service FORD SIERRA 1985 1.G Routine Manintenance And Servicing Workshop Manual
[x] Cancel search | Manufacturer: FORD, Model Year: 1985, Model line: SIERRA, Model: FORD SIERRA 1985 1.GPages: 22, PDF Size: 1.26 MB
Page 3 of 22
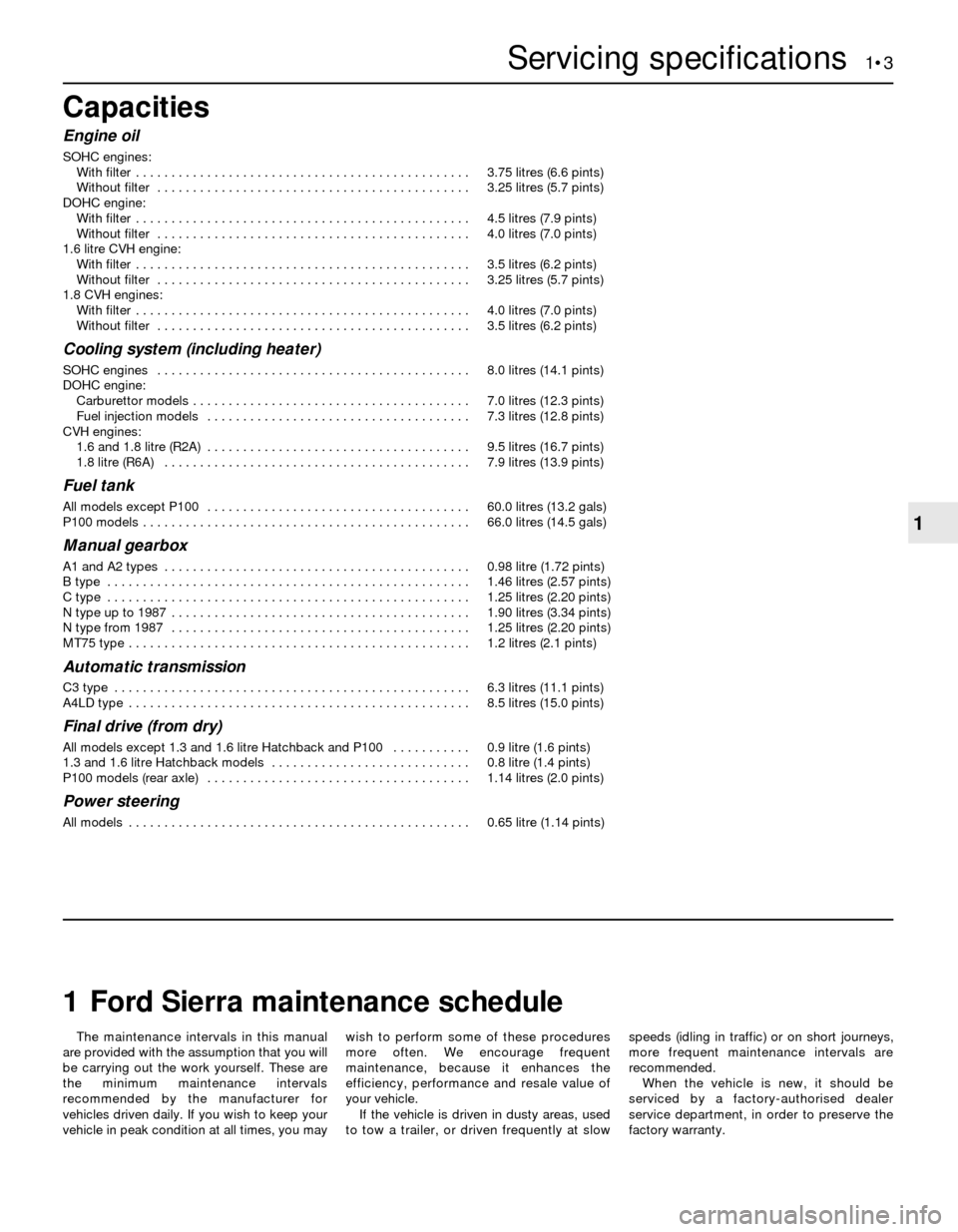
The maintenance intervals in this manual
are provided with the assumption that you will
be carrying out the work yourself. These are
the minimum maintenance intervals
recommended by the manufacturer for
vehicles driven daily. If you wish to keep your
vehicle in peak condition at all times, you maywish to perform some of these procedures
more often. We encourage frequent
maintenance, because it enhances the
efficiency, performance and resale value of
your vehicle.
If the vehicle is driven in dusty areas, used
to tow a trailer, or driven frequently at slowspeeds (idling in traffic) or on short journeys,
more frequent maintenance intervals are
recommended.
When the vehicle is new, it should be
serviced by a factory-authorised dealer
service department, in order to preserve the
factory warranty.
