transmission fluid FIAT PUNTO 1999 176 / 1.G User Guide
[x] Cancel search | Manufacturer: FIAT, Model Year: 1999, Model line: PUNTO, Model: FIAT PUNTO 1999 176 / 1.GPages: 225, PDF Size: 18.54 MB
Page 33 of 225
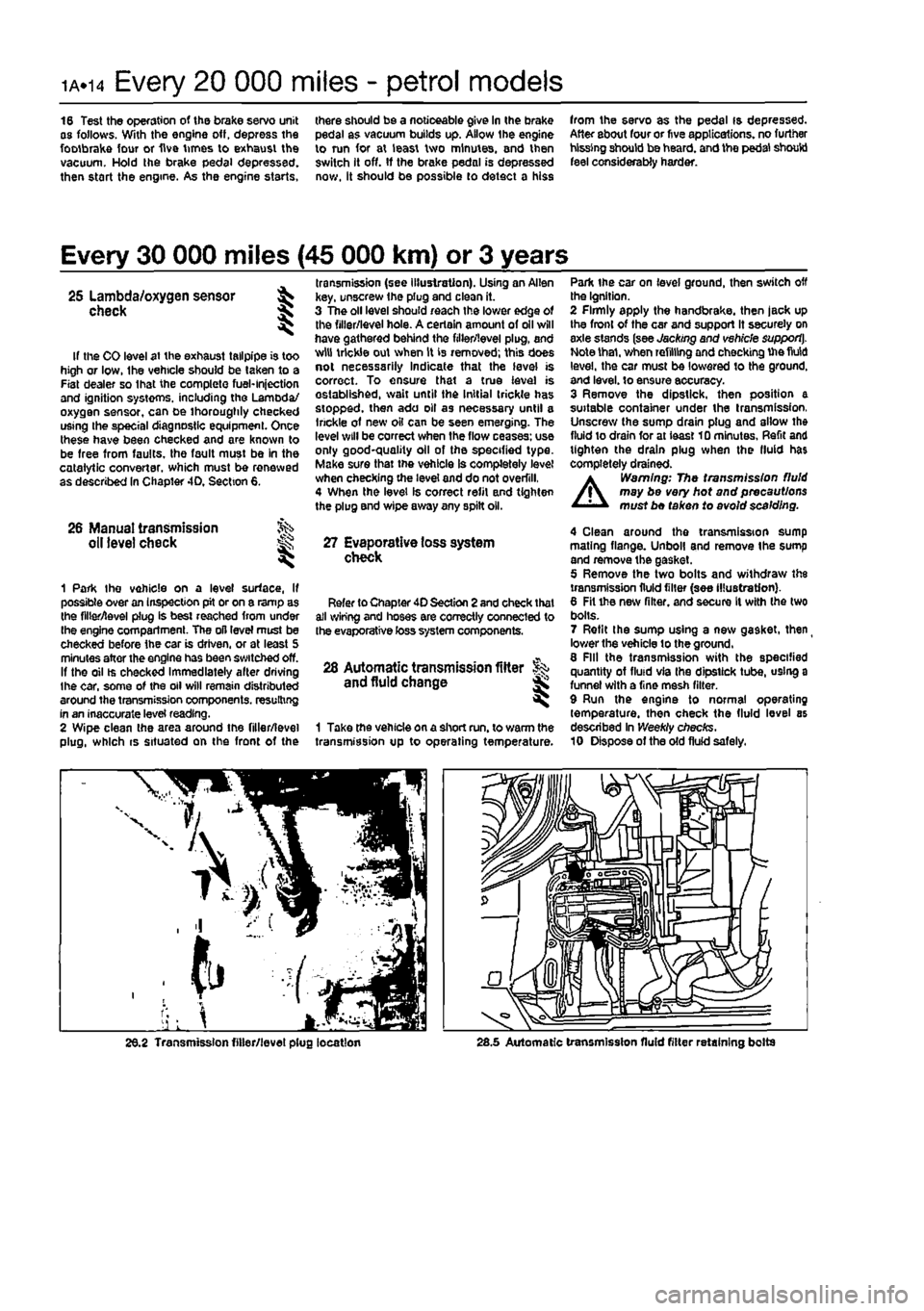
ia.14 Every 20 000 miles - petrol models
16 Test the operation of the brake servo unit as follows. With the engine off, depress the footbrake four or five times to exhaust the vacuum. Hold the brake pedal depressed, then start the engine. As the engine starts.
there should be a noticeable give In the brake pedal as vacuum builds up. Allow the engine to run for at least tsvo minutes, and then switch it off. If the brake pedal is depressed now. it should be possible to detect a hiss
from the servo as the pedal is depressed. After about four or five applications, no further hissing should be heard, and the pedal shouto feel considerably harder.
Every 30 000 miles (45 000 km) or 3 years
. transmission (see illustration). Using an Allen 25 Lambda/oxygen sensor ^ key, unscrew the plug and clean it. check \ 3 The oil level should reach the lower edge of ^ the filler/level hole. A certain amount of oil will have gathered behind the filler/level plug, and If the CO level at the exhaust tailpipe is too w,u tr,cWe out when is 'e™oved; this does high or low, Ihe vehicle should be taken to a «©l necessarily Indicate that the level is Fiat dealer so lhat the complete fuel-injection correct. To ensure that a true level is and ignition systems, including the Lamoda/ established, wait until the Initial trickle has oxygen sensor, can be thoroughly checked stopped, then ado oil as necessary until a using the special diagnostic equipment. Once ,r,ckle o1 new oil can be seen emerging. The these have been checked and are known to 'W wl" be correct when ,he flow ceases-us® be free from faults, the fault must be in the good-quality oil of the specified type, catalytic converter, which must be renewed Make sur®that vehicle Is completely level as described In Chapter 4D, Section 6. checking the level and do not overfill, 4 When the level Is correct refit and tighten the plug and wipe away any spilt oil.
26 Manual transmission oil level check ^ 27 Evaporative loss system ^ check
1 Park Ihe vehicle on a level surface, If possible over an inspection pit or on a ramp as the filler/level plug is best reached from under Ihe engine compartment. The oil level must be checked before the car is driven, or at least 5 minutes after the engine has been switched off. If the oil ts checked Immediately alter driving the car, some of the oil will remain distributed around the transmission components, resulting in an inaccurate level reading. 2 Wipe clean the area around the filler/level plug, which is situated on the front of the
Refer to Chapter 40 Section 2 and check that all wiring and hoses are correctly connected to the evaporative toss system components.
28 Automatic transmission fitter and fluid change
1 Take the vehicle on a short run. to warm the transmission up to operating temperature.
Park the car on level ground, then switch off the Ignition. 2 Firmly apply the handbrake, then jack up the front of the car and support It securely on axle stands (see Jacking and vehicle support]. Note thai, when refilling and checking Uie fluid level, the car must be lowered to the ground, and level, to ensure accuracy. 3 Remove the dipstick, then position a suitable container under the transmission, Unscrew the sump drain plug and allow the fluid to drain for at ieast 10 minutes. Refit and tighten the drain plug when the fluid has completely drained.
A
Warning: The transmission fluid may be very hot and precautions must be taken to avoid scalding.
4 Clean around the transmission sump mating flange. Unboll and remove the sump and remove the gasket. 5 Remove the two bolts and withdraw the transmission fluid filter {see illustration). 6 Fit the new filter, and secure It with the two bolts. 7 Refit the sump using a new gasket, then
_
lower the vehicle to the ground, 8 Fill the transmission with the specified quantity of fluid via Ihe dipstick tube, using a funnel with a fine mesh filter. 9 Run the engine to normal operating temperature, then check the fluid level as described In Weekly checks. 10 Dispose of the old fluid safely.
