belt FIAT PUNTO 1999 176 / 1.G Repair Manual
[x] Cancel search | Manufacturer: FIAT, Model Year: 1999, Model line: PUNTO, Model: FIAT PUNTO 1999 176 / 1.GPages: 225, PDF Size: 18.54 MB
Page 106 of 225
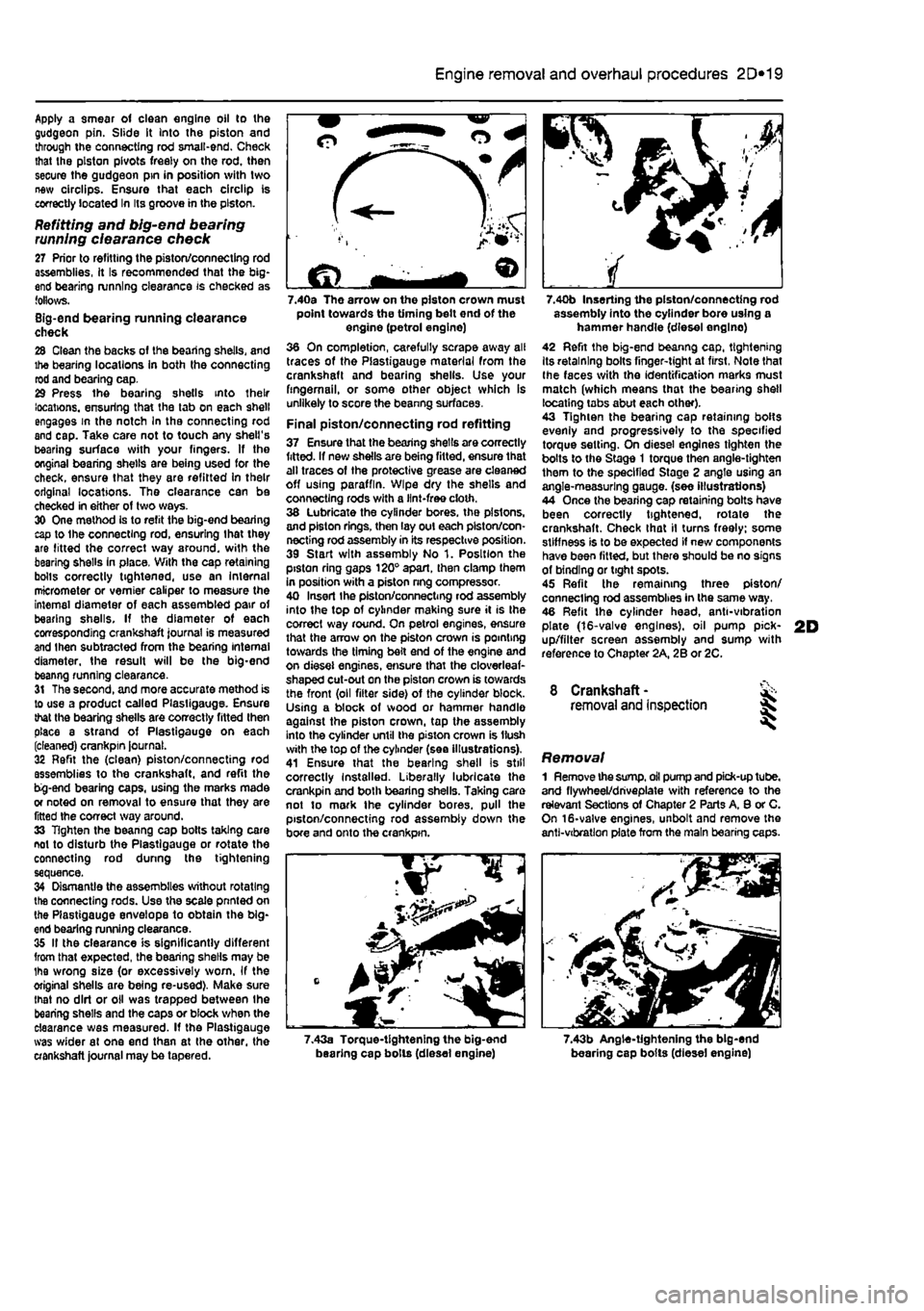
Apply a smear of clean engine oil to the gudgeon pin. Slide it Into the piston and through the connecting rod small-end. Check that the piston pivots freely on the rod. then secure the gudgeon pin in position with two new circlips. Ensure that each circlip is correctly located In Its groove in the piston.
Refitting and big-end bearing running ciearance check 27 Prior to refitting the piston/connecting rod assemblies, it Is recommended that the big-end bearing running clearance is checked as follows. Big-end bearing running clearance check 28 Clean the backs of the bearing shells, and the bearing locations in both the connecting rod and bearing cap. 29 Press the bearing shells into their locations, ensuring that the tab on each shell engages in the notch In the connecting rod and cap. Take care not to touch any shell's bearing surface with your fingers. If the onginal bearing shells are being used for the check, ensure that they are refitted in their original locations. The clearance can be checked in either of two ways. 30 One method is to refit the big-end bearing cap to Ihe connecting rod, ensuring that they are litted the correct way around, with the bearing shells in place. Wilh the cap retaining bolls correctly tightened, use an internal micrometer or vernier caliper to measure the internal diameter of each assembled pair of bearing shells. If the diameter of each corresponding crankshaft journal is measured and Ihen subtracted from the bearing internal diameter, the result will be the big-end beanng running clearance. 31 The second, and more accurate method is to use a product called Plasligauge. Ensure that the bearing shells are correctly fitted then place a strand of Plastlgauge on each (cleaned) crankpin journal. 32 Refit the (clean) piston/connecting rod assemblies to the crankshaft, and refit the bg-end bearing caps, using the marks made or noted on removal to ensure that they are fitted the correct way around. 33 Tighten the beanng cap bolts taking care not to disturb the Plastlgauge or rotate the connecting rod dunng the tightening sequence. 34 Dismantle the assemblies without rotating the connecting rods. Use the scale pnnted on the Plastigauge envelope to obtain the big-end bearing running clearance. 35 If the clearance is significantly different from that expected, the bearing shells may be Ihe wrong size (or excessively worn. If the original shells are being re-used). Make sure mat no dirt or oil was trapped between Ihe bearing shells and the caps or block when the clearance was measured. If the Plastigauge was wider al one end than at the other, the crankshaft journal may be tapered.
2D*10 Engine removal and overhaul procedures
7.40a The arrow on the piston crown must point towards the timing belt end of the engine (petrol engine) 36 On completion, carefully scrape away all traces of the Plastigauge material from the crankshaft and bearing shells. Use your fingernail, or some other object which is unlikely to score the beanng surfaces.
Final piston/connecting rod refitting 37 Ensure that the bearing shells are correctly fitted. If new shells are being fitted, ensure that alt traces of the protective grease are cleaned off using paraffin. Wipe dry the shells and connecting rods with a lint-free cloth. 38 Lubricate the cylinder bores, the pistons, and piston rings, then lay out each piston/con-necting rod assembly in its respective position. 39 Start with assembly No 1. Position the piston ring gaps 120° apart, then clamp them in position with a piston nng compressor. 40 Insert Ihe piston/connecting rod assembly into the top of cylinder making sure it is Ihe correct way round. On petrol engines, ensure that the arrow on the piston crown is pointing towards the timing belt end of the engine and on diesel engines, ensure that the cloverleaf-shaped cut-out on the piston crown is towards the front (oil filter side) of the cylinder block. Using a block of wood or hammer handle against the piston crown, tap the assembly into the cylinder until the piston crown is Hush with the top of the cylinder (sea illustrations). 41 Ensure that the bearing shell is still correctly Installed. Liberally lubricate the crankpin and both bearing shells. Taking care not to mark the cylinder bores, pull the piston/connecting rod assembly down the bore and onto the crankpin.
7.40b Inserting the piston/connecting rod assembly into the cylinder bore using a hammer handle (diesel englno) 42 Refit the big-end beanng cap, tightening Its retaining bolts finger-tight at first, Note that Ihe faces with the identification marks must match (which means that the bearing shell locating tabs abut each other). 43 Tighten the bearing cap retaining bolts evenly and progressively to the specified torque setting. On diesel engines tighten the bolts to the Stage 1 torque then angle-tighten them to the specified Stage 2 angle using an angle-measuring gauge, (see illustrations) 44 Once the bearing cap retaining bolts have been correctly tightened, rotate the crankshaft. Check that il turns freely; some stiffness is to be expected if new components have been fitted, but there should be no signs of binding or tight spots. 45 Refit the remaining three piston/ connecting rod assemblies in the same way. 46 Refit the cylinder head, anti-vibration plate (16-valve engines), oil pump pick-up/filter screen assembly and sump with reference to Chapter 2A, 2B or 2C.
8 Crankshaft -removal and inspection 35
Removal 1 Remove the
sump,
oil pump and pick-up tube, and flywheel/driveplate with reference to the relevant Sections of Chapter 2 Parts A, 8 or C. On 16-valve engines, unbolt and remove the anti-vibration plate from the main bearing caps.
