maintenance FORD SIERRA 1988 2.G Routine Manintenance And Servicing Workshop Manual
[x] Cancel search | Manufacturer: FORD, Model Year: 1988, Model line: SIERRA, Model: FORD SIERRA 1988 2.GPages: 22, PDF Size: 1.26 MB
Page 1 of 22
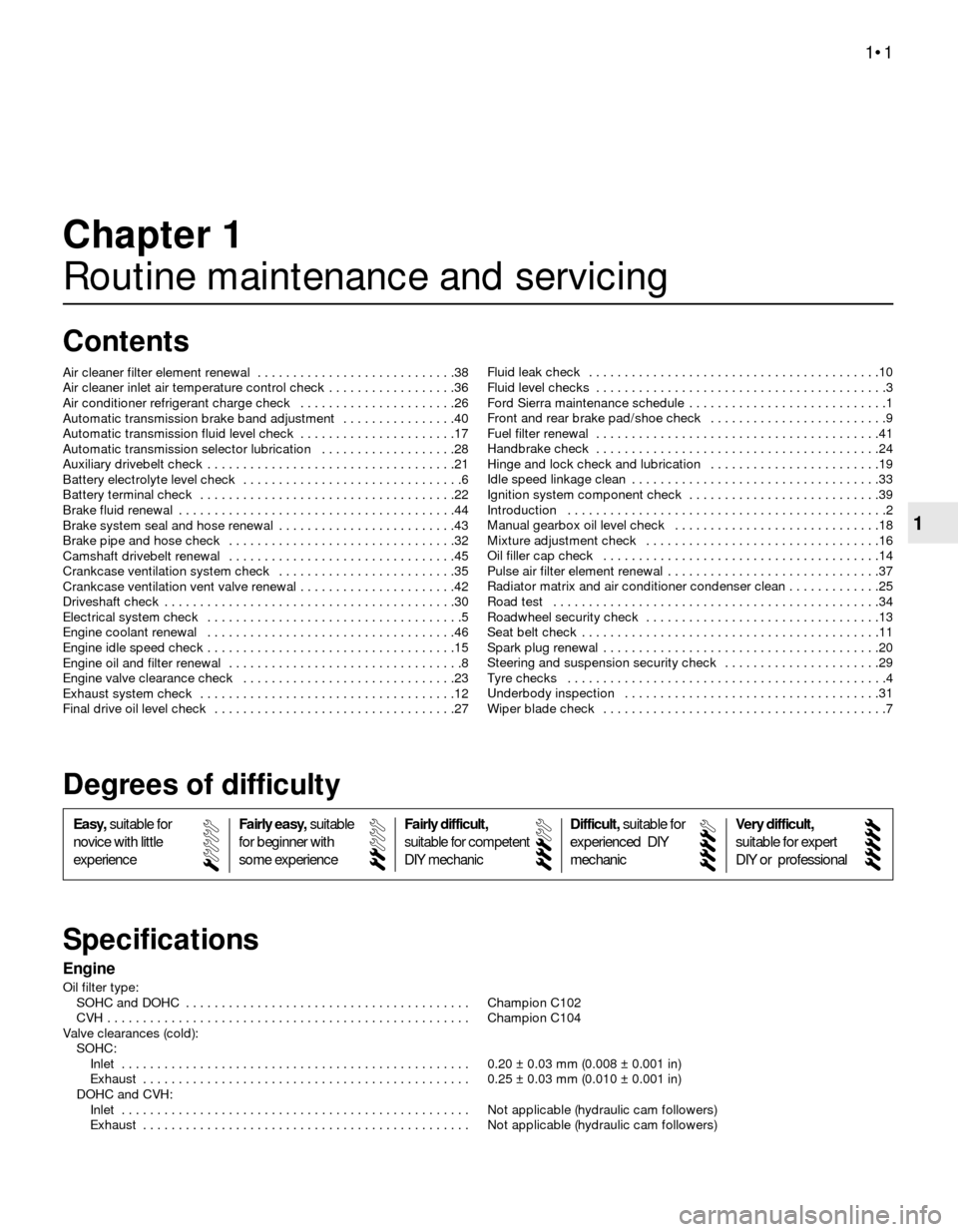
Engine
Oil filter type:
SOHC and DOHC . . . . . . . . . . . . . . . . . . . . . . . . . . . . . . . . . . . . . . . . Champion C102
CVH . . . . . . . . . . . . . . . . . . . . . . . . . . . . . . . . . . . . . . . . . . . . . . . . . . . Champion C104
Valve clearances (cold):
SOHC:
Inlet . . . . . . . . . . . . . . . . . . . . . . . . . . . . . . . . . . . . . . . . . . . . . . . . . 0.20 ± 0.03 mm (0.008 ± 0.001 in)
Exhaust . . . . . . . . . . . . . . . . . . . . . . . . . . . . . . . . . . . . . . . . . . . . . . 0.25 ± 0.03 mm (0.010 ± 0.001 in)
DOHC and CVH:
Inlet . . . . . . . . . . . . . . . . . . . . . . . . . . . . . . . . . . . . . . . . . . . . . . . . . Not applicable (hydraulic cam followers)
Exhaust . . . . . . . . . . . . . . . . . . . . . . . . . . . . . . . . . . . . . . . . . . . . . . Not applicable (hydraulic cam followers)
Chapter 1
Routine maintenance and servicing
Air cleaner filter element renewal . . . . . . . . . . . . . . . . . . . . . . . . . . . .38
Air cleaner inlet air temperature control check . . . . . . . . . . . . . . . . . .36
Air conditioner refrigerant charge check . . . . . . . . . . . . . . . . . . . . . .26
Automatic transmission brake band adjustment . . . . . . . . . . . . . . . .40
Automatic transmission fluid level check . . . . . . . . . . . . . . . . . . . . . .17
Automatic transmission selector lubrication . . . . . . . . . . . . . . . . . . .28
Auxiliary drivebelt check . . . . . . . . . . . . . . . . . . . . . . . . . . . . . . . . . . .21
Battery electrolyte level check . . . . . . . . . . . . . . . . . . . . . . . . . . . . . . .6
Battery terminal check . . . . . . . . . . . . . . . . . . . . . . . . . . . . . . . . . . . .22
Brake fluid renewal . . . . . . . . . . . . . . . . . . . . . . . . . . . . . . . . . . . . . . .44
Brake system seal and hose renewal . . . . . . . . . . . . . . . . . . . . . . . . .43
Brake pipe and hose check . . . . . . . . . . . . . . . . . . . . . . . . . . . . . . . .32
Camshaft drivebelt renewal . . . . . . . . . . . . . . . . . . . . . . . . . . . . . . . .45
Crankcase ventilation system check . . . . . . . . . . . . . . . . . . . . . . . . .35
Crankcase ventilation vent valve renewal . . . . . . . . . . . . . . . . . . . . . .42
Driveshaft check . . . . . . . . . . . . . . . . . . . . . . . . . . . . . . . . . . . . . . . . .30
Electrical system check . . . . . . . . . . . . . . . . . . . . . . . . . . . . . . . . . . . .5
Engine coolant renewal . . . . . . . . . . . . . . . . . . . . . . . . . . . . . . . . . . .46
Engine idle speed check . . . . . . . . . . . . . . . . . . . . . . . . . . . . . . . . . . .15
Engine oil and filter renewal . . . . . . . . . . . . . . . . . . . . . . . . . . . . . . . . .8
Engine valve clearance check . . . . . . . . . . . . . . . . . . . . . . . . . . . . . .23
Exhaust system check . . . . . . . . . . . . . . . . . . . . . . . . . . . . . . . . . . . .12
Final drive oil level check . . . . . . . . . . . . . . . . . . . . . . . . . . . . . . . . . .27Fluid leak check . . . . . . . . . . . . . . . . . . . . . . . . . . . . . . . . . . . . . . . . .10