26.2 Transmission filler/level plug location 28.5 Automatic transmission fluid filter retaining bolts
Page 37 of 225
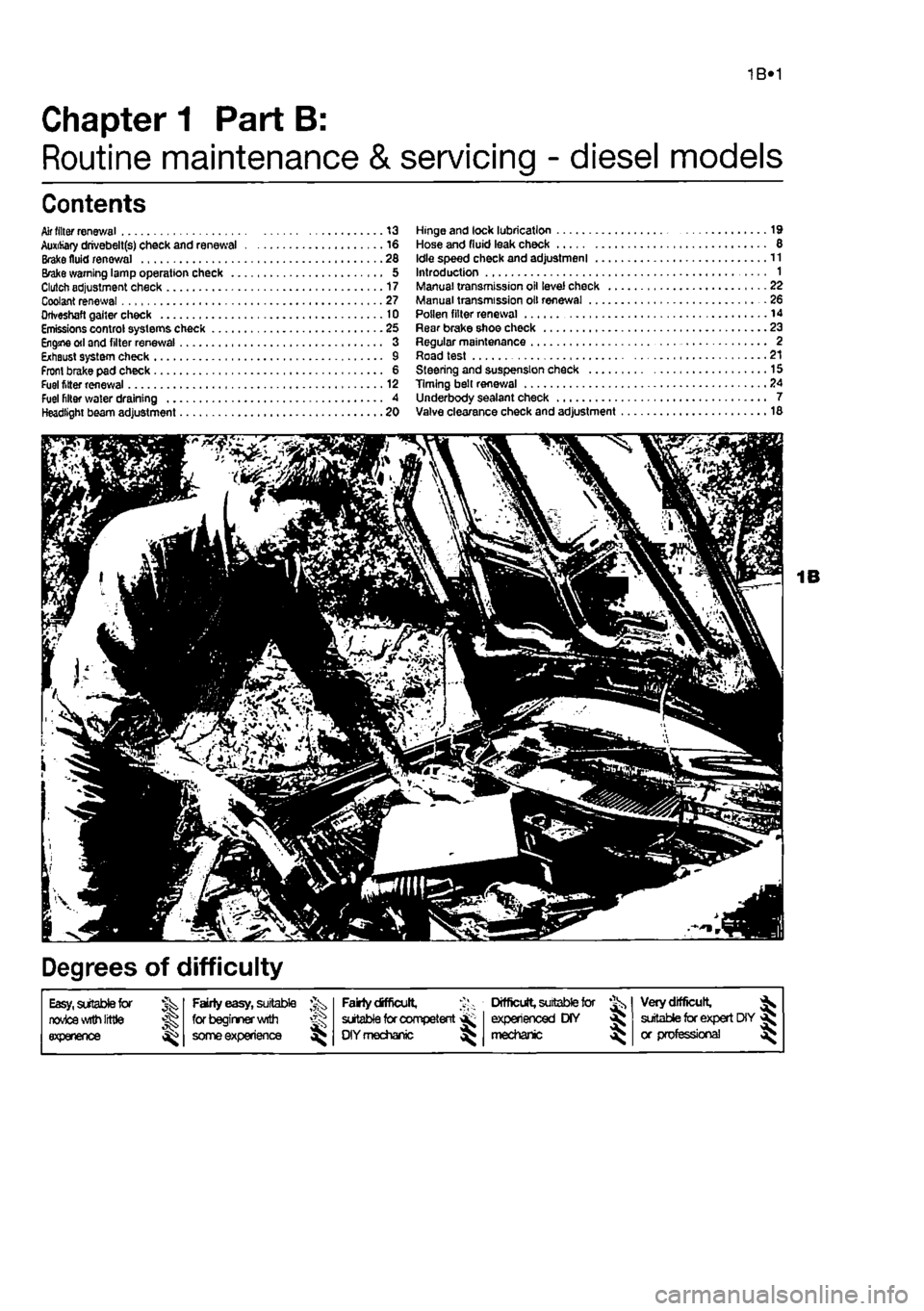
1B»1
Chapter
1
Part B:
Routine maintenance & servicing - diesel models
Contents
Air filter renewal 13 Auxiliary drivebelt(s) check and renewal 16 Brake fluid renewal 2d Brake warning lamp operation check 5 Clutch adjustment check 17 Coolant renewal 27 Drtv«shaft gaiter check 10 Emissions control systems check 25
Engage
oil and filter renewal 3 Exhaust system check 9 Front brake pad check 6
Fuel
fitter renewal 12 Fuel Filter water draining 4 Headlight beam adjustment 20
Hinge and lock lubrication 19 Hose and fluid leak check 6 Idle speed check and adjustmenl 11 Introduction ... 1 Manual transmission oil level check 22 Manual transmission oil renewal - 26 Pollen filter renewal 14 Rear brake shoe check 23 Regular maintenance 2 Road test 21 Steering and suspension check 15 Timing belt renewal 24 Underbody sealant check 7 Valve clearance check and adjustment 16
^m
Degrees of difficulty
Easy, sutable for % Fairly easy, suitable FaHycifficult, i'. Difficult, suitable fa Very difficult, novice with irttte % for beginner with suitable for competent experienced DIY
1
suitable for expert DIY * or professional jQ experience some experience DIY mechanic mechanic 1
suitable for expert DIY * or professional jQ
Page 38 of 225
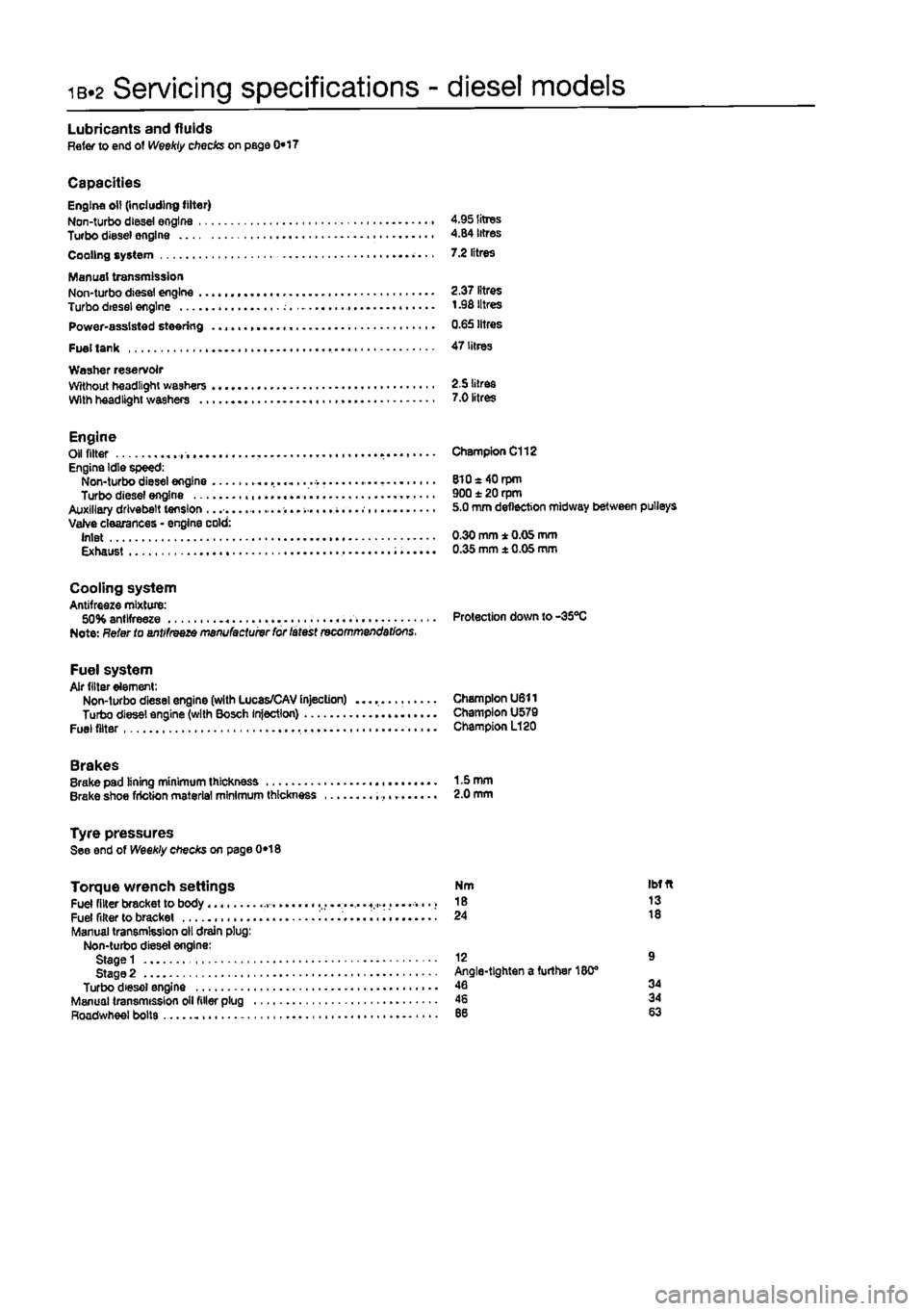
1B.2
Servicing specifications - diesel models
Lubricants and fluids Refer to end of Weekly checks on page 0*17
Capacities Engine oil (including filter) Non-turbo diesei engine 4.95 litres Turbo diesel engine 4.84 litres Cooling system 7.2 litres
Manual transmission Non-turbo diesel engine 2.37 litres Turbo diesei engine t .98 litres Power-assisted steering 0.65 litres
Fuel tank 47 litres Washer reservoir Without headlight washers 2.5 litres With headlight washers 7.0 litres
Engine Oil fitter Engine Idle speed: Non-turbo diesel engine Turbo diesel engine Auxiliary drivebelt tension ...... Valve clearances • engine cold: Inlet Exhaust
Champion C112
8l0«40rpm 900 ± 20 rpm 5.0 mm deflection midway between pulleys
0.30 mm * 0.05 mm 0.35 mm ± 0.05 mm
Cooling system Antifreeze mixture: 50% antifreeze Protection down to-35°C Note: Refer to antifreeze manufactuivr for latest recommendations.
