sensor FORD SIERRA 1985 1.G Routine Manintenance And Servicing Workshop Manual
[x] Cancel search | Manufacturer: FORD, Model Year: 1985, Model line: SIERRA, Model: FORD SIERRA 1985 1.GPages: 22, PDF Size: 1.26 MB
Page 6 of 22
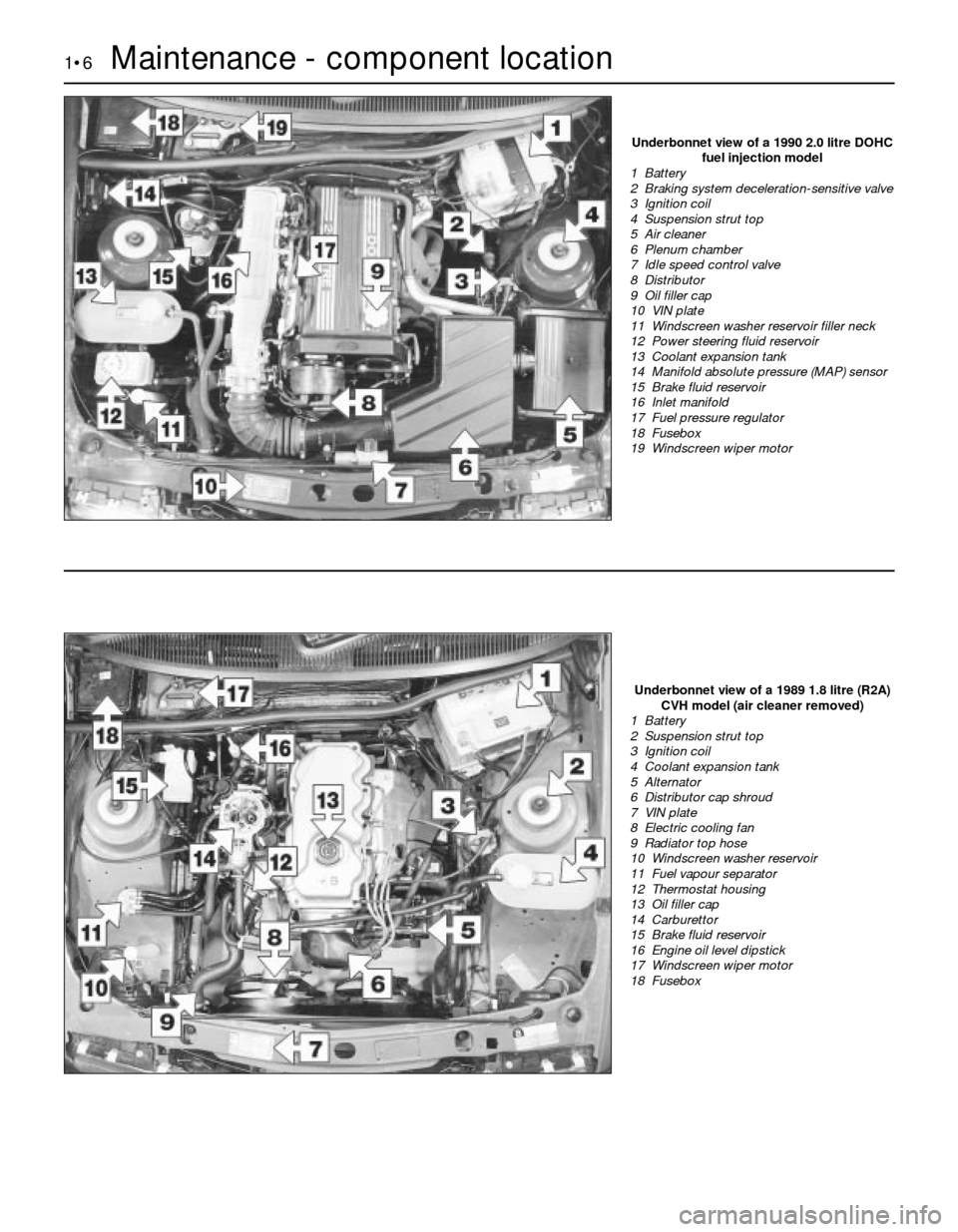
1•6Maintenance - component location
Underbonnet view of a 1990 2.0 litre DOHC
fuel injection model
1 Battery
2 Braking system deceleration-sensitive valve
3 Ignition coil
4 Suspension strut top
5 Air cleaner
6 Plenum chamber
7 Idle speed control valve
8 Distributor
9 Oil filler cap
10 VIN plate
11 Windscreen washer reservoir filler neck
12 Power steering fluid reservoir
13 Coolant expansion tank
14 Manifold absolute pressure (MAP) sensor
15 Brake fluid reservoir
16 Inlet manifold