Fluid level checks . . . . . . . . . . . . . . . . . . . . . . . . . . . . . . . . . . . . . . . . .3
Ford Sierra maintenance schedule . . . . . . . . . . . . . . . . . . . . . . . . . . . .1
Front and rear brake pad/shoe check . . . . . . . . . . . . . . . . . . . . . . . . .9
Fuel filter renewal . . . . . . . . . . . . . . . . . . . . . . . . . . . . . . . . . . . . . . . .41
Handbrake check . . . . . . . . . . . . . . . . . . . . . . . . . . . . . . . . . . . . . . . .24
Hinge and lock check and lubrication . . . . . . . . . . . . . . . . . . . . . . . .19
Idle speed linkage clean . . . . . . . . . . . . . . . . . . . . . . . . . . . . . . . . . . .33
Ignition system component check . . . . . . . . . . . . . . . . . . . . . . . . . . .39
Introduction . . . . . . . . . . . . . . . . . . . . . . . . . . . . . . . . . . . . . . . . . . . . .2
Manual gearbox oil level check . . . . . . . . . . . . . . . . . . . . . . . . . . . . .18
Mixture adjustment check . . . . . . . . . . . . . . . . . . . . . . . . . . . . . . . . .16
Oil filler cap check . . . . . . . . . . . . . . . . . . . . . . . . . . . . . . . . . . . . . . .14
Pulse air filter element renewal . . . . . . . . . . . . . . . . . . . . . . . . . . . . . .37
Radiator matrix and air conditioner condenser clean . . . . . . . . . . . . .25
Road test . . . . . . . . . . . . . . . . . . . . . . . . . . . . . . . . . . . . . . . . . . . . . .34
Roadwheel security check . . . . . . . . . . . . . . . . . . . . . . . . . . . . . . . . .13
Seat belt check . . . . . . . . . . . . . . . . . . . . . . . . . . . . . . . . . . . . . . . . . .11
Spark plug renewal . . . . . . . . . . . . . . . . . . . . . . . . . . . . . . . . . . . . . . .20
Steering and suspension security check . . . . . . . . . . . . . . . . . . . . . .29
Tyre checks . . . . . . . . . . . . . . . . . . . . . . . . . . . . . . . . . . . . . . . . . . . . .4
Underbody inspection . . . . . . . . . . . . . . . . . . . . . . . . . . . . . . . . . . . .31
Wiper blade check . . . . . . . . . . . . . . . . . . . . . . . . . . . . . . . . . . . . . . . .7
1•1
Easy,suitable for
novice with little
experienceFairly easy,suitable
for beginner with
some experienceFairly difficult,
suitable for competent
DIY mechanic
Difficult,suitable for
experienced DIY
mechanicVery difficult,
suitable for expert
DIY or professional
Degrees of difficulty
Specifications Contents
1
Page 3 of 22
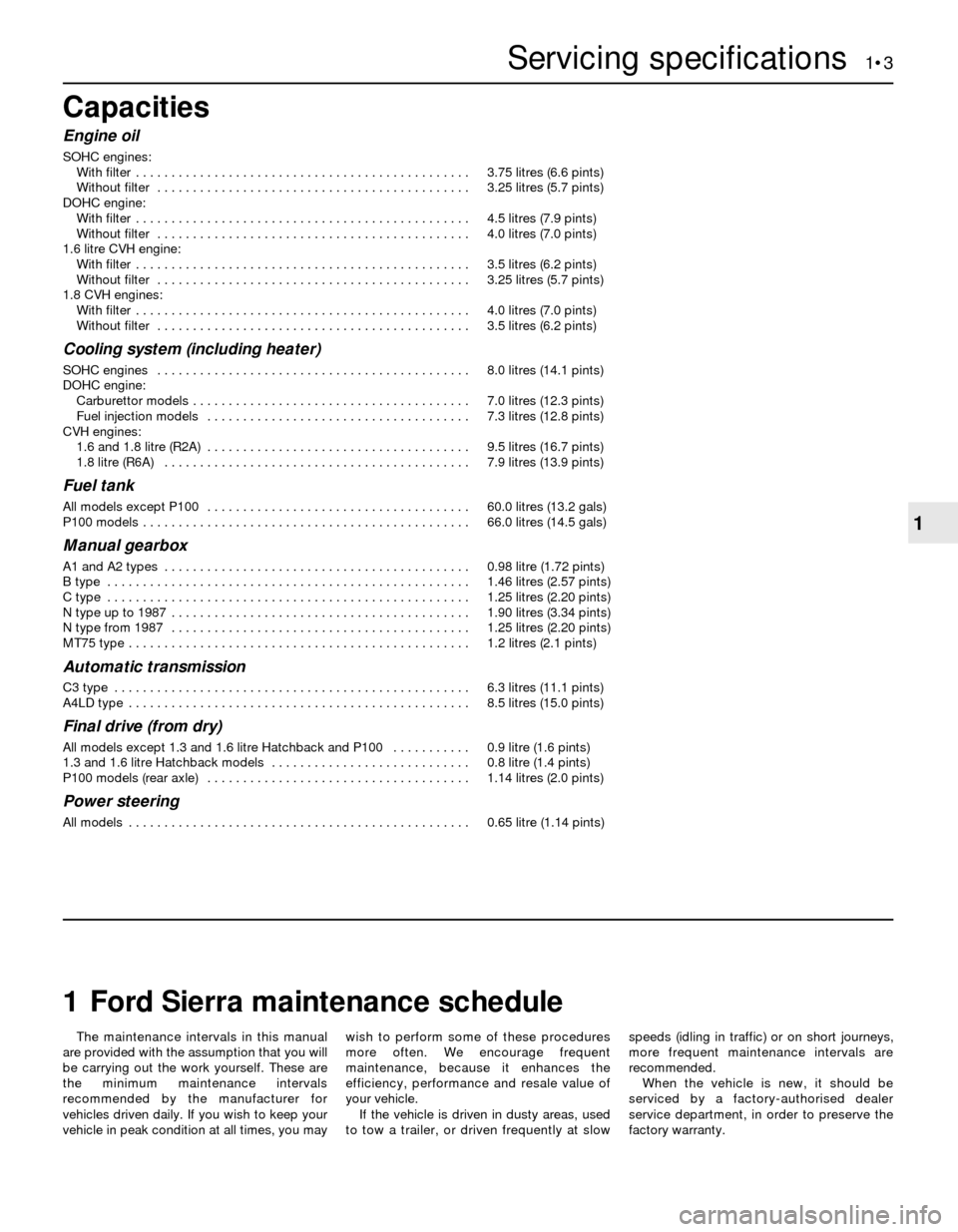
The maintenance intervals in this manual
are provided with the assumption that you will
be carrying out the work yourself. These are
the minimum maintenance intervals
recommended by the manufacturer for
vehicles driven daily. If you wish to keep your
vehicle in peak condition at all times, you maywish to perform some of these procedures
more often. We encourage frequent
maintenance, because it enhances the
efficiency, performance and resale value of
your vehicle.
If the vehicle is driven in dusty areas, used
to tow a trailer, or driven frequently at slowspeeds (idling in traffic) or on short journeys,
more frequent maintenance intervals are
recommended.
When the vehicle is new, it should be
serviced by a factory-authorised dealer
service department, in order to preserve the
factory warranty.
