headlight bulb FIAT PUNTO 1999 176 / 1.G Workshop Manual
[x] Cancel search | Manufacturer: FIAT, Model Year: 1999, Model line: PUNTO, Model: FIAT PUNTO 1999 176 / 1.GPages: 225, PDF Size: 18.54 MB
Page 17 of 225
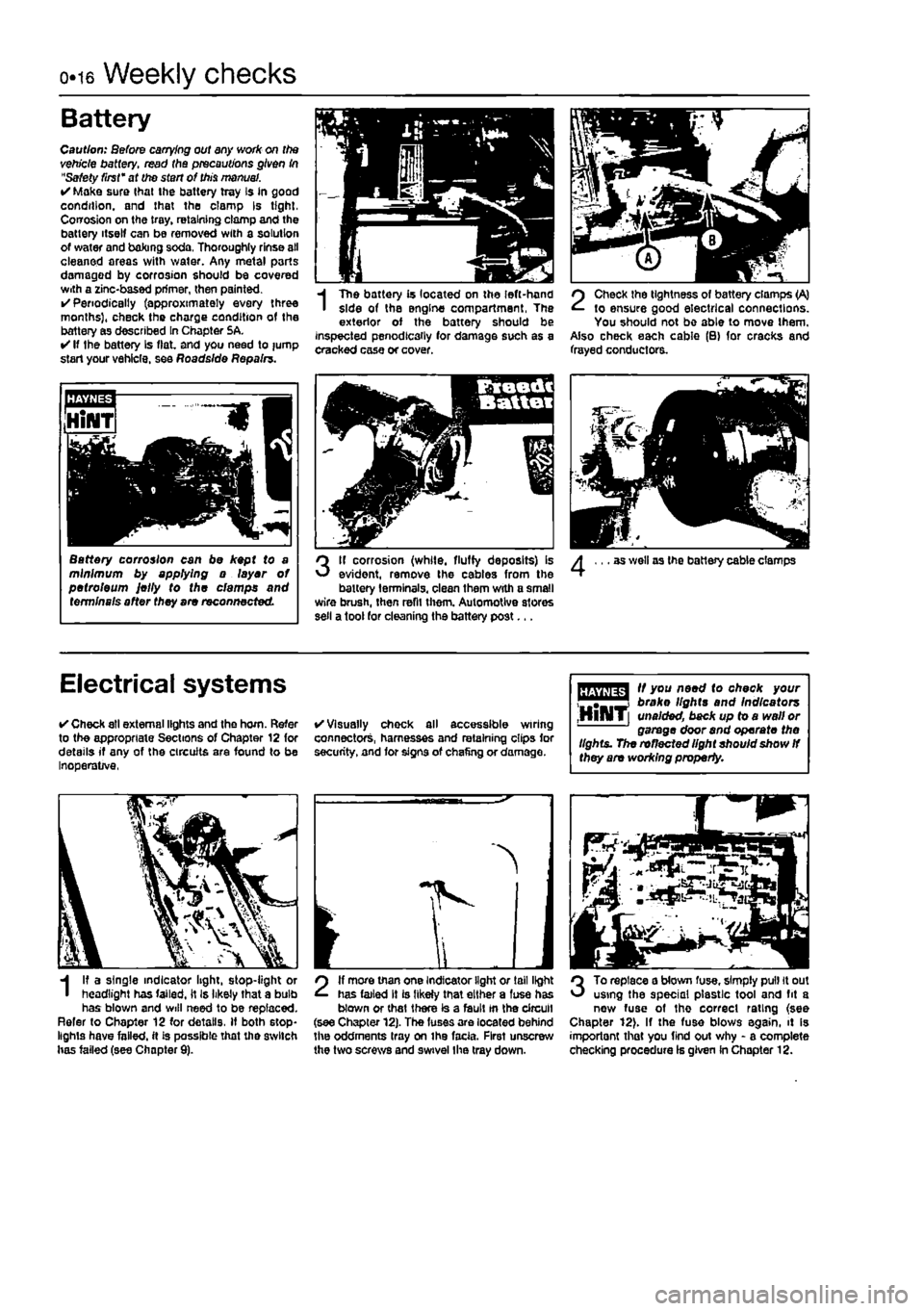
o«i6 Weekly checks
Battery
Caution: Before carrying out any work on the vehicle battery, read the precautions given In "Safety first" at the start of this manual. • Make sure thai the battery tray is in good condition, and that the clamp Is tight. Coirosion on the tray, retaining clomp and the battery itself can be removed with a solution of water and baking soda, Thoroughly rinse all cleaned areas with water. Any metal parts damaged by corrosion should be covered with a zinc-based primer, then painted. • Periodically (approximately every three months), check the charge condition of the battery as described In Chapter SA. • If the battery Is flat, and you need to jump start your vehicle, see Roadside Repalrz.
Battery corrosion can be kept to a minimum by applying o layer of petroleum Jelly to the clamps and terminals after they are reconnected
fin %
I
The battery is located on the left-hand side of the engine compartment, The exterior of the battery should be inspected penodlcaily for damage such as a cracked case or cover.
2
Check the tightness of battery clamps (A) to ensure good electrical connections. You should not be able to move them. Also check each cable (B) for cracks and frayed conductors.
3
If corrosion (while, fluffy deposits) is evident, remove the cables from the battery terminals, clean them with a small wire brush, then refit them. Automotive stores sell a tool for cleaning the battery post...
as well as the battery cable clamps
Electrical systems
• Check all external lights and the horn. Refer to the appropriate Sections of Chapter 12 for details if any of the circuits are found to be Inoperative,
• Visually chock all accessible wiring connectors, harnesses and retaining clips for security, and for signs of chafing or damage.
fffjffflg^ " y°u A**^ check your "T™*! broke lights and Indicators ,HllMT[ unaided, back up to a wall or garage door and operate the lights. The reflected light shouid show
If
they are working property.
I
I? a single indicator light, stop-light or headlight has failed, it Is likely that a bulb has blown and will need to be replaced. Refer to Chapter 12 for details. If both stop-lights have failed, it is passible that the switch has failed (see Chapter 9).
2
If more than one Indicator light or tail light has failed It is likely that either a fuse has blown or that there is a fault tn the circuit (see Chapter 12). The fuses are located behind the oddments tray on ihe facia. First unscrew the two screws and swivel Ihe tray down.
3
To replace a blown fuse, simply pull it out using the special plastic tool and fit a new fuse of tho correct rating (see Chapter 12). If the fuse blows again, it is importont that you find out why - a complete checking procedure Is given in Chapter 12.