17 Fuel pressure regulator
18 Fusebox
19 Windscreen wiper motor
Underbonnet view of a 1989 1.8 litre (R2A)
CVH model (air cleaner removed)
1 Battery
2 Suspension strut top
3 Ignition coil
4 Coolant expansion tank
5 Alternator
6 Distributor cap shroud
7 VIN plate
8 Electric cooling fan
9 Radiator top hose
10 Windscreen washer reservoir
11 Fuel vapour separator
12 Thermostat housing
13 Oil filler cap
14 Carburettor
15 Brake fluid reservoir
16 Engine oil level dipstick
17 Windscreen wiper motor
18 Fusebox
Page 7 of 22
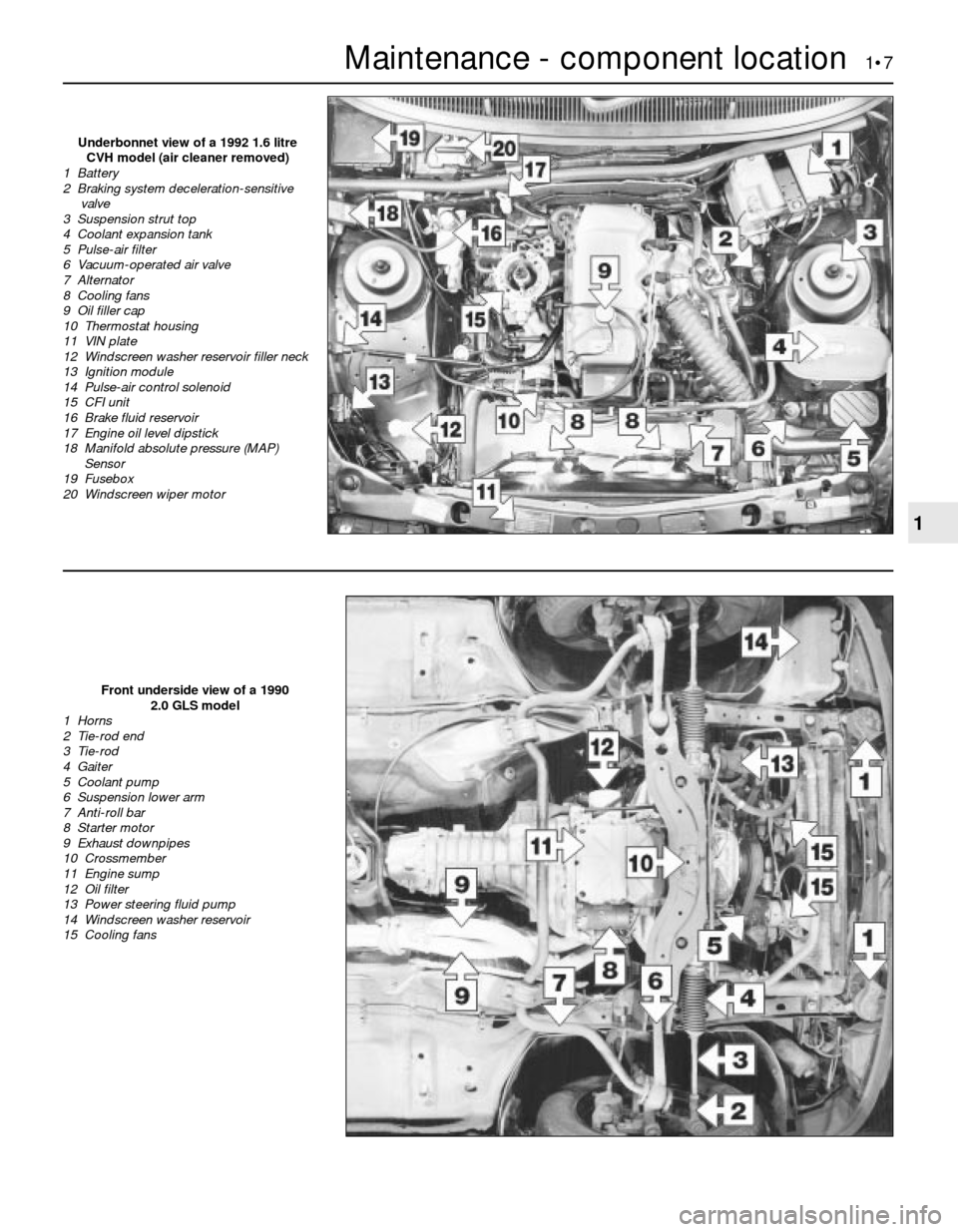
Maintenance - component location 1•7
1
Front underside view of a 1990
2.0 GLS model
1 Horns
2 Tie-rod end
3 Tie-rod
4 Gaiter
5 Coolant pump
6 Suspension lower arm
7 Anti-roll bar
8 Starter motor
9 Exhaust downpipes