Fuel system Air filter element: Non-turbo diesel engine (with Lucas/CAV Injection) Champion U611 Turbo diesel engine (with Bosch Injection) Champion U579 Fuel filter Champion L120
Brakes Brake pad lining minimum thickness 1-5 mm Brake shoe friction material minimum thickness 2.0 mm
Tyre pressures See end of Weekly checks on page 0*18
Torque wrench settings Fuel filter bracket to body ..... « Fuel filter to bracket i........ Manual transmission oil drain plug: Non-turbo diesel engine: Stage 1 Stage 2 Turbo diesel engine Manual transmission oil filler plug Roadwheel bolts
Nm Ibfft 18 13 24 18
12 9 Angle-tighten a further 180® 46 34 46 34
Page 39 of 225
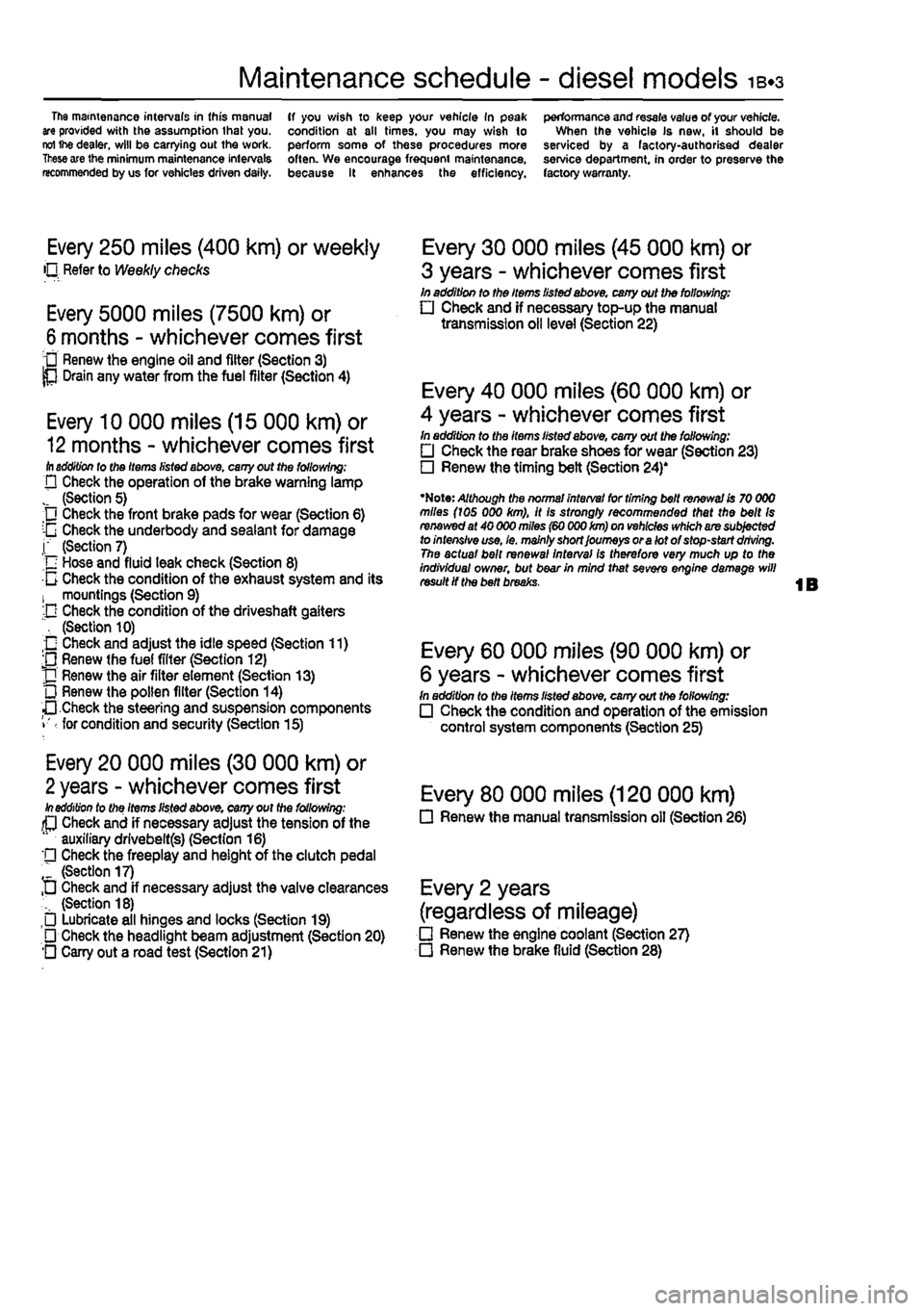
Maintenance schedule - diesel models 1B.3
The mamtenance intervals in this manual are provided with the assumption that you. reI ihe dealer, will be carrying out the work.
These
are the minimum maintenance intervals recommended by us for vehicles driven daily.
ff you wish to keep your vehicle In peak condition at all times, you may wish to perform some of these procedures more often. We encourage frequent maintenance, because it enhances the efficiency.
performance and resale value of your vehicle. When the vehicle Is new, it should be serviced by a factory-authorised dealer service department, in order to preserve the factory warranty.
Every 250 miles (400 km) or weekly O Refer to Weekly checks
Every 5000 miles (7500 km) or
6
months - whichever comes first • Renew the engine oil and filter (Section 3) P Drain any water from the fuel filter (Section 4)
Every 10 000 miles (15 000 km) or
12
months - whichever comes first ill addition lo tho Items listed above, cany out the following; D Check the operation of the brake warning lamp J (Section 5) Check the front brake pads for wear (Section 6) :-G Check the underbody and sealant for damage j" (Section 7) n Hose and fluid leak check (Section 8) 0 Check the condition of the exhaust system and its 1 mountings (Section 9) -D Check the condition of the driveshaft gaiters ", (Section 10) O Check and adjust the idle speed (Section 11) ;0 Renew (he fuel filter (Section 12) J] Renew the air filter element (Section 13) L) Renew the pollen filter (Section 14) •• Check the steering and suspension components • for condition and security (Section 15)
Every 20 000 miles (30 000 km) or
2
years - whichever comes first In addition to the Items listed above, cany out the following: (P Check and if necessary adjust the tension of the auxiliary drlvebeltfs) (Section 16) '• Check the freeplay and height of the clutch pedal " (Section 17) D Check and if necessary adjust the valve clearances (Section 18) Lubricate all hinges and locks (Section 19) • Check the headlight beam adjustment (Section 20) O Cany out a road test (Section 21)
Every 30 000 miles (45 000 km) or
3 years - whichever comes first In addition to the Items listed above, cany out the following: • Check and if necessary top-up the manual transmission oil level (Section 22)
Every 40 000 miles (60 000 km) or
4 years - whichever comes first In addition to the items listed above, cany out the following: • Check the rear brake shoes for wear (Section 23) • Renew the timing belt (Section 24)'
•Note: Although the normal interval for timing belt renewal is 70 000 miles (ids 000 km), it is strongly recommended that the belt Is renewed at 40 000 miles (60 000 km) on vehicles which are subjected to intensive use, le. mainly short Journeys or a lot of stop-start driving. The actual bait renewal interval Is therefore very much up to the Individual owner, but bear in mind that sevefe engine damage will result if the belt breaks.
