service FORD SIERRA 1982 1.G CVH Engines Workshop Manual
[x] Cancel search | Manufacturer: FORD, Model Year: 1982, Model line: SIERRA, Model: FORD SIERRA 1982 1.GPages: 24, PDF Size: 1.09 MB
Page 10 of 24
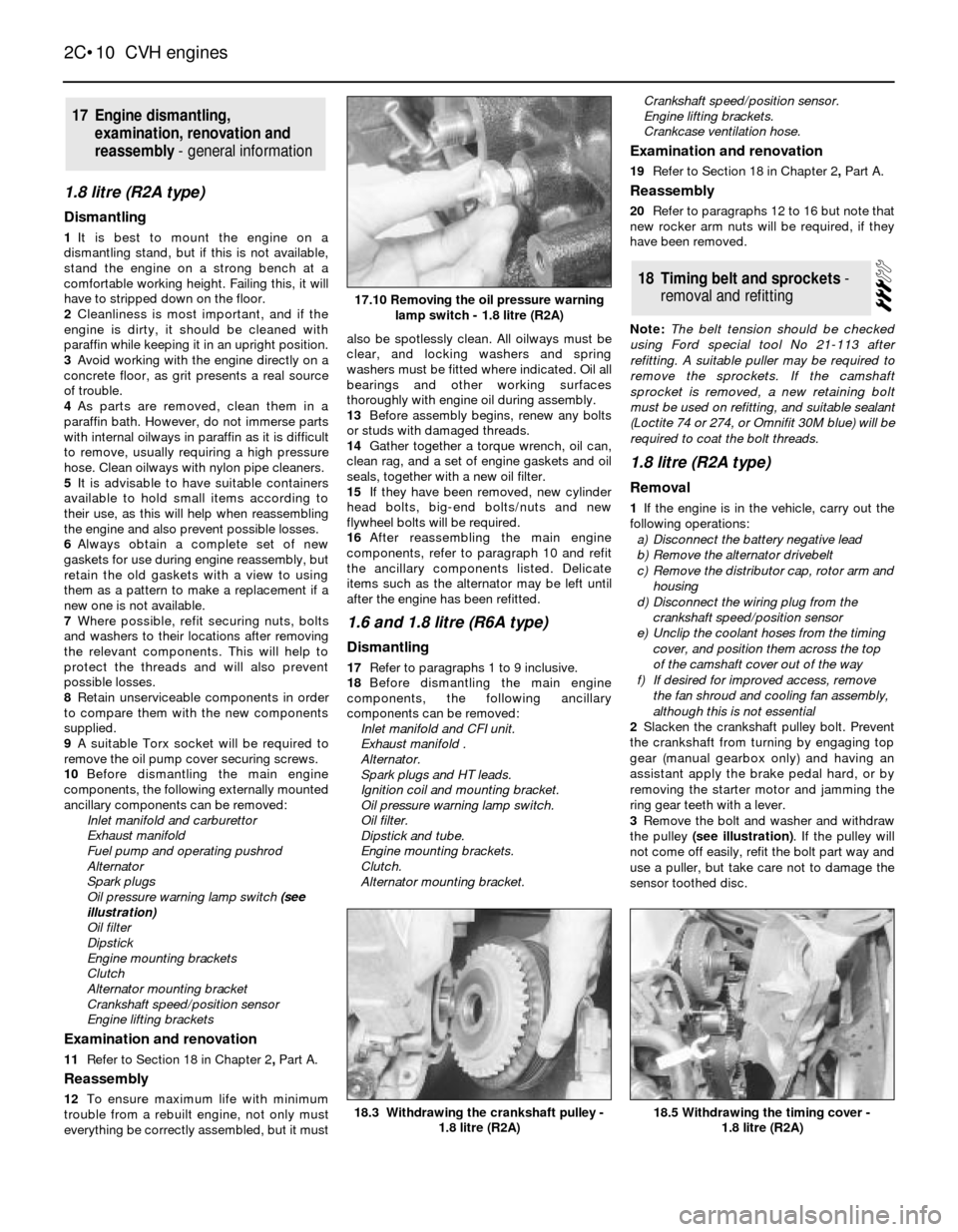
1.8 litre (R2A type)
Dismantling
1It is best to mount the engine on a
dismantling stand, but if this is not available,
stand the engine on a strong bench at a
comfortable working height. Failing this, it will
have to stripped down on the floor.
