). S Lift out the two rotors keeping them identified for position in relation to each other (see illustrations). 9 Depress the relief valve collar, then extract the retaining plate and withdraw the seat, spring and valve (see illustrations). 10 Clean the pump thoroughly, and Inspect the rotors for signs of damage or wear. Using a feeler blade, check the wear between the outer rotor and oil pump casing. Using the feeler blade and a straight-edge, check the endptay of Ihe rotors. If the rotors are worn in excess of the specified amount given in Specifications, the oil pump should be renewed as a complete unit (see Illustrations). 11 Check the condition of the relief valve and seating - If worn excessively the pump must be renewed. 12 If the components are In good condition, reassemble the pump using a reversal of the dismantling procedure. Before fitting the cover the rotors should be oiled and the cavity
13.15 Engine oil dipstick rubber grommet in the oil pump casing between them filled with clean engine oil. Make sure the cover screws are fully tightened. 13 Thoroughly clean the mating surfaces of the oil pump and cylinder block. 14 Dip the new oil seal in engine oil then locate it on the front of the oil pump with the sealing lips facing Inwards. Use a suitable tubular drift (or socket) to drive the seal into the oil pump casing (see illustration). 16 Examine the dipstick tube rubber grommet in the oil pump and renew il If necessary (see illustration).
Refitting 16 Smear a little engine oil on both sides of the new gasket then locate it on the cylinder block (see illustration), 17 To prevent damage to the new oil seal as it is passed over the nose of the crankshaft, wrap some adhesive tape around it and lightly oil it. 18 Carefully locate the oil pump over the crankshaft taking care not to damage the oil seal then Insert the bolts loosely. Remove the adhesive tape (see Illustration). 19 Using a straight-edge, position the oil pump so that the sump mating surface Is level with the surface of the crankcase (see illustration). With the pump correctly positioned, securely tighten the bolts in an even and progressive sequence. 20 Refit the oil pick-up tube together with a new gasket, and securely tighten the mounting bolts. 21 Refit the sump with reference to Section 12.
13.16 Positioning the oil pump gasket on the cylinder block 22 Refit the crankshaft sprocket with reference to Section 5 and the timing belt with reference to Section 4. 23 When starling the engine, let it Idle until the oil pressure warning light goes out.
14 Oil cooler -removal and refitting I I
Removal 1 The oil cooler is located on the right-hand side of the engine compartment. First remove the front bumper as described In Chapter 11. 2 Unbolt the support bar for the radiator and oil cooler. 3 Support the oil cooler then unscrew the upper mounting boll. Lower the cooler to the extent of the hoses. 4 Position a container beneath the cooler then unscrew the Inlet and outlet union nuts and disconnect the hoses from the oil filter. Note the fitted positions of the hoses for correct refitting. Allow the oil to drain into the container. 5 Fully unscrew the union nuts and disconnect the hoses from the oil cooler.
Refitting 6 Refitting is a reversal of removal, but top-up the engine oil level as necessary. Run the engine and check for leaks.
13.18 Locating the oil pump over the end of the crankshaft 13.19 Checking that the oil pump and sump mating surfaces are correctly aligned with a straight-edge
Page 114 of 225
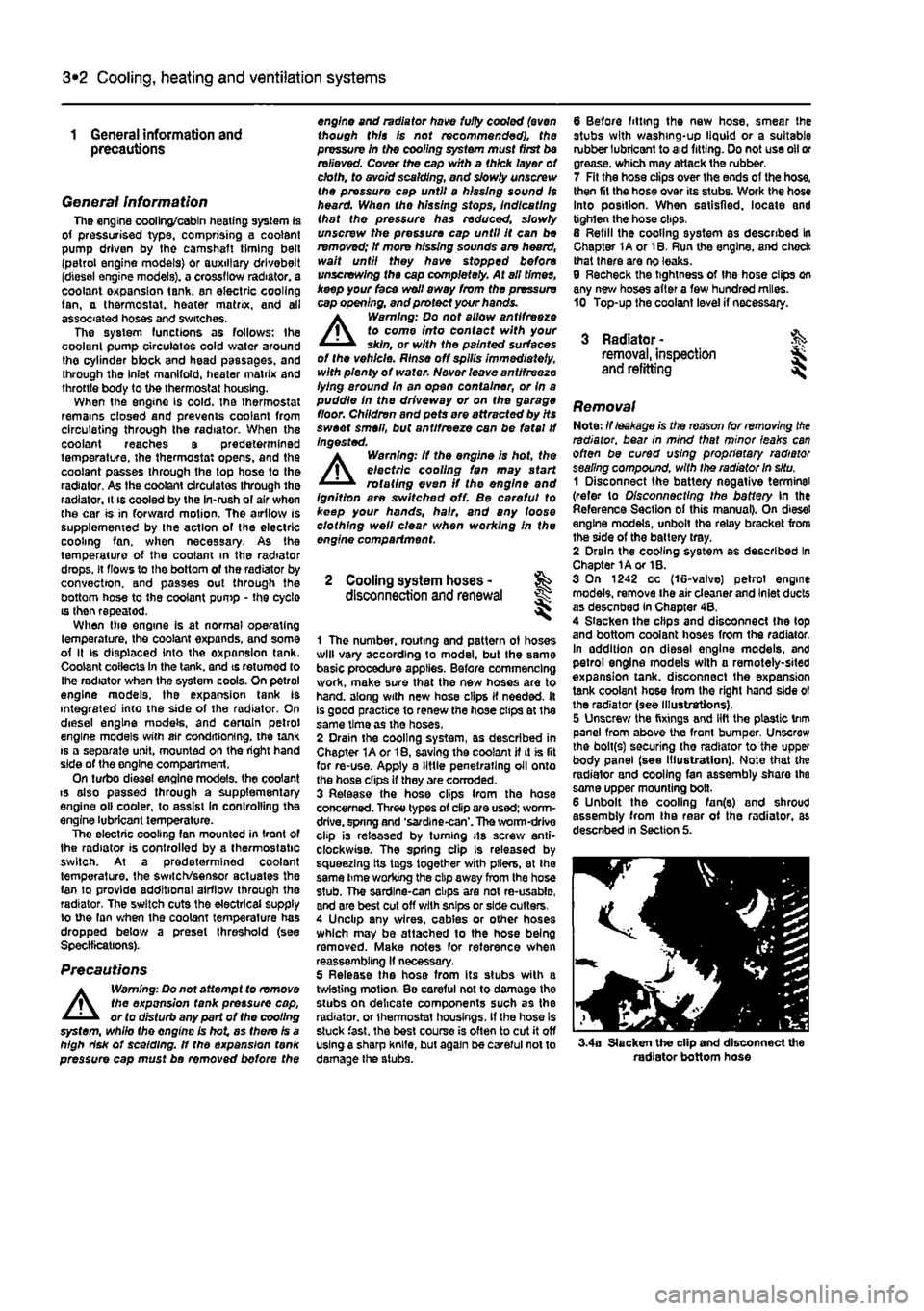
3*2 Cooling, heating and ventilation systems
1 General information and precautions
Genera/ Information The engine cooling/cabin heating system is ol pressurised type, comprising a coolant pump driven by the camshaft timing belt (petrol engine models) or auxiliary drlvebelt (diesel engine models), a crossllow radiator, a coolant expansion tank, an electric cooling fan, a thermostat, heater matrix, and all associated hoses and switches. The system functions as follows: Ihe coolant pump circulates cold water around the cylinder block and head passages, and through the Inlet manifold, heater matrix and throttle body to the thermostat housing. When the engine Is cold, the thermostat remains closed and prevents coolant from circulating through the radiator. When the coolant reaches a predetermined temperature, the thermostat opens, and the coolant passes through the top hose to the radiator. As the coolant circulates through the radiator, it is cooled by the in-rush of air when the car is in forward motion. The airllow is supplemented by the action of the electric cooling fan. when necessary, As the temperature of the coolant in the radiator drops, it flows to the bottom of the radiator by convection, and passes out through the bottom hose to the coolant pump - the cycle is then repeatod, When the engine is at normal operating temperature, the coolant expands, and some of It is displaced into the expansion tank. Coolant collects In the tank, and ts returned to Ihe radiator when the system cools. On petrol engine models, the expansion tank is integrated into the side of the radiator. On diesel engine models, and certain petrol engine models with air conditioning, the tank is a separate unit, mounted on the right hand side of the engine compartment. On turbo diesel engine models, the coolant is also passed through a supplementary engine oil cooler, to assist In controlling the engine lubricant temperature. Tho electric cooling fan mounted in front of the radiator is controlled by a thermostatic switch. At a predetermined coolant temperature, the swilch/sensor actuates the tan lo provide additional airflow through the radiator, The switch cuts the electrical supply to the Ion when the coolant temperature has dropped below a preset threshold (see Specifications).