Page 150 of 225
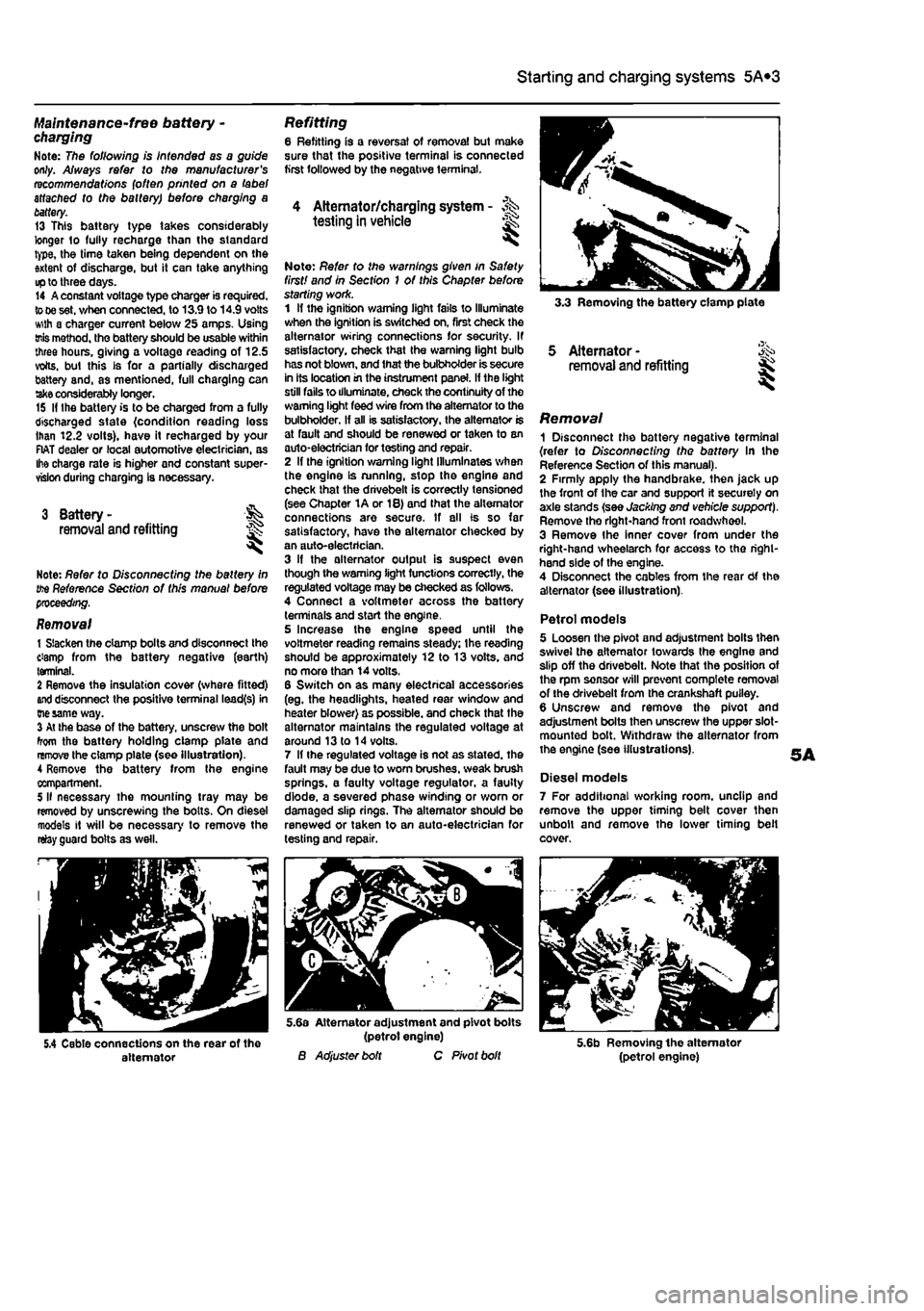
5A«2 Starting and charging systems
Maintenance-free battery -charging Note: The following is intended as a guide only. Always refer to the manufacturer's recommendations (often printed on a label attached to the battery) before charging a battery. 13 This battery type takes considerably longer lo fully recharge than the standard type, the time taken being dependent on the extent of discharge, but it can take anything
up
to three days. 14 A constant voltage type charger is required, tooe set, when connected, to 13.9 to 14.9 votts wth a charger current below 25 amps. Using
mis
method, the battery should be usable within three hours, giving a voltage reading of 12.5 vofts. but this Is for a partially discharged battery and, as mentioned, full charging can
take
considerably longer. 15 If Ihe battery is to be charged from a fully discharged state {condition reading loss lhan 12.2 volts), have it recharged by your FIAT dealer or local automotive electrician, as Ihe charge rate is higher and constant super-vision during charging Is necessary.
3 Battery -removal and refitting
Note: Refer to Disconnecting the battery in ifte Reference Section of this manual before proceeding.
Removal 1 Slacken the clamp bolts and disconnect the ctamp from the battery negative (earth) terminal. 2 Remove the insulation cover (where fitted)
and
disconnect the positive terminal lead(s) in
Die same
way. 3 At the base of the battery, unscrew the bolt from the battery holding clamp plate and remove the clamp plate (see Illustration). A Remove the battery from Ihe engine compartment. 5 II necessary the mounting tray may be removed by unscrewing the bolts. On diesel models it will be necessary to remove the relay guard bolts as well.
Refitting 6 Refitting is a reversal of removal but make sure that the positive terminal is connected first followed by the negative terminal.
4 Alternator/charging system - >%•> testing in vehicle
Note: Refer to the warnings given in Safety first! and in Section 1 of this Chapter before starting work. 1 If the ignition warning light fails to Illuminate when the ignition is switched on, first check the alternator wiring connections for security. If satisfactory, check that the warning light bulb has not blown, and that the bulbholder is secure in its location in the instrument panel. If the light still fails to illuminate, check the continuity of the warning light feed wire from the alternator to the bulbholder. If all is satisfactory, the alternator is at fault and should be renewed or taken to an auto-electrician for testing and repair. 2 If the ignition warning light Illuminates when the engine Is running, stop the engine and check that the drivebelt is correctly tensioned (see Chapter 1A or 18) and that the alternator connections are secure. If all is so far satisfactory, have the alternator checked by an auto-electrician. 3 If the alternator output is suspect even though the warning light functions correctly, the regulated voltage may be checked as follows. 4 Connect a voltmeter across the battery terminals and start the engine. 5 Increase the engine speed until the voltmeter reading remains steady; the reading should be approximately 12 to 13 volts, and no more than 14 volts. 6 Switch on as many electrical accessories (eg. the headlights, heated rear window and heater blower) as possible, and check that the alternator maintains the regulated voltage at around 13 to 14 volts. 7 If ihe regulated voltage is not as stated, the fault may be due to worn brushes, weak brush springs, e faulty voltage regulator, a faulty diode, a severed phase winding or worn or damaged slip rings. The alternator should be renewed or taken to an auto-electrician for testing and repair.
3.3 Removing the battery clamp plate
5 Alternator -removal and refitting
Removal 1 Disconnect the battery negative terminal {refer to Disconnecting the battery In the Reference Section of this manual). 2 Firmly apply the handbrake, then jack up the front of the car and support it securely on axle stands (see Jacking and vehicle support). Remove tho right-hand front roadwheel. 3 Remove Ihe Inner cover from under the right-hand wheelarch for access to tho right-hand side of the engine. 4 Disconnect the cables from the rear Of the alternator (see illustration).
Petrol models 5 Loosen the pivot and adjustment bolts then swivel the alternator towards the engine and slip off the drivebelt. Note that the position of the rpm sensor will prevent complete removal of the drivebelt from the crankshaft puiley. 6 Unscrew and remove the pivot and adjustment bolts then unscrew the upper slot-mounted bolt. Withdraw the alternator from the engine (see illustrations).