10 Crossmember
11 Engine sump
12 Oil filter
13 Power steering fluid pump
14 Windscreen washer reservoir
15 Cooling fans
Underbonnet view of a 1992 1.6 litre
CVH model (air cleaner removed)
1 Battery
2 Braking system deceleration-sensitive
valve
3 Suspension strut top
4 Coolant expansion tank
5 Pulse-air filter
6 Vacuum-operated air valve
7 Alternator
8 Cooling fans
9 Oil filler cap
10 Thermostat housing
11 VIN plate
12 Windscreen washer reservoir filler neck
13 Ignition module
14 Pulse-air control solenoid
15 CFI unit
16 Brake fluid reservoir
17 Engine oil level dipstick
18 Manifold absolute pressure (MAP)
Sensor
19 Fusebox
20 Windscreen wiper motor
Page 10 of 22
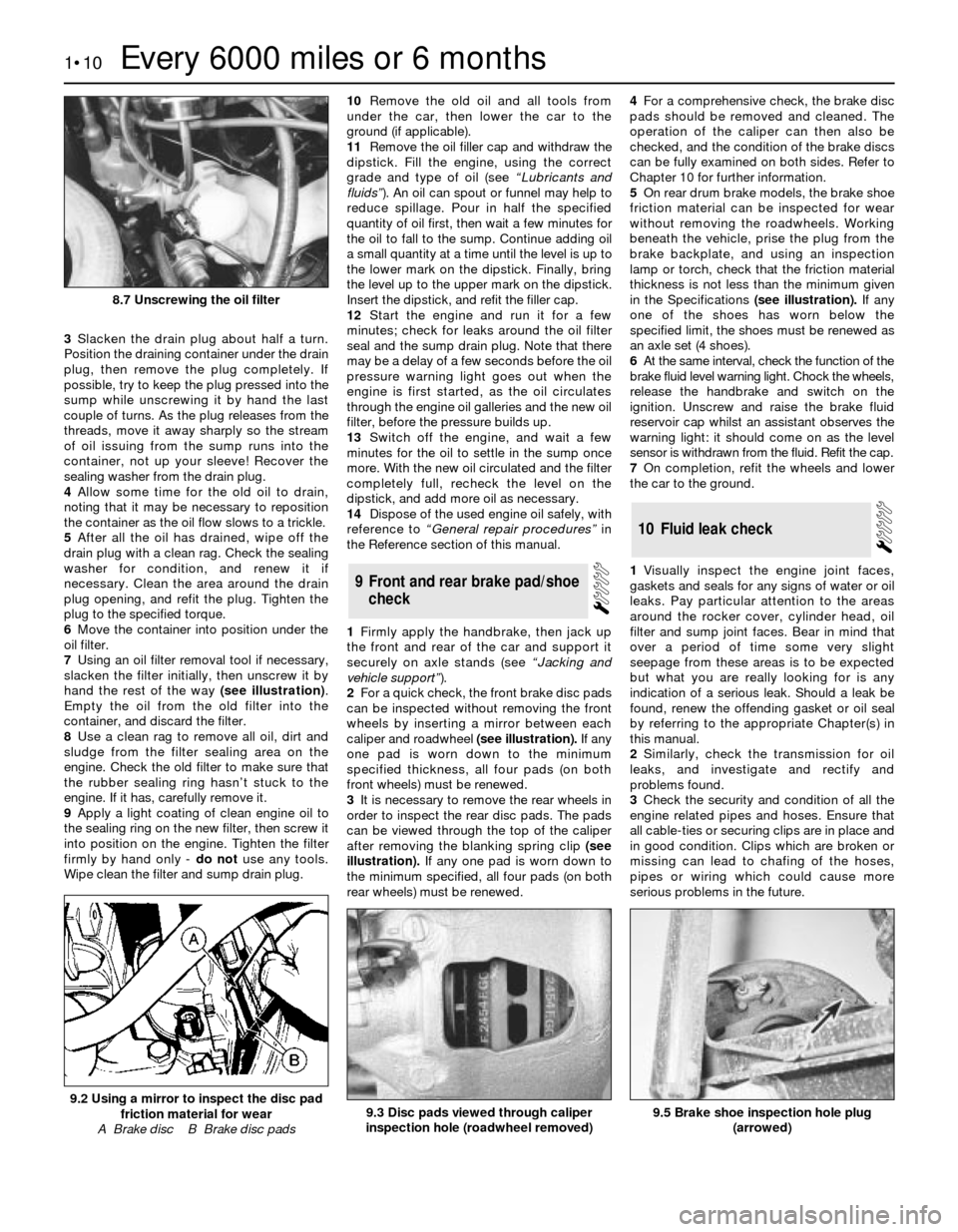
3Slacken the drain plug about half a turn.
