spark plugs replace FIAT UNO 1983 Service Repair Manual
[x] Cancel search | Manufacturer: FIAT, Model Year: 1983, Model line: UNO, Model: FIAT UNO 1983Pages: 303, PDF Size: 10.36 MB
Page 79 of 303
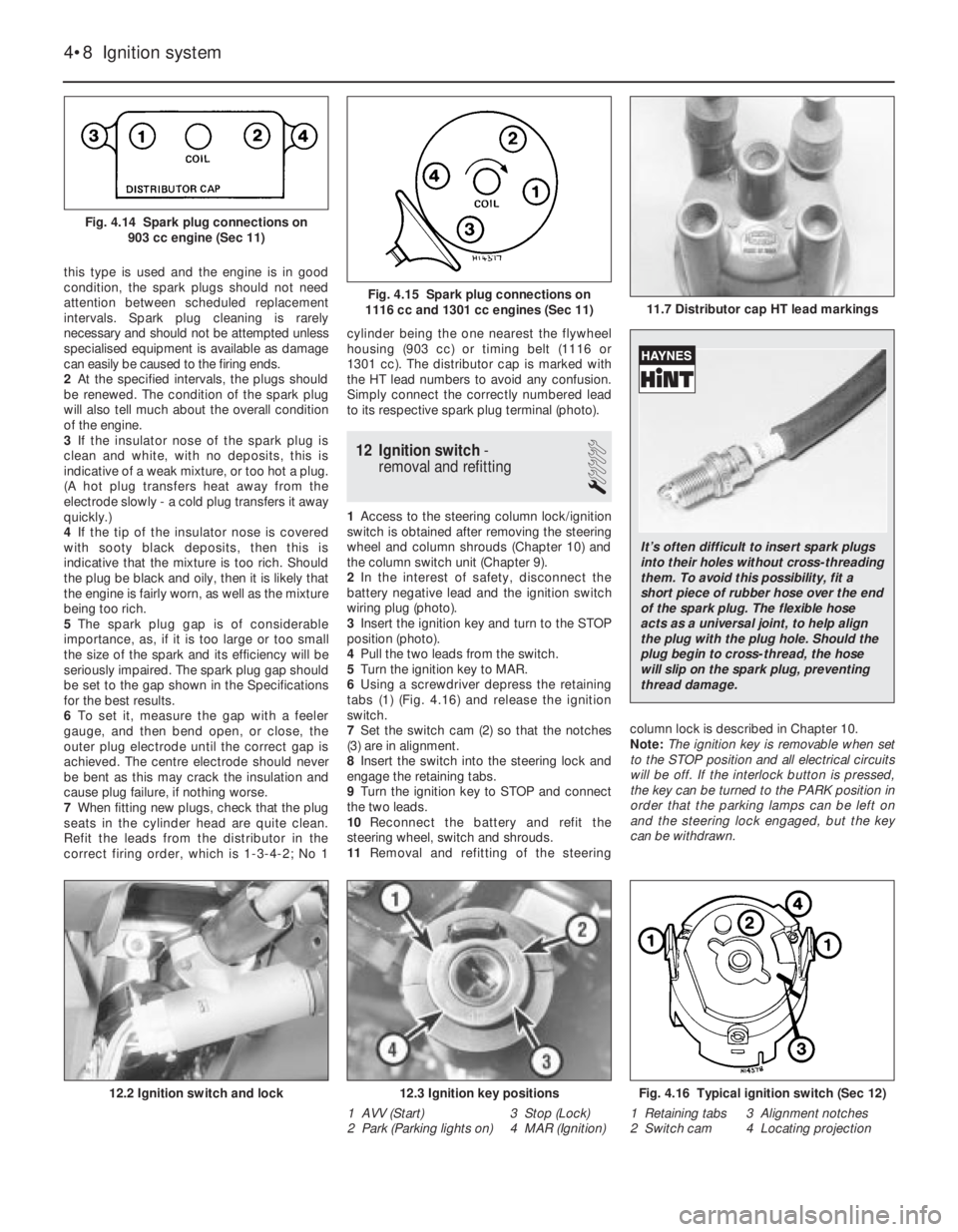
this type is used and the engine is in good
condition, the spark plugs should not need
attention between scheduled replacement
intervals. Spark plug cleaning is rarely
necessary and should not be attempted unless
specialised equipment is available as damage
can easily be caused to the firing ends.