Diesel models 7 For additional working room, unclip and remove the upper timing belt cover then unbolt and remove the lower timing belt cover.
5.4 Cable connections on the rear of the alternator
5.6a Alternator adjustment and pivot bolts (petrol engine) B Adjuster bolt C Pivot bolt 5.6b Removing the alternator (petrol engine)
Page 151 of 225
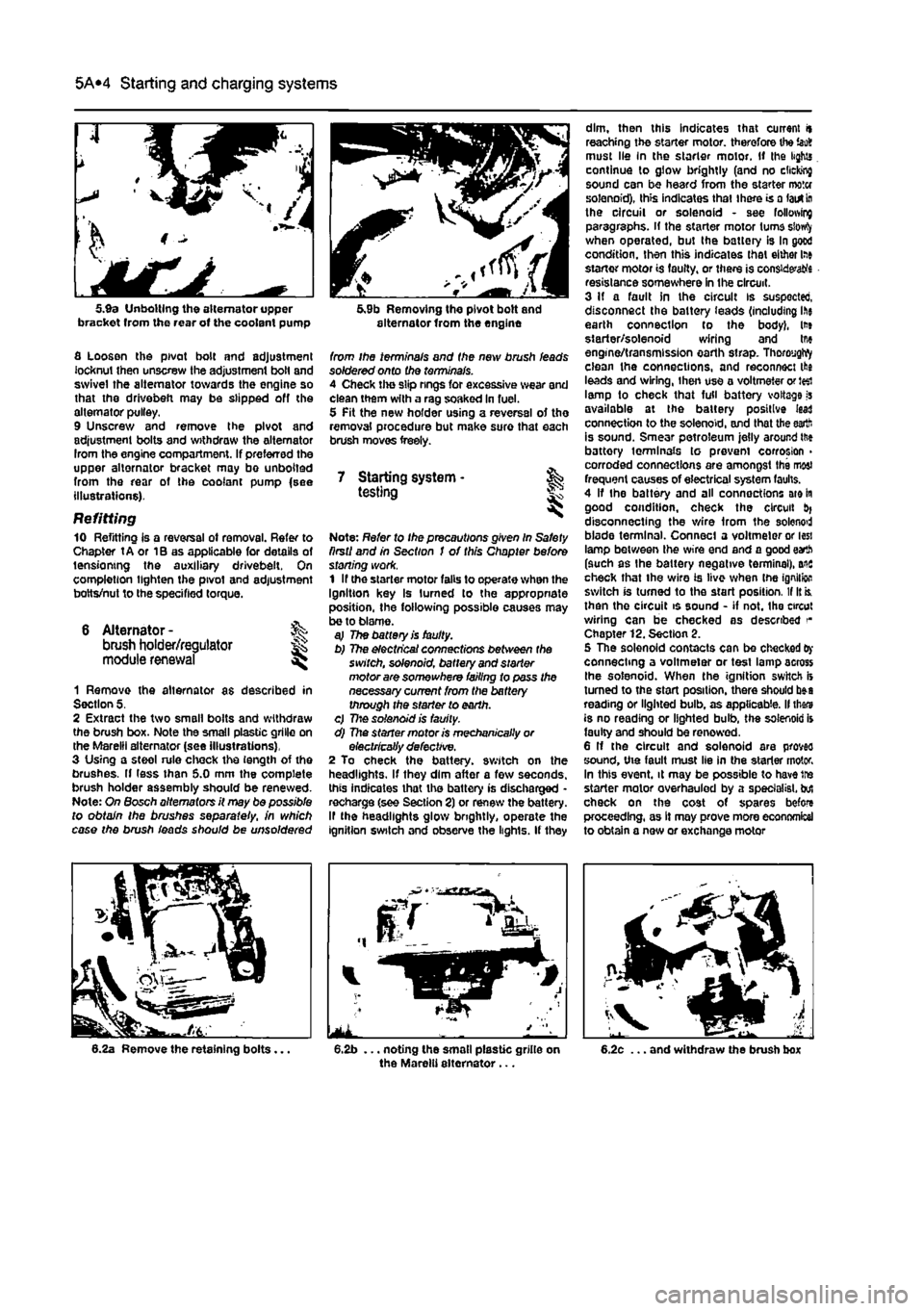
5A«2 Starting and charging systems
5.9a Unbolting the alternator upper bracket from the rear of the coolant pump
fl Loosen the pivot bolt and adjustment locknut then unscrew the adjustment bolt and swivel the alternator towards the engine so that the drivebefi may be slipped off the alternator pulley. 9 Unscrew and remove the pivot and adjustment bolts and withdraw the alternator Irom the engine compartment. If preferred the upper alternator bracket may bo unbolted from the rear of the coolant pump {see illustrations).
Refitting 10 Refitting is a reversal ot removal. Refer to Chapter tA or 1B as applicable for details of tensioning the auxiliary drivebeit. On completion lighten the pivot and adjustment botts/nut to the specified torque.
6 Alternator -brush holder/regulator module renewal
%
1 Remove the alternator as described in Section 5. 2 Extract the two small bolts and withdraw the brush box. Note the small plastic grille on the Marelli alternator (see illustrations), 3 Using a steol rule chock the length of the brushes. If less than 5.0 mm the complete brush holder assembly should be renewed. Note: On Bosch alternators it may be possible to obtain the brushes separate//, in which case the brush ieads should be unsoldered
5.9b Removing the pivot bolt and alternator from the engine
from ihe terminals and the new brush leads soldered onto the terminals. 4 Check the slip rings for excessive wear and clean them with a rag soaked in fuel. 5 Pit the new holder using a reversal of the removal procedure but make sure that each brush moves freely.
