drain bolt FORD SIERRA 1982 1.G Reference Workshop Manual
[x] Cancel search | Manufacturer: FORD, Model Year: 1982, Model line: SIERRA, Model: FORD SIERRA 1982 1.GPages: 26, PDF Size: 0.57 MB
Page 4 of 26
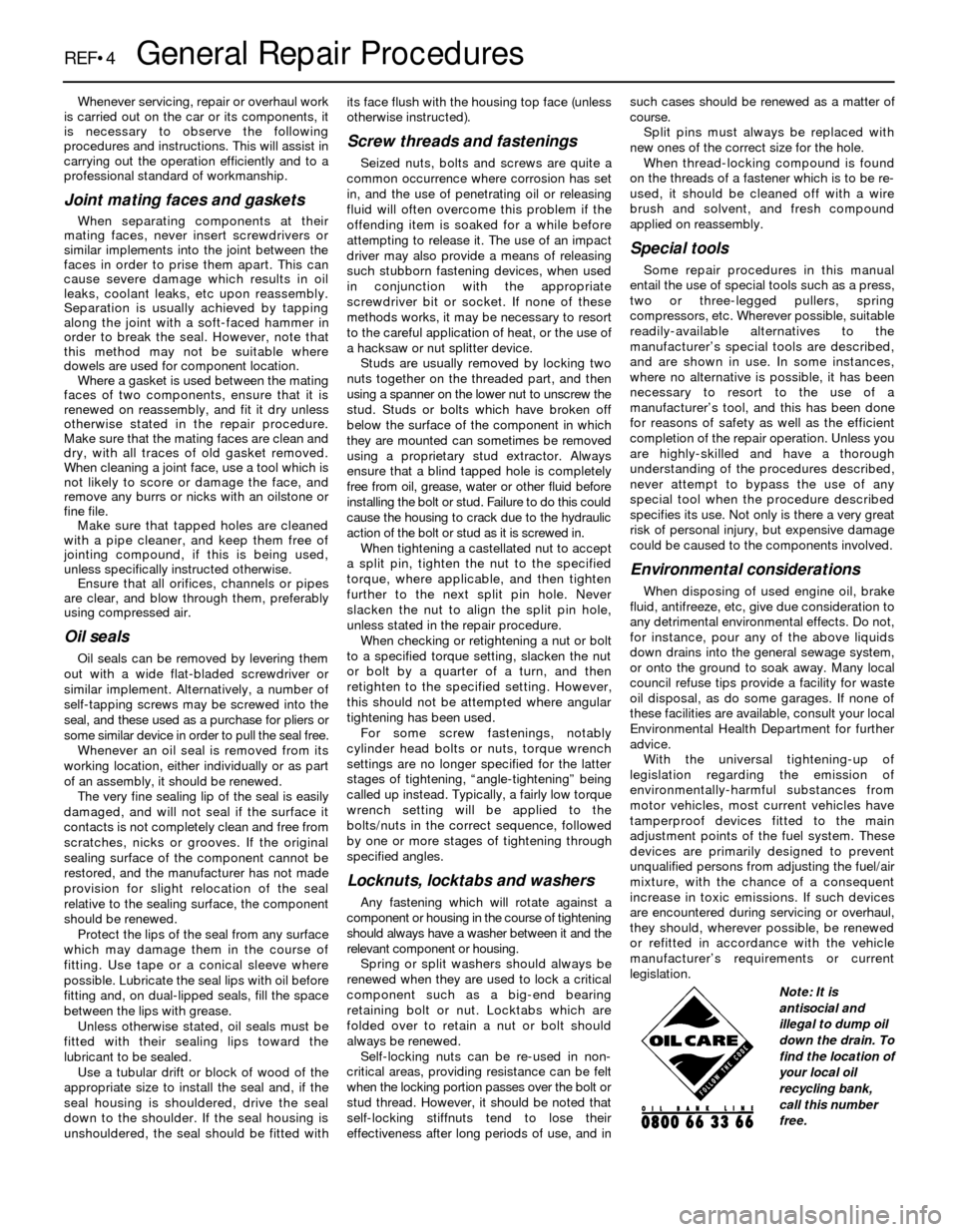
Whenever servicing, repair or overhaul work
is carried out on the car or its components, it
is necessary to observe the following
procedures and instructions. This will assist in
carrying out the operation efficiently and to a
professional standard of workmanship.
