check engine FIAT PUNTO 1998 176 / 1.G Owner's Guide
[x] Cancel search | Manufacturer: FIAT, Model Year: 1998, Model line: PUNTO, Model: FIAT PUNTO 1998 176 / 1.GPages: 225, PDF Size: 18.54 MB
Page 44 of 225
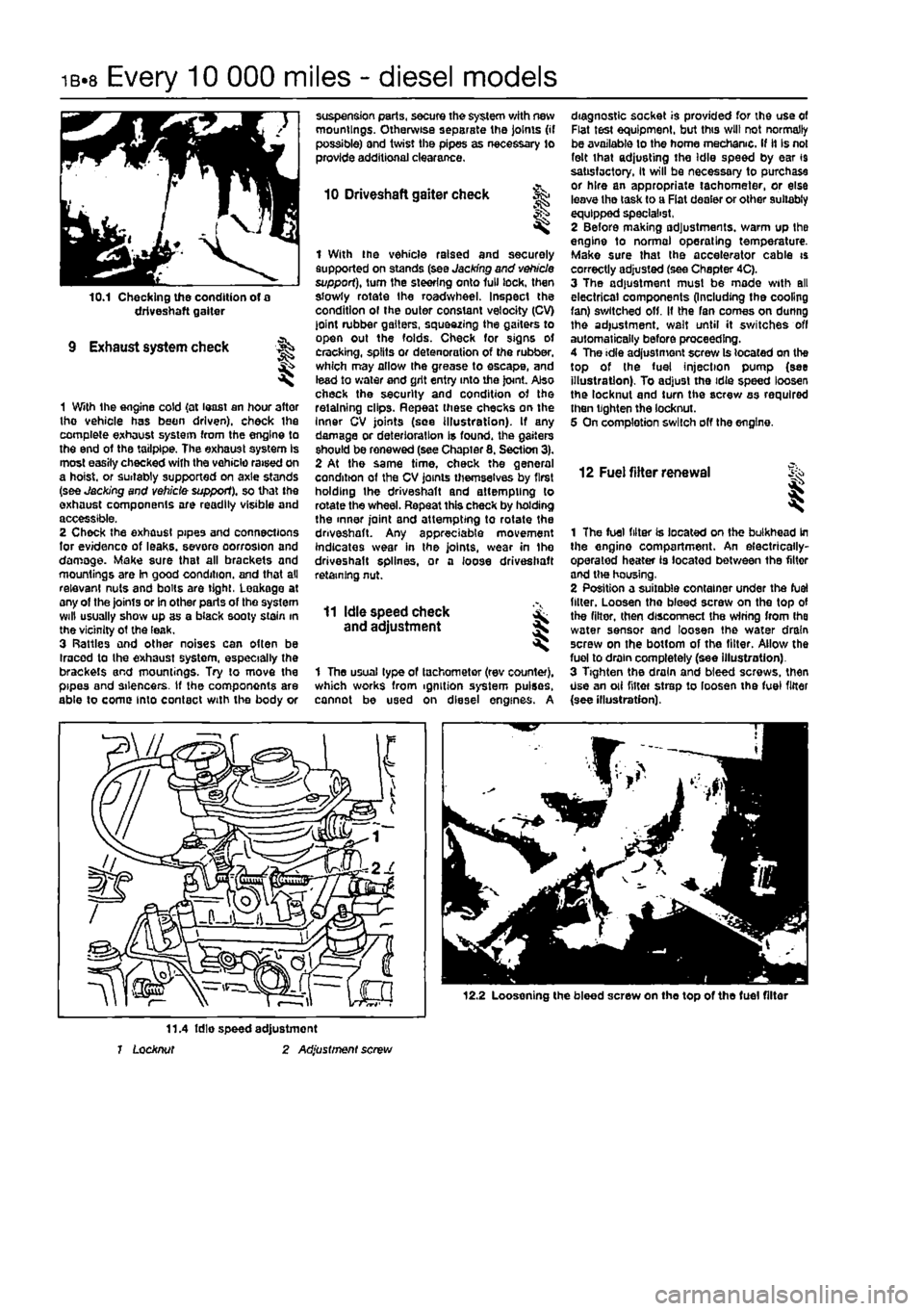
ib-8 Every 10 000 miles - diesel models
10.1 Checking the condition of a driveshaft gaiter
9 Exhaust system check
1 With the engine cold {at least an hour after tho vehicle has been driven), check ihe complete exhaust system from the engine to the end of the tailpipe. The exhaust system Is most easily checked with the vehicle raised on a hoist, or suitably supported on axle stands (see Jacking and vehicle support), so that the exhaust components are readily visible and accessible. 2 Check the exhaust pipes and connections for evidence of leaks, severe oorrosion and damage. Make sure that all brackets and mountings are In good condition, and that all relevant nuts and bolts are tight, Leakage at any of the joints or in other parts of tho system will usually show up as a black sooty stain in the vicinity ot the leak. 3 Rattles and other noises can often be Iracod to the exhaust system, especially the brackets and mountings. Try to move the pipes and silencers. If the components are able to come into contact with the body or
suspension parts, secure the system with new mountings. Otherwise separate the joints (if possible) and twist the pipes as necessary to provide additional clearance.
10 Driveshaft gaiter check
I
1 With the vehicle raised and securely supported on stands (see Jacking and vehicle support), turn the steering onto lull lock, then slowly rotate the roadwheel. Inspect the condition ol the outer constant velocity (CV) joint rubber gaiters, squeezing the gaiters to open out the folds. Check for signs ot cracking, splits or detenoration of the rubber, which may allow the grease to escape, and lead to water and grit entry into the joint. Also check the security and condition of the retaining clips. Repeat these checks on the Inner CV joints (see illustration). If any damage or deterioration is found, the gaiters should be renewed (see Chapter 8. Section 3). 2 At the same time, check the general condition of the CV joints themselves by first holding the driveshaft and attempting to rotate the wheel. Repeat this check by holding the inner joint and attempting to rotate the driveshaft. Any appreciable movement indicates wear in the joints, wear in Ihe driveshaft splines, or a loose driveshaft retaining nut.
11 Idle speed check and adjustment
1 The usual type of tachometer (rev counter), which works from ignition system pulses, cannot be used on diesel engines. A
diagnostic socket is provided for the use of Flat test equipment, but this will not normally be available to the home mechanic. If it Is not felt that adjusting the Idle speed by ear 19 satisfactory, It will be necessary to purchase or hire an appropriate tachometer, or else leave tho task to a Fiat dealer or other suitably equipped specialist, 2 Before making adjustments, warm up the engine to normal operating temperature. Make sure that the accelerator cable is correctly adjusted (see Chapter 4C). 3 The adjustment must be made with all electrical components (Including the cooling fan) switched off. It the fan comes on dunng the adjustment, wait until it switches off automatically before proceeding. 4 The idle adjustment screw Is located on the top of the fuel injection pump (see illustration). To adjust the idie speed loosen the locknut and turn the screw as required then tighten the locknut. 5 On completion switch off the engine.
12 Fuel filter renewal i
1 The fuel filter is located on the bulkhead in the engine compartment. An electrically-operated heater is located between the filter and tlw housing, 2 Position a suitable container under the fuel filler. Loosen tho bleed screw on the top of the filter, then disconnect the wiring from Ihe water sensor and loosen the water drain screw on the bottom of the filter. Allow the fuel to drain completely (see illustration). 3 Tighten the drain and bleed screws, then Use an oii niter strep to loosen the fuel filter {see illustration).
12.2 Loosening the bleed screw on the top of the fuel filter
11.4 fdie speed adjustment 1 Locknut 2 Adjustment screw
Page 45 of 225
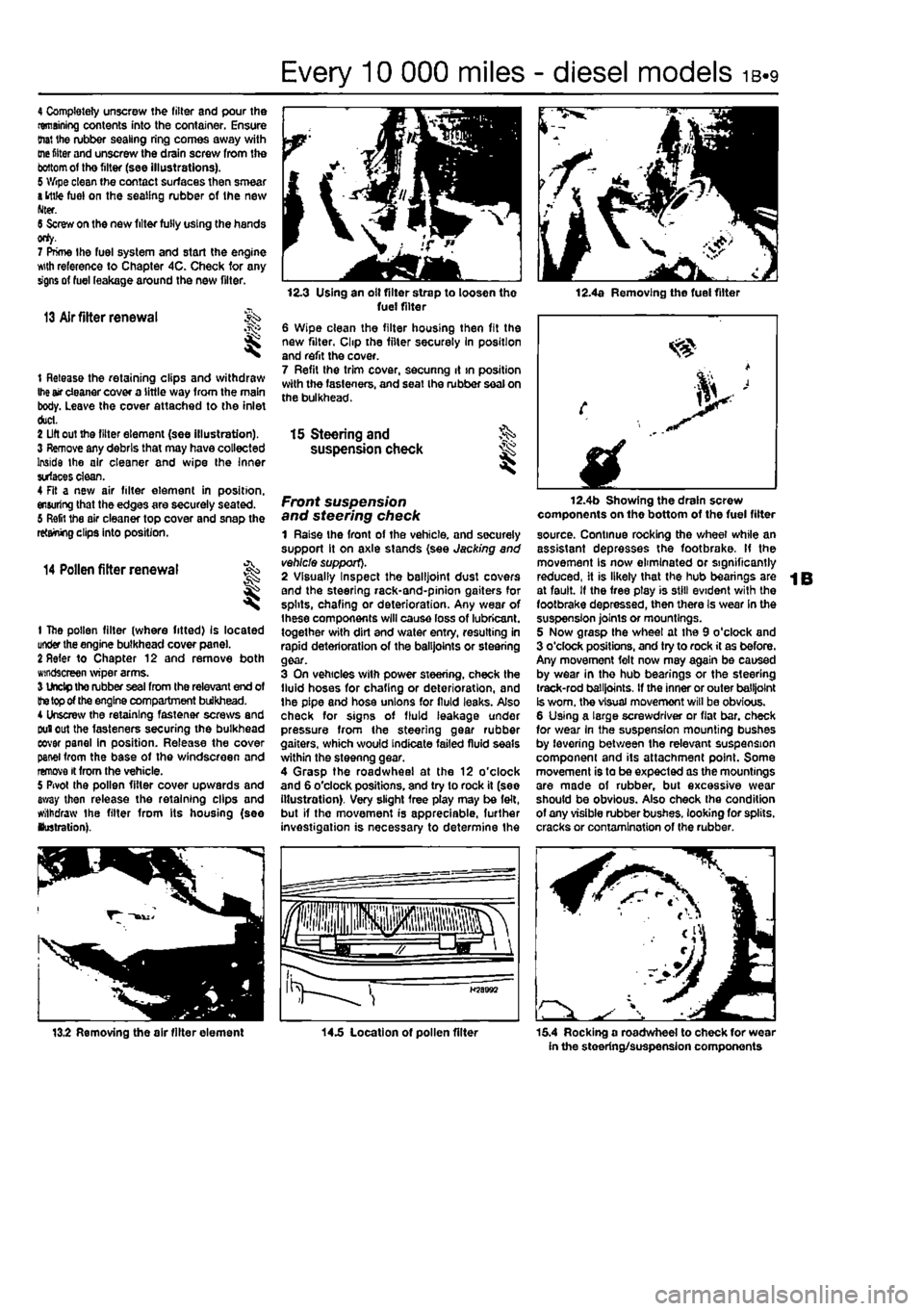
Every 10 000 miles - diesel models ib«9
4 Completely unscrew the filter and pour the remaining contents into the container. Ensure (hat the rubber sealing ring comes away with
me
fitter and unscrew the drain screw from the
bottom
of tho filter (see illustrations). 5 Wipe clean the contact surfaces then smear
a
ittfe fuel on the sealing rubber of the new Nter. 6 Screw on the new filter fully using the hands orty. 7 Prime the fuel system and start the engine wth reference to Chapter 4C. Check for any signs of fuel leakage around the new filter.