Capacities
Engine oil
SOHC engines:
With filter . . . . . . . . . . . . . . . . . . . . . . . . . . . . . . . . . . . . . . . . . . . . . . .3.75 litres (6.6 pints)
Without filter . . . . . . . . . . . . . . . . . . . . . . . . . . . . . . . . . . . . . . . . . . . .3.25 litres (5.7 pints)
DOHC engine:
With filter . . . . . . . . . . . . . . . . . . . . . . . . . . . . . . . . . . . . . . . . . . . . . . .4.5 litres (7.9 pints)
Without filter . . . . . . . . . . . . . . . . . . . . . . . . . . . . . . . . . . . . . . . . . . . .4.0 litres (7.0 pints)
1.6 litre CVH engine:
With filter . . . . . . . . . . . . . . . . . . . . . . . . . . . . . . . . . . . . . . . . . . . . . . .3.5 litres (6.2 pints)
Without filter . . . . . . . . . . . . . . . . . . . . . . . . . . . . . . . . . . . . . . . . . . . .3.25 litres (5.7 pints)
1.8 CVH engines:
With filter . . . . . . . . . . . . . . . . . . . . . . . . . . . . . . . . . . . . . . . . . . . . . . .4.0 litres (7.0 pints)
Without filter . . . . . . . . . . . . . . . . . . . . . . . . . . . . . . . . . . . . . . . . . . . .3.5 litres (6.2 pints)
Cooling system (including heater)
SOHC engines . . . . . . . . . . . . . . . . . . . . . . . . . . . . . . . . . . . . . . . . . . . .8.0 litres (14.1 pints)
DOHC engine:
Carburettor models . . . . . . . . . . . . . . . . . . . . . . . . . . . . . . . . . . . . . . .7.0 litres (12.3 pints)
Fuel injection models . . . . . . . . . . . . . . . . . . . . . . . . . . . . . . . . . . . . .7.3 litres (12.8 pints)
CVH engines:
1.6 and 1.8 litre (R2A) . . . . . . . . . . . . . . . . . . . . . . . . . . . . . . . . . . . . .9.5 litres (16.7 pints)
1.8 litre (R6A) . . . . . . . . . . . . . . . . . . . . . . . . . . . . . . . . . . . . . . . . . . .7.9 litres (13.9 pints)
Fuel tank
All models except P100 . . . . . . . . . . . . . . . . . . . . . . . . . . . . . . . . . . . . .60.0 litres (13.2 gals)
P100 models . . . . . . . . . . . . . . . . . . . . . . . . . . . . . . . . . . . . . . . . . . . . . .66.0 litres (14.5 gals)
Manual gearbox
A1 and A2 types . . . . . . . . . . . . . . . . . . . . . . . . . . . . . . . . . . . . . . . . . . .0.98 litre (1.72 pints)
B type . . . . . . . . . . . . . . . . . . . . . . . . . . . . . . . . . . . . . . . . . . . . . . . . . . .1.46 litres (2.57 pints)
C type . . . . . . . . . . . . . . . . . . . . . . . . . . . . . . . . . . . . . . . . . . . . . . . . . . .1.25 litres (2.20 pints)
N type up to 1987 . . . . . . . . . . . . . . . . . . . . . . . . . . . . . . . . . . . . . . . . . .1.90 litres (3.34 pints)
N type from 1987 . . . . . . . . . . . . . . . . . . . . . . . . . . . . . . . . . . . . . . . . . .1.25 litres (2.20 pints)
MT75 type . . . . . . . . . . . . . . . . . . . . . . . . . . . . . . . . . . . . . . . . . . . . . . . .1.2 litres (2.1 pints)
Automatic transmission
C3 type . . . . . . . . . . . . . . . . . . . . . . . . . . . . . . . . . . . . . . . . . . . . . . . . . .6.3 litres (11.1 pints)
A4LD type . . . . . . . . . . . . . . . . . . . . . . . . . . . . . . . . . . . . . . . . . . . . . . . .8.5 litres (15.0 pints)
Final drive (from dry)
All models except 1.3 and 1.6 litre Hatchback and P100 . . . . . . . . . . .0.9 litre (1.6 pints)
1.3 and 1.6 litre Hatchback models . . . . . . . . . . . . . . . . . . . . . . . . . . . .0.8 litre (1.4 pints)
P100 models (rear axle) . . . . . . . . . . . . . . . . . . . . . . . . . . . . . . . . . . . . .1.14 litres (2.0 pints)
Power steering
All models . . . . . . . . . . . . . . . . . . . . . . . . . . . . . . . . . . . . . . . . . . . . . . . .0.65 litre (1.14 pints)
Servicing specifications 1•3
1
1Ford Sierra maintenance schedule
Page 9 of 22
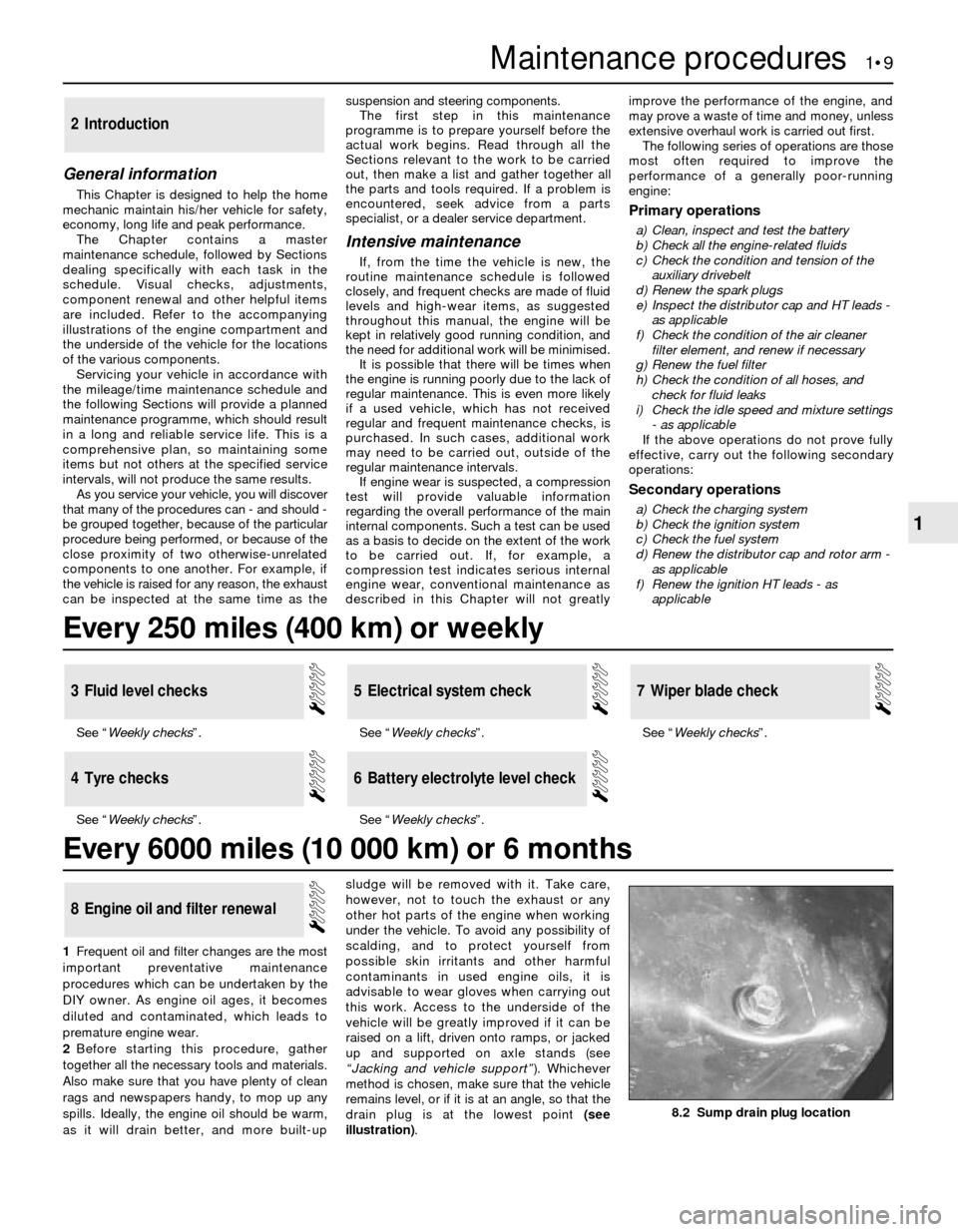
General information