Every 60 000 miles (90 000 km) or
6 years - whichever comes first In addition to the Items listed above, cany out the following: • Check the condition and operation of the emission control system components (Section 25)
Every 80 000 miles (120 000 km) • Renew the manual transmission oil (Section 26)
Every 2 years
(regardless of mileage) • Renew the engine coolant (Section 27) • Renew the brake fluid (Section 28)
Page 40 of 225
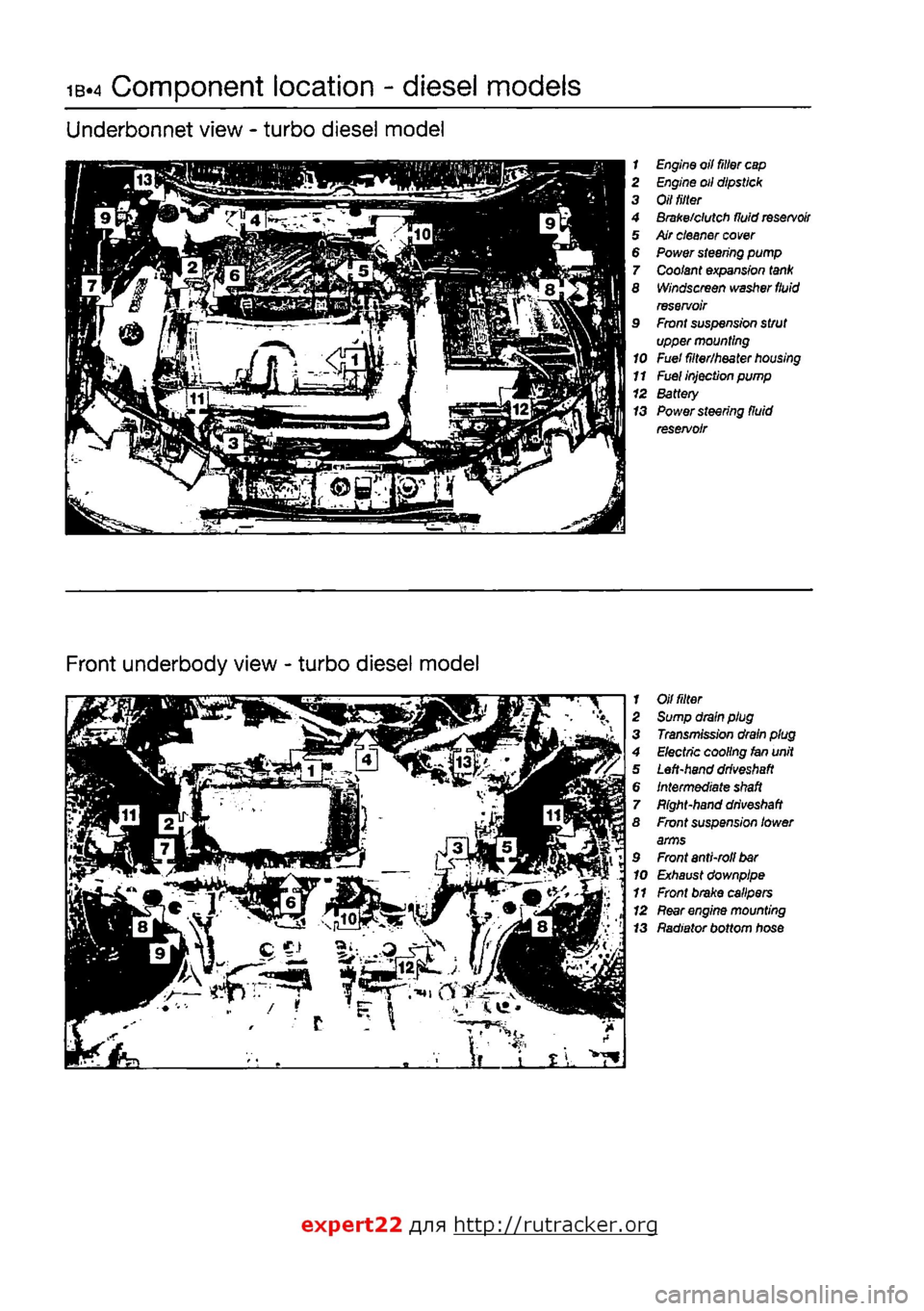
ib-4 Component location - diesel models
Underbonnet view - turbo diesel model
1 Engine oil filter
cap
2 Engine oil dipstick 3 Oil
tilter
4 Brake/clutch fluid
reservoir
5 Air cleaner
cover
6 Power steering pump 7 Coolant expansion
tank
8 Windscreen washer
fluid
reservoir 9 Front suspension strut upper mounting 10 Fuel filter/heater
housing
11
Fuel
injection pump 12 Battery 13 Power steering fluid reservoir
Front underbody view - turbo diesel model
1 Oil
fitter
2 Sump drain plug 3 Transmission drain plug 4 Electric cooling fan unit 5 Left-hand
driveshaft
6 Intermediate
shaft
7 Bight-hand
driveshaft
8 Front suspension lower arms 9 Front anti-roll
bar
10 Exhaust downpipe 11 Front brake calipers 12
Rear
engine mounting 13 Radiator bottom hose
expert22 fl/ia http://rutracker.org
Page 48 of 225
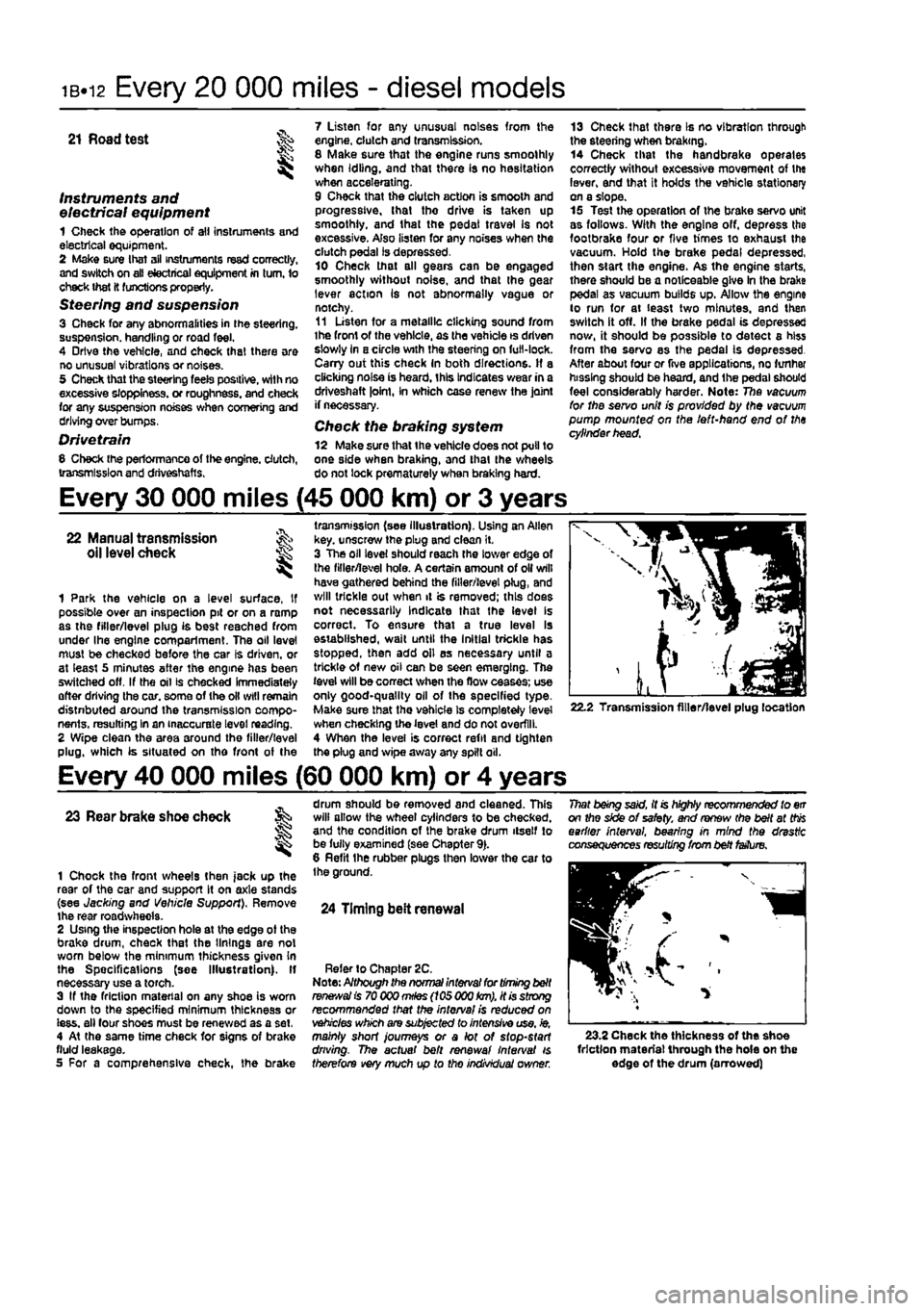
1B«12 Every 20 000 miles - diesel models
21 Road test
Instruments and electrical equipment 1 Check the operation of atl instruments and electrical equipment. 2 Make sure that all instruments read correctly, and switch on all electrical equipment rn turn, to check that It functions properly. Steering and suspension 3 Check for any abnormalities in the steering, suspension, handling or road feel. 4 Drive the vehicle, and check that there are no unusual vibrations or noises. 5 Check that the steering feete positive, with no excessive sloppiness, or roughness, and check for any suspension noises when cornering and driving over bumps. Drivetrain 6 Check (he performance of the engine, clutch, transmission and driveshafts.