7 Starting system • & testing
Note: Refer to Ihe precautions given In Safety firstI and in Section I of this Chapter before stoning work. 1 If the starter motor falls to operate when the Ignition key Is turned to the appropriate position, the following possible causes may be to blame. aj The battery is faulty. b) The electrical connections between the switch, solenoid, battery and starter motor are somewhere failing to pass the necessary current from the battery through the starter to earth. c) 77:© solenoid is faulty. d) The starter motor is mechanically or electrically defective. 2 To check the battery, switch on the headlights. If they dim after a few seconds, this indicates that the battery is discharged -recharge (see Section 2) or renew the battery. If the headlights glow brightly, operate the ignition switch and observe the lights. If they
dim, then this indicates that current it reaching the starter motor, therefore the iao8 must lie In the starter motor. If the lights continue to glow brightly (and no clicking sound can be heard from the starter motor solenoid), this indicates that there is a lairt
In
the circuit or solenoid - see following paragraphs, if the starter motor turns siowfy when operated, but the battery is In good condition, then this indicates that either lae starter motor is faulty, or there is considers resistance somewhere in the circuit. 3 If a fault in the circuit is suspected, disconnect the battery ieads (including ihe earth connection to the body), lt» starter/solenoid wiring and tne engine/transmission earth strap. ThoroygWy clean the connections, and reconnect the leads and wiring, ihen use a voltmeter or J«i lamp to check that full battery voltage is available at the battery positive lead connection to the solenoid, and that the earth is sound. Smear petroleum jelly around ttie battory terminals to prevent corrosion > corroded connections are amongst the most frequent causes of electrical system faults. 4 If the battery and all connections are in good condition, check the circuit disconnecting the wire from the solenod blade terminal. Connect a voltmeter or less lamp between the wire end and a good earth (such as the battery negative terminal), ais check that the wire is live when tne ignition switch is turned to the start position. If It is. then the circuit is sound - if not. the circut wiring can be checked as described Chapter 12. Section 2. 5 The solenoid contacts can be checked
Oy
connecting a voltmeter or test lamp across Ihe solenoid. When the ignition switch is turned to the start position, there should b»a reading or lighted bulb, as applicable. II thars is no reading or lighted bulb, the solenoid is faulty and should be renewed. 6 If the circuit and solenoid are proves sound, the fault must lie in the starter motor. In this event, it may be possible to have tre starter motor overhauled by a specialist, but check on the cost of spares before proceeding, as It may prove more economical to obtain a new or exchange motor
Page 214 of 225
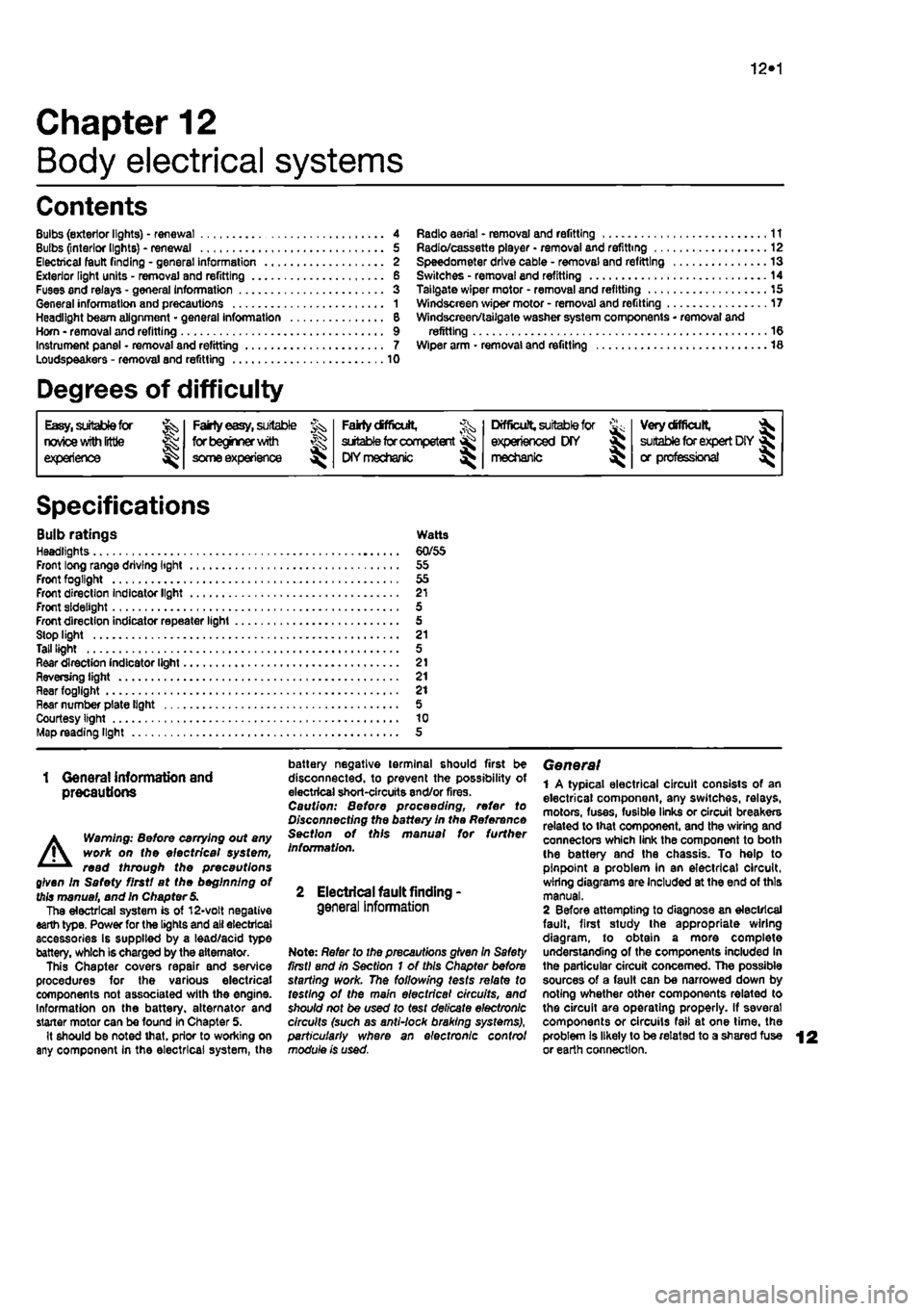
10*1
Chapter 12
Body electrical systems
Contents
Bulbs (exterior lights) - renewal 4 Bulbs (interior lights) - renewal 5 Electrical fault finding - general information 2 Exterior light units - removal and refitting 6 Fuses and relays - general Information 3 General information and precautions 1 Headlight beam alignment • general Information 6 Horn • removal and refitting 9 Instrument panel - removal and refitting 7 Loudspeakers - removal and refitting 10
Degrees of difficulty
Radio aerial - removal and refitting 11 Radio/cassette player • removal and refitting 12 Speedometer drive cable - removal and refitting 13 Switches - removal end refitting 14 Tailgate wiper motor - removal and refitting 15 Windscreen wiper motor - removal and refitting 17 Windscreen/tailgate washer system components • removal and refitting 16 Wiper arm • removal and refitting 18
Easy,
statable for ^
novice with liffle
|| experience ^
Fairly
easy,
suitable for beginner with ^ some experience ^
Fabtycffficiit,
suitable
for competent ^
DIY
mechanic ^
Difficult, suitable for
^ experienced DIY JR mechanic
Very difficult,
A,
suitable
for
expert DIY
Sj or professional ^
Specifications
Bulb ratings Watts Headlights 60/55 Front long range driving light 55 Front fogllght 55 Front direction Indicator light 21 Front sidelight 5 Front direction indicator repeater light 5 Stop light 21 Tall light 5 Rear direction indicator light 21 Reversing light 21 near fogllght 21 Hear number plate light 5 Courtesy light 10 Map reading light 5
1 Genera! information and precautions
A
Warning: fie/Ore carrying out any work on the electrical system, read through the precautions given in Safety first! at the beginning of this manual, and in Chapter 8. The electrical system is of 12-volt negative earth type. Power for the lights and all electrical accessories is supplied by a lead/acid type battery, which is charged by the alternator. This Chapter covers repair and service procedures for the various electrical components not associated with the engine. Information on the battery, alternator and starter motor can be found in Chapter 5. It should be noted that, prior to working on any component In the electrical system, the
battery negative terminal should first be disconnected, to prevent the possibility of electrical short-circuits and/or fires. Caution: Before proceeding, refer to Disconnecting the battery In the Reference Section of this manual for further information.
2 Electrical fault finding-general information
Note: Refer to the precautions given In Safety first! and in Section 1 of this Chapter before starting work. The following tests relate to testing ot the main electrical circuits, and should not be used to test delicate electronic circuits (such as antHock braking systems), particularly where an electronic con fro/ module is used.