2Cleanliness is most important, and if the
engine is dirty, it should be cleaned with
paraffin while keeping it in an upright position.
3Avoid working with the engine directly on a
concrete floor, as grit presents a real source
of trouble.
4As parts are removed, clean them in a
paraffin bath. However, do not immerse parts
with internal oilways in paraffin as it is difficult
to remove, usually requiring a high pressure
hose. Clean oilways with nylon pipe cleaners.
5It is advisable to have suitable containers
available to hold small items according to
their use, as this will help when reassembling
the engine and also prevent possible losses.
6Always obtain a complete set of new
gaskets for use during engine reassembly, but
retain the old gaskets with a view to using
them as a pattern to make a replacement if a
new one is not available.
7Where possible, refit securing nuts, bolts
and washers to their locations after removing
the relevant components. This will help to
protect the threads and will also prevent
possible losses.
8Retain unserviceable components in order
to compare them with the new components
supplied.
9A suitable Torx socket will be required to
remove the oil pump cover securing screws.
10Before dismantling the main engine
components, the following externally mounted
ancillary components can be removed:
Inlet manifold and carburettor
Exhaust manifold
Fuel pump and operating pushrod
Alternator
Spark plugs
Oil pressure warning lamp switch (see
illustration)
Oil filter
Dipstick
Engine mounting brackets
Clutch
Alternator mounting bracket
Crankshaft speed/position sensor
Engine lifting brackets
Examination and renovation
11Refer to Section 18 in Chapter 2, PartA.
Reassembly
12To ensure maximum life with minimum
trouble from a rebuilt engine, not only must
everything be correctly assembled, but it mustalso be spotlessly clean. All oilways must be
clear, and locking washers and spring
washers must be fitted where indicated. Oil all
bearings and other working surfaces
thoroughly with engine oil during assembly.
13Before assembly begins, renew any bolts
or studs with damaged threads.
14Gather together a torque wrench, oil can,
clean rag, and a set of engine gaskets and oil
seals, together with a new oil filter.
15If they have been removed, new cylinder
head bolts, big-end bolts/nuts and new
flywheel bolts will be required.
16After reassembling the main engine
components, refer to paragraph 10 and refit
the ancillary components listed. Delicate
items such as the alternator may be left until
after the engine has been refitted.
1.6 and 1.8 litre (R6A type)
Dismantling
17Refer to paragraphs 1 to 9 inclusive.
18Before dismantling the main engine
components, the following ancillary
components can be removed:
Inlet manifold and CFI unit.
Exhaust manifold .
Alternator.
Spark plugs and HT leads.
Ignition coil and mounting bracket.
Oil pressure warning lamp switch.
Oil filter.
Dipstick and tube.
Engine mounting brackets.
Clutch.
Alternator mounting bracket.Crankshaft speed/position sensor.
Engine lifting brackets.
Crankcase ventilation hose.
Examination and renovation
19Refer to Section 18 in Chapter 2, PartA.
Reassembly
20Refer to paragraphs 12 to 16 but note that
new rocker arm nuts will be required, if they
have been removed.
Note: The belt tension should be checked
using Ford special tool No 21-113 after
refitting. A suitable puller may be required to
remove the sprockets. If the camshaft
sprocket is removed, a new retaining bolt
must be used on refitting, and suitable sealant
(Loctite 74 or 274, or Omnifit 30M blue) will be
required to coat the bolt threads.
1.8 litre (R2A type)
Removal
1If the engine is in the vehicle, carry out the
following operations:
a)Disconnect the battery negative lead
b)Remove the alternator drivebelt
c)Remove the distributor cap, rotor arm and
housing
d)Disconnect the wiring plug from the
crankshaft speed/position sensor
e)Unclip the coolant hoses from the timing
cover, and position them across the top
of the camshaft cover out of the way
f)If desired for improved access, remove
the fan shroud and cooling fan assembly,
although this is not essential
2Slacken the crankshaft pulley bolt. Prevent
the crankshaft from turning by engaging top
gear (manual gearbox only) and having an
assistant apply the brake pedal hard, or by
removing the starter motor and jamming the
ring gear teeth with a lever.