This Chapter is designed to help the home
mechanic maintain his/her vehicle for safety,
economy, long life and peak performance.
The Chapter contains a master
maintenance schedule, followed by Sections
dealing specifically with each task in the
schedule. Visual checks, adjustments,
component renewal and other helpful items
are included. Refer to the accompanying
illustrations of the engine compartment and
the underside of the vehicle for the locations
of the various components.
Servicing your vehicle in accordance with
the mileage/time maintenance schedule and
the following Sections will provide a planned
maintenance programme, which should result
in a long and reliable service life. This is a
comprehensive plan, so maintaining some
items but not others at the specified service
intervals, will not produce the same results.
As you service your vehicle, you will discover
that many of the procedures can - and should -
be grouped together, because of the particular
procedure being performed, or because of the
close proximity of two otherwise-unrelated
components to one another. For example, if
the vehicle is raised for any reason, the exhaust
can be inspected at the same time as thesuspension and steering components.
The first step in this maintenance
programme is to prepare yourself before the
actual work begins. Read through all the
Sections relevant to the work to be carried
out, then make a list and gather together all
the parts and tools required. If a problem is
encountered, seek advice from a parts
specialist, or a dealer service department.
Intensive maintenance
If, from the time the vehicle is new, the
routine maintenance schedule is followed
closely, and frequent checks are made of fluid
levels and high-wear items, as suggested
throughout this manual, the engine will be
kept in relatively good running condition, and
the need for additional work will be minimised.
It is possible that there will be times when
the engine is running poorly due to the lack of
regular maintenance. This is even more likely
if a used vehicle, which has not received
regular and frequent maintenance checks, is
purchased. In such cases, additional work
may need to be carried out, outside of the
regular maintenance intervals.
If engine wear is suspected, a compression
test will provide valuable information
regarding the overall performance of the main
internal components. Such a test can be used
as a basis to decide on the extent of the work
to be carried out. If, for example, a
compression test indicates serious internal
engine wear, conventional maintenance as
described in this Chapter will not greatlyimprove the performance of the engine, and
may prove a waste of time and money, unless
extensive overhaul work is carried out first.
The following series of operations are those
most often required to improve the
performance of a generally poor-running
engine:
Primary operations
a)Clean, inspect and test the battery
b)Check all the engine-related fluids
c)Check the condition and tension of the
auxiliary drivebelt
d)Renew the spark plugs
e)Inspect the distributor cap and HT leads -
as applicable
f)Check the condition of the air cleaner
filter element, and renew if necessary
g)Renew the fuel filter
h)Check the condition of all hoses, and
check for fluid leaks
i)Check the idle speed and mixture settings
- as applicable
If the above operations do not prove fully
effective, carry out the following secondary
operations:
Secondary operations
a)Check the charging system
b)Check the ignition system
c)Check the fuel system
d)Renew the distributor cap and rotor arm -
as applicable
f)Renew the ignition HT leads - as
applicable
2Introduction
See “Weekly checks”.
See “Weekly checks”.See “Weekly checks”.