2At the specified intervals, the plugs should
be renewed. The condition of the spark plug
will also tell much about the overall condition
of the engine.
3If the insulator nose of the spark plug is
clean and white, with no deposits, this is
indicative of a weak mixture, or too hot a plug.
(A hot plug transfers heat away from the
electrode slowly - a cold plug transfers it away
quickly.)
4If the tip of the insulator nose is covered
with sooty black deposits, then this is
indicative that the mixture is too rich. Should
the plug be black and oily, then it is likely that
the engine is fairly worn, as well as the mixture
being too rich.
5The spark plug gap is of considerable
importance, as, if it is too large or too small
the size of the spark and its efficiency will be
seriously impaired. The spark plug gap should
be set to the gap shown in the Specifications
for the best results.
6To set it, measure the gap with a feeler
gauge, and then bend open, or close, the
outer plug electrode until the correct gap is
achieved. The centre electrode should never
be bent as this may crack the insulation and
cause plug failure, if nothing worse.
7When fitting new plugs, check that the plug
seats in the cylinder head are quite clean.
Refit the leads from the distributor in the
correct firing order, which is 1-3-4-2; No 1cylinder being the one nearest the flywheel
housing (903 cc) or timing belt (1116 or
1301 cc). The distributor cap is marked with
the HT lead numbers to avoid any confusion.
Simply connect the correctly numbered lead
to its respective spark plug terminal (photo).
12 Ignition switch-
removal and refitting
1
1Access to the steering column lock/ignition
switch is obtained after removing the steering
wheel and column shrouds (Chapter 10) and
the column switch unit (Chapter 9).
2In the interest of safety, disconnect the
battery negative lead and the ignition switch
wiring plug (photo).
3Insert the ignition key and turn to the STOP
position (photo).
4Pull the two leads from the switch.
5Turn the ignition key to MAR.
6Using a screwdriver depress the retaining
tabs (1) (Fig. 4.16) and release the ignition
switch.
7Set the switch cam (2) so that the notches
(3) are in alignment.
8Insert the switch into the steering lock and
engage the retaining tabs.
9Turn the ignition key to STOP and connect
the two leads.
10Reconnect the battery and refit the
steering wheel, switch and shrouds.
11Removal and refitting of the steeringcolumn lock is described in Chapter 10.
Note: The ignition key is removable when set
to the STOP position and all electrical circuits
will be off. If the interlock button is pressed,
the key can be turned to the PARK position in
order that the parking lamps can be left on
and the steering lock engaged, but the key
can be withdrawn.
4•8 Ignition system
Fig. 4.16 Typical ignition switch (Sec 12)
1 Retaining tabs 3 Alignment notches
2 Switch cam 4 Locating projection12.3 Ignition key positions
1 AVV (Start) 3 Stop (Lock)
2 Park (Parking lights on) 4 MAR (Ignition)12.2 Ignition switch and lock
11.7 Distributor cap HT lead markingsFig. 4.15 Spark plug connections on
1116 cc and 1301 cc engines (Sec 11)
Fig. 4.14 Spark plug connections on
903 cc engine (Sec 11)
It’s often difficult to insert spark plugs
into their holes without cross-threading
them. To avoid this possibility, fit a
short piece of rubber hose over the end
of the spark plug. The flexible hose
acts as a universal joint, to help align
the plug with the plug hole. Should the
plug begin to cross-thread, the hose
will slip on the spark plug, preventing
thread damage.