13 Air fitter renewal
t Release the retaining clips and withdraw
Ihe
air cleaner cover a little way from the main body. Leave the cover attached to the inlet duct. 2 Lift out the filter element (see illustration). 3 Remove any debris that may have collected Inside the air cleaner and wipe the Inner surfaces clean. 4 Fit a new air filter element in position, ensuring that the edges are securely seated. 6 Refit the air cleaner top cover and snap the retaining clips into position.
14 Pollen filter renewal
t
1 The pollen filter (where fitted) Is located under the engine bulkhead cover pane). 2 Refer to Chapter 12 and remove both windscreen wiper arms. 3 Undp tho rubber seal from the relevant end of
the top
of the engine compartment bulkhead. 4 Unscrew the retaining fastener screws and Duiout the fasteners securing the bulkhead eovar panel in position. Release the cover panel from the base of the windscreen and remove it from the vehicle. 5 Pivot the pollen filter cover upwards and away then release the retaining clips and withdraw the filter from Its housing (see lustration).
12.3 Using an olt filter strap to loosen the fuel filter 6 Wipe clean the filter housing then fit the new filter, Clip the filter securely In position and refit the cover. 7 Refit the trim cover, secunng it >n position with the fasteners, and seat Ihe rubber seal on the bulkhead.
12.4a Removing the fuel filter
15 Steering and §S> suspension check ^
Front suspension and steering check 1 Raise the front of the vehicle, and securely support it on axle stands (see Jacking and vehicle support). 2 Visually Inspect the balljoint dust covers and the steering rack-and-pinion gaiters for splits, chafing or deterioration. Any wear of Ihese components will cause loss of lubricant, together with dirt and water entry, resulting in rapid deterioration of the balljoints or steering gear. 3 On vehicles with power steering, check the fluid hoses for chafing or deterioration, and the pipe and hose unions for fluid leaks. Also check for signs of fluid leakage under pressure from the steering gear rubber gaiters, which would indicate failed fluid seals within the steenng gear. 4 Grasp the roadwheel at the 12 o'clock and 6 o'clock positions, and try to rock it (see illustration). Very slight free play may be felt, but if the movement is appreciable, further investigation is necessary to determine the
fplllll iHpjiiisisps fa^aJw a LJgr >
H58B92
12.4b Showing the drain screw components on the bottom of the fuel filter source. Continue rocking the wheel while an assistant depresses the footbrake. If the movement Is now eliminated or significantly reduced, it is likely that the hub bearings are at fault. If the free ptay is still evident with the footbrake depressed, then there Is wear In the suspension joints or mountings. 5 Now grasp the wheel at the 9 o'clock and 3 o'clock positions, and try to rock it as before. Any movement felt now may again be caused by wear in the hub bearings or the steering track-rod balljoints. If the inner or outer balljoint Is worn, the visual movemont will be obvious. 6 Using a large screwdriver or flat bar. check for wear in the suspension mounting bushes by levering between the relevant suspension component and its attachment point. Some movement is to be expected as the mountings are made of rubber, but excessive wear should be obvious. Also check the condition of any visible rubber bushes, looking for splits, cracks or contamination of the rubber.
13.2 Removing the air filter element 14.5 Location of pollen filter 15.4 Rocking a roadwheel to check for wear in the steering/suspension components
Page 46 of 225
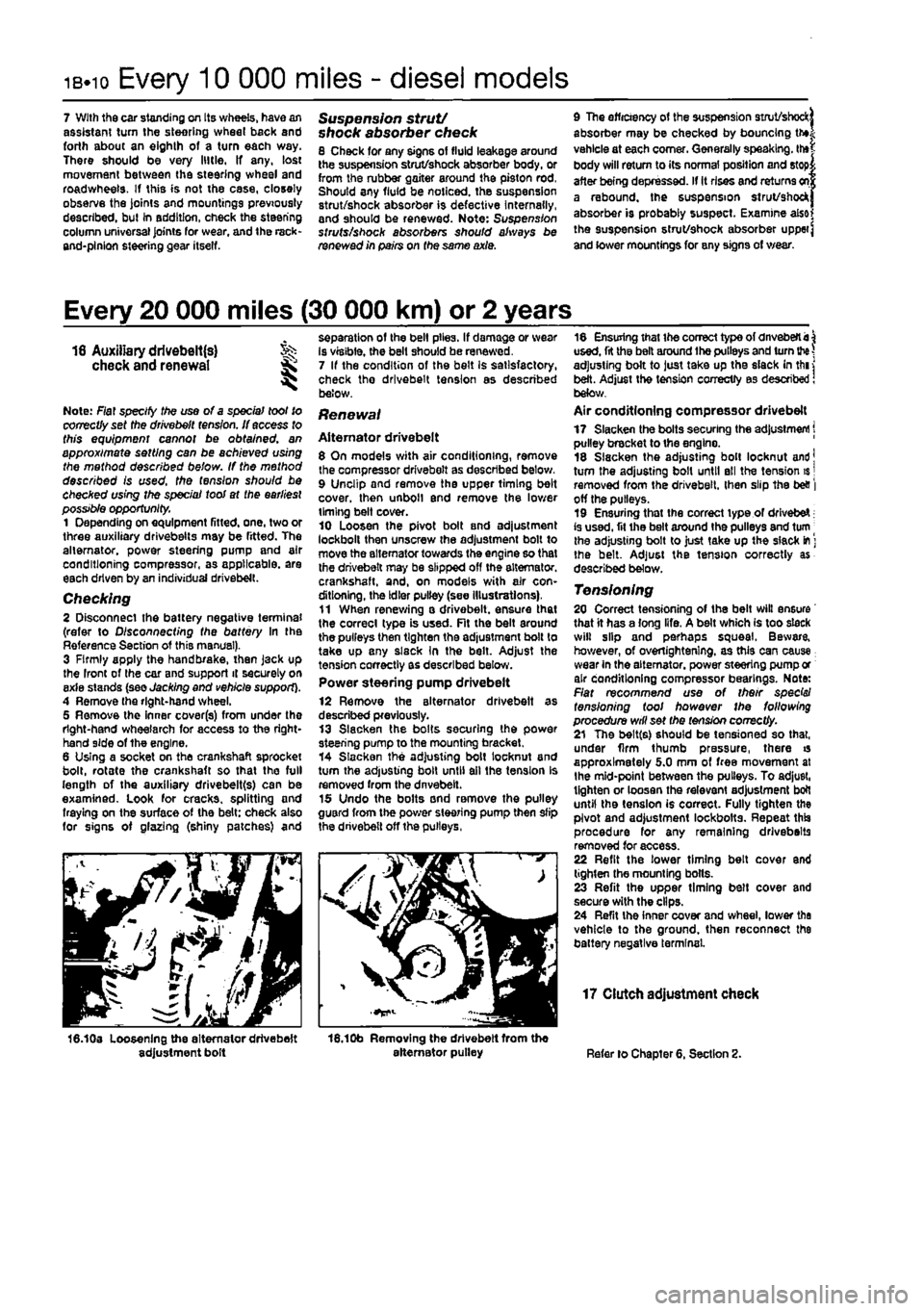
ib-io Every 10 000 miles - diesel models
7 With the car standing on Its wheels, have an assistant turn the steering wheel back and forth about an eighth of a turn each way. There should be very hide. If any, lost movement between the steering wheel and roadwheels. If this is not the case, closely observe the joints and mountings previously described, but in addition, check the steering column universal joints for wear, and the rack-and-plnion steering gear itself.
Suspension strut/ shock absorber check 8 Check for any signs of fluid leakage around the suspension strut/shock absorber body, or from the rubber gaiter around the piston rod, Should any fluid be noticed, the suspension strut/shock absorber is defective Internally, and should be renewed. Note: Suspension struts/shock absorbers should always be renewed in pairs on the same axle.
9 The efficiency of the suspension strut/shock] absorber may be checked by bouncing 0*1 vehicle at each comer. Generally speaking. th»| body will return to its normal position and 8top| after being depressed. If It rises and returns cn| a rebound, the suspension strut/shocH absorber is probably suspect. Examine also* the suspension strut/shock absorber uppeij and lower mountings for any signs of wear.