Position the draining container under the drain
plug, then remove the plug completely. If
possible, try to keep the plug pressed into the
sump while unscrewing it by hand the last
couple of turns. As the plug releases from the
threads, move it away sharply so the stream
of oil issuing from the sump runs into the
container, not up your sleeve! Recover the
sealing washer from the drain plug.
4Allow some time for the old oil to drain,
noting that it may be necessary to reposition
the container as the oil flow slows to a trickle.
5After all the oil has drained, wipe off the
drain plug with a clean rag. Check the sealing
washer for condition, and renew it if
necessary. Clean the area around the drain
plug opening, and refit the plug. Tighten the
plug to the specified torque.
6Move the container into position under the
oil filter.
7Using an oil filter removal tool if necessary,
slacken the filter initially, then unscrew it by
hand the rest of the way (see illustration).
Empty the oil from the old filter into the
container, and discard the filter.
8Use a clean rag to remove all oil, dirt and
sludge from the filter sealing area on the
engine. Check the old filter to make sure that
the rubber sealing ring hasn’t stuck to the
engine. If it has, carefully remove it.
9Apply a light coating of clean engine oil to
the sealing ring on the new filter, then screw it
into position on the engine. Tighten the filter
firmly by hand only - do notuse any tools.
Wipe clean the filter and sump drain plug.10Remove the old oil and all tools from
under the car, then lower the car to the
ground (if applicable).
11Remove the oil filler cap and withdraw the
dipstick. Fill the engine, using the correct
grade and type of oil (see “Lubricants and
fluids”). An oil can spout or funnel may help to
reduce spillage. Pour in half the specified
quantity of oil first, then wait a few minutes for
the oil to fall to the sump. Continue adding oil
a small quantity at a time until the level is up to
the lower mark on the dipstick. Finally, bring
the level up to the upper mark on the dipstick.
Insert the dipstick, and refit the filler cap.
12Start the engine and run it for a few
minutes; check for leaks around the oil filter
seal and the sump drain plug. Note that there
may be a delay of a few seconds before the oil
pressure warning light goes out when the
engine is first started, as the oil circulates
through the engine oil galleries and the new oil
filter, before the pressure builds up.
13Switch off the engine, and wait a few
minutes for the oil to settle in the sump once
more. With the new oil circulated and the filter
completely full, recheck the level on the
dipstick, and add more oil as necessary.
14Dispose of the used engine oil safely, with
reference to “General repair procedures”in
the Reference section of this manual.
1Firmly apply the handbrake, then jack up
the front and rear of the car and support it
securely on axle stands (see “Jacking and
vehicle support”).
2For a quick check, the front brake disc pads
can be inspected without removing the front
wheels by inserting a mirror between each
caliper and roadwheel(see illustration).If any
one pad is worn down to the minimum
specified thickness, all four pads (on both
front wheels) must be renewed.
3It is necessary to remove the rear wheels in
order to inspect the rear disc pads. The pads
can be viewed through the top of the caliper
after removing the blanking spring clip(see
illustration).If any one pad is worn down to
the minimum specified, all four pads (on both
rear wheels) must be renewed.4For a comprehensive check, the brake disc
pads should be removed and cleaned. The
operation of the caliper can then also be
checked, and the condition of the brake discs
can be fully examined on both sides. Refer to
Chapter 10 for further information.