See “Weekly checks”.See “Weekly checks”.
7Wiper blade check
6Battery electrolyte level check
5Electrical system check
4Tyre checks
3Fluid level checks
1Frequent oil and filter changes are the most
important preventative maintenance
procedures which can be undertaken by the
DIY owner. As engine oil ages, it becomes
diluted and contaminated, which leads to
premature engine wear.
2Before starting this procedure, gather
together all the necessary tools and materials.
Also make sure that you have plenty of clean
rags and newspapers handy, to mop up any
spills. Ideally, the engine oil should be warm,
as it will drain better, and more built-upsludge will be removed with it. Take care,
however, not to touch the exhaust or any
other hot parts of the engine when working
under the vehicle. To avoid any possibility of
scalding, and to protect yourself from
possible skin irritants and other harmful
contaminants in used engine oils, it is
advisable to wear gloves when carrying out
this work. Access to the underside of the
vehicle will be greatly improved if it can be
raised on a lift, driven onto ramps, or jacked
up and supported on axle stands (see
“Jacking and vehicle support”). Whichever
method is chosen, make sure that the vehicle
remains level, or if it is at an angle, so that the
drain plug is at the lowest point (see
illustration).
8Engine oil and filter renewal
Maintenance procedures 1•9
1
8.2 Sump drain plug location
Every 250 miles (400 km) or weekly
Every 6000 miles (10 000 km) or 6 months
Page 12 of 22
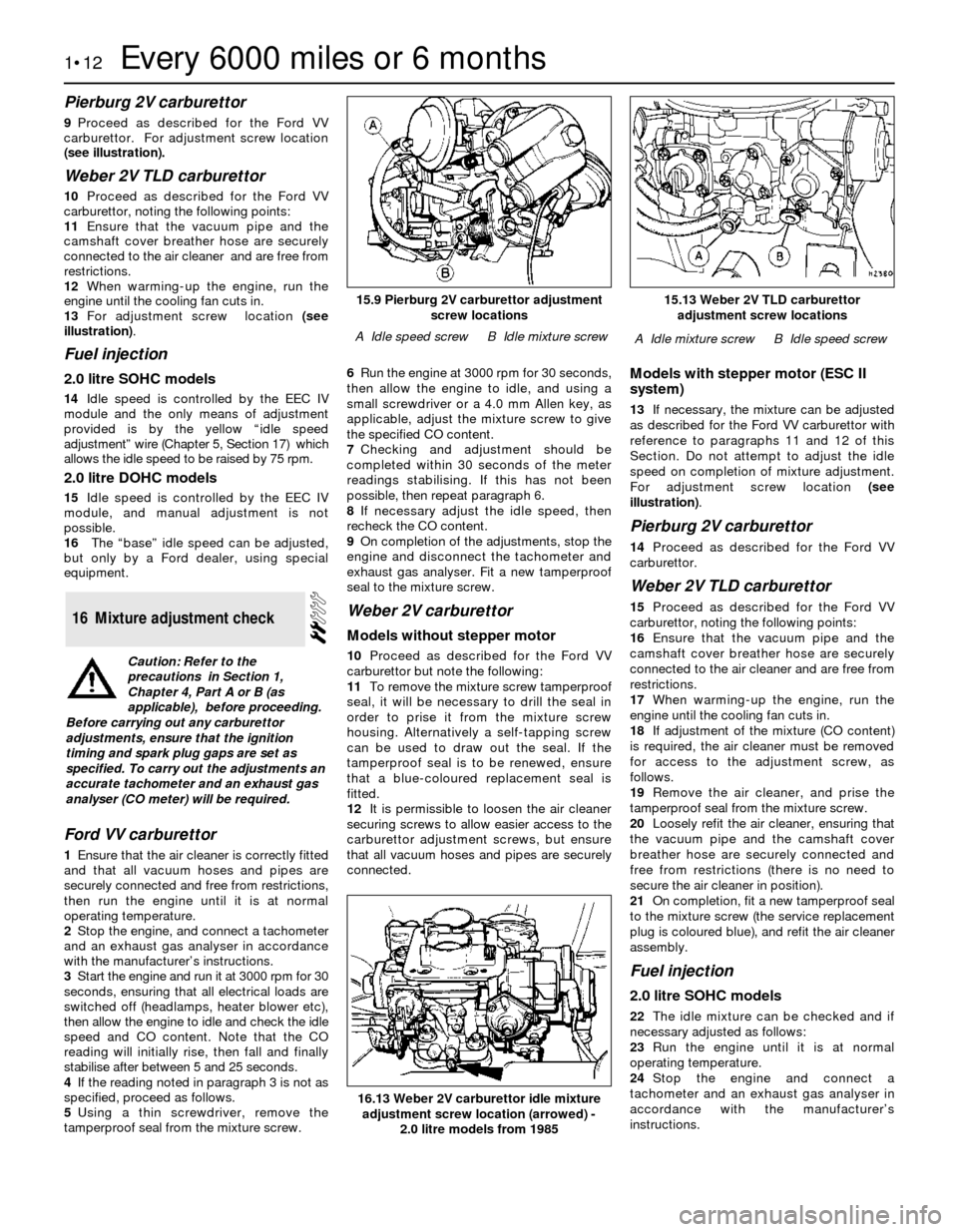
Pierburg 2V carburettor
9Proceed as described for the Ford VV
carburettor. For adjustment screw location
(see illustration).