General 1 A typical electrical circuit consists of an electrical component, any switches, relays, motors, fuses, fusible links or circuit breakers related to that component, and the wiring and connectors which link the component to both the battery and the chassis. To help to pinpoint a problem in an electrical circuit, wiring diagrams are Included at the end of this manual. 2 Before attempting to diagnose an electrical fault, first study the appropriate wiring diagram, to obtain a more complete understanding of the components included In the particular circuit concerned. The possible sources of a fault can be narrowed down by noting whether other components related to the circuit are operating properly. If several components or circuits fait at one time, the problem Is likely to be related to a shared fuse or earth connection.
Page 216 of 225
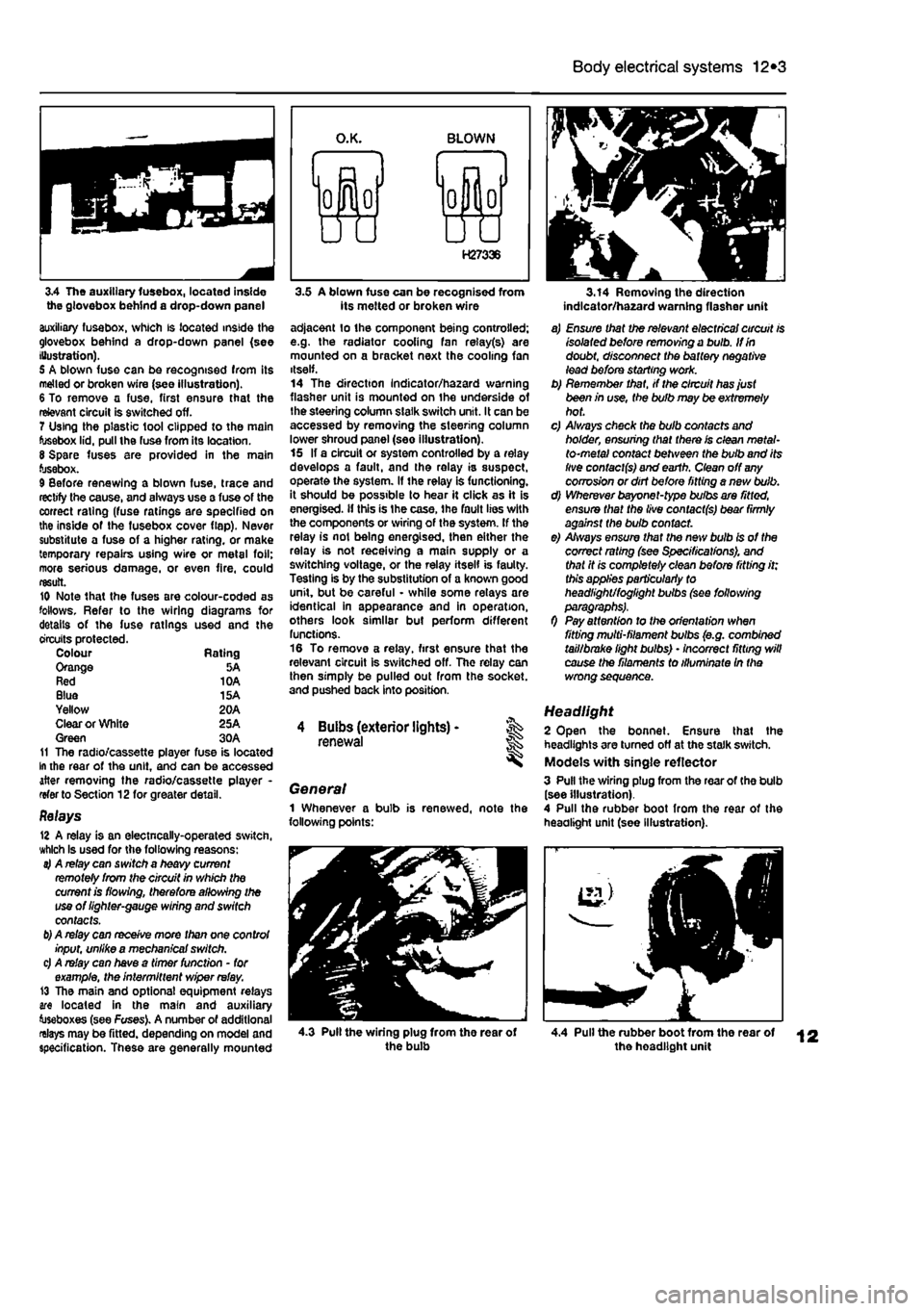
Body electrical systems 12*3
3.4 The auxiliary fusebox, located inside the glovebox behind a drop-down panel auxiliary fusebox, which is located inside the glovebox behind a drop-down panel (see Illustration). 5 A blown fuse can be recognised from its melted or broken wire (see illustration). 6 To remove a fuse, first ensure that the relevant circuit is switched off. 7 Using the plastic tool clipped to the main fusebox lid, pull the fuse from its location. 8 Spare fuses are provided in the main fusebox. 9 Before renewing a blown fuse, trace and rectify the cause, and always use a fuse of the correct rating (fuse ratings are specified on the inside of the fusebox cover flap). Never substitute a fuse of a higher rating, or make temporary repairs using wire or metal foil; more serious damage, or even fire, could result. 10 Note that the fuses are colour-coded as follows. Refer to the wiring diagrams for details of the fuse ratings used and the circuits protected. Colour Rating Orange 5A Red 10A Blue 15A Yellow 20A Clear or White 25A Green 30A 11 The radio/cassette player fuse is located In the rear of the unit, and can be accessed after removing the radio/cassette player -refer to Section 12for greater detail.
Relays 12 A relay is an electncally-operated switch, which Is used for the following reasons: 4 A relay can switch a heavy current remotely from the circuit in which the current is flowing, therefore allowing the use of lighter-gauge wiring and switch contacts.
b)
A relay can receive more than one control input, unlike a mechanical switch. c) A relay can have a timer function - for example, the intermittent wiper relay. 13 The main and optional equipment relays are located in the main and auxiliary toseboxes (see Fuses). A number of additional relays may be fitted, depending on model and specification. These are generally mounted
3.5 A blown fuse can be recognised from its melted or broken wire adjacent lo the component being controlled; e.g. the radiator cooling fan relay(s) are mounted on a bracket next the cooling fan itself. 14 The direction Indicator/hazard warning flasher unit is mounted on the underside of the steering column slalk switch unit. It can be accessed by removing the steering column lower shroud panel (see illustration). 15 If a circuit or system controlled by a relay develops a fault, and the relay is suspect, operate the system. If the relay is functioning, it should be possible to hear it click as it is energised, if this is Ihe case, the fault lies with the components or wiring of the system. If the relay is not being energised, then either the relay is not receiving a main supply or a switching voltage, or the relay itself is faulty. Testing is by the substitution of a known good unit, but be careful - while some relays are identical in appearance and in operation, others look similar but perform different functions. 16 To remove a relay, first ensure that the relevant circuit is switched off. The relay can then simply be pulled out from the socket, and pushed back into position.