7.43a Torque-tightening the big-end bearing cap bolls (diesel engine) 7.43b Angle-tightening the big-end bearing cap bolts (diesel engine)
Page 107 of 225
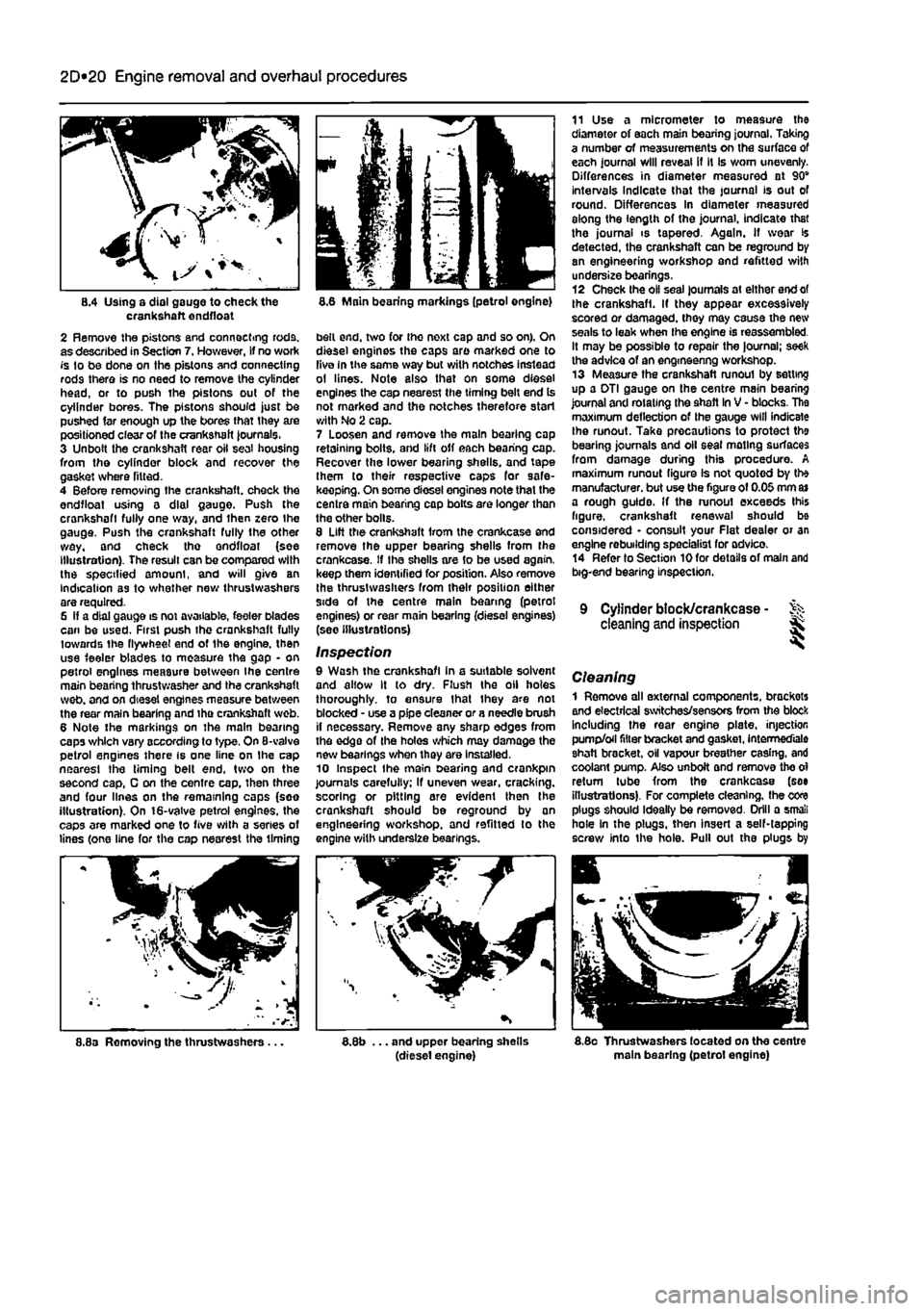
2D*10 Engine removal and overhaul procedures
8.4 Using a dial gauge to check the crankshaft endfloat 2 Remove the pistons and connecting rods, as described in Section 7. However, If no work fs to be done on the pistons and connecting rods there is no need to remove the cylinder head, or to push the pistons out of the cylinder bores. The pistons should just be pushed far enough up the bores that they are positioned clear of the crankshaft Journals. 3 Unbolt the crankshaft rear oil seal housing from the cylinder block and recover the gasket where fitted. 4 Before removing the crankshaft, check the endfloat using a dial gauge. Push the crankshaft fully one way, and then zero Ihe gauge. Push the crankshaft fully the other way, and check tho endfloat (see Illustration). The result can be compared with the specified amount, and will give an indication as to whether new thrustwashers are required. 6 If a dial gauge is not available, feeler blades can be used. First push the crankshaft fully towards the flywheel end of the engine, then use feeler blades to measure the gap - on petrol engines measure between the centre main bearing thrust washer and the crankshaft web. and on diesel engines measure between the rear main bearing and tha crankshaft web. 6 Note the markings on the main bearing caps which vary according to type. On 8-valve petrol engines there is one line on Ihe cap nearest the timing belt end, two on the second cap, C on the centre cap, then three and four lines on the remaining caps (soo illustration). On 16-valve petrol engines, the caps are marked one to five with a series of lines (one line for the cap nearest the timing
8.6 Main bearing markings (petrol engine)
belt end, two for tho next cap and so on). On diesel engines the caps are marked one to live In the same way but with notches instead ol lines. Note also that on some diesel engines the cap nearest the timing belt end Is not marked and the notches therefore start with No 2 cap. 7 Loosen and remove the main bearing cop retaining bolts, and lift off each bearing cap. Recover the lower bearing shells, and tape them to their respective caps for safe-keeping. On some diesel engines note that the centre main bearing cap botts are longer than the other bolls. 8 Lift the crankshaft Irom the crankcase and remove the upper bearing shells from the crankcase. If the shells are 1o be used again, keep them identified for position. Also remove the thrustwashers from their position either side of the centre main bearing (petrol engines) or rear main bearing (diesel engines) (see illustrations)
Inspection 9 Wash the crankshaft in a suitable solvent and allow It to dry. Flush the oil holes thoroughly, to ensure that ihey are not blocked - use a pipe cleaner or a needle brush il necessary. Remove any sharp edges from the edge of the holes which may damage the new bearings when they are installed. 10 Inspect the main searing and crankpin journals carefully; if uneven wear, cracking, scoring or pitting are evident then the crankshaft should be reground by an engineering workshop, and refitted to the engine with underslze bearings.
11 Use a micrometer to measure the diameter of each main bearing journal. Taking a number of measurements on the surface of each journal will reveal if it Is worn unevenly. Differences in diameter measured at 90" intervals Indicate that the journal is out of round. Differences In diameter measured aiong the length of the journal, indicate that the journal is tapered. Again. If wear is detected, the crankshaft can be reground by an engineering workshop and refitted with undersize bearings. 12 Check the oil seal journals at either end of the crankshaft. If they appear excessively scored or damaged, they may cause the new seals to leak when the engine is reassembled. It may be possible to repair the |ournal; seek the advice of an engmeenng workshop. 13 Measure the crankshaft runoul by setting up a DTI gauge on the centre main bearing journal and rotating the shaft In V - blocks. The maximum deflection of the gauge will indicate Ihe runout. Take precautions to protect the bearing journals and oil seal mating surfaces from damage during this procedure. A maximum runout figure Is not quoted by the manufacturer, but use the figure of 0.05 mm
a»
a rough guido. If the runoul exceeds this figure, crankshaft renewal should be considered • consult your Flat dealer or an engine rebuilding specialist for advico. 14 Refer to Section 10 for details of main and big-end bearing inspection.