Joint mating faces and gaskets
When separating components at their
mating faces, never insert screwdrivers or
similar implements into the joint between the
faces in order to prise them apart. This can
cause severe damage which results in oil
leaks, coolant leaks, etc upon reassembly.
Separation is usually achieved by tapping
along the joint with a soft-faced hammer in
order to break the seal. However, note that
this method may not be suitable where
dowels are used for component location.
Where a gasket is used between the mating
faces of two components, ensure that it is
renewed on reassembly, and fit it dry unless
otherwise stated in the repair procedure.
Make sure that the mating faces are clean and
dry, with all traces of old gasket removed.
When cleaning a joint face, use a tool which is
not likely to score or damage the face, and
remove any burrs or nicks with an oilstone or
fine file.
Make sure that tapped holes are cleaned
with a pipe cleaner, and keep them free of
jointing compound, if this is being used,
unless specifically instructed otherwise.
Ensure that all orifices, channels or pipes
are clear, and blow through them, preferably
using compressed air.
Oil seals
Oil seals can be removed by levering them
out with a wide flat-bladed screwdriver or
similar implement. Alternatively, a number of
self-tapping screws may be screwed into the
seal, and these used as a purchase for pliers or
some similar device in order to pull the seal free.
Whenever an oil seal is removed from its
working location, either individually or as part
of an assembly, it should be renewed.
The very fine sealing lip of the seal is easily
damaged, and will not seal if the surface it
contacts is not completely clean and free from
scratches, nicks or grooves. If the original
sealing surface of the component cannot be
restored, and the manufacturer has not made
provision for slight relocation of the seal
relative to the sealing surface, the component
should be renewed.
Protect the lips of the seal from any surface
which may damage them in the course of
fitting. Use tape or a conical sleeve where
possible. Lubricate the seal lips with oil before
fitting and, on dual-lipped seals, fill the space
between the lips with grease.
Unless otherwise stated, oil seals must be
fitted with their sealing lips toward the
lubricant to be sealed.
Use a tubular drift or block of wood of the
appropriate size to install the seal and, if the
seal housing is shouldered, drive the seal
down to the shoulder. If the seal housing is
unshouldered, the seal should be fitted withits face flush with the housing top face (unless
otherwise instructed).
Screw threads and fastenings
Seized nuts, bolts and screws are quite a
common occurrence where corrosion has set
in, and the use of penetrating oil or releasing
fluid will often overcome this problem if the
offending item is soaked for a while before
attempting to release it. The use of an impact
driver may also provide a means of releasing
such stubborn fastening devices, when used
in conjunction with the appropriate
screwdriver bit or socket. If none of these
methods works, it may be necessary to resort
to the careful application of heat, or the use of
a hacksaw or nut splitter device.
Studs are usually removed by locking two
nuts together on the threaded part, and then
using a spanner on the lower nut to unscrew the
stud. Studs or bolts which have broken off
below the surface of the component in which
they are mounted can sometimes be removed
using a proprietary stud extractor. Always
ensure that a blind tapped hole is completely
free from oil, grease, water or other fluid before
installing the bolt or stud. Failure to do this could
cause the housing to crack due to the hydraulic
action of the bolt or stud as it is screwed in.
When tightening a castellated nut to accept
a split pin, tighten the nut to the specified
torque, where applicable, and then tighten
further to the next split pin hole. Never
slacken the nut to align the split pin hole,
unless stated in the repair procedure.