5On rear drum brake models, the brake shoe
friction material can be inspected for wear
without removing the roadwheels. Working
beneath the vehicle, prise the plug from the
brake backplate, and using an inspection
lamp or torch, check that the friction material
thickness is not less than the minimum given
in the Specifications(see illustration).If any
one of the shoes has worn below the
specified limit, the shoes must be renewed as
an axle set (4 shoes).
6At the same interval, check the function of the
brake fluid level warning light. Chock the wheels,
release the handbrake and switch on the
ignition. Unscrew and raise the brake fluid
reservoir cap whilst an assistant observes the
warning light: it should come on as the level
sensor is withdrawn from the fluid. Refit the cap.
7On completion, refit the wheels and lower
the car to the ground.
1Visually inspect the engine joint faces,
gaskets and seals for any signs of water or oil
leaks. Pay particular attention to the areas
around the rocker cover, cylinder head, oil
filter and sump joint faces. Bear in mind that
over a period of time some very slight
seepage from these areas is to be expected
but what you are really looking for is any
indication of a serious leak. Should a leak be
found, renew the offending gasket or oil seal
by referring to the appropriate Chapter(s) in
this manual.
2Similarly, check the transmission for oil
leaks, and investigate and rectify and
problems found.
3Check the security and condition of all the
engine related pipes and hoses. Ensure that
all cable-ties or securing clips are in place and
in good condition. Clips which are broken or
missing can lead to chafing of the hoses,
pipes or wiring which could cause more
serious problems in the future.
10Fluid leak check
9Front and rear brake pad/shoe
check
1•10Every 6000 miles or 6 months
8.7 Unscrewing the oil filter
9.3 Disc pads viewed through caliper
inspection hole (roadwheel removed)9.5 Brake shoe inspection hole plug
(arrowed)9.2 Using a mirror to inspect the disc pad
friction material for wear
A Brake disc B Brake disc pads
Page 13 of 22
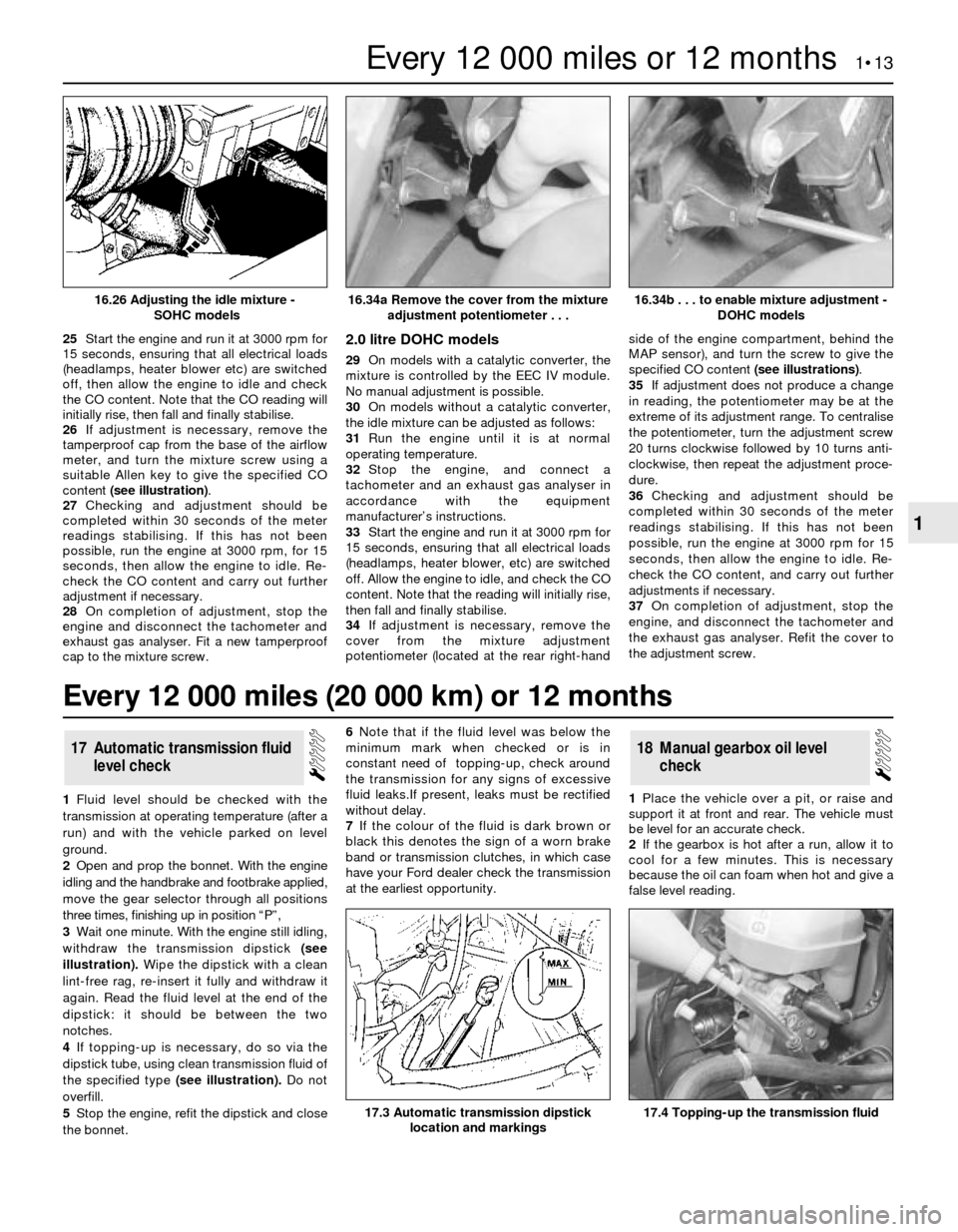
25Start the engine and run it at 3000 rpm for
15 seconds, ensuring that all electrical loads
(headlamps, heater blower etc) are switched
off, then allow the engine to idle and check
the CO content. Note that the CO reading will
initially rise, then fall and finally stabilise.
26If adjustment is necessary, remove the
tamperproof cap from the base of the airflow
meter, and turn the mixture screw using a
suitable Allen key to give the specified CO
content (see illustration).
27Checking and adjustment should be
completed within 30 seconds of the meter
readings stabilising. If this has not been
possible, run the engine at 3000 rpm, for 15
seconds, then allow the engine to idle. Re-
check the CO content and carry out further