9 Cylinder block/crankcase - % cleaning and inspection Sk
Cleaning 1 Remove all external components, brackets and electrical switches/sensors from the block Including the rear engine plate, injection pump/oil filter bracket and gasket, Intermediate shaft bracket, oH vapour breather casing, and coolant pump. Also unboit and remove the ol return tube from the crankcase (see illustrations). For complete cleaning, the core plugs should Ideally be removed. Drill a small hole in the plugs, then insert a self-tapping screw into the hole. Pull out the plugs by
8.8a Removing the thrustwashers.. ... and upper bearing shells (diesel engine) 8.8o Thrustwashers located on the centre main bearing (petrol engine)
Page 109 of 225
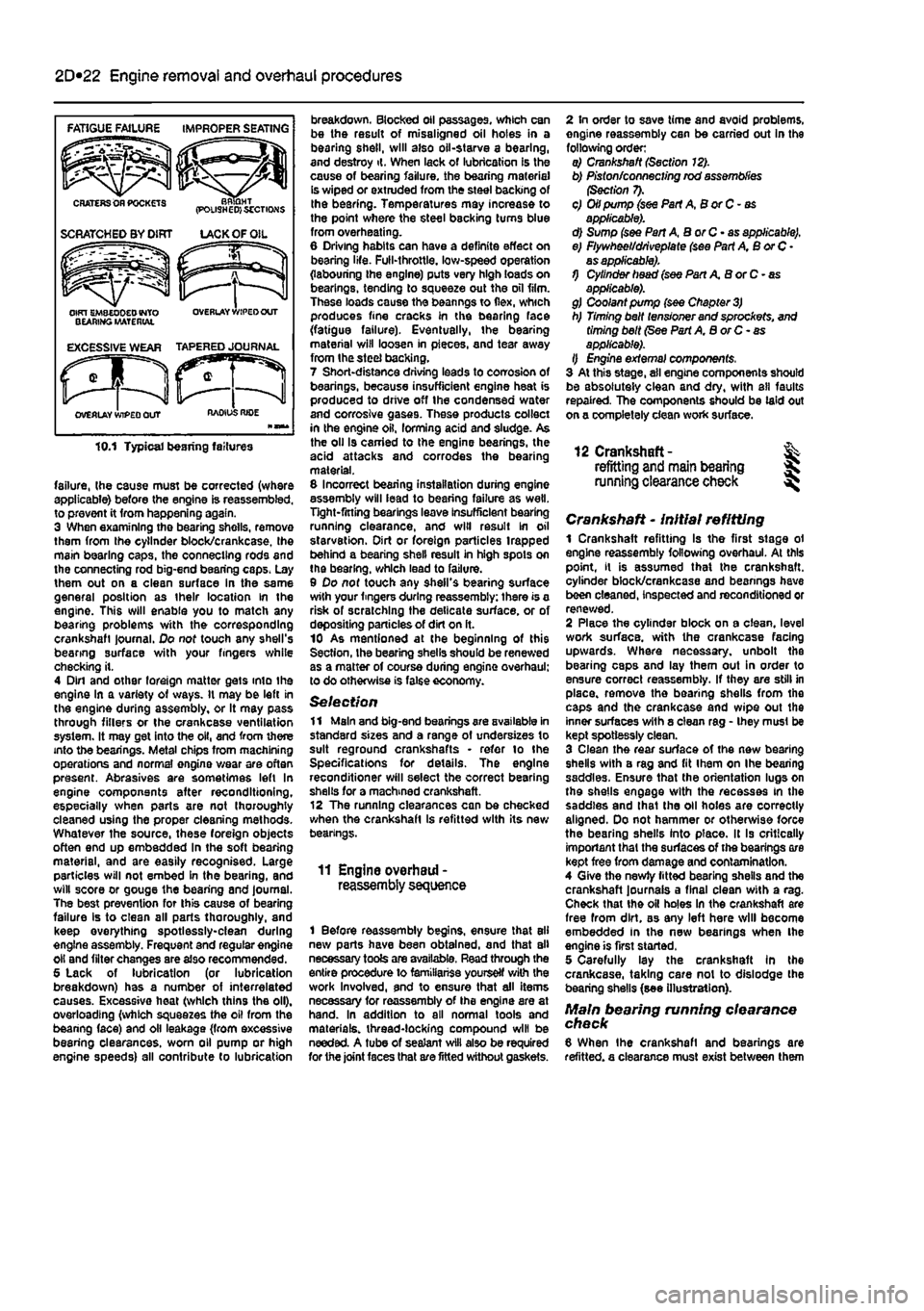
2D*10 Engine removal and overhaul procedures
failure, (he cause must be corrected (where applicable) before the engine is reassembled, to prevent it from happening again. 3 When examining the bearing shells, remove them from the cylinder block/crankcase, Ihe main bearing caps, the connecting rods and the connecting rod big-end bearing caps. Lay them out on a clean surface in the same general position as their location in the engine. This will enable you to match any bearing problems with the corresponding crankshaft journal. Do not touch any shell's bearing surface with your fingers while checking it. 4 Din and other foreign matter gets into the engine in a variety of ways. It may be left in the engine during assembly, or It may pass through fillers or the crankcase ventilation system. It may get into the oil, and from there into the bearings. Metal chips from machining operations and normal engine wear are often present. Abrasives are sometimes left In engine components after reconditioning, especially when parts are not thoroughly cleaned using the proper cleaning methods. Whatever the source, these foreign objects often end up embedded In the soft bearing material, and are easily recognised. Large particles will not embed in the bearing, and will score or gouge the bearing and journal. The best prevention for this cause of bearing failure Is to clean all parts thoroughly, and keep everything spotlessly-clean during engine assembly. Frequent and regular engine oil and filter changes are also recommended. 5 Lack of lubrication (or lubrication breakdown) has a number of interrelated causes. Excessive heat (which thins the oil), overloading (which squeezes the oil from the bearing face) and oil leakage (from excessive bearing clearances, worn oil pump or high engine speeds) all contribute to lubrication
breakdown. Blocked oil passages, which can be the result of misaligned oil holes in a bearing shell, will also oil-starve a bearing, and destroy it. When lack of lubrication is the cause of bearing failure, the bearing materiel is wiped or extruded from the steel backing of Ihe bearing. Temperatures may increase to the point where the steel backing turns blue from overheating. 6 Driving habits can have a definite effect on bearing life. Full-throttle, low-speed operation (labouring ihe engine) puts very high loads on bearings, tending to squeeze out the oil film. These loads cause the beanngs to flex, which produces fine cracks in the bearing face (fatigue failure). Eventually, the bearing material will loosen in pieces, and tear away from Ihe steel backing. 7 Short-distance driving leads to corrosion of bearings, because insufficient engine heat is produced to drive off the condensed water and corrosive gases. These products collect in the engine oil, forming acid and sludge. As the oil Is carried to the engine bearings, the acid attacks and corrodes the bearing material. 8 Incorrect bearing installation during engine assembly will lead to bearing failure as well. Tight-fitting bearings leave insufficient bearing running clearance, and will result in oil starvation. Dirt or foreign particles trapped behind a bearing shell result in high spots on the bearing, which lead to failure. 9 Do not touch any shell's bearing surface with your fingers during reassembly: there is a risk of scratching the delicate surface, or of depositing particles of dirt on ft. 10 As mentioned at the beginning of this Section, the bearing shells should be renewed as a matter of course during engine overhaul; to do otherwise is false economy.
Selection 11 Main and big-end bearings are available in standard sizes and a range of undersizes to suit reground crankshafts • refer to the Specifications for details. The engine reconditioner will select the correct bearing shells for a machined crankshaft. 12 The running clearances can be checked when the crankshaft is refitted with its new bearings.
11 Engine overhaul -reassembly sequence
1 Before reassembly begins, ensure that all new parts have been obtained, and that all necessary tools are available. Read through the entire procedure to familiariss yourself with the work Involved, and to ensure that ail items necessary for reassembly of the engine are at hand. In addition to all normal tools and materials, thread-locking compound will be needed. A tube of sealant will also be required for the joint faces that are fitted without gaskets.
2 In order to save time and avoid problems, engine reassembly can be carried out in the following order: a) Crankshaft (Section 12). b) Piston/connecting rod assemblies (Section 7). c) Oil pump (see Part A, B or C - as applicable). d) Sump (see Pan A, BorC-as applicable). e) Flywheel/driveplate (see Part A, B or C • as applicable). 1) Cylinder head (see Part A B or C - as applicable). g) Coolant pump (see Chapter
3)
h) Timing belt tensioner and sprockets, and timing belt (See Part A, B or C- as applicable). I) Engine external components, 3 At this stage, ail engine components should be absolutely clean and dry, with all faults repaired. The components should be laid out on a completely clean work surface.
12 Crankshaft- % refitting and main bearing S running clearance check ^
Crankshaft - initial refitting 1 Crankshaft refitting Is the first stage ol engine reassembly following overhaul. At this point, it is assumed that the crankshaft, cylinder block/crankcase and beanngs have been cleaned, inspected and reconditioned or renewed. 2 Place the cylinder block on a clean, level work surface, with the crankcase facing upwards. Where necessary, unbolt the bearing caps and lay them out in order to ensure correct reassembly. If they are still in place, remove the bearing shells from the caps and the crankcase and wipe out the inner surfaces wilh a clean rag - they musl be kept spotlessly clean. 3 Clean the rear surface of the new bearing shells with a rag and fit ihem on Ihe bearing saddles. Ensure that the orientation lugs on the shells engage with the recesses in the saddles and lhat the oil holes are correctly aligned. Do not hammer or otherwise force the bearing shells into place. It Is critically important that the surfaces of the bearings ore kept free from damage and contamination. 4 Give the newly fitted bearing shells and the crankshaft journals a final clean with a rag. Check that the oil holes In the crankshaft are free from dirt, as any left here will become embedded In the new bearings when Ihe engine is first started. 5 Carefully lay the crankshaft In the crankcase, taking care not to dislodge the bearing shells (see illustration}.