Capacities
Engine oil
SOHC engines:
With filter . . . . . . . . . . . . . . . . . . . . . . . . . . . . . . . . . . . . . . . . . . . . . . .3.75 litres (6.6 pints)
Without filter . . . . . . . . . . . . . . . . . . . . . . . . . . . . . . . . . . . . . . . . . . . .3.25 litres (5.7 pints)
DOHC engine:
With filter . . . . . . . . . . . . . . . . . . . . . . . . . . . . . . . . . . . . . . . . . . . . . . .4.5 litres (7.9 pints)
Without filter . . . . . . . . . . . . . . . . . . . . . . . . . . . . . . . . . . . . . . . . . . . .4.0 litres (7.0 pints)
1.6 litre CVH engine:
With filter . . . . . . . . . . . . . . . . . . . . . . . . . . . . . . . . . . . . . . . . . . . . . . .3.5 litres (6.2 pints)
Without filter . . . . . . . . . . . . . . . . . . . . . . . . . . . . . . . . . . . . . . . . . . . .3.25 litres (5.7 pints)
1.8 CVH engines:
With filter . . . . . . . . . . . . . . . . . . . . . . . . . . . . . . . . . . . . . . . . . . . . . . .4.0 litres (7.0 pints)
Without filter . . . . . . . . . . . . . . . . . . . . . . . . . . . . . . . . . . . . . . . . . . . .3.5 litres (6.2 pints)
Cooling system (including heater)
SOHC engines . . . . . . . . . . . . . . . . . . . . . . . . . . . . . . . . . . . . . . . . . . . .8.0 litres (14.1 pints)
DOHC engine:
Carburettor models . . . . . . . . . . . . . . . . . . . . . . . . . . . . . . . . . . . . . . .7.0 litres (12.3 pints)
Fuel injection models . . . . . . . . . . . . . . . . . . . . . . . . . . . . . . . . . . . . .7.3 litres (12.8 pints)
CVH engines:
1.6 and 1.8 litre (R2A) . . . . . . . . . . . . . . . . . . . . . . . . . . . . . . . . . . . . .9.5 litres (16.7 pints)
1.8 litre (R6A) . . . . . . . . . . . . . . . . . . . . . . . . . . . . . . . . . . . . . . . . . . .7.9 litres (13.9 pints)
Fuel tank
All models except P100 . . . . . . . . . . . . . . . . . . . . . . . . . . . . . . . . . . . . .60.0 litres (13.2 gals)
P100 models . . . . . . . . . . . . . . . . . . . . . . . . . . . . . . . . . . . . . . . . . . . . . .66.0 litres (14.5 gals)
Manual gearbox
A1 and A2 types . . . . . . . . . . . . . . . . . . . . . . . . . . . . . . . . . . . . . . . . . . .0.98 litre (1.72 pints)
B type . . . . . . . . . . . . . . . . . . . . . . . . . . . . . . . . . . . . . . . . . . . . . . . . . . .1.46 litres (2.57 pints)
C type . . . . . . . . . . . . . . . . . . . . . . . . . . . . . . . . . . . . . . . . . . . . . . . . . . .1.25 litres (2.20 pints)
N type up to 1987 . . . . . . . . . . . . . . . . . . . . . . . . . . . . . . . . . . . . . . . . . .1.90 litres (3.34 pints)
N type from 1987 . . . . . . . . . . . . . . . . . . . . . . . . . . . . . . . . . . . . . . . . . .1.25 litres (2.20 pints)
MT75 type . . . . . . . . . . . . . . . . . . . . . . . . . . . . . . . . . . . . . . . . . . . . . . . .1.2 litres (2.1 pints)
Automatic transmission
C3 type . . . . . . . . . . . . . . . . . . . . . . . . . . . . . . . . . . . . . . . . . . . . . . . . . .6.3 litres (11.1 pints)
A4LD type . . . . . . . . . . . . . . . . . . . . . . . . . . . . . . . . . . . . . . . . . . . . . . . .8.5 litres (15.0 pints)
Final drive (from dry)
All models except 1.3 and 1.6 litre Hatchback and P100 . . . . . . . . . . .0.9 litre (1.6 pints)
1.3 and 1.6 litre Hatchback models . . . . . . . . . . . . . . . . . . . . . . . . . . . .0.8 litre (1.4 pints)
P100 models (rear axle) . . . . . . . . . . . . . . . . . . . . . . . . . . . . . . . . . . . . .1.14 litres (2.0 pints)
Power steering
All models . . . . . . . . . . . . . . . . . . . . . . . . . . . . . . . . . . . . . . . . . . . . . . . .0.65 litre (1.14 pints)
Servicing specifications 1•3
1
1Ford Sierra maintenance schedule
Page 4 of 22

1•4Maintenance schedule
Every 250 miles (400 km) or weekly
m mCheck the engine oil level (Section 3)
m mCheck the engine coolant level (Section 3)
m mCheck the brake fluid level (Section 3)
m mCheck the power steering fluid level (Section 3)
m mCheck the screen washer fluid level (Section 3)