Precautions
A
Warning: Do not attempt to remove the expansion tank pressure cap, or to disturb any part of the cooling system, whlio the engine is hot, as then is a high risk of scalding, tf the expansion tank pressure cap must be removed before the
engine and radiator have fulty cooled (even though this is not recommended?, the pressure in the cooling system must first be relieved. Cover the cap with a thick layer of cloth, to avoid scalding, and slowly unscrew the pressuro cap until a hissing sound Is heard. When the hissing stops, indicating that the pressure has reduced, slowly unscrew the pressure cap until it can be removed; If more hissing sounds are heard, wait until they have stopped before unscrewing the cap completely. At all times, keep your face well away from the pressure cap opening, and protect your hands.
A
Warning: Do not allow antifreeze to come into contact with your skin, or with the painted surfaces of the vehicle. Rinse off spills immediately, with plenty of water. Never leave antifreeze lying around in an open container, or In a puddle In the driveway or on the garage floor. Children and pets are attracted by its sweet smell, but antifreeze can be fatal tf ingested.
A
Warning: If the engine is hot, the electric cooling fan may start rotating even if the engine and ignition are switched off. Be careful to keep your hands, hair, and any loose clothing well clear when working In the engine compartment.
2 Cooling system hoses - f&> disconnection and renewal ^
1 The number, routing and pattern of hoses will vary according to model, but the same basic procedure applies. Before commencing work, make sure that the new hoses are to hand, along wilh new hose clips if needed, it is good practice to renew the hose clips at the same time as the hoses. 2 Drain the cooling system, as described in Chapter 1A or 18, saving the coolant if it is fit for re-use. Apply a little penetrating oil onto the hose clips if they are corroded. 3 Release the hose clips from the hose concerned. Three types of clip are used; worm-drive. spring and 'sardine-can'. The worm-drive clip is released by turning its screw anti-clockwise. The spring clip Is released by squeezing Its tags together with pliers, at the same time working the cbp away from the hose stub. The sardine-can clips are not re-usable, and are best cut off with snips or side cutters. 4 Unclip any wires, cables or other hoses which may be attached to the hose being removed. Make notes for reference when reassembling If necessary. 5 Release the hose from its stubs with a twisting motion. Be careful not to damage the stubs on deltcate components such as the radiator, or thermostat housings. If the hose Is stuck fast, the best course is often to cut it off using a sharp knife, but again be careful not to damage the stubs.
6 Before fitting the new hose, smear the stubs with washing-up liquid or a suitable rubber lubricant to aid fitting. Do not use oil or grease, which may attack the rubber. 7 Fit the hose clips over the ends of the hose, then fit the hose over its stubs. Work the hose Into position. When satisfied, locate and tighten the hose dips. 6 Refill the cooling system as described In Chapter 1A or 1B. Run the engine, and chock that there are no leaks. 9 Recheck the tightness of Ihe hose clips on any new hoses after a few hundred miles. 10 Top-up the coolant level if necessary.
3 Radiator -
removal,
inspection and refitting
Removal Note: If leakage is the reason for removing
the
radiator, bear In mind that minor leaks can often be cured using proprietary radiator sealing compound, with the radiator in situ. 1 Disconnect the battery negative terminal (refer to Disconnecting the battery In the Reference Section of this manual). On diesel engine models, unbolt the relay bracket from the side of the battery tray. 2 Drain the cooling system as described In Chapter 1A or 1B. 3 On 1242 cc (16-valve) petrol engine models, remove the air cleaner and Inlet ducts as desenbed In Chapter 4B, 4 Slacken the clips and disconnect Ihe (op and bottom coolant hoses from the radiator. In addition on diesel engine models, and petrol engine models with a remotely-sited expansion tank, disconnect the expansion tank coolant hose from the right hand side ol the radiator (see Illustrations), 5 Unscrew the fixings and lift the plastic trim panel from above the front bumper Unscrew the bolt(s) securing tho radiator to the upper body panel (see Illustration). Note that the radiator and cooling fan assembly share the same upper mounting bolt. 6 Unbolt the cooling fan(e) and shroud assembly from Ihe rear ot the radiator, as described in Section 5.