Main bearing running clearance check 8 When Ihe crankshaft and bearings are refitted, a clearance must exist between them
Page 114 of 225
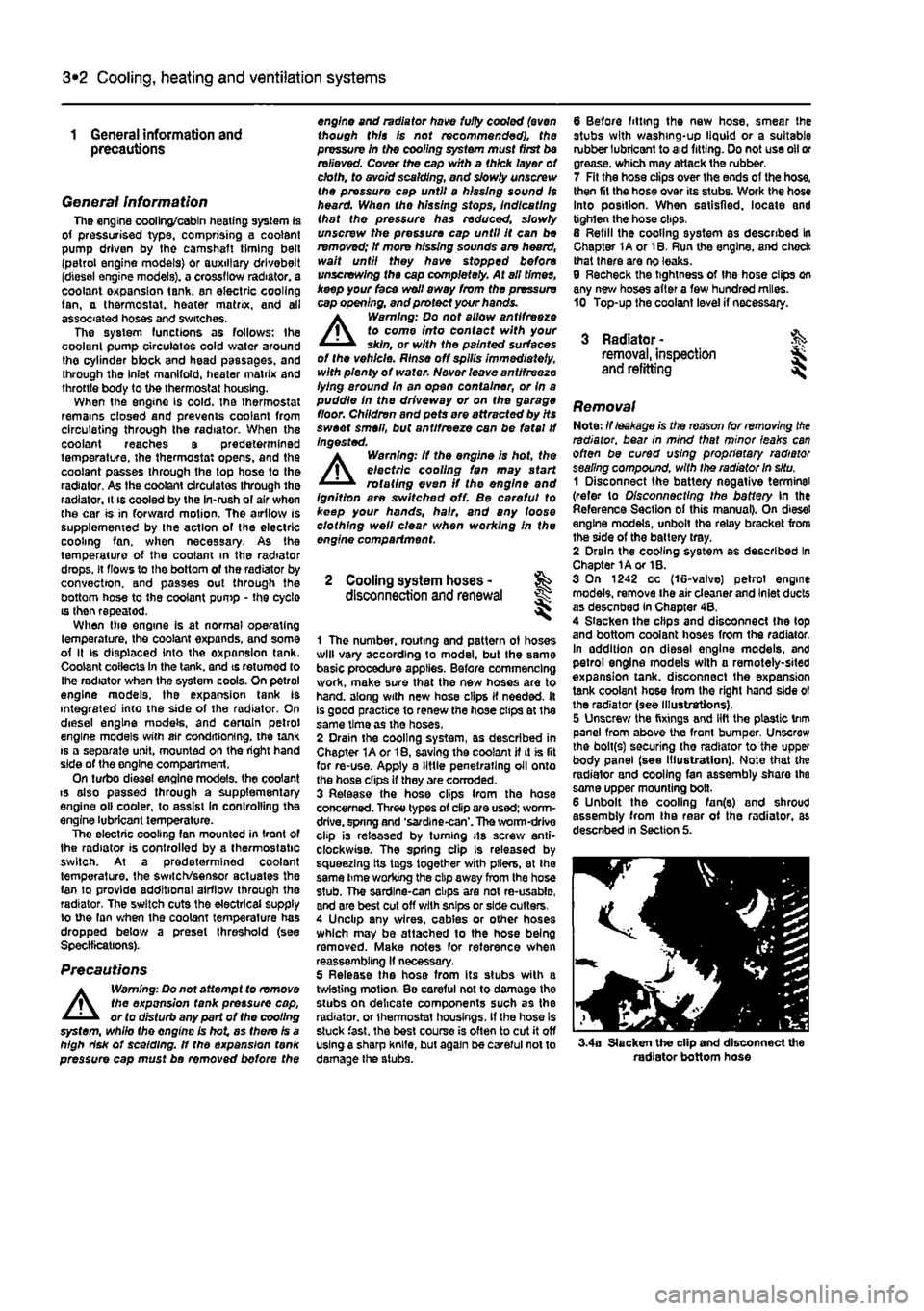
3*2 Cooling, heating and ventilation systems
1 General information and precautions
Genera/ Information The engine cooling/cabin heating system is ol pressurised type, comprising a coolant pump driven by the camshaft timing belt (petrol engine models) or auxiliary drlvebelt (diesel engine models), a crossllow radiator, a coolant expansion tank, an electric cooling fan, a thermostat, heater matrix, and all associated hoses and switches. The system functions as follows: Ihe coolant pump circulates cold water around the cylinder block and head passages, and through the Inlet manifold, heater matrix and throttle body to the thermostat housing. When the engine Is cold, the thermostat remains closed and prevents coolant from circulating through the radiator. When the coolant reaches a predetermined temperature, the thermostat opens, and the coolant passes through the top hose to the radiator. As the coolant circulates through the radiator, it is cooled by the in-rush of air when the car is in forward motion. The airllow is supplemented by the action of the electric cooling fan. when necessary, As the temperature of the coolant in the radiator drops, it flows to the bottom of the radiator by convection, and passes out through the bottom hose to the coolant pump - the cycle is then repeatod, When the engine is at normal operating temperature, the coolant expands, and some of It is displaced into the expansion tank. Coolant collects In the tank, and ts returned to Ihe radiator when the system cools. On petrol engine models, the expansion tank is integrated into the side of the radiator. On diesel engine models, and certain petrol engine models with air conditioning, the tank is a separate unit, mounted on the right hand side of the engine compartment. On turbo diesel engine models, the coolant is also passed through a supplementary engine oil cooler, to assist In controlling the engine lubricant temperature. Tho electric cooling fan mounted in front of the radiator is controlled by a thermostatic switch. At a predetermined coolant temperature, the swilch/sensor actuates the tan lo provide additional airflow through the radiator, The switch cuts the electrical supply to the Ion when the coolant temperature has dropped below a preset threshold (see Specifications).
Precautions
A
Warning: Do not attempt to remove the expansion tank pressure cap, or to disturb any part of the cooling system, whlio the engine is hot, as then is a high risk of scalding, tf the expansion tank pressure cap must be removed before the
engine and radiator have fulty cooled (even though this is not recommended?, the pressure in the cooling system must first be relieved. Cover the cap with a thick layer of cloth, to avoid scalding, and slowly unscrew the pressuro cap until a hissing sound Is heard. When the hissing stops, indicating that the pressure has reduced, slowly unscrew the pressure cap until it can be removed; If more hissing sounds are heard, wait until they have stopped before unscrewing the cap completely. At all times, keep your face well away from the pressure cap opening, and protect your hands.
A
Warning: Do not allow antifreeze to come into contact with your skin, or with the painted surfaces of the vehicle. Rinse off spills immediately, with plenty of water. Never leave antifreeze lying around in an open container, or In a puddle In the driveway or on the garage floor. Children and pets are attracted by its sweet smell, but antifreeze can be fatal tf ingested.
A
Warning: If the engine is hot, the electric cooling fan may start rotating even if the engine and ignition are switched off. Be careful to keep your hands, hair, and any loose clothing well clear when working In the engine compartment.
2 Cooling system hoses - f&> disconnection and renewal ^
1 The number, routing and pattern of hoses will vary according to model, but the same basic procedure applies. Before commencing work, make sure that the new hoses are to hand, along wilh new hose clips if needed, it is good practice to renew the hose clips at the same time as the hoses. 2 Drain the cooling system, as described in Chapter 1A or 18, saving the coolant if it is fit for re-use. Apply a little penetrating oil onto the hose clips if they are corroded. 3 Release the hose clips from the hose concerned. Three types of clip are used; worm-drive. spring and 'sardine-can'. The worm-drive clip is released by turning its screw anti-clockwise. The spring clip Is released by squeezing Its tags together with pliers, at the same time working the cbp away from the hose stub. The sardine-can clips are not re-usable, and are best cut off with snips or side cutters. 4 Unclip any wires, cables or other hoses which may be attached to the hose being removed. Make notes for reference when reassembling If necessary. 5 Release the hose from its stubs with a twisting motion. Be careful not to damage the stubs on deltcate components such as the radiator, or thermostat housings. If the hose Is stuck fast, the best course is often to cut it off using a sharp knife, but again be careful not to damage the stubs.
6 Before fitting the new hose, smear the stubs with washing-up liquid or a suitable rubber lubricant to aid fitting. Do not use oil or grease, which may attack the rubber. 7 Fit the hose clips over the ends of the hose, then fit the hose over its stubs. Work the hose Into position. When satisfied, locate and tighten the hose dips. 6 Refill the cooling system as described In Chapter 1A or 1B. Run the engine, and chock that there are no leaks. 9 Recheck the tightness of Ihe hose clips on any new hoses after a few hundred miles. 10 Top-up the coolant level if necessary.
3 Radiator -
removal,
inspection and refitting
Removal Note: If leakage is the reason for removing
the
radiator, bear In mind that minor leaks can often be cured using proprietary radiator sealing compound, with the radiator in situ. 1 Disconnect the battery negative terminal (refer to Disconnecting the battery In the Reference Section of this manual). On diesel engine models, unbolt the relay bracket from the side of the battery tray. 2 Drain the cooling system as described In Chapter 1A or 1B. 3 On 1242 cc (16-valve) petrol engine models, remove the air cleaner and Inlet ducts as desenbed In Chapter 4B, 4 Slacken the clips and disconnect Ihe (op and bottom coolant hoses from the radiator. In addition on diesel engine models, and petrol engine models with a remotely-sited expansion tank, disconnect the expansion tank coolant hose from the right hand side ol the radiator (see Illustrations), 5 Unscrew the fixings and lift the plastic trim panel from above the front bumper Unscrew the bolt(s) securing tho radiator to the upper body panel (see Illustration). Note that the radiator and cooling fan assembly share the same upper mounting bolt. 6 Unbolt the cooling fan(e) and shroud assembly from Ihe rear ot the radiator, as described in Section 5.