When checking or retightening a nut or bolt
to a specified torque setting, slacken the nut
or bolt by a quarter of a turn, and then
retighten to the specified setting. However,
this should not be attempted where angular
tightening has been used.
For some screw fastenings, notably
cylinder head bolts or nuts, torque wrench
settings are no longer specified for the latter
stages of tightening, “angle-tightening” being
called up instead. Typically, a fairly low torque
wrench setting will be applied to the
bolts/nuts in the correct sequence, followed
by one or more stages of tightening through
specified angles.
Locknuts, locktabs and washers
Any fastening which will rotate against a
component or housing in the course of tightening
should always have a washer between it and the
relevant component or housing.
Spring or split washers should always be
renewed when they are used to lock a critical
component such as a big-end bearing
retaining bolt or nut. Locktabs which are
folded over to retain a nut or bolt should
always be renewed.
Self-locking nuts can be re-used in non-
critical areas, providing resistance can be felt
when the locking portion passes over the bolt or
stud thread. However, it should be noted that
self-locking stiffnuts tend to lose their
effectiveness after long periods of use, and insuch cases should be renewed as a matter of
course.
Split pins must always be replaced with
new ones of the correct size for the hole.
When thread-locking compound is found
on the threads of a fastener which is to be re-
used, it should be cleaned off with a wire
brush and solvent, and fresh compound
applied on reassembly.
Special tools
Some repair procedures in this manual
entail the use of special tools such as a press,
two or three-legged pullers, spring
compressors, etc. Wherever possible, suitable
readily-available alternatives to the
manufacturer’s special tools are described,
and are shown in use. In some instances,
where no alternative is possible, it has been
necessary to resort to the use of a
manufacturer’s tool, and this has been done
for reasons of safety as well as the efficient
completion of the repair operation. Unless you
are highly-skilled and have a thorough
understanding of the procedures described,
never attempt to bypass the use of any
special tool when the procedure described
specifies its use. Not only is there a very great
risk of personal injury, but expensive damage
could be caused to the components involved.
Environmental considerations
When disposing of used engine oil, brake
fluid, antifreeze, etc, give due consideration to
any detrimental environmental effects. Do not,
for instance, pour any of the above liquids
down drains into the general sewage system,
or onto the ground to soak away. Many local
council refuse tips provide a facility for waste
oil disposal, as do some garages. If none of
these facilities are available, consult your local
Environmental Health Department for further
advice.
With the universal tightening-up of
legislation regarding the emission of
environmentally-harmful substances from
motor vehicles, most current vehicles have
tamperproof devices fitted to the main
adjustment points of the fuel system. These
devices are primarily designed to prevent
unqualified persons from adjusting the fuel/air
mixture, with the chance of a consequent
increase in toxic emissions. If such devices
are encountered during servicing or overhaul,
they should, wherever possible, be renewed
or refitted in accordance with the vehicle
manufacturer’s requirements or current
legislation.
REF•4General Repair Procedures
Note: It is
antisocial and
illegal to dump oil
down the drain. To
find the location of
your local oil
recycling bank,
call this number
free.