7 Listen for any unusual noises from the engine, clutch and transmission. 8 Make sure that the engine runs smoothly when Idling, and that there is no hesitation when accelerating. 9 Check that the clutch action is smooth and progressive, that tho drive is taken up smoothly, and that the pedal travel Is not excessive. Also listen for any noises when the clutch pedal is depressed. 10 Check that all gears can be engaged smoothly without noise, and that the gear lever action Is not abnormally vague or notchy. 11 Listen for a metallic clicking sound from ihe front of the vehicle, as the vehicle « driven slowly In a circle with the steering on full-lock. Carry out this check In both directions, if a clicking noise is heard, this Indicates wear in a driveshaft |oinl, in which case renew the joint if necessary.
Check the braking system 12 Make sure that the vehicle does not pull to one side when braking, and that the wheels do not lock prematurely when braking hard.
13 Check that there Is no vibration through the steering when braking. 14 Check that the handbrake operates correctiy without excessive movement of th« lever, end that it holds the vehicle stationery on a slope. 15 Test the operation of the brake servo unit as follows. With the engine off, depress the footbrake four or five times to exhaust the vacuum. Hold the brake pedal depressed, then start the engine. As the engine starts, there should be a noticeable give In the brake pedal as vacuum builds up. Allow the engine to run for at least two minutes, and then switch it off. If the brake pedal is depressed now, it should be possible to detect a hiss from the servo es the pedal is depressed. After about four or five applications, no fimher hissing should be heard, and the pedal should feel considerably harder. Note: The vacuum for the servo unit is provided by the vacuum pump mounted on the left-hand end of t/ie cylinder head.
Every 30 000 miles (45 000 km) or 3 years
22 Manual transmission oil level check ;5§
1 Park the vehicle on a level surface. If possible over an inspection pit or on a ramp as the filler/level plug is best reached from under Ihe engine compartment. The oil level must be checked before the car Is driven, or at least 5 minutes after the engine has been switched off. If the oil is checked Immediately after driving the car. some of the oil will remain distnbuted around the transmission compo-nents, resulting In an inaccurate level reading. 2 Wipe clean the area around the filler/level plug, which is situated on tho front of the
transmission (see illustration). Using an Allen key. unscrew the plug and clean it. 3 The oil level should reach the lower edge of the filler/level hole. A certain amount of oil will have gathered behind the filler/level plug, and will trickle out when it is removed; this does not necessarily Indicate that the level Is correct. To ensure that a true level Is established, wait until the Initial trickle has stopped, then add oil as necessary until a trickle of new oil can be seen emerging. The level will be correct when the flow ceases; use only good-quality oil of the specified type-Make sure that the vehicle Is completely level when checking the level and do not overfill. 4 When the level is correct refit and tighten the plug and wipe away any spilt oil.
22.2 Transmission filler/level plug location
Every 40 000 miles (60 000 km) or 4 years
23 Rear brake shoe check
1 Chock the front wheels then jack up the rear of the car and support It on axle stands (see Jacking and Vehicle Support), Remove the rear roadwhecla. 2 Using the inspection hole at the edge ot the brake drum, check that the linings are not worn below the minimum thickness given In the Spec ifi cat Ions (see Illustration). If necessary use a torch. 3 If the friction material on any shoe is worn down to the specified minimum thickness or iess. all four shoes must be renewed as a set, 4 At the same time check for signs of brake fluid leakage. 5 For a comprehensive check, the brake
drum should be removed and cleaned. This will allow the wheel cylinders to be checked, and the condition of the brake drum itself to be fully examined (see Chapter 9). 8 Refit the rubber plugs then lower the car to the ground.
24 Timing belt renewal
Refer to Chapter 2C. Note: Although the normal interval for timing belt
ranees/a!
is 70 000
mHes
(105 000
km),
it is strong recommended that the interval is reduced on vehicles which are subjected to intensive use, ie, mainly short journeys or a lot of stop-start driving. The actual belt renewal interval is therefore very much up to tho individual owner.
That being said, it is highly recommended to err on the side of safety, and renew (he belt at
this
earlier interval, bearing in mind the drastic consequences resulting from belt fetfure.
23.2 Check the thickness of the shoe friction material through the hole on the edge of the drum (arrowed)
Page 92 of 225
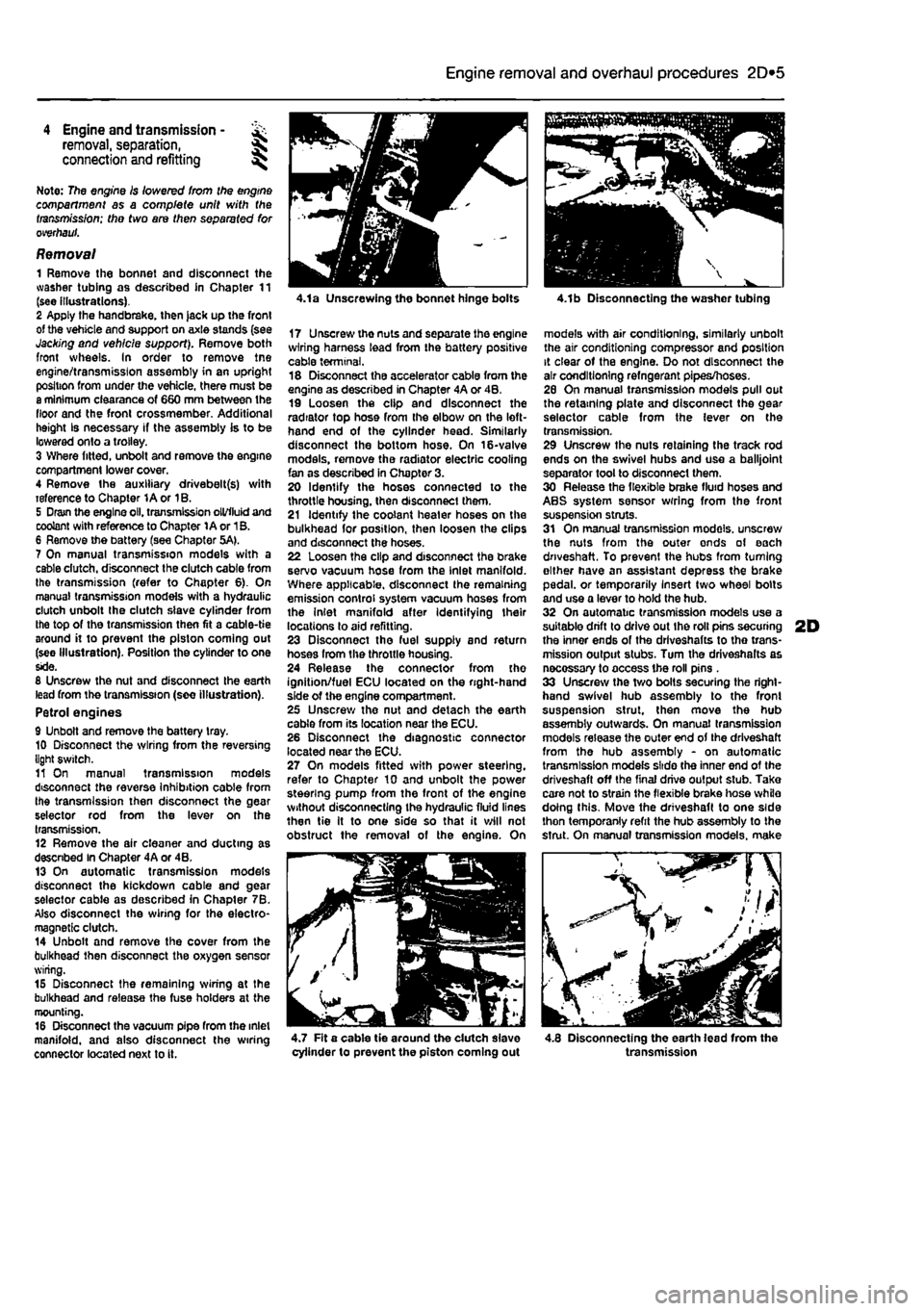
2D*10 Engine removal and overhaul procedures
Engine and transmission -removal, separation, connection and refitting
Note: The engine Is lowered from the engine compartment as a complete unit with the transmission; tho two are then separated for overhaul.