3.4a Slacken the clip and disconnect the radiator bottom hose
Page 117 of 225
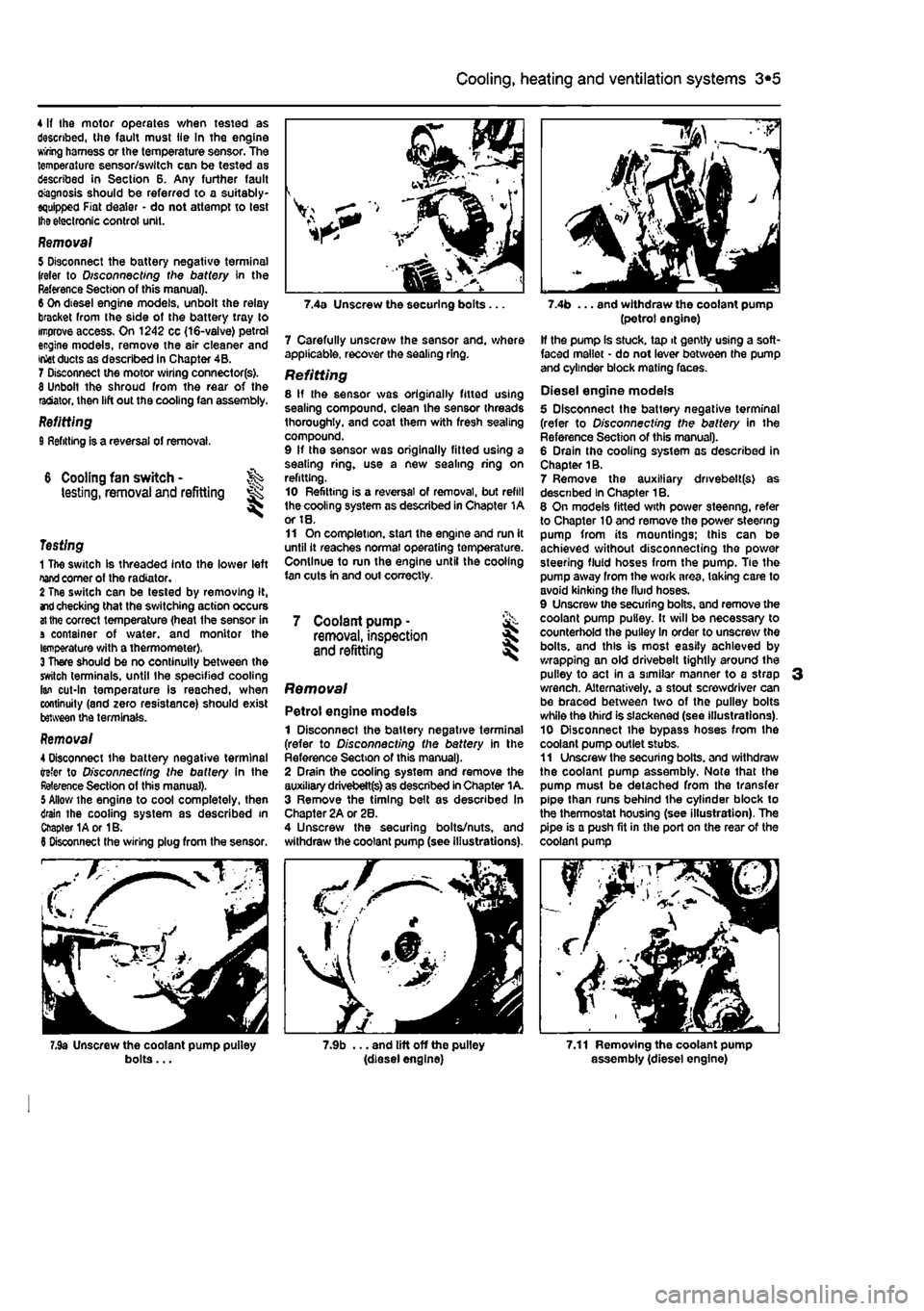
3*2 Cooling, heating and ventilation systems
4 If the motor operates when tested as described, (he fault must lie In the engine wring harness or the temperature sensor. The temperature sensor/switch can be tested as described in Section 6. Any further fault Diagnosis should be referred to a suitably-equipped Fiat dealer - do not attempt to test
Ihe
electronic control unit.
Removal 5 Disconnect the battery negative terminal (refer to D/scon oecf/ng the battery in the Reference Section of this manual). 6 On diesel engine models, unbolt the relay bracket from the side of the battery tray to improve access. On 1242 cc {16-valve) petrol engine models, remove the air cleaner and
inset
ducts as described in Chapter 4B. 1 Disconnect the motor wiring connectorfs). 8 Unbolt the shroud from the rear of the ratiator. then lift out the cooling fan assembly. Refitting 9 Refitting is a reversal of removal
6 Cooling fan switch -testing, removal and refitting ^
Testing 1 The switch is threaded into the lower left
nand
comer of the radiator. 2 The switch can be tested by removing it,
and
checking that the switching action occurs
at
the correct temperature {heat the sensor in a container of water, and monitor the temperature with a thermometer). 3 There should be no continuity between the switch terminals, until Ihe specified cooling fan cut-In temperature Is reached, when continuity (and zero resistance) should exist between the terminals.
Removal 4 Disconnect the battery negative terminal refer to Disconnecting the battery in the Reference Section of this manual). 5 Allow the engine to cool completely, then drain the cooling system as described in Chapter 1Aor 1B. 6 Disconnect the wiring plug from the sensor.
bolts...
7 Carefully unscrew the sensor and. whore applicable, recover the sealing ring. Refitting 8 If the sensor was originally fitted using sealing compound, clean the sensor threads thoroughly, and coat them with fresh sealing compound. 9 If the sensor was originally fitted using a sealing ring, use a new sealing ring on refitting. 10 Refitting is a reversal of removal, but refill the cooling system as described in Chapter 1A or 18. 11 On completion, start the engine and run it until it reaches normal operating temperature. Continue to run the engine until the cooling fan cuts in and out correctly.
7 Coolant pump • & removal, inspection 5 and refitting
Removal
Petrol engine models 1 Disconnect the battery negative terminal (refer to Disconnecting the battery in the Reference Section of this manual). 2 Drain the cooling system and remove the auxiliary drivebett(s) as described In Chapter 1 A. 3 Remove the timing belt as described In Chapter 2A or 28. 4 Unscrew the securing bolts/nuts, and withdraw the coolant pump (see illustrations).
7.9b ... and lift off the pulley (diesel engine)
(petrol engine) If the pump Is stuck, tap it gently using a soft-faced mallet - do not lever between the pump and cylinder block mating faces.
Diesel engine models 5 Disconnect the battery negative terminal (refer to D/s connecting the battery in the Reference Section of this manual). 6 Drain the cooling system as described in Chapter 1B. 7 Remove the auxiliary drivebelt(s) as descnbed In Chapter 1B. 6 On models fitted with power steenng, refer to Chapter 10 and remove the power steering pump from its mountings; this can be achieved without disconnecting the power steering fluid hoses from the pump. Tie the pump away from the work area, taking care to avoid kinking the fluid hoses. 9 Unscrew the securing bolts, and remove the coolant pump pulley. It will be necessary to counterhold the pulley In order to unscrew the bolts, and this is most easily achieved by wrapping an old drivebelt tightly around the pulley to act in a similar manner to a strap 3 wrench. Alternatively, a stout screwdriver can be braced between two of the pulley bolts while the third is slackened (see illustrations). 10 Disconnect ihe bypass hoses from the coolant pump outlet stubs. 11 Unscrew the securing bolts, and withdraw the coolant pump assembly. Note that the pump must be detached from the transfer pipe than runs behind the cylinder block to the thermostat housing (see illustration). The pipe is a push fit in the port on the rear of the coolant pump
7.11 Removing the coolant pump assembly (diesel engine)
Page 118 of 225
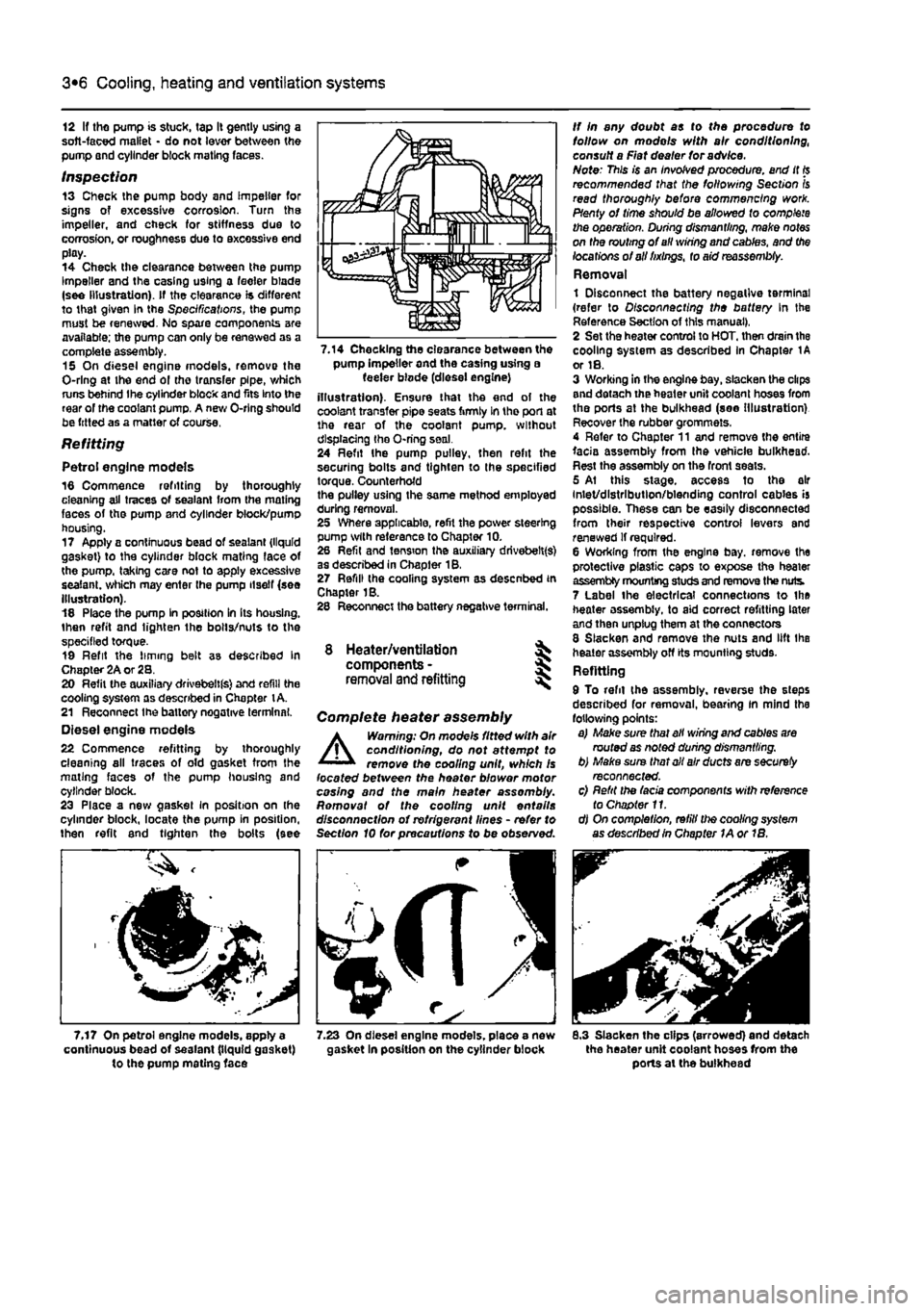
3*2 Cooling, heating and ventilation systems
12 If tho pump is stuck, tap It gently using a soft-faced mallet • do not lever between the pump and cylinder block mating faces.