3.4a Slacken the clip and disconnect the radiator bottom hose
Page 115 of 225
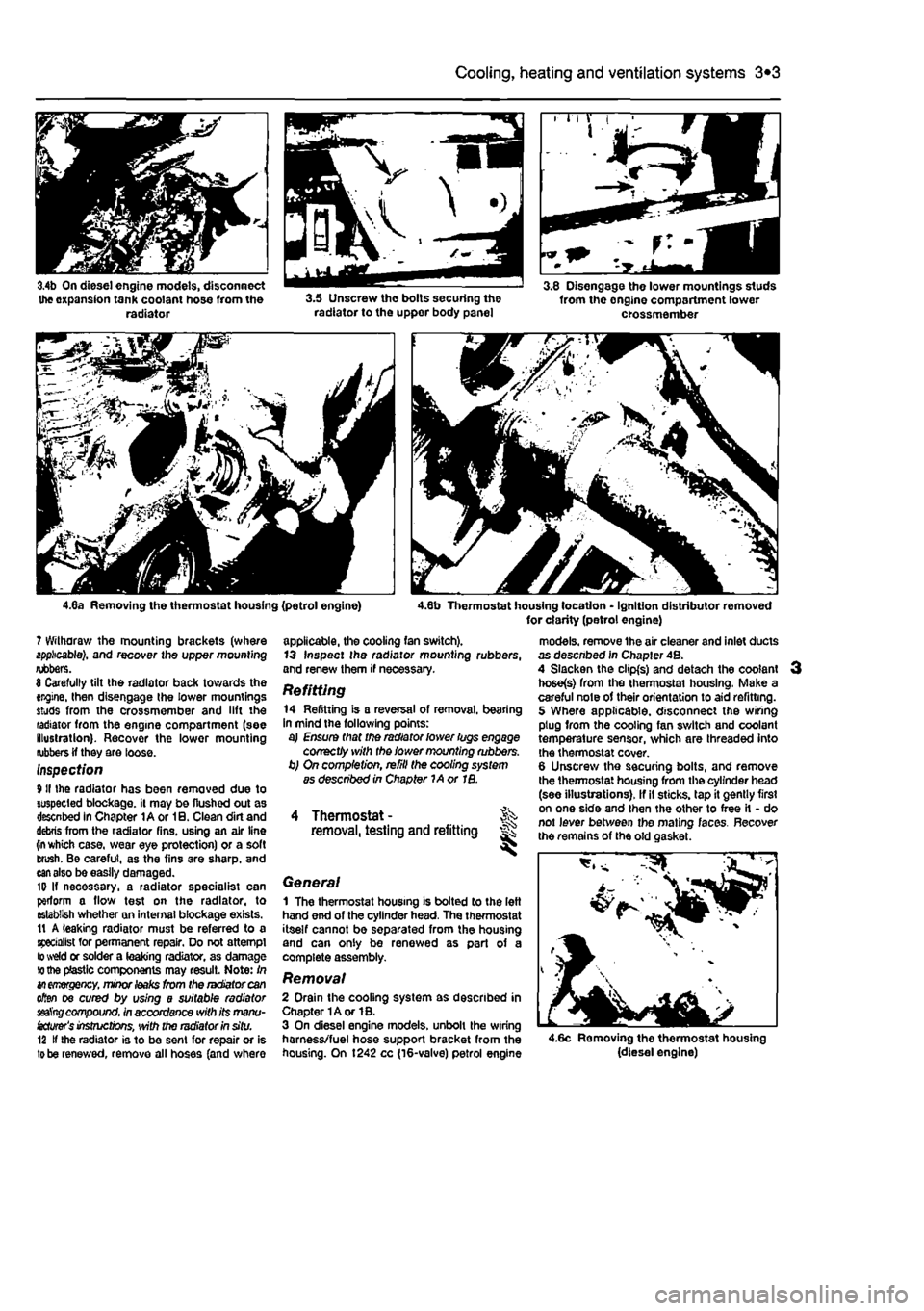
3*2 Cooling, heating and ventilation systems
3.4b On diesel engine models, disconnect the expansion tank coolant hose from the radiator 3.5 Unscrew the bolts securing the radiator to the uppor body panel
3.8 Disengage the lower mountings studs from the onglne compartment lower crossmember
4.6a Removing the thermostat housing (petrol engine) 4.6b Thermostat housing location - Ignition distributor removed for clarity (petrol engine) ? Withdraw the mounting brackets (where applicable), and recover the upper mounting rubbers. 8 Carefully tilt the radiator back towards the engine, then disengage the lower mountings studs from the crossmember and lift the radiator from the engine compartment (see illustration). Recover the lower mounting rubbers if they are loose. Inspect/on 9II the radiator has been removed due to suspected blockage, it may be flushed out as descnbed in Chapter lAor 10. Clean dirt and debris from the radiator fins, using an air line fn which case, wear eye protection) or a soft Brush. Be careful, as the fins are sharp, and
can
also be easily damaged. ID If necessary, a radiator specialist can perform a flow test on the radiator, to establish whether an internal blockage exists. 11 A leaking radiator must be referred to a specialist for permanent repair. Do not attempt to weld or solder a leaking radiator, as damage to the plastic components may result. Note: In
an emergency,
minor
leaks
from the radiator can often be cured by using a suitable radiator seat'ng compound, in accordance with its manu-
facturer's
instructions, with the radiator in situ. 12 If the radiator is to be sent for repair or is
to
be renewed, remove all hoses (and where
applicable, the cooling fan switch). 13 Inspect Ihe radiator mounting rubbers, and renew them if necessary. Refitting 14 Refitting is a reversal of removal, bearing in mind the following points: a) Ensure that the radiator lower lugs engage correctly with the lower mounting rubbers. b) On completion, refill the cooling system as described in Chapter 1A or IB.
Thermostat - Jk removal, testing and refitting #
General 1 The thermostat housing Is bolted to the left hand end of the cylinder head. The thermostat itself cannot be separated from the housing and can only be renewed as part of a complete assembly.
Removal 2 Drain the cooling system as described in Chapter 1A or 1B. 3 On diesel engine models, unbolt the wiring harness/fuel hose support bracket from the housing. On 1242 cc (16-valve) petrol engine
models, remove the air cleaner and inlet ducts as descnbed in Chapter 4B. 4 Slacken the clipfs) and detach the coolant hose(s) from the thermostai housing, Make a careful note of their orientation to aid refitting. 5 Where applicable, disconnect the wiring plug from the cooling fan switch and coolant temperature sensor, which are threaded into the thermostat cover. 6 Unscrew the securing bolts, and remove the thermostat housing from the cylinder head (see illustrations). If it sticks, tap it gently first on one side and then the other to free it - do not lever between the mating faces. Recover the remains of the old c,
4.6c Removing the thermostat housing (diesel engine)
Page 117 of 225
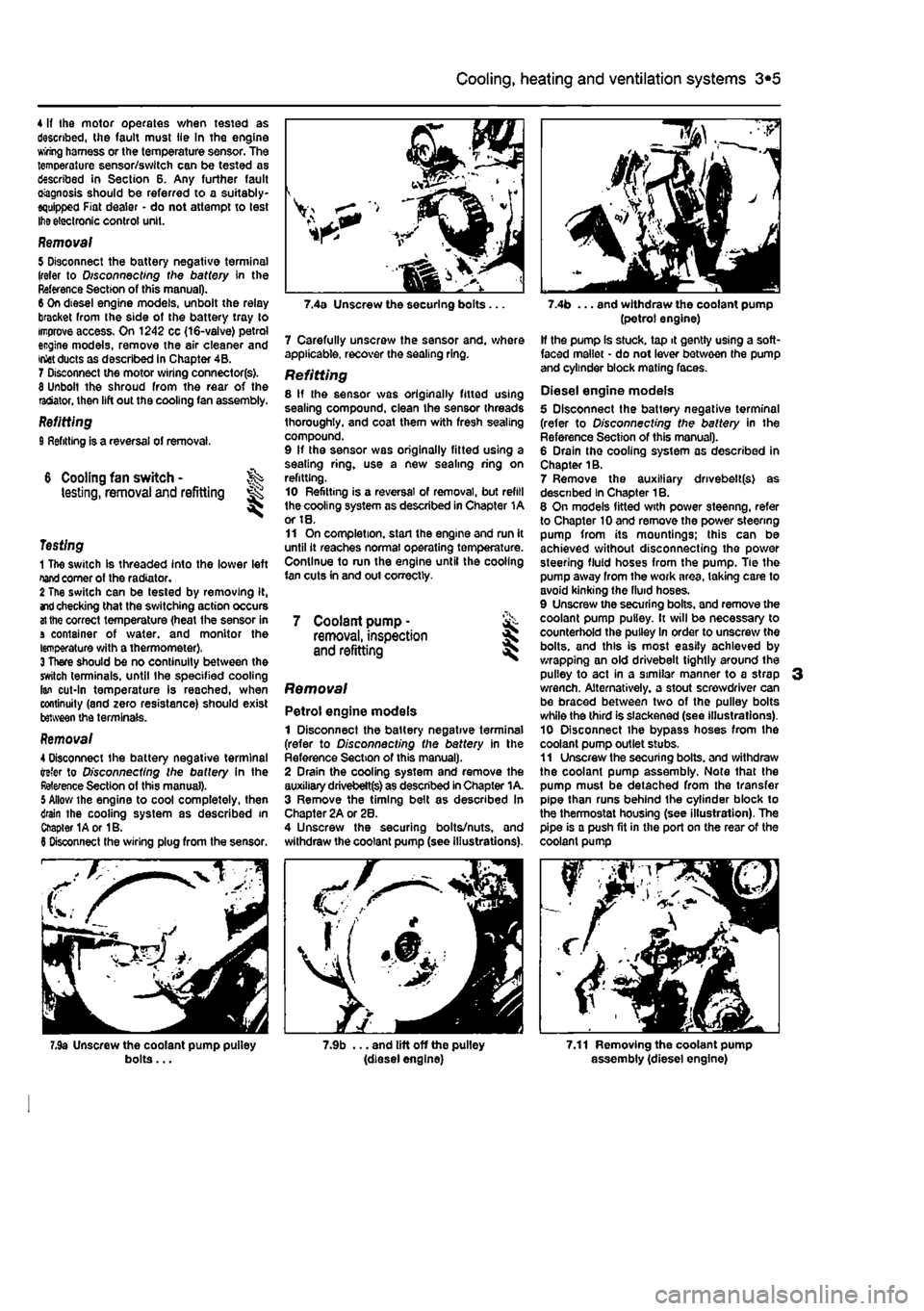
3*2 Cooling, heating and ventilation systems
4 If the motor operates when tested as described, (he fault must lie In the engine wring harness or the temperature sensor. The temperature sensor/switch can be tested as described in Section 6. Any further fault Diagnosis should be referred to a suitably-equipped Fiat dealer - do not attempt to test
Ihe
electronic control unit.