Weber 2V TLD carburettor
10Proceed as described for the Ford VV
carburettor, noting the following points:
11Ensure that the vacuum pipe and the
camshaft cover breather hose are securely
connected to the air cleaner and are free from
restrictions.
12When warming-up the engine, run the
engine until the cooling fan cuts in.
13For adjustment screw location (see
illustration).
Fuel injection
2.0 litre SOHC models
14Idle speed is controlled by the EEC IV
module and the only means of adjustment
provided is by the yellow “idle speed
adjustment” wire (Chapter 5, Section 17) which
allows the idle speed to be raised by 75 rpm.
2.0 litre DOHC models
15Idle speed is controlled by the EEC IV
module, and manual adjustment is not
possible.
16The “base” idle speed can be adjusted,
but only by a Ford dealer, using special
equipment.
Ford VV carburettor
1Ensure that the air cleaner is correctly fitted
and that all vacuum hoses and pipes are
securely connected and free from restrictions,
then run the engine until it is at normal
operating temperature.
2Stop the engine, and connect a tachometer
and an exhaust gas analyser in accordance
with the manufacturer’s instructions.
3Start the engine and run it at 3000 rpm for 30
seconds, ensuring that all electrical loads are
switched off (headlamps, heater blower etc),
then allow the engine to idle and check the idle
speed and CO content. Note that the CO
reading will initially rise, then fall and finally
stabilise after between 5 and 25 seconds.
4If the reading noted in paragraph 3 is not as
specified, proceed as follows.
5Using a thin screwdriver, remove the
tamperproof seal from the mixture screw.6Run the engine at 3000 rpm for 30 seconds,
then allow the engine to idle, and using a
small screwdriver or a 4.0 mm Allen key, as
applicable, adjust the mixture screw to give
the specified CO content.
7Checking and adjustment should be
completed within 30 seconds of the meter
readings stabilising. If this has not been
possible, then repeat paragraph 6.
8If necessary adjust the idle speed, then
recheck the CO content.
9On completion of the adjustments, stop the
engine and disconnect the tachometer and
exhaust gas analyser. Fit a new tamperproof
seal to the mixture screw.
Weber 2V carburettor
Models without stepper motor
10Proceed as described for the Ford VV
carburettor but note the following:
11To remove the mixture screw tamperproof
seal, it will be necessary to drill the seal in
order to prise it from the mixture screw
housing. Alternatively a self-tapping screw
can be used to draw out the seal. If the
tamperproof seal is to be renewed, ensure
that a blue-coloured replacement seal is
fitted.
12It is permissible to loosen the air cleaner
securing screws to allow easier access to the
carburettor adjustment screws, but ensure
that all vacuum hoses and pipes are securely
connected.
Models with stepper motor (ESC II
system)
13If necessary, the mixture can be adjusted
as described for the Ford VV carburettor with
reference to paragraphs 11 and 12 of this
Section. Do not attempt to adjust the idle
speed on completion of mixture adjustment.
For adjustment screw location (see
illustration).
Pierburg 2V carburettor
14Proceed as described for the Ford VV
carburettor.
Weber 2V TLD carburettor
15Proceed as described for the Ford VV
carburettor, noting the following points:
16Ensure that the vacuum pipe and the
camshaft cover breather hose are securely
connected to the air cleaner and are free from
restrictions.
17When warming-up the engine, run the
engine until the cooling fan cuts in.
18If adjustment of the mixture (CO content)
is required, the air cleaner must be removed
for access to the adjustment screw, as
follows.
19Remove the air cleaner, and prise the
tamperproof seal from the mixture screw.
20Loosely refit the air cleaner, ensuring that
the vacuum pipe and the camshaft cover
breather hose are securely connected and
free from restrictions (there is no need to
secure the air cleaner in position).
21On completion, fit a new tamperproof seal
to the mixture screw (the service replacement
plug is coloured blue), and refit the air cleaner
assembly.
Fuel injection
2.0 litre SOHC models
22The idle mixture can be checked and if
necessary adjusted as follows:
23Run the engine until it is at normal
operating temperature.
24Stop the engine and connect a
tachometer and an exhaust gas analyser in
accordance with the manufacturer’s
instructions.
16Mixture adjustment check
1•12Every 6000 miles or 6 months
15.9 Pierburg 2V carburettor adjustment
screw locations
A Idle speed screwB Idle mixture screwA Idle mixture screwB Idle speed screw
16.13 Weber 2V carburettor idle mixture
adjustment screw location (arrowed) -
2.0 litre models from 1985
15.13 Weber 2V TLD carburettor
adjustment screw locations
Caution: Refer to the
precautions in Section 1,
Chapter 4, Part A or B (as
applicable), before proceeding.
Before carrying out any carburettor
adjustments, ensure that the ignition
timing and spark plug gaps are set as
specified. To carry out the adjustments an
accurate tachometer and an exhaust gas
analyser (CO meter) will be required.