Every 20 000 miles (30 000 km) or 2 years
18 Auxiliary drivebeltfs) % check and renewal
Note: Fiat specify the use of a spec/a/ toot to correctly set the drivebelt fens/on. if access to this equipment cannot be obtained, an approximate setting can be achieved using the method described beiow. If the method described Is used, the tension should be checked using the spec/a/ too! at the earliest possible opportunity. 1 Depending on equipment fitted, one, two or three auxiliary drivebeits may be fitted. The alternator, power steering pump and air conditioning compressor, as applicable, are each driven by an individual drivebelt. Checking 2 Disconnect the battery negative terminal (refer to Disconnecting the battery In the Reference Section of this manual). 3 Firmly apply the handbrake, then Jack up the Iront of the car and support it securely on exie stands (see Jacking and vehicle support). 4 Remove the right-hand wheel. 5 Remove the Inner cover(s) from under the right-hand wheelarch for access to the right-hand side of the engine. 6 Using a socket on the crankshaft sprocket bolt, rotate the crankshaft so that the full length of the auxiliary drivebelt(s) can be examined. Look for cracks, splitting and fraying on the surface of the belt: check also for signs of glazing (shiny patches) and
16.10a Loosening the alternator drivebelt adjustment bolt
separation of the belt plies. If damage or wear Is visible, the bell should be renewed, 7 If the condition of the belt Is satisfactory, check tho drivebelt tension as described below.
Renewal
Alternator drivebelt 8 On models with air conditioning, remove the compressor drivebelt as described below, 9 Unclip and remove the upper timing belt cover, then unbolt end remove the lower timing belt cover. 10 Loosen the pivot bolt and adjustment lockbolt then unscrew the adjustment bolt to move the alternator towards the engine so that the drivebelt may be slipped off the alternator, crankshaft, and, on models with air con-ditioning, the Idler pulley (see Illustrations), 11 When renewing a drivebelt. ensure that the correct type is used. Fit the belt around the pulleys then tighten the adjustment bolt to take up any slsck In the belt. Adjust the tension correctly as described below. Power steering pump drivebelt
12 Remove the alternator drivebelt as described previously. 13 Slacken the bolts securing the power steering pump to the mounting bracket. 14 Slacken the adjusting bolt locknut and turn the adjusting bolt until ail the tension Is removed from the dnvebelt. 15 Undo the bolts and remove the pulley guard from the power steering pump then slip the drivebelt off the pulleys,
16.10b Removing the drivebelt from the alternator pulley
18 Ensuring that the correct type of dnveberti^ used, fit the belt around the pulleys and turn
the
adjusting bolt to just take up the slack in thi j belt. Adjust the tension correctly as described! below. Air conditioning compressor drivebelt 17 Slacken the bolts securing the adjustment j pulley bracket to the engine. 18 Slacken the adjusting bolt locknut and] turn the adjusting bolt until ell the tension is | removed from the drivebelt. then slip the be& | off the pulleys. 19 Ensuring that the correct type of drivebeX; is used, fit ihe belt around the pulleys and turn | the adjusting bolt to just take up the slack
m
] the belt. Adjust the tension correctly as described below.
Tensioning 20 Correct tensioning of the belt will ensure that it has a long life. A belt which is too slack will slip and perhaps squeal. Beware, however, of overiightenlng. as this can cause wear in the alternator, power steering pump or air conditioning compressor bearings. Note: Flat recommend use of their spec's/ tensioning tool however the following procedure will set the tension correctly. 21 The belt(s) should be tensioned so that, under firm thumb pressure, there is approximately 5.0 mm of free movement at the mid-point between the pulleys. To adjust, tighten or loosen the relevant adjustment bolt until the tension is correct. Fully tighten the pivot and adjustment lockbotts. Repeat this procedure for any remaining drivebeits removed for access. 22 Refit the lower timing belt cover end tighten the mounting bolts. 23 Refit the upper timing belt cover and secure with the clips. 24 Refit the inner cover and wheel, lower the vehicle to the ground, then reconnect the battery negative terminal.
17 Clutch adjustment check
Refer lo Chapter 6, Section 2.
Page 47 of 225
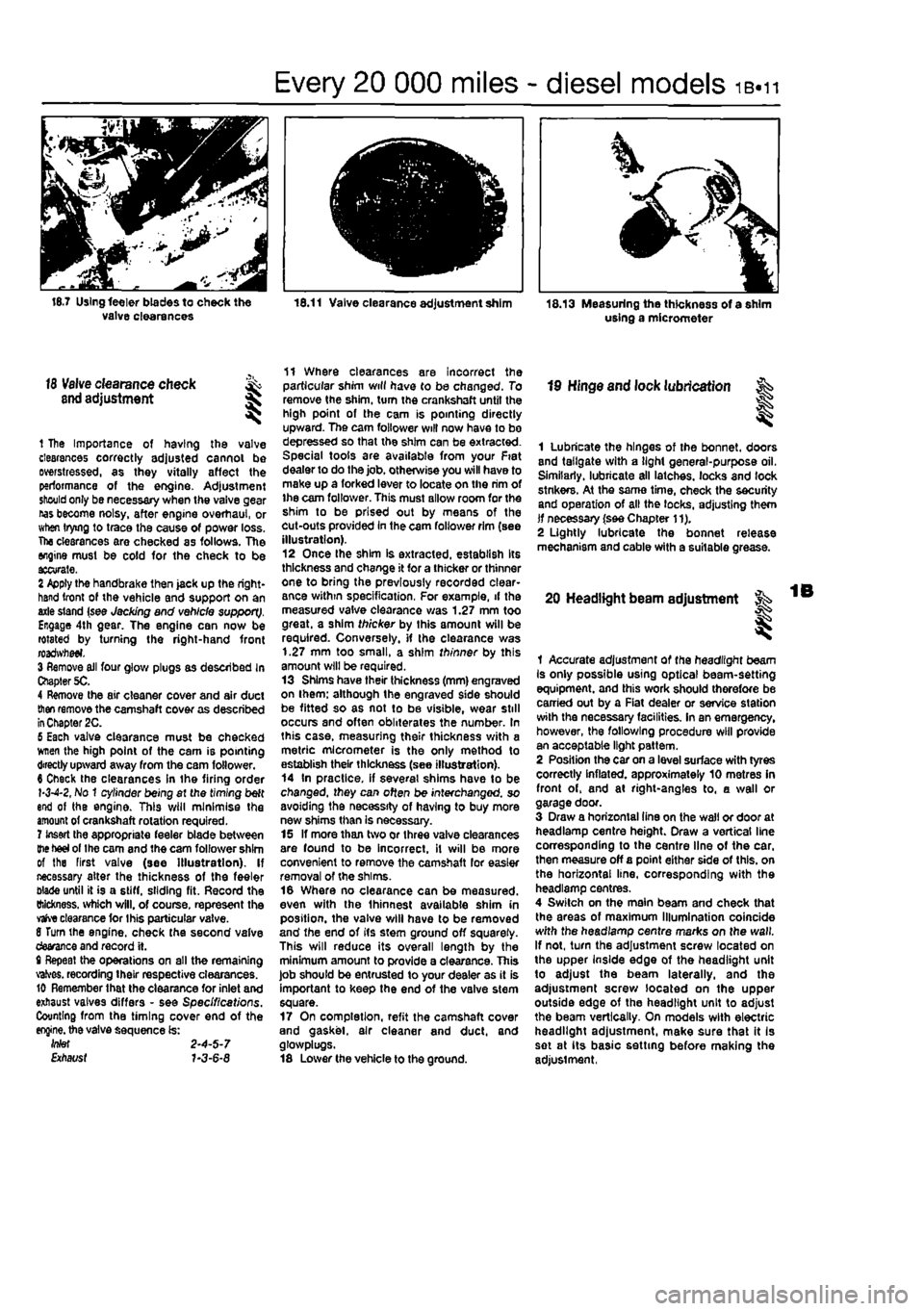
Every 20 000 miles - diesel models ib.h
18
Valve clearance check and
adjustment
1 The Importance of having the valve clearances correctly adjusted cannot be Distressed, as they vitally affect the performance of the engine. Adjustment should only be necessary when the valve gear nas become noisy, after engine overhaul, or when trying to trace the cause of power loss. The clearances are checked as follows. The engine must be cold for the check to be ttcurate. 2 Apply the handbrake then jack up the right-hand front of the vehicle and support on an axle stand (see Jacking and vehicle support). Engage 4th gear. The engine can now be rotated by turning the right-hand front roadwfteei. 3 Remove ail four glove plugs as described In Chapter 5C. 4 Remove the air cleaner cover and air duct
then
remove the camshaft cover as described
in
Chapter 2C. 6 Each valve clearance must be checked wnen the high point of the cam is pointing directly upward away from the cam follower. 6 Check the clearances in the firing order 1-3-4-2, No 1 cylinder being at the timing belt end of the engine. This will minimise the amount of crankshaft rotation required. 7 Insert the appropriate feeler blade between
the heel
of the cam and the cam follower shim of the First valve (see Illustration). If necessary alter the thickness of the feeler blade until it is a stiff, sliding fit. Record the thickness, which will, of course, represent the
vafve
clearance tor Ihis particular valve. 8 Turn the engine, check the second valve devance and record it. t Repeat the operations on all the remaining valves. recording their respective clearances. 10 Remember that the clearance for inlet and exhaust valves differs - see Specifications. Counting from the timing cover end of the
engine,
the valve sequence is: Wef 2-4-5-7 Etfiat/sf 7-3-6-8
11 Where clearances are incorrect the particular shim will have to be changed. To remove the shim, turn the crankshaft until the high point of the cam is pointing directly upward. The cam follower will now have to bo depressed so that the shim can be extracted. Special tools are available from your Fiat dealer to do the job. otherwise you will have to make up a forked lever to locate on the rim of ihe cam follower. This must allow room for the shim to be prised out by means of the cut-outs provided in the cam follower rim (see illustration). 12 Once Ihe shim is extracted, establish Its thickness and change it for a thicker or thinner one to bring the previously recorded clear-ance within specification, For example, if the measured valve clearance was 1.27 mm too great, a shim thicker by this amount will be required. Conversely, if the clearance was 1.27 mm too small, a shim thinner by this amount will be required. 13 Shims have their thickness (mm) engraved on ihem; although the engraved side should be fitted so as not to be visible, wear still occurs and often obliterates the number. In this case, measuring their thickness with a metric micrometer is the only method to establish their thickness (see illustration). 14 In practice, if several shims have to be changed, they can often be interchanged, so avoiding the necessity of having to buy more new shims than is necessary. 15 If more than two or three valve clearances are found to be incorrect, it will be more convenient to remove the camshaft lor easier removal of the shims. 16 Where no clearance can be measured, even with the Ihinnest available shim in position, the valve will have to be removed and the end of its stem ground off squarely. This will reduce its overall length by the minimum amount to provide a clearance. This job should be entrusted to your dealer as it is important to keep the end of the valve stem square. 17 On completion, refit the camshaft cover and gasket, air cleaner and duct, and glosvplugs. 18 Lower the vehicle to the ground.