3Remove the bolt and washer and withdraw
the pulley (see illustration). If the pulley will
not come off easily, refit the bolt part way and
use a puller, but take care not to damage the
sensor toothed disc.
18Timing belt and sprockets -
removal and refitting
17Engine dismantling,
examination, renovation and
reassembly - general information
2C•10CVH engines
17.10 Removing the oil pressure warning
lamp switch - 1.8 litre (R2A)
18.5 Withdrawing the timing cover -
1.8 litre (R2A)18.3 Withdrawing the crankshaft pulley -
1.8 litre (R2A)
Page 21 of 24
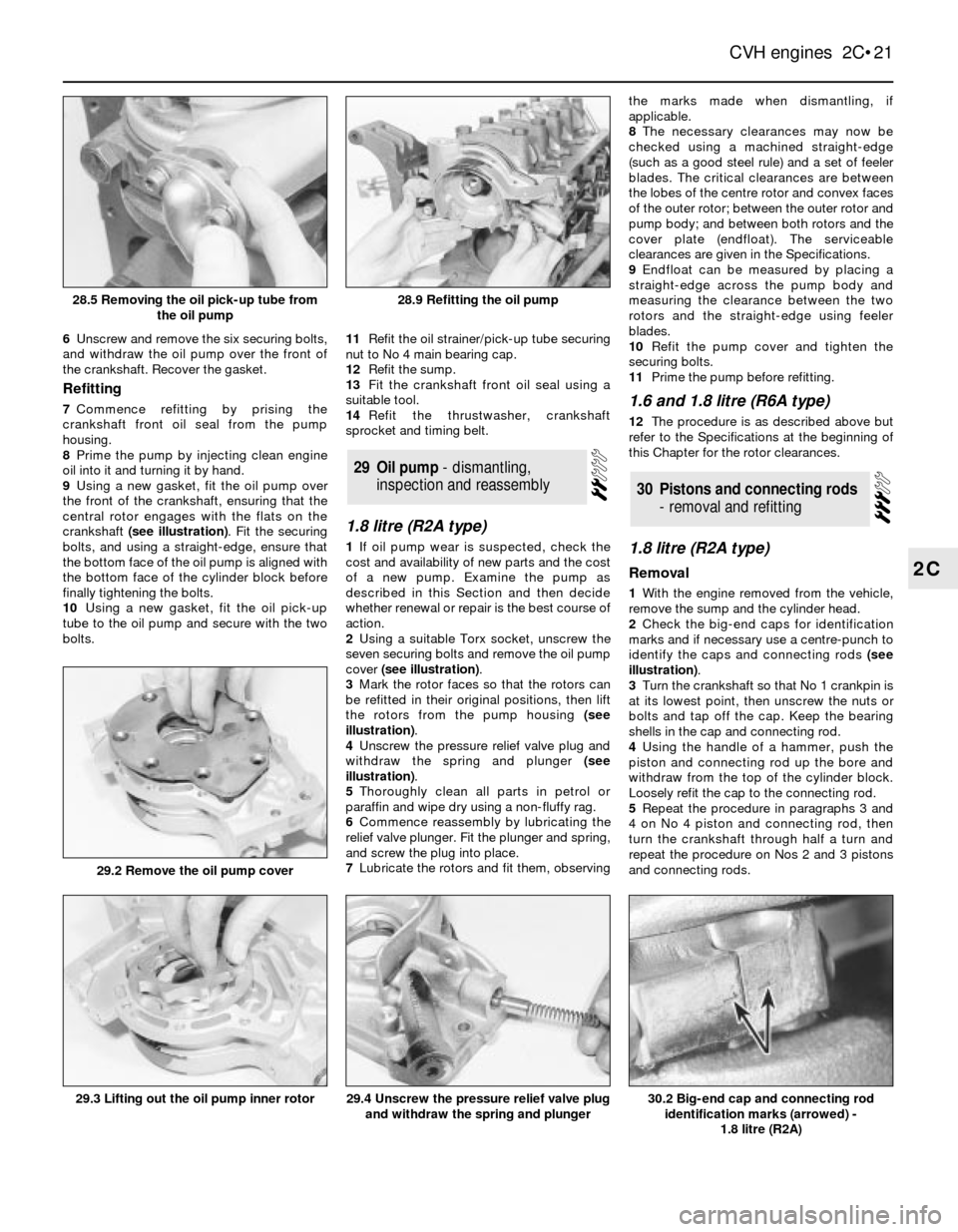
6Unscrew and remove the six securing bolts,
and withdraw the oil pump over the front of
the crankshaft. Recover the gasket.