Page 292 of 303
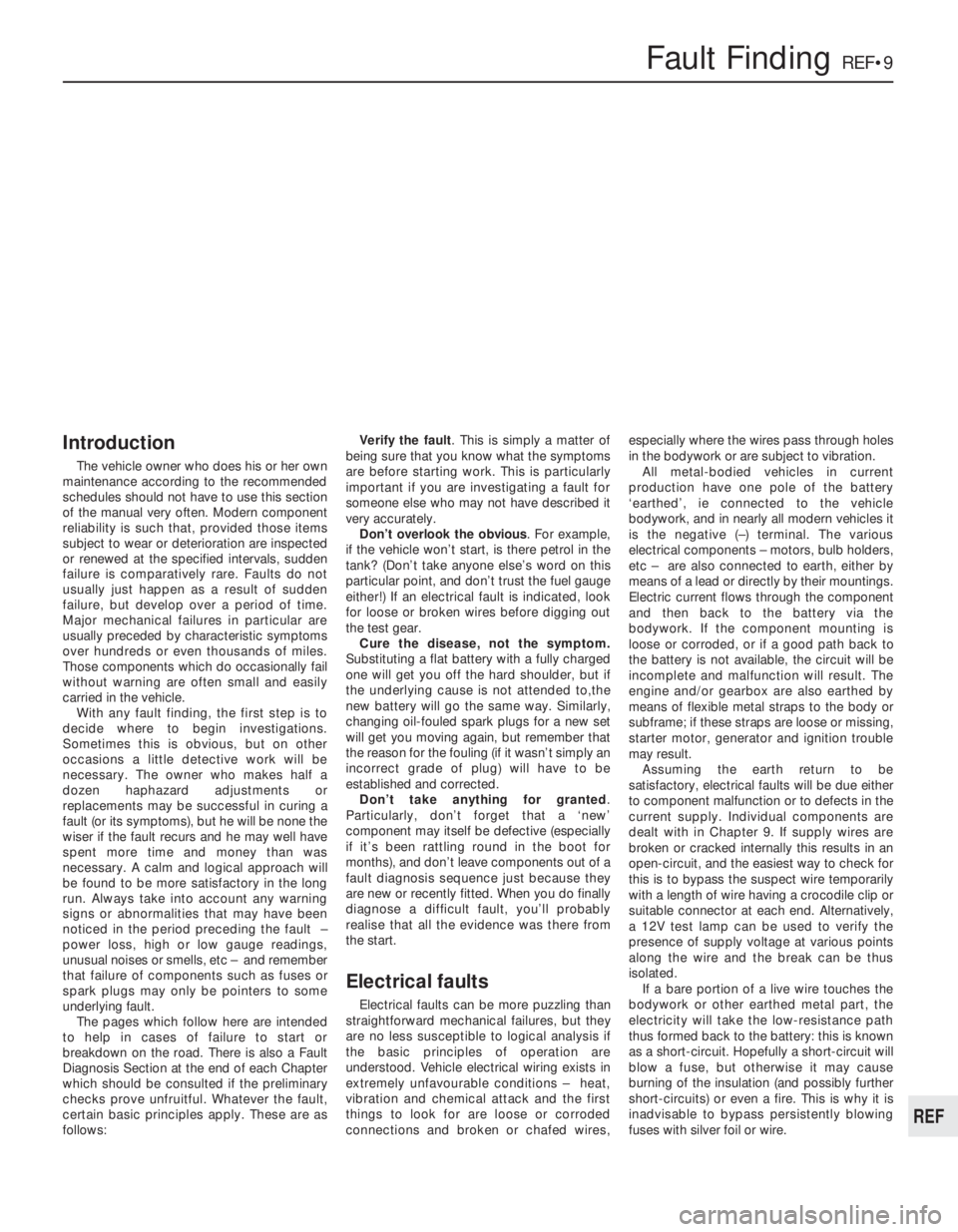
Fault FindingREF•9
REF
Introduction
The vehicle owner who does his or her own
maintenance according to the recommended
schedules should not have to use this section
of the manual very often. Modern component
reliability is such that, provided those items
subject to wear or deterioration are inspected
or renewed at the specified intervals, sudden
failure is comparatively rare. Faults do not
usually just happen as a result of sudden
failure, but develop over a period of time.
Major mechanical failures in particular are
usually preceded by characteristic symptoms
over hundreds or even thousands of miles.