19 Hinge and lock lubrication
I
1 Lubricate the hinges of the bonnet, doors and tailgate with a light general-purpose oil. Similarly, lubricate all latches, locks and lock stnkers. At the same time, check the security and operation of all the locks, adjusting them if necessary (see Chapter 11). 2 Lightly lubricate the bonnet release mechanism and cable with a suitable grease.
20 Headlight beam adjustment
I
1 Accurate adjustment of the headlight beam Is only possible using optical beam-setting equipment, and this work should therefore be carried out by a Fiat dealer or service station with the necessary facilities. In an emergency, however, the following procedure will provide an acceptable light pattern. 2 Position the car on a level surface with tyres correctly inflated, approximately 10 metres in front of, and at right-angles to, a wall or garage door. 3 Draw a horizontal tine on the wall or door at headlamp centre height. Draw a vertical line corresponding to the centre line of the car. then measure off a point either side of this, on the horizontal line, corresponding with the headlamp centres. 4 Switch on the main beam and check that the areas of maximum Illumination coincide with the headlamp centre marks on the wall. If not, turn the adjustment screw located on the upper Inside edge of the headlight unit to adjust the beam laterally, and the adjustment screw located on the upper outside edge of the headlight unit to adjust the beam vertically. On models with electric headlight adjustment, make sure that it Is set at its basic setting before making the adjustment,
Page 48 of 225
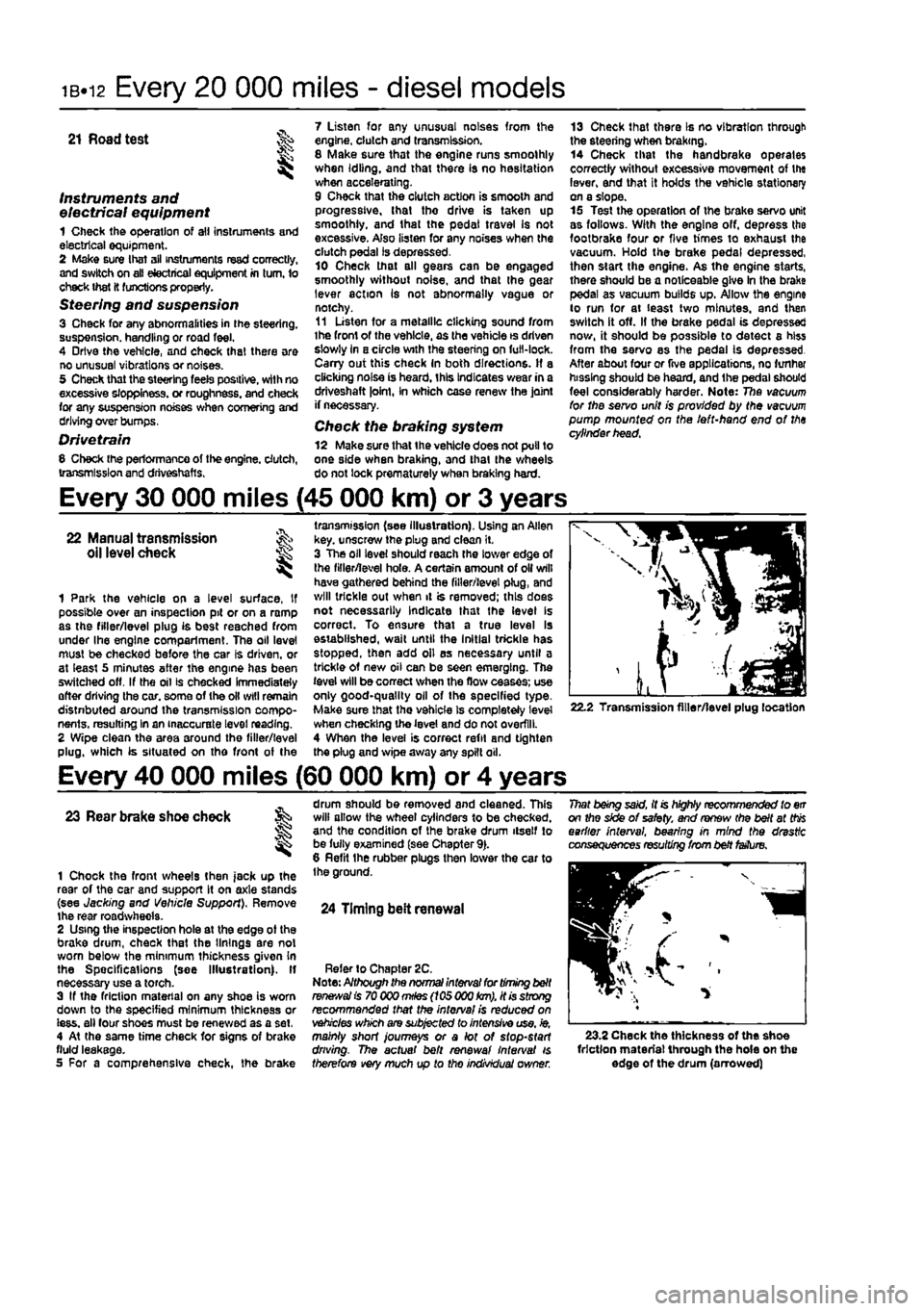
1B«12 Every 20 000 miles - diesel models
21 Road test
Instruments and electrical equipment 1 Check the operation of atl instruments and electrical equipment. 2 Make sure that all instruments read correctly, and switch on all electrical equipment rn turn, to check that It functions properly. Steering and suspension 3 Check for any abnormalities in the steering, suspension, handling or road feel. 4 Drive the vehicle, and check that there are no unusual vibrations or noises. 5 Check that the steering feete positive, with no excessive sloppiness, or roughness, and check for any suspension noises when cornering and driving over bumps. Drivetrain 6 Check (he performance of the engine, clutch, transmission and driveshafts.
7 Listen for any unusual noises from the engine, clutch and transmission. 8 Make sure that the engine runs smoothly when Idling, and that there is no hesitation when accelerating. 9 Check that the clutch action is smooth and progressive, that tho drive is taken up smoothly, and that the pedal travel Is not excessive. Also listen for any noises when the clutch pedal is depressed. 10 Check that all gears can be engaged smoothly without noise, and that the gear lever action Is not abnormally vague or notchy. 11 Listen for a metallic clicking sound from ihe front of the vehicle, as the vehicle « driven slowly In a circle with the steering on full-lock. Carry out this check In both directions, if a clicking noise is heard, this Indicates wear in a driveshaft |oinl, in which case renew the joint if necessary.
Check the braking system 12 Make sure that the vehicle does not pull to one side when braking, and that the wheels do not lock prematurely when braking hard.
13 Check that there Is no vibration through the steering when braking. 14 Check that the handbrake operates correctiy without excessive movement of th« lever, end that it holds the vehicle stationery on a slope. 15 Test the operation of the brake servo unit as follows. With the engine off, depress the footbrake four or five times to exhaust the vacuum. Hold the brake pedal depressed, then start the engine. As the engine starts, there should be a noticeable give In the brake pedal as vacuum builds up. Allow the engine to run for at least two minutes, and then switch it off. If the brake pedal is depressed now, it should be possible to detect a hiss from the servo es the pedal is depressed. After about four or five applications, no fimher hissing should be heard, and the pedal should feel considerably harder. Note: The vacuum for the servo unit is provided by the vacuum pump mounted on the left-hand end of t/ie cylinder head.
Every 30 000 miles (45 000 km) or 3 years
22 Manual transmission oil level check ;5§
1 Park the vehicle on a level surface. If possible over an inspection pit or on a ramp as the filler/level plug is best reached from under Ihe engine compartment. The oil level must be checked before the car Is driven, or at least 5 minutes after the engine has been switched off. If the oil is checked Immediately after driving the car. some of the oil will remain distnbuted around the transmission compo-nents, resulting In an inaccurate level reading. 2 Wipe clean the area around the filler/level plug, which is situated on tho front of the
transmission (see illustration). Using an Allen key. unscrew the plug and clean it. 3 The oil level should reach the lower edge of the filler/level hole. A certain amount of oil will have gathered behind the filler/level plug, and will trickle out when it is removed; this does not necessarily Indicate that the level Is correct. To ensure that a true level Is established, wait until the Initial trickle has stopped, then add oil as necessary until a trickle of new oil can be seen emerging. The level will be correct when the flow ceases; use only good-quality oil of the specified type-Make sure that the vehicle Is completely level when checking the level and do not overfill. 4 When the level is correct refit and tighten the plug and wipe away any spilt oil.
22.2 Transmission filler/level plug location
Every 40 000 miles (60 000 km) or 4 years
23 Rear brake shoe check
1 Chock the front wheels then jack up the rear of the car and support It on axle stands (see Jacking and Vehicle Support), Remove the rear roadwhecla. 2 Using the inspection hole at the edge ot the brake drum, check that the linings are not worn below the minimum thickness given In the Spec ifi cat Ions (see Illustration). If necessary use a torch. 3 If the friction material on any shoe is worn down to the specified minimum thickness or iess. all four shoes must be renewed as a set, 4 At the same time check for signs of brake fluid leakage. 5 For a comprehensive check, the brake
drum should be removed and cleaned. This will allow the wheel cylinders to be checked, and the condition of the brake drum itself to be fully examined (see Chapter 9). 8 Refit the rubber plugs then lower the car to the ground.