Inspection 13 Check the pump body and impeller for signs of excessive corrosion. Turn the impeller, and check for stiffness due to corrosion, or roughness due to excessive end play. 14 Check the clearance between the pump Impeller and the casing using a feeler blade (see Illustration). If the clearance is different to that given In the Specifications, the pump must be renewed. No spare components are available; the pump can only be renewed as a complete assembly. 15 On diesel engine models, remove the O-rlng at the end ol the transfer pipe, which runs behind Ihe cylinder block and fits Into the rear of the coolant pump. A new O-rlng should be fitted as a matter of course.
Refitting
Petrol engine models 16 Commence refitting by thoroughly cleaning all traces of sealant from the mating faces of the pump and cylinder block/pump housing. 17 Apply a continuous bead of sealant {liquid gasket) to the cylinder block mating face of the pump, taking care not to apply excessive sealant, which may enter the pump itself (see Illustration). 18 Place the pump In position In Its housing, then refit and lighten the bolts/nuts to the specified torque. 19 Refit the liming belt as described In Chapter 2A or 28. 20 Refit the auxiliary drivebeltfs) and refill the cooling system as described in Chapter
t
A. 21 Reconnect Ihe battery negative terminal. Diesel engine models 22 Commence refitting by thoroughly cleaning all traces of old gasket from the mating faces of the pump housing and cylinder block. 23 Place a new gasket in position on (he cylinder block, locate the pump in position, then refit and tighten the bolts (see
7.17 On petrol engine models, apply a continuous bead of sealant (liquid gasket) to the pump mating face
pump Impeller and the casing using a feeler blode (diesel engine) illustration). Ensure that the end of the coolant transfer pipe seats firmly In tho port at the rear of the coolant pump, without displacing the O-ring seal. 24 Refit Ihe pump pulley, then refit the securing bolts and tighten to the specified torque. Counterhofd the pulley using the same method employed during removal. 25 Where applicable, refit the power steering pump with reference to Chapter 10. 26 Refit and tension the auxiliary drivebelt(s) as described in Chapter 18. 27 Refill (he cooling system as desenbed in Chapter 1B. 28 Reconnect the battery negative terminal.
8 Heater/ventilation components - § removal and refitting
Complete heater assembly
A
Warning: On mode's fitted with air conditioning, do not attempt to remove the cooling unit, which Is located between the heater blower motor casing and the main heater assembly. Romovat of the cooling unit entails disconnection of refrigerant lines - refer to Section 10 for precautions to be observed.
rfJS
8.3 Slacken the clips (arrowed) and detach the heater unit coolant hoses from the ports at the bulkhead
Page 119 of 225
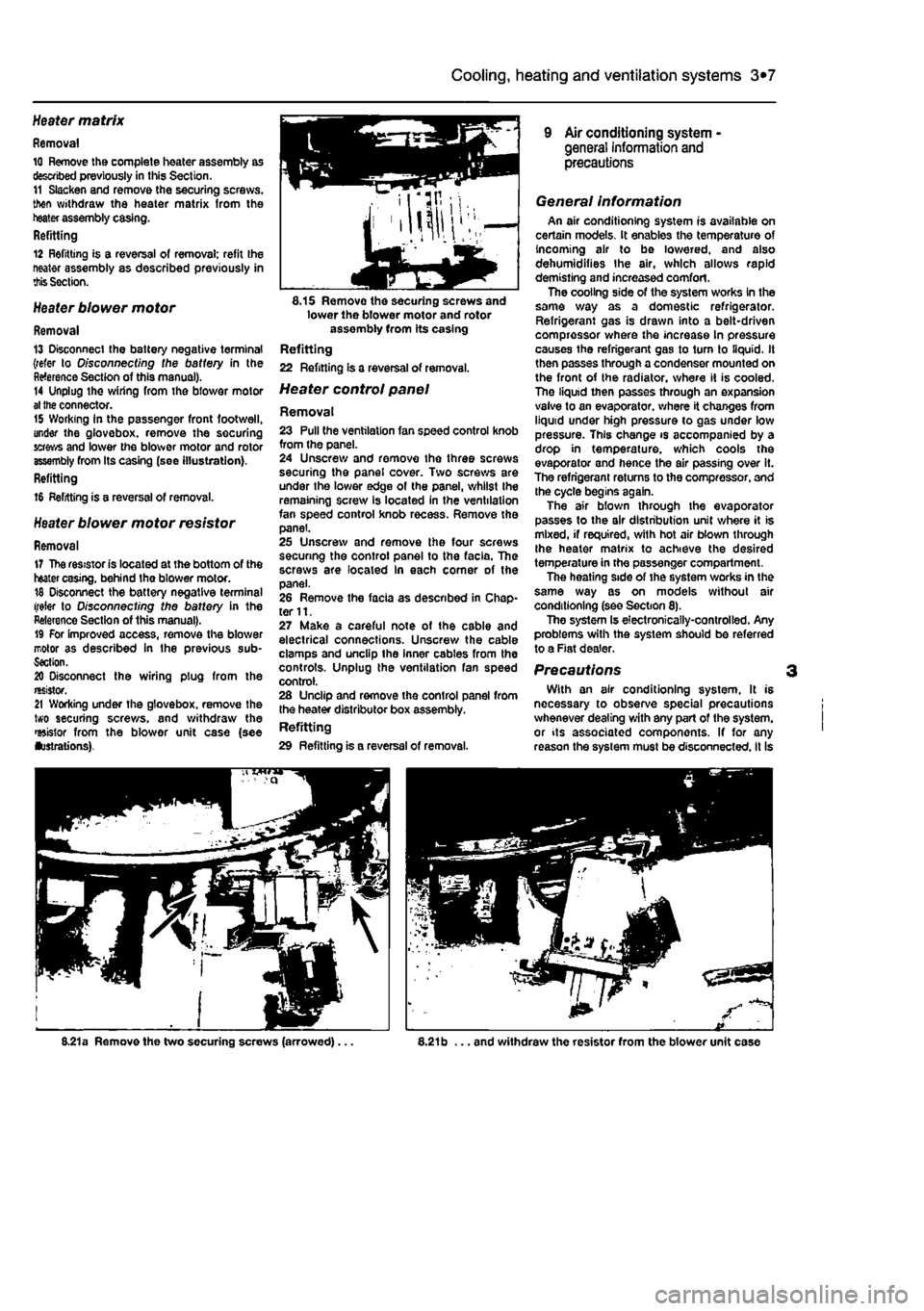
3*2 Cooling, heating and ventilation systems
Heater matrix Removal 10 Remove the complete heater assembly as described previously in this Section. 11 Slacken and remove the securing screws, then withdraw the heater matrix from the tester assembly casing. Refitting 12 Refitting is a reversal of removal; refit Ihe neater assembly as described previously in
this
Section.
Heater blower motor
Removal 13 Disconnect the battery negative terminal {refer to Disconnecting the battery in the Reference Section of this manual). 14 Unplug the wiring from the blower motor
al the
connector. 15 Working in the passenger front footwell, under the glovebox. remove the securing grows and lower the blower motor and rotor assembly from Its casing (see illustration). Refitting
16 Refitting is a reversal of removal.
Heater blower motor resistor
Removal 17 The resistor is located at the bottom of the heater casing, behind the blower motor. 18 Disconnect the battery negative terminal (refer to O/sconnecf/ng the battery in the Reference Section of this manual). 19 For improved access, remove the blower motor as described in the previous sub-Section. 20 Disconnect the wiring plug from the resistor. 21 Working under the glovebox. remove the two securing screws, and withdraw the resistor from the blower unit case (see lustrations).
8.15 Removo the securing screws and lower the blower motor and rotor assembly from its casing Refitting 22 Refining Is a reversal of removal.
Heater control panel
Removal 23 Pull the ventilation fan speed control knob from the panel. 24 Unscrew and remove the three screws securing the panel cover. Two screws are under the lower edge of the panel, whilst Ihe remaining screw is located in the ventilation fan speed control knob recess. Remove the panel. 25 Unscrew and remove the four screws securing the control panel to the facia. The screws are located in each comer of the panel. 26 Remove the facia as described in Chap-ter 11. 27 Make a careful note of the cable and electrical connections. Unscrew the cable clamps and unclip the inner cables from the controls. Unplug the ventilation fan speed control. 28 Unclip and remove the control panel from the heater distributor box assembly. Refitting 29 Refitting is a reversal of removal.
9 Air conditioning system -general Information and precautions
General information An air conditioning system is available on certain models. It enables the temperature of Incoming air to be lowered, and also dehumidifies the air, which allows rapid demisting and increased comfort. The cooling side of the system works In the same way as a domestic refrigerator. Refrigerant gas is drawn into a belt-driven compressor where the increase In pressure causes the refrigerant gas to turn to liquid. It then passes through a condenser mounted on the front of the radiator, where it is cooled. Tho liquid then passes through an expansion vaive to an evaporator, where it changes from liquid under high pressure to gas under low pressure. This change is accompanied by a drop in temperature, which cools the evaporator and hence the air passing over it. The refrigerant returns to the compressor, and the cycle begins again. The air bfown through the evaporator passes to the air distribution unit where it is mixed, if required, with hot air blown through the heater matrix to achieve the desired temperature in the passenger compartment. The heating side of ihe system works in the same way as on models without air conditioning (see Section 8). The system Is electronically-controlled. Any problems with the system should be referred to a Fiat dealer.