Removal 5 Disconnect the battery negative terminal (refer to D/scon oecf/ng the battery in the Reference Section of this manual). 6 On diesel engine models, unbolt the relay bracket from the side of the battery tray to improve access. On 1242 cc {16-valve) petrol engine models, remove the air cleaner and
inset
ducts as described in Chapter 4B. 1 Disconnect the motor wiring connectorfs). 8 Unbolt the shroud from the rear of the ratiator. then lift out the cooling fan assembly. Refitting 9 Refitting is a reversal of removal
6 Cooling fan switch -testing, removal and refitting ^
Testing 1 The switch is threaded into the lower left
nand
comer of the radiator. 2 The switch can be tested by removing it,
and
checking that the switching action occurs
at
the correct temperature {heat the sensor in a container of water, and monitor the temperature with a thermometer). 3 There should be no continuity between the switch terminals, until Ihe specified cooling fan cut-In temperature Is reached, when continuity (and zero resistance) should exist between the terminals.
Removal 4 Disconnect the battery negative terminal refer to Disconnecting the battery in the Reference Section of this manual). 5 Allow the engine to cool completely, then drain the cooling system as described in Chapter 1Aor 1B. 6 Disconnect the wiring plug from the sensor.
bolts...
7 Carefully unscrew the sensor and. whore applicable, recover the sealing ring. Refitting 8 If the sensor was originally fitted using sealing compound, clean the sensor threads thoroughly, and coat them with fresh sealing compound. 9 If the sensor was originally fitted using a sealing ring, use a new sealing ring on refitting. 10 Refitting is a reversal of removal, but refill the cooling system as described in Chapter 1A or 18. 11 On completion, start the engine and run it until it reaches normal operating temperature. Continue to run the engine until the cooling fan cuts in and out correctly.
7 Coolant pump • & removal, inspection 5 and refitting
Removal
Petrol engine models 1 Disconnect the battery negative terminal (refer to Disconnecting the battery in the Reference Section of this manual). 2 Drain the cooling system and remove the auxiliary drivebett(s) as described In Chapter 1 A. 3 Remove the timing belt as described In Chapter 2A or 28. 4 Unscrew the securing bolts/nuts, and withdraw the coolant pump (see illustrations).
7.9b ... and lift off the pulley (diesel engine)
(petrol engine) If the pump Is stuck, tap it gently using a soft-faced mallet - do not lever between the pump and cylinder block mating faces.
Diesel engine models 5 Disconnect the battery negative terminal (refer to D/s connecting the battery in the Reference Section of this manual). 6 Drain the cooling system as described in Chapter 1B. 7 Remove the auxiliary drivebelt(s) as descnbed In Chapter 1B. 6 On models fitted with power steenng, refer to Chapter 10 and remove the power steering pump from its mountings; this can be achieved without disconnecting the power steering fluid hoses from the pump. Tie the pump away from the work area, taking care to avoid kinking the fluid hoses. 9 Unscrew the securing bolts, and remove the coolant pump pulley. It will be necessary to counterhold the pulley In order to unscrew the bolts, and this is most easily achieved by wrapping an old drivebelt tightly around the pulley to act in a similar manner to a strap 3 wrench. Alternatively, a stout screwdriver can be braced between two of the pulley bolts while the third is slackened (see illustrations). 10 Disconnect ihe bypass hoses from the coolant pump outlet stubs. 11 Unscrew the securing bolts, and withdraw the coolant pump assembly. Note that the pump must be detached from the transfer pipe than runs behind the cylinder block to the thermostat housing (see illustration). The pipe is a push fit in the port on the rear of the coolant pump
7.11 Removing the coolant pump assembly (diesel engine)
Page 118 of 225
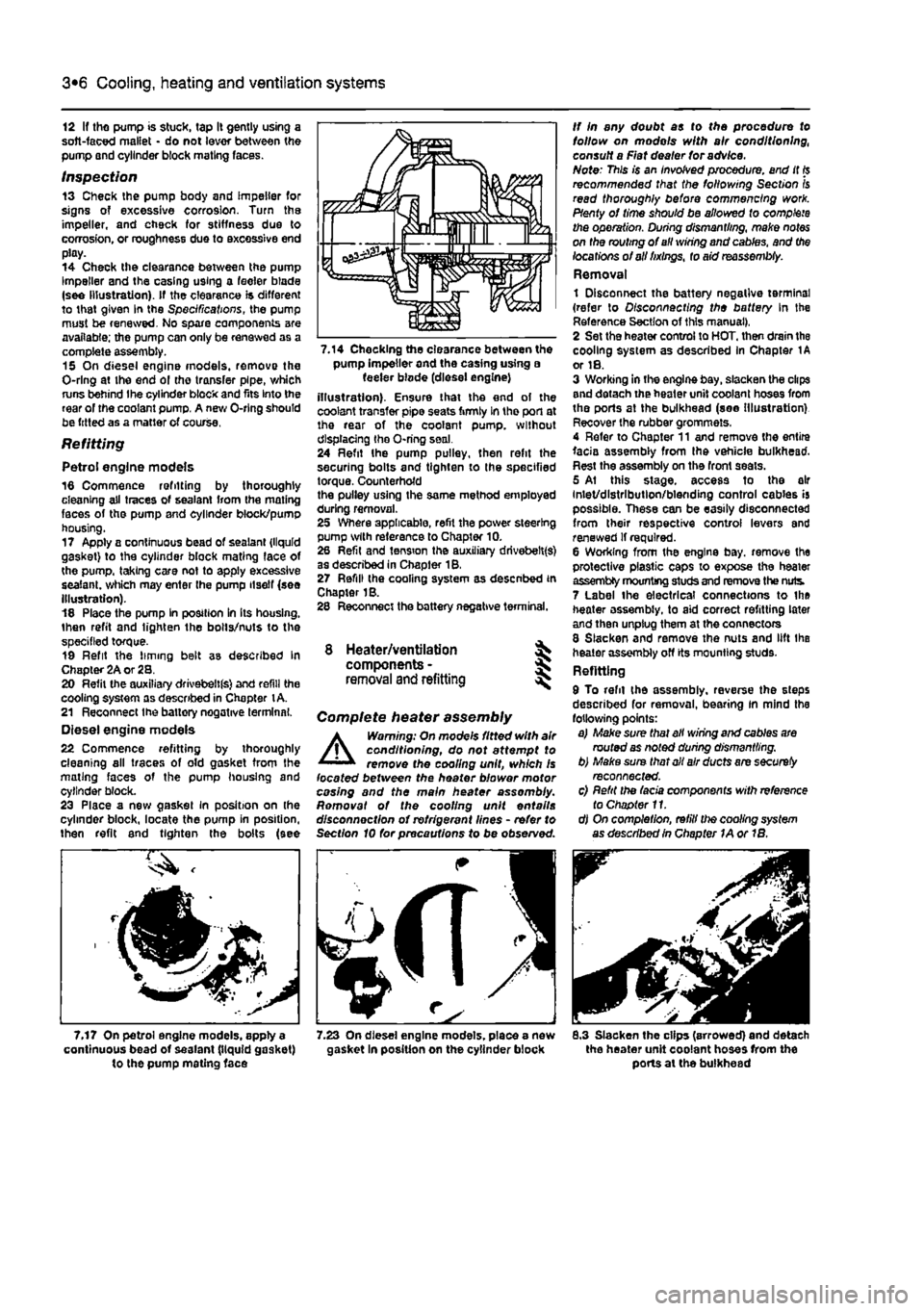
3*2 Cooling, heating and ventilation systems
12 If tho pump is stuck, tap It gently using a soft-faced mallet • do not lever between the pump and cylinder block mating faces.