m mVisually examine the tyres for tread depth, and wear
or damage (Section 4)
m mCheck and if necessary adjust the tyre pressures
(Section 4)
m mCheck and if necessary top-up the battery electrolyte
level - where applicable (Section 6)
m mCheck the operation of the horn, all lights, and the
wipers and washers (Sections 5 and 7)
Every 6000 miles (10 000 km) or
6 months - whichever comes sooner
m mRenew engine oil and filter (Section 8)
m mCheck brake pads or shoes for wear (front and rear)
(Section 9)
m mCheck operation of brake fluid level warning indicator
(Section 9)
m mInspect engine bay and underside of vehicle for fluid
leaks or other signs of damage (Section 10)
m mCheck function and condition of seat belts
(Section 11)
m mCheck condition and security of exhaust system
(Section 12)
m mCheck tightness of wheel nuts (Section 13)
m mClean oil filler cap (Section 14)
m mCheck idle speed (where applicable) (Section 15)
m mCheck mixture adjustment (where applicable)
(Section 16)
Every 12 000 miles (20 000 km) or
12 months - whichever comes sooner
m mCheck automatic transmission fluid level (engine hot)
(Section 17)
m mCheck manual gearbox oil level (Section 18)
m mCheck operation of latches, check straps and locks;
lubricate if necessary (Section 19)
m mRenew spark plugs (Section 20)
m mCheck condition and tension of auxiliary drivebelt(s);
adjust or renew as necessary (Section 21)
m mCheck tightness of battery terminals, clean and
neutralise corrosion if necessary (Section 22)
m mCheck engine valve clearances - SOHC only
(Section 23)
m mCheck handbrake mechanism (Section 24)
Every 24 000 miles (40 000 km) or
2 years - whichever comes sooner
m mCheck air cleaner inlet air temperature control
operation (carburettor models) (Section 36)
m mRenew pulse air filter element (1.6 litre CVH)
(Section 37)
m mRenew air cleaner element (Section 38)
m mClean and inspect distributor cap and HT leads
(Section 39)
m mCheck automatic transmission brake band
adjustment (Section 40)
m mRenew fuel filter (fuel-injection models only)
(Section 41)
m mRenew crankcase ventilation vent valve (SOHC and
DOHC) (Section 42)
m mClean radiator matrix and air conditioning condenser
fins (where applicable) (Section 25)
m mCheck air conditioning refrigerant charge (where
applicable) (Section 26)
m mCheck final drive oil level (Section 27)
m mLubricate automatic transmission selector/kickdown
linkage (Section 28)
m mCheck security and condition of steering and
suspension components, gaiters and boots
(Section 29)
m mCheck condition and security of driveshaft joints and
gaiters (Section 30)
m mInspect underbody and panels for corrosion or other
damage (Section 31)
m mInspect brake pipes and hoses (Section 32)
m mClean idle speed control linkage at throttle (where
applicable) (Section 33)
m mRoad test and check operation of ABS (Section 34)
m mCheck crankcase ventilation system (Section 35)
Every 36 000 miles (60 000 km) or
3 years - whichever comes sooner
m mRenew brake hydraulic system seals and hoses if
necessary (Section 43)
m mRenew brake hydraulic fluid (Section 44)
m mRenew camshaft drivebelt (optional on SOHC
models - compulsory on CVH) (Section 45)
m mRenew coolant (Section 46)
Every 12 000 miles (20 000 km) or
12 months - whichever comes sooner
(continued)
Page 5 of 22
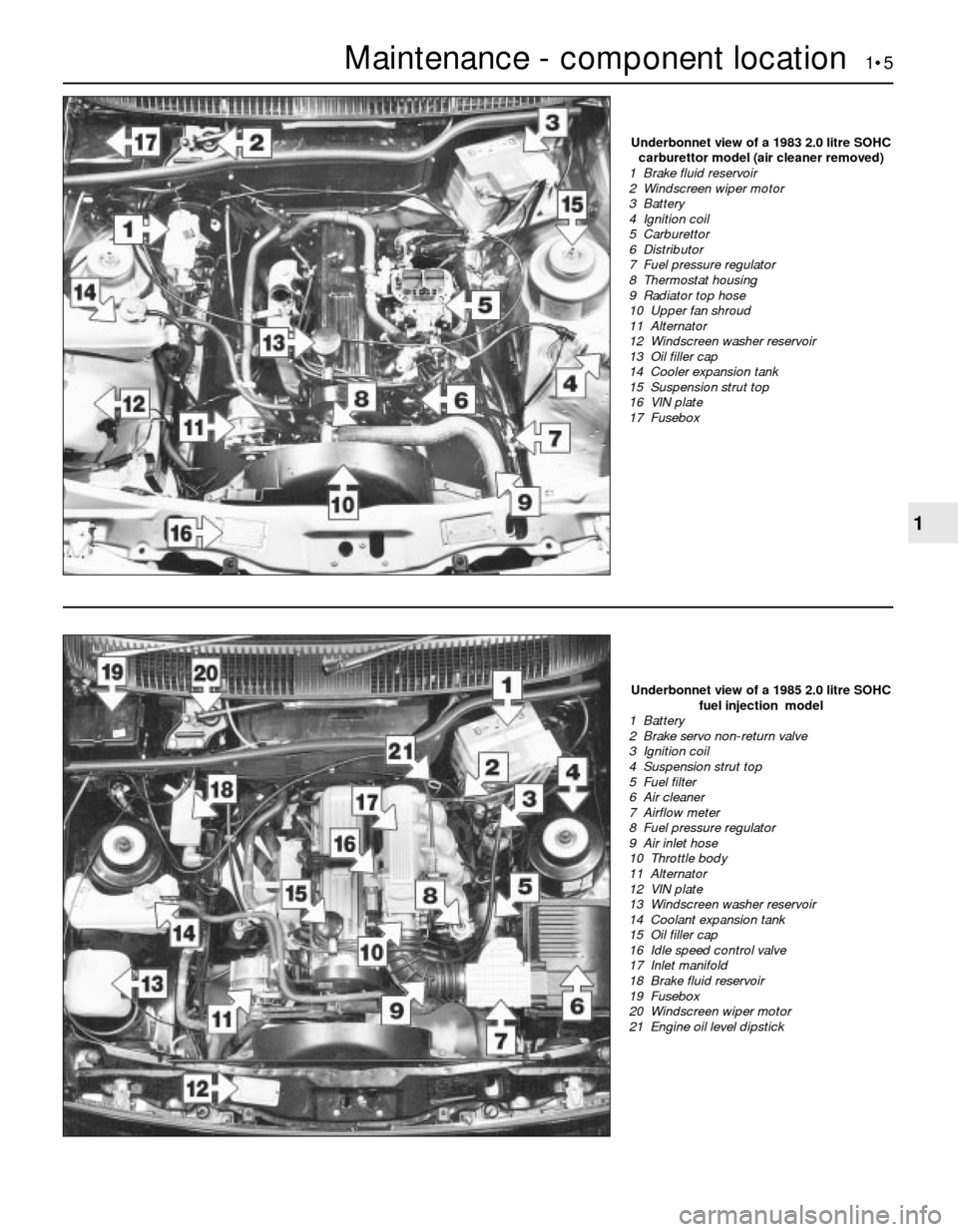
Maintenance - component location 1•5
1
Underbonnet view of a 1985 2.0 litre SOHC
fuel injection model
1 Battery
2 Brake servo non-return valve
3 Ignition coil
4 Suspension strut top
5 Fuel filter
6 Air cleaner
7 Airflow meter
8 Fuel pressure regulator
9 Air inlet hose
10 Throttle body
11 Alternator
12 VIN plate
13 Windscreen washer reservoir
14 Coolant expansion tank
15 Oil filler cap
16 Idle speed control valve
17 Inlet manifold
18 Brake fluid reservoir
19 Fusebox
20 Windscreen wiper motor
21 Engine oil level dipstick
Underbonnet view of a 1983 2.0 litre SOHC
carburettor model (air cleaner removed)
1 Brake fluid reservoir