24 Timing belt renewal
Refer to Chapter 2C. Note: Although the normal interval for timing belt
ranees/a!
is 70 000
mHes
(105 000
km),
it is strong recommended that the interval is reduced on vehicles which are subjected to intensive use, ie, mainly short journeys or a lot of stop-start driving. The actual belt renewal interval is therefore very much up to tho individual owner.
That being said, it is highly recommended to err on the side of safety, and renew (he belt at
this
earlier interval, bearing in mind the drastic consequences resulting from belt fetfure.
23.2 Check the thickness of the shoe friction material through the hole on the edge of the drum (arrowed)
Page 49 of 225
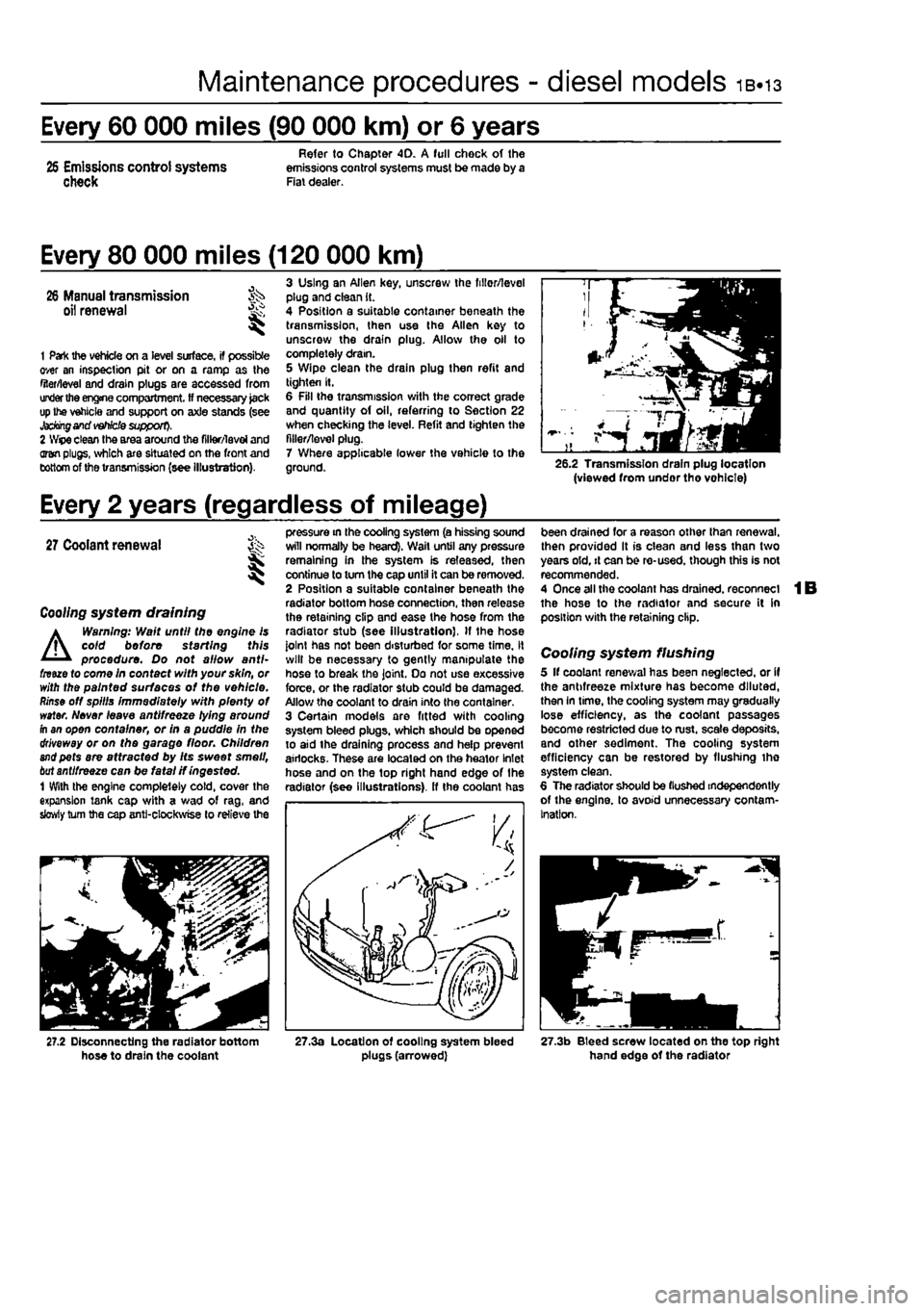
Maintenance procedures - diesel models 1B.13
Every 60 000 miles (90 000 km) or 6 years
Refer to Chapter 40. A full chock of the 26 Emissions control systems emissions control systems must be made by a check Fiat dealer.
Every 80 000 miles (120 000 km)
26 Manual transmission ,v->> oil renewal K
1 Pak the vehicle on a level surface, if possible over an inspection pit or on a ramp as the filer/level and drain plugs are accessed from
under the
engine compartment, ff necessary tack up Ihe vehicle and support on axle stands (see Jacking and
vehicle
support). 2
Wipe
clean the area around the filler/! a vol and vain plugs, which are situated on the front and bottom of the transmission (see Illustration}.
3 Using an Allen key, unscrew the fillor/level plug and clean it. 4 Position a suitable container beneath the transmission, then use the Allen key to unscrew the drain plug. Allow the oil to completely dram. 5 Wipe clean the drain plug then refit and tighten It. 6 Fill the transmission with the correct grade and quantity of oil, referring to Section 22 when checking the level. Refit and tighten the filler/level plug. 7 Where applicable lower the vehicle to the ground. 26.2 Transmission drain plug location (viewed from undor tho vohlcle)
Every 2 years (regardless of mileage)
27
Coolant renewal St I
Coo//ng system draining
A
Warning: Wait until the engine is coid before starting this procedure. Do not allow anti-fnue to come in contact with your skin, or with the painted surfaces of the vehicle.
Rinse
off spills immediately with plenty of water. Never leave antifreeze lying around fh an open container, or in a puddle in the driveway or on the garage floor. Children
and
pets are attracted by Its sweet smell,
bat
antifreeze can be fatal if ingested. 1 With the engine completely cold, cover the expansion tank cap with a wad of rag, and slowly turn the cap anti-clockwise to relieve the
pressure in the cooling system (a hissing sound will normally be heard). Wail until any pressure remaining in the system is released, then continue to turn the cap until it can be removed. 2 Position a suitable container beneath the radiator bottom hose connection, then release the retaining clip and ease the hose from the radiator stub (see Illustration), If the hose joint has not been disturbed for some time, it will be necessary to gently manipulate the hose to break the joint. Do not use excessive force, or the radiator stub could be damaged. Allow the coolant to drain into the container. 3 Certain models are fitted with cooling system bleed plugs, which should be opened to aid the draining process and help prevent airlocks. These are located on the heator Inlet hose and on the top right hand edge of the radiator (see Illustrations), ff the coolant has
been drained for a reason other than renewal, then provided It is clean and less than two years old, it can be re-used, though this is not recommended. 4 Once all the coolant has drained, reconnect the hose to the radiator and secure it in position with the retaining clip.
Cooling system flushing 5 If coolant renewal has been neglected, or if the antifreeze mixture has become diluted, then In time, the cooling system may gradually lose efficiency, as the coolant passages become restricted due to rust, scale deposits, and other sediment. The cooling system efficiency can be restored by flushing tho system clean. 6 The radiator should be (lushed independently of the engine, to avoid unnecessary contam-ination.
27.2 Disconnecting the radiator bottom hose to drain the coolant 27.3a Location of cooling system bleed plugs (arrowed) 27.3b Bleed screw located on the top right hand edge of the radiator
Page 50 of 225
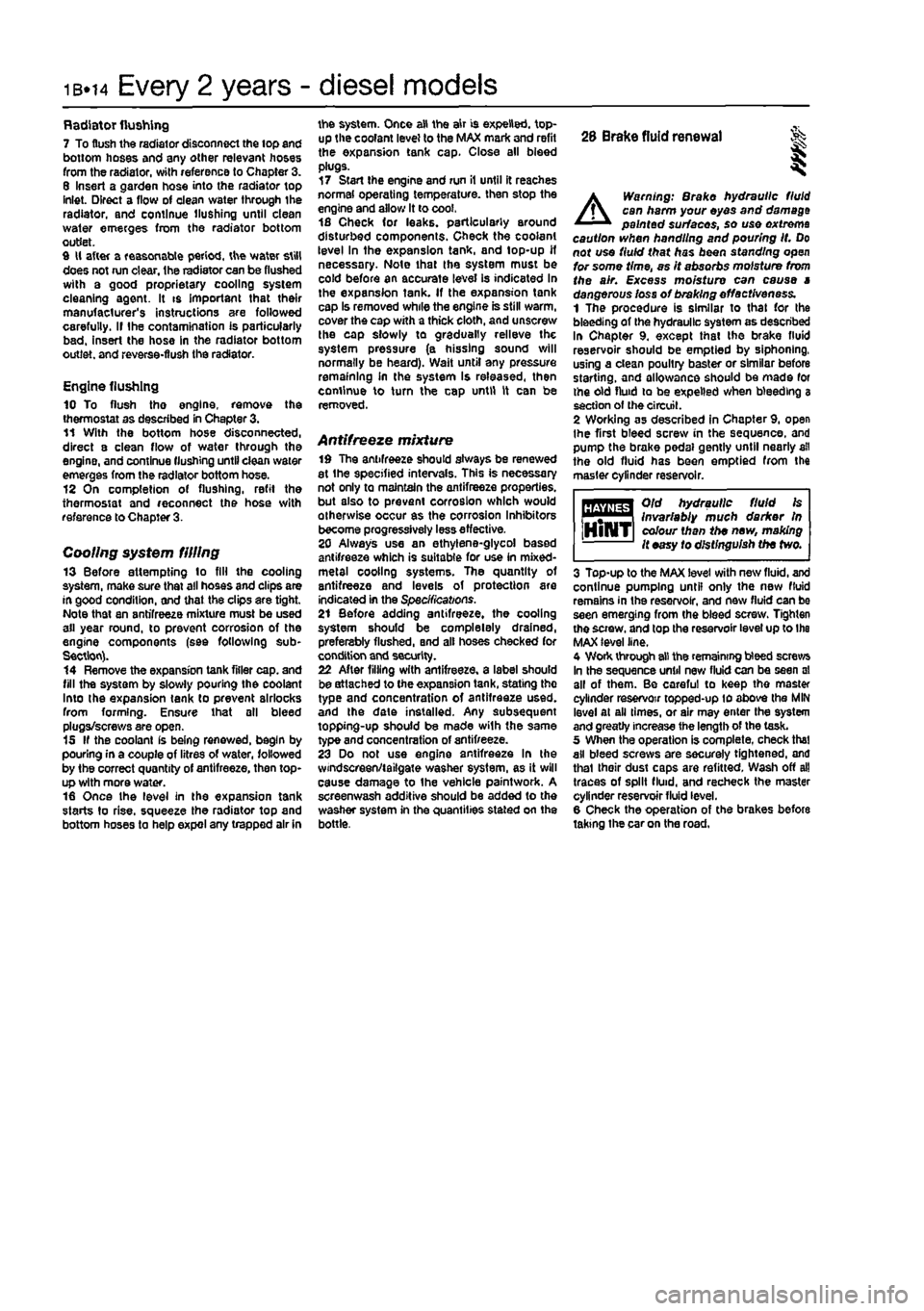
ib.14 Every 2 years - diesel models
Radiator flushing 7 To flush the radiator disconnect the top and bottom hoses and any other relevant hoses from the radiator, with reference to Chapter 3. 8 Insert a garden hose into the radiator top inlet. Direct a flow of dean water through the radiator, and continue Hushing until clean water emerges from the radiator bottom outlet. 9 II after a reasonable period, the water still does not run clear, the radiator can be flushed with a good proprietary cooling system cleaning agent. It is important that their manufacturer's instructions are followed carefully. If Ihe contamination is particularly bad, insert the hose in the radiator bottom outlet, and reverse-flush the radiator.