Page 14 of 22
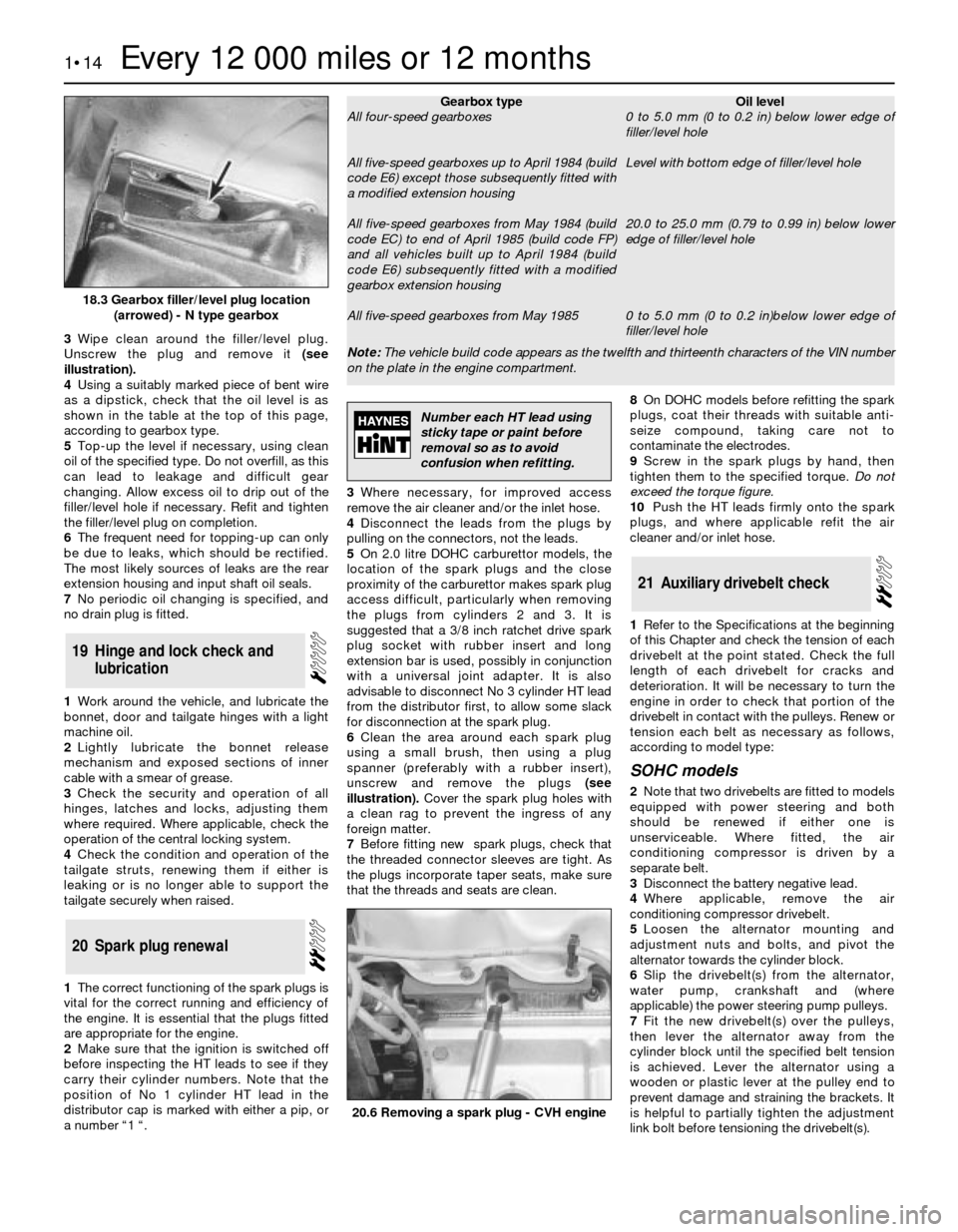
3Wipe clean around the filler/level plug.
Unscrew the plug and remove it(see
illustration).
4Using a suitably marked piece of bent wire
as a dipstick, check that the oil level is as
shown in the table at the top of this page,
according to gearbox type.
5Top-up the level if necessary, using clean
oil of the specified type. Do not overfill, as this
can lead to leakage and difficult gear
changing. Allow excess oil to drip out of the
filler/level hole if necessary. Refit and tighten
the filler/level plug on completion.
6The frequent need for topping-up can only
be due to leaks, which should be rectified.
The most likely sources of leaks are the rear
extension housing and input shaft oil seals.
7No periodic oil changing is specified, and
no drain plug is fitted.
1Work around the vehicle, and lubricate the
bonnet, door and tailgate hinges with a light
machine oil.
2Lightly lubricate the bonnet release
mechanism and exposed sections of inner
cable with a smear of grease.
3Check the security and operation of all
hinges, latches and locks, adjusting them
where required. Where applicable, check the
operation of the central locking system.
4Check the condition and operation of the
tailgate struts, renewing them if either is
leaking or is no longer able to support the
tailgate securely when raised.
1The correct functioning of the spark plugs is
vital for the correct running and efficiency of
the engine. It is essential that the plugs fitted
are appropriate for the engine.
2Make sure that the ignition is switched off
before inspecting the HT leads to see if they
carry their cylinder numbers. Note that the
position of No 1 cylinder HT lead in the
distributor cap is marked with either a pip, or
a number “1 “.3Where necessary, for improved access
remove the air cleaner and/or the inlet hose.
4Disconnect the leads from the plugs by
pulling on the connectors, not the leads.
5On 2.0 litre DOHC carburettor models, the
location of the spark plugs and the close
proximity of the carburettor makes spark plug
access difficult, particularly when removing
the plugs from cylinders 2 and 3. It is
suggested that a 3/8 inch ratchet drive spark
plug socket with rubber insert and long
extension bar is used, possibly in conjunction
with a universal joint adapter. It is also
advisable to disconnect No 3 cylinder HT lead
from the distributor first, to allow some slack
for disconnection at the spark plug.