4 Buibs (exterior lights) -renewal
General 1 Whenever a bulb is renewed, note the following points:
3.14 Removing the direction indlcator/ha2ard warning flasher unit
a) Ensure that the relevant electrical circuit is isolated before removing a bulb. If in doubt, disconnect the battery negative lead before starting work. b) Remember that, if the circuit has just been in use, the bulb may be extremely hot. c) A/ways check the bulb contacts and holder, ensuring that there is clean metal-to-metal contact between the bulb and its live contacts) and earth. Clean off
any
corrosion or dirt before fitting a nevt bulb. d) Wherever bayonet-type bulbs are fitted, ensure that the live contacts) bear firmly against the bulb contact. e) Always ensure that the new bulb is of the correct rating (see Specifications), and that it is completely clean before fitting it; this applies particularly to headlight/foglight bulbs (see following
0 Pay attention to the orientation when fitting multi-filament bulbs (e.g. combined tail/brake light bulbs) • incorrect fitting will cause the filaments to illuminate In the wrong sequence.
Headlight 2 Open the bonnet. Ensure that the headlights are turned off at the stalk switch. Models with single reflector 3 Pull the wiring plug from the rear of the bulb (see illustration). 4 Pull the rubber boot from the rear of the headlight unit (see Illustration).
4.3 Pull the wiring plug from the rear of the bulb 4.4 Pull the rubber boot from the rear of the headlight unit
Page 217 of 225
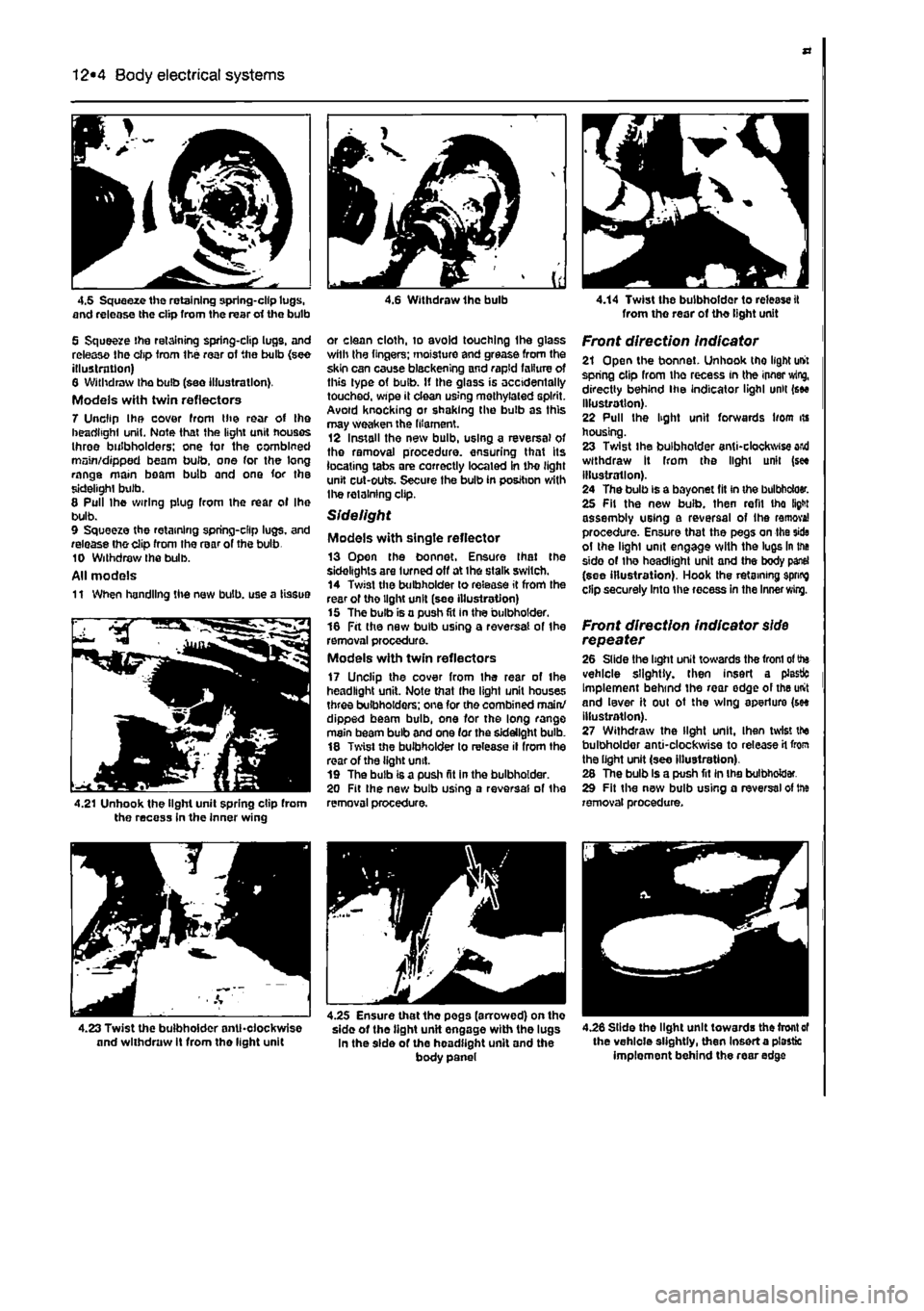
12*4 Body electrical systems
4.5 Squeeze the retaining spring-clip lugs, and release the clip from the rear erf the bulb
5 Squeeze the retaining spring-clip lugs, and release Ihe clip Irom the rear of the bulb {see illustration) 6 Withdraw the bulb (see illustration). Models with twin reflectors 7 Unclip Ihe cover from the rear of the headlight unit. Note that the light unit houses three bulbholders; one tor the combined main/dipped beam bulb, one for the long range main beam bulb and one for the sidelight bulb. 8 Pull Ihe wiring plug from the rear ol Ihe bulb. 9 Squeeze the retaining spring-clip lugs, and release tho clip from the rear of the bulb 10 Withdraw Ihe bulb. All models 11 When handling the new bulb, use a tissue
4.21 Unhook the light unit spring clip from the recess in the inner wing
4 6 Withdraw Ihe bulb
or clean cloth, to avoid touching Ihe glass wilh Ihe lingers; moisture and grease from the skin can cause blackening and rapid failure of this type of bulb. If the glass is accidentally touched, wipe it clean using methylated spirit. Avoid knocking or shaking the bulb as this may weaken the filament. 12 Install the new bulb, using a reversal of the removal procedure, ensuring that its locating tabs are correctly located in tho light unit cut-outs. Secure the bulb in position with Ihe retaining clip.
Sidelight
Models with single reflector 13 Open the bonnet. Ensure Ihat the sidelights are turned off at ihe stalk switch. 14 Twist the bulbholder lo release it from the rear of tho light unit (see illustration) 15 The bulb is a push fit in the bulbholder. 16 Fit the new bulb using a reversal of the removal procedure. Models with twin reflectors 17 Unclip the cover from Ihe rear of Ihe headlight unit. Note that Ihe light unit houses three bulbholders; one for the combined main/ dipped beam bulb, one for the long range main beam bulb and one (or the sidelight bulb. 18 Twist the bulbholder to release il from the rear of the light unit. 19 The bulb is a push fit in the bulbholder. 20 Fit Ihe new bulb using a reversal of the removal procedure.