2 Windscreen wiper motor
3 Battery
4 Ignition coil
5 Carburettor
6 Distributor
7 Fuel pressure regulator
8 Thermostat housing
9 Radiator top hose
10 Upper fan shroud
11 Alternator
12 Windscreen washer reservoir
13 Oil filler cap
14 Cooler expansion tank
15 Suspension strut top
16 VIN plate
17 Fusebox
Page 6 of 22
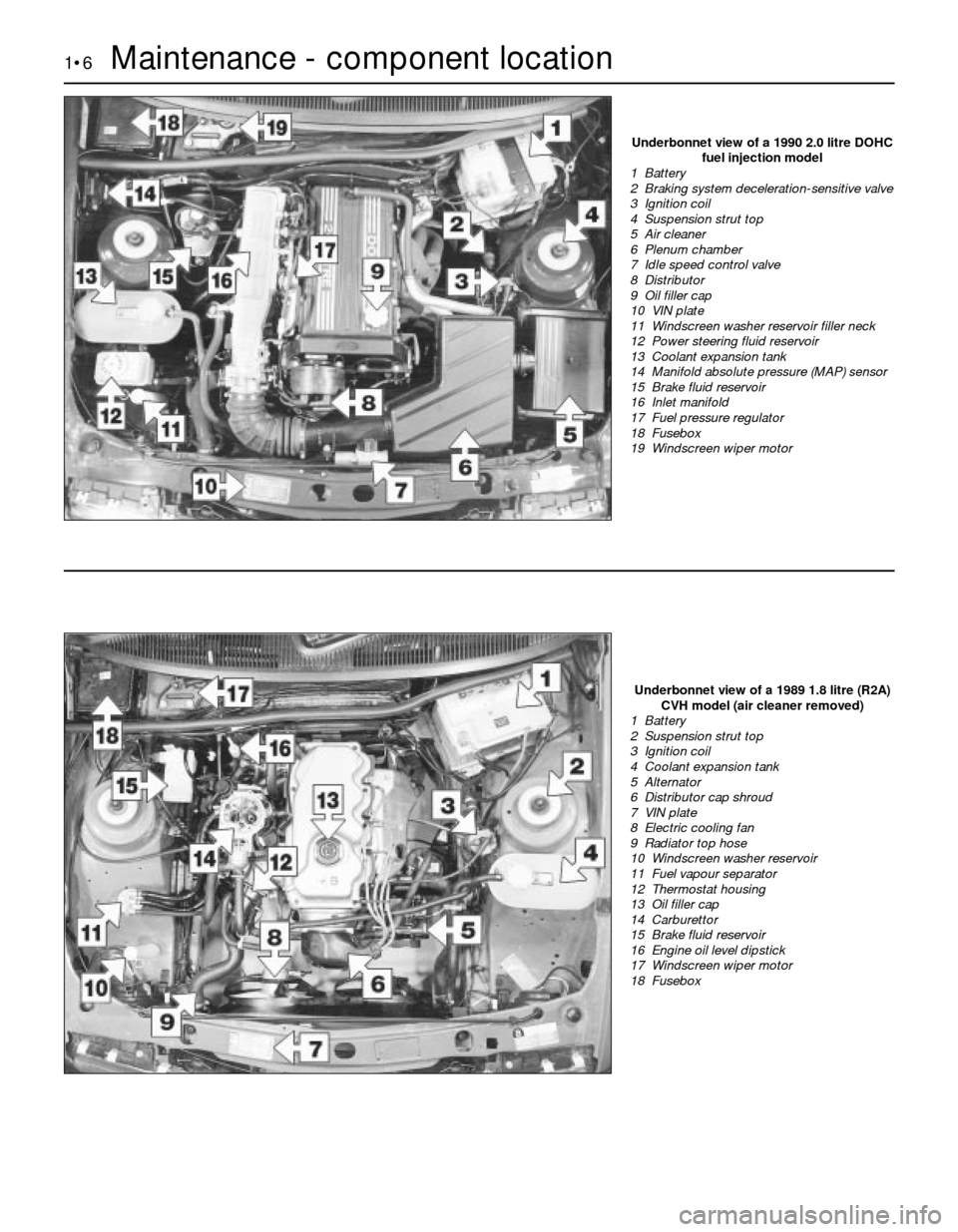
1•6Maintenance - component location
Underbonnet view of a 1990 2.0 litre DOHC
fuel injection model
1 Battery
2 Braking system deceleration-sensitive valve
3 Ignition coil
4 Suspension strut top
5 Air cleaner
6 Plenum chamber
7 Idle speed control valve
8 Distributor
9 Oil filler cap
10 VIN plate
11 Windscreen washer reservoir filler neck
12 Power steering fluid reservoir
13 Coolant expansion tank
14 Manifold absolute pressure (MAP) sensor
15 Brake fluid reservoir
16 Inlet manifold
17 Fuel pressure regulator
18 Fusebox
19 Windscreen wiper motor
Underbonnet view of a 1989 1.8 litre (R2A)
CVH model (air cleaner removed)
1 Battery
2 Suspension strut top
3 Ignition coil
4 Coolant expansion tank
5 Alternator
6 Distributor cap shroud
7 VIN plate
8 Electric cooling fan
9 Radiator top hose
10 Windscreen washer reservoir
11 Fuel vapour separator
12 Thermostat housing
13 Oil filler cap
14 Carburettor
15 Brake fluid reservoir
16 Engine oil level dipstick
17 Windscreen wiper motor
18 Fusebox
Page 7 of 22
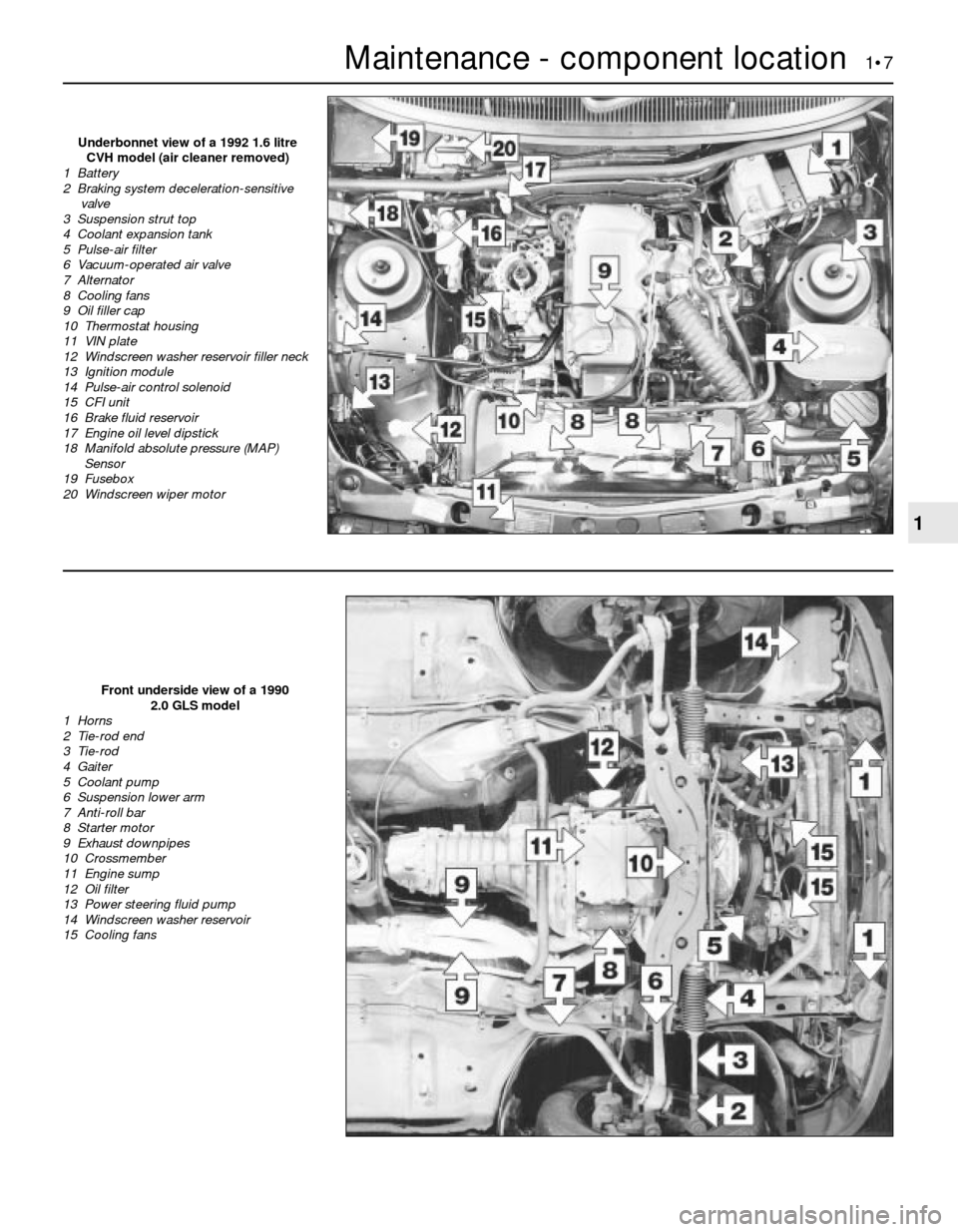
Maintenance - component location 1•7
1
Front underside view of a 1990
2.0 GLS model
1 Horns
2 Tie-rod end
3 Tie-rod
4 Gaiter
5 Coolant pump
6 Suspension lower arm
7 Anti-roll bar
8 Starter motor
9 Exhaust downpipes
10 Crossmember
11 Engine sump
12 Oil filter
13 Power steering fluid pump
14 Windscreen washer reservoir
15 Cooling fans
Underbonnet view of a 1992 1.6 litre
CVH model (air cleaner removed)
1 Battery
2 Braking system deceleration-sensitive
valve
3 Suspension strut top
4 Coolant expansion tank
5 Pulse-air filter
6 Vacuum-operated air valve
7 Alternator
8 Cooling fans
9 Oil filler cap
10 Thermostat housing
11 VIN plate
12 Windscreen washer reservoir filler neck
13 Ignition module
14 Pulse-air control solenoid
15 CFI unit
16 Brake fluid reservoir
17 Engine oil level dipstick
18 Manifold absolute pressure (MAP)
Sensor
19 Fusebox
20 Windscreen wiper motor
Page 8 of 22
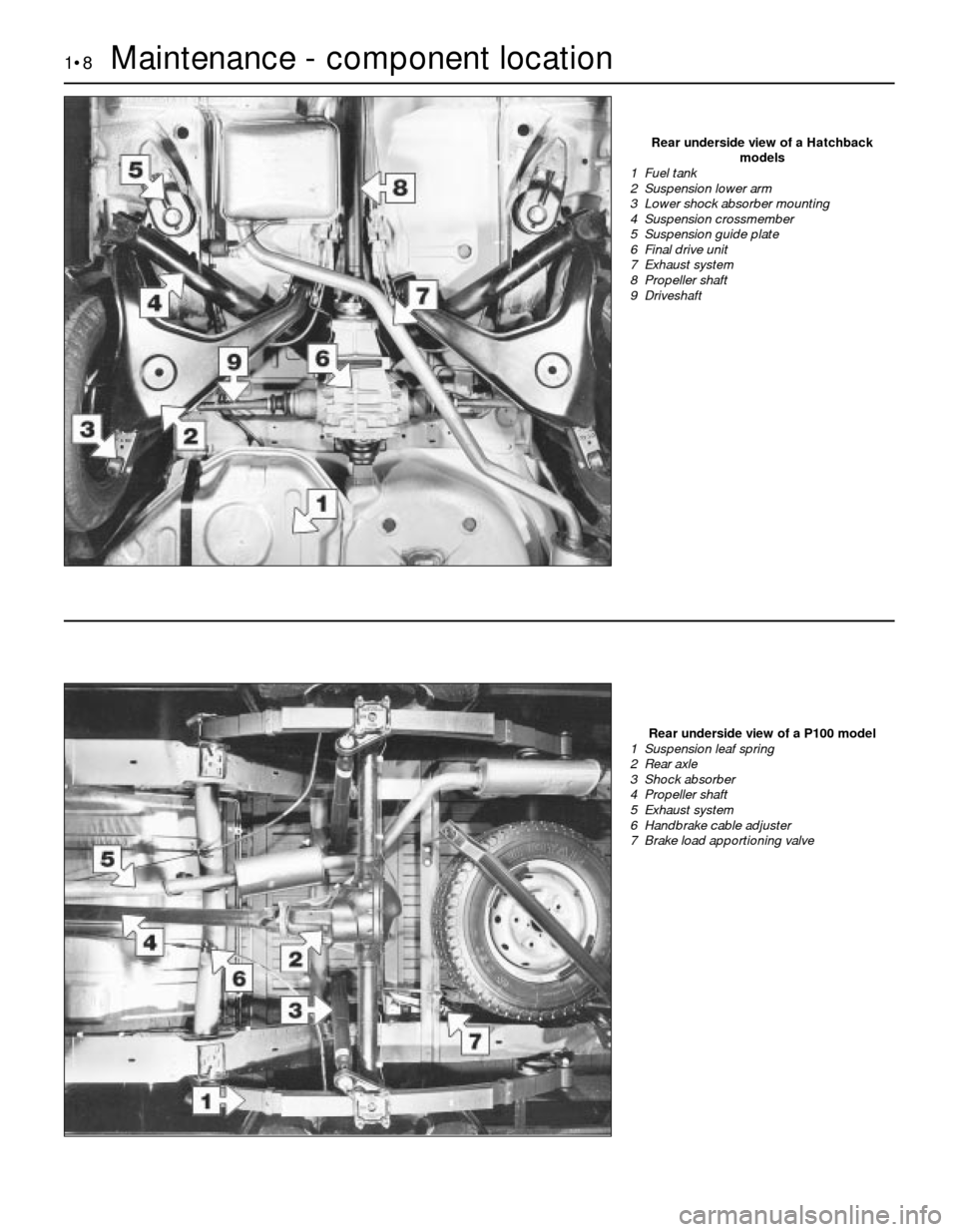
1•8Maintenance - component location
Rear underside view of a Hatchback
models
1 Fuel tank
2 Suspension lower arm
3 Lower shock absorber mounting
4 Suspension crossmember
5 Suspension guide plate
6 Final drive unit
7 Exhaust system
8 Propeller shaft
9 Driveshaft
Rear underside view of a P100 model
1 Suspension leaf spring
2 Rear axle
3 Shock absorber
4 Propeller shaft
5 Exhaust system
6 Handbrake cable adjuster
7 Brake load apportioning valve
Page 9 of 22
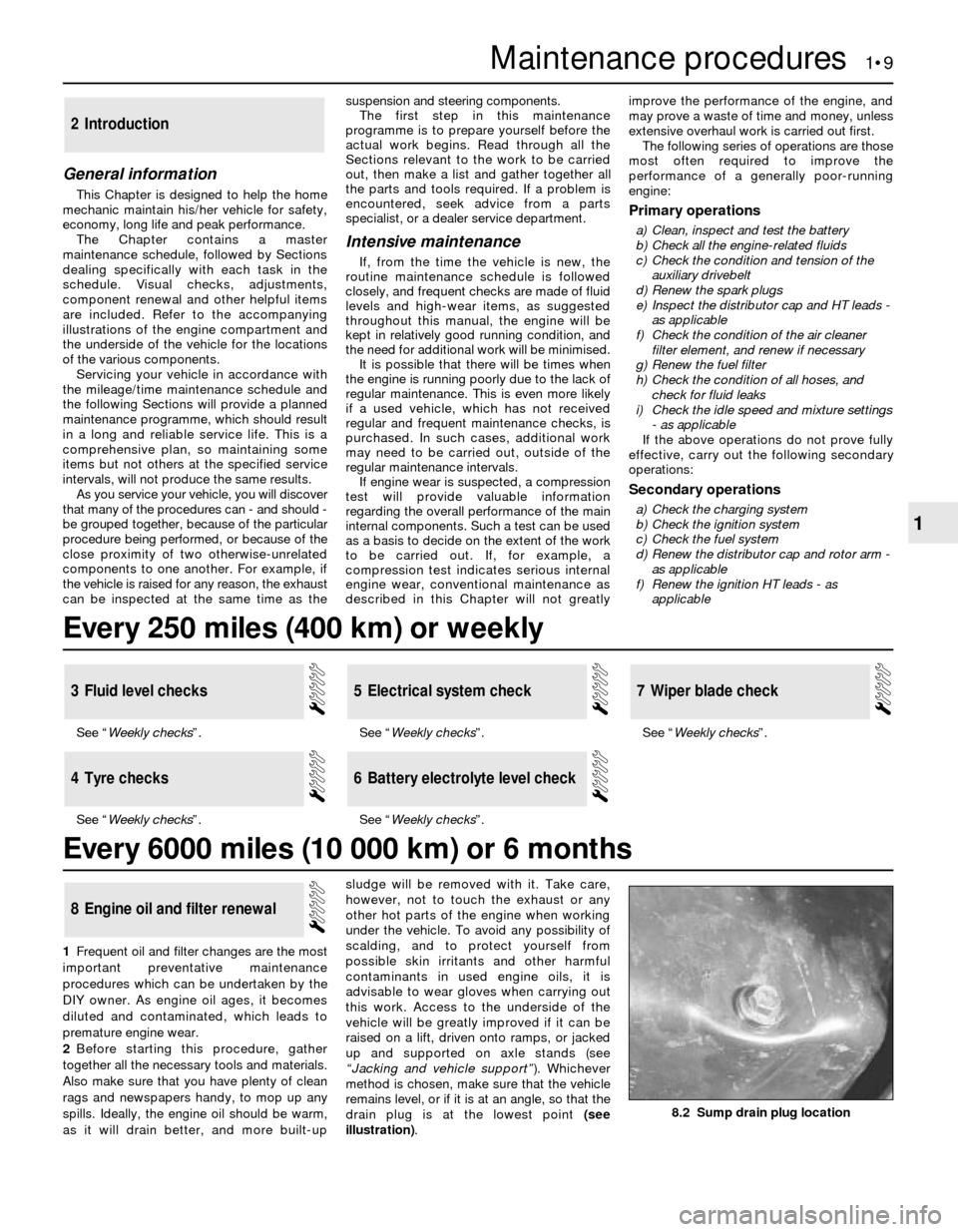
General information
This Chapter is designed to help the home
mechanic maintain his/her vehicle for safety,
economy, long life and peak performance.
The Chapter contains a master
maintenance schedule, followed by Sections
dealing specifically with each task in the
schedule. Visual checks, adjustments,
component renewal and other helpful items
are included. Refer to the accompanying
illustrations of the engine compartment and
the underside of the vehicle for the locations
of the various components.
Servicing your vehicle in accordance with
the mileage/time maintenance schedule and
the following Sections will provide a planned
maintenance programme, which should result
in a long and reliable service life. This is a
comprehensive plan, so maintaining some
items but not others at the specified service
intervals, will not produce the same results.
As you service your vehicle, you will discover
that many of the procedures can - and should -
be grouped together, because of the particular
procedure being performed, or because of the
close proximity of two otherwise-unrelated
components to one another. For example, if