6Clean the area around each spark plug
using a small brush, then using a plug
spanner (preferably with a rubber insert),
unscrew and remove the plugs(see
illustration).Cover the spark plug holes with
a clean rag to prevent the ingress of any
foreign matter.
7Before fitting new spark plugs, check that
the threaded connector sleeves are tight. As
the plugs incorporate taper seats, make sure
that the threads and seats are clean.8On DOHC models before refitting the spark
plugs, coat their threads with suitable anti-
seize compound, taking care not to
contaminate the electrodes.
9Screw in the spark plugs by hand, then
tighten them to the specified torque. Do not
exceed the torque figure.
10Push the HT leads firmly onto the spark
plugs, and where applicable refit the air
cleaner and/or inlet hose.
1Refer to the Specifications at the beginning
of this Chapter and check the tension of each
drivebelt at the point stated. Check the full
length of each drivebelt for cracks and
deterioration. It will be necessary to turn the
engine in order to check that portion of the
drivebelt in contact with the pulleys. Renew or
tension each belt as necessary as follows,
according to model type:
SOHC models
2Note that two drivebelts are fitted to models
equipped with power steering and both
should be renewed if either one is
unserviceable. Where fitted, the air
conditioning compressor is driven by a
separate belt.
3Disconnect the battery negative lead.
4Where applicable, remove the air
conditioning compressor drivebelt.
5Loosen the alternator mounting and
adjustment nuts and bolts, and pivot the
alternator towards the cylinder block.
6Slip the drivebelt(s) from the alternator,
water pump, crankshaft and (where
applicable) the power steering pump pulleys.
7Fit the new drivebelt(s) over the pulleys,
then lever the alternator away from the
cylinder block until the specified belt tension
is achieved. Lever the alternator using a
wooden or plastic lever at the pulley end to
prevent damage and straining the brackets. It
is helpful to partially tighten the adjustment
link bolt before tensioning the drivebelt(s).
21Auxiliary drivebelt check
20Spark plug renewal
19Hinge and lock check and
lubrication
1•14Every 12 000 miles or 12 months
18.3 Gearbox filler/level plug location
(arrowed) - N type gearbox
20.6 Removing a spark plug - CVH engine
Note: The vehicle build code appears as the twelfth and thirteenth characters of the VIN number
on the plate in the engine compartment.
Gearbox type
All four-speed gearboxes
All five-speed gearboxes up to April 1984 (build
code E6) except those subsequently fitted with
a modified extension housing
All five-speed gearboxes from May 1984 (build
code EC) to end of April 1985 (build code FP)
and all vehicles built up to April 1984 (build
code E6) subsequently fitted with a modified
gearbox extension housing
All five-speed gearboxes from May 1985Oil level
0 to 5.0 mm (0 to 0.2 in) below lower edge of
filler/level hole
Level with bottom edge of filler/level hole
20.0 to 25.0 mm (0.79 to 0.99 in) below lower
edge of filler/level hole
0 to 5.0 mm (0 to 0.2 in)below lower edge of
filler/level hole
Number each HT lead using
sticky tape or paint before
removal so as to avoid
confusion when refitting.
Page 16 of 22
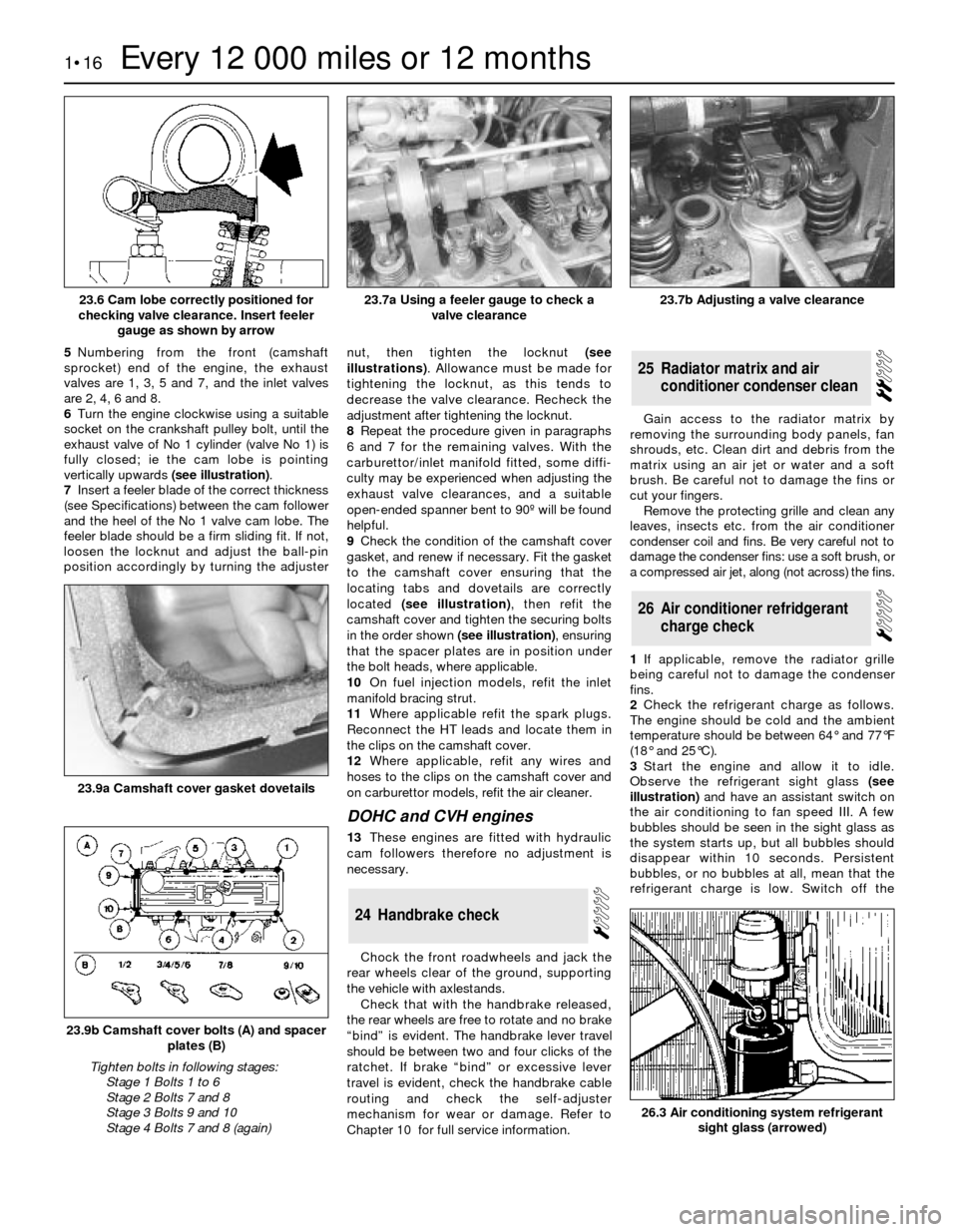
5Numbering from the front (camshaft
sprocket) end of the engine, the exhaust
valves are 1, 3, 5 and 7, and the inlet valves
are 2, 4, 6 and 8.