Page 16 of 26
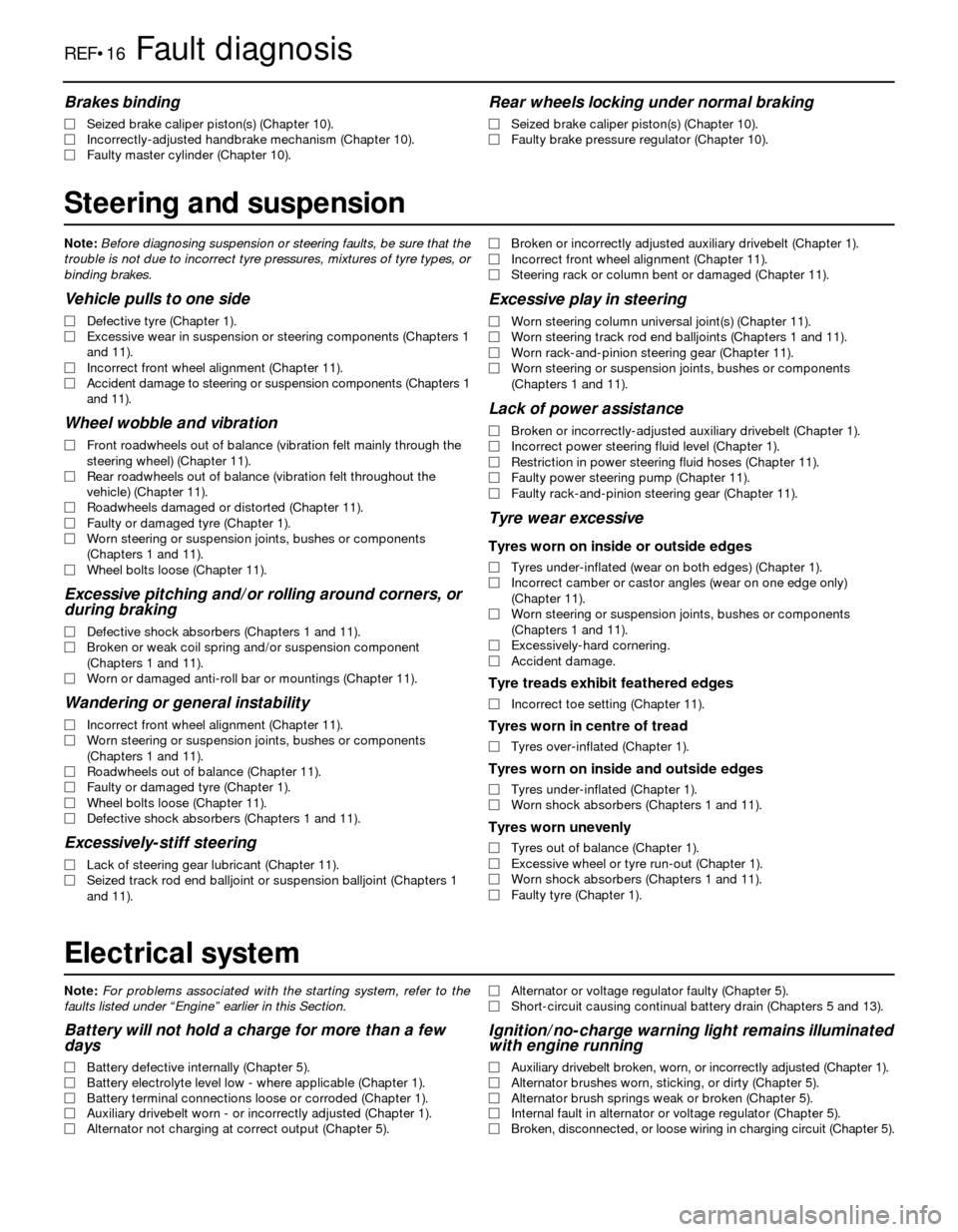
Brakes binding
MSeized brake caliper piston(s) (Chapter 10).
MIncorrectly-adjusted handbrake mechanism (Chapter 10).
MFaulty master cylinder (Chapter 10).
Rear wheels locking under normal braking
MSeized brake caliper piston(s) (Chapter 10).
MFaulty brake pressure regulator (Chapter 10).
Note:For problems associated with the starting system, refer to the
faults listed under “Engine” earlier in this Section.
Battery will not hold a charge for more than a few
days
MBattery defective internally (Chapter 5).
MBattery electrolyte level low - where applicable (Chapter 1).
MBattery terminal connections loose or corroded (Chapter 1).
MAuxiliary drivebelt worn - or incorrectly adjusted (Chapter 1).
MAlternator not charging at correct output (Chapter 5).MAlternator or voltage regulator faulty (Chapter 5).