the vehicle is raised for any reason, the exhaust
can be inspected at the same time as thesuspension and steering components.
The first step in this maintenance
programme is to prepare yourself before the
actual work begins. Read through all the
Sections relevant to the work to be carried
out, then make a list and gather together all
the parts and tools required. If a problem is
encountered, seek advice from a parts
specialist, or a dealer service department.
Intensive maintenance
If, from the time the vehicle is new, the
routine maintenance schedule is followed
closely, and frequent checks are made of fluid
levels and high-wear items, as suggested
throughout this manual, the engine will be
kept in relatively good running condition, and
the need for additional work will be minimised.
It is possible that there will be times when
the engine is running poorly due to the lack of
regular maintenance. This is even more likely
if a used vehicle, which has not received
regular and frequent maintenance checks, is
purchased. In such cases, additional work
may need to be carried out, outside of the
regular maintenance intervals.
If engine wear is suspected, a compression
test will provide valuable information
regarding the overall performance of the main
internal components. Such a test can be used
as a basis to decide on the extent of the work
to be carried out. If, for example, a
compression test indicates serious internal
engine wear, conventional maintenance as
described in this Chapter will not greatlyimprove the performance of the engine, and
may prove a waste of time and money, unless
extensive overhaul work is carried out first.
The following series of operations are those
most often required to improve the
performance of a generally poor-running
engine:
Primary operations
a)Clean, inspect and test the battery
b)Check all the engine-related fluids
c)Check the condition and tension of the
auxiliary drivebelt
d)Renew the spark plugs
e)Inspect the distributor cap and HT leads -
as applicable
f)Check the condition of the air cleaner
filter element, and renew if necessary
g)Renew the fuel filter
h)Check the condition of all hoses, and
check for fluid leaks
i)Check the idle speed and mixture settings
- as applicable
If the above operations do not prove fully
effective, carry out the following secondary
operations:
Secondary operations
a)Check the charging system
b)Check the ignition system
c)Check the fuel system
d)Renew the distributor cap and rotor arm -
as applicable
f)Renew the ignition HT leads - as
applicable
2Introduction
See “Weekly checks”.
See “Weekly checks”.See “Weekly checks”.
See “Weekly checks”.See “Weekly checks”.
7Wiper blade check
6Battery electrolyte level check
5Electrical system check
4Tyre checks
3Fluid level checks
1Frequent oil and filter changes are the most
important preventative maintenance
procedures which can be undertaken by the
DIY owner. As engine oil ages, it becomes
diluted and contaminated, which leads to
premature engine wear.
2Before starting this procedure, gather
together all the necessary tools and materials.
Also make sure that you have plenty of clean
rags and newspapers handy, to mop up any
spills. Ideally, the engine oil should be warm,
as it will drain better, and more built-upsludge will be removed with it. Take care,
however, not to touch the exhaust or any
other hot parts of the engine when working
under the vehicle. To avoid any possibility of
scalding, and to protect yourself from
possible skin irritants and other harmful
contaminants in used engine oils, it is
advisable to wear gloves when carrying out
this work. Access to the underside of the
vehicle will be greatly improved if it can be
raised on a lift, driven onto ramps, or jacked
up and supported on axle stands (see
“Jacking and vehicle support”). Whichever
method is chosen, make sure that the vehicle
remains level, or if it is at an angle, so that the
drain plug is at the lowest point (see
illustration).