6Turn the engine clockwise using a suitable
socket on the crankshaft pulley bolt, until the
exhaust valve of No 1 cylinder (valve No 1) is
fully closed; ie the cam lobe is pointing
vertically upwards (see illustration).
7Insert a feeler blade of the correct thickness
(see Specifications) between the cam follower
and the heel of the No 1 valve cam lobe. The
feeler blade should be a firm sliding fit. If not,
loosen the locknut and adjust the ball-pin
position accordingly by turning the adjusternut, then tighten the locknut (see
illustrations). Allowance must be made for
tightening the locknut, as this tends to
decrease the valve clearance. Recheck the
adjustment after tightening the locknut.
8Repeat the procedure given in paragraphs
6 and 7 for the remaining valves. With the
carburettor/inlet manifold fitted, some diffi-
culty may be experienced when adjusting the
exhaust valve clearances, and a suitable
open-ended spanner bent to 90º will be found
helpful.
9Check the condition of the camshaft cover
gasket, and renew if necessary. Fit the gasket
to the camshaft cover ensuring that the
locating tabs and dovetails are correctly
located (see illustration), then refit the
camshaft cover and tighten the securing bolts
in the order shown (see illustration), ensuring
that the spacer plates are in position under
the bolt heads, where applicable.
10On fuel injection models, refit the inlet
manifold bracing strut.
11Where applicable refit the spark plugs.
Reconnect the HT leads and locate them in
the clips on the camshaft cover.
12Where applicable, refit any wires and
hoses to the clips on the camshaft cover and
on carburettor models, refit the air cleaner.
DOHCand CVH engines
13These engines are fitted with hydraulic
cam followers therefore no adjustment is
necessary.
Chock the front roadwheels and jack the
rear wheels clear of the ground, supporting
the vehicle with axlestands.
Check that with the handbrake released,
the rear wheels are free to rotate and no brake
“bind” is evident. The handbrake lever travel
should be between two and four clicks of the
ratchet. If brake “bind” or excessive lever
travel is evident, check the handbrake cable
routing and check the self-adjuster
mechanism for wear or damage. Refer to
Chapter 10 for full service information. Gain access to the radiator matrix by
removing the surrounding body panels, fan
shrouds, etc. Clean dirt and debris from the
matrix using an air jet or water and a soft
brush. Be careful not to damage the fins or
cut your fingers.
Remove the protecting grille and clean any
leaves, insects etc. from the air conditioner
condenser coil and fins. Be very careful not to
damage the condenser fins: use a soft brush, or
a compressed air jet, along (not across) the fins.
1If applicable, remove the radiator grille
being careful not to damage the condenser
fins.
2Check the refrigerant charge as follows.
The engine should be cold and the ambient
temperature should be between 64°and 77°F
(18°and 25°C).
3Start the engine and allow it to idle.
Observe the refrigerant sight glass(see
illustration)and have an assistant switch on
the air conditioning to fan speed III. A few
bubbles should be seen in the sight glass as
the system starts up, but all bubbles should
disappear within 10 seconds. Persistent
bubbles, or no bubbles at all, mean that the
refrigerant charge is low. Switch off the
26Air conditioner refridgerant
charge check
25Radiator matrix and air
conditioner condenser clean
24Handbrake check
1•16Every 12 000 miles or 12 months
23.6 Cam lobe correctly positioned for
checking valve clearance. Insert feeler
gauge as shown by arrow23.7b Adjusting a valve clearance
26.3 Air conditioning system refrigerant
sight glass (arrowed)
23.9b Camshaft cover bolts (A) and spacer
plates (B)
Tighten bolts in following stages:
Stage 1 Bolts 1 to 6
Stage 2 Bolts 7 and 8
Stage 3 Bolts 9 and 10
Stage 4 Bolts 7 and 8 (again)
23.9a Camshaft cover gasket dovetails
23.7a Using a feeler gauge to check a
valve clearance