4.14 Twist the bulbholder to release it from tho rear of tho light unit
Front direction indicator 21 Open the bonnet. Unhook tho light unit spring clip from the recess in the innsr wing, directly behind ihe indicator lighl unit (see illustration). 22 Pull the light unit forwards liom its housing. 23 Twist ihe bulbholder anti-clockwise and withdraw It from the light unit (see illustration). 24 The bulb is a bayonet fit in the bulbbdoer. 25 Fit the new bulb, then refil tho fight assembly using a reversal of Ihe remove! procedure. Ensure that the pegs on the side ol the lighl unit engage with the lugs in the side of the headlight unit and the body panel (see illustration). Hook the retaining spring clip securely Into the recess in the Inner
wing.
Front direction indicator
side
repeater 26 Slide the light unit towards the from
ol
the vehicle slightly, then insert a plastic Implement behind the rear edge of the unit and lever it oul ot the wing aperture (see illustration). 27 Withdraw the light unit. Ihen twist the bulbholder anti-clockwise to release
H
from the light unit (see illustration). 28 The bulb is a push fit in the bulbholder. 29 Fit the new bulb using a reversal of trie removal procedure.
4.26 Slide the light unit towards the front
of
the vehicle slightly, then Insert a plastic implement behind the rear edge
4.23 Twist the bulbholder anticlockwise and withdraw It from the light unit
4.25 Ensure that the pegs (arrowed) on tho sido of tho tight unit engage with the lugs In the side of the headlight unit and the body panel
Page 220 of 225
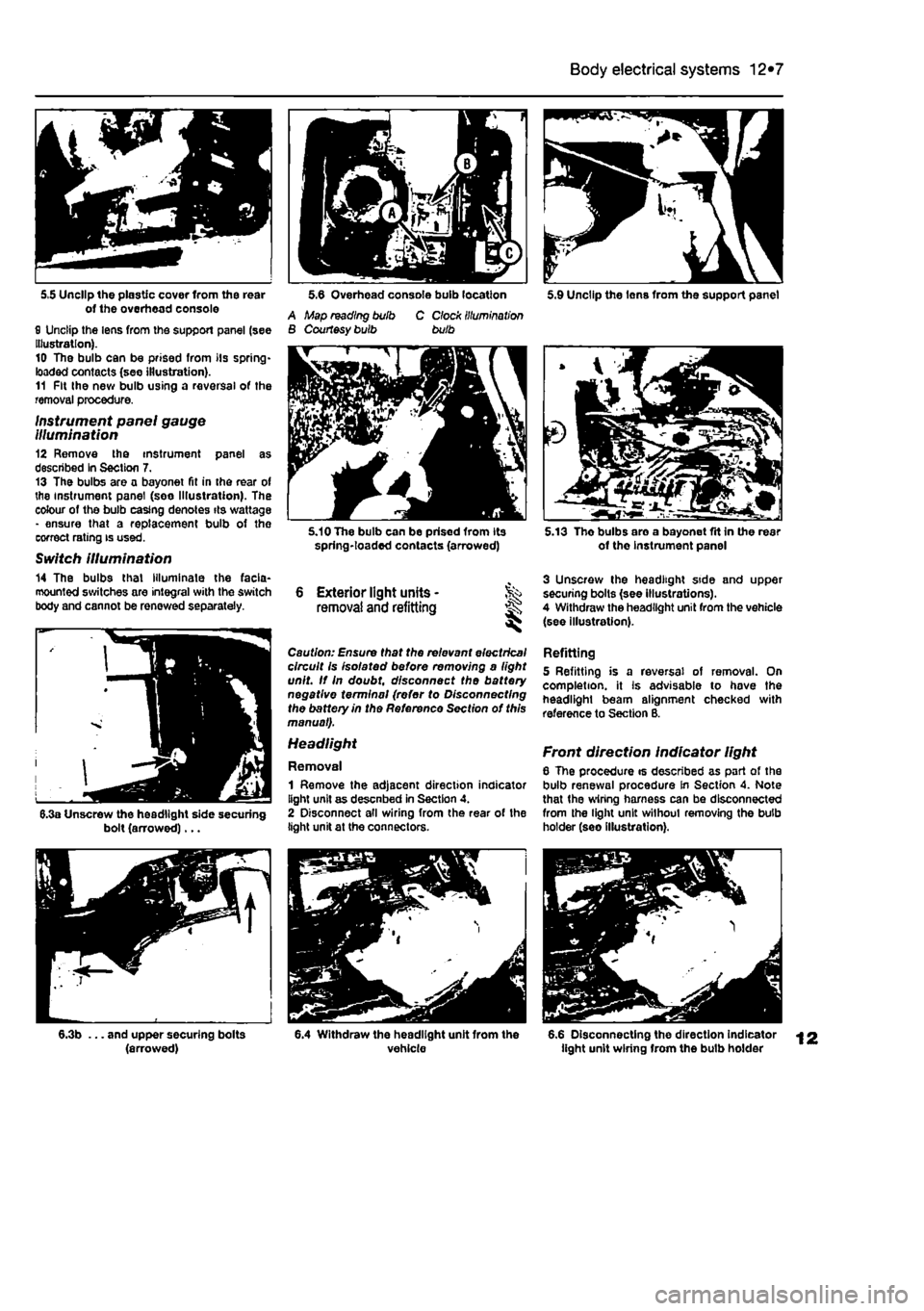
Body electrical systems 12*7
5,5 Unclip the plastic cover from the rear of the overhead console 0 Unclip the lens from the support panel (see Illustration). 10 The bulb can be prised from its spring-loaded contacts (see illustration). 11 Fit the new bulb using a reversal of the removal procedure.
Instrument panel gauge Illumination 12 Remove the instrument panel as described In Section 7. 13 The bulbs are a bayonet fit in the rear of the instrument panel (see Illustration). The colour of the bulb casing denotes its wattage - ensure that a replacement bulb of the correct rating is used.
Switch illumination 14 The bulbs that Illuminate the facia-mounted switches are integral with the switch body and cannot be renewed separately.
5.6 Overhead console bulb location 5.9 Unclip the Ions from the support panel A Map reading bulb B Courtesy bulb C Clock illumination bulb
6.3a Unscrew the headlight side securing bolt (arrowed)...
5.10 The bulb can be prised from its spring-loaded contacts (arrowed)
6 Exterior light units • removal and refitting ^ ^
Caution: Ensure that the relevant electrical circuit is isolated be/ore removing a light unit. If In doubt, disconnect the battery negative terminal (refer to Disconnecting the battery in the Reference Section of this manual).
1 Remove the adjacent direction indicator light unit as descnbed in Section 4. 2 Disconnect all wiring from the rear of the light unit at the connectors.
5.13 Tho bulbs are a bayonet fit in the rear of the instrument panel
3 Unscrew the headlight side and upper securing bolts (see illustrations). 4 Withdraw the headlight unit from the vehicle (see illustration).
Refitting 5 Refitting is a reversal of removal. On completion, it Is advisable to hove the headlight beam alignment checked with reference to Section B.