Engine flushing 10 To flush tho engine, remove the thermostat as described in Chapter 3. 11 With the bottom hose disconnected, direct a clean flow of water through the engine, and continue Hushing until clean water emerges from the radiator bottom hose. 12 On completion of flushing, refit the thermostat and reconnect the hose with reference to Chapter 3.
Cooling system filling 13 Before attempting to fill the cooling system, make sure that all hoses and clips are in good condition, and that the clips are tight. Note that an antifreeze mixture must be used all year round, to prevent corrosion of the engine components (see following sub* Section). 14 Remove the expansion tank filler cap. and fill the system by slowly pouring the coolant Into Ihe expansion tank to prevent airlocks from forming. Ensure that all bleed plugs/screws are open. 15 If the coolant is being renewed, begin by pouring in a couple of litres of water, followed by the correct quantity of antifreeze, then top* up with more water. 18 Once ihe level in the expansion tank starts to rise, squeeze the radiator top and bottom hoses to help expel any trapped air in
the system. Once all the air is expelled, top-up the coolant level to the MAX mark and refit the expansion tank cap. Close all bleed plugs. 17 Start Ihe engine and run il until it reaches normal operating temperature, then stop the engine and allow It to cool. 18 Check for leaks, particularly around disturbed components. Check the coolant level In the expansion tank, and top-up if necessary. Note that the system must be cold before an accurate level Is indicated In the expansion tank. If the expansion tank cap Is removed while the engine is still warm, cover the cap with a thick cloth, and unscrew the cap slowly to gradually relieve the system pressure (a hissing sound will normally be heard). Wait until any pressure remaining in the system Is released, then continue to turn the cap untH it can be removed.
Antifreeze mixture 19 The antifreeze should always be renewed at the specified intervals. This is necessary not only to maintain the antifreeze properties, but also to prevent corrosion which would otherwise occur as the corrosion Inhibitors become progressively less effective. 20 Always use an ethylene-glycol based antifreeze which is suitable for use in mixed-metal cooling systems. The quantity of antifreeze and levels of protection are indicated in the Specifications. 21 Before adding antifreeze, the cooling system should be complelely drained, preferably flushed, and all hoses checked for condition and security. 22 After filling with antifreeze, a label should be attached to the expansion tank, stating the type and concentration of antifreeze used, and the dale installed. Any subsequent topping-up should bs made with the same type and concentration of antifreeze. 23 Do not use engine antifreeze In the windscreen/tailgate washer system, as it will cause damage to the vehicle paintwork. A screenwash additive should be added to the washer system in the quantities stated on the bottle.
28 Brake fluid renewal
A
Warning: Brake hydraulic fluid can harm your eyas and damage painted surfaces, so use extreme caution when handling and pouring It. Do not use fluid that has been standing open for some time, as It absorbs moisture from the air. Excess moisture can causa a dangerous loss of braking effectiveness. 1 The procedure is similar to that for the bleeding of the hydraulic system as described In Chapter 9. except that the brake fluid reservoir should be emptied by siphoning, using a clean poultry baster or similar before starting, and allowance should be made for the old fluid to be expelled when bleeding a section of the circuit. 2 Working as described in Chapter 9, open Ihe first bleed screw in the sequence, and pump the brake pedal gently until nearly all the old fluid has been emptied from the master cylinder reservoir.
ffffTOgf Old hydraulic fluid Is
lifcjllitt*
Invariably much darker In [HINT] colour than the new, making /{easy to distinguish the two.
3 Top-up to the MAX level with new fluid, and continue pumping until only the new fluid remains in the reservoir, and new fluid can be seen emerging from (he bleed screw. Tighten the screw, and top the reservoir level up to Ihe MAX level line. 4 Work through all the remaining bleed screws In the sequence until new fluid can be seen al all of them. Be careful to keep the master cylinder reservoir topped-up 10 above the MIN level al all limes, or air may enter the system and greatly increase the length of the task. 5 When the operation is complete, check thai all bleed screws are securely tightened, and that their dust caps are refitted. Wash off ail traces of split fluid, and recheck the master cylinder reservoir fluid level. 6 Check the operation of the brakes before taking the car on the road,
Page 51 of 225
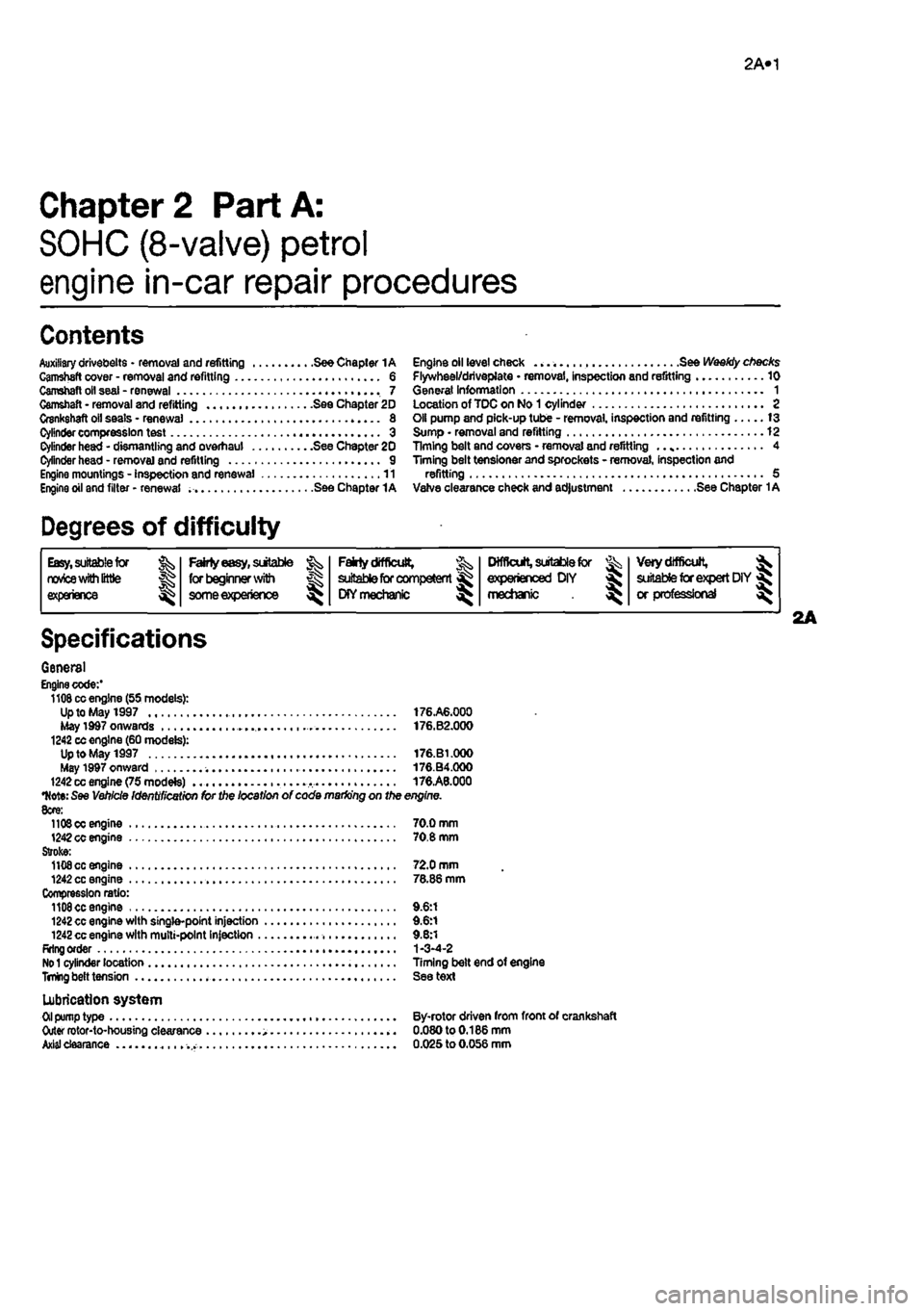
2A«1
Chapter 2 Part A:
SOHC (8-valve) petrol
engine in-car repair procedures
Contents
Auxiliary drivebelts • removal and refitting See Chapter 1A Gamstaft cover - removal and refitting 6 Camshaft oil seal - renewal 7 Camshaft • removal and refitting See Chapter 20 Crankshaft oil seals - renewal 8 Cylinder compression test 3 Cylinder head - dismantling and overhaul See Chapter 20 Cylinder head - remove] and refitting 9 Engine mountings - Inspection and renewal 11 Engine oil and filter • renewal See Chapter 1A
Degrees of difficulty