adjustment if necessary.
28On completion of adjustment, stop the
engine and disconnect the tachometer and
exhaust gas analyser. Fit a new tamperproof
cap to the mixture screw.2.0 litre DOHC models
29On models with a catalytic converter, the
mixture is controlled by the EEC IV module.
No manual adjustment is possible.
30On models without a catalytic converter,
the idle mixture can be adjusted as follows:
31Run the engine until it is at normal
operating temperature.
32Stop the engine, and connect a
tachometer and an exhaust gas analyser in
accordance with the equipment
manufacturer’s instructions.
33Start the engine and run it at 3000 rpm for
15 seconds, ensuring that all electrical loads
(headlamps, heater blower, etc) are switched
off. Allow the engine to idle, and check the CO
content. Note that the reading will initially rise,
then fall and finally stabilise.
34If adjustment is necessary, remove the
cover from the mixture adjustment
potentiometer (located at the rear right-handside of the engine compartment, behind the
MAP sensor), and turn the screw to give the
specified CO content (see illustrations).
35If adjustment does not produce a change
in reading, the potentiometer may be at the
extreme of its adjustment range. To centralise
the potentiometer, turn the adjustment screw
20 turns clockwise followed by 10 turns anti-
clockwise, then repeat the adjustment proce-
dure.
36Checking and adjustment should be
completed within 30 seconds of the meter
readings stabilising. If this has not been
possible, run the engine at 3000 rpm for 15
seconds, then allow the engine to idle. Re-
check the CO content, and carry out further
adjustments if necessary.
37On completion of adjustment, stop the
engine, and disconnect the tachometer and
the exhaust gas analyser. Refit the cover to
the adjustment screw.
1Fluid level should be checked with the
transmission at operating temperature (after a
run) and with the vehicle parked on level
ground.
2Open and prop the bonnet. With the engine
idling and the handbrake and footbrake applied,
move the gear selector through all positions
three times, finishing up in position “P”,
3Wait one minute. With the engine still idling,
withdraw the transmission dipstick (see
illustration).Wipe the dipstick with a clean
lint-free rag, re-insert it fully and withdraw it
again. Read the fluid level at the end of the
dipstick: it should be between the two
notches.
4If topping-up is necessary, do so via the
dipstick tube, using clean transmission fluid of
the specified type (see illustration).Do not
overfill.
5Stop the engine, refit the dipstick and close
the bonnet.6Note that if the fluid level was below the
minimum mark when checked or is in
constant need of topping-up, check around
the transmission for any signs of excessive
fluid leaks.If present, leaks must be rectified
without delay.