Removal 1 Remove the bonnet and disconnect the washer tubing as described in Chapter 11 (see illustrations). 2 Apply the handbrake, then jack up the front of the vehicle and support on axle stands (see Jacking and vehicle support). Remove both front wheels. In order to remove tne engine/transmission assembly in an upright position from under the vehicle, there must be a minimum clearance of 660 mm between the floor and the front crossmember. Additional height Is necessary if the assembly is to be lowered onto a trolley. 3 Where fitted, unbolt and remove the engine compartment lower cover. 4 Remove the auxiliary drivebelt(s) with reference to Chapter 1A or 1B. 5 Dram the engine oil. transmission oil/fluid and coolant with reference to Chapter 1A or 1B. 6 Remove the battery (see Chapter 5A). 7 On manual transmission models with a cable dutch, disconnect the clutch cable from the transmission (refer to Chapter 6). On manual transmission models with a hydraulic clutch unbolt the clutch slave cylinder from the top of the transmission then fit a cable-tie around it to prevent the piston coming out (see Illustration). Position the cylinder to one side. 8 Unscrew the nut and disconnect the earth lead from the transmission (see illustration). Petrol engines 9 Unbolt and remove the battery tray. 10 Disconnect the wiring from the reversing light switch. 11 On manual transmission models disconnect the reverse Inhibition cable from the transmission then disconnect the gear selector rod from the lever on the transmission. 12 Remove the air cleaner and ducting as descnbed In Chapter 4A or 4B. 13 On automatic transmission models disconnect the kickdown cable and gear selector cable as described in Chapter 7B. Also disconnect the wiring for the electro-magnetic clutch. 14 Unbolt and remove the cover from the bulkhead then disconnect the oxygen sensor wiring. 15 Disconnect the remaining wiring at the bulkhead and release the fuse holders at the mounting. 16 Disconnect the vacuum pipe from the inlet manifold, and also disconnect the wiring connector located next to it.
4.1a Unscrewing the bonnet hinge bolts
17 Unscrewthenutsandseparatetheengine wiring harness lead from the battery positive cable terminal. 18 Disconnect the accelerator cable from the engine as described in Chapter 4A or 4B, 19 Loosen the clip and disconnect the radiator top hose from the elbow on the left-hand end of the cylinder head. Similarly disconnect the bottom hose. On 16-valve models, remove the radiator electric cooling fan as described in Chapter 3. 20 Identify the hoses connected to the throttle housing, then disconnect them. 21 Identify the coolant heater hoses on the bulkhead for position, then loosen the clips and disconnect the hoses. 22 Loosen the clip and disconnect the brake servo vacuum hose from the Inlet manifold. Where applicable, disconnect the remaining emission control system vacuum hoses from the Inlet manifold after Identifying their locations to aid refitting. 23 Disconnect tho fuel supply and return hoses from the throttle housing. 24 Release the connector from the ignition/fuel ECU located on the right-hand side of the engine compartment. 25 Unscrew the nut and detach the earth cable from its location near the ECU. 26 Disconnect the diagnostic connector located near the ECU. 27 On models fitted with power steering, refer to Chapter 10 and unbolt the power steering pump from the front of the engine without disconnecting the hydraulic fluid lines then tie It to one side so that it will not obstruct the removal of the engine. On
4.1b Disconnecting the washer tubing
models with air conditioning, similarly unbolt the air conditioning compressor and position it clear of the engine. Do not disconnect the air conditioning refngerant pipes/hoses. 26 On manual transmission models pull out the retaining plate and disconnect the gear selector cable from the lever on the transmission. 29 Unscrew the nuts retaining the track rod ends on the swivel hubs and use a balljoint separator tool to disconnect them. 30 Release the flexible brake fluid hoses and ABS system sensor wrring from the front suspension struts. 31 On manual transmission models, unscrew the nuts from the outer ends of each driveshaft. To prevent the hubs from turning either have an assistant depress the brake pedal, or temporarily Insert two wheel bolts and use a lever to hold the hub. 32 On automatic transmission models use a suitable drift to drive out Ihe roll pins securing 2D the inner ends of the drlveshafts to tho trans-mission output stubs. Turn the driveshalts as necossary to access the roll pins . 33 Unscrew the two bolts securing the right-hand swivel hub assembly to the front suspension strut, then move the hub assembly outwards. On manual transmission models release the outer end of the driveshaft from the hub assembly - on automatic transmission models slide the inner end of the driveshaft off the final drive output stub. Take care not to strain the flexible brake hose while doing this. Move the driveshaft to one side thon temporanly refit the hub assembly to the strut. On manual transmission models, make
^ - / //
4.7 Fit a cable tie around the dutch slave cylinder to prevent the piston coming out 4.8 Disconnecting the earth lead from the transmission
Page 94 of 225
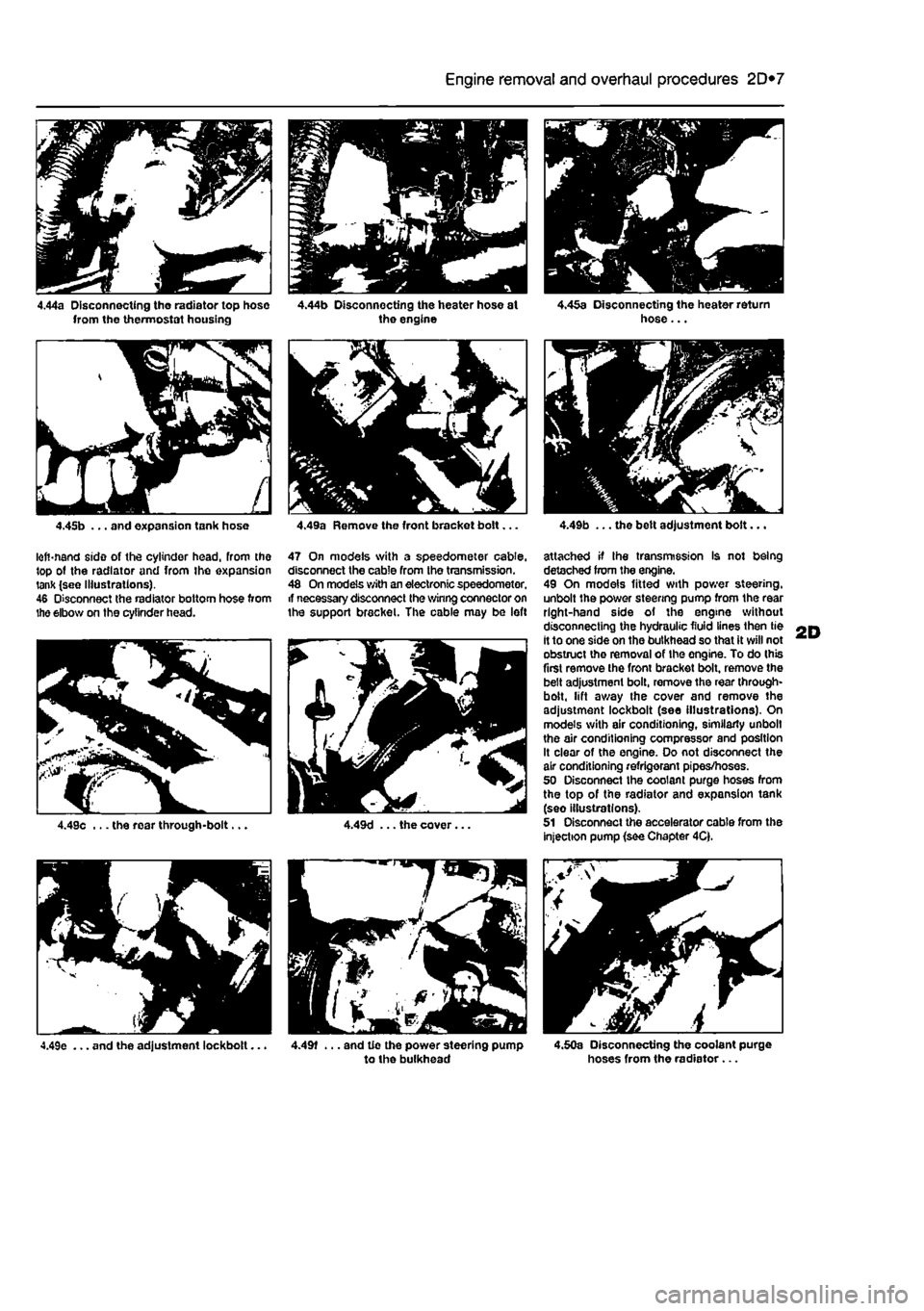
2D*10 Engine removal and overhaul procedures
4.44a Disconnecting tho radiator top hose from the thermostat housing
4.45b ... and expansion tank hose
lofi-nand side of the cylinder head, From the top ot the radiator and from the expansion tank (see Illustrations). 46 Disconnect the radiator bottom hose from the elbow on the cylinder head.