Engine oil level check See Weekiy checks Flywheel/driveplate • removal, inspection and refitting 10 General Information 1 Location of TOC on No 1 cylinder 2 Oil pump and pick-up tube - removal, inspection and refitting 13 Sump • removal and refitting 12 Timing belt and covers • removal and refitting .. 4 Timing belt tensioner and sprockets - removal, inspection and refitting 5 Vafve clearance check and adjustment See Chapter 1A
Easy, suitable (or twics with little |g experience ^
Fairty easy, suitable jk for beginner with & some experience ^
Fatrty difficult, ^ suitable for competent ^ CKYmechanic ^
Difficult, suitable for ^ experienced DIY « mechanic ^
Veiy difficult, ^ aiitabte for expert DIY « or professional
Specifications
General Engine code:' 1108 cc engine (55 models): Up to May 1997 176.A6.000 May 1d97 onwards • . 176.B2.000 1242 cc engine (60 models): Up to May 1997 176.B1.000 May 1997 onward 176.B4.000 1242 cc engine (75 modete) 176.A8.000
•Note:
See Vehicle Identification for the location of code marking on the engine. 8cre: 11O0OC engine 70.0 mm 1242 cc engine 70.8 mm Stroke: 1108 cc engine 72.0 mm 1242 cc engine 78.86 mm Compression ratio: 1108 cc engine 9.6:1 1242 cc engine with single-point injection 9.6:1 1242 cc engine with multi-point injection 9.8:1 Rrlng order 1-3-4-2
No 1
cylinder location Timing belt end of engine
TnUng
belt tension See text
Lubrication system
Oil
pump type By-rotor driven from front of crankshaft Outer rotor-to-housing clearance 0.080to0.186mm
Axial
clearance 0.025 to 0.056 mm
Page 52 of 225
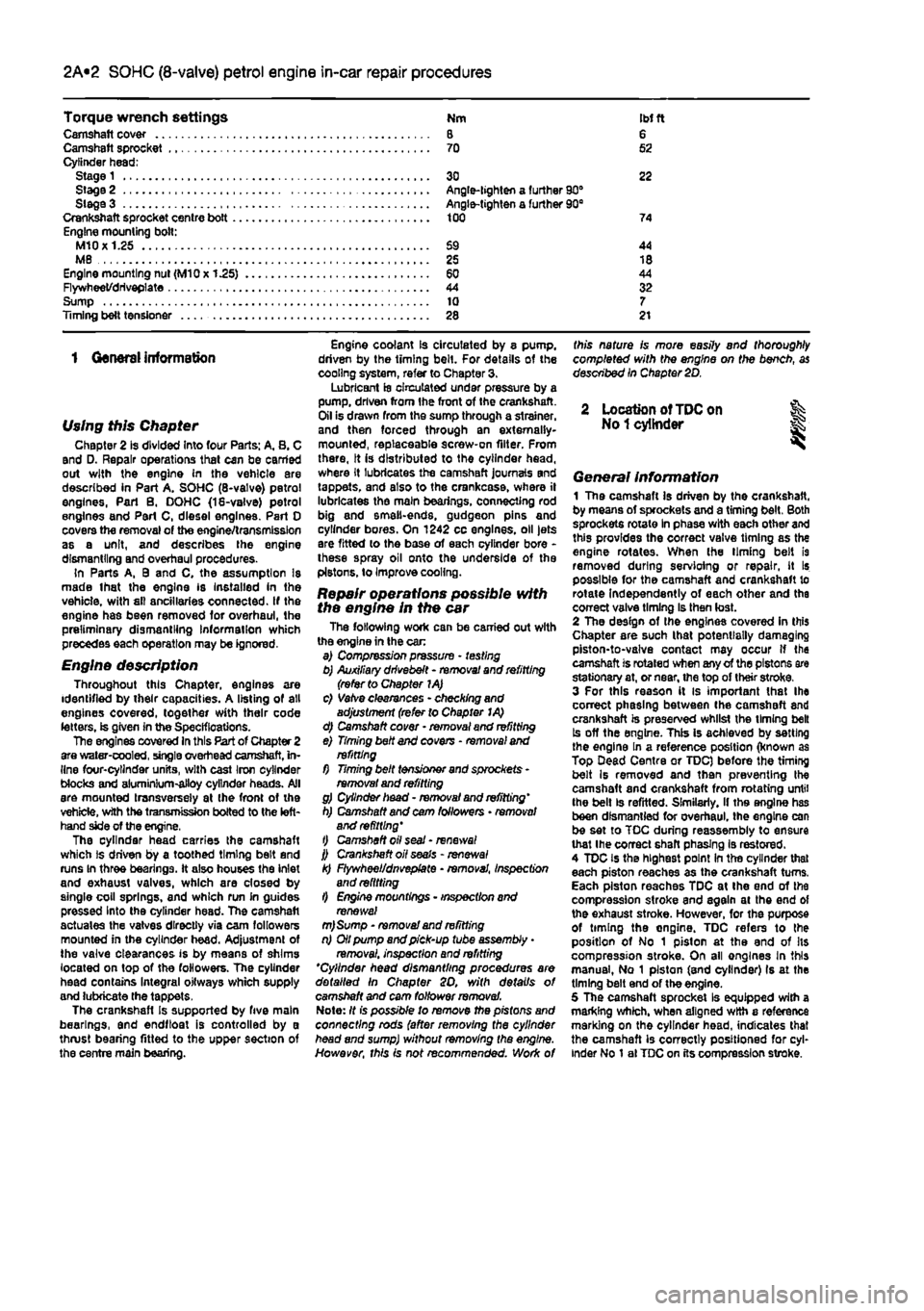
2A*10 SOHC (8-valve) petrol engine in-car repair procedures
Torque wrench settings Nm
IM
ft Camshaft cover 8 6 Camshaft sprocket 70 52 Cylinder head; Stage 1 30 22 Stage 2 Angle-lighten a further 90° Siege 3 Angle-tighten a further 90B Crankshaft sprocket centre bott 100 74 Engine mounting bolt: M10X1.25 69 44 MB 25 18 Engine mounting nut (M10x 1.25) 60 44 Flywheet/driveplate 44 32 Sump 10 7 Timing belt tensJoner 28 21
1 General information
Using this Chapter Chapter 2 is divided Into four Parts: A. 8. C and D. Repair operations that can be carried out with the engine in the vehicle are described in Part A. SOHC (8-valve) petrol engines, Part B. DOHC (18-valve) petrol engines and Part C, diesel engines. Part 0 covers the removal of the engine/transmission as a unit, and describes the engine dismantling and overhaul procedures. In Parts A, 9 and C, the assumption Is made lhat the engine is Installed in the vehicle, with sll ancillaries connected. If the engine has been removed for overhaul, the preliminary dismantling Information which precedes each operation may be ignored.
Engine description Throughout this Chapter, engines are identified by their capacities. A listing of all engines covered, together with their code letters, is given in the Specifications. The engines covered In this Part of Chapter 2 are water-cooled, single overhead camshaft, in-line four-cylinder units, with cast Iron cylinder Mocks and aluminium-alloy cylinder heads. All are mounted transversely at the front ot the vehicle, with the transmission bolted to the left-hand side of the engine, The cylinder head carries the camshaft which is driven by a toothed timing belt and runs In three bearings. It also houses the inlet and exhaust valves, which are closed by single coil springs, and which run in guides pressed Into the cylinder head. The camshaft actuates the vatves directly via cam followers mounted in the cylinder head. Adjustment of the valve clearances is by means of shims located on top of the followers. The cylinder head contains Integral oitways which supply and lubricate the tappets. The crankshafl Is supported by five main bearings, and endftoat is controlled by a thrust bearing fitted to the upper section of the centre main bearing.
Engine coolant is circulated by 8 pump, driven by the timing belt. For details of the cooling system, refer to Chapter 3. Lubricant is circulated under pressure by a pump, driven from ihe front of the crankshaft. Oil Is drawn from the sump through a strainer, and then forced through an externally-mounted, replaceable screw-on filter. From there, It is distributed to the cylinder head, where It lubricates the camshaft journals and tappets, and also to the crankcase, where il lubricates the main bearings, connecting rod big and smell-ends, gudgeon pins and cylinder bores. On 1242 cc engines, oil jets are fitted lo the base of each cylinder bore -these spray oil onto the underside of the pistons, to Improve cooling.
Repair operations possible with the engine in the car The following work can be carried out with the engine in the car a) Compression pressure - testing b) Auxiliary drivebelt - removal and refitting (refer to Chapter 1A) c) Vatve clearances - checking and adjustment (refer to Chapter I A) d) Camshaft cover - removal and refitting e) Timing belt and covens - removal and refitting f) Timing belt tensioner and sprockets -removal and refitting g) Cylinder head - removal and refitting' h) Camshaft and cam followers • removal and refitting' t) Camshaft oil seal - renews/ j) Crankshaft oil seals - renewal k) Flywheel/dnvepfate • removal, inspection and refitting l) Engine mountings - inspection and renewal m)Sump - removal and refitting n) Oil pump and pick-up tube assembly
•
removai. inspection and refitting *Cylinder head dismantling procedures are detailed In Chapter SO, with details of camshaft and cam follower removal. Note: It is possible to remove the pistons and connecting rods (after removing the cylinder head and sump) without removing the engine. However, this is not recommended. Work of
this nature is more easily and thoroughly completed with the engine on the bench, as described In Chapter 2D.