7If the colour of the fluid is dark brown or
black this denotes the sign of a worn brake
band or transmission clutches, in which case
have your Ford dealer check the transmission
at the earliest opportunity.1Place the vehicle over a pit, or raise and
support it at front and rear. The vehicle must
be level for an accurate check.
2If the gearbox is hot after a run, allow it to
cool for a few minutes. This is necessary
because the oil can foam when hot and give a
false level reading.
18Manual gearbox oil level
check17Automatic transmission fluid
level check
Every 12 000 miles or 12 months 1•13
1
16.34b . . . to enable mixture adjustment -
DOHC models
17.4 Topping-up the transmission fluid17.3 Automatic transmission dipstick
location and markings
16.34a Remove the cover from the mixture
adjustment potentiometer . . .16.26 Adjusting the idle mixture -
SOHC models
Every 12 000 miles (20 000 km) or 12 months
Page 18 of 22
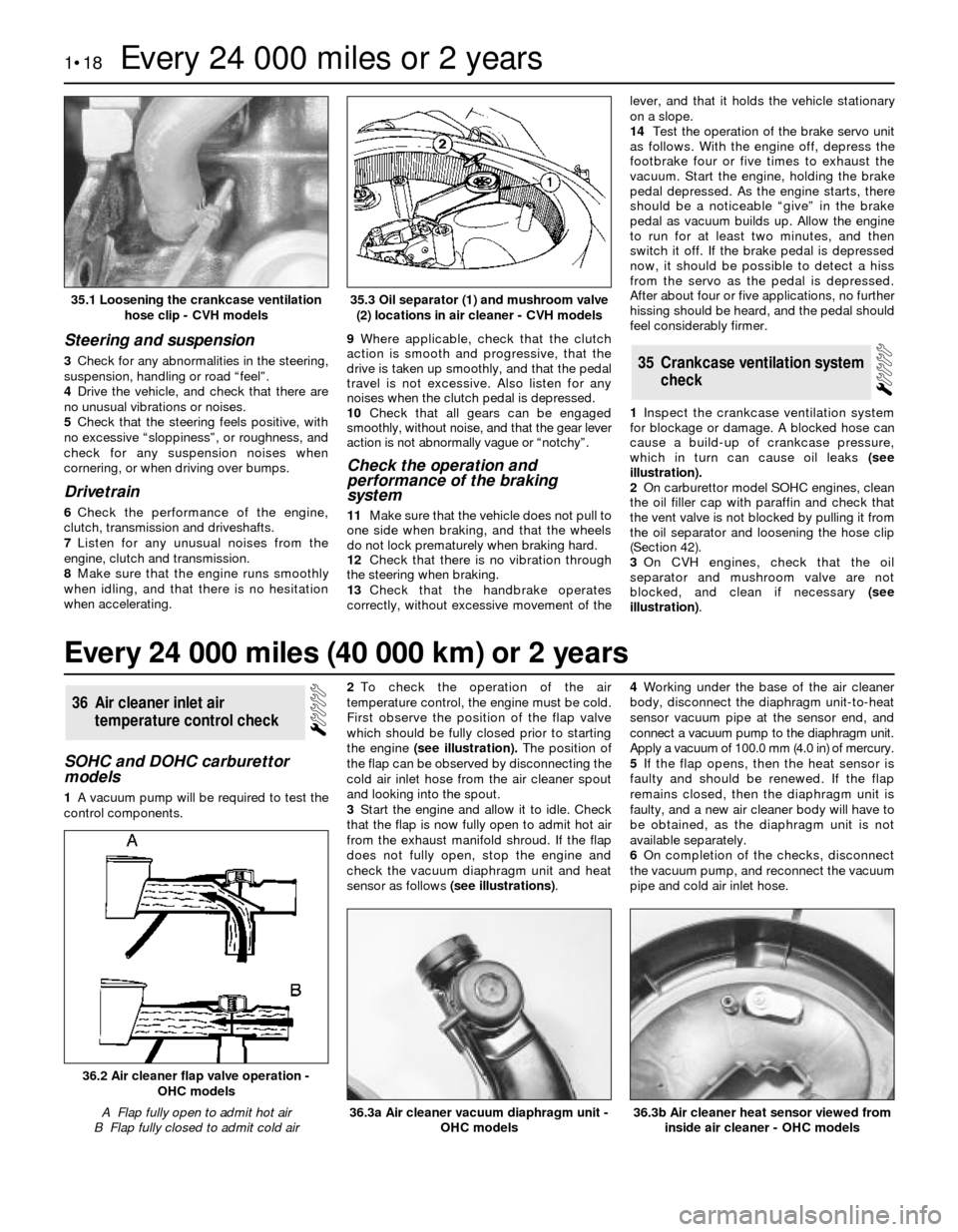
Steering and suspension
3Check for any abnormalities in the steering,
suspension, handling or road “feel”.