Precautions With an air conditioning system. It is necessary to observe special precautions whenever dealing with any part of the system, or its associated components. If for any reason the system must be disconnected, it Is
8.21a Remove the two securing screws (arrowed)... ,21b ... and withdraw the resistor from the blower unit case
Page 120 of 225
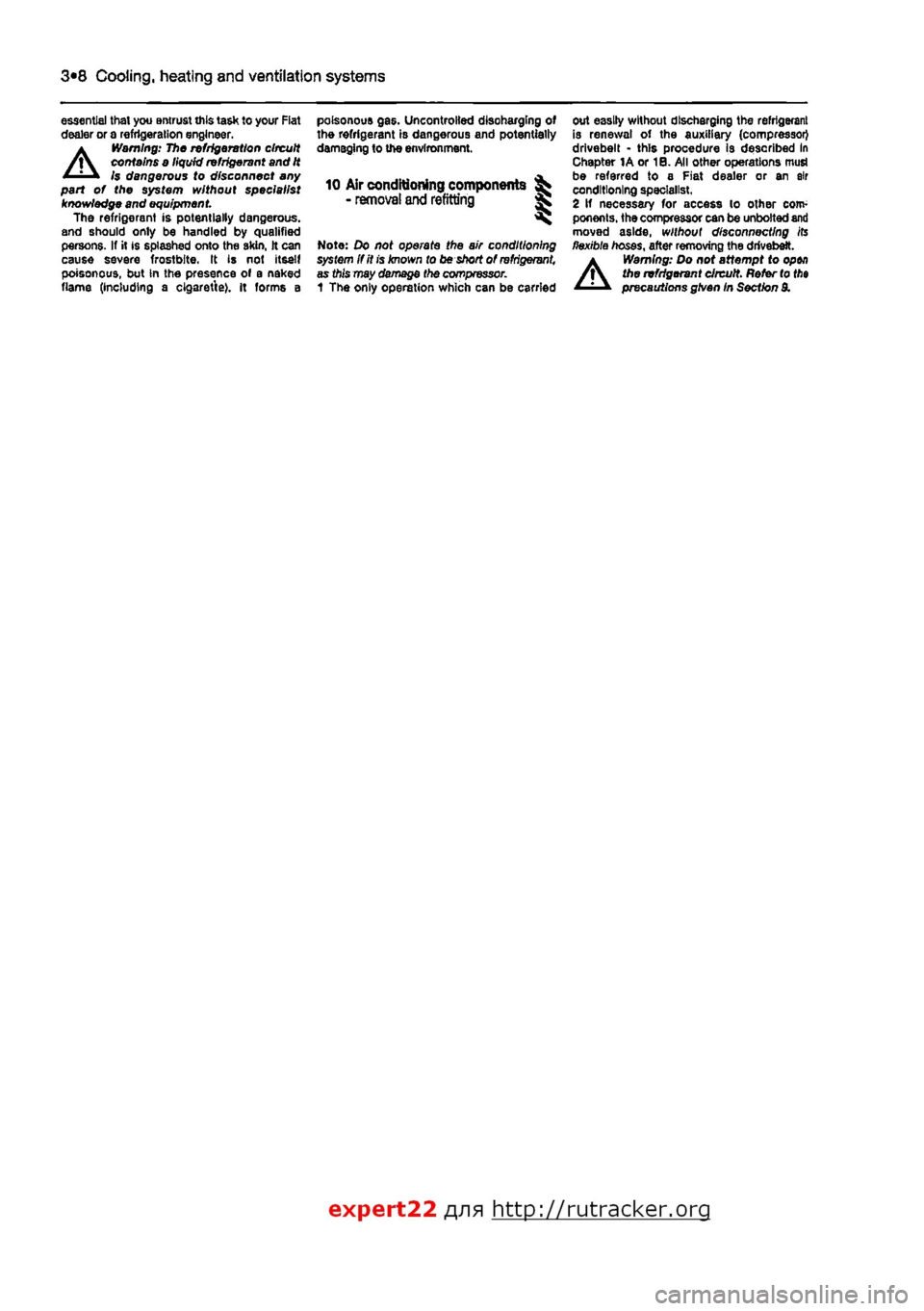
3*2 Cooling, heating and ventilation systems
essential that you entrust this task to your Flat dealer or a refrlgeralion engineer.
A
Warning: The refrigeration circuit contains a liquid refrigerant and
H
Is dangerous to disconnect any part of the system without specialist knowledge and equipment. The refrigerant is potentially dangerous, and should only be handled by qualified persons. If it is splashed onto tha skin, It can cause severe frostbite, tt Is not Itself poisonous, but In the presence of a naked flame (Including a cigarette), it forms a
poisonous gas. Uncontrolled discharging of the refrigerant is dangerous and potentially damaging to the environment.
10 Air conditioning components ^S - removal and refitting J
Note: Do not operate the air conditioning system If it is known to be short of refrigerant, as this may damage the compressor. 1 The only operation which can be carried
out easily without discharging the refrigerant is renewal of the auxiliary (compressor) drivebelt - this procedure Is described in Chapter 1A or 1B. All other operations must be referred to a Fiat dealer or an air conditioning specialist. 2 If necessary for access to other com-ponents, the compressor can be unbolted and moved aside, without disconnecting its flexible hoses, after removing the drivebelt.
A
Warning: Do not attempt to open the refrigerant circuit. Refer to
the
precautions given in Section 9.
expert22 a/ia http://rutracker.org
Page 136 of 225
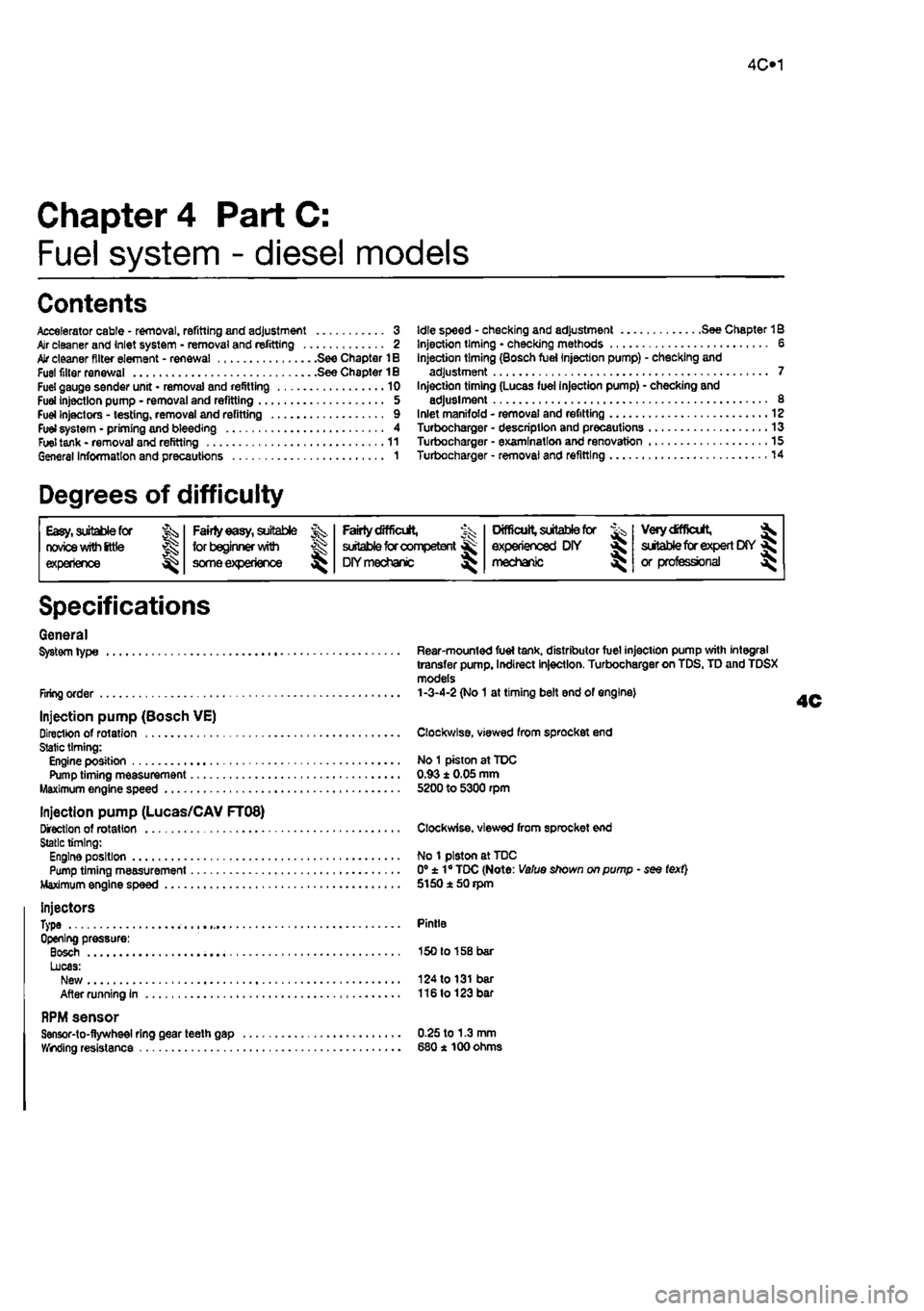
4C»1
Chapter 4 PartC:
Fuel system - diesel models
Contents
Accelerator cable • removal, refitting and adjustment 3 Air cleaner and inlet system • removal and refitting 2
AJr
cleaner filter element - renewal See Chapter IB Fuet filter renewal See Chapter 1B Fuel gauge sender unit • removal and refitting 10 Fuel injection pump • removal and refitting 5 Fuel injectors - testing, removal and refitting 9
Fuel
system • priming and bleeding 4
Fuel
tank - removal and refitting 11 General Information and precautions 1
Idle speed - checking and adjustment See Chapter 1B Injection timing • checking methods 6 injection timing {Bosch fuel Injection pump) • checking and adjustment 7 Injection timing (Lucas fuel Injection pump) - checking and adjustment 8 Inlet manifold - removal and refitting 12 Turbocharger - description and precautions 13 Turbocharger - examination and renovation 15 Turbocharger - removal and refitting 14
Degrees of difficulty
Easy,
suitable for novice
with Ittle
p experience sS^
Fairly easy, suitable (or beginner with some experience
Fairly tfifficuit, suitable
for
competent ^
DIY
mechanic
Difficult, suitable
for ^ experienced DIY jR mechanic ^
Very difficult, ^ sutable for expert
DIY
S or professional ^
Specifications
General System type
Firing order
Injection pump (Bosch VE) Direction of rotation Static timing: Engine position Pump timing measurement Maximum engine speed
Injection pump (Lucas/CAV FT08) Direction of rotation Static timing: Engine position Pump timing measurement Maximum engine speed
injectors Type Opening pressure: Bosch Lucas: New After running in
RPM sensor Sensor-to-flywheel ring gear teeth gap — Winding resistance
Rear-mounted fuel tank, distributor fuel injection pump with integral transfer pump. Indirect Injection, Turbocharger on TDS, TD and TDSX models 1-3-4-2 (No
1
at timing belt end of engine)
Clockwise, viewed from sprocket end
No
1
piston at TDC 0.93 ± 0.05 mm 5200 to 5300 rpm
Clockwise, viewed from sprocket end
No 1 piston at TDC 0° ± 1° TDC (Note: Value shown on pump - see text} 5150150 rpm
Pintle
150 to 158 bar
124 to
131
bar 116lo123 bar
0.25 to 1.3 mm 680* 100 ohms
Page 137 of 225
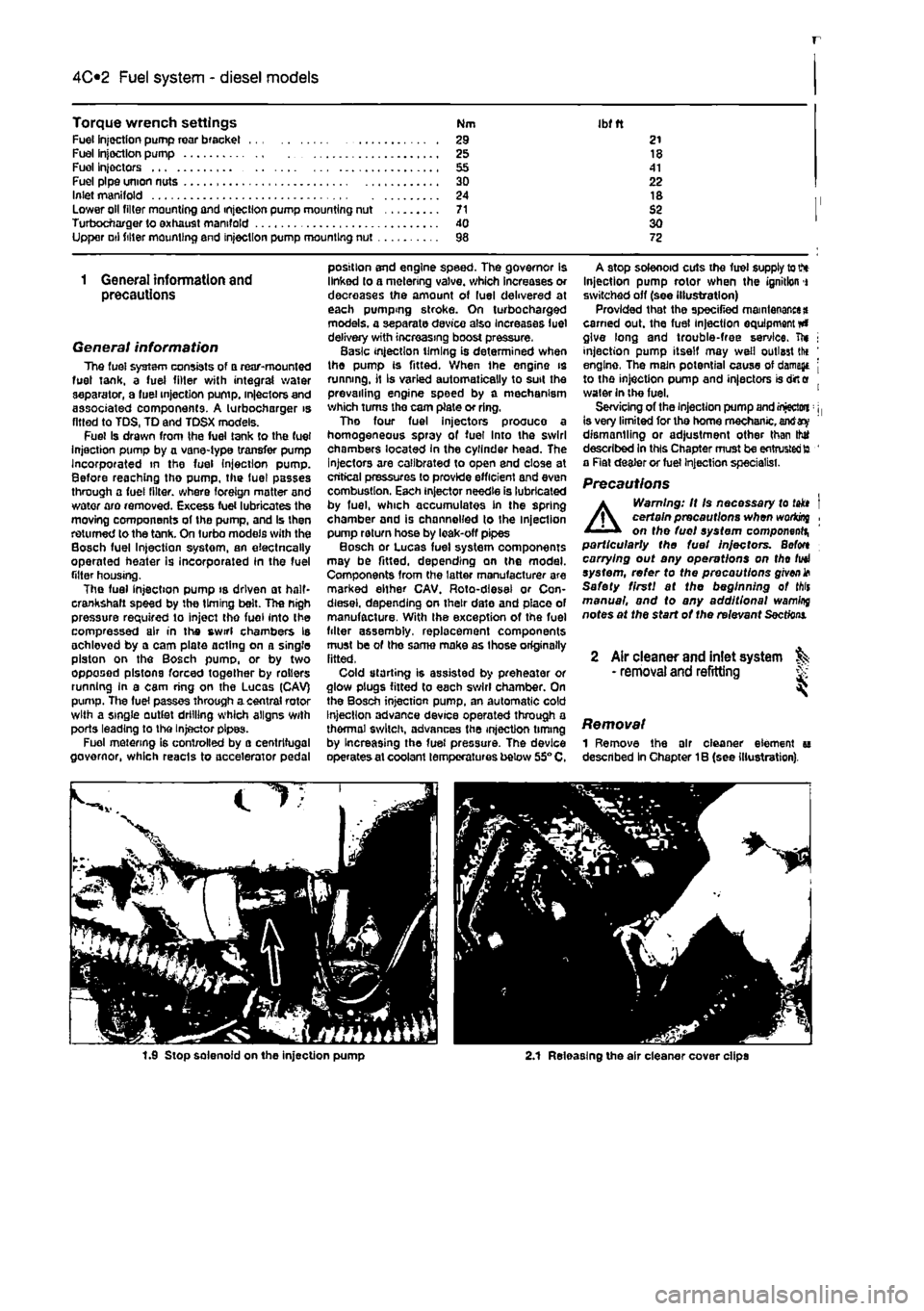
Fuel system - diesel models 4C*3