Those components which do occasionally fail
without warning are often small and easily
carried in the vehicle.
With any fault finding, the first step is to
decide where to begin investigations.
Sometimes this is obvious, but on other
occasions a little detective work will be
necessary. The owner who makes half a
dozen haphazard adjustments or
replacements may be successful in curing a
fault (or its symptoms), but he will be none the
wiser if the fault recurs and he may well have
spent more time and money than was
necessary. A calm and logical approach will
be found to be more satisfactory in the long
run. Always take into account any warning
signs or abnormalities that may have been
noticed in the period preceding the fault –
power loss, high or low gauge readings,
unusual noises or smells, etc – and remember
that failure of components such as fuses or
spark plugs may only be pointers to some
underlying fault.
The pages which follow here are intended
to help in cases of failure to start or
breakdown on the road. There is also a Fault
Diagnosis Section at the end of each Chapter
which should be consulted if the preliminary
checks prove unfruitful. Whatever the fault,
certain basic principles apply. These are as
follows:Verify the fault. This is simply a matter of
being sure that you know what the symptoms
are before starting work. This is particularly
important if you are investigating a fault for
someone else who may not have described it
very accurately.
Don’t overlook the obvious. For example,
if the vehicle won’t start, is there petrol in the
tank? (Don’t take anyone else’s word on this
particular point, and don’t trust the fuel gauge
either!) If an electrical fault is indicated, look
for loose or broken wires before digging out
the test gear.
Cure the disease, not the symptom.
Substituting a flat battery with a fully charged
one will get you off the hard shoulder, but if
the underlying cause is not attended to,the
new battery will go the same way. Similarly,
changing oil-fouled spark plugs for a new set
will get you moving again, but remember that
the reason for the fouling (if it wasn’t simply an
incorrect grade of plug) will have to be
established and corrected.
Don’t take anything for granted.
Particularly, don’t forget that a ‘new’
component may itself be defective (especially
if it’s been rattling round in the boot for
months), and don’t leave components out of a
fault diagnosis sequence just because they
are new or recently fitted. When you do finally
diagnose a difficult fault, you’ll probably
realise that all the evidence was there from
the start.
Electrical faults
Electrical faults can be more puzzling than
straightforward mechanical failures, but they
are no less susceptible to logical analysis if
the basic principles of operation are
understood. Vehicle electrical wiring exists in
extremely unfavourable conditions – heat,
vibration and chemical attack and the first
things to look for are loose or corroded
connections and broken or chafed wires,especially where the wires pass through holes
in the bodywork or are subject to vibration.
All metal-bodied vehicles in current
production have one pole of the battery
‘earthed’, ie connected to the vehicle
bodywork, and in nearly all modern vehicles it
is the negative (–) terminal. The various
electrical components – motors, bulb holders,
etc – are also connected to earth, either by
means of a lead or directly by their mountings.
Electric current flows through the component
and then back to the battery via the
bodywork. If the component mounting is
loose or corroded, or if a good path back to
the battery is not available, the circuit will be
incomplete and malfunction will result. The
engine and/or gearbox are also earthed by
means of flexible metal straps to the body or
subframe; if these straps are loose or missing,
starter motor, generator and ignition trouble
may result.
Assuming the earth return to be
satisfactory, electrical faults will be due either
to component malfunction or to defects in the
current supply. Individual components are
dealt with in Chapter 9. If supply wires are
broken or cracked internally this results in an
open-circuit, and the easiest way to check for
this is to bypass the suspect wire temporarily
with a length of wire having a crocodile clip or
suitable connector at each end. Alternatively,
a 12V test lamp can be used to verify the
presence of supply voltage at various points
along the wire and the break can be thus
isolated.
If a bare portion of a live wire touches the
bodywork or other earthed metal part, the
electricity will take the low-resistance path
thus formed back to the battery: this is known
as a short-circuit. Hopefully a short-circuit will
blow a fuse, but otherwise it may cause
burning of the insulation (and possibly further
short-circuits) or even a fire. This is why it is
inadvisable to bypass persistently blowing
fuses with silver foil or wire.