8Engine oil and filter renewal
Maintenance procedures 1•9
1
8.2 Sump drain plug location
Every 250 miles (400 km) or weekly
Every 6000 miles (10 000 km) or 6 months
Page 15 of 22
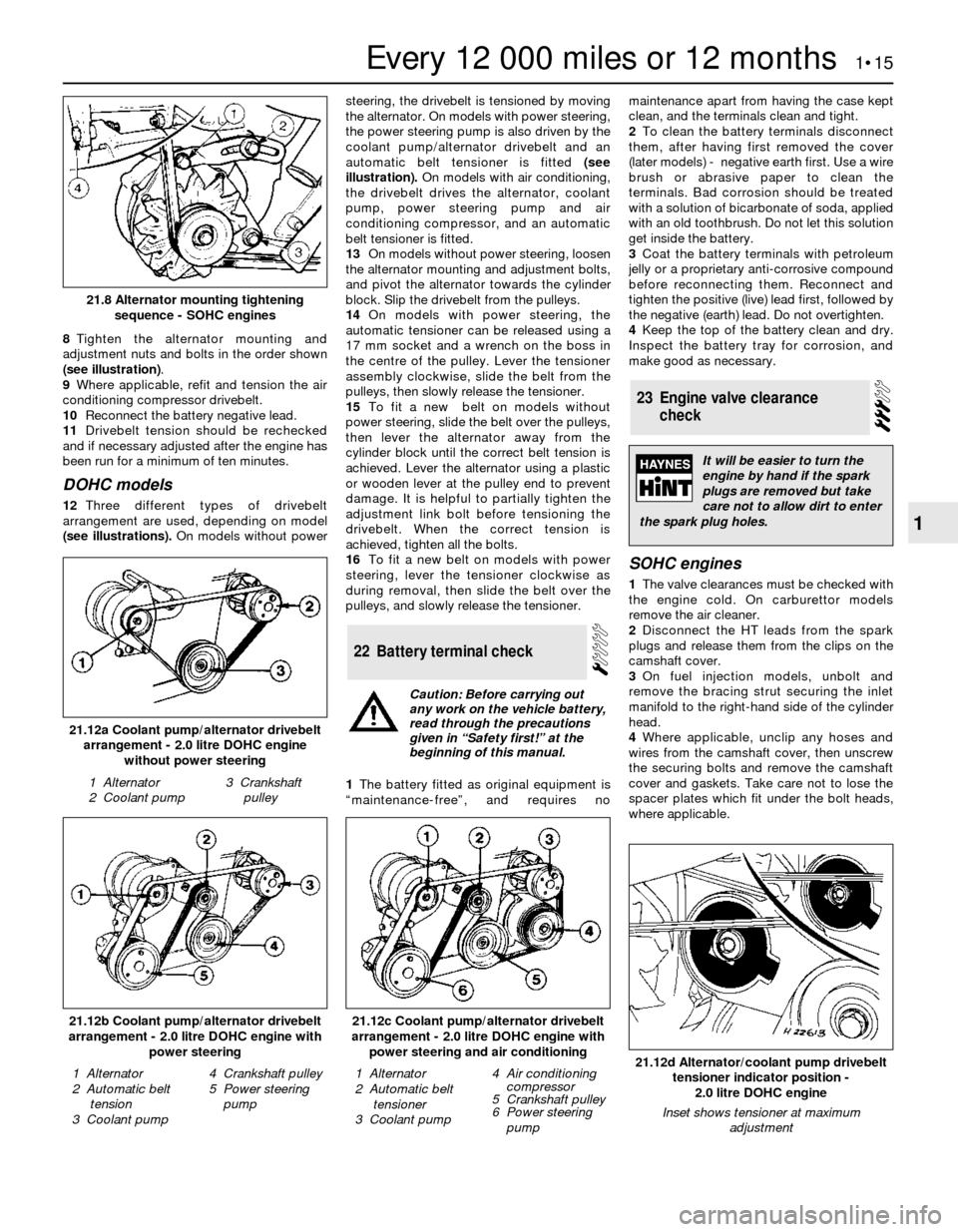
8Tighten the alternator mounting and
adjustment nuts and bolts in the order shown
(see illustration).
9Where applicable, refit and tension the air
conditioning compressor drivebelt.
10Reconnect the battery negative lead.
11Drivebelt tension should be rechecked
and if necessary adjusted after the engine has
been run for a minimum of ten minutes.
DOHC models
12Three different types of drivebelt
arrangement are used, depending on model
(see illustrations).On models without powersteering, the drivebelt is tensioned by moving
the alternator. On models with power steering,
the power steering pump is also driven by the
coolant pump/alternator drivebelt and an
automatic belt tensioner is fitted (see
illustration).On models with air conditioning,
the drivebelt drives the alternator, coolant
pump, power steering pump and air
conditioning compressor, and an automatic
belt tensioner is fitted.
13On models without power steering, loosen
the alternator mounting and adjustment bolts,
and pivot the alternator towards the cylinder
block. Slip the drivebelt from the pulleys.
14On models with power steering, the
automatic tensioner can be released using a
17 mm socket and a wrench on the boss in
the centre of the pulley. Lever the tensioner
assembly clockwise, slide the belt from the
pulleys, then slowly release the tensioner.
15To fit a new belt on models without
power steering, slide the belt over the pulleys,
then lever the alternator away from the
cylinder block until the correct belt tension is
achieved. Lever the alternator using a plastic
or wooden lever at the pulley end to prevent
damage. It is helpful to partially tighten the
adjustment link bolt before tensioning the
drivebelt. When the correct tension is
achieved, tighten all the bolts.
16To fit a new belt on models with power
steering, lever the tensioner clockwise as
during removal, then slide the belt over the
pulleys, and slowly release the tensioner.
1The battery fitted as original equipment is
“maintenance-free”, and requires nomaintenance apart from having the case kept
clean, and the terminals clean and tight.
2To clean the battery terminals disconnect
them, after having first removed the cover
(later models) - negative earth first. Use a wire
brush or abrasive paper to clean the
terminals. Bad corrosion should be treated
with a solution of bicarbonate of soda, applied
with an old toothbrush. Do not let this solution
get inside the battery.
3Coat the battery terminals with petroleum
jelly or a proprietary anti-corrosive compound
before reconnecting them. Reconnect and
tighten the positive (live) lead first, followed by
the negative (earth) lead. Do not overtighten.
4Keep the top of the battery clean and dry.
Inspect the battery tray for corrosion, and
make good as necessary.
SOHC engines
1The valve clearances must be checked with
the engine cold. On carburettor models
remove the air cleaner.
2Disconnect the HT leads from the spark
plugs and release them from the clips on the
camshaft cover.
3On fuel injection models, unbolt and
remove the bracing strut securing the inlet
manifold to the right-hand side of the cylinder
head.
4Where applicable, unclip any hoses and
wires from the camshaft cover, then unscrew
the securing bolts and remove the camshaft
cover and gaskets. Take care not to lose the
spacer plates which fit under the bolt heads,
where applicable.
23Engine valve clearance
check
22Battery terminal check
Every 12 000 miles or 12 months 1•15
1
21.12b Coolant pump/alternator drivebelt
arrangement - 2.0 litre DOHC engine with
power steering
1 Alternator
2 Automatic belt
tension
3 Coolant pump4 Crankshaft pulley
5 Power steering
pump21.12d Alternator/coolant pump drivebelt
tensioner indicator position -
2.0 litre DOHC engine
Inset shows tensioner at maximum
adjustment
1 Alternator
2 Automatic belt
tensioner
3 Coolant pump4 Air conditioning
compressor
5 Crankshaft pulley
6 Power steering
pump
21.12c Coolant pump/alternator drivebelt
arrangement - 2.0 litre DOHC engine with
power steering and air conditioning
21.12a Coolant pump/alternator drivebelt
arrangement - 2.0 litre DOHC engine
without power steering
1 Alternator
2 Coolant pump3 Crankshaft
pulley
21.8 Alternator mounting tightening
sequence - SOHC engines
Caution: Before carrying out
any work on the vehicle battery,
read through the precautions
given in “Safety first!” at the
beginning of this manual.
It will be easier to turn the
engine by hand if the spark
plugs are removed but take
care not to allow dirt to enter
the spark plug holes.