Inspection 13 Check the pump body and impeller for signs of excessive corrosion. Turn the impeller, and check for stiffness due to corrosion, or roughness due to excessive end play. 14 Check the clearance between the pump Impeller and the casing using a feeler blade (see Illustration). If the clearance is different to that given In the Specifications, the pump must be renewed. No spare components are available; the pump can only be renewed as a complete assembly. 15 On diesel engine models, remove the O-rlng at the end ol the transfer pipe, which runs behind Ihe cylinder block and fits Into the rear of the coolant pump. A new O-rlng should be fitted as a matter of course.
Refitting
Petrol engine models 16 Commence refitting by thoroughly cleaning all traces of sealant from the mating faces of the pump and cylinder block/pump housing. 17 Apply a continuous bead of sealant {liquid gasket) to the cylinder block mating face of the pump, taking care not to apply excessive sealant, which may enter the pump itself (see Illustration). 18 Place the pump In position In Its housing, then refit and lighten the bolts/nuts to the specified torque. 19 Refit the liming belt as described In Chapter 2A or 28. 20 Refit the auxiliary drivebeltfs) and refill the cooling system as described in Chapter
t
A. 21 Reconnect Ihe battery negative terminal. Diesel engine models 22 Commence refitting by thoroughly cleaning all traces of old gasket from the mating faces of the pump housing and cylinder block. 23 Place a new gasket in position on (he cylinder block, locate the pump in position, then refit and tighten the bolts (see
7.17 On petrol engine models, apply a continuous bead of sealant (liquid gasket) to the pump mating face
pump Impeller and the casing using a feeler blode (diesel engine) illustration). Ensure that the end of the coolant transfer pipe seats firmly In tho port at the rear of the coolant pump, without displacing the O-ring seal. 24 Refit Ihe pump pulley, then refit the securing bolts and tighten to the specified torque. Counterhofd the pulley using the same method employed during removal. 25 Where applicable, refit the power steering pump with reference to Chapter 10. 26 Refit and tension the auxiliary drivebelt(s) as described in Chapter 18. 27 Refill (he cooling system as desenbed in Chapter 1B. 28 Reconnect the battery negative terminal.
8 Heater/ventilation components - § removal and refitting
Complete heater assembly
A
Warning: On mode's fitted with air conditioning, do not attempt to remove the cooling unit, which Is located between the heater blower motor casing and the main heater assembly. Romovat of the cooling unit entails disconnection of refrigerant lines - refer to Section 10 for precautions to be observed.
rfJS
8.3 Slacken the clips (arrowed) and detach the heater unit coolant hoses from the ports at the bulkhead
Page 125 of 225
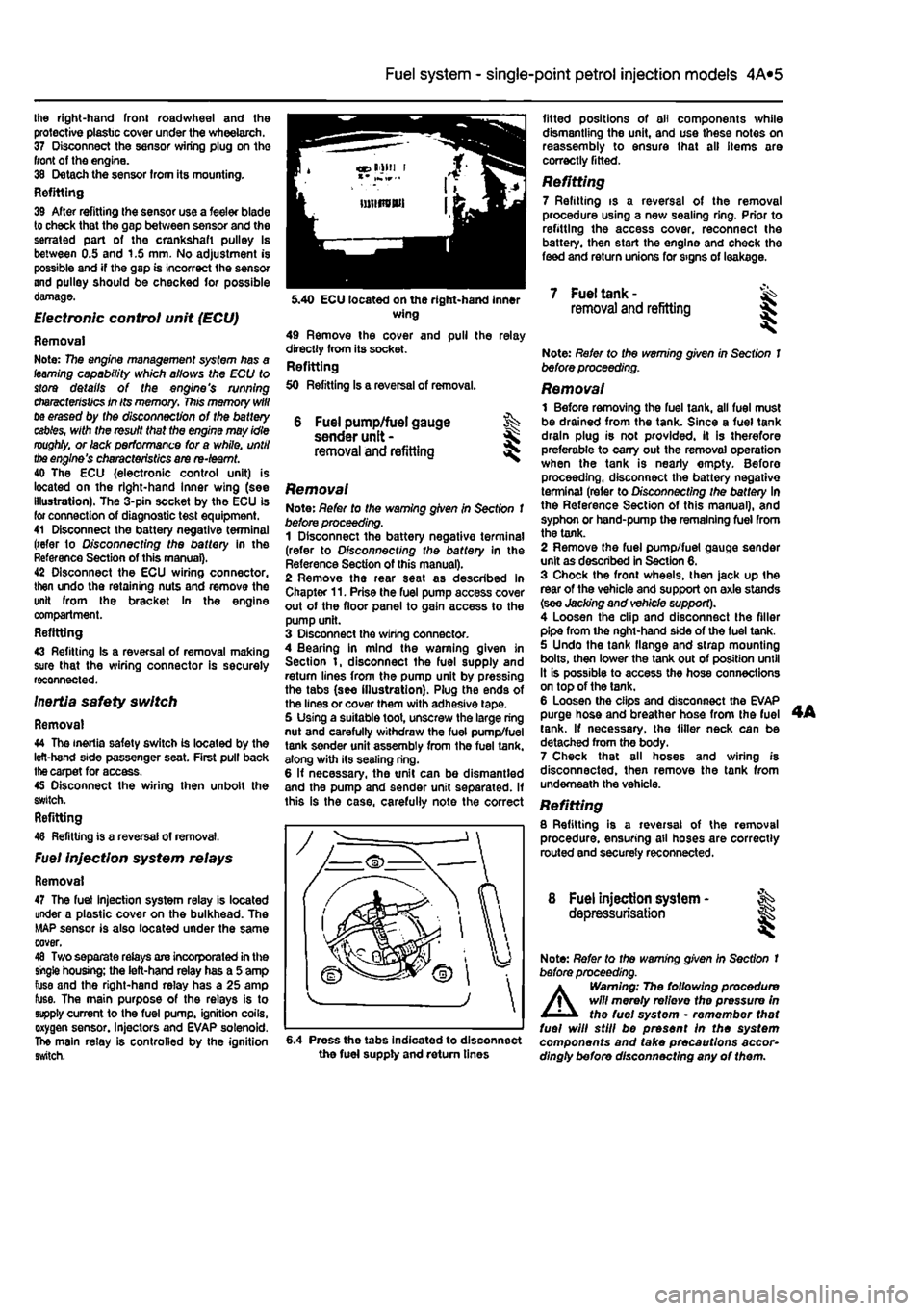
Ihe right-hand front roadwheel and the protective plastic cover under the wheelarch. 37 Disconnect the sensor wiring plug on the front of the engine. 38 Detach the sensor from its mounting. Refitting 39 After refitting Ihe sensor use a feeler blade to check that the gap between sensor and the serrated part of the crankshaft pulley Is between 0.5 and 1.S mm. No adjustment is possible and if the gap is incorrect the sensor and pulley should be checked for possible damage.