4Drive the vehicle, and check that there are
no unusual vibrations or noises.
5Check that the steering feels positive, with
no excessive “sloppiness”, or roughness, and
check for any suspension noises when
cornering, or when driving over bumps.
Drivetrain
6Check the performance of the engine,
clutch, transmission and driveshafts.
7Listen for any unusual noises from the
engine, clutch and transmission.
8Make sure that the engine runs smoothly
when idling, and that there is no hesitation
when accelerating.9Where applicable, check that the clutch
action is smooth and progressive, that the
drive is taken up smoothly, and that the pedal
travel is not excessive. Also listen for any
noises when the clutch pedal is depressed.
10Check that all gears can be engaged
smoothly, without noise, and that the gear lever
action is not abnormally vague or “notchy”.
Check the operation and
performance of the braking
system
11Make sure that the vehicle does not pull to
one side when braking, and that the wheels
do not lock prematurely when braking hard.
12Check that there is no vibration through
the steering when braking.
13Check that the handbrake operates
correctly, without excessive movement of thelever, and that it holds the vehicle stationary
on a slope.
14Test the operation of the brake servo unit
as follows. With the engine off, depress the
footbrake four or five times to exhaust the
vacuum. Start the engine, holding the brake
pedal depressed. As the engine starts, there
should be a noticeable “give” in the brake
pedal as vacuum builds up. Allow the engine
to run for at least two minutes, and then
switch it off. If the brake pedal is depressed
now, it should be possible to detect a hiss
from the servo as the pedal is depressed.
After about four or five applications, no further
hissing should be heard, and the pedal should
feel considerably firmer.
1Inspect the crankcase ventilation system
for blockage or damage. A blocked hose can
cause a build-up of crankcase pressure,
which in turn can cause oil leaks (see
illustration).
2On carburettor model SOHC engines, clean
the oil filler cap with paraffin and check that
the vent valve is not blocked by pulling it from
the oil separator and loosening the hose clip
(Section 42).
3On CVH engines, check that the oil
separator and mushroom valve are not
blocked, and clean if necessary (see
illustration).
35Crankcase ventilation system
check
SOHC and DOHC carburettor
models
1A vacuum pump will be required to test the
control components.2To check the operation of the air
temperature control, the engine must be cold.
First observe the position of the flap valve
which should be fully closed prior to starting
the engine(see illustration).The position of
the flap can be observed by disconnecting the
cold air inlet hose from the air cleaner spout
and looking into the spout.
3Start the engine and allow it to idle. Check
that the flap is now fully open to admit hot air
from the exhaust manifold shroud. If the flap
does not fully open, stop the engine and
check the vacuum diaphragm unit and heat
sensor as follows (see illustrations).4Working under the base of the air cleaner
body, disconnect the diaphragm unit-to-heat
sensor vacuum pipe at the sensor end, and
connect a vacuum pump to the diaphragm unit.
Apply a vacuum of 100.0 mm (4.0 in) of mercury.
5If the flap opens, then the heat sensor is
faulty and should be renewed. If the flap
remains closed, then the diaphragm unit is
faulty, and a new air cleaner body will have to
be obtained, as the diaphragm unit is not
available separately.
6On completion of the checks, disconnect
the vacuum pump, and reconnect the vacuum
pipe and cold air inlet hose.
36Air cleaner inlet air
temperature control check
1•18Every 24 000 miles or 2 years
35.1 Loosening the crankcase ventilation
hose clip - CVH models
36.3b Air cleaner heat sensor viewed from
inside air cleaner - OHC models36.3a Air cleaner vacuum diaphragm unit -
OHC models
36.2 Air cleaner flap valve operation -
OHC models
A Flap fully open to admit hot air
B Flap fully closed to admit cold air
35.3 Oil separator (1) and mushroom valve
(2) locations in air cleaner - CVH models
Every 24 000 miles (40 000 km) or 2 years