Refitting
7Commence refitting by prising the
crankshaft front oil seal from the pump
housing.
8Prime the pump by injecting clean engine
oil into it and turning it by hand.
9Using a new gasket, fit the oil pump over
the front of the crankshaft, ensuring that the
central rotor engages with the flats on the
crankshaft (see illustration). Fit the securing
bolts, and using a straight-edge, ensure that
the bottom face of the oil pump is aligned with
the bottom face of the cylinder block before
finally tightening the bolts.
10Using a new gasket, fit the oil pick-up
tube to the oil pump and secure with the two
bolts.11Refit the oil strainer/pick-up tube securing
nut to No 4 main bearing cap.
12Refit the sump.
13Fit the crankshaft front oil seal using a
suitable tool.
14Refit the thrustwasher, crankshaft
sprocket and timing belt.
1.8 litre (R2A type)
1If oil pump wear is suspected, check the
cost and availability of new parts and the cost
of a new pump. Examine the pump as
described in this Section and then decide
whether renewal or repair is the best course of
action.
2Using a suitable Torx socket, unscrew the
seven securing bolts and remove the oil pump
cover (see illustration).
3Mark the rotor faces so that the rotors can
be refitted in their original positions, then lift
the rotors from the pump housing (see
illustration).
4Unscrew the pressure relief valve plug and
withdraw the spring and plunger (see
illustration).
5Thoroughly clean all parts in petrol or
paraffin and wipe dry using a non-fluffy rag.
6Commence reassembly by lubricating the
relief valve plunger. Fit the plunger and spring,
and screw the plug into place.
7Lubricate the rotors and fit them, observingthe marks made when dismantling, if
applicable.
8The necessary clearances may now be
checked using a machined straight-edge
(such as a good steel rule) and a set of feeler
blades. The critical clearances are between
the lobes of the centre rotor and convex faces
of the outer rotor; between the outer rotor and
pump body; and between both rotors and the
cover plate (endfloat). The serviceable
clearances are given in the Specifications.
9Endfloat can be measured by placing a
straight-edge across the pump body and
measuring the clearance between the two
rotors and the straight-edge using feeler
blades.
10Refit the pump cover and tighten the
securing bolts.
11Prime the pump before refitting.
1.6 and 1.8 litre (R6A type)
12The procedure is as described above but
refer to the Specifications at the beginning of
this Chapter for the rotor clearances.
1.8 litre (R2A type)
Removal
1With the engine removed from the vehicle,
remove the sump and the cylinder head.
2Check the big-end caps for identification
marks and if necessary use a centre-punch to
identify the caps and connecting rods (see
illustration).
3Turn the crankshaft so that No 1 crankpin is
at its lowest point, then unscrew the nuts or
bolts and tap off the cap. Keep the bearing
shells in the cap and connecting rod.
4Using the handle of a hammer, push the
piston and connecting rod up the bore and
withdraw from the top of the cylinder block.
Loosely refit the cap to the connecting rod.
5Repeat the procedure in paragraphs 3 and
4 on No 4 piston and connecting rod, then
turn the crankshaft through half a turn and
repeat the procedure on Nos 2 and 3 pistons
and connecting rods.
30Pistons and connecting rods
- removal and refitting
29Oil pump - dismantling,
inspection and reassembly
CVH engines 2C•21
2C
29.2 Remove the oil pump cover
30.2 Big-end cap and connecting rod
identification marks (arrowed) -
1.8 litre (R2A)29.4 Unscrew the pressure relief valve plug
and withdraw the spring and plunger29.3 Lifting out the oil pump inner rotor
28.9 Refitting the oil pump28.5 Removing the oil pick-up tube from
the oil pump