Torque wrench settings Nm Ibfft Fuel injection pump roar bracket .. . 29 21 Fuel Injection pump .... 25 18 Fuel Injectors 41 Fuel pipe union nuts .... 30 22 Inlet manifold .... 24 18 Lower oil tiller mounting and injection pump mounting nut ..... .... 71 S2 Turbocnarger to exhaust manifold .... <10 30 Upper Dtl filter mounting end injection pump mounting nut 98 72
1 General information and precautions
General information The fuel system consists of a rear-mounted fust tank, a fuel filter with integral water separator, a fuel injection pump, in|eciors and associated components. A turbocharger is fitted to TDS, TD and TDSX models. Fuel Is drawn from the fuel tank to the fuel Injection pump by a vane-type transfer pump Incorporated in the fuel injection pump. Before reaching tho pump, the fuel passes through a fuel filter, where foreign matter and water aro removed. Excess fuel lubricates the moving components of the pump, and Is then returned to the tank. On turbo models with the Bosch fuel Injection systom, an eiectncally operated heater is incorporated In the fuel filter housing. The fuel injection pump is driven at half-crankshaft speed by the timing belt. The nigh pressure required to inject tho fuel into the compressed air in the swirl chambers Is achlovod by a cam plate acting on a single piston on the Bosch pumo, or by two opposed pistons forced together by rollers running in a cam ring on the Lucas (CAV) pump. Tlie fuel passes through acentral rotor with a single outlet drilling which aligns With ports leading to the Injector pipes. Fuel metering is controlled by a centrifugal governor, which reacts to accelerator pedal
position end engine speed. The governor is linked lo a metering valve, which increases or decreases the amount of fuel delivered at each pumping stroke. On turbocharged models, a separate device also Increases luel delivery with increasing boost pressure. Basic injection timing is determined when the pump is fitted. When the engine is running, it Is varied automatically to suit the prevailing engine speed by a mechanism which turns the cam plate or ring, Tho four fuel injectors proouco a homogeneous spray of fuel Into the swirl chambers located In the cylinder head. The Injectors are calibrated to open end close at critical pressures lo provide efficient and even combustion. Each injector needle is lubricated by fuel, which accumulates In the spring chamber and is channelled to the injection pump return hose by loak-off pipes Bosch or Lucas fuel system components mBy be fitted, depending on the model. Components from the latter manufacturer are marked either CAV. Roto-dlesel or Con-diesel. depending on their date and place of manufacture. With the exception of the fuel filter assembly, replacement components must be of tho same make as those originally fitted. Cold starting is assisted by preheater or glow plugs fitted to each swirl chamber. On the Bosch injection pump, an automatic cold Injection advance device operated through a thermal switch, advances the injection timing by Increasing the fuel pressure. The device operates at coolant temperatures below 55° C,
A stop solenoid cuts the fuel supply to V* Injection pump rotor when the ignition i switched off (see illustration) Provided that the specified maintenance* earned out. the fuel injection equipment #» give long and trouble-free service, ft* j injection pump itself may well outlast tlx ' engine, The main potential cause of damage j to the injection pump and injectors is dirt e water in the fuel. 1 Servicing of the injection pump and injectwi: j, is very limited for tho home mechanic, antf dismantling or adjustment other than thtf described In this Chapter must be entrusted to ' a Rat dealer or fuel Injection specialist.
Precautions
A
Warning: It Is necessary to takt I certain precautions when woriong , on the fuel system component^ particularly the fuel Injectors. Befon carrying out any operations on tho fuel system, refer to the precautions given* Safety first! at the beginning of Mis manual, and to any additional wamlrq notes at the start of the relevant
Sections.
2 Air cleaner and inlet system ^ • removal and refitting S
Removal 1 Remove the air cleaner element u described In Chapter 1B (see illustration).
1.9 Stop solenoid on the injection pump 2.1 Releasing the air cleaner cover clips