4.49e ... and the adjustment lockbolt...
4.44b Disconnecting the heater hose st the engine
4.49a Remove the front bracket bolt...
47 On models with a speedometer cable, disconnect the cable from the transmission. 48 On models with an electronic speedometer, if necessary disconnect the winng connector on the support bracket. The cable may be left
4.49f ... and tie the power steering pump to the bulkhead
. m " • V;
<4
4.45a Disconnecting the heater return hose...
4.49b ... the belt adjustment bolt...
attached if Ihe transmission Is not being detached from the engine. 49 On models fitted with power steering, unbolt the power steering pump from the rear right-hand side of the engine without disconnecting the hydraulic fluid lines then tie it to one side on the bulkhead so that it will not obstruct the removal of the engine. To do (his first remove the front bracket bolt, remove the belt adjustment bolt, remove the rear through-bolt, lift away the cover and remove the adjustment lockbolt (see illustrations). On models with air conditioning, similarly unbolt the air conditioning compressor and position It clear of the engine. Do not disconnect the air conditioning refrigerant pipes/hoses. 50 Disconnect the coolant purge hoses from the top of the radiator and expansion tank (seo illustrations). 51 Disconnect the accelerator cable from the injection pump (see Chapter 4Q.
4.50a Disconnecting the coolant purge hoses from the radiator...
Page 155 of 225
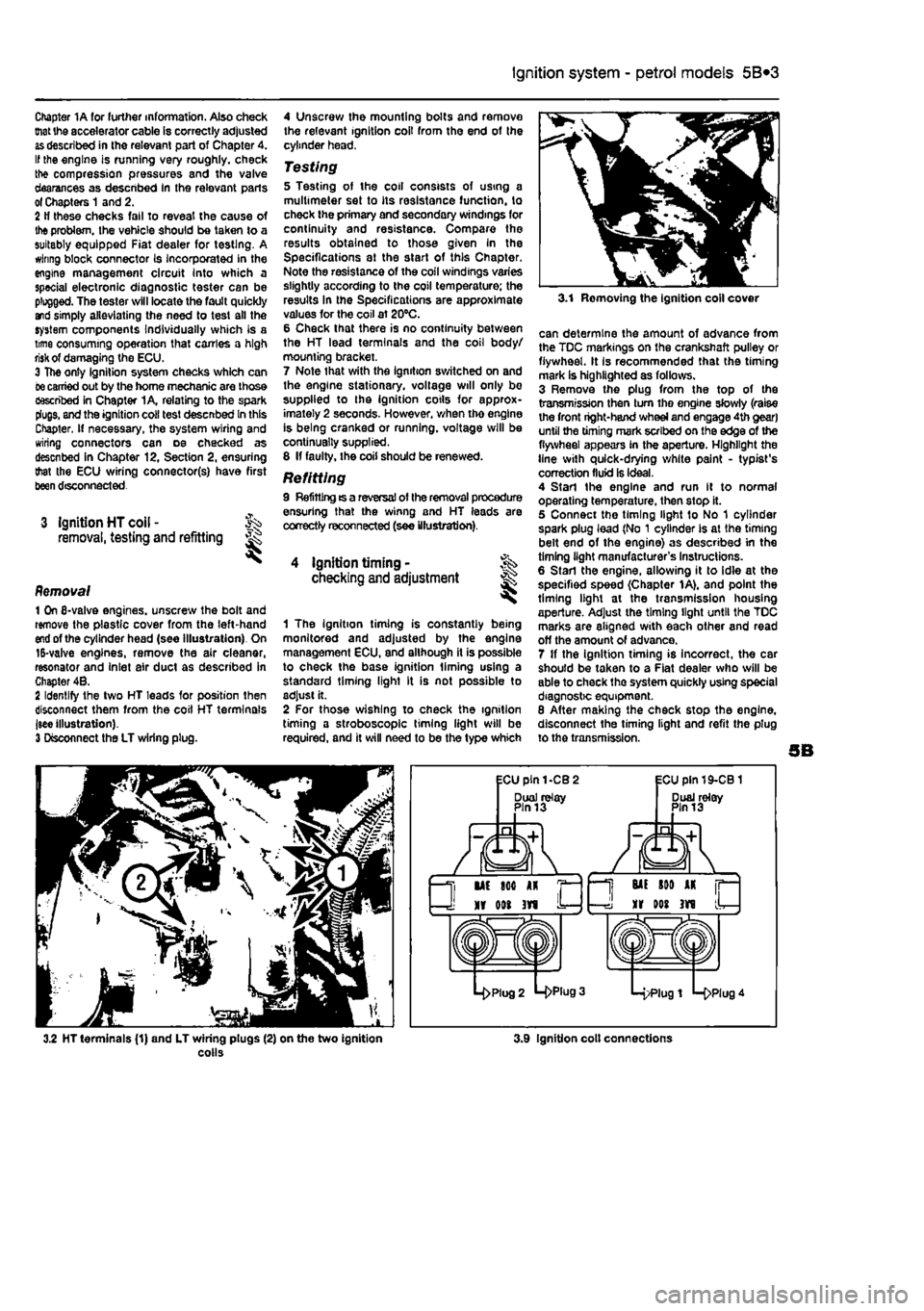
Ignition system - petrol models 5B®3
Chapter 1A tor further information. Also check tnat tha accelerator cable is correctly adjusted
as
described in the relevant part of Chapter 4. If the engine is running very roughly, check the compression pressures and the valve clearances as descnbed In the relevant parts of Chapters 1 and 2. 2
H
these checks fall to reveal the cause of the problem, the vehicle should be taken to a suitably equipped Fiat dealer for testing. A wiring block connector Is Incorporated in the engine management circuit Into which a special electronic diagnostic tester can be plugged. The tester will locate the fault quickly and simply alleviating the need to test all the system components Individually which is a time consuming operation that carries a high risk of damaging the ECU. 3 The only Ignition system checks which can
oe
earned out by the home mechanic are those cescribed in Chapter 1A, relating to the spark plugs, and the ignition coll test descnbed In this Chapter. If necessary, the system wiring and wiring connectors can oe checked as descnbed in Chapter 12, Section 2, ensuring that the ECU wiring connector(s) have first
been
disconnected.
3 Ignition HT coil - ^ removal, testing and refitting
Removal 1 On 6-valve engines, unscrew the boll and remove the plastic cover from the left-hand
end
of the cylinder head (see Illustration). On 15-valve engines, remove the air cleaner, resonator and Inlet air duct as described in Chapter 4B. 2 Identify the two HT leads for position then disconnect them from the coil HT terminals jsee illustration). 3 Disconnect the LT wiring plug.
4 Unscrew the mounting bolts and remove the relevant ignition coil from the end of the cylinder head,
Testing 5 Testing of the coil consists of using a multimeter set to its resistance function, to check the primary and secondary windings for continuity and resistance. Compare the results obtained to those given In the Specifications at the start of this Chapter. Note the resistance of the coil windings varies slightly according to the coil temperature; the results In the Specifications are approximate values for the coil at 20°C. 6 Check that there is no continuity between the HT lead terminals and the coil body/ mourning bracket. 7 Note that with the ignition switched on and the engine stationary, voltage will only be supplied to the ignition cotls for approx-imately 2 seconds. However, when tho engine is being cranked or running, voltage will be continually supplied. 8 If faulty, the coil should be renewed.
Refitting 9 Refitting ts a reversal of the removal procedure ensuring that the winng and HT leads are correctly reconnected (see illustration).