Electronic control unit (ECU)
Removal Note: 77ie engine management system has a (earning capability which allows the ECU to store details of the engine's running
characteristics
in its memory,
This
memory
will
tie erased by the disconnection of the battery
cables,
with the resuit that the engine may idle
roughly,
or lack performance for a while, until
the
engine's characteristics are re-teamt. 40 The ECU {electronic control unit) is located on the right-hand Inner wing (see illustration). The 3-pin socket by the ECU is for connection of diagnostic test equipment. 41 Disconnect the battery negative terminal (refer to D/sconnecffng the battery in the Reference Section of this manual). 42 Disconnect the ECU wiring connector, then undo the retaining nuts and remove the unit from the bracket In the engine compartment. Refitting 43 Refitting Is a reversal of removal making sure that the wiring connector is securely reconnected. Inertia safety switch
Removal 44 The inertia safety switch is located by the left-hand side passenger seat. First pull back
the
carpet for access. 45 Disconnect the wiring then unbolt the switch. Refitting 48 Refitting is a reversal of removal.
Fuel injection system relays
Removal 47 The fuel injection system relay is located under a plastic cover on the bulkhead. The MAP sensor is also located under the same cover. 48 Two separate relays are incorporated in the single housing; the left-hand relay has a 5 amp fuse and the right-hand relay has a 25 amp fuse. The main purpose of the relays is to supply current to the fuel pump, ignition coils, oxygen sensor. Injectors and EVAP solenoid. The main relay is controlled by the ignition switch.
4A*2 Fuel system - single-point petrol Injection models
6 Fuel pump/fuel gauge sender unit -removal and refitting
Removal Note: Refer to the warning given in Section 1 before proceeding. 1 Disconnect the battery negative terminal (refer to Disconnecting the battery in the Reference Section of this manual). 2 Remove the rear seat as described in Chapter 11. Prise the fuel pump access cover out of the floor panel to gain access to the pump unit. 3 Disconnect the wiring connector. 4 Bearing in mind the warning given in Section t, disconnect the fuel supply and return lines from the pump unit by pressing the tabs (see illustration). Plug the ends of the lines or cover them with adhesive tape. 5 Using a suitable toot, unscrew the large ring nut and carefully withdraw the fuel pump/fuel tank sender unit assembly from the fuel tank, along with its sealing ring. 6 If necessary, the unit can be dismantled and the pump and sender unit separated. If this is the case, carefully note the correct
fitted positions of oil components while dismantling the unit, and use these notes on reassembly to ensure that all items are correctly fitted.
Refitting 7 Refitting is a reversal of the removal procedure using a new sealing ring. Prior to refitting the access cover, reconnect the battery, then start the engine and check the feed and return unions for signs of leakage.
5.40 ECU located on the right-hand inner wing 49 Remove the cover and pull the relay directly from its socket. Refitting 50 Refitting Is a reversal of removal.
7 Fuel tank -removal and refitting
6.4 Press the tabs Indicated to disconnect the fuel supply and return tines
Note: Refer to the warning given in Section 1 before proceeding.
Removal 1 Before removing the fuel tank, all fuel must be drained from the tank. Since a fuel tank drain plug is not provided, it is therefore preferable to carry out the removal operation when the tank is nearly empty. Before proceeding, disconnect the battery negative terminal (refer to Disconnecting the battery In the Reference Section of this manual), and syphon or hand-pump the remaining fuel from the tank. 2 Remove the fuel pump/fuel gauge sender unit as described in Section 6. 3 Chock the front wheels, then jack up the rear of the vehicle and support on axle stands (see Jacking and vehicle support). 4 Loosen the clip and disconnect the filler pipe from the nght-hand side of the fuel tank. 5 Undo the tank flange and strap mounting bolts, then lower the tank out of position until It is possible to access the hose connections on top of the tank. 6 Loosen the clips and disconnect the EVAP purge hose and breather hose from the fuel tank. If necessary, the filler neck can be detached from the body. 7 Check that all hoses and wiring is disconnected, then remove the tank from underneath the vehicle. Refitting 8 Refitting is a reversal of the removal procedure, ensuring all hoses are correctly routed and securely reconnected.
8 Fuel injection system - ^ depressurisation
Note: Refer to the warning given In Section t before proceeding.
A
Warning; The following procedure will merely relievo the pressure in the fuel system • remember that fuel will still be present In the system components and take precautions accor-dingly before disconnecting any of them.
Page 126 of 225
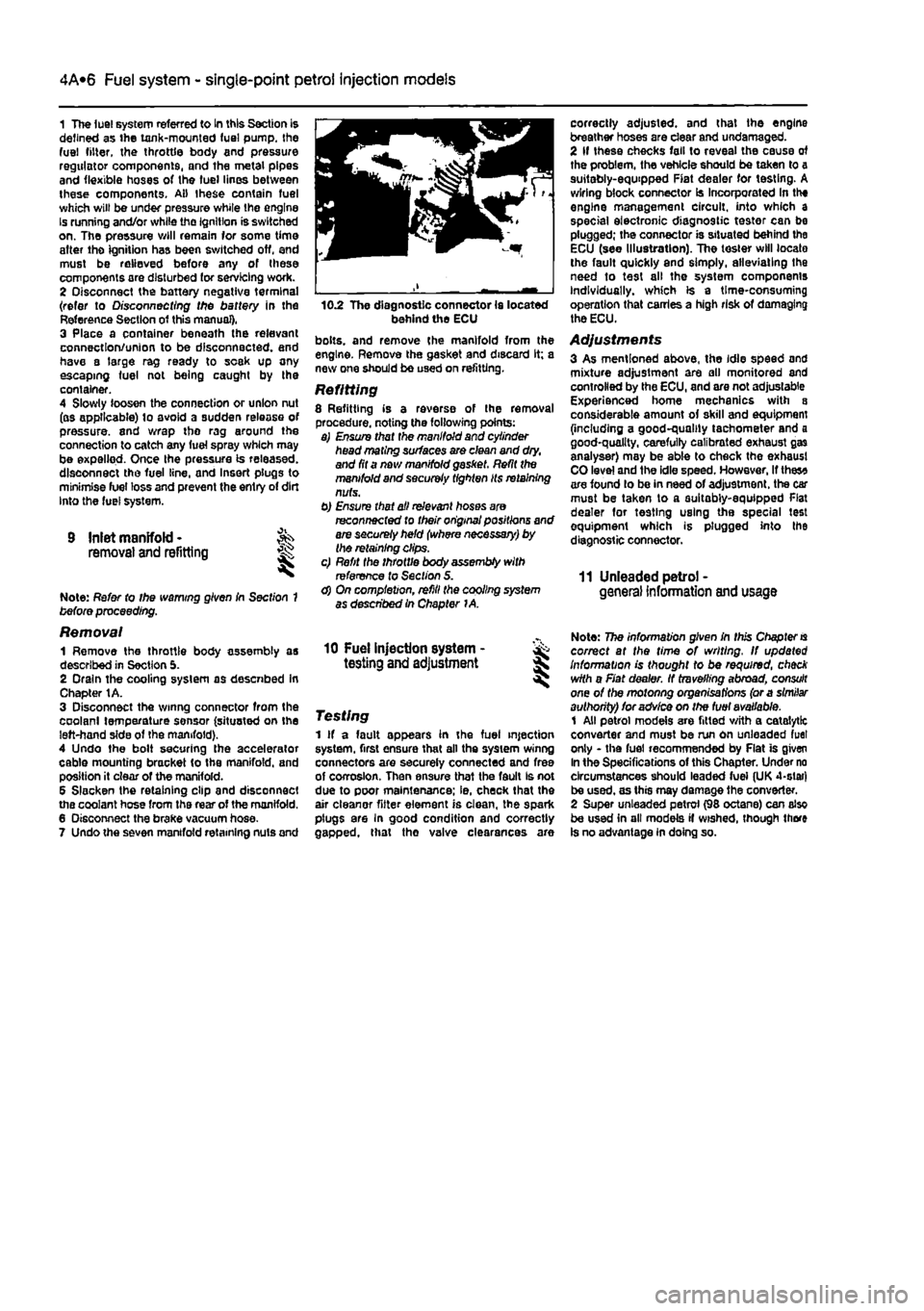
4A*2 Fuel system - single-point petrol Injection models
1 The luel system referred to In this Section is defined as the tank-mounted fuel pump, the fuel litter, the throttle body and pressure regulator components, and the metal pipes and flexible hoses of the fuel lines between these components. All ihese contain fuel which will be under pressure while the engine Is running and/or while tha Ignition is switched on. The pressure will remain for some time after tho ignition has been switched off, and must be relieved before any of these components are disturbed (or servicing work. 2 Disconnect the battery negative terminal (refer to D/sconnecf/ngr the battery in the Reference Section of this manual), 3 Place a container beneath the relevant connection/union to be disconnected, and have a large rag ready to soak up any escaping fuel not being caught by the container. 4 Slowly loosen the connection or union nut (as applicable) to avoid a sudden release of pressure, and wrap tho rag around the connection to catch any fuel spray which may be expelled. Once the pressure is released, disconnect the fuel line, and Insert plugs to minimise fuel loss and prevent the entry of dirt Into the fuel system.