Page 17 of 22
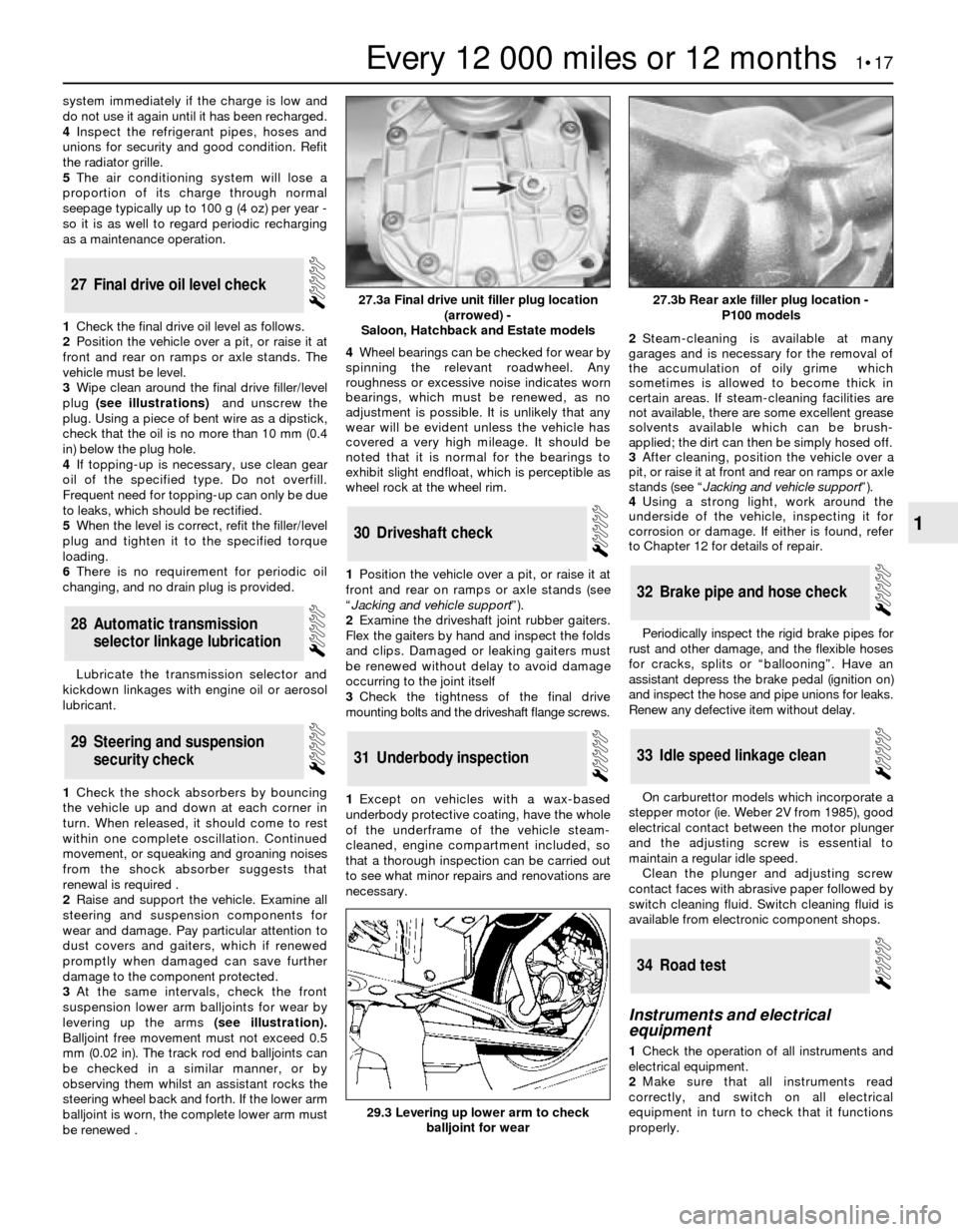
system immediately if the charge is low and
do not use it again until it has been recharged.
4Inspect the refrigerant pipes, hoses and
unions for security and good condition. Refit
the radiator grille.
5The air conditioning system will lose a
proportion of its charge through normal
seepage typically up to 100 g (4 oz) per year -
so it is as well to regard periodic recharging
as a maintenance operation.
1Check the final drive oil level as follows.
2Position the vehicle over a pit, or raise it at
front and rear on ramps or axle stands. The
vehicle must be level.
3Wipe clean around the final drive filler/level
plug (see illustrations) and unscrew the
plug. Using a piece of bent wire as a dipstick,
check that the oil is no more than 10 mm (0.4
in) below the plug hole.
4If topping-up is necessary, use clean gear
oil of the specified type. Do not overfill.
Frequent need for topping-up can only be due
to leaks, which should be rectified.
5When the level is correct, refit the filler/level
plug and tighten it to the specified torque
loading.
6There is no requirement for periodic oil
changing, and no drain plug is provided.
Lubricate the transmission selector and
kickdown linkages with engine oil or aerosol
lubricant.
1Check the shock absorbers by bouncing
the vehicle up and down at each corner in
turn. When released, it should come to rest
within one complete oscillation. Continued
movement, or squeaking and groaning noises
from the shock absorber suggests that
renewal is required .
2Raise and support the vehicle. Examine all
steering and suspension components for
wear and damage. Pay particular attention to
dust covers and gaiters, which if renewed
promptly when damaged can save further
damage to the component protected.
3At the same intervals, check the front
suspension lower arm balljoints for wear by
levering up the arms(see illustration).
Balljoint free movement must not exceed 0.5
mm (0.02 in). The track rod end balljoints can
be checked in a similar manner, or by
observing them whilst an assistant rocks the
steering wheel back and forth. If the lower arm
balljoint is worn, the complete lower arm must
be renewed .4Wheel bearings can be checked for wear by
spinning the relevant roadwheel. Any
roughness or excessive noise indicates worn
bearings, which must be renewed, as no
adjustment is possible. It is unlikely that any
wear will be evident unless the vehicle has
covered a very high mileage. It should be
noted that it is normal for the bearings to
exhibit slight endfloat, which is perceptible as
wheel rock at the wheel rim.
1Position the vehicle over a pit, or raise it at
front and rear on ramps or axle stands (see
“Jacking and vehicle support”).
2Examine the driveshaft joint rubber gaiters.
Flex the gaiters by hand and inspect the folds
and clips. Damaged or leaking gaiters must
be renewed without delay to avoid damage
occurring to the joint itself
3Check the tightness of the final drive
mounting bolts and the driveshaft flange screws.
1Except on vehicles with a wax-based
underbody protective coating, have the whole
of the underframe of the vehicle steam-
cleaned, engine compartment included, so
that a thorough inspection can be carried out
to see what minor repairs and renovations are
necessary. 2Steam-cleaning is available at many
garages and is necessary for the removal of
the accumulation of oily grime which
sometimes is allowed to become thick in
certain areas. If steam-cleaning facilities are
not available, there are some excellent grease
solvents available which can be brush-
applied; the dirt can then be simply hosed off.
3After cleaning, position the vehicle over a
pit, or raise it at front and rear on ramps or axle
stands (see “Jacking and vehicle support”).
4Using a strong light, work around the
underside of the vehicle, inspecting it for
corrosion or damage. If either is found, refer
to Chapter 12 for details of repair.
Periodically inspect the rigid brake pipes for
rust and other damage, and the flexible hoses
for cracks, splits or “ballooning”. Have an
assistant depress the brake pedal (ignition on)
and inspect the hose and pipe unions for leaks.
Renew any defective item without delay.
On carburettor models which incorporate a
stepper motor (ie. Weber 2V from 1985), good
electrical contact between the motor plunger
and the adjusting screw is essential to
maintain a regular idle speed.
Clean the plunger and adjusting screw
contact faces with abrasive paper followed by
switch cleaning fluid. Switch cleaning fluid is
available from electronic component shops.
Instruments and electrical
equipment
1Check the operation of all instruments and
electrical equipment.
2Make sure that all instruments read
correctly, and switch on all electrical
equipment in turn to check that it functions
properly.
34Road test
33Idle speed linkage clean
32Brake pipe and hose check
31Underbody inspection
30Driveshaft check
29Steering and suspension
security check
28Automatic transmission
selector linkage lubrication
27Final drive oil level check
Every 12 000 miles or 12 months 1•17
1
29.3 Levering up lower arm to check
balljoint for wear
27.3b Rear axle filler plug location -
P100 models27.3a Final drive unit filler plug location
(arrowed) -
Saloon, Hatchback and Estate models