4 ignition timing • checking and adjustment
1 The Ignition timing is constantly being monitored and adjusted by the engine management ECU, and although it is possible to check the base ignition liming using a standard timing light It is not possible to adjust it. 2 For those wishing to check the ignition timing a stroboscope timing light will be required, and it will need to be the type which
3.1 Removing the ignition coll cover
can determine the amount of advance from the TDC markings on the crankshaft pulley or flywheel. It Is recommended that the timing mark is highlighted as follows. 3 Remove the plug from the top of the transmission then turn tho engine slowly (raise the front right-hand wheel and engage 4th gear) until the timing mark scribed on the edge of the flywheel appears in the aperture. Highlight the line with quick-drying white paint - typist's correction fluid is ideal. 4 Start the engine and run It to normal operating temperature, then stop it. 5 Connect the timing light to No 1 cylinder spark plug lead (No 1 cylinder Is at the timing belt end of the engine) as described in the timing light manufacturer's Instructions. 6 Start the engine, allowing it to idle at the specified speed (Chapter 1A), and point the timing light at the transmission housing aperture. Adjust the timing light until the TDC marks are aligned with each other and read off the amount of advance. 7 If the ignition timing is incorrect, the car should be taken to a Fiat dealer who will be able to check the system quickly using special diagnostic equipment. 8 After making the check stop the engine, disconnect the timing light and refit the plug to the transmission.
3.2 HT terminals (1) and LT wiring plugs (2) on the two ignition colls 3.9 Ignition colt connections
Page 158 of 225
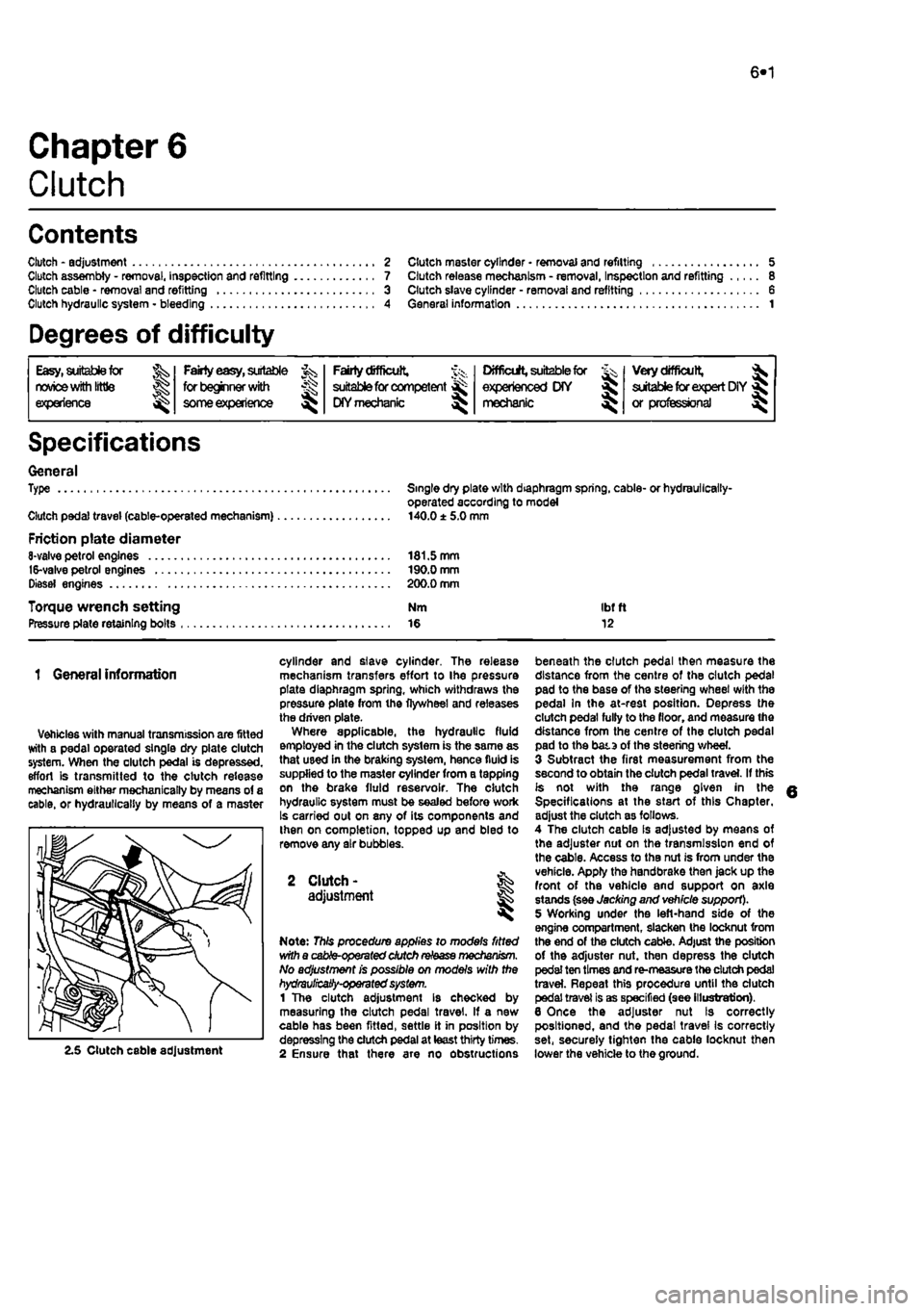
6*1
Chapter 6
Clutch
Contents
Clutch - adjustment Clutch assembly - removal, inspection and refitting Clutch cable • removal and refitting Clutch hydraulic system - bleeding
Degrees of difficulty
2 Clutch master cylinder • removal and refitting 5 7 Clutch release mechanism - removal, Inspection and refitting 8 3 Clutch slave cylinder - removal and refitting 6 4 General information 1
Easy, suitable for
novice with little experience oi^
Faidy easy,
suitable for beginner
with
^
some
experience
Fairly difficult, suitable
for
competent ^
DIY
mechanic ^
Difficiit, suitable for ^ experienced DIY JR mechanic ^
V<*y difficult,
jk
suitable
for expert
DIY
« or professional ^
Specifications
General Type
Clutch pedal travel (cable-operated mechanism)
Friction plate diameter 8-valve petrol engines 16-valve petrol engines Diesel engines
Torque wrench setting Pressure plate retaining bolts
Single dry plate with diaphragm spring, cable- or hydraullcally-operated according to model 140.0 ± 5.0 mm
181.5 mm 190.0 mm 200.0 mm
Nm Ibf ft 16 12
1 General information
Vehicles with manual transmission are fitted with a pedal operated single dry plate clutch system. When the clutch pedal is depressed, effort is transmitted to the clutch release mechanism either mechanically by means of a cable, or hydraullcally by means of a master
2.5 Clutch cable adjustment
cylinder and slave cylinder. The release mechanism transfers effort to Ihe pressure plate diaphragm spring, which withdraws the pressure plate from the flywheel and releases the driven plate-Where applicable, the hydraulic fluid employed in the clutch system is the same as that used in the braking system, hence fluid is supplied to the master cylinder from a tapping on the brake fluid reservoir. The clutch hydraulic system must be sealed before work Is carried out on any of its components and then on completion, topped up and bled to remove any air bubbles.
2 Clutch - % adjustment §§ ^
Note: This procedure applies to models fitted with a cable-operated dutch
release
mechanism. No adjustment is possible on models with the hydrauHcaSy-operated system. 1 The clutch adjustment Is checked by measuring the clutch pedal travel. If a new cable has been fitted, settle it in position by depressing the clutch pedal at least thirty times. 2 Ensure that there are no obstructions
beneath the clutch pedal then measure the distance from the centre of the clutch pedal pad to the base of the steering wheel with the pedal In the at-rest position. Depress the clutch pedal fully to the floor, and measure the distance from the centre of the clutch pedal pad to the bata of the steering wheel. 3 Subtract the first measurement from the second to obtain the clutch pedal travel. If this is not with the range given in the Specifications at the start of this Chapter, adjust the clutch as follows. 4 The clutch cable Is adjusted by means of the adjuster nut on the transmission end of the cable. Access to the nut is from under the vehicle. Apply the handbrake then jack up the front of the vehicle and support on axle stands (see Jacking and vehicle support). 5 Working under the left-hand side of the engine compartment, slacken the locknut from the end of the clutch cable. Adjust the position of the adjuster nut. then depress the clutch pedal ten times and re-measure the dutch pedal travel. Repeat this procedure until the clutch pedal travel is as specified (see illustration). 6 Once the adjuster nut Is correctly positioned, and the pedal travel Is correctly set, securely tighten the cable locknut then lower the vehicle to the ground.