9 Inlet manifold -removal and refitting ^
Note: Refer to the warning given In Section 1 before proceeding.
Removal 1 Remove the throttle body assembly as described in Section 5. 2 Drain the cooling system as described in Chapter 1A. 3 Disconnect the winng connector from the coolanl temperature sensor (situated on the left-hand sidB of the manifold). 4 Undo the bolt securing the accelerator cable mounting bracket to the manifold, and position it clear of the manifold. 5 Slacken the retaining clip and disconnect tha coolant hose from the rear of the manifold. 6 Disconnect the brake vacuum hose. 7 Undo the seven manifold retaining nuts and
10.2 The diagnostic connector la located behind the ECU bolts, and remove (he manifold from the engine. Remove the gasket and discard It; a new one should be used on refitting.
Refitting 8 Refitting is a reverse of the removal procedure, noting the following points: a) Ensure that the manifold and cylinder head mating surfaces are clean and dry, and fit a nev/ manifold gasket. Refit the manifold and securely tighten Its retaining nuts. b) Ensure that all relevant hoses are reconnected fo their original positions and are securely held (where necessary) by the retaining clips. c) Refit the throttle body assembly with reference to Section S. d) On completion, refill the cooling system as described In Chapter 1A.
correctly adjusted, and that the engine breather hoses are clear and undamaged. 2 If these checks fall to reveal the cause of the problem, the vehicle should be taken to a suitably-equipped Fiat dealer for testing. A wiring block connector Is Incorporated In the engine management circuit, into which a special electronic diagnostic tester can be plugged; the connector is situated behind the ECU (see Illustration). The tester will locate the fault quickly and simply, alleviating the need to test all the system components Individually, which is a time-consuming operation that carries a high risk of damaging the ECU.
Adjustments 3 As mentioned above, the idle speed and mixture adjustment are all monitored and controlled by the ECU, and are not adjustable Experienced home mechanics with a considerable amount of skill and equipment (including a good-quality tachometer and a good-quality, carefully calibrated exhaust gas analyser) may be able to check the exhaust CO level and ihe idle speed. However, If thes* are found lo be in need of adjustment, the car must be taken to a suitably-equipped Flat dealer for testing using the special test equipment which is plugged into the diagnostic connector.
11 Unleaded petrol -general Information and usage
10 Fuel injection system - & testing and adjustment S
Testing 1 If a fault appears in the fuel injection system, first ensure that all the system winng connectors are securely connected and free of corrosion. Then ensure that the fault Is not due to poor maintenance; ie, check that the air cleanor fitter element is clean, the spark plugs are In good condition and correctly gapped, that tho valve clearances are
Note: The information given in this Chapter
is
correct at the time of writing. If updated Information is thought to be required, check with a Fiat dealer. If travelling abroad, consult one of the motonng organisations (or a similar authority) for advice on the fuel available. 1 All petrol models are fitted with a catalytic converter and must be run on unleaded fuel only - the fuel recommended by Flat is given In the Specifications of this Chapter. Under no circumstances should leaded fuei (UK 4-slar) be used, as this may damage the converter. 2 Super unleaded petrol (98 octane) can also be used in all models if wished, though there is no advantage in doing so.
Page 134 of 225
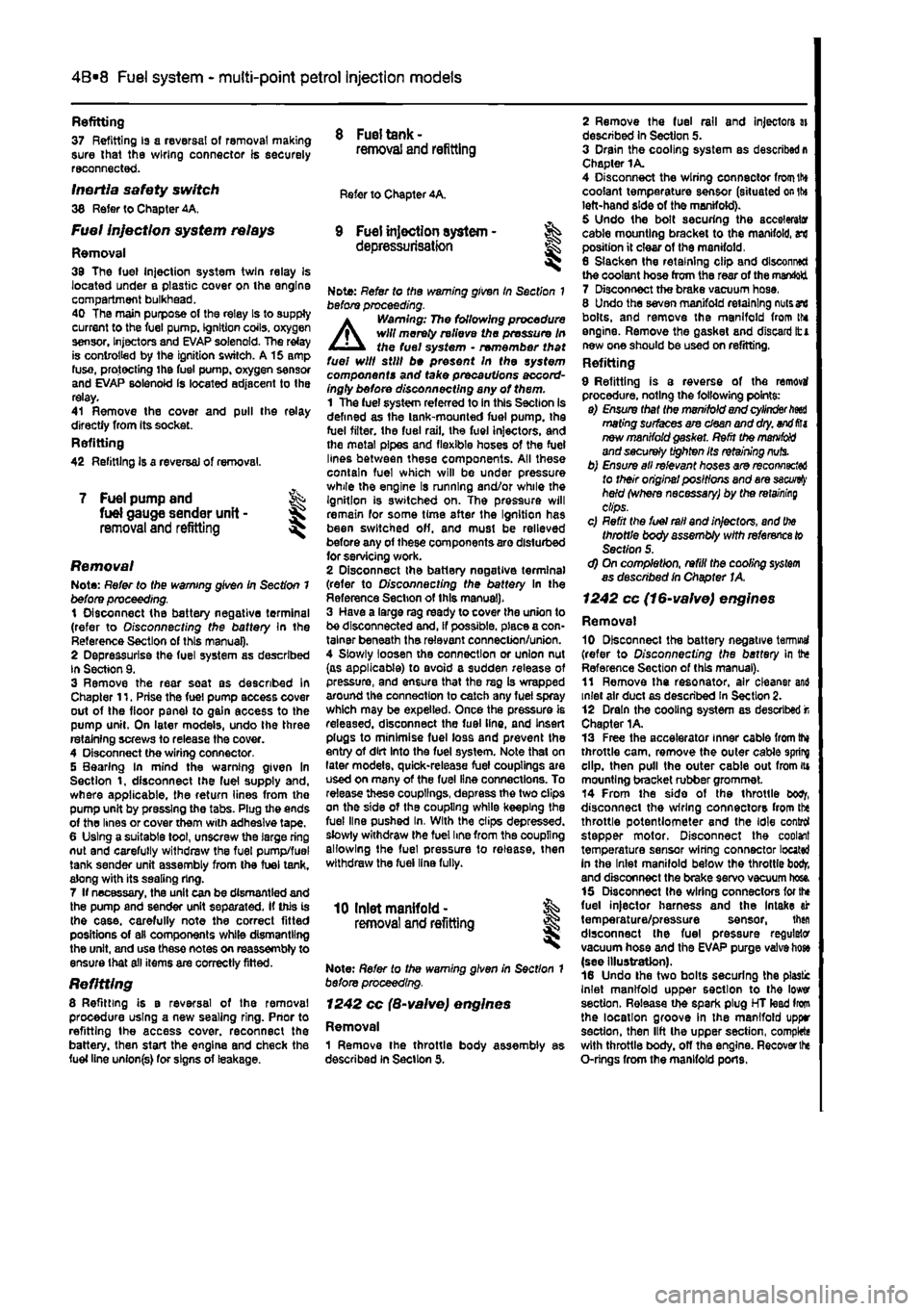
4A*2 Fuel system -
single-point
petrol Injection models
Refitting 37 Refitting Is a reversal of removal making sure that the wiring connector is securely reconnected.