2 Location of
TDC
on % No
1
cylinder
General Information 1 The camshaft Is driven by the crankshaft, by means of sprockets and a timing belt. Both sprockets rotate In phase with each other and this provides the correct valve timing as the engine rotates. When (he liming belt is removed during servioing or repair, it Is possible for the camshaft and crankshaft to rotate Independently of each other and the correct valve timing Is then lost. 2 The design of the engines covered In this Chapter are such lhat potentially damaging piston-to-valve contact may occur if the camshaft is rotated when any of the pistons are stationary at, or near, the top of their stroke. 3 For this reason it is important lhat Ihe correct phasing between the camshaft and crankshaft is preserved whilst the timing belt Is off the engine. This is achieved by setting the engine In a reference position (known as Top Dead Centre or TDC) before the timing belt Is removed and then preventing the camshaft and crankshaft from rotating until the belt is refitted. Similarly, if ths engine has been dismantled for overhaul, the engine can be set to TOC during reassembly to ensure that Ihe correct shaft phasing is restored. 4 TDC is the highest point In the cylinder that each piston reaches as the crankshaft turns. Each piston reaches TDC at Ihe end of the compression stroke and again at the end of the exhaust stroke. However, for the purpose of timing the ongine. TDC refers to the position of No 1 piston at the end of Its compression stroke. On ail engines In this manual, No 1 piston (and cylinder) Is at the timing belt end of the engine. 5 The camshaft sprocket Is equipped with a marking which, when aligned with a reference marking on the cylinder head, indicates that the camshaft is correctly positioned for cyl-inder No 1 al TDC on its compression stroke.
Page 53 of 225
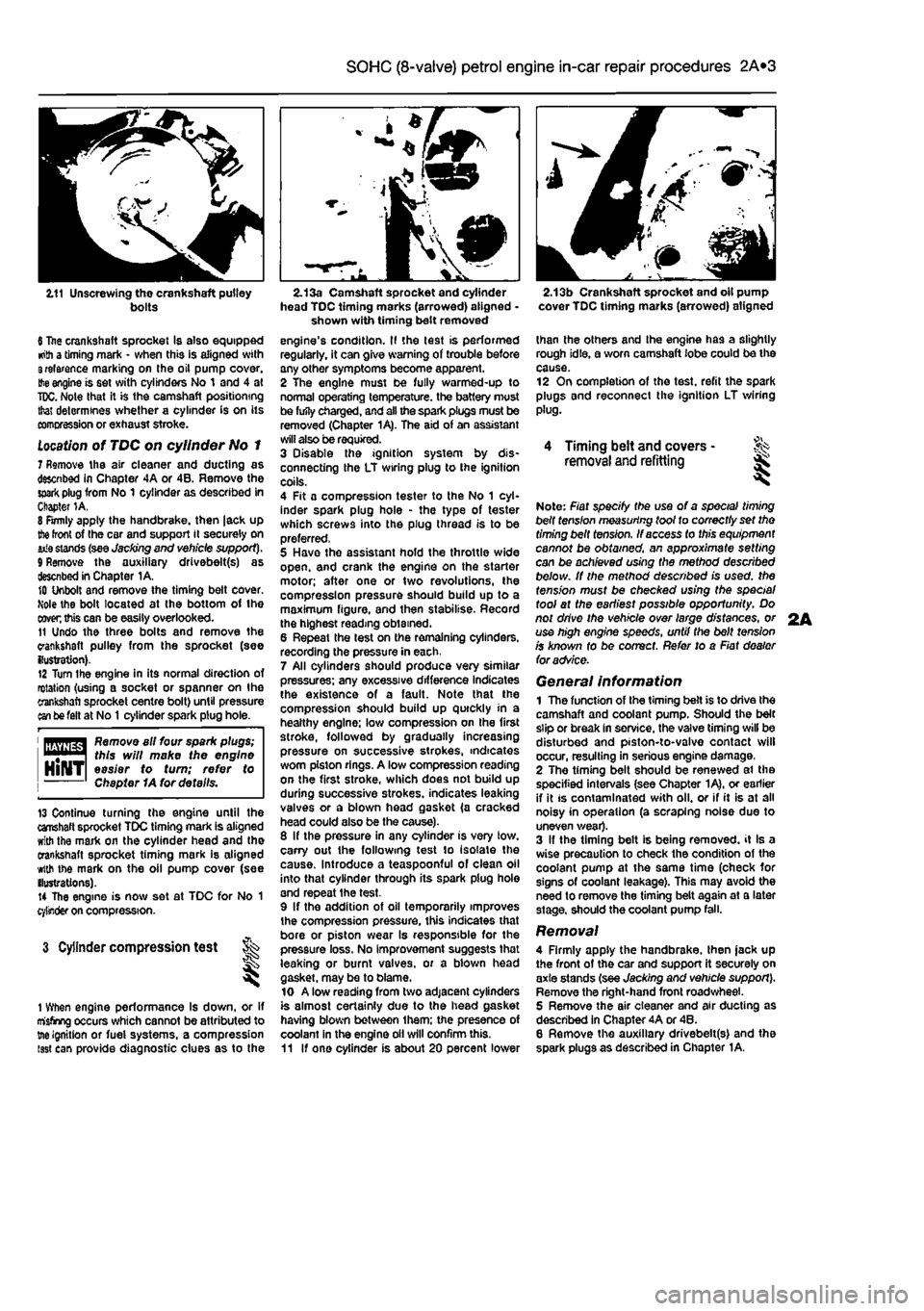
2A*10 SOHC (8-valve) petrol engine in-car repair procedures
2.11 Unscrewing the crankshaft pulley bolts
6 Itae crankshaft sprocket Is also equipped •nth a timing mark - when this is aligned with 3relarence marking on the oil pump cover.
Hie
engine is set with cylinders No 1 and 4 at
TDC.
Note that it is the camshaft positioning that determines whether a cylinder is on its comcression or exhaust stroke.
Location
of TDC on cylinder No 1 7 Remove the air cleaner and ducting as descnbed in Chapter 4A or 4B. Remove the
spark
plug from No 1 cylinder as described in Chapter 1A. 8 Firmly apply the handbrake, then |ack up
the
front of the car and support it securely on iiia stands (see Jacking end vehicle support). 9 Remove the auxiliary drivebelt(s) as described in Chapter 1A. 10 Unbolt and remove the timing belt cover. Mole the bolt located at the bottom of the
coven
this can be easily overlooked. 11 Undo the three bolts and remove the crankshaft pulley from the sprocket (see {lustration). 12 Turn Ihe engine in its normal direction of rotation (using a socket or spanner on Ihe crankshaft sprocket centre bolt) until pressure an be felt at No
1
cylinder spark plug hole.
1 flfliyflg^ Remove all four spark plugs; "••"•1 this will make the engine HlNTl easier to turn; refer to Chapter 1A for details.
13 Continue turning the engine until the crahaft sprocket TDC timing mark is aligned with the mark on the cylinder head and the crankshaft sprocket timing mark is aligned with the mark on the oil pump cover (see ilustrations). 14 The engine is now set at TDC for No 1 cylinder on compression.
3 Cylinder compression test t ^
1 When engine performance Is down, or if misfiring occurs which cannot be attributed to tne ignition or fuei systems, a compression isst can provide diagnostic clues as to the
2.13a Camshaft sprocket and cylinder head TDC timing marks (arrowed) aligned -shown with timing belt removed engine's condition. II the test is performed regularly, it can give warning of trouble any other symptoms become apparent. 2 The engine must be fully warmed-up to normal operating temperature, the battery must be fufly charged, and all the spark plugs must be removed (Chapter 1A). The aid of an assistant will also be required. 3 Disable the ignition system by dis-connecting the LT wiring plug to the ignition coils. 4 Fit a compression tester to the No 1 cyl-inder spark plug hole - the type of tester which screws into the plug thread is to be preferred, 5 Have the assistant hold the throttle wide open, and crank the engine on the starter motor; after one or two revolutions, the compression pressure should build up to a maximum figure, and then stabilise. Record the highest reading obtained. 6 Repeat the lest on the remaining cylinders, recording the pressure in each. 7 All cylinders should produce very similar pressures; any excessive difference indicates the existence of a fault. Note that the compression should build up quickly in a healthy engine; low compression on the first stroke, followed by gradually increasing pressure on successive strokes, indicates worn piston rings. A low compression reading on the first stroke, which does not build up during successive strokes, indicates leaking valves or a blown head gasket (a cracked head could also be the cause). 8 If the pressure in any cylinder is very low. carry out the following test to isolate the cause. Introduce a teaspoonful of clean oil into that cylinder through its spark plug hole and repeat the test. 9 If the addition of oil temporarily improves the compression pressure, this indicates that bore or piston wear Is responsible for the pressure loss. No improvement suggests that leaking or burnt valves, or a biown head gasket, may be to blame. 10 A low reading from two adjacent cylinders is almost certainly due to the head gasket having blown between them; the presence of coolant in the engine oil will confirm this. 11 If one cylinder is about 20 percent lower
2.13b Crankshaft sprocket and oil pump cover TDC timing marks (arrowed) aligned
than the others and Ihe engine has a slightly rough idle, a worn camshaft lobe could be the cause. 12 On completion of the test, refit the spark plugs and reconnect the ignition LT wiring plug.
4 Timing belt and covers -removal and refitting ^
Note: Fiat specify the use of a special timing belt fens/on measuring toot to correctly set tho timing belt tension. If access to this equipment cannot be obtained, an approximate setting can be achieved using the method described below. It the method described is used, the tension must be checked using the special tool at the earliest possible opportunity. Do not drive the vehicle over large distances, or use high engine speeds, until the belt tension is known fo be correct. Refer to a Fiat dealer foradvSce.
General information 1 The function of the timing belt is to drive Ihe camshaft and coolant pump. Should the belt slip or break In service, the valve timing will be disturbed and piston-to-valvo contact will occur, resulting in serious engine damage, 2 The timing belt should be renewed ai the specified intervals (see Chapter 1A), or earlier if it is contaminated with oil. or if it is at all noisy in operation (a scraping noise due to uneven wear). 3 If the timing belt is being removed, it Is a wise precaution to check the condition of the coolant pump at the same time (check for signs of coolant leakage). This may avoid the need to remove the timing belt again at a later stage, should the coolant pump fall.
Removal 4 Firmly apply the handbrake, then jack up the front of the car and support it securely on axle stands (see Jacking and vehicle support). Remove the right-hand front road wheel. 5 Remove the air cleaner and air ducting as described in Chapter 4A or 46. 6 Remove the auxiliary drivebelt(s) and the spark plugs as described in Chapter 1A.
2A