Front direction indicator light 6 The procedure is described as part of the bulb renewal procedure In Section 4. Note that the wiring harness can be disconnected from the light unit without removing the bulb holder (seo illustration).
6.3b ... and upper securing bolts (arrowed) 6.4 Withdraw the headlight unit from the vehicle 6.6 Disconnecting the direction indicator light unit wiring from the bulb holder
Page 221 of 225
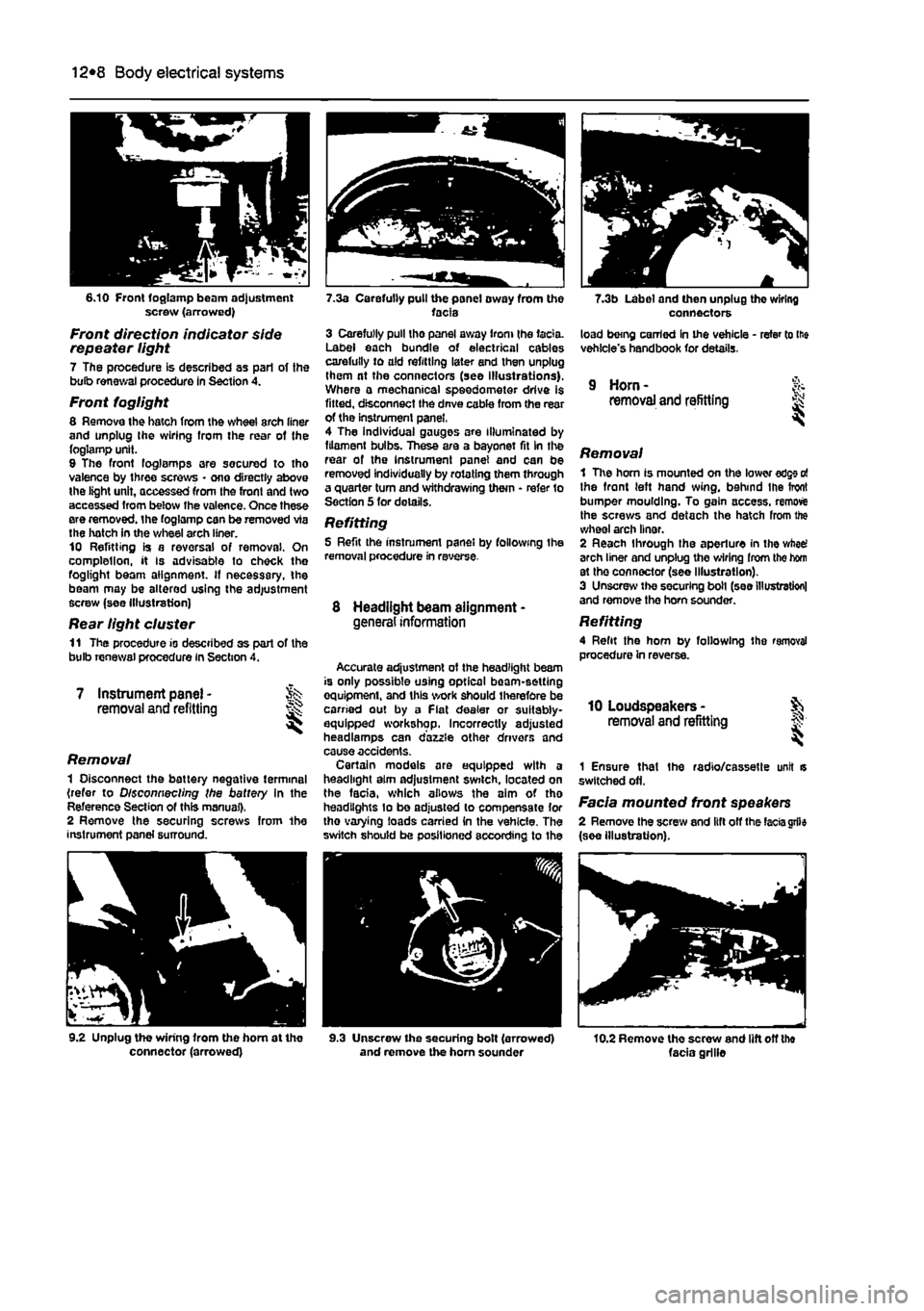
12*8 Body electrical systems
6.10 Front foglamp beam adjustment screw (arrowed)
Front direction indicator side repeater light 7 The procedure is described as pari of the bulb renewal procedure In Section 4.
Front foglight 8 Remove the hatch from the wheel arch liner and unplug Ihe wiring Irom the rear of the foglamp unit. 9 The front foglamps are secured to tho valence by three screws • one directly above the light unit, accessed from the front and two accessed Irom below the valence. Once these ere removed, the foglamp can be removed via the hatch in the wheel arch liner. 10 Refitting is a reversal of removal. On complellon, it Is advisable to check the foglight beam alignment. If necessary, the beam may be altered using the adjustment screw (see Illustration)
Rear light cluster 11 The procedure is described as part of the bulb renewal procedure in Section 4.
7 Instrument panel -removal and refitting
Removal 1 Disconnect the battery negative terminal (refer to Disconnecting the battery in the Reference Section of this manual). 2 Remove the securing screws from 1he instrument panel surround.
9.2 Unplug the wiring from the hom at tho connector (arrowed)
7.3a Carefully pull the panel oway from the facia 3 Carefully pull tho panel away from (he facia. Label each bundle of electrical cables carefully to old refitting later end then unplug them nt the connectors (see illustrations). Where a mechanical speedometer drive is fitted, disconnect the dnve coble from the rear of the instrument panel, 4 The individual gauges are Illuminated by filament bulbs. These are a bayonet fit In the rear of the Instrument panel and can be removed individually by rotating them through a quarter turn and withdrawing them • refer to Section 5 for details.
Refitting 5 Refit the instrument panel by following the removal procedure in reverse
8 Headlight beam alignment -general information
Accurate adjustment ot the headlight beam is only possible using optical beam-setting equipment, and this work should therefore be carried out by a Fiat dealer or suitably-equipped workshop. Incorrectly adjusted headlamps can dazzle other drivers and cause accidents. Certain models are equipped with a headlight aim adjustment switch, located on the facia, which allows the aim of tho headlights lo be adjusted to compensate lor tho varying loads carried in the vehicle. The switch should be positioned according to Ihe
9.3 Unscrew the securing bolt (arrowed) and remove the horn sounder
7.3b Label and then unplug the wiring connectors load being carried in the vehicle - refer to lie vehicle's handbook for details.
9 Horn -removal and refitting
Removal 1 The horn is mounted on the lower edge o! the front left hand wing, behind Ihe front bumper moulding. To gain access, remove the screws and detach the hatch from the wheel arch linor. 2 Reach through the aperture in the wheel arch liner and unplug the wiring Irom the hom st the connector (see Illustration). 3 Unscrew the securing boll (see Illustration) and remove the horn sounder.
Refitting 4 Refit the hom by following the removal procedure in reverse.
10 Loudspeakers -removal and refitting §;
1 Ensure that the radio/cassette unit is switched off.
Facia mounted front speakers 2 Remove the screw and lift off the
facia
grfle (see illustration).
10.2 Remove tho screw and lift off the facia grille