Inertia safety switch 36 Refer to Chapter 4A, Fuel injection system relays Removal 39 The fuel injection system twin relay Is located under a plastic cover on the engine compartment bulkhead. 40 The main purpose of the relay Is to supply current to the fuel pump, ignition coils, oxygen sensor, Injectors and EVAP solenoid. The relay is controlled by the ignition switch. A15 amp fuse, protecting ihe fuel pump, oxygen sensor and EVAP solenoid is located adjacent to the relay. 41 Remove the cover and pull the relay directfy from Its socket. Refitting 42 Refitting is a reversal of removal.
7 Fuel pump and fuel gauge sender unit - JK removal
and
refitting ^
Removal Note: Refer fo (he warning given in Section 1 before proceeding. 1 Disconnect the battery negative terminal (refer to Disconnecting the battery In the Reference Section of this manual). 2 Depreasurise the fuel system as described in Section 9. 3 Remove the rear soat as described In Chapter 11. Prise the fuel pump access cover out of the floor panel to gain access to the pump unit. On later models, undo the three retaining screws to release the cover. 4 Disconnect the wiring connector. 5 Bearing In mind the warning given In Section t, disconnect Ihe fuel supply and, where applicable, the return lines from tho pump unit by pressing the tabs. Plug the ends of the lines or cover them with adhesive tape. 6 Using a suitable tool, unscrew the large ring nut and carefully withdraw the fuel pump/fuel tank sender unit assembly from the fuel tank, along with its sealing rtng. 7 If necessary, the unit can be dismantled and the pump and sender unit separated. If this is (he case, carefully note the correct fitted positions of all components while dismantling the unit, and use these notes on reassembly to ensure that all items are correctly fitted.
Refitting 8 Refitting is a reversal of the removal procedure using a new sealing ring. Prior to refitting the access cover, reconnect the battery, then start the engine and check the fuel line unlon(s) (or signs of i
Fuel
tank -removal and refitting
Refer to Chapter 4A.
9 Fuel injection system -depressurisatton
Note: Refer to the warning given In Section 1 before proceeding.
A
Warning: The following procedure will merely relieve the pressure In the fuel system • remember that fuel will still be present In the system components and take precautions accord-ingly before disconnecting any of them. 1 The fuel system referred to in this Section is defined as the lank-mounted fuel pump, tha fuel filter, the fuel rail, the fuel injectors, and the metal pipes and flexible hoses of the fuel lines between these components. All these contain fuel which will be under pressure while the engine Is running and/or while the Ignition is switched on. The pressure will remain for some time after the Ignition has been switched off. and must be relieved before any of these components are disturbed for servicing work. 2 Disconnect the battery negative terminal (refer to Disconnecting the battery In the Reference Section of this manual). 3 Have a large rag ready to cover the union to be disconnected and, if possible, place a con-tainer beneath the relevant connection/union. 4 Slowly loosen the connection or union nut (as applicable) to avoid a sudden release of pressure, and ensure that the rag is wrapped around the connection to catch any fuef spray which may be expelled. Once the pressure is released, disconnect the fuel line, and Insert plugs to minimise fuel loss and prevent the entry of dirt Into the fuel system. Note that on later models, quick-release fuel couplings are used on many of the fuel line connections. To release these couplings, depress the two clips on the side of the coupling while keeping the fuel line pushed In. With the clips depressed, slowly withdraw the fuel line from the coupling allowing the fuel pressure to release, then withdraw the fuel line fully.
10 Inlet manifold-removal
and
refitting
Note: Refer fo the warning given in Section 1 before proceeding.
1242 cc (8-valve) engines
Removal 1 Remove ihe throttle body assembly as described in Section 5.
2 Remove the fuel rail and injectors at described in Section 5. 3 Drain the cooling system ss described n Chapter 1A. 4 Disconnect the wiring connector from ih* coolant temperature sensor (situated on it* left-hand side of the manifold). 5 Undo the bolt securing the accelerator cable mounting bracket to the manifold, am position it clear of the manifold. 6 Slacken the retaining clip and disconnect the coolant hose from the rear of the mandold 7 Disconnect the brake vacuum hose, 6 Undo the seven manifold retaining nuisw bolts, and remove the manifold from tta engine. Remove the gasket and discard tti new one should be used on refitting. Refitting
9 Refitting is a reverse of the removjf procedure, noting the following points: a) Ensure that the manifold and cylinder lim mating surfaces are dean and
dry.
and fill new manifold gasket. Refit the
manifold
and securely tighten Its retaining
nuts.
b) Ensure all relevant hoses are recorwscfed fo their original positions and are
sacurtfy
held (Where necessary; by the
retaining
clips. c) Refit the fuel rail and injectors, and
the
throttle body assembly with
reference to
Sect/on 5. d) On completion, refill the cooling
system
as described in Chapter 1A. 1242 cc (16-valve) engines
Removal 10 Disconnect the battery negative ternnncf (refer to Disconnecting the battery in ths Reference Section of this manual). 11 Remove the resonator, air cleaner and inlet air duct as described In Section 2. 12 Drain the cooling system as described r, Chapter 1A. 13 Free the accelerator inner cable from IN throttle cam. remove the outer cable spring dip. then pull the outer cable out from itt mounting bracket rubber grommet. 14 From the side of the throttle boOf, disconnect the wiring connectors from the throttle potentiometer and the Idle contrd stepper motor. Disconnect the coolant temperature sensor wiring connector located in the Inlet manilold below the throttie bodr, and disconnect the brake servo vacuum hose. 15 Disconnect Ihe wiring connectors for the fuel in|ector harness and the Intake a* temperature/pressure sensor, thtn disconnect the fuel pressure regulator vacuum hose and the EVAP purge valve
hose
(see illustration). 16 Undo Ihe two bolts securing the plastic Inlet manifold upper section to the lower section. Release the spark plug HT lead from the location groove in the manifold upper section, then lift Ihe upper section, complete with throttle body, off the engine. Recover
the
O-rings from the manifold pons.