MShort-circuit causing continual battery drain (Chapters 5 and 13).
Ignition/no-charge warning light remains illuminated
with engine running
MAuxiliary drivebelt broken, worn, or incorrectly adjusted (Chapter 1).
MAlternator brushes worn, sticking, or dirty (Chapter 5).
MAlternator brush springs weak or broken (Chapter 5).
MInternal fault in alternator or voltage regulator (Chapter 5).
MBroken, disconnected, or loose wiring in charging circuit (Chapter 5). Note:Before diagnosing suspension or steering faults, be sure that the
trouble is not due to incorrect tyre pressures, mixtures of tyre types, or
binding brakes.
Vehicle pulls to one side
MDefective tyre (Chapter 1).
MExcessive wear in suspension or steering components (Chapters 1
and 11).
MIncorrect front wheel alignment (Chapter 11).
MAccident damage to steering or suspension components (Chapters 1
and 11).
Wheel wobble and vibration
MFront roadwheels out of balance (vibration felt mainly through the
steering wheel) (Chapter 11).
MRear roadwheels out of balance (vibration felt throughout the
vehicle) (Chapter 11).
MRoadwheels damaged or distorted (Chapter 11).
MFaulty or damaged tyre (Chapter 1).
MWorn steering or suspension joints, bushes or components
(Chapters 1 and 11).
MWheel bolts loose (Chapter 11).
Excessive pitching and/or rolling around corners, or
during braking
MDefective shock absorbers (Chapters 1 and 11).
MBroken or weak coil spring and/or suspension component
(Chapters 1 and 11).
MWorn or damaged anti-roll bar or mountings (Chapter 11).
Wandering or general instability
MIncorrect front wheel alignment (Chapter 11).
MWorn steering or suspension joints, bushes or components
(Chapters 1 and 11).
MRoadwheels out of balance (Chapter 11).
MFaulty or damaged tyre (Chapter 1).
MWheel bolts loose (Chapter 11).
MDefective shock absorbers (Chapters 1 and 11).
Excessively-stiff steering
MLack of steering gear lubricant (Chapter 11).
MSeized track rod end balljoint or suspension balljoint (Chapters 1
and 11).MBroken or incorrectly adjusted auxiliary drivebelt (Chapter 1).
MIncorrect front wheel alignment (Chapter 11).
MSteering rack or column bent or damaged (Chapter 11).
Excessive play in steering
MWorn steering column universal joint(s) (Chapter 11).
MWorn steering track rod end balljoints (Chapters 1 and 11).
MWorn rack-and-pinion steering gear (Chapter 11).
MWorn steering or suspension joints, bushes or components
(Chapters 1 and 11).
Lack of power assistance
MBroken or incorrectly-adjusted auxiliary drivebelt (Chapter 1).
MIncorrect power steering fluid level (Chapter 1).
MRestriction in power steering fluid hoses (Chapter 11).
MFaulty power steering pump (Chapter 11).
MFaulty rack-and-pinion steering gear (Chapter 11).
Tyre wear excessive
Tyres worn on inside or outside edges
MTyres under-inflated (wear on both edges) (Chapter 1).
MIncorrect camber or castor angles (wear on one edge only)
(Chapter 11).
MWorn steering or suspension joints, bushes or components
(Chapters 1 and 11).
MExcessively-hard cornering.
MAccident damage.
Tyre treads exhibit feathered edges
MIncorrect toe setting (Chapter 11).
Tyres worn in centre of tread
MTyres over-inflated (Chapter 1).
Tyres worn on inside and outside edges
MTyres under-inflated (Chapter 1).
MWorn shock absorbers (Chapters 1 and 11).
Tyres worn unevenly
MTyres out of balance (Chapter 1).
MExcessive wheel or tyre run-out (Chapter 1).
MWorn shock absorbers (Chapters 1 and 11).
MFaulty tyre (Chapter 1).
REF•16Fault diagnosis
Steering and suspension
Electrical system